

Water & Sanitation Africa
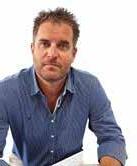
Complete water resource and wastewater management
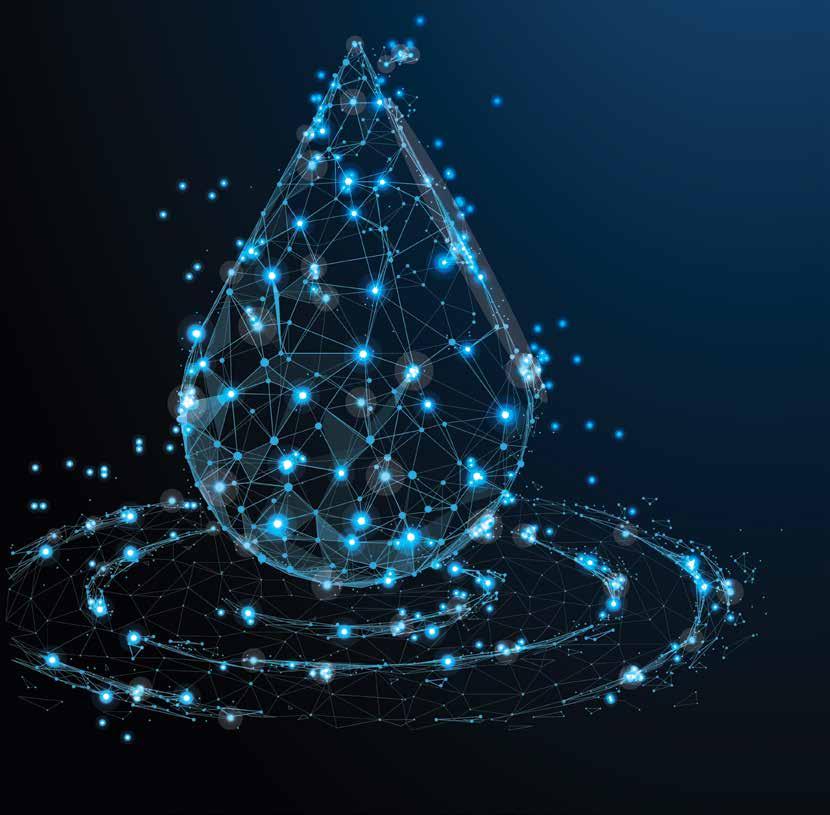
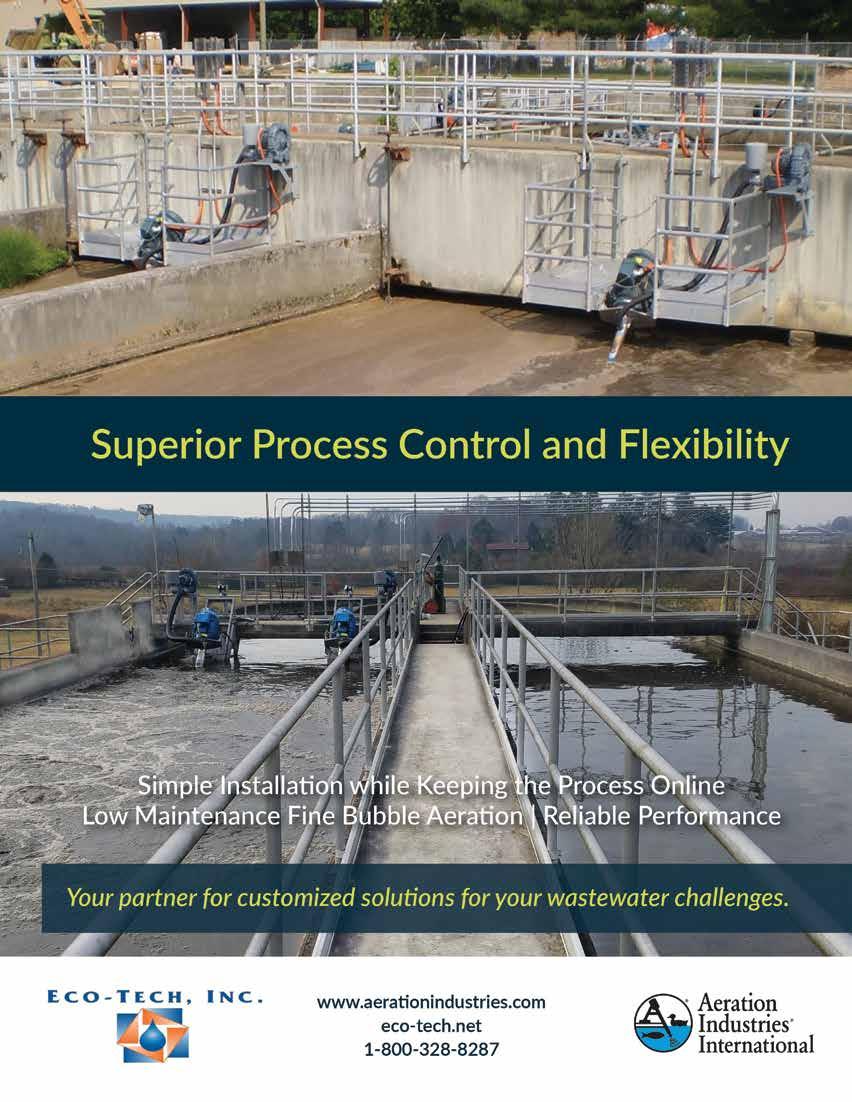

Mava Gwagwa n ew Business and Key a ccounts d irector, s B s tanks P10 Industry Ins I ght Under pressure
in the hot seat Industry 4.0 Keeping pace with technology s an I tat I on SA helps reinvent the toilet
“Due to the high-quality Zincalume® material employed and our w orld-class engineering processes, SBS Tanks are designed and engineered to have a lifespan of 60+ years under normal climatic and operating condi tions.”
rowan Blomquist CEO, Macsteel Fluid
Treat your water-energy like gold


















Unmet efficiency with up to 10%-20% energy cost reduction
Super high flow rate
Designed for superior cavitation resistance
High regulation capabilities
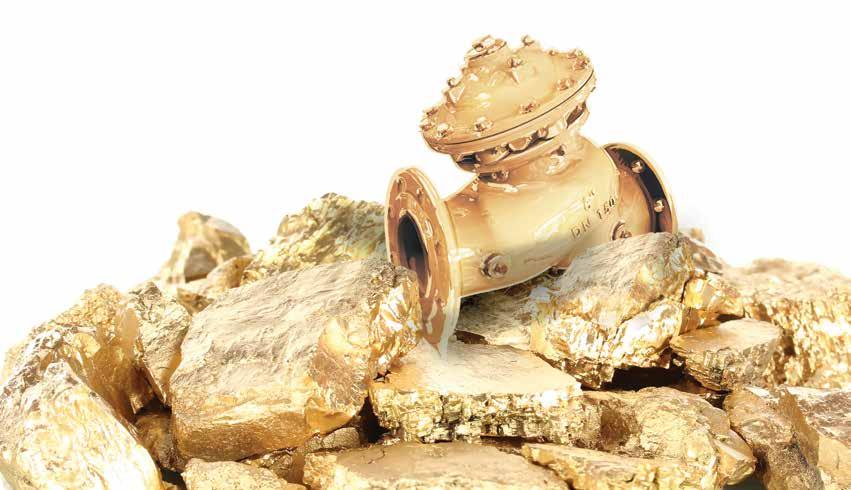

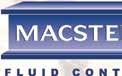



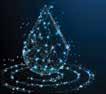
The water and wastewater industries are the guardians of one of the world’s most important resources, and continuous investment in infrastructure and new technologies is essential to their processes. endress+Hauser works to drive process automation, helping clients to increase their efficiency and ensure compliance. P4
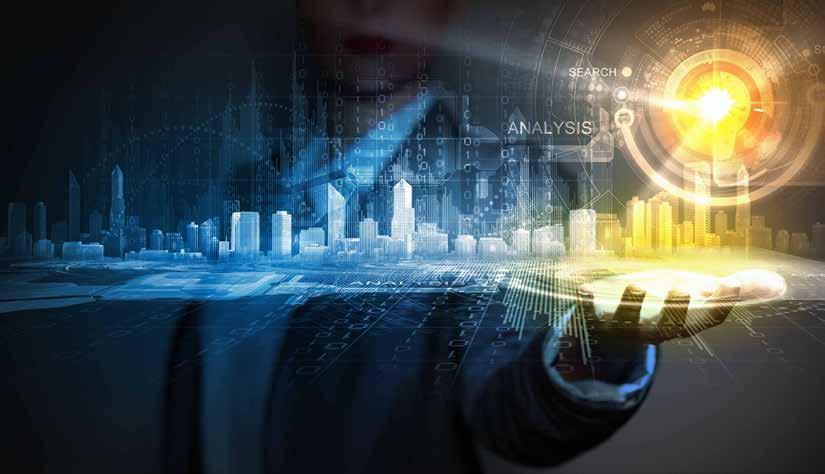
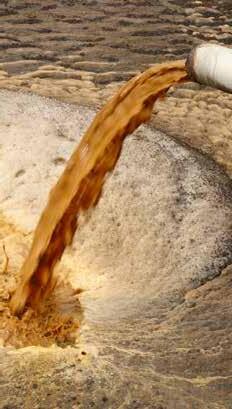
For the past 20 years, sBs has been actively contributing to south africa’s water security with its range of Zincalume water storage reservoirs. Mava gwagwa, new business and key accounts director at sBs Tanks discusses how access to water shapes a positive future. P10


south africa continues to lose millions of litres of water every year due to pipe leaks and bursts. pressure management is one of the most important interventions that should be considered when attempting to drive down water losses, explains rowan Blomquist, ceo, Macsteel Fluid control. P14
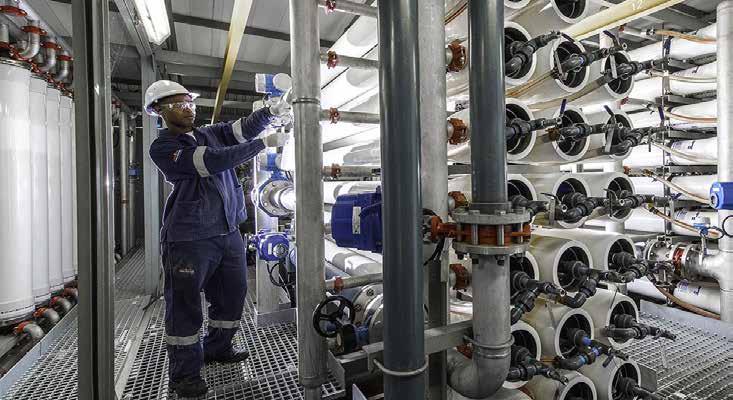
FroM WasTe To
Consistent quality requires consistent excellence ...

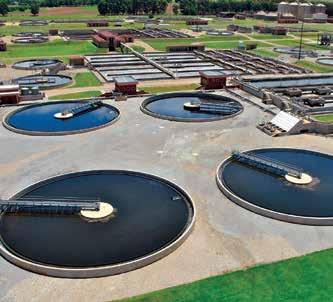
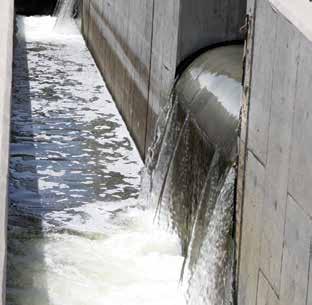
... in every area of wastewater management.
Serving both the public and private sectors, ERWAT promotes a healthy environment by providing cost-effective wastewater treatment solutions through innovative technologies. It specialises in sustainable, quality wastewater services, backed by focused technical, maintenance and engineering services. An ISO/IEC 17025 accredited laboratory renders a wide variety of specialised analyses, while industrial wastewater quality management assessments and advice are also offered.
East Rand Water Reg. No. 1992/005753/08
(Association incorporated in terms of section 21)
GPS Co-ordinates:
Address: Hartebeestfontein Office Park, R25, Bapsfontein/Bronkhorstspruit, Kempton Park.
Tel: +27 11 929 7000
E-mail: mail@erwat.co.za
www.erwat.co.za
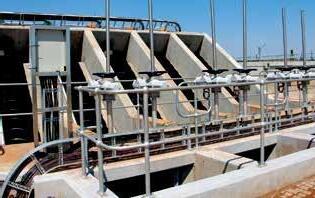

editor Danielle Petterson
Managing editor Alastair Currie
head of design Beren Bauermeister
Chief sub-editor Tristan Snijders
Contributors Lester Goldman, Derek G Hazelton, Valerie Naidoo, Carley Truyens
operations & production manager
Antois-Leigh Botma
Production coordinator Jacqueline Modise
Distribution manager Nomsa Masina
Distribution coordinator Asha Pursotham
Financial manager Andrew Lobban
Printers Paarl Media KZN
t +27 (0)31 714 4700
advertising sales Hanlie Fintelman
t +27 (0)11 467 6223 | c +27 (0)82 338 2266 h.fintelman@telkomsa.net
Publisher Jacques Breytenbach
Novus Print (Pty) Ltd t/a 3S Media 46 Milkyway Avenue, Frankenwald, 2090 PO Box 92026, Norwood 2117
Tel: +27 (0)11 233 2600 Fax: +27 (0)11 234 7274/5 www.3smedia.co.za
ISSN: 1990 - 8857
Annual subscription: R330 (SA rate) subs@3smedia.co.za
Copyright 2019. All rights reserved. All articles herein are copyright protected and may not be reproduced either in whole or in part without the prior written permission of the publishers. The views of contributors do not necessarily reflect those of the Water Institute of Southern Africa or the publishers.

WIsa Contacts:
Head office
Tel: 086 111 9472(WISA)
fax: +27 (0)11 315 1258
Physical address: 1st Floor, Building 5, Constantia Park, 546 16th Road, Randjiespark Ext 7, Midrand Website: www.wisa.org.za
BRaNChes
central Branch (Free State, Northern Cape, North West) chairperson: Dr Leana Esterhuizen company: Central University of Technology
Tel: +27 (0)51 507 3850 email: lesterhu@cut.ac.za
eastern cape: chairperson: Christopher Maduma company: Nelson Mandela Bay Municipality Tel: +27 (0)41 506 7527 cell: +27 (0)82 300 7044 email: citm@live.com
Gauteng chairperson: Ashwin Seetal company: CSIR
Tel: +27 (0)12 841 3477 cell: +27 (0)82 804 2852 email: aseetal@csir.co.za
KwaZulu-Natal
chairperson: Lindelani Sibiya company: Umgeni Water cell: +27 (0)82 928 1081
email: lindelani.sibiya@umgeni.co.za
Limpopo chairperson: Mpho Chokolo company: Lepelle Northern Water cell: +27 (0)72 310 7576
email: mphoc@lepelle.co.za
Mpumalanga Chairperson: Lihle Mbatha (Acting) Company: Inkomati-Usuthu Catchment Management Agency
Tel: +27 (0)13 753 9000
Email: mbathat@iucma.co.za
Western cape chairperson: Natasia van Binsbergen company: AL Abbott & Associates
Tel: +27 (0)21 448 6340
cell: +27 (0)83 326 3887
email: natasia@alabbott.co.za


Are you ready for change?
e’ve all heard buzzwords like Industry 4.0, 4IR and IoT, but what does any of it really mean?
The internet has made everyone’s lives significantly easier, but the new changes brought by the Fourth Industrial Revolution (4IR or Industry 4.0) could see life as we know it t urned on its head.
Described as disruptive technology, 4IR is characterised by a range of new technologies that are fusing the physical, digital and biologic al worlds – think self-driving cars and genetic engineering.
Developments like the internet of things (IoT) and artificial intelligence offer amazing capabilities, and we must ultimately accept that technology can perform many tasks better than humans. In the water space, we can look forward to advanced automation that ensures our plants run optimally, delivering the best quality outputs, and monitoring that is done automatically with little to no input.
However, it also makes the people who previously performed those tasks obsolete. It is expected that by 2025, one in three jobs will b e done by software, robots or smart machines. By 2030, it is anticipated that over 2 billion jobs will have disappeared (read more about this on page 19).
Preparing for change
So what does that mean for all those people put out of a job? I t means we must adapt and change.
It is believed that 60% of the jobs that will exist 10 years fr om now have not been invented yet, and basic computer programming will become a core skill required by over 40% of all jobs.
South Africa has realised that this change must be embraced. Pr esident Cyril Ramaphosa recently appointed a Presidential Commission on the Fourth Industrial Revolution, which will assist government in taking a dvantage of the opportunities presented by the digital industrial revolution. The aim is to identify relevant policies, strategies and action plans that will positi on South Africa as a competitive global player.
South Africa will also soon join the World Economic Forum's Cen tre for the Fourth Industrial Revolution Network (C4IR Network) alongside C hina, India and Japan. The Department of Science and Technology is expected to launch an Affiliate Centre in September as a public-private partnership b ased at the CSIR. The centre is expected to provide a platform for stakeholders i n South Africa to work together on the evolution of new technologies.
It is encouraging that South Africa is embracing the inevitable changes 4IR is bringing. The country faces many challenges, particularly in terms of poverty alleviation and the provision of education. However, it is vital that we embrace technology in addressing these issues and preparing people for a new era.
Minister of Science and Technology Mmamoloko KubayiNgubane even stated that it is no longer possible to discuss economic development without factoring in the impact of 4IR on the economy as a whole.
The world is changing, and South Africa must keep pace. It is time to embrace the change and incorporate new technologies into our businesses or risk being left behind and becoming obsolete.



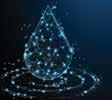
WIsa’s Vision Inspiring passion for water

Despite the fact that two-thirds of the earth’s surface is water, only 3% of this is fresh water, of which only one-third is available in liquid form. However, the world’s thirst is unquenchable. “All life and industries around the world depend on quality water in sufficient quantity,” elaborates Hennie Pretorius, industry Manager: Water & Wastewater, Endress+Hauser South Africa.
a valuable resource
From the water industry that collects and treats this valuable resource for drinking purposes to the downstream wastewater industry that collects and treats contaminated water before returning it to the natural water cycle, there are numerous processes that call for a great deal of measurement technology.
With a global focus on the water and wastewater industry, Endress+Hauser works to drive process automation, helping clients to increase their efficiency and ensure compliance.
Behind this global focus lie numerous small-scale activities devoted to this heavily fragmented industry.
“Although this is a global industry, it is driven by local demands and regulatory
The source of life
The
water and wastewater industries are the guardians of one of the world’s most important resources, and continuous investment in infrastructure and new technologies is essential to their processes.
requirements,” explains Pretorius. Megatrends such as demographic developments, urbanisation and climate change all impact differently from region to region.
In developed countries, for instance, most of the population has access to water and wastewater services. On the other hand, investments in infrastructure for water and wastewater treatment are only at the initial stages for many developing countries. In some regions, global companies shape the local market, acting simultaneously as planner, plant builder and operator. In other places, it is large national companies, while other services come from thousands of communal providers. In South Africa, the responsibility falls on municipalities and parastatal water boards.
Simple operation
“Globally, our customers have diverse needs, so we must adapt our instruments, solutions and services accordingly,” adds Pretorius. In general terms, the industry expects reliable, robust, simple-to-operate and low-maintenance measurement technology with an excellent priceperformance ratio. When building infrastructure, there is a tendency
to focus on lean, cost-optimised planning, as well as reliable systems that can be commissioned in a short period of time. In operation, focus shifts to matters such as efficiency improvements, resource conservation and modernisation.
Tighter regulations on water and wastewater quality also drive operators to make ongoing investments, such as fourth-stage treatment systems to remove micropollutants like pharmaceutical products and hormones. The new technologies required, in turn, increase system complexity and the degree of automation.
This extensive diversity is no challenge for Endress+Hauser. “We deeply understand our customers’ applications and processes thanks to our comprehensive industry knowhow and our strong expert network. We speak our customers’ language,” explains Pretorius.
A decentralised organisational structure allows Endress+Hauser to understand precise local requirements and situations, and respond quickly.
“We boast the industry's most extensive instrument portfolio and distinguish ourselves with a wide range of services and solutions. This allows us
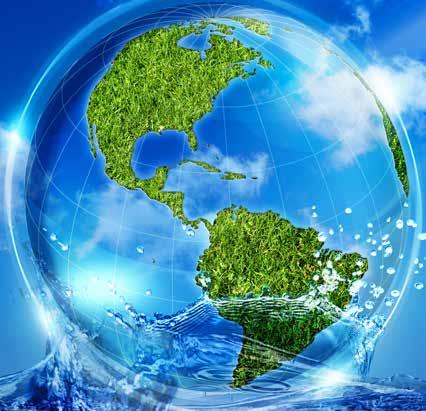
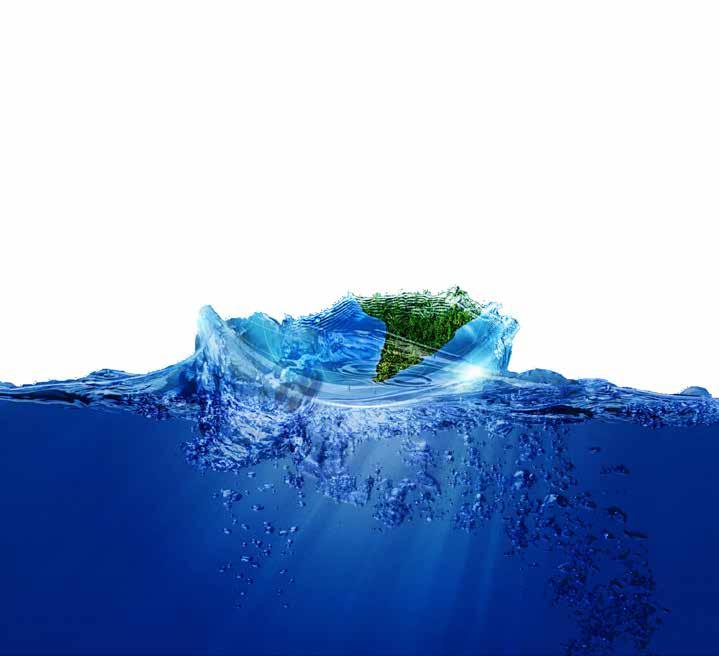
to offer our customers genuine added value.”
Globally anchored
In South Africa, Endress+Hauser's strength is in communal drinking and wastewater services, wherein lies significant growth potential, along with water reuse and desalination.
The key field of application is liquid analysis. The foundations of the company’s success in this area are the Liquiline platform and Memosens technology, both of which have evolved to a global standard, explains
Hennie Pretorius, Industry Manager: Water & Wastewater, Endress+Hauser South Africa.
Pretorius. These technologies provide digital communication between the advanced sensors and multichannel transmitter to allow for advanced diagnostics of the sensors.
Flow meters rank next, followed by level and pressure measurement technologies.
In the solutions area, Endress+Hauser offers: customised instrumentation cabinets, measurement containers and panels; asset management software; energy monitoring; and intelligent solutions for specific control tasks within treatment facilities. These aim specifically to limit nitrogen and phosphorus levels, even under fluctuating operational conditions, and thus ensure the optimal use of energy and chemicals. Services such as commissioning and flow verification, as well as maintenance and system audits for optimised plant upkeep assist to complete the complementary offering of products, services and solutions.

Endress+Hauser is already positioned to provide the right answers, and was recently nominated as a preferred supplier for critical analysis measurement points in Nereda, an innovative,
patented wastewater treatment process developed in the Netherlands. The technology requires only a quarter of the space of a conventional system and as little as half the energy, in addition to removing phosphate biologically without chemicals.
“This is proof that the industry views us as an innovative and reliable partner,” affirms Pretorius.
Ready for the future
So how does one go about building more compact systems, increasing process reliability, making better use of sludge and wastewater and, finally, conserving water as a resource? These are challenges facing operators all around the world. “In this industry, everything is forever in a state of flux,” says Pretorius. “Digitalisation, safety, efficiency and the industrial internet of things will frame the years ahead, and we have the solutions.”
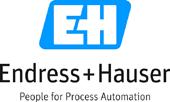
www.za.endress.com
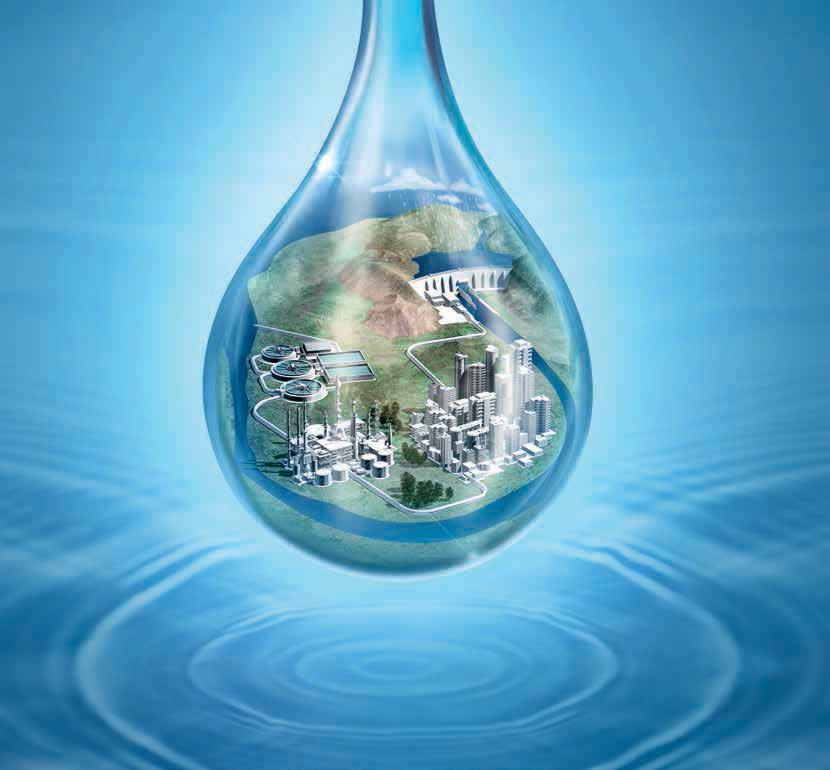
The cycle of solutions –water technology by KSB
Water is crucial for our survival – for every one of us, for all nations and peoples. Clean water supplies and efficient sewage treatment have never been more important. Prosperity and well-being depend on it, worldwide. KSB’s know-how and extensive pumps and valves product range help you meet all water supply and treatment requirements, efficiently and affordably. We are one of the few suppliers worldwide with endto-end solutions addressing all stages of the water cycle – from water extraction to sewage treatment.
KSB Pumps and Valves (Pty) Ltd
www.ksbpumps.co.za
Tel: +27 11 876-5600
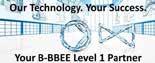
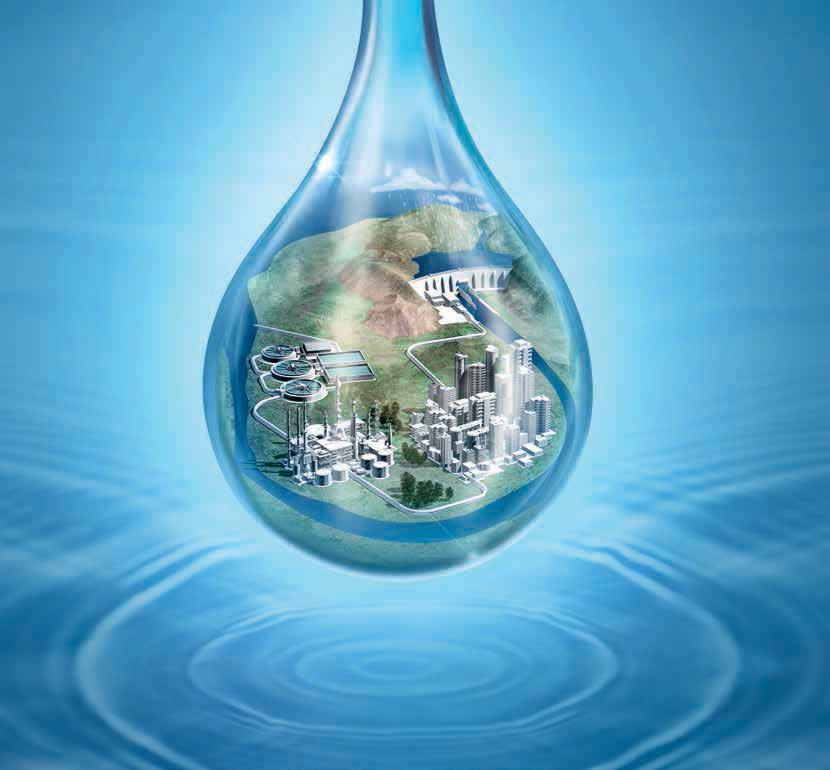
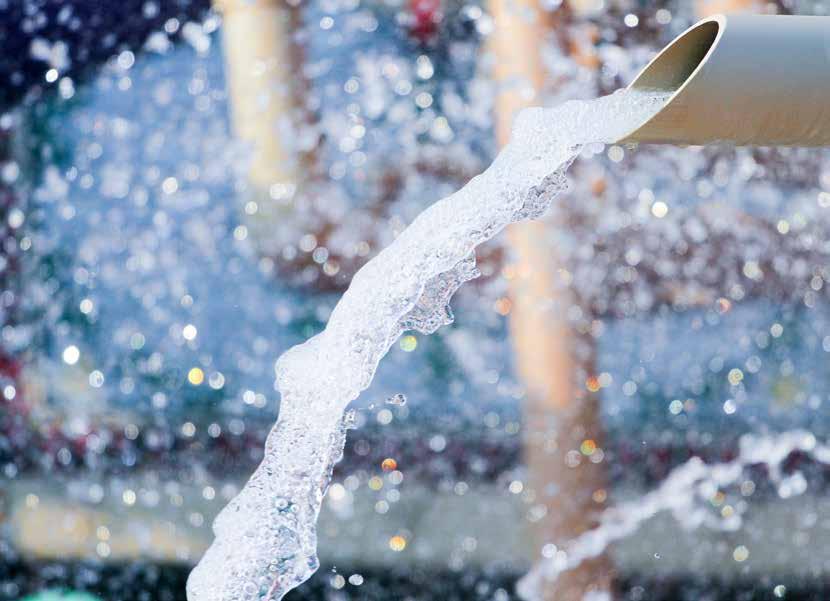
Embracing change
The degree and importance of automation at water and wastewater treatment plants have increased with the development of technology and ever-increasing treatment requirements. This issue of Water&Sanitation Africa focuses on automation and technology, aspects WISA is embracing in our efforts to support the African water sector.
WISA recently held its first ‘Membership Think Tank’ session, which saw members gather at four centres across the country and remotely connect to discuss strategic issues facing the water sector. Overall, I believe this inaugural event was a success, and we plan to grow these Membership Think Tank sessions in future to reach more members across the whole country. One of the prevailing concerns raised by members at this session was the need to reinstate the Blue, Green and No Drop reports. Last released in 2014, these reports provide a measure of efficacy for municipal treatment facilities, allowing for significant improvement and gap analysis, and therefore the opportunity for facility comparative analysis.
In 2018, the Parliamentary Portfolio Committee on Water reprimanded the Department of Water and Sanitation (DWS), for its ‘laxity’ in releasing these
reports. The sector needs these reports if there is to be any commitment to improving water quality and security. WISA has lobbied for the return and release of the Blue, Green, and No Drop reports for quite some time, and we will again raise this with the DWS, and offer support wherever we can.
e mbracing technology at ifaT a frica WISA is a proud partner to IFAT Africa and will be presenting on numerous topical issues during this show, being held from 9 to 11 July at Gallagher Estate. Also be on the lookout for the WISA Masterclass CPD events at IFAT, which provide unrivalled CPD value for money and excellent technical information. I am hoping to see many water sector professionals in attendance, especially our professional process controllers.
IFAT Africa will showcase numerous exhibitors, particularly in the automation and technology space, both local and global. If correctly
applied, the new technologies available present us with the opportunity to really close water quality gaps, and grow standards.
When (holding thumbs) the Blue, Green, and No Drop reports are released, I believe that automation and technology, along with the human development that WISA is focusing on, will be key to making significant improvements in these reports and the performance of the sector as a whole.
Dr Lester Goldman, CEO, WISA
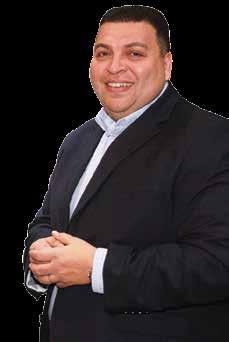
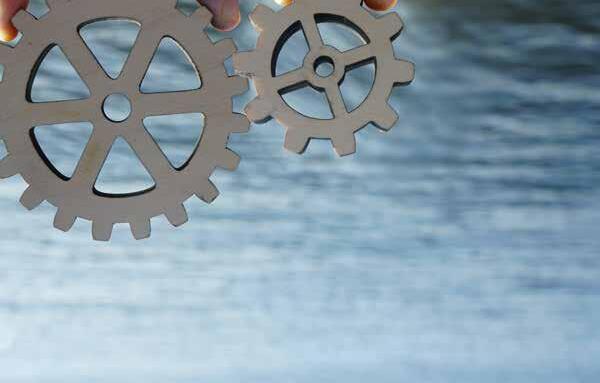
Is the water sector ready for Industry 4.0?
The world is moving into the Fourth Industrial Revolution, but is South Africa keeping pace? By
Dr Valerie Naidoo
The First Industrial Revolution shifted society from a largely agrarian and rural one to an industrialised and urban one, with the main symbol being the advent of the steam engine. It created a greater mobility for people, goods and services.
The Second Industrial Revolution transformed society through electricity and mass production into factories that were able to satisfy demand as never before. The Third Industrial Revolution is also called the digital revolution and transformed members of society from users of analogue and mechanical devices into ones that embraced the internet and personal computers. It also expanded the world from rural or urban to global markets.
We now sit with the Fourth Industrial Revolution (4IR or Industry 4.0), which is creating innovations that sit within the physical, biological and digital nexus, propelling disciplines such as the
industrial internet of things, robotics, nanotechnology, artificial intelligence and quantum computing to the forefront and disrupting systems of manufacture, scale, management and governance. The latter two revolutions are also contributing to societal disruptions making information available in real time, with little filtering, and leading to all sorts of privacy and ownership questions on data.
Sa in relation
The truth is that South Africa is sitting in the latter three stages of industrial revolution, with major portions of our society finding greater freedom and mobility to shift from agrarian to urban livelihoods. In addition, government policies are trying to drive a manufacturing economy but without fully embracing a high-productivity, mass production and highly mechanised system of factories – which is what is
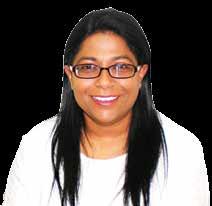
required to truly grow and compete in global markets.
In this regard, maybe the ship has sailed globally and it is time to embrace highquality niche markets with huge returns, while embedding 4IR and incubating the next big industry shift for the country. For the water sector, the big question is: what are the opportunities, challenges, and preparations required to derive benefits from this inevitable shift?
As the world of water planning and management becomes increasingly complex, demanding and difficult, it is important to understand the opportunities that the digital and 4IR offer for the water sector, while managing the dangers of cybersecurity. Several Water Research Commission studies have explored the opportunities for ICT in the water sector but have not really engaged in 4IR in a significant way. It has, however, funded academics around artificial neural networks (ANNs)
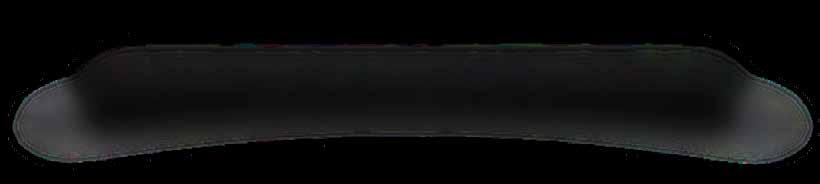

Dr Valerie Naidoo, chair, WISA
to evaluate opportunities to manage complexity. ANNs offer growing cities the opportunity to map their settlements as neural networks to better manage demand (service delivery), preventative maintenance, supply and customer satisfaction. The ICT platforms that we have engaged with in water have been largely around the Third Industrial Revolution and smarter data capture and use, improving monitoring, evaluation and learning, and flirted with automation – which is shot down every time as anti-labour.
accelerating adoption
The truth is that if government is to realise 4IR, then government itself has to become the early adopter of technologies and systems. A failure to do so puts our governance capability to manage the industry and cities of the future at risk. A deep and nuanced discussion is required with all unions, as the failure to move forward (and to be trained on new skills) runs the risk of South Africa being left behind by the world and investment. The most important side, however, is perhaps being left behind on improving one’s quality of life and work.
The water sector has been slow to adopt biosensors, sensors, drones, automation and analytics as a way to effectively manage the water business and integrate data, and share the costs of data capture and infrastructure management to the benefit of improved services and connectivity to our communities. In order to make it happen, decision-makers need to invest in models and integrated systems, the building of new capability in-house within government departments, while also investing in SMMEs that will support such systems and integrated networks. 4IR could allow us to fulfil both the human-centric approach to community participation and engagement, while shifting rural communities closer to decision-making and problem-solving spaces. But this type of shift calls for a bold set of leaders with the vision to go beyond the norm, driving the correct investments for such an integration platform. Imagine a world with a democratisation of data and information that empowers society, municipalities, government, businesses, customers, farmers, and decisionmakers in real time, while learning rapidly enough from scenarios to provide alerts and scenarios for planning and the investment of resources.


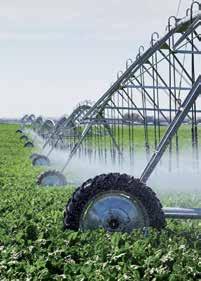

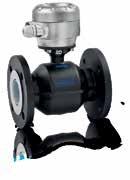
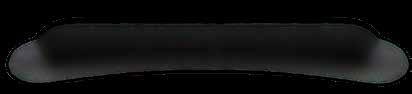

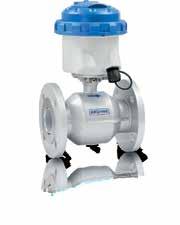
Precise monitoring of water flows and leak detection in irrigation networks
WATERFLUX 3070 –technology driven by KROHNE
• Electromagnetic water meter with integrated temperature and pressure measurement
• Line pressure monitoring for leak detection or pump efficiency control
• Multiple power concept for any location
• Remote transmission of readings and meter status as option
KROHNE South Africa
8 Bushbuck Close, Corporate Park South Randjiespark, Midrand, Tel.: +27 113141391
Fax: +27 113141681, Deon Rampathi, d.rampathi@krohne.com, www.za.krohne.com
All-terrain water storage
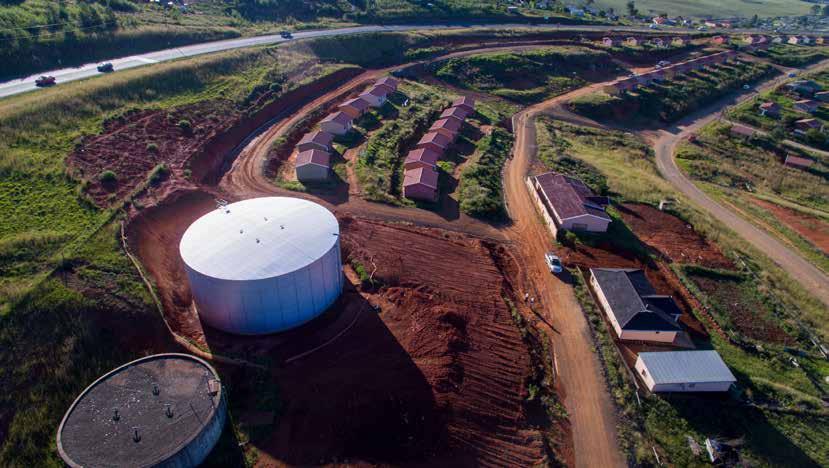
For the past 20 years, SBS, has been actively contributing to South Africa’s water security with its range of Zincalume® water storage reservoirs. Mava Gwagwa, new business and key accounts director, SBS Tanks, discusses how access to water shapes a positive future.
How is your traditional market base evolving?
MG We face many challenges as a country in terms of food and water security. In response, SBS has positioned itself to cater for both areas, responding to the needs of communities and industries. We regard agriculture as a key growth sector serving both formal and informal farming initiatives. In response, SBS has developed bespoke wet and dry storage solutions. These include a complete range of silos, conveying and drying equipment for the storage and processing of grain.
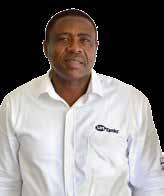
What is SBS Tanks’ past experience with rural farming communities?
The key requirement for every cultivating activity is a sustained water supply, which we cover with our tank solutions. We’ve also responded on the dry storage side, with an innovation that overcomes the lack of access to mechanisation and capex – post-harvest losses due to inefficient grain storage are a major problem. SBS Agri has developed a range of mechanical-pulley-driven grain storage hoppers for rural farming communities, which do not require electricity to operate.
How is SBS responding to drought alleviation initiatives?
A recent project entailed the installation of our tanks for a desalination plant in Cape Town. These were designed and commissioned in conjunction with Quality
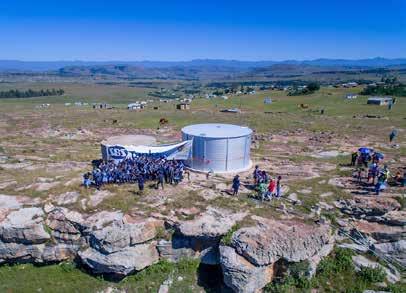
Filtration Systems to supply the Cape Town International Convention Centre with all its potable water requirements. For this particular project, three different tanks were installed to meet the various stages of the reverse osmosis and filtration process. Together, they provide a total of 436 000 litres of water storage.
is SBS working with municipalities and government agencies to find workable solutions to the infrastructure backlog? Yes, SBS assists in eradicating water supply backlogs and fast-tracking service delivery. The economic climate has made it necessary to focus on reprioritising existing resources towards areas where the most value can be derived for all South Africans.
Budget discussions take place with function groups that are made up of various institutions across the three

Learners in McClear in Joe Gqabi Municipality joyfully celebrate the handover of their newly installed tank
Mava Gwagwa, New Business and Key Accounts Director, SBS Tanks
spheres of government. These are strategically grouped to facilitate subject-specific discussions, targeting service delivery. By way of example, for Mandela Day 2018, SBS partnered with Salga KwaZulu-Natal to donate a tank to Mandlenkosi Primary School in Greytown. Pupils previously had to collect water from a nearby river.
What about opportunities for reuse?
Due to climate and environmental changes, treated wastewater has many downstream benefits. These include the irrigation of crops. If we look at the pig farming industry, for example, manure from the animals is pumped into anaerobic ponds and the solids removed. The wastewater is then used for irrigation purposes. Building roofs in general also presents excellent opportunities for rainwater harvesting. The water captured is treated and stored in SBS’s purpose-built range of reservoirs for downstream applications.
does Zincalume offer unique benefits? Yes, definitely. The prefabricated Zincalume methodology helps fast-track conveyance and installation. Zincalume panels consistently prove to be the superior choice, as they are lighter and easier to work with.
These tanks are:
• strong and resistant to damage caused by storms, wind and lightning
• robust and easy to repair
• sustainable, being 100% recyclable
• environmentally friendly – water is not exposed to unhygienic conditions
• easy to repair and maintain.
The largest SBS Tank – the ST31-09 – is designed to hold around 3.3 million litres of liquid and can be installed and commissioned in 17 days.
Because of their modular design, these tanks are easy to transport to site, especially in remote locations. For example, SBS has supplied drinking water tanks to a yoga resort on a Greek island. The tanks were transported over a number of trips via small boat from the mainland.
You don’t need to construct infrastructure like roads to access the build location, as would be the case with typical concrete reservoirs. Additionally, SBS’s reservoirs are installed utilising a jacking system from ground level, which
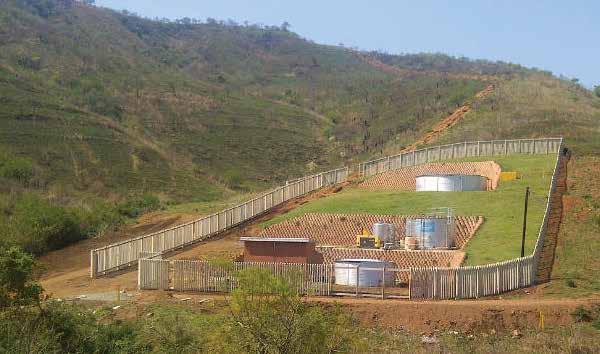
This SBS treatment plant in eMbuthweni, Mpumalanga, was developed to provide water for the municipality
means there is no need for scaffolding or cranes on-site.
are there opportunities for SMMe development?
Government has prioritised entrepreneurship and the advancement of SMME businesses as the catalyst to achieving economic growth and development. SBS’s systems are a good match for small and medium-sized contractors due to the low establishment costs. For our large tanks, a simple concrete ring beam base forms the foundation.
SBS has a database of preferred suppliers, which are provided with indepth training, project management and quality control support. It is mandatory for all suppliers to comply with SBS policies and procedures, specifications and standards.
What’s the typical lifespan of an SBS tank?
Due to the high-quality Zincalume material employed and our world-class engineering processes, SBS Tanks are designed and engineered to have a lifespan of 60+ years under normal climatic and operating conditions. Our tanks also carry a 12-month workmanship and materials guarantee. In addition, a 10-year non-leak warranty is applicable, provided the tank is installed by an approved SBS installer.
How is SBS making a difference in terms of its own social responsibility initiatives?
contact with our communities. We are achieving this through repeated brand exposure and shared PR opportunities, such as our upcoming ‘Build for Better’ campaign.
We believe strongly in nation-building: the belief that we all have a role to play in lifting our communities, our lives, and our country for the benefit of all. Our aim is to highlight the great stories that emanate from ordinary South Africans, be it through entrepreneurial efforts, community efforts or even a single act of kindness.
Other more traditional CSI projects we participate in include our annual cold drink donations. We sell cold drinks to staff throughout the year and the revenue collected is shared among local organisations at our annual Employee Appreciation Day.
We’re excited about our latest partnership with KwaCutswayo Primary School. This will see us donating toys for the grade R learners. These toys are made at a workshop within our office park. Members of staff have volunteered their time to assist in making them. The school is within 7 km of our factory and, therefore, a part of our community.
We have a number of other programmes we are embarking on, which include starting our own vegetable garden. Wherever possible, this garden will be irrigated via rainwater harvesting.

The SBS vision is to build long-term partnerships by having continuous www.sbstanks.com
Registration and abstracts submissions is
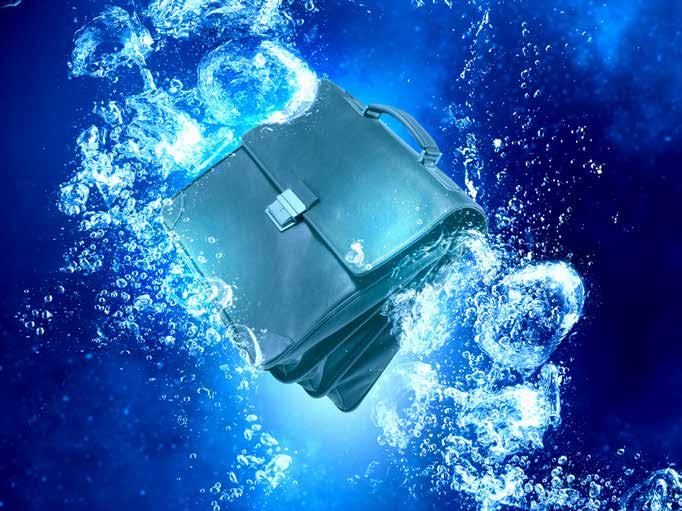
20 - 23 October 2019
Durban ICC, Kwazulu-Natal

Individual Registration
https://confco.eventsair.com/ wisaywp2019/registration/Site/Register

Group Registrations
https://confco.eventsair.com/ wisaywp2019/groupreg2019/Site/ Register
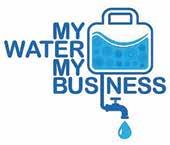
thandeka@confco.co.za
joanne@confco.co.za
Lindelani.sibiya@umgeni.co.za
Early bird rates are available so be sure to register early so as not to miss out!
Abstract Submission
Should you wish to submit an abstract https://ywpzaconference2019.co.za/ abstracts/
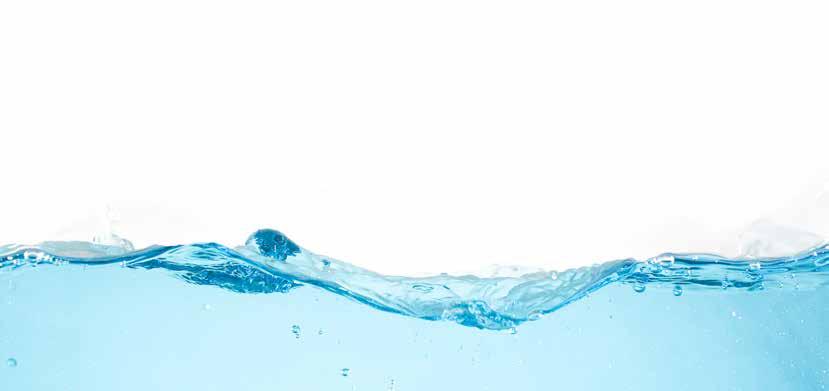
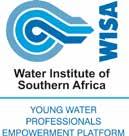
www.ywpzaconference2019.co.za
Changing the Narrative
The South African Young Water Professionals (YWP-ZA) Gauteng Chapter hosted an event entitled ‘Changing the Narrative’, which took place on 15 February 2019 at the Department of Water and Sanitation.
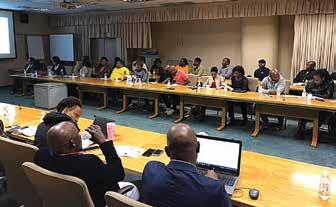
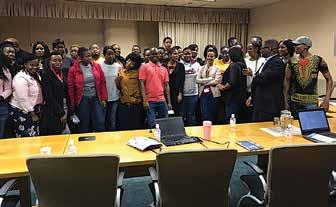
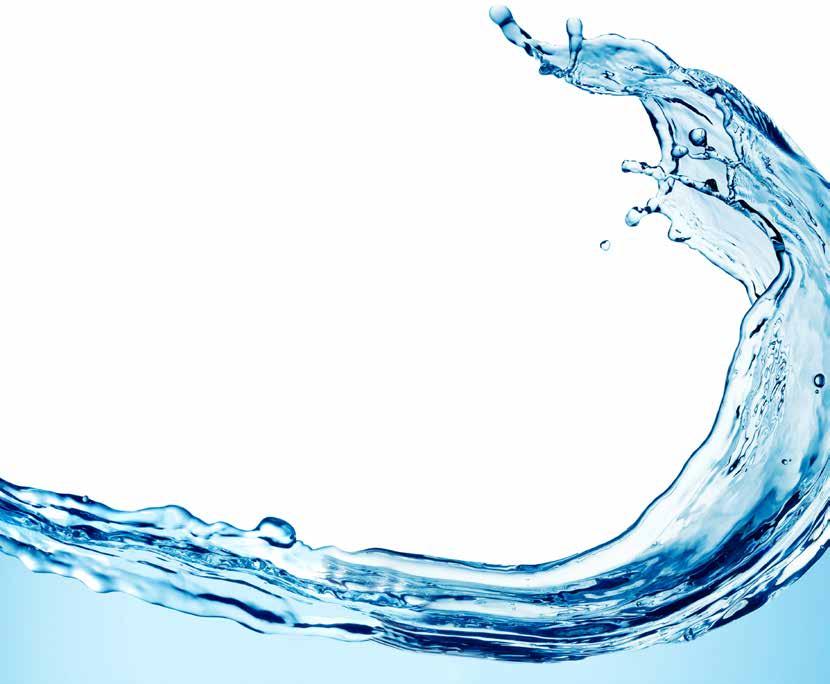
The event was opened by the provincial lead, Ms Vanessa Weber, who presented a holistic view of young water professionals in South Africa, highlighting their aim and function. Ms Weber alluded to the fact that “there is a need for an active role for WISA and IWA in the water sector”. She also indicated that, currently, the water sector “lacks the voice of the youth”. YWP-ZA provides a platform for the youth to reach their maximum potential.
This is achieved by young water professionals hosting events such as this, to provide a platform for the youth to engage with experts in the industry. YWP-ZA aims to have an active impact on the water sector, be it in the governmental space, private sector, parastatals or in research institutions. All the activities during the events are planned by young water professionals to facilitate soft-skill training and development.
The turnout was excellent, with over 100 delegates attending. Ayesha Laher, director, AHL Water, a speaker at the event, emphasised the point that young water professionals are “water warriors for South Africa”. She highlighted the fact that South Africa has good policies; however, it faces challenges in implementing these policies, but young water professionals can play a role in remedying this.
Nick Tandi, from the World Bank, representing WRG 2030, another speaker at the event, delivered an address, entitled ‘Excellence at the basics or constantly innovating? The likely future world of work for young professionals’. He alluded to the fact that more funding is required to meet the 2030 target than is currently available. Furthermore, he indicated that water recycling will be a reality much sooner than expected.
As young water professionals in South Africa, we are encouraged to adapt to the current disruption of the Fourth Industrial Revolution.
Participants of the recent Changing the Narrative event hosted at the Department of Water and Sanitation in Johannesburg
Under pressUre
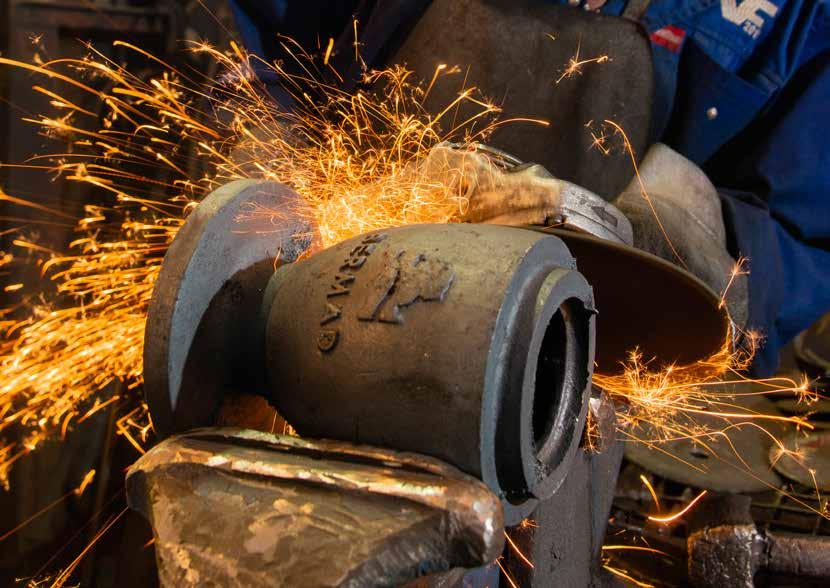

The common factor in every water system is the fact that leakage is driven by pressure. Reduce the pressure, even for a short period, and you reduce water leakage, explains Rowan Blomquist, CEO, Macsteel Fluid Control.
Possibly one of the simplest solutions in this regard is the use of pressurereducing valves (PRVs). These offer a way to easily and cost-effectively control the maximum pressure entering a zone. As the local supplier for Bermad products, Macsteel Fluid Control offers a range of PRVs that can help utilities to protect their water supply.
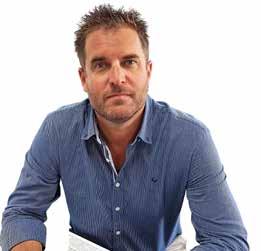
South Africa continues to lose millions of litres of water every year due to pipe leaks and bursts. Pressure management is one of the most important interventions that should be considered when attempting to drive down water losses.
case study: Monterrey
Monterrey is one of the largest cities in Mexico, and its rapid economic and population growth has continuously stressed the water distribution networks.
With the goal of becoming Monterrey’s top water provider, the Servicios de Agua y Drenaje de Monterrey (SADM) water utility turned to Bermad Mexico to help improve its ability to maintain the minimum water pressure while reducing leakages and pipe bursts.
Having experienced significant growth over the past 50 to 60 years, the city has repeatedly faced the threat of insufficient water supplies. At one time, the city relied entirely on wells located in and near the urban area. However, with the current population of almost five million people,
the city has had to develop new sources of water and now relies on surface water for about 60% of its water supply.
At the same time, its watershed ranks as one of the poorest in the world, with a per capita water use of just 290 ℓ per day per person – compared to a significantly higher global average of 3 795 ℓ
In the late 1990s, in an effort to proactively address its water supply problems, Monterrey began implementing district metering areas (DMAs) designed to serve clusters of about 300 to 400 customers. Now, with more than 3 300 DMAs, the city is able to monitor flows within much smaller areas, facilitating better leak detection and location.
In 2014, the city estimated that less than 6% of the water entering the distribution system was lost to leakage. However, given its vulnerability to water shortages in the face of continued growth, the city continues to look for ways to mitigate water loss within its distribution system.
Rowan Blomquist, CEO, Macsteel Fluid Control
Leakages and frequent bursts in distribution lines continue to be a problem in Monterrey, primarily due to the lack of adequate pressure regulation. In addition to the costs associated with non-revenue water, fixing burst and leaking pipes is a time-consuming and expensive process.
During times of peak demand, the pressure in Monterrey’s pipes is generally offset by water withdrawals. However, without a change in pressure to adjust for lower consumption at night, the pressure in its distribution system increased, causing leakage and pipe bursts. Monterrey needed a cost-effective way to reduce the average pressure during non-peak hours.
The Bermad solution
The solution to Monterrey’s problem was to install PRVs at strategic points in the system to manage the pressure. This allowed the minimum critical pressure to be dropped at low-demand times, such as in the afternoon or at night.
The utility conducted a hydraulic analysis and reviewed the sectorisation of the entire system to determine where the new valves would have the greatest impact. Then, in addition to providing the necessary valves, Bermad provided training to utility staff to help them bring the valves online and teach them how to properly calibrate and operate them.
In Monterrey, Bermad recommended the 7PM Flow Compensated PRV – a hydraulically operated, diaphragmactuated water PRV that automatically optimises downstream pressure according to the water demand.
This model offers many advantages, including operational cost savings and reliability because it does not rely on electrical power. It is also serviceable in-line and easy to install, requiring no
additional pipeline accessories. The 7PM’s double-chambered design allows for moderated valve reaction, which provides better protection for the valve diaphragm and system piping. Furthermore, the valve features a V-port throttling plug to provide a more accurate, stable and smoother response during pressure and flow regulation – particularly at low flow – while reducing noise and vibration, and increasing valve travel to optimise performance.
The results
SADM installed 16 of Bermad’s 7PM water pressure management valves over a period of six months.
Before the installation, the pressure was roughly 7 bar to 8 bar, with a consumption rate of 27 ℓ/s. Now, during non-peak hours, the valve automatically triggers a lower-pressure regime to help avoid leakage and burst frequency. The average pressures have since fallen to within 1.7 bar to 2.9 bar, and the minimum flow range reduced by 50%, while the maximum flow was reduced by 15%.
With a better-regulated system, SADM experiences fewer pipe bursts, resulting in reduced repair costs and water savings. In addition to reducing leakage by 50% to 60% in the areas where the 7PM valves were installed, the utility also recovered its entire investment in less than one year.
Following these dramatic improvements, SADM is now planning to install several more valves in eight additional areas.
Successful solutions
The Monterrey project offers an excellent example of how a well-planned pressure management programme can significantly reduce not only the volume of loss due to leakage, but also the costs associated with repairing pipes. The long-term impact is expected to result in even greater savings by reducing the occurrence of bursts and thereby extending the life of the system.
After supplying a number of well-known products for over 40 years, Macsteel Fluid Control is now manufacturing quality Bermad products locally. In line with government’s drive to boost local production, Macsteel Fluid Control has worked closely with Bermad to fine-tune the local casting and assembly of Bermad control and air valves to the necessary standards. The locally cast product will be exactly the same as the imported product in terms of quality and performance.
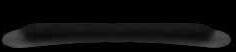
“Considering South Africa loses an estimated 37% of its potable water through leaks – representing approximately R7 billion in potential revenue – it is clear that PRVs have significant potential to secure water savings in South Africa,” comments Blomquist.
Bermad, together with local supplier Macsteel Fluid Control, offers a wide range of PRVs, providing costeffective solutions for any pressure management issue.

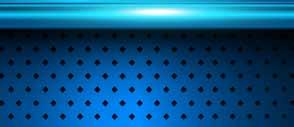

Bermad goes local


AFrICA
Water and sanitation in Africa
Citywide sanitation services
The Africa Urban Sanitation Investment Fund (Ausif), with support from the Bill & Melinda Gates Foundation, is funding a new initiative to promote innovation and citywide inclusive sanitation services for sub-Saharan Africa’s urban inhabitants.
The fund will be established under the African Water Facility Urban Sanitation programme (2018–2022), which builds on the partnership between the Gates Foundation, the African Water Facility and the African Development Bank (AfDB) started in 2011.
The AfDB and African Water Facility are committed to raising at least US$500 million (R6.8 billion) in new, citywide inclusive sanitation investments for the Ausif from public and private sources. At least 30% of those resources will finance non-sewered sanitation innovation that directly serves low-income communities.
The Gates Foundation is
committing $14.5 million (R197.2 million) in grant funding for the design and structuring of the fund and to support the development of an initial project pipeline.
“The potential impact of this new initiative, created to address urban sanitation in a comprehensive way, ensuring that the poor are also sustainably catered for, is long overdue,” said Wambui Gichuri, director: Water Development and Sanitation, AfDB.
“Support from the Bill & Melinda Gates Foundation enhances the fund’s ability to address sanitation in urban areas for greater outcomes, including in health, nutrition, environment and employment.”
The benefits of this comprehensive approach include: that everybody benefits from equitable sanitation service delivery outcomes; that human waste is safely managed along the sanitation service chain, from toilet to treatment; that waste is managed for resource recovery and reuse; and that authorities demonstrate political will, accountability and technical as well as
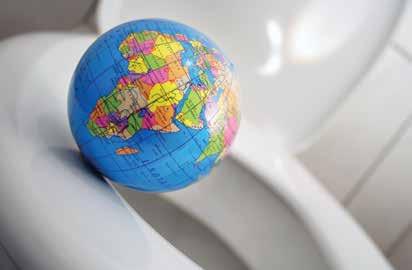
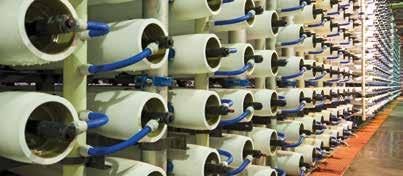
Egypt is expected to build four desalination plants, collectively supplying 56 000 m3/day of water
managerial leadership to drive innovation and to manage finances for sustained and equitable service delivery.

EgypT
Going big on desalination Egypt is expected to build four desalination plants in the South Sinai Governorate at a cost of roughly US$108 million (R1.47 billion).
The desalination plants, expected to reach completion in Q4 2022, will add 56 000 m3/day of water.
The four plants will be: a 30 000 m3/day plant at Sharm el-Sheikh, 15 000 m3/day in Abu Redis, 6 000 m3/day at Nabq, and 5 000 m3/day at Taba. The project also includes seawater intake and outfall infrastructures of highdensity polyethylene, and 38 km of pipeline to distribute the water.

ghAnA
Making sanitation finance accessible
Approximately four million Ghanaian households do not have a toilet for exclusive use by their family.
While access to basic sanitation in Ghana has increased from 21% to 25% in urban areas, statistics have proven that it is the poorest that are more likely to practise open defecation.
The recently launched Sanitation
Fund – a new loan initiative launched by Ghana’s Environmental Sanitation and Health Directorate under the Ministry of Sanitation and Water Resources, Unicef and the Embassy of the Kingdom of the Netherlands – offers a solution by providing many households in urban communities with the opportunity to build their own toilet.
The loans for household toilets – which are being offered with an operational fee of 12% and with less demanding lending criteria than other loans products –have the potential to change the landscape of urban sanitation for thousands of families.
Through a mass application process involving
The new Sanitation Fund will help Ghanaian households to build their own toilets
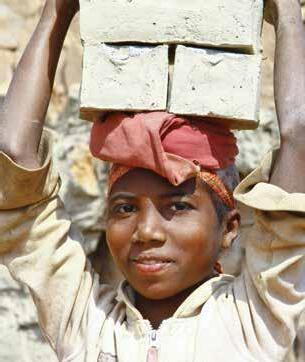
The new Africa Urban Sanitation Investment Fund will finance inclusive sanitation services for sub-Saharan Africa
environmental health officers and rural banks, a total of 457 loans have been approved for households and 15 for businesses. These loans will be released to beneficiaries in three metropolitan, municipal and district assemblies.
The Sanitation Fund is currently being rolled out in three major districts across Ghana: Ashaiman, Ho and Tamale.
“Access to finance is necessary in the sanitation subsector, to give access to sanitation service delivery and stir up entrepreneurship in the sanitation business. It is the sustainable way of reaching our SDG 6 target,” said Ron Strikker, the Netherlands’ ambassador to Ghana. Currently, suppliers can construct five facilities per week. Ghana would, therefore, need approximately 1 400 smallscale businesses working at maximum capacity between now and 2030 to reach the SDG target of universal basic sanitation. This additional financial support will make this task much more realistic.

MAlAwI
Sustainable water and sanitation services
A new water supply and sanitation project in Malawi is expected to provide jobs and boost the livelihoods of nearly 300 000 people.
The Nkhata Bay Town Water Supply Project will improve access to potable and sustainable water supply and sanitation services, directly benefiting 60 000 residents of Nkhata Bay and its surrounding areas, as well as 220 000 others who depend on services offered by the town. The project is also expected to create more than 300 jobs during
its construction phase and 50 additional jobs during its operation.
Nkhata Bay, a fast-growing port town on Lake Malawi, is a main link on the Mtwara Development Corridor, connecting Malawi, Tanzania and Zambia. It is also gaining popularity as a tourist destination and will benefit greatly from the project, which will kick off in January 2019 and is expected to be completed by the end of 2022.
Almost half the estimated project cost of US$30.4 million (R413.4 million), will come from an African Development Bank (AfDB) grant. A further $12 million (R163.2 million) loan from the OPEC Fund for International Development, to be administered by the AfDB, and $3.4 million (R46.2 million) from the government of Malawi will make up the remaining funding.
The new infrastructure to be built as part of the project, including water treatment plants, pipelines and reservoirs, is expected to increase Nkhata Bay residents’ access to potable water from 37% to 90% and access to sanitation facilities from 45% to 85%.
The project has enhanced social accountability and partnership between the town and the government due to the inclusion of Nkhata Bay
FAST FACTS
€6.2 million Four million $500 million
France has provided €6.2 million for water projects in Mozambique
The AfDB will invest $500 million in new citywide inclusive sanitation projects across sub-Saharan Africa
and surrounding residents in consultations during the design of the project – an exercise that will continue throughout the project’s implementation.

MozAMBIquE
Enhancing water availability
With the help of the French government, Mozambique will undertake a project to harness groundwater resources to enhance the availability of clean water in the Greater Maputo area.
The €6.2 million (R95.5 million) in French funding will allow for the establishment of 16 boreholes, a pumping station and pipes to carry water to the reservoirs. The aim is to make more than 40 000 m3 of water available to around 348 100 people in the southern Mozambican municipalities of Maputo, Matola and Boane by 2020.The project will

Four million Ghanaian households do not have their own toilet
also include a programme to reduce water losses by the Maputo Regional Water Company.

rwAndA
Providing water to 1.5 million Rwanda has received €115 million (R1.77 billion) in financing support to scale up the country’s largest water and sanitation sector investment programme.
The Sustainable Water Supply and Sanitation Program will provide access to improved, reliable and sustainable water supply services for 1.5 million people.
The government of Rwanda has shown consistent commitment to sector reforms and economic transformation, in furtherance of its recently approved National Strategy for Transformation − designed to propel Rwanda into an upper-middle-income country by 2035. The programme is bolstered by the country’s new Vision 2050, which aims to ensure a high standard of living for all Rwandans.
The funding will cover strategic cities and address water and sanitation challenges in areas with a low access rate of 45% − far below the national average of 85%.
Malawi, Mozambique and Rwanda are implementing programmes to provide secure water supply to residents
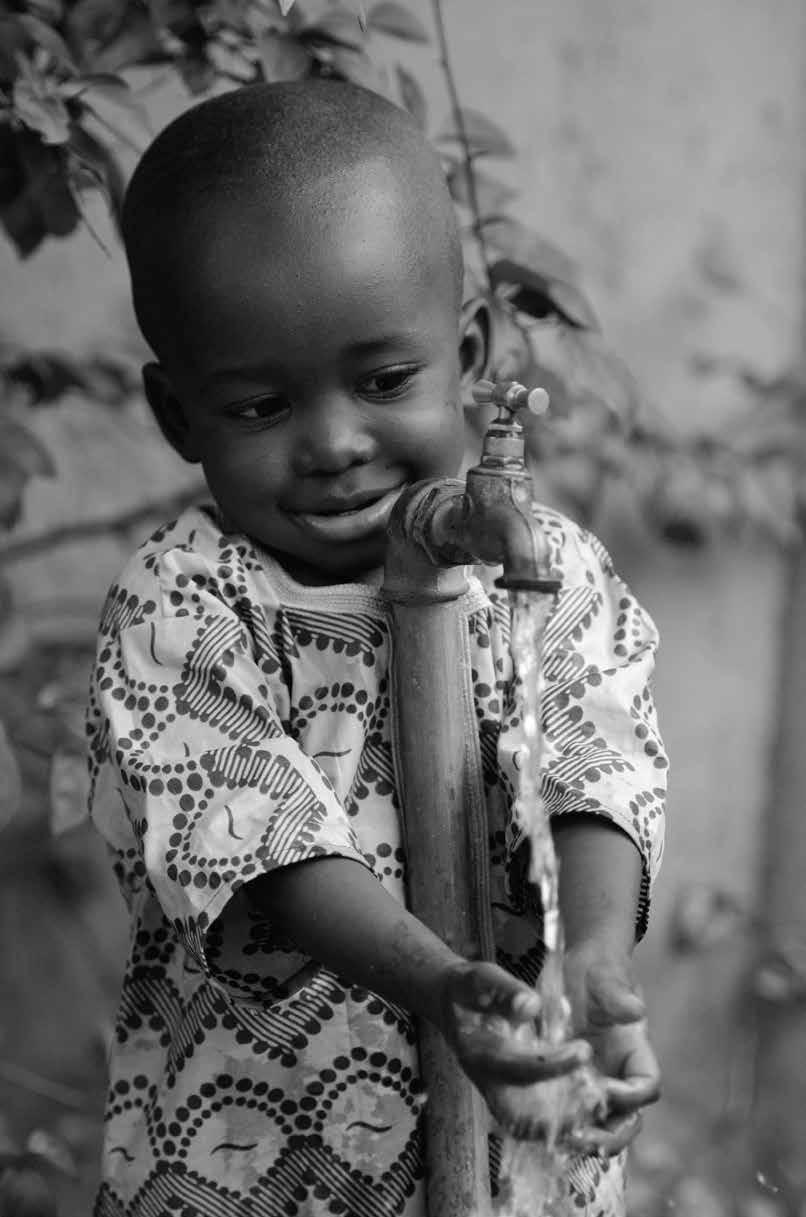
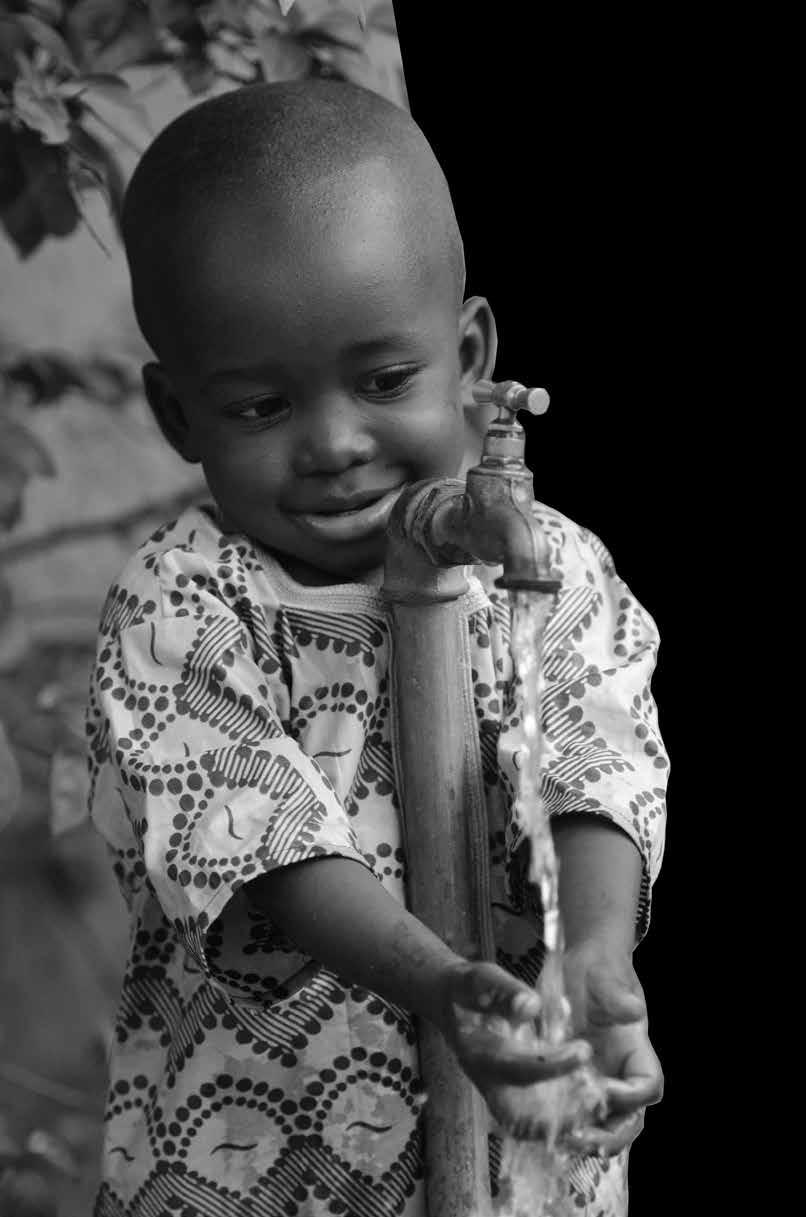
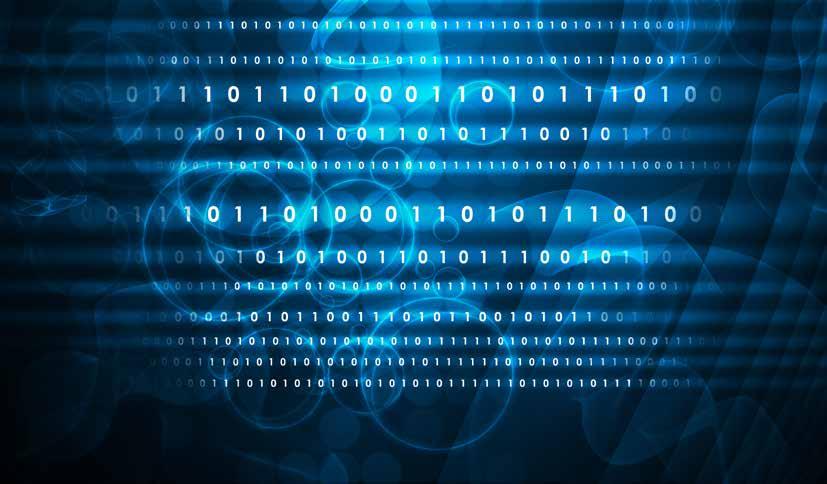
Keeping pace
The Fourth Industrial Revolution, or Industry 4.0, started in 2012 and we are now moving into uncharted territory. The future is arriving faster than ever before, and we must adapt.
By Danielle Petterson
The Fourth Industrial Revolution is changing life for individuals and businesses alike, but it can no longer be considered a future challenge. According to Professor Chris Adendorff, adjunct professor at Nelson Mandela Metropolitan University Business School, the changes we will experience within the next 10 to 15 years will be felt more than ever before. We must, therefore, be adaptive to change, and take the arrival of Industry 4.0 with a positive attitude.
“All of our efforts are and should be towards improvement,” he says.
Industry 4.0 is based on the use of cyber physical systems and comprises three elements:
1. Artificial intelligence (AI)
2. Internet of things (IoT)
3. Blockchain.
Of all of these, AI is possibly most concerning because, as Adendorff pointed out, it has the potential to move beyond the control of its creators. Sophia, the AI robot developed by Hong Kong-based company Hanson Robotics, is only three years old and can already imitate human gestures and
facial expressions and is able to answer certain questions and make simple conversation on predefined topics. In October 2017, Sophia became the first robot to receive citizenship in any country and is also the first non-human to be given any United Nations title.
“Key to effectively moving to Industry 4.0 is to move from a traditional waterfall approach to an agile approach.”
That being said, Adendorff is confident that the Fourth Industrial Revolution will make our lives easier, although the degree of complexity we will experience is much more intense. And a lot has already been done. R8.7 billion had been spent on IoT in 2012, when the Fourth Industrial Revolution began. By 2020, this is expected to increase to R50.1 billion. And it is expected that by 2025, one in three jobs will be done by software, robots or smart machines.
impact on jobs
While offshoring manufacturing jobs to low-cost economies can save up
to 65% of labour costs, replacing human workers with robots saves up to 90%, said Adendorff. Japan’s car manufacturing sector already has robots that are able to work around the clock for 30 days, unsupervised and without interruption. By 2030, over 2 billion jobs will have disappeared, freeing up talent for many fledgling industries and resulting in a surge of micro-training colleges to assist people in switching professions. It is expected that 60% of the jobs that will exist 10 years from now have not been invented yet, and basic computer programming will become a core skill required by over 40% of all jobs.
It is important to be prepared for and to manage these changes moving forward, and this will require vision, skills, resources and action plans from both the public and private sectors. “We need to start today, as
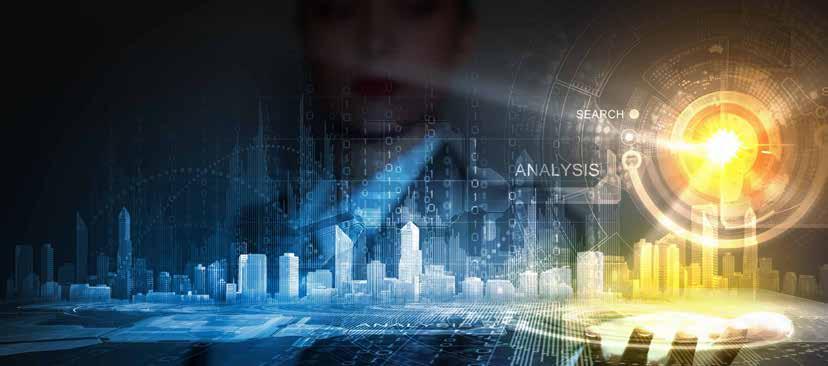
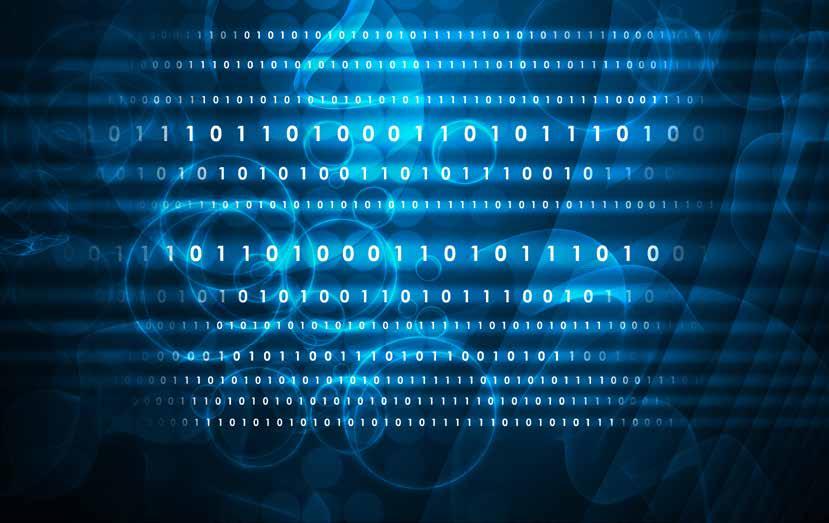
both individuals and organisations, to develop the ability to adapt as a core skill that will allow us to thrive in a context of constant transformation,” says Adendorff.
advice for Sa companies
While many South African enterprises are moving to embrace Industry 4.0 models and technologies, adapting to these new models is not without challenges.
Jesper Toubol, vice president: Elements and Moulds, Lego, who will be presenting the keynote address on Industry 4.0 at the upcoming Connected Industries Conference, notes that traditional business culture and a lack of effective change management can challenge efforts to move to an Industry 4.0 environment.
“Key to effectively moving to Industry 4.0 is to move from a traditional waterfall approach to an agile approach. It is not necessary to do massive roll-outs: development and change can be implemented faster in small stages,” he says.
“More connectivity and more connection equal more innovation, more invention and more opportunities.”
“It is also important to demystify what Industry 4.0 means, particularly among workforces, and to emphasise the business case and workforce benefits of moving to an Industry 4.0 environment.” Effective change management is therefore crucial.
Toubol goes on to note that the rapid advent of Industry 4.0 collides with the arrival of a wave of millennials and
26 Nagington Road, Wadeville, Germiston 1400, South Africa
Tel +27 11 824 4810 / Fax +27 11 824 2770
E-mail info@apepumps.co.za / info@matherandplatt.com Website www.apepumps.co.za / www.matherandplatt.com
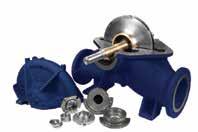
Split Case Pump
• Sugar and Paper Mills
• Refineries
• Petro Chemical


‘digital natives’ into the workplace. Although possibly daunting for older pre-internet management, this is resulting in myriad cultural and operational changes in industrial environments, and enterprises need to accept new ways of working.
Adendorff has a positive outlook in this regard: “More connectivity and more connection equal more innovation, more invention and more opportunities.
“The Industrial Revolution was a 10-million-person story. AI is a sample of a 1-billion-person story, and we are actually just at the beginning.”

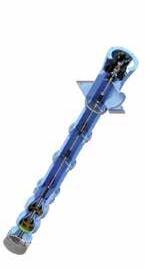




Crucial to any water treatment plant in the 21st century and the Fourth Industrial Revolution is the extended use of automation systems, with SCADA being a crucial aspect.
Although many municipal sectors see automation as an unnecessary complication to water treatment plants, water treatment specialist QFS argues that knowledge and support are key. Leading the way in automation and process control for the municipal and utilities sector, QFS has 22 years’ experience with supervisory control and data acquisition ( S CADA ) systems.
QFS offers service-level agreements and training with all its plants handling water and wastewater treatment as well
S C ada : the key to automation
as odour control.
Additionally, the company has good relations with its South African automation suppliers that help to source replacement parts quickly and effectively.
Successful projects
One of the many sites where QFS has successfully utilised S CADA is the V&A Waterfront desalination plant in Cape Town. Here, S CADA provides information reporting structures that can inform the municipality of the potable water quality.
Furthermore, QFS still plays a key role at South Africa’s very first reuse plant in Beaufort West, Western Cape, constantly monitoring the installed facility using S CADA systems and assisting the end user with fault finding and water-quality management. Trained technicians still regularly visit the site to assist in training operating personnel on the maintenance and operation of the plant.
The continual monitoring of plant performance is also undertaken at a wastewater reuse facility in
Ballito, KwaZulu-Natal, where QFS assists the client with training and operational support. The installed S CADA system empowers the end user with data that contributes to their knowledge and understanding of reuse plants, and assists in training new plant operators.
In addition, the end user at the De Doorns water reuse facility in the Cape Winelands has been given an effective S CADA system that allows them to quickly assess plant issues and that can help them address these issues with accuracy and efficiency.
i mproved safety
A final important aspect of S CADA is safety. The automation and controls that QFS implements on its S CADA systems ensure that end users are protected from harm. The programmers take safety seriously and QFS’s systems are programmed to ensure that the operator has peace of mind and protection, so that they will always be working in a safe environment.
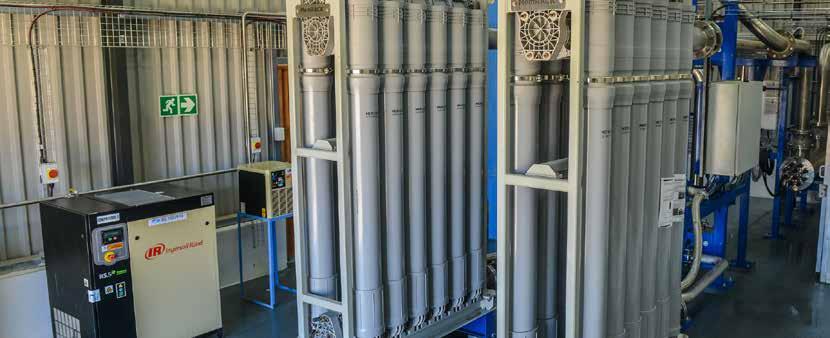
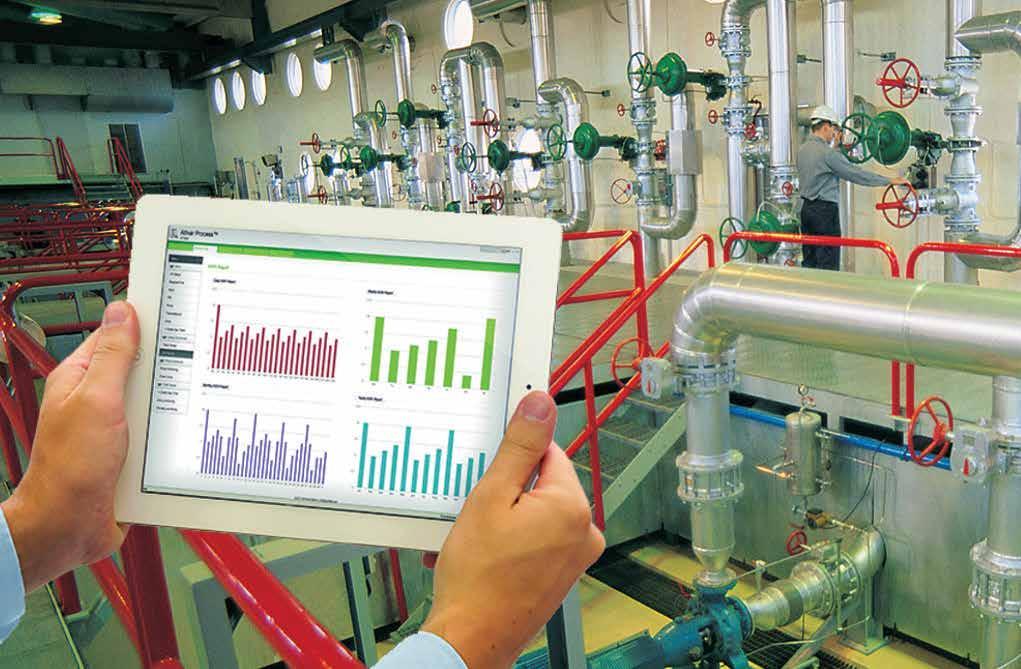
EcoStruxure™
Pumping Performance Advisor
Continuous improvement for pumping stations
EcoStruxure Pumping Performance Advisor is a digital service designed to manage your pump station performance through insights, recommendations and direct access to our service team of engineers.
• 15% savings on annual OpEx
• Results with sustainable improvements within first 3 months
• A simple, non-intrusive, agnostic and cybersecure solution
• No added workload on your side
EcoStruxure Pumping Performance Advisor is a digital service designed to manage your pump station performance through insights, recommendations and direct access to our service team of engineers.
Save up to 15% in OPEX through pump optimisation
Reduce energy cost and increase performance
Reduce unplanned downtime
Extend life of mechanical and electrical assets
Water at centre stage for Schneider Electric
In a world of water scarcity, implementing intelligent systems to process data can lead to improved efficiency and better management of water usage.
Only 0.3% of our global water resources can be used as clean drinking water, and the energy used to provide it accounts for 30% to 50% of total operating costs.
Scientists of the Joint Research Centre, the European Commission’s Science and Knowledge service, have released a technical report analysing Southern African weather patterns and precipitation over the past 36 years.
The report found that there is a strong probability of a 50% to 70% monthly precipitation deficit every five years – essentially more moisture is lost through evaporation and transpiration than is gained through rainfall.
“In addition, they found an increasing number of moderate to extreme heatwaves in Southern Africa over the last decade. These two factors combined – the repeated
occurrence of high precipitation deficit and more frequent heatwaves – exacerbate water shortages and could lead to crises that are more frequent in the future”, says Jacques Squire, segment lead: Water & Wastewater, Schneider Electric Southern Africa.
Scarcity of water resources, growth in urban population, environmental regulations and process inefficiencies are all contributing to the crises. Only 0.3% of our global water resources can be used as clean drinking water and the energy to provide it accounts for 30% to 50% of total operating costs. It is estimated that the amount of energy wasted through traditional methods of water processing and delivery can be cut by up to 25%.
Key to the reduction in water losses is that a comprehensive, integrated strategy be implemented by utility owners to leverage savings, implement infrastructure
improvements, address non-revenue water and drive maximum benefits from an existing capital investment that may or may not be performing to its highest potential.
Squire recommends a few performance contracting improvements that can save millions in energy costs and untold kilolitres of precious water, namely:
• pump efficiency
• cogeneration
• dynamic pump station optimisation
• technology process improvements
• advanced metering infrastructure.
“The future of precious water resources may depend on how well municipalities can find ways to fund these important energy- and watersaving upgrades,” Squire concludes. Schneider Electric helps the water and wastewater segment treat and deliver safer water 24/7, while lowering operating costs and using less energy.
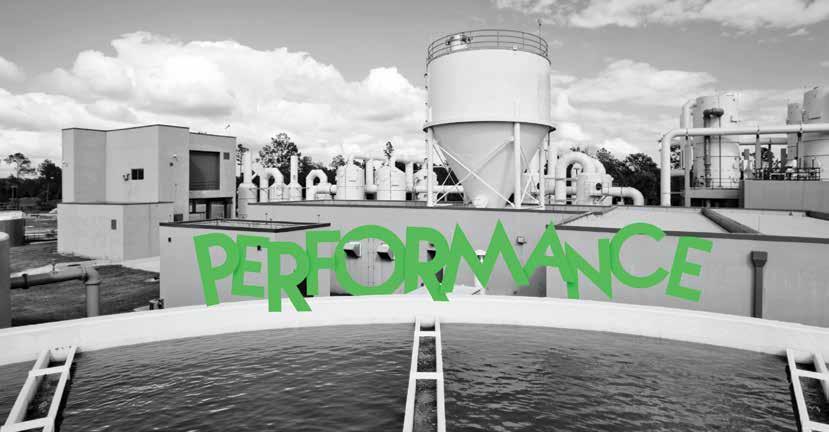
The next standard in the evolution of turbidity
Only the new TU5 Series Lab & Process Turbidimeters with 360° x 90° Detection™ deliver unprecedented confidence that a change in your reading is a change in your water.
Groundbreaking 360° x 90° Detection™ Technology
The TU5 Series employs a patented optical design that sees more of your sample than any other turbidimeter, delivering the best low level precision and sensitivity while minimizing variability from test to test.
Matching lab and online results
For the first time you will be able to remove the uncertainty of which measurement to trust, thanks to identical 360° x 90° Detection™ Technology in both instruments.
Everything about turbidity – faster
The TU5 Series dramatically reduces the time needed to get a turbidity measurement you can rely on, with 98% less online sample surface area to clean, sealed vials for calibration, and the elimination of the need for indexing and silicone oil in the lab. Not to mention, a smaller online sample volume means you will detect events almost immediately.
No surprises
Prognosys™ monitors your TU5 Series online instrument, proactively alerting you to maintenance needs before your measurement becomes questionable. And a Hach Service Agreement protects your investment and helps ensure that you stay in compliance and on budget.
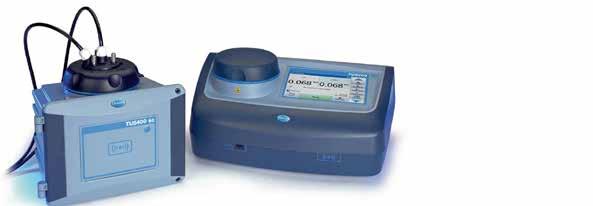
Principle of Operation
The TU5 Series turbidimeters measure turbidity by directing a laser into a sample to scatter off suspended particles. The light that is scattered at a 90° angle from the incident beam is reflected through a conical mirror in a 360° ring around the sample before it is captured by a detector.
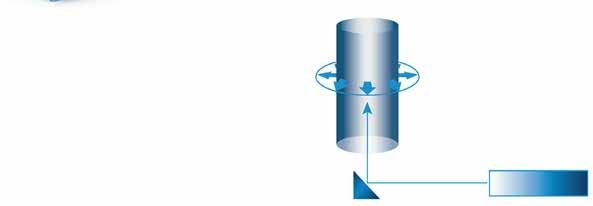

The amount of light scattered is proportional to the turbidity of the sample. If the turbidity of the sample is negligible, little light will be scattered and detected by the photocell and the turbidity reading will be low. High turbidity, on the other hand, will cause a high level of light scattering and result in a high reading.
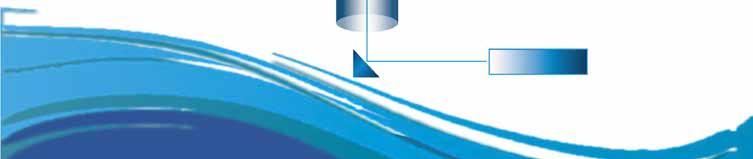
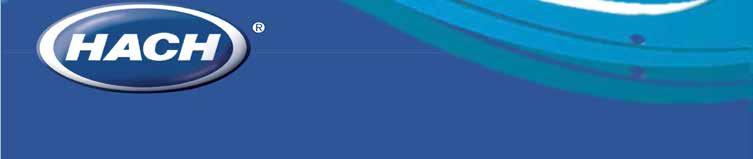

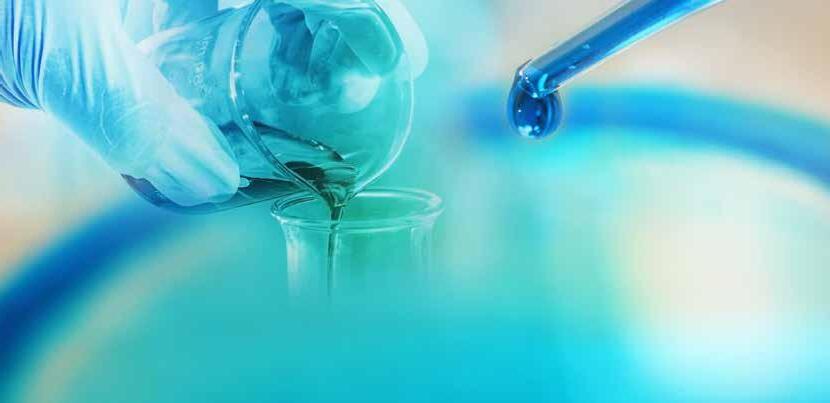
As an expert and pioneer in the turbidity measurement space, Hach has developed its TU5 series turbidimeters to provide a new standard in turbidity technology, enhancing accuracy and reliability.
The TU5 series uses groundbreaking detection technology to achieve a new standard in accuracy and reliability, while going a step further to ensure a better match between lab and online test results.
“Hach’s patented 360-degree by 90-degree detection technology uses a whole new methodology for measuring turbidity, conforming to the highest Environmental Protection Agency standards. These standards have been adopted by South Africa’s biggest water service providers, including the likes of Rand Water,” explains Steve Herbst, group director at Prei Instrumentation – the local distributor for Hach’s online instrumentation technologies.
importance of turbidity
Turbidity is important because it represents the ‘report card’ by which water quality can be measured.
The amount of insoluble matter present in drinking water is an essential quality indicator. Silt, sand, bacteria, spores and chemical precipitates all contribute to the cloudiness or turbidity of water. Highly turbid drinking water can be unpalatable and unsafe. The consumption of even low concentrations of certain bacteria and other microorganisms can cause serious health effects.
“The relevant local and international standards call for turbidimeters where raw water enters water treatment plants, in the settling tanks, the filters and, ideally, also the backwash filters. They can also be installed at the outfall of wastewater treatment plant but, because of the generally poor performance of the majority of the country’s wastewater treatment
plants, the technology is only used at flagship wastewater facilities,” explains Herbst.
“Moreover, the TU5 series solves persistent market challenges. For example, there is a problem getting the online results from field instrumentation to match with the lab equipment. The reason for this is lab conditions do not simulate the natural environment, lab technicians can get tired and make errors, or they might get up and go for lunch or a comfort break, allowing sediment in a lab sample to settle. Further, glass vials used in the lab can get scratched from frequent use – this throws off test results,” he adds.
What sets the TU5 series apart is that it makes calibration much easier and more accurate. Using a new, more accurate and affordable methodology, calibrations are performed automatically, negating the margin for error introduced through human intervention.
The technology goes a step further, by incorporating radiofrequency identification (RFID). “Samples that go to the lab have a magnetic band attached – when you touch samples to the unit, it downloads all the information on that RFID tag, doing away with handwritten labels and allowing the lab to handle large volumes of samples without mix-ups,” says Herbst.
Groundbreaking methodology
Both lab and online units utilise 360-degree by 90-degree detection technology – a new standard in turbidity testing.
“The first turbidimeters consisted of a candle under a jar. Divers would peer through cloudy water and judge how far away they had to be before they could no longer see the light from the candle. The next step in turbidity testing used nephelometric readings (light refracting at 90 degrees followed by measuring the amount of light bounced back by particles). Thereafter, infrared laser technology was
To ensure the utmost confidence in turbidity readings, Hach’s TU5 series offers sensitive and accurate readings comparable with laboratory results.
developed in Europe. This was highly accurate but incredibly expensive,” explains Herbst.
“What makes the TU5 series revolutionary is that it directs a laser into a sample to scatter light off suspended particles. The light scattered at a 90-degree angle from the incident beam is reflected through a conical mirror in a 360-degree ring around the sample before it is captured by a detector.”
The outcome is that the unit’s optical design sees more of your sample than any other turbidimeter, delivering the best low-level precision and sensitivity while minimising variability from test to test.
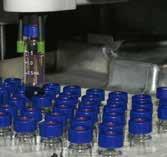
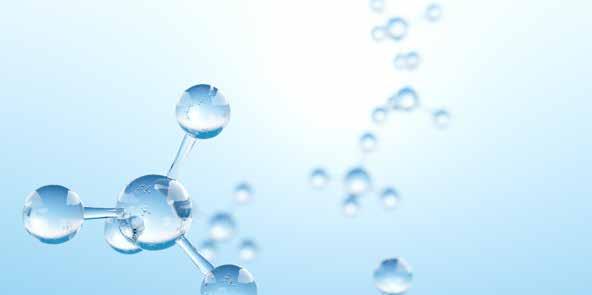
Large numbers of samples cause frequent mix-ups at the lab – by using a RFID tagging system, the TU5 series overcomes inaccuracies introduced by human error
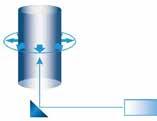
Graphic representation of Hach’s patented turbidimeter technology
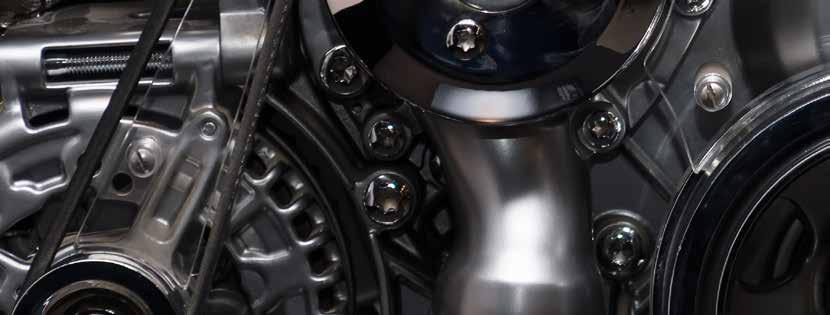
Water-tight solutions
Faulty and incorrectly installed seals are among the most common causes of premature submersible pump failures. AESSEAL has developed one of the most comprehensive component seal product portfolios available, designed specifically to overcome these challenges.
Ahigh-quality seal is essential to ensuring the longevity of pumps, saving on downtime and total cost of ownership. The AESSEAL Component Seal range has been developed over many years, and offers sealing solutions for a diverse range of industries and applications.
With some 10 000 product lines available, AESSEAL’s patented range of component seals enables 44 000 permutations to be configured. 100% compatible solutions with OEM parts and backwards compatibility ensures that products can be used with customers’ existing stock holding, and all sealing solutions can be provided direct from one source.
“Our patented, superior T05 solution is designed to help pumps operate optimally and increase mean time before failure. This is a unitised, all-steel double mechanical seal with lower overall operating costs.”
Benefits of the to5 series include:
• Easy installation
• No pump modifications
• No special fitting tools
• Made from stainless steel
• No plastic parts
• Most seals pre-set to working length with removable clips
• Monolithic seal faces on many seals
• Significant potential cost savings
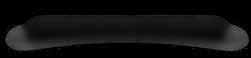
“We use the best-quality materials for our innovative designs, while still ensuring competitive pricing models for our customers,” explains Bevan Braybrooke, key accounts manager, AESSEAL.
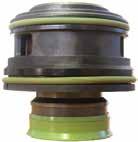
OEM seals often feature many plastic components (all parts in green and black are plastic). The disadvantage of the throw-away solution, however, is the accumulating cost associated with continual seal replacement.
“Our component seals are designed with modularity at their core, allowing for faster service while also incorporating design features that reduce the lifetime cost of the product.”
To5 Series
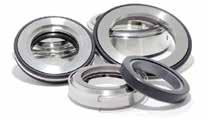
AESSEAL’s T05 Series of component seals offers a quality alternative for Flygt and Grindex submersible pumps and mixers.
Benefits of the to5Vc series:
• Full cartridge seal
• Fully integrated sleeve
• Fully integrated pumping device
• All stainless steel parts (no plastic)
• Hydraulic balanced seal
• Multi-spring out of the product
• Metal drive pins
• Tungsten faces product side
• Carbon/Cer faces oil side
• Nitrile O-ring
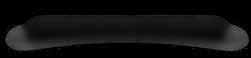
The T05 series is the result of a global strategy to expand the company’s product range, allowing further penetration into new markets and offering to customers a more complete service, says Braybrooke.
The seals are primarily made from stainless steel and feature no plastic parts. Many also benefit from the use of monolithic seal faces. “This range requires no pump modifications and no special fitting tools. The majority of the designs also have a pre-set working length with removable clips. In fact, AESSEAL offers one of the largest ranges of single-spring mechanical seals in the industry,” Braybrooke adds. These innovative designs, which significantly reduce the likelihood of incorrect installation by ensuring even face loading, are particularly important in places like South Africa, where installation is often conducted by bluecollar workers.
“Our products offers a lower total cost of ownership, backed up by excellent
The TO5 collection
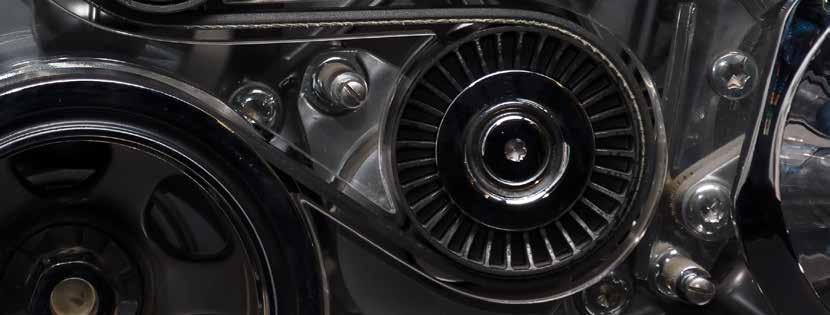
customer service, providing seals that last longer, work better, and save on downtime,” comments Braybrooke.
“Our TO5 seals have been installed on various Flygt submersible pumps in numerous applications, particularly sewage pumping stations, dramatically increasing the mean time between failure rates.”
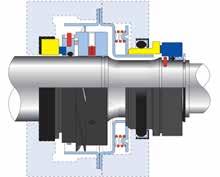
There is also a TO5VC range available, which offers plug-and-play solutions for quick and easy installation. The cartridge-type design features a fully integrated sleeve and pumping device and is made entirely from stainless steel.
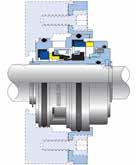
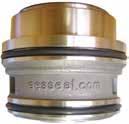
other capaBilities
Aside from providing high-quality seals, AESSEAL also offers bearing protection, gland wrapping, and seal support systems.
AESSEAL places a big emphasis on sustainability, with a focus on water savings, energy savings and waste reduction. The company has achieved significant water savings for many of its clients across the globe. one example is a paper mill in richards Bay, in which AESSEAL’s water management systems have cut water use by as much as 80 000 kℓ per month.
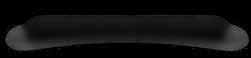
Reliable service
To ensure quick and reliable service, AESSEAL has embraced technology and inventoried its seals in state-of-the-art, computer-controlled carousel systems, automating customer order processing. The company’s online product selector tool also allows users to specify a mechanical seal via a simple multiplechoice method.
“Our seals are standardised to fit pre-existing pumps. All we need is the pump model number or OEM seal code and we can match it to our seals. We keep a large amount of stock in our warehouses globally and if we don’t have a product on hand, we can source it in as little as one to two weeks,” says Braybrooke.
All of the seals used in South Africa are manufactured in the United Kingdom, using parts sourced globally from the group’s extensive network.
Global backing
One of the biggest advantages behind AESSEAL’s offering is the support of a global network. Customer service is provided from 230 locations in 104 countries, including nine manufacturing and 58 repair locations. With an employee compliment of more than 1 700 worldwide, more than 300 AESSEAL customer service representatives visit industrial plants every day.
Over 7% of the group’s annual sales revenue has been reinvested in R&D over several decades, leading to an advanced range of sealing technology that allows customers to improve the reliability of their existing equipment without any modifications.
Every seal is developed using advanced computational facilities and numerical tools to design and optimise seal performance. All products are designed in 3D CAD, which is fully integrated with CAM. CAM controls and drives all machine tools centrally, while integration with PLM ensures control of changes so that products can be delivered quickly, affordably and repeatedly.
The use of quality stainless steel and no plastic parts reflects in the weight difference between the OEM and TO5VC seals. Although the initial purchase price of the T05VC seal is higher than the throw-away plastic seal, its lifetime cost is lower because of the accumulating cost of continually removing, discarding and replacing plastic seals over time. As soon as the break-even cost is reached, the lower variable cost of repairing the AESSEAL cartridge seal delivers an operational saving.
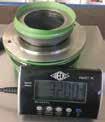
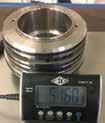
The TO5VC


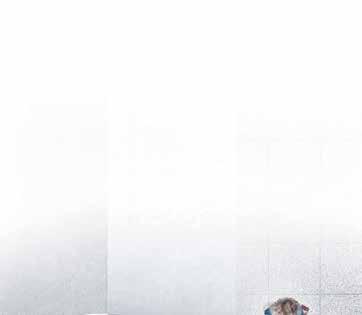


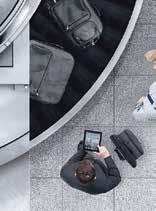
Gear units and motors from SEW-EURODRIVE Pty (Ltd) have always set the trend and established new standards in drive technology. For this reason, the quality label “made by SEW” has become a hallmark of quality in the drive industry Market-orientated products developed and manufactu red in-house, as well as uncompromising quality, are the cornerstones of our success
We drive industry SEW-EURODRIVE - Driving the world Quality Innovation Efficiency
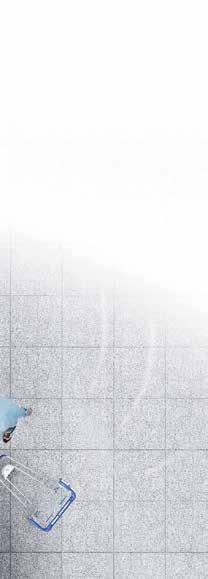
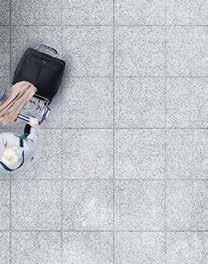
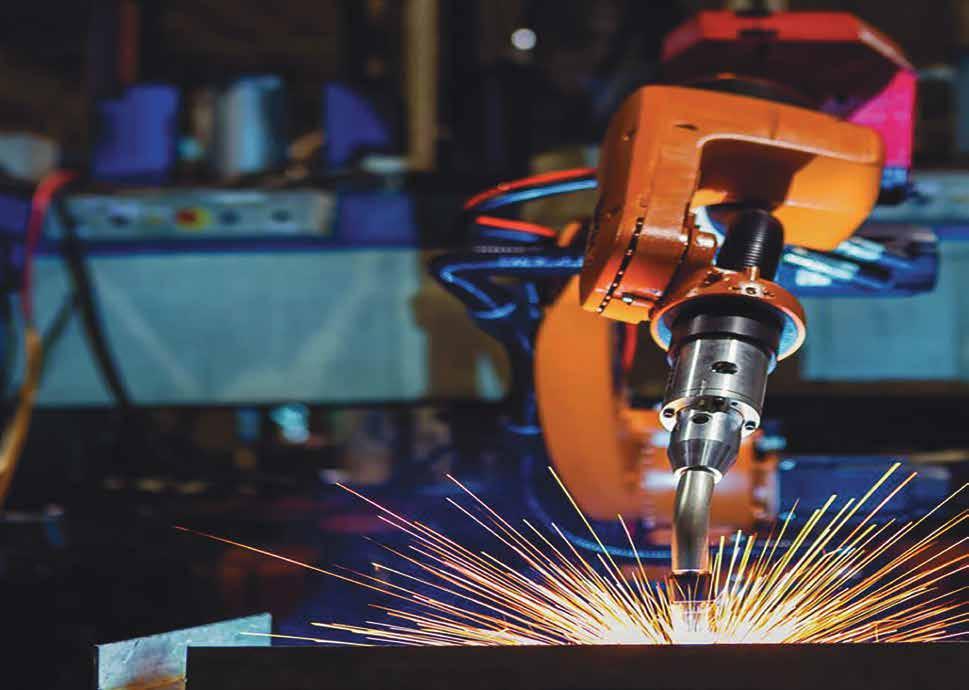

4TH-6TH JUNE 2019
Proven solutions for wastewater plants
Local OEM Wamechsi Group has standardised on SEW products for a range of wastewater treatment plants it has built throughout the country.
SEW-Eurodrive South Africa’s industrial gear units and geared motors are ideal for applications where a high level of performance is required for mixing and agitating liquid or pastetype substances. This includes wastewater treatment as well as chemicals, food and beverage, and mining.
The Wamechsi Group has selected these products for a number of wastewater projects across South Africa. The OEM manufactures a range of mechanical equipment for the various stages of the treatment process at a wastewater treatment plant, ranging from mechanical screens to washers and screw presses that wash and compact the material to be removed. Ancillary mechanical equipment includes screw pumps, surface aerators and clarifiers.
The group acquired its first SEW products in 2012, leading to a long-standing partnership predicated on good design, reliability, quality, and excellent aftermarket support and service, comments Jurie Niemand, CEO, Wamechsi Group.
The OEM’s latest projects to feature SEW products are Virginia Phase 2, which
incorporates six 75 kW industrial gear units specifically for aerators, an additional 22 geared motors for Theronia, and 15 geared motors for mixers at Buschkoppies.
Phase 1 of the Virginia project has already been completed, while Phase 2 is being commissioned. “The main reason that we have been so successful in this industry to date is largely due to our innovation and SEW’s reliable product range,” Niemand says.
Proven track record
According to Willem Strydom, sales manager, SEW, the company’s extensive experience and track record in the wastewater treatment industry means it is able to offer flexible and highly reliable total solutions. As a leading manufacturer of industrial gear units and geared motors, in addition to a large range of optional equipment, SEW ensures reliable drive solutions for the wastewater treatment industry.
With its flexible product platform, SEW offers a load-specific bearing concept. In addition to the transmitted torque, high radial or axial forces are often supported by the output shaft. No matter whether the process is horizontal or vertical, SEW has the expertise to be able to provide the optimal solution.
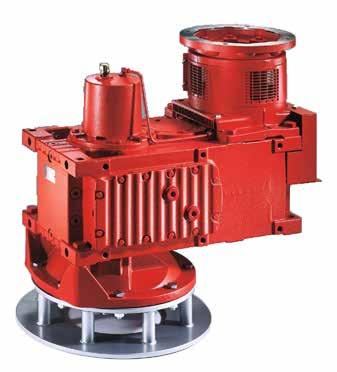
“With aerator and mixing applications, our project and engineering teams have to double-check all of the loads and bending moments. These loads are supplied to us by the client, based on their designs. We then ensure that the gearboxes selected are suited to the application at hand,” Strydom highlights.
This goes hand in hand with commissioning and maintenance support, as required.
SEW employs a special program designed specifically to determine if the
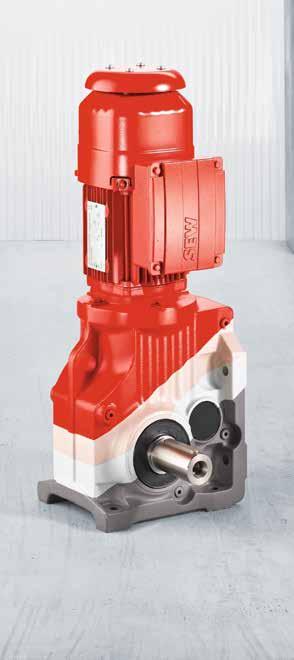
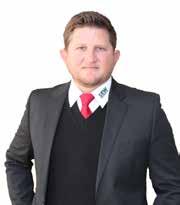
gearbox selection is adequate, based on the loads and bending moments. This is particularly important when it comes to aerators and mixers.
Meeting Sa’s needs
SEW is also doing its part to conserve water in South Africa. “We are now busy with projects where final effluent is being treated to potable water. Therefore, it is critical that our major component suppliers like SEW be at the cutting edge of technology,” Niemand points out.
“The wastewater treatment industry not only generates much-needed employment, but is essential for continued economic development, as the country’s residential needs cannot be met without this essential enabling infrastructure being put in place first.”
Willem Strydom, Sales Manager, SEW
A complete lowpressure portfolio
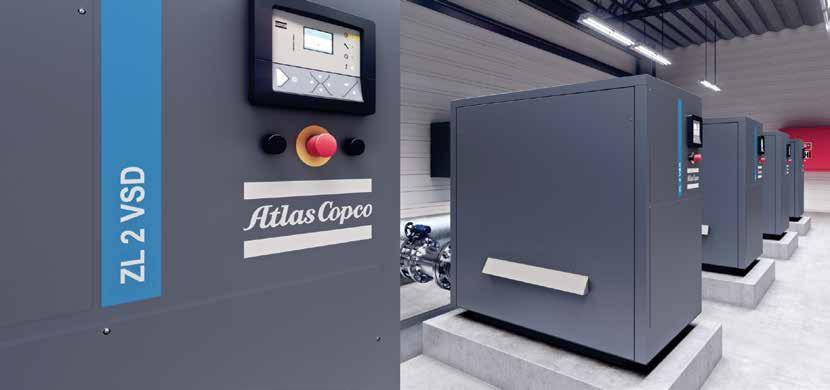
The re-introduction of the ZL lobe blower positions Atlas Copco as a total solutions supplier of highly cost-effective and reliable low-pressure compressed air.
The positive displacement principle of the ZL tri-lobe blower has proven itself as a reliable and stable technology for round-the-clock operation in the harshest environments and within a multitude of low-pressure applications, such as chemical processes and wastewater treatment.
“Due to an enhanced package, the ZL VSD is now available in a variety
of configurable models,” confirms JC Lombard, business line manager: Oil-free Air, Atlas Copco. “Customers now have the choice between a purely mechanical unit using dial gauges for pressure reading or a high-end solution with an integrated VSD inverter and Elektronikon® controller.”
With the introduction of the ZL VSD lobe blower, Atlas Copco is now able to offer customers not only what they
want but also what they have been using for years – a reliable machine at a cost-competitive price. Owing to the enlarged dual offer, Atlas Copco can further differentiate the lobe blower range and assist in fulfilling the specific needs of all its valued customers.
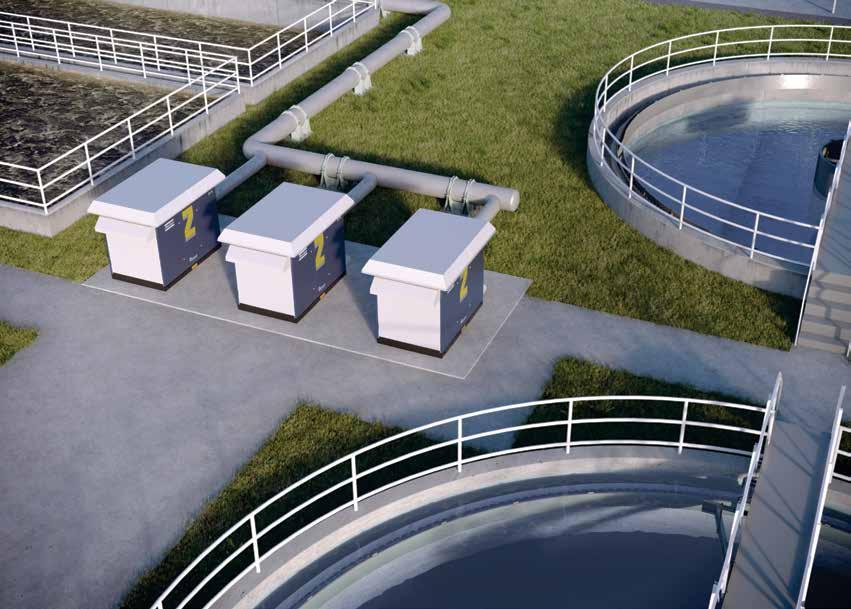
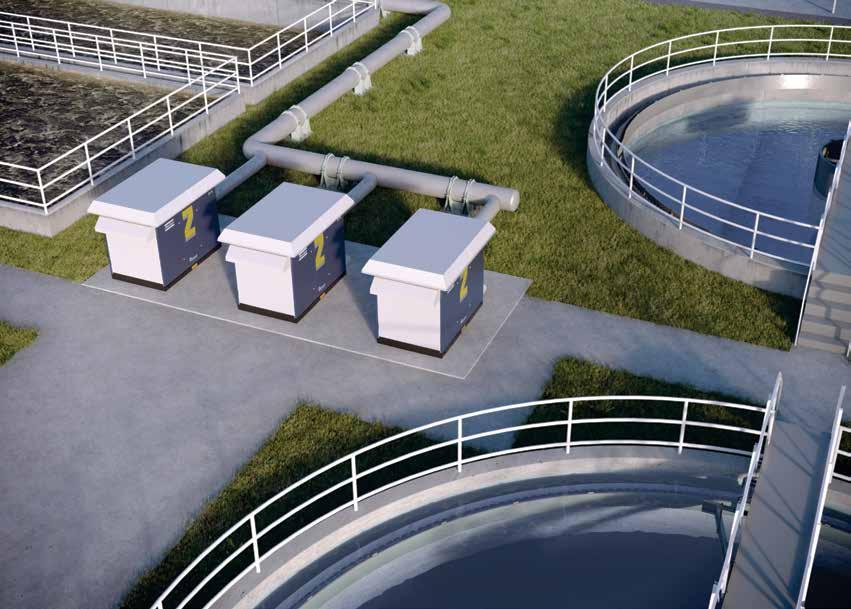
Innovative solutions to a growing crisis
The Department of Water and Sanitation reports that around 56% of the country’s wastewater treatment works (WWTWs) are in poor or critical condition. Unfortunately, these problems would cost trillions to fix using traditional methods.
The Vaal crisis is a prime example of the dire situation facing many of the country’s WWTWs. Maintenance is often not prioritised, and the harsh nature of WWTWs means they are frequently exposed to high levels of hydrogen sulfide (H2S), which causes significant corrosion damage and is also the leading cause of gas inhalation deaths in the industry. Water&Sanitation africa talks to Shaun Blackmore-Reed, director, UltraTech SA, about the company’s innovative solutions to some of the biggest challenges in the wastewater treatment space.
How do you combat the threat of H2S?
SB By eliminating H2S, you not only drastically reduce corrosion and odours – which translates into savings on maintenance, repairs and downtime – but you also create a safer work environment. While H2S simply results in an unpleasant rotten egg smell in lower quantities, in higher amounts it signals
your diaphragm to shut down, posing a serious safety concern.
Our Ultra-S3® product is an effective oxidising system suitable for WWTWs and a number of other related applications like abattoirs. Up to 3.5 times faster and 241% more effective than hydrogen peroxide (H2O2) alone, Ultra-S3 eliminates H2S quickly and efficiently. However, the two can be combined to form our Rapid Sanitizing System (RSS), which is three times more powerful than chlorine, making it ideal for WWTWs.
The RSS gets injected into the water stream to produce a compound that separates H2S into water and elemental sulfur so quickly that they cannot recombine, effectively eliminating H2S within three minutes.
What makes RSS so ideal for South Africa is that it can be introduced without making any changes to existing infrastructure, and the entire process is monitored by sensors, eliminating opportunities for error. Furthermore, utilities can
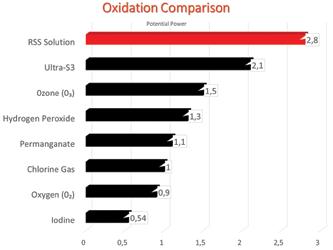

save up to 50% on their monthly chemical bill by eliminating chlorine and other associated chemicals.
What are the other applications for Ultra-S3?
Ultra-S3 is also a powerful sanitiser and has been shown to eliminate many common bacteria, including Pseudomonasaeruginosaand Corynebacteriumaquaticum , both of which present serious health threats. Ultra-S3 and RSS have also been shown to remove emerging pollutants like pharmaceuticals, which our current WWTWs are simply not designed to treat.
For a more holistic sanitising solution, S3 can be combined with our UltraArchaea® product.
Tell us more about Ultra-archaea.
Ultra-Archaea was first developed to eliminate the toxic conditions associated with oil spills, and proved its effectiveness in cleaning up the Deepwater Horizon spill in the Gulf of Mexico in 2008. However, the product also offers an excellent solution for wastewater treatment due to its affinity for organic waste matter.
Ultra-Archaea is a range of natural microorganisms that speed up the rate of natural degradation and help the bioremediation process occur in days and weeks rather than months or years. The microorganisms have a lifespan of around 12 weeks and will remain active as long as there is a food source, digesting
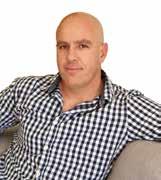
hydrocarbon molecules and breaking them down into harmless by-products of water, carbon dioxide and lipids.
Ultra-Archaea is a completely natural solution and has been shown to be highly effective. In a controlled study with samples from the Deepwater Horizon spill, Ultra-Archaea was found to perform better than three other leading products. Most notably, it removed 98.5% of PAHs (polycyclic aromatic hydrocarbons).
are these products safe for the environment?
Absolutely. Ultra-S3 has passed all three of the CSIR’s toxicity tests with a Class I result and has been classified as non-hazardous under the USA’s Toxic Substance Control Act of 1976. It is chemically engineered to target problem compounds without destroying environmentally beneficial microbes, and actually supports good biology by oxygenating water. There is also no threat to overdosing. In fact, the opportunity exists to purposefully overdose with S3 and Ultra-Archaea to help remediate catchment areas where sewage spills have occurred.
Ultra-Archaea is also completely safe because the microbes are 100% natural and not genetically engineered or modified. They are non-toxic and non-pathogenic.
Together, the products offer simple, fast and cost-effective solutions that have been successfully used in the US for decades.
Shaun Blackmore-Reed Director UltraTech SA
Beating the load-shedding crisis
Many of South Africa’s wastewater treatment plants are operating over capacity with old, unreliable equipment. Now, the ongoing power outages by Eskom pose an additional threat that could result in mass discharge of partially treated effluent into our catchments.
Despite the threats presented by loadshedding, there are ways in which to quickly bring wastewater treatment under control at a reasonable cost.
Existing aerobic digesters typically have a residence time of roughly 24 hours. Hyson Cells recommends that digesters be set to run for 6 to 12 hours at night, when the power grid is stable, as the power used by conventional treatment plants often breaks the bank of municipalities.
The partially treated effluent should then be outputted from the aerobic digester to the clarifier, where the clarifier sludge and supernatant
100% waterproof
The Hyson digester consists of a series of deep, conical reservoirs lined with 100% waterproof Hyson 3D BubbleLock and interconnected with pipes and solenoid control valves
liquid can be routed to a low-cost Hyson anaerobic thermophilic methane digester and then on to drying beds to complete the process (or to a potable water system).
Saving costs with the Hyson digester
The Hyson digester consists of a series of deep, conical reservoirs lined with 100% waterproof Hyson 3D BubbleLock and interconnected with pipes and solenoid control valves.
The reservoirs can be constructed at a small percentage of the cost of above-ground reinforced concrete works by labour-based SMMEs and offer an offgrid solution to wastewater treatment. Because the cones are underground, they are well insulated, allowing for the use of efficient but temperamental thermophilic bacteria. A percentage of the biogas produced via the digestion process is burned to generate heat so that the cones can operate with thermophilic bacteria at 55°C, while then remaining portion is used to assist mixing.
The use of thermophilic bacteria allows for a shorter resident time compared to mesophilic bacteria,
which function at lower temperatures. This process circumvents the need for electricity purchase and even offers the opportunity for additional energy production, which can then be sold by the municipality.
improved processing
In order to improve the total throughput capacity, Hyson Cells has developed a method that allows for the base undigested organic material to be moved back one cone in the set for reprocessing. This means the hard-todigest organic materials that require a longer digestion time do not hold up the process.
When each cone routes back the solids, the digested portion moves on to the next cone, where the methane and carbon dioxide are continuously taken from the roof and mixed with the liquid in the cones. This keeps the finer digesting solids in suspension and allows a percentage of gas to burn off in order to keep the cones at 55°C.
The balance of the gases is taken to the next cone, where a small percentage is used to run a small generation set to drive the pumps, making them
45%
Older wastewater treatment plants are highly energy intensive and the evaporation rate can be as high as 45% of the inflow water
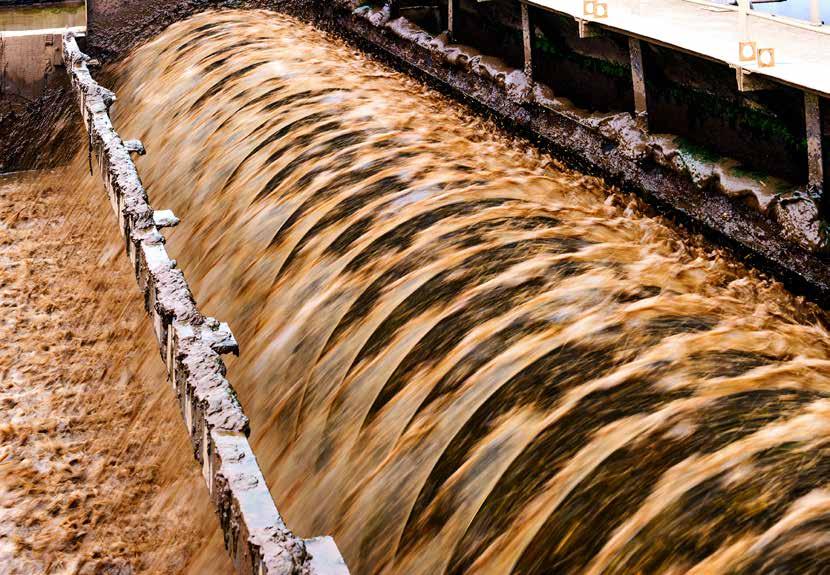
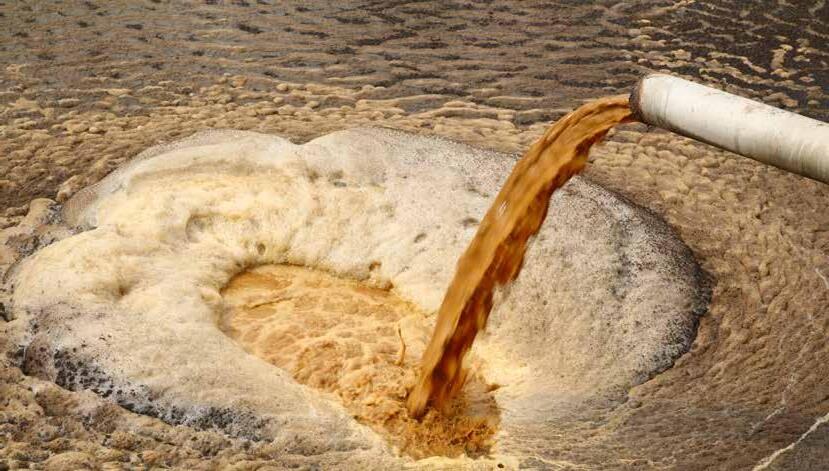
95%
self-sustainable. These pumps consist of ‘munching’ recirculating submersible pumps to route partially digested effluent back for reprocessing and sandpiper pumps to process the generated biogases.
In the last cone, the remaining gas is removed to a large generator where energy can be produced to feed back into the grid, or to keep the old treatment plant running until all the new flow from the screens and the munchers are taken up by the cones and the old works can be retired.
Older wastewater treatment plants are highly energy intensive and the
evaporation rate can be as high as 45% of the inflow water. Hyson Cells works to have 95% of water treated to become potable water. This is done by the last thermophilic cone, which only contains clear water with no solids. This cone is fitted with grow lights to feed algae, which multiply at eight-hour intervals. The algae is then dropped out with a flocculant and fed back to the first cone to make more methane. The water then goes to additional cones with activated carbon, to remove the odour and colour, before in-line ozone sterilisation takes place. The final step sees the water pumped to the potable water treatment plant, where it is chlorinated.
constructing your digester
The Hyson cones can be constructed in the drying beds of an existing plant.
Cones are 40 m to 50 m in diameter and 10 m deep, and can be excavated easily with a machine, or by hand after
the ground is loosened with shaped charges of subsonic explosives.
The waterproof lining is made up of three layers, namely a 4 mm bitumen layer sandwiched between two 75 mm Hyson 3D BubbleLock armouring layers filled with 20 MPa grout. This lining is soil-nailed every square metre using the rigging to the steep walls of the cones. Finally, one coat of food-grade bitumen is placed on the surface to protect the lining from attack by the water. If the system is taken to completion by including the algae, activated carbon, ozone and chlorination steps, the end result can be potable water. The system can then make money from the sale of water and electricity, as well as produce savings on the removal of sludge.
This innovative system provides municipalities with a simple way to deal with excess inflow resulting from urbanisation, meet compliance standards and, ultimately, make a profit.


Hyson Cells works to have 95% of water treated to become potable water
Decentralised treatment solutions

For more than 100 years, flushing toilets connected to a centralised sewerage network have been considered the gold standard for sanitation. However, for water-stressed countries like South Africa facing the pressures of a changing climate, connecting every household to a centralised sewerage network is neither feasible nor sustainable. By Carley Truyens*
However, for up to half the population, a safe, convenient toilet that is protective of human health and the environment remains out of reach. Approximately one quarter of South Africans lack access to safely managed sanitation, using unimproved sanitation facilities, shared facilities, or defecating in the open. And although more than two million South African households have access to basic on-site sanitation, these might include urine-diverting dry toilets (UDDTs) or ventilated improved pit latrines (VIPs). Although waterless on-site systems are relatively inexpensive to construct, they are less convenient and less accepted by users. In 2018 alone, two young children fell into pit toilets
and drowned. For this reason, many children are encouraged to defecate in the open, which is undignified and poses health risks to the entire community.
When toilets are located outside the home, women and girls are placed at greater risk for gender-based violence and may not feel safe leaving their homes at night to use the toilet. Further, when the pit is full, there may not be space to simply dig another one. However, although convenient for users, conventional sewers and wastewater treatment works are expensive and challenging to construct and maintain. Conventional sanitation relies on large volumes of potable water to transport excreta over long distances, often requiring significant energy input.
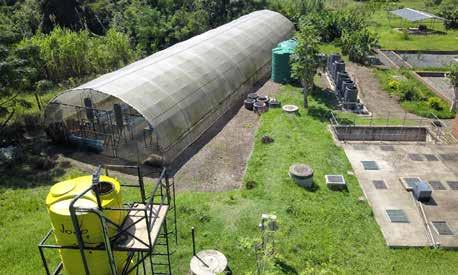
deWats principles:
1. Decentralisation – by decentralising treatment, dewats allows for greatly reduced lengths of trunk sewers and fewer pump stations, reducing cost and maintenance requirements.
2. Simplicity – wastewater is treated on-site without the use of chemicals or electrochemical equipment/energy input, and maintenance requirements are relatively low compared to conventional treatment.
3. Reuse – because dewats treats wastewater close to the source, the treated effluent can be used for non-potable uses by the community, with significantly reduced pumping requirements.

d ewats to fill the sanitation gap
A decentralised approach to wastewater treatment may offer a more cost-effective and easier-to-maintain solution than a conventional sewer network. A decentralised wastewater treatment solution (Dewats) can fill the gap between conventional and on-site sanitation.
Dewats is not a specific treatment technology, but rather a technical approach to wastewater treatment.
Key Benefits of deWats:
• No energy input required
• Relatively simple to operate and maintain
• Tolerant to inflow fluctuations
• Can be placed in or near community
• Minimal equipment with scrap value
• Potential to produce biogas and reuse treated effluent for irrigation
attach. The anaerobic microorganisms in the biofilm further transform organic matter. The combined ABR and AF can achieve a biodegradable COD reduction rate of up to 90% and a 1-2 log reduction of pathogens.


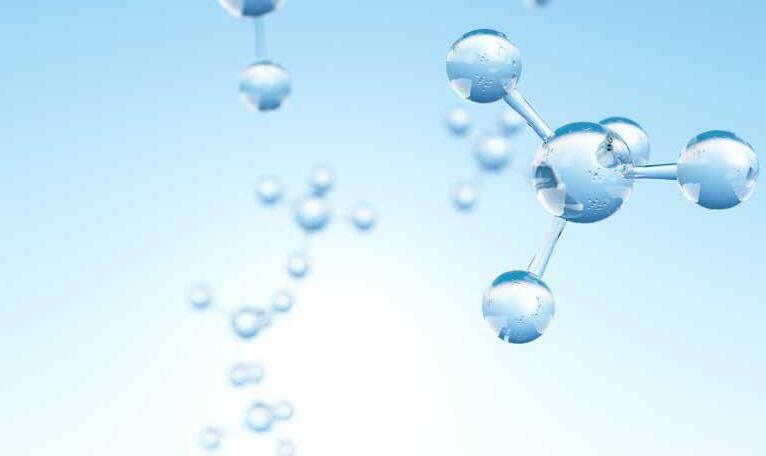
Simple treatment modules, which often include an anaerobic baffled reactor (ABR) and constructed wetlands, are combined based on wastewater characteristics, local conditions, and reuse or discharge requirements. Dewats are customisable for many applications and can be designed to treat domestic, industrial, or institutional organic wastewaterwith flows ranging from 1 m 3/day to 1 500 m 3/day.
c ommon d ewats modules
A settling chamber or biogas digester is often the first module of a Dewats plant, providing primary treatment through sedimentation and flotation. Next, the ABR is a key component of most Dewats plants, providing much of the organics degradation. The ABR consists of a series of chambers separated by baffles that force the wastewater to travel up and down through the chambers. This process anaerobically degrades suspended and soluble solids. The biomass that settles at the bottom of each chamber forms a sludge blanket, which provides intimate contact with the influent wastewater. Progressive anaerobic degradation occurs in the successive chambers.
To further degrade organics, an anaerobic filter (AF) may follow the ABR. The AF chambers are filled with coarse filter material such as stones, cinder or plastic rings, which provides surface area on which biofilms can
Additional treatment steps are required to further remove pathogens and nutrients. Tertiary treatment modules may include constructed wetlands, polishing ponds, or other treatment technologies, depending on discharge standards, reuse requirements and site conditions.
o peration and maintenance
Operation and maintenance of Dewats is relatively simple and can be carried out by service providers or trained maintenance personnel on-site. Although the maintenance requirements are low compared to conventional wastewater treatment works, proper operation and maintenance are critical to ensuring optimal operation.
d ewats globally and locally
The Dewats concept is not new, nor is it untested. BORDA, an expert NGO specialising in sanitation and urban development, pioneered the Dewats approach beginning in 1989 with partners from France, India and China. Over the last 30 years, BORDA has implemented more than 3 000 Dewats in partnership with local municipalities and partner organisations across the globe.
In 2006, BORDA began a partnership with eThekwini Water and Sanitation (EWS) and the University of KwaZuluNatal to test and implement Dewats in the South African context. Over 2009 and 2010, the partners constructed the Newlands Mashu Demonstration and Research Dewats, which receives wastewater from 84 households, treating up to 40 m 3/day of domestic wastewater.
Based on extensive research and operational experience at Newlands Mashu, EWS considers Dewats to be an
accepted technology. BORDA has since designed six Dewats plants for three fully subsidised housing developments in eThekwini that would not otherwise have access to waterborne sanitation. Construction of several of these Dewats is set to begin this year.
In the future, BORDA South Africa hopes to shift into a capacity development role, training members of the public and private sectors to design, implement, operate and maintain Dewats. BORDA will support Dewats practitioners by overseeing quality management and supporting a Dewats community of practice.
South Africa’s housing backlog sits at more than two million units and is growing, due in part to high rates of urbanisation. Much of the land available for subsidised housing is in peri-urban areas with no access to conventional sewers. If housing densities are to be maximised, VIPs, UDDTs and household septic tanks are not feasible. Dewats provide municipalities with an additional tool to more rapidly deliver sanitation services, addressing backlogs in subsidised housing delivery constrained by high infrastructure costs and stringent regulatory requirements. Dewats can bridge the gap between conventional and on-site sanitation, giving more South Africans access to sanitation that is safe, convenient, and protective of the environment.
*carleyTruyens,BScCivEng,MPH EnvHealth,PrEng(USA),iscountry coordinator for BORDA South Africa.
Check out WASA’s dewats video!
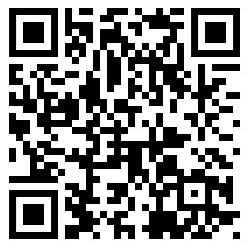

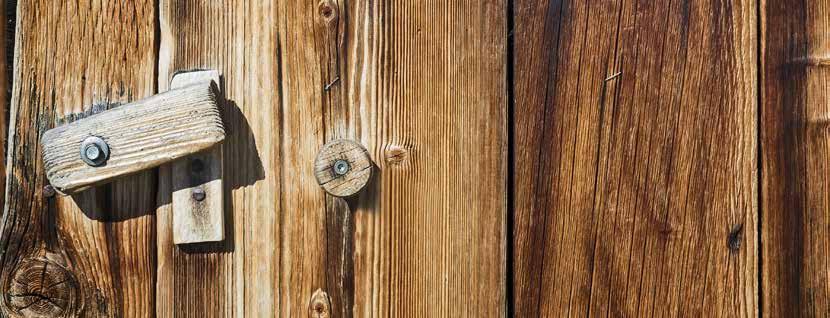
SA helps reinvent the toilet
For the 14 million South Africans without access to toilets, the Reinvented Toilet initiative championed by the Bill & Melinda Gates Foundation could be the key to providing safe, affordable, and adequate sanitation solutions.
By Danielle Petterson
Studies by the World Bank in 18 African countries showed that economic losses due to poor sanitation amount to US$5.5 billion (R80 billion) every year.
To address this, the Bill & Melinda Gates Foundation (BMGF) has invested $200 million (R2.9 billion) into its Reinvented Toilet initiative, and South Africa has played a critical role in enabling the introduction of these reinvented toilet technologies (RTT).
KZN field trials
The Pollution Research Group (PRG) at the University of KwaZulu-Natal’s (UKZN’s) School of Engineering has been involved with the Reinvent the Toilet Challenge since 2011, when the BMGF issued the call for the development of reinvented, off-the-grid sanitation systems.
The PRG provides technical and laboratory support to the technology developers, and has formed a strong partnership with eThekwini Municipality’s Water and Sanitation Unit, making Durban an ideal testing location for
these RTTs. Durban-based consulting engineering firm Khanyisa Projects has come on board as a third partner to provide the logistical and engineering support. It is responsible for bringing the prototype systems into Durban, preparing the sites, and conducting the installation and commissioning of the systems.
The Engineering Field Testing Platform was initiated in 2017, with the first prototypes being tested towards the end of 2017.
As at March 2019, the project team has worked with seven prototype developers to test their systems, either in the PRG laboratory, at a community or household level, or at schools.
Mercer, project manager, Pollution Research Group.
Reinvented technologies
The RTT systems being tested in Durban include new pedestal designs, waste processing and recycling units, or integrated systems that combine a redesigned pedestal and waste processing system.
People are not prepared to trade water savings for an unpleasant toilet experience
The aim of the field testing is to determine the robustness of the system, the user acceptance, and the applicability of the system to the South African environment, explains Susan
One example, a dry-flush pedestal developed by Cranfield University, was tested in the PRG laboratory and in six rural households to determine the robustness of the system and to obtain feedback from the community as to the product’s acceptability. According to Mercer, these trials successfully provided technical information and user feedback that contributed to the redesign of a new version of the pedestal, which is still to be tested.


Other systems, developed by Duke University, the University of South Florida, EcoSan/Caltech, EOOS, Natural Synergies and Eawag, are still being tested in communities, households and the laboratory for between 6 and 18 months. Data on the operation and performance of the respective systems is being collected, analysed and fed back to the technology developers to enable improvements to be made.
Researchers at Duke University believe it is incredibly valuable for technology
developers to have a team on the ground in South Africa to conduct field pilots.
The shortfalls
One of the main technical challenges experienced during the trials is the use of toilet paper and toilet paper alternatives within households and communities. Mercer explains that three of the systems being tested in Durban have previously been trialled in India and China, where toilet paper does not enter the wastewater stream. The use
of toilet paper has resulted in many design challenges that have had to be overcome. Furthermore, alternatives such as newspaper or cloths are sometimes used when there is no toilet paper, causing additional problems for the systems.
Working closely with the eThekwini Water and Sanitation Community Liaison Officer, Dr Cathy Sutherland, senior lecturer: Development Studies, UKZN, leads a team of field researchers who undertake surveys with the communities
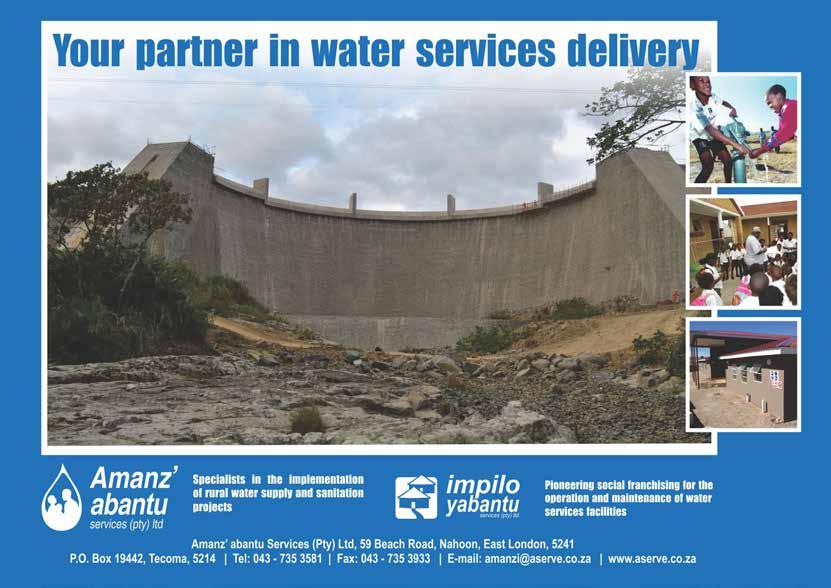
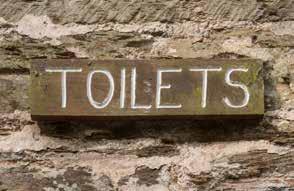

and households involved in testing these systems in order to assess user acceptability. To date, there have been no major challenges in user acceptance. In fact, Sutherland reports that several of the households involved in testing pedestals have contributed ideas for improvement.
One of the prototypes currently being tested in the PRG laboratories is the EOOS source separation toilet interface – a urine diversion toilet pedestal that looks and operates like a traditional flush toilet. This pedestal can be constructed as a low- or pour-flush option, and separates urine from faeces and flush water. Discussions are under way to incorporate these low-flush pedestals into new housing developments linked to decentralised wastewater treatment plants, and in schools.
a higher standard
Until recently, no standards were in place for RTTs and non-sewered sanitation. However, the BMGF has championed the newly published ISO 30500, which defines the operational requirements for the reinvented toilet, as well as other existing and future standalone, non-sewered sanitation technologies.
to test the ISO compliance of off-grid sanitation systems?
Sa’s situation
Although many of the systems being tested may not yet address the sanitation challenges South Africa faces, each prototype has a unique or innovative part or process in its design. “These innovations could, therefore, be used in combination with existing sanitation technologies, or with other prototype technologies to provide a sustainable sanitation solution that uses less water and energy, and which produces reusable by-products,” says Mercer.
She adds that despite South Africa’s many water challenges, the majority of the systems being tested make use of water for flushing, although typically at a reduced volume and using recycled flush water.
It is critical that we develop new forms of sanitation that can be used to address the lack of adequate sanitation in cities
The standard will make the adoption of new technologies much easier and ensure consistency across solutions, as it sets targets for safety, processing capability, operational performance, and waste by-products.
ISO 30500 gives a target for systems to achieve and a useful template for recording how a system performs, including the operation and maintenance requirements of the system, explains Professor Chris Buckley, head: Pollution Research Group.
Additionally, the prototype testing that is taking place in Durban has allowed the ISO 30500 methods to be tested and answers questions such as: (i) How expensive is it to test if a system is ISO compliant? (ii) What are the logistical requirements of those tests? (iii) Does South Africa currently have the testing facilities
“The social surveys have shown that people are intensely aware of the challenges of water shortages in South Africa and that saving water is something that interests them. However, people are not prepared to trade water savings for an unpleasant toilet experience. That means that low-flush or dry pedestals and systems that recycle water must still be odour-free, and easy and pleasant to use,” explains Sutherland. At the current prototype stage, maintenance requirements are still high and, as with any new technology, there will be the need for a trained workforce with the skills to operate and maintain systems. One of the advantages of testing the systems in South Africa is that local engineers are learning how the systems work and what the maintenance and operation requirements for those systems are.
The municipality can use this experience to understand how their current processes would have to change in order to accommodate new sanitation technologies. At a larger scale, the South African Water Research Commission (WRC) is keen to understand the sanitation business opportunities that may come from new technologies such as these.
did you KnoW?
Just one flush from a traditional sewer-based toilet uses up to 13 ℓ of water.
If all 56.72 million South African flushed just once, 737 million litres of water would be used.
In partnership with the Department of Science and Technology and the BMGF, the WRC has created the South African Sanitation Technology Evaluation Programme and framed an Accelerated Industrialisation Platform Model in order to assist businesses looking to grow sustainability options and competitiveness in their future growth strategies.
This model encourages capability building, localisation and manufacturing opportunities for South African companies, and provides an opportunity for them to use their national knowledge to develop improved systems that are dignified, affordable, and appropriate, explains Dr Valerie Naidoo, executive manager: Business Development and Innovations, WRC.
“This model allows for a more rapid spread of innovative technologies as businesses are agile while water sector authorities have defined mandates. In parallel, the WRC will look at policy, standards, training, and investment barriers and enter into dialogue with national departments to open the water and sanitation sector to improved delivery,” she adds.
According to the BMGF, the commercialisation of RTTs presents a $6 billion (R87 billion) a year global opportunity across the sanitation value chain in engineering and design, manufacturing, sales and marketing, installation, service and maintenance. The export potential for well-designed South African products is, therefore, enormous.
“It is critical that we develop new forms of sanitation that can be used to address the lack of adequate sanitation in cities. These will have to address and operate within other development deficits such as a lack of infrastructure, lack of or intermittent access to electricity, dense informal settlements, poverty, and inequality,” stresses Buckley.
“The opportunity to participate in the BMGF project has raised the technical and social profile of sanitation within the country. It offers an opportunity for South African companies to gain an early entry into the new sanitation industry where sanitation can be seen as a service and new products and approaches will disrupt a very conservative industry.”
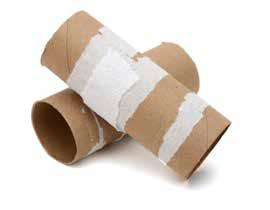
AGRULINE
fittings & pipes resistant to cracks
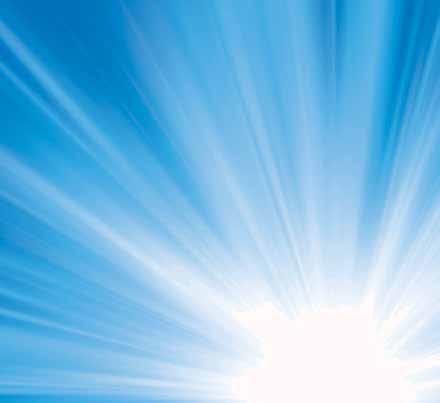
LONGER SERVICE LIFE crack resistant PE 100-RC
HIGH ECONOMIC EFFICIENCY sandbed-free installation
LASTING CONNECTIONS better welding results COMPLETE PIPING SYSTEM for gas, water and waste water
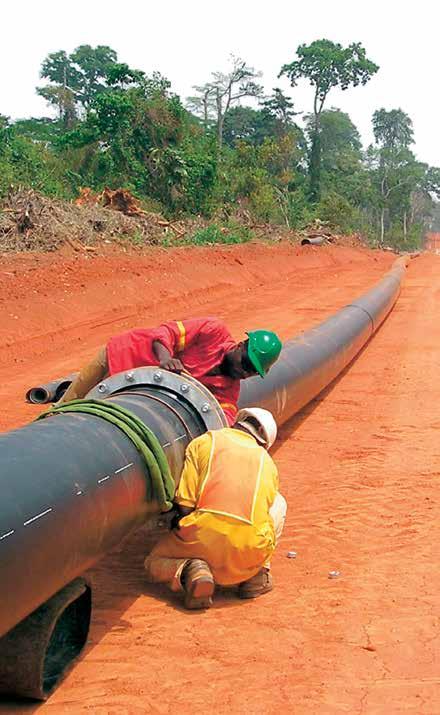
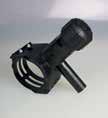
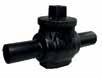



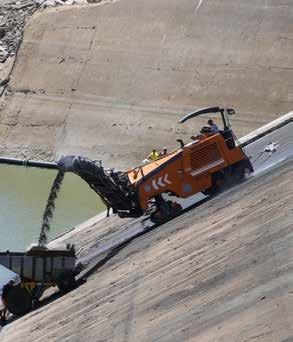
Resealing Von Bach Dam
The Von Bach Dam is the backbone of the water supply for Windhoek, Namibia. With the dam’s brittle asphaltic seal in need of urgent replacing and the rainy season fast approaching, the Namibia Water Corporation was under pressure to repair the dam.
Racing the clock
Time was of the essence for the project team as failure to successfully complete the project before the next rainy season could result in water shortages, which would have dire consequences for Windhoek’s water users and the economy.
Von Bach Dam is a concretefaced rockfill dam (CFRD) with a specially designed hydraulic asphaltic seal.
Asphaltic-faced rockfill dams are uncommon across Africa, which only houses approximately five similar dams, two of which are in Namibia.
Tests on the dam’s old asphaltic seal indicated that the brittle asphalt had to be replaced as soon as possible, and to an elevation as low as possible to optimise the repair effort. After a three-year drought the dam’s water reached approximately 10% – its lowest level in 20 years. This provided an ideal window of opportunity to rehabilitate the deteriorated asphaltic seal, which forms the watertight membrane of the dam.
Planning the project was a balancing act for consulting engineering firm Knight Piésold. The projected dam levels and rain inflows had to be considered together with the shipping and site establishment of imported construction machinery.
Specialised expertise was required to fast-track this project, with under three months available to demobilise the construction plant in Europe, ship it to Namibia, arrange temporary import clearance and taxes, establish equipment on-site, and complete the work.
The project’s complexity lay in the logistical arrangements to import the specialised construction equipment, arrange import taxes and clearances, work visas for foreign staff, get the asphalt plant operational, finalise the mix design, and get the project completed before the main onslaught of the approaching rainy season.
Benefits of an asphalt seal
Several CFRDs in Brazil and Lesotho have experienced embankment settlement, leading to the rigid concrete layers rupturing under concentrated compressive force, and therefore failure to contain water. Asphalt is unique in its ability to absorb settlement without cracking and act more like a flexible membrane than a rigid concrete shell.
Repairing Von Bach Dam’s asphalt face with a new asphalt seal, as opposed to a plastic membrane or conventional concrete, was therefore recommended.
Asphalt contains volatiles that escape when exposed to UV rays and the atmosphere. This can lead to increased brittleness and cracking of the asphalt surface. However, asphalt covered by water for a large percentage of the time is typically in a better condition than the asphalt above water level.
In a dry environment such as Namibia, where the dam’s water level frequently drops to below 50%, a large portion of the asphalt is exposed to natural elements. To counter the escape of volatiles, a sacrificial mastic seal layer of 2 mm to 3 mm of specific bitumen/filler
difficult work conditions
bitufill-oven and jointing materials, and jointing required manual labour by a team with experience in hydraulic asphalt seals.
Project success
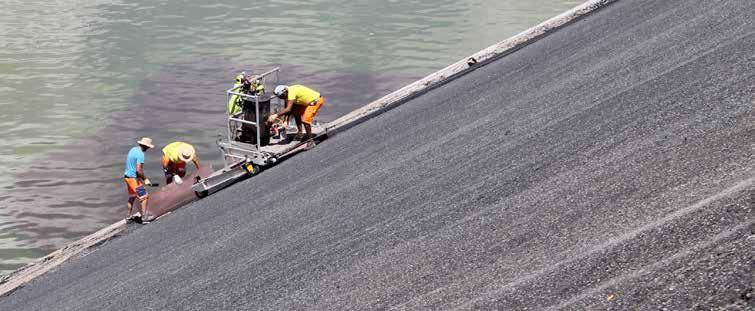
mix is spread over the asphalt seal. This mastic layer needs replacement every 10 to 15 years to ensure that the dense asphalt layer underneath remains protected and crack-free.
The Von Bach Dam seal design includes the protective mastic coating, as well as operational guidelines for inspections and replacement of the mastic layer when required.
If the client operates and maintains the new asphaltic seal and mastic coat according to the recommended operational guideline, the seal’s longevity should be ensured, beyond the roughly 45 years the original seal provided.
The steep slope of the dam posed a challenge in the removal and replacement of asphalt. No vehicle had sufficient traction to work on the steep slopes with a smooth asphalt surface, without damaging the asphalt. Heavy mobile winches were therefore employed to control the movement of construction equipment up and down the face of the dam.
The winches travelled horizontally along the crest road of the dam, from side to side, while the asphalt milling and paving machines travelled in a vertical direction –up and down the face of the embankment. The tracked milling and paving machines had pads installed between the ridges of the tracks to ensure even distribution of the machine weight on to the asphalt, without damaging the surface.
The preparation of joints on the sides of the embankment also required a mobile working platform equipped with
Effective teamwork by all parties led to successful project completion within the set time frame. The completed dam started receiving inflow within two weeks of completion and within two months the dam was at 60% full, inundating the newly placed seal.
The leakage rate of the dam has been reduced by nearly 50%, indicating that the old seal had likely been losing water through cracks. The new seal has also reduced the risk of failure and increased the operational life of the dam.
project team
Client: namibia water Corporation (NamWater)
Consulting engineer: Knight piésold
Contractor: wAlo International

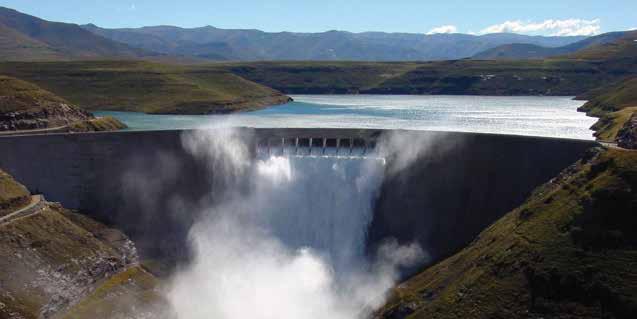



From waste to resource Providing water to local communities
The first phase of the Tweefontein Water Reclamation Plant is now fully operational, providing 9 MLD of clean drinking water.
Located 8 km east of the small town of Ogies in Mpumalanga, Glencore Operations South Africa has established the Tweefontein Water Reclamation Plant, which treats mine-affected water to potable standards for the surrounding community.
The first 9 MLD phase of the plant is fully operational, and produced its first water in November 2018. Glencore is now in discussions with the eMalahleni Local Municipality (ELM) on the possible upgrade of the plant in order to increase the throughput to 14 MLD. “There is potential to increase the capacity further depending on all the governing variables, including excess water in the mines and demand increase from ELM,” explains Shivani Chetram, head: Communications, Glencore Operations South Africa.
Supporting the community
Prior to the establishment of the Tweefontein Water Reclamation Plant, the surrounding community was often without running water for extended periods of time, largely due to growing demand and lack of capacity.
Although initially conceptualised as a way to manage mine-affected water in
Glencore’s Tweefontein, Goedgevonden and iMpunzi complexes, the plant also offered the opportunity to provide potable water to the Phola Township, north of Ogies. The fully fledged reverse osmosis plant treats the mine-affected water to drinking water standards, complying with SANS 241-2015.
did you KnoW?
The National Water and Sanitation Master Plan seeks to diversify South Africa’s water supply, ensuring 2% comes from treated AMd by 2040

Water is extracted from mined-out underground workings used for the storage of mine-affected water. Typical of water emanating from coal mining activities, the water entering the reclamation plant has a high sulfate level. This said, with the current process, the plant recovers approximately 96% clean water from the feed. With a further technological introduction, the plant will soon be recovering in excess of 99% clean water from the contaminated body of water, says Chetram.
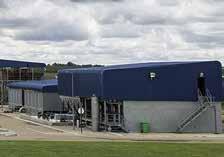
“The process to clean mine-affected water is very similar for all plants recovering water from old mine workings. Unfortunately, the water from different mining areas can differ significantly in respect of composition, making every water reclamation plant different from the next. The difference between the Glencore plant and other plants in the area exists not in the technology employed, but rather the manner in which the process was designed, resulting in the use of less chemicals in the recovery,” she continues.
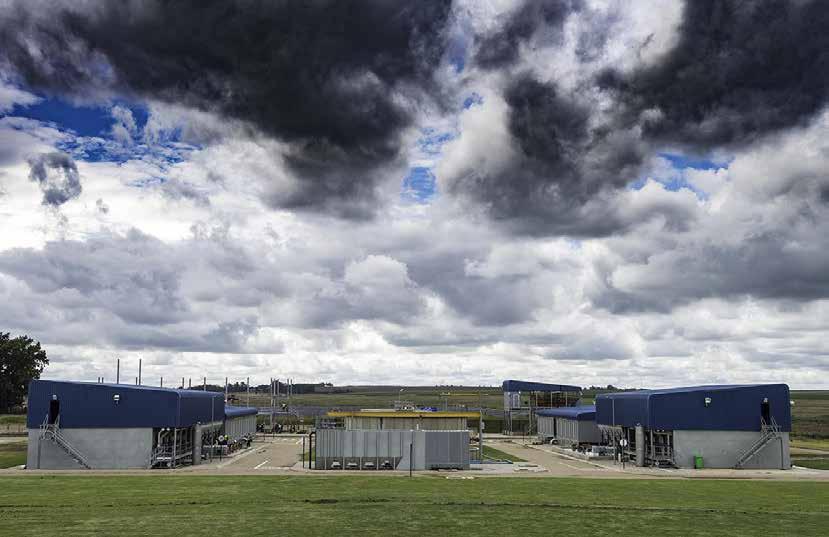
Significant infrastructure investment
The by-product of the treatment process is highly concentrated brine, which is stored in an evaporation brine pond. Established solely by Glencore Operations South Africa, this pond had to be constructed along with the entire infrastructure necessary to make the plant a reality. This included: boreholes and pumps; electrical infrastructure; reservoirs; transfer pump stations; pipelines; lined storage ponds for plant feedwater, sludge and brine; as well as
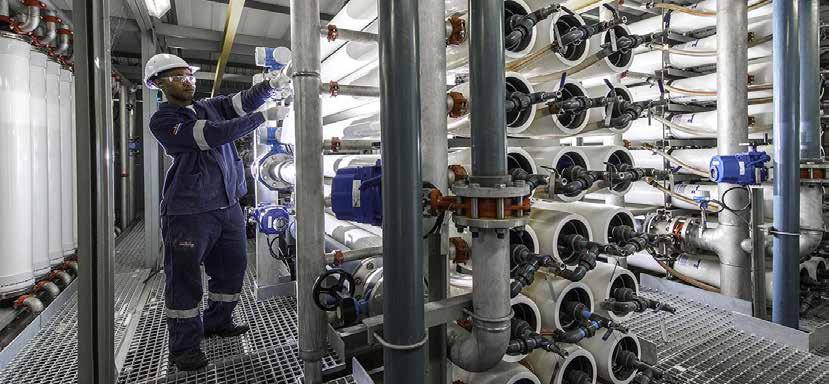
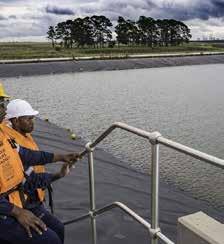
the complete reverse osmosis plant.
Associated support infrastructure – such as fencing, offices, security, operations and maintenance – was also necessary.
A 16 km pipeline was established between the water reclamation plant and Phola Township, where a potable water treatment facility, together with a reservoir and pump station, was established on the site to supply water to the area.
“We can now supply 9 MLD that was not available for consumption prior to the establishment of this plant, contributing to the overall water security of the area,” says Chetram.
“At the same time, the Tweefontein Water Reclamation Plant will
assist in reducing our water usage footprint from other water sources such as dams and rivers, while providing an effective solution for our current mining operations as well as the long-term management and treatment of water decant at eventual mine closure.”
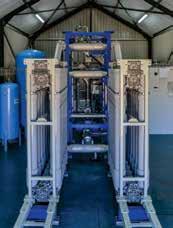
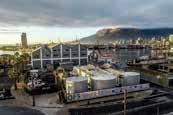





trenchless innovations for Cape town
Innovative trenchless design and methodology, coupled with the ability to adapt to changing circumstances, defined the project for the rehabilitation and upgrading of the Sanddrift Bulk Sewer, which won the 2018 Joop van Wamelen Award of Excellence.
Following minor collapses between 2003 and 2006, and subsequent condition assessments, it was recommended that sections of the Sanddrift Bulk Sewer (SBS), located just upstream of Montague Gardens in Cape Town, be closely monitored and rehabilitated.
Upon further investigation, it was found that a number of sections of the overfour-decade-old sewer were significantly degraded and in need of rehabilitation. Furthermore, the new Bridgeway Sewage Pump Station rising mains from Century City, which will discharge halfway down the existing 2 km SBS route, is expected to reach a peak discharge of 110 ℓ/s in the next 10 to 15 years, adding to the SBS’s already large catchment area, and flow. This increase in flow would exceed the future estimated peak wet weather flow capacity of the existing SBS, necessitating an upgrade downstream of this discharge point. The upstream section has enough hydraulic capacity to allow for trenchless rehabilitation.
The rehabilitation
consisted of reinforced concrete pipes with dolomitic aggregate and sacrificial lining. However, due to various sewerage rising mains of neighbouring catchments discharging at a constant flow into the upstream section of the bulk of the SBS, the sewer has been subjected to severe corrosion above the water line (only) into a non-circular/near-mushroom shape.
“Corrosion of the alkaline concrete sewer pipes occur when accumulated hydrogen sulfide gas in the effluent is released by turbulent flows or discharges to condensate on non-submerged sewer pipe walls to form corrosive sulfuric acid. In certain sections, the sewer had corroded right through the pipe spring-line to reveal external encasement concrete,” explains Konrad Röhrs, associate engineer, Aecom.
As the consulting engineers, Aecom concluded that the section of the sewer upstream of the Bridgeway rising mains would have just enough capacity to allow for the increased future flow estimates, and determined that the installation of a close-fit inverted or pull-in cured-inplace-pipe (CIPP) rehabilitation lining in the existing SBS was the only viable trenchless solution.
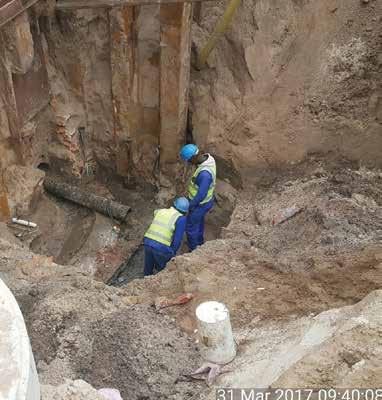
However, the mushroom shape of the existing sewer presented a significant design challenge and Aecom needed
project team
Client: City of Cape Town
Consulting engineer: Aecom
Contractor: CSV Construction
Subcontractor: Tuboseal

to compile a 3D computer-aided finite element model (FEM), mirroring the expected mushroom-shaped crosssection profile and constraints of the expected liner within the existing sewer.
The ‘ASTM 1216: Standard Practice for Rehabilitation of Existing Pipelines and Conduits by the Inversion and Curing of a Resin-Impregnated Tube’ design code only accommodates for circular linings with an allowance for ovality of up to 10%. The mushroom shape of the corroded sewer was not only expected to exceed this tolerance, but also to have a negative indentation/ curvature around the corroded sill above the constant discharge flow level. This would be compounded by the high water table exerting external pressure on the liner. Moreover, the inner diameter of the existing sewer was expected to vary significantly along its length due to the severe and potentially varied corrosion conditions.
The solution
To increase the incline, ribs were welded on to the pipe to suspend it at increased cumulative eccentricities
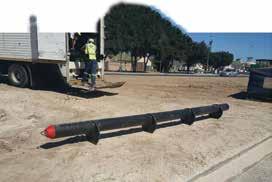
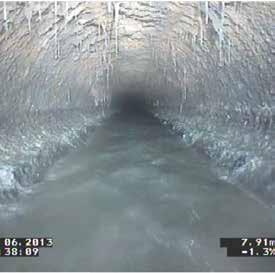
Using the 3D computer-aided FEM analysis, Aecom was able to explore resin and liner options, applying a realistic and calibrated set of ASTM 1216 design code parameters. The team found that adding an additional calibrated safety factor
Due to severe corrosion, the existing sewer had become a mushroom shape, presenting significant design challenges
The ribbed pipe was divided into 3 m long sections and lowered into a shored excavation

(increasing the lining wall thickness by an additional 20%) could be applied to accommodate for the non-circular shape of the sewer.
In order to mitigate variances in diameter along the corroded sewer length, the appointed contractor, CSV Construction, supported by Tuboseal and Aecom, selected an un-reinforced felt liner with a diameter slightly above the average of the actual measured diameters of the existing corroded pipes.
The un-reinforced liner was able to allow a 5% to 10% stretch to ensure a close fit of the liner around the circumference of the existing pipe. Where the existing pipe was smaller than the liner circumference, longitudinal creases perpendicular to the pipe circumference could potentially form; however, it was expected that wellcured, resin-filled creases would cure into structural webs – ultimately adding to the structural stiffness of the cured liner.
Röhrs further explains that this was preferable to a non-close-fit lining, which could result in an uneven invert of the pipe due to sections of the liner potentially becoming buoyant from ingress groundwater pressure, which would in turn negatively affect the hydraulic capacity of the rehabilitated pipe.
A pre-liner was also installed in advance of the actual
The main over-pumping system
material when installed under hydrostatic pressure (pre-cure).
Tuboseal installed the liner in seven portions – from both up- and downstream positions – with the longest portion being over 100 m. The end result was a set of seven cost-effective, well-cured and rehabilitated close-fit lined sewer sections with a total length of over 700 m, achieved well within the programme schedule of the overall contract.
The installation team faced various difficult technical challenges, including having to conduct the installation under and from within the underground parking garage of the Sable Square Shopping Centre. Through excellent coordination and communication, the installation was safely conducted, with minimal impact and disruption to the public.
“Although we mitigated a lot of risk by the additional design measures and simulations, this remained a non-standard installation and a lot of risk still applied. We insisted that Tuboseal have a very thorough quality assurance plan to provide security and monitor conditions on-site. We must
By omitting running costs of a temporary over-pumping system, the team secured significant cost savings
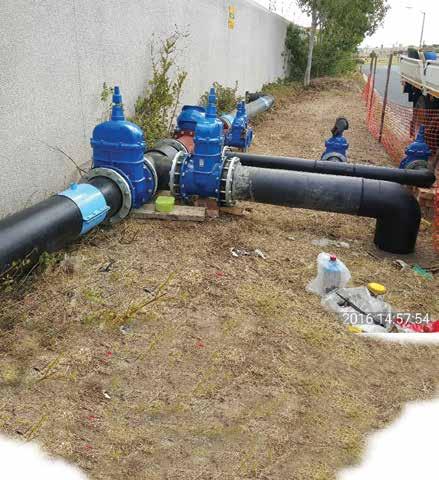
Every year, the Southern African Society for Trenchless Technology (SASTT) awards the Joop van Wamelen Award of Excellence to a leading project team in recognition of exceptional contributions to the active promotion and implementation of trenchless technology in Southern Africa.

commend Tuboseal on the fact that they presented us with a set of very thorough quality control documents and records – making post-installation inspections much easier and informed – so that no sections with any potential fault conditions were left unresolved or approved,” says Röhrs.
adapted slip-lining method
The section of the SBS that required upgrading could not follow the exact same route as the existing and still-active SBS. The upgraded ND 750 mm line provided to the SBS followed a new route; however, this resulted in the potential isolation of a small subcatchment of the existing SBS. This was overcome by ensuring the new sewer retained the same vertical alignment in this position as the existing sewer, to continue receiving a reduced flow of 30 ℓ/s – reduced from 120 ℓ/s. However, the reduced flow in the old large-diameter pipe brought a concern of sedimentation, says Röhrs.
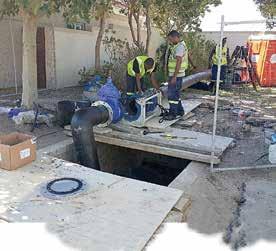
In order to ensure that the reduced flow would maintain scour velocity along this section of the bulk sewer, an adaptation to the normal slip-line method was proposed.
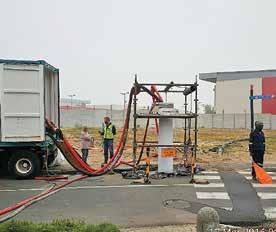
The CIPP installations had to be conducted on busy public roads
This involved using a slip-line of a smaller ND 200 mm HDPE at an increased slope, by suspending it in 25 mm thick perpendicular HDPE extrusion-welded ND 450 mm chamfered flanges/ribs, spaced at 1.5 m intervals. The ribs work to suspend the pipe at increased cumulative eccentricities, resulting in the required increased incline. Due to the limited workspace
joop Van Wamelen aWard

in the road reserve, the pipe was divided into 3 m long sections, to be lowered into a shored excavation, and joined by external electrofusion-welded couplings. This jointing method would ensure unobtrusive flow, unlike butt-welded beads, which could infringe on the flow of the effluent or strain any suspended solid materials, explains Röhrs.
innovative flow diversion
As part of the tender design, the contractor was required to accommodate the diversion of the bulk effluent flow resulting from the Brooklyn Chest Sewage Pump Station, where the SBS commences, through a 700 m long ND 450 mm continuously welded HDPE pipe. Röhrs explains that although the safe and effective system of silent pack pumps was provided for as per the tender design, the project team identified the opportunity for coupling the proposed 700 m ND 450 mm HDPE bypass rising main to the existing Brooklyn Chest pump station instead. Following investigation and testing, the two rising main systems
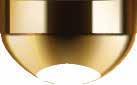



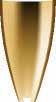





were joined effectively. By omitting running costs of the temporary over-pumping system, the team was able to secure significant cost savings for the City of Cape Town.
Furthermore, the local reticulation systems were intercepted and accumulated at a central point, halfway along the rehabilitation section, before being tied in to the main ND 450 mm HDPE bypass rising main. By combining localised bypass/over-pump systems and tying this into the main rising main, additional costs savings were realised.

These cost savings also allowed the project team to relocate the existing dilapidated and severely corroded rising main discharge chamber, previously positioned in a residential children’s play area, into the nearby public road reserve in a new, corrosion-protected, reinforcedconcrete chamber.
Mark Brodovcky, project engineer for the City of Cape Town, commended the team on this innovative method, which was only conceptualised after the tender
had been awarded and resulted in savings of several million for the city. Röhrs believes the overall design was well workshopped and executed by the project team, ultimately extending the life and functionality of the local sewer system. “A year later, we are very happy to see that the design and concept have been successful and the system is running as expected.”
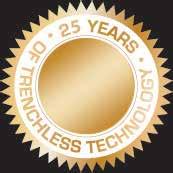




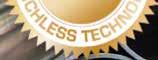



The existing bulk sewer was upgraded to ND 750 mm
WC/W d M cost recovery: Free basic water and cost recovery challenges
ThisisthesixtharticleinaseriesofeightbyDerekHazeltononWC/WDM.Theearlierarticlesappearedin Water&SanitationafricaVol.13Nos.4,5&6andVol.14Nos.1&2)
The first article in this series began by demonstrating that there is a water supply service delivery crisis in South Africa and that many water services authorities are close to financial collapse. It continued by stating that financial sustainability, or full cost recovery, is a primary aim of, and a precondition for, the successful implementation of WC/WDM. Because of the importance of full cost recovery and the challenges related to achieving it, the subject will be covered in the last three articles of this series.
By Derek G Hazelton
This article, and the following two articles, will cover all the items necessary to achieve full cost recovery equitably, so that, when these have been implemented with the other components of WC/WDM, water services authorities (WSAs) will be able to deliver the reasonable water needs of all their customers sustainably.
The items covered will include: Free Basic Water (FBW), an accurate understanding of the difficulties of achieving full cost recovery, the use of the Local Government Equitable Share (LGES) allocations, water volumes measurement and management, budgeting, the management of costs and resultant expenditure, tariff design, billing, and non-recovered revenue reduction.
The need for leadership and cooperation
In addition, full cost recovery requires healthy leadership from the municipal council and manager, and teamwork within and cooperation between the chief financial officer’s and the technical director’s departments. Finally, the leadership must be founded on an ethos of service and community participation,
and not on an ethos of domination and/ or partiality. This ethos is well described in the Department of Public Service and Administration’s Batho Pele White Paper.
free Basic Water
Universal versus targeted: There is a noticeable shift in WSAs from universal FBW provision to targeted provision. This change is supported but it is essential, in terms of the Constitution, the Local Government Municipal Systems Act, and CoGTA’s national framework for municipal indigent policies, that all poor households receive FBW that is enough for their basic needs. These documents, taken together, make it clear that the accessibility of free services must include all poor persons living in South Africa and must therefore embrace tenants, back yard and shack dwellers, all non-citizens, etc.
Targeting methods: In WSAs where indigent registers are used as the sole means of targeting, the number of households receiving free basic water is always too low. WSAs therefore need to include other methods of deeming households to be poor, such as low rateable evaluations, low-income suburbs

excluding households with a higher income lifestyle. It is also important that poor households that are not deemed to be indigent still have to access FBW. An indigent register is a suitable backstop for doing this, but WSAs must still take care that the information required to register does not exclude the most vulnerable. Self-targeting, for example, by means of an affidavit made at a police station, confirmed by a visiting ward councillor or social worker, and renewable every twelve to fifteen months, could be accepted by the WSA.
What percentage of households/ residents should be receiving fBW: Each municipality’s LGES of national taxes to subsidise free basic services is calculated by National Treasury (NT) from the percentage of households with a monthly income of less than two old age pensions. This percentage is published on NT’s website. WSAs can thus see what percentage of their customers should be receiving FBW.
allocating fBW on a per person basis: It appears that, while a few WSAs allocate FBW based on the number of households being metered by a single meter, no WSAs allocate water on a per
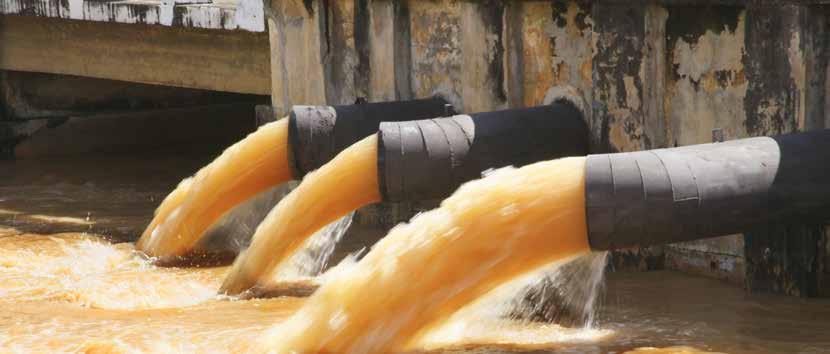
Derek G Hazelton, Pr Eng., FWISA, founder and manager of TSE Water Services
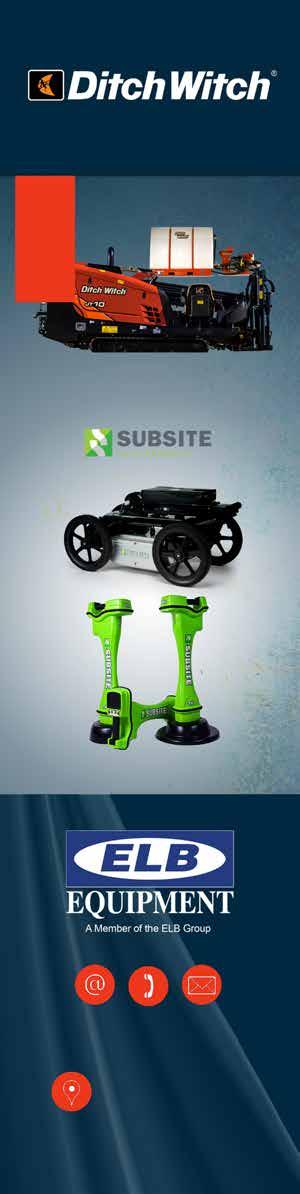
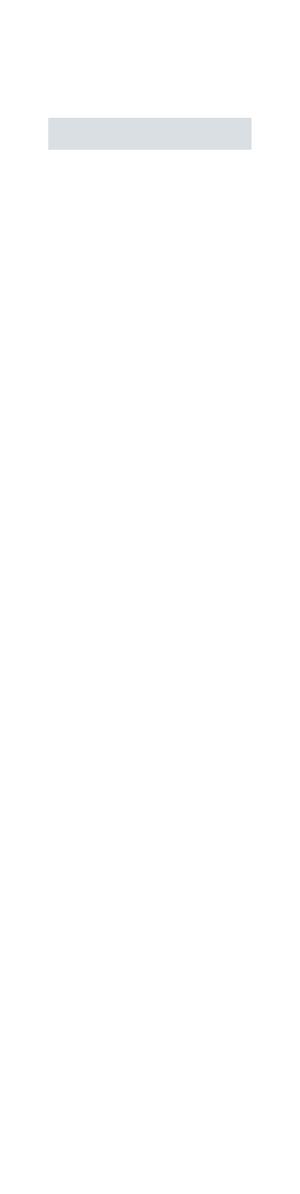
Urine Diversion Dry Sanitation in eThekwini Has it exceeded the original expectations?
Yes! It has…
Sanitation: Poor rural communities and high-income urban suburbs
Very different histories – similar futures?
person basis. This is a shortcoming that discriminates against poor areas where many people are likely to share a single allocation/water-meter. This shortcoming was clearly highlighted during the court action undertaken by some residents from Phiri, Johannesburg, where the average number of people per account holder was 8.8. The leading litigant lived on a stand with 20 occupants, which the municipality judged to be a single household. The High Court and the Supreme Court of Appeal both confirmed that FBW must be allocated on a per person basis. However, WSAs, using an ethos of domination rather than service, are ignoring the litigants’ arguments, and the judgements of these two courts. Rather, they are relying on the subsequent judgement of the Constitutional Court, which has been widely discredited, to give minimal relief to persons receiving substantially less FBW than their neighbours, and sometimes even less than the regulatory 25 ℓ per person/day. Thus, based on equity and efficiency, WSAs should change to allocating FBW on a per person basis as soon as is practical.
The total number of persons receiving FBW should then be at least equal to the percentage figure used by NT to calculate the WSA’s LGES grant, since, with this number of persons, the percentage of customer management units receiving FBW will be less than NT’s percentage of poor-households figure.
How much fBW is enough? In contrast to WSAs ignoring the Phiri residents’ plea to have FBW delivered on a per person basis, several WSAs have acknowledged
that the basic water needs of customers with waterborne sanitation is significantly higher than the basic water needs of households with dry sanitation. These WSAs have used quantities between 8 kℓ/mth and 15 kℓ/mth per household to define the FBW volume. It is recommended that WSAs use a minimum of 50 ℓ per person/day for defining FBW for customers with waterborne sanitation. By the time the WC/WDM turnaround project is complete, it should be feasible to gradually increase this figure safely to 75 ℓ per person/day, which is judged to reflect the true basic needs of households with waterborne sanitation.
This need for additional FBW for poor households with waterborne sanitation will always be a financial burden on WSAs. In addition, the Department of Water and Sanitation (DWS) says the provision of waterborne sanitation is unsustainable from a national water scarcity viewpoint. For all new housing developments, therefore, the use of dry sanitation needs to be considered. Hopefully, by using innovative dry technologies, sanitation in poor rural communities and high-income urban suburbs will have similar futures, as illustrated in Figure 1.
Alternatively, the poorest households could be allocated 75 ℓ per person/ day FBW, while other poor households are allocated 50 ℓ per person/day. Consideration should be given to reclassifying any “poor households” who consistently use less than the 75 ℓ per person/day as “poorest households”. Persons with dry sanitation eligible for FBW should be allocated a minimum of 25 ℓ per person/day. In keeping with the DWS’s water allocation reform (WAR) initiative, we should be moving towards ensuring fairness in access to
FIGURE 1 The desirable future of sanitation provision: innovative dry technologies
water for productive purposes. WSAs should therefore consider allocating a minimum of 45 ℓ per person/day to allow households to grow vegetables. In areas with water shortages or where the WSA is struggling to cover water delivery costs, the WSA could limit the allocation of additional FBW to poor households who are registered vegetable growers.
Where WSAs have a two-tier FBW allocation system, and/or the FBW allocation is adequate for all the households’ basic needs, the WSA could consider limiting such households’ water usage to the FBW, or a slightly higher amount. Households that wish to use more water could consider re-registering themselves as households with lower FBW benefits.
full cost recovery challenges post 1994
The challenge and National Treasury’s response: Before 1994, water supply services generated surpluses for municipalities. But we need to understand that these municipalities generally excluded the black majority. Today, with responsibility for universal delivery, and the allocation of enough FBW to all poor households, the challenges are much greater.
For this reason, NT has increased the value of LGES transfers dramatically since they were first introduced in 1998. Then, when NT still states that water tariffs must reflect true delivery costs, it discourages cross-subsidies from the rates account etc. However, especially in poor WSAs, the income from customers is not expected to cover all the delivery costs. Rather all WSAs are expected to ensure that the LGES water component is used for its intended purpose: to pay for the delivery of FBW to all poor households. Then the income from customers, plus the water component of the LGES grant, needs to cover the full costs of water delivery. allocating the full LGeS water component to support the delivery of fBW to all poor households: Despite the dramatic increase in LGES transfers since they were first introduced, until 2012, the transfers per poor household to DMs and rural LMs was significantly less than the transfers to other municipalities, even after the authorised service responsibilities of the different municipalities was considered. Of greatest concern was the low level of support allocated to these municipalities for overhead institutional costs. This meant that some of the basic services
components of the LGES allocation had to be diverted to pay for these institutional costs.
However, in 2012, the LGES formula was reviewed and modified after extensive consultation. During the review, it was decided that all municipalities are to receive the same per poor household (generous) funding to deliver basic quantities, of the four basic services, free to all poor households. Further, municipalities are to receive additional funding to cover institutional costs and the cost of other essential services on a sliding scale: from 0% for municipalities with the greatest ability to raise funds from own revenues, or other sources, to 100% for those with the lowest ability to raise funds. Applying these adjustment factors allows NT to keep the LGES allocation for the four basic services high, without increasing the available amount of LGES money.
After a five-year phase-in process, the resultant annual payment allocations of implementing the new formula are shown in Figure 2. These results reflect higher funding to the poorer provinces
FIGURE 2 2019 weighted annual average LGES allocations per poor household for metros and each province
and municipalities, which will allow all well-managed WSAs to supply basic quantities of FBW to all poor households. Some DM WSAs may find that their LGES allocations still under-subsidise local health services and institutional costs. But compensation for the terminated RSC/JSB levies is added to DM LGES allocations. This means any LGES under-funding can be overcome, using these compensation/replacement grants. Metros also receive RSC levies replacement grants, sourced through the general fuel levy. This additional funding

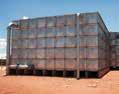
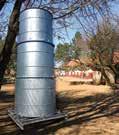
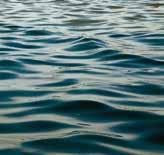
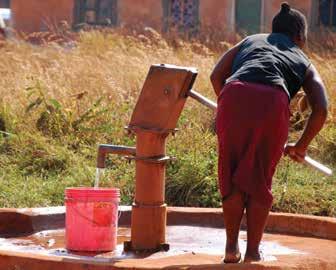
means metros have funds to deliver additional FBW to poor households with waterborne sanitation.
LM WSAs have no source of extra funding and may struggle to deliver addition FBW to poor households with waterborne sanitation if numbers are high. Table 1 is a duplication of Figure 2, with RSC levies replacement grants added, and reflects monthly, instead of annual, allocations. Local economic development (Led): The Constitution and the National Development Plan mandate local government to promote LED. Despite the LGES review, LED is still an unfunded mandate. However, if the implementation of WC/WDM projects includes community skills development and participation, and later these skills are used for the ongoing operation, monitoring and maintenance of the local water delivery infrastructure, as motivated in this series of articles, some of the LGES funds used to deliver FBW will be spent in the same communities, and thereby support LED. Thus, the water component of the LGES allocations will inject LED funds into communities, while simultaneously delivering FBW. Alternatively, one can affirm that the LGES will be used to alleviate poverty in two ways simultaneously.
*Forafulllistofreferences,pleasecontacttheauthorat tsewater@icon.co.za.
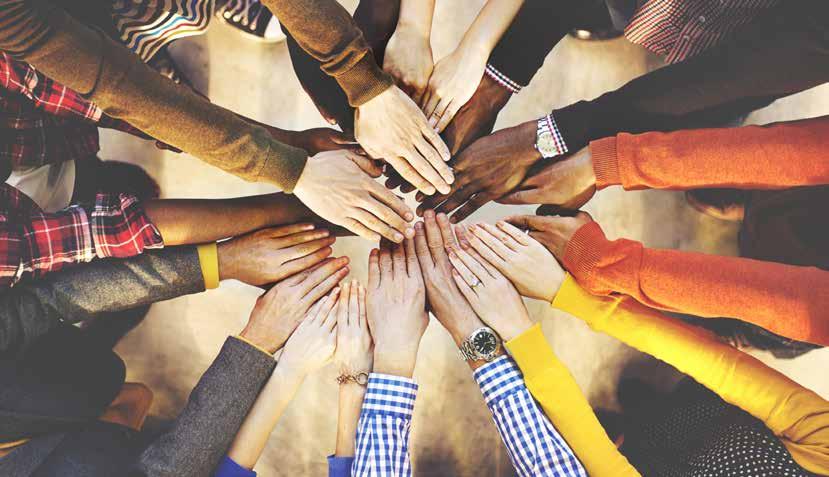
WISA recently held its first think tank to encourage members to take an active interest in the issues affecting the water sector and to provide input to help shape WISA’s strategy moving forward.
The inaugural WISA Membership
Think Tank session was held in April under the theme ‘All hands on deck’ – the same theme driving WISA’s upcoming 2020 Biennial Conference. Here, members discussed three key topics identified as the biggest issues facing the sector in the recent WISA member survey:
1. Water scarcity and quality
2. Skills development
3. Infrastructure management.
Nora Hanke-Louw, chair: WISA Board Strategic Committee, WISA, explains that the recent changes WISA has made to its Memorandum of Incorporation allow for greater member involvement and seek to better involve members in driving the institute’s strategic partnership with the sector.
an innovative approach
The Membership Think Tank saw members gather in four key locations across the country and join a conference call to allow members across South Africa to engage on key issues.
We are WISA Working together to find solutions
Members formed breakaway groups to discuss the three key topics, making suggestions on what needs to change, how individuals, branches and divisions can contribute and, on a larger scale, how WISA as an organisation can make a difference. This feedback has been passed on to the WISA Board Strategic Committee and board in order to assess how members’ suggestions fit into the current strategy, and to help inform WISA’s strategy going forward.
Water scarcity and quality
On the topic of water scarcity and quality, members highlighted the country’s deteriorating wastewater treatment infrastructure as a contributing factor to declining water quality. It was also noted that, unfortunately, the monitoring of water quality has largely fallen away.
A gap between those with the skills to address these challenges and those who make the decisions was also identified. Members called on WISA to play a role in closing this gap and breaking down silo mentalities, in order to facilitate better
implementation of water regulation and legislation.
Skills development
Breakaway groups discussing skills development agreed that skills gaps must be identified, and mentorships, internships and training be offered in response. In this regard, various needs were recognised, such as passing skills down to younger professionals through mentorship, retaining young people in the sector, and bridging the gap between graduate skills and those skills needed to effectively join the workforce.
Online training courses and better engagement with SETAs and universities were identified as a step in the right direction. There was also a call for members to volunteer their time in order to share their skills, and for employers to allow members time to actively engage in WISA activities.
A call went out for legislation to be updated to meet the sector’s needs, particularly in terms of designation. It was argued that more designations are
needed to align with what is needed, both in terms of jobs and pay scale, moving forward.
infrastructure management
Building on the discussions around water quality, members unanimously agreed that government should bring back the Blue, Green and No Drop reports, in order to improve infrastructure management. These reports were not only effective monitoring mechanisms but also created interest for local politicians, resulting in more money being spent on infrastructure.
There was also a call for better collaboration between divisions, such as Finance, Management and Engineering, in order facilitate the better planning and management of infrastructure. Good leadership and management skills are essential to create an enabling environment.
This was followed by a call for a change in mindset from government to not only repair infrastructure when it is broken, but rather prioritise opex and repairs budgets, instead of focusing on new builds.
Met with agreement from those present, one WISA member called for an end to the ‘shotgun approach’, with the establishment of set targets and the creation of a centre of excellence in water management for South Africa.
Working together
Summarising the day’s discussions, Hanke-Louw addressed the need to enhance member involvement in the water sector. The general consensus was that WISA needs to make better use of its strategic partnerships and that members needed to explore how their own organisations can create synergies for the betterment of the sector.
Similarly, Dr Valerie Naidoo, WISA Board Chair, reminded members of their own personal responsibilities to encourage
WISA membership, for managers to allow staff members time to engage and advocate for WISA membership budgets, for executives to explore partnerships, and, most importantly, for all members to volunteer their time.
“Ask yourself how you engage, how you empower, and how you get people volunteering,” she said, noting that individuals, branches and divisions all have an essential role to play.
“Some of you are already sharing your time, but how do you share more of that time? How do you understand the strategic intent of WISA and share specialists within your organisations and some of their time towards some of the issues on the ground?” Naidoo asked. She also called on patron members to devote CSI budgets where possible to work with WISA branches and divisions to create high-impact projects.
“We are WISA. There is no us and them. There isn’t somebody with a silver bullet who is going to solve these issues. We are going to solve these issues together.”
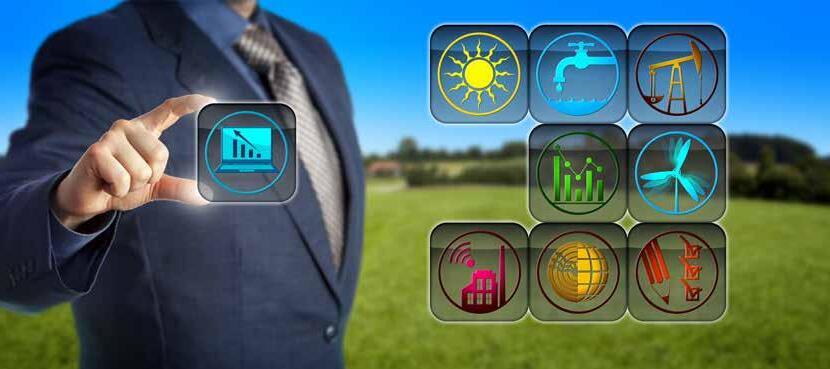
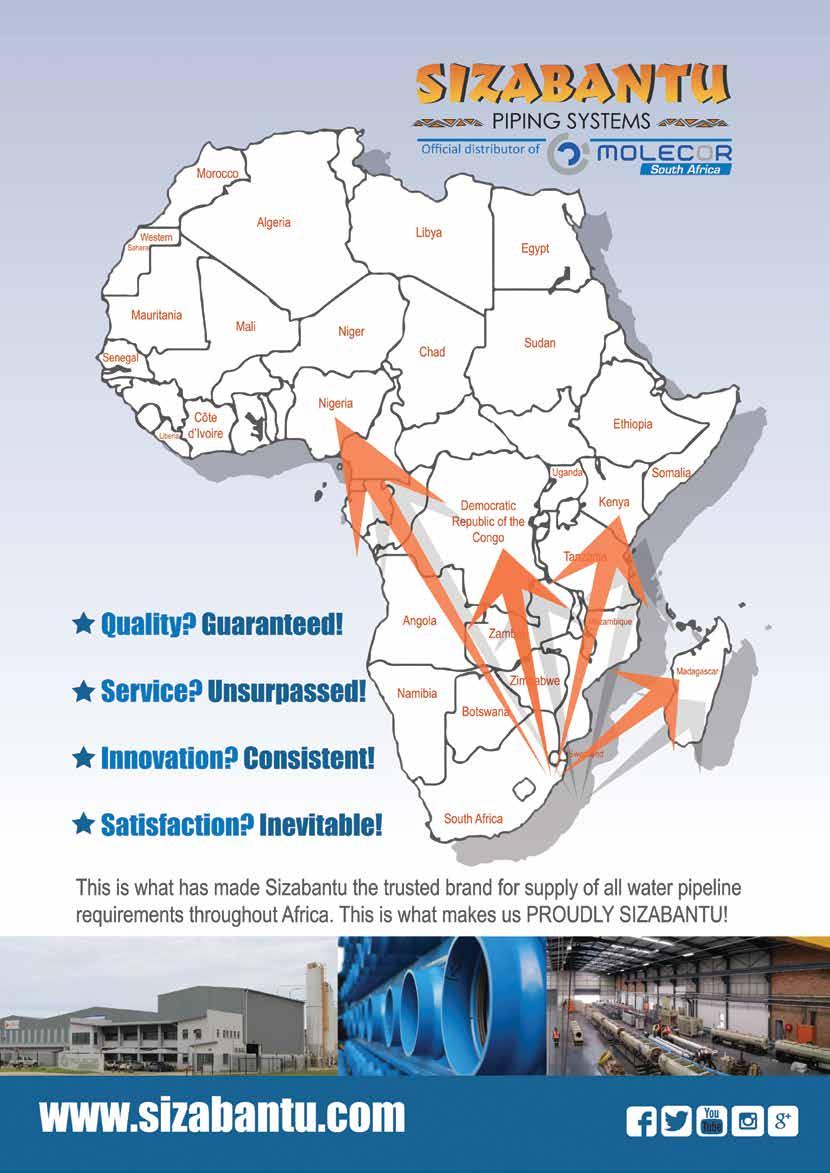
Superior
Process Control and Flexibility
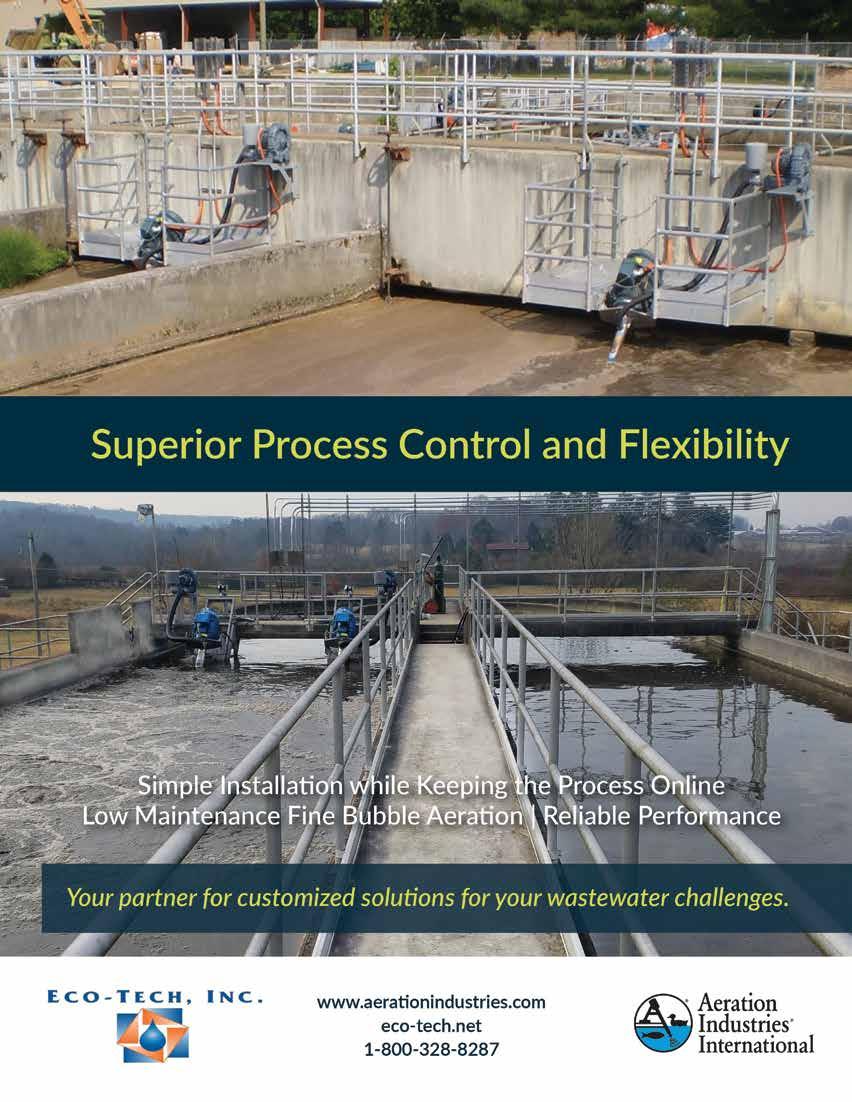
Your partner for customized solutions for your wastewater challenges.
The World’s Best Water and Waste Water Treatment Solutions


