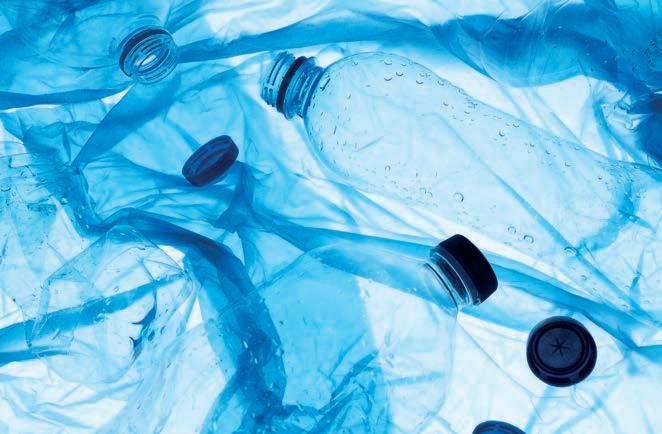
10 minute read
Depolimerizzare il PET fa bene all’economia circolare
Gli obiettivi del Green Deal europeo e di Zero net economy per il 2050 passano anche da una crescente attenzione ai processi del riciclo dei rifiuti in plastica prodotti ogni giorno in grandi quantità, come ad esempio le bottiglie e gli altri imballaggi in polietilene tereftalato. I processi di depolimerizzazione tradizionali del PET soffrono di alcune limitazioni, prime fra tutte le alte temperature di processo e la difficoltà di eliminare gli eventuali coloranti presenti. Nuovi e più efficienti processi si stanno affacciando all’orizzonte.
di Filippo Neri
Advertisement
Il riciclaggio più efficiente dei rifiuti è uno dei capisaldi delle politiche di economia circolare messe in atto negli ultimi anni dalla Commissione europea con l’obiettivo di rendere, da un lato, l’intero ciclo di vita dei prodotti più sostenibile sul piano ambientale, dall’altro dall’ottimizzare la gestione dei rifiuti, che puntano sempre più a trovare nuova vita secondo un insieme articolato di processi diversi (figura 1).
L’obiettivo della Zero net economy fissato per il 2050 dovrebbe passare anche attraverso importanti azioni sul piano del riciclaggio degli imballaggi in plastica, come delineato dalla proposta della Commissione EU di revisione della legislazione europea sul packaging e sui rifiuti da esso derivati del novembre 2022.
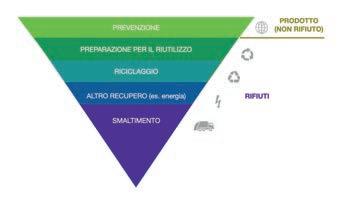
I dati dell’associazione di categoria Plastics Europe indicano in 5,5 milioni di tonnellate la quantità di plastica riciclata post consumo utilizzata per la produzione di nuovi prodotti o loro parti nel 2021, su un totale di 10 milioni ton inviate a riciclo. La plastica da economia circolare ha rappresentato nel 2021 circa il 9,8% di tutta la produzione mondiale; di questa, la componente maggiore (8,3%) era rappresentata da plastica riciclata (figura 2). A livello europeo, nello stesso anno la produzione di plastica riciclata post consumo e di quella bio-based e bio-attributed è stata, rispettivamente, del 10,1% e del 2,3% (figura 3).
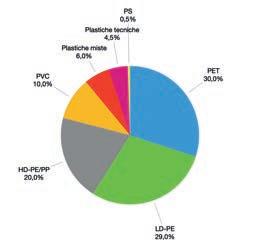
Il polietilene tereftalato (PET) rappresentava nel 2021 il 7,9% della domanda dei trasformatori di plastica (figura 4). I dati dell’associazione Plastics Recyclers Europe per il 2020 indicano che il PET conta per il 30% della capacità di riciclo della plastica installata in Europa. La Germania risulta il paese con la più elevata capacità di riciclo per questo polimero (25%), seguita da Spagna (14%), Italia (12%), Francia (10%) e Regno Unito (7%).
Il PET è uno dei polimeri più facili da riciclare in modo pressoché completo, tanto da essere l’unico caratterizzato dal codice di riciclaggio #1 per il rifiuto. Tra le caratteristiche che lo contraddistinguono, la temperatura di fusione relativamente bassa fa sì che sia possibile dargli forma più volte, dopo averlo frantumato in piccoli pezzi, lavato e decontaminato dalle sostanze estranee eventualmente presenti (riciclo meccanico).
Ma non solo. Sempre maggiore interesse vanno assumendo i processi di depolimerizzazione del PET, che permettono di rompere le catene polimeriche tornando ai mo-
Ambiente E Riciclo
nomeri che le compongono. Noto anche come “riciclo avanzato”, la depolimerizzazione è un processo più complesso del riciclo meccanico, richiede più energia, ma offre il vantaggio di poter riutilizzare i monomeri quali nuove materie prime per la produzione di tipi diversi di plastiche.
La scelta del processo dipende dalla purezza della materia prima Sebbene più semplice ed economico a causa delle minori energie in gioco, il riciclo meccanico del PET è adatto solo a rifiuti di elevata purezza. Negli altri casi, in dipendenza del grado e tipo di impurezze presenti, è più indicato ricorrere alla depolimerizzazione o, nei casi più estremi, all’utilizzo del PET quale fonte per la produzione di energia (tabella 1).
Il grado di purezza del rifiuto in PET viene determinato a livello fisico e chimico. Nel primo caso, riflette la presenza di residui macroscopici di sporco e contaminanti facilmente rimovibili o di residui microscopici più difficili da individuare e rimuovere. L’u-
I numeri del riciclo delle bottiglie in PET
• Il 58% delle bottiglie in PET sono attualmente riciclate in Europa;
• Obiettivo 2025: tutte le nuove bottiglie dovrebbero contenere almeno il 25% di PET riciclato (rPET);
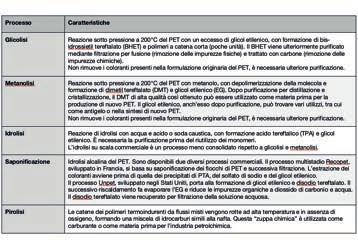
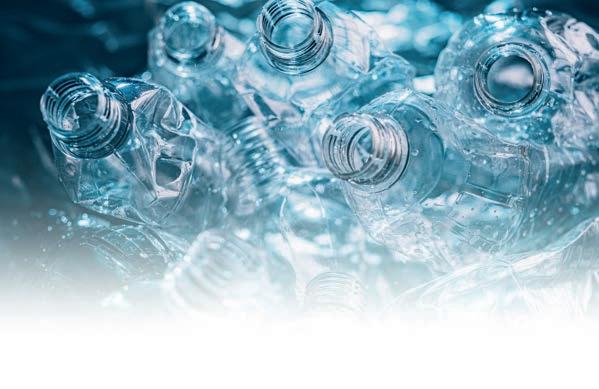
• Obiettivo 2029: nove bottiglie su dieci raccolte e riciclate;
• Capacità attuale per riciclare altri 11 miliardi di bottiglie l’anno, ma è necessario migliorare a livello di raccolta del rifiuto.
(fonte: recycletheone.com) so improprio dei contenitori vuoti in PET per conservare sostanze diverse da quella originaria può, invece, dar luogo a contaminazione di tipo chimico, con adsorbimento delle sostanze estranee all’interno della struttura polimerica.
Il riciclo di tipo chimico può avvenire secondo diversi tipi di processi, che hanno tutti in comune costi molto più elevati sia per la realizzazione degli impianti che per l’energia necessaria al processo. Anche in questo caso, la scelta del tipo di processo chimico (glicolisi, metanolisi, idrolisi, saponificazione, pirolisi sono quelli più tradizionali) dipende dal tipo di materiale di recupero disponibile per alimentarlo (ad esempio, con presenza o meno di coloranti, tabella 2).
Depolimerizzazione enzimatica
Oltre ai metodi tradizionali visti sopra, sono oggi disponibili anche nuovi processi per la depolimerizzazione del PET che puntano a garantire una maggiore sostenibilità e circolarità del ciclo di vita dei prodotti. La collaborazione tra l’azienda francese Carbios e Indorama Ventures, il principale produttore di bottiglie da PET riciclato, dovrebbe portare entro il 2026 all’attivazione del primo impianto di produzione basato sulla tecnologia di bioriciclo enzimatico.
Situato a Longlaville vicino a Clermont-Ferrand (F), e in prossimità dell’impianto Indorama–Glanzstoff, il nuovo sito è attualmente in fase di progettazione avanzata. Una prima unità dimostrativa è già attiva, e in grado di condurre in modo coordinato tutti i passaggi del processo, dal pre-trattamento dei rifiuti di PET alla produzione dei monomeri. La Reference Unit finale potrà processare fino a 50 mila tonnellate di rifiuti PET l’anno.
Carbios ha annunciato a inizio aprile 2023 la disponibilità della documentazione di licensing per la commercializzazione della sua tecnologia a livello globale (Technical Information Summary, Process Design Package e Process Book): obiettivo è concedere licenze per replicare l’impianto francese, che opererà secondo stringenti standard di Salute, Sicurezza e Ambiente (HSE).
A gennaio di quest’anno l’azienda francese ha anche siglato una partnership esclusiva di lungo periodo con Novozymes per la produzione e fornitura in scala industriale degli enzimi proprietari di Carbios da utilizzare nei nuovi impianti. Enzimi che sono stati isolati grazie a una collaborazione con il Toulouse Biotechnology Institute (TBI) e con il laboratorio cooperativo PoPLaB (Plastic Polymers and Biotechnologies), co-fondato da Carbios insieme all’ente pubblico di ricerca francese INSA. La caratterizzazione dell’enzima e del PET riciclato ottenuto a partire da esso è stata pubblicata nel 2020 su Nature (Tournier, V., Topham, C.M., Gilles, A. et al. An engineered PET depolymerase to break down and recycle plastic bottles. Nature 580, 216–219 (2020). https://doi. org/10.1038/s41586-020-2149-4). I dati indicano che la reazione di idrolisi enzimatica è in grado di degradare in sole dieci ore un minimo del 90% del PET, con una produttivi- bios è di circa 150 milioni di euro, a cui si aggiungono 50 milioni per la realizzazione delle infrastrutture; la Banca europea degli investimenti ha concesso un prestito di 30 milioni di euro, e un ulteriore supporto finanziario dovrebbe provenire dal governo francese. Una volta a regime, il nuovo impianto occuperà circa centocinquanta persone (indotto compreso). tà di 16,7 g di tereftalato/L per ora, pari a 200 g/kg di sospensione di PET.
I dati ottenuti nello scaling up del processo indicano, secondo quanto ripotato dall’azienda, risultati per la cinetica di depolimerizzazione e per la resa della reazione enzimatica simili a quelli ottenuti in laboratorio e in scala pilota. Restano ancora da ottimizzare le rese e la produttività del processo, oltre che la qualifica delle fonti di materia prima; anche i passaggi di purificazione sono ancora oggetto di messa a punto. Il principale vantaggio del metodo rispetto a quelli convenzionali è la possibilità di riciclare in modo completo tutte le tipologie di PET (anche da rifiuti tessili).
L’investimento previsto per la messa a punto della piattaforma tecnologica di Car-
Micronde per potenziare il processo d’idrolisi
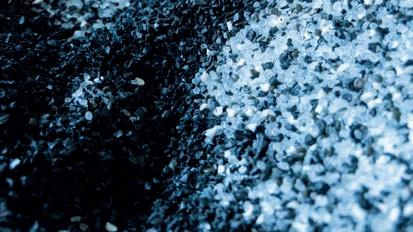
Parla svizzero, ma ha origini italiane, la tecnologia sviluppata da gr3n, azienda fondata da Maurizio Crippa che nel 2018 ha ricevuto il prestigioso premio Innovation Radar Prize della Commissione europea. Il primo prototipo dell’impianto è stato realizzato nei laboratori Labormak di Piacenza.
La piattaforma tecnologica utilizza in questo caso un sistema a microonde per velocizzare la reazione di idrolisi alcalina del PET, permettendo di lavorare a temperature minori di 200°C e portando all’ottenimento dei monomeri PTA ed EG in meno di dieci minuti (rispetto alle 3-5 ore richieste dai processi tradizionali operanti a 210250°C). Il processo, inoltre, rimuove com- pletamente dal prodotto finale le impurezze di tinture e coloranti. La circolarità del processo è supportata anche dalla reazione di elettrolisi che permette di riconvertire il cloruro di sodio (NaCl) prodotto durante la depolimerizzazione in idrossido di sodio (NaOH) e acido cloridrico (HCl), riutilizzati nei successivi cicli di reazione.
I fondi ottenuti dal premio europeo hanno permesso a gr3n di portare la Reactive Unit a microonde allo stadio TLR5 di sviluppo (“Tecnologia convalidata in ambiente (industrialmente) rilevante”). Il processo è stato ulteriormente migliorato all’interno del progetto europeo DEMETO, in cui l’azienda svizzera ha collaborato anche con NextChem per la realizzazione del primo impianto italiano per la depolimerizzazione di PET e poliesteri da tessuti (box 2). Un nuovo finanziamento del governo svizzero, infine, sta portando la piattaforma di gr3n a livello di sviluppo TLR8 (“Sistema completo e qualificato”).
Altri processi già consolidati
Ha inizio nel 2009 la storia di Ioniqa, azienda olandese nata come spin-off della Eindhoven University of Technology. Il suo primo impianto da 10 kton è stato avviato nel 2019, e può riciclare qualunque tipo di PET (compreso quello colorato) restituendo alla fine del processo monomeri di elevata qualità, utilizzabili anche per la produzione di packaging alimentare. Nel 2018 l’azienda olandese ha concluso concluso un accordo con Coca Cola Company volto a supportare lo sviluppo di tecnologie adatte a produrre PET riciclato di alto grado, da utilizzare per la produzione delle bottiglie dell’azienda di bevande, a partire da rifiuti di PET difficili da riciclare.
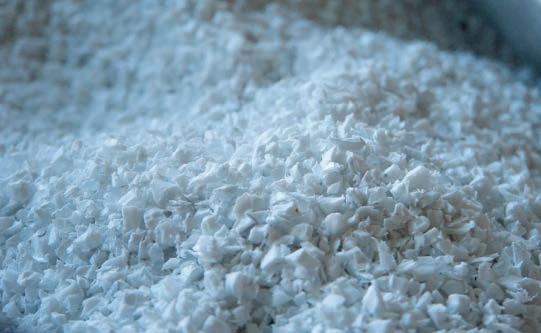
Il primo impianto dimostrativo in Italia di riciclo chimico di PET e poliestere da tessuti si trova a Chieti, nel Parco tecnologico d’Abruzzo, ed è stato aperto ad aprile 2022 da NextChem, società di Maire Tecnimont per le tecnologie per la transizione energetica. L’impianto è stato realizzato nell’ambito del progetto UE Horizon DEMETO e utilizza l’omonima tecnologia di depolimerizzazione basata sulla reazione di idrolisi alcalina con utilizzo delle microonde, di cui NextChem è co-licensor. Obiettivo è testare diverse tipologie di materiali, incluse le fibre tessili a base poliestere; l’impianto è in grado di riciclare quasi il 100% del materiale in entrata, pari a un milione di kg/anno.
(fonte: NextChem)
Anche la tecnologia messa a punto dalla canadese Loop Industries punta al riciclo completo di tutti i tipi di PET e poliestere, con l’obiettivo di costruire e dare in licenza impianti di depolimerizzazione/produzione di nuovi oggetti i PET localizzati in prossimità dei grandi centri cittadini.
Pallet in plastica riciclata per una movimentazione sostenibile
Due materiali molto diversi tra loro e, al contempo, due volti della stessa medaglia nel trasversale settore della logistica: plastica e legno, quando si parla di pallet, si contraddistinguono sempre e comunque per le loro specifiche peculiarità.
È inconfutabile che, a parità di portata, la plastica è più leggera - di conseguenza anche i camion su cui viaggia -, oltre che essere totalmente riciclabile. I pallet in plastica nestabili, inoltre, da vuoti occupano fino al 65% di spazio in meno, sia nello stoccaggio a terra che nella movimentazione. Rapportando questi dati al numero di camion e container quotidianamente in movimento, i vantaggi che derivano dal suo utilizzo diventano importanti e, soprattutto, quantificabili tramite dati oggettivi.
Dal 2010, Relicyc produce pallet in plastica 100% riciclata. Per rendere gli articoli prodotti nuovamente riciclabili e per offrire al mercato la migliore qualità, la materia prima è attentamente selezionata dall’azienda. Per tale ragione Relicyc presta massima attenzione alla fase di raccolta e macinazione, così da rendere il processo produttivo più efficiente e ottenere un prodotto di alta qualità. La filiera di recupero e lavorazione viene gestita all’interno dell’azienda per garantire un accurato controllo, massima qualità e un impatto ambientale ridotto al minimo.
I pallet in plastica prodotti da Relicyc, conosciuti con il marchio Logypal, rappresentano anche la vera alternativa al pallet in legno trattato ISPM-15, con un costo più vantaggioso, permettendo di evitare le certificazioni obbligatorie e i problemi di quantità minime ordinabili.
Leggeri, resistenti, maneggevoli, esportabili senza alcuna restrizione normativa e lavabili, i pallet in plastica Logypal non assorbono alcun liquido, non sono attacca-
14 - 15 giugno 2023
Fiere di Parma
INDUSTRIA DI PROCESSO: ARRIVA IN ITALIA L’EVENTO bili da muffe, parassiti o batteri e possono essere igienizzati con lavaggi ad alta pressione. Composti da un materiale completamente riciclato, restano inalterati nel tempo, esteticamente e strutturalmente, e mantengono un valore economico anche in caso di danneggiamento, in quanto non richiedono un costo per il recupero ma, al contrario, vengono valorizzati per poi essere completamente riciclati.
EASYFAIRS ORGANIZZA, PER LA PRIMA VOLTA IN ITALIA, L’EVENTO SOLIDS A PARMA. IN DUE GIORNI, IL 14 E IL 15 GIUGNO 2023, SARANNO MOSTRATE LE SOLUZIONI PER LA MOVIMENTAZIONE, LA LAVORAZIONE, LO STOCCAGGIO E IL TRASPORTO DI MATERIALI GRANULARI FINI E GROSSOLANI.
Un evento che per la prima volta sbarca in Italia e porta al cospetto di una filiera che abbraccia il Sud Europa le soluzioni per la movimentazione, la lavorazione, lo stoccaggio e il trasporto di materiali granulari fini e grossolani. SOLIDS Parma sarà l’evento di riferimento che avrà luogo per la prima volta presso Fiere di Parma, dal 14 al 15 giugno 2023. Organizzata da Easyfairs, già presente e consolidata in Germania, Belgio, Paesi Bassi e Polonia, la fiera farà il suo debutto in Emilia Romagna, regione strategica, sede di oltre 35.000 imprese attive nell’industria di processo.
Le anticipazioni al mercato
Saranno presenti circa 150 aziende produttrici di macchine per la movimentazione, lo stoccaggio, l’analisi e la trasformazione dei materiali a grana fine e grossolana, che mostreranno le soluzioni più innovative e anticiperanno le nuove tendenze nei seguenti settori: gomma e plastica, alimentare, agricoltura e mangimi, chimica e farmaceutica, costruzione macchinari, lavorazione dei metalli, minerario, carta e vetro, recycling.
Al momento della redazione di questo articolo, gli espositori che hanno già confermato la loro presenza sono WAM Group, Cuccolini Virto Group, Hecht Technologie, Ergomec, Steinhaus, Piovan, Agierre, Mix.
I visitatori (operatori professionali delle industrie di trasformazione) potranno toccare con mano queste tecnologie e scoprire le tendenze che guideranno l’evoluzione del settore, anche grazie a un programma di conferenze e tavole rotonde (in via di definizione).
Richiedi il tuo BIGLIETTO GRATUITO inserendo il codice 1407: https://register.visitcloud.com/survey/0bf86w4xg95y3/start?actioncode=1407&translation=2osctdwd2hreg&
SOLIDS Parma, Fiere di Parma (Pad 8), dal 14 al 15 giugno 2023!
Premium partner: