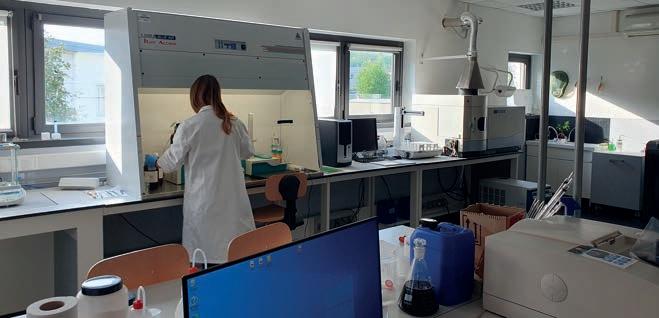
7 minute read
Il riciclo chimico che punta all’eccellenza
gr3n, che ha conquistato il mercato grazie a un efficiente processo di depolimerizzazione del PET, è riuscita, nonostante gli anni difficili, a portare avanti il suo fundraising e l’avvio nel 2023 della costruzione dell’impianto industriale.
di Eva De Vecchis
Advertisement
Èuna realtà svizzera dalle radici italiane. Si chiama gr3n ed è stata fondata da Maurizio Crippa che, nel 2018, ha ricevuto il prestigioso premio Innovation Radar Prize della Commissione europea. gr3n ha voluto portare sul mercato un efficiente processo di riciclo chimico del po- lietilene tereftalato (PET). Grazie alla sua tecnologia MADE (Microwave Assisted DEpolymerization), gr3n ha ideato e sviluppato una soluzione innovativa per chiudere il ciclo di vita del PET, fornendo vantaggi significativi sia per l’industria del riciclo, sia per l’intera filiera del poliestere.
Il processo sviluppato da gr3n scompone PET e tessuti a base poliestere nei suoi due componenti principali (i.e., acido tereftalico -TPA- e mono etilen glicole -MEG-) che possono poi essere fatti nuovamente reagire per ottenere plastiche della stessa qualità di quelle ottenute da petrolio. Si utilizza un’idrolisi alcalina che normalmente richiede 3-5 ore ma che, grazie all’utilizzo delle microonde, è possibile realizzare in 10 minuti, lavorando a meno di 200 °C.
L’obiettivo di gr3n è quello di eliminare il problema dei rifiuti plastici su base globale, considerando ogni polimero non come un ostacolo ma come una vera e propria risorsa per la produzione di nuovi monomeri e polimeri, e quindi andando nella direzione di una reale circolarità. Si tratta di un reale cambio di paradigma: utilizzare quello che al momento è considerato un problema come fonte di materie prime, andando anche a ridurre il consumo energetico e le emissioni di CO2 necessarie per ottenere l’acido tereftalico e il glicole monoetilenico. Progettando processi che utilizzano la plastica post-consumo e post-industriale come materia prima si riduce in modo significativo l’utilizzo del petrolio e permette di spostarsi da una economia lineare ad una circolare. Un percorso coraggioso, che ha richiesto anni di sviluppo e l’acquisizione di nuove conoscenze, perché il “valore aggiunto di quello che facciamo risiede proprio nella possibilità di imparare continuamente”, dice Maurizio Crippa, CEO e fondatore di gr3n, che ci spiega come stanno andando le cose.
Come si sono evoluti questi ultimi anni per gr3n?
“Sono stati senz’altro anni pieni di soddisfazioni e successi ma anche molto impegnativi, perché fare cose nuove prevede anche una certa dose di fallimenti. E se da una parte fallire significa crescere e imparare, dall’altra parte significa vedere il proprio obiettivo allontanarsi. Noi facciamo chimica pesante, quella chimica di processo che vuole produrre commodity partendo dalla spazzatura, per dirla senza grossi giri di parole. Questo processo richiede molti capitali e molto tempo e, storicamente, non veniva fatto dalle startup ma dalle grandi aziende chimiche attraverso reparti di ricerca e sviluppo strutturati. Stiamo facendo una cosa non comune dunque, ma l’aspetto positivo è che non sia- mo gli unici: insieme a noi ci sono i nostri competitors che, pur lavorando su processi e tecnologie diverse, combattono le nostre stesse battaglie, ovvero raccogliere consensi e reperire capitali sapendo che i risultati arriveranno in futuro. Qualcosa di simile lo si è visto nel mondo farmaceutico: richiedendo questo comparto grandi capitali e tempi di sviluppo molto lunghi, la ricerca e l’innovazione è stata per molti decenni appannaggio delle grandi società. Poi le cose sono cambiate, soprattutto con l’avvento delle biotecnologie: a quel punto le startup hanno cominciato a fare la vera ricerca e sviluppo e le grandi aziende farmaceutiche hanno finanziato/acquisito le startup più promettenti, interessanti, innovative. Sono le piccole realtà come la nostra, adesso, a segnare la strada e a portare avanti questo modo di approcciare ricerca e innovazione. Per quanto riguarda i progetti, dopo aver goduto di due progetti europei come SYMBIOPTIMA prima e DEMETO poi (www.demeto. eu) che ci hanno permesso di fare l’impianto pilota e il demo, abbiamo portato avanti il nostro fundraising. Abbiamo raccolto 7 milioni e mezzo di euro da quattro investitori esteri: un gruppo di investitori privati norvegesi, Standex International, un’azienda americana che si occupa di automotive e che porta avanti un progetto speciale sul poliestere, Intecsa Industrial, un EPC contractor spagnolo che fa parte dell’enorme gruppo francese Vinci e Chevron Technology Ventures, che ha investito in noi con molta lungimiranza. Grazie a questi finanziamenti, stiamo andando avanti nel nostro sviluppo: per l’estate avremo pronto il basic engineering dell’impianto industriale e da lì saremo pronti per realizzarlo”.
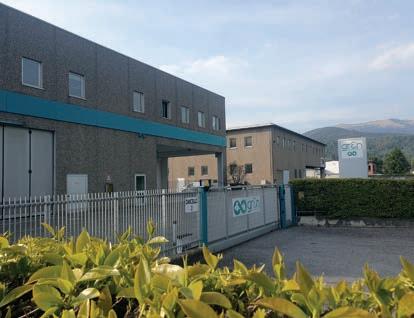
Siete riusciti a portare avanti tutto questo nonostante le difficoltà degli ultimi anni?
“Abbiamo chiuso un fundraising in pieno Covid, quindi direi di sì. Per la fine di quest’anno stiamo già preparando un round B, altra fase di un tipico percorso da startup. Certo, ormai siamo una realtà di 18 persone e ci stiamo evolvendo, abbiamo analizzato le scelte tecniche fatte fino ad ora e in molti casi le abbiamo migliorate, abbiamo un R&D in Italia con laboratori, impianto pilota e un impianto più grande che stiamo costruendo per sostenere il business. Oltre a questo, abbiamo qualificato il polimero con vari brand sia del modo packaging che del mondo tessile. A livello di ricerca e sviluppo sono ormai quasi due anni che lavoriamo principalmente per il tessile: ci siamo resi conto che a livello di reazione e purificazione il packaging presenta meno complessità e dopo tanti test sull’impianto pilota abbiamo capito che non stavamo più imparando, quando invece il valore aggiunto di quello che facciamo è proprio la possibilità di evolverci continuamente. Il tessile ci permette di farlo e, ad oggi, abbiamo già lavorato più di 200 diversi materiali e validato un processo estremamente robusto nei confronti dei contaminanti: immaginate quanti ce ne possano essere, per esempio, dentro una giacca in poliestere”.
Quindi continuerete a concentrarvi sul tessile?
Ogni anno nel mondo vengono prodotte all’incirca 90 milioni di tonnellate di poliestere; di queste, 30 milioni vanno nel packaging e 60 milioni confluiscono nel tessile. Inoltre, di questi 60 milioni, circa 30 milioni sono destinati al fashion, quindi si tratta di vestiti, mentre gli altri 30 milioni sono tutti filati utilizzati per le più svariate applicazioni (auto, divani, agende, tappeti, zaini, ecc.). Il packaging viene già, seppur in minima parte, trattato dai riciclatori meccanici e risulta essere di grande interesse anche per i nostri competitors, proprio per le minori complessità a cui facevo riferimento. Siamo in grado di trattare ogni tipo di imballaggio ma vista la nostra capacità di eliminare i contaminanti anche in materiali con composizioni diverse, riteniamo che il tessile sia un ambito in cui possiamo dire la nostra”.
Tra i vari progetti c’è anche la vostra piattaforma P-Turn. Ci può spiegare meglio come funziona?
“P-Turn risponde a un problema annoso. In Italia e in altri paesi le aziende che si occupano di raccogliere e separare i diversi tipi di rifiuto si dedicano principalmente alle bottiglie post-consumer di poliestere che, essendo il polimero più riciclato, si basa su una catena del valore consolidata. Volendo entrare nello specifico, in Italia il riciclatore meccanico si rivolge direttamente al Corepla (Consorzio Nazionale per la raccolta, il riciclo e il recupero degli imballaggi in plastica),
L’obiettivo di gr3n è quello di eliminare il problema dei rifiuti plastici su base globale, considerando ogni polimero non come un ostacolo ma come una vera e propria risorsa compra le bottiglie e le riceve in balle presso l’impianto di riciclo.
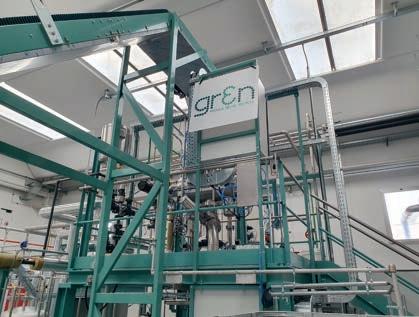
Oltre alle bottiglie esistono anche altri tipi di rifiuti con un alto contenuto di poliestere (e.g., scarti di filato, cimose di produzione dei tessuti, scarto derivante dal processo di riciclo meccanico, ecc.) ma, quando si parla di altri materiali, non c’è niente di strutturato e la situazione si complica. Questo materiale, oggi, non ha possibilità di rientrare nel ciclo produttivo ed è destinato al termovalorizzatore, in cui si recupera la porzione energetica ma non il materiale in sé.
Per questo abbiamo creato la piattaforma P-Turn, per tracciare questi scarti e raccogliere informazioni sul tipo di materiale, dove si trova, qual è la composizione, ecc. P-Turn è solo il mezzo con cui gr3n porta avanti un programma che parte dalla mappatura del mercato fino ad arrivare al contatto diretto con il potenziale fornitore, e al relativo contratto di fornitura. Il programma ha avuto un successo incredibile: siamo arrivati ad avere identificato 200.000 tonnellate, sia in Europa che nel bacino del Mediterraneo. Si tratta di materiale che oggi è destinato, nella migliore delle ipotesi, al termovalorizzatore e, in quella peggiore, alla discarica ma che, con l’impianto industriale cominceremo invece a processare e a rimettere sul mercato come polimero vergine”.
Nonostante le sue qualità, il riciclo meccanico produce materiali con proprietà effettivamente inferiori, rispetto al riciclo chimico, che invece riporta all’origine. Per questo si parla di “downcycling” per il ciclo meccanico: cosa lo differenzia dal processo di “upcycling” impiegato da gr3n e quali sono i vantaggi?
“Il riciclo meccanico prende una bottiglietta di PET, la lava, separa i diversi materiali presenti nell’oggetto (il tappo e l’etichetta sono di plastiche diverse, il primo in polietilene la seconda molto spesso in polipropilene) e poi macina il solo PET producendo fiocchi di plastica che diventano nuova materia prima per realizzare altri oggetti. I coloranti e tutto ciò che si trova all’interno del polimero non vengono però rimossi e, inevitabilmente, si ritroveranno nel prodotto finale.
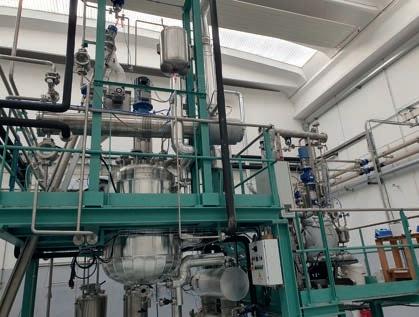
Questo porta quindi a un prodotto con proprietà inferiori rispetto a quello iniziale; per questo, storicamente, il prodotto del riciclo meccanico andava a fare il filato, oppure veniva utilizzato per applicazioni dove la richiesta qualitativa in termini di trasparenza, colore e proprietà meccaniche erano lievemente inferiori rispetto alla bottiglia d’origine. Questo accade perché c’è un’idrolisi delle cate- ne, quindi un accorciamento delle catene polimeriche e, per questo, le proprietà meccaniche subiscono un lieve abbassamento. Quello che facciamo noi di gr3n, invece, è di tagliare le catene polimeriche e separare i monomeri che compongono il polimero, così da togliere anche tutti i contaminanti a livello molecolare; successivamente, prendiamo i monomeri ormai vergini, identici a quelli che arrivano dal petrolio, e realizziamo un nuovo polimero. Il prodotto del nostro processo non è quindi un PET riciclato, ma un polimero in tutto e per tutto identico a quello originale ma ottenuto da monomeri riciclati”.
Avete progetti per il prossimo futuro?
“Nel corso di questo 2023 e quindi nel breve periodo, l’obiettivo è quello di lavorare con i grandi marchi per dimostrare come MADE non sia solo un processo molto innovativo, ma qualcosa che permette di inserire sul mercato nuovi prodotti partendo da materiale post-consumo e post-industriale. Stiamo lavorando con diversi partner e su diverse applicazioni, proprio perché il PET che otteniamo con il nostro processo ha le stesse proprietà di quello ottenuto dal petrolio. Il 2023 sarà anche l’anno in cui lanceremo la costruzione del primo impianto industriale basato sulla nostra tecnologia, un passo importante per il futuro di gr3n e del riciclo chimico in generale. Ma, come detto, siamo anche una azienda che fa ricerca e sviluppo, perciò nel medio-lungo periodo valuteremo come la nostra tecnologia possa essere trasferita ad altri polimeri e cosa sia possibile recuperare da tutto ciò che non è poliestere”.