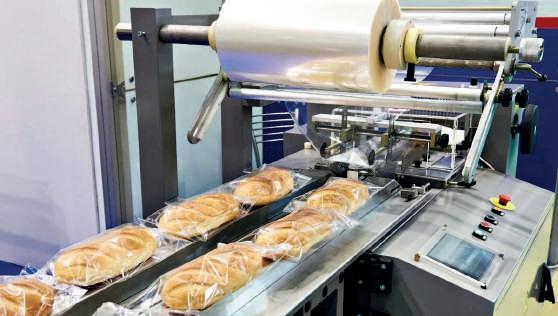
2 minute read
RIDURRE LE EMISSIONI NELLA PRODUZIONE DI CONTENITORI IN VETRO
Air Liquide implementerà una soluzione su misura per ridurre le emissioni di CO2 e il consumo di energia per Verallia, leader europeo e terzo produttore mondiale di imballaggi in vetro per bevande e prodotti alimentari. Grazie alla sua capacità di innovazione e al suo knowhow, il Gruppo supporterà la conversione dell’impianto di Verallia a Pescia (Pistoia) da un processo di combustione tradizionale a un’ossicombustione ottimizzata, in occasione della costruzione sul sito di un nuovo forno.
Nell’ambito di un contratto a lungo termine, il Gruppo costruirà e gestirà per Verallia un’unità produttiva di ossigeno di nuova generazione nel sito di Pescia. La soluzione sviluppata combina la fornitura di ossigeno e il riutilizzo del calore derivante dal processo di produzione. L’ossigeno prodotto dall’unità installata da Air Liquide andrà a sostituire l’aria immessa nel forno, permettendo così di fondere il vetro per ossicombustione e di migliorare l’efficienza del processo.
Advertisement
Inoltre, Air Liquide fornirà la tecnologia proprietaria HeatOxTM per recuperare il calore emesso dal forno al fine di ridurre ulteriormente la quantità di energia necessaria per produrre il vetro.
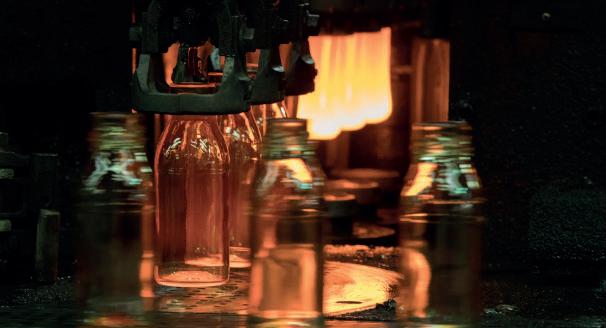
La soluzione fornita da Air Liquide contribuirà in modo significativo alla riduzione del 18% delle emissioni di CO2 (Scope 1 e 2) che Verallia si prefigge per la fornace di Pescia. Inoltre, l’unità produttiva di ossigeno di nuova generazione che sarà costruita e gestita da Air Liquide sarà dotata di un processo criogenico unico al mondo e avrà un’efficienza energetica superiore del 10% rispetto alla generazione precedente. La produzione di ossigeno sul posto eviterà inoltre la necessità di trasporto in forma liquida tramite camion.
“Questa partnership consentirà a Verallia di ridurre sia il consumo energetico che l’impronta ambientale della sua produzione di vetro a Pescia”, dichiara Matthieu Giard, vice president e membro del comitato esecutivo del
Gruppo Air Liquide, che supervisiona in particolare la business line Industrial Merchant. “Attraverso la conoscenza dei processi produttivi dei clienti, siamo in grado di combinare diverse innovazioni per sviluppare soluzioni su misura insieme a loro. Questa collaborazione risponde agli obiettivi del nostro piano strategico Advance, che mira a raggiungere la neutralità del carbonio entro il 2050 supportando le aziende nel loro processo di decarbonizzazione”.
Il Gruppo Argos ST, che dal 2020 unisce diverse importanti realtà nel panorama dei trattamenti industriali e dei rivestimenti superficiali, ha studiato e realizzato un innovativo rivestimento in politetrafluoroetilene (PTFE) caratterizzato da tre strati che, nella fase di chiusura dei sacchetti tubolari in polietilene (PE), permette di evitare che la pellicola si incolli alle guide di saldatura, risolvendo un problema che causa fermi macchina e conseguenti ritardi e rallentamenti nella produzione. I sacchetti in PE sono largamente utilizzati in diverse filiere, tra cui quella degli imballaggi e quella alimentare, in quanto consentono di proteggere la merce dall’umidità e dall’aria. Durante la produzione, ogni sacchetto viene riempito e sigillato tramite un saldatore per pellicole. L’innovativo rivestimento viene applicato direttamente sulla macchina, nello specifico sulla superficie delle barre saldanti, attraverso uno speciale processo di verniciatura e un successivo passaggio in forno a una temperatura di circa 400°C, per permetterne la polimerizzazione.
Sono numerosi i vantaggi che il rinforzo a tre strati porta al rivestimento. Prima tra tutti l’aumentata resistenza all’usura e all’alta temperatura di esercizio (fino a 260-280°C), poi l’elevata anti-aderenza, che garantisce una facile pulizia, un’alta produttività delle macchine e un’elevata qualità del prodotto finito e, da ultimo, la grande scorrevolezza superficiale del prodotto a contatto con la superficie trattata. Inoltre, il polimero in PTFE rinforzato a tre strati può essere associato a uno strato di ancoraggio in metallo duro, deposto tramite termospruzzatura, in grado di migliorarne la durezza e la resistenza all’usura.
“Grazie alla lunga esperienza e allo studio approfondito dei processi e dei trattamenti, puntiamo a fornire il rivestimento più idoneo a soddisfare le specifiche esigenze del cliente, sviluppando anche, se necessario, nuove formulazioni di rivestimenti antiaderenti personalizzati”, afferma Carlo Bruno, responsabile di produzione dello stabilimento Argos ST di Origgio (VA).