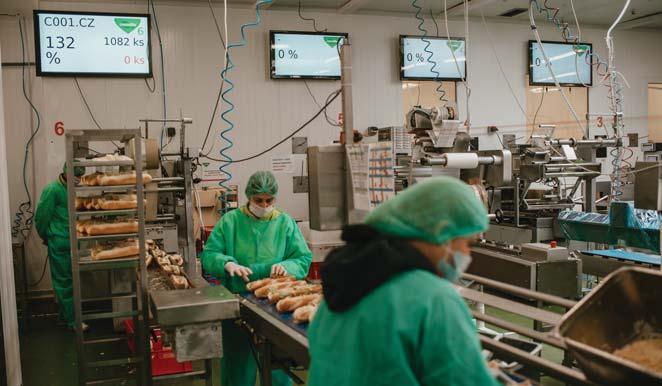
3 minute read
Čísla na obrazovkách motivujú zamestnancov. Problémy sa riešia hneď
DIGITALIZÁCIA V DODÁVATEĽSKOM REŤAZCI
ČÍSLA NA OBRAZOVKÁCH MOTIVUJÚ ZAMESTNANCOV. PROBLÉMY SA RIEŠIA HNEĎ
Advertisement
Vari každý pozná bagety Crocodille, či už balené, alebo čerstvo pripravené v sieti bagetérií Boulevard. Niet divu. Spoločnosť Crocodille ich ročne vyrobí 35 miliónov kusov. Balené bagety sa vyrábajú v závode v Žiželicích nad Cidlinou. Zvyšujúce sa personálne náklady prinútili manažment hľadať riešenie, ktoré by výrobu zefektívnilo.
Potrebný bol hlavne monitoring výrobných procesov, ktorý mal zároveň motivovať zamestnancov k vyššiemu výkonu a zvyšovať ich ochotu na zmeny. Spoločnosť Crocodille nechcela žiadnu univerzálnu službu, ale systém, ktorý bude presne zodpovedať podmienkam a potrebám jej kvalite, a pracujú podľa toho. Potvrdzuje to riaditeľ výrobného závodu v Žiželicích nad Cidlinou Ing. Pavel Kittner: „Ako najväčší prínos riešenia od Plantystu vidím prepojenie skutočne odvedenej práce so mzdou. Ľudia u nás si uvedomujú, že keď pracujú starostlivo a s chuťou, odráža sa to v ich odmene. Tiež sa už nesnažia maskovať problémy, ale sami prichádzajú s návrhmi, ako ich riešiť alebo im predchádzať.“
Monitoring výrobných liniek vykonáva Plantyst pomocou špeciálnych optických senzorov a na zber dát stačí pripojiť k linke malú čiernu škatuľku. Získané dáta systém odosiela nepretržite na
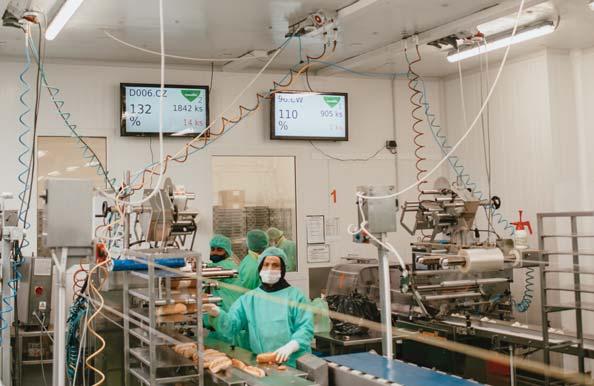
výroby. Hľadané riešenie malo byť navyše cenovo prijateľné a rozšíriteľné. Týmto požiadavkám dokázala vyhovieť fi rma Plantyst pomocou svojho riešenia Plantyst IoT Gateway. Firme Crocodille sa investícia vyplatila – vrátila sa jej za iba 3 mesiace a priniesla ročné úspory 17 miliónov českých korún. Pre zamestnancov závodu to znamenalo zvýšenie miezd o 10 – 15 %, a to bez navýšenia celkových mzdových nákladov.
PROBLÉMY VIDIEŤ SKÔR AKO NA KONCI LINKY
Predstavme si, ako vyzerá príprava balených bagiet – ich plnenie a balenie. V hale závodu funguje niekoľko výrobných liniek. Sú to dlhé pulty, na ktorých začiatku sa rozreže bageta, ktorú pás posúva k ďalším jednotlivým zamestnancom. Tí podľa vopred daného postupu plnia bagety jednotlivými ingredienciami. Na konci linky sa bagety počítajú a kontrolujú, aby sme ich my zákazníci dostali v kvalite, akú očakávame. Ak nie je nejaký výrobok v poriadku, musí sa vrátiť a upraviť. Okrem kontroly kvality je tiež potrebné dať včas kolegom vedieť, že už je napríklad hotový požadovaný počet klobásových bagiet a je čas prejsť na iný druh bagety. Predtým táto komunikácia narážala na rôzne limity od
jazykovej bariéry po priestorové usporiadanie linky. Pracovník na konci 13 metrov dlhého pultu nemohol vo chvíli, keď výrobky triedil, presne vedieť, koľko bagiet majú kolegovia ešte rozpracovaných ani či sú pripravené bezchybne. Ak niekto na niečo zabudol alebo urobil ledabolo, nešlo dohľadať, kto sa chyby dopustil. Chybovosť sa dala vyhodnocovať len spätne.
OKAMŽITÝ PREHĽAD ZVYŠUJE MOTIVÁCIU ZAMESTNANCOV
Teraz majú pracovníci aj majstri informácie v reálnom čase. Všetko sa ukazuje na obrazovke pri výrobných linkách. Pracovníci tak majú možnosť priamo pri práci sledovať, koľko a aké druhy bagiet naplnili, ako dlho im to trvá, ako sa im darí plniť plán zmeny. Rovnako tak majú prehľad o nekvalitných produktoch, ktoré je potrebné upraviť. Táto zmena výrazne zmenila myslenie zamestnancov. Pochopili, že sú odmeňovaní len za výrobky v stopercentnej spracovanie do cloudového prostredia Microsoft Azure a potom sa zobrazujú pomocou služby Power BI na obrazovke pri každej linke. Z dát, samozrejme, vznikajú reporty za jednotlivé dni alebo iné sledované obdobie. Je možné z nich prehľadne vyčítať, aké sú výsledky jednotlivých zmien, výrobných skupín alebo ako náročné na prípravu sú jednotlivé druhy bagiet. Nechýba ani súhrn prestojov vo výrobe alebo dôvody zastavenia liniek či informácie o povinných prestávkach. Manažment má skvelé podklady pre plánovanie zmien a ďalšie optimalizácie procesov alebo napríklad pre budúce investície do automatizácie.
Za prvý rok používania riešenia Plantyst IoT Gateway vzrástla efektivita závodu o 15 %. Prestoje liniek pri údržbe klesli o 70 % a chybovosť výroby sa znížila z 3,2 na 1 %. Riešenie má teraz spoločnosť Crocodille nasadené na šiestich výrobných linkách a v pláne je rozšírenie na ďalšie štyri.