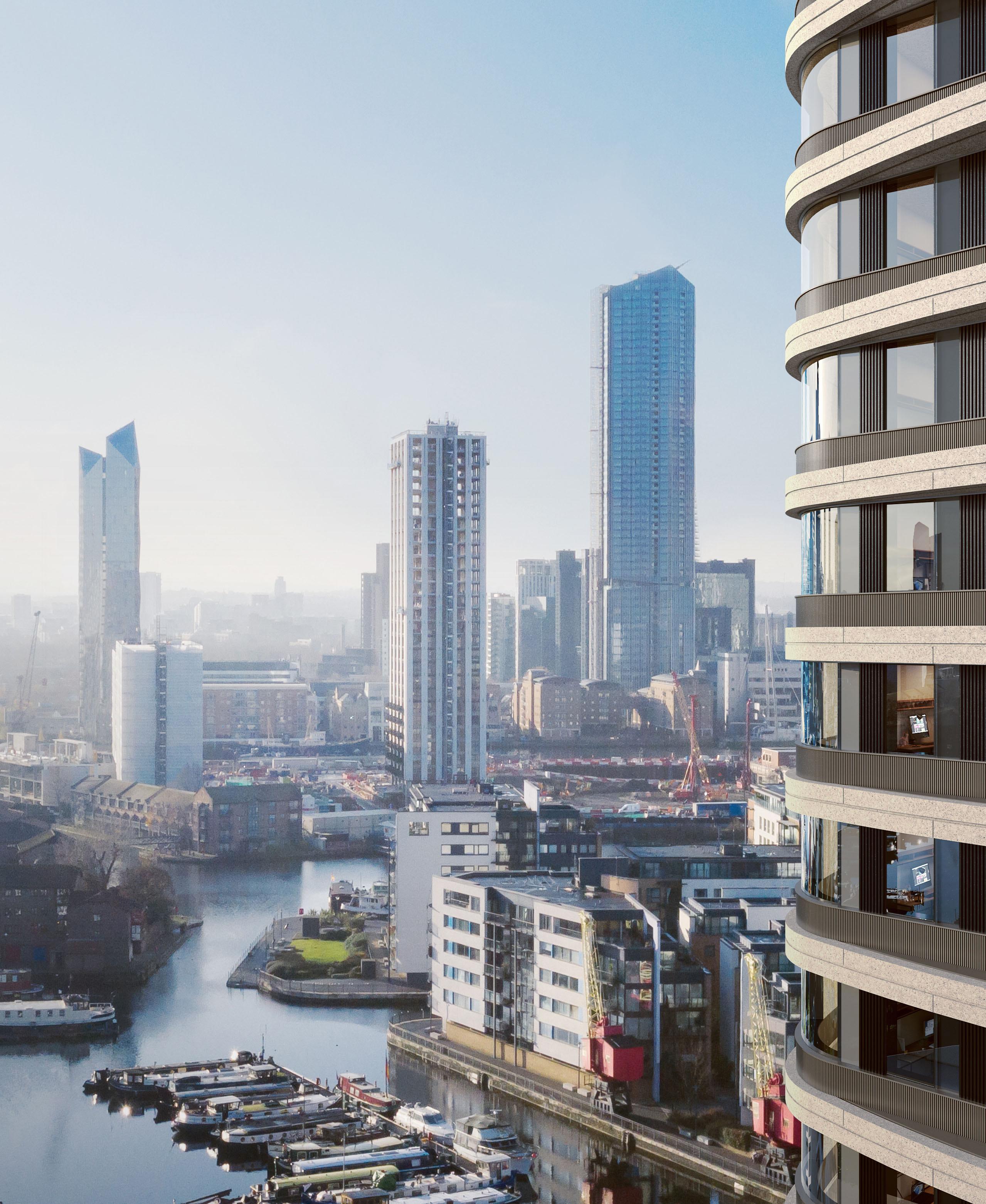
18 minute read
CARBON-LED FAÇADE DESIGN Gianluca Rapone - Associate and Sustainability Lead, FMDC
Carbon-led Façade Design
Gianluca Rapone, Associate and Sustainability Lead at FMDC, envisions what it will take to design façades with carbon saving as the main driver
Advertisement
Cultural shifts
By now we should all be aware of the crucial role the construction industry plays in reducing global carbon emissions; it is also obvious that it is naïve to think that everything can be solved merely with technical innovation and engineering optimisation. The whole industry will need to change radically if we want to come even close to achieving the carbon reductions required to keep global temperatures within the critical 1.5°C rise advised by the IPCC. We should expect shifts in clients’ expectations and in public perception, new economic and business models, a deep re-think of the way we design, procure, build, occupy, and decommission buildings. Essentially a change of culture in the world of architecture and construction which will involve pretty much every aspect.
2 Trafalgar Way is a mixed-use development in East London designed by APT Architects. It was designed to minimise energy demand and consumption as it aims to become the largest PassivHaus certified building in Europe. However, there were no embodied carbon targets for the project. (CGIs courtesy of APT Architects, under permission by Urbanest)
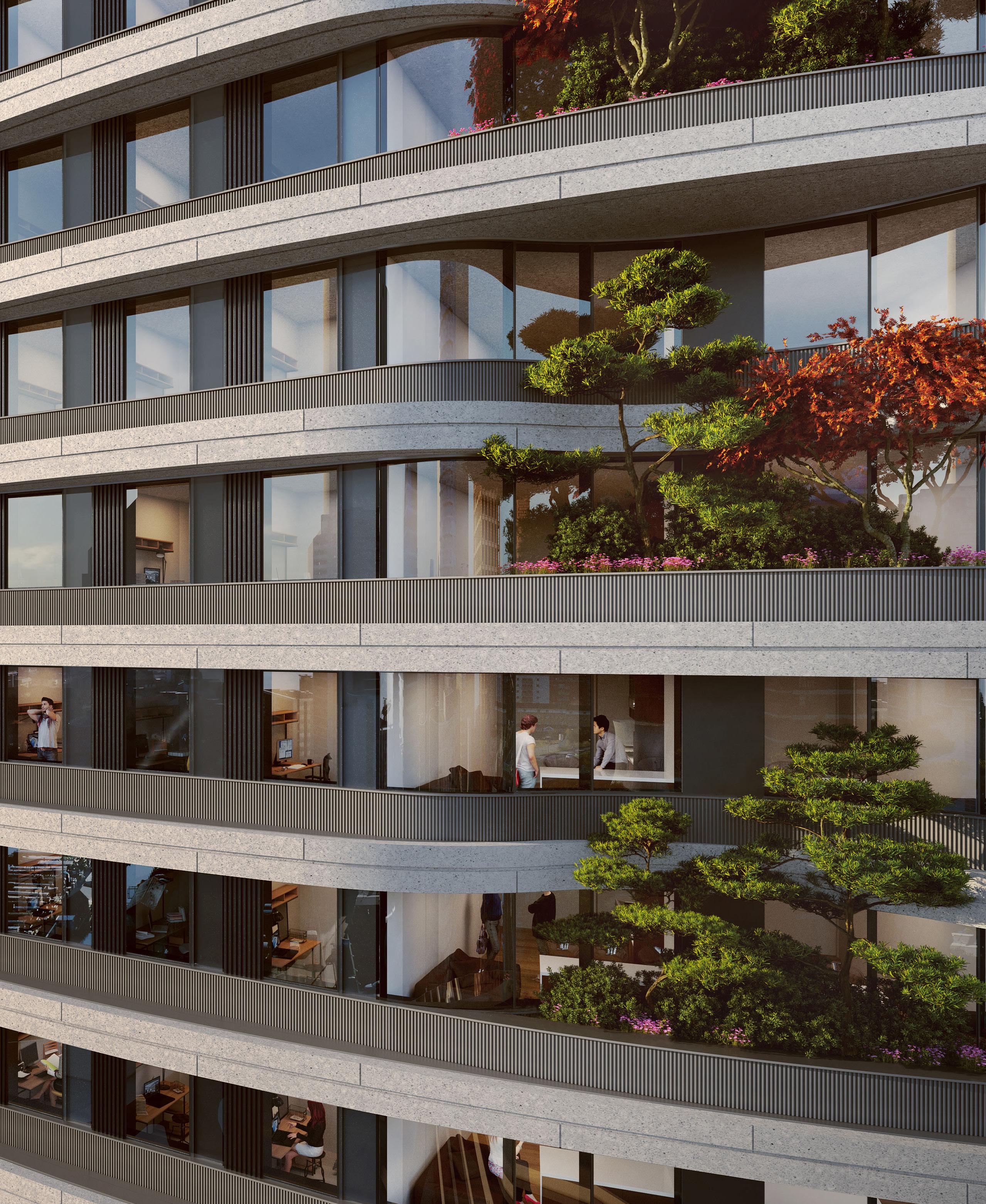
Although I consider such broader matters crucial, the remit of this article is limited to exploring the changes that I believe are required in the façade construction process, from design to procurement, from manufacturing to maintenance, all the way to end of life. Several publications by institutions like the UKGBC and LETI have informed us on the likely technical characteristics of ‘net zero’ buildings. Furthermore, comprehensive research has highlighted the need for circularity in the construction industry. The façade is put under enormous pressure by all these targets, from both operational energy and embodied carbon perspectives. A ‘business as usual’ approach, even if improved, will not deliver the necessary savings. We need to question every choice we used to make with the old model, and adopt a new attitude where carbon is at the centre of every decision.
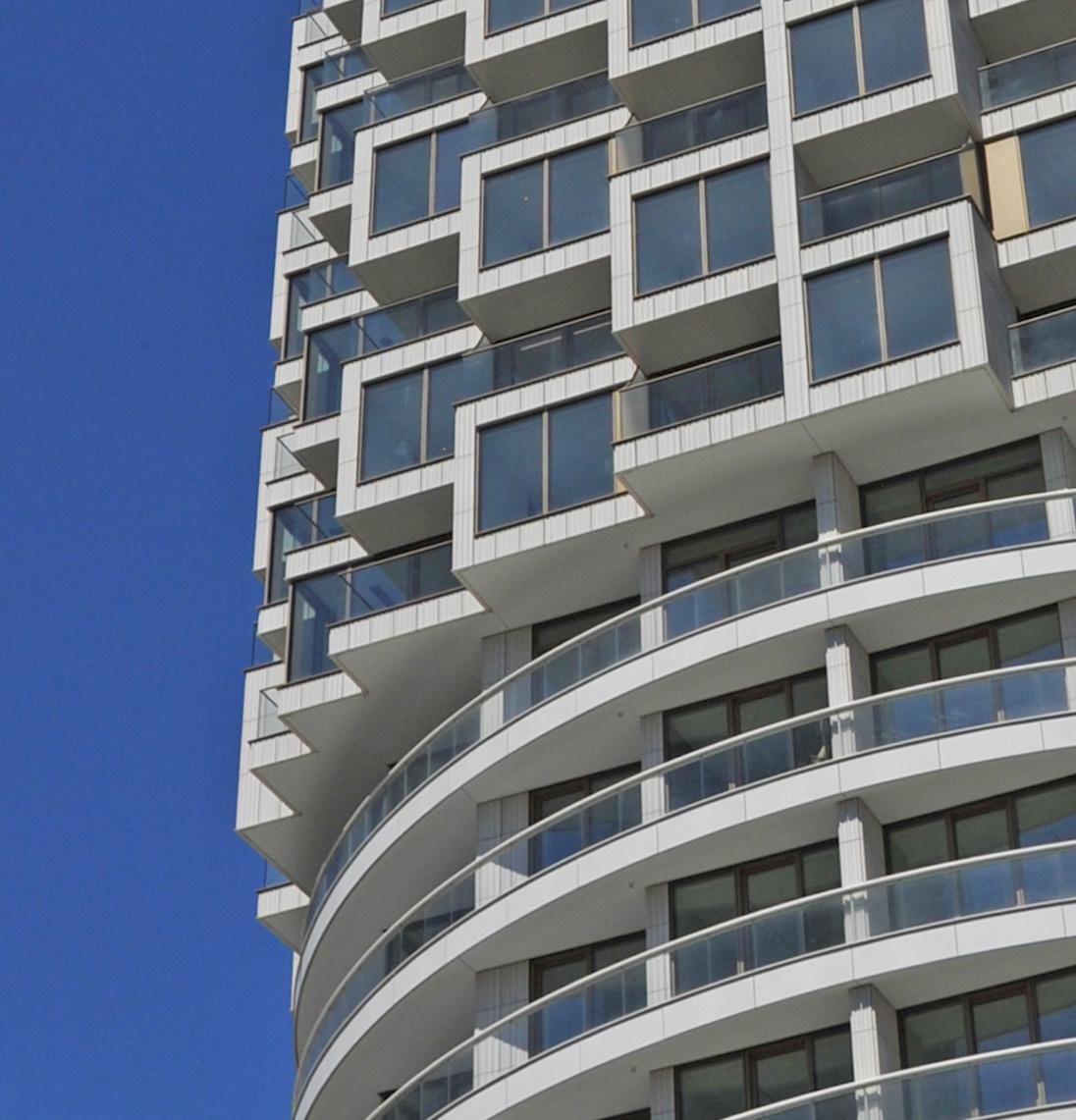
Design for real performance
The role of the façade in reducing operational carbon is inevitably interconnected with the wider approach to a building’s energy efficiency. Regulating energy demand via passive or active measures, while ensuring that the occupants’ thermal and visual comfort can be achieved is a subtle balance of conflicting requirements and inter-dependent factors.
One Park Drive © Paul Scott
Upfront embodied carbon of typical façade designs compared to present and future targets, for commercial and residential buildings. Significant reductions will be required.
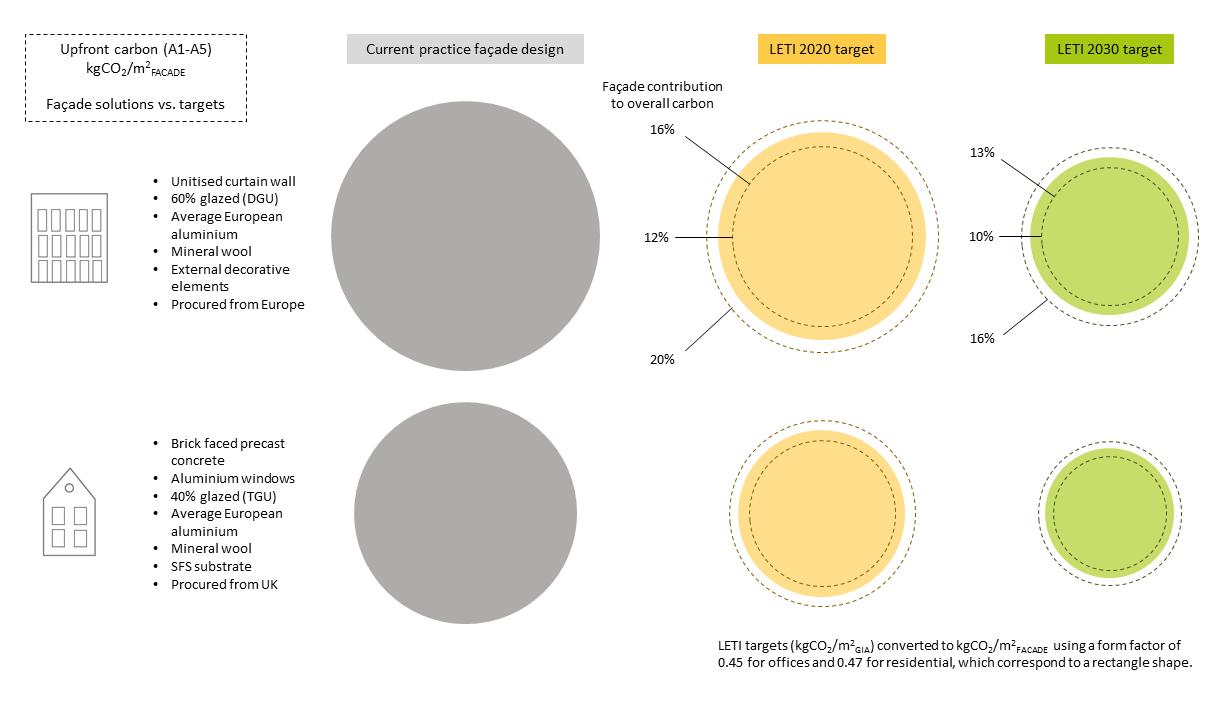
One Park Drive in Canary Wharf is an elegantly designed residential tower by Herzog & DeMeuron, boasting white fluted terracotta tiles on unitised curtail wall. The lively articulation of the façades is its most distinguished feature; however, it also means that the form factor is not as good as it could be for a circular floorplate. When designing low-carbon buildings, building shape will be an important aspect to consider. © Paul Scott Over the years, finding the appropriate solution to this problem has somehow strayed from its natural path due to what can be called ‘compliance culture’. The objective has not been to achieve the best possible performance as a whole, but instead to make sure single components comply with the relevant standards and with ‘box ticking’ environmental targets, whilst safeguarding architectural appearance. This however is finally changing in favour of a ‘design for performance’ approach, promoted by strict energy intensity targets for ‘net zero’ buildings, and by the adoption of performance-based rating schemes such as NABERS. In this context, we have the opportunity to go back to the drawing board and re-think every aspect of building design to enable the required energy savings.
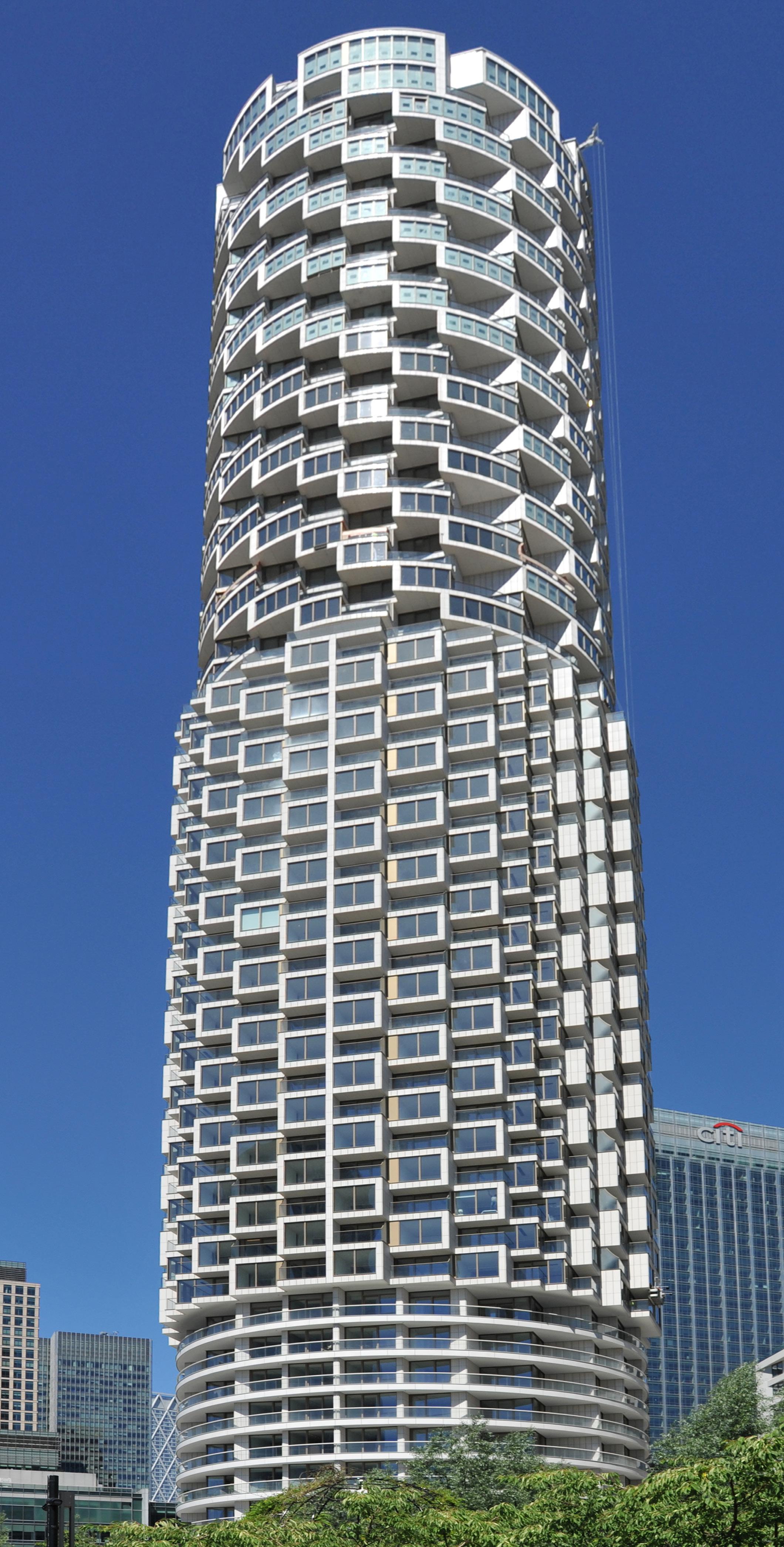
Basic architectural factors, such as early-stage massing, orientation and glazing percentage can have a significant influence on heating and cooling demand. The building ‘Form Factor’ governs the heat loss area, which in turn determines how hard the façade will need to work to achieve the heating demand target. Simply put: the most compact the building, the higher the heat retention, the less pressure on thermal performance of the envelope. Architects have the opportunity to set a project on the right path from the start, especially because an efficient form factor is also key for the façade embodied carbon budget, as we will observe in the next section.
When it comes to cooling loads and overheating, the matter becomes more intricate. The role of façades as ‘filters’ is a concept that has been around for centuries. Its modern interpretation is rooted in the technological developments of the midlate XX century, when increasingly complex solutions were introduced, mainly to control solar gains and daylight. Dynamic shading solutions can vary from simple (reflective blinds) to extremely advanced (DSF or CCF); although they are undoubtedly more efficient than static ones, very complex systems can add capital cost, maintenance needs, and embodied carbon. The aim on every project should always be to use to the simplest possible category that allows requirements to be met. This hasn’t always been the case in contemporary commercial buildings.
Farringdon East is a commercial building designed by PLP, with floor to ceiling glass and brightly coloured terracotta tiles. Future offices will likely need to reconsider the amount and configuration of glazing to achieve stricter U-value targets. © Paul Scott

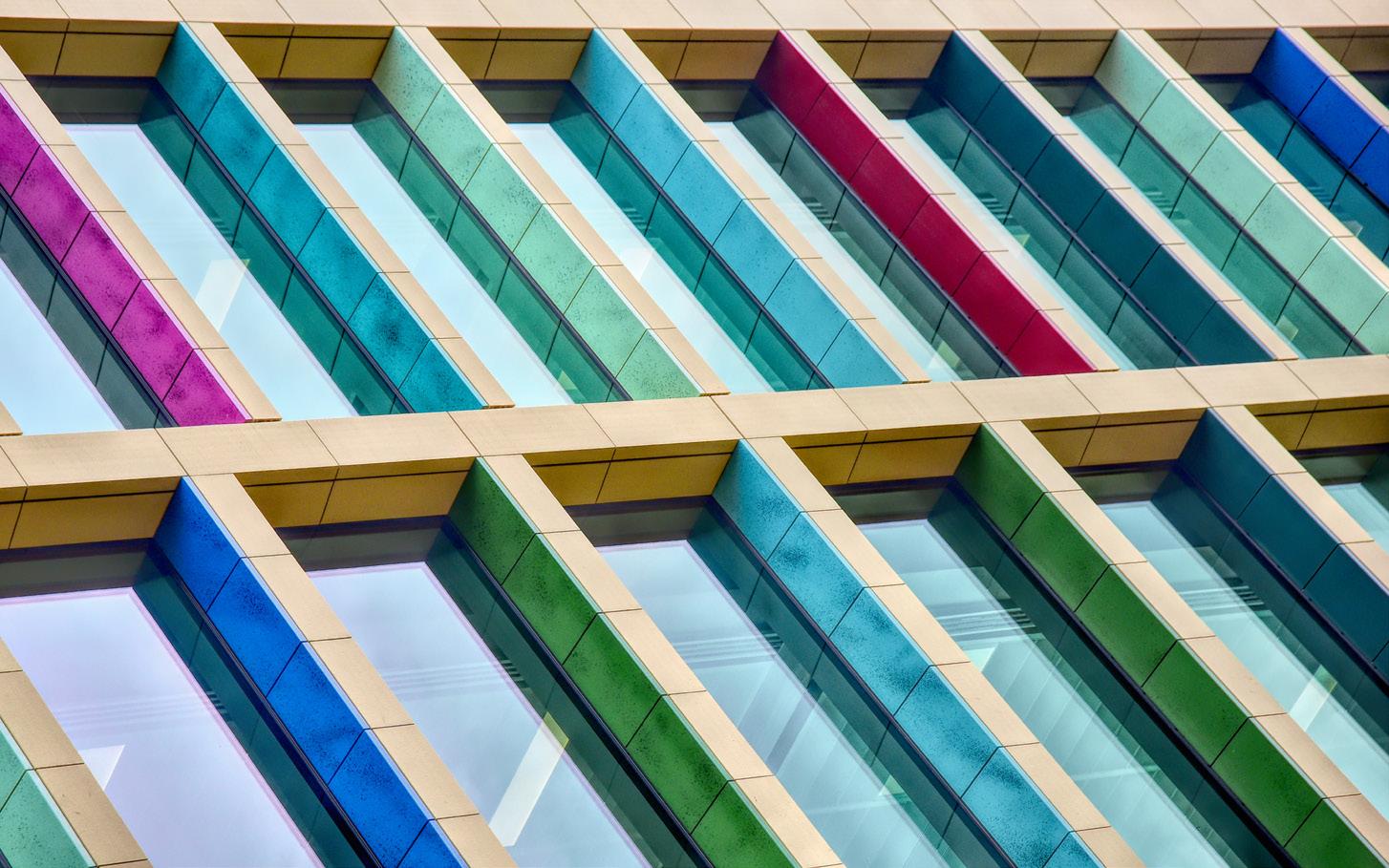
Farringdon East © Paul Scott A big issue with dynamic solutions is that their predicted performance is either modelled incorrectly, or not modelled at all. Mostly because of outdated tools used to prove compliance, but also due to lack of specific modelling knowledge, in the past we have missed the opportunity to properly specify these types of solutions and integrate them within the daily operation of buildings (either by BMS or manual occupants’ action). An update of regulations is necessary to reflect ‘design for performance’ strategies and accept the use of dynamic simulation modelling which is more accurate in predicting real performance.
Reducing the performance gap goes hand in hand with designing for performance. In the context of façades, it translates to setting more
Variation of U-value with glazing percentage for different façade solutions, compared to typical and ‘net zero’ target ranges. Rigorous U-values can only be achieved with lower glazing percentages.
realistic targets, a stricter scrutiny of calculations and installation during construction, and monitoring actual performance to implement feedback loops into the design phase.
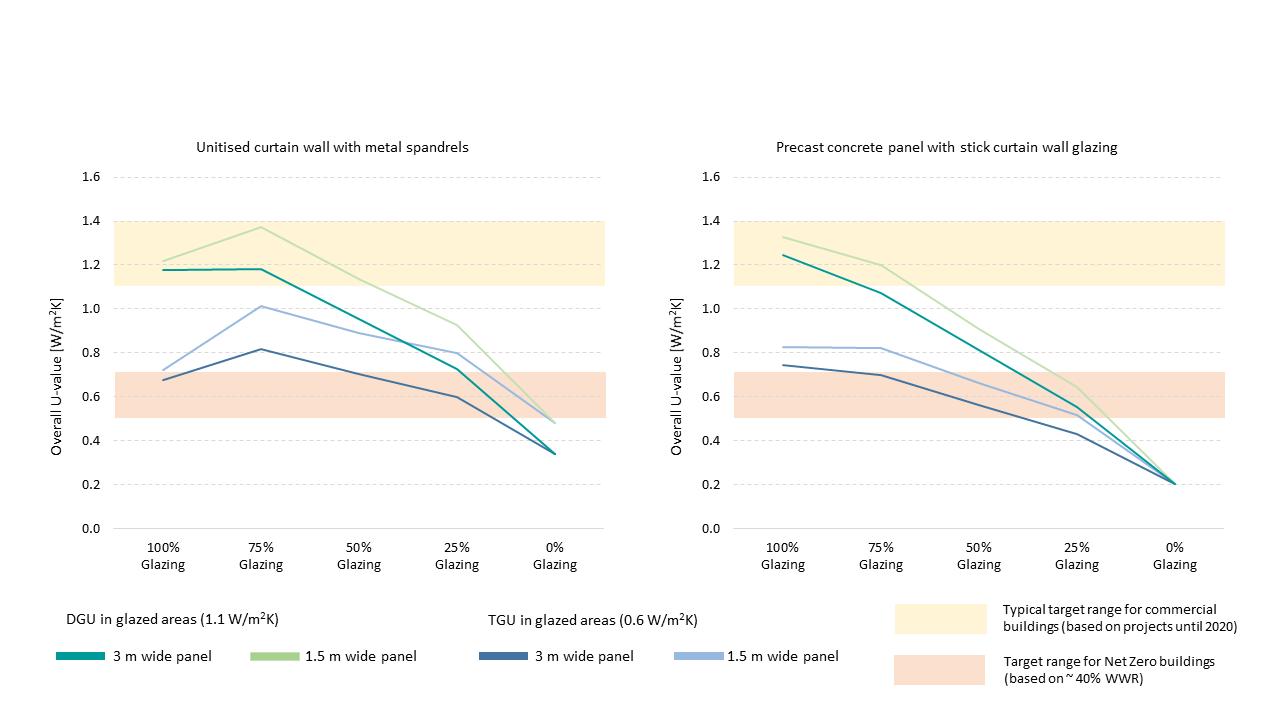
Embodied carbon first
Embodied carbon is a relative new factor, but one that has quickly taken centre stage because of its substantial weight in the whole life carbon balance. Operational energy has been the main focus for decades and its reductions have now reached a point of diminishing returns. On the contrary the role of embodied carbon has been overlooked until recent years and has now become the priority.

The trade-off between operational and embodied carbon is of key importance, as illustrated by this question: in a whole life scenario, is the reduction in future operational carbon brought about by triple glazing worth the additional embodied carbon? The answer depends on factors that are both project specific and general (e.g., grid decarbonisation, performance gap), and it’s hard to predict. Notwithstanding the actual answer, this example introduces the concept of ‘Carbon payback periods’; these will become a necessary tool to evaluate the whole life carbon impacts of important facade design decisions, such as whether to opt for a double skin or
10 Fenchurch Avenue, a commercial building designed by Eric Parry, includes a CCF (Closed Cavity Façade) with dichroic glass on the top five levels. The effectiveness of complex façade systems will need to be questioned in a whole life carbon context, taking into account grid decarbonisation. © Paul Scott
Potential carbon impacts of the use of triple glazing in lieu of double glazing in the context of its typical design life (25 years), for different scenarios of grid decarbonisation.

Influence of building geometry on embodied carbon budgets for the façade. The most compact the building, the higher the budget (i.e., the easier to achieve).
a closed cavity façade. For too long we have been striving exclusively for operational savings, now the focus should be on embodied carbon. Recently the Carbon Emissions (Buildings) Bill, kickstarted by the Part Z initiative, has made its way to Parliament; when approved its impact will be substantial. The contribution of the envelope to the overall embodied carbon of a building can vary depending on the type and characteristics of the project, but it’s one of the major factors with a proportion that can range from 10% to 20% approximately. The percentage is most likely going to increase in the near future because other elements of construction, such as the structure, are a step ahead in the pursuit of reducing their carbon content.
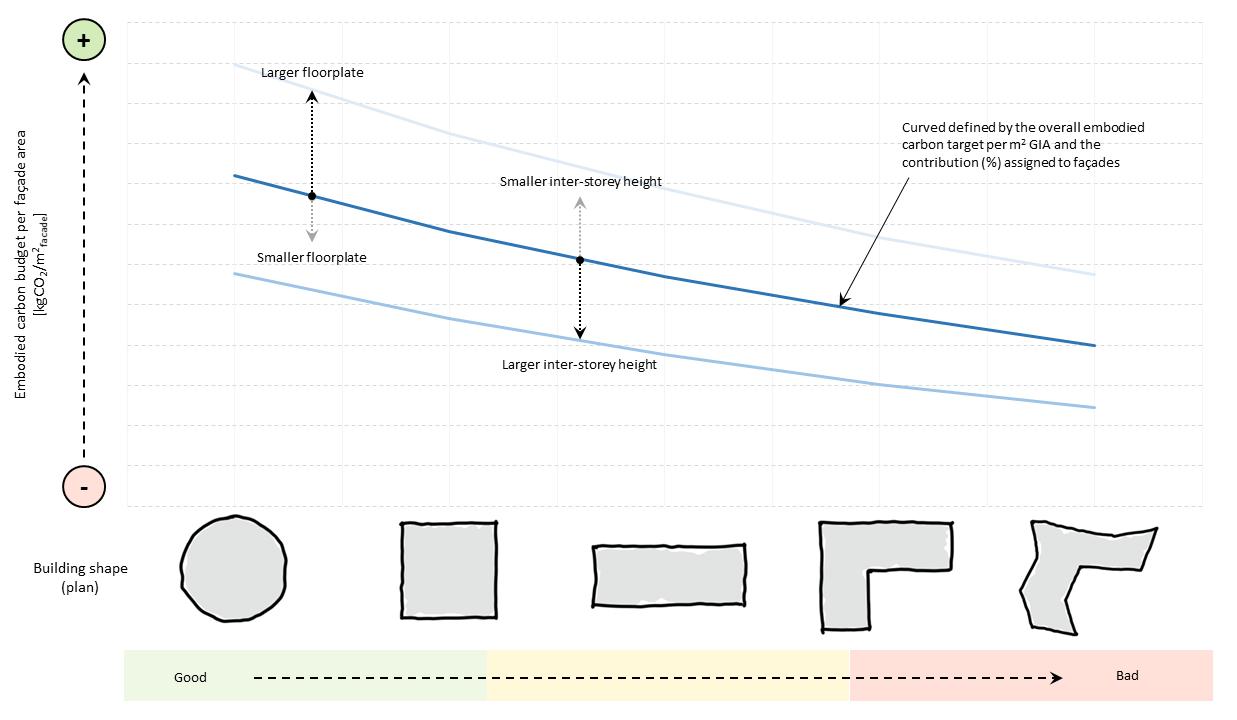
Before delving into specific materials, it is extremely important to point out that the basic geometrical characteristics of a building
can have a big influence on how the façade contributes to the overall embodied carbon. The ‘Form Factor’, which is essentially the ratio between envelope area and GIA, governs this relationship: the more inefficient the form factor, the higher the impact of façades. We can also express this concept the opposite way around: given an overall target, an inefficient form factor translates to a stricter carbon budget for the façades. This is why architectural considerations on building shape, floorplate size, and inter-storey height become very important.
The large number of materials, processes, and construction systems used in façades makes an embodied carbon calculation convoluted. Generally, sustainability consultants do not have a detailed understanding of how façades are manufactured, built, and maintained, which can lead to significant errors in the assessment. Lack of consistency in the data provided by EPDs also adds to the uncertainty. A common approach coupled with defined guidelines is clearly necessary. The CWCT (Centre for Window and Cladding Technology) is addressing this lack of direction and has formed a committee that is currently working to develop a common methodology to calculate embodied carbon of façades.
Material matters
The unrelenting timescale dictated by the climate emergency does not give us the luxury to wait for new low-carbon materials. Besides, two of the most fundamental materials in cladding, aluminium and glass, are not easy to substitute; unfortunately, these also happen to be the main culprits of carbon content in cladding. Timber is seen as the potential saviour, but its implementation in façades on a large scale might take longer than we hope, especially in the UK.
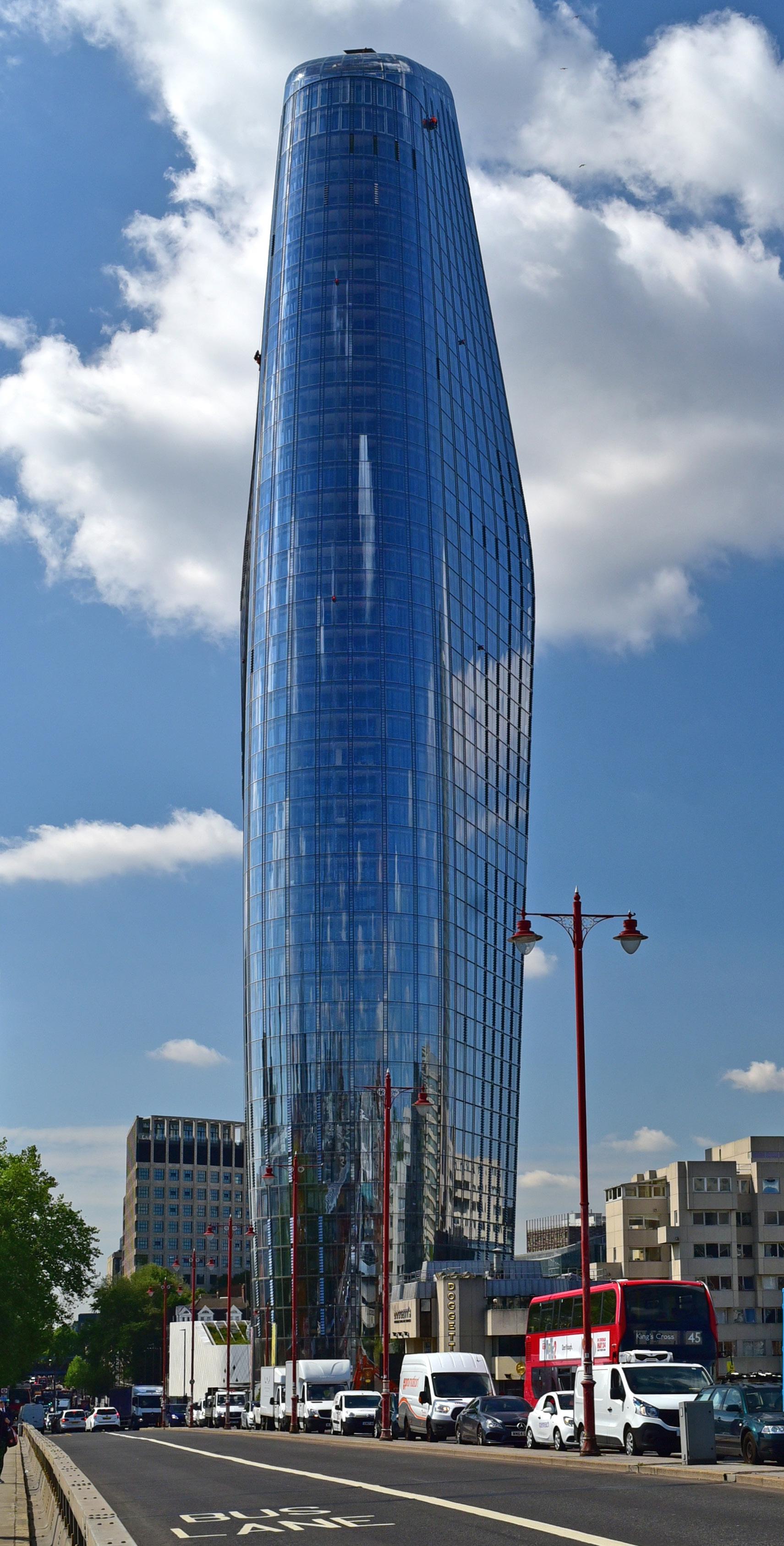
Until timber or other low-carbon solutions catch on, the industry needs to focus on reducing the environmental impacts of the materials already in use by interrogating every aspect of their life cycle. The main actions can be grouped into four categories: de-carbonise production, optimise design, extend service life, improve opportunities for reuse / recycle.
If we take glass as an example, manufacturers are already actively working on reducing the carbon footprint of float glass. In the UK, Glass Future’s ‘Industrial Fuel Switching’ initiative is
One Blackfriars, designed by Simpson Haugh, features a double skin façade with a fully glazed coated outer skin including ventilation louvres, and large sliding doors on the inner skin. The high embodied carbon due to the large quantity of processed glass would most likely exceed the expected targets for a residential development. © Paul Scott
One Blackfriars © Paul Scott evaluating alternative fuels for glass furnaces, which account for the largest part of emissions in glass production. Moreover, plans are being put in place to increase the use of cullet, especially post-consumer one, which reduces CO2 emissions both directly (cullet was already decarbonated during the initial raw materials fusion) and indirectly (reducing energy by lowering the melting temperature).
Designers should optimise build-ups structurally and design out the need for energy heavy processing such as heat treatment and lamination as much as possible. Avoiding floor to ceiling glass by raising it above 800 mm would negate the need for safety glass on windows: less laminated glass would not only reduce carbon content but also improve recyclability. Heat treatments could be limited by undertaking detailed analysis and by introducing measures to reduce the risk of thermal stress. If heat treated glass is necessary, accepting lower visual quality would allow to cut both waste and energy. More relaxed rules on pillowing would mean thinner glass in some instances. Renouncing extra-large glass sizes would mean avoiding the additional energy that comes with producing and installing them. All
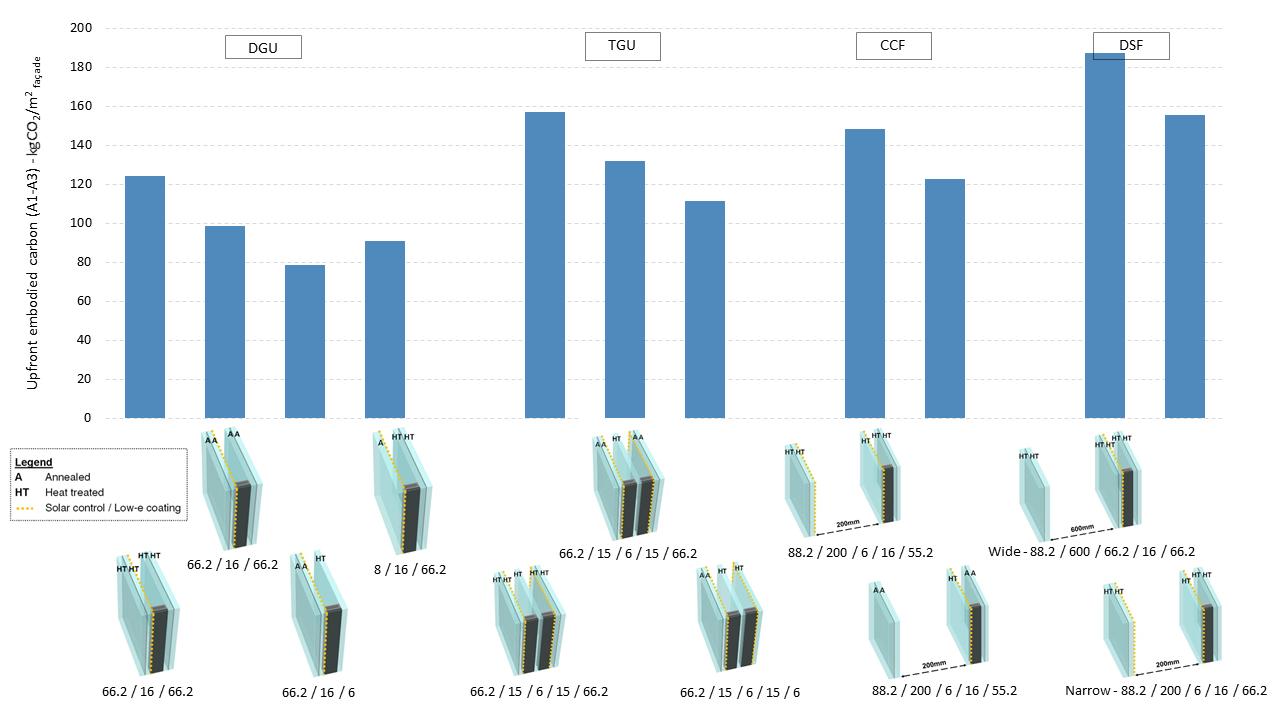
Comparison of embodied carbon (A1-A3) for different glazing solutions and build-ups. (Data for chart was taken from EPDs by Saint-Gobain Glass)
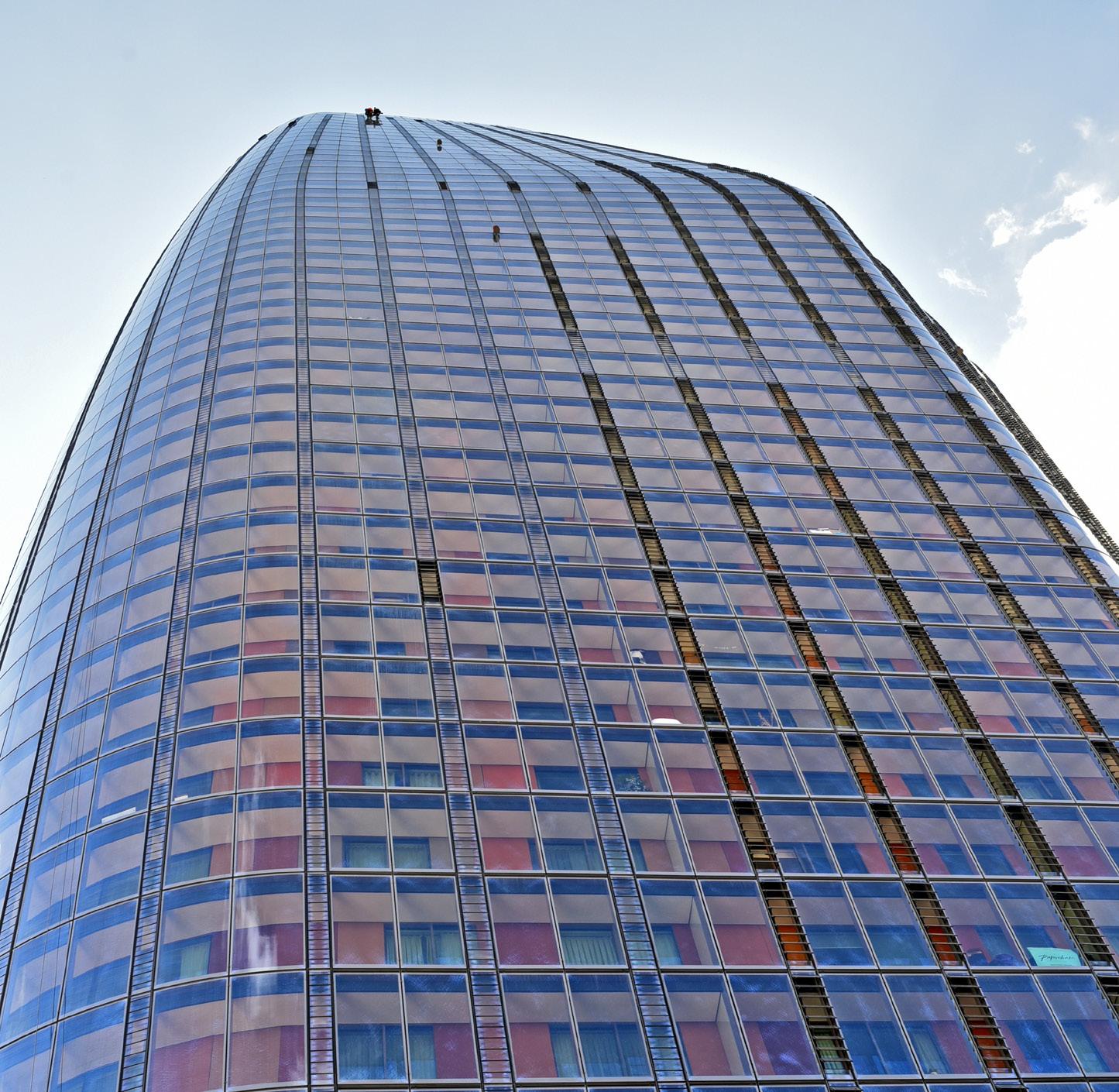
the above measures will have impacts on visual appearance and risk, challenging architects’ expectations and clients’ judgements.
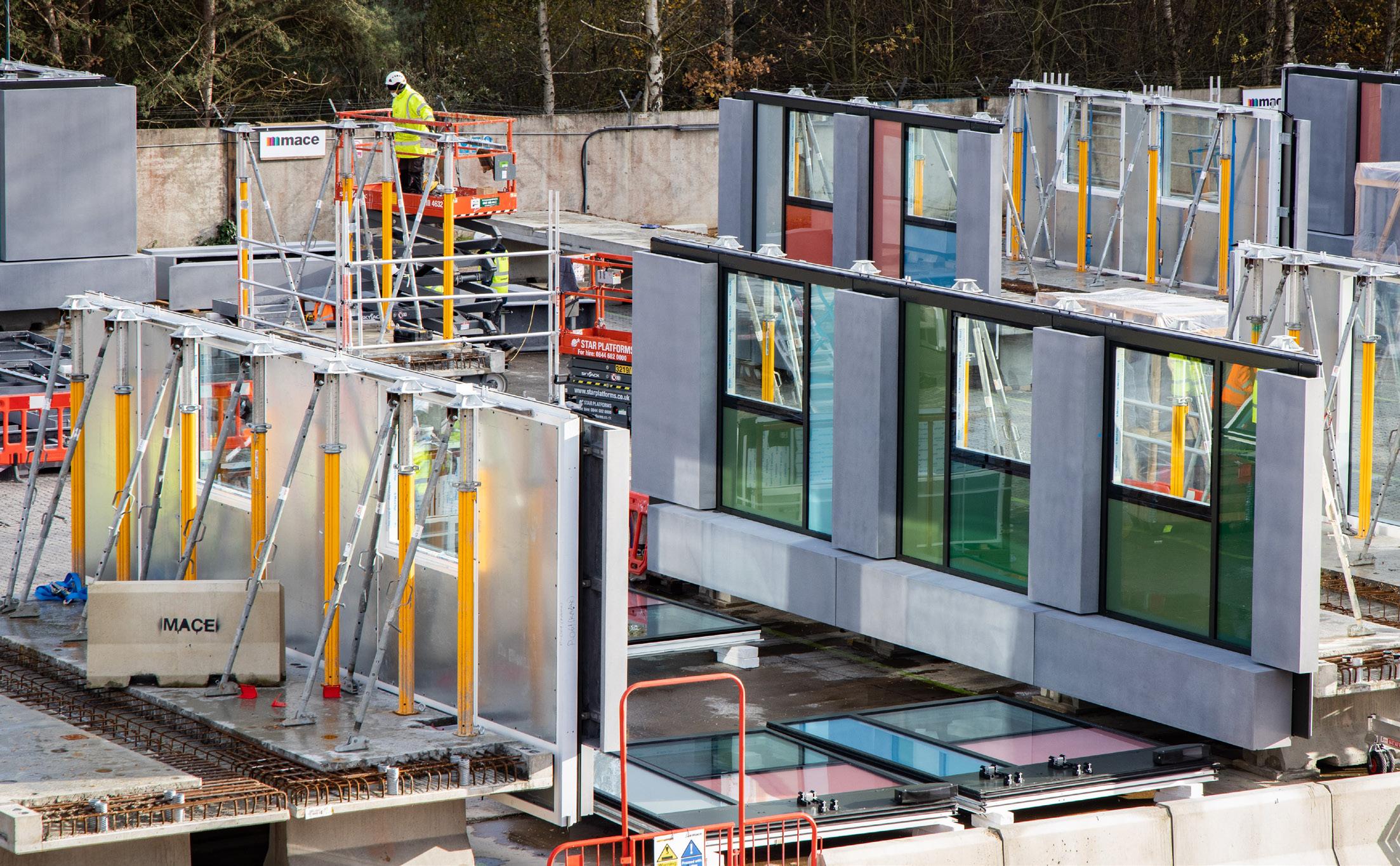
IGUs need replacing at least once during the typical life span of the building, essentially doubling up in embodied carbon. Research into methods to extend their service life is ongoing, and includes studies to improve longevity of edge seals, alternative strategies such as pressure equalisation, or the development of technologies to refill the gas. There are other examples where innovation can come to the rescue, hence the importance of funding and industry engagement to accelerate the transition from research to practical solutions.
Recycling glass has already been mentioned as a way to reduce emission from float glass production, but its importance is much greater when considering ‘zero waste’ targets. As part of the ‘Glass Forever’ initiative, SaintGobain Glass has committed to increasing the proportion of cullet in its glass to 50% by 2025. Key to this is the cullet return scheme put in place to collect post-consumer glass, process it, and re-introduce it into manufacture of new glass.
Unitised panels pre-installed on precast concrete slab sections off-site. The HRS system used by Mace to build East Village N06 allowed significant reductions of waste materials and number of site deliveries. Image credits: Mace Tech.
Similar considerations can be made for other materials used heavily in cladding, from aluminium to concrete, from terracotta to stone. Furthermore, the use of alternative materials with lower environmental impacts should obviously be considered where possible: for example, the energy required to produce zinc or copper rainscreen panels can be 8 to 20 times lower than aluminium.
Closing the loop
Regrettably, addressing upfront embodied carbon will not deliver the ‘whole life’ net zero ambition. We need to look beyond the service life of building elements and think about how we can reuse or re-cycle them in the future. This is a big challenge for an industry that until few years ago didn’t think much about what would happen to the building in operation, let alone at the end of its life.
Cladding systems lend themselves very well to pre-fabrication, which allows a better-quality control, faster installation, reduced risks on site, and the potential for easy disassembly. Modern Methods of Construction (MMC) involving façades are yet to catch on, but a trailblazing example was recently built in London. On the 'East Village' project in Stratford Mace employed their HRS system (High Rise Solutions), where the unitised cladding panels were fixed to long strips of precast concrete slabs; the latter were then installed at the perimeter of the floorplate. On 2 Trafalgar Way, a mixed used development by Urbanest targeting PassivHaus Classic, the use of such off-site construction method is currently being considered. However, in the context of whole life carbon the most important question we will need to answer is not how we are going to build the façade, but what we are going to do with it at the end of its life. We can easily design for disassembly, but what happens then?
The solution to this issue implies a change of attitude that involves a deep re-think of the traditional economic and supply systems governing the cladding market, to convert them from linear to circular. The barriers to wide adoption of circularity principles remain many. Although some of the technical hurdles are starting to be addressed by the façade industry, for example by improving transparency of information and introducing digital tracking of components, changes in commercial attitudes are trailing behind. The appetite to utilise used or recycled materials is still minimal, as it is cheaper and lower risk to use new ones. Most
Breakdown of contributions to embodied carbon (A1-A3) for a typical double glazed unit. The most ‘carbon heavy’ processes are clearly recognisable. (Data for chart was taken from EPDs by Saint-Gobain Glass)
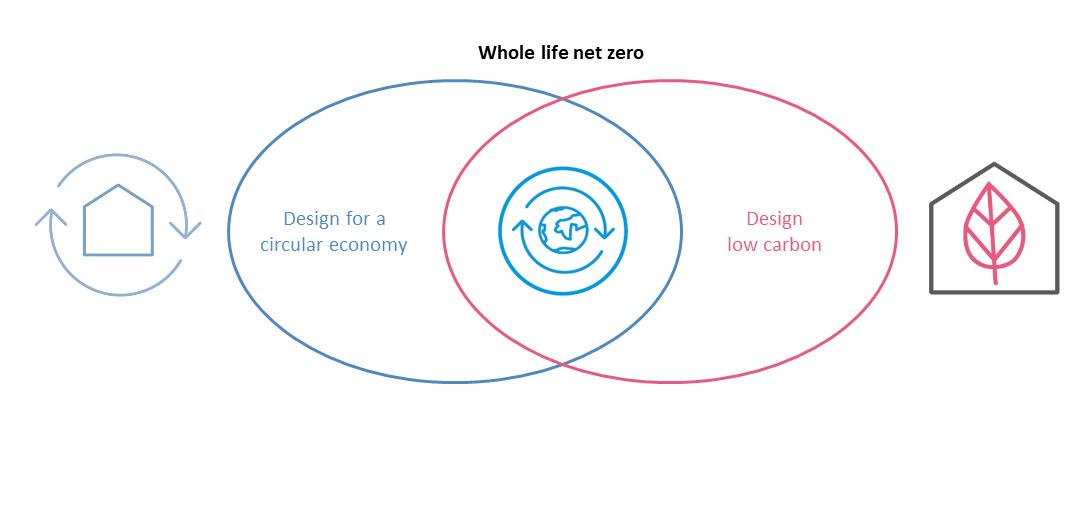
Designing the façade for a ‘whole life net zero’ building will depend on the application of circular economy principles. (Icons credits: LETI)
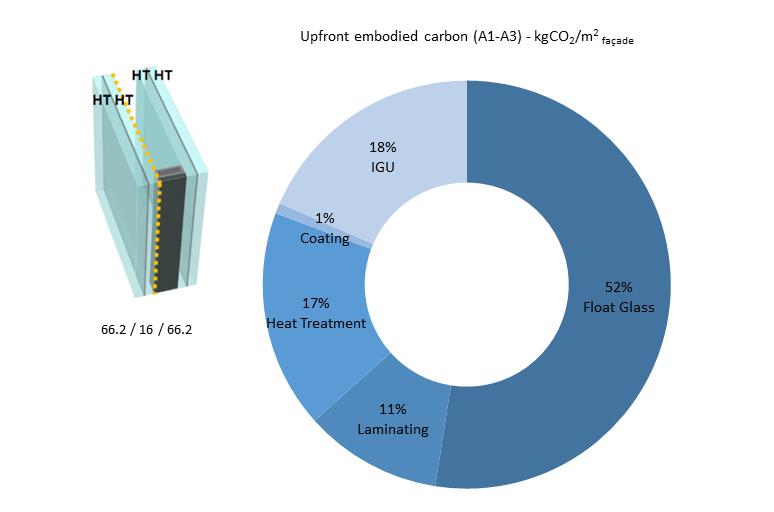
importantly it is not commercially attractive, as there is no established market for the reuse of products and materials.
The conundrum is that we are asked to design products to be reused in a market that doesn’t yet exist. If we want to create circular models, the priority must be to think of ways to retain the intrinsic value of products and materials by keeping them in use. If we imagine the building as a material bank, the façade would probably be the most valuable asset because of its density and variety of materials in limited space. On the other hand, because of such diversity, creating closed loop systems would not be trivial. The ’Façade ReLog’ project was created by TU Delft to unlock the potential for the recovery of metals and components in the European façade industry. By bringing together different stakeholders it tries address practical topics such as business models, industrial processes, and recovery logistics. performance, which will need to be combined with significant reductions in the carbon content of cladding materials. Key strategies of waste reduction, circular models and retrofit at scale will also need to be adopted.
The ambitious targets imposed by the climate emergency should be seen for what they are: a necessity, but also a great opportunity to make things right. They can only be achieved with a collective effort where clear end goals are shared by all stakeholders. The type of cultural changes required are typically slow to occur, but there is no time to waste in an emergency, so we should all act with more urgency.
Another more radical approach could be to turn the façade from product to service. This concept has been studied again by TU Delft through their ‘Façade Leasing’ scheme, which proposes a circular business model based on the use of façades as performance-delivering tools. The contractor / supplier becomes a service provider to the client, who leases the system and its performance rather than buying it. By retaining the ownership of their product, the supplier will commit to maintaining and upgrading it during building operation and will have the best interest to find ways to reuse and recycle components or materials at the end of their service life.
Collective Urgency
Designing building envelopes with carbon reductions as the main driver means adopting a whole life perspective where decisions are evaluated on the basis of trade-offs between operational and embodied carbon. Strict energy targets will dictate exceptional technical
Gianluca Rapone
Gianluca is an Associate at FMDC, one of the top façade and materials consultancies in the UK. He is a façade engineer with a strong background in building envelope physics; before moving to the UK, he completed a PhD in Italy where he studied the optimisation of façade design for energy savings and comfort. Since joining FMDC in 2017, he has been leading the Building Physics team and he has worked on projects across all stages, from concept design to construction. In recent years Gianluca’s keen interest in sustainability and low-carbon design has led him to coordinate FMDC’s efforts in investigating the role of façades in reducing both the operational and embodied carbon of buildings.
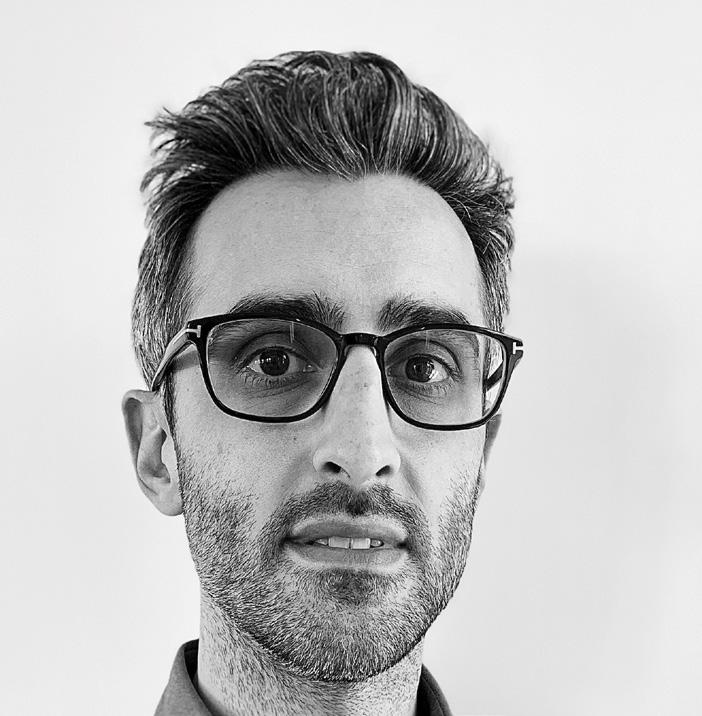

IGS Magazine Copywriting Service for Architecture, Glass and Facade Engineering Industries
IGS has a passion for creative thinking and highquality content that makes a real impact. Our team of journalists and designers have over 30 years’ experience in publishing, writing and editing content specific to architecture, glass and facade engineering.
Our aim is to deliver carefully considered, well executed content that builds your brand profile and connects you with your customers. So, if you’re looking for a creative content provider with a powerful injection of creativity to freshen the global face of your company, IGS Copyrighting Service could be just the tonic you need. The greatest writing is clear and concise, consequently getting your message across effectively is sometimes easier said than done. Our experienced team of in-house journalists and editors raise your profile with thoughtful and intelligent copy that trumpets your story, hitting the right note every time:
1. Whitepapers 2. Case studies 3. Project write-ups 4. Editorials + Advertorials 5. Blogs 6. Press releases
“I am irritated by my own writing. I am like a violinist whose ear is true, but whose fingers refuse to reproduce precisely the sound he hears within.” – Gustave Flaubert
If you can relate to this quote, contact Lewis to find out more: lewis@igsmag.com
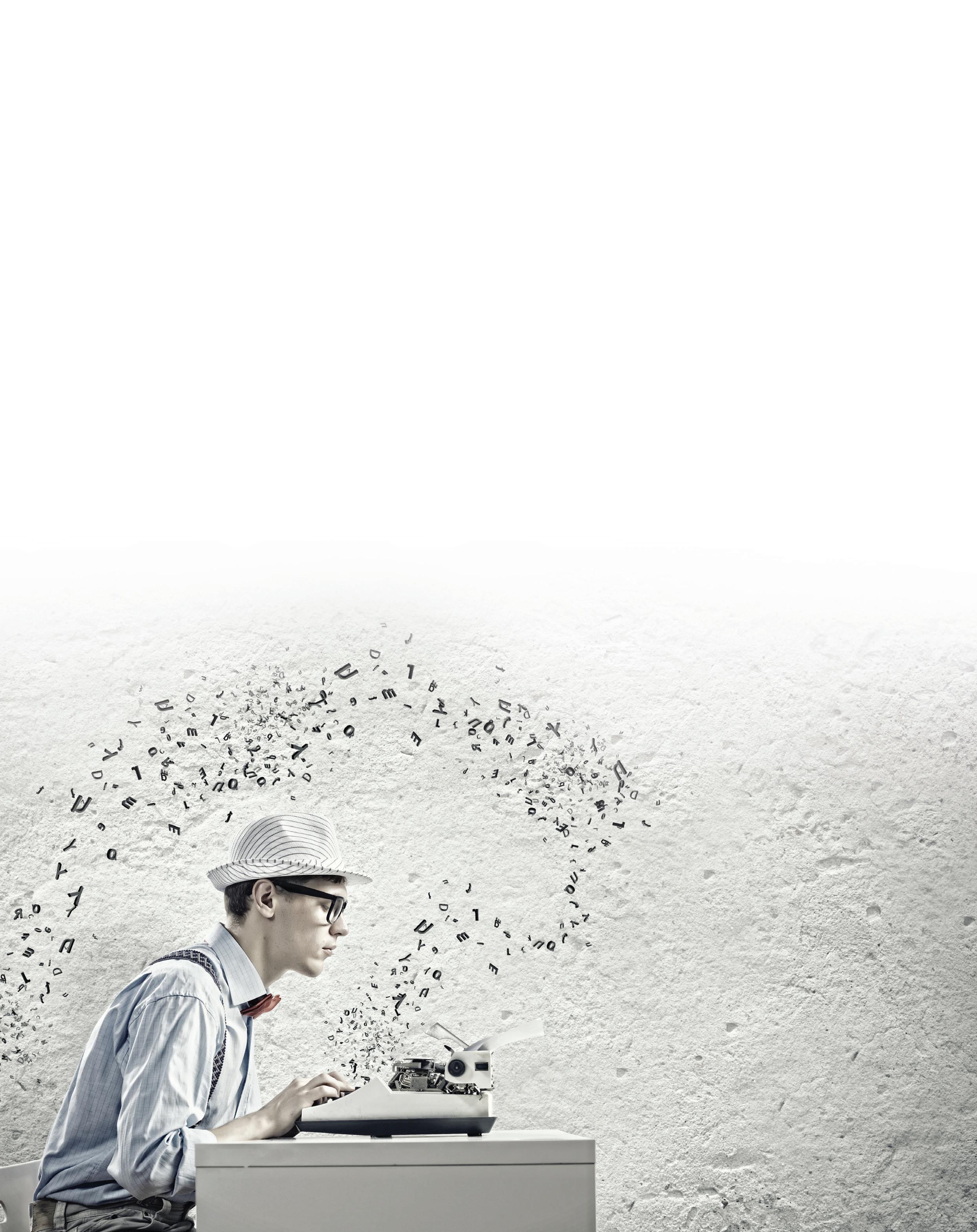