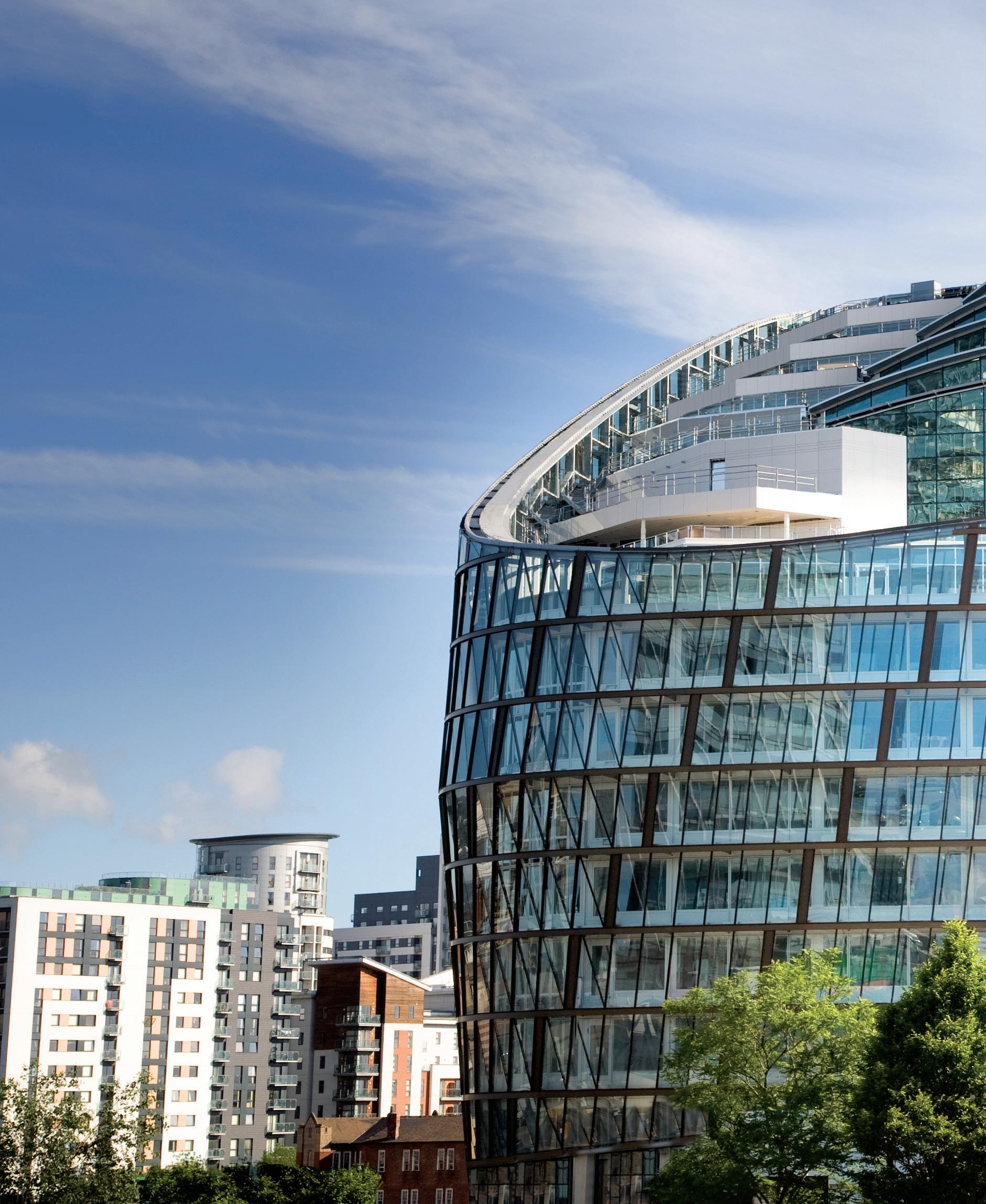
25 minute read
DESIGN AND ENGINEER WITH LESS IMPACT: CARBON NEUTRAL
Design and engineer with less impact
1 Angel Square, Manchester - The building was the first BREEAM rated ‘Outstanding’ regional office building in the UK and is EPC ‘A’ Rated. Courtesy of NOMA.
Advertisement
Carbon Neutral Silicones in Façades – a window of opportunity
Valérie Hayez, Jayrold Bautista
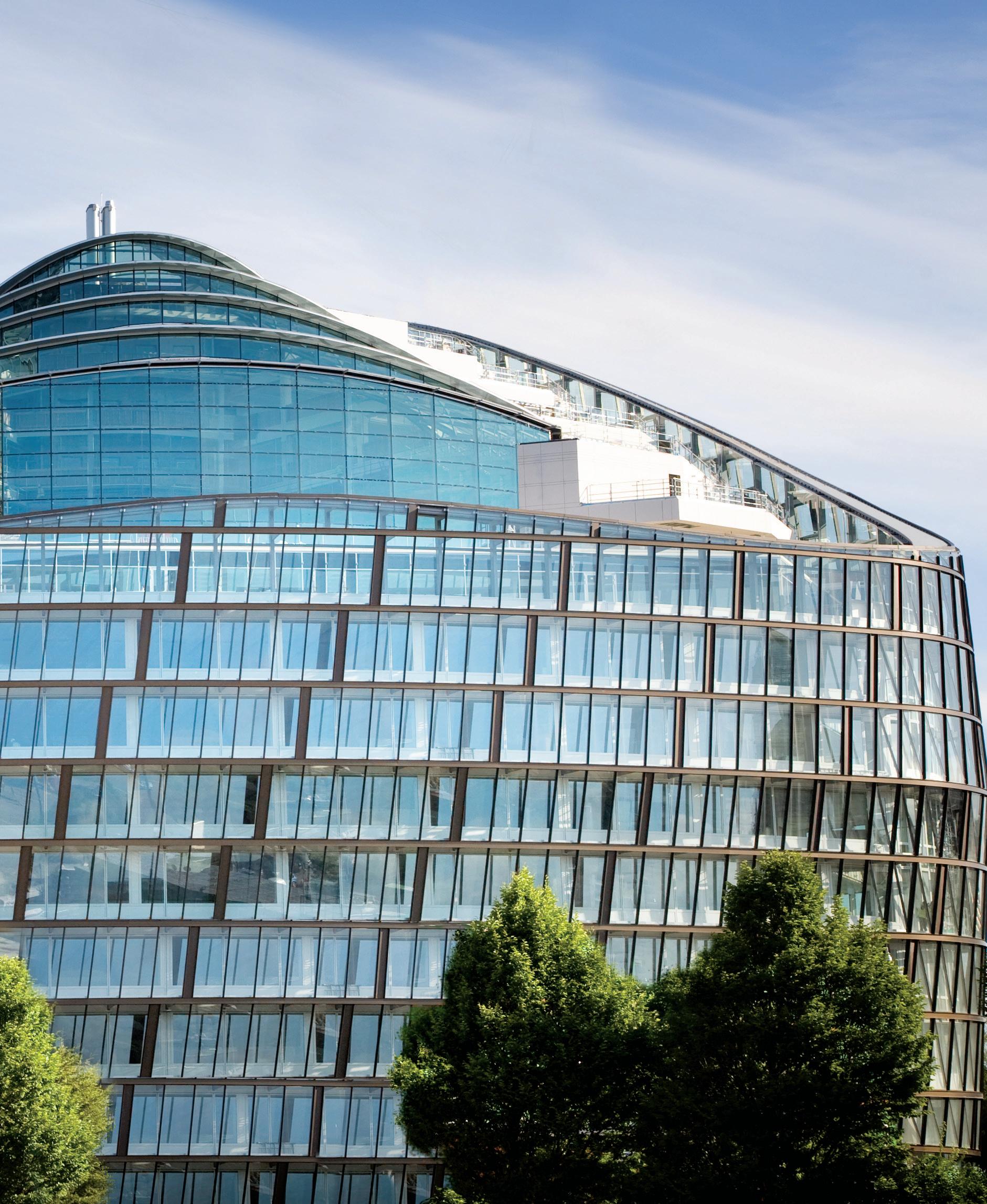
Global carbon emissions resulting from new and existing building stock are well documented. The 2016 Paris Agreement has sparked a plethora of lowcarbon options with many regions, cities and companies themselves creating their own carbon neutrality goals. Carbon targets will hence increasingly be required for planning permission with clients taking a more active role in developing a brief for commissioning their carbon measurements. Reductions in operational carbon - or from the energy used to power, heat and cool a building, have been tackled through energy efficiency measures and are where policymakers, developers, architects and engineers have made significant advances.
The remaining carbon emissions are from building materials and construction. This “embodied carbon” becomes more important as energy efficiency increases and can account for half of the total carbon footprint over the lifetime of the building. Whereas operational carbon can be tracked, embodied carbon
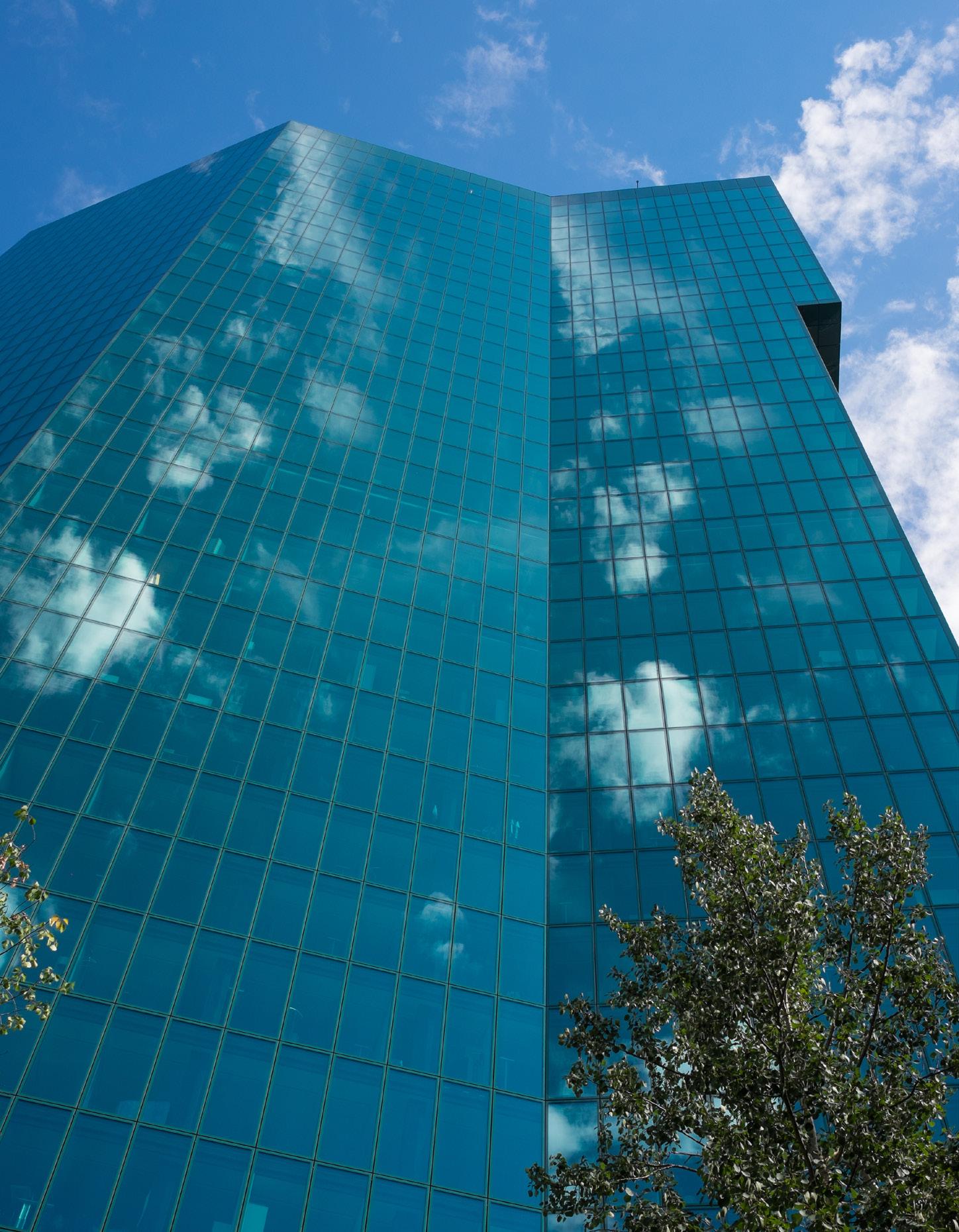
Prime Tower, Zurich, LEED Gold certification
Shanghai Tower – Boasts certifications from the China Green Building Committee and the U.S. Green Building Council for the building's sustainable design emissions, which are primarily generated during production due to energy consumption using fossil fuels and waste, is much more difficult to quantify. Following the push of architectural associations (e.g. CTBUH or AIA American Institute of Architects), building owners and property developers, various tools (e.g. EOC₂, a new REVIT plug-in designed by Eckersley O’Callaghan) are emerging to measure embodied carbon and become the criteria for meeting leading green building sustainable certifications such as LEED or BREEAM through more challenging standard life cycle assessments (LCA) calculations.
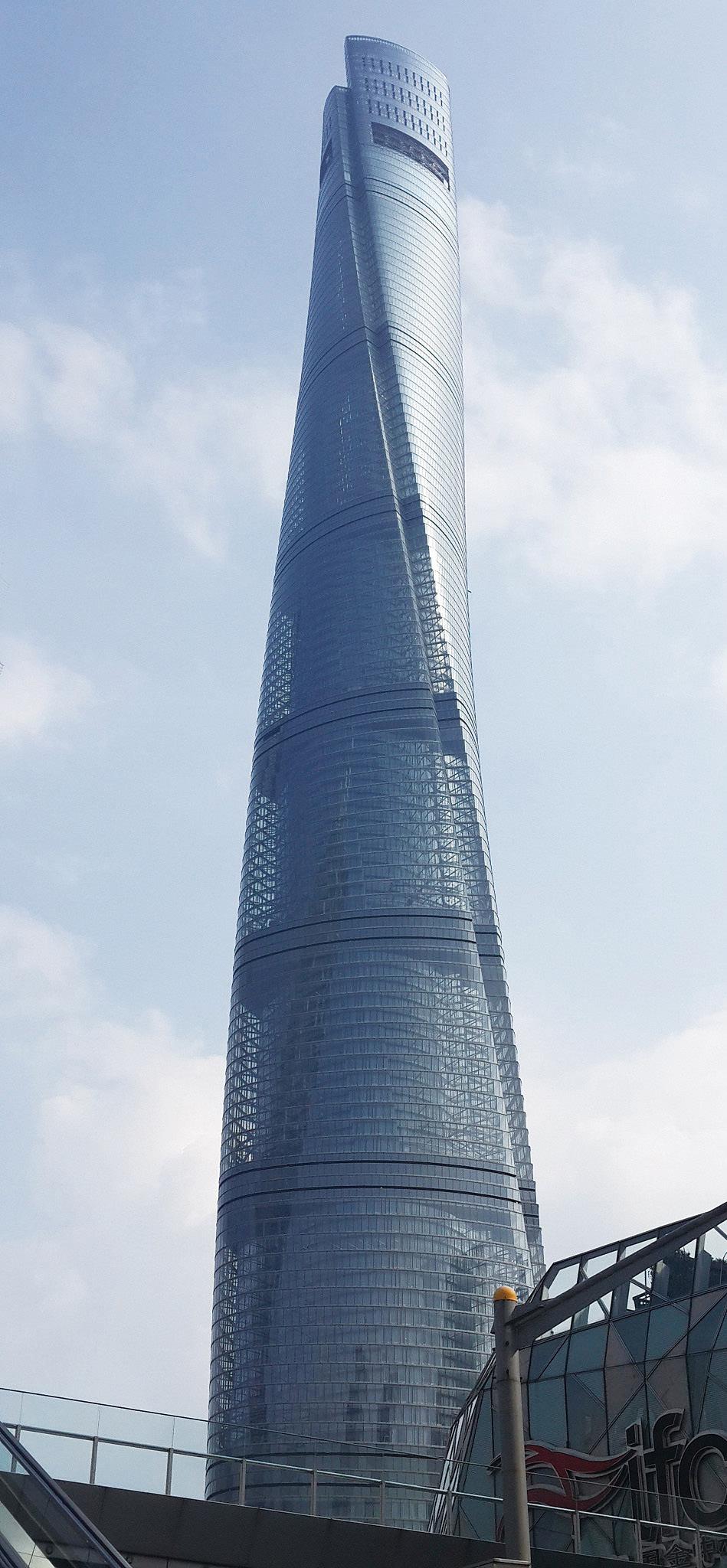
Dow Carbon Neutral Silicones for facades
Dow has the will to take a leading role in supporting the development and implementation of a more circular economy, taking into account a product’s lifecycle – from creation to use to disposal – in everything we do and generate.
Dow has recently been focusing on developing sustainable raw material and sustainable production to reduce our footprint through various environmental, social and governance investments (ESG). Dow is the very first silicone manufacturer that will offset the carbon footprint for the silicone used on a project-by-project basis, through the supply of registered carbon offsets that will net zero the carbon footprint of the material used. The silicone sealant’s contribution to building’s scope 3 emission can now be neutralized through this unique offering.
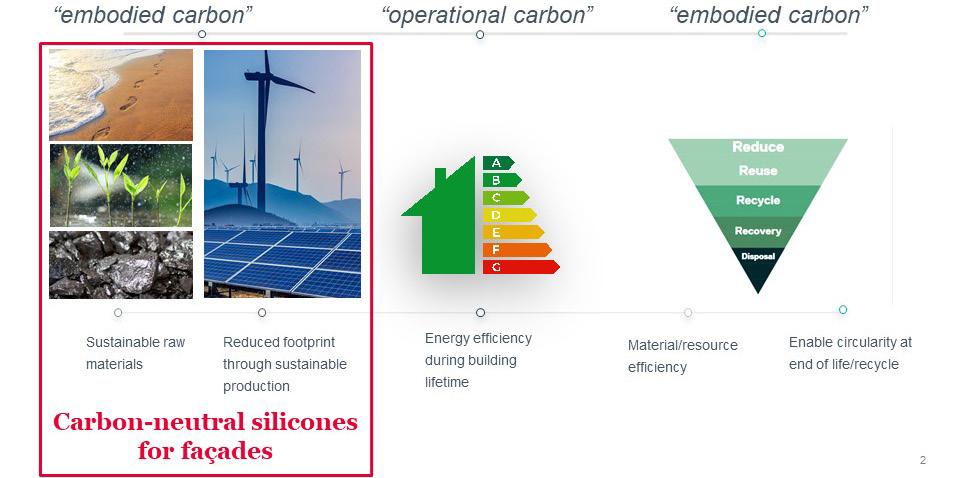
Dow has a unique advantage of being fully backward integrated from manufacturing of Si Metal to Siloxane and the finished products. We offer carbon neutral silicone sealants for facade, based on our efforts to significantly reduce the high silicon metal footprint and offset the remainder by our own generated offset from within our supply chain. These continuous efforts result today in the launch of the world’s first commercially available global carbonneutrality program for silicone applications on building facades, which are verified to the internationally recognized PAS 2060 specifications for carbon-neutrality. A Dow carbon neutrality certificate can be requested on a project-by-project basis.
It is important to note that these carbon-neutral silicones do not only contribute to a sustainable construction design through their sourcing and production, but also through their use. Carbon-neutral silicones can help to enable a sustainable design, through material and energy efficiency. Operational and embodied carbon savings of new high performance façade design and in existing building stock can be realised through a combination of design and engineering of carbon-neutral silicones. The review of how silicones can contribute to a more sustainable design would not be complete without assessing their circularity at end of life and renovation possibilities.
Carbon neutrality shall respect Environmental, Social and Governance aspects
With around 11% of carbon being generated by building materials, an enormous and ongoing effort is required of manufacturers to continually reduce levels of embodied carbon. This requires a significant contribution and investment into enrivonmental, social and governance (ESG), also referred to as the “ESG carbon”.
1 Angel Square, Manchester. Courtesy of NOMA
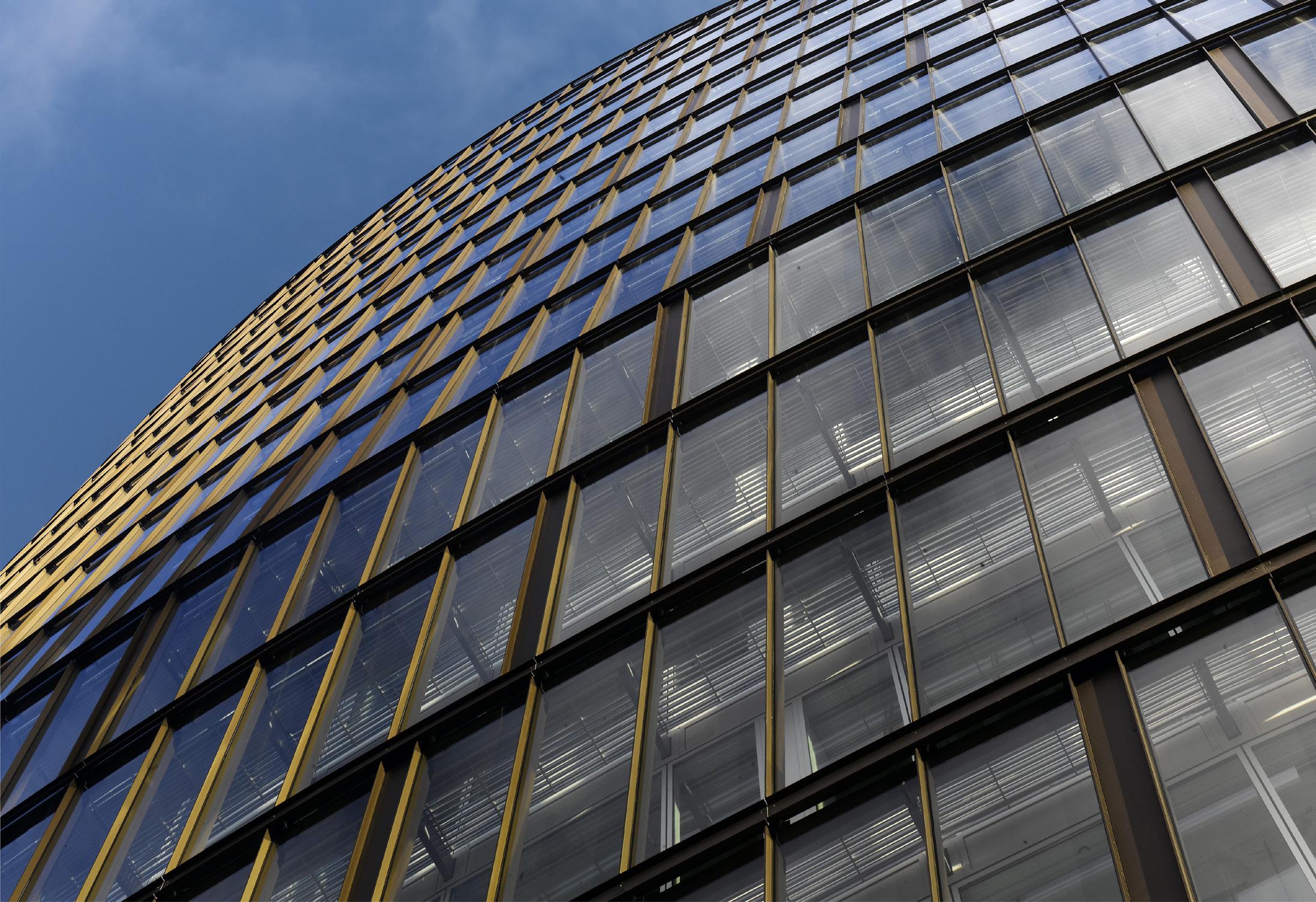
Figure 1: Dow’s back-integrated silicone manufacturing is a huge advantage
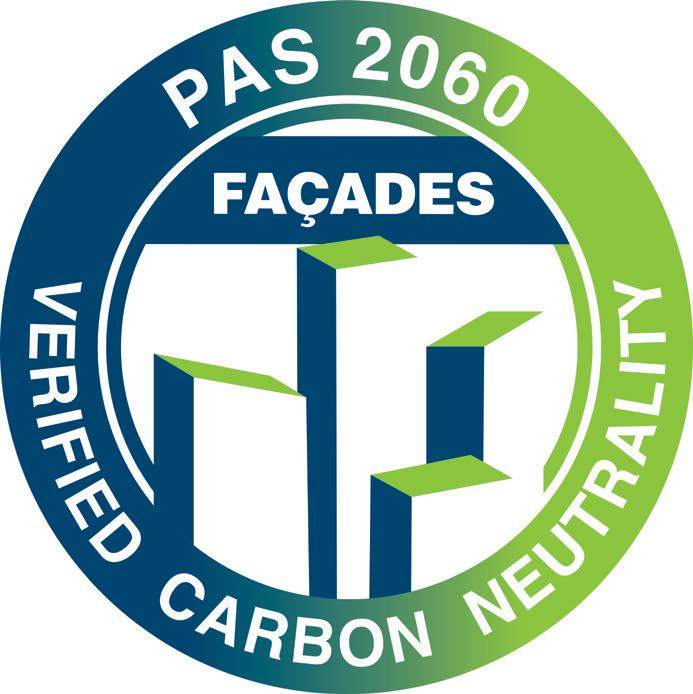
The biggest contribution to the embodied carbon of silicones resides in the raw material extraction and processing. Thanks to backintegration in the production process, Dow produces silicon metal with low carbon raw materials and renewable, non-fossil-fuel energy at two sizeable, protected rainforest locations. Raw materials are sourced and obtained locally. Dow utilizes quartz mines, waste from the wood industry and the Dow owned eucalyptus plantations. The production process is supplied largely with hydroelectric power. This allows to significantly reduce the silicon metal’s manufacturing footprint which dominates the overall emissions balance of a silicone production. using "insets", its own carbon offsets from the internal value chain, resulting from significant and sustainable investments in social capital. This is obtained not only from the above mentioned environmental investments, but also by making critical financial, educational and social investments in the local communities. Improving the area’s Human Development Index and discouraging further destruction of the Amazon rainforest are key initiatives. Dow is making a positive impact on the environment and local communities specifically with Project Ybá in the Amazon, which brings work to circa 4000 people living near the site, while producing the low-carbon materials needed for developing the first-ever carbon-neutral silicone sealants for high performance building façades.
Credible Carbon-Neutrality Services for Façades
LCAs following ISO 14040:2006 and ISO 14044:2006 have been prepared for individual products and the resulting low CO2 emissions are offset as explained before. The LCA conformance review statements and Qualifying Explanatory Statements (QES) were externally (third party) audited following ISO standards mentioned above and PAS 2060 requirements respectively. The PAS 2060 standard is the most well-known and established standard for organizational carbon-neutrality. It includes an “ambitious commitment to climate action” and is intrinsically linked to the efforts of a company’s ESG values which are critical components of a carbon reduction journey. This standard, published by the British Standards Institution in 2010, provides a guidance on how to offset greenhouse gas (GHG) emissions and how to create a continuous carbon reduction plan. Offsetting using verified credits emphasizes and requires the support of climate finance projects with the aim of adding social and environmental value such as Dow’s project Ybá. Annual audits contribute to continuous progress in the journey of reducing and offsetting emissions. As part of the carbon neutral program, the QES, containing the carbon neutrality achievement declaration, can be requested per project.
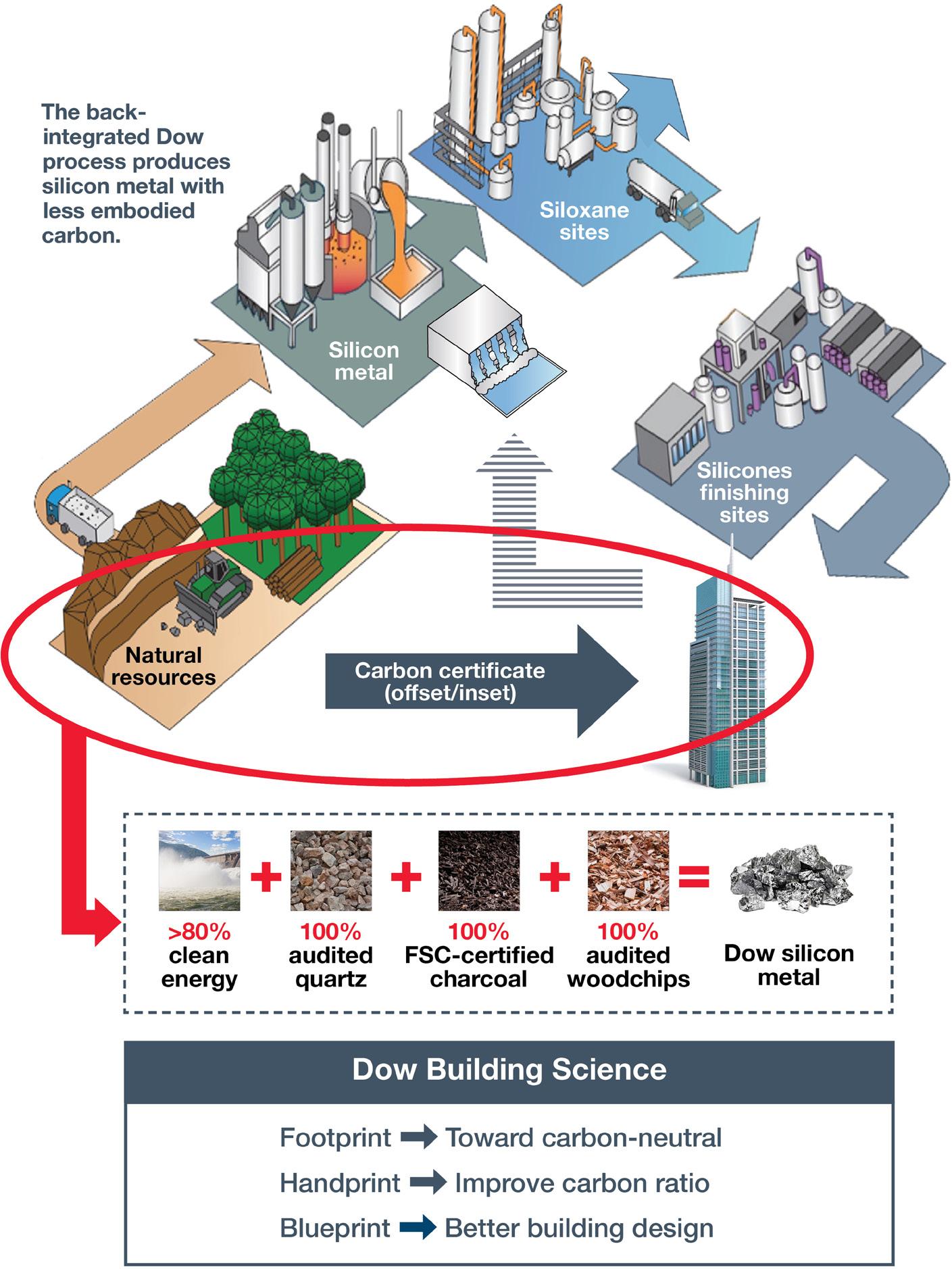
In parallel, the audited LCAs are used to produce Environmental Product Declarations (EPDs), which are a way of reporting the LCA data following so-called Product Category Rules (PCRs). PCRs provide category-specific guidance for estimating and reporting product life cycle environmental impacts, typically in the form of environmental product declarations and product carbon footprints.
Lack of global harmonization between PCRs or sector guidance documents has led to the development of duplicate PCRs for same products. Therefore, it is important to bear in mind that the values of different EPD considerations are not comparable unless they were issued by the same program operator and follow the same PCR.
Finally, Dow’s carbon-neutral program also includes guidance on the contribution of carbon-neutral silicones to securing green building certification credits/points. Building components can contribute to the overall rating if requirements of respective standards are fulfilled. The major schemes in place such as the internationally recognized BREEAM and LEED, and the Singapore Building and Construction Authority Green Mark (mainly recognized in Asia Pacific APAC and China) or the German Sustainable Building Council (DGNB) scheme (mainly used in central Europe) do include carbon-neutrality credits, mainly geared towards the major building components such as concrete, steel, and glass. The carbon neutrality of silicone sealants can also contribute to achieving credits from the innovation section of the green building ratings scheme.
Dow’s carbon-neutrality program is available for projects involving structural glazing (SG, bonded glazing), insulating glazing (IG) and weathersealing (WS), covering all geographical areas. This service is available for the following high performance silicones:
• DOWSIL™ 791 and DOWSIL™ 795
Weatherproofing Sealants • DOWSIL™ 3362, 3362N, 3363EU, 3363CN, 3363US Insulating Glass Sealant • DOWSIL™ 993, 993N and 983 Structural
Glazing Sealants
As an illustration, the carbon savings for a representative façade using Dow’s carbonneutral silicones versus standard silicones can be calculated. The considered façade has insulating glass units of 1.3m width and 2.5m height. These units (of which 30% are considered to be triple glazed) have silicone secondary seals of 10x18mm² and are bonded on the frame with 15x6.4mm² structural seals. Finally silicone joints of 10x15mm² are used to weatherproof the whole building envelope. Assuming 10-15% silicone waste at application, the silicone consumption for the SG, IG and WS applications totals respectively 0.28 l/m², 0.57 l/m² and 0.41 l/m². Using densities of SG and IG silicone at 1.33kg/l and at 1.48kg/l for WS, this translates in a corresponding weight of silicone per m² façade. Knowing that the carbon footprint reported for a standard silicone [1] lies between 8 and 12 kg CO2eq per kg of silicone sealant produced, depending on the formulation, we obtain corresponding kg of CO2 for each application per m² façade of 3.7kg CO2/m² for SG, 7.6kg CO2/m² for IG and 6.1kg CO2/m² for WS. The total carbon footprint for silicone per m² façade, considering SG, IG and WS can therefore reach up to 20kg CO2 eq/m². A building of 30.000m² using carbon neutral silicones represents therefore potential CO2 savings of up to 600ton eq, which can be avoided by switching to carbon neutral silicones. Depending on future evolution of CO2 industry, switching to carbon-neutral silicones for façades could result in significant savings for building owners [2].
Gaining access to Dow’s carbon-neutral silicones is straightforward. Project specific volumes to be consumed need to be disclosed together with project information and submitted to Dow. Please consult dow.com/ carbonneutralsilicones for more information.
Material efficiency
Material efficiency is an important aspect of a sustainable design. This approach focuses in the first place on building clever through preventing or reducing material usage which can help to further decrease the embodied carbon of a building envelope. To evaluate how bonded glazing, with or without carbon neutral silicones, can prevent or reduce material
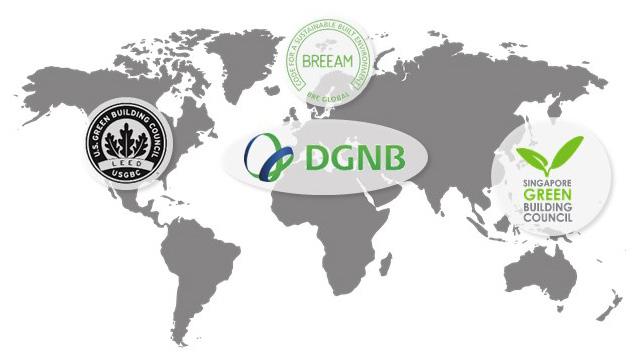
Table 1: Comparison of Ucw for different system configurations , at a fixed width of 1.3m
Model Frame size (mm) Glass thickness range (mm)
Structural Thermal Uf (W/m²K) System A SSG 63.5 x 190.5 6 - 25.4 Not listed 2.33 System A Capped 75 x 190.5 6 - 25.4 Not listed 2.73 System B SSG 63.5 x 165 6 - 25.4 1915Pa 1.93 System B Capped 63.5 x 190.5 6 - 25.4 1915Pa 2.50
resources, several state-of-the-art commercially available bonded (SSG) and mechanically fixed façade systems were compared from a structural and raw material usage. Representative systems for the APAC and North America (US) geographical areas were selected to cover a majority of projects worldwide. To isolate the benefit of the bonding itself, the systems were chosen in such a way that they both offer a bonded and capped version of the profile with very similar dimensions (in terms of sightline and depth) as well as very similar thermal performance (Uframe). Both APAC (System A) and US (System B) frame systems were unitized systems, selected so that both can accommodate the same wind load which was set at 2kPa, an average windload covering a majority of façade projects worldwide. The frames do not have specific features to cope with extreme loading like hurricane or blast loading.
The dimensions for the façade unit were average and fixed at 1.3m width, for a vision height of 3m and spandrel height of 1m. As an illustration Figure 2 shows the standard vision mullions for the profiles A and B. More details regarding the mullion at spandrel level, the transom and stacked joint profiles are available upon request. To compare material use, a simple aluminium weight calculation was performed for the considered curtainwall (CW) unit dimensions (1.3mx4m). The structural adequacy of both systems was confirmed for stress and deflection requirements following American codes and standards [3, 4, 5]. Looking at the profile cross section drawings it is obvious that at equal capacity in structural loading, for the bonded and capped system, the latter will require a higher amount of aluminium, mainly due to the presence of the cap, and this was quantified to reach up to 15% for the considered systems. It is important to note that the here presented data is not intended to be a general conclusion but to be used as an illustration, highlighting that SSG systems can be designed to bring material efficiency benefits to the building envelope. A wide variety of façade systems are however available on the market and material savings may differ from the hereby presented results. For example, Europe favors toggle systems, with a complexity that requires a more thorough material analysis making it difficult
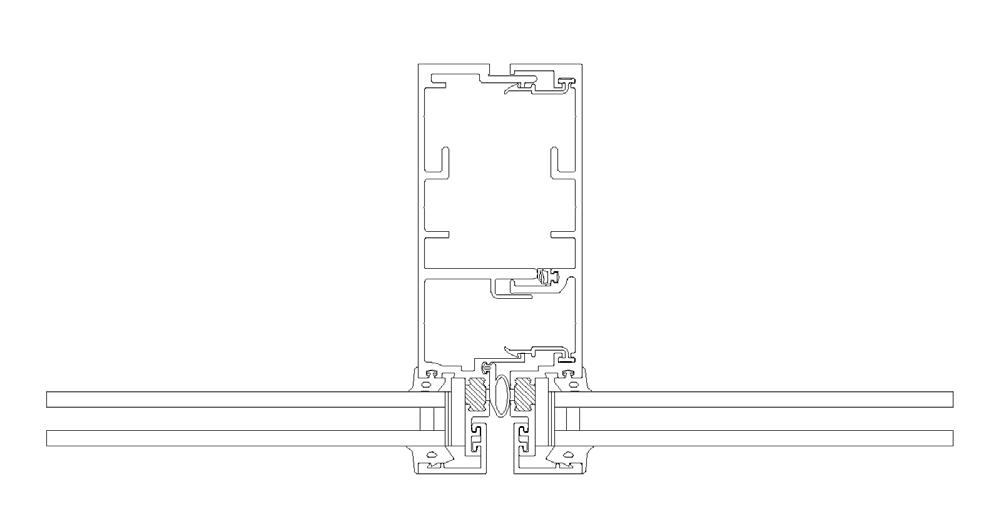
A: capped
STANDARD VERTICAL MULLION VISION
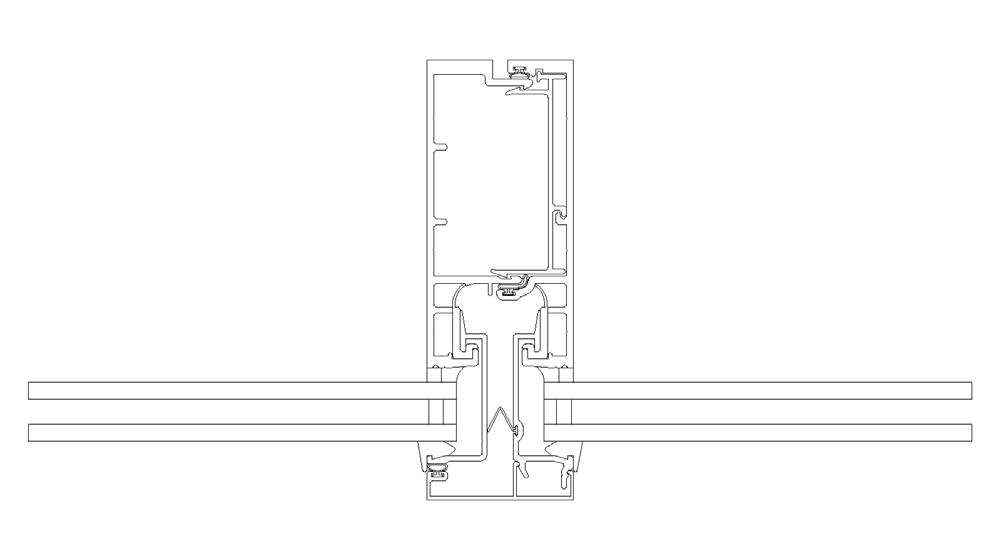
B: capped
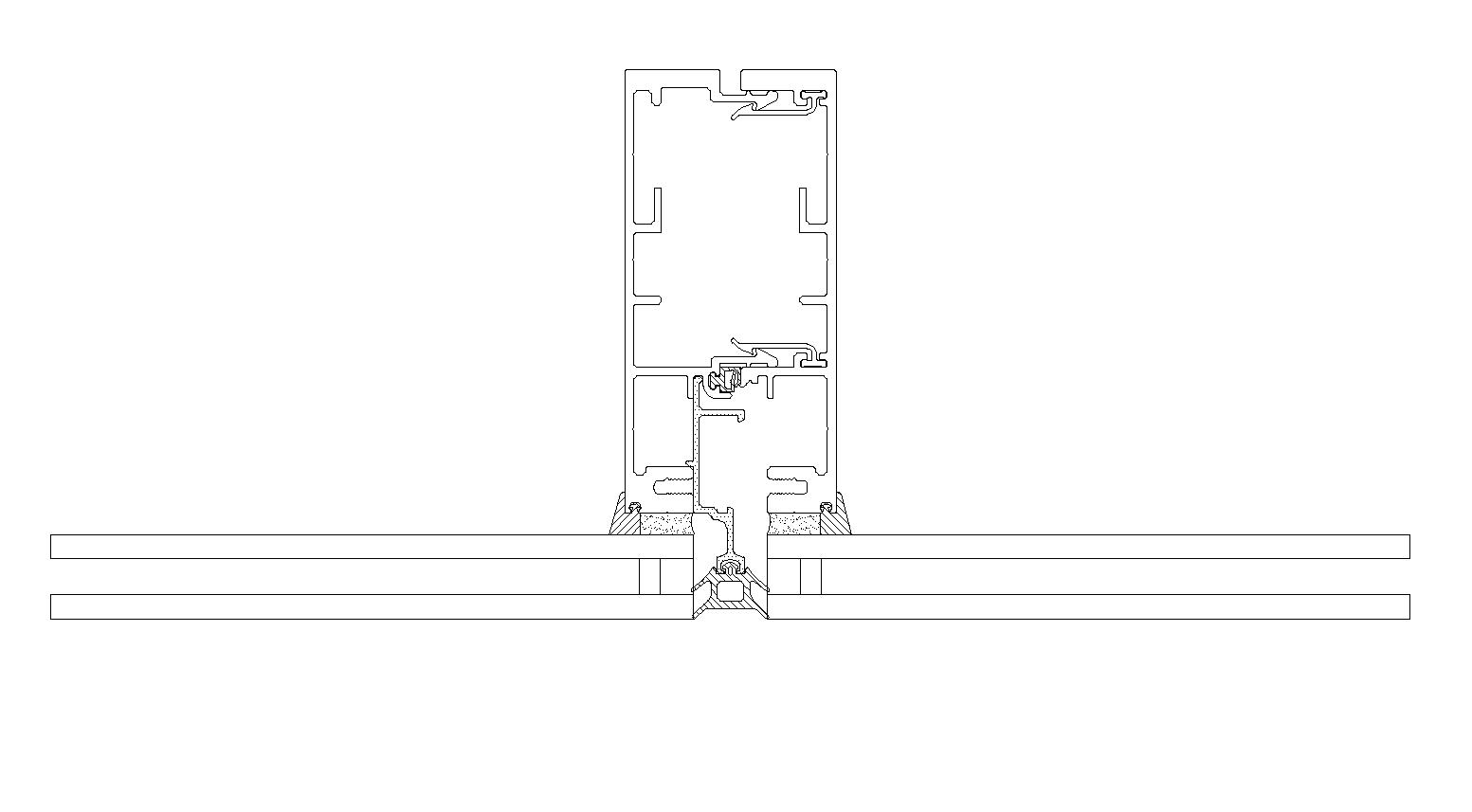
A: SSG
STANDARD VERTICAL MULLION VISION
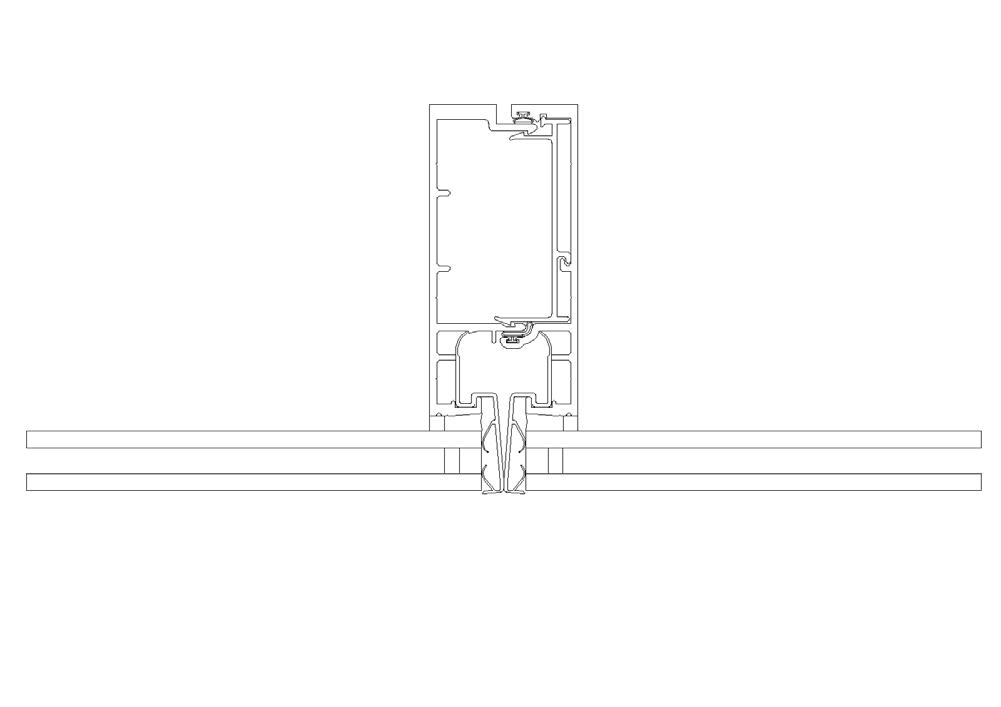
B: SSG
Reduced use of metal reinforcement in residential windows through bonding
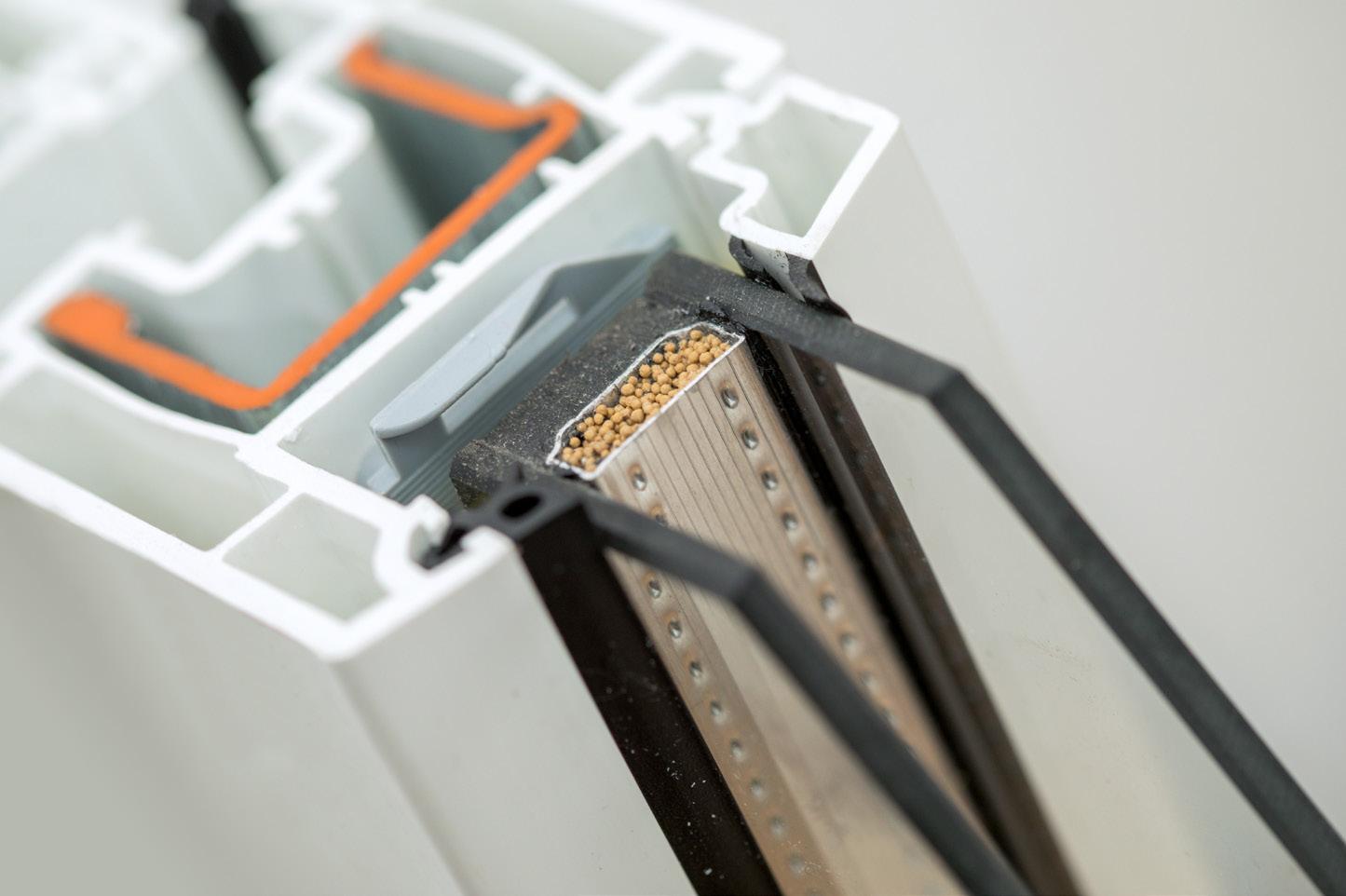
No replacement of gasket during lifetime of façade
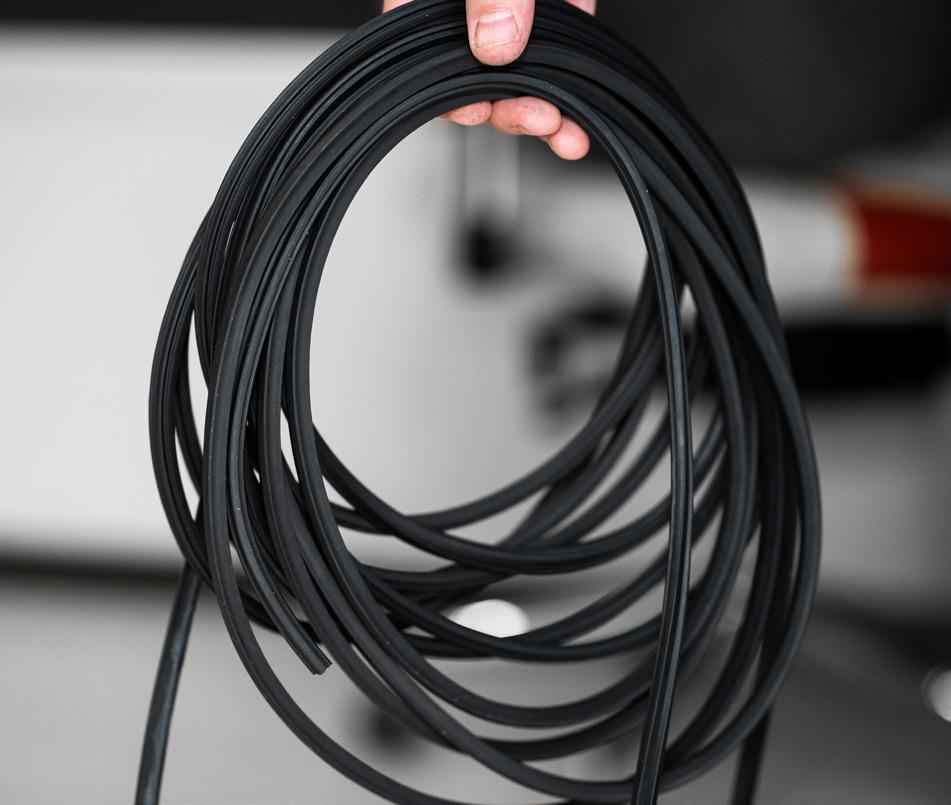
Advanced engineering methods optimize joint design: avoid Si over-dimensioning to determine typical material savings. Similar to the unitized systems, the mechanically fixed European version will use more aluminium due to the cap. However, the toggle version adds additional material through the use of toggles and pockets. The pocket can be plastic or metal based, whereas the toggle is normally a metal alloy. Both are typically punctual inserts which should not exceed 30% of the perimeter and their presence should have a limited influence on the overall material use.
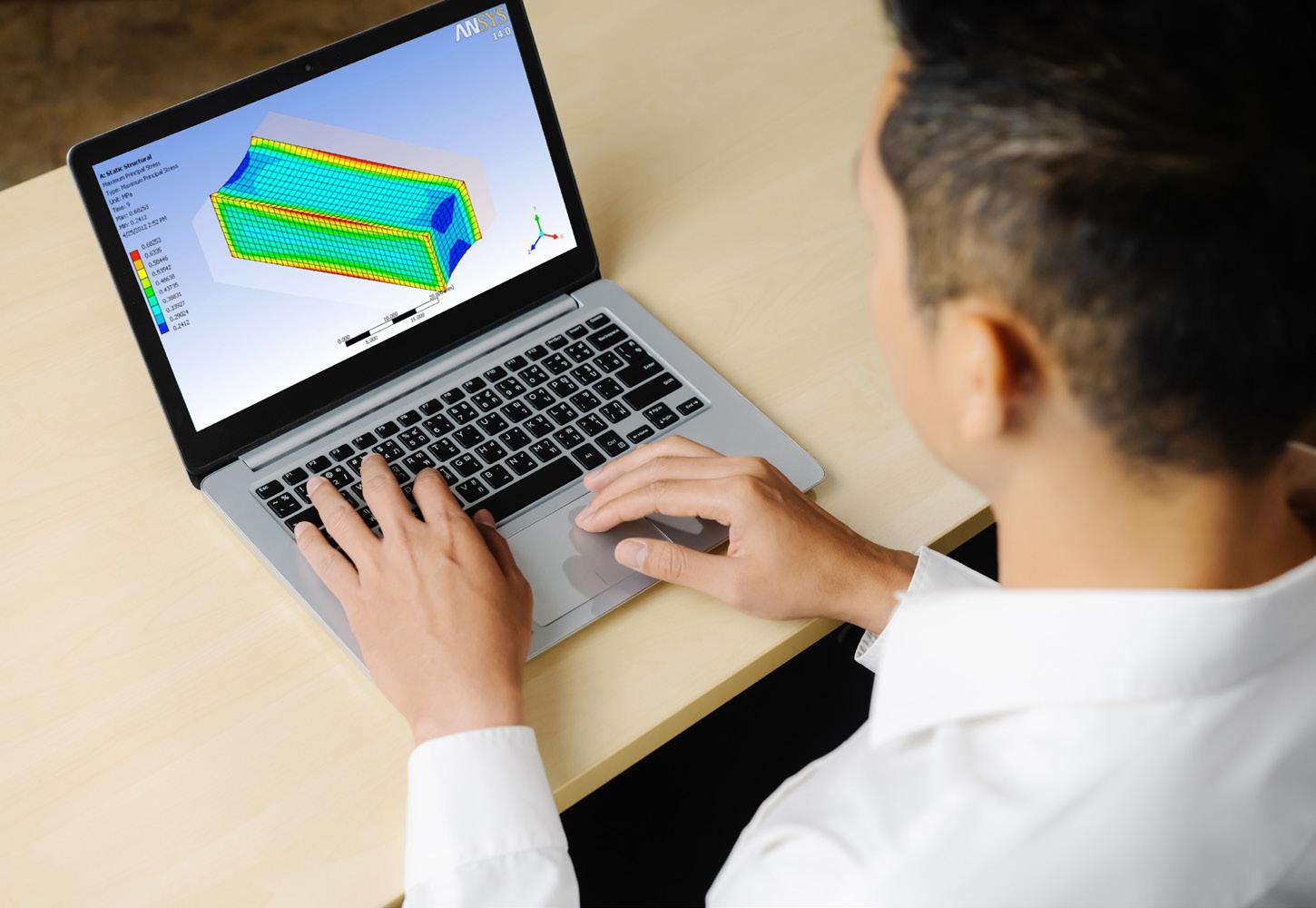
Building further on this benefit, bonding can be used to transfer the glass rigidity to the frame and support consistent lightweight construction, leading to material savings and increased resource efficiency in all phases of the product life cycle. This concept has been successfully implemented in bonded PVC residential window

frames, which only use steel reinforcements at larger loads or dimensions compared to a nonbonded window [6].
The composite behaviour of bonded assemblies is also used in the development of façade systems aiming to use less stiff frame materials than aluminium (e.g. fibre reinforced pultrusions [7]). Recognizing this benefit of bonding, the European curtain wall standard EN13830 [8] gives the possibility to work with lower profile stiffness (using slimmer profiles with less material and embodied CO2) provided the stiffening effect of the bonded façade elements is proven in the application through advanced calculation methods (e.g. finite element analysis).
In the above material usage considerations, only the aluminium reduction in SSG systems was
quantified based on the profile cross section comparison. However, for a full comparison of raw material usage, the quantity of silicone or EPDM gasket used could be assessed as well. Using the conventional joint dimensioning methods can result in some instances in oversized joints. Dow is however committed to developing advanced engineering methods which optimize constructive joint design and can reduce over dimensioning. As seen earlier, the lifetime of an SSG system is assumed to be 50 years, which also corresponds to the service life of a building. On the other hand, the service life of the EPDM gaskets for the dry glazed thermally improved system is assumed to be about 16.7 years. Gasket replacement may therefore be required during the lifetime of a façade. Due to the longer lifespan of the silicone components, the sealants can be used without need for replacement over the use phase of the building. As gaskets in dry glazed façade systems age over lifetime, air infiltration can increase more than is the case for the durable silicone wet sealed façades resulting in higher energy consumptions and consequently higher operational CO2 [9, 10], as will be discussed more in detail in the next section.
As an illustration, it is possible to quantify the benefit of SSG façades from an embodied carbon viewpoint. A captive façade of 30.000m² with units of 1.3x3m², uses on average about 12-14kg/m² aluminium which results in 10-11kg/ m² for a bonded façade taking into account the 15% saving. Assuming an average embodied carbon of 15-17kg CO2eq per kg of aluminium, the SSG version of the façade, using carbonneutral silicones will save almost 1000 ton CO2eq. This is a conservative estimate, as savings linked to the use of carbon-neutral silicones instead of gaskets needing replacement during the lifetime of the façade are not considered. Benefits linked to the composite behaviour are not included either as these require project related analysis.
Support energy efficiency
Using carbon-neutral silicones and structural glazing in façades will contribute to optimizing resource efficiency and reducing embodied greenhouse gas emissions. However, silicones also influence the operational carbon emissions (handprint) by ensuring energy efficiency of the building envelope [10, 11]. The application of silicone sealants in construction can enhance the long-term resistance to degradation of buildings and can protect and extend a
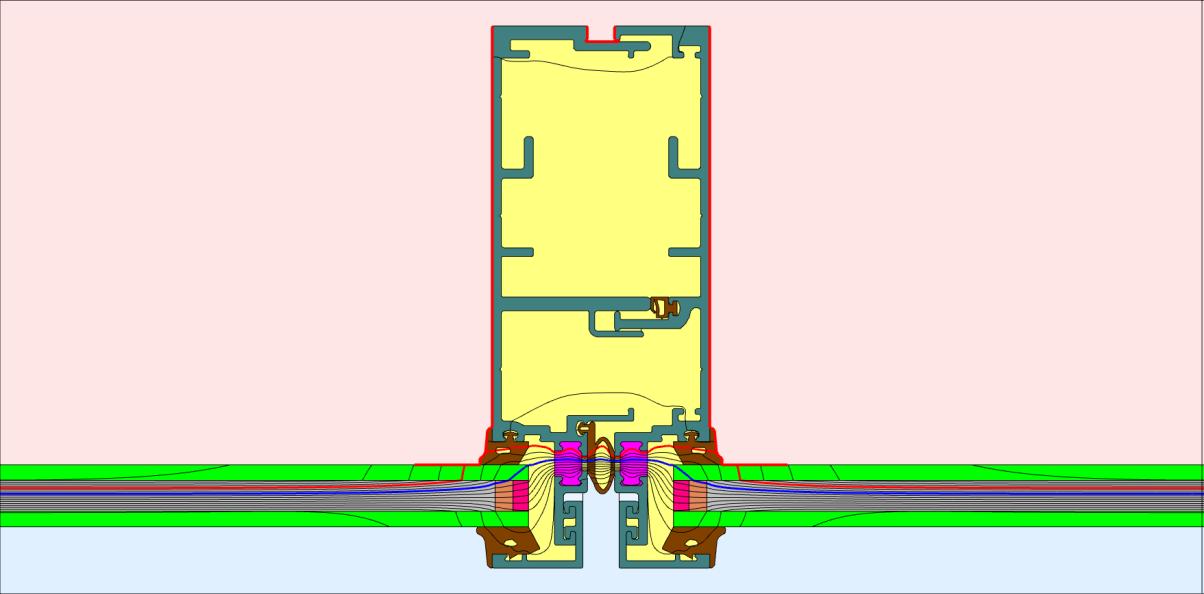

Figure 3: isothermal lines for the standard vision mullion for the System A profiles
building's lifetime [12]. Silicone sealants and adhesives do have outstanding performance features when it comes to climatic resistance and weatherability. They allow flexibility for differential thermal expansion between bonded substrates or long-term adhesion durability to glass under temperature extremes and movements. Silicone sealants used for weatherproofing or bonding help to ensure airtightness and energy efficiency of the building envelope, as well as the use of energy saving multi-pane insulating glass units.
Previous preliminary work by the authors had indicated the potential of specific SSG façades to help deliver a higher thermal efficiency compared to mechanically fixed façade systems [9, 10]. This study was updated by comparing the unitized façade systems described earlier. The thermal models were performed for each profile type, using the same double IGU with center of glass U value of 1.1 W/m²K. A representative warm edge spacer with linear thermal conductivity of 0.14 W/mK was used together with a silicone secondary sealing of 6 mm height. The thermal conductivities used for EPDM, silicone, insulation or aluminium are the tabulated values as per ISO 10456 [13] and the thermal modeling was done according to EN ISO 10077-2 [14]. Based on the various dimensions and U-value for the frames, as well as the U-values for the glass or spandrel and corresponding linear thermal heat transmittance values Ψ the U value of the curtain wall unit (Ucw), consisting of the vision and spandrel elements was calculated [15].
The following Ucw values are obtained using a maximum width of 1.3m and heights of vision and spandrel varying between 1 and 3m. The benefit of SSG versus capped varies depending on the system and configuration between 10 and 25%. This consequently could result in potential savings in operational energy consumption. This exercise was repeated for the representative European toggle system. A triple IGU with a centre of glass value of 0.7W/ m²K and same thickness for both systems was used, to avoid influencing the U value of the frame and the Ψ values. In this case, both the toggle SSG and the mechanically fixed reached similar thermal performance results.
Table 2: Comparison of Ucw for different system configurations , at a fixed width of 1.3m
Test Condition Vision/Spandrel height (m)
System A SSG Ucw (W/m²K)
System A Capped Ucw (W/m²K)
System B SSG Ucw (W/m²K)
System B Capped Ucw (W/m²K)
Case 1 Case 2 3/1 2/2 0.9
1.1 1.2
1.4 1.4
1.5 1.6
1.7
Silicone structurally glazed façades allow energy efficiency targets be be achieved while optimizing material efficiency. More details of this study can be received upon request.
Reuse and Recycle
As explained before, optimizing the material and energy efficiency is crucial to ensure a sustainable design. One aspect which should however not be overseen is the end of life consideration and ensuring reuse and recycle can happen. Due to their small weight, silicone sealants are typically not the primary target of recycling of the façade. Instead the façade industry is assessing how bonded units can be dismantled and their high value components, such as glass or metal, reused. Silicone sealants should not prevent this step. At first sight, there might seem to be a contradiction between the durability of silicone bonded assemblies and the need for disassembly for repair or at end of life. But silicone bonding has specific advantages compared to other adhesives to enable maintenance, reuse and recycling. As opposed to more rigid bonding solutions (eg PU), silicones offer a good potential for disassembly at end of life [16]. The method developed for the dismantling of bonded glazing can further benefit from over 50 years of expertise in façade inspection, deglazing and repair exercises. Thanks to the durability of DOWSIL™ Silicone, it is possible to leave a layer of silicone on the substrate and use this layer to bond again on the frame, provided the origin of the original silicone and compatibility with the new silicone can be confirmed. Should a reuse of glass or frame not be desired then the silicone can be mechanically removed from the disassembled substrates. To close the loop of the lifecycle of a silicone in a façade, Dow is preparing to recycle the silicones reclaimed from the bonding and secondary sealing of the IGU. Several options to reintegrate these silicones into the production line process are currently being evaluated. This process will save raw material usage and also avoid the high energy required for the initial transformation of silica into silicone metal. Similar to other manufacturers, these studies will most
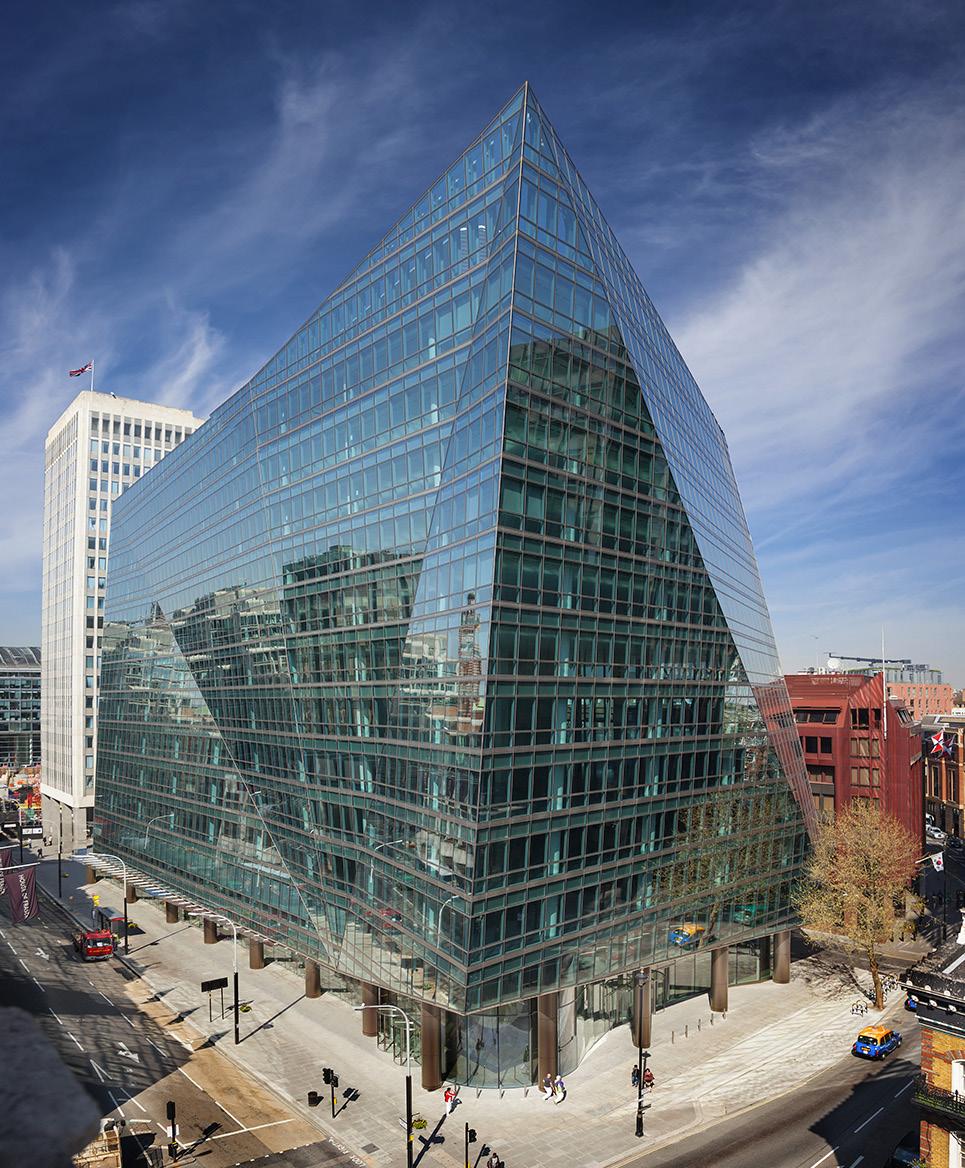
62 Buckingham Gate, London, BREEAM rating 'Excellent'
probably lead to the development of quality criteria requirements to allow injecting recycled silicone in the production. It is indeed crucial to ensure the origin and composition of the waste silicone.
Build tomorrow with carbon-neutrality and Dow Building Science
Dow’s investment into low carbon silicon metal manufacture, which embraces the advantages of backward integration, is just one example of our commitment to environmental, social and governance. Our industry-first carbonneutral silicones program, verified by annual audits, represents an important step toward reducing the carbon footprint of buildings. This program is underpinned by the 50+ years of successful performance of our structural glazing silicones.
Dow’s dedicated project support team, work in close collaboration with architects and consultants on a global basis, to offer support for engineering, design and sustainability.
Please contact us to learn more about Dow’s carbon-neutrality program, documentation and project support tools:
• Life Cycle Analyses (LCAs) • Third party verified ISO 14040:2006 and
ISO 14044:2006 LCA conformance review statements • PAS 2060 Carbon Neutrality – QES documents with details • EPDs • Contribution of carbon neutral silicones to securing green building certification credits/ points • Product specifications for use in submittals • Digital project management tools with integrated carbon-neutrality services on specific projects
Our innovative and performance-enhancing product technology showcase for sustainable and modern building design is available 24/7 at dow.com/buildingscienceconnect and documentation for project submittals may be downloaded at dow.com/submittalsemea. For further information, please visit dow.com/ carbonneutralsilicones.
50 Years ?, in Proceedings of Glass Performance
Days (2017) 13. EN ISO 10456: 2007, Building materials and products — Hygrothermal properties —
Tabulated design values and procedures for determining declared and design thermal values 14. EN ISO 10077-2:2017, Thermal performance of windows, doors and shutters — Calculation of thermal transmittance — Part 2: Numerical method for frames 15. Bauwerk, Thermal modeling Report reference dowcorning_211101_02b_en, 2022 16. Personal communication to the authors by Prof.
Mauro Overend, TU Delft
Acknowledgement
The authors wish to thank Meinhardt Façade Technology Singapore for the fruitful discussions on structural calculations
Disclaimer
NOTICE: No freedom from infringement of any patent owned by Dow or others is to be inferred. Because use conditions and applicable laws may differ from one location to another and may change with time, Customer is responsible for determining whether products and the information in this document are appropriate for Customer's use and for ensuring that Customer's workplace and disposal practices are in compliance with applicable laws and other government enactments. The product shown in this literature may not be available for sale and/or available in all geographies where Dow is represented. The claims made may not have been approved for use in all countries. Dow assumes no obligation or liability for the information in this document. References to “Dow” or the “Company” mean the Dow legal entity selling the products to Customer unless otherwise expressly noted. NO WARRANTIES ARE GIVEN; ALL IMPLIED WARRANTIES OF MERCHANT.
Literature
1. Global Silicones Council, Silicon-Chemistry Carbon
Balance, An assessment of Greenhouse Gas
Emissions and Reductions, https://www.silicones. eu/wp-content/uploads/2019/05/SIL_execsummary_en.pdf, accessed 25/2/2022 2. https://www.ista.com/corporate/company/ content-world/co2-price-in-germany-what-canwe-expect/ accessed 25/2/2022 3. The Aluminium Association, Aluminum Design
Manual (ADM): 2010 4. American Society of Civil Engineers, ASCE/SEI-7: 2016 - Minimum Design Loads and Associated
Criteria for Buildings and Other Structures 5. Meinhardt Façade Technology, Curtain Wall
Calculation of captive & SSG system report, 22
February 2022 6. Wolf A.T., Stiell J., Plettau M., Structural Bonded (Adhered) Window Systems, Conference Paper 7. Pascual C., Montali J., Overend M., Adhesivelybonded GFRP-glass sandwich components for structurally efficient glazing applications,
Composite Structures, Volume 160, 15 January 2017, Pages 560-573 8. EN 13830:2015+A1:2020, Curtain Walling- Product standard 9. Carbary L.D., Albert F., A Thermal Modeling
Comparison of Typical Curtainwall Glazing Systems, in Proceedings of Glass Performance Days (2007) 10. Carbary L.D., Hayez V., Wolf A.T, Bhandari M.,
Comparisons of Thermal Performance and Energy
Consumption of Facades Used in Commercial
Buildings, Proceedings of Glass Performance Days (2009) 11. www.feica.eu accessed 25/2/2022 12. Wolf A.T., Recknagel C., Wenzel N., Sitte S, Structural
Silicone Glazing: Life Expectancy of more than
Valérie Hayez PhD
Valérie Hayez is Global Façade Engineering & Architectural Design Engineer for High Performance Building Solutions at Dow, based in Belgium. She provides technical service to the design community, including façade system manufacturers, architects and engineers and communicates industry needs to Dow‘s Research and Development Community. Valérie has developed a broad expertise in façade engineering, including structural performance, fire safety, thermal or acoustic insulation and is active at standardization level. She holds an MSc and a PhD in Applied Sciences (electronics and optics) from the University of Brussels.
Jayrold Bautista
Jayrold Bautista is an Associate TS&D Scientist for Dow based in Singapore. He has over 15 years of experience in the built environment, providing technical, application and consulting expertise to stakeholders in the curtain wall and construction industry. He has helped many clients to achieve energy efficient, durable, well-designed facades for high-performance building projects with silicone and material science technology. Prior to joining Dow, he worked for a major façade consultancy firm and was involved in some tall building project projects in different parts of the world. Jayrold is a licensed civil engineer and has a degree in BS Civil Engineering from the University of the Philippines.
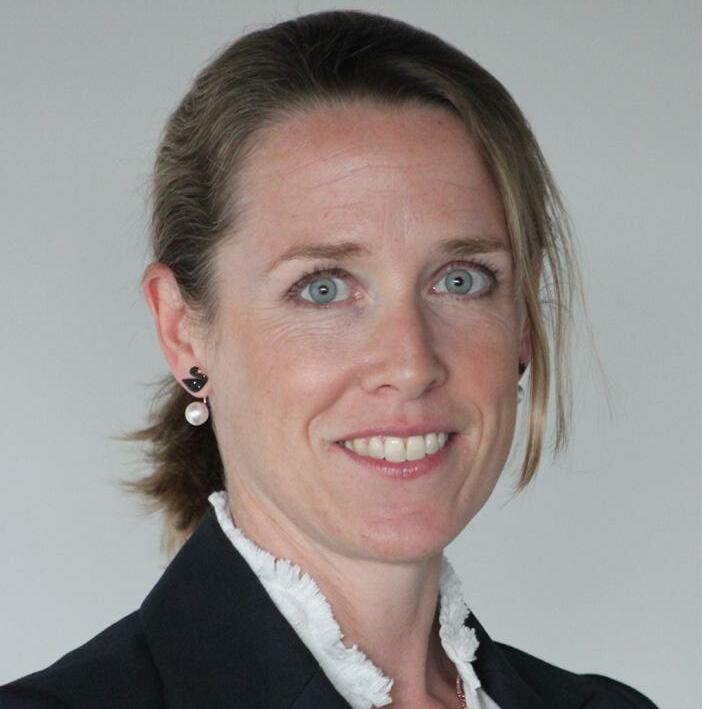
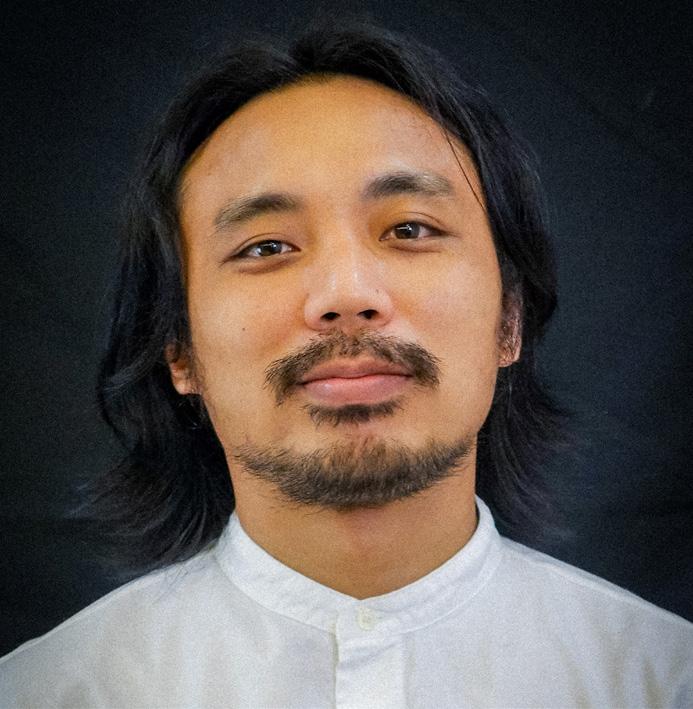
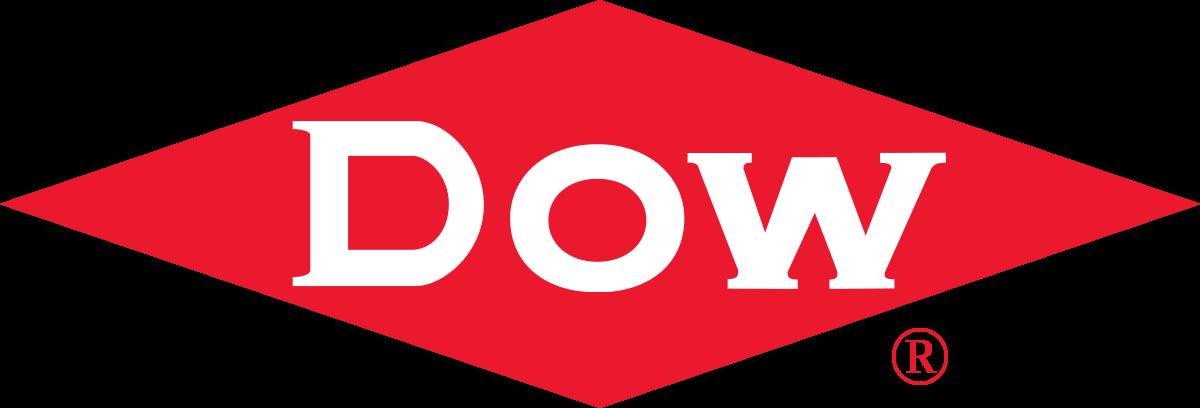
Reprints
Whenever your company products or services are mentioned in IGS, whether it’s an article, case study or new innovation we can produce a tailor-made reprint for you to use in your future marketing and promotional campaigns. Reprints can vary from a single page to multiple page brochures.
To order your reprints simply contact us at the following email address:
nick@intelligentpublications.com
or go to igsmag.com
REFLECTIONS FROM THE UN INTERNATIONAL YEAR OF GLASS 2022 REFLECTIONS FROM THE UN INTERNATIONAL YEAR OF GLASS 2022
Development and Trends of Glass Innovation Under Global Climate Change
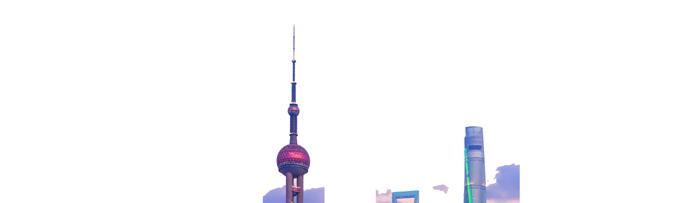
Prof. Peng Shou
Due to frequent extreme weather and climate events brought about by continuous warming of the global climate system, countries around the world are attaching increasing importance to carbon emission reduction. The Chinese government, in an effort to fulfill the new requirements posed by “carbon neutral” development, has been committed to advancing green transformation of the glass industry and actively promoting the development of Building Integrated Photovoltaic (BIPV), glass hydrogen cycle and glass zero-carbon process reengineering, carbon dioxide capture, utilization and storage (CCUS) and other technologies. This article puts forward three proposals for the glass industry to embrace the low-carbon development strategy.
EXECUTIVE BOARDROOM COMMENTARY EXECUTIVE BOARDROOM COMMENTARY
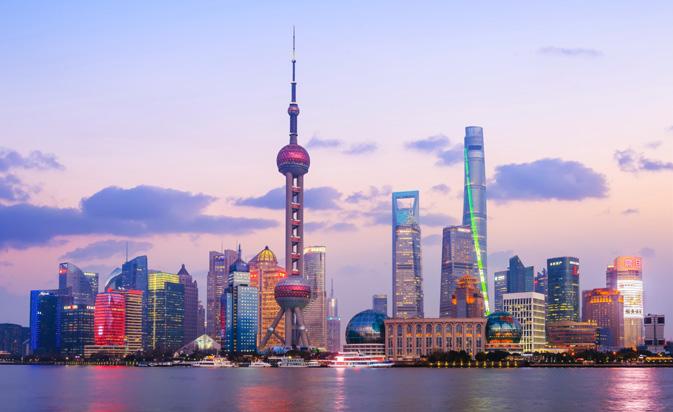
62 intelligent glass solutions | spring 2022 DECARBONIZE NOW! Laura Karnath, AIA, NCARB, Senior Associate and Senior Enclosure Technical Designer, Walter P Moore and Sophie Pennetier, Associate Director, Special Projects, Enclos
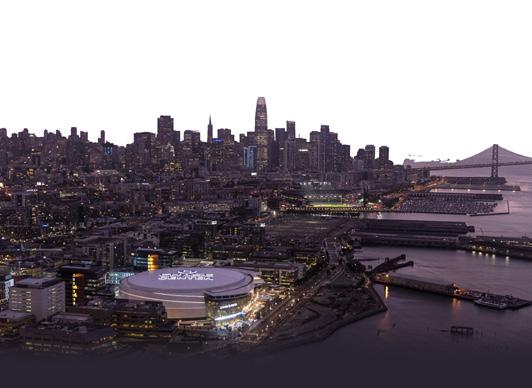
EXECUTIVE BOARDROOM COMMENTARY

THE NEXT FRONTIER IN GLASS FACADE INNOVATION
Walter P Moore and Enclos have worked together on several projects, including the LEED Gold Chase Center in San Francisco, California. Their collaboration on today's high-performance projects has inspired ideas about the future of design assist and bidding. Photo: Jason O'Rear | Golden State Warriors Addressing the costs of carbon through the life cycle of buildings, from manufacturing, transportation, use, and less tangible social costs
8 intelligent glass solutions | spring 2022 EXECUTIVE BOARDROOM COMMENTARY
intelligent glass solutions | spring 2022 9
Design and engineer with less impact
Carbon Neutral Silicones in Façades – a window of opportunity
Shanghai Bund, Shanghai, China. Photo by Edward He on Unsplash
intelligent glass solutions | spring 2022 63
1 Angel Square, Manchester - The building was the first BREEAM rated ‘Outstanding’ regional office building in the UK and is EPC ‘A’ Rated. Courtesy of NOMA.
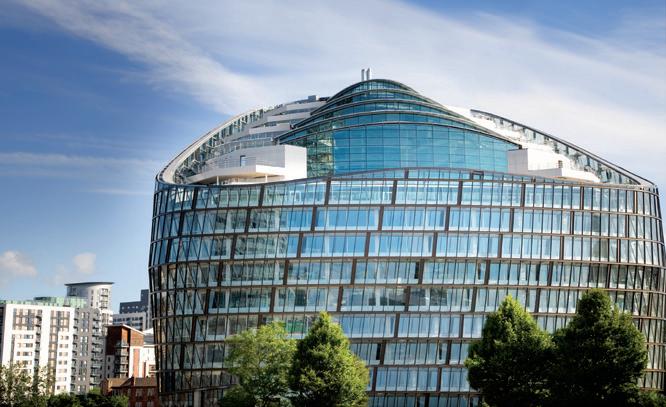
40 intelligent glass solutions | spring 2022 Valérie Hayez, Jayrold Bautista
intelligent glass solutions | spring 2022 41