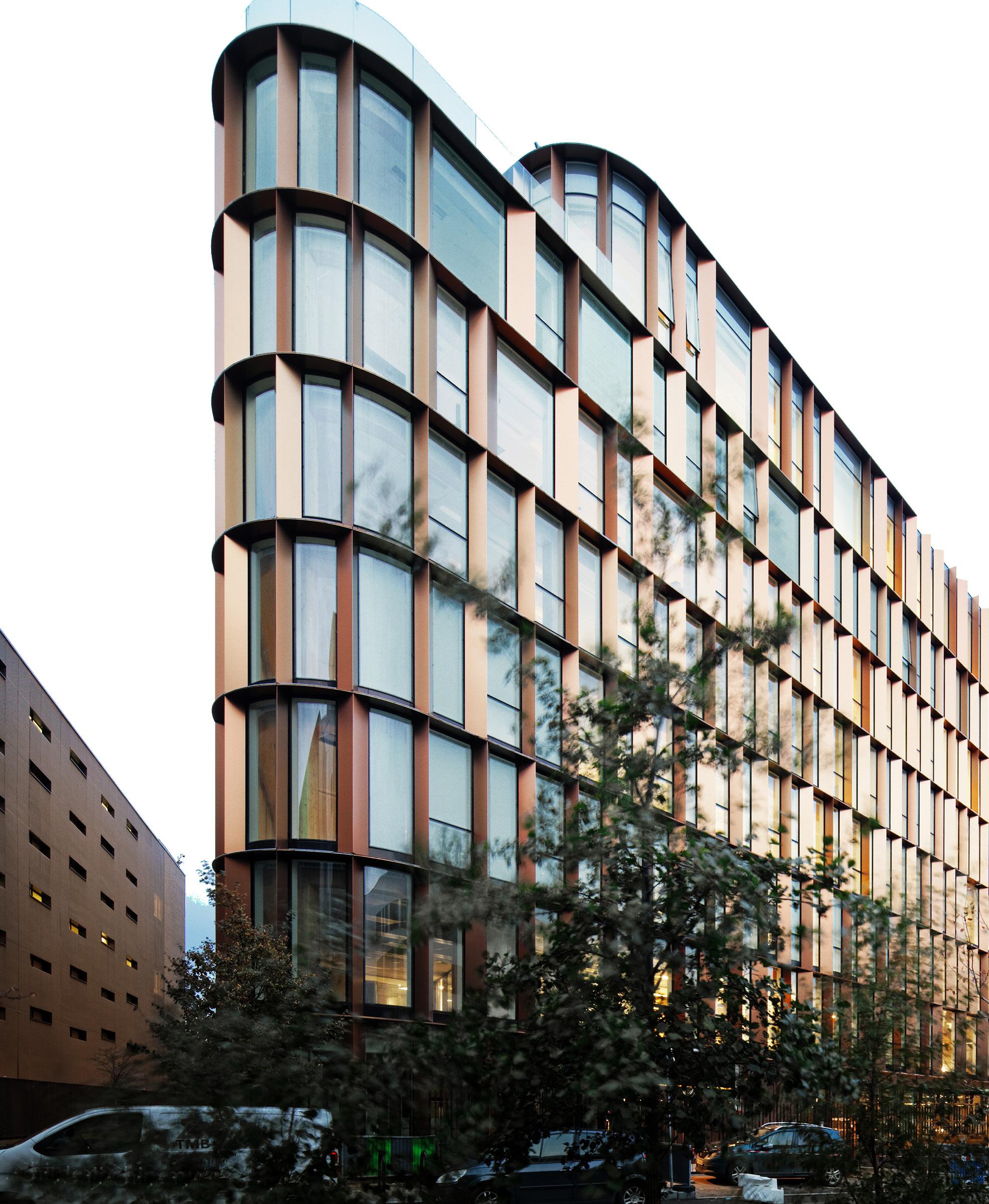
38 minute read
FLEXIBLE SPACERS: MORE EFFICIENCY IN THE
FLEXIBLE SPACERS:
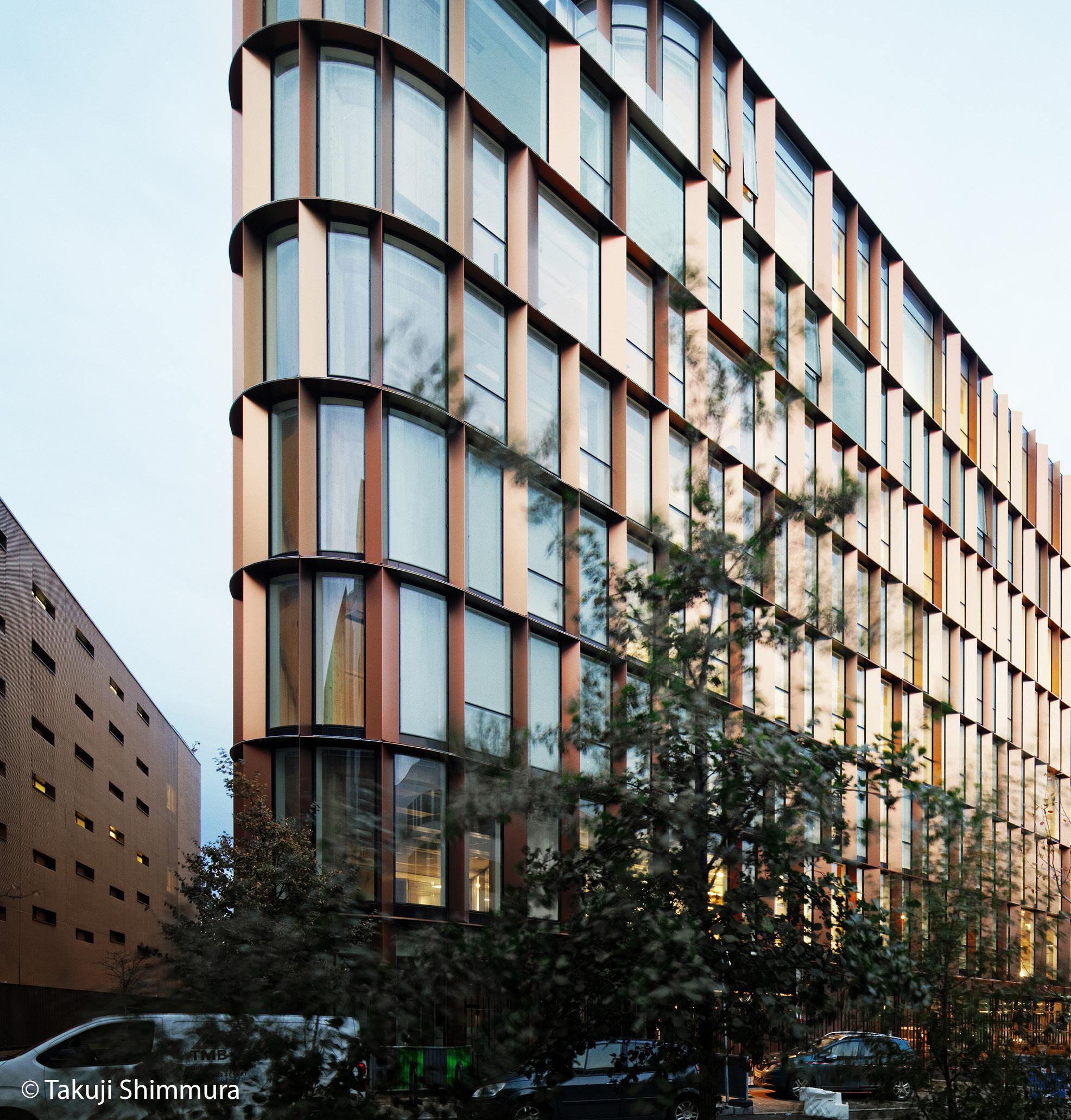
Advertisement
FLEXIBLE SPACERS:
More efficiency in the manufacturing of insulating glass
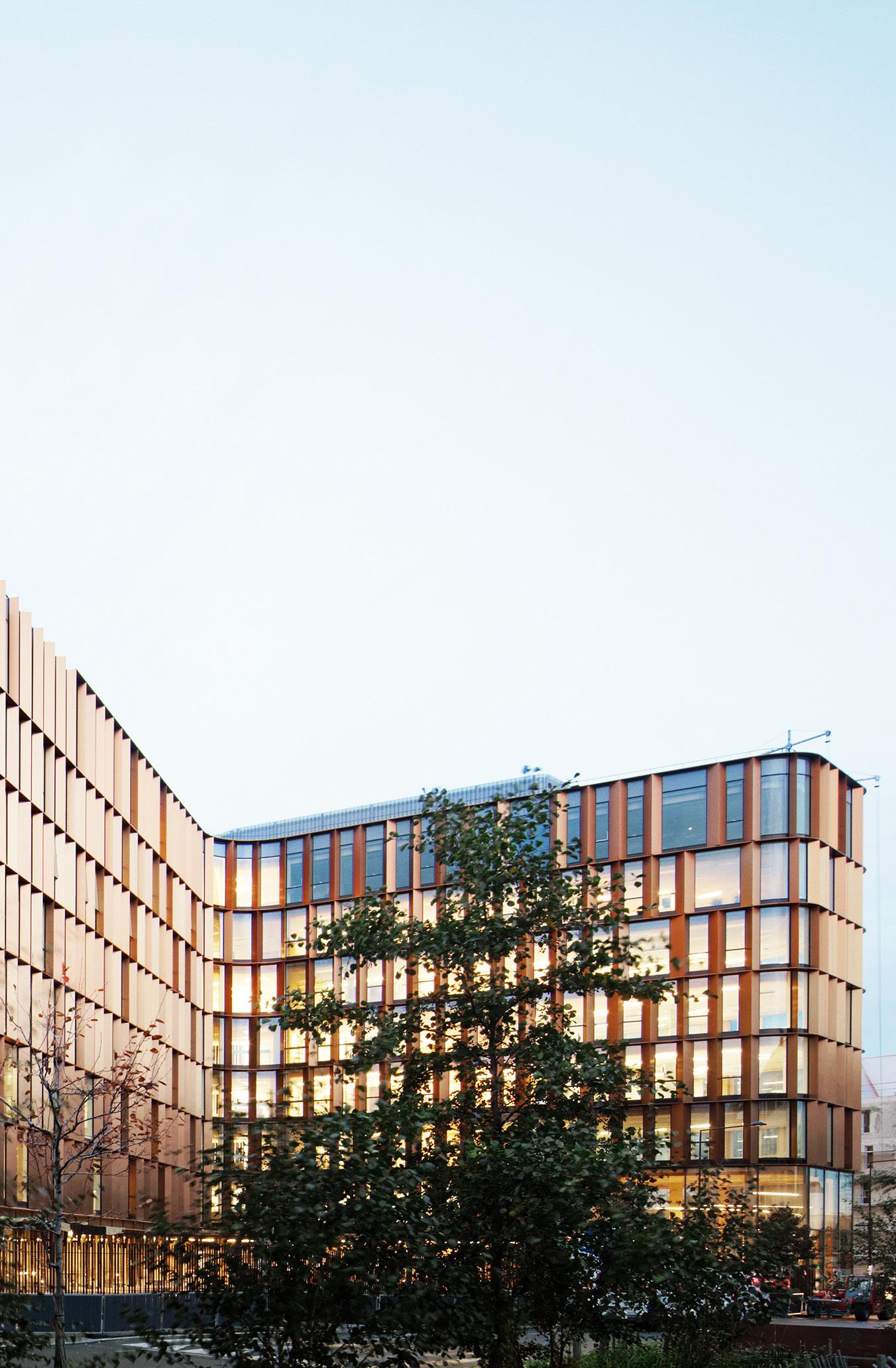
The warm edge insulating glass is a technically mature product for a highly competitive market that is characterised by low margins, a shortage of skilled workers and cheap imports, and also currently by supply bottlenecks and rising material costs. Christoph Rubel, European Technical Manager at Heinsberg’s Edgetech Europe GmbH, explains which levers the processor and manufacturer of insulating glass has got in order to increase efficiency and product quality in this volatile environment, using the Super Spacer® flexible insulating glass spacer system as an example.
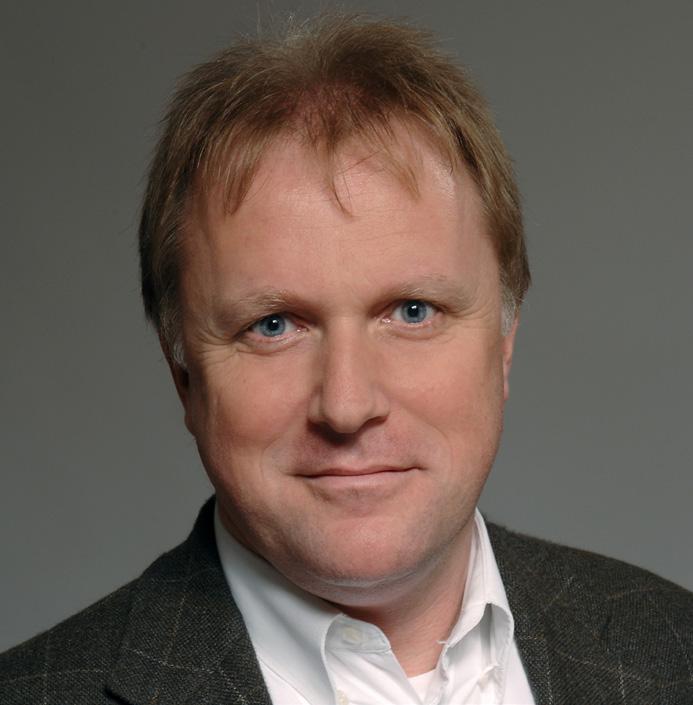
Christoph Rubel
The Scandinavian countries pioneered triple glazing and the rest of Europe has followed suit. In Switzerland and Austria, high-quality energy-saving windows have now more or less become the norm and in Germany, according to current information provided by the industry associations, around three quarters of window units in new residential and non-residential buildings are designed with triple glazing. There is a similar proportion of thermally optimised spacers. They prevent the formation of thermal shortcuts at the edges of the insulating glass through which valuable energy is lost. Anyone who decides in favour of a warm edge with a passive house certificate - whether as a processor, architect, builder or building owner - is opting for a mature, future-proof product, and to a large extent no longer has to compare the PSI values at the third digit after the decimal point. All these products make a significant contribution towards low U-values and thus lower heating and cooling costs as well as an improved indoor climate. In addition, condensation and mould formation at the edge of the glass virtually no longer occur.
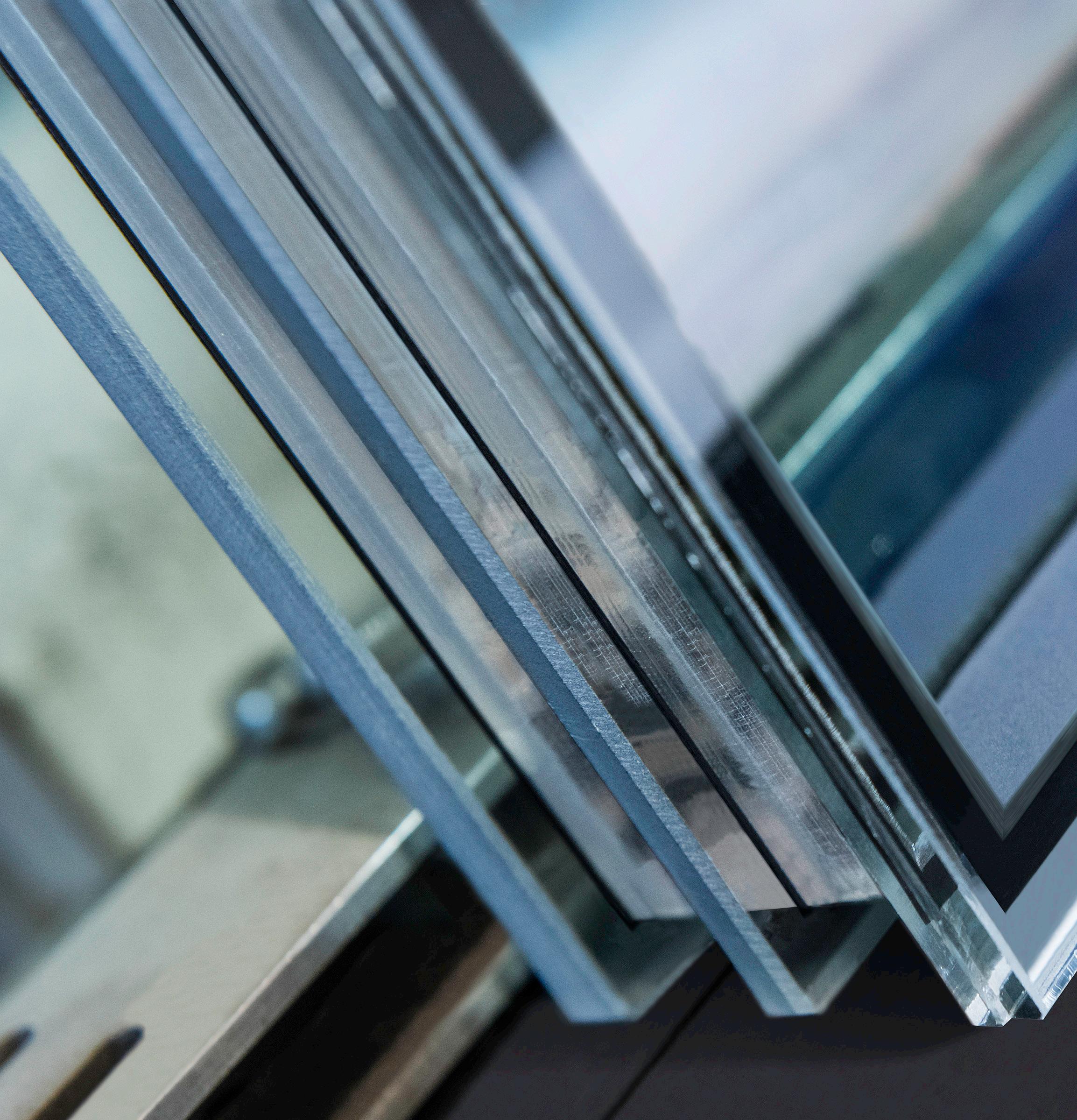
Lever 1: The structure of the edge seal
The expression, "the whole is more than the sum of its parts" also applies to the edge seal. The spacer and its desiccant capacity, in combination with primary seal and secondary sealant, are an essential element in ensuring the water vapour and gas impermeability and energy performance of the insulating glass unit throughout its entire product life, which is widely believed to be at least 25 years.
The various spacer technologies on the market can be roughly broken down into two categories, which, entail considerable differences where the manufacturing of the insulating glass is concerned: rigid hollow profiles that are filled with desiccant and assembled to form spacer frames, as well as flexible systems that already contain a desiccant. Flexible thermoplastic spacers made of Polyisobutylene are extruded from a barrel onto the glass pane while still hot; spacers made of silicone structural foam come prefabricated from the roll and are also applied automatically along the edge of the glass. Therefore, when using flexible spacers, the production steps of cutting, bending and assembling as well as desiccant filling and separate butyl application outside the insulating glass line are eliminated.
Super Spacer® warm edge spacers ensure high levels of manufacturing precision and quality, especially for large-format or triple insulating glass units. With Super Spacer® set in parallel down to the last millimetre, it guarantees a visually appealing and above all tight edge seal. Super Spacer® keeps the panes exactly at a distance and ensure that insulating glass is durable even after decades.
Spacers must be resistant to wind and climate loads, UV radiation, temperature as well as mechanical stress and form a permanent bond with the respective sealants such as Polyurethanes, hot-melt butyl or silicone. Gas must not be allowed to escape from the interior, nor must moisture be allowed to penetrate through the edge seal to the inside of the insulating glass, and last but not least, the edge seal is also responsible for ensuring the structural integrity of glass constructions in the facade.
Super Spacer® structural silicone foam design makes the edge seal flexible, cushions the pressure on it so to speak and the risk of breakage for the glass is significantly reduced. Less stress in the edge seal results in an improved seal tightness and durability of the glass units. The full or partial offsetting of the loads acting on the edge seal is an advantage that especially desiccant integrated preformed flexible spacers, such as Edgetech Super Spacer® TriSealTM can claim to possess by comparison with rigid spacers.
The manufacturer proves the material properties by means of corresponding tests. We at Edgetech/Quanex have, for instance, tested the shear load capacity for the quick handling of the glass units within the factory. An insulating glass unit measuring about 6 x 3 metres wide and 6 mm each thick, was only bonded by means of the integrated primary, high-strength acrylic adhesive. The unit was lifted on one supported glass lite using vacuum cups and the spacer did not give a single millimetre during the 30 minutes test phase. The test demonstrates: The additional adhesive layer reduces the stress on the primary PIB seal, which thus functions exclusively as a water vapour and gas barrier to the secondary seal.
In the so-called Dade Country Hurricane Test (an US based test), the units withstood wind speeds of 350 km/h where a positive wind

The structural foam of Super Spacer® is compatible with all quality brand insulating glass sealants such as hot melt butyl, Polyurethanes, 2-part Silicone and Polysulfide. The edge seal is responsible for ensuring the structural integrity of glass constructions in the facade. The elastic silicone structural foam of the Super Spacer® makes the edge seal flexible, cushions the pressure on it so to speak and the risk of breakage for the glass is significantly reduced compared to rigid spacer bars. Less stress in the edge seal results in an improved seal tightness and durability of the glass units. With Super Spacer®, the application process makes sure the spacer is perfectly aligned to create a perfect parallelism. Every corner at the edge seal has a perfect 90 degrees angle, no matter whether it is processed manually or automatically. By cutting straight 90° mitres out of the flexible spacer, corners can be cut very precisely and very accurately into sharp 90° corners.
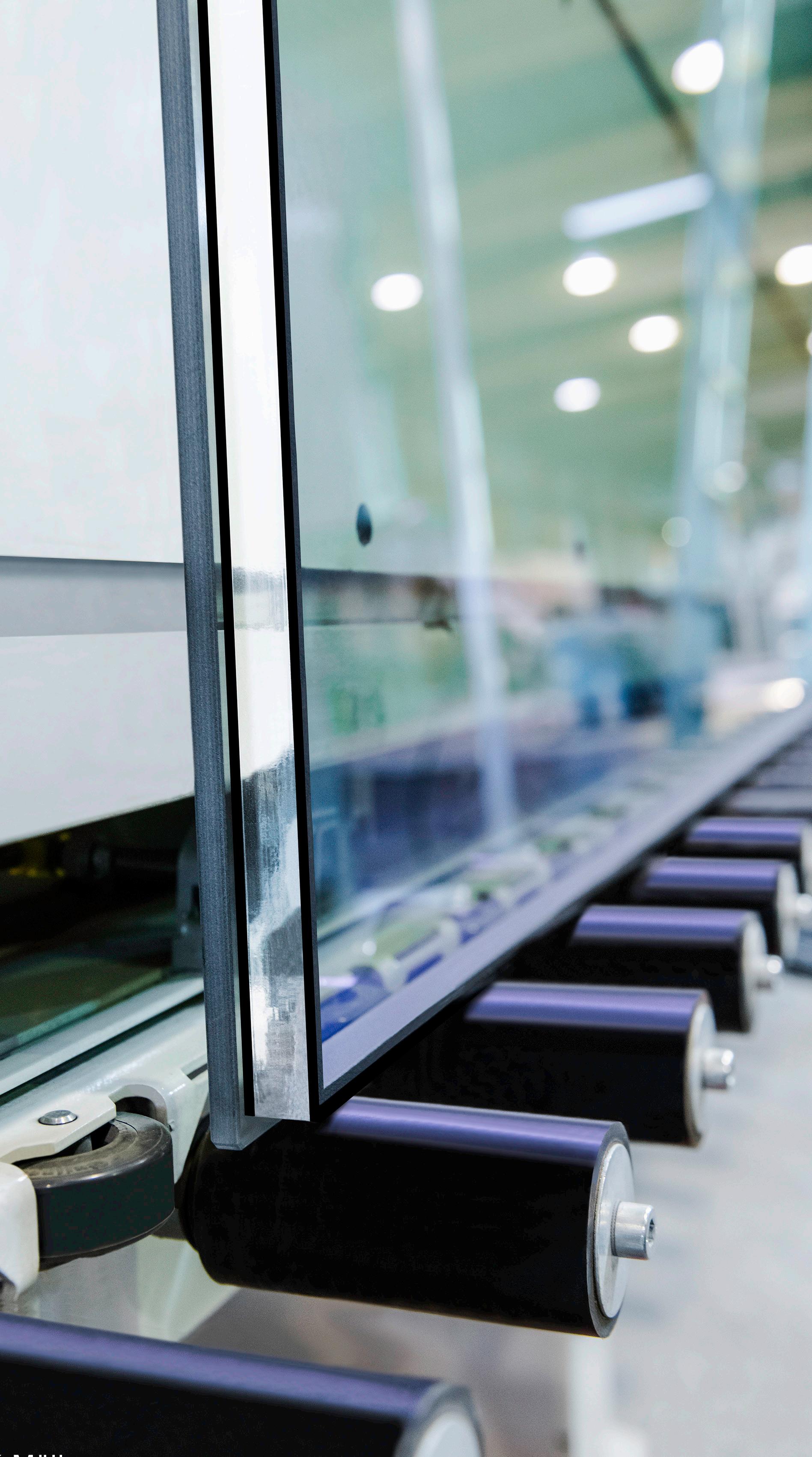
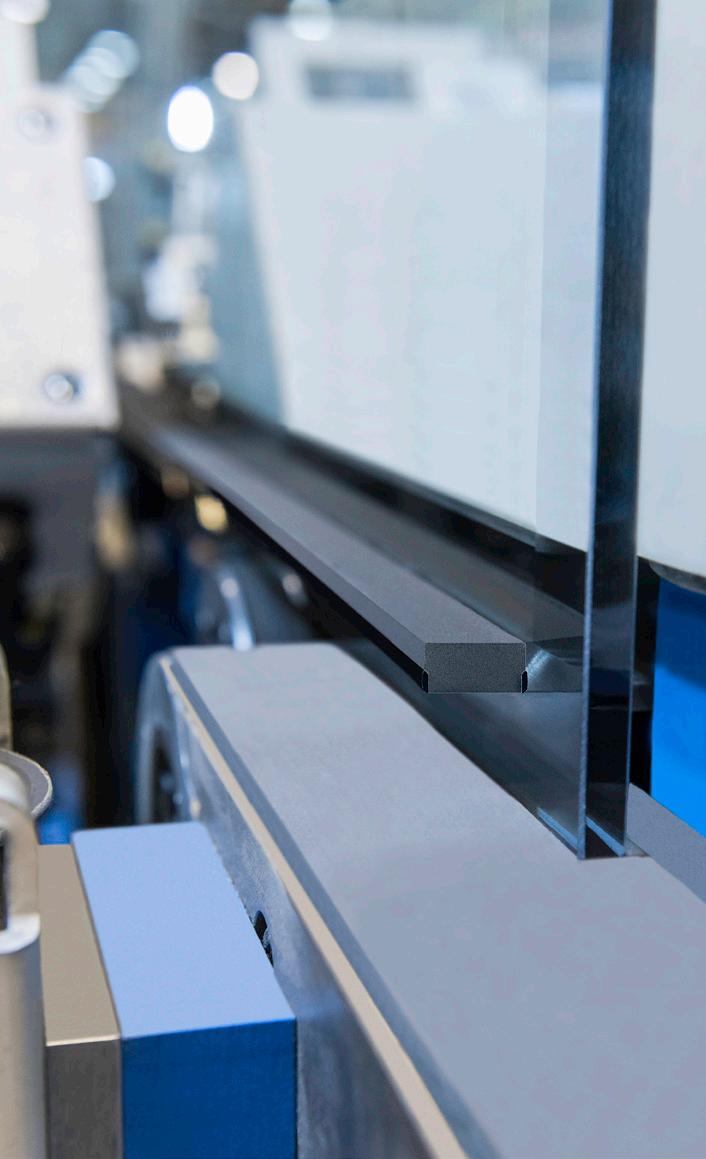
Flexible spacers from the roll are typically applied automatically via a double-head applicator, so the majority of set-up times are eliminated, and the line is flexible to the maximum possible extent in terms of the insulating glass dimensions, glass type, number of panes and spacer colour and widths. The efficiency is enhanced by the easy 3-step process for creating a more fluid production process.
pressure was present and of almost 400 km/h where a suction effect was evident. The test did not end in a unit failure, but was stopped as the test stand was not able to produce higher wind loads.
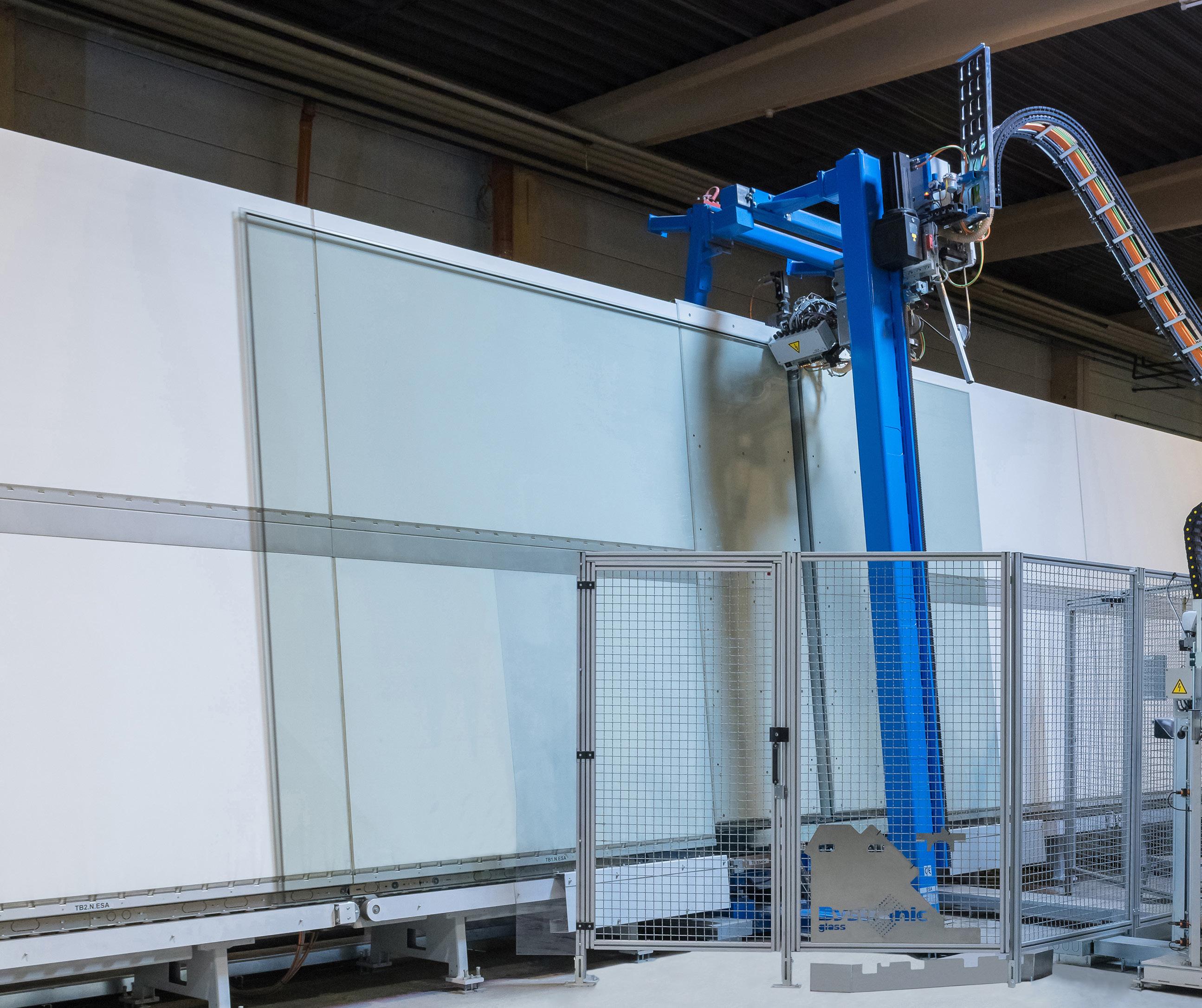
Lever 2: Variability and flexibility
A mix of series production and customised production as well as automation and manual activities, for instance for the handling and assembly of panes and spacers, characterises the situation in many European insulating glass companies. The trend towards large panoramic window panes as well as freeform and curved glazing further increases the complexity of the variant production that is typical for the industry. This traditionally meant that a large number of different spacer systems had to be kept in stock: ranging from inexpensive stainless steel profiles to rigid hollow plastic profiles on one side and flexible spacers on the other side, which reveal their benefits especially in the field of automated production. At Edgetech/Quanex we have always embraced a philosophy of "one for all". Super Spacer® flexible foam spacers are suitable for manual application in custom-made products, automatic processing in the edge seal of classic windows with and without internal or externally applied muntin- and glazing bars, insulating glass units in structural glazing facades and also for hot and cold formed curved insulating glass sections. Furthermore, the structural foam is compatible with all common sealants such as hot melt butyl, Polyurethanes, silicone and Polysulphide. Last, but not least, insulating glass units with Super Spacer® can be handled, packed and stored outdoors immediately after they have been processed, as the integrated desiccant dries down the interpane cavities very rapidly.
The additional price for Super Spacer® is just a few cents per running metre. Therefore, Edgetech recommend that any investment decision should take account of the considerable potential for savings elsewhere. Differences in energy consumption levels brought about by the various spacer technologies are also becoming increasingly important at a time of rising energy prices.
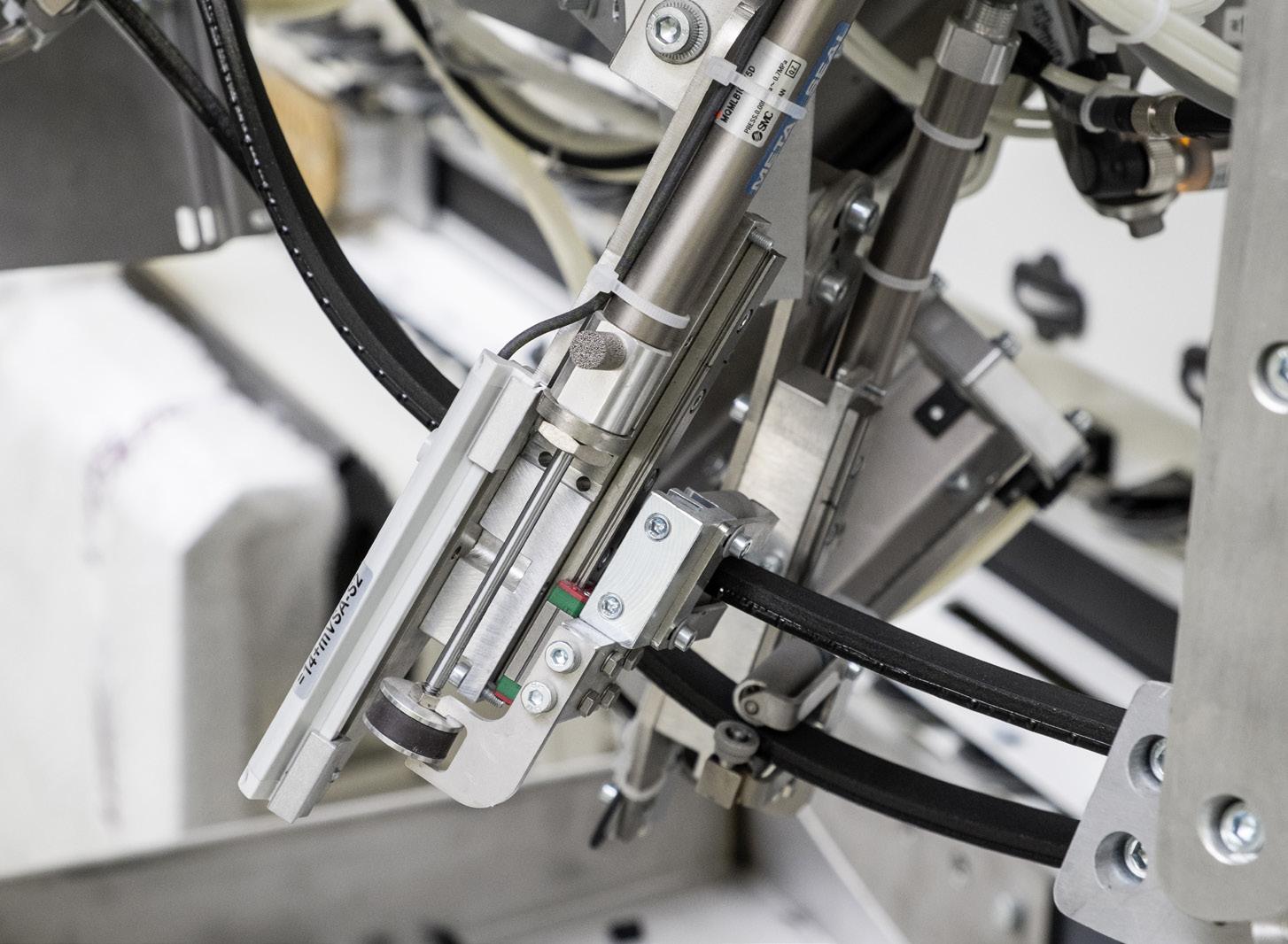
Lever 3: Automation
Since the era of Henry Ford, the idea of "economies of scale" has become second nature to us. We reduce our unit costs through greater output. According to this maxim, automation to increase efficiency is only worthwhile for larger production volumes. However, digitisation is now making precisely the opposite possible for the production of insulating glass: We make use of economies of scope. Costs are reduced by optimising the production landscape, processes and infrastructure so that we can use them to manufacture related products all the way down to a batch size of 1. Producing more quickly, more efficiently and in a more customised manner is also becoming a decisive
Super Spacer® can be applied in various widths (sizes 3 mm to 32 mm insulating glass cavity of which 8 to 28 mm can be applied in automation) via a double-head applicator without interruption. Due to the fact that the flexible Super Spacer® is already factory-equipped with desiccant, barrier film and structural acrylic adhesive, it supports automated processes and ensure high levels of manufacturing precision and quality, especially for large-format triple-glazed insulating glass units.
@ Edgetech competitive advantage for SMEs. In the best case, the insulating glass line does not care whether a rectangular pane is followed by a trapezoidal one, or a triple insulating glass unit follows a double insulating glass unit, the ERP system provides all the necessary information and takes care of the digital organisation of the order processing, work preparation, material provision, handling and logistics. This variety is theoretically unlimited and forces us to reduce complexity as far as possible.
Broken down in terms of our topic of spacers, flexible spacers also offer the greatest potential here. Fewer machines and the elimination of space-consuming magazines for the provision of the different six-meter-long spacer profiles and the elimination of handling steps reduce the need for machinery, space requirements, storage requirements and personnel requirements compared to the processing of rigid spacers. Flexible spacers are applied directly in the insulating glass line. Super Spacer® can be applied in various widths via a double-head applicator without interruption and, above all, down to the last millimetre and with no hand touching the glass between the start section of the washing machine and the pick off section behind the sealing robot. Due to the fact they are already factory-equipped with desiccant, barrier film and structural acrylic adhesive, they support automated processes and ensure high levels of manufacturing precision and quality, especially for large-format triple-glazed insulating glass units.
@ Takuji Shimmura
CASE STUDY 1: "ØKERN PORTAL" AND "THE CURVE" SCORE WITH SUSTAINABILITY AND AESTHETICS
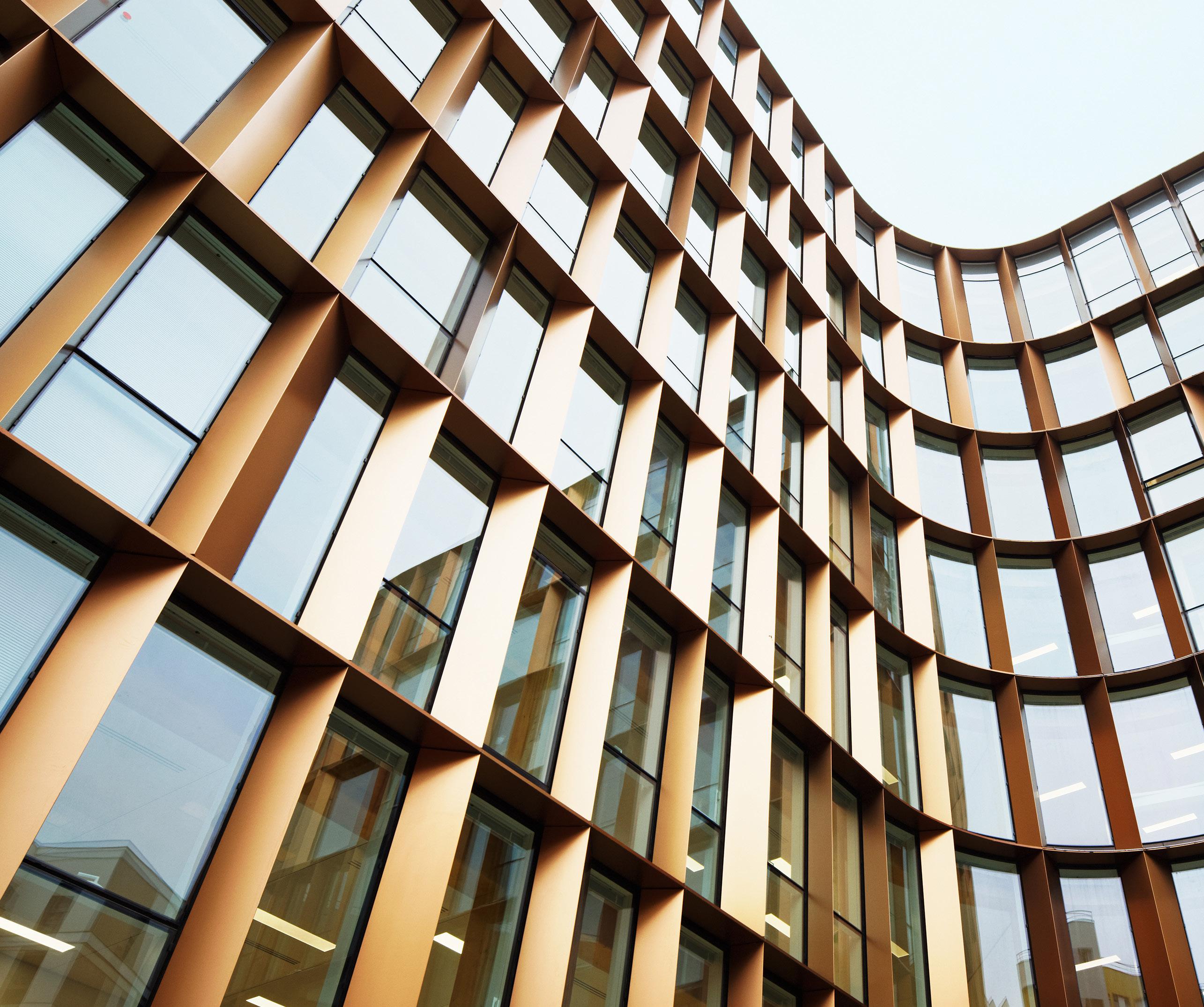
SUPER SPACER® WARM EDGE IN TWO BREEAM-CERTIFIED PROPERTIES
Resource-saving materials are increasingly competing with classic reinforced concrete and facades made of primary aluminium. The energy-efficient Super Spacer® warm edge spacers have been installed in two showcase projects whose main materials could not be more different, but which have an enormous amount in common when it comes to the circular economy. What's more, they exhibit a very unique aesthetic that harmoniously integrates architecture and nature.
Since January 2021, all new buildings in the EU have to meet the standard of a "lowest energy building" and should cover their energy needs with renewable energies wherever possible. But energy efficiency is only one side of the coin when it comes to sustainable building. On the other side, the discussion about grey energy as well as the circular use of the raw materials and materials used is gaining more and more momentum. It is not only from politics that sustainable construction is receiving tailwind. Tor-Christian Møglebust, partner in the Oslobased architecture firm DARK Arkitekter, tells us in an interview that the first major tenant of the Økern Portal office complex designed by DARK had explicitly insisted on BREEAM Excellence certification.
Økern Portal with facade made of recycled aluminum
Økern Portal is one of the largest development projects ever realized in Norway. But it is also outstanding because of its striking 14,600 m2 facade made of recycled aluminum. Aluminum producer Hydro's CIRCAL® 75R alloy, made from at least 75 % end-of-life aluminum, has a carbon footprint that is second to none: the guaranteed carbon footprint under 2.3 kg of CO2 per 1 kg of aluminum is 84 % lower than the average for primary extraction and is equivalent to the CO2 released when wood is burned. With WICTEC EL evo from Wicona as the main facade and the Sapa 4150 facade system for the lower two floors, two brands from the Norwegian aluminum specialists are installed in the showcase building.
The client and owner is Oslo Pensjonsforsikring. The complex offers 80,000 m2 of space for
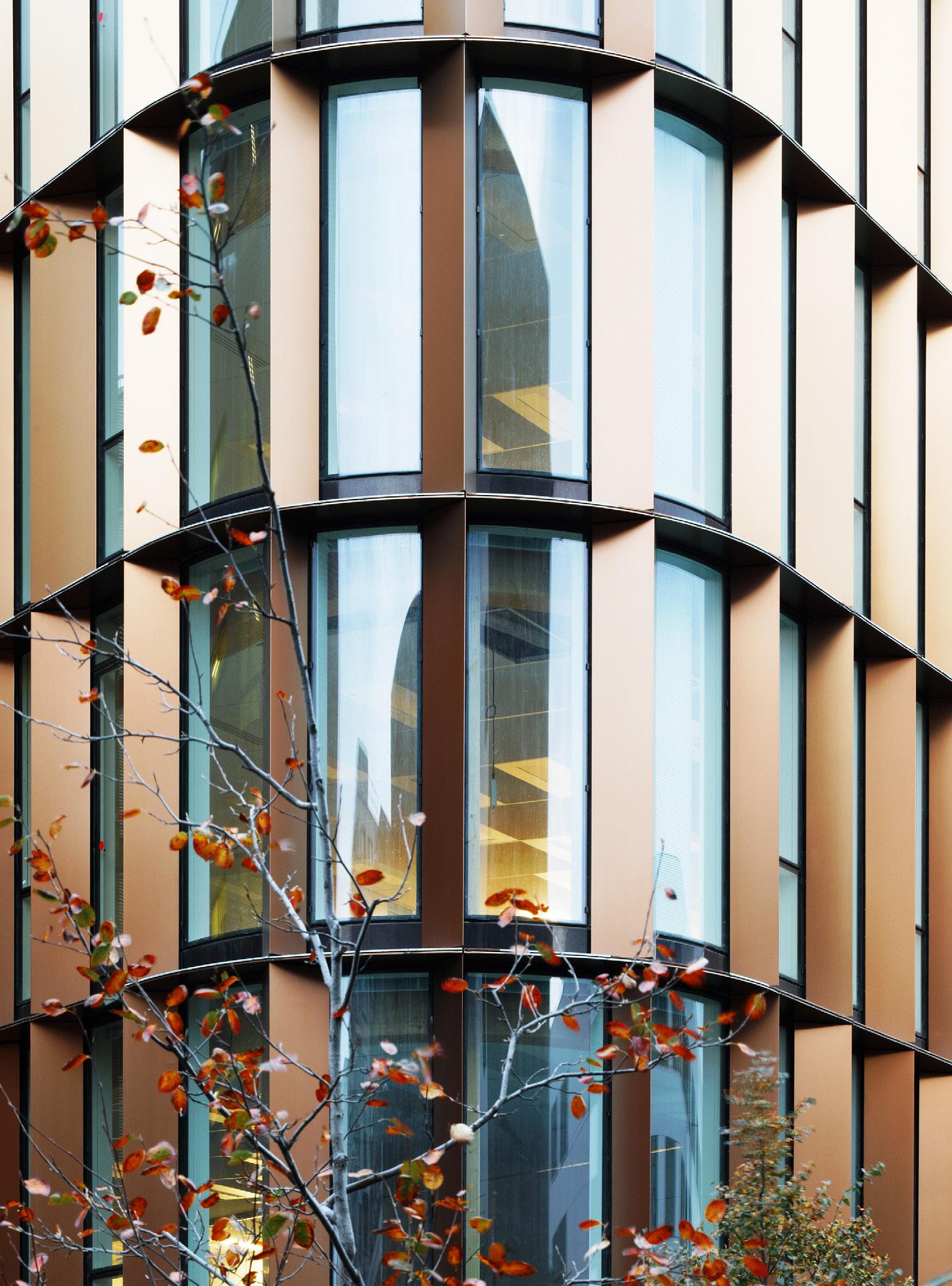
@ Takuji Shimmura @ Takuji Shimmura
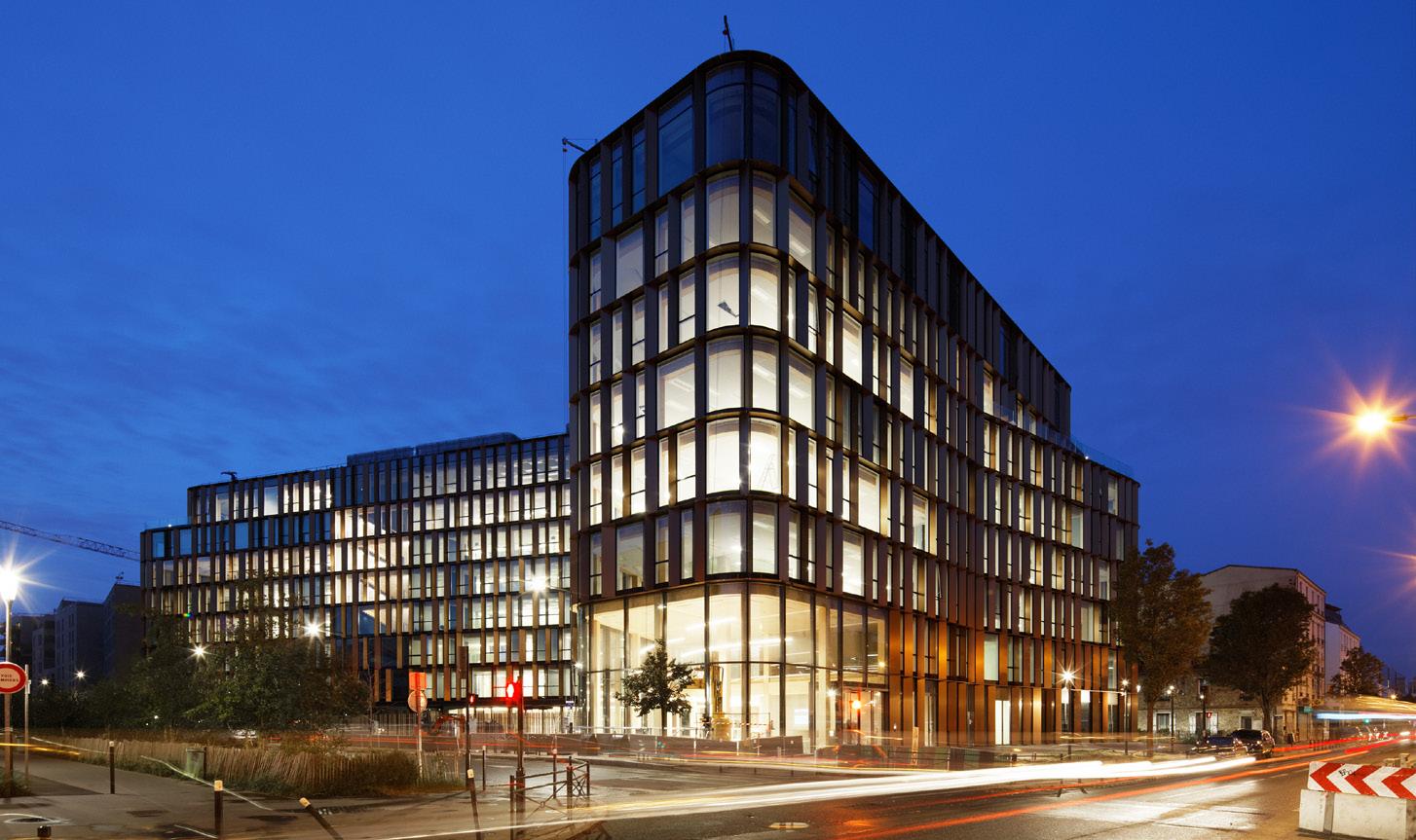
offices, a hotel, common areas and a food court. Urban gardening, beehives and a running track are planned on the green roofs. Despite the size, the DARK Arkitekter office has managed to breathe lightness into the design. The building stands on stilts to allow for fluid transitions between the public park and the commercial spaces. The aesthetics of the facade, installed by Staticus, establish a connection with the surrounding nature through the arrangement of its 1,588 trapezoidal aluminum elements. Vertically running bands are reminiscent of tree trunks, while the faceting of the horizontal "leaf elements" creates plays of light and shadow and emphasizes the liveliness of the building envelope. The sophisticated system of solar shading, opaque surfaces and double glazing
@ Roger Holmen
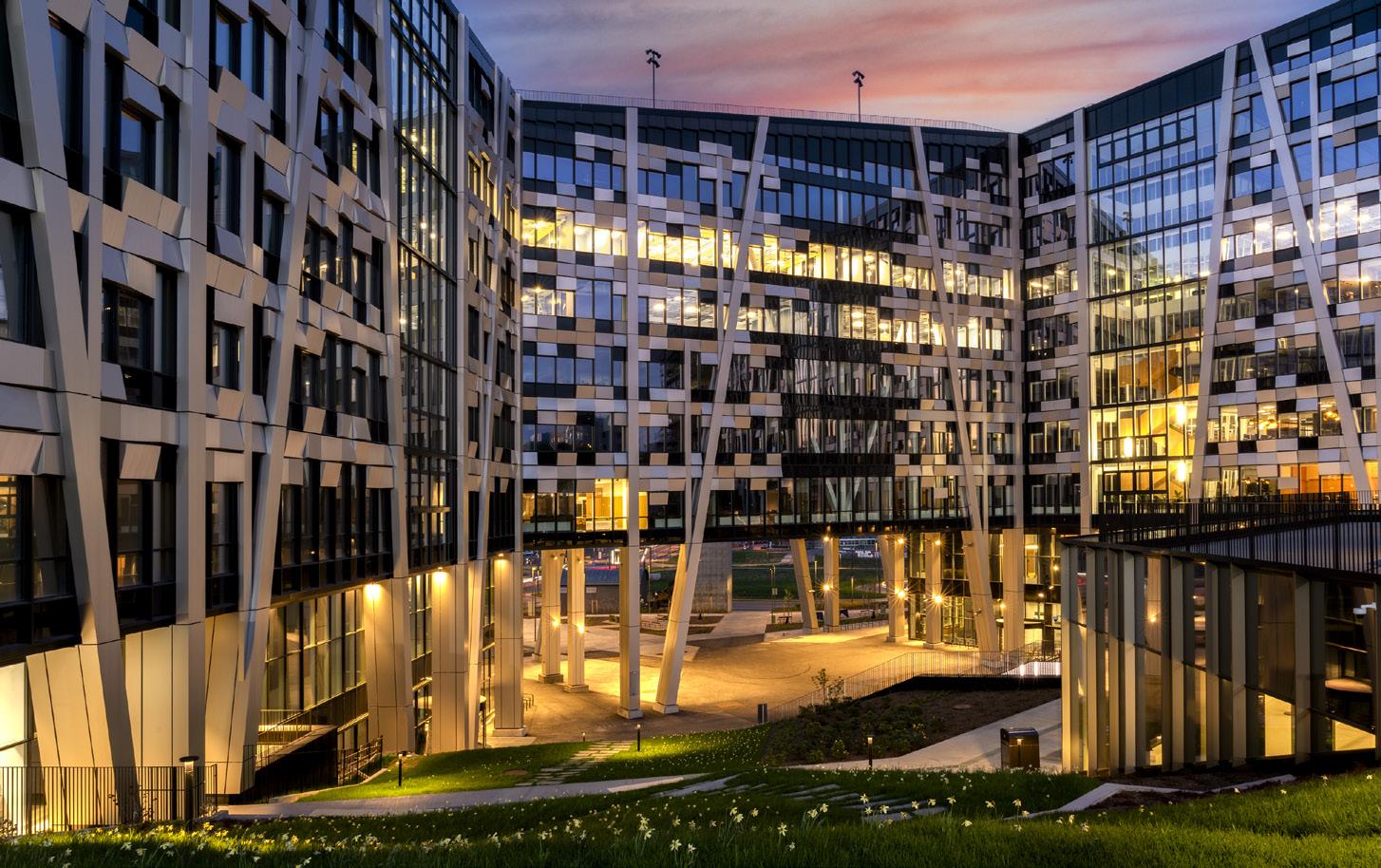
ensures that the facade meets all regulations and energy efficiency requirements.
Insulating glass on demand on the first two floors
The first two floors, executed by H-fasader with a Sapa standard facade profile, face in six different directions. Glaseksperten A/S from Hjørring, Denmark, therefore customized the total of 3,000 m2 of triple glazing to meet the different requirements in terms of sound insulation, thermal insulation, safety and space utilization. Among other things, insulating glass with varying sound insulation values between 32 and 39 dB was installed. In addition, invisible sound insulation for walls and ceilings ensures that the retail and commercial areas can be used for a wide range of purposes.
"The project was challenging," explains Kent R. Beresford, Sales Manager Norway at Glaseksperten. 12 different glass assemblies were produced in sizes up to 1,200 by 3,000 mm, and the specification for the U-value was 0.6 or less. The outer panes have a highly translucent, color-neutral solar control coating, Sunguard SuperNeutral 70S, while the inside is tempered or laminated glass in various thicknesses. To achieve a thickness of 55 mm for each unit, Super Spacer® T-Spacer™ Premium spacers in widths of 14, 16 or 18 mm were changed accordingly during production in an automated process. "Super Spacer is our preferred warm edge for demanding sustainability projects such as the Økern Portal due to its excellent energy performance. In addition, we always ensure the required precision in spacer application, even under high deadline pressure," adds Glaseksperten Sales Manager Jess Gregersen.
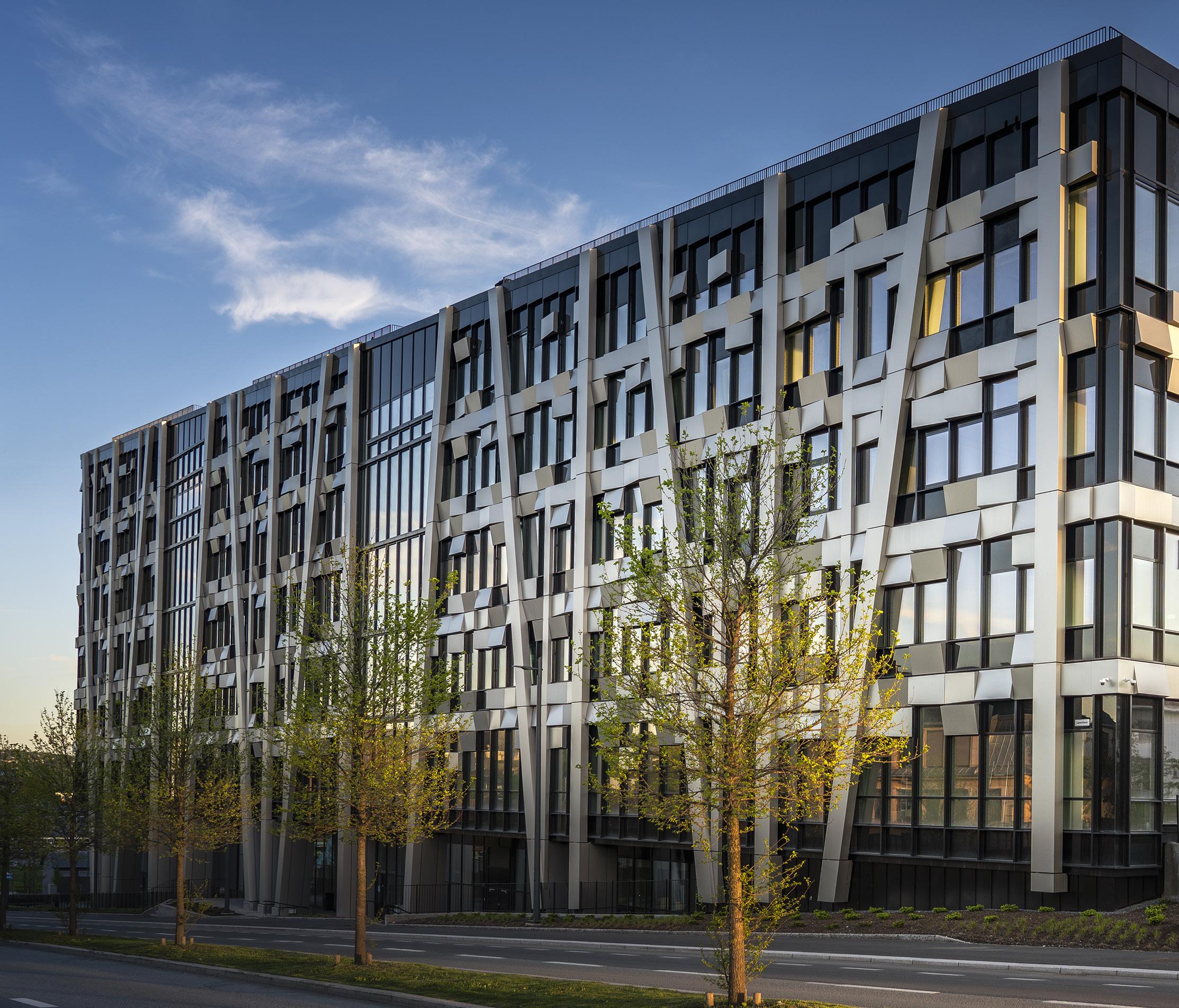
Saint-Denis becomes the secret wood capital of France
When, in the 1960s, the A1 highway cut through the historic royal road that led from Paris to Saint-Denis Cathedral, the industrial city in the north of Paris finally became a banlieue. The royal city, which made history as the cradle of Gothic architecture and the burial place of the French royals, and where the famous Wagon-Lits dining cars were once built, degenerated with the decline of the industrial region into a problem zone with prefabricated housing. But in the shadow of the Stade de France, Saint-Denis is gradually softening the boundaries between the banlieue and Paris. Efforts are being boosted by numerous construction and infrastructure projects for the Olympic Games. Well-known media and service companies have settled here and, according to the city planners, a lively quarter for living and working is being created, which is also developing into a stronghold of French timber construction. For the Olympic Village, which will be built in Saint-Denis by 2024, all buildings under eight stories must be constructed in wood, and taller buildings must at least be designed to be as low-carbon as possible. Thanks to its natural insulating properties, its function as a natural CO2 reservoir and its ease of material recycling, wood from sustainably managed regional forests is an ideal ecological building material. Factory-prefabricated timber frame elements also make timber construction projects increasingly economical compared to classic reinforced concrete construction.
Another sign of the new beginning is the 30-hectare eco-district ZAC de la Montjoie in the city center, where particularly strict specifications apply for the promotion of biodiversity and the use of sustainable materials such as wood. In 2020, BNP Paribas Real Estate implemented one of the largest, large-scale European projects in timber construction here with the 7-story office complex. "The Curve", designed by the Chartier Dalix office, houses around 1,600 workplaces, catering facilities and a fitness center on an area of 24,400 m2. The elegantly curved basic form leaves room for 1,400 m2 of open space, and two green areas planted with trees delimit the building from the street.
5,000 m3 of cross-laminated timber elements from Binderholz form the structure; only the building core and the four basement levels are made of low-carbon concrete. BNP Paribas is more committed to sustainability than almost any other real estate developer. "The Curve" is 40% below the energy consumption limits of 50 kWh per square meter on average according to the RT2012 thermal insulation regulations and was designed for HQE Exceptional, Effinergie+ and BREEAM certifications. All bidders were invited to submit proposals for the lowest possible carbon materials.
Plane and curved panes form a visual unit
The 10,000 m2 element facade, realized by Metal Yapi, is also part of the sustainable overall concept. In order to flood the offices with as much natural daylight as possible, floor-to-ceiling window areas with windings of between 1,000 and 2,000 mm and a height of 3,285 mm were planned. Saint-Gobain Pietta manufactured the double glazing. In order to find the ideal compromise between comfort, aesthetics and energy efficiency, an extremely transparent and highly selective solar control glass from Saint-Gobain was chosen.

The insulating glass units for the rounded building corners were concavely and convexly curved at Döring Glas in Berlin. The asymmetrical pane structure consists of an outer laminated glass with COOL-LITE® XTREME 70/33 coating on the inside, 16 mm Super Spacer® Triseal™ Premium Plus Black as a warm edge, and an 8 mm float glass.
"We had ourselves certified according to CEKAL especially for this project in order to underline our high quality standards," says Döring Glas project manager Martin Lenz. He continues, "Despite our vast experience, the panes on the first floor and entrance area were a challenge in terms of manufacturing and logistics. The units are up to 3,000 mm wide and 4,102 mm high, weighing in at just under 900 kg. One unit was also screen-printed with a white pattern to provide a barely perceptible visual screen from the outside to the inside. Another requirement from the customer was to precondition each individual insulating glass unit to increase its service life. For each individual insulating glass unit, the pre-calculated pressure was set individually according to the specifications."
Joachim Stoss, Managing Director of Edgetech Europe GmbH and Vice President International Sales at Quanex is proud: "Architecture is currently on an incredibly exciting path. I am confident that together we as an industry will succeed in significantly reducing the carbon footprint of buildings thanks to sustainable materials and consistent circular economy. We are very happy that we at Økern Portal and The Curve were able to make a small contribution again with our warm edge."
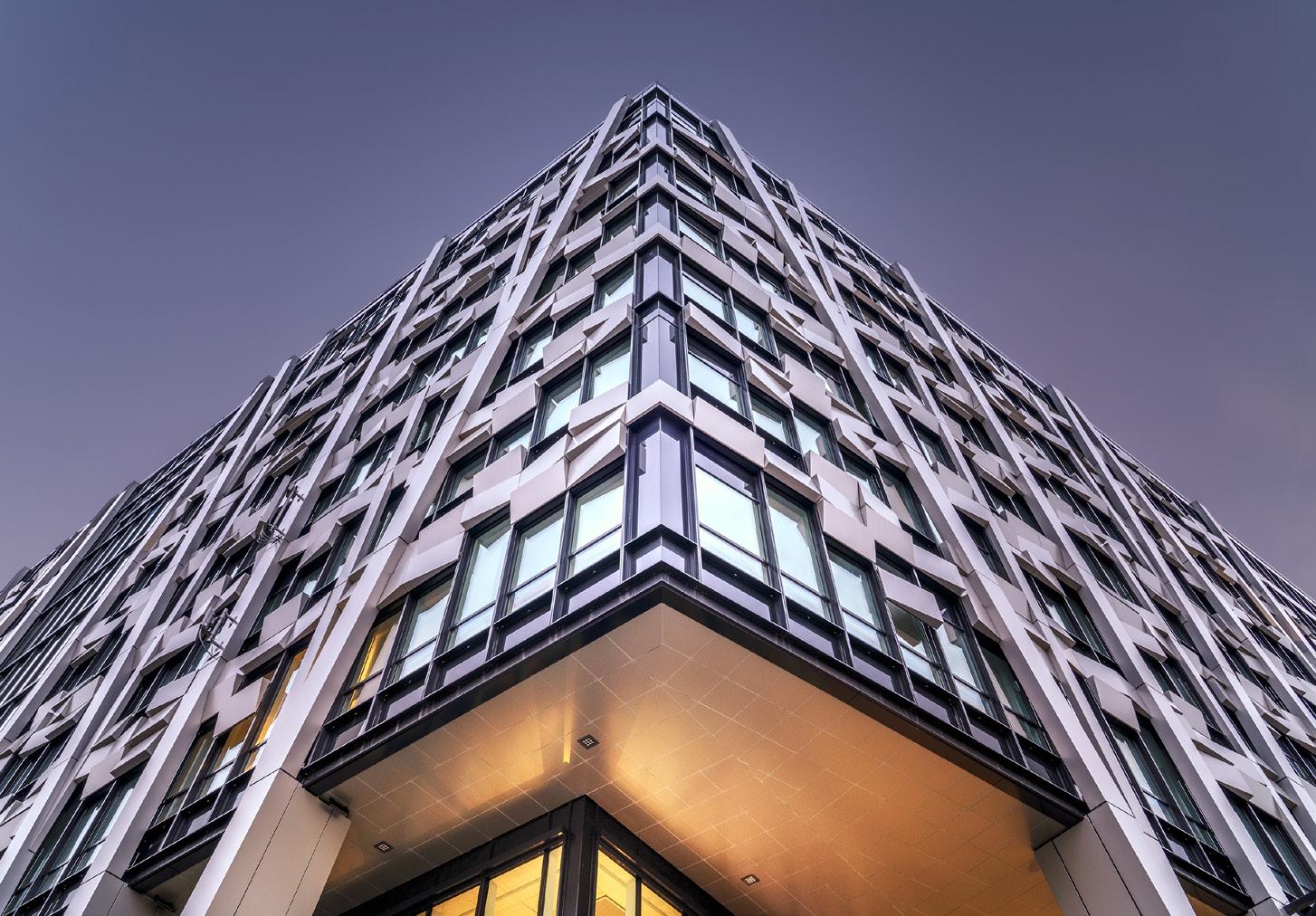
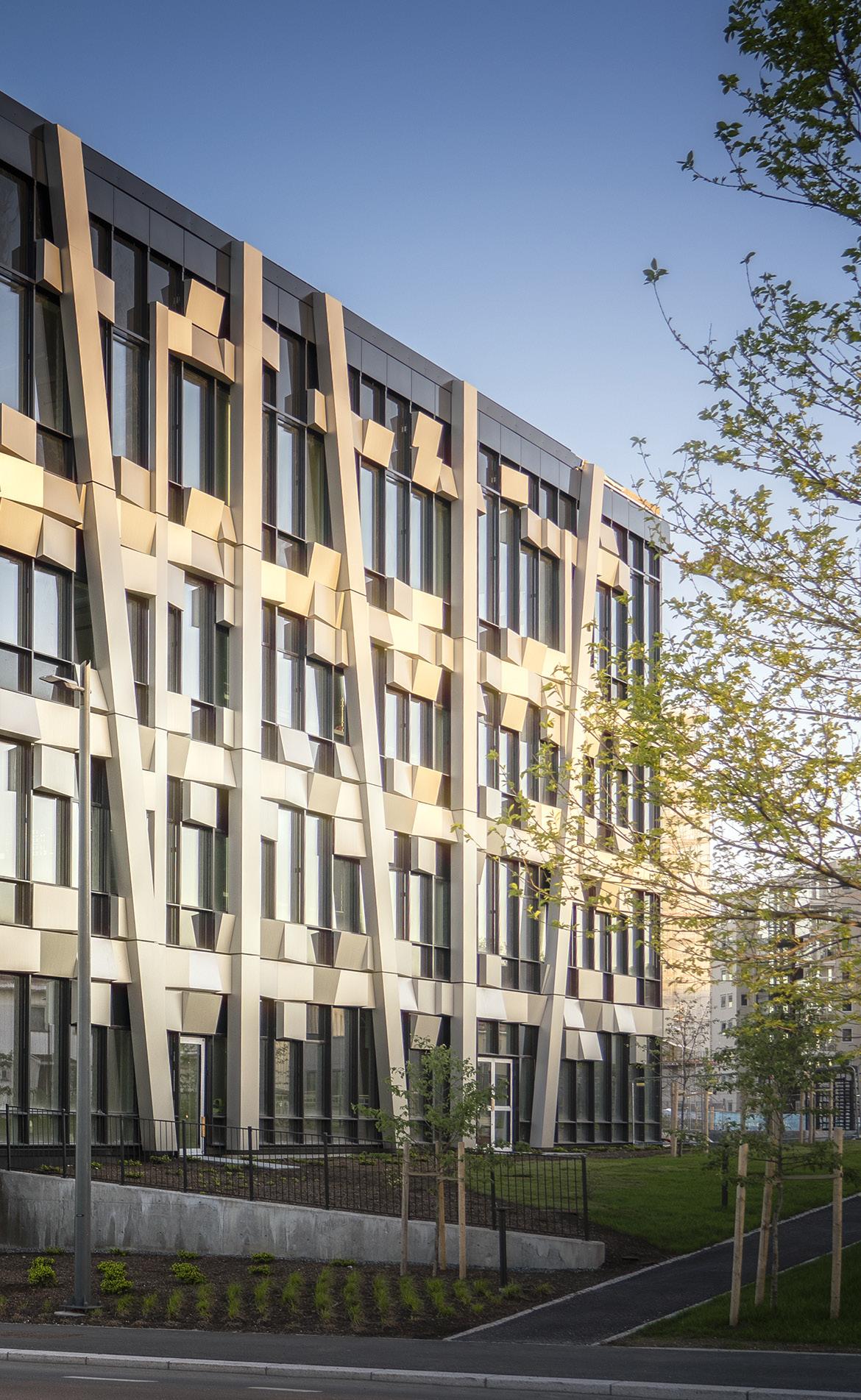
@ Roger Holmen
@ Roger Holmen
CASE STUDY 2: ECOLOGICAL AND ECONOMIC FLAGSHIP PROJECT IN DENMARK
SUPER SPACER® INSTALLED IN THE BASECAMP LYNGBY
Affordable architecture is one of the most pressing concerns of our time. However, the issues of sustainability, energy efficiency, land sealing, recycling management, comfort and social integration are contrary to the economic demands. Lars Gitz Architects and BaseCamp Student pulled off the remarkable feat of combining these complex requirements within a spectacular, multi-award-winning student residence. Serial, modular construction, lowcost, recyclable facade materials, renewable energies and near-natural building greenery and seepage areas were the key to success here. One of Scandinavia's leading glass processors, Glaseksperten A/S, has contributed towards the realisation of the ambitious building concept of the BaseCamp Lyngby on several occasions: Automated production of the insulating glass units, varying direction-dependent glass construction and use of the warm edge spacer system Super Spacer® T-Spacer™ Premium Plus.
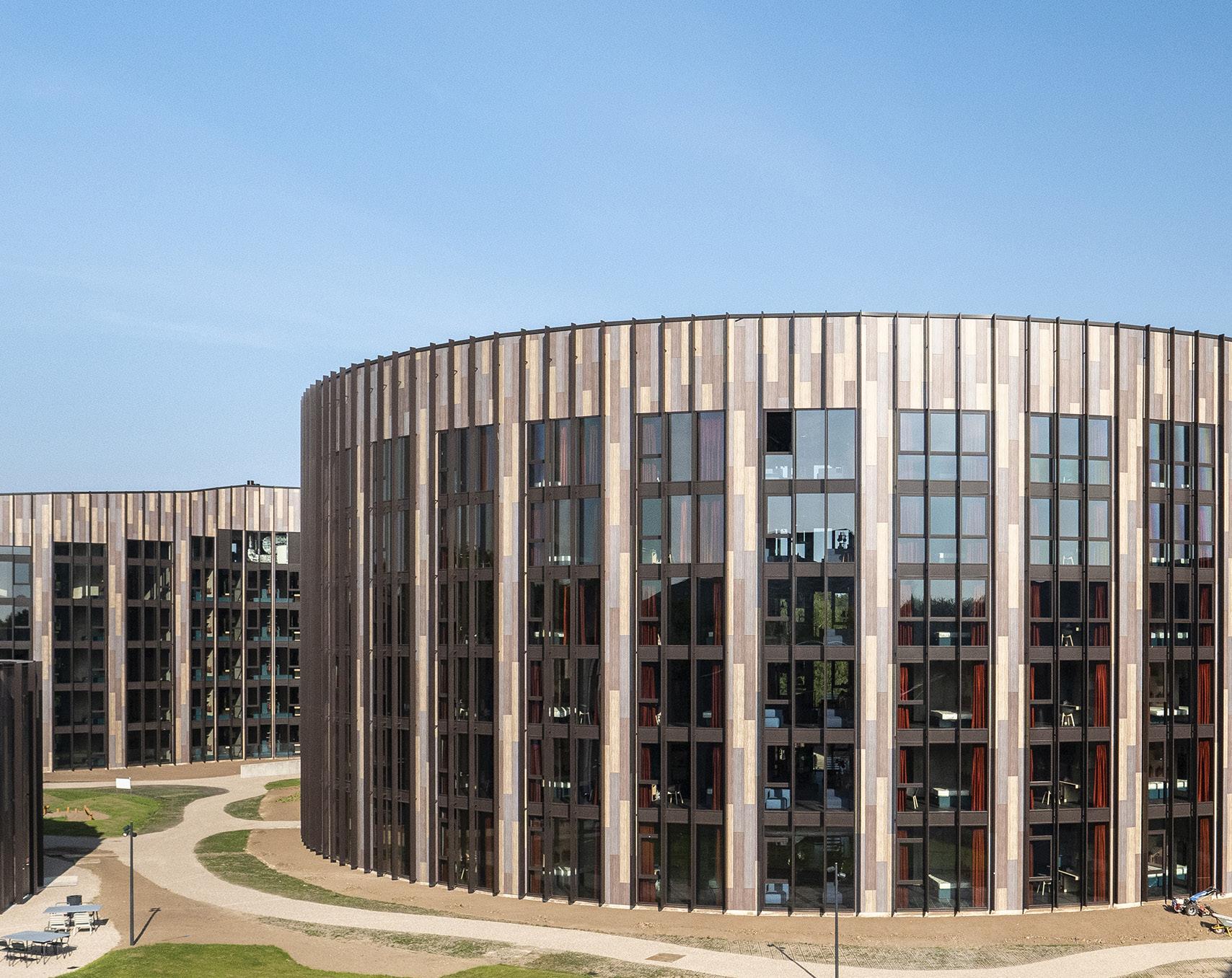
Record-breakingly fast, sustainable and economical
The running track on the roof of Google's new European headquarters in London will be used for the first time in 3 to 4 years at the earliest. The residents of BaseCamp Lyngby, built on a 41,000 square metre site, were able to don their running shoes as early as August 2020: a park landscape was created on the green roof of the extensive student residence complex in northern Copenhagen using a system of biodiverse planting, urban gardening areas and an 800-metre-long path that can be used for walking or jogging as you please. From the flat terrain, it winds its way up six storeys above the organically shaped building back down to the starting point while enclosing cosy inner courtyards and a circular community centre in the process. The facades are reminiscent of tall trees and forests by virtue of the vertical arrangement of the panels in three different shades of oak wood as well as the line of windows, and in just the same way as the entire complex they blend harmoniously within the surrounding nature. The project developer, BaseCamp Student Nordics, a part of the Europe-wide BaseCamp Group, deliberately wanted to give something back to Lyngby Municipality and enter into dialogue on social and environmental aspects. The roof is therefore open to the public to provide meeting areas.
The construction time for a project of this size is impressive. The 786 flats, including 639 student
@ Kontraframe

@ Kontraframe

@ Kontraframe
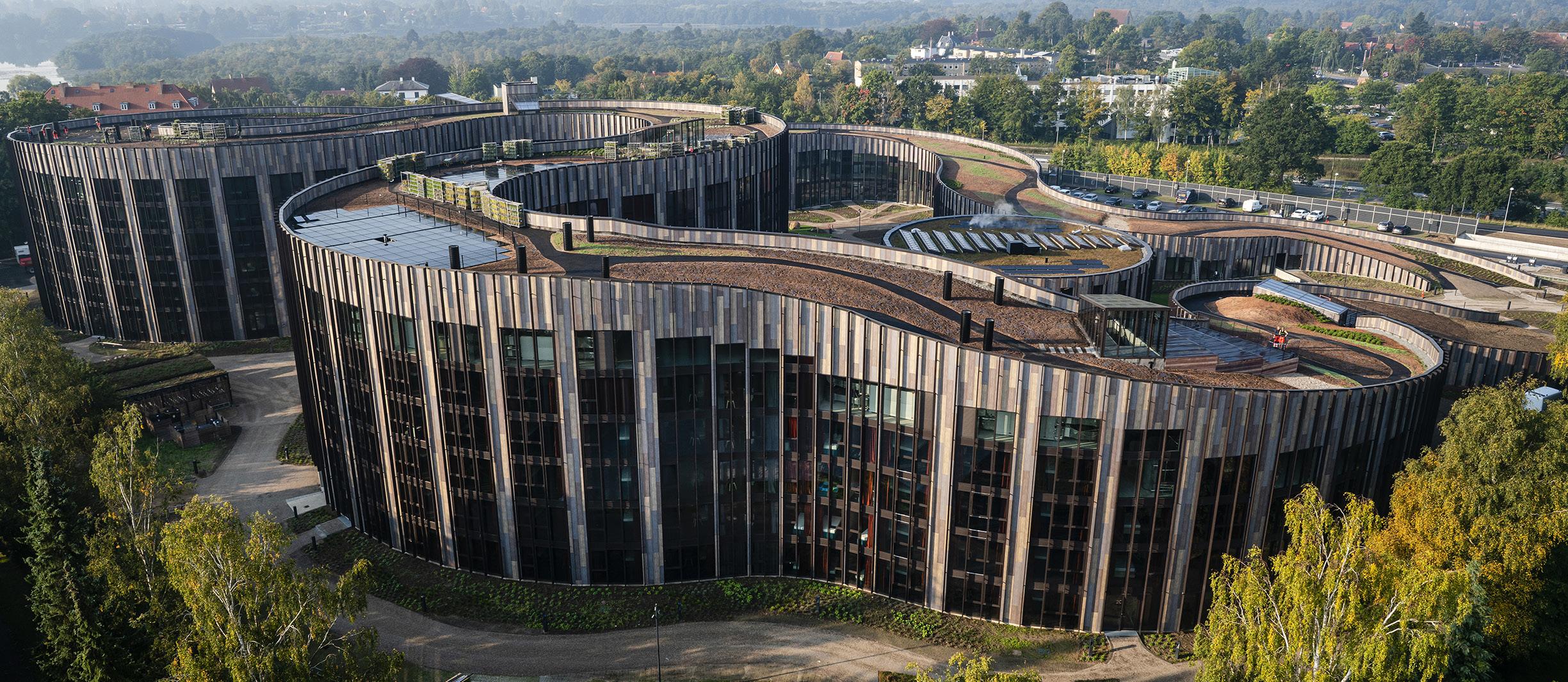

flats and 48 senior flats, were completed near Lyngby University of Technology within the space of two and a half years. The building was also intended to be no less spectacular, but one aspect distinguishes BaseCamp Lyngby from many other major projects: Ecology and economy determined the architectural concept equally.
Modules as the basis of architectural aesthetics
In order to meet the estimated construction costs of around € 75 million the Danish firm of Lars Gitz Architects designed a trapezoidal module that is repeatedly rotated by 180° and stacked at different heights to create the gently rounded structure. The outer skin also constitutes a model example of cost-efficient construction. The ventilated curtain wall is insulated with rock wool and clad with slabs made of pressed volcanic basalt rock from Rockpanel. With a weight of 8.4 kg per m2, the extremely light material can be cut to size on site and simply attached to the substructure.
The facades panels with their natural wood look almost entirely consist of natural volcanic rock and recycled rock wool and can be repeatedly reused in line with the idea of a circular economy. This makes the facade one of the pillars of the sustainability concept, which has been awarded BREEAM Very Good certificate (equivalent to the DGNB certificate in silver). The energy-saving green roof with the photovoltaic modules serves as a form of thermal insulation, an energy provider and natural air conditioning. The rainwater that is captured is returned to the natural water cycle via evaporation, which consequently relieves the burden on the sewage system and lowers the ambient temperature.
Energy-efficient windows with warm edge spacers
The aluminium windows with triple glazing
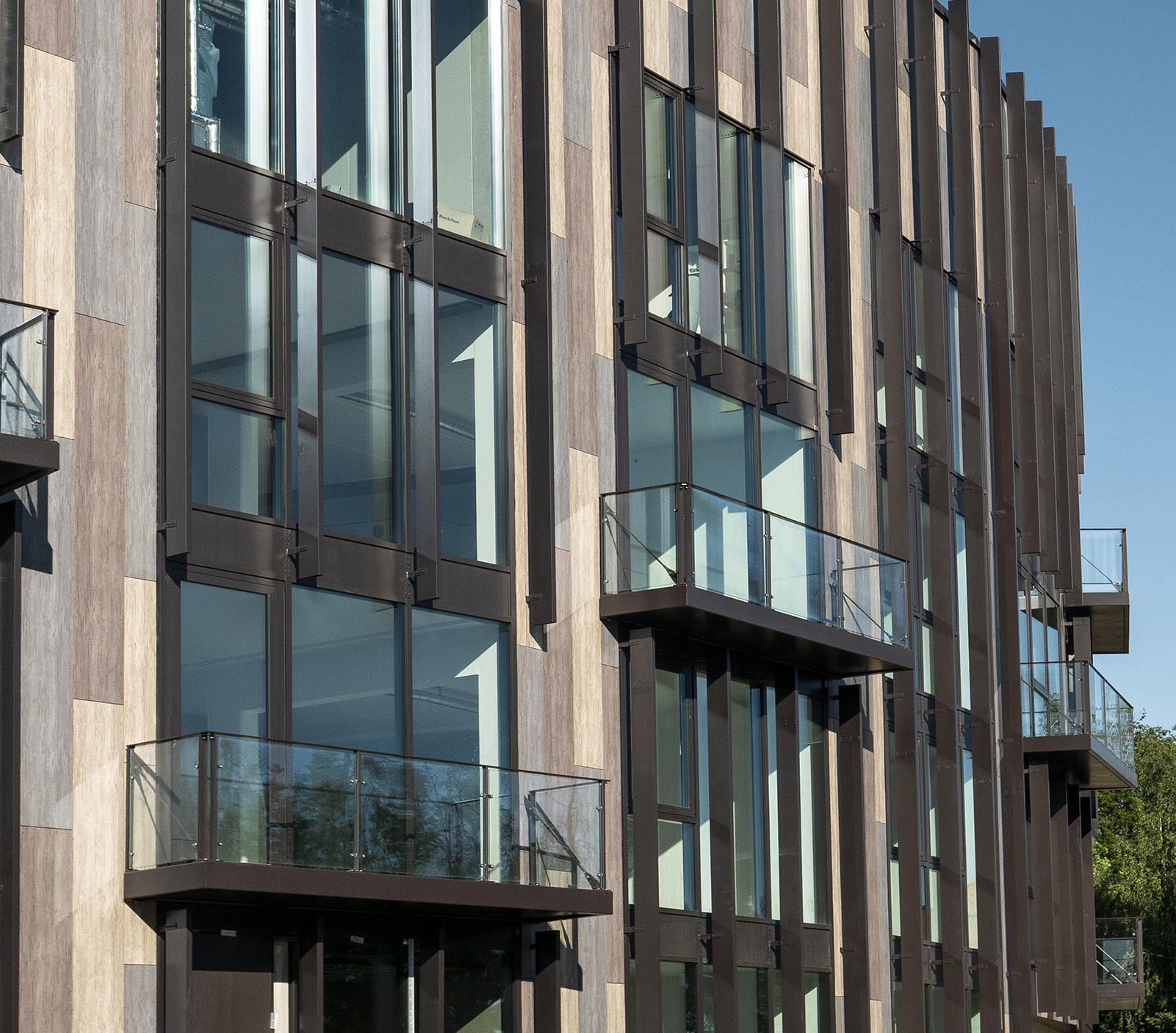
also form part of the overall concept. As is so often the case in Scandinavian architecture, the BaseCamp studios and communal areas are glazed down to floor level to allow as much daylight as possible into the room even during the winter. The Danish insulating glass manufacturer Glaseksperten supplied 4,000 insulating glass units packaged in sizes of up 4.011 x 1.127 metres to the construction site in accordance with a meticulous logistics plan. Due to the organic shape of the building, the glass structures change according to the direction. Depending on the heat input and amount of light, solar control glass, thermal insulation glass or clear glass with varying
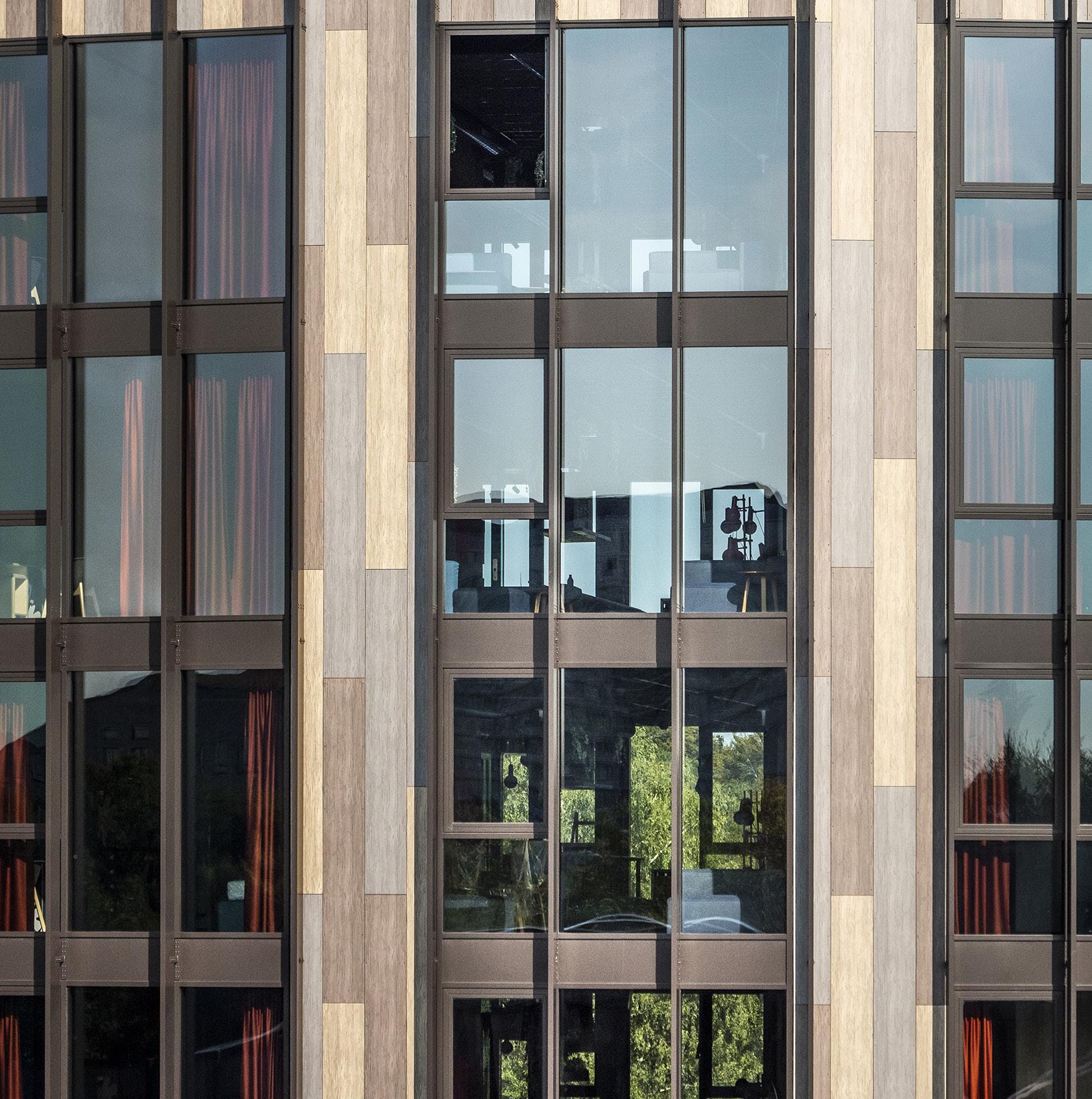
@ Kontraframe
@ Kontraframe
coatings and glass thicknesses were used. Glaseksperten opted for Super Spacer® T-Spacer™ Premium Plus in various widths as the warm edge spacer system. Sales Manager Jesper Hønning declared: "An ever-increasing number of our customers wish to install energy-efficient windows. We consistently use low-emission thermal insulation glass and solar control glass combined with non-metal warm edge spacers in order to avoid thermal bridges and optimise the heat transfer coefficient.” At the company's headquarters in Hjørring, an ultramodern, automated IG line is available for the production of insulating glazing for sizes of up to 3.2 x 6 metres. "Super Spacer is of key importance to Glaseksperten in supplying quality products which also ensure we are a leading company in economical and ecological terms", Hønning went on to say, "the fully automated continuous application of spacer from the reel saves time and money and guarantees top class product quality that is reproducible.” Joachim Stoss, Managing Director of Edgetech Europe GmbH and Vice President International Sales at Quanex added: "Northern Europe is a global pioneer in the field of climate protection and therefore one of the growth markets for warm edge products. Of course, we are extremely proud that our Super Spacer system has been installed in another Scandinavian flagship project".
About Edgetech Europe GmbH, A Part of Something Bigger
Edgetech Europe GmbH, located in Heinsberg, Germany, is a fully owned subsidiary of Quanex Building Products Corporation, (NYSE: NX) a global, publicly traded manufacturing company primarily serving OEMs in the fenestration, cabinetry, solar, refrigeration and outdoor products markets. Edgetech Europe GmbH services markets in continental Europe with a total of 490 employees and 17 extruders. We are “A Part of Something Bigger” by improving the performance and aesthetics of end products through continuous innovation, helping customers achieve greater production efficiencies, and giving back to communities where we operate. Visit quanex.com for more information.
A GLOBAL INDUSTRY IN NEED OF
January 2021, Glass Futures’ container glass biofuel trial at Encirc, (a Vidrala Company) for the Industrial Fuel Switching Phase 3 programme

the Glass Industry and Built Environment:
The world is in a tumultuous and changing period and it feels like every industry, business, country and individual has a reason to respond more than ever to the world around it. I personally feel that the commonly used phrase of the past two years, “the new normal” is precisely the right terminology for the world to adopt when thinking about the approach to business and sustainability in the 21st century.
INDUSTRY IN NEED OF LOCAL SOLUTIONS
In reading about the impacts of climate change and shifting geopolitical sands, what is very evident is that the events happening around us apply more pressure to the system and force it to adopt a new footing. Business is focused on providing a stable operation, with predictable returns in known markets. The events of the past two years have caused a seismic shift in “business as usual” and sustainability is being recognised at board level due to its increased prevalence as an over-arching issue that will outlast any pandemic or conflict.
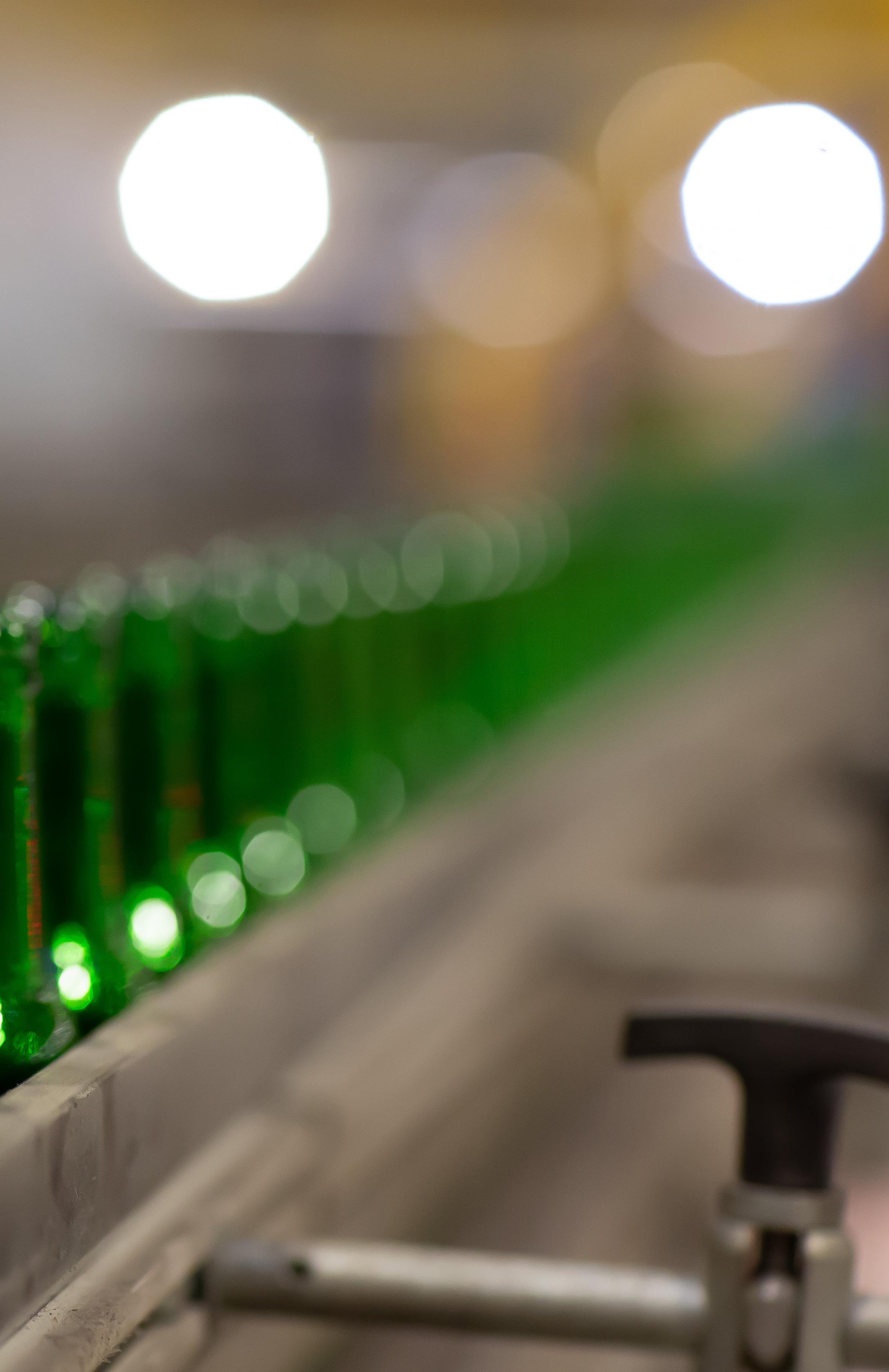
It can be difficult to see how such established industries with entrenched processes can also keep up with the rate of change of society but the reality we face is that they must move with the times, lest they cannot serve the society that we are building. In my brief time working across the built environment sector, it is easy to understand how multi-faceted projects, relying on complex supply chains can find it hard to move away from the standard and implement new and changing approaches.
In much the same way, industry must take fewer risks for the safety of its businesses, processes and people, the built environment is not inclined to take risks when it comes to designs, specifications and delivery. Ultimately, certainty is our safety net but when looking around, one thing everyone would be happy to acknowledge is that we are far from certain about what our future holds.
Whilst it is easy to discuss these items and sometimes feel like entrenched systems are immovable, the last 12 months have shown me that the glass industry is on the move after a prolonged period of stability and certainty; it is not afraid to get ahead of the curve. The rise of Glass Futures is both riding on and helping to shape a wave of change built around a few key ideals that I have heard re-enforced across industry, which are critical to the way we approach the new normal:
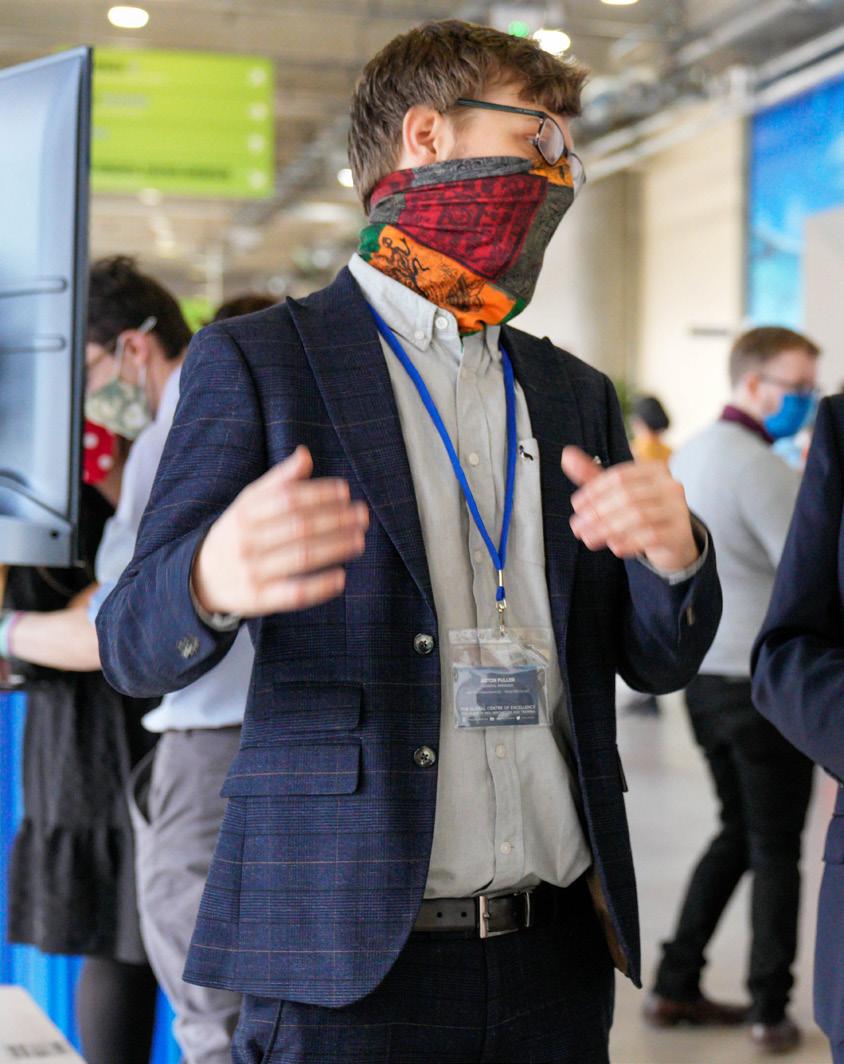
• Some challenges are too big for individual organisations, and we must collaborate to move forward. • We do not know what the future looks like, but we know we must think differently.
The real challenge for the industry
The world needs change and the method for manufacturing glazing is very similar throughout the entire world so any single solution could be rolled out across the world with relative ease, in theory. The big issue is that there are several different key aspects that determine each manufacturing sites’ decision-making process:
• Local laws and environmental policies • Energy prices for operational energy • Costs for energy infrastructure • The age of the installation • Design and capex philosophy of the company • Size and space constraints on site • Domestic and international competition
As seen from the above list, the truth is most of the impacts that determine a plant's approach to sustainability will be largely driven by geographically dependant aspects. All the above feed into a complex list of decision making processes which ultimately come down to cost, profitability and the balance of strategy.
Consumers vote with their money, and in the glass world, consumer facing brands are leading the way when it comes to sustainability because the consumers of the world are bringing the sustainability question to bear. Within the construction sector, a “sustainable” approach is almost still reserved for the public sector and wealthy clients who can afford to
Image taken by UKRI: CEO UKRI speaks to Richard Katz, Chief Executive of Glass Futures & Aston Fuller – General Manager of Glass Futures while visiting the UKRI stand in the Green Zone at United Nation’s COP26, Glasgow UK on 09 November 2021.
invest in the “extras” that are associated with sustainability.
The reality is that the world is committed both legally and morally to decarbonising but we do not know how to do this in a way that is economically sustainable yet. Companies the world over have equally made commitments but these targets and commitments require
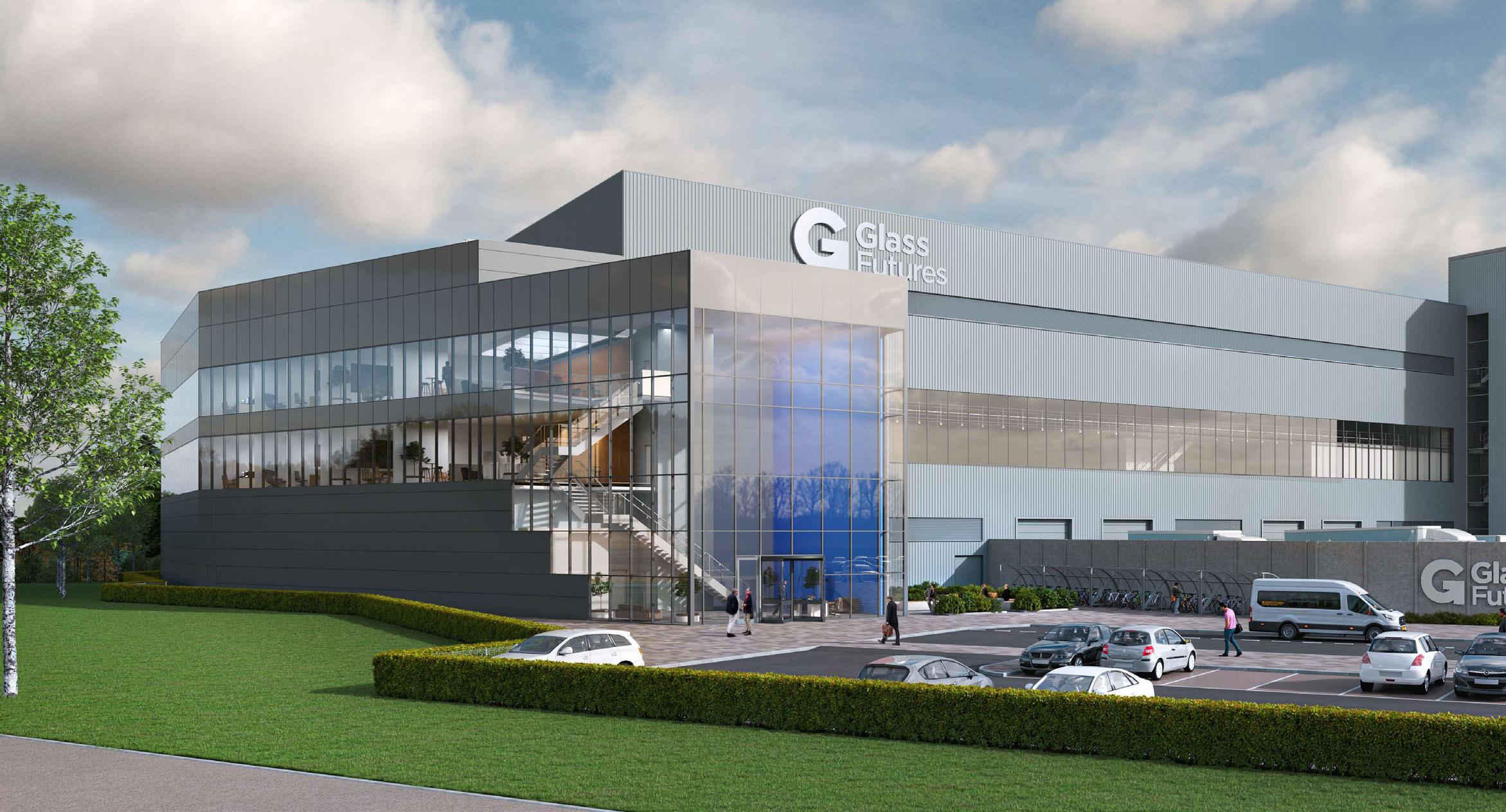
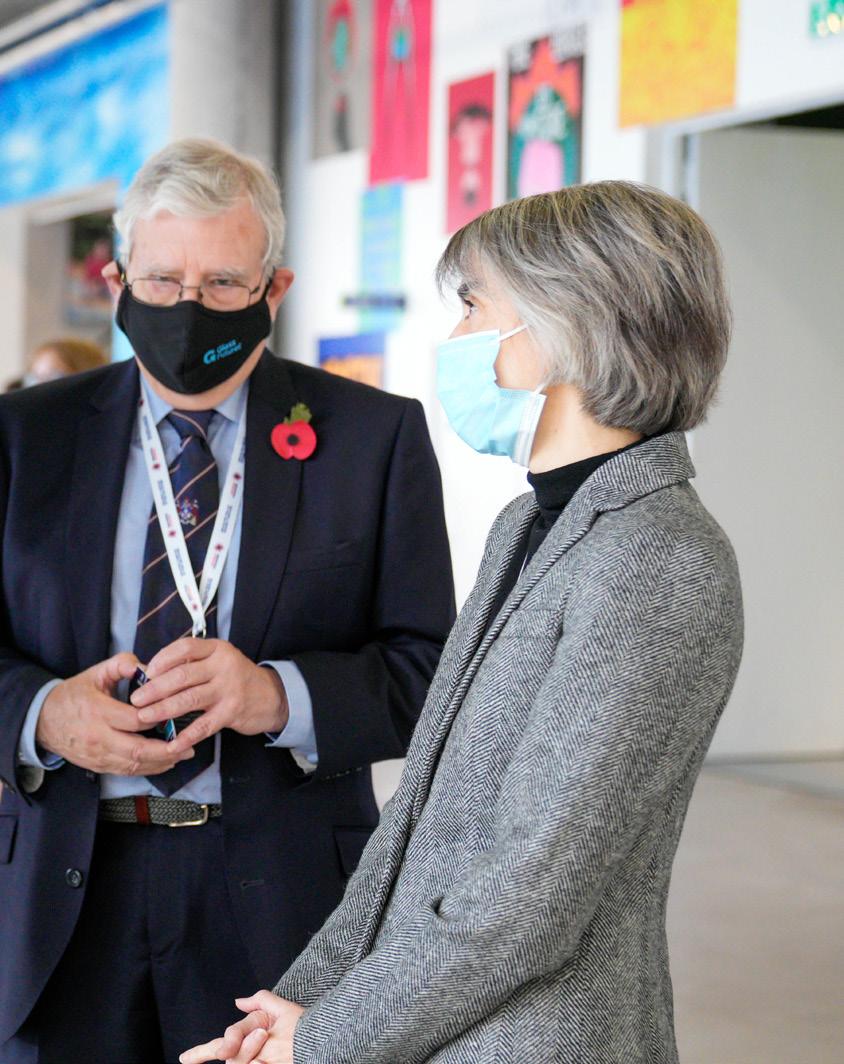
support, investment and hard work to be achieved.
I, myself and several colleagues saw just how far reaching this commitment goes at COP 26 last year and it invigorated me to see that from the biggest to the smallest countries around the world, every industry is looking at ways to transform and become the thought leader.
The United Nation’s COP26 summit
Like many others who applied to exhibit at COP26, we hoped to present at this exhibition to showcase challenge and demonstrate the action we are taking to lower carbon emissions. 15–20 permanent exhibits were successfully selected from thousands of applications, Glass Futures being one of them.
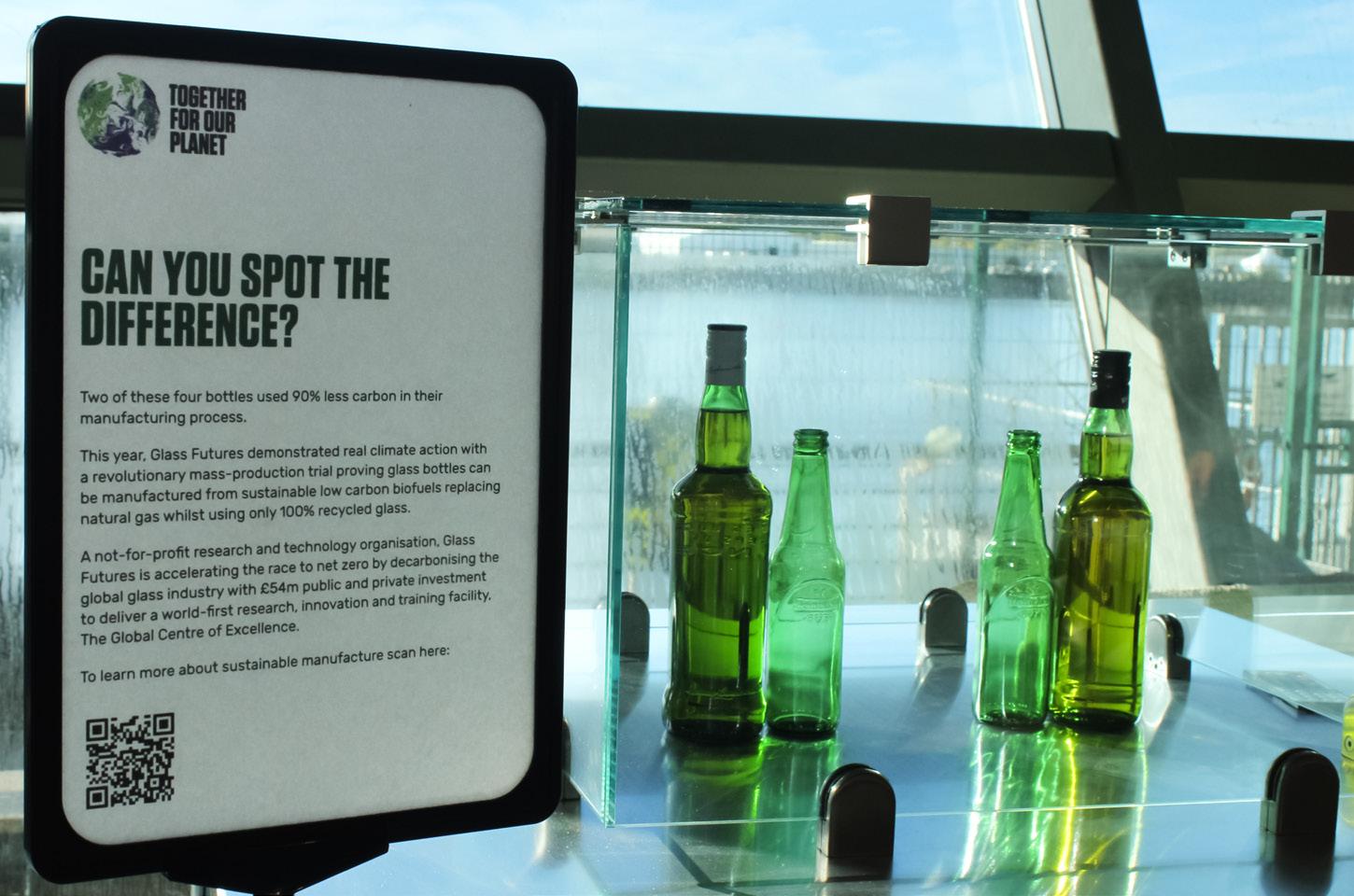
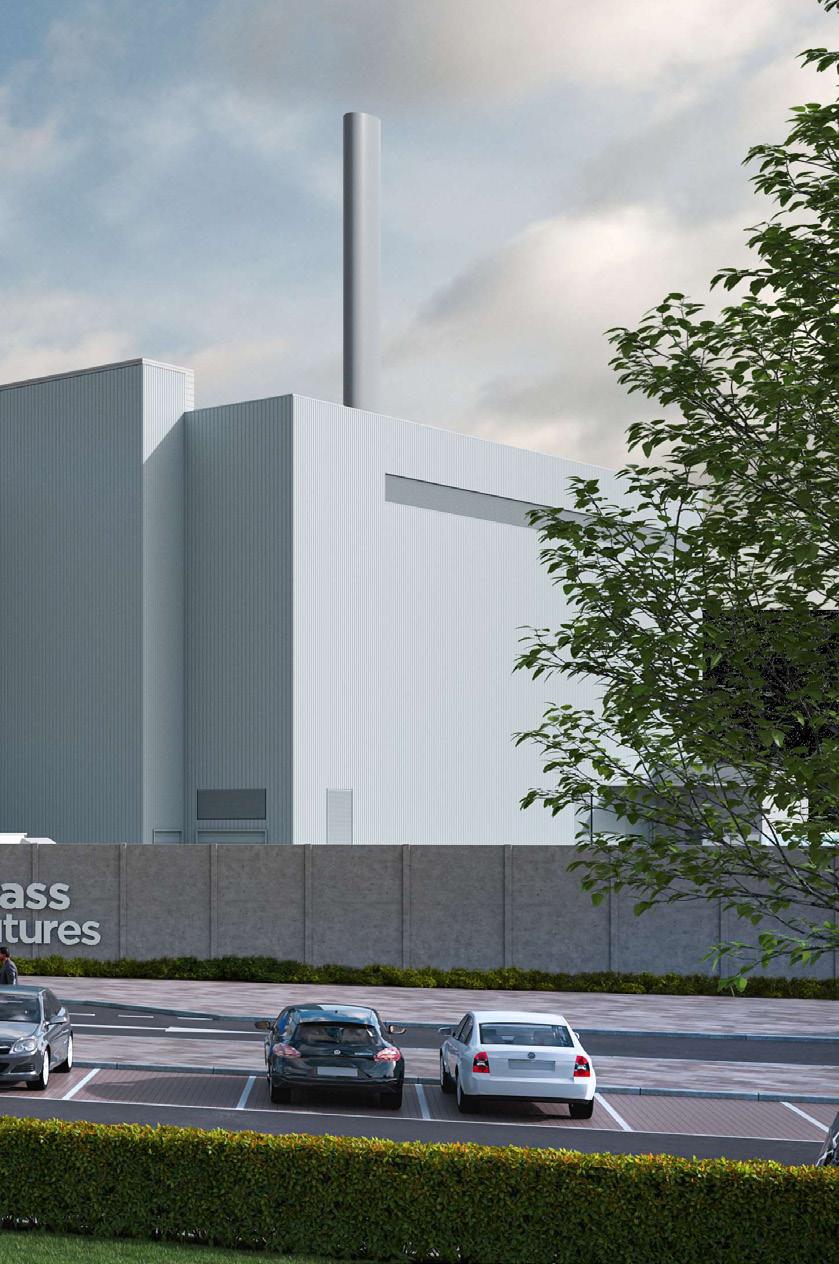
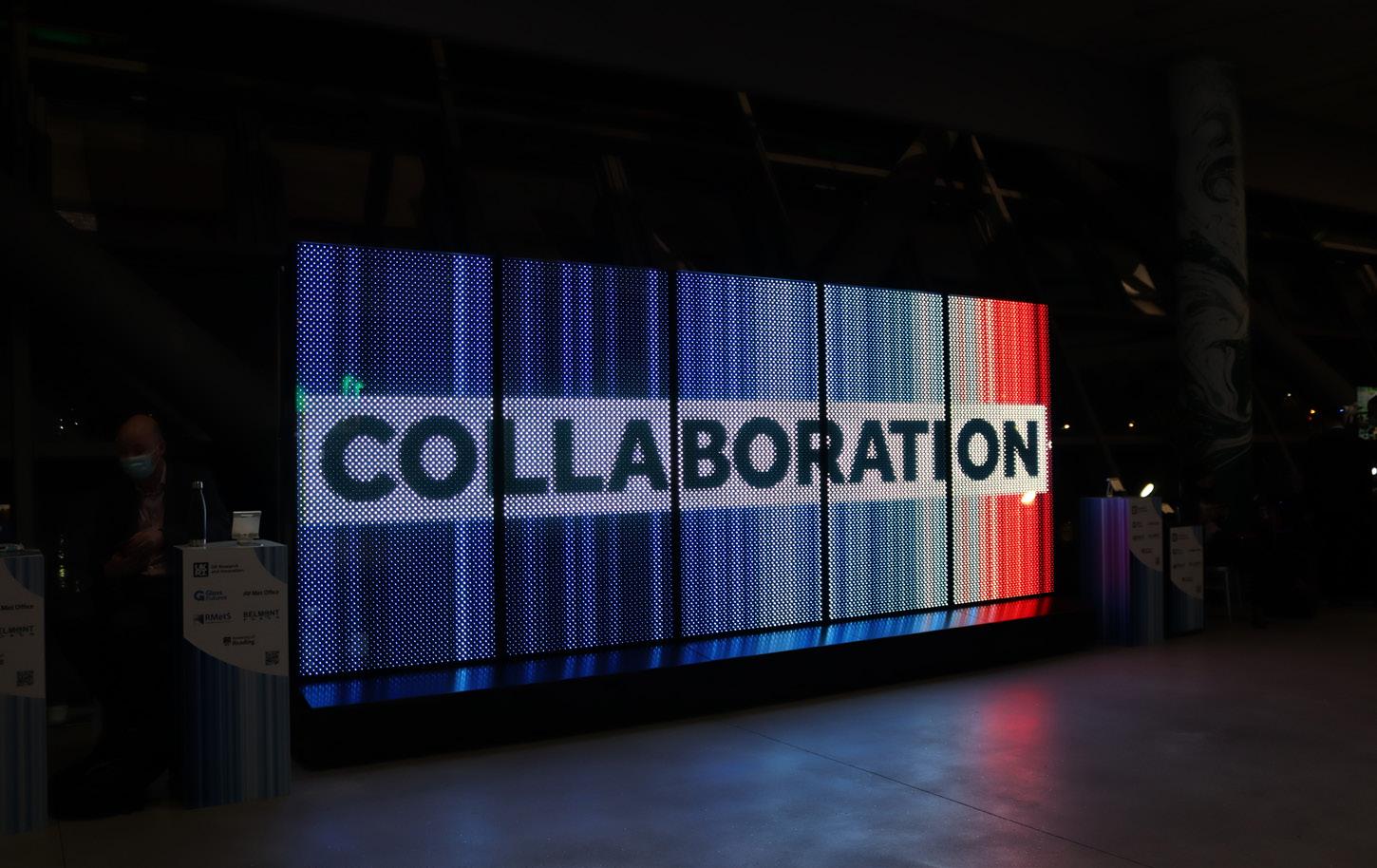
I believe our selection was a recognition of the urgent need to collaborate effectively to achieve carbon goals being set. In my opinion, our project exemplifies what a highly positive collaboration can actually achieve, not just as a long-term target but demonstrable in the here and now. We successfully conveyed a message of collaboration and that this is an industry that can work together with the public and private sectors.
We did this by working together with organisations to help share their own messages and what they are doing to support sustainability. This was sponsored by one of our major corporate members and they openly provided the opportunity for competitors in the industry to share the same platform. This kind of action helps extend the olive branch and lets organisations know that through the ideal of mutual benefit, we can achieve momentous results, together.
This message is precisely the underpinning sentiment of COP26 and I am glad that we embodied the message on the world stage.
Glass Futures at United Nation's COP26 summit in the Green Zone, Glasgow UK, exhibiting revolutionary trial as part of the Industrial Fuel Switching Phase 3 Programme
Exhibition by UK Research and Innovation (UKRI), Diageo, Glass Futures and the global glass industry at the United Nation's COP26 summit in the Green Zone, Glasgow UK
Economics of green combustion
I am proud that recently Glass Futures has been breaking the mould in its approach to changing the industry, as such, we are almost continuously running trials into low carbon alternative fuels for glass furnaces as part of Glass Futures’ Government contracted Industrial Fuel Switching Phase 3 programme. Given that combustion is the key energy source for most global glass manufacturing, if we can move away from natural gas, we can decarbonise the manufacturing process at the source. The reality here however is that large furnaces melting upwards of 800 tonnes per day are highly risk averse and the need to de-risk these activities is essential before anything at a meaningful scale can be done.
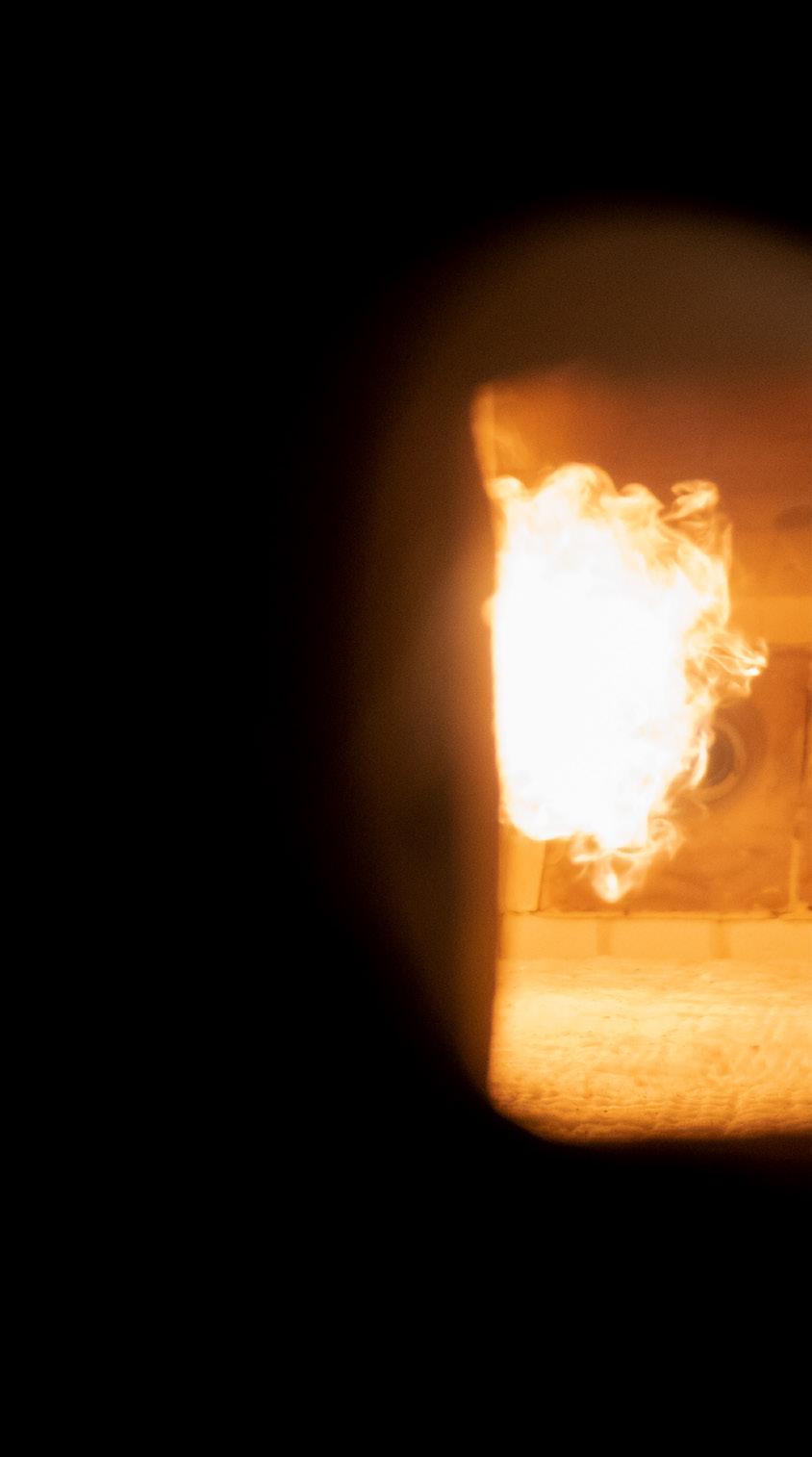
The 350kW combustion test bed for the Industrial Fuel Switching Phase 3 programme In January 2020, Glass Futures was awarded a £7.1m contract by The Department of Business, Energy and Industrial Strategy’s (BEIS) Energy Innovation Programme. This work involves test firing hydrogen and biofuels in a scale model glass furnace at temperatures in excess of 1500 °C, simulating real world firing conditions for alternative fuels to lay the foundation for full scale trials. The project is also evaluating the associated technical, economic, and environmental aspects of fuels and encompasses a wide range of industrial and academic partners; the final report for this work is due to be published by BEIS in summer 2022.
It is very clear from the work that is publicly available that the success of the programme
First flame’ for the Industrial Fuel Switching Phase 3 programme, image taken inside the 350kW combustion test bed

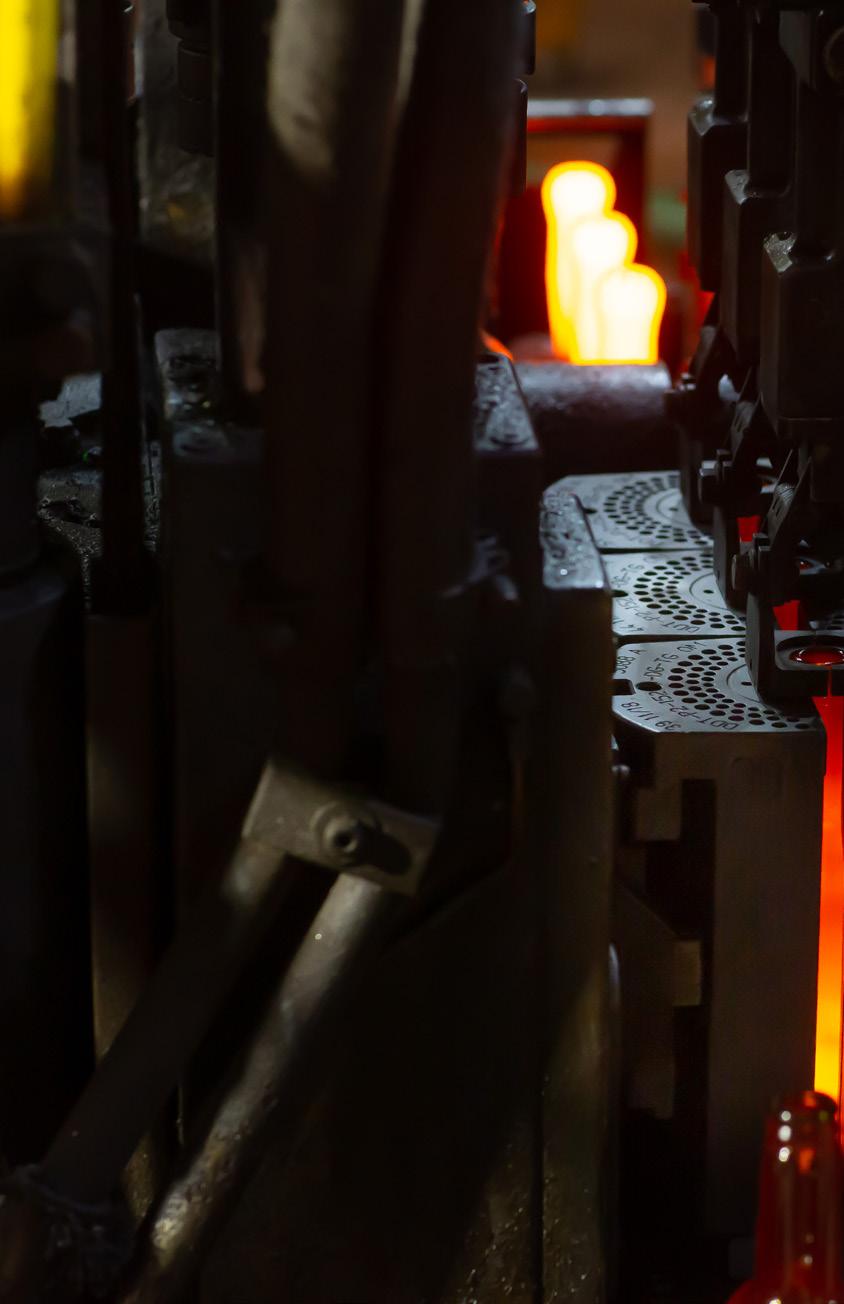
January 2021, Glass Futures’ container glass biofuel trial at Encirc, (a Vidrala Company) for the Industrial Fuel Switching Phase 3 programme
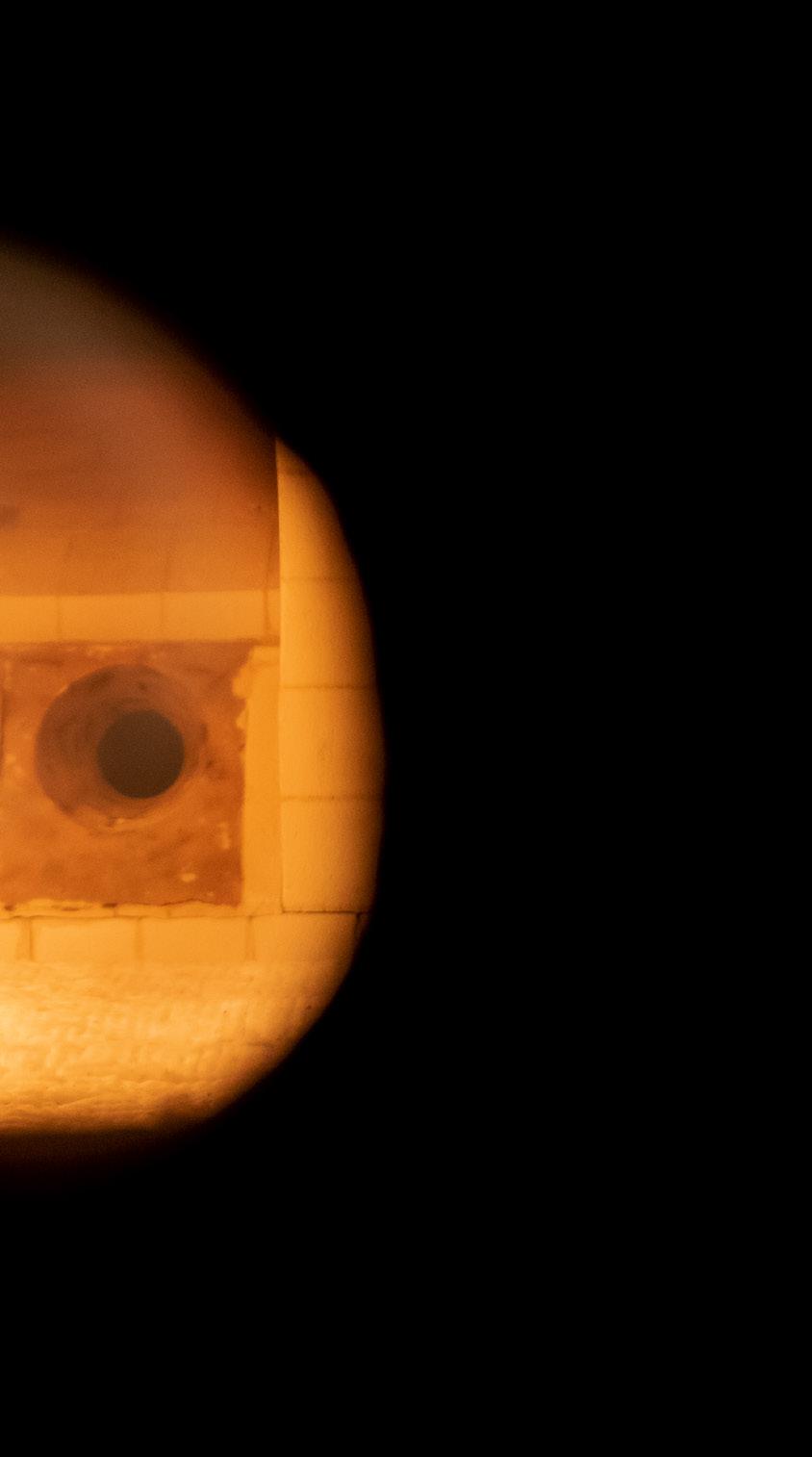
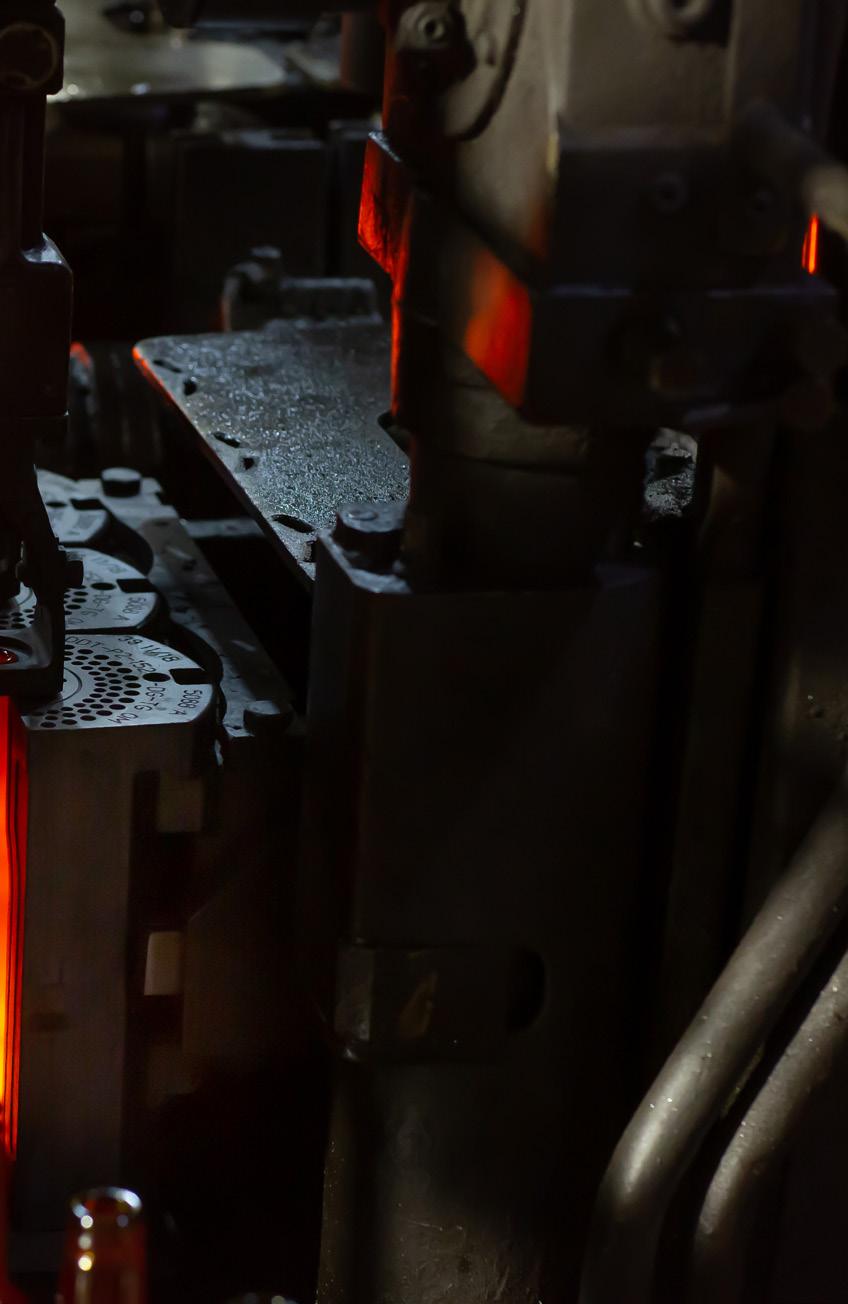
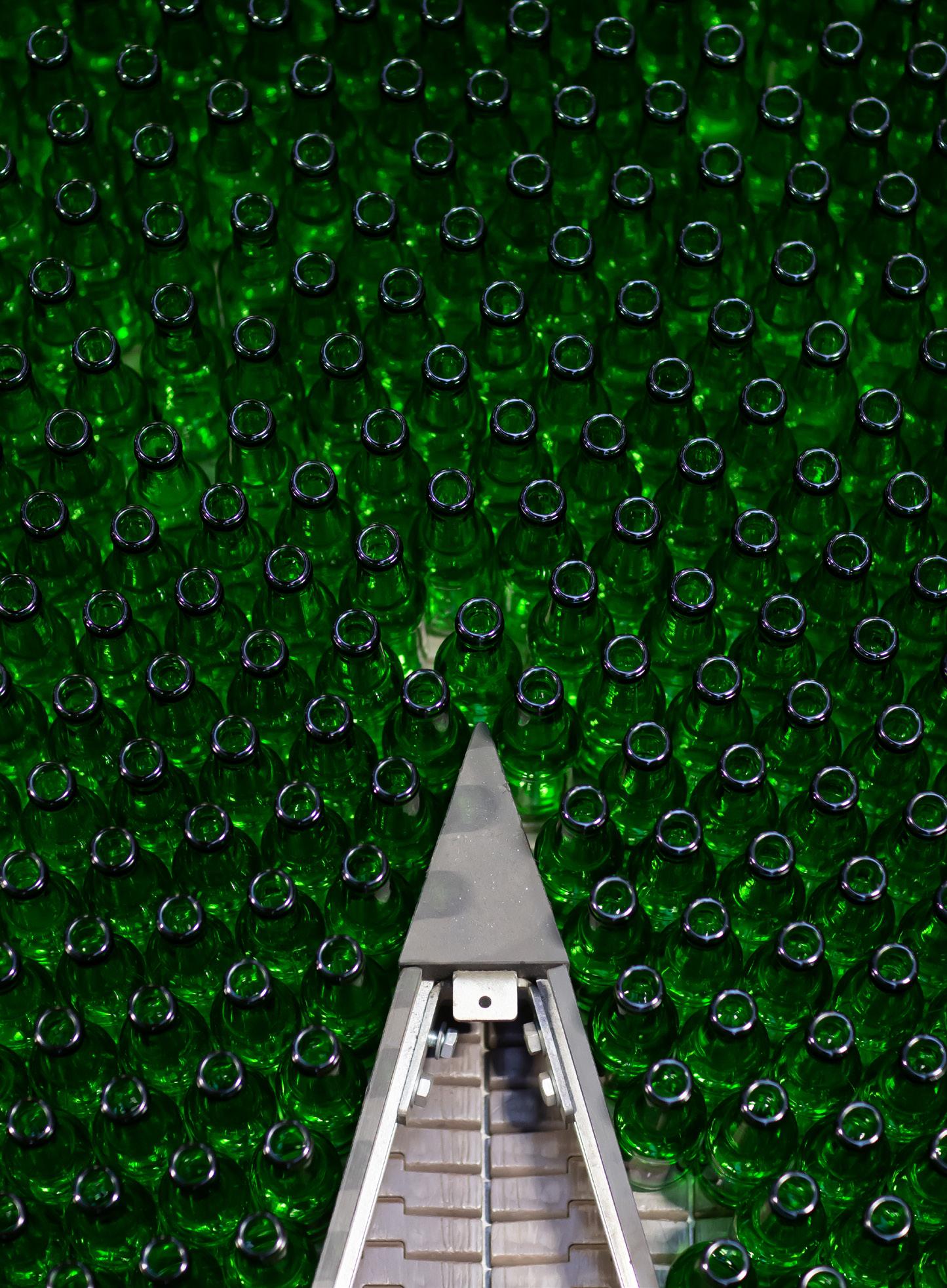
has been outstanding and it is due in large part to the collaboration and co-operation of the whole glass industry, not just within the UK, where we carried out our trials, but also across the global business owners based across North America and the EU.
The UK Government released its Net-Zero strategy ahead of COP26 , which sets out how the UK will deliver on its commitment to reach net-zero emissions by 2050, outlining measures for the transition to a green and sustainable future. The strategy announces an extra £500 million towards innovation projects, bringing the total funding for net-zero research and innovation to at least £1.5 billion to support technologies that decarbonise glass and other industries. This amount of funding is simply the UK commitment! Horizon 2021 funding in the EU, Department of Energy in the US and many other global institutions are spending a significant amount of money investigating this question and it is understandable, looking at the rate of change needed and the technical questions that need to be answered in the meantime.
Encirc and the “world’s most sustainable bottle”
In January 2021, as part of this revolutionary project, glass container manufacturer, Encirc (a Vidrala company) and Glass Futures demonstrated that new bottles can be made from 100% recycled glass, using only
January 2021, Glass Futures’ container glass biofuel trial at Encirc, (a Vidrala Company) for the Industrial Fuel Switching Phase 3 programme
January 2021, Glass Futures’ container glass biofuel trial at Encirc, (a Vidrala Company) for the Industrial Fuel Switching Phase 3 programme
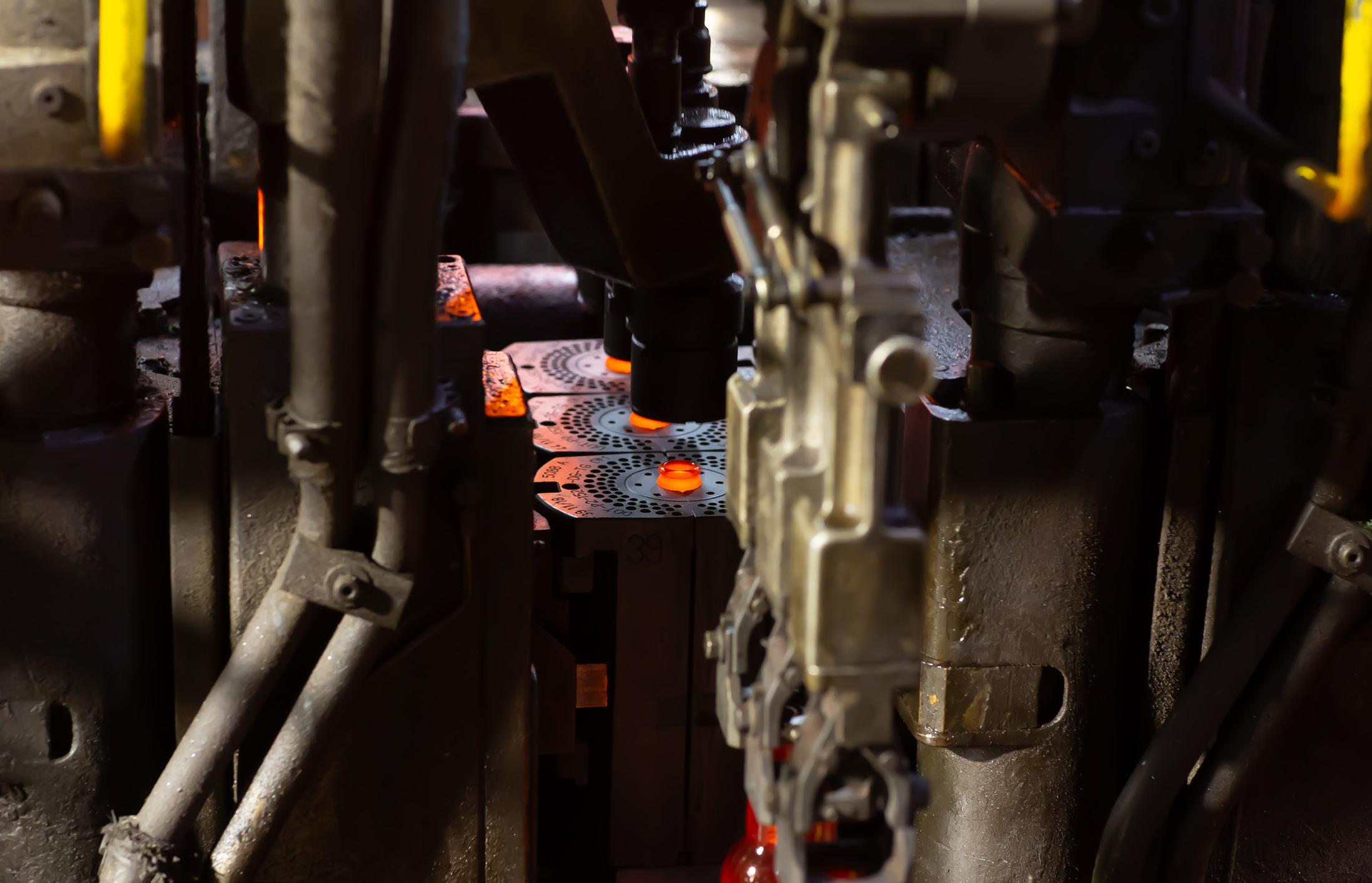
the energy from burning ultra-low-carbon biofuels, achieving a 90% reduction in carbon footprint, I was personally on-site during these trials and seeing something achieved in a real world manufacturing environment was truly energising.
Made from waste organic materials, biofuels are a renewable and sustainable fuel source when compared with those traditionally used by the glass sector and can reduce the carbon footprint of each tonne of glass by up to 90%. By using up to 100% recycled glass to create the new bottles, the trial was able to even further minimise the lifetime impact of these products.
As part of this trial, millions of containers were manufactured for a number of wellknown global drinks organisations including Diageo and Heineken, putting real, low carbon products into the hands of consumers throughout 2021 well ahead of any global net zero targets. This trial ran for three weeks on a full-scale furnace and allowed us to de-risk the planned trial for a float glass furnace which was the next step following a successful demonstration.
NSG and the “World’s lowest carbon float glass”
In February of this year, Glass Futures supported Pilkington United Kingdom Limited (part of the NSG Group) to manufacture the world’s first flat glass produced by a furnace fired on 100% biofuel as part of one of the key final deliverables for our Industrial Fuel Switching project.
We ran the trial successfully for four days, creating 165,000 sq ft of the lowest carbon float glass ever made. The embodied carbon within this glass contains circa 70% less CO2 than traditional float glass made and one of the home truths which we faced in talking to the wider market about the opportunities is that no one is asking for low carbon glazing at the moment, because customers have never been offered such a product before. I believe generally most people have thought that low carbon products are a thing of 2030 or 2035 but it has been empowering to see we have proved we can do this now if the market demanded it.
The truth as it currently sits is that while all these things are possible, they come with an economic cost without doubt, this means we will see low carbon products being seen as a premium
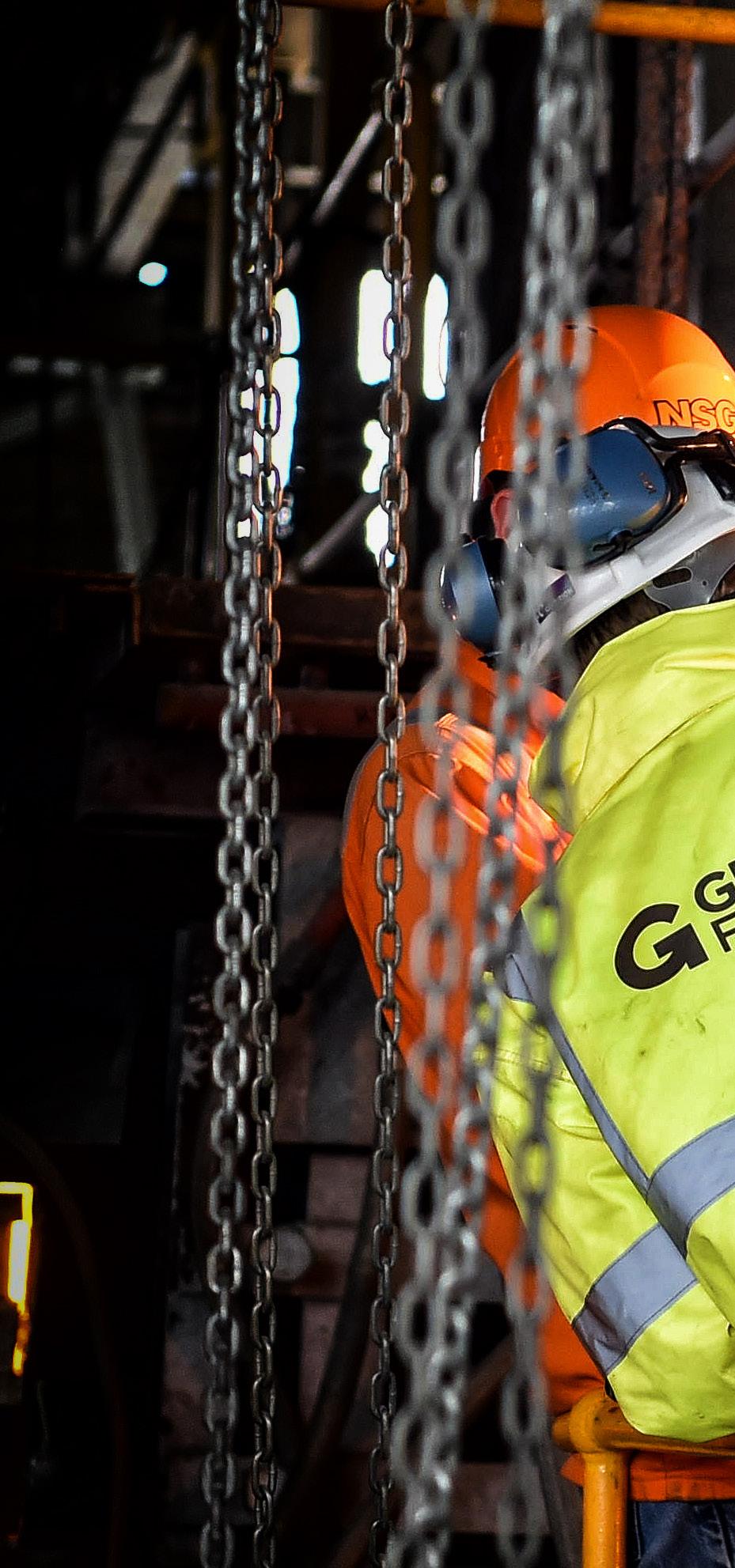
option in the short term, before becoming more mainstream.
Global Industry
It is sometimes easy to miss that with such a large global commodity market that we still tend to move towards domestic manufacturing, and while the rise of global shipping has sometimes seen domestic manufacturing move abroad, this trend struggles when dealing with very heavy, relatively low cost materials, of which glass (in its pure form, without coatings) certainly is.

This is driven by the high energy requirement and use of sand, limestone, soda ash and cullet which are all products that you want to pay as little for transport as possible. And the same will go for our low energy sources of the future, we will rely on keeping costs down including reducing manufacturing costs. We have seen
January 2021, Glass Futures’ container glass biofuel trial at Encirc, (a Vidrala Company) for the Industrial Fuel Switching Phase 3 programme
February 2022, Glass Futures flat glass biofuel trial at Pilkington United Kingdom Limited, (part of the NSG Group) for the Industrial Fuel Switching Phase 3 programme
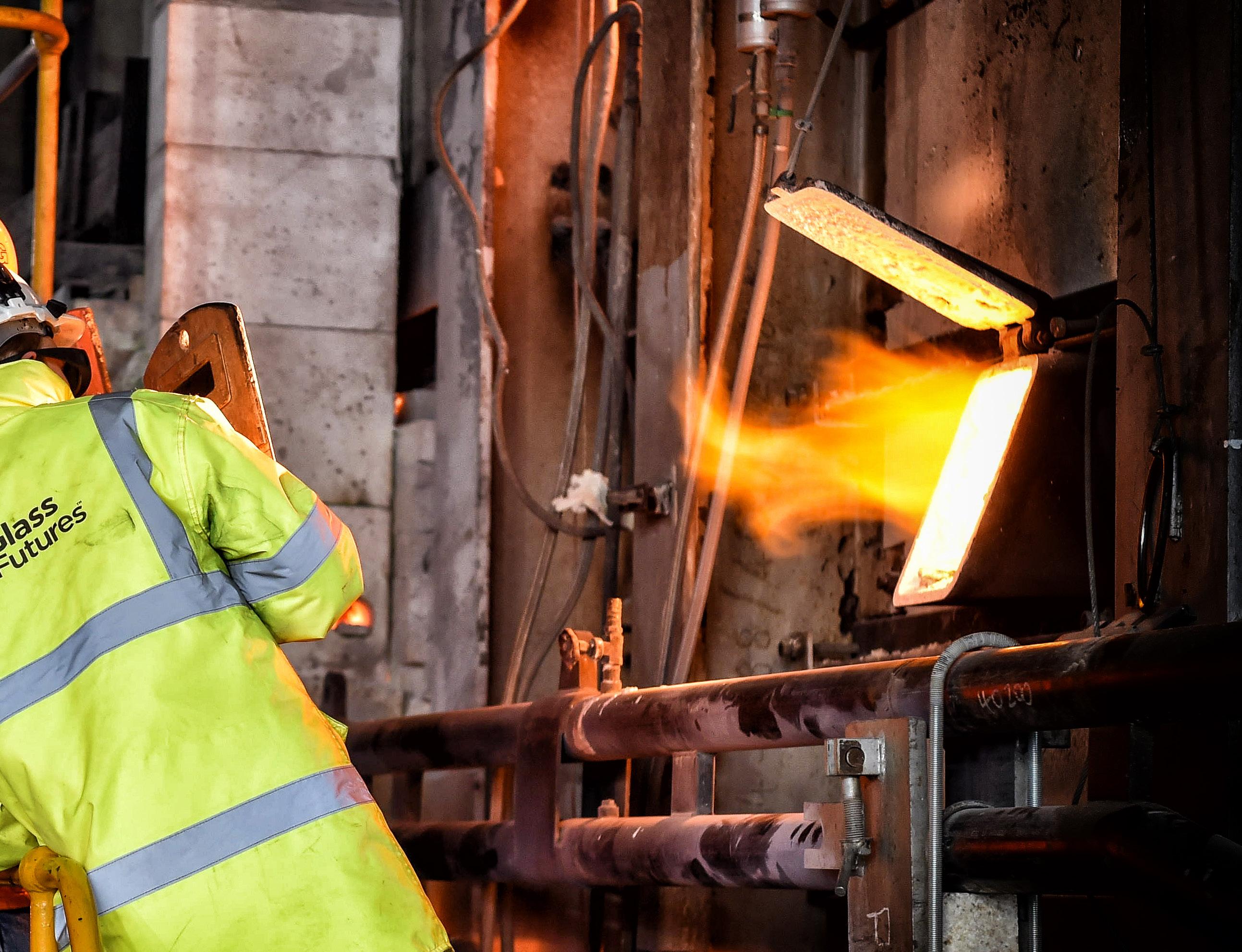
from our research that geography is going to play such a big part in the future energy use of all industries, driven by local, regional and international policies around hydrogen, biomass, electricity and of course, natural gas.
A Problem Shared
The issues discussed are not only a glass industry issue, and moreover within the whole built environment everyone is facing the same challenges but at different times and levels of growth. As such we have realised that working across materials is vitally important, in particular within other Foundation Industries that serve civilisation and the built environment. There are parallels seen in brick making, steel manufacturing, chemicals and plastics, and cement.
Everyone has to make huge changes sooner rather than later and we must look across innovations of old and new within all of these sectors to ensure we progress as quickly as possible; this is where the entire supply chain becomes vitally important. For all architects, specifiers, public policy makers, quantity surveyors this is where you can help play a role by driving the conversation and the request to ensure that our materials, from the beginning of the supply chain are made in a sustainable way.
The Big Problem
The decisions we must make as an industry rely on long term confidence and ultimately there is a huge amount of uncertainty in the world around us, but there is no choice in the end, so we are left with a few key questions: How does the industry change its model to keep pace with the change of society?
How can we enable the industry to make bold decisions in the face of uncertainty for regional energy availability and prices?
What technology developments need to be carried out and what can we do to increase economic certainty in energy prices?
To Collaborate Is To Create
If we do not work together and help create an industry working to change its manufacturing processes, the industry will stifle innovation in deep decarbonisation. I believe that if we do work together, we can accelerate innovation and increase visibility for sustainability projects. This is exactly the reason I am deeply and personally attached to the work of Glass Futures. We are a not-forprofit research group with a mission to help bring about low carbon glass sooner rather than later. Much of the answer is rooted in connecting across the entire value chain, and we welcome all who want to be involved in this global shift.
There is a huge amount of passion across this sector to see this change happen but the answers we need are a combination of processes, cost and people and the space we occupy as a facilitator, introducer and thought provoker allows us to work with our members to promote a new approach to problem solving, so people can find unique solutions for themselves or their clients.
Aston Fuller, General Manager at Glass Futures
Aston is the General Manager of Glass Futures. He is responsible for the day-to-day running of Glass Futures and to ensure that the activities carried out across the Glass Futures programmes align with industry trends, technology and direction.
Aston has worked in the glass industry for over 10 years. He spent 8 years with Ardagh Glass, gaining experience in furnace management, operation, maintenance and capital construction, wider plant engineering and energy management before working with British Glass and GTS on wider cullet recycling research projects, prior to joining Glass Futures.
With a keen interest in entrepreneurship and innovation, especially in relation to sustainability, Aston has over the past few years developed a passion for driving change in sustainable engineering, manufacturing and in helping open knowledge of the glass industry to a younger generation of engineers.
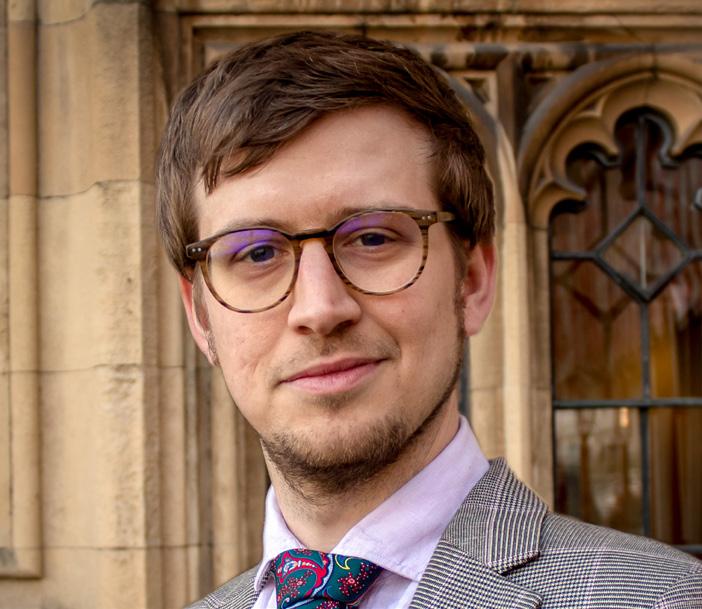


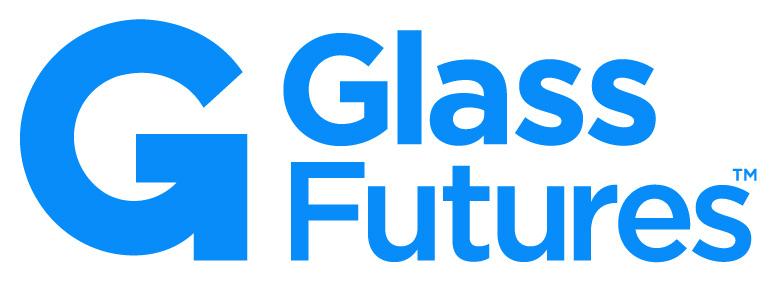