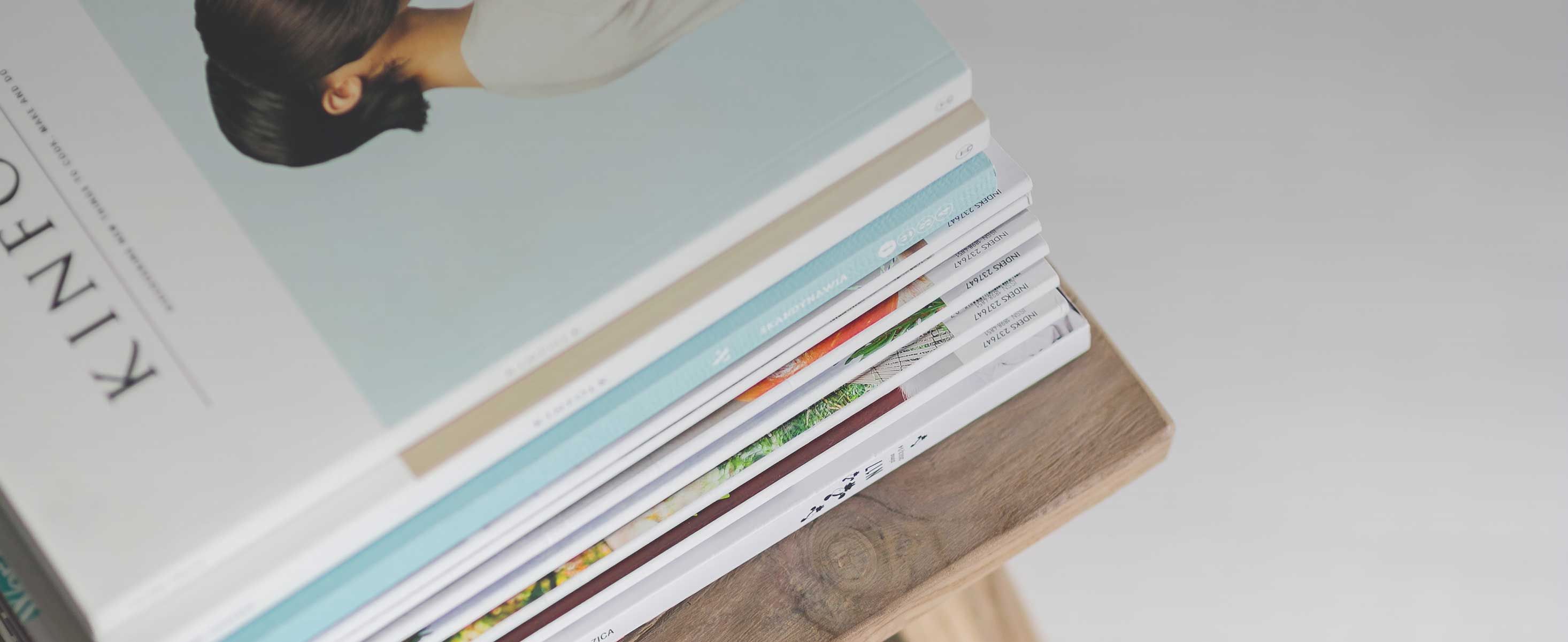
8 minute read
THE PUBLISHER
It’s the start of a New Year and therefore good reason to be optimistic about the future.
Being optimistic has a habit of influencing others positively and I’m sure these same positive vibes are taken on board by our pets.
Having pets that are happy with their owner’s disposition is only part of meeting the pet’s needs, while its food should not be overlooked as another very important part of ensuring they continue to see owners as valuable partners.
Roger Gilbert Publisher – International Petfood
Therefore, it’s important that our editorial team stays focused on what contributes to making the best petfood and which in turn gives pet owners the confidence they need in meeting their pet’s wholistic needs.
We, as a magazine, are focusing on issues relating to nutrition in terms of health and disease prevention, and which is led in each edition by Professor Simon Davies along with the production or manufacture of the final food products themselves which is covered by Joe Kearns.
In this first-of-the-year edition I would like to draw your attention to three compelling articles that I believe will provide you with much useful information.
The first is our article, on Page 16, by Juan Javierre, a Nutrition Scientists with Layn Natural Ingredients in the USA. He talks about the opportunities opening up following changing regulations and greater consumer awareness towards plant-based animal feed ingredients. This article provides greater insight into what we should be considering as we take the industry forward in terms of pet nutrition and health management.
The second, on Page 20 is by Birth Isaksson, the Global Food and Beverage Segment Manager at ABB in Switzerland who highlights the growing difficulties being experienced by food producers due to restrictive supplies on grains, oilseeds and other ingredients along with the impact of higher energy costs. Getting a feel for where we might focus our attention – in this case on greater efficiencies – is important if we are to provide the best service to customers.
The third article on page 24 is from a mechanical point-ofview and has been contributed by Ali Koyuncu, a Research and Development Engineer with Yemmak in Turkey who takes us through the effect extrusion processing has on protein, starch, fats and fibre and provides an alternative view to what’s occurring in the barrel.
All this and the rest of the magazine makes for good reading.
Our Spanish language and English editions
We are pleased to say that International Petfood, which is published in both English and Spanish, is now available via our online library for you to access both the current edition and read back issues at your pleasure.
By signing up for an annual subscription - which for those attending the IPPE event in Atlanta in January 2023 is complimentary with the Coupon Code we have promoted - you will have specific access to our FlickRead website where you will find every monthly edition published in 2022 - in either English or Spanish, the choice is yours.
While we acknowledge that digital copies mean we can reach readers in far-flung places we are also very keen to provide those who value a magazine as a printed version for reading pleasure and reference.
So please go to either of the following links to gain access to your personal library and to manage your own subscriptions in future: English - https://flickread.com/edition/Petfood Spanish - https://flickread.com/edition/petfood_espanol
The Petfood Journal
If our experience with other titles carries over to International Petfood with content being cited and/or referred to in papers in other publications. That is very encouraging for the authors of the articles we publish, sand as a result we wish to credit the materials provided to us. But that is about to change!
IPF is introducing in this month’s issue of International Petfood is the ‘Petfood Journal’. We are now set up to peer-review contributions and provide an open-access platform on our website to accommodate submissions from companies, organisations and individuals who have done considered work and wish to have their contributions properly reviewed and accredited. We will peer-review submissions across the board including equipment and processes.
Unlike the normal features and articles, we publish, there will be a charge to cover the review process, the managing of the papers submitted, their timely publication as peer-reviewed documents and the management of the library where they reside. It may take some time to receive regular contributions to this service. We have posted the opening page of the ‘Petfood Journal’ in this edition. If you wish to contact the manager of the service, please write to the journal@perendale.co.uk in the first instance.
Did you miss our December 2022 edition? If so, don’t panic!
The Interview
With Roger Townsend, President, Behlen Grain Systems
Roger Townsend grew up in a rural area in Southwest Pennsylvania, USA. As a teenager he worked for most of the surrounding farmers, experiencing everything from dairy, hog production, and crop production. He graduated from Grace College, Winona Lake, Indiana, Psychology and Business Administration. Throughout his college years he worked in a local factory and learned manufacturing processes, with a special emphasis on steel fabrication. In 1977 he started in the grain bin industry at Brock Grain Systems, with roles starting as a machine operator, ultimately become Executive VP General Manager.
To read more, go to: https://issuu.com/international_aquafeed/docs/ipf2212_web/36
Mixing, dosing, plant design, standard petfoods, raw materials test for verification
Happy New Year to all as we hope 2023 is a spectacular year for all of our readers. Since we are at the beginning of the year lets discuss the beginning of a petfood process. The raw materials which include all the needed nutrients vitamins and minerals the pets require historically were simple and based on standard available feed style ingredients. Corn soybean meal, wheat mids and meat and bone meal were the main components. Today the sky is the limit for petfood ingredients and many are human food grade. The one element that came along for the ride into pet foods was and still is bacteria. Initially the design and production goal of petfood extrusion was heat pressure and allot of it to get the expansion and cell structure desired. This of course, not by design, eliminated all bacteria off the extruder when 125OC was achieved. As knowledge of the process grew and machinery advanced the science of petfood production and process requirements grew to include elimination of bacteria due the human involvement, touching the product in order to feed the pet.
Joseph P Kearns Editor, International Petfood Magazine
them but personnel movement so as to avoid bacteria’s from following along for the ride. Rooms separation and air pressure of these rooms also reduced dust movement so as guarantees of kibble without bacteria is achieved.
There are now systems which collect samples move them to the lab and automatically place them in testers to ensure product quality without human contact, greatly reducing possible interaction or movement of bacteria on the product after the extrusion or bacteria kill step. Today many fresh products such as mechanically deboned meats are used in the fresh state and considerations for these high bacteria products is also handled by keeping this material in a chill room with only a pipe, sanitary design, going through the wall to the extruder as a separate flow stream. Same for other possible liquid additions.
Standard petfood production in past years was much like making farm animal feeds, basic feed mill designs which were open air and dusty operations. The start of the process in both modern and older plant designs include all the receiving, storage, conveying, grinding, mixing and micro ingredient addition systems. There was not much dust control equipment as mainly the design created dust. Today visits to current technology petfood facilities are generally cleaner than you can imagine. In past years on a trip to Argentina visiting Mars production facilities I met Mrs. Jacqueline Mars. As she passed through the plant. We had a brief discussion and I recall telling her I was impressed with all their facilities in the world. She asked why and I informed here she had the cleanest kitchens in the petfood industry. Obviously, there were others just as clean but in hind sight these companies knew the need for cleanliness, bacteria control, dust control.
Processes in the raw material area, all of them, are quite good at creating dust. Conveying, grinding, mixing etc. all created dust. In the late 60’s and early 1970’s dust control equipment was coming on strong along with pneumatic conveying for raw materials as well as in the production area. These were tremendous in filtering the air and moving products with less dust development or release into the factory. It is now normal to have dust control on grinders, mixers and conveying equipment. Mixers, micro systems and grinders specifically with the addition of air movement control greatly reduced losses of ingredients some of which are quite expensive. Closed loop, air movement, individual systems greatly improving the control of bacteria movement in the plant. Verification of the bacteria in raw materials needs to be assumed as negative as you can bet it is present. Better coefficient of variance of mixers as well as accurate dosing systems created a more homogenous batches insuring all of the kibble included the same nutritional benefits.
Plant designs changes in addition to the equipment improvements where raw material prep and production operations were separated not only the atmosphere between
Having seen plants throughout the years and changes as they developed there are many different possibilities to achieve the desired goals. Separate building for batch preparation with pneumatic conveying to the process building, plants with virtually no windows, controlled entrance points, employee sanitation rooms or stations, methods to clean the plant with verification swabs or test methods for machinery surfaces, machinery designs to reduce bacteria build up with standard operation procedures to ensure priorities are in position and followed.
In this year’s issues we hope to cover many of the abovementioned possibilities. Positive and negative pneumatic systems for powders or raw materials, finished goods as well as between extrusion and drying. Grinding with air assistance and dust control and the same for the other processes involved. Discussions on the end of the extruder kill step verification, dryer moisture control and other topics greatly effecting product quality and bacteria elimination. Having mentioned a number of these topics can you imagine trying to control all of these processes by hand, without some sort of management system such as computer assistance or control. It was not that long ago that the operator of the extruder did it all by hand, started motors, turned steam and water valves, checked the product out of the conditioner before and after the extruder, ran around to be sure the raw material area was giving him what was needed to make a kibble. Have you ever seen an operator struggle to make a product putting tons on the floor due to some sort of situation? How about something so simple as an ingredient was somehow left out which greatly changed the expansion of the kibble. Low steam pressure, no water, product quality off the dryer, how about the coating system is the % added in liquid form correct? Hand checking all flow rates to confirm or predict the outcome. To be honest it was hectic to say the least and one that was worth living through so complete understanding of what is going on understood. This knowledge is used when the current computer systems require an investigation as to what needs to be corrected and/ or be calibrated for accuracy of production. With the modern computer control packages for the entire system all calibrated is a wonder to see in operation. Looking forward to 2023 and all the possibilities in front of us.
Professor Simon Davies Nutrition Editor, International Petfood