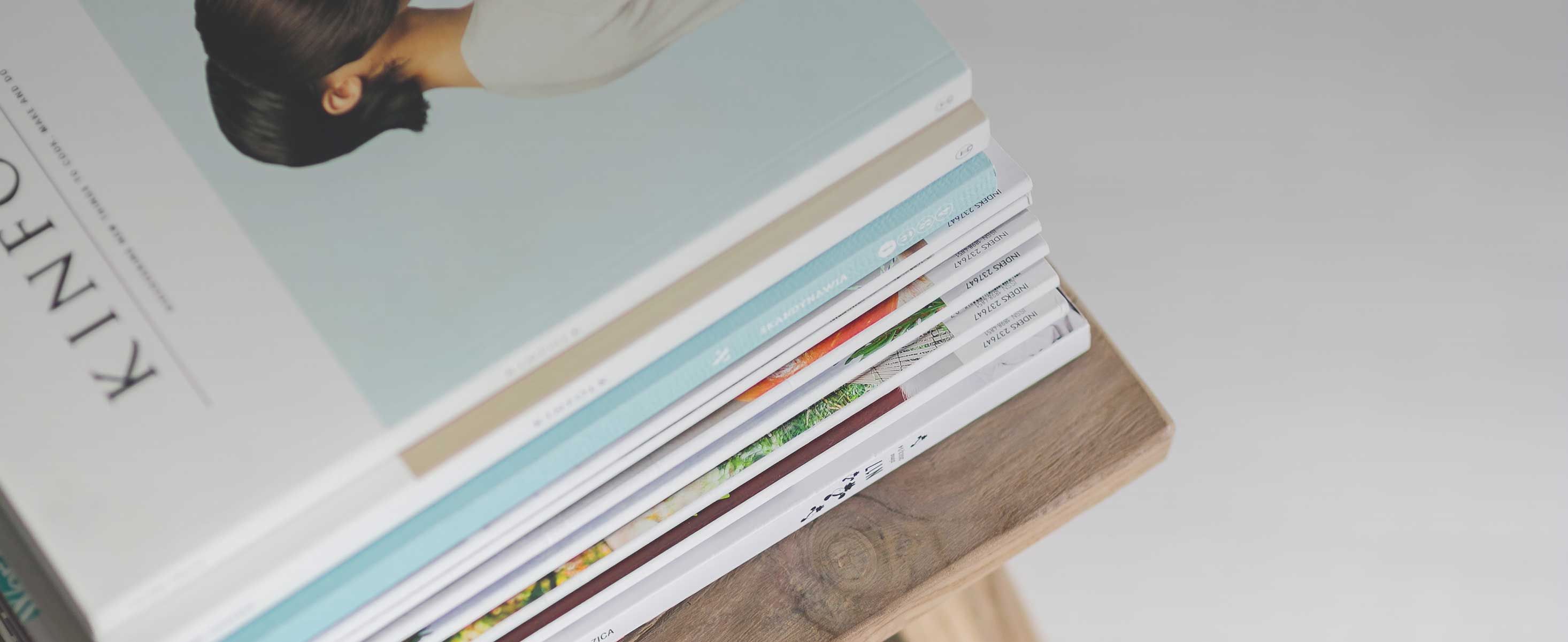
3 minute read
Troubleshooting
Situations in the petfood production process require in some cases looking backwards on how things were done in the past to solve the problems associated with the modern control of the system. Computer controls are great and work very well in all cases but they can cause some head scratching when you are sitting in front of a computer screen trying to accomplish production. Solving problems when in production might require using old school ideas to succeed. The computer system is designed to do what was done by hand historically. Dry flow rate, the feeder screw to the conditioning cylinder now mostly use loss in weight for flow control. Historically it was a volumetric method so the speed of the screw associated with the density of the dry raw materials actually set the extruder rate. With LIW systems the computer knows what should be flowing and it searches for this exact rate by feeder screw RPM. Sitting at the computer panel you see the system changing for the right set flow rate and it is modulating. What is going on as the RPM is increasing but the feed rate is not as it searches for the correct volume. Solution, check feeder screw and remove the blockage, flow corrected. When hand operated an operator would turn the RPM on the feeder screw up to achieve the rate based on a calibration of flow rate vs RPM for that recipe. A graph of flow rate vs RPM is made at different RPMs to generate a curve allowing the capacity to be set by the RPM reeding. Made by collecting a sample at an RPM for 30 or 60 seconds and repeat at different RPM ranges. The graph then allows estimation of what RPM for the desired rate. Had a situation once where the feed rate was off as the load cells on a computer-controlled system was not calibrated exactly. Was receiving one tonne extra dry raw materials then expected plugging the extruder as the liquid injecting were not enough for the dry flow rate. Staff surprised when a large scale was requested and bags to check weigh dry flow rate against what the computer showed. The operators learned that day that what the computer showed was in some cases not true and how to figure it out with the old school methods. Load cells calibrated and then all in order.
Same goes for the liquid flow rates. Calibration of the flow to achieve the right mix. Check the flow rates with a bucket at the level of the injection for accuracy. Had one situation when all was perfect and in the middle of the operation everything went wrong kibble way to wet and a mess and nothing was changed? Further review showed the system ran the boiler out of steam and we were pumping water instead of steam into the extruder.
The goal is understanding what the process is and what the computer is doing and how to verify the system is working correctly. Sometimes it might require some old school methods to test and determine what not working correctly
Previously on Troubleshooting...
1. Density
An examination of product density and its relationship with moisture levels, heating, cooling feeder screw rate and automation.
2. Non-uniform and rough appearance
A guide to understanding the science involved in improving the art of making products of all the same size.
3. Extrusion dies
This article takes a look at aspects of the process including high, medium and low shear as well the adjustments required when producing feed for small mammals.
4. Dryers
The dryer is without a doubt one of the machines in the system which greatly impacts the bottom line.
5. The Extruder Barrel - Part 1
Forming extruders are used for some select products –thus this part of the discussion centres on single and twin designs.
6. Cook in the Extruder Barrel – part 2
As discussed last month, the extruder barrel has a number of functions, but the main goal is to finalise the cook, yield the desired shape with the density target.
7. Coating
The coating process has a few areas of importance, with this edition of ‘Troubleshooting’ exploring the most important of these.
8. Expanded cat food
Dry expanded cat food production is similar to dog food production, but there are some differences, with this edition exploring a choice selection of these.
9. Extrusion during operation
This month we discuss steam input into the conditioner. During the water addition process, the steam is usually in the two-bar range.