
3 minute read
BUCKET ELEVATOR EFFICIENCY
Continuous bucket elevators are widely used in many facilities for the transportation of bulk solids. While a well-designed continuous bucket elevator is an effective material transport method, there are factors which can degrade the overall efficiency of a piece of equipment.
In this article, UniTrak highlight four tell-tale signs of bucket elevator inefficiency and their potential causes, whilst also explaining that if these issues are not addressed, they can seriously compromise the performance of your equipment.
Sign #1: Infeed losses
A critical, but often overlooked aspect of bucket elevator design and operation is considering how the equipment will be fed. Failure to control and regulate the feed of material into the elevator can result in product losses and damage, as well as reduced throughput.
Common causes of infeed losses include:
- Failing to achieve an even distribution of product within the elevator’s buckets. This problem often arises when product is being fed at right angles to the elevator.
- Overfilling the buckets. Feeding product at too fast a rate can result in bucket overfilling, spillage, and plugging of the elevator’s infeed section.
- Dropping product into the elevator from too high a height. This can cause particle damage and attrition.
- Feeding the elevator before the running speed is achieved. Feeding in product before the optimum running speed is achieved can result in underfilling of the buckets.
Sign #2: Reduced speed
Reducing the running speed of a continuous bucket elevator below the designed or planned rate is often a response to other problems, such as the infeed problems described above.
Reduced speed may also be necessary when the elevator spills or damages product when running at the planned rate, or when downstream equipment is unable to accept all product from the elevator when it runs at the planned rate.
The solution in all cases is to investigate and correct the root cause of the problem so that the elevator may be run at the rate that it was intended for.
Sign #3: Reduced yield
Reduced yield can take several forms. First, the quantity of product that the elevator delivers to downstream equipment may be lessened through losses from spillage, failure of some product to discharge from the buckets, etc.
Secondly, the quality of product delivered by the elevator may be compromised as it moves through the equipment. Both types of losses, quantity and/or quality, represent yield losses.
For the first case, addressing the causes of spillage or failure of material to discharge will improve the quantity of product delivered by the elevator. Material spillage can be a function of equipment design as well as operating procedure.
For example, continuous bucket elevators designed with interlocking buckets, as opposed to those which merely overlap, will always be more effective at preventing spillage.
In addition, overfilling the buckets, either by presenting material to the elevator at too fast rate or running the elevator at too slowly, can result in material spillage.
The solution in either case is to make the necessary adjustments to material feed rates and/or the run speed to achieve the optimal bucket fill. Failure of material to fully discharge from the elevator buckets can be addressed through the use of discharge aids, such as ‘bucket knockers,’ which are designed to dislodge material from the elevator buckets at the point of discharge.
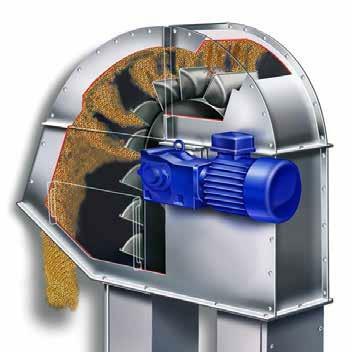
In addition, conveying materials which are inherently sticky, and can have a propensity to adhere to the bucket surfaces may require the use of buckets with Teflon-coated or dimpled surfaces.
Quality degradation often manifests itself through particle attrition or breakage. The solution in this case is to use an elevator designed for high-care conveying and which is capable of gentle handling. This will prevent particle attrition or breakage and ensure that what goes into the elevator is what comes out.
Sign #4: Unplanned downtime
Unplanned equipment downtime due to parts failure can seriously erode the operating efficiency of a continuous bucket elevator. Whilst you may never entirely prevent the occurrence of unplanned downtime, there are certain steps that one can take to minimise the impact of such events when they do occur.
These steps include:
- Keep a bench stock of critical operating parts on hand at all times. This allows fast recovery from an unplanned downtime event.
- Track your parts failure history to discover which elevator parts are most prone to failing and which should be stocked.
- Practice condition-based maintenance. Maintenance of the elevator should be based on its actual condition, rather than according to a calendar-based schedule. Elevators can also be fitted with condition-based monitoring devices which alert operators and maintenance personnel when an abnormal condition is developing.
UniTrak manufactures the TipTrak® line of continuous bucket elevators. These elevators are renowned for their high reliability and gentle handling.
To find out more about the TipTrak line of continuous bucket elevators, visit the company’s website at: https://mymag. info/e/1537