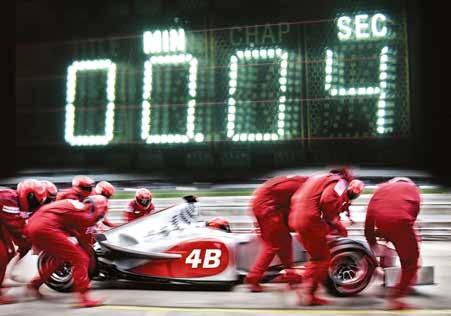
3 minute read
Animal feed Energy efficient technology for a vital food segment
by Brith Isaksson, Global Food and Beverage Segment Manager, ABB, Switzerland
The animal feed production industry’s top priority is to produce healthy, high-quality and ethical products to ensure that poultry, fish and other livestock are well-nurtured. However, it is also under increased pressure to improve the costefficiency, safety, sustainability and overall productivity of its processes.
This concern has been heightened by an ongoing supply chain crisis which has resulted in a global shortage of grains and oilseeds. It has added even greater urgency to make existing animal feed production processes as efficient as possible, with minimum wastage. The rise in oil and gas prices, along with labour shortages, has also produced an additional squeeze on costs for businesses.
Furthermore, the actual production process for animal feed – whether that’s chicken feed for poultry farms or fish feed for aquaculture – typically involves the use of various industrial machines required to run optimally at all times. These could include hammer mills, extruders, mixers, and conveyors, depending on the specific type of feed.
These applications are primarily controlled by motors, drives, and programmable logic controllers (PLCs), the selection of which is critical for several reasons.
Reliable motors for steady production
Motors often have unique and demanding requirements in segments such as animal feed production. Reliability and 24/7 operation are critical to ensure a steady production environment in all conditions while responsibly using raw materials and energy.
Crucially, animal feed production must be a carefully controlled, precise process to provide the right quality and mix of food for animals and avoid unnecessary wastage.
Whether or not these production processes can be performed optimally depends on how well the motors and drives control the machines. With growing pressure on farms and the wider food supply chain, these motors and drives must also be as robust and reliable as possible, avoiding unnecessary downtime that could disrupt operations.
Digitised methods such as remote condition monitoring – the practice of using sensors and software to monitor equipment performance – are also business-critical. Disrupting machines for maintenance is troublesome when considering the cost implications of asset downtime, labour, and spare parts, not to mention the contamination risks when opening up a machine for repairs mid-cycle.
By providing real-time data that shows fluctuating asset behavior, condition monitoring tools make it possible to perform predictive maintenance. Once the erratic behavior exceeds the accepted, user-defined norms for the asset, the plant leaders and maintenance personnel receive an alert through the monitoring platform, which allows them to act before a problem becomes acute.
This approach eliminates the waste typically associated with unnecessary routine maintenance checks.
SynRM technology for optimal energy efficiency
Animal feed production can be very energy-intensive and expensive, especially with the increasing costs of energy. It is, therefore, in the best interest of production companies to fully optimise the energy usage of their heavy machine applications.
Deploying a condition monitoring solution can also provide real-time data on energy usage. This allows an operator to make manual adjustments or add a PLC (such as ABB’s AC500) to make automatic adjustments to reduce energy consumption and cut costs.
Further, electric motors will typically run at full speed all the time, regardless of the particular demands of the process, which wastes energy. Pairing motors with variable speed drives (VSDs) can automatically adjust the motor’s speed and torque to match demand.
Swiss-based UFA’s Sursee poultry feed mill is one of only a few unmanned feed mills in the world, running from 9pm until 5am every day without any operating personnel. The plant’s production is overseen by only one mechanical engineer.
Until 2015, the mill used an aspiration ventilator with a conventional 75-kilowatt (kW) induction motor directly coupled to the power grid and operating at a fixed speed. While the ventilation system was considered advanced when it was installed in the 1980s, it was time for a replacement.
Having read about a hospital ventilation system that uses synchronous reluctance motor (SynRM) technology, the engineer was impressed with the high energy efficiency of these motors. On his advice, UFA decided to invest in the same motors for the feed mill’s new ventilation plant.
ABB installed a 37 kW SynRM motor to power the new aspiration ventilator, controlled by an ACS880 variable speed drive. Combining the latest ventilation and motor-drive technology resulted in a 50 percent drop in power consumption and a considerable reduction in CO2 emissions. As a result, the drive package paid for itself quickly.
Motors & drives for added safety
Animal feed production is critical for all animals in the food supply chain, as livestock safety is paramount. Animal feed must be nutritious and free of contaminants so that food products are safe for human consumption.
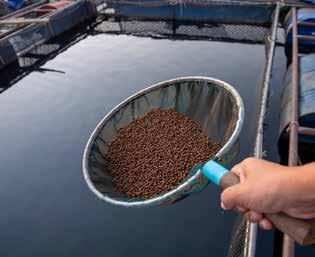
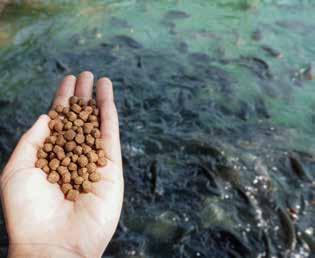
The quality of animal feed is also highly regulated. It’s possible to address all these safety concerns by ensuring that different animal feed applications run as safely and efficiently as possible, using the right drives, motors and services. Moreover, when these applications work correctly, it also minimizes the chance of accidents that endanger people working at production facilities or on farms.
Balancing the need for hygiene with the need for productivity and reliability is a challenge. However, new developments in electric motor technology are helping animal feed production facilities to meet hygiene standards while still achieving maximum uptime.
Yet drives, motors, PLCs, and service all play a vital part. Therefore, specifying the best equipment for each environment is essential in ensuring optimised, reliable, and efficient production.