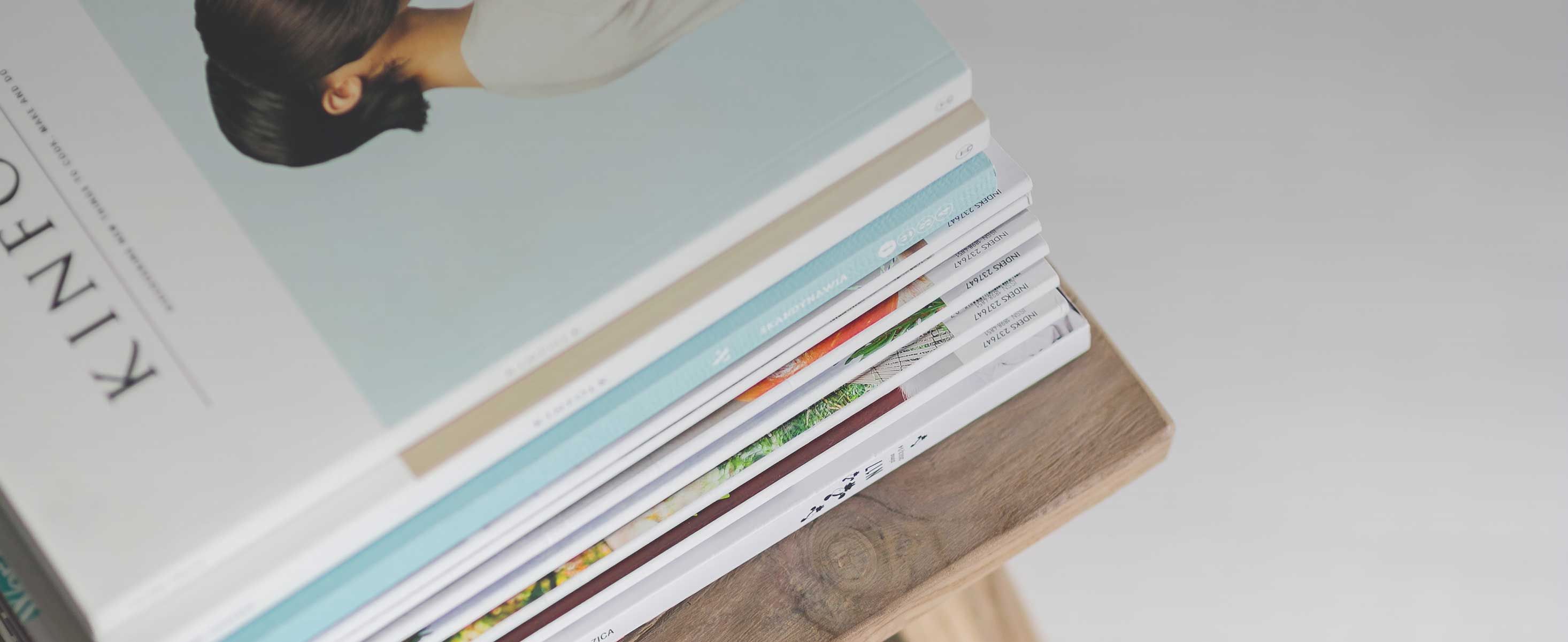
4 minute read
THE PUBLISHER Our last edition
Did you miss our December 2022 edition? If so, don’t panic!
The Interview
With Roger Townsend, President, Behlen Grain Systems
Roger Townsend grew up in a rural area in Southwest Pennsylvania, USA. As a teenager he worked for most of the surrounding farmers, experiencing everything from dairy, hog production, and crop production. He graduated from Grace College, Winona Lake, Indiana, Psychology and Business Administration. Throughout his college years he worked in a local factory and learned manufacturing processes, with a special
Gilbert
emphasis on steel fabrication.
In 1977 he started in the grain bin industry at Brock Grain Systems, with roles starting as a machine operator, ultimately become Executive VP General Manager.
To read more, go to: https://issuu.com/international_aquafeed/docs/ipf2212_web/36
Aquaria feed for fish is in my mind considered a petfood. They must have a complete diet for long and health life. The process differences between aquaria and commercial aquatic feed for farmed fish if negligible. However, there are differences, mechanically speaking grinding of the raw materials, the extrusion dies and the dryer configuration to name a few. Other than extrusion drum dryers are also used to make steam flaked aquarium feeds. Extruded aquarium feeds can have a very small diameter, down in the 0.5 mm range. The future for aquarium feeds over the next 10 years or so looks good with a compounded annual growth rate, CAGR, predicted to be 5.5 percent. It is expected these kinds of feeds would be batch made in a controlled environment on smaller production equipment designed for micro feed production if extruded. Making them is the easier part, packaging small amounts in numerous various designed containers is in my opinion much more complex.
Joseph P Kearns Editor, International Petfood Magazine
Additional topics for Feb include freeze dried petfoods which are growing at a CAGR of 7.7 percent in the next 7 to 8 years. Driven by the desire to have shelf stable products and healthy snacks. This segment is predicted to close in on 30 billion in sales over the next decade. As pets continue to become family members, we will see a move to more humanized petfoods become available.
The ever-increasing complexity in petfood production of all types we will also see a continued growth in the control segment of the business. Regulations as well as product complexity and the stated nutritional and product characteristics on every bag requires exacting control. Throw in the benefits of efficiency, reduced losses, increase in productivity as well as improvements in the controls make this area one of the fastest growing activities in petfood production. Having started in the era where you were lucky to see an indicator of valve position on some valves and very lucky to see flow meters on the water and liquid inputs to today’s standards was most interesting to be involved. Steam was definitely a guess and the operators did have a major input in product quality. This historic period did generate the data and designs to predict and model extrusion as well as other production methods so the hardware became more predictable and long lasting. Example, if dryers improved to 0.5 percent +/- moisture variation then what use is a measuring device that is good to 1.0 percent? The industry did catch up and flowmeters liquid and dry, measuring sensors for temperature and pressures, pump accuracy, motor controls and many others have had big impacts on the petfood industry.
I do not recall lacking extruder head temperature controls and in historic photos only the earliest models did not have jacketed extruder heads for steam or water flow. Standard on any large capacity extruder today with either liquid or electrical designs. My perspective over time is these jackets allowed greatly for getting into production by heating the heads to temperature, and it worked. Once running as expected the heads mostly went to cooling and specifically towards the discharge end of the barrel. Steam jackets back in the day of extruder stoppage or blockage allowed heating them up and possibly get them going without disassembly. Typically, if the heads are too hot the extruded might surge and produce non uniform products. You might see a higher motor load, sticky and clumping of product as well as variation in density. Today computer control has all of these specifications entered for each product and can be monitored quite easily. In addition to temperature control pressure reading along the barrel can give an indication of barrel fill in one or multiple areas. Allows for understanding where the cook is occurring and where liquid injections can be made. Ten bar steam pressure is the norm for having the ability to inject into the extruder barrel in the needed zones. Water normally added in the back of the barrel is lower as in the 4-bar range.
Dryers as well as coolers have also greatly advanced with sensor capabilities to measure the air temperature, flow rate, dew point both wet and dry allowing for computer control for efficiency and product quality. Systems are available to collect a sample off the extruder for density and moisture content, feed a signal back to the control system to adjust density if needed as well as adjust dryer knowing the moisture into the dryer while running. Similar systems post dryer can do the same with the idea of adjusting the dryer based on discharge moisture and verify density before coating.
Long good pet treats of the extruded variety require a die where the flow through each orifice is adjustable so the strips travel downstream at the same rate. Normally these type treats are high in meat and die cutting directly is not effective. Cutting at the end of a take away belt with a rotary cutter allows for product set up before cutting. Gentle conveying and handling are needed when using a dryer and or cooler. Cooler, moveable try style, only if it is a semi moist stye product.
Reader input asked about the Ukraine and Russia petfood industry. A bit of research has shown that Western major producers have slowed and even stopped production and shipments into Russia. This has placed a shortage on petfoods with specialty feeds hardest hit. The Russian market is changing with less import petfoods pet owners are buying larger volumes of locally produced products resulting in increases in Russian local production. Ukraine is receiving aid from multiple sources internationally for pet needs with donations. If interested, google pet food donations for Ukraine and multiple sites will appear. These situations will remain until the crisis is resolved.
Professor Simon Davies Nutrition Editor, International Petfood