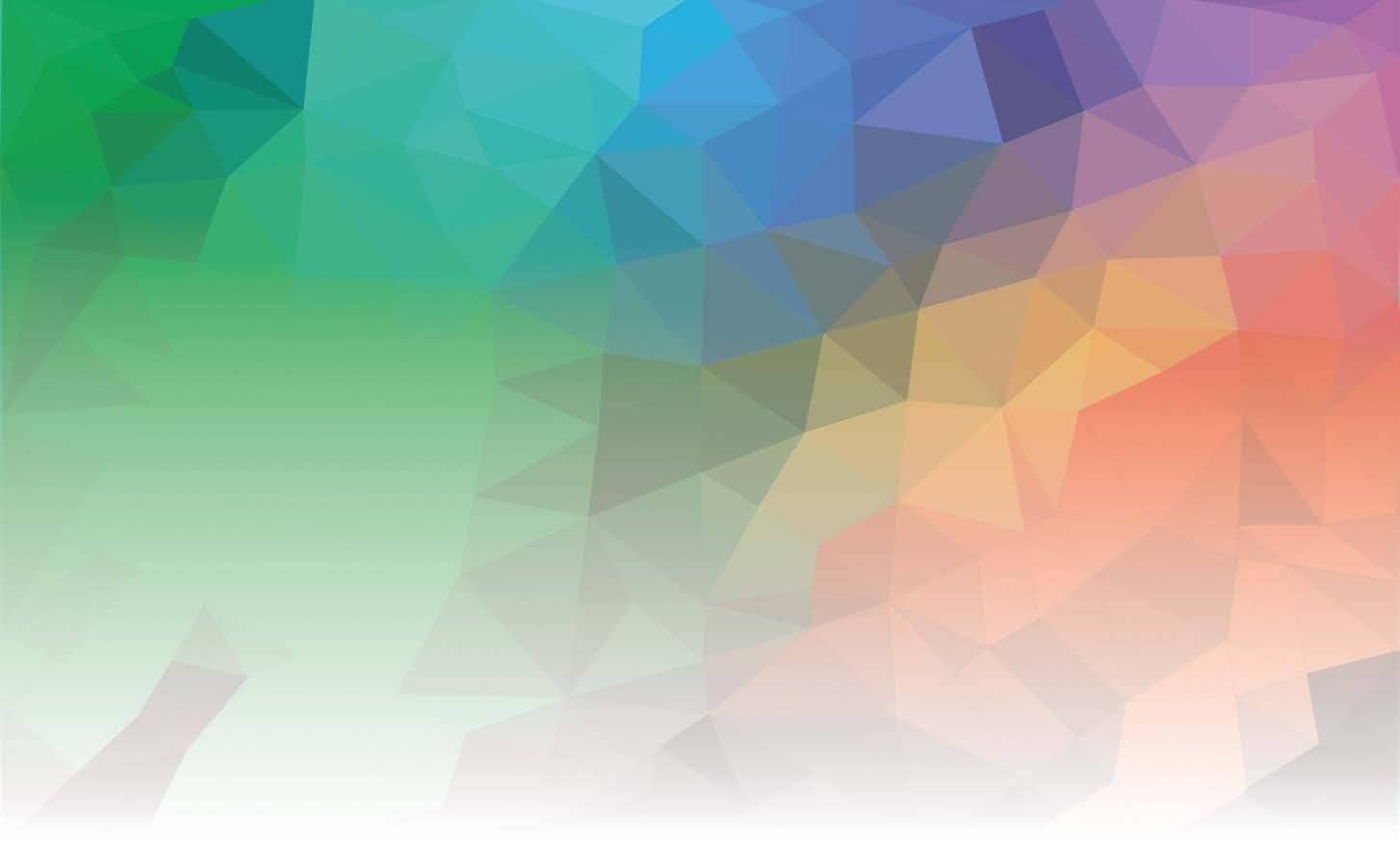
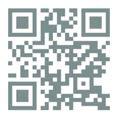
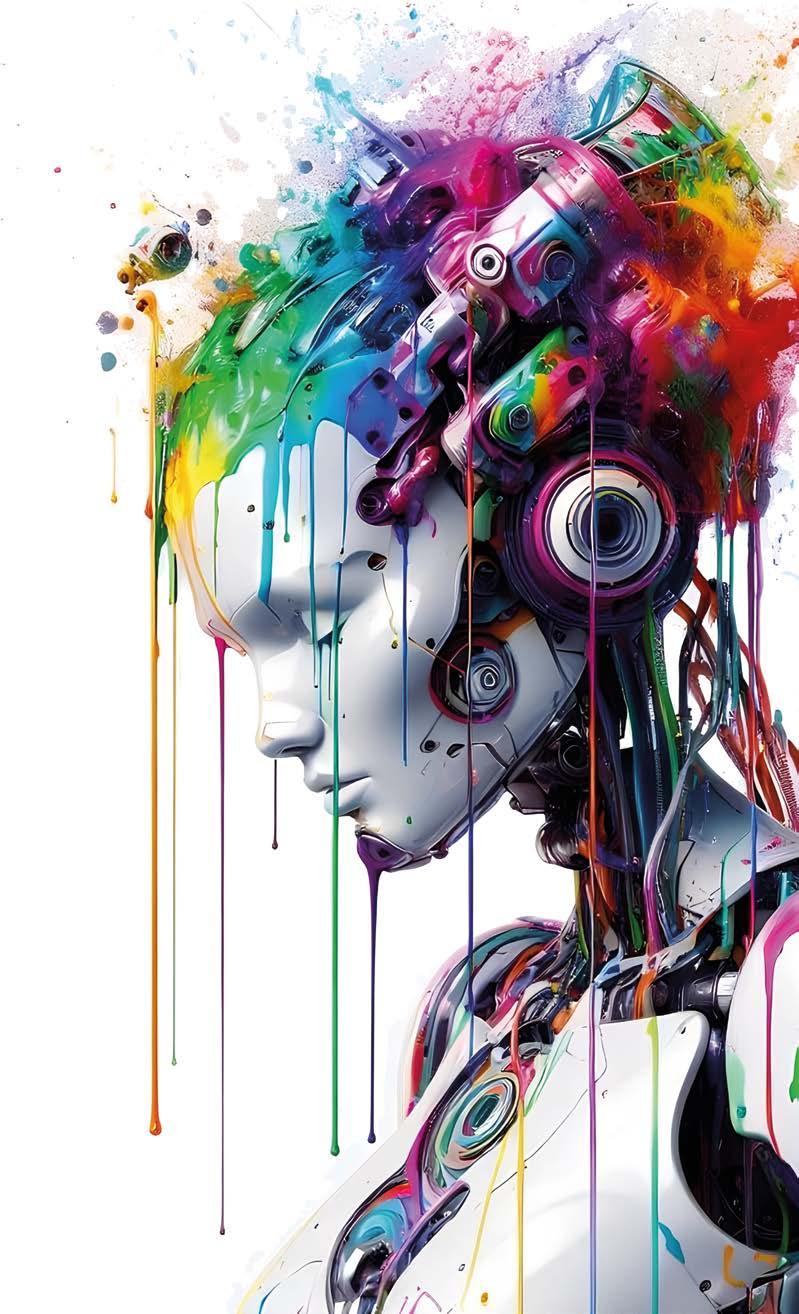
Sustainable. Durable. Revolutionary.
Unlock a new era in sustainable design with Alesta® BioCore™, the innovative bio-based powder coating that reduces scope 3 emissions by up to 25%.
Developed from non-food organic waste, our products seamlessly blend environmental responsibility with top-tier performance.
Environmentally Friendly Innovation
Using biobased resins derived from non-food, organic waste, Alesta® BioCore™ does not compete with food resources, supporting a more sustainable supply chain.
Proven Excellence
As the first in the industry to earn the International Sustainability and Carbon Certification PLUS (ISCC PLUS), Axalta sets the standard for eco-conscious manufacturing.
Equivalent Quality, Lower Emissions
Our Alesta® BioCore™ solutions match the quality and properties of traditional polyester resins but with a significant advantage: they enable an average CO2 emissions reduction of 25%.
Our Premium Range:
Alesta® SD BioCore™: Architectural SuperDurable
Alesta® AP BioCore™: Architectural Alesta® IP BioCore™: Industrial
Make the switch today and embrace sustainability without compromise. Alesta® BioCore™ offers a responsible choice for a greener tomorrow.
Learn more: www.axalta.com/biocore
User-friendly and ergonomic manual powder gun
LIFETIME FINISH QUALITY:
Long life waterfall durability and HV performance
BALANCED AND ERGONOMIC DESIGN: No repetitive strain damage, less fatigue
Visit us at Surface Technology Germany in Stuttgart from 04 to 06 June. Hall 1 / Booth C26
DELTA-PROTEKT ® TC 502 GZ is a silver hybrid topcoat with excellent friction properties for use on metric components.
FOCUS ON TECHNOLOGY Towards Excellence: Pleion Revolutionises the Coating of its Thermal Collectors with a New Plant ADVANCEMENTS Carbon Fibre Coating: Technologies and Solutions to Preserve Performance and Elegance
HIGHLIGHT OF THE MONTH
SpeXparts: an Italian Company of Excellence in the Production of High-Quality Hoses for the Industrial Painting Sector
Oregon State Researchers Advance Pigment Chemistry with Moon-Inspired Reddish Magentas
Painting Srl Increased the Quality of Its Products by Installing a New Powder Coating Plant and Implementing TORAN 3®
Energy Savings Hinge on Pump Selection and Installation
STANDARD&LEGISLATION The 5.0 Transition Plan Goes Beyond Industry
MEETING THE INDUSTRY
Technology and creativity share much more than we might think. In fact, creativity is the main trait of technology. Creativity is also the main competitive driver of any ecosystem, as its ability to produce ideas and innovations is what enables it to stand out and excel over others.
If technology is the realm of machines, creativity is the dominion of the human mind. There can be no technology without human capital that knows how to use, control, and master it. There could be no technology without the innovative creativity of those who invented it.
Even in fields where technology apparently does not belong, it actually breaks forth with the power of creative ideas, when new colours are created, new shapes engineered, new materials formulated. And new technologies are invented, along a continuum that is proper to human development.
Does it make sense to demonise technology?
No, it does not, because it is a product of humans – and as long as it remains a tool for humans.
Transition 5.0, a topic I introduced in the previous issue of ipcm® and which is also discussed on page 138 of this magazine, finds its meaning precisely in the centrality of human beings in their relationship with machines, suggesting new models of ethics and sustainability, which some farsighted companies have already been putting into practice for some years.
In this issue of ipcm®, which contains a focus on architecture & design but also presents many innovations seen at PaintExpo 2024, the two worlds of creativity and technology meet, converge, and intersect, revealing their mutual potential and influences.
It is an issue full of colours, shapes, and emotions, with lots of content showing the increasingly sophisticated integration of technology into design, up to becoming an integral part of the everyday human experience.
It is an issue proving the critical role of storytelling around a product’s manufacturing process, with a focus on the quality of raw materials and processing phases. This approach emphasises the need for developing optimised and controlled workflows that guarantee high standards of quality, functionality, and aesthetics in products.
It is an issue that tells the stories of great companies such as La Marzocco – one of the Italian firms of excellence that the world envies us, especially where coffee is most loved and appreciated – and Pintarelli Verniciature – one of the most qualified and certified coating contractors in Italy, active above all in the field of architecture. We will also delve into the trends that emerged during Milan Design Week 2024 and some new technologies in the finishing world that facilitate the work of engineers and designers.
Finally, in the wake of the great success of PaintExpo 2024 – this trade fair’s most international edition ever – we will explore some of the innovations presented there, reaching industrial worlds far removed from design but just as fascinating and capable of paying the utmost care and attention to finishing with a view to sustainability. We will walk through the doors of Next Hydraulics, one of the leaders in the field of hydraulic cranes, Pleion, a supplier of solar energy equipment in Italy, and Painting, a coating contractor that has chosen to invest in sustainability in terms not only of environment but also of its workflow, hand-picking the right technologies to offer a reliable, customised, high-quality service to its selected customers. Many voices and many experiences, united by creativity and sustainable innovation.
The innovative ceramic materials for metal coatings can potentially increase the efficiency of gas turbine, enabling power plants to produce more electricity and aircraft to consume less fuel.
The researchers at Skoltech have recently identified ideal ceramic materials for metal coatings that would increase the efficiency of gas turbines. They will subject these materials to further experimental tests and, if successful, the coatings will enable power plants to produce more electricity and aircraft to consume less fuel.
In fact, thermal barrier coatings are used to protect turbine blades in power plants and jet engines. The blades are made of nickelbased superalloys, which offer an excellent combination of high temperature resistance, toughness and resistance to degradation. However, when temperatures get high, the superalloy softens and can even melt.
Therefore, protective coatings allow turbines to operate at higher temperatures without compromising their integrity and increasing efficiency.
“Thermal barrier coatings are nowadays made of yttria-stabilized zirconia, but if a material with better properties were used instead, that would allow you to get more useful power out of the turbine. To find such materials, you first have to come up with candidates whose properties you predict computationally. We have tested a range of methods and determined the best of them for calculating the relevant material properties, particularly thermal conductivity. In the paper, we list some promising candidates, and we’ll keep on
looking,” has stated Artem Oganov, who heads the Material Discovery Laboratory at Skoltech. Furthermore, a material for thermal barrier coatings must fulfil several requirements:
Having a very high melting point and a very low thermal conductivity;
When heated, the material must expand at approximately the same rate as the superalloy, otherwise it will flake off the surface;
The material must not undergo phase transitions between ambient and turbine operating temperatures, which would cause the coating to crack;
It must resist the effects of dust particles and oxygen at high temperatures and prevent oxygen ions from reaching the underlying metal and oxidising it.
“While we did calculate the other properties, the crux of the problem is predicting thermal conductivity. We showed such predictions are computationally feasible and reasonably accurate with homogeneous nonequilibrium molecular dynamics simulations. This proves somewhat unexpected, as such simulations involve a massive number of computations and extensive statistics, resulting in high computational complexity. Nevertheless, we managed to simplify the method by supplementing it with machine learning potentials: That is, the interactions between the atoms were predicted using artificial intelligence, rather than being directly calculated,” has added Majid Zeraati, Skoltech PhD student.
For further information: https://new.skoltech.ru/en/
AkzoNobel transformed the Interpon user experience with a new interactive website.
The Interpon division of the international paints and coatings manufacturer AkzoNobel has recently launched a vibrant new stylish website, which will include a host of new features and digital tools to enable a more interactive and dynamic user experience for visitors.
The new redesigned website is a single hub imagined to enhance the customer experience by making it simpler and more intuitive. As a matter of fact, it has been created with a customer-first mindset, highlighting the extensive involvement of the company across key sectors – from architectural to industrial powder coating. The design prioritises ease of navigation, allowing users to seamlessly access information on range of products, their applications and the markets served. In addition, it will also include updates on product launches and industry news.
The new Resources section features a wide range of tools, from the product finder to the latest brochures, all aimed at making information access as straightforward as possible, while the Showcases gallery offers a visual tour of architectural projects worldwide, providing a glimpse into
the potential applications and aesthetic contributions to buildings and structures.
Among the new and exciting features there is also an interactive map of the world, in order to quickly allow customers to find their nearest Approved Applicator by simply entering a Zip or postcode, alongside in-depth case studies of how AkzoNobel is supporting its clients around the globe.
“The website is all about enhancing the customer experience: it is a user-friendly destination for customers to learn more about the innovation, sustainability and colour expertise in powder coatings of AkzoNobel, with the best apps and interactive tools to provide all the of information you need at your fingertips. We are incredibly proud of our new site which is the result of a significant investment in time, resource and imagination and enables customers to fully experience the Interpon difference,” has stated Remco Maassen van den Brink, the marketing director of AkzoNobel Powder Coatings.
For further information: www.interpon.com/gl/en
Orion presented its portfolio of high-performance gas black pigments, three new sustainable carbon blacks and the PRINTEX® kappa 50 conductive black.
At the American Coatings Show + Conference, the global trade fair dedicated to the paints, coatings and inks industry that took place from 30th April to 2nd May in Indianapolis (U.S.A.), the international specialty chemicals manufacturer Orion S.A showcased its portfolio of high-performance gas black pigments, three new sustainable carbon blacks and the PRINTEX® kappa 50 conductive black.
The XPB 10045 is the first circular gas black for coatings systems designed by Orion. It has been specifically developed for high-jetness applications and it is compatible with all suitable coatings systems. The XPB 10042 and XPB 10049 powders, on the other hand, are the first circular furnace blacks of the company for tinting applications
“Our new circular grades based on pyrolysis oil and renewable sources meet the same application requirements as conventional specialty carbon blacks. As a result, formulators can create more sustainable coatings with comparable application properties to regular specialty carbon blacks,” has stated Jennifer Stroh, the director of sales and marketing of Orion.
The company also presented several other sustainable products. The
PRINTEX kappa 50 powder meets or exceeds performance requirements for conductivity, dispersibility and cleanliness at lower concentrations than conventional conductive carbon blacks, achieving the percolation threshold with low carbon black loading and good coloristic properties. Furthermore, COLOUR BLACK FW 200, COLOUR BLACK FW 2, SPECIAL BLACK 4 and SPECIAL BLACK 6 feature excellent degrees of dispersion plus high purity. Their UV absorption mitigates weathering and their low pH makes the grades ideal for UV coatings systems.
“The gas black process produces a deep black with properties that are ideal for coatings and printing systems. The high structure and high purity of gas blacks lead to exceptional dispersibility compared to other carbon blacks of the same particle size,” has stated Carlos Hernandez, the Orion marketing manager for coatings and printing systems in the Americas region. “In addition, the narrow particle size distribution of the gas blacks speeds pigment development and thus coatings production, while improving colour performances.”
For further information: https://orioncarbons.com
Mankiewicz was the only supplier to be honoured with the special award for operational excellence.
The international manufacturer of paints and coatings Mankiewicz has received two supplier awards by Airbus during the Supply Chain & Quality Improvement Programme - Supplier Day 2024.
The company, which has been named as an accredited supplier once again, is also the only one to be awarded with the special prize for operational excellence. The award is presented annually to companies that have distinguished themselves through exceptional performances in the areas of product quality and delivery reliability. The operational excellence is described as the ability to continuously optimise processes and systems across the entire value chain by following a clear strategy, implementing best practice processes, and achieving the highest performance in a well-structured organisation.
“We are so delighted that we have been awarded with the highest honour as an accredited supplier again, plus the extra award for our operational excellence. The recognition is a testament to our
commitment to customer service and quality and we are excited to continue our partnership with Airbus. We are delighted that it values the efforts and commitment to excellence and outstanding customer service and would like to extend this award to all colleagues in all disciplines around the world,” has stated René Lang, the executive managing director of the Aviation division at Mankiewicz. “This award therefore represents the special recognition for the continuous development of our processes in all areas of our global setup since we received our first award already back in 2013.”
For further information: www.mankiewicz.com/en/
The ninth edition of PaintExpo, the world’s main trade fair for industrial coating technologies, attracted over 10,400 visitors from 76 countries and hosted more than 430 exhibitors, confirming its leading position in the industry. Held at the Karlsruhe Trade Fair Centre (Germany) from 9 to 12 April 2024, it fully met the expectations of all industry players, providing them with a wide range of innovations and business opportunities.
For four days, from 9 to 12 April, the Karlsruhe Trade Fair Centre was the beating heart of the global surface treatment and coating industry, providing industry professionals with a comprehensive overview of technologies and services along the entire supply chain, from pre-treatment to plant engineering, from paint application to final quality control and packaging.
With the participation of 431 exhibitors from 25 countries over 31,500 square metres of exhibition space, PaintExpo was a true oasis of innovation: sustainability, energy efficiency, and process digitalisation were the protagonists, with numerous globally premiered, cutting-edge solutions. It attracted an international audience of 10,400 visitors – a steadily growing figure reflecting the global
interest in the latest industry trends and making this edition the most international ever.
This ninth edition was therefore a huge success, enabling countless high-level professional conversations and the creation of new contacts and concrete networking opportunities, with the exhibitors’ and visitors’ high degree of engagement and satisfaction further consolidating the event’s position as a leader in the industry. “We are extremely satisfied with the excellent turnout of visitors, which was even better than the previous edition. PaintExpo was a powerful and innovative event, and this edition was more international than ever. For four days, it was the nerve centre of the whole industrial coating technology sector, confirming itself as the most important driving force in the industry worldwide,” stated Markus Geisenberger, the CEO of Leipziger Messe, the trade fair organiser.
The whole industrial coating world in one place
A dynamic, engaging, and optimistic atmosphere permeated the air in the three exhibition halls of PaintExpo, fostering the creation of interesting business opportunities. As mentioned, this year’s event was more international than ever, with more than a third of the visitors coming from abroad. International exhibitors accounted for 45% of
the total, confirming PaintExpo’s position as a global benchmark in the industry.
WAGNER International CEO Michael Müller expressed great satisfaction with the professionals who attended the event:
“Our stand was crowded from the moment the doors opened. Half of the visitors we welcomed came from abroad: from Argentina to Japan, they hailed from all over the world. As a company that operates globally, we consider this trade fair’s internationality an extremely important value.”
“This was the second PaintExpo edition in which Helios Italquartz participated, so we are still uncovering this event’s full potential. However, PaintExpo 2024 far exceeded our expectations: as the industrial curing sector cuts across all the markets where we are present, this trade fair provided us with many different and varied connections, and the meetings at our stand were highly technical and very promising,” said Veronica Bassani, Marketing Specialist at Helios Italquartz.
“Mirodur participated in PaintExpo for the first time as both a visitor and exhibitor. Although it was a leap of faith, we were very satisfied with this trade fair overall. The size of the exhibition centre, which was not excessively chaotic, and the attendance of not numerous but high-quality visitors were the event’s main strengths. Despite this being a niche trade fair, the exhibitors also belonged to quite diverse sectors. The support of ipcm®’ team was of great help, who sympathetically and professionally acted as an intermediary for Italian exhibitors,” indicates Riccardo Vitelli, Sales Representative at Mirodur.
“Our first participation in PaintExpo was undoubtedly a positive experience, which enabled us to establish business relationships with companies worldwide. Industrial coating is one of the main fields of application of our vacuum evaporation technologies, and visitors to the trade fair saw our solutions as an answer to one of the challenges they face daily: the treatment of waste water and its total recovery,” noted Francesca Colombo,
Marketing & Sales Assistant at Eco-Techno.
“For us, PaintExpo is not just a trade fair but a meeting point for all companies that collaborate and work with us. Often, during the year, we are so immersed in our own activities that we forget the pleasure of getting together. PaintExpo is also about that! Moreover, it is nice to see the number of Italian exhibitors and visitors grow year after year, with the conviviality that is our hallmark in the world. We also enjoyed receiving visits from our competitors as if they were old friends,” said Stefano Gerletti from Futura Convogliatori Aerei.
“Participating in PaintExpo is crucial for consolidating existing partnerships and starting new collaborations. Chemtec has been participating in PaintExpo since 2012, and the 2024 edition also gave us the opportunity to identify new opportunities for development and growth. We are happy to announce that we already intend to participate in the next edition of PaintExpo as well,” stated Beatrice
Turri from Chemtec’s Sales & Marketing department.
“Once again, PaintExpo confirmed itself as the European trade fair that brings together the most companies in our industry with its wide range of solutions. For Global Mask, it was a pleasure to be part of this event and have the opportunity to share with other professionals the innovations and solutions to which each of us is contributing in terms of knowledge and experience,” noted Marta Farré, the CEO of Global Mask International SL.
were also greatly pleased Such a high degree of satisfaction was found not only among PaintExpo’s exhibitors but also among visitors, including many key decisionmakers in the industry. In the follow-up survey, nine out of ten said they were willing to recommend PaintExpo and to attend the next edition of the trade fair. The level of participation of decision-makers, professionals,
and senior executives was extraordinarily high, with 83% of visitors influencing investment decisions in their companies.
“PaintExpo offers excellent opportunities to generate new contacts and initiate business. Networking is crucial here. Nordson’s participation has always been a very positive experience, and we were thrilled to be back at PaintExpo,” said Sergey Guskov, Sales and Service Manager, Central and North Europe Industrial Coating Systems, at Nordson Deutschland.
“We are delighted to share that ALIT Technologies participated in PaintExpo 2024 with great success. During the event, we had the opportunity to connect with numerous industry stakeholders, exchanging views and ideas on the present and future of industrial coating. Our presence at the trade fair attracted great interest, especially concerning in-line frame paint stripping. Visitors were enthusiastic about our innovative solutions and sustainable, energy-efficient paint stripping processes. It was a special moment to strengthen ties with our long-standing customers and beloved distributors, creating a beautiful atmosphere at our stand. In short, PaintExpo 2024 was an unforgettable experience, and we are grateful for the opportunity to be part of this vibrant global network,” said ALIT Technologies’ Marketing Manager, Andrea Gobbi.
Although the market is facing a difficult, challenging time, the four days of PaintExpo were a beacon of optimism and new business opportunities.
“Last year posed considerable challenges for our industry, and we had to postpone or abandon many projects. However, since mid-Q1 2024, we have been seeing signs of recovery and increased investment in sustainable technologies and innovative automation solutions. I perceived the same positive trend at PaintExpo, with many visitors
and existing customers exploring the latest developments in these areas. I am convinced that a multitude of fascinating, cutting-edge projects will emerge from these encounters, and I feel optimistic about the rest of the year. We look forward to the next PaintExpo and are already committed to participating again,” explained Thomas Rippert, Managing Director at RIPPERT.
Oliver Zanner, the Marketing Manager of FreiLacke, also praised this year’s event: “Even before the start of PaintExpo, the enormous interest among visitors was palpable. The trade fair was intense, unlike the last edition. We exchanged ideas with many visitors, and the quality of the conversations was excellent. As paint specialists and manufacturers, we can meet our target customers from a wide range of industries here at PaintExpo, which is the most important event on our agenda.”
A place to network, share ideas, and toast together eos Mktg&Communication, the publisher of the ipcm® magazines, also participated enthusiastically in PaintExpo as the event’s official agency for Italy, Spain, Portugal, Argentina, and Brazil ipcm®’s stand was designed as a space for networking, sharing ideas, and toasting together. Visitors were immediately immersed in a cosy and dynamic bar-like atmosphere, complete with a cocktail and aperitif service and a football table. The idea behind this stand’s concept was to create an experience beyond the mere promotion of the company’s products and services. “We wanted to offer an informal space for sharing and exchanging ideas, where exhibitors and visitors could interact freely. The result of this innovative concept was a welcoming environment where industry professionals could meet, discuss new technologies and trends, and establish contacts for future collaborations,” noted Alessia Venturi, the Editor-in-Chief of the ipcm® magazines.
At the same time, the bar setting was also
specially created to celebrate and toast an important milestone: the fifteenth anniversary of eos Mktg&Communication and the ipcm® magazines. “We also paid tribute to the companies that have believed in this project from the beginning. We hung the magazine covers we published in these first fifteen years on our stand’s ceiling, creating a visual installation that celebrated our long history of collaboration and mutual trust with many firms in the industry. Each cover represented a significant moment in ipcm®’s journey and conveyed our desire to express gratitude and recognition to those who have played a key role in our growth path.”
After the great success of this edition, the trade fair’s organiser is already working to make PaintExpo 2026, to be held from 14 to 17 April 2026 in Karlsruhe, an even more memorable event. The survey compiled by the exhibitors at the end of the trade fair revealed high satisfaction: 94% said they also intend to attend the next edition. Such positive feedback is also reflected by the fact that only a month after the end of the 2024 edition, numerous companies have already confirmed their participation, booking an exhibition space for the 2026 edition and demonstrating strong interest and confidence in this event.
Aware of the incredible value of this trade fair, which manages to bring together thousands of professionals in the sector, eos Mktg&Communication is also already at work to contribute to the success of the tenth edition of PaintExpo, once again as the exclusive agency for Italy, Spain, Portugal, Argentina, and Brazil.
Design and manufacturing of plants and chemicals for industrial wastewater treatment
Chemical-physical plants
Sludge treatment and compactor systems
Ion exchange demineralization systems and reverse osmosis systems
Oil separators
Filtering systems
Batch type systems
Flotation units
Chemicals and spare parts for water treatment
Technical service, support and maintenance of wastewater treatment plants
The experts from DÖRKEN are looking forward to numerous exciting discussions and talks on various topics at SurfaceTechnology Germany 2024.
Like many industries, the surface technology sector is facing constantly growing challenges. Increasing demands on environmental protection, geopolitical tensions and the development of new materials and technologies are just a few examples of the issues that companies are dealing with these days.
These are the conditions under which the industry will be meeting at SurfaceTechnology Germany, held from 4th to 6th June 2024 at the Messe Stuttgart. Understanding these challenges as an opportunity and engaging in close dialogue with partners, customers and other players in the market – that it what the trade fair is all about. Trade visitors will gain insights into current trends and developments and can speak directly with experts on various topics.
PFAS in focus
DÖRKEN will also be in attendance again this year. The supplier of microlayer corrosion protection systems from Germany will be represented with a booth at SurfaceTechnology Germany. In hall 1 at booth C26, employees of the company with more than 130 years in the field of coatings will be available to answer any questions.
In addition to the zinc flake solutions, which reliably protect a wide variety of components against corrosion, the topic of chemical restrictions also plays a major role. The company has been working on PFAS-free products even before the European Chemicals Agency (ECHA) proposed a ban on the production, use and marketing (including import) of perfluorinated and polyfluorinated alkyl substances (PFAS).
DÖRKEN has various products in its portfolio, such as the DELTAPROTEKT® TC 502 GZ topcoat, taht has a very narrow friction coefficient window on metric components like screws or nuts. With this solution, DÖRKEN has also the opportunity to win the Stuttgart surface technology prize “DIE OBERFLÄCHE” 2024, which will be awarded during the trade fair. The prize honours the most innovative applications and technologies within all disciplines of surface technology.
DELTA-PROTEKT® TC 502 GZ has made it onto one of the five winners’ podiums, the exact ranking will only be announced at the award ceremony.
For further information: www.doerken.com
Evonik expanded its curing agent portfolio with the UV-resistant Ancamine® 2880 for topcoat flooring applications.
The international specialty chemicals manufacturer Evonik has recently presented Ancamine® 2880, a new fast-curing and UVresistant epoxy curing agent for topcoat flooring applications that offers excellent mechanical properties, abrasion resistance and colour stability throughout its service life.
The new modified cycloaliphatic epoxy curing agent from Evonik addresses current performance gaps of existing products, as it offers good balance of fast cure speed with strong carbamation, water-spotting and abrasion and chemical resistance, even under adverse conditions. It can also be cured at ambient and low temperature, while its rapid hardness development enables early walk-on floors. In addition, Ancamine 2880 offers excellent aesthetics and possesses and enhanced EH&S profile, so it is then suitable for applications requiring excellent surface appearance – thanks to its low colour and
high gloss – underscoring the commitment of the company in meeting the evolving needs of the global coatings industry by providing innovative solutions that satisfy the highest performances and environmental standards at the same time.
“Our customers need solutions that provide performance advantages and meet the latest labelling requirements, so we are excited to introduce our new high-performance curing agent in the Ancamine series to the market. Ancamine 2880 addresses the performance gaps found with existing available curing agents and its excellent EH&S profile make it a game-changer for the coatings market,” has declared Christian Schmidt, the head of the Crosslinkers business line at Evonik.
For further information: https://crosslinkers.evonik.com/en/products/ ancamine/ancamine-2880
The recent acquisition of the specialty chemicals distributor Lawrence Industries will allow Brenntag to further strengthen its position in the British and Irish coatings market.
The international chemicals and ingredients distributor Brenntag has announced the acquisition of Lawrence Industries, a British specialties distributor, in order to enhance its coatings, adhesives, sealants and elastomers sustainable product portfolio.
“The acquisition of Lawrence Industries will further strengthen our specialty offering in the UK and Ireland and is perfectly in line with our strategy in Material Science. Lawrence Industries has developed an industry leading reputation. I am deeply impressed with Lawrence Industries and its highly capable and outstanding team, their long-established regional presence, strong specialty portfolio and experienced technical set-up. I look forward to further expanding our technical and value-added services to our top tier suppliers and
valued customers with a particular focus on innovative and sustainable solutions, leveraging each other’s capabilities,” has commented Lars Schneider, Global President Brenntag Specialties Material Science.
“We are excited to join the Brenntag family. Gaining the international reach is an important next step for us as a leading distributor of specialty chemicals in the UK. Moreover, acquiring access to Brenntag’s extensive Innovation & Application Centre network enable our current and future customers to benefit from best-in-class value added services,” has added Charles Henn-Allen, Managing Director of Lawrence Industries.
For further information: www.brenntag.com
Starting from 4th March 2024, Cornelia Tietz is in charge of the European Printing Ink Association (EuPIA) to keep consolidating its global position.
The European Printing Ink Association (EuPIA) appointed Cornelia Tietz as its new Director, succeeding to Martin Kanert.
“It is a great honour and for sure a challenge to take over from Martin Kanert who has been the driving force of EuPIA for so many years. I am truly looking forward to embark on this new and exciting journey together with the EuPIA members and the CEPE team,” declared Cornelia Tietz, the newly-elected Director of EuPIA.
Cornelia Tietz holds two master’s degrees in humanities and has almost 20 years of experience in the industry, where she served as the Secretary General of the European Solvents Industry GroupESIG and its sector association. “I am proud to have helped EuPIA develop into what it is today. It goes without saying that this has only been possible with the substantial support and dedication of the many people engaged in EuPIA’s committees, working groups and task forces. And I am happy that with Cornelia, the EuPIA Council has found such an experienced and knowledgeable successor,” has added Martin Kanert, former Director of EuPIA.
“In the current revision of so many EU regulations relevant to our industry, a dynamic and well structures trade association is of benefit to its members, and we will continue to contribute under the lead of the Director to give an answer to societal questions. I would personally like to thank Martin for two decades of leadership and at the same time extend a warm welcome to Cornelia who will help and support us through a transition into a sustainable future,” has concluded Mehran Yazdani, EuPIA’s Chairman.
For further information: www.eupia.org
The new modern and sustainable complex will ensure even greater customer proximity and exclusive seminar offerings.
The international manufacturer and provider of specialty chemicals BYK has recently presented the plan for a new cutting-edge innovation laboratory and seminar complex in Wesel (Germany).
The company estimates a total implementation period of four years, with completion envisaged in the second quarter of 2028.
The €25 million project testifies the commitment to Germany as an innovation location and will ensure even greater customer proximity and exclusive seminar offerings thanks to integrated function rooms. The aim of the investment is to generate new innovations together with and for customers in end-use facilities.
“It will be of especial benefit to our customers who seek to develop their project solutions here on site with BYK experts. It was therefore logical to plan a further story where we will soon be able to host customer events, visits and seminars. At around 25 million euros construction costs, a particular intention of the innovation complex is to provide modern state-of-the-art laboratories for BYK end uses while at the same time allowing more breathing space for existing end use, applications labs and R&D facilities,” has stated Stefan Mößmer, the Marketing & Commercial Managing Director of BYK.
The complex will be created on the existing site of the company and will cover a total area of 5,100 m2. The heating and cooling systems will be fed with 100% renewable energy generated through heat pumps and photovoltaic panels. In addition, several other sustainable materials will be deployed throughout the entire project.
“BYK is networked with its customers worldwide; with this innovative laboratory complex, it will be creating space for effective communication as well as for developments and cooperation with our customers and distributors. At the same time, the new building will offer us more opportunities for our exclusive on-site seminars that are so much in demand,” has also added Jörg Hinnerwisch, the president of BYK Additives. “With regard to sustainability, safeguarding the future, and ecology, we wish to equip the building – and further adjacent laboratory buildings – with heat recovery, as well as meeting the full energy needs of this new innovations construction with 100 percent renewable energies.”
For further information: www.byk.com/en
ASK Chemicals showcased its new sustainable and VOC-free binders for paints and coatings at the 2024 American Coatings Show, which took place from 30th April to 2nd May.
ASK Chemicals has showcased its VOC-free, sustainable binders for industrial paints and coatings at American Coatings Show 2024. ASK Chemicals highlighted new binders for industrial coatings, complemented by offerings for the formulation of decorative coatings. In particular, the company presented NECOWEL alkyd resins, two-component paints and its REZIANCE range of industrial phenolic resins, developed for different industrial applications.
ASK Chemicals Group, headquartered in Hilden near Düsseldorf (Germany), is a global supplier of high-performance industrial resins and materials. The company’s products are mainly used in foundries and in the production of friction, abrasives, refractories, impregnation, coatings, insulation and composite materials.
The Foundry division offers an exceptionally wide and innovative range of foundry consumables including binders, coatings, risers, filters, release agents as well as metallurgical products such as inoculants, inoculation wires and master alloys for iron casting.
The Industrial Resins division is a leader in the field of specialty phenolic resins. Our phenolic resins are the preferred choice when it comes to meeting the highest requirements in the areas of fire protection, energy consumption, service lifetime, health, and safety at work.
The company has a production and sales network in 22 countries and employs approximately 1800 people worldwide. ASK Chemicals Group sees itself as a driving force of industry-specific innovations with research centres and laboratories in Europe, Asia, Americas and Africa.
For further information: www.ask-chemicals.com
Hi Joe,
I’m selling powder coating in South America. So now I have many questions regarding powder coatings. But the most important is this: how long after the expiration date can a powder coating still be used?
Thanks Claudia Helsum Medellin, ColombiaHello Claudia,
Thanks for the question. I have travelled and worked in Colombia and have very fond memories of my time spent there. I will be very happy to answer your question.
The stability of a powder coating is influenced by many factors. First, I must differentiate two distinct types of stability. Physical stability involves the requirement for the individual particles to resist clumping or fusing together. Chemical stability refers to a powder coating’s resistance to premature polymerization during storage and handling. Physical stability is influenced by the melt point or more specifically the Tg (glass transition temperature) of the powder coating and the storage conditions. A powder coating with a low melt point will sinter and clump more readily than one with a higher melt point. Accordingly powders stored in high temperature environments will clump more readily than those stored in cooler areas. Additionally powders exposed to high humidity environments tend to absorb moisture which will also cause clumping (please note that most powders are supplied in moisture impervious containers and the exposure to moisture occurs after the package has been opened). Clumping obviously makes a powder difficult to fluidize, transport, and spray in an application system. On the other hand, chemical instability causes a powder coating to chemically advance or polymerize during storage. Fast-reacting and low-temperature curing powders can start polymerizing in hightemperature storage or transport conditions. This premature chemical advancement reduces the melt flow of a powder coating causing a more textured finish. Both physical and chemical instability can be present in a powder coating. Typically fast-cure (or low-temperature cure) powders also have low melt points to help facilitate better melt flow at low cure temperatures. Consequently these types of powders are most susceptible to clumping and chemical advancement and should be stored and applied in a climate-controlled environment. I recommend less than 27 °C and 50 to 70% relative humidity.
Now to answer your question. Standard curing powder coatings (175 -200 °C) that have been stored in a reasonable environment can remain usable long after their “due date”. Lowcure powders and those that have been stored in environments exceeding 27 °C for long periods can suffer from clumping and chemical advancement. I would inspect (for clumps, etc.) then spray and bake a sample of any powder that is past its due date and make the determination yourself. If the finish is still within your requirement for smoothness and appearance (no blistering, dirt, etc) then I would continue to use it.
Claudia, I hope that this helps you. Someday I hope to return to Colombia to enjoy the beautiful weather, excellent food, and wonderful people.
Peace, Joe
Afternoon Joe,
I have a question about powder coating. What is the best powder coating primer to use as a base coat on fencing outdoor iron rails? We then apply gloss black as a topcoat. We use zinc-rich primer as our base, but the topcoat and base are starting to peel off.
Thank you,
Joel Menchaca Houston, USA
Morning Joel,
This sounds like a serious problem. Using a zinc primer should be okay as your base coat (aka primer) as long as it’s processed properly. It’s important to ensure the iron rails are properly prepared before applying the primer. By proper preparation, I am referring to first removing all “oils and soils”, then preparing the metal for the best adhesion of the primer. The O&S can be removed by solvent wiping (acetone works well) or by applying an alkaline
cleaner followed by a clean water rinse. Pretreating the metal is the next step and can be accomplished by media blasting (remember to use only clean media) or a chemical pretreatment such as iron phosphate or zirconium/silane solution. Clean rinsing with deionized water or water processed through reverse osmosis is recommended to ensure the best surface for the primer to adhere to. The metal must be thoroughly dried, preferably in a forced air oven.
After applying the primer it is wise to partially cure or “gel” the powder. Best topcoat adhesion is achieved over a partially cured primer. So, reduce the recommended primer bake time by 50% and proceed to topcoating. Bake the top-coated rails per the recommended powder bake as disclosed on the Product Data Sheet provided by your powder supplier.
If you’re still having adhesion issues after following these recommendations, then I would switch to a non-zinc primer. They work as well as most zinc-rich types and are much easier to spray. In addition, you get significantly more coverage per pound of powder because the specific gravity of a nonzinc primer is considerably lower than that of the zinc-rich material. We’ve seen excellent corrosion resistance of the newer non-zinc primers in our laboratory. Remember that clean, well pretreated metal is essential as is a partial cure of the primer for optimal intercoat adhesion.
Best of luck.
Joe
Venturi ipcm®
At the PaintExpo 2024 trade fair, J. Wagner – a leading global supplier of systems and components for industrial surface technology - presented some important innovations for both powder coating and liquid painting. We took the occasion up to visit the booth and to talk with Markus Sonnenstatter, CSO Industrial Solutions, and Jens Arnoscht, CTO Industrial Solutions, at J. Wagner GmbH about sustainability, Industry 5.0, smart and accessible solutions for paints and coatings application in the General Industrial.
ipcm®: Can you please briefly present the main exhibits of J. Wagner at PaintExpo 2024?
MS: At PaintExpo 2024, our main purpose was to show innovative products for both liquid paints and powder coatings application, and we had a lot of them: the new generation of our manual powder coating
unit, Sprint 2; the Flowsense system, a ground-breaking technology that measures and fully automatically controls the powder output; a new bell with internal charge for solvent-based paints, the TOPFINISH RobotBell 1/Bell 1S; a new automatic flushing system which allows to recover a lot of unused paint in the hoses and to reduce the consumption of flushing
solvent. At our booth in Hall 3 we showed all these technologies live, accompanying our customers along the path of innovations. The claim of the booth was “Wagner better for you”: we wanted our customers to tell us why they work with Wagner, so why Wagner is better for them.
JA: At PE 2024 Wagner addressed the key trends of sustainability, digitisation, and the scarcity of human resources. This last aspect is the focus of our most recent developments. Our new powder coating technologies are especially addressed to ramping up quickly the expertise of new employees of the coating technology. From the automatic application side, we want to “democratise” robotics so that everybody is able to install and use a robotic solution in a coating line very easily, without the need of programmers. Finally, we want to make powder coating application easier for the customer. This means that Wagner’s technologies must be able to provide process stability without manual intervention and regardless of spare part wear: the powder coating system must be working stable regardless of any issues you may have, like
powder blockage for example, because the system itself alerts the operators with a simple traffic light signal, so that they can take care of the problem very quickly, without creating unnecessary waste.
ipcm®: The focus of the surface technology market is currently on powder coating: what are Wagner’s new offerings in this field? Both for manual and automatic application
MS: At PaintExpo we showed two new technologies for powder coating: the Sprint 2 manual unit and the Flowsense automatic control of the powder quantity.
The new generation of the Wagner manual unit has been modernised in terms of design and functionality. With the Smart 2 manual unit we can allow operators with less experience to apply powders in a very fast and easy way. The WACON Sprint 2 XE (successor to the EPG SPRINT XE control unit) has the new DSO (Digital Surface Optimizer) assistance function, which reduces overcharge effects such as orange peel, edge build-up and similar. This advantage is particularly relevant for decorative coatings on complex
workpiece geometries or with challenging powder coatings. The DSO function supports the coater in achieving an even more homogeneous surface finish. The intuitive controls and even clearer arrangement of the operating elements make day-to-day work easier: the coater has all the important parameters at a glance and can make all adjustments, including recipe selection, quickly and easily using a central rotary knob. WAGNER’s Air Flow Control (AFC) technology constantly measures and regulates the air volume during the coating process, creating a uniform powder cloud for high-quality coating results.
JA: The second big innovation we brought to the trade fair was Flowsense, a groundbreaking technology that measures and fully automatically controls the powder output. This delivers consistently high-quality results and reduced powder consumption thanks to constant layer thicknesses.
As part of the Flowsense technology, each individual feeding element is equipped with high-precision measuring sensors. The smart system constantly monitors the powder flow and compares the powder quantity with the target values. Flowsense can even measure the powder output in g/min and individually for each gun. The exact dosing of the powder quantity can be saved in the recipe and is permanently reproducible, without any manual corrections, which would be necessary without Flowsense. With Flowsense, however, the output parameters are adjusted independently and deviations are corrected automatically. The system even compensates for influences on the output, e.g. caused by fluidisation and fluctuating powder levels. The sawtooth effect is smoothed out by the control to a micro-sawtooth that can no longer be measured. The powder output can be adjusted much better to the target layer thickness, which in turn minimizes the safety margin. This results in significant powder
savings. Constant coating thicknesses within certain limits are also an important criterion for certification by quality associations for industrial coating. Another advantage is predictive maintenance: as Flowsense permanently monitors the powder flow, blockages, for example, are detected in time and rejects are avoided. In combination with the injector technology, Flowsense also provides information on the current status of the collector nozzles. This is clearly visualised on the touchscreen of the powder center in a traffic light system. This allows the operator to see the exact system status at all times and provides
continuous information on whether the coating is achieving the desired quality. This allows the user to replace the collector nozzles in a very short time and exactly when it is needed. Flowsense is a real quantum leap in powder application!
ipcm®: What were the highlights on the liquid part?
JA: One of the highlights was definitely the new bell WAGNER TOPFINISH RobotBell 1/Bell 1S. It’s an internal charge bell for solvent-based applications, which comes along with a control unit that is, again, easy to use for the applicator: the touchscreen shows different operator modes, from a beginner level for operators who may not have an expert knowledge of the paint application, to an expert level for a painting line manager who can adjust more values in the controller. This is the ideal solution package for integrators that are maybe not too experienced with bells and do not have their own SPS programmers. You can buy the control unit or just the bell: with this approach we see bells being used for non-automotive applications up to job coating.
MS: The second highlight for liquid paint application is our active flushing system for high pressure applications, where we provide an additional accessory that makes it possible to flush the pump after the entry of the gun so that the flushing can be done either with solvent or with solvent and air mixed. In this way you can flush the system more quickly, more efficiently, with less solvent and less paint loss, since the active flushing system also recovers all the unused paint in the hose prior to flushing.
Flowsense is a ground-breaking technology that measures and fully automatically controls the powder output.
ipcm®: The IPS powder centre, presented to the market at PaintExpo 2018, has been a great success in Europe. After 6 years, is there any further development planned for this ground-breaking technology?
MS: Well, the IPS is the best powder centre available on the market, because it is the only one with a really automatic colour change without manual intervention, while the SFT feeding concept (“Smart Feeding Technology”) delivers powder stability over time and a great transfer efficiency with powder saving. These are its main advantages, making it so successful in the market. Even though it is the best technology available, we will not stop its development, since we want to remain a technology leader in the future. However, I cannot share more details about this!
ipcm®: After the fourth industrial revolution of the last decade, now we are already going towards Industry 5.0. How does Wagner approach this new paradigm?
JA: As we said at the beginning of this interview, we have recognised two megatrends in the industry: the scarcity of skilled workforce and sustainability. The Industry 5.0 concept reflects a focus on social value and well-being. It is a new phase of industrialisation in which humans work together with advanced technology and AI-driven robots to improve processes and to improve sustainability. What we showed at PaintExpo 2024 is going in this direction.
Patrizia Lancini had been working for the Italtecno group ever since she finished her foreign language studies. In just a few years, she became an expert in technical matters as well, particularly regarding anodizing equipment. She rose to become the group’s sales manager, keeping contacts with agents, distributors, and final customers in more than 30 countries worldwide.
Every year, she actively participated in exhibitions, congresses, and seminars about aluminium surface treatments. Indeed, her last activity was the presentation of her paper titled “Special Effects in Anodizing: The New Trend in Europe” at the Aluminium Two Thousand Congress between September 19th and 21st, just a few days before her fatal accident in October. She spent more than two months in the hospital before her premature departure on December 17th at the age of 56. She leaves behind immense sadness for all those who loved her deeply.
The team at Italtecno and all her friends bid her this final goodbye:
“Some people come into our lives and quickly go. Some stay for a while, leaving footprints on our hearts, and we are never, ever the same.”
Flavia WeednDear Patrizia, your bright light has illuminated darkness and calmed rough seas. Your love and joyful heart have brought happiness to so many. I will miss your laugh, your smile, and your easy, loving nature. As your soul moves on to your next great adventure, I feel lucky to have known you, spent time with you, and created so many beautiful memories together. You leave behind an empty space as vast as the oceans your loved ones sail, and your pure love and light leave a legacy that will serve as a buoy in the rough seas they must now navigate without you. I know the love you have given will be like sand beneath their feet, cushioning their journey. The expectation of a shared future gone too soon.
Love never dies. It is within us. With us. Around us.
So, sail on, my friend, knowing you have left footprints on our hearts, and we will never be the same.
“Goodbyes are only for those who love with their eyes. Because for those who love with heart and soul, there is no such thing as separation.” Rumi
Philipp Jarke
Technische Universität Graz – Graz, Austria philipp.jarke@tugraz.at
The material delays the formation of ice crystals and reduces the adhesion of ice layers. Thanks to an innovative production method, the coating is very robust and adheres to numerous surfaces.
Ice-repellent coatings have been around for some time, but until now they have been very sensitive and detach quite quickly from the surfaces they are meant to protect.
A research team led by Anna Maria Coclite and Gabriel Hernández Rodríguez from the Institute of Solid State Physics at Graz University of Technology (TU Graz) has now succeeded in remedying this shortcoming. They have developed a highly ice-repellent coating that adheres to a wide variety of materials and is very resistant to abrasion. The complete paper was published in the journal ACS Applied Materials & Interfaces1
1 https://pubs.acs.org/doi/10.1021/acsami.3c18630
The researchers achieved this progress by using a manufacturing technology called initiated chemical vapour deposition (iCVD). This makes it possible for a strongly adhesive primer material to gradually transition into the ice-repellent compound. This stepless transition is achieved by applying the two materials as a changing gas mixture to the surface to be coated. Initially, the gas mixture consists purely of the primer material, but the proportion of the ice-repellent material is continuously increased during application, from 0 to 100 per cent. The result is a coating with a strongly adhesive underside and a top side that prevents ice crystals from sticking.
Random alignment of the molecules creates an ice-repellent effect
During their experiments, Anna Maria Coclite and Gabriel Hernández Rodríguez discovered what the ice-repellent property of their coating is based on.
“The ice-repellent material consists of elongated molecules that adhere to the primer in a vertical or horizontal orientation,” explains Gabriel Hernández Rodríguez. “The thicker we applied the material, the more random the alternation between vertical and horizontal molecules became. And the more random
the arrangement at the surface, the greater the ice-repellent effect.” This mechanism was previously unknown.
A wide range of applications are conceivable for this new type of coating, for example in the aviation industry: “Such a coating could speed up the de-icing of aircraft and use less antifreeze,” says Anna Maria Coclite.
Sensors exposed to the weather that are disturbed by ice could also benefit from such coating.
In world-wide competition with comparable institutions, Graz University of Technology pursues top teaching and research in the fields of the engineering sciences and the technical-natural sciences. An integral part of putting together excellent education and training programs is knowing about the needs of society and the economy. Ultimately, the quality of the education and training at Graz University of Technology is carried by the strength of its knowledge-oriented and applied research. Numerous competence centres, the Christian-Doppler laboratories, special research fields, research focuses, and large EU projects are
only a few examples of the University’s extremely active and successful research.
Solid state physics is the study of how atoms arrange themselves into solids and what properties these solids have. By examining the arrangement of the atoms and considering how electrons move among the atoms, it is possible to understand many macroscopic properties of materials such as their elasticity, electrical conductivity, or optical properties. The Institute of Solid State Physics focuses on organic, molecular, and nanostructured materials. Often detailed studies of the behaviour of these materials at surfaces are made. Its research provides the foundation for important advances in technology such as energy efficient lighting, solar cells, electronic books, environmental sensors, and medical sensors.
In order to efficiently manage the transition from solvent-based to water-based DTM technology and meet its sustainability targets, Next Hydraulics chose Verind, a company of the Dürr Group, as its partner for the supply of integrated water-based 2K coating application and management technology based on a “green concept” characterised by high transfer efficiency, reduced overspray, and halved raw material consumption.
The acronym DTM indicates two-component paint products that act as both primers and top coats and can be applied directly to suitably prepared metal surfaces, with excellent adhesion and corrosion resistance properties even in the absence of a base coat. Direct-to-Metal products have revolutionised the industrial coating sector by becoming popular in various application contexts, from agricultural and earth-moving machinery to heavy metalwork fabrication, thanks to their ability to streamline processes, reduce costs, and ensure long-lasting aesthetics and performance.
In some cases, by virtue of these chemical and operational characteristics, they are even chosen for components or semi-finished products already coated with a primer applied by the production and machining workshop or with a foundry primer. That is because the possibility of concentrating the coating process into one step and
achieving even higher corrosion protection properties while reducing emissions and raw material consumption is significantly convenient for many companies.
This is the case for Next Hydraulics, a company based in Boretto (Reggio Emilia, Italy) specialising in hydraulic cranes, which has chosen a DTM coating to finish around 60% of its components. And that is not all: with a view to improving sustainability and lowering the environmental impact of its processes to obtain ISO 14001 certification – which it did at the beginning of 2024 – the company based in the Emilia-Romagna region has decided to switch to a water-based paint product. As this entailed upgrading several plant engineering aspects related to paint management, supply, and application, it selected Verind (Rodano, Milan, Italy), a Dürr Group company specialising in automotive and industrial coating, surface protection, ultrafiltration, and water treatment, as well
Opening photo: Next Hydraulics (Boretto, Reggio Emilia, Italy) specialises in the production of hydraulic cranes and truck stabilisers sold worldwide.
Hydraulics’ liquid coating plant and truck stabilisers waiting for DTM application.
© ipcm as the main integrator of Dürr products in the industrial market, as its technological partner. Verind carried out two interventions on Next Hydraulics’ coating plant:
setting up the water-based DTM product mixing, feeding, and electrostatic application circuit with an EcoDose 2K mixing machine;
revamping the top coat booth’s feeding system to prepare it for the forthcoming transition to a water-based product by installing a second EcoDose 2K unit.
Founded in 1989, Next Hydraulics offers lifting solutions with a production divided into three product lines:
Maxilift, a range of mono-boom cranes from 0.5 to 5 tm with a modular construction concept, ideal for installation on light and ultra-light vehicles;
Cobra, a range of service cranes from 1.8 to 10.9 tm designed for installation on “mobile workshop” vehicles, perfect for working off road, in countries like Australia, North America.
Maxistab, a range of supplementary stabilisers known worldwide and adopted by the major crane manufacturers.
Stabiliser cylinders awaiting coating.
A 4-metre-long load bar entering the chemical pre-treatment tunnel. The bulk of the production is sandblasted in an off-line manual cabinet.
Production takes place in three modern buildings with a total covered area of around 10,000 m2, and around 60 people employed. Next Hydraulics’ 2023 turnover was around 35 million Euros.
Next Hydraulics has always been looking for the increase of automation of its manufacturing stages, with major investments in robotics for coating and packaging, but also in logistics and its own internal lifting and handling systems. The design, development, and engineering of the three product lines are carried out entirely in its Technical Department, then tested in its in-house Trials Department. In 2021, the company became part of the Swedish LIFCO Group, which brings together a number of European and global companies, all characterised by a high level of product quality, high sector specialisation, and an established market position. The LIFCO Group’s strong drive to strategically invest in key industrial sectors further motivated the move.
“Next Hydraulics is the only EU manufacturer of service cranes serving the North American market: all competitors are based in the US,” notes Francesco Filonzi, Production and Plant Manager at Next Hydraulics. “Lorries stabilisers account for the other half of our production: in this field, we are suppliers to all the most important truck crane manufacturers in Europe. Becoming part of the Swedish LIFCO Group has opened up new horizons for us while still ensuring the continuity of these product lines of excellence. Today, we sell to almost the entire world: our target markets are Italy, Europe including Great Britain, North and South America, Australia, the Middle East, and Mediterranean Africa.”
The production process
“At our factory in Boretto, we design cranes and stabilisers in line with market developments and customer requirements,” explains Francesco Filonzi. “We develop, design, engineer, and prototype our products in-house, whereas for the custom manufacturing and machining of individual components we rely on the Emilia Romagna Industrial Hub. When we receive these back, we take care of the coating, assembly, testing, and shipping operations. Coating, therefore, is the only actual production step that takes place within our factory because we attach great functional importance to finishing. Our specifications call for applying a finishing with at least 80 microns of paint product with a salt spray resistance of at least 500 hours and a glossy finish.”
Next Hydraulics’ automatic coating plant dates back to 2000 and at that time it was considered avant garde for its high automation with a layout, time and cicles designed to apply two-coat systems with solvent-based 2K paints. 60% of its products, particularly truck stabilisers, are coated after assembly in one colour, black, with a single-layer paint – a strategic choice to give them superior quality. The remaining production (arms, bases, rods, cylinders, and so on) is
coated in the various colours specified by the customers with a two-coat primer + top coat system. “The plant had been designed for automatic electrostatic application, through 7-axis articulated robots, of both a solventbased 2K epoxy primer + polyurethane top coat and a solvent-based DTM coating devoted to that first 60% of production. As the company evolved, however, production grew exponentially, and the use of those solvent-based products was increasingly intensifying its environmental impact, both for waste and sludge and for atmospheric emissions,” explains Giovanni Benevelli, APTIndustry technical sales expert from Verind. “With a view to obtaining environmental certification, two years ago, we switched from a solvent-based DTM product to a water-based one in cooperation with our paint supplier, Colorificio Sanmarinese,” indicates Francesco Filonzi from Next Hydraulics. “Currently, therefore, we use two coating systems: a solvent-based one, which includes a primer and a top coat and is applied on about 30% of our products, and a water-based, one-coat one. These are applied in two coating booths, one devoted to the water-based DTM system, which has been equipped with technology supplied by Verind, and the other for primer + top coat application, where Verind carried out its second intervention at the end of 2023 because it is will also soon switch to watersoluble technology for its applied two-coat system.”
Verind’s plant engineering intervention for transitioning from solvent-based to water-based products
Previously, the solvent-based DTM coating was handled in the top coat application booth, as it was a 2K product, too. With the transition from solvent-based to waterbased technology, we integrated an EcoDose
machine into the primer booth to configure it to apply the new DTM paint,” explains Giovanni Benevelli from Verind. “Naturally, since this booth was previously devoted to primer application alone, we had to make a minor modification in the technical room to create a niche to transfer the solvent-based primer application system. However, it is interesting to note that we managed to maintain the gun already in use, although now fed by two separate feeding channels, one for the solventbased 2K primer and the other for the water-based DTM coating. We developed a flexible, modular system that combines electrostatic application with an automatic 2K paint dosing and mixing equipment using Gear Flow Meter technology with optic fiber; the EcoDose 2K equipment is an advanced electronic system for stoichiometric dosing and mixing of 2K/3K solvent-based, water-based, HS, and DTM coating products.”
“The challenge was to harmonise the plant’s technology, which dates back to 2000, with these technological upgrades in its feeding and application systems,” says Francesco Filonzi from Next Hydraulics.
“However, we were able to find a high-performance solution that enabled us to transition to a water-based coating on our existing plant, without any modifications to its booths or ovens. The upgrade was also challenging in terms of layout: we had to choose where to integrate the water-based DTM technology to ensure a suitable process. The paint itself was developed in cooperation with Colorificio Sanmarinese, which provided us with a DTM coating with the adhesion and sealing characteristics required by our products. The next step will be developing a two-coat, water-based cycle as well. This will be a more complicated step, which will certainly require plant modifications.”
“Verind was already one of our suppliers and has earned respect and esteem from our management thanks to its ability to solve problems and foster mutual growth. The results we achieved are certainly positive, and we have attained them within a tight timeframe because Verind made targeted changes to our system without revolutionising it. That has allowed us to continue producing with only minor downtime.”
The coating cycle
Next Hydraulics’ coating plant accommodates 4-metre long load bars that can carry one complete assembled stabiliser or a series of smaller parts or components. Its takt time is 10 minutes. The parts arrive at the painting installation after sandblasting (most of them) or chemical pre-treatment. Others, like the stabilisers’ cylinders, reach the factory with a primer layer already applied, and they are sent directly to the water-based DTM product application. The parts that underwent chemical pre-treatment go through an oven-drying and blowing phase. The two coating booths are automatic and equipped with robots. Booth no. 1 applies both the solvent-based primer and the water-based DTM coating. This is followed by a 7-minute flash-off phase. Then, the top coat is applied in booth no. 2. Finally, the components dwell in the baking oven for 35/40 minutes. “The second intervention Verind performed on this plant was to prepare booth no. 2 for applying water-based products. Here, too, we integrated an EcoDose 2K machine. The existing mixVer system was suitably modified and upgraded to newer technology so that it could be used for primer application,” illustrates Benevelli.
The environmental sustainability targets achieved “In March 2024, we obtained ISO 14001 environmental certification,” proudly says Luca Pezziga, Painting System Manager at Next Hydraulics. “This investment in water-based DTM technology, and therefore in the systems needed for its management and application that Verind provided us with, was part of a broader sustainability-oriented approach. Our factory is equipped with solar panels (108 kW capacity) for self-producing the energy required for our processes, and we have always paid great attention to waste management, safety, and the creation of a healthy working environment.”
“Indeed, the primary objective of this investment was undoubtedly the ISO 14001 certification,” concludes Francesco Filonzi. “The new waterbased DTM coating has helped us lower our product costs because, although this paint has a higher price than the one we used to apply, transfer efficiency is greater, so the yield is higher and, by reducing overspray, it creates less waste and sludges to be disposed of, perfectly aligning with our objectives.”
The most important industry events at your fingertips
myFAIR is a free web app that can be accessed from both desktop and mobile devices, which allows you to stay up-to-date with the leading events of the surface treatment sector.
The New York City Library’s ‘Wizard Hat’ Coated with Fluropon® Patina Green by Sherwin-Williams Coil Coatings
FOCUS ON TECHNOLOGY
A New Laser Scanner System for Pintarelli Verniciature’s Programming-Free, Automatic Powder Coating Plant: a Further Boost to the Quality of Its Certified Coatings
HIGHLIGHT OF THE MONTH
From Raw Materials to Applied Colours: ST Powder Coatings at Fuorisalone 2024 to Make Powder Coatings the Stars of Design
FOCUS ON TECHNOLOGY
When Every Detail Matters: La Marzocco’s New Coating Plant
Bio-based Powder Coatings: the Next Frontier for Tackling Scope 3 Emissions?
HIGHLIGHT OF THE MONTH
TIGERator - The Ultimate Online Tool for 3D Surface Configuration
Carbon Fibre Coating: Technologies and Solutions to Preserve Performance and Elegance
HIGHLIGHT OF THE MONTH
An Industry at the Service of Design: Trends and Inspirations from Milan Design Week 2024
HOW IT'S COATED
AkzoNobel Painting a More Secure Future for Historic Dutch Windmills
OUTLOOK
A FEM Approach to Explore the Thermal Dynamics of Steel Parts During Powder Coating Process
FOCUS ON TECHNOLOGY
Towards Excellence: Pleion Revolutionises the Coating of Its Thermal Collectors with a New Plant
Europolveri recently obtained the Qualicoat Class 2 approval for its 52R SD powder product architectural series.
Europolveri, one of Italy’s historical companies specialising in the manufacturing of powder coatings and headquartered in Sandrigo (Vicenza), has achieved another significant milestone: the Qualicoat Class 2 approval for its 52R SD powder product series. These are matte wrinkled finishes, also available in metallic and bonded versions.
“This certification is part of a growth project in the architectural market, aimed at strengthening Europolveri’s already wide presence in this sector, with the goal of providing customers with the widest range of products. Offering products that ensure ever-increasing durability reflects the company’s commitment to produce ever-higher quality powder coatings. Furthermore, the objective is clear: to increase the durability performance of our products so that they are more aligned with the average lifespan of the products on which they are applied, especially in the world of architecture. A long-lasting product is an environmentally friendly product,” stated the company.
Europolveri was founded in 1982 by Giuseppe Zaniolo, who, with its forward-thinking vision, recognised the need for innovation in the world of coatings. The founder’s spirit has been passed down to successive generations, who over the years have guided the company through strategic growth paths in terms of products, innovation, and opening new markets. Today, the company employs over 100 people and is a leader in the manufacturing of powder coatings in Europe. With a strong entrepreneurial spirit, a people-oriented approach, a keen sensitivity to ecological and environmental contexts, and a predominant inclination towards research and development of innovative products and solutions, Europolveri is a historic and established brand in continuous and constant evolution.
For further information: https://europolveri.it/en/home-3-eng/
During Fuorisalone 2024, the event that takes place every year in conjunction with the Milan Design Week, Lechler, leader in the paint and surface treatments sector, presented “The Way of Ethic Colors”, a new project that proposes four collections that explore the ethical dimension of colour and create new chromatic and material landscapes for the interiors of our homes.
In recent years, we have witnessed a paradigm shift in the real estate market, thanks to greater awareness and social responsibility stemming from the fundamental value of sustainability. Thus, the focus is on the recovery of real estate heritage and urban regeneration, concepts that aim to preserve, conserve, and renew, maintaining the existing as much as possible. It is in this context that Lechler presents its new project, Color Design “The Way of Ethic Colors”, during Fuorisalone 2024.
“The Way of Ethic Colors” is born out of the awareness that colour is not just an aesthetic element but also a tool capable of influencing behaviors, promoting sustainability, and conveying ethical values. We could talk about “dematurity” applied to the habitat sector: a process that sees the preservation and renewal of living spaces through the use of innovative and sustainable colour schemes. The new collection is structured into four themes: Involvement, Equilibrium, Awareness, and Change, each of which interprets different approaches to colour design, always under the sign of sustainability. It guides people in their journey of mindset change, going from neutral and polymaterial schemes, designed to last over time, to polychromatic and high-contrast solutions, intended to be easily updated or modified.
Involvement is inspired by emotional intensity, with colours ranging from blues to cold greys combined with warm and deep reds, ideal for creating spaces characterized by temporary chromatic and emotional focus.
Equilibrium finds its essence in harmony with nature, offering a palette of complementary colours, tonal greens and pinks, with matte and pearl finishes, which are perfect for spaces in dialogue with the outdoor environment.
Awareness reflects consciousness and durability, with neutral tones and iconic materials that integrate into urban and historical contexts, maintaining a longlasting visual connection with the existing environment.
Change expresses transformability through vivid and saturated colours, designed to energize spaces and facilitate their adaptation to new needs or desires.
“The Way of Ethic Colors” is an invitation to professionals and enthusiasts to discover how color can become a powerful tool for change and innovation, in the name of ethics and social responsibility. With this project, Lechler reaffirms its commitment to a future where beauty, innovation, and sustainability meet to create environments that inspire and enhance individual and collective well-being.
For more information: www.lechler.eu
The Stavros Niarchos Foundation library’s Patina Green colour and “wizard hat” shape create new icon respecting historic design of former department store.
The Stavros Niarchos Foundation Library in New York City transforms the skyline of Midtown Manhattan by vertically expanding an historic building and creatively updating a former department store. The award-winning project is pursuing LEED Silver certification and welcomes all to the only free, publicly accessible roof terrace in the area.
Mecanoo of the Netherlands and Beyer Blinder Belle of New York designed the repurposed 1914 property for The New York Public Library (NYPL). NYPL moved into the building in 1970 and modestly renovated the interior 1978. Minimal changes to the existing space were made in more than four decades.
Expanded upward from six to seven stories, the 180,000-square-foot
(just over 16,700 square meters) modern library’s immediately recognizable iconic form showcases a new, sculptural, geometrical, aluminium roof structure resembling the angular shape of a wizard’s hat. Highlighting the magic and knowledge of libraries, this distinctive metal roof is finished with Fluropon® Patina Green by Sherwin-Williams Coil Coatings.
Bringing wisdom, drama and magic “The Stavros Niarchos Foundation Library is a powerhouse of wisdom, and its street presence brings drama and magic to Manhattan, visibly expressed with its Wizard
Hat,” described Francine Houben, creative director and founding partner of Mecanoo. In a joint statement, Houben and Beyer Blinder Belle’s managing partner Elizabeth Leber shared: “Libraries are and will always be repositories of knowledge; but that knowledge resides in its librarians as much as in its bookshelves. Working together with NYPL’s talented staff, our firms strove to meet the library’s needs with an inclusive program, humanistic planning and design, and iconic architecture.”
Houben added, “Libraries are incredibly unique spaces, houses of knowledge and creation that must inspire, welcome and
serve all. In this case, we were entrusted with a historic building in New York City, one that receives millions of visits every year, but was never built to be a library. We needed to take the bones of that building and reimagine the ultimate library.”
Respecting the century-old building’s architectural heritage, the Patina Green colour, while new, already appears to have gracefully aged with time and weather. The signature Patina Green colour was inspired by the neighbourhood’s Beaux Art style, copperclad, mansard roofs. Providing exceptional colour retention and consistency to uphold the project’s desired aesthetic, Fluropon 70% PVDF resin-based coatings will protect the metal for many years to come. This product, which is available in over 50,000 colours, is Sherwin-Williams flagship 70% PVDF coating system for architectural metal building products, which boasts superior durability and colour retention features.
Creating high-performance, visually impressive, valuable space
Achieving the project’s performance requirements, Fluropon 70% PVDF resin-based coatings meet the industry-leading AAMA 2605 specification. This specification outlines the highest performance level for exterior aluminium coatings, resulting in outstanding resistance to humidity, chalking and gloss loss. Fluropon coatings meeting this highperformance standard also successfully pass 4,000 hours of accelerated salt spray testing. This is important in New York City as both a coastal environment and a climate that uses salt to mitigate roadway icing in winter. The finish also resists UV radiation and colour fading from direct daylight on sunny days. Taking advantage of seasonal opportunities, the renovation included adding a rooftop terrace. This expanded the previously unused space into an attractive destination. The L-shaped, wraparound outdoor venue welcomes all to enjoy its elevated patio,
urban garden and impressive city views. Houben said, “We created a welcoming public space that will be beautiful and functional now and 100 years from now, with… a unique and beautiful Wizard’s Hat on top with a free public terrace.”
Delivering the intended visual effect, the Fluropon® coating in Patina Green on the Stavros Niarchos Foundation Library’s wizard hat roof was applied by Brightsmith using a factory-applied coil coating process to finish the numerous metal panels and attached snowguards.
Rising 184 feet (approximately 56 m) above street level, the roof is clad ZIP-RIB aluminium panels from Merchant & Evans Co., Inc. (M&E), now Innovative Metals Co. Inc. (IMETCO).M&E provided 6,400 square feet (595 m2) of perforated screen wall panels plus 9,500 square feet (882 m2) of solid roof and wall panels. M&E also supplied the library roof’s internal gutters, fall protection, snow guards and custom light brackets – all were finished to match the panels in Fluropon Patina Green.
“Several of the team’s design choices solve the functional needs of the bustling central circulating library with iconic architectural gestures,” said Beyer Blinder Belle’s marketing manager Bisela Garrett. “Relocating some of the building’s mechanical equipment to the penthouse level above the new seventh floor frees up the valuable rooftop space for public uses.”
The painted and perforated screen wall metal panels to creatively conceal the HVAC equipment and enhance the Wizard’s Hat’s distinctive visual appeal.
Balancing geometry, colour and longevity
“For this particular project, the geometry and colour of the ‘Wizard’s Hat’ played a key role in matching the patinated copper-clad mansard roofs that are seen on many iconic buildings throughout Midtown Manhattan,” added Josh Younger, marketing manager at IMETCO.
He explained, “The ZIP-RIB panel is a 2.5-inch-deep mechanically seamed cladding system for roofs and walls that can be factory-formed or field-formed depending on the demands of the project. ZIP-RIB panels accommodate complex roof configurations including convex and concave curves and tapers.”
“The ZIP-RIB panel has been a staple solution in the roofing industry since 1964, with many original roofs installed as far back as 1970 still in operation today. This longevity has led to many lessons learned in the field that have produced useful solutions that we now rely on when faced with new challenges,” elaborated Younger.
Each panel’s position was determined by the architectural team to present a rhythmic pattern that integrates with the seventh floor’s glassenclosed spaces. BIM and 3-D modelling helped ensure all the roofing
products were properly aligned before they arrived in the field. Approximately 80% of the roof’s construction was prefabricated and assembled offsite, then shipped in sequence to the jobsite for installation. The Jobin Organization Inc. installed all the metal roofing components working in collaboration with general contractor Tishman Realty Construction.
Beyer Blinder Belle estimated that the prefabricated roof system saved two months in the construction schedule. The $200 million renovation project was completed in 2020 and officially opened in June 2021.
Along with its two million items in circulation and more than 400,000 books, the library building also offers new educational and programming spaces. These include dedicated areas for children and teens, a career services learning centre, a world-class business centre, a multimedia studio, and classrooms for English language, literacy, media and technology training.
The Stavros Niarchos Foundation Library conveniently is located across the street from the Stephen A. Schwarzman Building, which hosts NYPL’s reference collections and receives more than 1.7 million annual visitors. Together, they serve as NYPL’s Midtown
The OptiCenter All-in-One (OC10) powder management centre is equipped with the latest generation of OptiSpray All-in-One pump technology and guarantees the fastest powder output response times for consistent coating results.
Campus. The campus and its buildings reflect NYPL’s mission “to fight ignorance, and provide New Yorkers with the tools that they need to foster a better understanding of each other across racial and all other divides.”
“Libraries are the most important public buildings of all,” emphasized Mecanoo’s Houben. “There is something to inspire every visitor in the most diverse City in the world, and I am proud of that.”
Among the library’s many accolades, the project earned the Best Adaptive Reuse Award from the Municipal Art Society of New York’s 2021 MASterworks Awards. It also received top honours as the Grand Award winner and New Metal Roofs category winner in the 2021 Metal Construction News Project Excellence Awards.
Commenting as an awards judge, Steve Dumez, FAIA, praised the roof’s multi-functional design saying, “It’s providing a public space, it’s providing a mechanical space, and it’s providing an architectural cap that’s very dynamic… all of it adds up to a pretty wonderful piece.”
NYPL president Anthony W. Marx summarized, “It is the central circulating library New York City has long needed, wanted, and deserves. As we all look towards our next chapter of recovery and renewal, it is important that learning and opportunity be readily and freely accessible to all. There is no more important or better-timed civic infrastructure project to accomplish those ever present and pressing goals. We have waited a long time to give this great gift to the people of New York City.
We are so proud to share it now when the needs are so pressing.”
“This library is exactly what New York needs right now: a truly open and public place accessible to all, where people of all ages and backgrounds can experience wonder, grow in their understanding of the world, and launch on new trajectories that enrich life for all of us,” concluded Andreas Dracopoulos, co-president and director of the Stavros Niarchos Foundation. In total, the Foundation provided more than $60 million in support to NYPL.
For further information: www.coil.sherwin.com
Pintarelli Verniciature is one of the best-known companies in the contract powder coating industry thanks to its ability to anticipate market needs, its research into internationally certified processes, and its collaboration with universities and firms in the sector to study and develop quality-oriented solutions. The latest one, implemented in January, was a Dynamic Contour Detection system from Gema.
In our industry, quality certifications are tools especially recognised and sought-after by the most quality-conscious companies, be they businesses coating their products in-house or contractors. The most prestigious international quality marks are QUALICOAT for aluminium coatings and QUALISTEELCOAT for steel coatings.
The former was created in 1986, when a number of national associations, including the coaters of architectural components made of aluminium and its alloys, founded a structured organisation capable of establishing rules and procedures to increase and standardise quality levels throughout Europe. In recent decades, QUALICOAT has played a key role in
ensuring the quality of aluminium parts used in architecture, involving not only applicators but also various stakeholders in the aluminium industry, suppliers of coating materials, and manufacturers of surface treatment chemicals. Similarly, in 2006, the steel coating industry felt the need to set up a European organisation with the same characteristics to guarantee the quality of liquid and powder-coated steel: QUALISTEELCOAT was thus created to promote the dissemination of culture on metal corrosion protection in different atmospheric environments. The first Italian company to have obtained and maintained this certification has been Pintarelli Verniciature Srl since 2013. Pintarelli Verniciature Srl specialises in contract powder coating of metal components for several different sectors, particularly architecture, air conditioning, and furniture. Alessandro Pintarelli, the founder of this company based in Lavis (Trento, Italy) together with his sister Tiziana, explains: “Together with the QUALICOAT certification obtained in 2018 and our Qualicoat Class 3 approvals with paint suppliers AkzoNobel and TIGER Drylac®, this gives us a competitive edge over our competitors and is highly appreciated by companies requiring coatings with high corrosion protection properties, particularly on components that have to travel long distances to destinations all over the world.”
Pintarelli Verniciature is a well-known player in the coating industry: always attentive to market evolutions and the development of new solutions, it has been collaborating with the Corrosion Control Laboratory of the Department of Industrial Engineering at the University of Trento for over thirty years, where it carries out application tests and feasibility analyses, as well as initiating specific R&D projects of common interest. “To maintain the high level of quality required by these certification procedures, we need the best technology on the market. The latest innovation we have integrated into our coating line is the second-generation Dynamic Contour Detection system developed by Gema Europe Srl. Thanks to its new laser scanners, it ensures greater coating precision, increases transfer efficiency and finishing quality, and eliminates any risk of error due to programming parameters.”
Pintarelli Verniciature: a powder coating pioneer Pintarelli Verniciature was founded in 1987 to provide a local customer with a liquid painting service, soon joined by powder coating, which was still uncommon at the time. “Our company has always had a pioneering vocation,” confirms Alessandro Pintarelli.
“This has led us to anticipate market demands on many occasions, also supported by the collaboration with the Corrosion Control Laboratory of the University of Trento, started in 1993.” To keep abreast of this rapidly changing industry, the company has gradually integrated more and more state-of-the-art plants and equipment, to such an extent that the whole history of Pintarelli Verniciature has been proceeding hand in hand with the progress of powder coating technology over the years.
“In 1999,” says its owner, “we replaced our manual powder coating booth in galvanised steel with one made of dielectric plastics, which
allowed us to change colour more quickly by eliminating the problem of residual electrostatic fields. That enabled us to expand the range of powder RAL colours we could offer our customers. Between 2002 and 2003, the plant was fully upgraded to improve performance control and increase production flexibility in terms of size, processable parts, and colour range: the drying and curing ovens were replaced, and a new four-stage pre-treatment tunnel was installed.”
Between 2008 and 2012, the company initiated a research project called “Duplex: hot-dip galvanised steel coatability” in collaboration with the University of Trento’s Corrosion Control Laboratory and a well-known hot-dip galvanising company based in the area. “The goal,” recalls Pintarelli, “was to verify the influence of the hot-dip galvanising process on the coatability of steel components.” Further applied research projects were conducted in the following years, between 2014 and 2023, focusing on different topics such as coating durability, the influence of coatings on the environment, and the characterisation of low-e coatings. 2013 marked a significant turning point in the growth of Pintarelli Verniciature, as it moved to a new 11,000 m2 headquarters to accommodate a new, fully automated coating plant and a new R&D division. “During the same period, as a result of our constant research studies on the corrosion protection of steel, we were among the first companies to obtain QUALISTEELCOAT certification. In 2017, our 30th anniversary year, we integrated a new pre-treatment plant for aluminium in compliance with the QUALICOAT Product Certification we obtained in 2018. Two years later, we focused on our application equipment: we transformed our plant according to Industry 4.0 parameters, installed Gema’s innovative powder feeding system Smart Inline Technology to replace its Venturi pumps to improve film
Each individual gun is positioned and activated automatically and dynamically based on the precise digital reproduction of the piece, moving along an autonomous horizontal axis independent of the others. Right photo: the inside of the booth.
distension and application quality, and replaced its powder centre with Gema’s new OptiCenter OC07 unit to achieve optimal and consistent coating results. Finally, in 2022, we installed a new fully automated stainless steel pre-treatment tunnel connected to our central management system; intending to completely automate our factory, we also automated the paint warehouse using a MODULAR system. That is how, although we started out as a simple coating contractor tied to one local customer, we have now achieved an enviable and diversified customer portfolio in different sectors and geographic areas, including Switzerland and Austria.”
Beyond coating: from the Kanban system to assembly
Thanks to the improvement of its logistics and warehousing operations and the integration of an assembly department, Pintarelli Verniciature has developed into a full-fledged external production department for its customer companies, capable of providing an all-round service that complements powder coating. “We directly purchase the components that must be mounted on the coated parts. Especially with architectural parts, we can thus place them in their assembly kits and ship them directly to the construction sites. This has a double value for us: we reduce our delivery times by providing a service that the market seemed to need for a long time and we further meet our customers’ needs with an added-value operation.”
To manage the purchase of steel and aluminium components and their storage in its warehouse, Pintarelli Verniciature adopted the Kanban system. “Based on bar codes, it enables the warehouse manager to have full control over the level of supplies. Our warehouse is so well
structured that it even acts as a logistics hub for some of our customers, storing their components and informing them when the stock starts to run low via data sharing software.”
In Pintarelli Verniciature’s production department, the monorail conveyor first takes the parts to the pre-treatment tunnel, which performs the following stages: degreasing, two rinses with mains water, deoxidation of aluminium and galvanised steel parts if required and further rinse, two rinses with demineralised water, and application of Henkel’s Bonderite® APNR (Adhesion Promoter No Rinse). Once the parts are dried, the powder application phase can begin, followed by oven-curing with a temperature of up to 200 °C and unloading.
“The protocols for obtaining and maintaining our certifications entail frequent checks of the values both of the baths and of samples by designated bodies such as Qualital. Thanks to the high quality of our pre-treatment and powder application phases, we can achieve corrosion class C5H even with Sendzimir sheet steel, which we paint in three coats, i.e. two layers of primer and one of top coat. We are the only company to provide this service, in response to a specific request from some customers needing to achieve this corrosion protection class with this type of sheet metal.”
For Pintarelli Verniciature, one of its team’s most delicate jobs is making customers aware of the crucial role of surface quality: “In our workshops, we try to make our stakeholders aware of the importance of meeting minimum product requirements as an objective involving the entire supply chain, in order to achieve the expected corrosion and durability
properties, as defined by law and by the technical specifications of the QUALISTEELCOAT and QUALICOAT certifications. We also noticed that whereas until recently, very few clients requested this type of certification and it was always our team that brought it up first, today, especially in the field of architecture, a quality-oriented culture is spreading that also translates into the demand for these two certifications. And we are already prepared to meet it, thanks to the continuous updating of our systems, including the recent integration of Dynamic Contour Detection.”
“This technology,” illustrates Gianluigi Baroni, the Sales Manager of Gema Europe Srl, “uses laser scanners to detect the shapes of complex parts. The dynamic contour detection process takes place through two stages: reading and application. Installed at the booth’s entrance, the laser scanners work in two-dimensional mode and provide a digital image of the contour of the application area. This data, combined with precise speed tracking via a dedicated encoder, generates an exact three-dimensional contour of the object, immediately sent to the MagicControl 4.0 device. Each individual gun is positioned and activated automatically and dynamically based on this precise digital reproduction, moving along an autonomous horizontal axis independent of the others.” Thanks to multi-angle technology, the scanners can detect the contours of the thinnest workpieces and the most complex shapes.
“We also changed the guns’ layout inside the booth,” emphasises Pintarelli Verniciature’s Production Manager, Paolo Ferrero, “significantly reducing the distance between one gun and the other. This gave us greater control over the thickness and quantity of powder dispensed by each nozzle and improved our degree of quality and application efficiency thanks to higher dispensing consistency and, therefore, better film distension. Greater application control also means significant powder savings. Although this new system has only recently been integrated, one of its advantages is already clear: out of the three operators per shift in charge of pre- and post-finishing activities, one has already been transferred and assigned to other functions. That means we have assigned this people to logisticsrelated activities, which, as mentioned, are becoming increasingly relevant.”
“In addition to the concrete advantages brought by this new system,” adds Ferrero, “we are gradually changing the mindset of our operators, who were used to working by holding the powder application gun in their hands to carry out pre- and post-finishing operations. Now, on the other hand, they have to learn how to use another type of device, the Coatmaster® Flex, intended exclusively
for measuring coating thicknesses and, if there are any defects, adjust the operating parameters on the MagicControl 4.0 touch screen. That is undoubtedly a significant transition from a mechanical operation where results were visible in real-time to a mental effort requiring to understand which values need to be adjusted to improve the application results. Once our operators have complete control of these new functions, we will be able to work at full capacity.
“Thickness control is carried out on a sample basis because, thanks to the laser scanners of the Dynamic Contour Detection system, the recipes’ setting options make it easier to ensure high process repeatability. The process is more reliable, and its effectiveness can be compared to that of a numerical control machine, precisely because the guns adapt to the thickness-related parameters for better coating results even with minimal thicknesses, such as those required by the architectural sector.”
“Despite my initial scepticism about the three-year ROI guaranteed by Gema,” admits Alessandro Pintarelli, “I had to change my mind. For example, fire regulations for buildings are rapidly becoming stricter and stricter, such as EN 13381-8, which defines the maximum thickness applicable to steel sheets: if the thickness value exceeds it,
the component is not compliant. Thanks to the new system installed by Gema, our guns can apply paint at the same distance and with the same flow rate even with calendered or concave sheet metal, which leads not only to better film distension and powder savings (currently 20%) but also to full control of paint application, which does not exceed the thickness parameters imposed by the standard.”
In future, Pintarelli Verniciature also expects an increase in its production capacity, as it will be less and less necessary to stop the conveyor to carry out manual touch-ups, which is also a significant advantage in terms of end results. “We are finding fewer and fewer paint defects due to human error, such as the orange peel effect, and we can provide products that are not only corrosion-resistant but also aesthetically pleasing, something that is also increasingly in demand in the architectural sector.”
Its far-sightedness and its ability to anticipate market needs and react quickly to customer demands have made Pintarelli Verniciature one of the best-known companies in the contract coating industry.
“We were among the first to study and refine a process to obtain QUALISTEELCOAT certification, and this testifies to the attention to quality ingrained in our DNA, also evident when it comes to selecting devices and equipment for our factory – such as Gema Europe Srl’s Dynamic Contour Detection system.”
CHEMTEC’S technologies are designed to have a very limited environmental impact, to reduce consumption of resources and for a greater operational simplicity.
CHEMTEC develops customized solutions that aim to maximize the customer’s satisfaction.
NANOTECHNOLOGICAL CONVERSION COATING
WATER PURIFICATION AND RECIRCULATION
ONE STEP METAL PRETREATMENT
PAINT STRIPPERS
DISCOVER MORE ON WWW.CHEMTEC.IT
Giulia Gentile ipcm®
Design is synonymous with shapes but also with colours. That is why Italian manufacturer ST Powder Coatings decided to present its products at Fuorisalone 2024, emphasising that colour is an essential element within the artistic design process of furniture and accessories.
Designing today is not only about creating sketches but also – and above all – researching. In today’s world, the path is part of the goal, and anything that goes into making an object contributes to determining its value. That is why, once again, Fuorisalone 2024 decided to reserve a place of honour for materials, which are a crucial part of creating design pieces and which, in turn, develop from specific paths. It is precisely on this concept that ST Powder Coatings focussed
its participation in Materially Now, the exhibition that celebrated materials during Design Week 2024 by involving many companies that are driving the evolution of this sector.
Process-oriented design
ST Powder Coatings (Montecchio Maggiore, Vicenza, Italy) is a company specialising in the production of powder coatings to be applied on metal
surfaces for aesthetic and functional purposes. For years, it has been offering a wide range of colours in polyester, epoxy-polyester, epoxy, polyurethane, and silicone systems, in both standard and customised formulations, with different degrees of gloss, from super-matte to glossy, and various textures, including smooth, rusticated, wrinkled, damascened, gator effect, and hammered. Precisely because of its ability to produce paint products with a very high aesthetic impact, it has established itself as one of the leading suppliers of powder coatings for the design and architecture sector. And, as it serves this market segment, it was natural for ST Powder Coatings to be present at Materially Now to disseminate knowledge about powders themselves.
“For us, taking part in this exhibition is a unique opportunity to prove our capabilities, highlighting the work done in our research and development laboratories,” stated the company’s owner, Marco Zadra, who also added: “Our installation shows the whole process of creating coatings, from raw materials to end products. We would like to make the Design Week visitors understand that finishes are not just a matter of colour but also involve other important functional and performance parameters. Understanding this process helps designers make more informed choices as they can grasp all the results that can be achieved through any given finish.” Indeed, as anticipated, there seems to be a trend in the world of design, among both professionals and end consumers, towards paying greater attention to the history of objects: it is becoming increasingly important to know their origins, retrace their creation process, and identify the characteristics of the materials used. With this in mind, ST Powder Coatings created an evocative installation that could make design professionals aware of what lies behind what is trivially called “colour”. The process starts with pigments: their mixture determines the recipe for the formulation of the powder coating being produced.
This recipe takes into account several variables, such as colour, chemistry, and the technical functions that the paint must guarantee. Once the ingredients have been determined, they are mixed, passed through an extruder for uniform blending, subjected to a process of melting and re-solidification, and finally broken into “chips”, i.e. the semi-finished products that are subsequently ground and reduced to very fine powder. “We aim to meet a need for knowledge because when designing an object, it is necessary to know what is entailed in choosing a particular paint product in terms of both aesthetics and functionality. What we wanted to achieve at the Fuorisalone was presenting an exhibition that explained the path from raw materials to semi-finished products and finally to coatings ready to be applied in the “language of the eyes”, so crucial in this context,” explained Zadra.
An all-Italian staging in an international setting
For ST Powder Coatings, this was the second participation in Fuorisalone. After the 2022 edition, the company chose to be present again this year because the Materially Now event was an excellent opportunity to emphasise the quality of its products and their key role in creating designer objects. “This event is part of Design Week, an international showcase where, at the same time, we are “playing at home”, demonstrating to foreign visitors that the quality typical of Made in Italy can be found even in powder coatings,” stated Enrico Dall’Igna, the marketing manager of ST Powder Coatings. At Materially Now, ST Powder Coatings set up an exhibition consisting of aluminium spheres coated with smooth, matte, and micalised finishes, allowing visitors to touch and see first-hand
the endless possibilities of powder coatings. As the aesthetic and functional characteristics of products depend on the raw materials chosen for the paints and how they are subsequently processed, ST Powder Coatings’ goal was to inform designers on these aspects and ultimately enable them to communicate their needs more precisely, in order to better collaborate in finding the ideal solutions to realise the objects they have in mind.
Green Oasis: the sustainable powder coating line
Precisely because the value of an object has so much to do with the process that leads to its creation, it is also more essential than ever to highlight any effort to reduce its environmental impact. ST Powder Coatings’ philosophy has always been focused on technical innovations geared towards developing solutions that are not only aesthetically pleasing but also bring tangible benefits to people and the environment. “Since 2012, our R&D lab has been on a pioneering path, working on the creation of coatings made from renewable raw materials. This commitment has been a turning point in the industry, leading to the creation of a series of innovative and sustainable products,” illustrated the company’s marketing manager.
Over the years, ST Powder Coatings’ R&D department has refined its insights, peaking with the development of a line of powder coatings called “Green Oasis”. This is the culmination of the company’s efforts towards sustainable growth, as these coating systems not only offer superior performance and exceptional aesthetics but are also manufactured responsibly. “With the Green Oasis series, we want to provide our customers with high-quality products and, at the same time, the opportunity to actively contribute to environmental protection by choosing sustainable solutions for their coating needs. We are convinced that this new product line is a significant step forward in our commitment to promoting responsible
practices. We know that professionals in the design world pay special attention to these issues, so we are happy to be at the Fuorisalone to showcase our solutions,” added Zadra. During the most important week of the year for the design sector, ST Powder Coatings thus enthusiastically presented itself to industry insiders with a strong desire to share insights. Its aim was to prove itself as a partner capable of “giving colour” to designers’ and architects’ ideas by developing customised powder coatings for their projects. “Our hope for the present and future is to continue to be a benchmark supplier in this thriving sector. Our goal is to sit down with designers and architects and illustrate our manufacturing process, making clear that not only the colour but also the gloss and texture of their objects strongly depend on the substances used to produce the selected paints and their processing methods ,” concluded Marco Zadra.
Overspray free paint application with EcoPaint Jet
Revolutionar y pr e cision in automatic appl ic ation br ings ef f icienc y to pr o duc t customization. Dürr’s solution EcoPaintJet applies sharp-edged paint lines on surfaces, pushing the limits for efficient and resources av ing co ating: No over spr ay, no mor e masking of your product www verind.it
A cutting-edge, water-based coating cycle, a new plant designed by Silvi in collaboration with Futura and CMA Robotics, and a water treatment system supplied by Water Energy to optimise environmental sustainability: these were the technical choices made by La Marzocco, an Italian manufacturer of excellence in the industry of high-end professional coffee machines.
In the world of premium coffee, a symphony of elements converges to create an unparalleled taste experience: every detail matters, from the beans’ selection to the grind’s precision. However, one aspect that is often overlooked is the design of the coffee machine. Yet, for coffee lovers who appreciate not only this drink’s taste but also the rituality and art of coffee preparation, coffee machines are much more than just tools.
La Marzocco stands out in this field as a leading Italian company in the handcrafted production of high-end professional coffee machines. Founded in the heart of Tuscany in 1927, it has been able to combine craftsmanship and technological innovation to create true works of functional art.
Every coffee machine produced by La Marzocco is the result of a relentless commitment to excellence: in addition to guaranteeing
superior performance, these objects are designed to enrich the environments in which they are placed with peculiar, refined design. Every detail, from the selection of materials to the choice of finishes, is handled with the utmost attention.
Coating plays a crucial role in this constant quest for excellence. “It is not simply a matter of surface protection but rather a fundamental element in giving our products that touch of style and sophistication that sets them apart,” states La Marzocco’s Purchasing Operations Manager Elena Ciuffi. That is why the company recently decided to equip its production plant, located in Scarperia (Florence, Italy), with a new coating system designed and installed by Silvi Srl (Peregallo di Lesmo, Monza e Brianza, Italy), specialising in surface treatments for over thirty-five years. The project also involved other leading partners in the coating sector, including Futura Convogliatori Aerei (Robecco Pavese, Pavia, Italy), CMA Robotics (Pavia di Udine, Udine, Italy,) and Water Energy (San Pietro in Casale, Bologna, Italy). As well as improving coating quality, the resulting plant is also going to speed up production, enabling the company to meet its customers’ requests in a more flexible and timely manner.
An Italian icon around the world: La Marzocco
The history of La Marzocco is a testimony to passion, tradition, and innovation that has deep roots in the heart of Florence. Founded way back in 1927 by two brothers ahead of their time, Giuseppe and Bruno Bambi, this company started out as a small workshop where coffee machines were tailor-made with great care and dedication. “In the early 1900s, coffee underwent a significant transformation by becoming espresso, i.e. freshly prepared, thanks to innovative espresso machines that helped enhance its qualities,” explains Giada Biondi, Communications Manager at La Marzocco. “For this reason, from its earliest stages, our company has been and still is characterised by its focus on the quality of coffee extraction, recognising the crucial importance of this process for the consumer experience.”
At the same time, what has distinguished La Marzocco from the beginning has been its open and future-oriented mindset: while remaining true to its heritage and Florentine roots, influenced by the Renaissance and the aesthetic concept of Beauty, it has also always welcomed customer feedback in a constructive manner, thus constantly reinventing itself and expanding its horizons. “1939 was an eloquent example of this, as the Bambi brothers decided to market the world’s first horizontal-boiler espresso machine. This innovation improved ergonomics thanks to a more efficient layout of the dispensing units while, at the same time, the absence of a vertical column improved the interaction between baristas and customers, giving them a chance to have a conversation. This originated the convivial, socialising aspect associated with the preparation of coffee in cafés, which became a meeting and sharing opportunity,” Biondi adds. In the following years, La Marzocco continued to evolve by adapting the design of its machines to historical contexts and consumer needs. “In the 1950s, for example, it embraced the trend of lever machines, which enabled to prepare perfectly creamy coffees thanks to constant, 9-bar pressure for extraction. The period of the post-war economic boom, which corresponded with the entry into the company of Piero Bambi, Giuseppe’s son, marked a crucial moment for La Marzocco’s success: thanks to their refined design and revolutionary technology, including horizontal boilers and the use of stainless steel instead of copper, its machines became synonymous with reliability, durability, and high performance, first locally and then internationally.
In the first coffee machines, the brewing groups were placed on a vertical column.
Customised production and maximum attention to finishing
“Especially in the last decade, we have opened key subsidiaries in China, the US, South-East Asia, Scandinavian countries, Australia, the UK, and lately also in the Middle East. Recently, there has been higher and higher demand for La Marzocco machines in Italy, France, and Spain, too: a trend that reflects a growing interest in the quality of coffee and the experience associated with it. Indeed, La Marzocco has espoused the specialty coffee movement – supporting the use of coffee of excellence, rated 80+ by experts – embracing the quest for the highest quality, authenticity, and customisation of the taste experience to reach the target clientele of coffee connoisseurs. We have also contributed to enhancing the barista profession by sponsoring world championships and training courses, recognising its crucial role in transforming coffee from a raw material into an extraordinary drink. Finally, the latest breakthrough occurred in 2015, when La Marzocco launched the La Marzocco Home division, introducing a line of coffee machines for home use.”
Customised production and attention to finishing are the distinctive traits of La Marzocco. “Each machine is characterised by recognisable aesthetics, with the predominant use of steel and exposed assemblies, but it is fully customisable to suit customer preferences,” says Ciuffi. “Since 2014, we have experienced exponential growth in our production. Although we currently produce 40,000 units per year, however, we still manage to carry out traditional craftsmanship operations. Our factory has no assembly lines, and each machine is produced with the utmost care and attention by our employees. Over the years, we have forged significant and fruitful partnerships with a number of local suppliers that provide us with pre-formed metal sheets and the mechanical components needed to build our machines. Within our production department, we deal exclusively with the welding of boilers, which are the heart of our machines, using automatic robots, as well as the assembly and testing phases – plus, for a few weeks now, the coating step.”
La Marzocco recently decided to insource its coating operations to achieve higher finishing quality and extreme customisation flexibility. “We used to outsource this delicate phase to four companies specialising in contract coating. However, our machines have three
to five coated parts each, and, unfortunately, having components painted by different contractors often led to colour-matching and coating uniformity issues. The decision to install a coating line gave us greater control over the process, ensuring that each machine has a uniform, high-quality finish in line with our exacting standards. These are the factors that prompted us to invest in a coating plant,” indicates Ciuffi. La Marzocco has two production lines: one for producing professional coffee machines and grinders and one for its Home range. “We use six colours for our professional products: white, black, red, yellow, light blue, and metallic silver, as well as some limited editions. For the Home product range, we use a much wider selection of tints,” she notes.
“Finishing is an integral part of our quality concept. Every machine must be perfect and tailored to the customer’s specifications. Finishes and custom elements are not just aesthetic details for us but key differentiators. Through constant communication with distributors all over the world, we realised that many of our machines were being adjusted locally to meet customer requirements: therefore, we decided to offer a customisation service ourselves to ensure that each La Marzocco machine is perfectly in line with our customers’ expectations,” says Matteo Urzetta, Purchasing Specialist at La Marzocco.
e ripristino. Modifica o sostituzione di parte dei componenti. Adeguamento alle norme di sicurezza vigenti. Sviluppo di processi di miglioramento delle prestazioni.
The new line installed in February 2024 was designed to coat mainly AISI 304 and 43 steel sheets. The plant features a highstability, power&free inverted conveyor supplied by Futura Convogliatori Aerei, specifically developed to enable the in-line chemical pre-treatment of the parts in a tunnel performing five stages: degreasing, two rinses with mains water, a rinse with demineralised water, and the application of a no-rinse passivating agent. “DN Chemicals (Caleppio, Milan, Italy) developed the chemical products. Currently, it is also helping us assess the possibility of adding a stage for the application of a nanotechnology passivating agent by atomisation to make the pre-treatment cycle even more efficient,” explains Urzetta. “The application of the nanotechnological passivation product DOLLCOAT SA 116 can in fact improve the anti-corrosion properties and promote the paint adhesion. The main problem to be solved was not the cleaning of the surfaces and their passivation, but the total removal of glue residues used in the peelable films that protect the metal before mechanical processing and pre-treatment. These glues tend to leave residues in parts with folds or more complex geometries, making it necessary to use specific additives for their complete removal", explains André Bernasconi, General Manager of DN Chemicals.
The components are then taken to an air-blowing booth and a drying oven. Afterwards, the automatic paint application phase begins inside three booths equipped with robots supplied by CMA Robotics. “The booths are devoted respectively to the application of the primer, coloured base coat, and clear coat and feature an overspray collection system with a water curtain and a grid bottom with a water collection tank underneath,” illustrates Silvi’s Sales Manager Daniele Fumagalli. “We have created heated flash-off areas and storage buffers between one booth and the other. In addition, there are hot water batteries above the booths and flash-off areas, connected with a heating plant to maintain constant temperatures from 60 to 80 °C. Finally, all the areas that make up the line are pressurised, heated, and air-conditioned.”
“Based on La Marzocco’s requirements, we supplied three different drying ovens in line with the types of paint products used. For primer drying, the company wanted to maintain relatively low temperatures, so we supplied an oven featuring a generator with a hot water battery; for drying the coloured base coat and clear coat, on the other hand, we installed two convection ovens with direct exchange burners because they needed much higher temperatures,” adds Fumagalli. After coating, the components are finally conveyed into a storage buffer with forced cooling before reaching the unloading area.
rotoli, pannelli e celle in fibra di vetro
celle filtranti per alte temperature
rotoli e pannelli in fibra sintetica
accumulatore
vernice “Columbus”
filtri “Andreae”
cartucce filtranti
filtri assoluti
applicazioni speciali
rolls, panels and cells of glass fiber
filtering cells for high temperatures
rolls and panels of synthetic fiber
paint accumulator “Columbus”
“Andreae” filters
filtering cartridges
absolute filters
special application
distributori esclusivi per l’Italia
massima efficienza
massimo accumulo di vernice
massima durata
minori costi di smaltimento
rispetto ai filtri oggi in commercio =
minori costi di manutenzione
L’esclusivo design alveolare permette di trattenere quantità di overspray notevolmente superiori
“Thanks to the high flexibility of the plant, in addition to the technical end-of-shift emptying operations, it is possible to compensate for any differences in process times, also taking advantage of the intermediate storage buffers included in the conveyor’s layout. In addition, the integrated command and control system not only connects all the various stations but also enables to acquire data online and match it with the code assigned to each load bar. This data is then sent to the management system during the unloading phase,” indicates Stefano Gerletti from Futura Convogliatori Aerei.
Water-based clear coat: a major technological challenge
“A small part of our production is powdercoated, but over 90% of the components we manufacture are liquid-coated by electrostatic application. Given our strong focus on environmental impact reduction and sustainability, we have chosen to use only water-based paints by relying on Vernici Caldart (Pojana Maggiore, Vicenza, Italy),” states Elena Ciuffi. “We immediately found the perfect primer and coloured base coat products. The challenge was finding an acrylic two-component transparent top coat that would suit our production. Water-based clear coats are a very innovative product from a technological point of view, but they present several problems, especially related to yellowing over time. Through a process of research and development and after several tests, we overcame these issues and found the right solution to guarantee this product’s high quality and durability. This success certainly represented an important step forward in our quest for high-quality, environmentally friendly finishes.”
Water treatment: a key pillar for environmental sustainability
“The importance we place on the ecological impact of our activities is reflected in every stage of our production. We are actively trying to reduce our ecological footprint and improve
the sustainability of our production processes. We will soon install photovoltaic panels to cover part of the new coating line’s energy needs.” As for the actual coating phase, La Marzocco relied on Water Energy’s know-how to install several innovative water treatment solutions. Based in Bologna (Italy) and specialising in coating water treatment plants, this company supplied three Skimmerflot 3000 series sludge separators, one for each application booth.
“The Skimmerflot units operate by mechanically separating sludge from water, allowing it to emerge and be removed through continuous skimming of supernatant particles, which are sent to special containers equipped with drainage bags. To facilitate the separation of pollutants and the flotation of sludge, Water Energy uses micronised air injected directly into both the feeding circuit and the bottom of the reaction tank,” says Tommaso Ponara, the owner of Water Energy. “We also installed an automatic demineralisation system in the pretreatment tunnel with the aim of continuously recirculating the demineralised water used in the last rinsing phase, to maintain the rinsing water’s quality high and prevent the presence of any residues from jeopardising optimum paint adhesion.”
Water-based paints tend to generate more foam than solvent-based ones as they contain surfactants that keep the product fluid and promote its adhesion to the workpieces during application.
“However, we believe this can be managed effectively by carefully and precisely identifying the ideal chemical products. Water Energy supplied La Marzocco with various chemicals, including flocculants, denaturants, defoamers, and a pH corrector that also acts as a sanitiser.” The addition of a flocculant helps lump the sludge produced in the booth and the denaturant prevents the paint from remaining sticky once it comes into contact with water, promoting the formation of micro-flakes that float in the collection tank. This way, the system’s pump can recirculate the water without recirculating the sludge. Afterwards, a flotation system further separates the floating sludge, which is then sent to the Skimmerflot unit, where it is removed and gathered in a dedicated collection tank. This process results in highly solid eluate, reducing residual moisture in the sludge and improving its drainability once collected in bags for disposal. The system was designed in line with the Industry 4.0 parameters and allows remote monitoring and intervention to
solve any problems that may arise, as well as displaying process parameters and any anomalies.
“In addition, La Marzocco has joined a Plastic Free programme to further reduce the environmental impact of its business. We supply full drums in exchange for empty ones to encourage reuse and avoid plastic disposal. If any drums are damaged, we are committed to recycling them for other activities, always ensuring responsible waste management and promoting environmental sustainability,” indicates Tommaso Ponara.
The new coating line, which has only been operational for a few weeks, is the result of months of work and technological testing by all the companies involved. “We chose Silvi as our partner to design and install our system after careful market research. Its team was willing to support and introduce us to the world of coating, in which we had little experience and technical knowledge. We are also pleased with the collaboration with all the other partners that worked on this project and contributed to its success.”
“Installing this new coating line was a significant step forward for La Marzocco, as it solved many of the logistical and quality-related challenges we faced with external contractors.
The increase in production year after year and the growing demand for customised finishes for our Home line made this plant essential for maintaining high quality standards and avoiding interruptions in our workflow.
“One of our next goals is to obtain B Corp certification as a company committed to assessing and improving its environmental and social performance with the same attention traditionally paid to economic results. This commitment is also reflected in our choice to use water-based paints, the water treatment system we selected, our participation in Water Energy’s Plastic Free programme, and the installation of solar panels,” concludes Ciuffi.
Let‘s talk about injector technology. A technology that you should keep an eye on. Actually, it‘s just getting started. And now, Flowsense takes it to a new level. FLOWSENSE? It‘s a software masterpiece and a bunch of small sensors that do big things: Consistent powder output from the rst to the thousandth workpiece. Put quality on repeat!
Sally Put
Axalta Coating Systems GmbH, Basel - Switzerland sally.put@axalta.com
In order to help its customers to minimise their carbon footprint, Axalta developed Alesta® BioCore™: a new range of powder coating solutions derived from non-food organic waste that replaces traditional polyester resins with an alternative based on natural materials, reducing CO2 emission by up to 25%.
Surface coatings are in many ways the unsung heroes of the construction and architectural world. Though perhaps not the first thing that springs to mind when thinking of a beautiful design, they play a crucial role in enhancing aesthetics and improving the durability of surfaces. Structures that withstand the test of time are inherently more sustainable and high-quality surface coatings can support this aim.
The same performance requirements that one would associate with surface coatings must also be reconciled with ever more stringent sustainability pressures. The question, now is how surface coatings can also contribute towards the environmental and sustainability goals of a project? The answer: more so than many people think.
The rise of sustainability In the space of a few short years, sustainability has gone from being a peripheral concern to one of the main priorities of the coatings industry and its customers. Across these industries, businesses are continuously looking for ways to reduce their environmental impact, eliminate waste and utilise resources more efficiently.
People increasingly want to work with sustainable businesses, so continuous improvement is a must in order to remain competitive. Against the backdrop of the Sustainable Development Goals of the United
Nations, businesses face mounting pressure to demonstrate their impact towards emissions goals. This need for transparency is at the heart of an intense focus on identifying potential opportunities for improvement.
Easy as (scope) 1-2-3!
Architectural and manufacturing businesses have all made enormous progress in tackling emissions across their own operations. And yet, even if we factor in the additional impact of scope 2 emission reductions, it is clear that cutting scope 3 emissions holds the greatest potential impact. Scope 3 accounts for the
largest portion of overall emissions and while this represents an invaluable opportunity, this also comes with additional complexity. This requires a business to look at the entire value chain and how each step contributes to the overall impact.
A large number of emissions reside within the raw materials that comprise powder coatings solutions, bringing the strategic importance of supply chains into clear focus.
Small changes, big results
If we consider the makeup of conventional powder coatings, it is clear that much of their
Besuchen Sie uns:
Halle 1
Stand B 48
embodied carbon is contained within the polyester resins that are a key ingredient. Spotting an opportunity, Axalta developed Alesta® BioCore™1, a range of powder coating solutions derived from non-food organic waste. By replacing traditional polyester resins with an alternative based on natural materials, which are inherently less carbon intensive to source than their fossil fuel counterparts, can deliver a CO2 reduction of up to 25%. Such benefits can be accessed immediately by switching to Alesta BioCore and without any drop in performance, since they offer the same properties and benefits. For customers targeting a reduction in scope three emissions, it provides an effective and immediate route to achieve their sustainability goals.
The green supply chain
Earlier in 2024, Axalta became the first manufacturer within the powder coatings industry to receive International Sustainability and Carbon Certification PLUS (ISCC PLUS) for biobased feedstock sourcing practices. As customers become increasingly focused on tackling scope 3 emissions, the appeal of verifiable and fully-traceable feedstock sourcing practices will only continue to grow. Choosing to source feedstock from non-food waste can be seen as a more responsible choice. as it does not create any additional burden on food supply.
1 www.axalta.com/biocore
Introducing Alesta® BioCore™
Providing a sustainable alternative to incumbent products containing fossil fuel-based polyester resins, Alesta BioCore will be on sale in Europe from 21st May 2024 and includes:
Alesta SD BioCore Architectural SuperDurable, a range of super durable biobased powder coatings formulated with high performance exterior grade pigments of the highest quality. This Qualicoat Class II- and AAMA2604-certified product line delivers exceptional weather and UV resistance and is backed by a warranty of up to 25 years;
Alesta AP BioCore Architectural, a range of standard durable biobased powder coatings formulated with high quality exterior grade pigments. Designed for outdoor architectural substrates and outdoor structures such as cladding, it is compliant with standards such as Qualicoat Class I, AAMA 2603 and GSB Florida 1 (Standard) and is backed by a warranty of up to 15 years;
Alesta IP BioCore Industrial, a range of biobased powder coatings for outdoor industrial applications, offering excellent weather resistance, outstanding mechanical properties for outdoor durability, and first-rate reactivity.
Low
From an interview with Daniel Pelikan TIGER Coatings GmbH & Co. KG, Wels – Austria
The new TIGERator allows to create real-time, realistic renderings of products coated with TIGER Drylac® finishes in different colours, gloss and surface textures directly in the web browser, ending the lengthy brainstorming and decision-making processes and helping to choose the perfect powder coating finish for each project in a matter of seconds.
In the dynamic landscape of industrial design, envisioning the perfect finish for a project has often been a challenge. However, with advancements in technology, particularly in the realm of 3D visualisation and digital rendering, the process has become significantly streamlined.
During the first day of PaintExpo, the leading trade fair dedicated to industrial painting and coating technologies held at the Karlsruhe Exhibition Centre (Germany) from 9th to 12th April 2024, TIGER unveiled its new digital tool: TIGERator represents a significant leap forward in the realm of powder coating visualisation. Building upon their previous software, which allowed users to upload 3D renderings of their projects and experiment with different colours and finishes, TIGERator now offers an even more comprehensive solution.
Users can now access a vast library of common objects already uploaded onto the platform and apply digital representations of TIGER Drylac® powder coating finishes in an array of colours, effects, and textures.
The new TIGERator digital visualisation tool
By digitising real-world surfaces and simplifying the process of applying powder coating finishes, the TIGERator offers new possibilities for visualising and creating design concepts.
Originally conceived as a solution for architects and product designers, the tool has evolved to cater to a broader audience, including coating companies and job-shop. The TIGERator particularly provides job shop customers with an indispensable tool for the often-lengthy process of
defining materials. The selection process can thus be made significantly more efficient – impacting good customer service. Ultimately, the TIGERator is the perfect digital supplement to conventional colour cards, clearly setting TIGER apart from its competition. This also completes the sustainability cycle by substantially decreasing paper consumption through minimised use of printed colour cards.
The key to its effectiveness lies in its simplicity and realism. The digital surfaces included in the tool dataset are based on real scans of powdercoated surfaces, providing users with an unparalleled level of accuracy. With just a few simple steps, users can obtain a realistic preview complete with the desired powder coating finish. This preview serves as a valuable aid in decision-making, allowing users to visualise the final appearance of a product before any physical work begins.
“The digital surfaces included in the tool dataset are based on real scans of powder-coated surfaces, offering the unique opportunity to paint rendered objects with powder at the click of a mouse or via touch. With just a few steps, the users can finally obtain a realistic and useful
preview of a variety of TIGER powder coatings applied on selected 3D models, in order to bring their vision to life. Its capabilities will also expand in the near future, with plans to introduce metallic colours,” declared Daniel Pelikan, Online Marketing Specialist for TIGER.
The process of using TIGERator is straightforward and intuitive. Users begin by selecting a 3D model from the extensive library, categorised by application areas such Architecture, Design Elements, Furniture, Transportation, General Industry, and more. Once a model is chosen, users can browse through the extensive range of TIGER Drylac® products and select the desired colours, textures (i.e. rough, hammertone, and fine texture) and effects. With a simple drag-and-drop interface, users can apply the chosen finish to the 3D model and check it from all angles, rotating and it as needed.
The tool allows to apply different finishes to the several parts composing the selected component and examine the result with a light source
An example of application.
coming from the top, in order to understand how the reflection will influence its appearance.
Additionally, users can also leverage an augmented reality (AR) functionality, allowing them to visualise 3D models in real-world environments, providing invaluable insights into scale and appearance. “We wanted to grant customers the ability to examine how a particular finish looks on a real-word object. For example, you can take a picture of your car, select a finish for the wheel and position it in front of your car,” explained Pelikan. Once satisfied with the design, users can download it with a single click, share it with collaborators and customers or they can proceed directly to the web-shop, refer the product data sheet and purchase it in the TIGER Webshop.
One of the standout features of TIGERator is its accessibility. The tool operates entirely within a web browser, eliminating the need for additional software installation or updates. This means users can get started right away on a desktop or on mobile devices with an internet connection, simplifying collaboration with customers and partners.
Rendering is web-based and live – with no comparable service available on the market.
“We already had offered our product coatings as digital scans for three years. These are digital files that weigh more than 50 megabytes, so until now they were mostly used by architects and product designers. It was a great solution for them, because by adding the desired powder coating finishes on their digital model, they could understand the appearance of colours, the surface structure and its gloss in a realistic manner”, added Pelikan. “But the previous version required specific software and a license, as well as someone who was able to operate the software and create 3D models and renderings. So, it was not accessible to every coating company or every architect. But now we have installed a 3D scanner in our headquarters, so each newly-produced panel or product is being scanned and uploaded on the tool, so that users don’t need to do that themselves.”
“TIGERator represents a groundbreaking advancement in powder coating visualisation, offering users a simple yet powerful tool for
1. Open the TIGERator webpage: www.tigerator.com;
2. Make your selection from an extensive 3D library of application areas such as Architecture, Furniture Transportation, General Industry, and More;
3. Decide on a model that you would like to coat digitally with TIGER Drylac® powder coating;
4. Browse through the extensive TIGER Drylac® product range and select the appropriate finish;
5. Drag and drop the desired surface onto the 3D model and view it from all angles by rotating and turning it;
6. Download the design with one click or share it easily with your customers and partners;
7. Go to the TIGER webshop and use the possibility to order original effect samples coated with TIGER Drylac®, download TIGER Digital Finishes for CGI rendering programs or buy the powder coating product directly;
bringing their design visions to life. With its realistic representation, ease of use, and accessibility, it is poised to revolutionise the way designers, architects, and manufacturers approach powder coating selection and application,” concluded Pelikan. “Although it provides an incredibly realistic representation of the final product, some degree of variation may occur, depending on the quality of the display device. To ensure complete satisfaction, we then offer the option to request a real sample of the chosen powder coating finish, allowing users to verify the colour, effect, gloss, and structure firsthand.”
For decades, Radial has been designing, building and installing tailor-made coating plants for metals, plastics and wood. Our systems are the ideal choice for those who desire a cutting-edge turnkey solution.
Choosing the right products and processes for coating carbon fibre is crucial to preserving its properties and enhancing its aesthetics. The right system, including the 30100 CARBON PRIMER TRX FILLER primer and the 30102 CARBON LOOK FINISH clear coat, ensures a high-quality, weather-resistant finish. The pigmented primers 30101 Carbon Grey Filler and 30103 Carbon Black Filler also allow experimenting with a wide range of effects and finishes. Lechler’s goal is to provide solutions that improve the aesthetic and mechanical characteristics of carbon fibre and make any creative customisation possible.
Thanks to its exceptional strength and lightness properties, carbon fibre is now increasingly used in a variety of sectors, from automotive and aeronautics to design and high-end consumer goods production. However, to maintain its characteristics over time and enhance its aesthetics, particularly its distinctive texture, it is crucial to adopt a suitable coating cycle. Therefore, choosing the right coating products and techniques is key not only to preserving its mechanical and structural properties but also to enhancing the aesthetic appearance of this innovative material,
making it ideal for applications requiring both high performance and elegance. The coating process should begin with a thorough surface preparation phase by sanding the resin matrix in which the carbon fibre is impregnated. Indeed, one of the main challenges in processing carbon fibre is the presence of pores and defects that can compromise the structural integrity and visual appearance of finished parts. After sanding and degreasing the surface, the application cycle continues with the application of a high-fill primer, the 30100 CARBON PRIMER TRX FILLER product. Using this high-thickness primer helps
fill such imperfections, creating a smooth and even surface for improved paint adhesion. In addition, its high transparency ensures that the carbon fibre’s characteristic woven texture remains visible, thus maintaining the desired aesthetics. This product is designed to improve the performance and aesthetics of carbon fibre components, offering significant advantages in terms of surface finish and durability of end products. Thanks to its high fill and transparency properties, it is an effective solution for optimising production and ensuring high-quality results even in the most demanding sectors, such as automotive and product design.
After carefully sanding and degreasing the primer layer, the subsequent step is the application of the clear coat, the 30102 CARBON LOOK FINISH product. This step in the process is crucial to achieving high-quality results. The 30102 finish is specially formulated to offer an exceptional gloss degree that enhances the beauty and complexity of the carbon fibre weave. It is characterised by high weathering resistance, which means end components can maintain their integrity and aesthetics without any degradation due to exposure to natural agents, humidity, temperature variations, and other environmental factors. In addition, its excellent
surface hardness makes it resistant to abrasion, scratches, and wear, thus guaranteeing a long service life and maintaining the beauty of the coated parts over time.
Two pre-pigmented primers developed specifically for application on carbon fibre complete the offer: 30101 Carbon Grey Filler and 30103 Carbon Black Filler. These can be easily over-coated with top coats and matte base coats from the Lechsys and Lechsys Effect systems. Such compatibility enables end users to experiment with a wide range of finishes, from the simplest pastel colours to the most sophisticated effects, always guaranteeing cycles of the highest quality. In fact, Lechler’s objective is to offer solutions that not only protect and improve the mechanical and aesthetic characteristics of carbon fibre but also enable to customise the aesthetics of components, thus meeting the most diverse creative and design requirements.
Lechler has launched a series of high-quality products to offer solutions that not only protect and improve the mechanical and aesthetic characteristics of carbon fibre but also enable to customise the aesthetics of components.
The world of design could be seen as a giant planet orbited by all the industrial sectors that adapt to its needs, follow its trends, and draw inspiration from them. That is because it is characterised by a strong ability to establish and emphasise trends that then gradually touch many branches of the economy, as in a chain reaction. And since every planet needs its own universe, the ipcm® team set out to explore it. The Salone Internazionale del Mobile trade fair fascinated us and made us deeply aware of the leading role that design plays in driving the aesthetic trends of entire sections of the market.
Every year, Milan Design Week attracts numerous visitors eager to discover the latest trends in the world of design and furniture. Aware of the importance of this event, the ipcm®_International Paint&Coating Magazine team immersed themselves in the hectic atmosphere of Salone Internazionale del Mobile and explored the installations and exhibitions of Fuorisalone, aiming to identify the most relevant and interesting trends. Through meetings with designers, companies, and experts, we outlined an overview of the direction contemporary design is taking. In this article, we will summarise the key trends that are inevitably going to affect companies along the entire production chain, from raw materials to manufacturing, up to our sector of interest, that of finishing.
Interior design and construction: sustainability as a common thread Interest in sustainable materials and processes is growing steadily, both for interiors and for buildings and large architectural projects. Designers and architects are increasingly incorporating recycled, biodegradable, and
environmentally friendly materials into their projects. Green building, the branch of architecture that deals with designing and constructing structures limiting environmental damage, mainly uses natural materials such as wood, stone, and clay. These projects promote energy efficiency and human well-being through effective thermal insulation, optimised building orientation to make the most of passive solar energy, and renewable energy technologies such as solar panels and rainwater harvesting systems. A key aspect of this is biodesign, which integrates natural elements into buildings to improve sustainability and indoor air quality, promoting the health and well-being of people. Projects designed with this in mind include vertical gardens, green roofs, phytopurification devices for waste water, and natural ventilation systems.
At Salone Internazionale del Mobile 2024, a dominant trend that caught visitors’ attention was the increasingly sophisticated integration of technology into interior design. Innovation embraces practicality and aesthetics through home automation, augmented reality, and 3D printing coming together to create cutting-edge living experiences. Technology is no longer just an additional feature but an integral part of the living experience, making homes smarter and more functional. At the same time, a subtle revolution is taking place: technology is incorporated more discreetly, gently blending in with its surroundings.
Electronic devices and home automation solutions are no longer isolated objects but smoothly integrated into the design of homes, preserving the elegance and harmony of spaces. This approach reflects the growing interest towards timeless aesthetics, where technology is at the service of comfort and functionality.
This trend is a tangible response to the growing desire to reconnect with nature, even within domestic spaces. Organic shapes and materials evoking natural elements have taken centre stage in the design scene, focusing on the harmonious fusion of built and natural environments. Materials such as wood, stone, terrazzo, and rattan featured prominently in the displayed creations, conveying a feeling of calm and authenticity. The choice of natural materials went hand in hand with the integration of tactile textures, which not only add comfort to the spaces but also help stimulate the senses and enrich the overall aesthetic experience. At the same time, the dominant colour palette included earthy and natural tones, with variations of green, terracotta, and ochre pervading the exhibition spaces and reflecting the human desire to reconnect with nature and create cosy and reassuring atmospheres, thus promoting relaxation and contemplation. Indeed, nature-inspired design represents a major evolution in furniture and architecture, providing reflective spaces where individuals can escape from the hustle
and bustle of modern life and find balance and well-being. As evidence of this trend, most of the Salone Internazionale del Mobile stands paid homage to nature by including walls characterised by vertical greenery, impressive plants, and natural stone.
This edition of Salone Internazionale del Mobile saw the emergence of multi-functional design for both living spaces and objects. This trend reflects the growing awareness of the world’s rapidly evolving needs. Home environments and furniture are no longer conceived as static but rather dynamic and flexible, to adapt to everyday life’s different activities and situations. Multi-functional design solutions ensure versatility and practicality because they maximise the available spaces and meet a broader range of needs without compromising on style or aesthetics. This philosophy is reflected in furniture that can be transformed to perform different functions, such as sofa beds or extendable tables, and in living spaces that can be reorganised to serve various purposes, such as turning a living room into a meeting room or a remote workspace. As well as optimising the use of space, multi-functionality promotes a more sustainable lifestyle by reducing the need to own a wide range of objects and facilitating the transition to a more minimalist and conscious lifestyle. It ultimately entails an important evolution in interior design, which responds to the changing needs and challenges of modern life with creative solutions.
Despite neutral colours being widespread on walls and the main furniture elements, another key trend emerged during Milan Design Week 2024: the use of bold and vibrant hues to infuse interiors with liveliness and personality. Coral orange and burgundy especially stood out as the event’s big stars. Coral orange, a colour often considered difficult to match with others, has been enthusiastically embraced by major Italian brands such as Zanotta, Cassina, Poltrona Frau, and Magis. Sunny and cheerful, it warmed the mood and added a touch of freshness to the exhibition spaces. Two glaring examples of this were the Z24 727 storage unit designed by Muller van Severen for Zanotta and the re-editions in a coral version of Magis’ Puppy chair and Bombo stool by Cini Boeri,
a tribute conceived by Loro Piana in the company’s showroom. The presence of coral orange suggests that this colour may soon find its way into our homes, bringing a sense of warmth and joy capable of transforming the surrounding atmosphere. Burgundy, on the other hand, was used in curtain fabrics and on painted walls, creating enveloping environments full of personality. With its timeless elegance, this deep and refined colour was chosen by several leading brands to lend a sense of welcome and sophistication to spaces. Perfect for those longing for luxurious atmospheres, burgundy manages to combine modernity and tradition. Brands such as Minotti, Gallotti&Radice, LAGO, and Baxter have embraced this shade for their 2024 collections. And, whereas at the trade fair it was mixed with other colours such as orange and green, it was virtually unrivalled at Fuorisalone. Sabato De Sarno, Gucci’s creative director, celebrated the darkest red by calling his selection Rosso Ancora (literally, “red again”) and relaunching five Italian design icons in their burgundy versions, confirming it as the label’s new signature colour.
At Salone Internazionale del Mobile 2024, practical well-being took centre stage in living spaces, reflecting the growing interest in creating environments that promote physical and mental health. This trend translates into carefully conceived design to promote well-being with a focus on natural light, ventilation, and the creation
Eurotherm solves every problem concerning painting processes, creating complete lines for the entire process.
Our structure is organized and flexible and able to satisfy the most demanding requests.
Customers who turn to Eurotherm are customers who, despite knowing the “painting process”, want to improve production by adopting highly customized technical solutions.
Eurotherm S.p.A.
T +39 011 98 23 500 | M info@eurotherm.eu
Eurotherm France S.A.S.
T +33 6 76 72 48 65 | M france@eurotherm.eu
Eurotherm Oberflächentechnik GmbH
T +49 7571 92795 10 | M germany@eurotherm.eu
Eurotherm Benelux Srl
T +33 6 47 44 96 27 | M dekergorlay@eurotherm.eu
of environments that induce calm and concentration. The rooms are devised to maximise natural light, using large windows and lighting systems that replicate sunlight to enhance the mood and boost energy levels. Air quality is optimised through advanced filtration systems and eco-friendly materials that ensure a healthy, pollutant-free indoor environment.
The production process revolution: the importance of quality, from raw materials to end products
Another significant trend concerns the increasing importance placed on the production process from start to finish, with a focus on the quality of raw materials and processing phases. This approach calls for developing optimised and controlled manufacturing processes that meet high
quality, functionality, and aesthetic standards in finished products. The awareness that the beauty and functionality of objects depend directly on the quality of the raw materials used and the processing methods employed is increasingly widespread. That translates into an increased focus on research, the selection of the best raw materials available on the market, and the implementation of advanced and sustainable manufacturing processes – in other words, a commitment to creating high-quality products that not only meet the users’ aesthetic and functional needs but also promote sustainability and the well-being of the environment and people.
As mentioned in the introduction to this article, the design world sets trends and influences many other branches of the economy and industry in a chain reaction. The finishing sector is affected by these trends, too. Sustainability, the focus of this year’s Milan Design Week, is certainly not a new theme for the finishing industry. However, with its emphasis on the environment, this event seems to have been a further push towards responsible practices.
In recent years, ipcm® has presented several articles in its magazines on the development of more sustainable paint products, such as waterbased coatings, which are becoming increasingly popular as they emit less VOCs thus reducing their impact. In addition, companies in the sector are working to minimise waste and paint consumption during the finishing phases by optimising production processes and adopting more sustainable packaging solutions. Technologies that reduce energy consumption in paint production are becoming increasingly popular, using more efficient equipment and energy management practices. Finally, companies are developing solutions for recycling used paint and improving disposal practices. Certifications and regulations such as REACH set standards for the safety of chemicals and promote the responsible use of chemicals. In other words, sustainability in the coating industry requires a holistic approach to the entire life cycle of products, aiming to reduce environmental impact and promote greater social responsibility. At the same time, as mentioned, the trends identified at Salone Internazionale del Mobile 2024 strongly influence this sector, driving its colour and finish choices. Vibrant hues such as coral orange, which dominated the show, and tints that evoke a greater connection with nature, in particular, are inspiring the selection of bolder colours for both indoor and outdoor use.
The partnership with the Kinderdijk World Heritage Foundation involves the use of AkzoNobel’s innovative coatings to preserve the windmills and restore them to their original colours.
The iconic 18th century windmills at Kinderdijk in the Netherlands are being preserved with help from AkzoNobel’s Sikkens brand.
Declared a UNESCO World Heritage Site in 1997, the company has signed a six-year agreement to protect the 19 windmills, which were built around 1740. The partnership – with the Kinderdijk World Heritage Foundation – will involve using AkzoNobel’s technical expertise and innovative coatings to preserve the windmills and restore them to their original colours.
“Kinderdijk is unique and irreplaceable,” explains Peter-Jan van Steenbergen, Director of the Kinderdijk World Heritage Foundation.
“Our UNESCO site sets an example to the world and only the best maintenance plans and products are good enough. We’re therefore extremely pleased to have agreed this partnership with AkzoNobel.” Regarded by many as a national treasure, the Kinderdijk windmills have come to symbolize how the Dutch have mastered the art of smart and sustainable water management over hundreds of years. It’s also a long-established tourist attraction, with more than 350,000 people visiting every year. Located around 15 kilometres east of Rotterdam, most of the 19 windmills are still inhabited, with one family having been resident for ten generations. In many ways, they embody the country’s
centuries-old struggle with water and how the Netherlands has managed to survive below sea level for so long. “We believe our paint expertise and focus on sustainability can make a genuine difference at Kinderdijk,” adds Kees-Jan Starrenburg, Country Director for AkzoNobel Netherlands. “I’m proud to see our products being used at this beautiful UNESCO site, which highlights the importance we attach to safeguarding cultural heritage for future generations.” The six-year agreement builds on a relationship which AkzoNobel first established with the Kinderdijk World Heritage Foundation in 2016. Kinderdijk is also one of several UNESCO World Heritage Sites that feature the company’s coatings. They include La Sagrada Familia in Barcelona, Spain; Westminster Abbey in London, UK; Göbekli Tepe in Türkiye; Malacca in Malaysia; and Ouro Preto in Brazil.
• > 90% WATER RECYCLING
• REDUCTION OF DISPOSAL COSTS
• ZERO LIQUID DISCHARGE
• ZERO EMISSIONS
• EASY MAINTENANCE
• FULLY AUTOMATIC
S. Lanthaler and Z. Mir
Forster Profilsysteme AG – Romanshorn, Switzerland sonja.lanthaler@forstersystems.com - zahid.mir@forstersystems.com
Michael Schreiner
RhySearch Das Forschungs- und Innovationszentrum Rheintal – Buchs, Switzerland michael.schreiner@rhysearch.ch
Powder coating fundamentally depends on the precise polymerisation temperature; therefore, the quality of the coating is primarily dependent on the temperature of the component’s surface on which it is applied. In a study at the Eastern Switzerland University of Applied Sciences (OST), the temperature of the coating process was studied for various geometries. A summary of the investigation is presented in this article.
During the powder coating process, a layer of a desired powder is applied to the metallic part. The metal part is then placed in a preheated oven for a certain period of time to allow the powder to cross-link, which leads to the formation of the desired coating. The degree of cross-linking is decisive for the quality of the coating. The desired degree of cross-linking is achieved when the powder has been exposed to a temperature precisely defined by the powder manufacturer for a certain duration. The target surface temperature in turn is mostly dependent on thickness of the substrate as well as other contributing factors such as its geometry etc. In cases where the desired substrate temperature of the metal part is not achieved, an adequate cross-linking of the powder will not take place. This will create flaws in the coating and degrade the production quality. On the other hand, estimating the degree of cross-linking of the powder on a surface is not an easy process and it is usually determined by various destructive testing methods.
To enhance the quality control process and avoid redundant testing trials on actual parts, a reference body was defined whose thickness can be varied by screwing together a desired number of steel plates (Fig. 1). As such, this specimen’s thermal inertia can be easily adjusted to match that of the metal part in focus, allowing its thickness to be adjusted accordingly. By conducting the powder coating tests on this reference body instead of the actual part, it not only protects the part from potential incorrect coatings but also guides the oven baking process specific to the metal part and a specific coating powder. Consequently, the coating quality on the reference body should mirror that of the actual part, facilitating targeted testing and adjusting oven exposure time for efficient cross-linking of a particular powder
type. However, implementing this strategy is a challenging task. To evaluate if this concept would work or not, a numerical strategy based on Finite Element Method (FEM) analysis was employed to study the heating behaviour of the reference body and aim to correlate the results with various steel components that could be coated under identical conditions as the reference body. This article thus presents the summary of a recently conducted bachelor thesis focusing on this concept [1]. Although a parity between reference body and an actual component of a certain thickness is achieved for simple geometries, it is however not so straightforward for complex geometries.
As depicted in Figure 1 the reference body is designed is such a way so that several thin metal plates (layers) can be conveniently joined together with the help of four screws.
A mounted magnetic attachment which is fixed on one of the external plates is intended to hold a small thin plate having a certain coating powder (not shown in Figure 1). This design stipulates that layers could be quickly added or removed according to the thickness of the steel part being imitated.
As the plates come in contact, a minor thermal resistance layer is formed between the plates due to the inherent slight imperfections and roughness features on the surface of the plates (Fig. 2). This resistance is further amplified because the plates are not perfectly flat, and their surfaces exhibit roughness peaks and oxides due to atmospheric corrosion. As such, these asperities come in contact with each other arising from opposing surfaces but also creating minuscule air gaps as shown in Figure 2.
Therefore, the resulting heat transfer through the reference body occurs both via direct contact between the connecting surfaces (blue arrow) and through these air-filled gaps (red arrow), with the latter offering lower thermal conductivity compared to steel.
The heat transfer coefficient
A conventional powder coating oven is heated with hot air. Hot air is blown into the oven via vents, creating an air flow whose speed can vary depending on the position of air inlet, dimension of the oven and placement of parts in the oven.
This moving air will then heat the components, but the rate at which the components are heated, depends on the heat transfer coefficient. It indicates how much energy is transferred during the heat exchange between the warm air and the surface of the colder components. On the one hand, this heat transfer coefficient depends on the flow velocity and the direction of flow and on the other hand on the dimensions and shape of the component.
Thermal measurements and simulation model
In order to study the thermal dynamics of the reference body, a Finite Element Method (FEM) [3] based simulation model using COMSOL [4] was generated (Fig. 3). Temperature dependent material properties (heat conductivity, specific heat capacity and density) of steel were taken from Eurocode [5].
To be able to model the heat flow from the external environment to the reference body, it is important to know the heat transfer coefficient “h” also known as the film coefficient, which governs the transfer of heat from the warm air to the colder component (reference body in this case).
Additionally, in order to accurately capture the flow of heat between the plates i.e., via metal asperities and discontinuities, it is important to know the effective thermal resistance “R” between the plates. Both these parameters are visualised in Figure 3. As both “h” and “R” were unknown for the test specimen, measurement was carried out in a lab oven (ThermoTEC Weilburg, Germany) at OST to find these parameters and calibrate the model for the reference body.
During the initial tests it was ascertained that it is difficult to find values for “h” and “R” if the specimen is exposed to hot air on all sides. To reduce the complexity of the problem, the reference body was embedded in an insulation mould made of Purenit [6] leaving only one surface exposed to air. As such, the problem was reduced from a 3D to a 1D case (Fig. 3). Thermal sensors Type K were attached to the front (exposed face) and the backside (embedded side) surface (Fig. 4). The reference body was thus placed in an oven in various configurations i.e., with various number of plates at a time and also measured against a solid body (as a reference) with similar thickness to study the effect of contact i.e., thermal resistance “R”. For some measurements, a graphite based high conductivity heat pad (0.2 mm thick) was used between the plates to overcome the effect of any air slits between the plates in case if the plates were not perfectly flat or rather slightly curved. Measurements were conducted for 2, 3 and 5 plates, without heat pads (Fig. 5, left), with heat pads (centre) and solid block in the same thickness (right).
electrostatic systems for liquid painting
electrostatic systems and spraying booths for powder coating
pneumatic systems for high-, medium-, and low-pressure painting
robot and reciprocators IR and UV drying systems
Additionally, Figure 5 shows the configuration in which the samples were embedded in the Purenit [6] insulation and positioned in the lab oven establishing a 1D heat transmission. The measurements were started at 20 °C and the lab oven was heated until all surface sensors (shown in the Figure 5) reached 120 °C. Additionally air temperature in the oven was measured with two additional sensors on the left and right side of the specimen (not visible in Figure 5). Using FEM and Nusselt’s theory, the thermal resistance and heat transfer coefficient parameters were calibrated. This made it possible to calculate the thermal behaviour of the test specimen for the different numbers of plates. Here too, the insulation was used for the calculations, which is why a 1D model was used for the simulation (Fig. 3). A comparison of an experiment done with three plates with a numerical model also containing three plates is shown in Figure 6. A similar agreement was obtained for other thickness configurations of the reference body. Hence, a well calibrated model was established for the reference body which includes appropriate values of “h” and “R” [1].
Numerical comparison of various steel components with the reference body
To effectively compare actual steel components with the reference body, it is necessary to understand the distribution and transport of heat within the steel components when exposed to oven conditions. For this purpose, the heat transfer coefficients for simple geometries such as a flat plate, a round bar and an I-section were determined using Nusselt’s theory. The flow was assumed to be along the length of the steel part (Fig. 7). These values were used to calculate the heat distribution in the steel components with the same boundary conditions as the reference body. Flowing air with a temperature of 200 °C was set as the boundary conditions [1].
As shown in Figure 8, the time taken to reach 180 °C for a steel plate with 8 mm thickness and a reference body with 2 plates (effective thickness 8 mm) is comparable. Similar observation is observed when a 12 mm steel plate is compared with a reference body with 3 plates (effective thickness 12 mm) as well as for a 16 mm steel plate with reference body with 4 plates.
As the thickness of the part increases from 8 mm to 16 mm, the time needed in the oven to reach 180 °C also increases, showing a roughly linear trend. As such a correlation could be established which relates the thickness of the steel plate with the reference body. This result can thus be used in deciding the oven time required for a particular coating with the help of this reference body and would in turn correlate with the thickness of the plate under consideration. The temperature comparison was conducted at the least heated point on the plate which is the centre point (marked with red cross in Figure 7) of the plate’s surface with the surface temperature of the reference body. Such a comparison makes sure that all material points on the steel plate reach at least 180 °C.
In contrast, it was difficult to establish a correlation when curved geometries such as a round bar were compared with the reference body (Fig. 9). The time required to reach 180°C for round steel bars with various diameters such as 150 mm, 200 mm and 250 mm could not be accurately corelated with the reference body with 2, 4 and 5 plates as shown in Figure 9. Other comparison such as with an I-section
with various thickness were also carried out in this study and these calculations can be found in detail in the thesis [1].
Conclusion
In this study, it was intended to design a reference body which could be used for non-destructive quality testing of powder coating process at an industrial scale. The underlying concept aims at establishing a correlation between the wall thickness of various steel components with the reference body upon exposure to hot air in powder coating ovens. As a starting step, multiple measurements were conducted in a lab oven, and the surface temperature of the reference body was recorded in different configurations with respect to its thickness. Based on these results, a 1D FEM model was set up and calibrated for heat transfer coefficient and thermal resistance between the plates of the reference body.
To evaluate the concept, the temperature evolution of three steel components i.e., steel plates of different wall thicknesses, round steel bars with various diameters and an I-section with various web and
9 - Time required to reach 180 °C for the steel round bar in various diameters and the corresponding reference body.
flange thicknesses upon exposure to powder coating oven conditions were compared with suitable configurations of the reference body. For simpler geometries which are flat and without any curved surfaces, a correlation with the reference body could be established. This can directly facilitate the non-destructive quality control in powder coating plants. However, for curved geometries, it was difficult to establish a correlation and additional work is recommended to understand this correlation. Further continuation of this work is recommended wherein a comparison with other geometries especially with those containing hollow cavities should be studied. Furthermore, correlations of the reference body with components made of other materials such as aluminium or stainless steel should be investigated.
The authors express their gratitude to the Eastern Switzerland University of Applied Sciences for granting them access to their lab facilities for their testing and research. The authors also thank GSB International e.V. for their support, providing the reference body and the temperature measuring device. A special thanks goes to Mr. Daniel Scheffler from ENVIRAL Oberflächenveredelung GmbH for his help with the preliminary testing. The authors declare no conflict of interest.
References
[1] S. Lanthaler, Numerische und experimentelle Untersuchung und Analyse des Wärmetransportes beim Pulverbeschichten, Bachelor Thesis, Ostschweizer Fachhochschule, Buchs, 2023.
[2] A. Bejan, A.D. Kraus, Heat transfer handbook, John Wiley & Sons, 2003.
[3] J. Fish, T. Belytschko, A first course in finite elements, Wiley New York, 2007.
[4] Comsol, Multiphysics®, version 6.0, Heat Transfer Module User’s Guide, COMSOL, 2022
[5] European Committee for Standardisation, Eurocode 3: Design of steel structures-part 1-2: General rules-structural fire design, April 2005.
[6] Puren, Downloads - Technische Datenblätter. [Online]. Available: https://www.puren.com/fileadmin/user_upload/2_loesungen/2_6_purenit/03_td_purenit_c_2208_eu-de.pdf (URL)
Pleion, an Italian company specialising in the design, production, and marketing of solar thermal collectors and photovoltaic systems, has been establishing a close partnership with Linea Eco Air that has promoted a continuous exchange of technical and technological expertise, culminating in the supply of a liquid coating plant for the external surfaces of the pipes installed within the company’s collectors.
The thermal collector market is a constantly evolving sector, fuelled by growing environmental awareness and the search for sustainable energy supply solutions. Indeed, thermal collectors play a crucial role in the field of renewable energy, transforming solar energy into heat that can be used for domestic heating and hot water production. These devices’ technological core consists of steel pipes through which mains water flows. However, the aggressive nature of water, which varies depending on the types of water systems, can
significantly affect their performance and longevity. That is why taking effective measures to protect them against corrosion and any issues caused by water pressure is essential. In this context, coating their surfaces emerges as a key element not only to ensure their protection against corrosive agents but also to optimise their energy efficiency.
“Particularly relevant is the use of black top coats that, thanks to their high capacity to absorb sunlight, allow collector pipes to maximise the captured energy and convert it into heat more efficiently.
This is crucial in improving the performance of thermal systems and optimising their overall efficiency,” says engineer Filippo Gangi, the technical office manager of Pleion, an Italian company specialising in the design, construction, and installation of solar thermal collectors and photovoltaic systems. In 2019, it turned to Linea Eco Air (Sona, Verona, Italy) to install a liquid coating system for treating the external surfaces of the pipes lying at the heart of its solar thermal collectors. This investment was a significant step in its growth path, enabling it to consolidate its market leadership position and demonstrating its commitment to providing innovative and reliable solutions.
Growth and innovation in the solar energy sector: Pleion’s story
Founded in 2009 in Cerea (Verona), Pleion aims to revolutionise the solar energy sector in Italy. Initially, its core business was the marketing of high-end solar thermal collectors imported from Switzerland and distributed domestically. However, a sudden, significant change in the exchange rate between the Euro and the Swiss Franc prompted Pleion to reconsider its business strategy. “This unforeseen event called for a decisive breakthrough: starting an in-house production of solar thermal collectors. Although motivated by a circumstance beyond our control, this move turned out to be extremely positive, leading the quality of our
offered products to significantly improve and our company to grow,” says Pleion’s president, Adalberto Scarrone.
In addition to producing and selling solar thermal collectors, which is its core business, Pleion has also been established for years in the photovoltaic panel sector. It offers complete, turnkey installation services for a wide range of sectors, including hotels, hospitals, and other large architectural projects. “Despite being a leader in the solar thermal sector, we are also capable of adapting to new market trends. Such offer diversification has enabled us to meet the needs of an increasingly diverse customer base looking for sustainable and innovative energy solutions, as well as to successfully overcome many challenges due to market changes,” adds Scarrone.
Pleion has maintained steady growth in recent years, even during the COVID-19 pandemic. Thanks to its resilience, it has been maintaining high production levels serving both the domestic and European markets and recorded a significant increase in turnover in 2021 and 2022. “With its dedicated research and development team, Pleion continuously invests in innovative solutions in the field of solar energy, aiming to further expand into international markets, including France, Portugal, Spain, and the Near East by offering competitive, state-of-the-art products,” states the company’s president.
How is a solar thermal collector produced?
Solar thermal systems operate by heating a liquid, either directly domestic water or a “heat transfer” fluid, which gives up its heat through an “exchanger”; this allows heating the water in a house or swimming pool and provides additional heat in the heating circuit.
The production cycle of Pleion’s solar thermal collectors is a complete and meticulous process designed to ensure optimal performance and harmonious aesthetics. It is carried out entirely in-house at one of Pleion’s four factories to ensure high quality.
“We subject sheets made of special steel for naval use to a series of machining operations. They are cut lengthwise and subjected to calendering, a process that uses rollers to
bend them into a tubular shape. Once the required shape has been obtained, the pipes are welded lengthwise to ensure that the structure is tight and solid. Finally, the pipes are closed with special caps patented by Pleion,” explains Gangi.
Each collector consists of 3 to 7 pipes with a length of about 2 metres and a diameter of 150 mm, which are connected and subjected to strict quality controls. After testing, they are enclosed within PVC plastic shells available in different colours, allowing them to be perfectly integrated into the surrounding environment and compliant with any municipal landscape restrictions. “Using a higher number of smaller tubes compared with market standards reduces the height of the collectors and thus their aesthetic impact on the environment.
In addition, our solar thermal collectors are designed with an easily removable frame and versatile design in various colours, such as tile red, moon white, and aluminium, ensuring a harmonious aesthetic integration into any architectural context.”
The liquid coating plant treating the external surfaces of pipes
In 2019, Pleion made an ambitious decision: to raise the level of its production flow by installing a new finishing plant. Previously, it only had a few stand-alone booths, which, although guaranteeing proper coating, were unsuitable to achieve higher quality standards.
“After a careful market analysis, we chose to rely on the know-how of Linea Eco Air. We needed an expert in the coating field, and Linea Eco Air guided us towards the ideal plant solution for our needs.” Pleion thus installed a complete line for liquid coating the external surfaces of the pipes that make up its thermal collectors. “The special naval steel we use in our production has excellent corrosion resistance: coating it optimises our collector pipes’ heat absorption capacity. That is why we chose to coat our components with a thermosetting top coat pigmented in black, a colour known for its ability to absorb light and solar heat,” notes Gangi.
“After manual loading, the coating process begins inside the approximately 10-metrelong cleaning tunnel equipped with three tanks performing phosphodegreasing and two rinses at room temperature, respectively.”
Subsequently, the components pass through a drying oven at 130 °C and then reach the coating booth, equipped with a reciprocator and two guns supplied by Tecnocoating (Vigarano Mainarda, Ferrara, Italy). The booth features sensors to adjust the chain’s position and the guns’ height along the axis and make the application phase as precise as possible. Once the coating has been applied to the first pipe section, a device inside the booth moves the pipe in about 60 seconds to allow the
remaining section to be treated,” explains Gianfranco Soliani, the owner of Linea Eco Air. At the end of the application phase, the parts are first taken to the baking oven at 130 °C, where they dwell for about 25 minutes, and then to a storage buffer at room temperature for about 10 minutes before being unloaded by an operator,” illustrates Gangi. Designed in line with the Industry 4.0 principles, this plant ensures precise control of operating parameters and an overview of the process’ status.
A plant engineering company ready to meet all production needs
The coating system supplied by Linea Eco Air was custom-designed to meet all of Pleion’s requirements, with the necessary flexibility to adapt to any production developments. “
By working closely with Linea Eco Air, we were also able to make some changes after the plant’s start-up,
optimising efficiency and reducing waste. Our innovative sectional pipe coating system is a tangible example of this collaboration,” says Gangi. “Originally, each pipe was coated as it rotated and moved, but we quickly noticed that an excessive amount of paint and filters was wasted. Therefore, we developed a solution that allows coating one section of a pipe, move it in about 60 seconds, and then proceed with coating the next section, thus drastically reducing paint consumption” explains Soliani. “In addition, to optimise energy efficiency and minimise heat loss, we installed insulation panels with rubber fans that reduce the natural circulation of air among the different zones of the plant.” Linea Eco Air’s coating system is user-friendly and easy
to use, thanks to its reliability and low maintenance requirements. Any maintenance work is handled quickly and efficiently, ensuring optimal plant operation.
“Linea Eco Air has proved to be a key partner for the growth of our company: in 2019, it introduced us to the world of industrial coating, enabling us to make a quantum leap from stand-alone static booths to a complete, automated system. In the near future, it will continue to support us in realising a unique coating plant. We are extremely satisfied with this collaboration and the expertise of Linea Eco Air’s team members. They respond promptly, and they are flexible and always ready to help,” concludes Pleion president Scarrone.
Federico Melideo, ipcm®
Powder and liquid coating contractor Painting Srl has recently installed a new manual powder coating plant from Eurotherm and implemented Chemtec’s TORAN 3® pre-treatment technology to improve its process sustainability and operational flexibility.
Technological innovation determines the production and market dynamics of many industries, including the coating one. With the introduction of new plants and technologies, many companies are currently redefining their workflows to improve the quality of their products and the sustainability of their processes. That is also the case with Painting Srl (Ariccia, Rome, Italy), a benchmark industrial powder and liquid coating contractor in the Lazio region.
Luca Flore, at the helm of the company, recounts its origins: “Our roots lie in the experience of Trinca Vittorio, a long-standing coating contractor since 1952, specialising in powder coating since the 1980s, which distinguished itself as the first company in Lazio and the second in Italy to pioneer this field.”
Painting Srl was founded in 2012, and maintained its headquarters in Frascati (Rome) until 2023, when it moved to Ariccia. “At the same time, we replaced our old powder coating line with a new, state-of-the-art plant,” adds Flore.
Today, Painting’s core businesses are the powder coating of metal and aluminium products intended mainly for the construction industry and the liquid coating of components for the medical and military sectors. “Relocating from Frascati to Ariccia also marked a critical change in our target customer base, which now operates above all in the construction industry. This strategic change has led us to specialise in the coating of metal architectural components such as shutters and grilles, although still maintaining a presence in the industrial sector on a smaller scale,” says Flore. “I believe that maintaining an all-Italian industrial-oriented
structure for treating components subject to strong international competition is economically unsustainable. Competition is no longer limited to Lazio alone but extends nationally and internationally. Many industrial parts are produced and painted in Bulgaria, Poland, Croatia, Turkey or China.” Painting’s response was to adopt a more targeted business strategy focused on quality and sustainability, installing a new powder coating plant and implementing Chemtec’s TORAN 3® pre-treatment technology. “Our ultimate goal is to ensure flexibility, service customisation, and timely deliveries,” indicates Flore.
Technical characteristics of TORAN 3®
“TORAN 3® is an innovative pre-treatment technology suitable for all types of metal, including sandblasted substrates. It is a VOC-free, onestage, cold technology requiring no water, heating, or rinsing, reusable, and entailing no disposal operation,” explains Carlo Guidetti, the CEO & co-founder of Chemtec Srl. “Adding some fresh product is enough to restore the bath. With the TORAN 3® process, the workpiece is cleaned for one to three minutes, followed by draining and drying in an oven. That forms an organic coating on the treated surface with a thickness of around 300-400 nanometres, which improves paint adhesion and provides corrosion resistance. The oils removed from the part are absorbed by the polymer and become an integral part of the passivation film, whereas solid impurities are filtered out by a 50-micron filter so that the bath never has to be replaced in its entirety.”
The benefits of the new pre-treatment process
“We opted for implementing the TORAN 3® pre-treatment system because of its sustainability. It does not generate sludge, thus eliminating waste disposal costs and keeping the tank clean over the years. It requires very little maintenance, also eliminating the need to clean the spray nozzles. With TORAN 3®, in compliance with provincial regulations, there is no need for air emission analyses, as it does not require heating and has no critical emission points. Finally, being based on organic high-boiling fluids, it has a low environmental impact,” notes Flore. “In terms of performance, adopting the TORAN 3® technology has significantly improved the quality of our pretreatment and powder coating phases. Compared with the three-stage phosphodegreasing operation we used to perform, it also provides superior paint adhesion, as evidenced by the salt spray test results achieved, equal to 1,000 hours.”
“It is important to emphasise that TORAN 3® is a chemical product with a neutral pH value of 7, which makes it suitable for use in galvanised sheet metal plants. This also leads to considerable savings in terms of machine design, as pregalvanised sheet metal can be used instead of stainless steel, thus reducing the investment cost for a pre-treatment tunnel by 50%,” adds Guidetti.
new manual powder coating plant 4.0
Painting’s new powder coating plant, installed in July 2023 and supplied by Eurotherm (Volpiano, Turin, Italy), consists of as follows:
an automatic Ecojet pre-treatment tunnel using TORAN 3®;
a powder coating booth;
a drying/curing oven with an air steam burner;
a central overhead conveyor with a manual transfer unit with a capacity of 1500 kg, featuring load bars with a maximum capacity of 1000 kg and 6 metres in length;
a lift station for loading and unloading the workpieces hung onto the load bars; a storage buffer;
Industry 4.0-oriented connection solutions with a
touch-screen PLC, allowing for remote assistance.
“We installed a flexible structure capable of coating workpieces up to a maximum size of 6 x 3 m and a maximum weight of 1000 kg. The plant covers an area of only 250 m², and is equipped with a central overhead conveyor that moves the parts among the storage buffer, the lift station, the pre-treatment tunnel, the powder coating booth, and the curing oven,” illustrates Flore.
“The storage buffer plays a crucial role in this Cartesiantype system. For example, it allows pre-treated parts to be stored before being coated in the booth, should this be already in use,” notes Davide Quartana, Project Manager at Eurotherm SpA. “The drying/curing oven operates at temperatures between 180 and 200 °C and is located in front of the booth to enable the overhead conveyor to easily move the coated parts from the latter to the former, which performs two functions: drying the TORAN 3® product and curing the powder. Its temperature is adjusted via software based on pre-set automatic parameters. Alternatively, the operator can
select the option of drying at 120 °C or curing at 180 °C. In addition, a given temperature can be selected according to customer specifications, also considering the powder product chosen and the thickness of the workpiece.”
“Recipes are created by indicating the required times and temperatures. The coating manager is responsible for setting the operating parameters, the access to which is restricted. This innovative system thus enables the operators to start the machine and select the right production cycle with the advantage that recipes, temperatures, and operating times are loaded automatically,” adds Gianpaolo Candelero from the technical office of Eurotherm SpA.
Installing the new powder coating plant and implementing TORAN 3® pre-treatment technology resulted in a significant step forward in Painting’s journey towards improving the quality of its products. These investments have enabled it to maintain a competitive position in both the national and international markets by offering increasingly customised and high-quality services. Additionally, the new pretreatment technology has not only brought benefits in terms of performance and environmental sustainability but has also optimised the company’s production processes, reducing its operating costs and improving the overall efficiency of its paint shop.
“I must say that we are extremely satisfied with the results obtained. Despite the small size of this coating plant, we have achieved exceptional levels of productivity, managing to coat up to 56 load bars per day, each with an average coatable area of 12 m², totalling over 600 m2 of coated surface. Moreover, the new oven with an air stream burner has provided us with significant cost savings, reducing LPG consumption by 50% compared with the previous static oven,” states Painting’s owner Luca Flore.
Chemtec CEO Carlo Guidetti, finally, concludes by pointing out that “this plant’s flexibility is further increased by the fact that TORAN 3® is a ready-to-use product that does not require pre-heating, a feature that has also helped significantly reduce fixed costs.”
The dry booth for liquid paint application.
The drying/curing oven.
From left to right: Carlo Guidetti from Chemtec, Luca Flore and Massimiliano Trinca from Painting Srl, and Beatrice Turri from Chemtec.
via E De Nicola, 18 - I-20090 Cesano Boscone (MI) Italy - tel +39 0255210608 www.ravarinicastoldi.it - dive@ravarinicastoldi.it
Focusing on its products’ safety and performance and offering tailor-made solutions for every need has enabled SpeXparts to become a leader in the production of hoses and fittings for various sectors, including industrial painting.
The focus on high product quality and the constant striving for ever-higher standards are fundamental pillars for the success of any company. SpeXparts stands as an excellent example of this: specialising in manufacturing and marketing hoses and fittings for a wide range of sectors, including the painting industry, it faces significant challenges on a daily basis to guarantee maximum product performance and safety. In the industrial landscape, the latter is indeed a top priority: SpeXparts fully understands that and is committed to ensuring that its offer always reaches the highest possible level of safety, with a view to safeguarding not only the well-being of operators but also the continuity of industrial activities. At the same time, in addition to putting safety first, it also constantly invests in modern production technologies and carefully selects raw materials to provide the market with reliable and efficient products.
SpeXparts: a reliable and flexible partner for the painting industry
SpeXparts was founded in 2018 in Trezzano sul Naviglio (Milan, Italy) and specialises in producing and marketing metal and textile braided hoses, high and low-pressure thermoplastic hoses, and fittings for various industries, from braking systems for cars, bicycles, and scooters to hydraulics, up to the painting sector. Its product range intended for the painting industry includes as follows:
hoses for painting systems intended for the automotive and motor vehicle sectors;
hoses for industrial painting plants;
hoses for professional diaphragm pumps;
professional high and low-pressure airless hoses for Airmix systems;
hoses for professional piston pumps.
“SpeXparts is a unique company in the Italian manufacturing landscape, as it is an all-female business handling processes commonly associated with an all-male world. Over the years, we have gained specific expertise in the production of high and low-pressure hoses, fittings, and flexible hoses with a particular focus on the industrial painting sector, which we supply with both standard and special, tailor-made products meeting any need and requirement,” states Gabriella Barone, the company’s owner and sales and marketing manager. “In addition, our R&D activities enable us to consistently improve the quality of all the services and products we offer, made with the meticulous craftsmanship-oriented approach that characterises the Italian industrial tradition.”
Tailor-made solutions to meet the most diverse needs
“Relying on a small company like ours means receiving a very adaptable service, as we can quickly meet individual requirements with customised products,” says Barone. SpeXparts’ strengths are precisely its attention to detail and its customised approach. In addition to producing a wide range of painting hoses, it has a warehouse storing hoses of various diameters ready for delivery to meet standard market demands with 100-m rolls or coils. It also has a facility where it can connect hoses to customer orders and manufacture customised solutions in terms of materials, internal and/or external diameter, length, and operating temperature and pressure according to specific requirements. Finally, SpeXparts can personalise its products with its customers’ names, colours, and lettering (in addition to the texts required by law, indicating each hose’s diameter, working pressure, and burst pressure) to support them in their branding activities as well by providing clear and precise identification.
“We analyse the industry’s daily problems to create innovative products designed specifically for each customer need and offer special, customised solutions. Our team, made up of professionals with specific skills and experience also gained in international companies, supports our customers in choosing the most suitable elements to create painting hoses that fully meet their requirements
through a targeted, high-quality consultancy service, capable of clarifying any doubts and overcoming any technical issues,” emphasises Barone. “For example, one of our latest projects concerned the production of a hose with a special coating, which we made by creating a polymer mix that we then tested in-house, thus obtaining an extrusion granule specifically for hose coating. It allows the hoses used in painting robots and systems to slide without creating friction even in the presence of multiple hoses running parallel to each other and inserted in the chains and, therefore, also without causing abrasion and without generating any dust that could be deposited on the painted parts.”
In-house production to constantly monitor quality
Another key to SpeXparts’ success lies in the choice to manufacture its hoses entirely in-house and in the special attention paid to raw materials, such as the steel, Kevlar, and polyester yarns used to make braided hoses; the extruded polymers for hose sub-layers or cores, which are generally of polyamide; and the polymers used for the hoses’ coatings, which are made of abrasion-resistant polyurethane and/or innovative polymers produced based on special technical specifications. Extruded materials with special polymers such as PTFE are purchased from certified companies that provide the relevant declarations of conformity and quality, which SpeXparts always requires from its suppliers. That ensures total and constant control over the quality of the materials employed, guaranteeing superior and long-lasting performance. However, SpeXparts’ commitment to quality extends well beyond materials. Each stage of its production process is subject to rigorous quality controls, including chemical and physical analyses, laboratory tests on samples, and mechanical bench tests to check the pressure and bursting performance of the hoses. In addition, connected hoses are subjected to burst tests at specific pressures to assess their strength, inspections, leakage tests at working pressures, and go/no-go gauge tests to check the correct pressing of the fittings and the suitability of flushing and cleaning operations.
“These tests are conducted using sophisticated
instruments and following strict company procedures, certified according to ISO 9001. The same supervision process is implemented in all our departments, with technicians verifying compliance with each batch’s technical specifications. All of our hoses carry information related to their production batch stamped on their sub-layers and coatings, and those assembled by us also carry information on their batch and production week stamped on their bushings. In the world of industrial painting, the quality of materials and the safety of application equipment components are often underestimated, but they are actually of paramount importance. SpeXparts has earned an unrivalled reputation precisely because of its attention to detail and commitment to achieving and exceeding extremely high quality standards. The main properties of our hoses for paint application pumps and their coatings are reliability, flexibility, versatility, durability, and safety,” indicates Gabriella Barone.
As well as careful design aimed at achieving customised, highperformance solutions, industrial painting plants require the use of hoses with specific technical and operational characteristics but also excellent strength, flexibility, and above all safety properties. All products manufactured by SpeXparts are therefore built in compliance with the ISO 8028 standard. “For hoses intended for painting pumps, the required safety factor (operating pressure to burst pressure ratio) is 1:4, especially for equipment working at 300-500BAR operating pressures. Actually, this parameter is not always met, as we often find hoses with a safety factor of 1:2 or 1:3 available on the market, aimed at raising operating pressures, which customers and users are most interested in. Yet, this significantly reduces the safety of the products. That is why SpeXparts’ hoses are manufactured with a safety factor of 1:4 (e.g. with an operating pressure of 500BAR, the burst value is 2,000BAR) to protect operators and prevent dangerous accidents. In other words, our hoses are products of the highest quality and reliability, ideal for all companies operating in the industrial painting sector,” concludes Barone.
Connected hoses produced by SpeXparts and installed on painting equipment.
SpeXparts’ stand at PaintExpo, the leading trade fair for industrial paint and coating technologies.paint and coating technologies.
EcoSupply P Core is a new paint supply system developed by Dürr for industrial applications.
The new EcoSupply P Core is a modular paint supply system based on pigging technology. This paint supply method has already proved beneficial in the automotive painting world, but Dürr has gone one step further and enhanced it for use in other industries for the first time.
The EcoSupply P Core is now adaptable wherever different paint colours are applied in small quantities, such as in the construction, woodworking or automotive supplier industries. This system efficiently recovers unused paint, minimizing rinsing agent consumption and speeding up colour changes. The desire for a comprehensive colour palette extends beyond the automotive industry. Customers use their colour preferences as unique identifiers in other industries, whereas companies use distinctive
colours as a unique selling point for themselves and their products.
Manufacturers from the construction and plastic industries, for example, require a multitude of available shades to cater to their customers’ needs. However, each colour change in the supply line results in paint and rinsing agent waste during the painting process.
This can involve disproportionately high costs, particularly with very small quantities. This is because current paint supply systems clean the hoses using solvent and compressed air to remove all paint and rinsing residues left behind before preparation of the next colour run can begin. This process is laborious and time-consuming, with longer and thicker hoses resulting in higher paint losses.
For pigging technology, Dürr uses a fitting body tailored to the internal diameter of the hoses – the so-called pig – to make the process more efficient and reduce paint and rinsing agent consumption. The paint, flowing through the pigging hose, pushes the pig from the source to the target module. This process removes any rinsing agent residue in the hose. Distributor stations, with the option of integrating up to four into one pigging line, provide the connection to the application technology. After the paint application, compressed air blows the pig back towards the source module. In the process, the paint left in the hose is transported back into the paint container. Rinsing agent then flows through the pigging hose towards the destination module. After cleaning, the process repeats.
The EcoSupply P Core comes in single-pass and circulating versions and is suitable for applying both water and solvent-based paints. In both instances, reduced effort makes for faster colour changes. Additionally, the modular design simplifies maintenance, allowing flexible configuration of individual components to adapt to user requirements and integrate into existing systems. Thus, the EcoSupply P Core can also integrate with other Dürr systems, such as the EcoSupply2 Core paint supply station.
Starter kit with everything you need Dürr’s starter kit contains all important components, including a source and destination module, a distributor station for connecting to the application technology, hoses (which come in lengths of up to 100 meters), and the pig itself. The starter kit also includes sensors for monitoring the pig position, maintenance and commissioning tools, and EcoDocu-technical documentation in digital format, complete with system examples.
The EcoSupply P Core offers the manufacturing sector a cost-effective, easy-to-use paint supply solution for smaller quantities and applications in the low-pressure range. The new development is the culmination of Dürr’s 25 years of experience with the pigging technology featured in the EcoSupply P. Globally recognized, this tried-and-tested paint supply system with pigging technology has established its effectiveness in automotive painting.
Franchi&Kim has launched Ikaro, the new integrated colourimetry system consisting of a mobile app for formulation, a spectrophotometer, and two software packages, one for time-saving and travel-free order management and one for quick and easy colour tone formulation and correction.
Innovation has always driven progress in the vast panorama of colourimetry-related technology. Franchi&Kim is proud to present an epoch-making breakthrough in this field: Ikaro1, the first portable sphere spectrophotometer controlled and managed from a smartphone via a formulation app. A combination of scientific precision and modern practicality destined to radically transform the way all colour operators work.
The Ikaro project goes back a long way: the idea to simplify colour detection and, above all, formulation management was conceived in 2019. Over the years, our colourimetry and tintometry department has dedicated its time to finding the ideal device for the best performance, while our software development team realised the dream through its vast colourimetric and mathematical know-how, encapsulating the necessary functions into quick and easy formulation steps.
Our company’s vision for this innovation is based on three objectives:
facilitating and speeding up colour detection with a mobile app;
performing remote data collection and colour formulation by immediately sending the production order to a retailer;
broadening the range of users of colourimetric tools, including non-specialised operators and businesses that have never considered investing in spectrophotometers and related software for economic reasons. With Ikaro, all users and retailers can replace multi-angle colourimeters and spectrophotometers with devices capable of formulating products from scratch, thus avoiding needing to derive the closest hue to the detected one from the stored ones.
Specifically, Ikaro is an integrated colourimetry ecosystem consisting of a mobile formulation app, a portable spectrophotometer, and optional, easy-to-use order and formulation management software.
1 www.ikaro-spectro.com
Combining these elements enables to formulate and correct pastel tints quickly and easily, as well as manage their related production orders. Indeed, the device is connected to a centralised database on an ultra-performing cloud server, which processes the various requests and instantly delivers formulations and recipes based on pre-set parameters.
Ikaro is a revolutionary application that uses a spectrophotometer with diffuse d/8° sphere geometry and LED technology. It is not a multi-angle handheld device. It is a newgeneration ergonomic instrument capable of ensuring high-quality spectral distribution, high measurement speed, and excellent colour detection accuracy through the 31 points derived from the reflectance curve between 400 and 700 nm.The new frontier of colourimetry is reached thanks to complete, remote colour management through the Order Sender module: from formulation to correction, up to the automatic sending of orders directly from the mobile app to the desktop order management software package. The app enables to define the formulation parameters, consult the archive of measurements, formulations, and executed orders, and use the most common colour charts on the market as starting points. It is also possible to integrate the Ikaro Formula tool whenever formulation and quality control tasks are required relating to ingredient priorities, colour combinations, and other aspects concerning colour coordinates and tolerance values.
With three simple steps and a few clicks, you can detect, formulate, and order a colour wherever you are.
After connecting the spectrophotometer to the smartphone app via Bluetooth, it is possible to detect the sample to be reproduced or choose a tint from a colour chart. The app handles all colour detection and product selection operations and sends the data to the server.
The cloud server performs the necessary calculations on the pre-set databases and generates the formulation for the desired colour and the required quantity. Any correction of the generated formulation can also be made from the app.
Once the formulation has been defined, this is sent to the desktop order management software package with the quantity needed per product so the required order can be sent to production.
Ikaro’s advantages
Some of the benefits of this new system can be summarised as follows:
time savings: it is not necessary to visit a customer’s premises to collect samples and to one’s own tinting laboratory to deliver colour references;
autonomy: end-users are independent of their retailers in detecting colours and sharing formulations and orders;
ease of use: even non-specialised operators or those not used to utilising colourimetric instruments can detect a tint with just a few clicks, thanks to the innovative app-based management system;
sustainability: the cost is lower than that of conventional colourimetric instruments while maintaining the high technical level of the most expensive tools on the market.
In other words, Ikaro brings a new, revolutionary experience for both retailers and end users to elevate their technical expertise and profession. This project is aimed at all distributors that wish to provide their customers (coaters, body shops, manufacturing companies in different product sectors) with a loyalty-based service while managing colour remotely and obtaining orders without the physical availability of samples in their point-of-sale’s tintometric laboratory.
With its cutting-edge technology, ease of use, and ability to significantly improve the colour formulation process, Ikaro is set to become the new colourimetry standard in the paint market. Its outstanding power and advanced functionality promise to transform how colours are created and managed, enabling users to achieve excellent results faster, more efficiently, and more accurately than ever before.
At your fingertips and within everyone’s reach.
INNOVATION
PERFORMANCE
NANO TECHNOLOGY
R&D
ESG
TECHNICAL ASSISTANCE
Rossi Spa has installed a new liquid coating system for its gearboxes, gearmotors, and electric motors and has chosen IMEL as the right partner for its design and implementation.
Belonging to the HABASIT GROUP, Rossi Spa has been a world leader in the production of gearboxes, gearmotors, and electric motors used in even the most demanding applications for over seventy years. Recently, it has equipped one of its production sites with a new state-of-the-art coating line supplied by IMEL Spa (Codroipo, Udine, Italy), specialising in the design and installation of coating systems since 1964. This further strengthens IMEL’s presence in the Italian market and consolidates its position as a high-level supplier in the industrial coating sector.
The line was started up successfully and perfectly on time through meticulous engineering and activity coordination. It is characterised by flexible coating cycles and accurate climate control of the process chambers. Specifically, it can apply paint products in one or two coats, either manually or automatically and with or without an intermediate drying stage. In addition, it was conceived to be highly compact and save space through careful design, a characteristic that has always distinguished IMEL’s systems. Another strength of this plant is its ecological aspect, as it is powered by LPG and self-produced electricity and uses only water-based paints.
This collaboration with such a prestigious customer has also enabled IMEL to further prove its skills in building reliable plants for the high-end industry sector.
For further information: www.imelspa.com
PPG has appointed Lyndee Brassieur as Vice-President EHS to help the company with its focus on advancing employee safety, incident prevention and regulatory compliance.
The international paints and coatings manufacturer PPG has recently announced that Lyndee Brassieur has been named Vice-President for environment, health and safety (EHS): She will focus on advancing employee safety, incident prevention and regulatory compliance.
Lyndee Brassieur played a key role in defining and overseeing operational excellence and manufacturing strategies at PPG’s global SCM manufacturing facilities. In her 25 years of industrial experience, she has held various roles of increasing responsibility for production and continuous improvement as well as environmental, health and safety management. Additionally, she holds a bachelor’s degree in chemical engineering with a concentration in environmental sciences from McNeese State University in Lake Charles (USA). “Congratulations to Lyndee on her appointment to this key leadership role at PPG. Our most important core value is the health, safety and well-being of our employees, customers and communities. I am confident that under Lyndee’s leadership, our teams will be able to further demonstrate our commitment to the environment, and the health and safety of our people,” has stated Ram Vadlamannati, senior Vice-President operations at PPG.
For further information: www.ppg.com
CMA Robotics, one of the leading manufacturers of coating robots, celebrated its 30th anniversary.
Ever since the launch of its first robot in Italy’s Friuli Venezia Giulia region in 1994, CMA has been developing a well-established global presence in the most diverse fields of application. It offers complete solutions, courses, and a laboratory carrying out tests and simulation trials in total safety, which allows verifying the results of a robotic application process on each customer’s components.
CMA Robotics is recognised as one of the most technologically advanced companies in the world of robotic coating, capable of guaranteeing high quality with up-to-date certifications and easy-to-use equipment. It is now part of a large group of companies focused on robotics, the Efort Group. For this Italian company, having an international team means sharing research, development, projects, and innovation to create new technological, commercial, and financial synergies that can meet multiple customer needs quickly and reliably.
“Gathering here, once again, to celebrate our achievements and cast a glance into our future honours us and fills us with joy,” said Sergio Della Mea, one of the founding members of CMA Robotics during the 30th anniversary celebration. “Every single employee, customer, supplier, and collaborator we have met over the years has given CMA the
opportunity to grow and achieve the results we can now see and share,” proudly added the other founding member, Marco Zanor. The floor then passed to the president of the Efort Group, You Wei, who recalled his first meeting with CMA in China and the beginning of a fruitful collaboration. The event was also attended by numerous representatives of the local authorities, including the Councillor for Productive Activities and Tourism Sergio Emidio Bini, the General Director of Confindustria Michele Nencioni, and Beppino Govetto, the Mayor of Pavia Di Udine, where CMA Robotics’ headquarters is located.
“CMA has a vocation for innovation, which translates into a mission that enables us to be still here after 30 years and that will enable us to be at the top of our industry in the coming years as well,” concluded Marco Zanor. Toasts, music, and smiles then filled this celebration, held at the company’s recently renovated premises together with employees, customers, suppliers, and collaborators, in a unique setting encompassing its history and future of great successes.
For further information: www.cmarobotics.com
The BYK-Gardner seminar will address the latest technological innovations in quality control instruments.
BYK-Gardner has announced a one-day free seminar that will highlight the latest technological innovations in quality control instruments. The event will focus on:
Ultrasonic multi-layer thickness gauge;
Surface texture;
Visual and instrumental color evaluation;
Appearance control;
New smart-chart software functions;
News on physical properties testing equipment.
The seminar – which includes lunch and coffee break – will take place on Thursday 4th July 2024 at the CDH Hotel Parma & Congressi, from 9:30 am to 4:00 pm. You can register until June 14th by sending an e-mail to sara.malanchini@altana.com or by completing the specific form at this page: https://seu1.cleverreach.com/f/163470-237345/
The EcoInCure oven concept from Dürr was recognised with the PACE award for its improved curing performances on car bodies.
The German company Dürr has proudly announced that it has won the PACE Award for the time year in a row, this time thanks to its EcoInCure oven concept, which addresses critical customer requirements such as topcoat paint quality and improved overall curing performance for car bodies.
The 29th annual PACE Awards competition, presented by Automotive News, was open to suppliers that contribute products, processes, materials or services directly to the manufacture of cars or trucks. The winners have been selected by an independent review board.
The EcoInCure oven has been specifically developed to cure complex car bodies with superior paint quality faster and more efficiently than conventional solutions, in order to exceed the evolving needs of drying both traditional internal combustion engine vehicles and electric vehicles.
“We are very excited that our technology has been recognised as a cutting-edge innovation that shapes the automotive industry. The EcoInCure from Dürr stands for a new generation of car body curing. It does not only ensure the best surface quality, but is also by far the most sustainable oven system on the market thanks to its design and potential use of renewable electricity,” has declared Mark Murray, the director of sales and marketing for Dürr in North America.
For further information: www.durr.com
Lavaggio Industriale
Lavaggio di precisione
Sgrassanti interoperazionali
Miscele di tensioattivi
Protezione temporanea
Galvanica Funzionale
Zinco e leghe di zinco
Passivanti e Sigillanti
Rivestimenti resistenti all'usura
Pretrattamento
SurTec Italia Sas di Externa Holding Srl
Via Boito, 251 Tel.: +39 059 8579901
41019 Soliera (MO) E-Mail: info-it@surtec.com Italia Web:www.SurTec.com
Pretrattamento metalli alla verniciatura
Processi di conversione esenti
Cromo e Fosfati
Fosfatanti a bassa temperatura
Passivanti per acciaio zincato a caldo
Passivazione conduttiva su
Alluminio TCP
Galvanica Decorativa
Rame, Nichel e Cromo
Deposizione su plastica (POP)
Stagno e leghe di Stagno
Pretrattamento
Paul Cardon
Mouvex® PSG - Terrace (IL), USA paul.cardon@psgdover.com
Low-power consumption pumps, like the Mouvex G-FLO Series eccentric disc pump, paired with design modifications help operators obtain noticeable energy savings in paint and coatings operations.
The cost of energy has dramatically increased in recent years, a break from its traditional patterns over the past few decades. The rapid shift in these costs caused all industries to take measures aimed at energy savings wherever possible. These new behaviours are
essential as these costs are unlikely to change in the foreseeable future. Among all items in an industrial production process, pumping systems can be among the most “power hungry.” According to the Hydraulic Institute (USA), pumping systems account for nearly 20% of the world’s
electrical energy demand. In these times of pricey and scarce energy, it is paramount to find different ways to reduce their power consumption. Any industry that uses pumps can find energy savings by evaluating their equipment. This holds especially true for a pump-heavy industry: paint and coatings. Fundamentally consisting of pigments suspended in a liquid medium, paint and coatings have evolved from primitive substances like charcoal and berry juice to sophisticated compounds manufactured through high-tech processes. Over the past 25 years, the industry has seen a transformation driven by new coating technologies. These technologies replace traditional solvent-based formulations with eco-friendly alternatives such as waterbased paints, low-VOC coatings and powder coatings. Innovations like nanotechnology and smart coatings further enhance performance and aesthetics, shaping a diverse and vital global market. Today, paint and coatings play pivotal roles in various applications, including traffic markings, house coatings, automobile exteriors, and packaging materials. This evolution underscores a stark departure from primitive origins, demonstrating how technological advancements have propelled the industry into a realm where environmental consciousness,
durability, and aesthetics converge for enhanced product offerings and widespread utility.
This whitepaper will examine the costs associated with a common pump technology – positive displacement (PD) – used in this industry and how one shines above the others as the most economical and energy efficient.
The typical cost breakdown for a positive displacement pump over its lifetime is showed in Figure 1
The initial costs (blue) are only paid once during the installation phase. These are minor costs associated with a pump’s total cost of ownership. The major costs are those shown in different shades of brown, which are paid during the life of the installation. Energy represents almost half of the total cost of ownership among total expenditures. Rising energy prices will cause that percentage to increase, impacting the overall cost of the pump’s total cost of ownership.
There are mainly two areas to focus on to reduce energy consumption: the pump and the installation.
Focusing on these two areas, either when designing a new installation or improving an existing one, can, in some extreme cases, lead to energy consumption divided by three.
Several positive displacement pumping technologies are available on the market. However, they are far from equal in terms of energy consumption. In both cases above and in most others, the same pumping technology appears to be the most economical: The Mouvex® G-FLO Series seal-less eccentric disc pump1
Why is this pumping technology considered energy efficient?
Some pumping technologies are based on a two-shaft design with timing gears. Gears and more bearings generate extra friction on the power end (with parts rotating in lubricating oil) and the wet end (parts rotating in pumped product).
The Mouvex G-FLO Series has only one shaft, which rotates in clean oil inside double or triple bellows, isolating it from the pumped product. This minimizes friction, lessening the impact on its energy consumption.
The Mouvex G-FLO Series eccentric disc technology is based on two pumping parts: a static cylinder and a moving disc, which does not rotate but rather follows a circular translation around the cylinder. Eccentric disc pumps consist of a cylinder and pumping element mounted on an eccentric shaft. As the eccentric shaft is rotated, the pumping element forms chambers within the cylinder, which increase in size at the intake port, drawing fluid into the pumping chamber. The fluid is transported to the discharge port where the pumping chamber size is decreased. This action squeezes the fluid out
1 https://www.psgdover.com/mouvex/products/eccentric-disc-pumps/g-flo-series
into the discharge piping (Fig. 2). The differential linear speed between the cylinder and disc is low and equal at every point of the disc. This “slow motion” requires less energy than pumps with rotating parts, which function with high peripheric speed.
Some pumping technologies are based on a shaft held by bushings in the pumping chamber. Though manufactured in materials offering a low friction coefficient, these parts are still in a friction zone. As mentioned earlier, in the Mouvex G-FLO, the rotating shaft is not in contact with the pumped product but instead protected by multiple-layer stainless steel bellows. The only parts in contact with the product are the casing, bellows and the disc/cylinder set.
A mechanical seal is based on the friction between two rotating faces. These faces show a low friction coefficient, but extra energy is needed to overcome this, especially in a multiple seal arrangement (up to four mechanical seals on pumps with two shafts). Additionally, a double mechanical seal requires a fluid barrier that generates energy consumption: fluid circulation, control, etc.
Seal-less solutions, such as magnetic drive, which do not have friction parts, still require more power because of the strong magnetic fields needed for torque transmission. The Mouvex G-FLO Pump has no mechanical seal or magnets. Shaft tightness is provided by the bellows, linked to the pump casing on one side and to the disc on the other side. This solution does not generate any extra friction while providing total containment and lessening the need for frequent maintenance.
In many cases, Mouvex G-FLO Series pumps maintain lower shaft rotation speed for equal flow rate and differential pressure. In most applications, a Mouvex pump will have a rotation speed between one and two times lower than other technologies. A lower speed requires less energy and improves the durability of moving parts, such as bearings.
Even with a lower speed, the Mouvex G-FLO Series Pump can reach a flow rate of up to 70 m3/h (308.2 GPM) and 10 bar (145 psi). On mid/lower viscosities, and for identical flow rate and pressure conditions, deltas up to 40% can be observed between different pumping technologies. With higher viscosities, discrepancies can sometime be even more spectacular with up to 90% gaps (Figs. 3 and 4).
with a complete service that includes system design manufacturing, installation, technical support and chemicals
SPRAY BOOTHS WATER SLUDGE REMOVAL
RESIN DEMINERALIZATION SYSTEMS
REMEDIATION OF CONTAMINATED SITES
BIOLOGICAL SYSTEMS
BATCH TREATMENTS
PHYSICAL-CHEMICAL SYSTEMS
ADSORPTION FILTRATION
REVERSE OSMOSIS
MEMBRANE SYSTEMS
EVAPORATORS
BIOGAS BIOMASS SYSTEMS
OIL SEPARATORS
DESANDERS
DESALINATION SYSTEMS
PYROCHAR
OTHER SYSTEMS
CHEMICALS
Paint and coatings manufacturers must select pump technology that ensures product quality and energy efficiency. Some pumps can achieve product quality but falter with energy efficiency and vice versa.
Eccentric disc pumps, such as the Mouvex G-FLO, offer performance attributes that ensure the best quality prduct while keeping energy costs down.
Unlike traditional pumps reliant on centrifugal force, eccentric disc pumps precisely displace a fixed amount of fluid per rotation, maintaining consistent flow rates regardless of pressure or viscosity fluctuations.
This design ensures reliable performance with challenging fluids and minimizes energy consumption by reducing internal friction and turbulence, yielding noticeable energy savings for industrial production processes.
Many operators will look to save on costs by selecting smaller-diameter piping when possible. Smaller diameter piping is cheaper and does not need as much support as larger variants.
However, these are the typical costs of the “blue section” in Figure 1: they are only paid once during the installation phase. However, this parameter can have a huge influence on pumping installation power consumption, meaning the real expense will be paid over the lifetime of the installation.
Low-viscosity products will not have a negative effect on a smaller-diameter piping system. As viscosities rise, however, those smaller diameters will become problematic.
The example of a complete installation shown in Figures 5 and 6 will demonstrate how important this parameter can be regarding energy consumption.
Let’s consider this installation with the following parameters:
Flow Rate: 10 m3/h (44 GPM)
Viscosity: 500 cSt.
SUCTION LINE
Piping Length: 2 m (7 ft)
2 Butterfly Valves
DISCHARGE LINE
Piping Length: 40 m (130 ft)
6 Elbows
2 Butterfly Valves
6 m (20 Ft.) Lift
If we build the installation with 40 mm (1.5”) piping, the resulting differential pressure on the pump ports will be 9.2 bar (133 psi). If the differential pressure is within the selected pump limits, the installation will operate without issues. But let’s see what happens if we build the installation with 50 mm (2”) piping (only one standard pipe size above). Differential pressure drops down to 3.7 bar (54 psi). Regarding energy consumption, the result on the pump’s absorbed power is telling (Fig. 7). By selecting a slightly larger piping, power consumption and costs drop from 37% to more than 50%, depending on the selected pumping technology. By increasing the piping diameter and switching to a more energy-efficient pumping technology – like the Mouvex G-FLO Series – the difference becomes exponentially greater, dividing the energy consumption by three in some cases. The next question is whether we would gain even more by enlarging the piping again. If we use DN65 (2.5”) piping, differential pressure will decrease to 2.9 bar (42 psi), compared to 3.7 bar (54 psi) with DN50 (2”) piping (Fig. 8). This time, the delta is reduced, and the absorbed power reduction is not as substantial; it comes close to zero for some pumping technologies.
From top to bottom:
Figure 7 – Adsorbed power (HP) vs. piping diameter with 38.1 and 50.8 mm (1.5” and 2”) piping.
Figure 8 - Adsorbed power (HP) vs. piping diameter with 38.1, 50.8 and 63.5 mm (1.5”, 2” and 2.5”) piping.
Figure 9 – Friction loss (psi) in a 3 m (10 ft.) long, 65 mm (2.5”) pipe with a 10 m3 (44 GPM) flow rate and 1,000 cSt viscosity.
Another way to reduce energy consumption is by “streamlining” piping with as few elbows as possible and only strictly necessary ancillaries. A simple example reveals this. Consider a piping section with the possible designs showed in Figure 9: in this short section, the resulting friction loss can be multiplied by five depending on the design and ancillaries.
Naturally, more pressure means more energy consumption.
Longer piping on a pumping system will generate more friction loss, resulting in a higher pump operating differential pressure. With other equal parameters, the friction loss is proportional to the piping length. It is not always possible to shorten the piping on an existing site. However, when designing a new one, this parameter should be considered. It will reduce the building and operating costs.
Conclusion
Lighting, heating or heavy manufacturing equipment are often targeted as the first items to reduce to obtain energy savings. Some operators
do not consider the energy savings that are possible with pumping installations. By selecting low power consumption pumps like the Mouvex G-FLO Series combined with the proper design of new installations and the improvement of existing ones, operators can generate noticeable energy savings on industrial production processes.
Mouvex was created in 1906 and is a leading brand of positive displacement pumps, screw compressors, and hydraulic coolers for use in the refined-fuels, oilfield, energy, food/ sanitary, military, transport, and chemical-process industries.
Mouvex is a product brand of PSG®, a Dover company. Headquartered in Oakbrook Terrace, IL, USA, PSG is comprised of several world-class brands, including Abaque®, All-Flo™, Almatec®, Blackmer®, Ebsray®, emtec®, Griswold®, Hydro™, Malema™, Mouvex®, Neptune®, PSG® Biotech, Quantex™, Quattroflow®, and Wilden®. PSG products are manufactured on three continents – North America, Europe and Asia – in state-of the-art facilities that practice lean manufacturing and are ISO-certified. PSG is part of the Pumps & Process Solutions segment of Dover Corporation.
Steve Lundeberg
Oregon State University, Corvalis (OR) – United States steve.lundeberg@oregonstate.edu
The researchers from the Oregon State University have developed new chromium-based reddish magenta pigments taking inspiration from the moon.
An Oregon State University researcher who made colour history in 2009 with a vivid blue pigment has developed durable, reddish magentas inspired by lunar mineralogy and ancient Egyptian chemistry. Mas Subramanian, distinguished professor of chemistry, and collaborators at OSU report the findings of the study, funded by the National Science Foundation, in the journal Chemistry of Materials1
The new pigments, which could be used as energy-efficient coatings for vehicles and buildings, are based on divalent chromium, Cr2+, and are the first to use it as a chromophore; chromophores are the parts of a molecule that determine colour by reflecting some wavelengths of light while absorbing others.
“To date, no earth-based mineral has been reported to contain chromium in the divalent state as one of the components,” said Subramanian, the Milton Harris Professor of Materials Science in the OSU College of Science. “However, the analysis of lunar mineral samples collected from Apollo missions showed the occurrence of chromium in the divalent state.”
Divalent chromium has the same number of unpaired electrons as trivalent manganese, the chromophore responsible for the intense colour of YInMn blue2, which Subramanian’s team discovered 15 years ago. The Shepherd Colour Company licensed3 YInMn blue for use in a wide range of coatings and plastics, and it also inspired a new Crayola crayon colour4: Bluetiful.
When YInMn blue was discovered, researchers had been experimenting with new materials that could be used in electronics applications and mixed manganese oxide – which is black in colour – with other chemicals, then heated them in a furnace to nearly 2,400 degrees Fahrenheit. One of their samples turned out to be a brilliant blue, named YInMn blue after the component elements yttrium, indium and manganese. It was the first blue pigment discovery in two centuries and a huge advance in safety and durability as well as vividness.
In the new study, Subramanian, research associate Jun Li and graduate student Anjali Verma were inspired by the divalent copper that serves as a chromophore in Egyptian blue, which is the world’s first known synthetic pigment and dates to more than 5,000 years ago. The researchers replaced the divalent copper in Egyptian blue with divalent chromium, leading to durable, reddish magenta pigments.
To stabilize the divalent chromium on Earth, researchers maintained high temperatures, almost 2,500 degrees Fahrenheit, under high vacuum during the synthesis that started from chromium metal, chromium trioxide and other chemicals.
1 https://pubs.acs.org/doi/abs/10.1021/acs.chemmater.4c00253
2 https://www.ipcm.it/en/open/ipcm/2023/80/136.aspx
3 https://today.oregonstate.edu/archives/2015/may/licensing-agreement-reached-brilliant-new-blue-pigment-discovered-happy-acciden
4 https://today.oregonstate.edu/archives/2017/may/pigment-discovered-oregon-state-university-inspires-new-crayola-crayon-color
“Most of the magenta-coloured pigments used today are organic chemicals and suffer from stability issues when exposed to ultraviolet rays and heat from the sun because they can break down organic chemical bonds,” Subramanian said. “Inorganic magenta pigments are rare, and most require a significant amount of cobalt salts that are hazardous to both humans and the environment.”
The magenta pigments developed by OSU researchers are thermally and chemically inert because of their high preparation temperature and remain unaltered structurally and optically upon exposure to acid and alkali, the authors note.
In addition, unlike pigments that contain cobalt, the chromium-based magenta pigments are highly reflective of heat from the sun – meaning they have a cooling property that would lead to energy savings for cars and structures coated in them.
“Most pigments are discovered by chance,” Subramanian said. “The reason is because the origin of the colour of a material depends not only on the chemical composition but also on the intricate arrangement of atoms in the crystal structure. So someone has to make the material first in a laboratory, then study its crystal structure thoroughly to explain the colour.”
Despite recent advances in quantum mechanical theories and computational methods, predicting a crystal structure that will produce an intense inorganic pigment of a desired colour is still elusive, he added.
“We got lucky the first time with YInMn blue, and now we are coming up with some fundamental chemical and crystal structural design principles to rationally create new pigments,” he said. “Determining the key structural ingredients required for making vivid colours should allow for shorter times between pigment discoveries. Science doesn’t always follow a prescribed path, but we’re exploring pigments with divalent chromium as a chromophore in diverse coordination environments in crystal structures of various inorganic compounds.”
The NSF funding for the just-published study was a special grant earmarked for high-risk, high-reward research.
The grant is known by the acronym EAGER5, which stands for Early Concepts Grants for Exploratory Research.
As one of the largest academic units at OSU, the College of Science has seven departments and 12 pre-professional programs. It provides the basic science courses essential to the education of every OSU student, builds future leaders in science, and its faculty are international leaders in scientific research.
5 https://www.nsf.gov/pubs/policydocs/pappguide/nsf09_1/gpg_2.jsp#IID2
In the global industrial landscape, the advent of technology marked an era of unprecedented transformation. The Industry 4.0 paradigm brought a significant step forward in the automation and digitalisation of production phases. However, the evolution process has not stopped yet. This article deals with Transition 5.0 and how the shift towards the fifth revolution is leading to overcoming the very concept of “industry”.
Industry 4.0 has revolutionised how factories produce goods by integrating advanced technologies such as the Internet of Things (IoT), artificial intelligence (AI), and robotics. The resulting transformation has led to greater efficiency, flexibility, and customisation in production, paving the way for new business opportunities and process improvements.
On the other hand, the Transition 5.0 concept refers to the process of adaptation and change required to move from the current economic and industrial model (often associated with Industry 4.0) to a new paradigm that integrates humanity, sustainability, and technological innovation. It is based on the idea that technological innovation, although necessary, cannot be the sole driver of social and economic development. On the contrary, it emphasises balancing economic growth with human welfare and environmental sustainability. This transition entails a change not only in infrastructure and industrial processes but also in society’s values and priorities. It requires adopting advanced technologies such as artificial intelligence, automation, and the Internet of Things, but with an emphasis on social responsibility, equity, and creating an inclusive work environment. In essence, Transition 5.0 aims to create a future in which technological innovation serves humanity and sustainability rather than being an end in itself. That also calls for close collaboration among governments, businesses, academic institutions, and civil society to develop policies and practices that promote equitable, sustainable, and inclusive economic growth.
At the same time, it should be highlighted that one element was omitted in the transition from 4.0 to 5.0: the word “Industry”. This is probably because Transition 5.0 focuses on a broader and more holistic view of society beyond the mere industrial context. A concept has been lost concerning change that starts from and is for the benefit of industry, broadening the socio-economic landscape.
In other words, whereas Industry 4.0 mainly refers to the digitalisation and automation of industrial processes, Transition 5.0 fosters a more inclusive perspective embracing social, environmental, and economic aspects. While continuing to integrate advanced technologies into the industry, Transition 5.0 recognises that technological innovation alone is insufficient to address the complex global challenges our society faces. Transition 5.0 – again, without the word “Industry” – implies a more integrated, future-oriented vision that promotes sustainability, equity, human well-being, and harmony with the environment, in addition to economic growth. This approach applies not only to the industry but also to other sectors such as education, health, energy, and so on. Therefore, whereas Industry 4.0 focuses specifically on the industrial sphere, Transition 5.0 broadens its scope to include a more comprehensive, inclusive vision of social and economic progress. That is one of the themes on which UCIF invites its members and their guests to reflect, exploring them in depth through its We Talks, web conferences on subjects of topical interest to the surface finishing and treatment industry.
Micronora will take place from 24th to 27th September 2024 at Besançon (France).
Can you give us an overview of the current marketing situation at Micronora this year?
Fanny Chauvin: To give our exhibitors a perfect idea of the costs of participating in Micronora, we had to start marketing campaign later than usual. However, we are very confident about this year’s edition, and we are already almost 98% booked. Following the same trends as previous editions, we will be welcoming around 33% international companies from some twenty countries, demonstrating the global appeal of our trade fair. As usual, just over 80% of exhibitors remain loyal to us, and we thank them. With countless fields of application and the ability to transfer technologies from one sector to another, microtechnology is an undeniable asset that enables companies to diversify and open to new markets. This is undoubtedly why we regularly welcome new exhibitors,
including some from the USA and Canada this year, countries that have had little or no representation in previous editions. This testifies to the vitality and growing appeal of our event. We also note the growing demand from our exhibitors for larger surface areas.
This year’s Zoom theme is intelligent microtechnology. Could you tell us why this is particularly relevant in today’s industrial context?
FC: At a time of dwindling resources and energy issues, it is crucial for all sectors of industry to integrate intelligent solutions into their businesses to be more efficient. They help optimise production by analysing data in real time, identifying inefficiencies, and improving machine performance. What is more, their proper use can cut costs by proactively planning maintenance, for example, or by optimising resource utilisation and minimising manufacturing defects. Finally, intelligence in production can foster innovation by opening the way to new possibilities for improving processes and products, thus strengthening a company’s competitiveness in a constantly evolving industrial environment, and this is all the truer in microtechnology, a sector that must always be at the cutting edge of innovation.
This year’s Zoom, the show’s flagship event, will focus on intelligent microtechnology, because we need digital twins, intelligent sensors, and solutions that enable us to correct machines if monitored measurements show a drift. We will also be presenting augmented reality solutions for predictive maintenance and assembly assistance. And because not every
company can change its entire machine park, we will be showing how traditional machines can be made more intelligent with just a few modifications.
FC: For the 2024 edition, we have tried to work in cooperation with the region in several areas. This year, you will discover a regional village highlighting companies with fewer than 15 employees working in microtechnology and precision, offering them 100% visibility to visitors. In addition, we have launched a start-up village offer, with special support for regional start-ups.
As usual, a programme of technical conferences will be offered to exhibitors and visitors alike, and this year we will also have the pleasure of welcoming writer and trainer Arthur Keller, a specialist in systemic risk and resilience strategies, to open the program on September 24th at 2.30pm. Those present at this conference will no doubt say on leaving they will have a before and after! I will leave you to find out.
Finally, we are planning a magnificent exhibition on the theme of “From watchmaking know-how to the technologies of the future,” which will provide a unique opportunity to discover how the Micronora association and our fair have evolved over the years, and will showcase manufacturers and their innovations over the past 75 years.
For further information: www.micronora.com
Eos Mktg&Communication srl www.eosmarketing.it - info@eosmarketing.it www.myipcm.com - info@ipcm.it
Redazione - Sede Legale: Via Pietro Mascagni, 8 - 20811 - Cesano Maderno (MB) - Italy Tel. +39.0362.503215 - Fax. +39.0362.1794768
EDITOR IN CHIEF / DIRETTORE RESPONSABILE
ALESSIA VENTURI venturi@ipcm.it
EDITORIAL DIRECTOR / DIRETTORE EDITORIALE
FRANCESCO STUCCHI stucchi@ipcm.it
EDITORIAL OFFICE / REDAZIONE
PAOLA GIRALDO giraldo@ipcm.it
MONICA FUMAGALLI fumagalli@ipcm.it
NICOLE KRAUS kraus@ipcm.it
MATTEO SOTTI sotti@ipcm.it
ILARIA PAOLOMELO paolomelo@ipcm.it
GABRIELE LAZZARI redazione@ipcm.it
FEDERICO MELIDEO melideo@ipcm.it
GIULIA GENTILE gentile@eosmarketing.it
EDITORIAL OFFICE AND GRAPHICS
ELISABETTA VENTURI grafico@ipcm.it
MEDIA SALES
FRANCESCO STUCCHI stucchi@ipcm.it
ILARIA PAOLOMELO paolomelo@ipcm.it
NICOLE KRAUS kraus@ipcm.it
Prof. Massimiliano Bestetti: Department of Chemistry, Material and Chemical Engineering, Politecnico of Milan –Section of Applied Chemistry and Physics
Prof. Paolo Gronchi: Department of Chemistry, Material and Chemical Engineering, Politecnico of Milan –Chemical Engineering Section
Kevin Biller: ChemQuest Powder Coating Research
Prof. Stefano Rossi: Material Engineering and Industrial Technologies, University of Trento - Product Design
Dr. Fulvio Zocco: Environment and quality
LAYOUT/ IMPAGINAZIONE
ELISABETTA VENTURI
grafico@ipcm.it
The smart journal for surface treatments
This magazine is wrapped with a biodegradable and compostable film. Questa rivista è confezionata con un film biodegradabile e compostabile.
PRINT/ STAMPA SEBEGRAF SRL info@sebegraf.eu
SUBSCRIPTION SERVICE - SERVIZIO ABBONAMENTI:
Sale only on subscription - Vendita solo su abbonamento E.mail info@ipcm.it
Subscription Rates 2024 - Tariffe Abbonamento 2024:
Annual subscription print + digital:
EMEA 110,00 € (postage included)
Rest of world 350,00 € (fast airmail shipping included)
Abbonamento annuale cartaceo + digitale:
EMEA 110,00 € (spese postali incluse)
Resto del mondo 350,00 € (spedizione via aerea inclusa)
Single copy: 15,00 € EMEA (postage included) - Rest of world (postage excluded)
Back issues: 30,00 € EMEA (postage included) - Rest of world (postage excluded)
Fascicolo singolo: 15,00 € EMEA (spese postali incluse) - resto del mondo (spese postali escluse) Arretrati: 30,00 € EMEA (spese postali incluse) - resto del mondo (spese postali escluse)
Subscriptions can be made by bank transfer to the following account: Eos Mktg&Communication Srl IBAN IT97F0844033270000000084801 - SWIFT CODE CRCBIT22 or via payment online at: www.myipcm.com
Gli abbonamenti possono essere sottoscritti versando il relativo importo a mezzo b/b IBAN IT97F0844033270000000084801 intestato a eos Mktg&Communication Srl oppure con carta di credito direttamente dal sito www.myipcm.com L’Iva sugli abbonamenti, nonchè sulla vendita di singole copie è assolta ai sensi dell’art.74 comma 1 lett. C DPR 633/72, DM 29/12/1989.
Registrazione al Tribunale di Monza N° 1970 del 10 Dicembre 2009Eos Mktg&Communication srl è iscritta nel Registro degli Operatori di Comunicazione con il numero 19244
POSTE ITALIANE S.P.A. – SPEDIZIONE IN ABBONAMENTO POSTALE –D.L. 353/2003 (CONV. IN L. 27/02/2004 N.46) ART. 1, COMMA 1 LOM/MI/4351
It is forbidden to reproduce articles and illustrations of “ipcm®” without authorization and without mentioning the source. The ideas expressed by the authors do not commit nor magazine nor eos Mktg&Communication S.r.l and responsibility for what is published is the authors themselves.
È vietata la riproduzione di articoli e illustrazioni di “ipcm®” senza autorizzazione e senza citarne la fonte. Le idee espresse dagli autori non impegnano nè la rivista nè eos Mktg&Communication S.r.l e la responsabilità di quanto viene pubblicato rimane degli autori stessi.
Since 1981 CIE Group’s mission is Since 1981 CIE Group’s mission is to realize plants for Aluminum to realize plants for Aluminum Finishing Lines. With more than Finishing Lines. With more than 200 realizations the CIE Group is 200 realizations the CIE Group is today one of the main today one of the main worldwide leaders. worldwide leaders.
Se hai bisogno di un rivestimento protettivo che rimanga inalterato nel tempo, anche dopo che gli altri sono svaniti nella memoria, Interpon D3020 è in grado di soddisfare le tue esigenze.
Le sue prestazioni iperdurevoli garantite in tutte le condizioni atmosferiche, dal sole cocente del deserto al gelo della pioggia artica, sono accompagnate da una favolosa gamma di colori e finiture, da quelle opache a quelle metallizzate, sempre di tendenza.
Offre fino a 30 anni di garanzia globale sulle prestazioni del rivestimento, se applicato da un applicatore autorizzato, nonché una certificazione Qualicoat 3.
Essendo un rivestimento in polvere, è privo di COV, crea pochi o nessun rifiuto e sostiene un futuro più sostenibile.
La vostra immaginazione inizia con la nostra finitura.