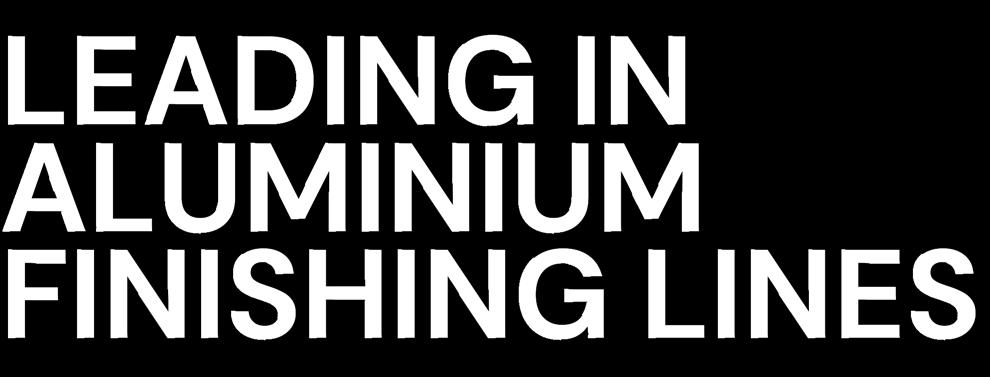


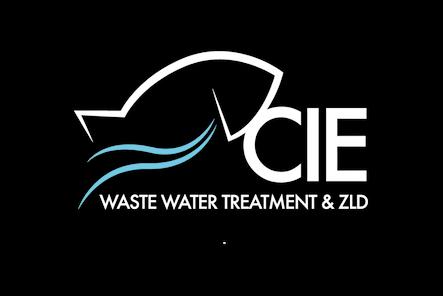
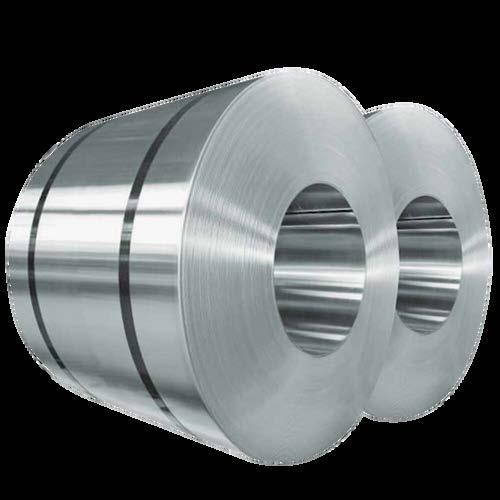

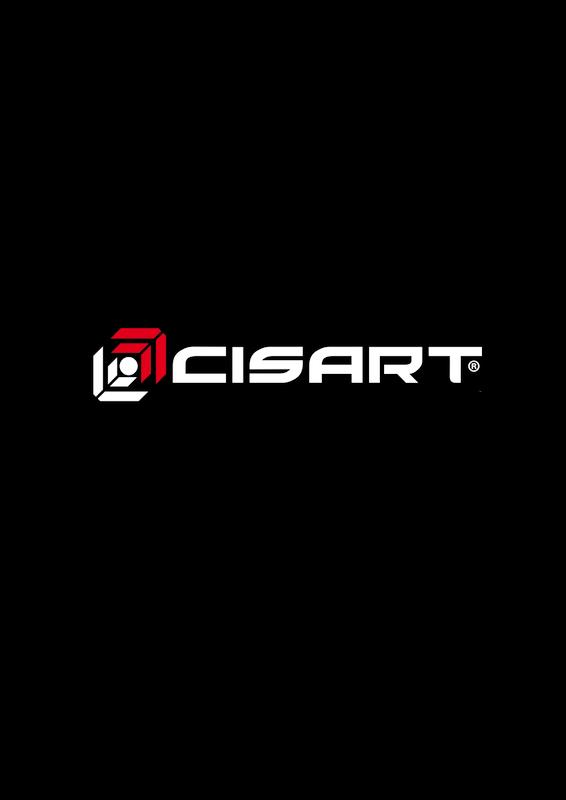
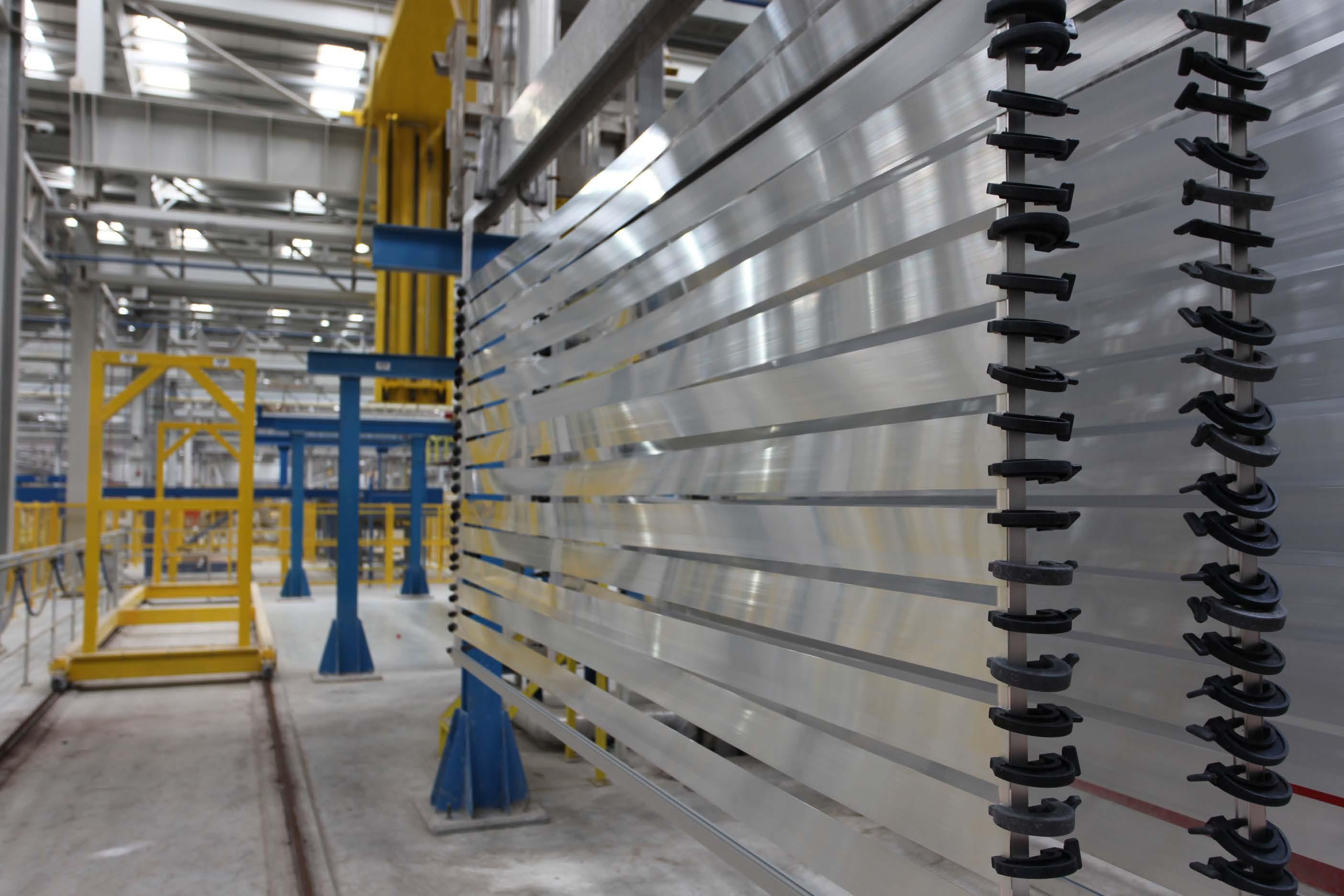
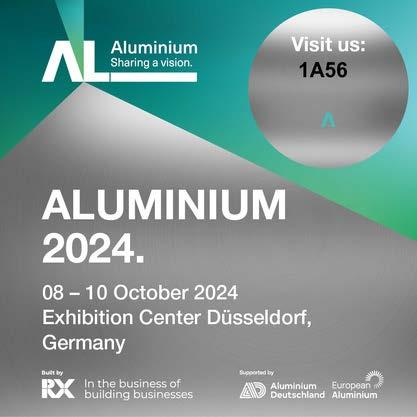

For over 25 years, your partner for industrial painting
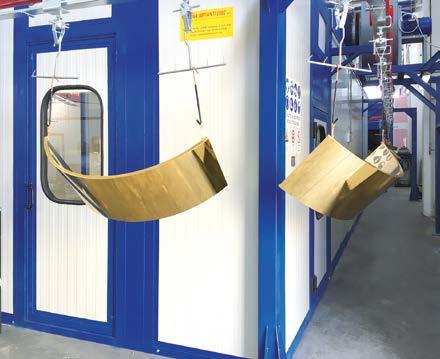
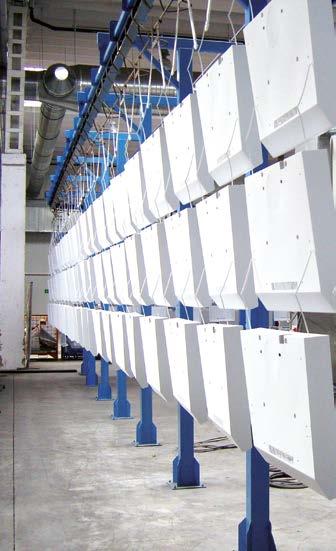
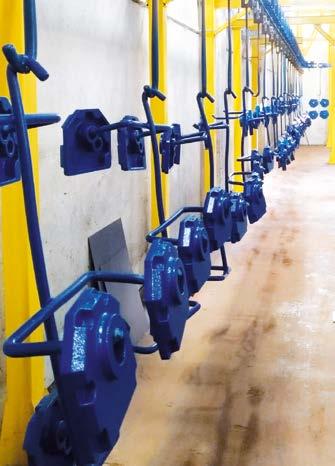
For over 25 years, your partner for industrial painting
Verona Impianti designs, manufactures , and installs tailor-made coating plants, pretreatment lines, and drying systems. Reliability, competence, and experience: these are the three nouns that best describe the team of VERONA IMPIANTI 2002 .
Helios Quartz Group SA
Via Roncaglia 20 6883 Novazzano - Switzerland
Tel. +41 (0) 919233555/6 Fax +41 (0) 919233557
swiss@heliosquartz.com www.heliosquartz.com
Helios Italquartz S.r.l. Via delle Industrie 103/A 20040 Cambiago - Milano - Italy
Tel. +39 02 95 34 93 18 Fax +39 02 95 34 50 85
italy@heliosquartz.com www.heliosquartz.com
TRATTAMENTO ACQUE
WATER TREATMENTS
PREVERNICIATURA E NANOTECNOLOGIE
COATING PRETREATMENT AND NANOTECHNOLOGIES
SGRASSANTI INDUSTRIALI DEGREASERS
SVERNICIANTI
PAINT STRIPPERS
Product Developments in Powder-In-Mould Coating
Successfully
WITHIN SURFACES
Julie Mehretu’s BMW Art Car Celebrates its World Premiere at the Centre Pompidou in Paris
ON TECHNOLOGY
Outsourcing Is No Longer
OF THE MONTH CHROME+: Green Chrome Plating on Plastic Without Galvanic Processes
IED Torino Presents ALISEA: the Concept Hypercar which Pay Tribute to ZONDA’s 25th Anniversary Wears Lechler Products
ROAD TO 2050 right° and Dürr Calculate Climate Impact of Paint Shops for the Automotive Industry
OF THE MONTH
Precision in Quality Control: TecoLight Systems for Detecting Surface Defects
ART WITHIN SURFACES The Eroded Surface: Arsham Transforms the MV Agusta’s Superveloce into a Timeless Sculpture
FOCUS ON TECHNOLOGY A New Liquid and Powder Application Plant with an Innovative Air-Curtain Oven Was Part of SVI Verniciatura Industriale’s Project to Maximise Flexibility
Our 70 years experience in Surface Treatment is ready for the E-Mobility market.
Research, innovation, development.
In 70 years, our vision towards the future has never stopped. Today, Tecnofirma provides quality to the electric market which is the most evolving technology in the automotive industry. Our impregnation, cleaning and painting plants are the result of the constant commitment to offer cutting-edge solutions and products anytime, anywhere.
FOCUS ON TECHNOLOGY
The Perfect Combination of Mechanical and Chemical Pre-Treatment Improves the Corrosion Protection of the Coatings Applied on ABF Color’s Heavy and Light Metal Fabrications
HIGHLIGHT OF THE MONTH
Merck Italy Effect Day 2024: “If you Can Dream it, you Can Do it”
- ICT
Italian Company of Excellence: Trafilerie Mussari and Its Tube Treatment Process
TO 2050 - ICT
STUDY - ICT
Cleaning Is Essential for Tecnotrasmissioni
OF THE MONTH - ICT
Commitment to Training Future Technicians
THE INDUSTRY - ICT
Lavaggio Industriale
Lavaggio di precisione
Sgrassanti interoperazionali
Miscele di tensioattivi
Protezione temporanea
Galvanica Funzionale
Zinco e leghe di zinco
Passivanti e Sigillanti
Rivestimenti resistenti all'usura
Pretrattamento
SurTec Italia Sas di Externa Holding Srl
Via Boito, 251 Tel.: +39 059 8579901
41019 Soliera (MO) E-Mail: info-it@surtec.com Italia Web:www.SurTec.com
Pretrattamento metalli alla verniciatura
Processi di conversione esenti
Cromo e Fosfati
Fosfatanti a bassa temperatura
Passivanti per acciaio zincato a caldo
Passivazione conduttiva su
Alluminio TCP
Galvanica Decorativa
Rame, Nichel e Cromo
Deposizione su plastica (POP)
Stagno e leghe di Stagno
Pretrattamento
Nuovi TIXO Clear e TIXO Filler. Qualità superiore per superfici in fibra di carbonio.
La linea Tixo ridefinisce la finitura delle superfici in carbonio, sia lucide che opache. Progettati specificamente per questo materiale, i prodotti TIXO offrono una tixotropia e una pienezza straordinarie, permettendo applicazioni di spessori notevoli con una distensione eccellente e un aspetto estetico impeccabile. Grazie alla loro elevata resistenza, queste vernici UHS riducono il numero di mani necessarie, garantendo lavorazioni più rapide e efficienti. La brillantezza eccezionale e la resistenza ai graffi delle vernici TIXO portano gli standard qualitativi a un livello superiore.
Scopri sul sito tutti i prodotti Vernici Caldart studiati per l’Automotive.
Alessia Venturi Editor-in-chief Direttore Responsabile
Bespoke comes from the verb bespeak, meaning “request”, “order”, or “hire”. It derives from the English tailoring lexicon of the 19th century: at that time, every tailor’s shop used fabric cuts already selected by customers so that, after taking the necessary measurements, the garments could be made from the tissues that had been spoken for. Hence the adjective bespoke for “ordered”1. Borrowed from the world of fashion, this word is now extending its semantic range as a synonym for luxury – luxury for the few, for those who can afford to invest in a product that is not only made-to-measure but rather unique and exclusive, be it a garment, a furnishing solution, or a car. The epitome of this concept is Ferrari’s One-of-a-Kind programme, which brings together the exclusivity of unique pieces created over time to express the personality, tastes, and desires of this car manufacturer’s customers2
Bespoke thus also becomes applicable to the service sector and the manufacturing industry, where an increasing number of suppliers are solving their customers’ specific problems by customising plants, machines, and chemical formulations down to the smallest detail.
To achieve this, companies must bring in the know-how and experience required to smoothly manage project sharing, material manufacturing, product and process validation tests up to logistics, installation, and commissioning.
Added to this is the need for a parallel but extremely useful skill: the ability of all the partners involved in a bespoke project to interact proactively, constructively, and timely and provide an equally personalised after-sales service.
From the raw materials that make up coatings to plant management software, today’s surface treatment field is also increasingly oriented towards extreme customisation to achieve aesthetically perfect finishes with functional performance that even exceeds specifications. This is the only way to guarantee consistent quality in increasingly complex products in terms of both design and stringent functional and durability requirements – what is more, in a context of environmental and economic sustainability, which is difficult to achieve using standardised solutions. This approach reflects the technological maturity of an industry that has realised its strategic value for the commercial success of products. From a necessary but insignificant step to complete the manufacturing cycle of an object, it has become a pivotal process to ensure its beauty, usability, durability, and sustainable life cycle.
The concept of bespokeness recurs in many pages of this summer issue of ipcm®, dedicated to the wonderful and fertile (in terms of innovations, ideas, design) world of cars and transport. After all, right after fashion, it is the automotive industry that generates dreams, dictates trends, and is a fruitful ground for new industrial paradigms to take root.
This issue of ipcm® was produced while the entire editorial team was also busy organising something equally important: the event to celebrate 15 years of activity of Eos Mktg&Communication, the publisher of ipcm® magazines. In the September issue, you will find an extensive account of the evening that saw us celebrate with many customers and suppliers.
Errata Corrige: In the March/April issue No. 86 on p. 74, we erroneously attributed the Qualisteelcoat certification obtained by Univer 2000 (Zané, Italy) to the coating of aluminium instead of steel.We apologise to all readers and interested parties.
1 https://lanieri.com/blog/en/difference-ready-wear-made-to-measure-bespoke-suits/
2 https://www.ferrari.com/en-GB/museums/one-of-a-kind
Verona Impianti 2002’s new website enhances user experience with a streamlined, intuitive design to ensure easy navigation and improved engagement for visitors.
The Italian manufacturer of coating plants Verona Impianti 2002 has recently launched its new website, offering a simple and intuitive browsing experience. The company has been designing, manufacturing and installing powder and liquid coating systems as well as pre-treatment, curing and drying machinery, offering solutions tailored to specific customer requirements for the Italian and European markets.
“The decision to create a new company website goes far beyond the simple desire to make over the look. In fact, it comes from the necessity to adapt to the needs of an increasingly digital and faster world, which manages to catalyse the attention of the target audience, only with distinctive contents and a tailored experience”, has stated Pietro Tamellin, owner of Verona Impianti 2002. The new website has undergone both structural and graphic restyling to streamline the communication of services offered and better share news and values of the company, facilitating visitor engagement. The accessibility of the site has been developed with a responsive design
to ensure easy and interactive navigation, even on mobile devices. Additionally, the new website includes a special section dedicated to history and mission of Verona Impianti, as well as a page detailing the team’s skills.
An in-depth technical analysis of the entire product portfolio was carried out, which includes:
Complete powder and liquid coating systems;
Pre- and after-sales services;
Realisation of modifications, revamping and extensions of existing plants;
Routine and extraordinary maintenance;
Consulting services for painting plants and processes.
Finally, the News area offers visitors a continuous update on products, services offered, regulations issued in the sector and allows interesting case studies and technical insights to be shared.
www.veronaimpianti.com
Gerdau’s NanoCORR improves anticorrosive performance with a lower chemical dosage and makes paint production more sustainable.
Gerdau Graphene has recently launched NanoCORR Shield, a graphene-enhanced anticorrosive chemical additive for solvent-based anticorrosive coatings. The new product demonstrated a 30-70% increase in corrosion resistance in salt spray tests. In fact, the addition of a small amount of graphene - an ultra-strong carbon nanomaterial - in paints and coatings increases the barrier effect against corrosive elements such as water, oxygen and chlorides. In addition, NanoCORR reduces paint consumption by reducing the nominal thickness of the coating, while maintaining the performance of the paint or coating.
“NanoCORR offers a quality solution to combat corrosion and extend the useful life of metal structures, reducing the need for frequent maintenance and associated costs. Its positive impact goes beyond protection against corrosion, promoting sustainability and economic efficiency in multiple sectors,” has stated Alessandra Zanuto, Technical Manager of Products and Sales of Chemical Additives at Gerdau Graphene. Moreover, NanoCORR complements Gerdau’s growing line of chemical additives for the paint and coatings market, which includes the anticorrosion additive G2D NanoCORR for waterbased paints and coatings, G2D NanoLAV W107 and G2D NanoDUR W102.
“G2D NanoCORR Shield was designed to help producers deliver ultra-high-performance paint and coating products while reducing the use of non-sustainable inputs such as heavy metals.
This product joins our expanding portfolio of additives serving the paints and coatings market and underscores our commitment to developing innovative, sustainable graphene-based solutions for this industry,” has added Valdirene Peressinotto, Executive and Innovation Director at Gerdau Graphene.
For further information: www.gerdaugraphene.com
From an interview with Oscar García, Project Manager Spray SA, Barcelona (Spain)
Electrostatic force is the basis of the electrostatic coating process, applicable to both powder and liquid paint products. In this interview, Oscar García, project manager at Spray SA, which has been in the electrostatic liquid and powder coating sector for 40 of 56 Spray SA’s years, explains in detail the operating principles, mechanisms, application limits, and advantages of electrostatics, with some interesting digressions into health and environment-related topics.
ipcm®: What is electrostatics, and how does it work in a coating process?
O.G.: We need to distinguish two aspects to answer these questions. First of all, we should delve into the basics of electrostatics; secondly, we should analyse why and how we can use it specifically to achieve the goal of coating a workpiece. Then, we can answer the most crucial question: can we obtain the required coating results?
To explain what electrostatics is in a clear way, we can define it as a branch of physics that studies the phenomena and properties of electric charges at rest and analyses how they behave and interact, attracting or repelling each other, and how they distribute on a surface or inside an object thus influencing its ability to conduct electricity, as occurs in conductive elements, insulating media, or dielectric materials. However, to avoid delving into complex principles such as electric charge, force between point charges, and electric field or electric potential, I suggest we start with the concept of ionisation to understand its impact and how electrostatics can help in a liquid coating or powder coating application process.
ipcm®: We understand the need to use technical terms to detail the basic principles of electrostatics, but let us begin with that: how does ionisation affect coating processes?
O.G.: Although these basic concepts are essential to understanding why we use electrostatics and how it helps us to achieve our goals, what truly matters is ionisation, which is the basis of all these principles and of the electrostatic application process itself. The air we breathe is made up of molecules of various elements, and each molecule is composed of one or more atoms. We can imagine atoms or molecules
as a central nucleus of positive charges surrounded by an equal number of negative charges, i.e. electrons, moving around it. A simple analogy is that of the planets moving around the Sun. With the same amount of positive and negative charges, atoms or molecules are electrically neutral. However, if a molecule loses electrons for any reason, it will have a net positive charge. Conversely, if it gains electrons, it will have a net negative charge. These charged molecules are called positive ions or negative ions. Therefore, we will have ionised air. It should be pointed out that nature provides us with a constant supply of atmospheric negative ions sufficient to meet the needs of organic life on the planet, for example, through the action of ultraviolet light from the sun, lightning from storms, and other instrumental ways. Many methods have been developed to mimic what nature itself offers us. However, to answer your question, we will focus on one of them: corona discharge.
ipcm®: How is the corona discharge mechanism achieved, and what is it based on?
O.G.: Corona discharges can occur in nature, producing a large quantity of positive or negative ions. However, we must create an equivalent artificial process to validate the coating operation. In short, we need to supply a high voltage to a certain type of surface that generates a large amount of negative ions and place a workpiece at a certain distance from said object. To determine what kind of object to connect to high voltage, we need to think about the Van der Graaff generator’s operating principle: the greater the curvature of the object, the greater the intensity of the electric field at that point, which goes so far as to break the insulation of air and create a flow of charged molecules, thus
ionising it. It is therefore common to use a small electrode connected to a high-voltage source [80kV - 100kV]. The process that follows is well known: the stronger the field generated, the greater the speed acquired by the electrons emitted by the electrode, which will hit the air molecules and split them into two electrons and a positive ion, thus keeping the ionisation process going constantly.
ipcm®: So, once a defined space between the electrode and the workpiece has been ionised, what process is required for electrostatics to be effective for coating purposes?
O.G.: When we feed liquid or powder paint into the ionised field, the negative ions charge the paint particles electrostatically. These charged particles are then drawn towards the previously grounded workpiece.
ipcm®: What are the advantages (operational, environmental, etc.) and the limitations of electrostatics?
O.G.: The industrial electrostatic coating process offers several operational and environmental advantages, including as follows:
Higher transfer efficiency: the percentage of sprayed liquid or powder coating that adheres to the workpiece. Several factors can affect this percentage but if they are properly taken care of, the reduction in wasted paint is considerable.
Better adhesion and durability: electrostatically charged paint particles adhere better to surfaces, providing a more durable and resistant finish.
Lower emissions: by increasing transfer efficiency, emissions of volatile organic compounds (VOCs) are reduced. In the case of liquid paint, this depends on the type of product (solvent-based or water-soluble), the type of solvent, and, above all, the design of the overspray filtration system and the disposal of paint residues from the filters.
Overspray reduction: the mist (or overspray)
generated by spraying paints with conventional or non-electrostatic airbrush methods is drastically reduced. This reduces air pollution and improves working conditions for operators.
Less solid waste: powder coating is partially reusable, as only a small percentage that ends up in the filter must not be recycled. This is one of the key benefits of powder coating, as it results in cost savings and sustainability.
Better working conditions: reducing or eliminating solvents and overspray creates a cleaner and safer environment in terms of hazardous substances and improves indoor air quality.
Lower energy consumption: the process’ efficiency reduces the need for touch-ups, lowering energy consumption and the costs associated with these operations.
Health benefits for operators: naturally occurring negative ions offer numerous benefits for human health.
To summarise, electrostatic technologies in the application of liquid and powder coatings offer multiple operational and environmental benefits, including reduced waste and emissions, energy savings, and improved working conditions, contributing to more sustainable and environmentally friendly industrial practices.
ipcm®: How do negative ions affect health?
O.G.: First of all, I am not a doctor but a scholar of all aspects related to my profession. That said, I can tell you that negative ions do as follows:
Improving mood: they increase the levels of serotonin, a neurotransmitter that contributes to a feeling of well-being, which helps combat depression and anxiety.
Increasing energy: some research studies indicate that exposure to negative ions helps reduce fatigue and increases energy.
Improving sleep quality: they balance the levels of serotonin and other chemicals in the brain.
Reducing allergies and asthma: negative ions can help eliminate dust particles, pollen and other allergens from the air, reducing the symptoms of allergies and asthma.
Strengthening the immune system: they improve the immune function.
Improving concentration and mental performance: they can increase oxygen flow in the brain.
Of course, it would be advisable to consult a doctor, or perhaps devote a longer article to this topic. In any case, the generation of free negative ions should not be confused with ozone.
ipcm®: What do you mean by that? Some ozone generators are considered ideal for offices and enclosed spaces. What is the disadvantage of ozone, if any?
O.G.: We are getting a bit off-topic, but I think a brief comment will be of interest to your readers. The difference lies in the nature of the particles produced and their effects on the environment and health. A negative ion, as mentioned, is an atom or molecule that has gained an electron, with the advantages I have listed above. Ozone is a molecule composed of three oxygen atoms. It is formed in the stratosphere and protects us from ultraviolet radiation, but the vast majority of devices available are actually considered negative ion generators, sea or mountain air generators – in other words, generators of an element with high oxidising properties, effective in neutralising odours but toxic to health, especially with respiratory diseases or reduced lung function.
ipcm®: Let us go back to an important question: what are the limitations of electrostatics in liquid and powder coating?
O.G.: We should distinguish between liquid and powder application, as they are two different processes. However, there is a common denominator, and we can say there are limitations in terms of as follows:
Surface and geometry: non-conductive surfaces, such as some plastics or wood, cannot be treated without a prior pre-treatment process that makes them conductive. Similarly, parts with complex shapes or sharp edges can cause the so-called Faraday effect due to the protection provided by the electrostatic field lines.
Retro ionisation: it is generated by free ions that do not adhere to the surfaces and charge the coating particles (this is more evident in powder coating). By travelling through the field lines, these free ions pass through the paint layer and create
discharges within it, reducing its uniformity and resulting in cissing or orange peel effects after curing.
Humidity and environmental conditions: as high humidity can reduce the effectiveness of electrostatic attraction, it is necessary to maintain controlled environmental conditions.
Material compatibility: in some cases, the coating’s formulation must be modified in terms of viscosity and resistivity. The polymerisation process also ensures good adhesion.
Installation, operation, and maintenance costs: implementing an electrostatic process may require a high investment, together with the need for specialised personnel to ensure optimal performance and the amortisation of the process’ cost.
Drains and fire safety equipment: if applying solvent-based paints, a spark can occur due to an error in design, the type of solvent, or incorrect maintenance; if applying powders, the danger lies in powder concentration due to an error in calculating the peripheral
system’s suction flow rate or a lack of maintenance. Therefore, in any electrostatic process, each element must be adequately earthed and feature fire detection systems.
Surface efficiency: the workpiece to be coated must be free of contaminants to achieve good paint adhesion.
ipcm®: Why choose an electrostatic application process instead of an airbrush one?
O.G.: I think we have already touched on some reasons. Although I believe that some applications must necessarily be carried out with an airbrush or with airless or mixed-air technologies, these are the key advantages:
Increased transfer efficiency: paint savings are around 60%.
Reduced overspray.
Uniform coverage and better finishes.
Fewer defects such as runs, bubbles, and other imperfections.
Less residues.
Less VOC emissions and pollution in the work environment and the atmosphere.
Cleaner work environment.
Less exposure of operators to chemical compounds.
More controlled and consistent application process with uniform, high-quality finishes when handling high production volumes. Despite these advantages, it is important to consider certain factors when choosing an electrostatic application technology, such as the initial costs, the nature of the workpieces’ surfaces, and the environmental conditions, as mentioned above.
ipcm®: How does electrostatics affect coating quality?
O.G.: In detail, these are the main ways in which it improves finishing results and paint durability:
Uniform particle attraction: paint particles are evenly attracted to all areas of the workpiece’s surface, including corners, edges, and difficultto-reach areas. This results in a more uniform and consistent paint layer.
Higher attraction force: the particles adhere more firmly to the part’s surface, producing a more durable and wear-resistant coating.
Fewer defects: the better adhesion rate reduces the likelihood of defects appearing.
Uniform thickness: this process ensures more precise control of the paint layer’s thickness, which is crucial for applications requiring specific thicknesses for corrosion protection.
Smooth surfaces without imperfections: it improves the aesthetic appearance of the coated part.
Increased wear resistance: this is particularly important in industrial and automotive applications where durability is of the essence.
Environmental protection: it provides a protective barrier against moisture, chemicals, and UV radiation, prolonging the service life of the coated component.
Repeatable results: it ensures consistent and repeatable results in high-volume production processes, ensuring that every part has the same degree of finishing quality.
ipcm®: How has electrostatic application in industrial coating evolved, and what are the most recent advances?
O.G.: I think I will not get this answer wrong because developments in most fields have a common denominator: the remarkable evolution of electronics. Although the chemical industry continues to evolve and produce advanced solutions, such as water-soluble coatings or UV powders for coating thermally sensitive materials, electronics has made great progress in terms of colour change operations, automatic cleaning of systems, remote control, development of more efficient and safer cascade voltage multipliers, reduction of the Faraday cage effect (TCC system), part detection systems, robotics, arrangement and movement of fixed guns on multiple axes programmed according to part type, elimination of manual control of various pneumatic or electrical parameters through touch screens, and other countless advantages ensured by the giant strides made by technology.
ipcm®: Can you describe an advanced electrostatic powder and liquid application process designed by Spray SA?
O.G.: Although Spray SA has just celebrated its 56 anniversary and many companies from different industries have already installed our products (operating in several fields, including aeronautics,
construction, automotive, wood, plastics, and many more), I would like to mention two recently designed electrostatic plants with 4 high-speed discs each to apply a water-soluble coating on various metal components with a significant height. Their reciprocators are 6 metres high and are controlled automatically through specific programmes set up by an operator. The latter controls all parameters affecting the application system, including cleaning and automatic colour change. As for powder coating, I would like to mention a fully automatic system applying a primer and a top coat on car chassis with a total of 16 automatic guns divided into 2 booths. Although the colour of the primer and the top coat are different, there is no variation in colour. The entire line, including the peripheral devices, the fire detection system, and the recovery and screening unit, is operated automatically through special programmes linked to each other and controlled by a single operator.
In summary, although electrostatic technology offers many significant advantages, it is crucial to consider and manage its limitations to ensure an effective and safe application process. This may include the proper selection of materials, the control of environmental conditions, investment in appropriate equipment, and the training of operators.
MEGAPOL® F SD ULC is the latest powder coating innovation from CIN Performance Coatings, designed to address major market trends.
Qualicoat approved for Class 2, MEGAPOL® F SD ULC is a polyester finish specifically developed for the protection of steel and aluminium, recommended for applications requiring high durability, such as large architectural projects and ACE projects. This powder coating is characterized by its ambivalent curing regime: it can be cured at lower temperatures than conventional systems, resulting in energy savings, or it can undergo a faster cure by adjusting the temperature accordingly. MEGAPOL® F SD ULC is available in all gloss levels and various finishes, including solutions with the MEGABOND® quality seal, applicable to all bonded metallic finishes. This innovative technology creates unique effects with perfect distribution of metallic pigments.CIN Performance Coatings works daily to develop the best paint and varnish solutions, whether liquid or powder, with a focus not only on top performance but also on environmental impact and product sustainability.
MEGAPOL® F SD ULC is energy efficiency for any project.
With over 100 years of experience in the coatings industry, CIN has been the Iberian market leader since 1995. In 2023 reached a turnover of 395 million ranking as the 10th largest European paint manufacturer* and the 36th worldwide **.
CIN operates in all four main market segments (Architectural, Industry, Protective Coatings and Yachting and Marine), with over 1639 employees in more than 15 countries, with a direct presence in Portugal, Spain, France, Italy, Poland, Angola, Mozambique, South Africa and Mexico; and exporting to various markets in Central Europe, Latin America and Africa.
For further information: www.cin.com
* European Coatings Journal, May 2024
** Coatings World Top Companies Report, July 2023
In 2024, Idrotecnica proudly celebrates its 40th anniversary, marking four decades of excellence and innovation in the water treatment sector. This important milestone is not only an opportunity to reflect on past successes but also to look to the future with renewed commitment and determination.
Idrotecnica has been transforming the industrial landscape since 1984, offering plant solutions for the purification and demineralisation of process water for a variety of sectors, including industrial coating, cosmetics, chemicals, and many others. This celebration is a special occasion to reflect on its journey and share its vision for the future: “When Idrotecnica was founded, the goal was clear: to become a benchmark manufacturer of water purification and demineralisation equipment and plants. Today, after four decades of hard work, dedication, and innovation, we can proudly say that we have achieved and surpassed this goal. Every system we design and build tells a story of precision, reliability, and passion for excellence,” says Idrotecnica’s owner, Federico Marcenaro.
Idrotecnica’s philosophy: simplicity, reliability, and a customer-centric vision
“Our mission is to build modern water treatment systems that are extremely simple to operate and robust. We use first-class components and proven solutions, guaranteeing high performance and ease of maintenance. When required, we offer a quick and decisive pre- and after-sales assistance service that ensures timely support and the supply of spare parts worldwide.”
Idrotecnica meets the needs of its customers through a diversified product range:
Standard plants: over 110 standard models of ion exchange demineralisation, reverse osmosis, and filtration systems. Standardised production guarantees fast response times and competitive costs.
Customised plants: tailor-made solutions to meet specific requirements.
“The trust of our customers is our highest priority. Our production volumes grow year after year thanks to the loyalty of our customers and dealers worldwide. Our focus on offering a quick and responsive service before and after each sale enables us to build lasting relationships and continue to evolve with our partners from a wide range of industries,” Marcenaro adds.
A future of opportunities
“Idrotecnica’s 40th anniversary is a significant milestone in our company’s history. We look to the future with enthusiasm and determination, ready to overcome new challenges and seize the opportunities to come. Our commitment to excellence, innovation, and customer satisfaction remains unchanged as we continue to expand our global presence and strengthen our position as a leader in the water purification and demineralisation market. We would like to thank all those who have contributed to our success, and we are committed to maintaining the standards of excellence that have made us a leader in the industry,” concludes the owner of Idrotecnica.
For further information: www.idrotecnica.com
The awarded Flowsense technology developed by J. Wagner GmbH increases productivity and quality while reducing consumptions.
Flowsense technology developed by J. Wagner GmbH has been honoured with the ‘Die Oberfläche (The Surface)’ award during the ceremony held on Tuesday 4th June 2024 at the Surface Technology Germany trade fair, the event showcasing all the most important trends for the surface finishing sector (held from 4th to 6th June in Stuttgart).
The jury recognised Flowsense for its increased productivity, powder savings, enhanced quality and reduced carbon footprint as most notable achievements. It is the only powder coating technology to
receive the award, as the other prizes were won by technical solutions in the field of electroplating.
The Flowsense powder quantity control by J. Wagner GmbH
Compared to liquid solutions, in powder coating the set output quantities might be neither known nor constant over the medium term due to wear and other process parameters, with users compensating by accepting higher tolerances or more frequent manual inspections.
The Flowsense powder quantity control
developed by J. Wagner GmbH has succeeded in controlling the painting process in a reproducible manner, helping the clients to achieve consistently high surface quality. It acts as an autopilot in the powder coating process, automatically navigating the coating process and leading to better coating results – allowing also the operator to focus on other tasks.
The Stuttgart Surface Technology award ‘The Surface’
The award recognises outstanding developments from across the industry in surface treatment and finishing technologies. It has been presented at the SurfaceTechnology Germany trade show to honour the most innovative applications or technologies in all disciplines.
Wagner won the recognition for the first time in 2013 thanks to its pioneering technology for process-safe powder coating for standard MDF boards.
“The award recognises the ubiquitous but often overlooked cross-sectional technology that often plays a key role in the degree of innovation and progress of numerous industries without this being known to the general public,” has stated Martin Metzner, the head of the electroplating technology department at the Fraunhofer Institute for Manufacturing Engineering and Automation IPA who founded the prize in 2012.
For further information: www.wagner-group.com
During Biobased Coatings Europe 2024, Dörken presented also its new preservative-free range of ecological pastes.
The international paints and coatings manufacturer Dörken has recently expressed satisfaction for its participation at Biobased Coatings Europe 2024, the event dedicated to exchanging ideas regarding environmentally-friendly and future-proof products and services along the entire value chain of biobased materials, paints and coatings held in Valencia (Spain) from 5th to 6th June.
“We got a lot of interesting input from Valencia: not only through the conversations at our stand, but also through the presentations of other companies and the lecture programme of the event,” has commented Guido Strauch, the director of sales for the tinting solutions at Dörken. “Key topics at the event included the market overview and trends, current directives and regulations of the European Union, as well as new technologies, opportunities and challenges.”
In addition, the company also presented its new preservative-free Dörken® Ecological range of pastes and held several useful discussions around sustainable, compatible and high-quality innovations in the field of pigment pastes, providing valuable information and insights on other solutions and semi-finished goods as well.
“We addressed important current issues with our preservative-free paste range: sustainability, compatibility and quality. At Biobased Coatings Europe 2024, we saw that we are already doing a lot of things right. But we are of course constantly working on bringing future-proof solutions to the market,” has declared Christopher Jahn, the director of the Architectural Coatings division for Dörken.
For further information: www.doerken.com
Bringing your surface to perfection.
Dürr offers high-quality and easy to integrate painting solutions from manual to automatic.
www verind.com
Gema has recently announced the official handover of the keys to its new ultra-modern company headquarters in Gossau Sommerau (Switzerland), that host more spacious and conformable offices, innovative production areas and a contemporary high-bay warehouse.
The building testifies the commitment of the manufacturer of powder coating technologies, equipment and accessories to forwardlooking and environmentally-friendly solutions and business practices, since it has been constructed to meet the latest sustainability standards and offers a welcoming working environment for the employees and also optimal conditions for further development. As a matter of fact, with 20,000 m2 of floor space, it will enable the manufacturing processes to be further optimised and the quality of the products to be raised thanks to a modern test and customer application laboratory equipped with four coating lines.
For further information: www.gemapowdercoating.com
Andy Doyle, President and CEO of American Coatings Association, has been awarded with a Silver Medal during the British Coatings Federation Conference held in Manchester on 23rd May 2024.
The American Coatings Association
President and CEO, Andy Doyle, has recently received a Silver Medal from the British Coatings Federation (BCF) for representing the federation on the European stage and for maintaining its high-profile with international associations. Additionally, Andy Doyle has contributed to the research and understanding of Coatings Care and PaintCare. Andy Doyle was instrumental in the founding of the World Coatings Council in 1992 before becoming president and has been involved with the BCF throughout the same period. The unique relationship between the has proved invaluable, both in and out of the European Union.
“I’m extremely honoured and humbled by this recognition from the BCF. I have always felt that our two organisations share a special bond. The BCF is an exceptional association, deftly led by their CEO Tom Bowtell and admired not only in the UK but globally as well. I am very grateful for the many years of friendship and have greatly enjoyed the
chance to work alongside a terrific BCF team,” has commented Andy Doyle, President and CEO of American Coatings Association.
“Andy exemplifies the commitment to the industry that the Silver Medal was developed to recognise. He has been a prominent figure in the global coatings industry and is a huge advocate for the BCF. We would like to thank
Andy for his support and expertise throughout the years and congratulate him on this very much deserved accolade,” has added Tom Bowtell, CEO of the BCF.
For further information: https://coatings.org.uk
Total Finishing S stems is a leading designer and integrator of high-q alit and comple ind strial finishing s stems Whether o need an in-depth process anal sis or req ire finishing eq ipment and components, o r eq ipment e ceeds e pecta ons and o r inno a on and a toma on is ind str leading
Chemtec announced its nanotechnological passivation product PRONORTEC has received the Qualisteelcoat certification: this quality seal reaffirms the effectiveness of the solution specifically developed to improve adhesion and increase corrosion resistance during the pre-treatment of metals.
The Italian company Chemtec Srl, a leader in the formulation, production and distribution of technologies for the industrial finishing, surface treatment and industrial water purification sectors, is proud to announce that it has received the Qualisteelcoat certification for its PRONORTEC nanotechnology for the following classes:
ST2 C3H
SZ1 C3H
SZ2 C4H
HD1 C4H
HD2 C5H.
Specifically developed to offer a real, simpler, environmentally-friendly, and more economical alternative to tricationic/ microcrystalline phosphating, the PRONORTEC nanotechnology guarantees the excellent adhesion of the paint to the metal substrates and very high levels of corrosion resistance. Since it is a one-component process, it is therefore not necessary to add additives to correct pH or the concentration of other components. Furthermore, by exploiting the organic chemistry of phosphorus and not containing heavy metals such as zinc,
chromium or nickel, PRONORTEC protects the health of the operators and the environment without sacrificing performance.
“The PRONORTEC nanotechnology allows to reduce both the energy consumption typical of phosphating plants and the costs associated to wastewater and water treatment. It is neither a toxic nor a harmful product; therefore, it significantly improves all aspects related to the pre-treatment and painting of metals. The Qualisteelcoat certification is a further demonstration of the quality of PRONORTEC and the work carried out by the entire Chemtec team”, stated Carlo Guidetti, CEO and Co-Founder of Chemtec Srl.
The Qualisteelcoat certification is an international brand developed specifically to validate the quality of painting and coating systems, whether powder or liquid, applied to new constructions or steel equipment built or used in more or less aggressive environments, as detailed in ISO 12944-2.
The compliance with the quality requirements is verified by an independent certification and inspection body – recognised by Qualisteelcoat – which issues a certification for painting and coating cycles examined with positive results. The PRONORTEC nanotechnological passivating solution met all the requirements.
For further information: www.chemtecitalia.it
From an interview with Carlo Enrico Martini Sales manager of SAITA Srl
SAITA Srl inaugurated SAITA Lab, a new centre of excellence for R&D in water treatment focusing on innovation, sustainability, and professional training.
To meet the growing market demand for sustainable practices, companies are currently facing numerous challenges that lead them to evolve and seek innovative solutions. This calls for committing to research and development and adopting cutting-edge technologies to reduce their activities’ environmental impact and increase their production processes’ efficiency. Water treatment, in particular, represents a crucial challenge for many industries needing to upgrade their processes for better environmental protection.
That is why SAITA Srl (Limena, Padua, Italy), a company with long experience in waste water treatments for various sectors, has recently inaugurated SAITA Lab, a new laboratory devoted to R&D, analysis, and professional training. This reflects its commitment to continuously improving its services and technological solutions, and it is a significant step towards creating more advanced and sustainable processes.
SAITA Lab aims to act as a point of reference for companies looking for innovative water treatments but also institutions and universities, thanks to its training programme that aspires to attract new talent.
ipcm®_International Paint&Coating Magazine had the opportunity to interview Carlo Enrico Martini, sales manager of SAITA, who told us about the motives and objectives behind the creation of this new laboratory.
ipcm®: Why did you decide to create SAITA Lab?
C.E.M.: Our laboratory’s activity has been the beating heart of our company for about 30 years now. Ever since SAITA’s foundation, my father has always placed great emphasis on research and development, investing heavily in an in-house laboratory to carry out process tests and analyses. This year, we decided to further leverage our expertise by creating a specific brand, SAITA Lab. It will carry out the same activities we have performed over the years but in a more structured manner, acting as a centre of excellence for developing water purification and recycling technologies for various industrial operations, such as coating and electroplating. The aim is also to develop greener and greener
processes, as we believe that protecting the environment by offering state-of-the-art, sustainable solutions is essential.
In addition, with SAITA Lab, we would like to establish an academy to train users and dealers as well as attract young professionals from academia. We are going to organise training activities using our pilot plants, demonstrating our water treatment and purification processes. In addition, to provide added value to all those who work with our company, such as maintenance technicians and SAITA dealers, the new laboratory will constantly offer technical information for the operation and maintenance of our systems.
ipcm®: What equipment and technology does the laboratory have?
C.E.M.: Currently, we are integrating our pilot plant line with new technologies for vacuum evaporation, filtration, demineralisation with ion exchange resins, membrane filtration (ultrafiltration, nanofiltration,
and reverse osmosis), and advanced ozone and UV lamp oxidation. We also have reactors for testing physical-chemical processes.
ipcm®: What types of tests will you perform at SAITA Lab?
C.E.M.: There are two main types of tests we carry out in our laboratory. When a customer presents us with a problem related to recirculating or purifying waste water, we can either conduct laboratory tests or use our pilot plant line to simulate the entire process.
More specifically, the first stage consists of the customer filling in a questionnaire to provide details about the volume of water to be treated, the equipment used, the operating costs, and the company’s objectives and required results. After that, the customer sends a sample
of a few litres to be analysed in our laboratory with operations tailored to its unique needs: at this stage, we carry out a water characterisation process and perform all the necessary tests, e.g. evaporation, filtration, and clariflocculation. Finally, if further study is needed, we test samples from 500 to 1000 litres with our pilot plants. The customer can attend the trials and actively participate in our tests.
ipcm®: How important is SAITA Lab’s activity for the success of your company?
C.E.M.: Although we are now presenting our laboratory activity to the market, this has actually been the core of SAITA for many years, enabling us to analyse the processes and technologies we offer to our customers
but also to provide them with a comprehensive, timely, and professional service. Our laboratory technicians work in synergy with the service and maintenance team to quickly solve any issues that may arise from using our systems. When a customer encounters a problem, we analyse water samples, perform laboratory tests and analyses, and provide the most appropriate solution, for example, by suggesting it changes the chemical used, replaces the filter mass, or cleans the water treatment system circuit.
Some phases of the treatment and purification process of waste water containing hexavalent chromium.
ipcm®: Are you also planning to create synergies with the academic world?
C.E.M.: Our company has been collaborating with secondary schools and educational institutions for years, with the aim of expanding technical knowledge and know-how in the waste water treatment sector. In the near future, we will continue collaborating with the academic world, including universities, institutes, and research centres, to attract new talent and introduce young people to the world of work.
ipcm®: In terms of communication, how do you plan to promote this project?
C.E.M.: We deeply believe in the power of sharing knowledge and know-how. In addition to getting students and professionals directly involved, we would like to raise awareness of the importance of water treatment and recycling. We plan to open social media pages dedicated to SAITA Lab to share short information clips, explanatory videos, and technical content.
However, we will not stop there: we envision SAITA Lab as an entity with its own identity, a place where theory and practice can meet. At our headquarters in Limena, we are expanding and creating spaces devoted to training and educational environments where our technicians can work alongside anyone who wishes to operate in the water treatment sector.
Monica Fumagalli ipcm®
Appearance matters even in the field of enclosures for industrial applications. With a coating process borrowed from the automotive sector, ETA was the first company in the industry worldwide to introduce a cataphoresis + powder application process to provide its wireless switchboards with both protective and cosmetic finishes. To meet the demands of a market that is focussing on ever greater production automation and placing increasingly demanding requirements, it has recently upgraded its coating line by integrating a SuperCenter EVO powder feed and colour change system and two latestgeneration IPS systems developed by its long-standing partner Wagner Spa.
When designing a production plant, choosing the electrical cabinet to protect the machinery’s most critical components, such as control elements, circuits, cables, and switches, against dust, humidity, water, and extreme temperatures is probably the last but indeed not the least important phase.
ETA was the first company in its industry worldwide to implement a cataphoresis + powder application process for its wireless switchboards.
The slightest error in its configuration can not only change the project’s technical characteristics but also compromise the operability of the entire system.
Antonio Turati, the Production Manager of ETA Spa (Canzo, Como, Italy), specialising in the design and construction of wireless enclosures since 1978, introduces us to this sector by explaining that “although it was conceived as an accessory element in the industrial automation landscape of the boom years, this simple product has become indispensable, in an industrial scenario where companies can no longer do without automated production to stay ahead. For those who design and manufacture switchboards, it is first of all essential to identify the environment in which they are to be placed, ensuring that
they are protected against dust and humidity, if they are intended for sheltered and enclosed facilities such as factories, or from corrosion and atmospheric agents, if they are installed outdoors.
“That is why, in 2017, for the first time in this sector, we developed and implemented the E DUP (Double Layer Protection) treatment in our paint shop. Combining cataphoresis with powder coating, it proved to be a success. More recently, as our production throughput continues to grow, we have upgraded our powder feed and colour change system by installing 3 new powder centres, i.e. 1 SuperCenter EVO and 2 IPS plants. The latter is the only powder centre on the market to enable a true automatic colour change operation without manual intervention. It was recently developed by Wagner Spa, with which we have been
collaborating since our coating plant was built in 2008. To date, this also integrates a two-tier power & free conveyor from Futura Convogliatori Aerei, a pre-treatment tunnel and drying and curing ovens from Tecnofirma, and cataphoresis plant installed by Silvi Srl in 2017.”
Established in 1978 by the heirs of Turati Antonio, the company now sees the involvement of the family’s third generation while continuing to be run by two of its founders, Aldo and Luigia, joined by Samanta and Antonio some years ago. “Thanks to the know-how acquired over more than 45 years in the machining of sheet metal, stainless steel, and aluminium extrusions, ETA is a benchmark manufacturer in the international enclosure industry, recognised for its high quality standards and ability to provide solutions for both the industrial
automation and IT worlds,” explains QHSE Manager & ATEX Specialist Andrea Re. “Our company is governed by values inspired by the concepts of sustainability, quality, innovation, and flexibility, which are reflected both in our daily actions and in every aspect of our workflows: from design to sheet metal machining, from coating to assembly, up to dispatch.”
“In recent years, we have focused a lot on customisation even for small batches and on product diversification. In this almost halfcentury of company history, the other major change that has enabled ETA to distinguish itself from its competitors has indeed been the development of new switchboards for harsh environments, lowvoltage power distribution, and servers and data centres. “ETA’s mission is to create a link between hardware and software through technologically advanced products, and this is reflected not only in the solutions we offer to our customers but also in our production processes. At the same time, in line with our scrupulous policy for
the protection of the environment and our surrounding area, all our investments are subjected to an environmental impact assessment beforehand. We have installed two photovoltaic plants on the roofs of our factories, i.e. our headquarters in Canzo and the building in Albavilla, a few kilometres away, which supply electricity for about 1 MW. We also use recycled materials, and we always select machines with low CO2 emissions, such as the latest ones acquired for laser cutting and welding. Finally, it is worth mentioning that we supply flatpack solutions to optimise shipping costs and volumes.”
In addition to the two production sites in Canzo, where the first processing phases are carried out, and Albavilla, taking care of the final production phases, the ETA Group also includes a production site in Romania for small and non-standard switchboards; three foreign sales subsidiaries in the UK, France, and Poland, soon to become four with the opening of a new division in the US; and a widespread sales network throughout Italy and in over 40 countries worldwide.
The Canzo site is equipped with 2 production lines: one for processing stainless steel parts – which are rubberised, i.e. a polyurethane gasket is applied to prevent external elements from penetrating the switchboard, assembled, and packaged at this plant – and one for processing carbon steel parts – which are then coated, rubberised, and assembled at the Albavilla site. Ultimately, all of ETA’s products are shipped from the Albavilla plant, which was established in 1998 precisely as a logistics hub: the finished stainless steel components are also transported here for this purpose.
“In the past, we were supported by an external coating contractor,” notes Giovanni Desantis, the Paint Shop Manager. “However, in 2008, we decided to insource this process by creating an ad hoc department. The investment in the related line was made to support the company’s development: it was undoubtedly oversized compared with business volumes back then, but it was designed with a view to growth.
“To do this, we started a project to renovate our Albavilla plant, previously only used for shipping, including the construction of a new paint shop on the factory’s first floor. On the ground floor, we receive panels with a maximum size of 3 x 2.5 m or pre-assembled box profiles with a maximum depth of 500 mm, which are tracked by PLCs along the entire production route from the loading area (where a lift takes them to the first floor) to the 4 unloading areas (which they reach via a lowerator after passing through the paint shop). Once they reach the upper floor, depending on the required colour, they are distributed among the pre-treatment and cataphoresis plant, the drying oven, the 3 Wagner booths (1 single-colour and 2 multicolour), and the curing oven. The power & free conveyor that runs along the two floors of the building and the elevator and the lowerator that serve the loading and unloading bays were designed by Futura Convogliatori Aerei (Robecco Pavese, Pavia, Italy). The conveyor has a total length of 7 km and features 250 load bars hanging on 3 m-long frames with a load capacity of 500 kg.”
The E DUP (Double Layer Protection) treatment consists in the application of an epoxy resin primer in the cataphoresis tank and of a thermosetting polyester powder top coat. The choice of this process, implemented here for the first time in the electrical cabinet sector, resulted from several analyses and tests to find the optimal solution.
“Eventually, we opted for this combined cycle because it produces coatings that have both high aesthetic and performance properties and are suitable for a wide range of environments and applications, while ensuring the degree of flexibility we need to differentiate our products. With oversized parts that cannot be immersed in the cataphoresis tank, we manually apply a zinc-rich powder primer in the booth and then the finishing coat. ETA’s cabinets are characterised by a standard colour, the textured ETA RAL7035, but we can apply the entire range of RAL colours upon request, since our customers have also become more demanding in terms of tints.
To integrate the cataphoresis tank into the company’s coating line,
Silvi Srl (Lesmo, Monza e Brianza, Italy) revamped the existing pre-treatment plant originally built by Tecnofirma SpA (Monza, Italy) in 2008, adding 2 stages after degreasing and rinsing: nanotechnology atomisation and a rinse with demineralised water. The cataphoresis tank has a capacity of 45 m3 and is equipped with 26 tubular anaphoresis dialysis cells. “Tecnofirma Spa had already designed the 7.5 m-long tank to reduce the paint content in proportion to the parts’ size,” explains Silvi’s CEO, Daniele Fumagalli. “It is equipped with a weir to keep the level constant and ensure the total absence of foam. Finally, it is insulated with an internal 3 mm-thick PVC sheet.” After immersion, the parts are taken to the doublepass through UF cleaning tunnel made of 316 stainless steel, also supplied by Silvi, and then to
the drying oven. “The cataphoresis plant is managed by a control PLC with a keyboard and a digital panel, interconnected with the company’s management system,” illustrates Fumagalli.
The 3 coating booths (2 for colour changes and 1 for applying a single colour) were supplied in 2008. “We immediately chose Wagner’s application equipment because this company is a leader in the design and installation of that kind of plant and is, therefore, a reliable partner for this delicate stage of the production process. We knew it could ensure the high coating quality we were looking for,” states Turati. “We perform 10 to 25 colour changes per day in a 12-hour shift. We needed to upgrade our application system, and the revamping carried out
by Wagner over a year, between December 2022 and the same month in 2023, enabled us to further improve our operational performance, saving time for gun flushing and streamlining application management for our operators.”
“We upgraded ETA’s booths to enable it to make a real quantum leap in operational terms,” confirms Marco Spada from Wagner. “The 3 booths have the same features. They have 18 (9+9) automatic dosing devices plus 2 manual ones and a scanning system that identifies the incoming workpieces and activates the application system according to preset programmes. In order to revamp the system, we replaced the reciprocators and nozzles and integrated our classic SuperCenter EVO system, the first powder centre designed to be in line with Industry 4.0 parameters, in one multi-colour booth and our new IPS system in the other multi-colour booth and the single-colour one. This latter powder centre model is equipped with a twofold fresh powder feeding system, allows powder preparation
by ultrasonic sieve, vibration, and fluidisation, and features accurate gun dosing systems; its integrated sensors for weight, flow, pressure, and level and its fully automatic colour change system guarantee high productivity and economic efficiency.”
The advantages of the new IPS system
Marco Spada emphasises that the advantages of the new system are considerable compared with conventional powder feed and colour change devices: “IPS is based on a revolutionary concept for the coating industry because it approaches application equipment as a highly automated machine tool, thus increasing productivity, maintaining high quality standards, making it easy to operate, and consistently reducing colour change times. In addition to lower powder consumption and easier handling, another benefit is the greater coating uniformity achieved by the new dosing devices, which
accurately apply around 80 g of coating per minute. Thanks to the reduced amount of powder dispensed and the low flow velocity in the piping, these nozzles require maintenance work to be carried out only once a year. They also feature an advanced dosing system capable of accurately and precisely dosing the paint product –which is what reduces its consumption. Finally, the Smart Feeding Technology (SFT) ensures constant powder feeding even at high flow rates over a long time.”
“As well as allowing for uniform application of our standard thickness of 80 microns,” says Desantis, “the new paint management system also guarantees excellent performance when we treat cabinets that are intended for exposure to harsh environmental conditions such as marine environments. In addition, the operators can easily set the conveyor’s speed from a minimum of 1.8 to a maximum of 3 m/ min: this is a huge advantage because, as the 3 booths are working
simultaneously, the storage buffer could get congested before the parts can enter the curing oven. The new system allows reducing the plant’s speed to a minimum to avoid this, while reducing the powder flow rate and extending the application times for easier part handling. As a result, after revamping our application system with the latest Wagner technology, the only errors that might arise are those related to cycle programming.”
After powder application, the components are taken to the curing oven designed and manufactured by Tecnofirma, where they are first pre-cured with IR panels to fix the powder and avoid contamination
between components and then cured at 180 °C for a total of about 18 minutes. At ETA, a standard coating cycle takes about 4 hours, with an average of 400 load bars per day, including unloading on the ground floor.
“Futura also equipped us with a bypass line to speed up the processing of workpieces with absolute priority. In that case, the cycle lasts about 2 hours. The conveyor’s layout is functional to our needs. There is only one loading area but 4 unloading bays, one for each different type of product we handle: 1 for box profiles, 1 for accessories, and 2 for panels, allocated according to size to facilitate the assembly and rubberising operations, so that each workpiece is sent exactly where the operator needs to perform the following step.”
Innovation through experimentation
Few companies have experimented with innovative technological solutions as frequently as ETA. “We were the first in the industry to install a laser welding system and the first in the world to experiment with the E DUP treatment inspired by the automotive coating process, precisely because our customers demand premium finishes comparable to those found on cars. We were also one of the first Italian companies to implement Wagner’s new IPS powder centre when we upgraded our booths,” notes Antonio Turati.
“In our Albavilla site, we have also recently installed a fully automated sheet metal processing plant that can read the drawings, activate the necessary mechanical operations,
and produce finished box profiles: this is an absolute novelty for our industry, as well as a major investment for our company. Keeping up with technological developments is key to our customers’ satisfaction. That is also why, since 2017, we have been collaborating with ETA Next, which is not a mere R&D office but rather a laboratory of ideas where we design products and solutions and develop our customers’ plant engineering projects at best.”
Such a quest for innovation is reflected in the continuous updating of this company’s machine fleet: “To mention just a few of the latest investments we made, in addition to updating the powder application system in the paint shop and replacing the pyrolytic oven with 2
tanks for chemical paint stripping of hooks after each cycle, we have replaced all our rubberising plants over the last two years and, in the last month (June 2024, Ed.), we installed a new packaging machine and completed the connection of the paint shop’s management and control systems with the company’s general one, in line the parameters of Industry 4.0. Our coating plant is currently operating at 70% of its capacity: we aim to use it at full capacity within a short time, thanks also to the new IPS powder feed technology, which we have trusted from the beginning to confirm the coating phase, which previously was our bottleneck, as one of the added values of our electrical cabinets.”
Ultimate Online Tool for your 3D Surface Configuration With the TIGERator, you can find the perfect powder coating finish for your project in a matter of seconds! This innovative online solution offers a realistic preview of a wide range of TIGER Drylac® powder finishes on selected 3D models, bringing your visions to life with just one click – easily and browser-based on your desktop, smartphone or tablet.
Alessia Venturi ipcm®
With the acquisition of CISART’s brand and know-how at the end of 2022, CIE (San Zenone al Lambro, Italy) completed its portfolio of engineering and chemical solutions for the aluminium surface treatment sector. CISART is a long-standing engineering company, a leader in the design of aluminium anodising and coating plants, with more than 200 machines built in Italy and around the world since its establishment in 1972: its acquisition now enables the parent company CIE/MST Chemicals to offer complete and comprehensive engineering and chemical solutions for anodising and coating processes, from pre-treatment to water purification and speciality chemicals.
After the takeover, we interviewed Franco Falcone, the founder of CIE-MST Chemicals Group, and Claudio Cittadini, an expert designer and technologist known and respected throughout the world of aluminium finishing, the former General Manager of Cisart, and today the head of the Anodizing and Coating Plants division of CIE. We discussed the Group’s new market objectives and analysed the current surface treatment-related trends in the aluminium industry, not only in the architectural sector but also in the general industry and automotive ones.
ipcm®: How would you describe the corporate entity created by the merger of CIE, MST Chemicals, and Cisart?
Franco Falcone: This merger has resulted in a company with excellent skills in all aluminium surface treatment and related water purification processes, enabling its customers to comply with the new standards regarding consumption, savings, and sustainability. Our primary goal is to offer a complete package thanks to the know-how of the two companies, both of which are prestigious, well-established, and experienced. Our second goal is to focus even more on water savings and zero liquid discharge solutions, since the combination of CIE and Cisart’s expertise naturally favours the integration of purification technology. Regarding commercial developments, we are focussing on European markets as well as the Indian and Turkish once, which we believe in a lot.
The vertical anodising line built by Cisart in Turkey in 2005.
ipcm®: What are Cisart’s technological strengths?
Claudio Cittadini: We have all-round expertise in the world of aluminium surface treatment. We started out as an anodising business, then over the years we also developed coating, right up to anaphoresis, although anodising remains our core business, a sector in which we are leaders. We have built plants that even our competitors have never built, for example, the anodising line of bars up to 20 metres at Talex in Abu Dhabi. What distinguishes us is innovation: we have never stopped in the face of special requests, and throughout our history, we have accepted some significant technological challenges, such as, for example, developing a vertical anodising plant.
Designing such a system requires a profound knowledge of the process: being it carried out vertically calls for much more complex physical-
chemical maintenance of the baths for even treatment results, especially when profiles also require electrocolouring in addition to anodic oxidation. The volumes in the baths are far greater than in a horizontal line: they are typically 9 metre-high tanks with 120 m3 of chemical solution. Under these conditions, it is necessary to ensure uniformity and consistency of the oxidation and electrocolour layers’ thicknesses from the top to the bottom of the profile. Vertical anodising plants are ideal for mass production – about 1,500/1,700 m2 of oxidised material per hour, equal to 1,200/1,300 profiles with a 15-micron anodising thickness. We built the first of these vertical plants in Turkey in 2005.
ipcm®: What are the current trends in the anodising market?
CC: It depends on the sector: it is not easy to
generalise. In the automotive industry, high productivity is a must, along with performance and quality. Companies that treat safety-critical car components, such as brake callipers, do not compromise on these. The architecture sector, on the other hand, favours productivity - which at Cisart is always accompanied by quality and performance - because there is much more competition, and unfortunately, I must admit I have seen a little too much technical levity in customers.
ipcm®: What is anodising used for in the automotive industry?
CC: Cars are now largely composed of aluminium, and all these components must undergo surface treatment. In the specific case of anodic oxidation, the greatest demands come from brake calliper manufacturers, especially for racing or high- and very high-end cars. In most cases, they require a hard anodising process, a different type of anodising operation, done at a low temperature (0 to -5 °C). It gives the oxide layer greater hardness and mechanical strength properties, producing a different, more closed-pore oxide conformation than the traditional process. As regards car bodies, it is certain that, within this decade, all cars from Class C onwards will be entirely made of aluminium. Then the competence and ability to create specific
pre-treatment systems for aluminium will benefit those who, like us, know aluminium in depth.
ipcm®: What are the synergies between Cisart and CIE/MST Chemicals?
Franco Falcone: When I set up the CIE/MST Chemicals Group, I aimed to combine mechanics (i.e. the CIE purification plants) and chemistry (i.e. the purification chemicals for the CIE plants’ operation). By integrating Cisart, the goal was to complete the process, i.e. starting with the surface treatment of aluminium and ending with the purification of treatment water, using the chemicals produced by the Group for both processes. In fact, MST Chemicals has also developed a range of speciality chemicals for pre-treatment, mainly for coating.
ipcm®: What is sustainability for Cisart and CIE/MST Chemicals?
CC: The trend is to recover energy, water, and resources. Cisart has then developed technologies for energy saving applied to refrigerators and for the recovery of heat generated during the zero liquid discharge purification process.
Gabriele Lazzari ipcm®
Italsab has enhanced its contract coating offer by upgrading its automatic powder plant’s technology. Its collaboration with Avin and Gema, which installed several innovative solutions, such as the Dynamic Contour Detection system for 3D scanning of components, has enabled the company to increase the flexibility of its finishing cycle, improve film distension, and reduce coating consumption.
To remain competitive in the sector of industrial contract coating for the ACE market, quickly adapting to different quality requirements, handling parts with very different dimensions, shapes, and technical specifications, and meeting increasingly tight delivery times are no longer enough. It is also vital to comply with regulations concerning corrosion protection for the most extreme environments. Therefore, companies in this field are now looking for technologies that enable them to develop coating cycles that meet even the highest standards required by the industry to get certified for classes C3H, C4H, and C5H. One of them is Italsab. Standing out for its constant search for innovative solutions, it has revamped its equipment several to achieve ever-higher quality. For its most recent modernisation project, it chose to rely on the experience and expertise of Avin Srl (San Martino al Tagliamento, Pordenone, Italy) and Gema Europe Srl (Trezzano sul Naviglio, Milan, Italy), which upgraded Italsab’s automatic powder coating plant with
innovative solutions, such as the Gema Dynamic Contour Detection system for three-dimensional scanning of parts, to successfully overcome the sector’s challenges. This collaboration has brought a significant improvement in the precision and operational efficiency of the company’s coating application phase, optimising the entire production process and, consequently, reducing consumption and its associated costs while ensuring a high level of corrosion resistance.
Italsab is a family-run company founded in 2004 in Faenza, Italy, in a small, 1,000 m²-wide factory (still operational today) devoted to the shot blasting and coating of medium-small metalwork parts with a line featuring a monorail overhead conveyor and powder and liquid booths – which was revamped in 2019 to adapt it to the need to finish hydraulic components
and parts requiring excellent aesthetics. In 2015, the company opened a second plant with 3,500 m² of covered area and 5,000 m² of uncovered area, accommodating an automatic plant with a power & free conveyor structured so as to be able to apply both thermosetting powder coatings and liquid paints on mediumlarge metalwork parts (with a maximum size of 6 metres), 3 additional manual booths for special and customised parts, a 12-turbine shot blasting machine with an inverter from OMSG’s Lauco series, and an automatic air-conditioned warehouse for storing powder coatings. Two years later, Italsab started working with Magni Telescopic Handlers Srl, which became its primary customer and which, in 2020, made its factory in Castelfranco Emilia (Modena, Italy) available to the company to enable it to expand further.
“We started as a small family business serving the local area with nine employees. However, our precision and reliability, combined with the production solutions we have adopted and our ability to solve any coating-related problem together with our customers, have allowed us to constantly expand our range of services, in parallel with the equipment at our disposal and our number of employees, which are now more than seventy. Indeed, Italsab can be regarded as a partner, not just a supplier. The start of our collaboration with Magni, which has enabled us to inaugurate a third 5,400 m2-wide plant with a 15,000 m2-wide external service area in 2021, is proof of this,” says Cristina Griguolo, the owner of Italsab.
From the top:
The loading bay’s lowerator.
One of the storage buffers designed by Avin.
Before the revamping project, the automated plant installed in the recently-built Modena plant included a power & free conveyor from Futura Convogliatori Aerei (Robecco Pavese, Pavia, Italy), inline shot blasting and chemical pre-treatment stations, a powder coating booth, and a curing oven. In addition, the site has a manual plant featuring filling and sanding areas, a manual powder coating booth for large parts, and a curing oven. Italsab has also set up a quality control department equipped with the latest monitoring and prevention equipment and an analysis laboratory with a humidostatic chamber, a salt spray chamber, and cyclic corrosion test devices to check the quality of the powder coatings applied daily.
“Of our plants, the one in Modena is the largest and most technologically advanced. There are two production lines at this site, to meet our customers’ more than doubled demands for the finishing of light and heavy-duty metalwork parts but also the coating of mechanical and hydraulic components, agricultural and earthmoving machinery parts, and lifting system components. However, the increase in the number and type of parts to be processed also meant that the quality requirements to be met and the shapes to be handled diversified. Therefore, we felt the need to improve our coatings’ degree of corrosion protection and film distension. One of our powder coating suppliers presented us with a new paint system that, if combined with proper pre-treatment, allows exceeding 1,000 hours in salt spray tests. During further trials in external laboratories to verify the feasibility of this process and optimise it, we also decided to test various cutting-edge technologies to improve powder distension and decrease consumption. We found that Gema’s new technologies could increase our edge and point coverage rate while, at the same time, reducing our consumption of paint material,” indicates Angelo Corallo, the company’s Chief Technology Officer and Cristina Griguolo’s husband. Therefore, at the beginning of 2024, Italsab decided to rely on Avin, with which it had already collaborated in the past, to develop a project to revamp its automatic powder coating plant. This entailed the upgrade of the existing booth (now devoted to primer application only) and the integration of a second booth from Gema for the finishing coat, both of which are equipped with the Dynamic Contour Detection device for 3D scanning of the incoming components; the installation of an additional oven with a standard burner from Avin for primer gelling; the expansion of the existing curing oven, which can accommodate up to 14.8 m long x 2.50 m high x 1.50 m wide load bars; and the addition of the MagicControl 4.0 production monitoring and management system. A 12 m vertical warehouse for powders was also integrated, ensuring optimal storage conditions.
The automatic powder coating plant, upgraded by Avin and equipped with Gema application technologies, starts with a station with two loading bays featuring lowerators for hanging the parts on the load bars, with a maximum capacity of 2,000 kilograms each. The Futura power&free overhead conveyor leads them into a storage buffer before mechanical pre-treatment. The parts are shot blasted and dedusted with an automatic blow-off device before moving to a second storage buffer. The conveyor then passes through the four-stage chemical spray pre-treatment tunnel (phosphodegreasing, mains water rinsing, demineralised water rinsing, and passivation). Afterwards, it reaches a platform where pre-coating surface preparation operations take place, including filling, masking, and sealing. Following a final check of each load bar, carried out in a third storage buffer by an experienced operator who verifies compliance with the parameters required by the customer for each production batch, the primer layer can be applied inside the first Gema EquiFlow BA04 booth and then gelled in an oven. The process is then repeated in the second booth with the application of the finishing coat. After complete curing in the final oven, the coating cycle ends with the unloading of parts in two bays, which are also connected to the
lowerators. This is where the final quality control occurs, performed by visual analysis and measuring dry film thicknesses with the Coatmaster tool.
Production flexibility with consistent, traceable results
Currently, the plant’s takt-time is one load bar every 6 minutes: the multiple storage buffers created along the conveyor route ensure flexible management of the workflow and of each phase’s timing. Moreover, the handling system enables to carry out the mechanical and chemical pretreatment stages successively or individually, depending on the technical specifications of the parts to be coated.
“Designing this plant was a challenge that Avin met with great success. In particular, the curing of the coating film created by our two-coat system had to be uniform and take place at a constant temperature: therefore, we asked Avin to develop a static oven, although connected with the power & free conveyor, with an inlet pre-chamber and an outlet postchamber with airtight seals to avoid heat dissipation. In addition, again in collaboration with Avin, we are finalising the creation of Industry 4.0 production management software interconnected with the coating plant, aimed at monitoring the quality of the entire process from raw material
procurement to packaging and shipping. That will give both us and our customers the possibility of tracking the status of each order in real time along the entire production chain,” explains Luca Cozza, Operation Manager at Italsab.
Gema’s application technologies and Dynamic Contour Detection system
Italsab’s automatic powder coating plant is now equipped with 2 EquiFlow BA04 booths, each with 16 OptiGun GA03 automatic dispensing guns (8 on each side), and 2 manual booths for pre- and post-finishing operations with conventional Venturi All-in-One injectors; an OptiCenter® All-in-One OC06 powder centre for rapid colour change operations; a MagicControl 4.0 plant control unit connected with the GemaConnect app for remote data readout on PCs, tablets, and even smartphones; and a Dynamic Contour Detection system. The dynamic contour detection process carried out at the entrance to the booths takes place in two steps: laser scanners calculate the contour of the part to be coated and identify the ideal distance to each dispensing gun, so that the MagicControl 4.0 control system can then segment the workpiece according to the available guns and position them precisely by adjusting their axes.
The non-conductive plastic structure of the booth, in combination with the EquiFlow extraction technology, prevents powder from accumulating on the bottom and adhering to the walls, while its “H”-shaped floor ensures excellent air distribution and balanced suction, as the three slits in the bottom guarantee optimal powder containment and ventilation in the manual application area. This creates a uniform airflow that ensures easy control of the application process and outstanding coating results. These technologies also enable the automatic cleaning of the internal circuits, the float, the spray pipes, and the spray guns and offer an automatic filter emptying function. Finally, the user-friendly interface of the MagicControl 4.0 control unit, with its convenient icon-based touch screen, can be easily mastered by the operators to create standardised programmes for multiple batches by setting the required film thickness and changing it when different parts need to be coated.
From left to right:
Overview of the coatings application area.
Parts entering one of the two Gema powder application booths.
The dispensing guns guided by the Dynamic Contour Detection system.
Increased quality, reduced consumption, and improved corrosion protection
Investing in these advanced technologies has enabled Italsab to strengthen its position in the market, improving the quality of its services and ensuring sustainability and continuous innovation in the industrial coating sector. The primer and top coat application booths, with their automatic gun adjustment system based on a threedimensional laser scanner, have significantly improved the quality of the company’s end products while reducing paint consumption and environmental impact.
“In an industrial context where sustainability and efficiency are increasingly valued, investing in advanced technologies and automated solutions is a strategic choice to meet the needs of a dynamic and ever-evolving market. Thanks to Gema’s 3D scanning system, which allows the guns to self-adjust their distance from the workpieces and their spraying parameters, also resulting in optimal film distension, we now have greater control over the applied thicknesses and the amount of powder dispensed by each nozzle. That translates into improved and consistent application efficiency, which increases the quality of our finishes even at very low thicknesses and guarantees considerable powder savings. Moreover, Gema’s application systems enable us to also properly cover edges and complex shapes, increasing the corrosion resistance provided by our two-coat coating cycle combined with mechanical pre-treatment, whereas the presence of two booths equipped for rapid colour changes has sped up operations, doubling our production capacity,” indicates Corallo.
“This collaboration with Avin and Gema turned out to be an immediate success not only because of the results achieved but also because our partners fully met both our expectations and the deadlines we had set. Clear and precise communication allowed us to avoid work stoppages and divert our staff to other activities or sites. We could not be more satisfied,” Griguolo concludes.
The Gold Rating award from EcoVadis positions Westlake Epoxy among the top 5% of rated businesses in the chemical industry globally.
Westlake Epoxy has announced that it has been awarded with a 2024 Gold Medal from EcoVadis, the largest and most trusted provider of corporate sustainability ratings globally, assessing corporate social responsibility (CSR) performance using international standards such as the Global Reporting Initiative, the UN Global Compact and ISO 26000.
Westlake Epoxy offers epoxy resins, modifiers and curing agents for several industries, including aerospace, automotive, civil engineering and construction, composites and wind energy, electronics, electrical equipment, and marine and protective coatings.
EcoVadis awarded Westlake Epoxy Europe a Gold Medal in the evaluated areas of Environment, Labour and Human Rights, Ethics and Sustainable Sourcing. In all categories, Westlake Epoxy achieved a total score of 75 points out of 100 in 2024, ranking 97% of companies in the chemicals sector (‘basic chemicals, fertilisers and nitrogen compounds,
plastics and synthetic rubber’) for its CSR performance. In addition, EcoVadis ratings allow customers, investors and stakeholders to assess and compare the CSR performance of their partners.
“Sustainability is the foundation of Westlake Epoxy’s strategy, integrated into our operations and product offering. This EcoVadis Gold rating reaffirms our dedication to forging a sustainable present and future, aligned with our mission of Enhancing Your Life Every Day®. We use the well-established rating system to uncover details about our strengths and opportunities, ensuring that our materials and technical solutions remain essential for our customers today while we commit to providing for their future needs and identifying areas for improvement,” has stated Karl-Martin Schellerer, Senior Vice-President, Europe and Asia at Westlake Epoxy.
For further information: https://westlake.com
The recent Arkema’s innovative recycled-based technology for powder coatings resins uses post-consumer polyethylene terephthalate to replace fossil-based raw materials and reduce product’s carbon footprint.
Arkema has recently announced a significant initiative to enhance its powder coatings resins by integrating up to 40% postconsumer recycled content sourced from end-of-life packaging products. This initiative aims to empower end markets to more effectively meet growing societal demands for resource conservation and climate impact reduction. Recent advances have enabled powder coatings resins to become more sustainable by generating minimal waste, incorporating recycled materials and being solvent-free. So, Arkema’s innovative recycled-based technology uses post-consumer polyethylene terephthalate from endof-life packaging, replacing traditional fossil-based raw materials and
enabling products containing up to 40% recycled PET, while reducing the product’s carbon footprint by up to 20%.
“Alongside our Bio-based and Mass Balance offers, increasingly incorporating recycled feedstocks is another step towards ensuring more circular high-performance solutions and a more sustainable lifestyle. The new Arkema’s recycled based powder coating resins further enriches sustainable solutions for our partners,” has stated Richard Jenkins, Member of Executive Committee at Arkema.
For further information: www.arkema.com
Eisenmann has always represented customized engineering solutions for economically and ecologically sustainable paint shops for the automotive industry, metal and wheel industries.
Our technologies provide consistent quality standards throughout the whole process from pre-treatment to final assembly.
Alessia Venturi ipcm®
The European Union’s Corporate Sustainability Reporting Directive (CSRD) has extended the range of companies and corporations affected by the sustainability reporting obligation to include all large-sized, listed and unlisted firms with more than 250 employees and an annual turnover of over 40 million Euros. This group will become broader and broader in the coming years, up to involving small and micro enterprises as well. Sustainability thus becomes an inescapable priority, as are the practices and strategies implemented to manage the environmental, social, and ethical aspects of one’s business.
Reducing industrial waste, promoting the efficient use of resources, and producing high-quality, environmentally friendly paints are imperative for the industrial surface finishing sector. In the powder coating sector, in particular, it is estimated that automatic application lines generate 25% of waste disposed of by incineration, with obvious environmental and pollution-related consequences and, accordingly, high operating costs. However, Fusion Srl’s RE-POW(D)ER project can activate a virtuous cycle that benefits all those involved in powder coating, from coaters to paint manufacturers, up to Earth itself. The circular economy model, which entails sharing, lending, reusing, repairing, reconditioning, and recycling existing materials and products for as long as possible1, is slowly gaining ground throughout Europe, and, in the long run, it is destined to undermine the linear economy model still prevailing today. The basic principle of the circular economy model is generating new value with products that have reached their end-of-life, helping to extend their life cycle and that of the raw materials they are made of while minimising waste generation.
In the last few years, the sustainability models applied to the production and application of powder coatings have been numerous and varied. Some have chosen to use bio-based raw materials instead of fossilbased ones to formulate more sustainable paints, others have focused on recycled raw materials derived from waste; process-wise, the preferred solution is the formulation of low-cure temperature products in all possible chemical natures and quality standards. However, there have been very few projects focusing on reusing waste paint, i.e. the oversprayed product that ends up in the final filter because its particle size is too small for it to be recovered and recirculated into the application cycle, despite retaining all its original performance characteristics. For some years now, a few companies have been offering a service consisting of recovering and regenerating these fine powders to manufacture different products. Still, until now, no industrial project has entailed their reuse as secondary raw material for new, high-quality powder coatings.
One of the companies offering the service of purchasing spent powder to reuse it in other production cycles is Fusion Srl, founded by Euroimpianti (Valeggio sul Mincio, Italy) in 2016 with the specific objective of pursuing an innovative vision in the field of sustainability for the powder coating sector, anticipating the growing demand of an increasingly environmentally aware market. Fusion produces certified thermal insulation and soundproofing panels incorporating fine powders recovered from coating lines. Such powders are injected into matrices placed in ovens reaching a very high temperature (800 °C),
1 https://www.europarl.europa.eu/topics/en/article/20151201STO05603/circular-economy-definition-importance-and-benefits
where they undergo a ceramicisation process.
The result is mats of plastic material that Fusion uses to produce sandwich panels employed as an insulating system for the pretreatment tunnels and coating booths of Euroimpianti’s lines, guaranteeing a 14% reduction in gas consumption for heating water and significantly limiting fan noise.
However, Fusion soon came up against a much higher supply of recovered powder than needed to produce these soundabsorbing and heat-insulating panels. In Italy, it is estimated that between 20 and 25% of the powder paint purchased by coaters is disposed of by incineration every year. That is why the company initiated an in-
depth research study to develop a method for collecting and recycling spent powder to produce new coatings in a circular way.
a new life for powder granules
The main problem with recovering oversprayed fine powder from coating
booths is that it reaches the final filter completely mixed up in terms of colour and chemical nature. That prevents its reuse in formulating new coatings, even though it is fully functional and retains all its original technical characteristics: at the high curing temperatures required by powders, polymers of different natures mixed together would “explode”, causing bubbles and cissing in the cured coating film. The colours formulated with this recovered paint mixture would also be in the grey scale only precisely because they are derived from a blend of many different tints. Preliminary studies by Fusion have shown that the big bags for collecting fine dust from automated booths contain 97% raw material and only 3% “talc”, i.e. powder with such a low particle size that it cannot be reused in any way. The key issue, therefore, is finding a way to intercept this powder mass and separate it by colour and brand before it mixes up in the final filter, i.e. during booth operation.
After seven years of studies and technical tests, Fusion has finally launched the REPOW(D)ER project, a unique circular model that, through the installation of the Fusion Eco-Filter, a patented Euroimpianti filter positioned before the final filter of a coating booth, allows recovering powder coatings as secondary raw material and avoiding their disposal as special waste. The Fusion Eco-Filter ensures the full recovery of the estimated 97% of raw material contained in big bags, which can be resold to powder manufacturers as secondary raw material, perfectly in line with the circular economy approach.
The patented filter integrates management software with a scanner that reads the powder box to be used in production, capturing data on the brand, colour, finish, and chemical nature (epoxy, hybrid, polyester, etc.). During the application of that paint product, the filter automatically diverts the
overspray and waste powder into a box before it reaches the final filter, which only collects the “talc” to be utilised for producing heat-insulating and sound-absorbing panels. The filter management software package, developed in cooperation with some Italian and foreign powder manufacturers that have enthusiastically joined the project, then labels the recovered powder box appropriately so that it can be returned to the plant and manufacturer of origin, which can use up to 10% of the by-product obtained as raw material, mixing it with 90% of fresh raw material to produce a new product perfectly equal in colour, finish, and performance to the original powder from which the by-product was derived.
Thanks to RE-POW(D)ER, powder coating manufacturers are offered the unmissable opportunity to manufacture first-class, green-certified powders with 10% recycled powders – which are equivalent to primary powders even after several life cycles. This is the same virtuous circle already successfully tested in the aluminium production sector, where the use of a percentage of secondary aluminium has become mandatory.
The operational phases of the RE-POW(D)ER project
Filter installation
Fusion provides the coaters with its special Fusion Eco-Filter, designed to capture and separate the coating by-product while ensuring precise sorting by brand and colour. The filter intercepts the fine particles before they reach the final filter. It can be installed on any type of powder coating booth, and it is especially effective on systems that perform numerous colour changes or employ several guns.
By-product generation
The high-quality by-product is carefully sorted via software to facilitate the subsequent regeneration process.
Collection, purchase, and delivery
Fusion buys and takes back the by-product already correctly sorted by brand, colour, and chemical nature from the coaters. That means the latter no longer have to dispose of the powder as waste or keep disposal records. On the contrary, waste powder turns into a profit
WATER RECOVERY
MINIMIZATION OF WASTE TO BE DISPOSED OF REUSE OF DISTILLATE
DISPOSAL COST REDUCTION
ZLD: ZERO LIQUID DISCHARGE
for their businesses. The only investment required of the (in-house or contracting) coaters is the purchase of the Fusion EcoFilter, which quickly pays for itself in the form of savings on resources previously destined for disposal. Once collected, the by-product is delivered by Fusion to the relevant
manufacturers for reuse as raw material for producing new powder coatings.
Paint manufacturers use this by-product, originally generated in their own factories, to produce high-quality green paints in line
with strict environmental and sustainability standards.
The sustainable paint these manufacturers produce is sold back to coaters, completing the virtuous cycle of RE-POW(D)ER. This enables the coaters to use environmentally friendly paint perfectly in line with their required standards (without compromising on the quality of coating results) and available in their supplier’s full range of colours and finishes.
Access to new markets
Reduced operating costs
European incentives
Proactive innovation
Corporate social responsibility
Reusing recovered powders significantly lowers the cost of producing new paint. This approach reduces the environmental impact of activities and, at the same time, optimises production efficiency, contributing to the overall reduction of operating costs.
Participation in the RE-POW(D)ER project allows companies to expand their reach and stand out in an increasingly competitive industry, attracting new customers that value environmental commitment and the responsible use of resources. They can also qualify for financial incentives, tax breaks, and funding offered by the European Union, aligning with the EU’s environmental goals for 2030. Finally, they can anticipate and respond effectively to market trends and future environmental regulations, positioning themselves as a leader in the field of sustainability.
Reduced environmental impact ©
Generation of additional revenue
Reduced waste
Competitive advantage
Market positioning
By participating in the RE-POW(D)ER project, coaters can turn operational challenges into financial opportunities, significantly reducing the costs associated with waste management and disposal through active prevention and the efficient recovery of excess paint with the innovative filter. Users also have the unique opportunity to generate profit by selling the recovered by-product, generating value from products traditionally considered waste. This approach not only aligns with global environmental sustainability goals, including 5.0 regulations and European targets for 2030, but also demonstrates an active commitment to environmental protection and a concrete effort to meet the expectations of increasingly conscious customers by actively contributing to a greener future.
Participation in RE-POW(D)ER thus becomes a strategic asset, transforming sustainability into a communicative and commercial strength capable of generating new value for a company and its stakeholders. In other words, it ensures effective differentiation on the market, enhancing a business’ image by consolidating its reputation as a leader in environmental responsibility.
RE-POW(D)ER aims at involving all major powder producers worldwide to give the greatest possible chance of recovering and recycling paint to the users that decide to invest in the installation of its patented selective filter.
Fusion is conducting extensive trials with various European powder manufacturers to ensure that the paint products obtained by mixing 10% recovered powder with fresh raw material fully meet the required quality specifications and regulations.
At the same time, it is working towards green certification for its Fusion Eco-Filter to guarantee it fully complies with the most stringent international quality standards for coating processes.
All data contained in this article were compiled and provided by Fusion Srl, which holds sole ownership and responsibility for them.
OneWheel, a Colourful Proposition for Aluminium Wheel Coatings
HOW IT’S COATED
Rolls-Royce Unveils Arcadia Droptail: a Coachbuilt Haven of Tranquillity
Automated Corrosion Evaluation on Coated Surfaces in the Automotive Industry with Deep Learning
ON TECHNOLOGY
Novation Tech: A New Liquid Coating Line to Treat Carbon Fibre Components for High-End Cars
ON TECHNOLOGY
Eisenmann VarioShuttle XL: Highly Flexible and Ready for the Future
Enhancing Paint Transfer Efficiency in Vehicle Exterior Applications
FOCUS ON TECHNOLOGY When Outsourcing Is No Longer Enough: The New Liquid Coating Plant for Exterior and Interior Plastic Car Parts Installed by a Leading Manufacturer of Plastic Components for the Automotive Industry
TIGER’s Product Developments in Powder-In-Mould Coating Continue Successfully
Dürr Builds the First EU Taxonomy-compliant Paint Shop
140
Dürr
HIGHLIGHT OF THE MONTH Extreme Precision in Quality Control: TecoLight Systems for Detecting Surface Defects
ART WITHIN SURFACES
Julie Mehretu’s BMW Art Car Celebrates its World Premiere at the Centre Pompidou in Paris
WITHIN SURFACES
The Eroded Surface: Arsham Transforms the MV Agusta’s Superveloce into a Timeless Sculpture
142 FOCUS ON TECHNOLOGY
A New Liquid and Powder Application Plant with an Innovative Air-Curtain Oven Was Part of SVI Verniciatura Industriale’s Project to Maximise Flexibility
148
SUCCESS STORIES
Water-based Coating Systems for Axles, Decks, Universal Joints, and Filters for the Automotive and Railway Industries: The Challenges Faced by Mirodur
152
SUCCESS STORIES
Spray Paint Removal for Alloy Wheels
Gustavo Carvalho AkzoNobel Powder Coatings – Amsterdam, The Netherlands gustavo.carvalho@akzonobel.com
Times are changing and new trends emerging. Like the trend we’ve observed in how vehicle OEMs need to guarantee that the product they deliver in one country is identical to the product they deliver in another. It’s a trend that has evolved from a ‘nice to have’ and ‘close enough is good enough’, to one where only precise replication and consistency will do.
The trend is evident in every element of the manufacturing process, including the design, manufacture and supply of wheels. Vehicle OEMs want their wheel suppliers to be close to where they build the cars. Wheel manufacturers demand the same of their suppliers, and this trend of ‘near-shoring’, not only supports greater supply chain security, but also reduces costs and support a more sustainable business operation.
‘Near-shoring’ is only possible, of course, by working with suppliers that have a global footprint. Being global, with global systems and technology platforms and global manufacturing, brings consistency and certainty wherever you happen to be in the world. Such certainty in delivery and supply is essential, as is another trend we’ve identified, which is the need to have the technical teams close at hand – locally – to optimize your processes and performance.
Most wheel manufacturers are global businesses with operations in multiple countries. The cars made in China are the same cars manufactured in Mexico, and they need the wheels to match.
This is not an easy task. But understanding the requirement enables businesses like ours to engineer a solution. In this case, having a global infrastructure enables us to map their global need with local manufacture and delivery. It means delivering consistency in colour and performance through manufacturing excellence. It means giving customers the assurance that our coatings have been rigorously tested in accordance not just with global industry standards, but also the specific standards demanded by each OEM. This brings peace of mind and a guarantee of quality. It also means giving customers products that are more sustainable.
Manufacturers are increasingly looking to measure and reduce carbon emissions throughout their business and the supply chain as part of their Environmental, Social and Governance (ESG) responsibilities. Coatings manufacturers are themselves, therefore, seeking to develop products such as primers that cure at lower temperatures. If a coating cures at only 150°C, for example, then it requires considerably less energy that a coating that cures at a higher temperature. As such, it
reduces an OEMs carbon footprint by being more energy efficient.
Coatings manufacturers are similarly constantly seeking to do more with less. To that end they are developing layering systems with much higher efficiency. This means that less material (i.e. less of the coating) is required to achieve the results desired, without any detriment to performance.
By layering a combination of powder coatings and liquid coatings, as featured in our ‘OneWheel’ portfolio, for example, OEMs can create a ‘system’ to match every need comprising a choice of primers, basecoats and clearcoats.
The principal purpose of the powder coating primers, for example, is to prepare the substrate to receive colour and offer degassing properties for creating a smooth basis for applying the basecoat. They are important because they not only contribute to the final appearance of the coating system, but also deliver the most efficient protection against corrosion that can be caused when surfaces are damaged by road debris and stone chips.
Basecoats play a crucial role in bringing the colour to life; they are also available in various, different special effects, from metallic to mica shades, conforming to OEM specifications.
The main advantage of the clearcoat is as a further layer of protection for the basecoat, to retain colour, gloss and integrity. Interpon’s acrylic clearcoat is the OEM standard in the US aluminium wheel market. With outstanding application consistency and film performance (approved by all major OEMs), its clearcoat combines Class A elegance and OEM-specified durability in a super smooth finish with crystal clear transparency.
Interpon’s KSP (Korrosionschutzpulver) and KSL (Korrosionsschutzlack) clearcoats comprise an advanced, high-clarity formulation that is specifically developed to enhance filiform corrosion resistance on diamond cut aluminium wheels. This provides long lasting protection from chipping, scratching, wheel cleaners and corrosive road environments. There is another important trend: today, manufacturers want their supply partners not only to keep up with the latest design styles, but also to predict - and play a part - in what comes next.
The capital outlay in buying a car is significant. Customers have become more demanding. They reflect our outward personality and individuality and how we like to be seen by our peers. OEMs know this; it’s why the aesthetic design of every part of a vehicle is now important. Wheels, brake callipers and trim which were previously ‘functional’ are now integral to the vehicle’s design - a way to accentuate its power and style, and say things about the owner, especially for higher performance models. We witness this with all OEM, and how the trend now is towards copper and blues. There is also a clear trend towards more idiosyncratic hues of yellow and green, as well as mixed colours, gloss finishes and etched designs.
Wheel designs help make a statement that reflect the unique brand personality, and as such, manufacturers want colours that are their own, unique to their model and brand. This is where the ability to replicate locally a colour that the customer wants to use globally – and to do so consistently – is essential in supporting manufacturers as they increasingly seek to differentiate their products from their competitors. But it is also about working in partnerships with customers to design and develop new colours, and identify and determine new trends to keep our customers out in front. Then it is not about replication, but rather creating something that is fundamentally new, and innovating not just new colours, but also coatings with enhanced performance,
with greater resistance to chipping and scratching, and the damage caused by UV light.
Performance of the coating really matters. It mustn’t only protect against chips and general wear and tear as already highlighted. It must also be able to protect the wheel and its parts from the risks posed by corrosion, chemicals (e.g. gasoline, brake fluid etc), and brake dust, to make them easier to clean and looking better for longer.
The automotive industry is renowned for its innovation. It is constantly re-inventing itself. Open wheel designs are now an established trend, especially for high-end sports cars. Closed wheel designs are also a trend, notably for electric vehicles, helping to further improve aerodynamic efficiency. In both cases, they are creating a demand for more colour, more style and even greater performance. They are also confirming the need for global partners with an established global footprint.
Being able to offer manufacturers the full design spectrum is key. With both powder and liquid coatings in the AkzoNobel ‘OneWheel’ portfolio, colour choice is effectively limitless. While we have literally thousands of colours to choose from, including the increasingly popular tinted clearcoats, our true expertise lies in our ability to create bespoke colours to address a specific need, enabling customers to stand out from the crowd.
HUBO Automation has always focused the attention to the market needs and to the technological evolution. This allowed the company to establish itself as a leader for the industrial automation and painting. Thanks to the experience of the technical staff and to the continuous investment in new technologies, HUBO is able to satisfy dynamically the requests of a wide range of industries.
HUBO core business is the painting division. The wide range of automation solutions fully meets any need of automatic painting; in addition, the combination of special systems can satisfy particular requests and can guarantee a flexible and reliable painting system from all points of view.
ROBOTISED PAINTING SYSTEMS
STANDARD AND CUSTOMISED RECIPROCATORS
AUTOMATIC FEEDING SYSTEMS FOR PAINTING PLANTS
With its latest bespoke car, the English automotive manufacturer aimed to evoke an oasis of peace and beauty: Arcadia reflects in both the exterior and interior finishes of the vehicle that sense of harmony and affinity with the world of architecture and design requested by the client. The following article reveals in detail the care with which Rolls-Royce designers have studied this project.
Last February, Rolls-Royce Motor Cars presented Rolls-Royce Arcadia Droptail, an exquisite coachbuilt expression of tranquillity.
Arcadia Droptail is the epitome of quiet irreverence towards expected codes of luxury, celebrating purity of form and natural materials while serving as a bold statement of the client’s personal taste. Commissioned by an individual who possesses a distinct affinity for architecture and design, Arcadia Droptail is a testimony to the patron’s
sensibilities and personal codes of luxury, defined by purity and subtle restraint, reflecting their firm belief in distilling complexity to reveal the inherent, fundamental essence.
This coachbuilt commission takes its name from the mythical realm of Arcadia, a place depicted in Ancient Greek mythology as ‘Heaven on Earth’ – a land renowned for its extraordinary natural beauty and perfect harmony. Like the haven that inspires its name, Arcadia Droptail was
envisioned by the client as a serene space characterised by reduction, material depth and tactility that would serve as a refuge from the complexities of their business life. In capturing the theme of tranquillity, Coachbuild designers embarked on an exploration of design, sculpture and architecture from the client’s favourite regions around the world. This included the precision and richness of modernist tropical sky gardens seen in Singapore, Indonesia and Vietnam as well as British ‘Biomimetic’ architecture, where organic forms and material honesty are celebrated.
In addition to these references, the client was also inspired by the motor car itself and the purity of the Droptail design concept. The commissioning client insisted that their Coachbuild motor car should be absolutely faithful to the earliest hand-drawn sketch they were first presented with in 2019. It was the profile of this highly contemporary projection of the roadster body type that resonated so strongly with the commissioning client. They were particularly compelled by the motor car’s bold, low stance, ensconcing cabin design and dramatic body lines. They also immediately recognised the nautical inspiration behind Droptail’s ‘sail cowls’: named after their resemblance to a yacht’s jib, these sharp, angular forms rise behind the doors and curve gently inwards, subtly directing the eye to the motor car’s occupants.
In order to fulfil the client’s ambition to honour Droptail’s form, Rolls-Royce Coachbuild designers developed a calm, natural duotone colourway for the motor car’s coachwork. The client’s aspiration was to define a timeless white, appearing as a solid colour at first glance, but creating a level of intrigue upon further study under natural light. To achieve this, the main body colour is a solid white infused with aluminium and glass particles. This not only creates an effervescent shimmer
when the light strikes the coachwork but, upon close inspection, creates the illusion of unending depth in the paint. Rolls-Royce specialists developed a more faceted, striking metallic using larger sizing of aluminium particles. The client was very particular and involved in their request for the Bespoke silver to contrast against the white, not only in colour, but also in terms of intensity.
In a key departure from the other three coachbuilt Droptails in this series, the carbon fibre used to construct the lower sections of Droptail is painted in the solid Bespoke silver colour rather than left fully or partially exposed, visually ‘lifting’ the motor car in profile to intensify its lithe, dynamic intent. In tribute to the brilliant mirror finish of brightwork on historical Rolls-Royces, which particularly fascinate the client, the exterior grille surround, ‘kinked’ vane pieces and 22-inch alloy wheels have been fully mirrorpolished.
While Arcadia Droptail’s exterior palette is rich in subtle detail, its primary intention is to celebrate the form and proportions of
the coachwork. The client was particularly compelled by Droptail’s clean, monolithic surfacing and bold use of negative sculpture –features that are amplified by the motor car’s muted paint colours, which reflect sunlight and cast dramatic shadows, highlighting Droptail’s many subtle design gestures.
As the exterior of Rolls-Royce Arcadia Droptail celebrates the motor car’s form, the interior is a deeply personal reflection of the client’s individual aesthetic, reflective of the style they have curated in their residences and business spaces around the world. Arcadia Droptail’s colour palette and material treatment was envisioned to be a truly personal statement and instantly recognisable as a personal signature of the commissioning client. Wood development was central to Arcadia Droptail’s interior and the client’s focus, whose very specific expectations concentrated on the texture, grain, colour and richness of the material itself. The client shared many examples of preferences and inspiration
from architecture, residences and classic cars, to guide Rolls-Royce Coachbuild designers and material specialists.
Santos Straight Grain was eventually selected as the most modern statement, based upon its rich texture and visual intrigue, which is derived from its unique, interlocking grain pattern.
Using this high-density hardwood on Droptail’s interior posed a significant challenge for the marque’s craftspeople. Santos Straight Grain has one of the finest grain types of all the wood species used within a Rolls-Royce – if not handled with the greatest care, it easily tears when machined and ‘checks’ (a crack that appears parallel to the grain) during the drying process. Despite the challenges of working with this delicate material, Santos Straight Grain is used throughout Droptail, including the aerodynamically functional rear deck section, where the grain of the open pore veneer is laid at a perfect 55° angle. To achieve a perfect composition over complex geometry, Rolls-Royce artisans used a total of 233 wood pieces throughout Arcadia Droptail, with 76 pieces applied to the rear deck alone.
Given that Arcadia Droptail will be used internationally, including some tropical climates, specific attention was paid to developing a protection
system and testing process for the exterior wood surfaces. Coatings used on superyachts were initially considered but rejected given that they require regular servicing and re-application. Instead, a Bespoke lacquer was developed that requires just one application for the lifetime of the motor car.
To validate this coating, Rolls-Royce specialists conceived a unique testing protocol wherein veneer pieces were subject to a punishing cycle inside a specialist machine simulating global weather extremes. This involved spraying sample wood pieces with water intermittently, between periods of leaving them to dry in darkness and exposing them to heat and bright light. This was repeated for 1,000 hours on 18 different samples before the marque’s specialists were satisfied with the endurance of the pieces. In total, the wood pieces and protective coating required more than 8,000 hours of development.
The Arcadia Droptail’s interior is a study in white, featuring leather finished in two bespoke hues named after the client and exclusively reserved for their use. The main colour, Bespoke White, continues
the exterior paint theme, complemented by a bespoke tan contrast leather designed to harmonize with the selected wood. The interior also showcases the exquisite shawl panel, the largest continuous wood section ever seen in a Rolls-Royce, crafted from Santos Straight Grain open pore veneer, book-matched at a 55° angle. CAD tools were employed to precisely map the placement of each wood piece, revealing a panel composed of 40 sections digitally mapped before installation. To accommodate the wood on Droptail’s intricate curves, Rolls-Royce engineers developed a new substructure using carbon fibre layering techniques akin to Formula 1, ensuring the stability of wood components amid dynamic extremes.
Bespoke timepiece: a precision instrument
The bespoke timepiece in the Arcadia Droptail’s Santos Straight Grain veneer is a pinnacle of Rolls-Royce craftsmanship. It features a complex clock face with a geometric guilloché pattern in raw metal, symbolizing Rolls-Royce’s heritage and crafted over five months after two years of development. The clock includes 12 thin hour markers, partly polished hands, and employs high-precision techniques like ceramic coating and hand-painting under 100x magnification. Its design echoes throughout
the instrument dials, emphasizing luxury and meticulous detail in line with the motor car’s aesthetic.
Reflecting the patron’s global lifestyle, the Arcadia Droptail is tailored with left-hand drive for international usability. The client experienced the car worldwide using Rolls-Royce’s ‘holodeck’, a virtual reality platform. This immersive process ensured the design harmonized with diverse global settings.
Arcadia Droptail embodies a unique vision realized through Rolls-Royce’s Coachbuild process, spanning over four years. Designers meticulously interpreted the client’s personal tastes, integrating elements of modernity, natural materials, and precision. The result is a minimalistic masterpiece that resonates deeply with the client’s aesthetic and has become a benchmark for their future commissions.
Coatings give a car more than just long-lasting protection. Brilliant gloss and innovative colors transform contours into dynamics and design into emotion. Lines and curves are united and edges and contours are brought to life. When color and shape come together, and paint evokes passion, it’s because at BASF, we create chemistry.
www.basf-coatings.com
DL-based solution significantly optimizes the corrosion evaluation process, providing objective and reliable assessments of corrosion severity in a fraction of the time compared to manual evaluations.
SPECIAL ISSUE ON AUTOMOTIVE AND TRANSPORTATION
Ana Bermejo Escudero and Hendré Swart
BASF Coatings: Global Technology OEM Digitalization and Automation
Enrique Alcalde Grau
BASF Digital Solutions: Analytics and AI - Advanced Imaging
A team of researchers from BASF Coatings and BASF Digital Solutions Divisions has developed an automated method based on Deep Learning (DL) to replace traditional manual evaluations that are laborious and time-consuming.
The automotive industry is an essential industry sector that encompasses the design, production, and sale of vehicles. With the increasing demand for durability and longevity of vehicles,
Original Equipment Manufacturers (OEMs) focus heavily on corrosion
protection. Corrosion can cause severe damage to vehicle components, leading to reduced performance, safety concerns, and costly repairs.
One of the methods employed by OEMs to combat this issue is the application of an E-Coat, or cathodic electrophoretic deposition.
The E-Coat layer, in combination with the pre-treatment layer, provides a barrier against corrosion and enhances the lifespan of vehicles, making it a standard choice for corrosion protection.
To ensure the effectiveness of the E-Coat for corrosion protection, automotive manufacturers conduct corrosion testing through accelerated weathering. This testing process involves exposing automotive components or finished vehicles to harsh conditions, including extreme temperatures, high humidity, salt spray, and UV radiation, simulating the effects of long-term exposure to environmental elements. The result of this testing allows OEMs to evaluate their resistance to corrosion, durability, and overall performance under adverse conditions, enabling them to identify potential weaknesses in the corrosion protection system and make necessary improvements to ensure the longevity and reliability of their products.
The evaluation process for corrosion in OEMs relies on manual and visual assessment, which presents several challenges. Firstly, it leads to low repeatability and reproducibility due to subjective interpretations of defect levels by different evaluators. This inconsistency impedes accurate and reliable assessment of corrosion severity. Secondly, the
manual evaluation requires expert knowledge, limiting the pool of individuals who can reliably perform the assessment. Lastly, the manual nature of the evaluation process is time-consuming. Therefore, a clear opportunity exists for the development of an automated and objective approach that enhances repeatability, reproducibility, and efficiency in the corrosion evaluation process.
To address the challenges of manual and visually assessed corrosion evaluation, an automated method based on Deep Learning (DL) has been developed. This DL-based approach replaces the previous labourintensive and time-consuming manual evaluations. By leveraging DL, various corrosion protection tests can now be rapidly and accurately evaluated. This automated method not only streamlines the testing process but also serves as the foundation for the development of a model-based formulation prediction approach. This approach aims to accelerate the development of new E-Coat products, leading to more efficient and effective corrosion protection solutions in the automotive industry.
The implementation of the DL-based solution involved certain steps, as it can be seen in Figure 1, including image generation, annotation,
training, and validation. To create a large dataset of high-quality images of corroded samples, automated image generation techniques were employed. These high-resolution images were carefully annotated with pixel-level resolution, enabling the accurate identification of different corrosion types such as Scribe (DIN EN ISO 21227-3), Stonechipping (DIN EN ISO 21227-2), Filiform (DIN EN ISO 21227-4), and Edge corrosion. By training the DL model on this annotated dataset, the system learned to recognize corrosion patterns with high precision and accuracy. This DL-based solution significantly optimizes the corrosion evaluation process, providing objective and reliable assessments of corrosion severity in a fraction of the time compared to manual evaluations.
Multiclass semantic segmentation is a key technique used in this DLbased solution and offers a detailed identification and classification. Convolutional Neural Networks (CNNs) were employed to extract features and patterns from the input image, allowing for precise classification of each pixel into its corresponding corrosion type class. Figure 2 provides an illustration of the flow of the input image through the convolutional layers to learn features and generate the segmentation output.
The multiclass semantic segmentation architecture, employed in this study, offers advantages over other DL models. It allows for accurate differentiation between multiple classes of corrosion categories in a single step, eliminating the need for the two-step approach that involves
first classifying the types of damage and then applying segmentation only to the area of interest. By performing classification and segmentation simultaneously, it reduces the computational complexity and processing time required compared to the two-step approach. This efficiency is particularly beneficial in scenarios where real-time analysis of corrosion images is important. The inference phase in DL refers to the stage where a trained model is used to make predictions or generate outputs based on new, unseen data. During this phase, the trained multiclass semantic segmentation model calculates the probability for each pixel to belong to each of the corrosion category classes (Figure 2). It is achieved by analysing the learned features and patterns within the input image. By evaluating the probabilities, the model determines the likelihood of a pixel belonging to a specific corrosion class. Subsequently, the pixel with the highest probability is assigned the prediction class, enabling a comprehensive and accurate segmentation of corrosion levels within the evaluated images. After repeating this process for all pixels in the image a mask (Fig. 3) is generated. To ensure accurate segmentation for a wide range of corrosion images, differing considerably in background colour, extent of damage, extent of corrosion etc., the DL algorithm was trained on dataset containing a substantial number of highresolution images.
To measure the performance of the DL-model, the Intersection over Union (IoU) was used. It provides a measure of how well the predicted segmentation aligns with the ground truth (the manually labelled segmentation). The IoU calculates the ratio of the overlapping area between these two regions to the total area encompassed by both regions (Fig. 4).
The IoU score ranges from 0 to 1, where a score of 1 indicates a perfect alignment between the predicted segmentation and the ground truth. Stone-chipping corrosion achieves an IoU score of 0.84, indicating a good alignment between the predicted and ground truth segmentations. Scribe corrosion and filiform corrosion achieve high IoU scores of 0.92 and 0.89,
respectively, demonstrating a strong match between the predicted and ground truth segmentations as it can be seen in Figure 5. However, the IoU score for edge corrosion is 0.64, suggesting the need for improvement the annotation quality or increasing the number of images for training the DL model, since the model is currently inadequately segmenting this type of corrosion.
In the context of future work, it is essential to broaden the scope of the machine learning based corrosion evaluation approach to include a wider range of corrosion scenarios and incorporate face corrosion detection. This expansion will enable a more comprehensive evaluation of corrosion across the overall surface, providing a deeper understanding of its characteristics. Furthermore, leveraging colour analysis techniques becomes crucial in this attempt as it allows for the classification of the diverse types of rust present on corroded surfaces. The coloration of rust can vary significantly, depending on factors such as the underlying metal, its pretreatment, and environmental conditions. By incorporating these techniques, a more refined and accurate assessment of corrosion can be achieved. Besides expanding the different use cases, next steps aim to improve the accuracy and robustness of the current DL segmentation model by exploring various approaches (Figs. 6 and 7). One of them involves leveraging synthetic data, where artificial corrosion images will be generated using techniques such as Generative Adversarial Networks (GANs) or diffusion models. By generating synthetic data, the annotation process, which is one of the most timeconsuming steps for model improvement, could be simplified. This could allow for more efficient training and refinement of the model.
This relevance extends not only to the corrosion cases the model is currently trained on but also encompasses those that are planned to be included in the future.
To further enhance the segmentation model, efforts will be made to increase the number of images per category class. This involves acquiring and
incorporating additional images of the same corrosion cases, to enhance the model’s understanding of different instances and variations within each class. This expanded dataset will contribute to the continuous improvement and advancement of the automated corrosion evaluation.
Another exploratory branch in the context of corrosion evaluation is to combine 3D topographical data with the 2D images to distinguish between corrosion and delamination. By incorporating 3D topographical information, such as surface roughness and height variations, along with the 2D images of the corroded surface, a more comprehensive understanding of the corrosion phenomena can be achieved. This integration of multi-dimensional data can provide valuable insights into the structural integrity of the material and help differentiate between localized corrosion and delamination, which is a separation of layers within the coating layers. By utilizing this combined approach, the accuracy and reliability of the corrosion evaluation process could be significantly enhanced.
In conclusion, the future work in this context contributes significantly to collect quantitative and qualitative data in the context of corrosion. All these advancements have a significant potential to improve accuracy and effectiveness in corrosion assessment, facilitating decision making in the development of new cathodic E-Coat products. This project continues to push the boundaries of knowledge and innovation in this field, driving progress in the pursuit of predictive coatings formulations (Fig. 8).
Figure 6 - To address the challenges of manual and visually assessed corrosion evaluation, an automated method based on Deep Learning (DL) has been developed.
Figure 7 - Besides expanding the different use cases, next steps aim to improve the accuracy and robustness of the current DL segmentation model by exploring various approaches.
Figure 8 - This project continues to push the boundaries of knowledge and innovation in this field, driving progress in the pursuit of predictive coatings formulations.
via E De Nicola, 18 - I-20090 Cesano Boscone (MI) Italy - tel +39 0255210608 www.ravarinicastoldi.it - dive@ravarinicastoldi.it
Ilaria Paolomelo ipcm®
When coating carbon-fibre components for premium cars, flawless cosmetic finishes and excellent corrosion and weathering resistance are vital. This challenge recently prompted Novation Tech, one of Europe’s leading manufacturers of carbon fibre and composite components, to install a new coating plant. For this ambitious project, it turned to a pool of leading companies in the industrial coating sector: Linea Eco Air for designing and installing the plant, SE.PO. for the conveyor, and CMA Robotics for robotic application equipment.
In the last few years, the automotive sector has been witnessing the increasing adoption of advanced materials such as carbon fibre and composite materials. These are especially valued for their outstanding mechanical properties, such as lightness, tensile strength, and stiffness. The reduction in overall vehicle weight achieved by using
them contributes to improved performance and energy efficiency and also reduces CO2 emissions, making cars more environmentally friendly. However, the coating of carbon fibre components poses a unique challenge in the automotive industry, as the surface treatment of composite materials calls for specific processes to ensure optimal paint
adhesion and long-lasting protection against external agents. Unlike traditional metals, carbon fibre composites require meticulous surface preparation, which may include cleaning, sanding, and the application of special primers to ensure optimal adhesion of the coating. Finishing quality and aesthetics are also fundamental prerequisites, especially for parts intended for high-end cars – such as those handled by Novation Tech, a leading carbon fibre and composite component manufacturer. “To meet the high aesthetic standards of premium car manufacturers, finishes must be flawless, free of defects such as microbubbles, and perfectly uniform. Aiming at successfully meeting these challenges, Novation Tech has entrusted Linea Eco Air (Sona, Verona, Italy) with the installation of a new coating system that will enable us to improve process control, guarantee superior finishing quality, and increase production efficiency,” says Beatrice Buziol, Novation Tech’s Sustainability and Marketing Manager.
Founded in 1967 in Montebelluna, in the province of Treviso (Italy), Novation Tech started out in the metal moulding sector and later specialised in special alloy machining and plastic injection. “2007 marked a significant turning point in our company’s history. After developing and installing several state-of-the-art production technologies, we created the first carbon fibre backrest for sports cars. This success prompted us to invest further in new processes and improved technologies, as well as enabling it to reach new markets: in 2011, we opened a production site in Hungary, and in 2019, we started construction of a plant in Croatia, operational since 2020,” states Beatrice Buziol.
“The automotive industry is our core business, accounting for 92% of our turnover. The production of components for the aerospace and sports & leisure sectors accounts for the remaining 8%,” explains Gabriele Tiveron, Key Account Automotive at Novation Tech. The technological expansion continued in 2021 with the opening of a new, fully integrated department for manufacturing components in various materials using four different 3D printing technologies. In mid-2022, the company also renovated two factories in Trevignano (Treviso), achieving the same production capabilities as the Montebelluna site and creating an advanced robotics hub, as well as installing the Group’s first complete coating line.
Today, Novation Tech employs more than 1400 people across 5 locations and is one of Europe’s leading manufacturers of carbon fibre and composite components for a variety of industries. “Constant R&D activity and technological innovation, combined with streamlined production management, have enabled Novation Tech to become a reliable partner for the world’s biggest automotive brands, able to quickly meet market needs and always offer top-notch products,” emphasises Tiveron.
The production process of carbon fibre components
“Since 2007, Novation Tech has been a supplier of various car elements for major automotive groups – seats, interior and structural components, body parts, and so on. Their production process is highly specialised and accurate as the automotive industry is extremely demanding and regards high quality and precision as top priorities,” notes Tiveron.
Novation Tech’s manufacturing cycle starts with developing a master model and preparing a pre-preg material kit. These are followed by lamination, i.e. the manual positioning of carbon fibre layers on the mould, a delicate phase that requires great care and expertise. The parts are then placed inside the autoclave, the heart of Novation Tech’s production process. Inside it, the components undergo a polymerisation cycle lasting 4 hours at 140 °C and 6 bars. That ensures even pressure and temperature distribution, vital for the correct polymerisation of carbon fibre materials and the production of top-quality components. After polymerisation, the carbon parts are removed from the mould using special equipment, and each workpiece is carefully inspected and checked for compliance with its drawing. “The process continues with milling, where the parts are placed on a template and finished with extreme precision, and glueing with any plastic or metal parts, if required by the project specifications. Before coating, the parts undergo
a mechanical pre-treatment that includes sanding, sandblasting, and thorough cleaning to remove release agents and residues deposited during the previous processes. Glueing and sanding can be done manually or by a robot to ensure perfect adhesion of the different parts and consistent surface preparation,” explains Tiveron.
Novation Tech’s new coating system, installed by Linea Eco Air, was designed to paint car exterior components such as skirts, bonnets, and bumpers. The cycle begins with a deionisation phase that removes dust particles and residues deposited during previous stages through air jets. The components then enter the manual primer application booth and, subsequently, the flash-off area, where they are heated at 40 °C for about 25 minutes. “This booth has a suction wall to ensure the airflow is
horizontal and the operator is never hit by overspray. In addition, to ensure safe operation, we have installed a foot pedal that allows each workpiece to be moved to its optimal position and locked before application. Until the workpiece – usually with a length of over 2 metres – is brought back to its initial position, the conveyor does not move to prevent it from colliding with the line’s components,” illustrates Gianfranco Soliani, the owner of Linea Eco Air. The following two coating booths, devoted respectively to applying the first clear coat layer and a coloured or a second clear coat layer depending on customer specifications, are equipped with an articulated robot model GR 6150 HW supplied by CMA Robotics (Pavia di Udine, Udine, Italy). Painting
The deionisation phase removes dust particles and residues deposited during previous stages through air jets.
The primer application booth is equipped with a suction wall and a foot pedal to move each workpiece to the optimal position for the operator.
Clear coat application with an articulated robot provided by CMA Robotics.
products are supplied by Vernici Caldart (Cagnano, VI) and PPG (Quattordio, AL).
“These two automatic booths are also devised to ensure maximum operator safety, thanks to an alarm system that automatically stops the robot if someone accidentally accesses them. In addition, pneumatic doors avoid any risk of contamination between one area and another,” says Soliani.
“The robot offers great flexibility of use thanks to the special configuration of its hollow wrist, which makes it easy to reach every surface area by rotating each axis more than 360°. For programming the work cycles, a point-to-point system is used, consisting of detecting and processing some geometrically relevant points on the surface to be coated by
special software. Corrections can be made at any time to points, speed rates, connections, and process parameters. The programmes are stored and managed by a computer integrated into the control desk, and they are sorted by alphanumeric codes on Compact Flash storage devices. They can be selected manually with a standard keyboard, with a quick search system, or automatically through remote control,” explains CMA Robotics’ Sales Manager, Marco Zanor.
“Between the two application booths is another flash-off station heated by natural gas generators with an air stream burner. Finally, after the application of the second coat, the components enter the baking oven, where they dwell for about 45-50 minutes, and then the forced cooling area, where we use air taken from outside to reduce their surface temperatures so that the operator can easily handle them in the unloading phase,” says Soliani.
“The plant is equipped with an inverted monorail conveyor featuring a trolley with four weight-bearing wheels. This compact configuration allows handling parts while maintaining a high level of stability of the conveyor, both during transport along the track and during rotation and
coating in the booth. The components treated by Novation Tech range from 2 to 2.5 metres in length, so we had to find a solution to handle such large parts without causing vibration or swinging, which could create defects in the coating layers,” indicates Marco Pozzi, the owner of SE.PO. (Olginate, Lecco, Italy).
The new coating line was conceived to meet the company’s need for a guaranteed coating cycle time and number of treated parts. That is why Novation Tech opted for a step-by-step system, unlike most automotive plants built with a continuous-flow conveyor. “We initially agreed that our ideal takt time was 5 minutes, but we soon realised that with this system, we could reduce it even further, thus improving performance. In addition, a step-by-step system ensures greater consistency and precision in coating,” adds Tiveron.
The new line was also designed to ensure meticulous process control, which is essential to finish exterior components that must meet strict aesthetic and functional parameters, as well as having excellent
corrosion and weathering resistance properties.
“In the high-end automotive industry, the finishing of components is of crucial importance. The level of quality required by our customers is extremely high since we work with leading high-end car manufacturers,” emphasises Tiveron.
Novation Tech reworks about 20% of its coated components, confirming the importance of its finishes’ appearance. “At the beginning of a project, we agree with the customer on so-called “quality books”, which define the maximum number of acceptable defects, such as microdots and microinclusions. If the defects exceed that number, the part is sanded and re-painted. At the end of the coating cycle, the components are inspected under special light tunnels where the operators check the uniformity of the paintwork, which must be free of defects such as vibration-related issues
or holograms. We also subject them to rigorous mechanical and ageing tests, such as climate, salt spray resistance, and water immersion tests.”
Novation Tech has always been committed to sustainability and environmental protection. In 2023, it took a significant step forward in this area by investing in photovoltaic systems for its plants in Italy and Hungary to reduce energy consumption and carbon footprint. Such a focus on sustainability is also evident in the design choices made for the new coating plant. “We decided to use an air stream burner instead of one with a combustion chamber because this solution significantly reduces fuel consumption. Air stream burners do not have a combustion chamber or a flue-gas stack, which allows recirculating all energy within the system and
From left to right:
Components inside the drying oven.
The plant is equipped with an inverted monorail conveyor designed by SE.PO., featuring a trolley with four weight-bearing wheels.
only using exhaust fans to maintain a healthy environment. In addition, we have installed rotating bells on the robots to reduce emissions by 30-40% and improve paint consumption efficiency through electrostatic technology. These choices clearly demonstrate our commitment to promoting more sustainable and environmentally friendly production practices,” notes Buziol.
A successful partnership
“We decided to install this new coating plant because we needed to equip our factory with an articulate and advanced production structure as a key to improving the aesthetic and functional quality of our products’ finishes. The limited space in our facilities had always prevented us from setting up a complete coating system, forcing us to use body shop booths. However, with the increasing production volumes and the need to solve some quality issues such as bubbling
and cissing, we took the opportunity to equip ourselves with a suitable line when we acquired the new factory in Trevignano.
“This new space has allowed us to install an automated system ensuring strict control of all process stages. We turned to Linea Eco Air, with which we had already collaborated in the past and of which we appreciated the expertise in the finishing sector. Its collaboration was fundamental, as we defined and designed every detail of the system together. In this company, we have found an attentive partner capable of understanding and meeting all our needs. Its technical team proved to have great knowledge of coating processes, helping us approach a field we knew only superficially and guiding us in every decision. Results to date include higher finishing quality and greater control over our end products’ quality. With the plant soon to be fully operational, we also anticipate a significant increase in productivity, which will further strengthen our ability to meet any market demand,” concludes Tiveron.
Jörg Robbin
Eisenmann GmbH, Böblingen – Germany joerg.robbin@eisenmann.com
Charbel Sleiman
EISENMANN Inc., Greenville (SC) – United States charbel.sleiman@eisenmann.com
The Eisenmann VarioShuttle XL allows maximum flexibility in pre-treatment and cataphoretic dip coating at Volkswagen Commercial Vehicles.
Pre-treatment (PT) and cataphoretic dip painting (E-Coat) are the cornerstone of the complex automotive painting process. Already here, details are crucial for a smooth production process and a high-quality coating. This requires special and sophisticated conveyor technology that is designed to meet the specific requirements of the car bodies and the production process.
Today, the German company Eisenmann GmbH headquartered in
Böblingen, has the world’s largest portfolio of conveyor systems for PT/E-Coat processes in automotive manufacturing and for general industries.
Since every customer requires a solution that is individually tailored to his needs in terms of capacity and workpiece geometry, Eisenmann offers its customers a total of six possible conveyor systems for PT and E-Coat. These include Power & Free systems, simple pendulum
conveyors and electric overhead conveyors, but above all, the three flexible rotary immersion systems E-Shuttle 200, E-Shuttle 300 und VarioShuttle.
Volkswagen Nutzfahrzeuge is using a further developed version of the proven VarioShuttle series. While these systems were previously designed for car bodies weighing up to 1,000 kilograms, the newly developed VarioShuttle XL can now handle payloads of up to 2,000 kilograms. The VarioShuttle XL allows the car bodies to be rotated during the immersion process and can transport them through the process tanks. Each VarioShuttle XL has its own onboard control unit, which allows the immersion curves to be individually and optimally programmed for each body type and process tank.
This feature is important for the success of the project in Hanover, as it allows large vehicles such as light commercial vehicles or vans to be transported through the PT and E-Coat process without any problems. This is where the VarioShuttle XL proves its versatility.
As a leading manufacturer of light commercial vehicles, Volkswagen Nutzfahrzeuge (VWN) focuses on the clean and sustainable transport of goods, people and services. At three locations, around 24,000 employees produce the Transporter, Multivan, Caddy, Crafter and, from
May 2022, the all-electric ID. Buzz. VWN is also the Volkswagen Group’s leading brand for autonomous driving.
The versatility of the models requires production facilities that always meet the highest standards. This also applies to the paint shop, where the manufacturer has launched an extensive project. After 28 years, the time had come to renew the technology from the ground up, explains the plant planner at Volkswagen Nutzfahrzeuge: “To ensure our future viability, we decided about two years ago to bring the paint shop up to date. In addition to pre-treatment (PT) with eleven pre-treatment tanks and cataphoretic dip coating (E-Coat), the project also includes dryers and ancillary equipment, such as for waste water management. The new paint shop works extremely resource-efficient and ensures that process times are met“, says the project manager.
In order to guarantee the desired requirements for productivity and paint quality, the strengths of various system manufacturers were combined and integrated into a tailor-made concept for the new paint shop at VWN. Conveyor technology from Eisenmann GmbH, for example, now ensures that the car bodies move safely and efficiently through the surface treatment process.
Jörg Robbin, Head of Research and Developement at Eisenmann,
emphasizes the proven technology and production reliability of the VarioShuttle, whose basic technology has already been tried and tested in many applications: “Existing VarioShuttle systems can be retrofitted with the XL version at any time. Parallel operation of different shuttle versions is possible. The Eisenmann engineers have incorporated a great deal of experience into the development, for example, the E-Coat cables are located inside the shuttle housing. This enables current transmission of up to 1,000 amperes. We rely on a proven sealing system, a moisture sensor in the pendulum and do not need to pressurize with compressed air. The key priority was to combine proven technologies with advanced new developments, while maintaining unrestricted high availability,” continues Robbin.
The VWN project manager emphasizes that the commercial vehicle sector in particular requires maximum flexibility.
“Previously, our bodies went through PT and E-Coat treatment in a pendulum curve. Now we can also run model-optimized, individual rotation curves. This process guarantees the highest coating quality for all body variants.
At Volkswagen Nutzfahrzeuge, for example, the immersion curve can be adjusted at any time as required, with simulation and process control playing a key role. Eisenmann operates a test setup for the VarioShuttle XL at the headquarter in Böblingen, Germany, puts the system through its paces and also provides software support.
The VarioShuttle XL thus reflects Eisenmann’s efforts to keep proven products up to date and at the same time to be a pioneer in the field of innovative painting systems and conveyor technology. The aim is to create high added value for the user”.
CHEMTEC’S technologies are designed to have a very limited environmental impact, to reduce consumption of resources and for a greater operational simplicity.
CHEMTEC develops customized solutions that aim to maximize the customer’s satisfaction.
NANOTECHNOLOGICAL CONVERSION COATING
WATER PURIFICATION AND RECIRCULATION
ONE STEP METAL PRETREATMENT
PAINT STRIPPERS
DISCOVER MORE ON WWW.CHEMTEC.IT
SPECIAL ISSUE ON AUTOMOTIVE AND TRANSPORTATION
Marie-Anne Guilldou
SAMES – Pioltello (Milan) marie-anne.guilldou@sames.com
The paint shop is a critical stage in vehicle production where throughput, quality, and sustainability must be meticulously balanced. Paint application specialist, Sames has identified key areas for improving efficiency in vehicle exterior paint application.
Opportunities for enhanced efficiency
Sames has concentrated on vehicle exterior paint application to increase transfer efficiency. Over the past decade, advancements in paint shop technology have resulted in robot speeds exceeding 1 meter per second as manufacturers strive to enhance throughput and minimize the number of robots in use. However, these improvements necessitate
higher paint flow rates, increased bell cup rotation speeds, and more air control flow, which ultimately reduce paint transfer efficiency.
Sebastien Salze, Business Development Specialist – Automotive at Sames, highlights the potential for significant improvements. “We believe we can enhance transfer efficiency by ten points for exterior painting robots, effectively halving the overspray.
Current transfer efficiency for exterior body painting is between 70-80%, but we aim to achieve up to 90%. This improvement also considers material and energy costs, as reducing overspray conserves materials and lowers the energy needed to capture it with air downdraft systems. We’re working on upgraded sprayers to enable a more efficient and low-energy painting process.”
Sames, in collaboration with global paint shop integrator partners, has identified the significant potential for improving paint transfer efficiency. Their initial approach focused on optimizing the best possible scenario by reducing the paint flow rate, bell cup rotation speed, and air control flow. This also involved decreasing the spray nozzle distance to the car body and the robot speed. In partnership with a paint supplier, Sames adjusted paint conductivity to achieve optimal electrostatic effect and efficiency. Although the results were impressive, the adapted process wasn’t feasible for high-volume production due to the need for more robots and increased paint booth footprint. Consequently, Sames developed process and applicator technology that aligns with standard robot speeds and existing paint shop configurations, simplifying the retrofitting of existing paint shops for improved efficiency.
Salze explains, “With our spray systems, only the bell cup and the air shroud need to be changed, adapting the air control to maintain the pattern. We’ve validated our system at a robot speed of 500 mm per second and reduced the nozzle distance to the car body by 50%, from 200 mm to 100 mm. The main challenge remains maintaining the same film build quality with a slower bell cup rotation speed while using less air and energy.”
Another significant challenge is reducing the
down draft air velocity in the paint booth, which offers substantial energy savings but is not as simple as just reducing airflow. Sames collaborates closely with other stakeholders in this sector to address this issue. The ventilation equipment in paint booths is designed to meet specific requirements and sizes, so downsizing the existing ventilation system might be necessary for the low energy approach.
ATEX zoning presents additional challenges, particularly where reduced airflow may increase solvent build-up in certain paint operations. To comply with regulations, OEMs must introduce external fresh air into the booth to reduce solvent concentrations. By reducing overspray, the percentage of external air (which needs heating) required decreases. Sames has validated the low overspray, low downdraft process with paint shop ventilation system suppliers to address potential ATEX zoning issues.
Salze explains, “I calculated that by increasing paint transfer efficiency by ten points to 90%, we could reduce downdraft air velocity by a third and still lower solvent concentration in the booth. This could decrease solvent
concentration to 19% of the explosive limit, enhancing safety and efficiency.”
Sames is also addressing the specific requirements of different substrates in their development process. “Initially, we focused on clear coat for vehicle bodies. Next, we’ll work on primer, where film build quality is less critical than thickness. The base coat presents challenges due to metallic particles requiring precise air alignment. For nonmetallic base coats, we have a promising solution for existing two-tone paint booths, typically used for roof sections in black or white. This technology can be applied to both base and clear coat stations, allowing for easier downdraft reduction in smaller booths compared to older single painting lines with large air ventilation systems. We plan to test this process with a plastic manufacturer this summer,” notes Salze. By focusing on enhancing paint transfer efficiency, Sames is paving the way for more efficient, cost-effective, and sustainable vehicle paint applications.
Ilaria Paolomelo ipcm®
A European leading company in the production of plastic components has recently turned to Varnish Tech/ Trasmetal to install a new automatic liquid coating line. This investment will enable the company to coat bumpers and other exterior and interior plastic car components with superior quality and absolute control over the entire finishing cycle.
Outsourcing is a business strategy based on which a company entrusts external suppliers with the management of certain production activities or processes. This practice has become increasingly popular in various sectors, including industrial coating, thanks to its many advantages. Above all, these include reduced operating costs, as companies can take advantage of the economies of scale of specialised providers, and increased efficiency, resulting from access to advanced skills and technologies that may not be available in-house. Outsourcing also enables to focus on one’s core competencies while improving operational flexibility and responsiveness to market dynamics.
Trasmetal/Varnish Tech has supplied a new coating system for automotive components.
Another significant advantage is risk management: by outsourcing certain functions to suppliers, companies can mitigate the risks associated with investing in expensive infrastructure and technology. Moreover, the risk associated with human resource management and staff training can be transferred to the supplier company, which already has expert staff with the necessary skills. On the other hand, despite all these advantages, outsourcing can also bring some challenges, including the potential loss of direct control over quality and production times and the company’s dependence on suppliers to meet the required deadlines and quality standards. A European leading manufacturer of plastic components for the automotive industry outsourced its coating phase until very recently. However, the acquisition of new important projects, the increasing demand from major automotive groups and the need for greater control over quality and production volumes prompted it to reconsider this strategy. The decision to install a new liquid coating plant for the automotive components manufactured within their factory represented a
significant step towards production autonomy, allowing it to manage its entire production process in-house and meet even higher quality standards.
“The new coating system is a key element of our company’s global strategy, aimed at strengthening our presence in Eastern Europe, where the automotive sector is rapidly expanding. Providing our customers with a comprehensive service, which includes painting, is essential for positioning ourselves competitively in the market,” says Graziano Macchiarolo, the Technical Painting Manager of the company. For this ambitious project, this enterprise chose to rely on Varnish Tech, a company now merged with Trasmetal (Milan, Italy), for the design, construction, and installation of a new coating plant for exterior and interior plastic car components. Trasmetal also used technologies produced by other Italian companies: SE.PO. (Olginate, Lecco) supplied an inverted power & free conveyor and Water Energy (San Pietro in Casale, Bologna) the booth water treatment plant.
The coating cycle of plastic components
All plastic components, including bumpers, mudguards, and skirts, are produced and painted within the company’s factory with an advanced and well-structured manufacturing process designed to ensure the highest quality and compliance with the car industry’s rigorous standards. The cycle begins with the plastic moulding phase, followed by assembly. The assembled components are then manually loaded by operators onto the new coating line and subjected to a pre-treatment phase that is crucial for removing the dust particles generated in the previous processing steps. It includes four stages:
hot cleaning,
a first rinse with mains water,
a second rinse with mains water,
and a final rinse with demineralised water.
The latter is produced with a Water Energy WO2000 2,000 l/h reverse osmosis unit, allowing to discharge less than 25% of the mains water used with a permeate quality of less than 10 microSiemens. After leaving the pre-treatment tunnel, the parts pass through a blow-off station equipped with 2 robots, which are only activated when necessary, for example when there is excessive water in the components’ cavities. This is followed by a drying phase inside the oven, where the components dwell for about 35 minutes at a maximum temperature of 80 °C, and possibly a flame hardening
phase. “The flame hardening robot only comes into operation when treating polypropylene materials, whereas ABS parts do not need to be subjected to this operation,” indicates Varnish Tech/Trasmetal General Manager Luca Maitan.
The components are transported via a floor conveyor first to the primer application booth, then to the coloured topcoat application one, and finally to the clear coat application one. SE.PO. provided a continuous-flow power & free conveyor characterised by a large crosssection to prevent the components from swinging, even at the switch between the two lines.
“Each booth is equipped with 2 ABB IRB 5550 robots, which are highly flexible and ideal for the automotive industry: they guarantee shorter cycle times and optimised processes and have a digital platform ensuring excellent coating quality and time savings. The robots are complemented by bells and guns specifically designed to achieve high productivity rates in automatic coating operations. Each coating booth is followed by its own flash-off tunnel where the material dwells for about 15 minutes, under thermo-hygrometric conditions that allow most of the solvent in the coating film to evaporate to ensure the end products are free of defects,” adds Maitan. Due to structural limitations that prevented excavating a deep foundation pit, the booths were raised to overcome construction issues without compromising operational efficiency.
After coating, the components dwell for 40 minutes at 80 °C in the 40-metre-long baking oven, structured exactly like the drying one. The coating cycle ends with natural and forced flash-off phases. Finally, the components are unloaded manually by the operators, polished, tested, and prepared for shipment to car manufacturers worldwide.
The new coating line supplied by Varnish Tech/Trasmetal is designed to achieve a production capacity of 60 frames/hour with a maximum size of 2.2 metres in width and 1.7 metres in height. “The objective of this new finishing plant was to increase our degree of coating quality but enable us to meet the needs of the automotive sector in terms of production volumes and delivery times,” notes the Plant Operation Manager.
The pre-treatment system consists of a tunnel and tanks made of AISI 304 stainless steel, which was also used for the pipes, manifolds, and vertical pumps. The 35-metre-long drying oven consists of a tubular structure with walls and a ceiling made of sandwich panels with rock wool to minimise heat loss. Its temperature is electronically controlled by probes, and air exchange is ensured by centrifugal electric fans,” illustrates the General Manager of Varnish Tech/Trasmetal. “The coating application area, located within a clean room to prevent the presence of dust particles larger than one micron, is characterised by three airconditioned booths with air exchange and high-efficiency wet filtration units, each connected to its respective flash-off tunnel.
“In addition, the plant is equipped with 3 paint management systems, each located adjacent to its respective booth: the primer management system has 2 paint feeding units, the base coat one has 10 onecomponent paint feeding units, and the clear coat one has 3 paint + hardener feeding units. All the paint management units also include a solvent circuit and are fed with fresh air from the line’s primary air handling unit (AHU) to ensure adequate air exchange.
“A further distinctive element of this coating line is its management system, which Varnish Tech developed on the Siemens S7 platform. The interface is user-friendly, allowing controlling all parameters and recording all events. It is an open system, and it can be managed remotely via VPN and integrated into Profinet networks for secure communication with coating systems and other machines.”
The new coating line is a model of efficiency and sustainability, also integrating advanced technologies for air and water treatment. One of its strengths is its booths’ efficient wet abatement units featuring Venturi systems. After being filtered and brought to the required thermo-hygrometric conditions, the air is conveyed into the plenum space on the booth’s roof. It undergoes further filtration and is then diffused evenly in the coating chamber below. During its downward motion, the air passes through the operating area, carrying away the particulate generated during coating and ensuring continuous chamber cleaning. On its way to the abatement unit, the resulting air-particulate mixture impacts an air curtain barrier, accelerates in the Venturi zone, and finally reaches the settling chamber where the finest particulate is released. Finally, the air is sucked in by the AHU, where the correct thermo-hygrometric conditions are re-established,” explains Maitan. The plant boasts the presence of 3 central air handling central stations for air recirculation in the coating booths and a primary air handling central station for air exchange and feeding to the paint management units. The chiller, producing chilled water for the AHUs’ cooling coil systems, is located outside, close to the AHUs themselves, to ensure adequate cooling of the evaporator; it is also equipped with a heat recovery system that provides hot water to feed the heating coil system, allowing significant savings in energy costs.
The afterburner, located outdoors, uses the solvents in the air for self-feeding, thus significantly reducing purification costs.
This coating line was indeed designed with energy efficiency in mind. Another significant example is the use of an afterburner taking advantage of the solvents in the air for self-feeding, thus significantly reducing purification costs: thanks to effective air recirculation, it achieves a self-sustaining level by burning solvent instead of methane, with a concentration of 3.5 g/m³ of solvent in the air. This innovative system cuts operating costs while improving environmental sustainability.
As for water treatment, Varnish Tech/Trasmetal got Water Energy involved in the project for supplying with 3 Skimmerflot 5000 series sludge separators, one for each coating booth. The treatment process begins inside the booths themselves, where a pump recovers the water and sends it to the sludge separator, designed to separate it from pollutants using micronised air to facilitate flotation and sludge removal. The system guarantees a high degree of cleanliness of the coating booths, with 80% sludge recovery efficiency and a sludge moisture content of less than 40%, as well as dramatically reducing maintenance needs and ensuring smooth operation of the scrubber, also through remote control of the system’s status and product levels via an app that can be installed on the maintenance technicians’ phones.
“This system is designed to reduce energy costs and protect the
environment: with the Re.A.S. (REcycle Air System) recirculation units in the coating booths, heating and cooling costs are reduced by 80 to 90%, and the emission purification cycle is streamlined. Varnish Tech/ Trasmetal also pays special attention to environmental sustainability issues, and energy-saving goals play a primary role when designing our coating plants,” states Matilde Maitan, the Marketing Manager of Varnish Tech/Trasmetal.
Varnish Tech, the protagonist of a merger with Trasmetal last December, had already been collaborating with this leading company active in the automotive sector for a long time, as it had supplied other sites of the Group with numerous systems in the past. “They have been a trusted supplier for many years, so when we decided to insource
coating operations in the new factory, turning to them was a natural choice,” explains Plant Operation Manager. “Having overseen many installations, I can confidently state my satisfaction not only with the quality of the plant and technologies provided by Trasmetal, but also with the technical expertise demonstrated by our supplier,” continues Macchiarolo.
Installed in May, this coating system represented a significant step forward in terms of quality control and process efficiency. “Although it has only been operational for a few weeks and is not working at full capacity yet, we have already had the opportunity to appreciate the quality level of its coating process. The integration of advanced technologies, such as the Venturi and scrubber-based abatement systems, ensures that no contaminants can jeopardise the quality of our painted components,” concludes the Plant Operation Manager.
SPECIAL ISSUE ON AUTOMOTIVE AND TRANSPORTATION
Edited by TIGER Coatings Wels, Austria pimc@tiger-coatings.com
Fiber-reinforced composites (FRP) is the material of the future, characterized by outstanding mechanical and structural properties. Used in a wide range of high-performance applications - for example in the aviation and automotive industries, in transportation and in the field of renewable energies.
TIGER has been using innovative powder-in-mould coating (PIMC) since the early 2000s and has continuously developed this technology. Today, primers as well as base and topcoats are available in all colours of the RAL spectrum for high-quality surface finishing of fibre composites.
For in-mould powder coating, highly reactive powder coating is applied to a preheated press tool, where it immediately begins to gel. The fibrereinforced plastic material is then applied, which can be demoulded as a finished coated component after pressing. This one-step process is compatible with all common release agents and produces resistant
surfaces in Class A quality. TIGER’s PIMC process effectively prevents so-called telegraphing (fibre marking), which can occur on commercially coated fibre-reinforced plastics due to the influence of temperature or moisture fluctuations.
Powder-in-mould coating can be combined with all common technologies for the production of fibre-reinforced plastics, with all thermoplastic and thermoset fibre-reinforced composites (FRC materials) as well as all fibre types and geometries. Even composites with elements made from sustainable raw materials - so-called “bio composites” - are compatible with the process.
PIMC saves costs and reduces environmental impact
Another distinctive advantage of powder-inmould technology is the elimination of time-, energy- and cost-intensive drying phases as well as complex sanding and filling work, which is often outsourced. Components manufactured using the PIMC process are impressively lightweight - despite a high layer thickness of up to 400μm - which promises additional benefits:
By using lightweight parts, the automotive industry can reduce fuel consumption and thus also CO2 emissions, while trains designed with lightweight components cause less wear and tear on the track.
The absence of volatile organic compounds
(VOCs) and the reusability of the overspray also make powder-in-mould coating a “green alternative” for the conventional coating of fibre-reinforced plastics.
An overview of the advantages of PIMC
Fully automated application of the primer and top coat layer to the mould using the fibre-reinforces composites process. No manual preparation of the FRC materials is required.
Excellent adhesion to all thermoplastic and thermosetting FRC-matrix-materials and compatible with sustainable “bio composites”.
Coatings with a wide range of top coats for the automotive, aerospace and sports industries, consumer products and industrial goods.
Robust, durable and elastic coatings with high heat and chemical resistance.
Finished surfaces with consistent quality that meet the requirements for Class A surfaces.
Suitable for injection moulding, compression moulding and the processing of fibre matrix semi-finished products. No intermediate sanding required for most applications.
Sustainable, green technology without volatile organic compounds (VOCs). Powder coating can be recycled and reused in the cycle without compromising component quality.
Carina Lachnit
Dürr Systems AG - Bietigheim-Bissingen, Germany carina.lachnit@durr.com
Paint shops must become “greener” to help vehicle manufacturers feel certain about meeting their ambitious climate targets. Assessing a technology’s sustainability is a complex task. In a comprehensive life cycle analysis, the Fraunhofer Institute for Building Physics (IBP) studied the carbon footprint of two different paint shop concepts. The result: Dürr’s paint shop with the EcoQPower system, which networks all energy flows to supply all process steps, reduces carbon emissions by 19.2 percent over its entire life cycle compared to paint shops without this system. This is mainly due to an energy consumption reduction of about 21 percent in the utilization phase, making it the first paint shop to comply with EU Taxonomy requirements.
Paint shops consume the most energy throughout the entire vehicle manufacturing process since applying paint and drying car bodies are very energy-intensive. Consequently, modern paint shops’ carbon footprints are still significant despite technical progress.
“The EU wants to be climate neutral by 2050. We had this target in mind when we adopted a new strategy on the path to a carbon-neutral paint shop from an energy perspective. Instead of continuously increasing the energy efficiency of individual elements such as paint booths and
ovens, as we did before, we developed the EcoQPower system, which considers all paint shop energy sources and network components, as well as energy flows,” explained Jens Oliver Reiner, Senior Vice President Sales in the Paint and Final Assembly division at Dürr. The new concept analyzes energy sources and energy sinks in operation, considering various operating states and historic climate data. Based on this analysis, the EcoQPower energy network systematically recovers energy in one place, which can then be reused elsewhere.
Significant carbon footprint reduction
Sustainability is often promised, but these promises frequently turn out to be nothing more than greenwashing. Dürr partnered with the Fraunhofer Institute for Building Physics to prove that the first paint shop optimized with EcoQPower being built for a German vehicle manufacturer emits fewer greenhouse gases than a paint shop without the energy network system. The scientists analyzed the effects on the carbon footprint by simulating and calculating the values for two identical, all-electric factories in the same location and with the same performance data – one with and one without an EcoQPower system.
In keeping with the circular economy, the entire life cycle from paint shop production, including the transportation of materials to the utilization phase and the end of life, was analyzed. The Fraunhofer Institute for Building Physics’ study found that the EcoQPower system reduces the carbon footprint by 19.2 percent over this entire period. Since 91 percent of emissions are produced in the utilization phase, EcoQPower enables paint shop operators to run a more climate-friendly business. The investment also pays off in terms of sustainability, with Dürr’s energy consumption analysis confirming that EcoQPower reduces utilization phase energy consumption by 20.6 percent, making the optimized paint shop about 21 percent more energy efficient than a modern standard system. As a result, operators can reduce their energy costs by seven figures over the assumed utilization period of 15 years and 110,000 painted car bodies per year.
EcoQPower is based on the concept that each manufacturing area only receives the appropriate energy and temperature level it actually needs. In a standard paint shop, all process steps, such as pretreatment, the oven, and the paint booth, have been viewed and supplied as individual components until now. For example, excess energy from the drying process that could be applied elsewhere is released unused into the environment. By considering the entire scope, the EcoQPower system delivers real benefits by integrating all waste heat
sources, including those not previously used, and reuses energy at low temperatures. Heat pumps generate heating and cooling energy simultaneously, which is possible because Dürr’s experts measure each paint shop process step’s heating and cooling requirements using proprietary software. With this knowledge, they leverage synergies from the processes and – in combination with resource-saving technology – enable economical energy use.
The EU Taxonomy is an instrument developed under the Green Deal, with the political objective of making Europe the first climate-neutral continent by 2050. By providing a transparent classification of sustainable investments, the regulation aims to ensure that financial resources fund projects that support climate and environmental protection. “Sustainability is becoming increasingly important for companies in the manufacturing sector. We help our customers make their production processes as energy-efficient as possible to achieve their decarbonization targets. We know that companies engaged in sustainable production will have more and more advantages in the long term for sourcing funding in Europe,” explains Reiner.
Monica Fumagalli ipcm®
The main workshops of the SBB (Swiss Federal Railways) in Bellinzona, responsible for the maintenance of the company’s fleet, recently pioneered a significant innovation in the field of booth air treatment. In collaboration with Eurotherm, the Italian plant engineering company that won the tender to supply SBB’s three maintenance sites with new coating systems, they installed a booth with a side extraction system that not only guarantees flexibility and energy savings but also avoids the need for excavations to build a floor system, thus also speeding up delivery and meeting the tight deadlines.
“L’arrivée d’un Train en Gare de La Ciotat” by the Lumière Brothers, one of the very first films screened in public in 1896, is a 45-second short showing the arrival of a train pulled by a steam locomotive at the railway station of the coastal town of La Ciotat, near Marseille, in France. Legend has it that some spectators in the auditorium, attending a film screening for the first time, ran away because they were frightened by the illusion of a moving train seemingly about to come out of the screen.
It was with these early experiments that the history of cinema began. But why did the Lumière Brothers choose a train as the subject of their first cinematographic endeavours? Because the train was, and still is today, synonymous with movement, speed, and... innovation. The construction of railway networks travelled by freight trains and passenger carriages in the first half of the 19th century changed the economic and social face of the industrialised world of the time, speeding up connections and expanding geographical horizons.
Today, the country that holds the record for train travel in Europe is Switzerland. According to one of its latest press releases1, Schweizerische Bundesbahnen AG (SBB), the public company controlled by the Federal Council that acts as the infrastructure manager and principal operator of this nation’s rail network, ended 2023 in the black for the first time since 2019, in the pre-Covid period, thanks to a new record number of travellers.
The rolling stock owned by SBB, which includes electric multiple units, freight wagons, and special-purpose infrastructure vehicles, reflects the diversity of an integrated railway company. “The train,” the statement reads, “is a climate- and land-friendly means of transport and will continue to play a central role in the global mobility of the future. At the same time, due to increasing demand, the capacity of railway nodes and the complexity of the system are reaching their limits. In order to meet these challenges, based on the RAIL 2050 perspective formulated by the Federal Council, SBB is developing a long-term strategy for its railways, which will ensure more flexible, frequent, and fast connections.”
To ensure such growth, however, the light and heavy maintenance of rolling stock calls for enhanced technologies and structures to guarantee the resistance of components against corrosion and wear and prolong their use as much as possible. Railway rolling stocks and their components are exposed to the atmospheric agents of the
1 https://news.sbb.ch/it/media/articolo/127444/ffs-di-nuovo-in-attivo-grazie-al-record-di-viaggiatori
environment in which they operate, temperature changes, and humidity: therefore, if not adequately protected, they are subject to corrosion that can cause damage and, in the worst cases, even serious accidents. To avoid this risk, rolling stock must be protected with specific treatments enabling it to withstand corrosive stress throughout its entire nominal service life. Therefore, appropriate design and maintenance solutions must be chosen to achieve effective corrosion protection.
“Most of the work we do here, at the Bellinzona SBB workshops,” says Marco Siccardi, Project Manager of SBB (the German acronym by which the Swiss Federal Railways are identified), “relates to the heavy maintenance of railway vehicles. That means carriages and components must wait here for months for the maintenance activities to be completed as planned, in contrast to light maintenance, where partial intervention is possible each time a convoy reaches the station until completion.” When a train reaches the workshop, it is disassembled, and the wagons and other components are subjected to various repairs, including recoating. “One of our most recent investments was for a new liquid paint application and drying booth. Our company put out a public tender, which was won by Eurotherm Spa (Volpiano, Turin, Italy). This Italian company thus supplied us with a flexible plant with a totally innovative side extraction system.”
In 2023, the rolling stock owned by SBB amounted to 691 electric trains, 219 shunting locomotives, and 172 selfpropelled special-purpose infrastructure vehicles, totalling 1,916 passenger carriages and 4,518 freight wagons2. “SBB has three train maintenance industrial hubs in Olten (one of the most important railway hubs in Switzerland, where mainly passenger trains are maintained), Yverdon-les-Bains (in the canton of Vaud), and here in Bellinzona, where maintenance work is carried out on passenger trains,” explains Siccardi. “Our rolling stock maintenance department is located underneath the railway station, from where convoys of a minimum of 7 and a maximum of 11 carriages travel directly to the underground floor along a track built especially for this purpose. We perform maintenance on all kinds of internal and external components.”
After the total dismantling of the wagons, the required restoration work mainly related to corrosion issues and any modifications are carried out, followed by shot blasting, recoating with water-based paints, and drying, before final reassembly.
“The Bellinzona SBB workshops,” Siccardi notes, “will be soon relocated from this long-standing site to a new area. After more than 135 years of activity in the heart of Bellinzona, the need has arisen to relocate the structure, which is no longer suited to meet the new requirements of the transport sector in the long term. After careful consideration, the choice of the new location fell on an area in the municipality of ArbedoCastione, located a short distance from Bellinzona. That will free up a large area of around 120,000 m2, where around 500 people are currently employed, offering the chance to build a model district from scratch that will transform the surface currently occupied by the SBB workshops into a driver for the city’s urban development. At the same time, the new premises in Arbedo-Castione will allow a wide range of work to be carried out, with a focus on light and heavy maintenance of rolling stock, especially in the passenger train sector. With this project, SBB intends to build a new industrial hub that is socially, environmentally, and economically sustainable.”
2 https://reporting.sbb.ch/en/rolling-stock?highlighted=&scroll=700&sv_ lang=3&sv_lang_change=true&years=1%2C4%2C5%2C6%2C7
SBB had put out a tender for installing new coating booths in Olten and Yverdon-les-Bains and building two coating plants on the new site in Arbedo-Castione. Siccardi confirms: “No new booth was intended to be acquired for the Bellinzona workshops because, with the site expected to be decommissioned, it would have made no sense to invest in a new system at the moment. However, since the beginning of 2023, we have been working on a renovation project for the Astoro fleet, a group of electric trains undergoing a wide-ranging renovation, upgrading, and recoating process whose completion is scheduled for 2027, and we needed to upgrade our paint shop to do this with excellent results. We had initially considered installing an inexpensive booth with essential features precisely because of the temporary nature of the plant, but we soon realised that we could not have achieved the required level of quality and, therefore, opted for a more professional system.”
The new Eurotherm booths were to be installed first in the workshops in Olten, then in Yverdon-les-Bains, and finally in the new plant in ArbedoCastione. However, as Siccardi illustrates, “the workshops in Bellinzona
urgently needed one, so we required it before the other maintenance sites: we started working with Eurotherm in October 2023, and on 1 May 2024, the booth was already installed at our premises.” That was also possible thanks to an innovative feature designed by this Italian plant engineering company: the booth’s side extraction system enabled to avoid excavations for the construction of a floor system, as is typical with this type of booth, thus speeding up delivery times.
“The liquid paint application and drying booth we designed and installed at the Bellinzona industrial workshops,” states Eng. Davide Quartana, Project Manager at Eurotherm, “was conceived specifically for the railway sector and can accommodate both components and actual carriages. The challenge the customer presented us with was twofold: it required a flexible solution to coat different types of rolling stock, and it wanted to avoid building work for its construction, since it is a booth for an existing plant. Our technical team, therefore, customised the line by equipping it with a side extraction system partitioned into three distinct sectors:
a series of extraction walls with a total length of 34 metres on both sides virtually divides the booth into three segments, each managed by an air handling unit (AHU) to guarantee recirculation over the three zones with the possibility of managing each zone independently. During coating, the operation of the extraction system is constrained by the operator platform’s positioning, which means that only two of the three available air handling units are active at the same time. Moreover, in addition to the 60 °C-drying function, the booth has a controlled temperature and humidity management system.”
A completely independent extraction system
“After preparing each wagon for the coating stage by cleaning its surfaces and shot blasting them if required,” emphasises Quartana, “the customer applies three colours (white in two coats, blue, or red) and two lacquered layers. Thanks to the extraction system’s advanced 4.0 software, the operators can adjust different parameters to manage the temperature-controlled surface preparation and application phases. Air supply comes from the roof through a plenum space that is also accessible from the platforms to facilitate maintenance work. With this system, air is taken directly from outside the factory, poured into the plenum space via an extractor fan, and introduced by high pressure. The air thus enters the coating chamber and, after being filtered, heated or cooled, and humidified at constant values, it is always expelled outside, creating a cycle that is totally independent of the factory’s internal environment.”
Each of the three AHUs is equipped with an automatic water system to cool or heat the air according to the seasonal outdoor temperatures, so that the booth maintains a constant temperature range throughout the year. “The operator simply enters the parameters from the touch panel of the control PLC to automatically set the required temperature,” indicates Quartana. “The water chiller was designed and manufactured by Eurotherm, whereas hot water is supplied directly by the SBB workshops and distributed to
the various batteries via servo-controlled valves.” Each of the three AHUs is also equipped with a system for controlling the humidity level through an osmosis water plant, which prepares the water to be atomised inside the unit, whereas humidity sensors are placed directly in the plenum space. “Another interesting aspect of this air treatment plant is that, due to its enormous size, we had to resort to a helicopter to place its chimneys outside our building, a procedure that is quite common in a factory with oversized equipment such as the Bellinzona workshops.”
The advantages of the new solution
“In addition to the flexibility of the plant, which enables us to coat any type of rolling stock, from entire wagons to the smallest components, there are two aspects that we particularly appreciated in the design of this booth,” says Siccardi. “One, as already mentioned, is the innovative side extraction system that eliminated the need for excavations to install a floor system – which in an already existing factory is a complex operation and can lead to long production stoppages – thus reducing costs and simplifying maintenance, which can take place at the floor level.
The other relates to energy savings: partitioning the booth into three zones with three independent AHUs means that only two out of three air handling units are activated at the same time, i.e. those in the area where operations are actually taking place, ensuring significant savings in terms of energy consumption.”
Innovation that breaks new ground
“Eurotherm’s team,” adds Quartana, “is going to inaugurate the construction site for the paint shop at the Olten site in October. It will include a shot blasting booth and two coating booths similar to the one installed in Bellinzona but with a floor extraction system. Finally, the Arbedo-Castione plant will have a shot blasting booth, booths for preparing the wagons and components, and two coating booths. The work carried out so far has been challenging due to the tight schedule, and we would not have been able to meet the deadlines and complete the job in the best possible way without the invaluable cooperation of the specialised train maintenance technicians of the Bellinzona workshops.”
Let‘s talk about injector technology. A technology that you should keep an eye on. Actually, it‘s just getting started. And now, Flowsense takes it to a new level. FLOWSENSE? It‘s a software masterpiece and a bunch of small sensors that do big things: Consistent powder output from the rst to the thousandth workpiece. Put quality on repeat! go.wagner-group.com/
“SBB is mobilising to purchase new rolling stock and renew its fleet,” says Siccardi. “The number of passengers and goods handled by our railway network is constantly increasing. For example, this is borne out by the fact that not long ago, we had to carry out major maintenance work on some old carriages that had to be put back on the tracks to cover the morning and evening rush hours at Zurich station. Our work is essential not only to bring these worn-out vehicles back to life but also to ensure their excellent durability. That is why we must be put in a position to work with the best plant engineering and technological solutions, as was done here in Bellinzona. This project was an important turning point because SBB now knows it can take into consideration booths with similar characteristics to the one built here for future investments. This system’s performance is such that we will keep some parts of it in the
new premises in Arbedo-Castione: we plan to move the booth’s external structure there and adapt the machine’s equipment to the new spaces, also to recover a part of our investment.”
More and more people are choosing the train as a means of transport because it is considered more sustainable and convenient for covering long distances than cars or planes. That is why it is safe to predict that the number of travellers and the amount of goods transported by these vehicles is going to increase exponentially in the coming years –and, with them, the required rolling stock. Therefore, its maintenance, upgrading, and recoating will play an increasingly strategic and decisive role, making innovative solutions that can facilitate these interventions indispensable for the sector.
Tensioni residue di compressione prima della pallinatura*: 11 MPa una profondità di of 24 μm
When you look at any car, one of the first things you will notice is its colour. In the belief that “colour is an element of form”, Mazda’s focus on developing colours that highlight the beauty, quality and uniqueness of its Kodo design aims to evoke the same feelings as appreciating a work of art. With a reputation for striking exteriors and award-winning design, Mazda has led the way to bring the beauty of its car design to life through a selection of premium paints that use advanced technology to highlight exterior shape and beauty in a uniquely Mazda way.
The evolution of Mazda’s unique design philosophy – Kodo: Soul of Motion – aims to breathe life and personality into every vehicle. With dynamic shapes that capture the very instant energy becomes motion, flowing body lines that show off the nuances of curves are highlighted by the shifting reflections from the interplay of light and shadow, developing a paint to match this is a complex craft in which designers work relentlessly to stretch the possibility of paint and scrutinise the ideal colour.
Mazda’s approach uses advanced paint technology to create colours with rich depth and radiance that highlight every sensuous curve and line of a car, while also ensuring to reduce the environmental impact of
the painting process in keeping with the brand’s long-term Sustainable Zoom-Zoom 2030 vision1
In a process called, Takuminuri (Takumi: master craftsman, Nuri: painting), cutting-edge painting robots use data obtained through simulation painting with Mazda’s best craftsmen to replicate traditional techniques to give mass-production vehicles a precise, high-quality and hand-sprayed finish which enhances the beauty and sophistication of Kodo design.
1 https://www.mazda.com/en/notification/20190225/#:~:text=Towards%20 %E2%80%9CSustainable%20Zoom%2DZoom%202030%E2%80%9D&text=The%20 new%20vision%20defines%20our,the%20value%20found%20in%20cars
The surprising red Red is one of Mazda’s most symbolic and iconic colours. Building on the Takuminuri technology and with the idea to create the “world’s most beautiful red” to symbolise the Kodo philosophy, Mazda designers studied how people perceived colour and light and translated this ideal red into numerical values based on ergonomics to spray with Mazda’s Aqua-tech system, specially developed by the Japanese automaker to apply water-based paints while simultaneously reducing VOC and CO2 emissions, and using energy and paint materials much more efficiently than traditional systems. Thanks to the development of these technologies, Mazda has created several distinctive shades of red for its vehicles, known for their depth and vibrancy:
True Red: a bright and classic red that highlights the car’s contours and design features.
Soul Red Premium Metallic: the original high-gloss red that set the standard for Mazda’s striking red shades.
Soul Red Crystal: known for its intense depth and gloss, achieved through a three-layer paint process.
Artisan Red Premium: a newer addition, designed to evoke the sophistication of a mature wine, with an emphasis on craftsmanship.
Starting with Soul Red Metallic, the three-layer structure comprising of clear, translucent and reflective coats with aluminium flakes allowed Mazda designers to achieve colour brightness and depth at the highest level. In fact, not wanting to add a fourth layer of paint due to its environmental impact, Mazda design experts challenged convention to combine light-absorbing flakes along with high-brightness aluminium flakes in a single paint layer to create more depth and saturation while retaining its low environmental credentials.
In 2022 Mazda Motor Corporation applied its proprietary painting
technology Takuminuri to develop a new special colour named Artisan Red Premium. This fourth Takuminuri colour was developed to extend the range of how the world views red, one of the colours symbolizing Mazda, as a culmination of the Takuminuri evolution to mark the 10th year since the first colour Soul Red Premium was released.
Accounting today for 20.8 percent of UK sales (figure recorded in 2023), the introduction of Soul Red Crystal Metallic in 2017 represented an evolution of Mazda’s design and innovation to achieve more stunning levels of transparency to highlight the beauty and quality of Kodo design’s dynamic body shapes. Boasting an increase of approximately 20 per cent greater colour saturation and 50 per cent more depth than the already popular Soul Red Metallic, the development of Soul Red Crystal achieved precisely controlled reflections which produced more vivid highlights and even deeper shadows for a fresher, lustrous appearance.
Mazda has always led the way in paint innovation
Throughout Mazda’s history, the brand has always led the way in paint technology and colours. From the iconic bright colours and two-tone paint finishes to highlight the dynamic forms of Mazda’s first passenger car, the R360 Coupé, to paints such as ‘Grand Prix red’, ‘Corn Yellow’ and ‘Impulse Blue’ on the 323 to appeal to chic European couture in the late ‘70s. Not forgetting the world’s best-selling sports car, the Mazda MX-5 has had an array of limited-edition colours to match its popularity and presence on the road since 1989. With editions such as the ‘British Racing Green’, the distinctive orange and green ‘Le Mans 24’ livery and most recently the exclusive Racing Orange body paint available for the 30th Anniversary Edition, the Mazda MX-5’s paint continues to embody its stylish and fun to drive character.
PPG coatings will continue to protect the track walls, grandstands and fuel stations at the Indianapolis Motor Speedway following the renewal of their partnership.
The international paints and coatings manufacturer PPG has recently extended its partnerships with the Indianapolis Motor Speedway - INDYCAR® - and Team Penske through 2029. The agreement also makes PPG the entitlement sponsor of the Brickyard 400 NASCAR® CUP series race, which takes place at the IMS.
“We are excited to build upon our extensive history with Team Penske, INDYCAR, and IMS. To be able to expand and strengthen these relationships speaks to the commitment and success we’ve had together. I look forward to the seeing the PPG name on Team Penske cars and at the Brickyard 400 for years to come,” has stated Tim Knavish, PPG Chairman and CEO.
PPG is the official paints and coatings supplier of the IMS and INDYCAR. Indeed, its products protect the track walls, grandstands and fuelling
stations, as well as building signage at the IMS. In addition, the bright blue-and-white PPG livery is a colourful presence in the Team Penske lineup.
“For more than four decades, PPG has been one of the most trusted, innovative and dedicated partners in motorsports. We look forward to building on our long-term relationship with PPG at Team Penske for many years to come. We are also excited about the opportunities that lie ahead as we continue to feature PPG and their commitment to enhancing our communities across INDYCAR and at the Indianapolis Motor Speedway,” has added Roger Penske.
For further information: www.ppg.com
FASTRIP S is a vertical spray system for the chemical stripping of metals, a smart and innovative machine that speeds up the stripping process and reduces consumption and environmental impact, as well as guaranteeing excellent quality results. It is suitable for stripping metal, iron, and light alloys workpieces without damaging their surfaces. The parts to be treated are arranged in baskets that can be custom designed according to their intended use like automotive moldings, alloy wheels, etc.. In order to ensure homogeneous treatment, the platform on which the baskets are loaded rotates and the spray jet creates a cascade effect. Fastrip S operates with high temperature stripping cycles, which are fully adjustable according to the combination of materials and coating used. We recommend to use the METALSTRIP chemical products series by ALIT TECHNOLOGIES in order to get an optimized result.
FONDITAL chose the environmental sustainability and versatility of the cataphoresis line designed by IMEL for coating its radiators and automotive components distributed worldwide.
FONDITAL S.p.A., the world’s major manufacturer of aluminium radiators, an international leader in heating systems, and a producer of structural castings for the automotive industry, has chosen to collaborate with IMEL Spa (Codroipo, Udine, Italy), which has been designing and producing coating systems since 1964, to integrate a new cataphoresis line into its production structure, particularly for the manufacture of radiators and automotive components. This project significantly strengthened IMEL’s presence in the Italian market.
The plant has been designed to perform extremely versatile pretreatment and coating cycles while ensuring energy savings, no emissions, and a high degree of automation. One of its strengths is indeed environmental friendliness: in addition to total recovery of waste water, the plant recovers heat for heating both the oven and the pre-treatment baths using a VOC abatement system developed by IMEL.
The plant’s advanced automation, the implementation of some modules of the i4paintshop® platform, and the interconnection between the line and the company’s management system allow for the automatic execution of different coating cycles selected according to the incoming parts’ product codes.
They also ensure automatic management of incoming and outgoing data streams, complete process traceability, energy consumption monitoring, efficient maintenance scheduling, and fast digital data readout on all plant components.
The line also stands out for its high-quality equipment, compact design that optimises space, and the attention to detail typical of this supplier.
The collaboration with FONDITAL has enabled IMEL to showcase its expertise and further establish itself as a leader in high-end industrial coating treatments.
All the leading German automotive OEMs have already validated the plant and its pre-treatment and cataphoresis processes.
For further information: www.imelspa.com
Available in a wide array of colours and sparkling metallic effects, the new rage of powder coatings from AkzoNobel combines sustainability, durability and style.
The international paints and coatings producer AkzoNobel has recently introduced Interpon A3000, its new range of powder coatings dedicated to protecting and enhancing the body parts, wheels and trim of motorbikes and any other two-wheel vehicle, in line with the performance levels specified, tested and approved by the original equipment manufacturers.
The new range is ideally suitable for clients aiming to achieve greater cost efficiencies and enhanced sustainability, without however sacrificing the performances or aesthetic quality. As a matter of fact, Interpon A3000 can be applied as a single layer, thus reducing costs and consuming less energy in the coating process. Furthermore, there is also a low energy version available, which allows the powder to cure at a lower temperature and further reduce the energy consumed. The durability of the powder coatings from the Interpon A3000 portfolio helps to prevent the formation of corrosion generated from the weather and the interference from fuel, oil and other chemicals. In addition, they also protect against damage caused by excess heat, as well as having high resistance to chipping from stones and pebbles. In order to satisfy the various aesthetic demands, the range is available in a wide array of colours and sparkling metallic effects.
“Interpon has a proven portfolio of products for the sector. The new range gives motorcycle manufacturers and their suppliers the perfect combination of sustainability, durability and style for their modern designs,” has stated Gustavo Carvalho, the automotive segment director of AkzoNobel Powder Coatings. “With a single layer system, we can also help reduce the costs of our customers, since application times are much shorter. This contributes to reduce their carbon footprint. The powder coating provides an excellent flow-finish and delivers high aesthetic appeal and clarity, supporting the quality that OEMs demand to further enhance their brand.”
For further information: www.interpon.com
The interplay of aesthetics, sustainability and functionality of the Zenomenon automotive colour by BASF fascinated the Red Dot jury.
The international paints and coatings manufacturer BASF has recently announced that its Zenomenon colour had received the Red Dot Award for product design. The colour developed by the Coatings division of the company is the only automotive paint to be honoured this year during the Red Dot Award celebration, one of the most prestigious design competitions in the world. The innovative technology and the special aesthetics of the coating have impressed the independent experts on the Red Dot jury in the ‘Materials and Surfaces’ category: “The development of Zenomenon is remarkably future-oriented. In particular, the interplay of aesthetics, sustainability and functionality is fascinating.”
Instead of classic pigments, the formulation of Zenomenon is based on special polymer structures (suitable for LIDAR or radar sensor systems) with a high proportion of renewable materials developed by the cooperation partner Cypris Materials. So, the colour represents a more sustainable alternative in the area of surface aesthetics for automotive coatings. The result is a unique colour effect that arises from
self-assembled layered structures, reflecting light in the visible spectrum with a flop effect – giving the surface a shimmering and strikingly iridescent shine.
“Being awarded the Red Dot prize for product design is a very special honour for us, especially as a chemical company. The award underlines our design and technology expertise and the trust in innovative solutions that our customers in the automotive industry place in us,” has stated Mark Gutjahr, the global head of automotive colour design for BASF.
All submissions had been assessed based on the four basic principles of good design: the quality of function, the quality of seduction, the quality of use and the quality of responsibility. All award-winning products, including a sample coated with Zenomenon, will be showcased until May 2025 as part of an exhibition at the Red Dot Design Museum at the UNESCO World Heritage Site Zollverein in Essen (Germany).
For further information: www.basf-coatings.com
Gert große Deters
Venjakob Maschinenbau GmbH & Co KG - Rheda-Wiedenbrück, Germany gert.grossedeters@venjakob.de
Partnership between Venjakob and Plasmatreat replaces costly film wrapping process.
Local expertise from East Westphalia-Lippe (NRW) bundled, innovative solution developed for international battery production: Plasmatreat GmbH (Steinhagen) and Venjakob Maschinenbau
GmbH & Co. KG (Rheda-Wiedenbrück) are now making battery production more efficient and reliable thanks to a newly developed process. For reliable electrical insulation, plasma-cleaned battery cells are given a special coating instead of a complex film wrapping. Battery manufacturers are benefiting from the proximity of the two companies, which are working together to simulate processes under realistic conditions and produce small batches.
The e-mobility sector is looking for solutions to further improve battery reliability and safety. One starting point for optimization is electrical insulation. Traditionally, battery cells, especially prismatic cells, are wrapped with a film. The process is costly, time-consuming and contains sources of errors. Now an innovative process is making battery production more efficient, faster and more reliable: the battery cells are coated with a special lacquer instead of foil. The companies Venjakob and Plasmatreat have combined their expertise.
Plasmatreat - Perfect lacquer adhesion through ultra-fine cleaning
Plasmatreat is the world leader in atmospheric plasma technology and has developed Openair-Plasma technology. In this case, it is used for
ultra-fine cleaning of the bare battery cell and enables reliable, longterm stable lacquer application. The Openair-Plasma is precisely applied to the metal surface of the battery cells in a plasma treatment unit (PTU) at atmospheric pressure using simple compressed air and electricity through specially designed nozzles. Compared to conventional cleaning methods, the process is much more environmentally friendly, selective and inline capable.
The surfaces of the battery cells are reliably cleaned of wafer-thin layers of dust and residual traces from the production process, such as oil or grease. This allows the protective coating to be applied without gaps. Long-term adhesion is achieved.
Venjakob – Contact-free coating, minimizing sources of error
The mechanical engineering company Venjakob, a specialist in coating lines, has developed a fully automated system for a continuous contactfree coating process. Battery cells in various formats are coated with a 100% UV coating after ultra-fine cleaning using Openair-Plasma. A specially designed tool carrier ensures that sensitive areas and the electrical poles of the battery cells are reliably protected from overspray. Since the process requires no gripping, turning or other handling, the risk of damage to the battery cells is minimized. The contact-free process also allows for higher production speeds. The immediate curing
of the UV coating means that the cells can be processed directly. This speeds up the entire battery manufacturing process.
Various analyses confirm the high efficiency of the innovative insulating coating, which achieves adhesion values in excess of 15 MPa in tensile shear tests. The two partners attribute the success of the project primarily to the fact that they matched each other in key areas. These include extensive technological expertise, uniformly high-quality standards, flexible adaptability to changing customer requirements, and intensive communication based on mutual trust. In this case, the joint customers also benefit from the close proximity, which has made it possible to demonstrate and evaluate ultra-fine cleaning and coating in a near-series process in Steinhagen and Rheda-Wiedenbrück.
Using compressed air and electricity, the surfaces of the batteries are reliably cleaned of wafer-thin layers of dust and residual traces from the production process, e.g. oil or grease, so that the protective coating can be applied without gaps and long-term adhesion is achieved.
From an interview with
Mauro Margherita CEO of Kenosistec Srl
CHROME+ is the only chrome plating process for plastics available on the market that ends directly with the deposition of the PVD layer and does not require any galvanic process. Using a two-layer process with the application of a high-solid, solvent-free UV coating followed by an under-patent PVD deposition phase, Kenosistec’s CHROME+ technology is a revolution in the field of automotive chrome coatings. It passes the most rigorous industry-standard tests, including hydrolysis, condensation, and climatic tests, known to be among the most demanding in the sector. And, of course, at the same time, it is applicable in any other industry that uses chrome plating, such as the production of small and large household appliances.
In the automotive sector, reducing the vehicles’ weight is a priority for reasons ranging from energy efficiency to improved performance and environmental sustainability. In recent years, and more precisely between 2008 and 2020, the automotive industry has made considerable progress by decreasing the weight of cars by around 20%. However, there is still plenty of room for improvement and various strategies and processes that can help to further reduce vehicle weight. “The main areas of focus are material substitution, component design optimisation, and production innovation,” says Mauro Margherita, the CEO of company Kenosistec. Using lighter materials such as plastics is indeed one of the strategies increasingly adopted by OEMs to reduce the overall weight of vehicles. “Green and biodegradable plastics are promising, but their use is currently limited by the existing deposition technologies. At the same time, new ‘engineering plastics’ are emerging as viable alternatives to metals: with similar or even superior mechanical properties and significantly lower weight than metals, they are going to help reduce fuel consumption and CO2 emissions, improving sustainability and energy efficiency in the automotive sector,” adds Margherita. That is why Kenosistec Srl, a manufacturer of vacuum and sputtering equipment for PVD and PECVD coatings based in Casarile (Milan, Italy), has recently launched CHROME+. This innovative, patented technology provides a two-layer PVD coating solution for glossy and/or matte chrome plating on plastic components. Surpassing the rigorous standards of the automotive sector that typically require galvanic processes, CHROME+ is set to become an industry benchmark.
How the CHROME+ deposition process works
CHROME+ is the only plastic chrome plating technology available on the market that does not require galvanic processes. It is a two-
layer deposition process. The first layer is a UV-cured base coat serving as the primer for chromium deposition. Then, the Hi.P.Po (High Productive Powered Sputtering Cathode) PVD sputter coating technology developed and patented by Kenosistec deposits a chrome layer with the required thickness. Operating at low temperatures, Hi.P.Po. maintains a rapid deposition rate and does not overheat the treated plastics, thus preventing them from deforming. “CHROME+ is a real revolution in the field of automotive coatings. Thanks to a unique combination of UV coating and a special PVD sputter coating technology, it can meet stringent standards, including hydrolysis, condensation, and climate tests, known to be among the most demanding in the carmaking industry,” says Margherita.
The Hi.P.Po. patented technology
Hi.P.Po. is a patented next-generation sputtering source designed for largescale production. This technology ensures a deposition rate ten times higher than conventional planar cathodes, making it not only competitively priced but also more repeatable than metallisation. One of the main advantages of Hi.P.Po. is the possibility of depositing various materials, including nitrides and carbides, thanks to its special cylindrical geometry, thus offering a wide range of consistent colours and finishes.
In terms of energy efficiency, Hi.P.Po. consumes less than a third of the energy compared with conventional sources for the same deposited thickness. Kenosistec’s new patented technology also ensures target
material savings of over 65% thanks to its motorised magnetic array, which consumes the target uniformly and almost entirely and reduces the target change frequency compared with standard technologies. Finally, Hi.P.Po. guarantees a reduction in the chamber’s volume by around 40%, even when using the same carousel as conventional planar magnetron batch coaters. This reduces the pumping time per cycle, increasing the overall efficiency of the process.
The CHROME+ technology offers numerous advantages, making it an ideal solution for multiple applications. First of all, it guarantees high resistance to corrosion and wear, protecting the components from external agents and ensuring long-lasting finishes. Secondly, in terms of aesthetics, it provides cool-touch, haptic effects that give the components a high-quality, pleasant touch feel, as well as smooth, shiny finishes. Thirdly, it guarantees better colour retention over time without fading. In the fourth place, being a two-layer technology, CHROME+ reduces the time and cost of the deposition process by about 30% while ensuring all the functional advantages of three-layer systems. Finally, it is compatible with a wide range of materials, including acrylic, PET, HDPE, PEEK, PMMA, nylon, polyamide, polyetherimide, AB, polyurethane S, polypropylene, polyethylene, PVC, polyester, phenolic, polycarbonate, and epoxy, and it is compliant with the Regulation (EC) No. 1907/2006 (REACH), which aims at reducing the use of materials considered hazardous in industrial processes. “This innovative technology not only enables to deposit chrome on plastic materials but also reduces the use of harmful substances, offering an environmentally friendly solution for companies that want to increase the safety and environmental sustainability of their processes,” confirms the CEO.
The ideal solution for the automotive sector and beyond
The automotive sector can benefit enormously from the CHROME+ technology, whose high-gloss and satin finishes can be applied to handles, rear-view mirrors, window frames, and other interior components. Its ability to pass the most rigorous tests makes CHROME+ a preferred choice for car manufacturers. At the same time, in addition to the automotive sector, Kenosistec’s PVD technology can find application in a variety of industries, including as follows:
Motorbike accessories: coating of mirror covers, knobs, and decorative covers.
Household appliances: coating of stove knobs, decorative parts for electronic devices, and handles.
Electronics: coating of housings or external parts of technological devices.
Bathroom accessories: covering of plastic hand showers and furnishing accessories.
Solar energy: coating of photovoltaic panels.
Medical equipment: coating of instruments and prostheses.
Data storage.
“The CHROME+ process developed by Kenosistec represents a breakthrough in plastic chrome plating, offering numerous advantages in terms of durability, aesthetics, and sustainability. The advanced Hi.P.Po technology and the two-layer deposition process make CHROME+ the ideal choice for the automotive industry and other sectors, promising to revolutionise how plastic components are treated and coated. It is currently available in the chrome colour and its variants, but other tints are also being developed,” summarises Mauro Margherita.
Unveiling of the full scale prototype developed by Istituto Europeo di Design, designed by the students of the Master Course in Transportation Design in collaboration with the Modena-based car manufacturer, that launched the iconic two-seater designed by Horacio Pagani a quarter of a century ago.
Atwo-seater that challenged the norm with its distinctively essential nature recalling the timeless appeal of the classics, not disregarding a strong sportiness. A vanguardist design combining aerodynamic features and racing touches. A project that picks up the baton from the most iconic hypercar, projecting it into the future. It’s ALISEA, the new concept car created by the students of the Master Course in Transportation Design for the 2022/2023 a.y. at IED Torino, in collaboration with Pagani Automobili. It is the result of a path involving 24 young designers and Pagani design team who worked for months on end to imagine the evolution of the Zonda, 25 years after the model redefined design standards and raised the bar in terms of style and performance.
The concept hypercar unveiled today at the Reggia di Venaria is a futuristic take on the undisputed carbon fibre masterpiece that shook the motoring world at the 1999 Geneva Motor Show. As part of their Master’s thesis, the young designers worked as members of a true design centre. The result is a simultaneously analogical and technological car, blossoming from meticulous research; a job
made done to turn heads. Its surface has no decorative elements or interruptions: ALISEA is a single, clean, and legible shape, with no hollows in any part of the body. The dynamic shape of the two-seater lies within an ellipse that ideally connects the front end and tail, framing a drop-shaped cockpit ending in the four iconic round tailpipes. The finish sinuously envelops both the driver and the powerful V12 engine. The colours, carried out by Freeland.car with Lechler products for the Industry, underline the aerodynamic sections hiding the spoiler in the side view to make the overall design lighter and more uniform. The 1:1 scale model, whose yearly creation confirms IED Torino’s educational quality, will enrich the prestigious collection of concept cars developed in partnerships with the most renowned manufacturers in the world and with the support of technical sponsors Pirelli, OZ Racing, and Lechler as well as technical partners Freeland.car, MINTT, AM Costruzione Modelli, Raitec, and Italian Design Wrap.
For further information: www.lechler.eu
Mechanical and plant engineering company Dürr produced its 18,000th painting robot for Audi in Ingolstadt. The robot features the latest EcoBell4 atomizer with 4-main needle technology for rapid color changes with minimal paint and rinsing agent losses.
Dürr equipped a new top coat line for car manufacturer Audi in Ingolstadt to paint the interior and exterior of the new Audi Q6 e-tron series. The milestone robot, an EcoRP L033i, was installed in May in the interior paint booth. The six-axis painting robot, equipped with Dürr’s latest EcoBell4 atomizer, requires just four seconds for each color change thanks to the patented 4-main-needle technology. “This application technology enables us to connect our three most frequently used colors directly to the atomizer, significantly reducing paint and rinsing agent consumption,” explained Sven Veit, Director Manufacturing Engineering Paint Shop at AUDI AG. With Dürr’s latest EcoBell4 atomizer technology, the car manufacturer not only saves operating costs but also protects the environment with fewer VOC emissions.
Sustainable paint supply
The new top coat line includes a total of 28 robots and corresponding application technology. Dürr is also supplying a quality measurement cell to measure paint layer thickness, structure, and shade, as well as a cleaning station where two EcoRS Clean F
Delivering the 18,000th Dürr painting robot to AUDI AG. From left to right: Jürgen Haas, Head of Product Development Application Technology, Dürr, Marcus Treppschuh, Head of Sales Application Technology, Dürr, Jörg Spindler, Head of Manufacturing Engineering, AUDI AG, Dr. Lars Friedrich, Head of the Application Technology division, Dürr, Sven Veit, Director Manufacturing Engineering Paint Shop, AUDI AG, Hannes Kupke, Manufacturing Engineering Paint Shop Audi Ingolstadt site.
robots use feather rollers to clean the car bodies. For this project, Audi is also using Dürr‘s EcoSupply P special color supply system with pigging technology to flexibly provide unlimited colors consecutively for application.
In 1998, Dürr supplied its first painting robot, an RP7 robot, to Nissan in Spain. The mechanical and plant engineering company is now on its third robot generation, introduced in 2016, benefiting from a modular structure that places the color changer and metering pump on the robot’s front arm, ensuring fast color changes with minimal paint loss and rinsing agent consumption.
At the end of April, Dürr delivered the milestone robot to Audi at its BietigheimBissingen headquarters. “We are always prepared to take on a challenging project. After all, painting a large volume of cars to a high-quality standard is what we do every day. New at Audi are the numerous innovations we are implementing for the first time: the EcoBell4 with 4-main needle technology and high transfer efficiency painting technology. This is what makes the project so special,” said Dr. Lars Friedrich, Head of Division Application Technology at Dürr.
For further information: www.durr.com
Carina Lachnit Dürr Systems AG - Bietigheim-Bissingen, Germany carina.lachnit@durr.com
The climate tech company right° and the mechanical and plant engineering firm Dürr are working together to calculate the climate impact of paint shops for the automotive industry. The aim is to express the climate impact of painting as a degree Celsius figure. In addition, the climate impact of different painting concepts will be evaluated to enable comparisons. Going forward, automotive manufacturers will be able to use the results as a basis for decision-making when investing in painting technologies. An initial feasibility study has yielded positive results, prompting closer collaboration.
“The Dürr Group develops innovative technologies for climate-friendly automotive production. Together with right°, we want to quantify the climate impact of our painting technology products in the form of a simple degree figure. This
enables us to support our customers even better in achieving their individual climate targets,” says Dr. Jochen Weyrauch, CEO of Dürr AG.
The X-Degree Compatibility (XDC) model by right° calculates the climate impact of an
economic unit, for example a company or a factory. The result is expressed in a degree Celsius format that is both science-based and easy to understand. In the collaboration between right° and Dürr, a paint shop is viewed as an economic unit.
After developing the calculation approach in a preliminary project, it is now to be applied in practice. To this end, right° is developing a software prototype that Dürr can use to make the calculations available to its customers in a clear and transparent format. In addition, the degree figures for different painting concepts are currently being calculated.
“Energy-efficient painting technologies can make a major contribution to the decarbonization of automotive production. Being a quality supplier, it is important for us to quantify this contribution professionally.
right° and Dürr are working together to calculate the climate impact of paint shops. Going forward, the result –expressed in degree Celsius – can be used by automotive manufacturers as a basis for decision-making when investing in painting technologies.
This means that our customers know exactly what impact their investments have on the climate,” says Hanjo Hermann, Head of Sustainability at Dürr AG.
The Dürr Group is part of a group of exclusively selected customers with whom right° is developing use cases for the XDC model with high potential for large-scale use. “By calculating the degree figure of an individual technology, we enable buyers to understand the climate impact of their investment. This allows investment decisions to be made with a specific focus on their contribution to the 1.5°C target. And this, in turn, is necessary for more capital to be invested effectively in the climate transition,” says Hannah Helmke, co-founder and CEO of right°. The results of the project are expected in the fourth quarter of 2024.
The X-Degree Compatibility (XDC) model developed by right° calculates the climate impact of an economic unit and expresses the result in a °C format that is easy to understand. The climate performance of the unit is calculated by comparing its economic emission intensity with a 1.5°C benchmark. By scaling the performance to a global level, it is then possible to calculate the amount of emissions that would be released into the atmosphere if the world had the same performance as the unit. Finally, a climate model converts the emissions into a °C figure, which can be directly related to the 1.5°C target as the climate impact of the unit.
About right°
right. based on science GmbH (right°) is a multi-award-winning climate tech company that makes the climate impact of economic activities transparent: in a plain and simple °C format. The climate impact is calculated using the proprietary X-Degree Compatibility (XDC) model. The results can be directly related to the 1.5°C target of the Paris Climate Agreement.
For further information: www.durr.com
Edited by ipcm®
With their adjustable illumination capacity, high output of up to 93,600 lm for the arch T15 model, and ergonomic design, the TecoLight systems manufactured by Asco 3/Tecopoint can reveal every tiny surface defect, while at the same time promoting sustainable practices thanks to the latest LED technology.
In the automotive industry, coating and polishing quality is a key pillar in ensuring excellent aesthetics but also the durability and market value of vehicles.
Every imperfection, even the smallest one, can significantly affect the appearance and durability of a car, making the implementation of advanced quality control systems crucial.
As a manufacturer of systems and equipment for body shops and the general industry, Asco 3/Tecopoint developed the TecoLight systems precisely to respond to these requirements. Using the latest LED technology, the TecoLight product range offers optimised lighting solutions for automotive QC processes. Designed to improve the accuracy and efficiency of visual inspection operations, these devices perfectly suit the specific needs of automotive workshops and production lines: thanks to their natural and uniform illumination capability, they allow even the slightest imperfections to be precisely identified, supporting the car industry in achieving ever higher quality standards.
TecoLight: advanced coating quality control technology
The TecoLight range from Asco 3/Tecopoint includes three models, i.e. the arch with 15 lights, the suspended arch with 15 lights, and the semiarch with 4 lights, all characterised by the following technical characteristics:
Possibility of setting the colour of individual lights in three different shades, i.e. warm, intermediate, and cold, to create proper contrast on the examined surface and thus facilitate the detection of defects.
Adjustable LED lights from 2300 to 7300 lm to adapt to the specific requirements of each QC process, ensuring excellent visibility in all conditions.
Lightness and ease of handling despite the systems’ size: convenient integrated handles allow the lights to be directed exactly where needed, ensuring precise and targeted lighting.
Latest LED technology: the ideal choice to protect the environment thanks to its energy efficiency and reduced environmental impact.
“Tecopoint/Asco 3’s TecoLight systems are an advanced and sustainable solution for coating quality control in the automotive industry. With their adjustable lighting capability, high power, and ease of use, the TecoLight devices are ideal for modern body shops aiming for aesthetic and functional perfection in vehicles,” states Giampaolo Luise, the owner of Asco 3/Tecopoint.
Eurotherm solves every problem concerning painting processes, creating complete lines for the entire process.
Our structure is organized and flexible and able to satisfy the most demanding requests. Customers who turn to Eurotherm are customers who, despite knowing the “painting process”, want to improve production by adopting highly customized technical solutions.
Eurotherm S.p.A.
T +39 011 98 23 500 | M info@eurotherm.eu
Eurotherm France S.A.S.
T +33 6 76 72 48 65 | M france@eurotherm.eu
Eurotherm Oberflächentechnik GmbH
T +49 7571 92795 10 | M germany@eurotherm.eu
Eurotherm Benelux Srl
T +33 6 47 44 96 27 | M dekergorlay@eurotherm.eu
Christiane Pyka
BMW Group, Munich – Germany christiane.pyka@bmwgroup.com
Last May BMW presented to the public the 20th BMW Art Car designed by Julie Mehretu at the Centre Pompidou in Paris.
Designed by renowned New York-based contemporary artist Julie Mehretu, the 20th BMW Art Car project transformed the BMW M Hybrid V8 race car into a performative work of art, continuing a longstanding tradition of BMW Art Cars and competitive racing. Just a few weeks after its World Premiere in the French capital, the newest edition in the storied BMW Art Car collection participated in the 92nd edition of the 24 Hours of Le Mans (held from June 12 to 16) and was entered by BMW M Team WRT.
“The whole BMW Art Car project is about invention, about imagination, about pushing limits of what can be possible. I don’t think of this car as something you would exhibit. I thought of it as something meant to race at Le Mans. It’s a performative painting. My BMW Art Car was created in close collaboration with motorsport and engineering teams,” says Julie Mehretu. “The BMW Art Car is only completed once the race is over.”
The collaboration between BMW and Julie Mehretu also includes a joint commitment to a series of PanAfrican Translocal Media Workshops for filmmakers, which will tour various African cities in 2025 and 2026, and will culminate in a major exhibition at the Zeitz Museum of Contemporary Art Africa in Cape Town.
“The BMW Art Cars are an essential part of our global cultural commitment. For almost 50 years, we have been cooperating with artists who are just as fascinated by mobility and design as they are by technology and motorsports. Julie Mehretu’s vision for a racing car is an extraordinarily strong contribution to our BMW Art Cars series,” said Oliver Zipse, Chairman of the Board of Management of BMW AG. “Julie Mehretu has created more than an amazing Art Car. Her ideas provided the impetus for us to expand the cultural commitment of our Art Cars to promote the creativity of young artists in Africa.”
A Performative painting is created
Space, movement and energy have always been central motifs in Julie Mehretu’s work. For the design of the 20th BMW Art Car, she transformed a two-dimensional image into a three-dimensional representation for the first time, with which she succeeded in bringing dynamism into form. Julie Mehretu used the colour and form vocabulary of her monumental painting “Everywhen” (2021 - 2023) as a starting point for her design.
The work is currently on view at “Ensemble”, the artist’s exhibition at the Pinault Collection - Palazzo Grassi in Venice and will subsequently become part of the permanent collection of the Museum of Modern Art (MoMA) in New York, to which it has been gifted. Its abstract visual form results from digitally altered photographs, which are superimposed in several layers of dot grids, neon-coloured veils and the black markings characteristic of Mehretu’s work. “In the studio where I had the model of the BMW M Hybrid V8 I was just sitting in front of the painting and I thought: What would happen if this car seemed to
go through that painting and becomes affected by it,” Julie Mehretu says. “The idea was to make a remix, a mash-up of the painting. I kept seeing that painting kind of dripping into the car. Even the kidneys of the car inhaled the painting.”
The fusion of image and vehicle was realised with the help of 3D mapping, with which the motif was transferred to the contours of the vehicle.
The elaborate foiling allows for the fully designed BMW M Hybrid V8 to compete at the 24 Hours of Le Mans. Before the race it was exhibited jointly with other BMW Art Cars with Le Mans history at the Concorso d’Eleganza. BMW Motorsport drivers Sheldon van der Linde (RSA), Robin Frijns (NED) and René Ras (GER) entered the 20th BMW Art Car with starting number 20 at the Circuit de la Sarthe on 15 June: unfortunately, the Art Car driven by Robin Frijns ran off the track and had a huge collision with the tyre wall. To honour the Art Car project and reward the WRT team for their hard work, the car returned to the track shortly before the end after a long repair break and crossed the finish line.
The collaboration between BMW and Julie Mehretu was conceived from the beginning beyond the automobile. It will culminate after the 24 Hours of Le Mans in a project for emerging artists on the African continent: The PanAfrican Translocal Media Workshops. Together, the partners are focussing on the creative potential across the African continent, where the BMW Group has been making a contribution to social responsibility with educational projects for over 50 years. Julie Mehretu and Mehret Mandefro, Emmy-nominated producer, writer and co-founder of the Realness Institute, which works to strengthen the media ecosystem in Africa, will organise workshops in various African cities and regions throughout 2025. The goal of the project is to provide a space for artists and filmmakers to collaborate and exchange ideas. These meetings will offer a forum for artists to develop new pathways towards a just civic future in their respective communities.
The PanAfrican Translocal Workshop series will visit the cities of Dakar (Senegal), Marrakech (Morocco), Kigali (Rwanda), Lagos (Nigeria) and Cape Town (South Africa). The results of the workshops will be presented together with the 20th BMW Art Car at the Zeitz Museum of Contemporary Art Africa in Cape Town in the first half of 2026.
The BMW Group is thus consistently continuing its decades-long support for film and creative talent: from the short film series ‘The Hire’ and the partnership with the Cannes International Film Festival to the acquisition of works by students from art academies in the neighbourhoods of the company’s plants worldwide.
Julie Mehretu is a world-renowned American painter. She was born in
Addis Ababa, capital of Ethiopia, in 1970. Together with her family she moved to the U.S. at the age of seven. She lives and works in New York City and Berlin.
Mehretu’s practice in painting, drawing and printmaking engage the viewer in a dynamic visual articulation of contemporary experience, a depiction of social behavior and the psychogeography of space by exploring palimpsests of history, from geological time to a modern-day phenomenology of the social.
Mehretu received her Bachelor’s Degree from the Kalamazoo College in Michigan, spent a year abroad at Cheikh Anta Diop University in Dakar, Senegal, and completed her Master’s degree of Fine Art with honors from The Rhode Island School of Design in 1997. Mehretu has received numerous awards, including the The MacArthur Award (2005), The Berlin Prize: Guna S. Mundheim Fellowship at The American Academy in Berlin (2007) and the U.S. Department of State Medal of Arts Award (2015). A midcareer survey of Mehretu’s work recently toured at LACMA (Los Angeles), High Museum (Atlanta) The Whitney Museum of American Art (New York) and The Walker Museum of Art (Minneapolis) from 2019 to 2023. Her largest European solo exhibition to date entitled “Ensemble” opened March 17, 2024 at Palazzo Grassi in Venice. Mehretu is a member of the American Academy of Arts and Letters, the American Academy of Arts and Sciences and The National Academy of Design. Her global representative is Marian Goodman Gallery. She also exhibits with White Cube, London, and Carlier Gebauer, Berlin.
Statement from the jury for the 20th BMW Art Car
Julie Mehretu was unanimously selected in 2018 by a jury of highranking representatives of the international art world to design the 20th BMW Art Car. The panel includes renowned curators and museum
directors from various countries, including Koyo Kouoh, Executive Director and Chief Curator, Zeitz MOCAA, Cape Town; Hans-Ulrich Obrist, Artistic Director of the Serpentine Galleries, London; and Cecilia Alemani, Donald R. Mullen, Jr. Director and Chief Curator, High Line Art, New York. On the occasion of the World Premiere of the BMW Art Car designed by Julie Mehretu in Paris, the jury members published the following statement: “We are thrilled with Julie’s BMW Art Car! Okwui Enwezor had already coined the phrase ‘Dynamism in Form’ during our jury session and nothing applies better to her BMW M Hybrid V8 race car. Julie’s first three-dimensional work combines her aesthetics and formal language with the idea of the glitch and the blur, turning speed into a visceral experience. This energetic space is as fierce and competitive in racing as it is ambitious as a creative playground of the imagination. It not only pays homage to the art cars of Jenny Holzer and Frank Stella, but also spins a visual web from Mad Max to graffiti and street art that is unique within the series of BMW Art Cars.”
The canvas for the 20th BMW Art Car is the BMW M Hybrid V8. The new race car from BMW M GmbH features a hybrid electric drivetrain system with approximately 640 hp, powered by a 4.0-litre V8 engine supported by an electric motor (top speed: up to 345 km/h or 215 mph, depending on the race track layout). During this year’s official FIA World Endurance Championship races, the BMW M Hybrid V8 will take on high-calibre competition in the Hypercars category. The car competed in the 24 Hours of Le Mans – the first BMW M Motorsport prototype to do so since the BMW V12 LMR, which won the classic race in 1999.
Renowned artists from all over the world have participated in the BMW Art Car program since 1975. The initiative came from the French racing driver and art lover Hervé Poulain, who, together with the then BMW Head of Motorsport Jochen Neerpasch, asked his artist friend Alexander Calder to paint a car. The result was a BMW 3.0 CSL, which competed in the 24 Hours of Le Mans in 1975 and became a crowd favourite. This was the birth of the BMW Art Car Collection. In the years that followed, renowned artists such as Frank Stella, Roy Lichtenstein, Andy Warhol, Robert Rauschenberg, Esther Mahlangu, David Hockney, Jenny Holzer, Ólafur Elíasson and Jeff Koons enriched the collection with further BMW Art Cars, each in their own individual style. Most recently, the Chinese multimedia artist Cao Fei and American conceptual artist John Baldessari each presented a BMW Art Car based on the BMW M6 GT3 and GTLM respectively in 2016 and 2017. The BMW Art Cars are not only shown at their home, the BMW Museum in Munich, but are also on tour around the world as part of international exhibitions.
By MV Agusta Motor S.p.A. Varese, Italy
The Italian luxury motorcycle manufacturer MV Agusta and Daniel Arsham announced their collaboration in creating a super-exclusive limited series to 6 units of MV Agusta Superveloce: the Superveloce Arsham.
MV Agusta is one of the world’s leading premium motorcycles manufacturers.
Based in Varese, in Northern Italy, it crafts legendary racetrack-derived bikes. Iconic design and class-leading performance through advanced technologies and materials make MV Agusta motorcycles admired the world over and celebrated as unique pieces of Motorcycle Art. Since 1945, the brand has evolved to become a point of reference in the industry, having won 37 World Championship titles. A record still undisputed.
For one of its most recent projects, the Italian company joined forces with the internationally acclaimed artist Daniel Arsham in order to create a dedicated super-exclusive limited series of Superveloce1, presented to the world at Miami Art Basel on December 8th
The MV Agusta Superveloce is MV Agusta’s most iconic motorcycle currently in production and its distinctive neo-retro design was chosen by the New York-based artis to create a true art piece using his iconic erosion technique. Daniel Arsham is known for breaking the rules of academic artistry, a trait fully expressed in his signature “erosion” technique.
1 Every Superveloce Arsham is based on fully functioning Superveloce 800, however those motorcycles will be sold as works of art that cannot be registered for road use and will not be covered by factory warranty. The Superveloce Arsham will not be available through MV Agusta official dealers, but MV Agusta’s top customers and Daniel Arsham’s collectors have already been given the opportunity to request one of the 6 motorcycles available. The price is provided upon request and it is not disclosed to the public.
Arsham’s avant-garde erosion method renders the concept of passing time through sculptures. Working in a multitude of disciplines, he creates and crystallizes ambiguous in-between spaces and situations, and stages what he refers to as future relics of the present. Always iconic, most of the objects that he fabricates refer to the late 20th century or millennial era, when technological obsolescence unprecedentedly accelerated along with the digital dematerialization of our world. While the present, the future and the past poetically collide in his intruiging yet playful visions between romanticism and pop art, Arsham also experiments with the timelessness of certain symbols and gestures across cultures.
The concept is astonishingly reminiscent of the intimate nature of the Superveloce itself: disturbingly attractive, avant-garde, incredibly iconic and high-tech yet with clear references to the great classics of motorcycling, MV Agusta’s Superveloce was a natural choice for this project. The series will be limited to only 6 units, this will also make this particular model a true rarity and an object of desire for passionate collectors.
Timur Sardarov, CEO, MV Agusta Motor S.p.A., said: “I am thrilled about this incredible collaboration with Daniel Arsham, an artist I truly admire and that has so much in common with MV Agusta in terms of values and philosophy. His works are amazingly inspiring, and together we will take our Motorcycle Art to the next level.”
Daniel Arsham, said: “I was always fascinated by the automotive world. The design ethos of cars and motorcycles, always fits a particular era and they mark time through their design. The project on the Superveloce was the opportunity to explore a “moving sculpture”, a functional motorcycle that have been transformed into a sculpture, by adding crystal erosions and by applying a colour that is reminiscent of my other artworks and style. Together with MV Agusta we created everything on the bike, including the stand, overcoming engineering challenges and resulting in a new interpretation of Motorcycle Art.
About the artist: Daniel Arsham
New York based artist Daniel Arsham work explores the fields of fine art, architecture, performance, design and film. Raised in Miami, Arsham attended the Cooper Union in New York City where he received the Gelman Trust Fellowship Award in 2003. Soon thereafter Arsham toured worldwide with the Merce Cunningham Dance Company as the company’s stage designer. The experience led to an ongoing collaborative practice which continues as Arsham works with world renowned artists, musicians, designers, and brands including Porsche and Dior.
In recent years Arsham’s practice has begun to bridge the gap between fine art and commerce through a number of commercial business ventures dedicated to the conception of limited edition artworks aimed at reaching a wider global audience, such as Arsham Editions, Arsham Living and Objects IV Life.
In 2021 Arsham was appointed the role of creative director of the Cleveland Cavaliers, becoming the first-ever fine artist to hold a position of this nature.
Arsham’s work has been shown at PS1 in New York, The Museum of Contemporary Art in Miami, The Athens Bienniale in Athens, Greece, The New Museum In New York, Contemporary Arts Center Cincinnati, SCAD Museum of Art in Savannah GA, California and Carré d’Art de Nîmes, and the High Museum of Art in Atlanta GA. Arsham is represented by Galerie Perrotin in Paris, Hong Kong, New York, Seoul, Shanghai and Tokyo. Arsham also shows with Baró Galeria in Lisbon and Mallorca, Ron Mandos in Amsterdam, Nanzuka Gallery in Tokyo, Friedman Benda in New York, and König Galerie in Berlin.
Monica Fumagalli ipcm®
SVI Verniciatura Industriale is a long-established coating contractor specialising in dip and spray liquid and powder coating of cast iron, aluminium, and steel components. Recently, it inaugurated a new coating plant designed and installed by Verona Impianti 2002 to easily switch from powder to liquid application and achieve optimal results through flexible temperature management in the baking/curing oven.
Among the requirements that make cast iron one of the most used materials in the mechanical industry are good resistance to corrosion due to its electrochemical nature; excellent wear resistance thanks to the high surface hardness
and the presence of graphite which acts as a “lubricant” between two mutually sliding bodies; and good thermal conductivity, ideal for applications requiring heat dissipation, such as, for example, engine components and industrial equipment.
The corrosion and wear resistance properties can be further improved by applying paint products characterised by high baking temperatures, which ensure the coatings remain stable and do not degrade under the difficult thermal conditions to which the cast iron components are subjected. According to data reported by Assofond, the Italian Foundries’ Association1, there are approximately 1,000 foundries in Italy, of which 122 specialise in cast iron. This industrial sector is particularly developed in Northern Italy, where the Brescia foundry district is located, but also has some small hubs in other parts of Italy, such as, for example, the long-standing one situated in the Emilia-Romagna region between Cento and Modena. From the 1970s onwards, this area has been home to several production plants manufacturing agricultural machinery first for Lamborghini Trattori and then for FIAT Trattori Spa. Their presence here has created a number of satellite activities, especially cast iron foundries. Initially, castings only had to be primed for corrosion and wear protection; now, due to the increasingly strict functional but also aesthetic requirements, they also need to be painted in several coats.
1 https://www.assofond.it/en/foundries-in-italy
It is in this context that SVI Verniciatura Industriale Srl was established, now specialising in dip and spray liquid and powder coating of cast iron castings and aluminium and steel parts. “Our company’s first activity was coating the gear sticks of the FIAT 127 and 128 cars with a layer of primer,” says Gianantonio Gallerani, the heir with his brother Giorgio to the company founded by their father in 1974. “When the Turinbased manufacturer ceased production of these two small cars’ gearbox assemblies and started focussing on agricultural machinery, we began to coat cast iron castings for tractor engines. We thus became coating contractors for FIAT as well as for local foundries that still supply industry leaders such as CNH, Fendt, and John Deere. Agricultural machinery has remained our core market: it still accounts for 60% of our production. At the same time, we now also coat gearmotors, industrial vibrators, and marine engines (20%), as well as light and heavy-duty metalwork components (10%). Finally, we treat parts for the street furniture, food, and water pump industries (10%).”
Today, the company, established under the name SVI Verniciatura Industriale in 1992, occupies a total area of 15,000 m2 where it coats cast iron, steel, and aluminium parts weighing between 200 grams and 1 tonne. Its plant has cast iron manual deburring and shot blasting departments plus 4 coating lines, i.e. 3 semi-automatic systems, one of which performs dip coating operations, and 1 manual plant for solvent-based coating application on small batches or prototypes. With the most recent line, designed and installed by Verona Impianti 2002, a supplier with many years of experience in the design, production, and installation of systems and consultancy services for pre-treatment, coating, and drying machines, the company wanted to upgrade its equipment fleet to make the workflow more flexible and faster, create a cleaner and more comfortable work environment, improve coating performance, and implement Industry 4.0 parameters.
The flexibility of the new system
SVI installed a dip coating plant for medium and large cast iron components in 1980, which was joined in 2001 by another system with the same characteristics but with doubled capacity thanks to a 40,000-litre coating tank. “Faced with the uncertainties related to
LAYOUT OF THE PAINTING PLANT
1 – Pre-treatment tunnel
2 – Drying oven
3 – Powder coating booth
4 – Liquid painting booth
5 – Baking/curing oven
6 – Monorail conveyor
7 – Electrical control unit.
the metallurgical industry, also confirmed by the recessionary trend in the foundry sector in recent months (-12.6% of ferrous foundries compared to the first quarter of 2023),” emphasises Gallerani, “we started to look for a plant solution that would meet our high versatility requirements and, therefore, be able to apply both liquid and powder coatings depending on the needs and demands of the market. Its team was among the few consulted who met the strict timelines for the dismantling of the old painting plant and the installation and commissioning of the new one. Their proposal seemed the most suitable to us from a technical standpoint to reach the 220 °C in the oven required to bake the paint film on particularly large items.” Compared with the previous system, the only elements that remained unchanged were the loading and unloading areas and the 3-stage stainless steel pre-treatment tunnel (phosphate degreasing and 2 rinses - see Layout, 1), which had been installed in 2021 to replace the previous one. Verona Impianti 2002 thus designed and installed a new drying oven (see Layout, 2), a manual liquid coating booth (see Layout, 4), and an air-curtain baking/curing oven with a double blown air burner (see Layout, 5). It also relied on its partner Se.Po (Olginate, Lecco, Italy) to develop and install a boxed monorail workpiece handling system (see Layout, 6). The powder coating booth (see Layout, 3), on the other hand, was chosen directly from SVI: “We opted for SiverNordson’s dense phase coating technology,” Gallerani continues, “and decided to install a booth with 2 reciprocators and 4 guns per side and a manual post-finishing station, turning to Nordson’s exclusive dealer for Italy, Siver Srl (Corciano, Perugia). We can now choose between liquid and powder application depending on the material to be coated and
the current production flow. Given the greater resistance and durability of powders, one- and two-component liquid paints are mainly used for parts that are to be repainted at the customer’s premises after assembly or that cannot be powder coated because they do not can withstand paint curing temperatures”.
“For SVI to achieve significant energy savings and minimise its impact on the indoor and outdoor environment,” says Albino Tamellin, the owner of Verona Impianti 2002, who took care of the design and installation of the new system together with his sons Pietro and Stefano, “we adopted two special technical measures. One is the suction system of the dry liquid coating booth, with vertical airflow and Andreae and Paint-stop filters: instead of placing it on the side, as is usually done, we installed its suction device on the floor to improve the coating chamber’s degree of cleanliness. The other relates to the characteristics of the oven, which we have equipped with two 40 kW convection burners to reach the 220 °C required for powder curing and with air curtains designed to retain heat inside the oven and avoid dispersion, combined with a system for reintroducing hot air through the parts’ inlet and outlet (“economiser”). Thermal insulation in mineral wool with low thermal conductivity allows heat loss from the walls and, therefore, heat consumption to be reduced to a minimum.”
“As for the liquid booth’s suction system,” Gallerani confirms, “we immediately noticed that the area was cleaner: our operators now work more easily and with improved visibility. At the same time, the accurate management of the oven temperatures guaranteed by the 2 burners is
Turn key solutions for industrial wastewater treatment
Design and manufacturing of plants and chemicals for industrial wastewater treatment
Chemical-physical plants
Sludge treatment and compactor systems
Ion exchange demineralization systems and reverse osmosis systems
Oil separators
Filtering systems
Batch type systems
Flotation units
Chemicals and spare parts for water treatment
fundamental to achieving perfect coating results on a hard material like cast iron. Regarding energy consumption, the current oven cannot be compared to the previous one due to the distance in time and technology between them. However, we can certainly say we are pleased with this investment both in terms of methane gas consumption and because the Verona Impianti 2002 team was able to install a very large oven in the reduced space we had made available to it, with the opening for the passage of parts reaching a size of 1200 x 2000 mm. The conveyor is 199 m long in total, and its path inside the oven has a useful length of 55 meters for baking/ curing. After baking, the parts are taken outside the factory for cooling and then back inside for unloading. In total, an average cycle lasts 3 hours.”
“We chose to use this new system alongside the dip coating one to be able to effectively meet any need of this fluctuating market, the evolution of which is so difficult to grasp,” explains Gallerani. “With the closure of many foundries and their relocation abroad, we looked for a solution that would enable us to continue to serve our customers in a sector that has become increasingly competitive precisely because of the state of the foundry industry. We manage batches according to the size of the components: on this new line, we can handle parts up to 900x900x1410 mm that can weigh up to 250 kg, whereas in the dip coating line the workpieces can be up to 2200 mm in height and half a tonne in weight.”
Technical service, support and maintenance of wastewater treatment plants
This continuous-flow plant installed in 2001 consists of a 4-stage pre-treatment tunnel, a 40,000-litre immersion tank, an external dripping area, a drying oven, and a powder booth. “This is used as an alternative in case of breakdowns or work peaks and complements the 6 automatic liquid booths and the touch-up area where we apply a finishing coat on already-primed castings” –, and a baking oven that can reach 210 °C and where the components dwell for 1 hour. “The line is also equipped with 2 stainless steel blast chillers with showers that cool the outgoing fumes and filter any resin or solvent that could be released into the atmosphere.”
Work on the installation of the new system began at the end of May 2023, and the line was already in operation by mid-July.
“Verona Impianti 2002 had guaranteed to us that the new plant installation, including the dismantling of the existing plant, would be completed quickly, in about a month and a half. Indeed, its technical team managed to meet the planned delivery schedule despite working in conditions that were not always easy. This was another element that convinced us of this company’s worth. In addition to the environmental aspect, as we were looking for a sustainable plant solution that would also allow us to respect the outside environment due to our proximity to the city centre, we also greatly appreciated the possibility of fully monitoring our coating process data in terms of consumption and times in line with the Industry 4.0 parameters. This enables us to make coherent offers to our customers, who do not risk any unpleasant surprises: this is a significant advantage for a contractor like us.”
Despite reiterating that this is not the best time to further grow the company, Gallerani says: “Our next step will be to move our shot blasting department to expand the robotised liquid plant and especially its oven, thus speeding up the workflow and increasing production capacity. For this project, too, we intend to rely on the professionalism and expertise of Verona Impianti 2002.”
The entrance to the baking/curing oven: the dimension of the opening for the passage of workpieces is 1200 x 2000 mm.
The outside of the baking/curing oven.
A liquid-coated marine engine.
To meet the requirements of a major company in the railway sector, Mirodur developed a water-based coating system specifically designed for train axles, providing excellent results in terms of paint adhesion and corrosion resistance. In addition to its success in the railway sector, Mirodur works with numerous international manufacturers in the car and truck-making industries, which it supplies with customised, high-performance coatings for decks, axles, universal joints, and oil filters.
In modern industry, high-quality surface treatments are crucial to ensure the high durability and performance of metal components in critical sectors such as rail and automotive. At the same time, the continuous evolution of technologies and environmental regulations requires paint and coating manufacturers to develop more and more innovative and customised solutions that meet increasingly stringent requirements.
Mirodur Spa, an Italian producer of paints and coatings based in Aprilia (Latina), stands out on the market for its ability to develop personalised solutions that meet the specific needs of each customer. One of Mirodur’s most recent successful projects involved a major company in the railway sector, which had to solve a series of problems related to using a one-component coating on train axles. Although this paint product was imported from Germany and certified to Deutsche Bahn standards, it did not fully meet the company’s expectations due to some issues, including adhesion, corrosion resistance, and application difficulties, which compromised the operational efficiency and quality of the treated components. The need to improve the performance degree of its train axle surface treatments had become a priority for this company, which turned to Mirodur to develop a
better performing and more environmentally friendly coating in line with the sustainability trends in the automotive sector. The Italian manufacturer met these requirements with an innovative, tailormade solution, demonstrating its ability to solve complex problems and significantly improve the quality of surface treatments in the railway industry.
The customer needed a paint product that ensured as follows:
Improved corrosion resistance and long-lasting protection against weathering;
Ease of application and compatibility with existing coating equipment: the coating had to be easy to apply and compatible with the production processes already in place without requiring significant modifications to the plant or automated devices such as robots and reciprocators;
Optimal chemical and physical properties, such as high adhesion, mechanical strength, and chemical resistance;
Higher sustainability.
The solution offered by Mirodur: Idralpox
Mirodur specially formulated a water-based two-component epoxy product that met these specifications. After carefully analysing the requirements, its technical department worked with the customer to formulate a paint perfectly suited for use in automatic coating systems, maintaining an optimal viscosity level and catalysis ratio without compromising its pot life.
The solution developed, marketed under the name Idralpox, is a two-component, waterdilutable, rust-proof epoxy product that offers numerous advantages, including as follows:
Excellent barrier effect;
Effective protection against corrosion thanks to the special inhibitors it contains;
Excellent resistance to condensation and neutral salt spray;
Exceptional adhesion on various substrates, including iron, stainless steel, galvanised sheet metal, and aluminium;
Ease of application and compatibility with the customer’s equipment and automated systems.
The results achieved
The product developed by Mirodur significantly improved the quality of the coating application process and passed all the required corrosion resistance tests, including salt spray tests. Based on these results, the customer was convinced of the effectiveness of Mirodur’s two-component epoxy coating and decided to replace the previously used product.
Mirodur’s innovative and customised approach also proves that close cooperation with the customer and in-depth technical knowledge can lead to the formulation of high-performance solutions that guarantee excellent results even under the most challenging conditions. For the railway sector,
Mirodur also produces one-component coatings with high resistance to weathering and high temperatures, complying with the technical specifications of Ferrovie dello Stato Italiane. Its products are designed for durability and for withstanding the mechanical and chemical stresses to which railway components are subjected.
In addition to the railway sector, Mirodur also produces a range of customised paint products for the car and truck sectors, particularly for the following parts:
Axles: Mirodur offers a diverse range of products, including primers, one-component vinyl paints, and acid components for higher paint adhesion. These solutions are designed to improve the adhesion and durability of coatings on metal surfaces, meeting the unique needs of
the automotive and truck production sectors.
Universal joints: the company favours the use of water-soluble, one-component products that have been extensively tested to effectively withstand salt spray environments for up to 250 hours. For customers with more demanding requirements, Mirodur also offers two-component epoxy solutions.
Oil filters: Mirodur provides solutions based on thermosetting enamels, which are ideal for high-volume applications thanks to their superior scratch resistance and adhesion. These products are designed for long service life and optimal performance in automated and robotic production cycles.
Mirodur’s products comply with the main industry regulations, such as Italian Legislative Decree no. 161/2006, and are designed to pass rigorous salt spray tests and meet high quality and safety standards.
Ral-Est details the technology for chemical paint stripping developed by ALIT Technologies Spa through a case study on the use of METALSTRIP 1333/1.
“The Estonian company Ral-Est OÜ began its operations nine years ago with the goal of providing innovative solutions to the Estonian painting industry.
Today, Ral-Est is the official distributor of ALIT Technologies Spa in the Estonian market and offers complete ALIT technical solutions
for chemical paint removal, providing its customers with both paint stripping chemicals and equipment technology. Ral-Est also offers an excellent direct powder coating service carried out in its own coating line and a job paint stripping service using both immersion and spray chemical stripping systems.
ALIT’s regional manager Bojan Stevanovic asked Ral-Est’s CEO, Olev Ustinov, to share how Ral-Est’s journey in the paint removal field began. Ustinov explained: “Nine years ago, chemical solutions for paint removal were relatively unknown in the Baltic countries, and we at Ral-Est were the first Estonian company to adopt and propose this type of solution based on the practical needs of the time. Our first partner and supplier of paint stripping chemicals and technologies was based in North America. The information provided to us at that time was scarce, and this collaboration proved to be difficult, complex, and ultimately expensive. This sparked a strong interest in us to seek better paint removal solutions, leading us over the years to collaborate with the Estonian Institute of Chemistry, funded by the European Development Fund. We tested products from most of the companies supplying the European paint stripping market, and today we can confidently say that the best products we have tried have been brought to the market by ALIT Technologies Spa.”
Olev Ustinov continues his analysis by stating: “The paint removal sector is rapidly evolving; we believe that the main competitive advantage lies not only in the ability to chemically strip products quickly and accurately but also in the ability to rapidly identify the best technical solutions to meet the specific requests of customers. In this aspect, the collaboration with ALIT has proven to be positive. We consider technical
support, the development of innovative solutions, and the proposal of specific equipment and chemicals as crucial requirements for a profitable collaboration. All these aspects are exactly what ALIT represents and provides.”
We asked Olev Ustinov to present a practical example of collaboration with ALIT, and he shared the case of a Ral-Est customer equipped with a small spray paint stripping machine. “The customer was using a competitor’s paint stripper and was dissatisfied with the excessive cycle times and the rapid deterioration of the paint stripping bath. Ral-Est proposed the use of Metalstrip 1333/1, an alkaline, waterfree, multi-metal paint stripper that is non-aggressive on aluminum products. The first test proved to be immediately positive; the product, applied by spray at 70°C, provided good paint removal in a short time, but most importantly, the duration of the paint stripping bath was finally satisfactory for the customer, making the process economically fast and advantageous. In this example of collaboration with ALIT, the customer’s request was quickly analyzed by both the Ral-Est and ALIT teams, and the proposed solution immediately proved to be correct, with great satisfaction on both sides.”
Engineering specialized in the supply of systems for surface treatment, painting and coating
E-COAT SYSTEMS
LIQUID PAINTING SYSTEMS
POWDER COATING SYSTEMS
SELF-LEARNING ROBOTS FOR AUTOMATED PAINTING
SYSTEMS FOR THE TREATMENT OF VOCs EMISSIONS
Olev Ustinov continues by describing the feedback from using METALSTRIP 1333/1. This information comes from over a year of product use directly in the Ral-Est paint stripping plant, as well as feedback from end customers.
“In Estonia, the product METALSTRIP 1333/1 is predominantly used by spray at a temperature of 70°C. The application field is multi-metal, but the most common use is the paint stripping of automotive alloy wheels. The paint stripping times vary depending on the type of paint, the thickness applied and often the geographical origin of the product. For example, 15-30 minutes for car wheels from China, and 30-120 minutes for car wheels from Germany, with applied thicknesses up to 250µm. After the paint stripping phase, a spray rinse stage is necessary; subsequently, the wheel can be dried and repainted.”
Olev Ustinov further specifies that “the best performance of the paint stripping bath is achieved by adjusting the alkalinity of the bath by dosing of METALSTRIP AKTIVATOR 1533, and by regularly removing paint sludge. This filtration activity can be done using a filter press or more primitive sedimentation systems, but filtration certainly allows for a
longer duration of the paint stripping bath.
Olev Ustinov confirms that “the results we have obtained in our paint stripping plant using METALSTRIP 1333/1, combined with the satisfaction index of our customers, have given us a lot of enthusiasm!”
“Following the good results obtained and the great energy of the RalEst team, an important commercial and marketing activity has started, including actual visits to potential customers in the Estonian painting industry, and all this promises very interesting results in the medium term” Bojan Stevanovic concludes, stating also that “The satisfaction is mutual, in the sense that ALIT is also very satisfied with the relationship with Ral-Est, both professionally and personally. Ral-Est presents itself on the market with a clear willingness to support the customer, providing them with chemicals, equipment, and transferring all the necessary know-how to ensure quality and sustainability of the paint stripping process.”
For further information: https://alit-tech.com
The strength of Europolveri products does not derive from the sole mixture of carefully selected raw materials, but rather from the people who study, model and formulate powder coatings thanks to more than 40 years of experience, and provide customers with the best solutions on the market A clear corporate philosophy and a shared vision have allowed to supply a vast range of produc ts for three generations With more than 1000 products available in stock and over 40,000 already formulated, Europolveri offers infinite solutions to customer requests
Kevin Biller kbiller@chemquest.com
Hi Joe,
I hope things are going well with you. As you know, most industrial powder coating systems have about 60-70% transfer efficiency on average, which means about 30-40% of the powder does not adhere to components being powder coated. Therefore, they tend to work on reusing the excess overspray powder (aka reclaimed powder) in order to increase efficiency and cost-effectiveness. Consequently, we have started evaluating the possibility of reusing reclaimed powder in a thermal spray (flame spray) coating process. We prepared some sprayed metal components with 100% reclaimed powder and tested them against some sprayed metal ones with 100% virgin powder. The results showed no differences between them, in terms of other parameters such as coating adhesion, wear performance, etc. Also, the chemistry of the reclaimed powder remained within our spec. As we are still evaluating this, I’d like to get your opinion and thoughts on reusing reclaimed powder. I know you are very experienced and have seen many different applications. Have you seen others using reclaimed powders (particularly in a flame-spray coating process)? Is this something that you recommend? If yes, what mix ratio of reclaimed powder vs. virgin powder would you recommend?
Thank you for your time. Your answer to my question will be greatly appreciated.
I am looking forward to hearing from you.
Thank you,
Reza Eghtesad Tulsa, OK
Thank you for your question. You offer an interesting path to managing overspray powder coating. You are correct that typical application systems operate with 60-70% first-pass transfer efficiency. Of course, this depends on what you spray and the quality of your application equipment and controls. For example, transfer efficiency is poor when spraying wire racks (mostly air), but pretty good when coating flat panels. As for flame spraying reclaim or a mix of reclaim and virgin powder, it sounds like a good idea and may work. Here are my comments and concerns:
1. Powder sprayability is mostly tied to particle size distribution (PDS). Virgin powder, if properly manufactured, will have an ideal PSD. Reclaim contains the less-than-desirable particles, such as a higher concentration of fines and coarse particles. This makes the reclaim more difficult to fluidize, transport, and electrostatically charge. Consequently, reusing reclaim powder involves blending it with virgin powder. How much depends on how the blend behaves in the application process, namely fluidity, transport, and charging. With flame spray, you obviously eliminate the requirement to charge the powder.
2. To be honest, I’m not a big fan of the flame-spraying powder process. Why, you may ask? I think it’s a bad idea to create a cloud of fine organic particles with lots of air (i.e., oxygen), move it through space, then pass it through a flame. I can see the generation of a flamethrower effect or, worse yet, rapid combustion (Ka-BOOM). That said, there may be alternate thermal-spray processes such as plasma or high-intensity IR that may be safer, but I am not sure.
3. Regarding the ratio of virgin to reclaim powder, you should incorporate a fluid-flow additive to help the non-ideal PSD fluidize and
transport better. This can impair electrostatic charging; however, if you’re using a thermal spray process, that should not be an issue. Fluid-flow additives are typically based on fumed silica or fumed alumina and should be incorporated at low levels (say 0.1-0.2% by weight). Good luck with your inventiveness. It’s always encouraging to see someone thinking outside of the box...of powder. Kind regards, Joe Powder
Dear Joe,
We are utilizing two separate grinder/mixers for premixing and chips milling in the powder coating laboratory. Can you explain why using separate grinders is so important to prevent craters or other surface imperfections? Is cleaning only one extruder for premixing and chips milling insufficient to overcome the crater formation?
Best wishes,
Cuneyt Altindas
Turkey
Dear Cuneyt,
Thank you for contacting me. This is a good question. The reason for using separate mixer/grinders for premixing and milling (pulverization of extruded chips) is to avoid contamination of one product into the other. Specifically, contaminating chips with premix will probably result in film defects such as craters and extraneous “bits.” This is because the unprocessed raw materials in the premix are incompatible with the extruded material.
For decades, Radial has been designing, building and installing tailor-made coating plants for metals, plastics and wood. Our systems are the ideal choice for those who desire a cutting-edge turnkey solution.
For example, some of the additives in the premix (e.g., the flow agent) can cause craters in extruded chips or the final powder. In addition, dry pigment and fillers may not be dispersed (de-agglomerated) and could cause “bits” in the final film.
Extrusion (aka compounding) melts and mixes the resinous components in a powder formula, thereby making them compatible. The shear caused by the extrusion process also deagglomerates and disperses the pigments. This provides better color development and consistency. If you intend to use the same mixer/grinder for both premixing and milling, you must thoroughly clean the equipment between processes, especially going from premixing to milling.
I hope that this helps.
Kind regards, Joe
Hi Mr. Joe Powder!!
I have a question, we have a powder coating process here in our facility, and we use an epoxy powder from a reputable manufacturer. This powder doesn’t pass an accelerated exposure test. My question is, will this kind of powder pass the QUV test?
I ask because we are having trouble with our customers.
Thanks for your time.
Tito Mansilla Monterrey,
Mexico
Buenos días Tito,
Thank you for the question. The QUV test simulates the exposure a coating can experience in a high-intensity UV environment like South Florida or Mexico. The QUV wavelengths are close but not identical to the sun. Regardless, it can be used as a decent comparative test for similar formulations.
Epoxies will not last long in a QUV chamber without fading and chalking. Similarly, a hybrid powder coating that also contains epoxy resin will degrade quickly in a QUV cabinet. Consequently, epoxy and hybrid powder coatings will fade and chalk very quickly when exposed to sunlight.
Powder coatings possessing good to excellent QUV and outdoor performance are based on the following chemistries: polyester TGIC, polyester HAA, polyurethanes, acrylic (automotive), and fluoropolymer (high-end architectural). Pigmentation and additives in the formulations also have a strong influence on UV resistance. I recommend you discontinue using epoxy and hybrid powder coatings for any parts that will be exposed outdoors.
If you need more guidance, please let me know.
Best Regards, Joe
Monica Fumagalli ipcm®
Powder coating contractor ABF Color has identified mechanical pre-treatment as the key to its success. This company was indeed one of the last coaters to be established in its area but one of the first to install a shot blasting machine from Carlo Banfi, now an OMSG brand, for the mechanical pre-treatment of large parts. In 2023, it acquired its third coating plant, retaining its trusted suppliers, including OMSG, Silvi, Gema, and Futura, and combining mechanical pre-treatment with a chemical stage for even more effective substrate preparation.
The optimal adhesion of paint layers and the effective corrosion protection of metal substrates cannot be guaranteed without adequate surface preparation.
During machining, sheet metal surfaces are contaminated with either organic residues, such as lubricants used to reduce friction and/or heat, or inorganic residues, such as oxides and calamine resulting from hot machining stages or burrs and dust generated in stamping or cutting operations. For the latter, the introduction of laser cutting in manufacturing has brought many advantages over traditional mechanical systems, both from an economic point of view, because the process is faster, and in terms of results, since it allows for higher precision with a tolerance of +/- 0.1 mm, thus eliminating the need for further treatments. This type of operation does, however, result in the formation of inorganic residues such as dust and burrs, albeit in small quantities.
“Shot blasting is the ideal solution to ensure the complete removal of these limited amounts of contaminants that can, however, substantially affect the quality of the subsequent coating operation,” states Adriano
Baesso, the owner of ABF Color Srl (Curtarolo, Padua, Italy) with his brother Francesco. “This is one of the last companies established in our area to powder coat large-sized fabrications. As such, in an area –the Veneto region – dotted with many contractors offering the same service as ours, we chose to differentiate ourselves by specialising in the surface preparation of steel by shot blasting and immediately equipping ourselves with the first of three plants that we would go on to have OMSG - Officine Meccaniche San Giorgio (Milan, Italy) design and install for us. This strategic choice enabled us to win the trust of our customers in just a few months, which has grown exponentially since then.”
The Baesso family is the heir to a long-standing company celebrating its 130th anniversary this year.
“My father runs Fratelli Baesso, which has been producing wine-making machines since 1895,” Adriano tells us, “and has an in-house coating department for the steel they are made of. ABF Color’s experience in
ABF
Many institutional representatives attended the inauguration of the new factory in 2019.
of the line installed in 2019, with a shot blasting machine, an oven, and a powder coating booth.
surface coating comes from there – an incredible training ground, as the regulations governing food-contact coatings are among the strictest. Partly due to the family business’ celebrity, the establishment of ABF Color in 2013 raised a lot of curiosity but also mistrust on the part of other local companies. Such scepticism, probably motivated by the fact that my family’s name was linked to the wine industry and not to the coating one, was, however, quickly overcome. Within a few months, we had presented all the region’s leading metalworking companies with our services, promoting shot blasting as an alternative to traditional surface preparation. As mentioned, we were among the first to install a shot
blasting plant for structural steelwork in our area, and this choice was the springboard for our business.”
The Veneto region’s coating cluster
“We have also gained a lot of trust from institutions. In 2019, several regional and European government representatives attended the inauguration of our new factory, built in partnership with company Peruzzo Srl, which produces machines for public green care and sports facilities. The event’s appeal enabled ABF Color to become known in a wider geographical area. At the same time, our business ethics soon
The plant installed
can treat components up to 11 m in length and over 5 tonnes in weight.
© ipcm
led us to collaborate with other local companies offering the same services as us to create a coating cluster that today also attracts customers from other regions. We can perform special cycles with an excellent quality/price ratio, and this has also been a winning weapon.”
As a result, ABF Color’s production volumes grew well beyond expectations. At the end of 2023, it inaugurated a new factory with a third coating plant, which is now fully operational. “We dismantled our first plant, installed in 2013,” indicates Adriano Baesso, “and we currently manage our volumes using the other two lines: the 2019 one handles large-sized, heavy-duty components, whereas the newest one coats lighter and smaller parts, such as the ones intended for the agricultural sector.”
The coating plant for heavy-duty components
The coating line built in 2019 has a step-by-step monorail conveyor built by Silvi (Lesmo, Monza e Brianza, Italy), which also acted as the prime contractor and took care of the design and installation of the curing oven. The plant can treat components up to 11 m in length, 3
m in height, 1.6 m in width, and over 5 tonnes in weight. “This is the only line in the region with these characteristics,” says Baesso. “Silvi’s technical team developed for us a unique structure to handle very heavy components. It collaborated with OMSG –which had already supplied us with our first shot blaster in 2013 and, for this project, provided a shot blasting machine from Carlo Banfi, the brand it acquired in 2017 – and Gema – which designed and installed a custom booth equipped with 12 guns (6+6) and Venturi injectors to powder coat the peculiar components we are required to treat. All of these three companies have been our trusted suppliers since 2013. Futura Convogliatori Aerei became one of them more recently after supplying us with the conveyor for the latest coating line.”
The parts coated here are predominantly beams, metal mezzanines, and large structural metalwork, which undergo mechanical pre-treatment, with spherical steel abrasive designed in partnership with supplier Winoa to achieve the SA 2½ cleanliness grade and the roughness profiles required by customers, and the application of one- to three-layer coating systems for iron and stainless steel, up to corrosion class C5 for hot-dip galvanised steel. “Our next milestone will be obtaining ISO 12944 certification, confirming the corrosion protection effectiveness of our coatings.”
One of the projects of which ABF Color is most proud is the one realised for the Lakhta Center in Saint Petersburg (Russia), which houses the offices of Gazprom. “We coated the structural metalwork of 30 of the 90 floors of this building facing the Baltic Sea and, therefore, subjected to a high degree of salinity, successfully exceeding all specified quality standards. Lately, we have also been making a name for ourselves in the naval sector, thanks to a customer that
manufactures components for the British navy: after an initial request to coat material for three ships, we have received an order for six ships, confirming that our coating results are excellent and guarantee perfect resistance to the saline environment. We also coat furnishings for cruise ships: the tests conducted on them also proved their excellent degree of corrosion resistance after one year of daily exposure to the marine environment.”
The coating plant for light-duty components
“The decision to build a new line arose from the need to relieve the larger plant of batches with smaller parts – mainly intended for the agricultural sector, whose major brands, such as Kubota, have certified our coating cycle – and speed up our production flow,” explains Baesso.
“Unlike the other plant, where we only perform mechanical pretreatment, this line can perform a chemical, mechanical, or combined chemical + mechanical pre-treatment operation to prepare the surfaces adequately depending on the type of finish required by the customer.” This new line, therefore, consists of a continuous-flow, boxed, monorail conveyor from Futura (the largest in the range of this type of overhead conveyor) with 3 m load bars with a capacity of 500 kg each and a speed of 1 m/minute; a Tunnelblast shot blasting machine supplied by OMSG; a four-stage chemical pre-treatment tunnel; an oven divided into two zones, one for drying after chemical pre-treatment and one for powder curing at 180 °C; and a Magic Cylinder EquiFlow booth from Gema, also equipped with 12 guns and two stations for post-finishing to reduce the scrap rate.
Characteristics of the Tunnelblast machine
“The Tunnelblast 1525/12 series system,” illustrates Enzo Dell’Orto, the CEO of OMSG, “is the third shot blasting machine installed by OMSG at ABF Color. It is a tunnel-type plant suitable for treating medium and large-sized components moved horizontally, combined with an overhead conveyor (monorail or power&free type). The maximum workpiece dimensions are 1.5 m in width and 2.5 m in height. The shot blasting operation is carried out through 12 7.5-kW, single-disc turbines equipped with a direct drive motor, which project the metal abrasive at about 80 m/s over each workpiece’s entire surface as it moves through
the tunnel. 12 inverters control the rotational speed of the turbines and the resulting kinetic energy of the abrasive, preventing the deformation of thin sheets. The plant is also equipped with 12 special valves to feed the turbines, with two pneumatic cylinders. One of the main features of this shot blasting machine is that the rubber bands acting as screens to prevent the abrasive from escaping can be opened automatically by a device operated by pneumatic cylinders, to enable the workpieces that do not need to be subjected to shot blasting to pass through quickly. Finally, the machine is managed by a Siemens S7-1200 PLC with a 12” touch panel, already prepared to comply with the Industry
The two units performing chemical (left) and mechanical (right) pre-treatment on light-duty metal components.
Components exiting the shot blasting system.
The Tunnelblast shot blasting machine installed in 2023.
The rubber bands can be opened automatically through a device operated by pneumatic cylinders so that the workpieces that do not require a shot blasting treatment can pass through quickly. The 4-stage pre-treatment tunnel.
4.0 parameters and be integrated with the company’s management system, which is currently in the ramp-up phase.”
The pre-treatment tunnel and the drying and curing oven
The pre-treatment tunnel consists of four stages: 180-second degreasing, two rinses of the same duration (60+60 seconds, one with mains water and one with demineralised water), and a nanotechnology no-rinse passivation stage. “Identifying the right size for each zone was crucial to avoid any product overflow or dragging that would pollute the adjacent stages,” emphasises Silvi CEO Daniele Fumagalli. “The system we supplied to ABF Color is 28.3 m long, 1.6 m wide, and 4.68 m high, and the workpiece maximum dimension is 1.2 x 2.5 m. Both the upper part, which houses the actual tunnel where the spray bars are placed, and the lower part, where the tanks are located, are made of AISI 304 stainless steel. The tanks are also insulated with rock wool with a thickness of 60 mm. The tunnel has three doors for inspection and an access ladder. The demineralisation plant can treat 3,000 litres of water per hour.”
Silvi also designed and installed the drying and curing oven: “The drying
oven, which operates at a maximum temperature of 180 °C, consists of a robust supporting structure made of electro-welded galvanised steel profiles and an insulating layer of highly insulating rock wool. Our technical department has developed a special type of high-efficiency, backward electric fan to circulate the heating air. A plenum space is placed over the entire base of the oven for even distribution of hot air. Suction is regulated with adjustable shutters located on the underside of the oven. A fan specially positioned on the roof ensures the discharge of the products resulting from the curing of powders. At the same time, this air mass is compensated with filtered air intake. Finally, the curing oven has two combustion chambers totalling 300,000 kcal/ hour and can reach a maximum temperature of 240 °C. ABF Color uses it under special operating conditions.”
“Our two- or three-coat cycles,” Baesso confirms, “include a dry-on-dry application process with two or three dwells in the curing oven for 50 minutes. We decided on such a long curing phase because we noticed that the paint layer can flake off more quickly if it lasts less. Originally, the oven temperature was up to 180 °C, but the temperature of the
parts leaving it did not exceed 120 °C. However, we need them to reach 180 °C as well. Therefore, we have them dwell longer than standard in the curing oven, with excellent results for both high sheet thicknesses (55 mm) and reduced thicknesses (35 mm).”
As Adriano Baesso emphasised several times in our interview, ABF Color has always been supported in its growth path by the same suppliers. “Since our establishment, we have strived to select the best technologies on the market. In the case of OMSG, we started collaborating as early as 2013, and we immediately established an excellent personal relationship with its owner, Enzo Dell’Orto, which went well beyond the professional partnership. The reliability of this company is undisputed, as is the efficiency of its service: it has always solved any issue faced by ABF Color in a very short time. Silvi, represented by its owner Daniele Fumagalli, acted as the prime contractor for the two most recent installation projects: I chose it
because it presented us with solutions that I had not considered at all and whose effectiveness I was able to assess by visiting several plants installed by this Monza-based company. As for Gema, in addition to providing the best application equipment in terms of performance and speed, it offers truly innovative solutions. One of its latest innovations I would like to implement in our new plant is the Dynamic Contour Detection system, whose laser scanners ensure greater coating precision, increased transfer efficiency and finishing quality, and faster production flow with reduced touch-up frequency. Once I will verify its degree of performance, I may consider installing it on the older line as well.
“I would like to conclude by emphasising that we would not have grown up to this point without the collaboration of all these partners: their know-how and expertise have always compensated for the investment made in their equipment,” says Baesso. And ABF Color’s growth will not stop here: the company has already acquired another one-hectare plot of land on which it plans to build a new coating plant.
Frank Siegel
Walther Trowal GmbH & Co. KG - Haan, Germany f.siegel@walther-trowal.de
The new anti-friction lacquers that were specially adapted to the Rotamat coating systems, contain no chemicals that do not decay over time.
At the DKT 2024 exhibition, which took place from July 1 to 4, 2024 in Nürnberg (Germany), Walther Trowal and the Italian C.S.I.
Centro Servizi Industriali Srl presented an eco-friendly solution for the coating of mass-produced small parts made from elastomers. The new coating material, for the first time PFAS-free, has been specifically adapted to the Rotamat systems. PFAS (Per- and polyfluoroalkyl substances), which until today are part of many coating materials, decay very slowly in the environment or do not decay at all. They are also suspected of causing cancer. It is highly likely that the EU will completely prohibit the use of PFAS in the near future. For this reason, at the DKT exhibition the two companies presented the new PFAS-free anti-friction lacquers CSIP13 and CSIPN18 for sealing components made from elastomers or plastic - for example, O-rings or flat seals. Even though the new lacquers contain no PFAS, they have the same low friction coefficient as PTFE-based coating materials and offer the same life expectancy. C.S.I. developed the new lacquer specifically for the Rotamat coaters, exhibited at the DKT by Walther Trowal. Especially the Rotamat R 100 with its highvolume drum capacity is increasingly used by customers, who coat large components, for example, pleated protective covers.
Danilo Olivino, technical manager C.S.I., explains what challenges his team had to overcome: “We had to replace all substances containing
fluoride with an alternative anti-friction material. This demanded numerous trials regarding the general composition of the lacquer but also regarding the actual coating process. With its possibilities to run coating processes consistently within a wide range of different parameters, the Rotamat offers the ideal technology to precisely control the spraying operation in the drum. Especially the coating of parts for the automotive industry demands high process stability and consistency of results – the Rotamat systems offer these characteristics”.
Olivino continues: “The comprehensive sensor technology in the Rotamat precisely measures the data for controlling the flow rate per minute down to one tenth of a gram. This guarantees that the right amount of coating material is applied onto the work pieces and that the specified coating thickness is precisely maintained in a consistent manner”.
Walther Trowal already has a few customers who are successfully coating mass-produced small parts with PFAS-free anti-friction lacquers. For example, the Dutch Brüning Flexible Coating B.V., is coating, among others, O-rings and X-rings in several Rotamat systems.
The Rotamat system represents an economical solution for coating mass-produced small parts, such as O-rings, handles, springs and
screws. It allows the treatment of a broad spectrum of parts made from metal, wood and all kinds of plastic materials. This includes parts for the automobile and cosmetic industry, components for stationary supplies, toys, parts for the textile industry as well as seals and attenuators (dampening elements). The coating materials can be water- as well as solvent-based.
Rotamat systems are used for decorative coatings with numerous water- and solvent-based ornamental and functional lacquers.
But they are also employed for coating with anti-friction lacquers, bonding agents, corrosion protection materials or isolation lacquers.
In Rotamat systems batches of small parts are coated in a rotating, closed spraying chamber (drum). Automatic spray guns are evenly applying the coating material onto the work pieces, which are continuously tumbling over each other. This results in precisely coated surfaces with an even coating thickness and an excellent life expectancy of the applied coating material.
Even geometrically complex or very delicate parts are discharged from the machine with an even coating, in single flow and completely dry. After leaving the Rotamat the work pieces can be immediately processed in downstream manufacturing or assembly operations. The coating process runs fully automatically. The operator must only load new batches of raw parts and unload the batches with finished parts. The costly and time-consuming placement of the parts on special racks – required with conventional coating systems – is completely eliminated.
From the left: thanks to the new PFAS-free lacquers from C.S.I. the coating in Rotamat systems is particularly eco-friendly; in its plant in Bolgare at Lago d’Iseo/Italy, C.S.I. operates a total of five Rotamat coaters; the Dutch Brüning Flexible Finishes B.V. also coats O-and X-rings with PFAS-free lacquers.
The system with OptiSpray All-in-One pump technology and double OptiSpeeder powder hoppers (DualSpeeder) enables the handling and preparation of two independent colours one after the other for ultra-fast colour changes or in parallel for simultaneous coating from both OptiSpeeder powder hoppers.
Federica Alberti
SG Projects Srl – Voghera (Pavia, Italy) federica.alberti@sgprojects.it
Cataphoresis is one of the most widely used surface treatments to protect components against chemicals and corrosion. As a company specialising in the design and installation of coating solutions including cataphoretic technology since 1985, MEGA-TEC has found in SG Projects its trusted distributor in Italy to meet the needs of the most demanding customers.
Cataphoresis is an economical, sustainable, and environmentally friendly coating method. This advanced technology for the surface treatment of metal is widely used to protect steel, galvanised steel, and aluminium components both as a primer and as a one-layer surface finish. Cataphoretic coating systems significantly improve the performance and durability of the treated parts. Their main areas of application include the automotive industry (cars, motorbikes, and bicycles), agricultural and construction machinery, household appliances (washing machines and refrigerators), air conditioning and heating systems (radiators), electrical appliances, metal furniture, and building structures.
The workpiece to be coated is connected as a cathode to the direct current field of the electrolyte (aqueous paint solution) and attracts cations from the paint. Electrophoretic cells (EFC) that can be flat, semicircular, or tubular are connected as anodes and are used to maintain equilibrium concentration in the paint bath. The thicker the coating, the more resistant the layer. That leads to the formation of an even layer over the entire surface, including difficult-to-reach areas such as edges. The achieved thickness is usually between 15 and 45 μm. The coating must then be cured in a curing oven at temperatures between 160 and 180 °C. Therefore, a part must possess three prerequisites to undergo cataphoresis: it must be made with a conductive material, it must be able to be immersed in a cataphoretic paint bath, and it must withstand temperatures of around 180 °C.
The main advantages of this technology include as follows:
reduced environmental impact thanks to the low solvent content (0.5-2%);
minimal paint loss thanks to the closedloop coating system (paint yield: 99.9%);
reduced emissions and limited production of solid waste and waste water;
high corrosion resistance of the coating (approx. 25 μm/1000 hours in a salt spray chamber);
high adhesion and mechanical resistance of the coating;
uniform coating thickness over the entire surface, including difficult-to-reach areas;
automatic thickness control;
quick (about 180 s), simple, and repeatable process;
easy process automation and control;
reduced workload and limited demand on operators;
overcoatability with specific products;
increased safety thanks to the innovative features related to the electrodes and the membrane type.
the only manufacturer of all cell types
MEGA-TEC (Czech Republic) designs, produces, and supplies coating lines based mainly on KTL technology, membrane process units, and EFC cells equipped with RALEX® membranes, developed and produced in-house. Currently, MEGATEC is the only manufacturer worldwide that can supply all types of EFC cells: it produces both welded and extruded tubular cells and flat and semicircular cells. It also manufactures membranes for both cataphoresis and anaphoresis.
With over thirty years of experience in the e-coat field, it can always find the ideal solution to meet the most demanding customer requirements. It offers complete customer assistance services with up to four years of warranty, after-sales services, and the optimisation and upgrade of
production lines. In particular, MEGA-TEC’s partner company for distributing its coating products in Italy is SG Projects, ensuring continuous customer support and acting as a responsive intermediary to solve any problem that may arise on cataphoresis lines.
Welded tubular cells: thanks to MEGA-TEC’s experience in developing electro-separation membranes since 1985, its welded tubular cells with a RALEX® AM6HD (diameter 81 mm) membrane are among the best EFC cells. The most effective permselectivity on the market and low electrical resistivity ensure ideal pH recovery in the bath. MEGA-TEC can provide a four-year warranty for all its membranes because they are produced with its specially designed in-house automatic welding equipment.
Extruded tubular cells: within this product family, the RALEX® AMXT membrane (diameter 65 mm) is the latest successful solution developed by MEGA-TEC. Thanks to these membranes’ mechanical properties, the extrusion process without welds ensures smoother surfaces and, therefore, streamlined cleaning operations. Tubular extrusion also guarantees compatibility with currently used extruded membranes.
Flat and semicircular cells: the cells with a RALEX® AM5HD membrane are ideal for retrofitting projects and any application requiring flat and semicircular cells. As a manufacturer, of course, MEGA-TEC can also produce any cell type required by the market in customised dimensions.
Long-lasting attractiveness of facades, buildings and industrial products made of aluminium, steel and galvanized steel
Anne Banuls, a professional with a long career in the powder coatings industry, recently joined SherwinWilliams as Segment Manager for Building Products, one of the key business segments of Sherwin-Williams. During our interview, Banuls shared key trends – such as lean production, reduction of complexity, product lines simplification, innovation on purpose and quality performances – that were clearly showcased at the PaintExpo trade fair last April, where Sherwin-Williams was an exhibitor.
Banuls shared key learnings from her career and her vision for the SherwinWilliams Building Products and Design segment: To keep fun in what we are doing every day and to maintain passion in one’s work. She’s ready to take the passion she has maintained throughout her career and bring it to SherwinWilliams to achieve her ambitious goals. Let’s learn more about what she envisions.
ipcm®: Can you outline your career, experience and key learnings in the paint and coatings industry?
Anne Banuls: I am a chemist and I have a master’s degree in biotechnology and another in marketing. I have been working in the field of paints and coatings for 28 years now, in particular in the powder coating segment, covering different roles. I can easily say that my career has been a journey from raw materials to end-user applications. I started in a French lab as a young chemist; during that period, I came to understand the basics of formulation. After that, I became the Lab Manager for the European laboratory of my first company in the powder coating industry. There, I was able to learn the importance
of the platform concept and the simplification approach while also starting to go toward customers. To do that, I took on the role of Technical Field Manager, and it was extremely interesting because I learned the value of our products for customers. Sometimes, in the lab, we would develop innovative products, but it is crucial that these developments are made with purpose. Working in front of customers as a Technical Assistant – training them to the use of the coating products and handling claims and returns – made me understand the connection between the technology and the end user. For professional growth, I took on the role of Product and Marketing Manager to learn market intelligence, for example, how to define which type of product line we need to develop in the lab, how we can train our sales force and how to sell the right product to the right market. Finally, I became Business Manager for powder coatings in Europe. During that period, I was also fully involved in label organizations. For 20 years now, I have been a member of the Qualicoat and Qualisteelcoat organizations,
which are important for the architectural business.
To sum up, key learnings of my career are the need for purposeful innovation; the concept of “the leaner, the better,” which means to reduce production complexity both product-wise and process-wise; and the importance of collaboration within the team. Alone, we are fast; together, we are going further.
When Sherwin-Williams asked me to join the Company to take manage the Building Products and Design segment, which has been a core segment throughout my career, I was very happy and very committed to the new challenge.
ipcm®: What goals have you set for the Sherwin-Williams Building Products and Design segment?
Anne Banuls: Sherwin-Williams has over 30 years of expertise and experience in the metal architecture industry in Europe, but under different company names and product line names. So, one of my first
goals is to unify the brand names and to strengthen Sherwin-Williams brand awareness in the market. To do so, the first step – which we have already started – is to unify our existing powder coatings product portfolio under the brand name of Syntha Pulvin®. The second goal is to grow through innovation and differentiation since we already have best-in-class product quality. The third is to execute our sustainability strategy. Powder coatings offer some sustainability attributes due to low levels of VOCs and pure solid content. Sherwin-Williams is working to continuously enhance its powder coating sustainability attributes and performance.
ipcm®: What are the strengths of Sherwin-Williams in the Building Products and Design segment?
Anne Banuls: Sherwin-Williams is a big-scale company with a global
vision, a regional strategy and a local presence. This allows us to capitalize on the power of procurement on a global level and on the synergies between different business units and different sites, and also have people in front of the customer. The customer-supplier relationship is very crucial in the business. Sherwin-Williams has a Design Engineering team dedicated to our customers who can recommend designs or energy optimization methods, which is important for powder coatings.
So, global vision and local presence are the first strength. The second one is that Sherwin-Williams is present across different coating segments, like textile, wood, automotive, furniture and – of course - metal architecture. This brings us a deep understanding of colour trends and design. We have a extensive product in stock, on top of specific collections like the Syntha Pulvin Anodite Collection and the
recently launched Vision 2030 Collection. For example, we recently invested in state-of-the-art bonding equipment1 to do some best-inclass metallics, which we call Mastered Metallics, in our Minerbio, Italy, production site near Bologna, Italy.
ipcm®: What are the needs and requirements that you are recognizing in the market right now?
Anne Banuls: I recognize two trends or needs in the market. One is related to the product itself, and one to service, to customer support. In the Building Products and Design segment, asset protection is increasingly important and is also one aspect of sustainability, since the longer an asset will last, the less often it will require being restored or replaced. As far as aluminium is concerned, asset protection means UV resistance: The trend is definitely from Qualicoat Class 1,
1 A. Venturi, A New State-of-the-art Colour Bonding Technology Brings a Wealth of Product Enhancements at Sherwin-Williams: Higher Quality, Efficiency, and Sustainability in the Manufacturing of Metallic Powder Coatings, ipcm® n. 83, Vol. XIV, Sept-October 2023, pags 72-78
which is now the standard quality, to Qualicoat Class 2. Key decisionmakers among powder coating manufacturers have been working toward this for more than a decade. In this context, Sherwin-William offers the Syntha Pulvin Class 2 generation of powder coatings with enhanced performance, including the enhanced UV fastness but also low consumption (g/m2) and improved carbon footprint with low-bake properties.
As far as steel is concerned, corrosion protection is key for durability of an asset. Sherwin-William has developed the Valde Prime range, with Qualisteelcoat approval for a number of configurations. The range contains special anticorrosive pigments and provides good resistance to chemical agents, fuels, oils and mechanical damage.
Product-wise, I see another trend emerging: The need to make powder-coating application easier in order to compensate for the increasing complexity of extruded profiles in terms of geometry and to offer robust formulations due to increasingly high line-speed.
Powder coatings manufacturers can help applicators by working on their products to promote thickness uniformity, better penetration, and yield and process efficiency during application. Reducing the complexity of application is not only a task for equipment manufacturers – we can be of great help in this respect as well. As a powder coatings supplier, Sherwin-Williams is working on simplifying its product portfolio and the colour offerings to be able to best serve the customer.
As one last trend, I would mention the need for agility and reactivity of customer service. The market requires a shorter time-to-market and fast responsiveness to technical inquiries.
ipcm®: How do you translate the word “sustainability” within your market strategy for the Sherwin-Williams Building Products segment?
Anne Banuls: We translate it into low-bake generation powder coatings with uniformity of gloss and finish across the different chemistries. The Sherwin-Williams Research and Development team is
working to have all products, classes, glosses and finishes have a lowbake option with the same optimized curing window, which is not the lowest possible but the most appropriate for that application. I would say that this is the credo we plan to promote and that are solutions the customer can use or, as I said at the beginning of the interview, reflect innovation with purpose. Sustainability is also using recycled materials or bio-based raw materials. Sherwin-Williams is more in favour of reusing materials; as a matter of fact, we have developed a new product range called Powdura® ECO, which has enhanced UV resistance, low bake (answer to the energy optimization need) and made of recycled materials rPET.
“If you Can Dream it, you Can Do it”
Monica Fumagalli ipcm®
The last edition of Merck Effect Day, the annual event organised by the German multinational’s Italian branch to inform on current trends in materials, finishes, and colour, was held in Modena on 12 June.
Merck KGaA, a global company based in Darmstadt (Germany) and specialising in science and technology, develops solutions in three main areas: Healthcare, Life Science, and Electronics, to which the division dedicated to manufacturing effect pigments and additives for industrial production also of paint products belongs.
Every year, its Italian branch organises a conference to take stock of the current situation and stimulate new ideas as the foundations for future trends. With an eye always turned to the centrality of people in the industrial and social context, this year’s conference organisers have chosen as their motto one of the favourite aphorisms of Enzo Ferrari, the man who built the myth of the “red car”:
“If you can dream it, you can do it”.
The selected location is also one of the most iconic Italian places dedicated to the Italian entrepreneur, the Enzo Ferrari Museum in Modena. Passion and respect for work have always characterised Ferrari, who passed away at the age of 90 in August 1988, and those words chosen as the common thread of the Merck Italy Effect Day symbolise his creative spirit more than anything else – he used to be defined as a “concrete dreamer”.
Imagination and concreteness: when put together, they create an oxymoron. However, if adequately pursued, they can form the basis for significant developments, especially in a field such as industry, which evolves precisely thanks to innovative ideas turned into actual, functional products. “Enzo Ferrari’s favourite motto is also the slogan of the day we organised in the name of innovation and creative inspiration,” confirms Fabio Carati, Senior Regional Marketing Manager EMEA. “In one of the most iconic locations devoted to style and passion, we presented the most innovative products, the latest colour trends, and ideas for new materials and special finishes, ranging from packaging to automotive and cosmetics, with a continuous reference to current events and human history to launch new product solutions and, at the same time, inspire future ones.”
During the meeting, which was attended by over 80 professionals including clients, designers, and Brand Industries, numerous presentations focused on the new digital tools made available by the German company.
Fabio Carati introduced the latest version of MBOX: with M-box 2.0, Merck continues its analysis of current trends through three stories that create the framework for future aesthetic research.
Based on the importance of the concept of CMF (Colour, Materials, Finish) in different sectors, such as automotive, product design, and packaging, Merck’s experts presented the new pigments and functional solutions through a journey made of 65 samples showing how to materialise the future and balance the physical and digital worlds.
Another confirmation of the company’s focus on digital is the launch of a new portal presented by Laia Serra Hernandez, from the Customer Excellence Team. Users can be inspired by the formulations and styling tips collected here, find the right product for each specific application, request samples and test them in their own laboratories, and easily access technical documentation on products.
In a presentation entitled “Rise Up for the Better”, Stefano Corrado, Account Manager Coatings, and Laura Zanini, Account Manager Decoratives&Functionals, presented an innovative demo tool with 20 new colour proposals, developed in the laboratories of the German multinational company and inspired by six historical and cultural events that demonstrated that by working side by side, things become possible that a single person cannot achieve. Six special effects were created by drawing inspiration from some of the most important events in recent history, each in two variants: the Carnation Revolution of April 1974 in Portugal and the fall of the Berlin Wall inspired Carnation Revolution and 1989, respectively. Orange Revolution was based on the colour chosen to identify the Buddhist religion, whereas Messel Pit was inspired by the battle of a group of citizens of the German town of Messel who defended its ancient oil shale quarry from being turned into a landfill site and had it declared a UNESCO World Heritage Site in 1995. As for Citizen Forests e Rave the Planet, the former drew inspiration from the initiatives around the planet that bring together unused plots of land, willing volunteers, and donors of plants to grow small Miyawaki forests, and the latter was based on techno music, which in the 1990s began to bring together people who were very different from each other but united by the quest for ecstasy.
The Merck team’s latest research studies involved the relaunch of two
mica-based pigments: Iriodin®, produced for more than forty years and applicable in all industrial sectors (coating, plastics, and inks – from mass colouring, cosmetic packaging, textiles, paper, and paints to the automotive industry), and Pyrisma®, supplied for around twenty years and whose chromaticity has now been enhanced, by optimising colour and saturation and eliminating the milky effect related to pure colours, as were performance and the colour space concept, which until now had not been fully exploited.
Functional solutions: polysilazanes & laser marking
Functionals superpowers
Laura Zanini’s presentation entitled “Surfaces with Superpowers” introducing Durazane® polysilazanes, special polymers available in both organic and inorganic versions.
These are exclusive products of the German company used as binders for coatings that react with the treated surface to become an integral part of the material and provide scratch resistance and protection even under extreme conditions. Durazane® polysilazanes are applicable in various sectors, including automotive, public transport, industry, and architecture, and can protect multiple materials such as aluminium, glass, wood, and ceramics while also offering anti-graffiti, hydrophobic, and anti-fingerprint solutions. These coatings also have high hardness, durability, and UV resistance properties, positioning themselves as an innovative and versatile solution for surface protection.
The sustainability of laser marking
Cristiano Casiraghi, Account Manager Plastics, then introduced the Iriotec® series by demonstrating the advantages of laser marking and emphasising its sustainability, reliability, durability, and costeffectiveness in identifying plastic products with an individual mark. It can be used for plastic packaging, automotive components, cables, and electronic devices, providing an alternative to ink or labels and improving end-of-life product recyclability.
Merck’s solutions for the food & beverage industry
Another presentation highlighted Merck’s innovative solutions in the field of food and beverage packaging, with a focus on the sustainability and safety of food contact materials (FCM). The F&B packaging market is expanding, driven by growing demand for sustainable solutions and strict regulations limiting the use of harmful substances such as PFAS, BPA, and phthalates. Merck has obtained a Food Contact Notification (FCN) from the US Food and Drug Administration (FDA) for several pigments, including Syn Mica, Miraval®, Rutile, Al2O3, and Cassiterite, certifying their safety for food use.
What sustainability means to Merck
Fabio Carati explained that the Surface Solutions division has set itself several goals to meet the multinational company’s sustainability objectives, including as follows:
using 80% renewable electricity from third parties by 2030 and expanding solar capacity at its production sites to obtain more green/renewable energy;
reducing greenhouse gas emissions (scopes 1 and 2) by 50% by 2030, achieving climate neutrality by 2040, and being transparent on the carbon footprint of key products (“honest and open”);
reducing water use intensity by 10% by 2025.
Merck is a collaborative member of the TfS (Together for Sustainability) initiative for the chemicals sector, which aims at standardising supplier assessments and audits worldwide and promoting responsible sourcing of goods and services. By joining TfS, Merck emphasised the importance of supplier management as part of its corporate responsibility policy.
This event, therefore, presented a complete overview of the company’s latest innovations, allowing participants to leave the Enzo Ferrari Museum’s evocative conference room with a wealth of ideas to use as a basis for further developments without setting any limits in their realisation – because “if you can dream it, you can do it”.
with a complete service that includes system design manufacturing, installation, technical support and chemicals
SPRAY BOOTHS WATER SLUDGE REMOVAL
RESIN DEMINERALIZATION SYSTEMS
REMEDIATION OF CONTAMINATED SITES
BIOLOGICAL SYSTEMS
BATCH TREATMENTS
PHYSICAL-CHEMICAL SYSTEMS
ADSORPTION FILTRATION
REVERSE OSMOSIS
MEMBRANE SYSTEMS
EVAPORATORS
BIOGAS BIOMASS SYSTEMS
OIL SEPARATORS
DESANDERS
DESALINATION SYSTEMS
PYROCHAR
OTHER SYSTEMS
CHEMICALS
Alessandro Soba
Verind S.p.A. – Milan
Consolidating the relationship between industry and university is an important objective to help lay the foundations for a more modern and sustainable future in manufacturing. This was also the goal of the seminar held at the Politecnico di Milano for students in Advanced Organic Coatings with the engineering-focused contribution of Verind Spa, PPG Spa, and EssilorLuxottica Spa.
May 2024 saw the end of the second semester of classes at the Politecnico di Milano, Italy’s leading university for technical and scientific education and among the top twenty universities in the QS World University Rankings in the Engineering & Technology category1
1 https://www.topuniversities.com/university-subject-rankings/engineering-technology/2023?page=0
Students of the Master’s Degree Course in Materials Engineering and Nanotechnology, which aims to train new technicians with broad-ranging knowledge in the areas of production, processing, and application of materials and the more innovative field of nanotechnology, recently had the opportunity to meet some companies from the surface finishing sector. These presented them with manufacturing-related concepts for the automotive and industrial sectors concerning as follows:
creation of paint products and assessment of the quality of the applied film – PPG
paint application technologies and equipment – Verind
high-productivity plastic eyewear coating lines from a customer’s point of view –EssilorLuxottica.
Held in English by Alessandro Soba from Verind (Dürr Group), Davide Bariona and Mattia Gambarin from PPG (Quattordio), and Alessandro Giacetti from EssilorLuxottica, the seminar organised for the Advanced Organic Coatings class was a concrete example of possible interaction between students and companies. The students, supported by Raffaella Suriano, lecturer at the Department of Chemistry, Materials, and Chemical Engineering “Giulio Natta” of the Politecnico di Milano, were particularly interested and asked several questions during and at the end of the lecture.
“In our speech,” says Davide Bariona from PPG, “we first presented PPG as a global company and described its presence in Italy. We then went into colour theory from a physical and chemical point of view, focusing on the development and production aspects of colour. We devoted much space to colour control, its subjective aspects, and the methods developed over the years for objective measurements. Finally, the PPG team illustrated the application systems we use at our sites and devoted the final part of the presentation to the analysis of some test panels and examples of coating defects.”
Alessandro Soba from Verind illustrated Dürr’s latest application technologies, such as the EcoBell electrostatic device, the EcoDose 2k electronic dosing tool using Coriolis mass flowmeters for 2K and 3K coatings, PIG systems, and Process Robot Arms. “All these solutions generate savings and efficiency in the coating process,” explains Soba. “Through videos showing painting and coating lines and plants in the automotive and general industry sectors and the classroom presentation of specific equipment for automatic and
manual coating, we addressed several topical themes related to application technologies for improved process sustainability, efficiency, and digitalisation.”
Finally, the students listened to the technical report of EssilorLuxottica, the French-Italian world leader in the eyewear industry, as an example of a company operating in the general industry that is a user of numerous coating processes. “After illustrating the various surface treatment technologies implemented in the eyewear supply chain,” explains Alessandro Giacetti, “we focused on our automatic 2K coating line for glasses and plastic components. We examined in detail all process stages, from surface preparation to paint application and curing, highlighting the key peculiarity of 2K processes, namely the need for continuous-flow formulation due to the short pot life of two-component coatings. In the final part of the presentation, we placed emphasis on solutions and tools for process control, which is essential to ensure the high level of productivity and quality required of a manufacturing department. Finally, we discussed the role and activity of engineers in today’s industrial environment, projecting the students towards the imminent start of their careers.”
“This collaboration between academia and industry,” concludes Raffaella Suriano from the Politecnico di Milano, “was made possible by PoliEfun, an association of this university that promotes business culture in the surface treatment sector2. PoliEfun encourages the involvement of professionals from this industry in the academic world through inpresence and online masters courses such as ISM11 (Industrial Short Master, now in its eleventh edition). Thanks also to the support of the School of Industrial and Information Engineering and the Master’s Degree Course in Materials Engineering and Nanotechnology, the Advanced Organic Coatings class could once again devote 40% of lecture hours to laboratory teaching during the 2023-24 academic year, thus further strengthening the skills and technical-scientific know-how of our future engineers through practical experience and experimental tests.”
2 www.poliefun.com
Monica Fumagalli ipcm®
An ambiguous colour for a long time, both linguistically and chromatically, orange has a complex history. It was little appreciated, until its use was sanctioned first by Newton and then by Impressionist painters. Today, its best-known applications are related to its visibility characteristics – but, as always in the study of colours, it also has some surprising facets.
“Orange is red brought nearer to humanity by yellow” - Wassily Kandinsky
The result of the combination of red and yellow, orange is a captivating colour, capable of polarising attention and ever-present in many moments of our daily lives, also considering it is the only colour whose name derives from a fruit we have before our eyes every day: the orange, of course. In the many languages spoken in Europe, before the introduction of this fruit in the 15th century by Portuguese sailors who imported it from Asia, there was no precise term or definition for this colour. According to some sources, that is why we usually use phrases such as “red fish” and “red hair” to indicate things that are actually not red. It thus remained undefined not only linguistically but also chromatically, since the mixture of red and yellow is technically difficult to reproduce in dyeing and painting. For a long time, it was also associated with the negative aspects of the two colours that make it up, only regaining appreciation when it began to be linked to gold. In nature, orange is the colour of autumn, of bright sunsets, of fire,
of fruits such as oranges, apricots, and persimmons, and of flowers such as lilies and tulips. It evokes freshness, cheerfulness, excitement, strength, cooperation, honour, generosity, adventure, warmth, good health, joy, spontaneity, positivity, energy, and vitality. It is thought to be one of the colours that children most love. However, it also has some negative associations with superficiality, arrogance, cockiness, pride, and impatience. Because of its high visibility, finally, it is the colour of traffic cones, work bibs, American prison uniforms, and life rafts, but also of Halloween with its pumpkins, of some iconic architecture of our time, and of rust.
As mentioned, the term “orange” (in Italian arancione, in French and German orange, in Spanish and Portuguese naranja) has been in use since the 1500s to refer to the colour of the orange fruit, the name of which has, however, a much more complex etymological origin. The first documented use of the word dates back to 1502, when it was chosen to describe some of the fabrics kept aside for the wedding of Princess
Margaret Tudor to King James IV of Scotland. It derives from the Sanskrit word naranga, which was used to refer to the orange tree and which, in turn, was possibly related to the saffron-yellow hue of the pistils of a plant called nāgakesara (its current scientific name is mesua ferrea). This was later used in the Persian language as narang and in the Arabic language as naranj (from which the Venetian dialect term naranza or narancia is also derived). In Low Latin (arangia or aurantia) and later in several European languages, the loss of the initial “n” was perhaps due to the influence of the Latin word aurum, i.e. “gold”, with which orange began to be associated from the 16th century onwards.
Orange in ancient history
Despite not having a name, orange was present in ancient history since prehistoric times. The oldest cave painting ever found in the world is that of a banteng bull dating back 40,000 years in the cave of Lubang Jeriji Saléh, on the island of Borneo (Indonesia), where red-orange ochre pigments or iron oxide were used to paint the walls and ceiling with hundreds of handprints (probably dating back 52,000 years), animal depictions, and anthropomorphic figures. In early civilisations, such as in Ancient Egypt, orange was obtained from a mineral called realgar, considered by many to be the only pure orange pigment in existence until the 19th century. In Ancient Rome, it was joined by another mineral, orpiment, which was at least as dangerous and toxic as the former. Both were widely used until the Middle Ages for miniated manuscripts – in particular, Christians used orange as a symbol for sins of gluttony. Its natural golden yellow hue made orpiment of great interest to alchemists, too, who speculated that it contained the secret to creating gold. In Ancient India and China, where orpiment was employed as a medicine despite its high arsenic content, a semi-precious stone called carnelian, which was undoubtedly safer and less toxic, was used instead to obtain orange tints.
The fortune and misfortune of orange between the Middle Ages and the Renaissance
In the Middle Ages, orange remained a difficult mixture to obtain and a tint that did not meet the criteria for quality colours at the time, namely saturation and stability. That changed when it began to be obtained from saffron, a rare, expensive, and delicate product reserved for precious fabrics such as silk. Above all, it was the increased knowledge of the properties of the fruit of the same name that redeemed it and led it to be increasingly associated with golden yellow, exoticism, and later with power and wealth in both Eastern and Western societies. During the Renaissance, however, it underwent another decline: orange lost importance – there are few paintings of the time in which it is present –and ended up being used in fabrics intended for the clothes of peasants or the middle class who wanted to imitate the red-embellished clothes of the nobility.
redemption of orange
Finally, in 1670, Isaac Newton officially codified orange in the spectrum. In 1765, a rare, bright orange-red crystalline mineral called crocoite was discovered in the Beresof mine near Yekaterinburg in the Siberian Urals (Russia): that led to the creation of the synthetic orange chromium pigment in 1809, soon to be followed by other synthetic pigments, such as cobalt orange. Between the 17th and 18th centuries, paintings began to become more widespread that used this colour in association with positive concepts. For instance, Pomona, the fertile goddess of abundance whose name derived from the Latin word pomon, meaning “fruit”, was often depicted wearing an orange dress or cloak. In England, it became very popular among the Pre-Raphaelites: the flowing orangered hair of Elizabeth Siddal, the wife of the painter Dante Gabriel Rossetti, became a symbol of this movement. Albert Joseph Moore, active in the second half of the 19th century, also painted festive scenes
of Romans wearing bright orange cloaks – brighter than any Roman would ever actually wear.
Orange in contemporary art
Starting in the 19th century, the new synthetic pigments mentioned and the invention of the metal paint tube in 1841 enabled artists to paint outdoors and capture the colours of natural light. The first painter to inaugurate the technique later known as en plein air was the Englishman William Turner, remembered today as ”the painter of light”, who was joined by the Italian Macchiaioli movement and the French Barbizon school – from which the Impressionist current took off, of which Pierre-Auguste Renoir and Claude Monet were exponents. The latter painted “Impression, Sunrise” in 1872 – hence the movement’s name, Impressionism – whose focal point is a tiny orange sun, with its reflection illuminating the water surface. Orange thus became a crucial colour for all Impressionist painters: they had studied colour theory and knew that orange placed next to blue made both colours appear much brighter. To cite just one example, Renoir painted boats with orange brushstrokes applied directly from the paint tube. The importance of this tint was also evident in the following period: to fill his works with light and exoticism, the Post-Impressionist artist Paul Gauguin made extensive use of it as a background colour and for the clothes and skin tones of the Tahitian women featured in his famous paintings.
Van Gogh’s orange
The painter we most associate with orange and yellow is undoubtedly Vincent Van Gogh. This artist depicted many touching and enthralling landscapes with the skilful use of these colours, which recall the pure sunlight of Provence or, by contrast, the moon and stars in a cobaltblue sky. It was probably this that later inspired the use of orange in
more introspective paintings, where it was applied to achieve a positive contrast to dramatic subjects: just think of Edvard Munch’s “The Scream” (1893-1910), Egon Schiele’s “Self-Portrait in Orange Jacket” (1913), and Francis Bacon’s “Three Studies for Figures at the Base of a Crucifixion” (1944). At the same time, orange was also the protagonist of more light-hearted works such as Paul Klee’s “Senecio” (1922), in which a face composed of a series of overlapping circles and squares is depicted using the typical cubist technique and whose predominant colours are orange, yellow, and blue. A fun fact to close this artistic roundup: one of the most expensive works of contemporary art in the world is the painting “Orange, Red, Yellow”, created by the American artist Mark Rothko in 1961 and sold at the Christie’s auction house in New York for USD 86.9 million in 2012 – it is an actual dive into a canvas densely coloured with the three tints mentioned in its title.
Some cultures consider orange sacred because it represents a link between red’s strength and yellow’s perfection. In Hinduism, orange is worn by the god Krishna. The typical orange robe of Buddhists, the kesa, represents enlightenment and the renunciation of earthly pleasures, an opposite meaning to that attributed to this colour by early Christians, as mentioned before. As the official colour of the Netherlands, worn by its representatives at various sporting events and their fans, orange recalls the origins of the royal family from the principality of Orange-Nassau; it was also present in the country’s national flag until 1937, when a royal decree established that red would replace orange near white and blue. In the Western world, it has been used on several occasions to support specific political factions: it became the symbol of Viktor Yushchenko’s nonviolent revolution in Ukraine in the aftermath of the presidential elections on 21 November 2004 and of the Protestant party in Northern
Hippopotamus “sweat” consists of red and orange pigments.
When it came to choosing the colour of the Golden Gate Bridge, the architect in charge of the work, Irving Morrow, chose international orange to make the bridge visible to incoming ships even when Karl The Fog – that is what residents call the mist that characterises this stretch of coastline – makes it impossible to distinguish anything in the bay.
Ireland, recalling the Protestant group that supported William of Orange in the War of the Two Kings, which culminated in the defeat of the Catholic monarch James II; it was included in the official flag of the Irish Free State alongside green, which represents the Catholic community, at least according to some sources, and white, which represents the element of reconciliation between the two factions.
Orange in nature: from hippo sweat to Alaskan river rust
This colour is also much present in the animal world, perhaps more than we might believe. It is the chromatic characteristic of some birds’ beaks (toucan, cardinal, and oystercatcher) and plumage (Guianan cock-of-the-rock), but did you know that it is also found in the sweat of hippos? Yes, because their “sweat” – technically not sweat at all – is composed of red and orange pigments, with the former containing an antibiotic and the latter absorbing UV rays: together, they protect these mammals’ epidermis against bacterial infections and sun damage, creating a natural sunscreen. Also, did you know that dogs, cats, but also deer cannot distinguish the colour orange? Some researchers at
the University of Georgia have carried out in-depth studies to reach this conclusion, which is helpful for both scientists and anyone wishing to approach a deer (with good or bad intentions) without being noted. In natural elements, this colour is more challenging to identify. However, a few months ago, news reported by CNN revealed a surprising phenomenon by which some Alaskan rivers are turning from clear blue to orange. According to scholars, this colour change, which is actually common in some geographical areas such as the Appalachians due to the presence of mining settlements but exceptional in wild, uncontaminated areas far from mines, could be due to the toxic metals released by thawing permafrost. We in the surface treatment sector could argue that, for once, the harmful phenomenon of rust is not due to the lack of prevention and maintenance that typically causes corrosion of metal structures... although it is little consolation in this case.
This colour’s high visibility and contrast characteristics led it to be chosen for the uniforms of American prisoners and the suits of
astronauts during spacecraft take-off and re-entry. In the former case, this tint makes prisoners more identifiable in the event of an escape; in the latter case, it is useful in the event of accidents during take-off or re-entry, when astronauts may be forced to abandon their damaged vehicles, often ending up in the middle of the sea: thanks to their “international orange” suits, they would be more easily spotted for rescue. International orange is indeed a colour used all over the globe to mark obstacles, contrasting them with the surrounding landscape or structures and the background of the sky. It is also used in architecture with the same function.
For example, it was chosen for the Golden Gate Bridge in San Francisco (USA) so that the ships reaching the bay can distinguish it from its surroundings and amidst the typical coastal fog. The origin of the adjective “golden” attributed to this bridge is, in fact, linked to its location above the Golden Gate Strait, connecting the Pacific Ocean to the San Francisco Bay. Did you know that the Eiffel Tower was also painted yellow-orange in 1899? Before the “brun Tour Eiffel” was definitely
chosen in 1968, the Parisian tower wore several “dresses” in different colours, changing hues from yellow to ochre to orange. In fashion, someone who liked to wear orange – quite unexpectedly, considering her role – was the late Queen Elizabeth II: she probably chose it to stand out better and make it easier for security personnel to monitor her movements. Finally, in marketing, many famous companies have selected this tint for their logos. To name a few: Amazon for its “smile”, Italy’s Wind, the Netherlands’ TNT (perhaps for patriotic reasons), Denmark’s Just Eat (associated with reassurance and friendliness), and USA’s Harley Davidson and Nickelodeon (to express an idea of adventure and fun).
At the end of this lengthy excursus on the history of orange, we can conclude that Kandinsky undoubtedly nailed the essence of this colour, which remained ambiguous for such a long time: orange is how the joyful, lighter yellow makes the impetuousness and violence of red more acceptable to human eyes.
Sources
- https://getd.libs.uga.edu/pdfs/cohen_bradley_s_201105_ms.pdf
- www.linkedin.com/feed/update/urn:li:activity:7001092899694129152
- www.color-meanings.com/history-color-orange/ - www.artsandcollections.com/article/a-history-of-the-colour-orange/
- www.guichetdusavoir.org/question/voir/52532#:~:text=Ce%20terme%20est%20employ%C3%A9%20d%C3%A8s,de%20vue%20chromatique%20que%20terminologique
- https://berghconsulting.com/color-meaning-orange/ - www.colorcom.com
- https://edition.cnn.com/2024/05/29/climate/orange-rivers-permafrost-alaska/ - www.goldengate.org
REGISTRATI ORA
Esplora le più recenti tendenze e tecnologie nel mondo della pittura e dei rivestimenti, mentre stringi preziose connessioni con i leader del settore.
Paint & Coatings: il luogo dove l’ispirazione, l’apprendimento e le opportunità di networking si incontrano per trasformare il tuo business!
A new white paper from Henkel explains how to boost efficiency and sustainability with Bonderite M-NT 41044.
The Adhesive Technologies division of Henkel has recently published a new white paper illustrating the process-related and ecological advantages of its new cleaning and coating technology and the associated best practices employed by the household appliance manufacturer BSH Turkey.
The cleaning and coating steps provide metal surfaces with important properties, such as corrosion protection and paint adhesion. However, these processes – whether for household appliances, office furniture, heavy machinery or mechanical equipment – require a high water and energy consumption. The new solution is a cleaning and coating technology that offers a more efficient metal pre-treatment in just one step, allowing users to reduce the number of process steps by half while also saving energy and water.
The white paper from Henkel explains how the conventional eight to ten process steps (for example, in the case of conversion processes with zinc and iron phosphate), can be reduced to four thanks to Bonderite M-NT 41044, a product that cleans and coats metal parts in a single step. The product can be used together with other powder, liquid or cataphoresis applications.
“Our commitment to a sustainable metal industry is at the heart of the business of Henkel. Together with our customers, we are re-thinking the status quo and reinventing existing processes to deliver a positive impact. This optimisation process is focused on highperformance products with a responsible approach to natural resources,” has stated Volker Mansfeld, the vice-president Industry EIMEA at Henkel Adhesive Technologies.
For further information: www.henkel.com
The new Malaysian distribution hub will allow GMA to meet the increasing demand for industrial garnet abrasives in the region.
GMA Garnet Group has opened a new distribution hub in Port Klang (Malaysia) that will allow the company to strengthen its strategic expansion and meet the increasing demand for industrial garnet abrasives in the Asia-Pacific region by ensuring timely product delivery and providing local customer services.
“The new distribution hub in Malaysia represents a significant milestone for GMA: its location strengthens our supply chain capabilities, demonstrating our commitment to meeting the growing demands of the Asia-Pacific region and enhancing our ability to meet the needs of our customers, efficiently and reliably,” has stated Grant Cox, the CEO of GMA Garnet Group.
At the beginning of June, GMA delivered its first bulk shipment to the new facility directly from its mine in Port Gregory (Western Australia).
The Malaysian centre has met all quality assurance measures and will begin shipping products to customers by the end of the month.
“Our new, fully stocked facility will ensure excellent service and fast shipping for our clients in the Asia-Pacific region. It will reinforce the focus of GMA on customer satisfaction, superior garnet quality and industry-leading quality control processes,” has added Flynn Cowan, General Manager International Sales & Marketing at GMA. “This new distribution and packaging hub allows us to streamline our processes, maintaining the high standards of quality and reliability that GMA is known for globally.”
For further information: https://gmagarnet.com/
Manuela Casali
UCIF – Italian Surface Treatment Equipment Manufacturers’ Association, Milan, Italy info@ucif.net
Summer always brings a natural slowdown in activities due to the heat but also the traditional perception of June as a stocktaking month. For UCIF, the Italian Surface Treatment Equipment Manufacturers’ Association, this is also a time to reflect on the first six months of the year, which were characterised by fervent dynamism and passion.
2024 opened with UCIF Next, a crucial event for members hosted by our President’s company, Geico. During this meeting, we openly discussed how the Association should evolve in the coming years. The debate led to the creation of a Vademecum, presented at the June Ordinary Assembly, summarising all the activities and opportunities available to member companies to communicate their membership using both their own and UCIF’s channels. From February to May, the focus was on the third edition of the S.M.A.R.T. conference. The event was attended by over 140 people, 12 speakers, and 6 sponsors, confirming the growing interest and complexity of the project. New this year was the creation of a website dedicated to the event, which will soon become a web portal for the finishing and surface treatment industry, also with a view to the next edition of S.M.A.R.T.
The We Talks web conferences on various current issues, reserved for UCIF members, continued simultaneously. In early June, 40 participants logged in to discuss the theme “Industry 4.0 and Transition 5.0”, interacting directly with experts who answered their questions live. In mid-June, the Ordinary Assembly, christened Move On, marked a
further step along the path mapped out during UCIF Next. In addition to the usual institutional formalities, the Assembly saw the election of a new Board of Directors, expanded from 5 to 7 members to ensure a more complete representation of the different sectors of belonging of UCIF’s members. Daryush Arabnia from Geico was re-elected President, with Claudio Minelli from Verind (Dürr Group) re-elected Treasurer.
Sergio Castagna from Hubo Automation and Marina Scavini from Savim Europe were elected Vice Presidents.
UCIF also actively participated in PoliEfun, the Politecnico di Milano’s association that acts as a bridge between companies and students in the field of surface engineering.
What will our return from the summer break have in store for us?
Certainly, new events and meeting opportunities for both our members and those who, after reading this article, are curious to learn more about us.
For further information: www.smart-ucif.it, www.ucif.net, info@ucif.net
The second workshop devoted to the world of paint was held at the Department of Industrial Engineering of the University of Trento (Italy) on 18 June 2024. It was an opportunity for the main stakeholders, including university bodies, raw material and coating producers, applicators, manufacturers of measuring and control instruments, and colour designers, to come together to discuss the sector’s state of the art in a cross-disciplinary event.
After the success of the first edition held in June last year1, the Department of Industrial Engineering of the University of Trento organised a new workshop devoted to coating systems on 18 June, intended to start with the analysis of raw materials and move on to the different types of paint products and their application processes. The meeting aimed at illustrating technological developments, issues, trends, green solutions, and design aspects to inform the sector’s players and stimulate curiosity and debate.
Moderated by Stefano Rossi, the Head of the Coatings & Industrial Corrosion Control laboratory, and Michele Fedel, Associate Professor at the Department of Industrial Engineering, who formed the event’s Scientific Committee together with Maria Alba Fusco from Liberty Magona (Piombino, Italy), Stefano Corrado from Merck, and Tiziana Pintarelli from Pintarelli Verniciature, the conference was attended by around 80 professionals representing companies and institutes from a wide variety of sectors.
After the initial greetings of Flavio Deflorian, the Rector of the University of Trento, Alessandro Pegoretti, head of the Industrial Engineering Department, and Andrea Dorigato, Associate Professor at the Department and a Councillor of Trento’s Engineers Association, the first speech of the morning session focused on the theme of pre-painted coil’s flexibility and sustainability. Entitled “The versatility of pre-painted flat sheet metal”, it was delivered by Giovanni Depedro and Benedetto Callegari from Sandrini Metalli (Costa Volpino, Bergamo, Italy).
The floor was then passed to Tiziana Pintarelli from Pintarelli Verniciature, a leading powder coating applicator. After explaining what colour is and presenting some examples of optical illusions to emphasise how easy it is to believe that two shades are identical when they are not, she illustrated one of the most topical issues that painters face when applying special powders with tactile or 3D effects, which are increasingly in demand in the architectural sector: not only among different batches but also within the same batch, it can happen that, once applied, these paint products create different colour effects that are not immediately noticeable at the end of the coating cycle
1 https://www.ipcm.it/en/open/ipcm/2023/82/148.aspx
(because there are no control instruments to do so) but only once the components have been placed side by side or even already mounted. A possible solution, as Pintarelli emphasised, could be found in closer cooperation between powder producers and coating equipment manufacturers.
Lorenzo Soldavini from PPG described the low-temperature thermosetting powder solutions for outdoors that the company is developing to speed up production flows for applicators without affecting coating quality. He also announced that PPG is developing software to quantify the benefits these coatings can bring to each user.
Andrea Carosso from Cofomegra concluded the first part of the morning session by focusing on measurement and control instruments in his talk entitled “Powder thickness control before curing”, in which he also illustrated the advantages of the CoatMaster Flex portable digital thickness gauge, capable of checking coating thicknesses in 5 seconds before the parts enter the curing oven thus avoiding delays and material waste, and the 3D thermographic surface analysis instrument developed for more complex coatings, such as the insulating products applied to car battery packs.
After the coffee break, the second part of the morning session started with a presentation by Stefano Corrado from Merck of the 20 new
colours developed by this German multinational manufacturer of pigments for paint products, inspired by six historical and cultural events from the Carnation Revolution in Portugal to the fall of the Berlin Wall.
“From thought to matter to meet light and take shape: stories of colour” was the title of the speech delivered by Vicky Syriopoulou, colour designer at OIKOS (Gatteo Mare, Forlì-Cesena, Italy), a manufacturer of decorative paints and coatings for interiors and exteriors, who illustrated some case studies on the search for special colours and effects in the fields of exhibition stands and spas, two of the most challenging sectors.
The morning session ended with a talk by Alessio Carlotto from ST Powder Coatings entitled “GREEN OASIS, the sustainable oasis of powder coatings”, which presented the new range of powders produced by this company based in Montecchio Maggiore (Vicenza, Italy) and divided into three lines: R series, P series, and Plus series.
During the break with a buffet lunch offered by sponsors Cofomegra, Estalia, Nikon, Pintarelli, and ST Powder Coatings, each with its own stand at the event, the attendees could visit the university laboratories specialising in tests on industrial coatings in general and protective coatings in particular.
The afternoon started with the speech of Paolo Artoni from The Sherwin Williams Group (Minerbio, Bologna, Italy), who explained how his division is working to anticipate regulatory restrictions on the use of certain products by seeking solutions to replace them before the ban of the European Chemicals Agency (ECHA) comes into force, also considering the future demand for a “passport” for each paint product.
Stefano Tonini and Piergiorgio Savoldi from Estalia (Castenedolo, Brescia, Italy) introduced the topic “Progress in the formulation of water-based coatings: towards sustainable, high-performance products”, emphasising that close cooperation between regulatory bodies and R&D laboratories is needed to achieve a circular approach. Alisea (Vicenza), represented here by its owner Susanna Martucci, has
based its whole business on the circular economy concept, producing design objects from recovered production waste since 1994. As part of this activity, it has discovered the chromatic characteristics of graphite, which is now used in the formulation of wood coatings such as those produced by Icro Coatings (Chignolo d’Isola, Bergamo), represented at the event by Luca Broggi. The report presented by Martucci and Broggi, “The virtuous symbiosis between companies for design and sustainability”, touched on aspects such as the reduction of environmental impact (for which Icro Coatings has developed a software programme to calculate the carbon footprint of paints) and the importance of cross-sectoral influences among different industries (which is an added value to R&D activities and from which the collaboration between Alisea and Icro Coatings was born).
The conference ended with a talk by Alberto Coffre from Nikon Europe B.V., who described the equipment the multinational company has developed for surface characterisation.
Sponsored by Assovernici and organised on the back of requests from many participants given the success of the first edition, this workshop also offered numerous insights to an industry that is looking for answers in multiple areas, from new powders with special effects to environmental impact reduction, from the circular economy to new regulations, and many more. “The presence of numerous industry representatives with different skill sets,” said Stefano Rossi, “made it possible to build a complete picture through the participants’ interaction, useful for both users of organic systems and product designers. We sincerely hope to be able to organise another edition of this important meeting opportunity in future.”
For further information: www.dii.unitn.it
S.M.A.R.T. (Surface. Manufacturing. Advanced. Research. Technology.) is the acronym used to identify the conference that UCIF, the Italian Surface Treatment Equipment Manufacturers’ Association, representing the finishing sector within ANIMA Confindustria, organises every two years to talk about innovation and progress in the industry.
Events like this provide an important platform for companies from the surface treatment and finishing sector to share their experiences, present their newest technologies, and discuss challenges and opportunities. They not only foster the exchange of knowledge and best practices but also help promote a culture of sustainability and innovation within the industry.
On 22 May, the third edition of S.M.A.R.T. took place at the Fondazione Cariplo in Milan, titled “The Finishing of the Future between Innovation and Sustainability” to emphasise that surface treatment and finishing technologies have been engaged in a complex balance between technological development and sustainability for several years now. The ten reports presented by leading players in the world of surface treatments covered three main themes:
Responsible innovation
The mechanical engineering industry is called upon to develop design and technological solutions that aim not only to improve the performance and efficiency of products and processes but also to minimise the use of non-renewable natural resources, reduce polluting emissions, and promote safe and ethical working conditions throughout the production chain.
Sustainability and the circular economy
In the current era, sustainability has become a key pillar for companies in all sectors, including the mechanical engineering industry. Traditionally associated with high consumption of natural resources, greenhouse gas emissions, and significant environmental impact, this is now called upon to take a central role in promoting sustainability and building a responsible future.
Optimised use of resources
Optimising resources is crucial in promoting sustainability in the mechanical engineering industry. Reducing waste and encouraging the recycling and reuse of materials can significantly limit its overall environmental impact.
The ten speeches presented several success cases revolving around dedusting, waste water recirculation and treatment, cleaning for absolute cleanliness, chemical paint stripping, sustainable and circular coating application, and PVD coating. The conference also included
several networking moments where participants could introduce themselves and get to know each other.
The event received the patronage of Poliefun (an association operating within the Politecnico di Milano), MADE (Competence Centre for Industry 4.0), and the Municipality of Milan. Supporting S.M.A.R.T. 3 as sponsors were KPMG, WIDE Group, and Imagine.
At the end of the conference, UCIF organised a social programme that included a tour to discover the traditions of Milanese artisans and their historical workshops in the heart of the city, with professional guides telling several stories and anecdotes, and a happy hour in the Foyer of the Teatro alla Scala.
A significant innovation brought by the S.M.A.R.T. 3 conference is the SMART portal. The platform currently hosts news related to the various editions of the S.M.A.R.T. biennial conference, but it also aims to be and become a vital point of reference for information related to all things surface treatments.
For further information: www.smart-ucif.it
The most important industry events at your fingertips
myFAIR is a free web app that can be accessed from both desktop and mobile devices, which allows you to stay up-to-date with the leading events of the surface treatment sector.
Held on Wednesday, 10 July, the event “Color Design at Lechler Village” was an opportunity for the company to present its customers and partners with its new thematic village devoted to the culture of colour and its project “The Way of Ethic Colors”, which includes four collections exploring the ethical dimension of colour and creating new chromatic and material landscapes for home interiors.
Colour is not just an aesthetic element but also a force capable of influencing emotions, behaviours, and values. It was with this in mind that Lechler, the paint manufacturer based in Como, Italy, opened the doors of its new “Lechler Village” on Wednesday, 10 July. Conceived as a “factory of ideas”, this innovative place welcomed customers and partners in a hearty environment designed with creativity and sharing as the focal points. During the event, Lechler also presented its new project, “The Way of Ethic Colors”, which includes four collections exploring the ethical dimension of colour.
The Way of Ethic Colors: the four themes of the new offer Lechler’s new collection, premiered at Fuorisalone 2024, is divided into four main themes: Involvement, Equilibrium, Awareness, and Change. Each of them reflects a different approach to colour design, always with sustainability as a key element.
Involvement: inspired by emotional intensity, this collection features tints ranging from blues to cool greys juxtaposed with deep, warm reds. These are ideal for crafting spaces with a temporary chromatic and emotional focus, capable of engaging and stimulating the emotions of those who live within them.
Equilibrium: it finds its essence in harmony with nature, offering a palette of complementary colours, such as tonal greens and pinks, with matte and pearl finishes. This combination is perfect for spaces in
dialogue with the outside environment, creating balance and serenity.
Awareness: it represents consciousness and durability, with neutral tones and iconic materials that blend into urban and historical contexts.
Change: it expresses transformability through bright, saturated colours designed to dynamise spaces and make it easier for them to adapt to new requirements or desires. This theme is ideal for those looking for versatile spaces ready to evolve with changing needs.
The new “Lechler Village” presents itself as a future-oriented place, an authentic “factory of ideas”. Conceived to create a welcoming, healthy, and comfortable environment, it is designed to offer shared working, thinking, and living spaces. The aim is to enhance the creativity that emerges from exchange and contamination inside and outside the company. Initially, construction has focused on the Village Gardens and the “Le Déjeuner sur l’herbe” Bistrot, surrounded by native vegetation. This union with nature represents a harmonious beginning, ideal for fostering relationships. After a walk through these spaces, where participants could directly explore the colour choices made and the products used for painting the various areas, the event ended with a happy hour at Lechler’s Bistrot, a moment of conviviality and an opportunity for dialogue among all participants.
For further information: www.lechler.eu
For the first time ever, FABTECH heads to the Orange County Convention Center in Orlando (FL, United States), from October 15-17, 2024.
“We’re excited to take FABTECH to one of the best convention centers in the U.S.,” notes CCAI Executive Director, Anne Goyer. “It’s amazing how much the Finishing Pavilion and Conference have grown since we became a part of FABTECH back in 2010. The growth has been phenomenal, and we feel very fortunate to be a FABTECH partner.” The FINISHING Pavilion is sold out and attendees will find the largest gathering of suppliers to the finishing industry under one roof this year.
CCAI is celebrating its 15th year as a FABTECH partner. The CCAI FINISHING Pavilion and Conference continue to thrive and offer great innovations and educational opportunities on all aspects of industrial surface finishing. Whether a company is just getting into finishing, looking for new solutions to challenges, or upgrading their finishing lines, FABTECH provides a wealth of products and services to help companies meet their finishing needs.
Continuous learning and education have consistently been the cornerstone of CCAI’s mission. The FABTECH conference program provides an ideal stage for CCAI to spotlight the expertise and knowledge of its members, offering valuable insights for both newcomers to the finishing industry and those seeking to enhance their skills and broaden their understanding. CCAI’s FINISHING Conference features 23 sessions, encompassing a broad spectrum of technical presentations, from basic to advanced, addressing topics of interest for everyone involved in finishing technologies. For complete descriptions of each session and registration information, visit www.fabtechexpo.com/ conference#track=event-track-finishing
Now in its seventh year as a FABTECH highlight, CCAI is once again sponsoring the FAB to FINISH Production Experience on the show floor. The program gives attendees a first-hand opportunity to walk a part from fabrication to finishing. Attendees will follow a production route to participating FINISHING exhibitors’ booths to experience the part being cleaned, powder coated, cured, and tested. Some routes will feature paint stripping. Each year the program grows in popularity as exhibitors and attendees alike want to participate.
To review the current FINISHING Conference Program and list of FINISHING Pavilion exhibitors, visit: www.fabtechexpo.com / To view the FINISHING conference sessions, visit www.fabtechexpo.com/conference, scroll down and click the FINISHING button on the right side of the page/
To view the current list of FINISHING exhibitors, visit www.fabtechexpo. com/exhibitor-directory, select the Exhibitor Directory button then use the advanced search tab and check the finishing category to view all finishing exhibitors and booth numbers. Note that the FINISHING Pavilion and Conference sessions are located in the West Building. FREE Exhibition Registration: Enter promo code FBCCAI for free admission to the Expo.
For further information: www.fabtechexpo.com
Viteria, bulloneria e fissaggi industriali
Fissaggi per costruzioni
Sistemi di assemblaggio e installazione
Tecnologia per la produzione di viteria e bulloneria
Stoccaggio, distribuzione e attrezzature di fabbrica
Informazione, comunicazione e servizi
SURFAIR is the International Event for key players in the Aeronautic Surface Finishing Industry. We recognize the critical importance of surface finishing in the aviation industry. This process goes beyond improving the appearance of aircraft; it is essential for ensuring their safety and efficiency. Our goal is to establish a platform where industry leaders can collaborate, share expertise, and discover the latest innovations in surface finishing technology.
24 - 26 SEPTEMBER 250+ 40+ 30+ 5
Biarritz, FRANCE
surfaircongress.com
High-level speakers
Industry-leading partners
Themes : regulation compliance, sustainability, automation, production performance, durability International attendees
Richard Geiss GmbH saves about 25 percent energy as a result of the complete conversion of its in-house rotary kiln and the “Waste to Energy” concept.
CO2-neutral solvents: the goal of Richard Geiss GmbH. The solvents specialist from Offingen (Bavaria) has moved a big step closer to this goal by converting its inhouse rotary kiln.
Distillation residues arising from the solvent treatment process are thermally recycled on site in the rotary kiln. Richard Geiss GmbH uses the resulting energy for solvent processing and is able to reduce its gas consumption by around a quarter with its “Waste to Energy” concept. This also reduces the CO2 footprint by 1,482 tons per year. The family-run company recently invested 2.1 million euros for the complete conversion of the rotary kiln.
“We have successfully completed our mammoth ‘oven modernisation’ project and
laid a milestone on our path to CO2-neutral solvents. This is because CO2-reduced production not only has a positive effect on the CO2 footprint of our company, but ultimately also on the CO2 balance of our products. This is of course also interesting for our customers and their environmental management,” explains Bastian Geiss, Managing Partner of Richard Geiss GmbH.
For decades, the solvent specialist from Offingen has been practicing recycling management and is one of Europe’s leading experts in solvent recycling. Some of the distillates save up to 90 percent CO2 compared to fresh goods.
25 percent less gas as a result of a modernized rotary kiln
Richard Geiss GmbH is able process up to 50,000 tons of used goods per year into high-purity distillates at its site in Offingen. “Thanks to the modernized rotary kiln, we now generate around a quarter of the energy for the distillation process ourselves at our site and therefore save gas, which reduces the CO2 footprint of our solvent recyclates enormously,” explains Bastian Geiss. The modernization of the rotary kiln has also significantly expanded the range of materials that can be recycled there. This has also doubled the incineration capacity: from 3,000 tons to 6,000 tons per year.
Another advantage: since the solvent specialist can independently thermally recycle the residues from distillation directly on site, it has not only further deepened the concept of the circular economy, but also saves on logistics and transportation routes. The family business estimates that thanks to the modernised rotary kiln, there will be a good 300 fewer truck loads per year that were previously sent for external disposal. This is also a plus for the environment and saves CO2
Not only does Richard Geiss GmbH produce its own heating energy, but also 65 percent of the electricity that it needs, in the form of hydropower and solar energy. The solvent specialist consumes around three million kilowatt hours of electricity a year, as much as almost 750 four-person households. Some two thirds of this comes from a hydroelectric power plant and a photovoltaic system at the Offingen site. “For years now, we have been pursuing a self-sufficient energy supply. For us, it is particularly important that the electricity
BETTINA NILIUS
Richard
Geiss GmbH – Offingen, Germany
bettina.nilius@geiss-gmbh.de
EFFICIENT CLEANING AND DEBURRING SYSTEMS FOR VARIOUS INDUSTRIAL PARTS AND COMPONENTS.
we produce ourselves comes from renewable energy sources,” emphasizes Bastian Geiss. Most of the electricity produced is supplied by a hydroelectric power plant at the site, one that the solvent specialist has been operating for decades. About two thirds of the electricity from this flows into the production of Richard Geiss GmbH every year. Since 2014, a solar system has been supplementing power generation at the site. More than 260,000 kWh per year come from the PV system, which also feeds 100 percent directly into the company.
Transport and mobility
When it comes to the transportation of solvents and the mobility of
Experience our Systems and Solutions: www.ecoclean-group.net
employees, the Richard Geiss GmbH also pursues an environmentally friendly approach. Solvents are increasingly being transported by rail for distribution. In 2023, 170 tons of CO2 were saved thanks to rail transport. With its own state-of-the-art fleet of vehicles, the recycling company not only offers a complete all-round service for customers, but also maximum safety when transporting the solvents.
There are also e-charging stations in the Offingen parking lot. They are available for employees to “refuel” their electric vehicles. The company has already converted 13 company cars to hybrid. Also cool and green: Richard Geiss GmbH offers its employees bike leasing for an environmentally friendly and healthy commute.
“Everybody wants a climate-neutral industry: the German government by 2045, the EU by 2050. Especially the chemical industry is facing major upheavals and has to make various adjustments in order to achieve this goal,” explains Bastian Geiss, Managing Partner of Richard Geiss GmbH. “That is why we continue to focus consistently on the circular economy and the reprocessing of solvents in order to conserve resources. We also produce most of the energy we need ourselves and want to expand this even further in the future,” says Bastian Geiss, giving an insight into the future.
A study conducted by the German Chemical Industry Association (VCI) in 2019 has shown that Greenhouse gas-neutral chemistry in Germany is technologically possible; the key to zero CO2 is primarily in the type of energy supply. At present, this still comes largely from fossil fuels. “We show how things can be done differently: with a circular economy and self-produced energy,” emphasizes Bastian Geiss.
Located in Offingen in the district of Günzburg, Richard Geiss GmbH is one of Europe’s leading specialists in the field of solvent recovery. The company produces high-purity distillates from solvent waste by distillative processing. Richard Geiss GmbH supplies solvents for use in industrial surface cleaning, textile cleaning and the chemical and pharmaceutical industries. Contract degreasing completes the range of services as the fourth business segment. Richard Geiss GmbH employs around 100 people in Offingen. The company has an approved processing capacity of 50,000 tons of solvents per year which are processed into high-purity distillates and it is certified according to ISO 9001, ISO 14001, ISO 45001, ISO 50001 and as a waste management company. Richard Geiss GmbH was founded in 1959 by Richard Geiss. Today, Bastian Geiss is the third generation to run the family business.
Cosmogas, an Italian manufacturer of heat pumps and condensing boilers, has recently installed a new cleaning system supplied by IFP Europe (Galliera Veneta, Padua, Italy) to enhance its production process, improve product quality, and optimise energy management.
In this era of rapid technological development, the industrial cleaning sector is seeing a significant acceleration, pushing companies to implement increasingly efficient strategies to meet growing demands for quality and environmental sustainability. Such transformation is taking place in the context of Industry 5.0, a paradigm that integrates advanced technological innovation with environmentally conscious practices to promote human-machine collaboration in creating customised and sustainable production environments. Cosmogas stands out as an emblematic example of this evolution. Positioning among the leading players in the field of heat pumps and condensing boilers, it has improved its production efficiency by adopting Industry 5.0 principles for responsible and environmentally friendly production with the installation of a new cleaning plant.
Alberto Alessandrini, Head of the Research & Development Center at Cosmogas Srl, emphasises the importance of its in-house development, production, and patenting capability to drive innovation in the industry – its Research & Development Center enables Cosmogas to remain
at the forefront of the condensing boilers and heat pumps market by anticipating market trends, developing innovative products that meet emerging needs, and constantly improving production processes: “Our Research & Development Center plays a crucial role in future-proofing our products. It improves Cosmogas’ competitiveness while contributing to developing more efficient and sustainable solutions, thus positioning us as an industry leader.”
“In particular, we have expanded our range by introducing state-of-theart, 4.0 heat pumps to meet growing market demand. This development, however, made implementing a dedicated cleaning system for tubes and gas circuits essential to meet the highest cleanliness and performance standards. For this critical project, we relied on IFP Europe, which designed and installed our new plant,” states Alessandrini.
Cosmogas is an Italian family business based in Meldola, Forlì Cesena, founded by Arturo Alessandrini in 1966. Originally specialising in the
production of kerosene boilers, it later expanded its product portfolio with methane gas boilers following the advent of methane in Italy. Today, Cosmogas designs, manufactures, and markets a wide range of technologies including hybrid systems using renewable energy and heat pumps, as well as condensing boilers and water heaters. “Condensing boilers are our flagship product, along with hybrid systems and heat pumps. Starting with raw materials, we can design, produce, and deliver finished products to installers and distributors,” Alessandrini explains. “Cosmogas has a strong global presence, with significant market shares in Europe (especially England, France, Austria, Greece, and Spain), America (Canada, USA, and Mexico), and Asia (China and South Korea).
We serve both the residential and the commercial and industrial sectors, offering advanced solutions that meet the growing need for energy efficiency and environmental sustainability,” adds Alessandrini. “We have a special focus on quality for both domestic and high-power systems, including schools, hotels, restaurants, and universities. In addition, we have established ourselves in the swimming pool market with condensing pool heaters built with pure titanium tubes, a popular solution in the US.”
Cosmogas’ manufacturing cycle is characterised by an organised process aimed at ensuring the highest quality and efficiency of products. “Our workflow starts with the procurement of the essential materials for heat pumps and boilers production, such as sheet metal and tubes as well as other components. The former are sent to the sheet metal and tube working departments, whereas the latter are stored in a dedicated warehouse. Once prepared, the materials are processed to build the heat exchanger, the heart of our boilers, for which we hold several patents,” illustrates Alessandrini. “The process continues with the assembly of the kits with all the required components and the transfer of the resulting materials to our production lines. These steps occur in a tense flow environment, meaning they take place continuously without interruption, minimising waiting times between operations and ensuring optimal production synchronisation. This approach reduces waste and costs but also improves our end products’ quality by ensuring they are assembled and manufactured efficiently and smoothly.”
Within this manufacturing cycle, the cleaning phase is vital to guarantee the excellent quality and functionality of products. Their components are often contaminated with oils and emulsions left by machining or moulding operations, and they must be perfectly cleaned before laser cutting, as even a simple fingerprint could compromise the entire process. “The gas circuits of heat pumps must be completely free of impurities. Previously, we had some external contractors clean our workpieces, but this posed several problems related to quality and cleanliness. For example, residual dirt could cause defects during welding, especially with our new-generation heat pumps. That is why we installed a cleaning machine capable of guaranteeing a high level of cleanliness, also suitable for sheet metal mouldings. It is a closedloop modified alcohol machine, and it has been operational for about two months now. Since we use photovoltaic energy, we have also implemented software to schedule distillation and stripping cycles, each lasting six hours, during weekends: this prepares the machine for the Monday cleaning operations, thus ensuring an uninterrupted start to the week. In parallel, we installed a double filter to guarantee the machine’s operational continuity, even during automatic draining and drying of the clogged filter, a measure taken in anticipation of the growing demand for our products,” says Alessandrini.
“The complete cleaning process, performed under vacuum, comprises several essential steps. The first is the preliminary vacuum phase, during
which air is removed from the chamber to ensure that the cleaning fluid can reach every surface of the part to be treated without encountering resistance from air bubbles. This is followed by the cleaning phase, which includes a spray cleaning stage with a fluid from a tank at a temperature of around 40 °C and an immersion cleaning stage with a fluid taken from a second tank at around 70 °C. The chamber is then saturated with solvent vapours generated by an integrated boiler, which condense on the part’s surfaces to perform the final rinsing and heating phase. For the drying phase, vapours are evaporated and diffused in a cold trap fed by an internal chiller, with the gas expanding at around -30 °C. Finally, during the door pre-opening phase, outside air is fed into the chamber to pressurise it, allowing the door to open safely,” explains IFP Europe’s CEO Giacomo Sabbadin.
The cleaning system installed by IFP Europe is a KP 600 MAX plant designed to carry out a full vacuum treatment cycle down to 1 millibar, providing excellent results for the most demanding applications. “The system has a nominal load capacity of 600 x 1200 x 600 mm and can handle parts up to 600 kg. Its productivity rate is 4 cycles/hour, adaptable to the type of workpieces and their contamination level. It uses modified alcohols as solvents,” Sabbadin explains.
“The cleaning cycle takes place entirely under vacuum and can include up to two consecutive cleaning phases with different types
of mechanical activation, using inverter-controlled basket movement for thorough and deep cleaning. The rinsing phase uses vapours with precise electronic control of the chamber’s saturation degree. During the drying phase, the plant operates under vacuum down to 1 millibar, thanks to two high vacuum pumps and stainless steel heat exchangers fed by a direct refrigeration system that reaches -30 °C. Solvent distillation is carried out with a continuous flow and completely under vacuum, with a capacity of up to 300 litres/hour of distilled alcohol and the complete separation of oil and alcohol, and it is followed by the continuous-flow automatic discharge of residues. Solvent filtration also occurs under vacuum and with a continuous flow, with automatic filter drainage and automatic chip drying steps before opening,” indicates Sabbadin.
“The machine is equipped with control systems to constantly monitor all functional parameters, such as the vacuum, temperature, and pressure values in the cleaning chamber, software redundancy detection, and hardware safety control, with network connection capability for monitoring and troubleshooting. In addition, the fact that the treatment cycle, including cleaning, drying, deodorising, and distillation, occurs fully under vacuum has positive consequences on the type of solvent used and its management, the quality of the cleaning results, and the operation’s environmental impact. This treatment makes it possible to safely use class AIII non-chlorinated hydrocarbon solvents and modified alcohols, achieving quality results comparable to those obtainable with more toxic and dangerous solvents but without the associated risks.”
“Vacuum cleaning provides excellent results and is particularly effective with complex-shaped surfaces and narrow cavities, penetrating down to the microstructure of sintered materials. The absence of air bubbles in the cleaning liquid ensures homogenous and optimal treatment. And, at the end of the process, the parts are deodorised and free of solvent residues, preventing any risk of environmental contamination,” states Sabbadin. “Our cleaning machines are flexible and able to perform various treatment processes depending on the degree of contamination, adapting to a wide range of parts and allowing programming the required operations and cycle times via the control panel. Moreover, vacuum treatment at low temperatures prevents the thermal dissociation of solvent, thus eliminating the need for stabilisers.
From left to right:
- The cleaning plant’s loading and unloading roller conveyor.
- The entrance to the cleaning booth.
- The cleaning booth.
Our cleaning machine can perform a continuous-flow, complete distillation process ensuring the total recovery of solvent – and making the residue reusable without solvent: residue stripping also takes place under vacuum, reducing the residual solvent content to 1% without compromising productivity.”
Cosmogas maintains a leading position in the industry through a combination of family tradition and constant innovation. Installing this new cleaning system represented a significant step towards excellence in boiler and heat pump production, meeting future challenges and improving workplace safety. “We are extremely satisfied with our purchase and our cooperation with IFP Europe. After extensive assessment and practical tests on IFP’s machines, we can confirm this was a high-quality investment. The ability to treat simple and complex parts with specific recipes and an average cycle time of 15 to 20 minutes demonstrates the flexibility and efficiency of our new system,” concludes Alberto Alessandrini, Head of the Research & Development Center at Cosmogas. “It complies with the Industry 4.0 requirements and includes an integrated PLC, also allowing IFP Europe to provide remote technical assistance and perform remote checks and modifications – an added value we will take advantage of starting next year.”
Giacomo Sabbadin, the CEO of IFP Europe, emphasises the importance of the high degree of environmental quality and work safety offered by the new cleaning plant: “The full vacuum treatment provides greater environmental protection both within the working area and in the outside atmosphere. The depressurisation of the plant prevents the escape of any vapours or gases, whereas the installed safety systems manage these functions effectively and consistently. Finally, throughout the whole cycle, the operators never come into contact with the cleaning liquid.”
From top to bottom:
The touchscreen.
Fittings cleaned in the new IFP Europe plant.
Lavatrici Sottovuoto Alcoli Modificati . Idrocarburi
LAVAGGIO DEL FUTURO… ADESSO
• ULTERIORE RIDUZIONE DEL CONSUMO ENERGETICO DEL 30%
• POMPE A VUOTO POTENZIATE ESENTI DA MANUTENZIONE
• DISTILLATORE PRINCIPALE RADDOPPIATO
• SISTEMA DI RISCALDAMENTO INNOVATIVO
• DRASTICA RIDUZIONE DEL TEMPO CICLO
• NUOVO SOFTWARE DI GESTIONE INTUITIVO
• RIDUZIONE DEGLI INGOMBRI ESTERNI
• ACCESSO FACILITATO PER LA MANUTENZIONE
• NUOVO DESIGN
For Tecnotrasmissioni, the cleanliness of industrial components is a prerequisite for all its operations. As it remanufactures transmissions and gearboxes, it has to make sure that all parts are precisely clean to clearly separate those that can be reused and those that need to be replaced. For more than twenty years, this company has been working with Teknox, which recently supplied it with a new Robur 1400 HT one-stage cleaning system.
The industrial cleaning of parts often plays a vital role within manufacturing flows, as an intermediate stage to remove impurities that could jeopardise the production of a component or its use in more complex systems or as the final one, performed to improve its aesthetics.
For Tecnotrasmissioni, it is the very foundation of its operations, without which it could not offer its services. This firm remanufactures mechanical transmissions and gearboxes using original spare parts acquired directly from parent companies or their suppliers, so as not to compromise the quality and efficiency of its end products. The correct cleaning of individual parts is therefore a crucial prerequisite, as it enables Tecnotrasmissioni’s technicians to identify worn parts that need to be replaced and components that can be reconditioned, in order to reuse the transmissions.
The continuous improvements and investments made by this company over the years have enabled it to develop an industrially advanced and standardised production process that ensures high efficiency and effectiveness. However, such constant growth also generated the need to improve its cleaning operations. Satisfied with its twenty-year collaboration with Teknox (Budrio, Bologna, Italy), Tecnotrasmissioni asked the cleaning machine manufacturer to develop a new one-stage system that would allow it to double its production, reducing operating times while maintaining high cleaning efficiency.
Tecnotrasmissioni Srl was founded in Calderara di Reno (Bologna, Italy) in 1988. Since its inception, the company has specialised in remanufacturing mechanical transmissions, particularly manual and semi-automatic transmissions for passenger cars and commercial vehicles. Over time, it has expanded by moving to a more modern factory in Valsamoggia (Bologna) in 2002 and then building a new production site with an adjoining warehouse in 2014. That has enabled it to differentiate its offer by also including the remanufacturing of rear differentials, rear axles, and front transfer cases. Today, with over thirty-six years of experience, Tecnotrasmissioni employs 40 people who remanufacture more
than 5,000 transmissions annually, distributing its products on 6 continents and offering spare parts for more than 2,000 models of 30 different makes.
“We have always maintained a firm commitment to quality and innovation, using original or high-quality spare parts and complying with the technical specifications of manufacturers. Throughout our history, we have been able to develop a high level of technical expertise and cultivate a dense network of relationships with all leading car manufacturers, such as Stellantis, whose catalogue includes parts and gearboxes remanufactured by us,” says Riccardo Trombini from Tecnotrasmissioni Srl’s Sales & Marketing department.
“Thanks to an increasingly well-developed and well-trained technical office, we can study every new gearbox put into production down to the last detail, thus combining experience and innovation to provide regional, national, and international spare parts dealers and distributors as well as garages and end consumers with an increasingly complete and wide range of products. Italy and Europe are our main markets, but we also have a solid presence in South America.”
Disassembling, cleaning, and assembling original transmissions and gearboxes
Tecnotrasmissioni’s production flow is well-structured and highly efficient. The company only uses original spare parts (when it is possible) and complies with all the technical specifications imposed by their manufacturers, thanks to an industrialised and standardised work method with state-of-theart equipment and tools. That has also enabled the company to obtain ISO 9001 certification (the international standard for quality management systems) and IATF16969 certification (the international standard for the production of components in the automotive sector).
From top:
A case of transmissions remanufactured by Tecnotrasmissioni.
The first cleaning machine, used for treating aluminium outer cases.
The Robur 1400 HT cleaning machine from Teknox.
Tecnotrasmissioni receives the used products directly at its Bologna site and disassembles them into each individual component. Then, it cleans all parts thoroughly in order to remove neat oils and other contaminants from their surfaces, which could make it difficult to spot any signs of wear or damage.
After carefully checking the condition of components, it proceeds with selecting compliant parts, which are stored and ultimately reused for new assemblies, whereas defective parts are discarded and replaced with original or high-quality spares. After assembly, the transmissions are tested, and if necessary, some of their components are coated to improve their appearance.
“Tecnotrasmissioni’s goal is to restore components to serviceable condition so they are fully equivalent to a new product. Of course, we always try to recover as many parts as possible, which translates into savings for our customers and us. At the same time, however, we must ensure that the quality of the end product is high and certified, as a transmission needs to be durable. Therefore, even the smallest sign of wear means the part is discarded,” Trombini explains. “The control of the individual parts that make up the gearboxes must be precise and strict. Cleaning, therefore, plays a key role in our activities. It is not merely intended to improve the aesthetics of aluminium outer cases: it is essential for our operations.”
Tecnotrasmissioni is still using a single-chamber, one-stage cleaning machine built by Teknox over twenty years ago. However, the constant growth of the production capacity and quality standards brought the need to speed up and perfect the cleaning phase as well. Therefore, the company requested a new version of the same technology from its supplier. As a result, Tecnotrasmissioni has doubled its production and optimised its processes: it now cleans steel gears and other transmission components with the new system, whereas aluminium outer cases are treated in the old one.
“We clean hundreds of components every day. After being placed in baskets, which in turn are arranged on a turntable, the parts undergo a spray cleaning phase with a multi-material detergent. Its duration is variable, but the standard cycle lasts about 7 minutes. At the same time, a one-stage machine gives us a high degree of flexibility: it allows us to set very short cycle times (down to 30 seconds) for parts with few contaminants or longer durations for components that need thorough cleaning, without the technical times typically required by multi-stage solutions, for example, for the degreasing product to drain off before rinsing or the passivation phase. Although dated, moreover, our first cleaning machine is still highly efficient, and we use it every day.
When we saturated its capacity, we had no hesitation in asking Teknox to supply us with the same system,” says Trombini.
“The new machine is a Robur 1400 HT type, an upgraded version of the one already available to Tecnotrasmissioni. The only substantial change concerns the spray bars: in addition to the upper ones and those positioned in the two opposite front corners, we have added two additional vertical spray bars in the centre of the chamber. This ensures that the cleaning product envelops the components, also penetrating their cavities. At the same time, we have replaced the traditional cleaning pump with a high-pressure one to increase the force with which the jet hits the parts and thus improve the system’s capacity to remove contaminants,” explains Marcello Maffei, Sales Manager at Teknox. “We simplified the management of the system thanks to an industrial PLC, programmed for remote assistance and compliant with Industry 4.0, and perfected the user interface, which allows to freely create up to 16 programmes and start all the features of the system including emptying the tank, starting the oil separator and activating the energy saving mode with a simple touch of the screen. The software, developed by Teknox, provides weekly programming of heating and oil removal times, to allow operators to find the system ready when they start their shift, thus offering significant savings in time and process quality. Furthermore, all external metal surfaces are thermally insulated to ensure maximum safety for users and the working environment.”
Teknox’s Robur 1400 HT plant recently installed at Tecnotrasmissioni’s premises is a one-stage machine with a jet cleaning system. It is equipped with a lower, a vertical, and an upper spray bar that ensure complete cleaning from all sides with a solution
composed of water and detergent specifically developed by Teknox. This operation is followed by a drying phase with compressed air blowoff. The plant also features a system to control the maximum liquid level in the tank with its filling solenoid valve, a rotary platform in AISI 304 stainless steel, and a drawer for cylindrical filters located between the cleaning area and the rinsing tank to retain impurities larger than 1 mm. Additional hat filters with a finer mesh size retain solid particles larger than 25µm. A centrifugal condenser connected to the machine’s suction system was mounted above the plant: this patented device is an air/air heat exchanger that condenses the emitted vapour into liquid, which is then sent back to the machine’s tank, thus avoiding dispersing vapour outside the factory. The system is also equipped with an external pneumatic oil separator with floats, fully insulated for safety reasons (protection from contact with hot surfaces > 60 °C) and fitted with wheels for easy handling. Made entirely of stainless steel, it ensures the separation of neat oils by coalescence: thanks to a system of floats and a pneumatic pump, the liquid is sucked from the surface of the cleaning bath, to which the unit is connected via a flexible pipe. Before entering the oil separator, the liquid is filtered with a 32 mesh cartridge filter and then through the coalescence separators, which aggregate the individual oil particles to form droplets that rise to the surface. The neat oil is thus collected by overflowing in a 30-litre PVC tank, whereas the purified liquid is recirculated to the cleaning tank via a flexible pipe.
Thanks to the Teknox machine, Tecnotrasmissioni has thus been able to further improve its production process, obtaining high-quality remanufactured products and meeting its customers’ requirements with greater efficiency.
“Although it is not a particularly complex technology, it is nevertheless a solution that meets all our needs: we use it in a standardised way, but it still gives us the possibility to adapt the cleaning process to the specific requirements of parts. Having worked with Teknox for many years, we have become intimately familiar with their work ethic, the professionalism of their technicians, and the flexibility of their machines, always customised to our requirements. Our decision to install the new Robur 1400 HT is proof of this: we turned to them without a second thought, and the results have confirmed this was the right choice. Cleaning is more uniform, thorough, and quicker thanks to the additional vertical spray bar, the one-stage cleaning product that does not require additional rinses reduces downtimes and increases productivity, and the plant’s insulated structure and energy-saving system with the possibility to programme on/off times help reduce our operating costs,” Trombini says with satisfaction.
Fismet Service Srl, a long-standing company in the industrial cleaning sector, has been helping train the technical professionals of the future for many years. On 23 September, as part of the Industrial Short Master, it will hold a lecture entitled “Surface preparation. Seeking absolute cleanliness while respecting the environment (sustainability – circular economy). Surface preparation technologies – A case history”.
Technical and vocational training is vital for anyone wishing to pursue a career in industry. At the same time, however, many Italian manufacturing companies have long complained about the lack of adequately trained professionals. Fismet Service Srl, a long-standing company based in Cornaredo (Milan, Italy) specialising in the production and sale of high-tech industrial cleaning systems and contract cleaning services, has for years been at the forefront of technical training and know-how sharing to shape the technicians of the future.
The company cooperates with various educational and research institutions by contributing to their advanced technical training programmes. These collaborations aim to create concrete opportunities for students to come into contact with the world of
work, facilitating the transition from theory to practice. One of the key elements of technical training is indeed the combination of theoretical classroom lessons with practical experience directly in the field: this allows students to gain an in-depth understanding of technological and design issues, but also of the innovative solutions developed by the industry.
“Our desire, which is also a need for the Italian manufacturing industry, is to train professionals capable of thoroughly understanding and managing the many technological and design issues entailed in all those professional and research fields where the use and, now more than ever, the recycling of materials are linked to surface treatments,”
explains Sabino Di Pierro, the founder and owner of Fismet Service Srl. “We would like to offer hands-on experience of the production, research, and development processes occurring within a company that has dedicated itself to perfecting the cleaning of metals and plastics for over forty years. We have also always been committed to spreading the idea that only through a solid industrial culture is it possible to effectively combat surface contaminants with innovative solutions in terms of both plant engineering and material recovery or reuse. Fismet also disseminates this vision through participation in several technical conferences, such as the recent S.M.A.R.T. 3 event organised by the Italian Finishing Equipment Manufacturers’ Association (UCIF).”
That is also why it has been offering its contribution to the Industrial Short Master organised by PoliEfun (the association created from the collaboration between companies in the surface treatment sector and the university world, under the guidance of the Politecnico di Milano), Aital (the Italian Association for Aluminium Surface Treatments), and Qualital (the Institute for Industrial Certification of Aluminium and Other Materials). Sabino Di Pierro will deliver his lecture entitled “Surface Preparation. Seeking absolute cleanliness while respecting the environment (sustainability – circular economy). Surface preparation technologies – A case history” on the morning of 23 September 2024.
Fismet Service’s environmental vocation
“Seeking absolute cleanliness while respecting the environment” is, therefore, the theme of Di Pierro’s lecture, but it is also the principle on which Fismet’s entire philosophy is based. “The most common cleaning systems entail the use of chemicals that are problematic in terms both of storage and disposal and of the extensive use of water required,” he adds. “On the other hand, we advocate for the least polluting cleaning technology, based on a mechanical principle combined with the action of ultrasound. We have extensive experience designing and constructing cleaning machines, which is also a guarantee for companies that directly entrust us with cleaning their components. We can develop a tailor-made cycle for each customer, even with the most complex, porous, and difficult-to-treat materials, such as aluminium and magnesium, ensuring optimum results.
“In addition to these traditional functions, cleaning has taken on a strategic role with a view to the circular economy like no other operation in the surface treatment industry, as it allows for the cleaning and potential reuse of any component. At the same time, another
aspect that we at Fismet consider very important and for which our laboratory carries out constant R&D activity is the possible recovery of removed dirt, which can be turned from waste into an unexpected resource. We have already proved this is possible with the GHOST project: through mechanical tilting and rotating movement combined with the action of ultrasound, we have recovered fishing nets that were restored to their original function and, at the same time, reused the removed dirt for applications in other sectors, such as cosmetics1. The latter is incidentally one of Fismet’s target markets: our company is also a member of Polo Tecnologico della Cosmesi, an association formed by the best companies in Italy’s Lombardy region representing the entire cosmetics supply chain.”
Di Pierro is going to illustrate this and other case histories during his lecture. “We must make it clear to the new generations of technicians in training that technological development is fast and the continuous search for innovative solutions to anticipate not only market demands but also the planet’s needs is the best innovative tool at our disposal,” he summarises.
1 https://www.ipcm.it/en/open/ipcm/2019/60/194-196.aspx
The first edition of the new trade fair PARTS FINISHING will take place from 12th to 13th November 2025 at the Exhibition Centre in Karlsruhe (Germany).
Never before has the industry changed as rapidly as it is doing today. This fact also affects the requirements made on trade fairs. DeburringEXPO will therefore no longer take place as an independent event, but will be incorporated into the new trade fair called PARTS FINISHING, taking place for the first time next year on 12 and 13 November 2025. The new two-day event will combine the subjects of deburring technologies, component cleaning and surface finishing and will be held at the exhibition centre of Karlsruhe. Megatrends such as the mobility and energy transition, demographic changes and digitalisation pose new challenges for the economy and society, but also present opportunities. They demand new products and adapted manufacturing strategies of the manufacturers and companies far down the supply chain. These changes are not failing to have an effect on the trade fair landscape.
“After numerous discussions with companies that exhibited at DeburringEXPO and having closely observed the development of various trade fairs, we have reached the decision no longer to hold the trade fair for deburring technologies as an independent event”, explains Hartmut Herdin, managing director of the private trade fair organiser fairXperts GmbH & Co. KG. “In future, the subject of deburring technologies will be combined together with the fields of component cleaning and surface finishing at the new two-day trade fair PARTS FINISHING.” The area of surface finishing will include the process steps of fine and ultra-fine grinding, polishing, honing, lapping, vibratory grinding, blasting and brushing.
The market has reacted very favourably to this innovative concept, and the experienced trade fair organiser has already received bookings from well-known and less well-known plant manufacturers. “Our discussions also showed that many interested companies have already drawn up their plans and budgets for trade fairs this year. We therefore decided to postpone the launch of PARTS FINISHING by one year and carry it out on the Karlsruhe exhibition grounds on 12 and 13 November 2025”, elucidates Hartmut Herdin. The event will subsequently continue to take place in uneven years at two-year intervals.
By bringing together these three important and quality-critical areas of parts production over a two-day period, the organiser is fulfilling the requirements and wishes of the market. “More and more companies are questioning the cost-benefit ratio of exhibiting at a traditional trade
fair”, says Hartmut Herdin. “In order to present machines, for example, at a stand, a great deal of stand space is required, which incurs a lot of expense. These days, however, there are also very good ways to present efficient performance and expertise digitally.”
These aspects were taken into account in the trade fair concept for PARTS FINISHING. Firstly, the concept makes it possible for people who are responsible for parts production to obtain concise information about solutions, and it facilitates a dialogue between users and exhibitors in the cross-process development of solutions for special applications. Secondly, the length of the trade fair being reduced to two days means less costs incurred for journeys, accommodation and staff. “This aspect is facilitated by high-quality, turn-key, customisable stand packages that are available at fixed costs and save time, money and resources right from the early stages of preparing the trade fair,” adds the trade fair organiser. The PARTS FINISHING concept thus concentrates on the very purpose of trade fairs: to help establish and maintain contacts between users and offerors and build and intensify networks among exhibitors. “The latter makes it possible to form strategic partnerships and to jointly approach new projects as a systems supplier”, remarks Hartmut Herdin.
For further information: www.parts-finishing.de
Trafilerie Mussari (Lurate Caccivio, Como, Italy) is a company of excellence in the production of drawn high-precision stainless steel tubes. About two years ago, it embarked on a complete renovation path with a view to quality and the sustainability of the speciality chemicals it uses in production, followed by the installation of three innovative machines, aimed at making pickling and degreasing more efficient from an environmental point of view, and a specially developed degreasing unit. And it chose Condoroil (Casale Litta, Varese, Italy) with its Chemical and Stainless divisions, as its only partner for this upgrading project.
Drawing is a production process that starts with a tube to create a smaller one with special mechanical, structural, and dimensional characteristics. It is an industrial operation with a deep-rooted craftsmanship component – where automation is important, but human expertise is still fundamental to manufacturing a tailored product. Founded in 1975 based on the entrepreneurial idea of Salvatore Mussari, Trafilerie Mussari is preparing to celebrate its 50th anniversary with significant growth results in terms of both production volumes
and, thanks to its high focus on quality, the number of increasingly demanding sectors served. Among other products, Mussari manufactures stainless steel tubes for industries with special requirements such as aerospace, hydrogen, and oil and gas. This article presents the recent innovations this company implemented in the field of chemical surface treatments, which, as you will appreciate, were conceived with a strong focus on the environment and the well-being of operators.
The first innovation entailed the progressive replacement of traditional drawing lubricants, i.e. non-reactive salts, oxalates, and soaps, with special oils and polymer-based products. The polymer selected from the range of speciality chemicals offered by Condoroil Chemical is diluted in water to a concentration of 80%, applied in one step, and then directly dried without needing intermediate rinses. The absence of salts in its formulation results in perfectly homogeneous and shiny surfaces.
As for pickling, Trafilerie Mussari, one of the first companies to stop using nitric acid in favour of so-called nitric-free products with a lower environmental impact back in the 1990s, asked Condoroil Chemical for a continuous-flow solution that would ensure perfectly repeatable results over time. In addition to providing for constant monitoring and restoration of the correct concentration values of active species and of the redox potential by qualified personnel, the company also chose
to install a regeneration plant with acid-delay technology, keeping the concentration of dissolved metals constant.
Thanks to the use of special resins, the RESIBED regeneration plant supplied by Condoroil Stainless allows to continuously remove the metal, which is solubilised during the pickling operation, from the tank, thus preventing its concentration from varying over time and resulting in changes in treatment times.
This regeneration unit’s operating principle is based on the ability of suitable ion retardation resins to slow down the flow of mineral acids in the pickling solution while allowing the metal salts contained to pass through. As the adsorption process is reversible, the acids adsorbed by the resins are simply removed with water and recirculated to the pickling baths.
The system does not require chemical reagents. Energy consumption is practically zero and limited to the energy needed to run pumps with modest flow rates. This technique has been long established in the pickling and anodising industry and allows the baths to be maintained at a constant metal content while avoiding the need to discharge and
purify the free acids present, which are mostly recovered.
The main benefits of integrating a RESIBED unit are as follows: pickling capacity maintained at a constant level;
reduced acid consumption;
reduced amount of sludge;
reduced consumption of reagents in the neutralisation phase;
reduced staff intervention for acid and process solution management.
As regards the degreasing phase, Trafilerie Mussari worked with Condoroil focussing on three key areas to achieve the high quality standards required by the market, namely as follows:
chemistry, by defining a treatment cycle with suitably performing formulations;
plant engineering, by creating a system capable of providing adequate mechanical action during degreasing, even within 18 m long pipes with a small internal diameter (down to 2 mm);
management, by integrating the cleaning section with a plant for continuous regeneration of the degreasing solution and the final rinse section with a recycling demineraliser to maintain a negligible
concentration of dissolved salts. The degreasing phase thus provides optimal results over time and perfectly clean surfaces free of any deposits.
The degreasing system conceived and developed by Mussari and Condoroil Stainless is designed to accommodate the tube bundle head in a confined chamber where it is hit with a strong flow of solution. Its peculiar geometry forces the solution into the bundle, allowing for proper mechanical action both at the contact points and within the tubes; periodic rotation of the bundle allows the contact points to be changed, ensuring that the tubes are completely clean.
The complete cycle includes alkaline degreasing to remove the lubricants’ organic component, acid degreasing to solubilise the inorganic components and revitalise the surface, post-treatment rinses, and a demineralised water rinse. All steps are carried out automatically, and dedicated software makes it possible to adjust times, temperatures, and handling operations, as well as simplify the treatment cycle when the degree of contamination allows it.
To prevent the cleaning results from worsening over time as the contaminants in the solution increase, Trafilerie Mussari chose to install an ultrafiltration system from Condoroil Stainless’ Minerva series to
continuously regenerate the alkaline solution, which is the one that pollutes the fastest over time. The ultrafiltration plant guarantees the continuous removal of pollutants, i.e. the lubricant residues removed from the machined tubes’ surfaces. These are discharged in concentrated form, whereas the solution always remains clean and never needs to be replaced. Keeping the solution constantly clean also means that rinses are less polluted, which in turn reduces the volume of eluates produced by the recycling demineralisation plant, the IONEX ion exchange unit also supplied by Condoroil Stainless.
The project to renovate the chemical section of Trafilerie Mussari was launched in 2022, when the company selected Condoroil as its partner for both the chemicals and the continuous-flow treatment and purification plants. Condoroil Chemical is an Italian company that has been developing and producing surface treatment chemicals for over 50 years. Research on products and processes has always been directed towards the formulation of solutions with a lower environmental impact, resulting in a considerable evolution over the years that has seen the company constantly expand its range of products and sectors served.
In the 1990s, it also embarked, together with the current Condoroil Stainless, on the joint development of chemical formulations and processes to minimise waste through product regeneration and raw material recovery technologies.
The technologies offered by Condoroil Stainless, a “Green Engineering” pioneer, have demonstrated that it is possible to reduce the consumption of natural resources through targeted solutions in line with the philosophy of the circular economy, which favours their recovery and reuse directly on-site.
From left to right:
Operational diagram of the RESIBED system.
The degreasing line developed by Condoroil Stainless together with Trafilerie Mussari.
Operational diagram of the degreasing line.
“We have known Condoroil as a chemical supplier for a number of years, as it replaced our long-standing speciality chemical supplier by better aligning with our ESG policy, focussed on increasing quality and reducing the environmental impact of our production,” states Simone Mussari, the CEO of Trafilerie Mussari, headquartered in Lurate Caccivio, Como. “More recently, we started collaborating with the Condoroil Stainless division to improve the efficient use of speciality chemicals, from lubricating oils to drawing acids and degreasing agents, by installing regeneration, demineralisation, and degreasing units. We chose to embark on this investment path that has lasted over two years
together with Condoroil because, apart from the professionalism and expertise of its technicians and the market’s positive feedback, we have found great reliability in the machines they supplied us with.
“Today, I can say that Condoroil is a strategic partner for our growth, also thanks to its excellent after-sales technical assistance. We are currently approaching market sectors where product quality, quality warranties, and compliance with regulations are decisive. The results we have achieved with these investments in machines and chemicals have helped us enter them successfully.”
Eos Mktg&Communication srl www.eosmarketing.it - info@eosmarketing.it www.myipcm.com - info@ipcm.it
Redazione - Sede Legale: Via Pietro Mascagni, 8 - 20811 - Cesano Maderno (MB) - Italy Tel. +39.0362.503215 - Fax. +39.0362.1794768
EDITOR IN CHIEF / DIRETTORE RESPONSABILE
ALESSIA VENTURI venturi@ipcm.it
EDITORIAL DIRECTOR / DIRETTORE EDITORIALE
FRANCESCO STUCCHI stucchi@ipcm.it
EDITORIAL OFFICE / REDAZIONE
PAOLA GIRALDO giraldo@ipcm.it
MONICA FUMAGALLI fumagalli@ipcm.it
NICOLE KRAUS kraus@ipcm.it
MATTEO SOTTI sotti@ipcm.it
ILARIA PAOLOMELO paolomelo@ipcm.it
Prof. Massimiliano Bestetti: Department of Chemistry, Material and Chemical Engineering, Politecnico of Milan –Section of Applied Chemistry and Physics
Prof. Paolo Gronchi: Department of Chemistry, Material and Chemical Engineering, Politecnico of Milan –Chemical Engineering Section
Kevin Biller: ChemQuest Powder Coating Research
GABRIELE LAZZARI redazione@ipcm.it
FEDERICO MELIDEO melideo@ipcm.it
GIULIA GENTILE gentile@eosmarketing.it
EDITORIAL OFFICE AND GRAPHICS
ELISABETTA VENTURI grafico@ipcm.it
MEDIA SALES
FRANCESCO STUCCHI stucchi@ipcm.it
ILARIA PAOLOMELO paolomelo@ipcm.it
NICOLE KRAUS kraus@ipcm.it
Prof. Stefano Rossi: Material Engineering and Industrial Technologies, University of Trento - Product Design
Dr. Fulvio Zocco: Environment and quality
LAYOUT/ IMPAGINAZIONE
ELISABETTA VENTURI grafico@ipcm.it
SUBSCRIPTION SERVICE - SERVIZIO ABBONAMENTI:
Sale only on subscription - Vendita solo su abbonamento E.mail info@ipcm.it
Subscription Rates 2024 - Tariffe Abbonamento 2024:
Annual subscription print + digital:
EMEA 110,00 € (postage included)
Rest of world 350,00 € (fast airmail shipping included)
Abbonamento annuale cartaceo + digitale: EMEA 110,00 € (spese postali incluse)
Resto del mondo 350,00 € (spedizione via aerea inclusa)
Single copy: 15,00 € EMEA (postage included) - Rest of world (postage excluded)
Back issues: 30,00 € EMEA (postage included) - Rest of world (postage excluded)
The smart journal for surface treatments
This magazine is wrapped with a biodegradable and compostable film. Questa rivista è confezionata con un film biodegradabile e compostabile.
PRINT/ STAMPA
SEBEGRAF SRL info@sebegraf.eu
Fascicolo singolo: 15,00 € EMEA (spese postali incluse) - resto del mondo (spese postali escluse) Arretrati: 30,00 € EMEA (spese postali incluse) - resto del mondo (spese postali escluse)
Subscriptions can be made by bank transfer to the following account: Eos Mktg&Communication Srl IBAN IT97F0844033270000000084801 - SWIFT CODE CRCBIT22 or via payment online at: www.myipcm.com
Gli abbonamenti possono essere sottoscritti versando il relativo importo a mezzo b/b IBAN IT97F0844033270000000084801 intestato a eos Mktg&Communication Srl oppure con carta di credito direttamente dal sito www.myipcm.com L’Iva sugli abbonamenti, nonchè sulla vendita di singole copie è assolta ai sensi dell’art.74 comma 1 lett. C DPR 633/72, DM 29/12/1989.
Registrazione al Tribunale di Monza N° 1970 del 10 Dicembre 2009. Eos Mktg&Communication srl è iscritta nel Registro degli Operatori di Comunicazione con il numero 19244
POSTE ITALIANE S.P.A. – SPEDIZIONE IN ABBONAMENTO POSTALE –D.L. 353/2003 (CONV. IN L. 27/02/2004 N.46) ART. 1, COMMA 1 LOM/MI/4351
It is forbidden to reproduce articles and illustrations of “ipcm®” without authorization and without mentioning the source. The ideas expressed by the authors do not commit nor magazine nor eos Mktg&Communication S.r.l and responsibility for what is published is the authors themselves. È vietata la riproduzione di articoli e illustrazioni di “ipcm®” senza autorizzazione e senza citarne la fonte. Le idee espresse dagli autori non impegnano nè la rivista nè eos Mktg&Communication S.r.l e la responsabilità di quanto viene pubblicato rimane degli autori stessi.