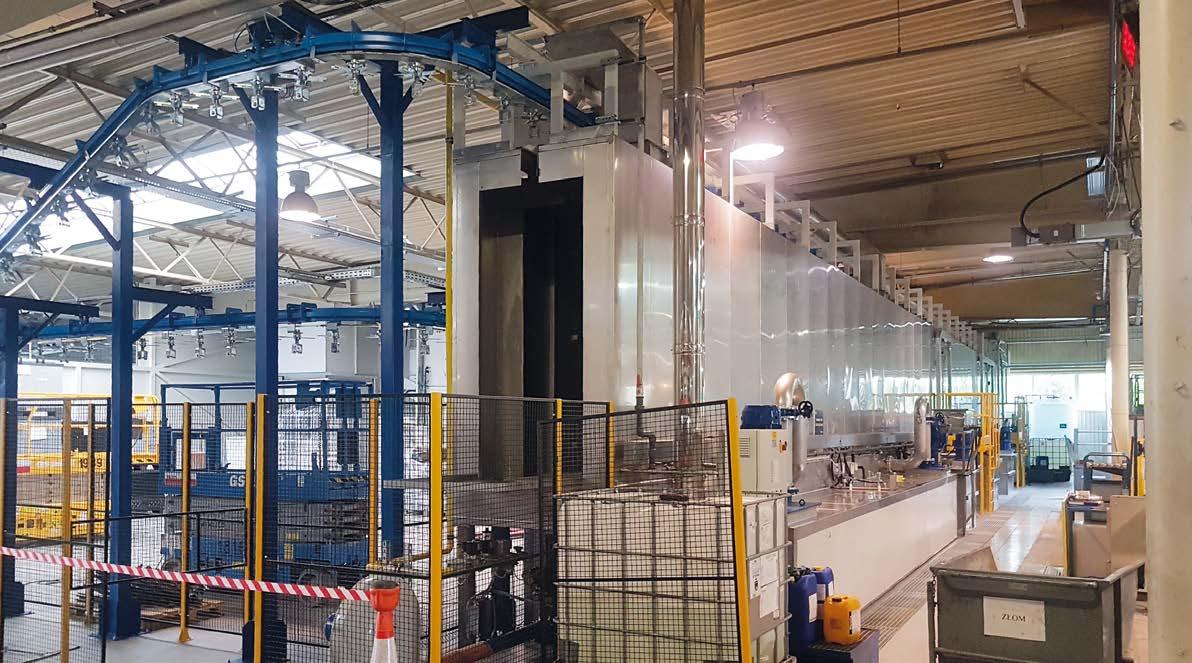
4 minute read
HIGHLIGHTS OF THE MONTH
A coating system during the assembly phase.
© Avin
HIGHLIGHT OF THE MONTH
SPECIAL ISSUE ON AUTOMOTIVE
Avin – A Strategic Partner for First Aid in Paintshops, Also in the Automotive Sector
Francesco Stucchi ipcm®
The assistance service for the systems maintenance and revamping is the core business of Avin, a company specialized in operations on the industrial coating lines.
In technical magazines such as ipcm®, success stories about the installation of new coating systems are always presented in emphatic tones, often the result of large investments and company expansion projects. Rarely, however, is another issue dealt with, which is very important not only for painting systems but for industrial plants in general: maintenance, modifications, and revamping – all aspects that, in the course of the service life of an industrial production line, sooner or later have to be coped with critically and competently. Since 2009, Avin Srl (San Martino al Tagliamento, Udine, Italy) has been dealing with plant modernisations, upgrades, modifications, revamping, relocations, and recovery projects on a turnkey basis, with expertise and professionalism. It is even organised to guarantee a 24-hour first-aid assistance service, carried out by its highly trained, specialised technical staff. This service is offered on a European scale in many industrial sectors, including the automotive industry, and it is mainly focused on restoring the functionality of elements such as overhead conveyors and handling systems, for which Avin also provides spare parts. Assembly and start-up services, another of Avin’s core businesses, are carried out by its subsidiary company, Met. Sp. Z.o.o (Limanowa, Poland), specialised in providing complete assistance up to the
turnkey delivery of the systems, including after-care and maintenance in agreement with each customer. “Avin was established to fill a gap in the coating plant market, namely the provision of a range of services that are often underestimated, but actually essential for properly managing an industrial plant and extending its service life. I am referring to system modifications, which are necessary when production needs change but the existing plants are still functional and recently built; to complete revamps, when a company chooses to retain a few parts of its existing system (e.g. the spray paint booths or the conveyor) and replace all other components; and to maintenance, which is often underestimated but in fact strategic for the efficiency of production lines. Finally, we also deal with upgrading projects, which, at present, are all related to digitalisation, remote control, and the Industry 4.0 in general,” says Morgan Infanti, the General Manager of Avin. “Another very complex task is plant relocation: at the moment, for example, we are working on a major relocation project of a wheel coating line. We operate mainly at the European level, but we also have active customers in China, India, Russia, the Arab States, North Africa, the United States, and South America.” “Avin also supplies a range of components that are essential for plant optimisation, such as diaphragms and cells for cataphoresis, oil separators,

© Avin
A cataphoresis tank during the maintenance phase. Avin provides with membranes, cells and any kind of spare parts.

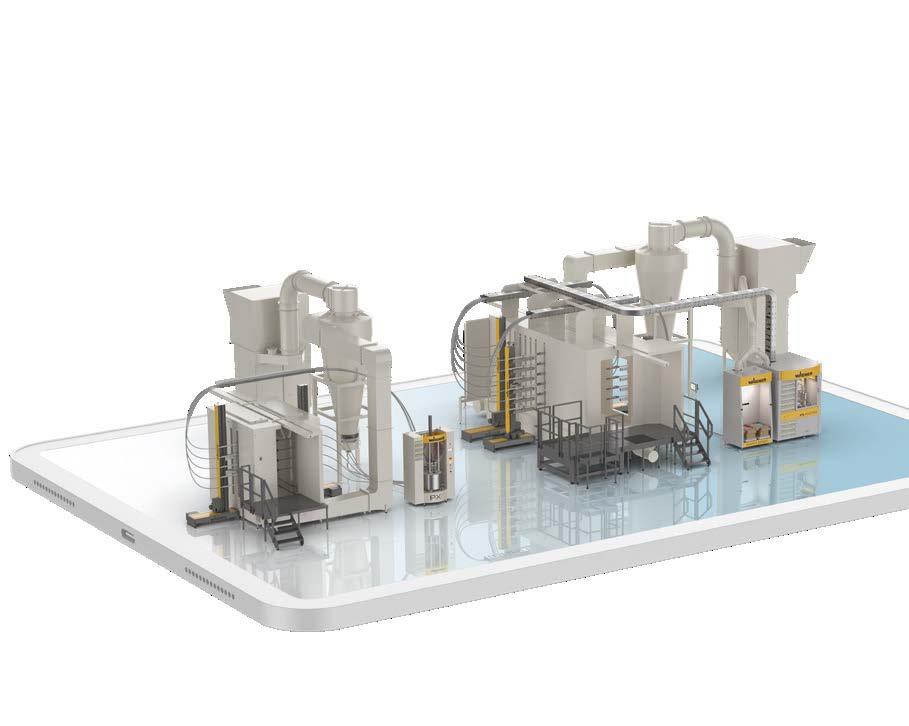
The pre-treatment tunnel is the heart of the coating plant, and it requires frequent maintenance and revamping.

© Avin
and water purification and demineralisation plants,” indicates Infanti. “While gradually training our skilled, knowledgeable staff at the mechanical and electrical levels, we first concentrated on maintenance and assembly activities, thus building a portfolio of customers that are not interested in buying new systems but simply in renewing and optimising their already existing ones. Avin, therefore, is not a competitor of coating plant engineering and manufacturing firms, but it can act as a strategic partner for them, able to support them with professionalism, expertise, precision, and accuracy and with highly trained teams of fitters and professionals.” Many markets, especially the Italian one, are currently in a recovery phase and several manufacturers find themselves with machines that need to be adjusted to meet new quality and production requirements. Avin offers an all-round plant first-aid service. “Our customers are firms looking for a good solution without investing in new equipment – although some revamps can cost more than a million Euros,” explains Infanti. “Since the beginning of the year, we have seen a big increase in demand, especially for part replacement, expansion, and optimisation tasks. Its drivers are digitalisation, increased production rates, and higher product quality requirements. The latter aspect, in particular, frequently calls for changes to pre-treatment tunnels, which are often designed for treatment cycles with a few stages, unsuitable to meet the new requirements in terms of quality degree and outdoor and corrosion resistance. In these cases, we often suggest the application of nanotechnology-based pre-treatment products, which involve the use of demineralised or osmosis water or of atomising systems.”