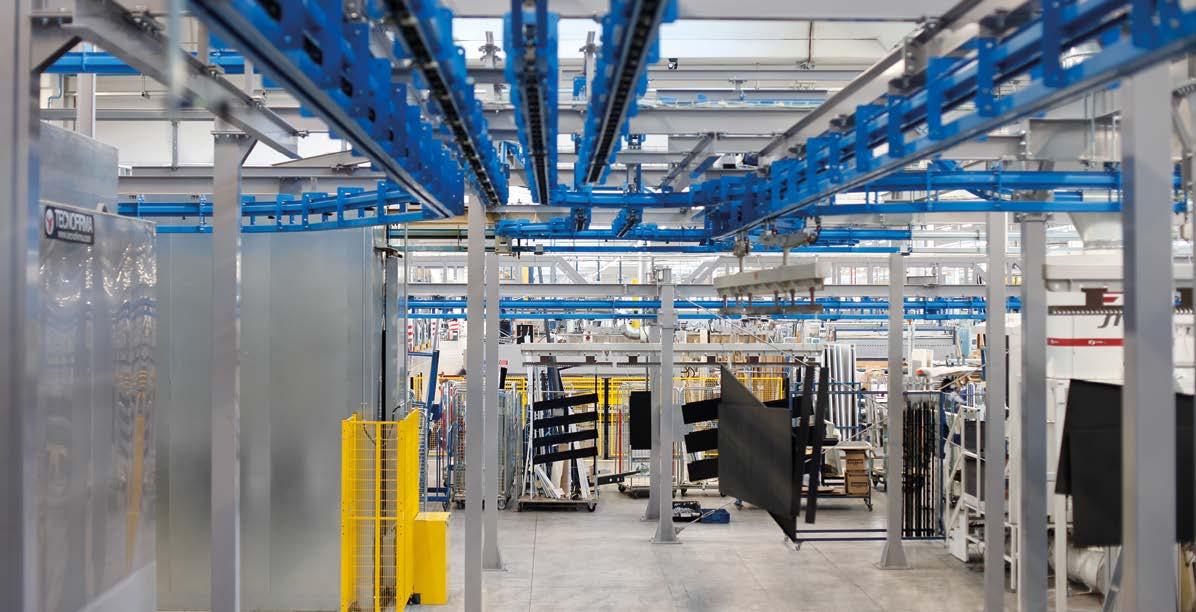
10 minute read
SUCCESS STORIES
© Tecnofirma
The Tecnofirma’s coating system with the Futura’s conveyor installed at ISA’s plant.
At ISA’s Plant, a New Coating System 4.0 Proves Strategic for the Efficient Use of Energy Resources
In the manufacturing industry, there are increasing demands for environmentally friendly production processes. Designing and manufacturing surface treatment equipment, Tecnofirma Spa has made this its mission. In ISA Spa, specialising in the production of refrigerated display cabinets and furniture for public premises, it found a customer that shares its same vocation so much so that it has decided to invest in a new Industry 4.0-oriented coating plant guaranteeing maximum efficiency of energy resources.
In the HVACR sector, the focus on saving energy sources has become ingrained in the research and development of increasingly highperformance products. This is why, when it started designing its new factory five years ago, ISA Spa, one of the most important Italian manufacturers of refrigerated display cabinets and furniture for public premises, laid the foundations for a path aimed at maximising the efficiency of energy resources in a completely Industry 4.0-oriented structure. “ISA was founded in 1963 in the Umbria region,” says Roberto Mela, Business System Manager of the company based in Bastia Umbra (Perugia, Italy). “It represents the excellence of an area internationally recognised for its high standards in the fields of fashion and design. With our 5 brands (ISA, COF, TASSELLI, ABACO, and HIZONE), we currently export to 110 countries quality products with a high level of technology and innovation, also in terms of sustainability through the use of natural refrigerants. ISA is one of the world’s most important
players in the field of furnishings for public premises, refrigerated display cases and cabinets for ice cream parlours and pastry shops, and professional furniture.” In order to meet the new challenges of the global market, in 2017 the firm inaugurated a new 65,000 m2 factory, perfectly integrated with its surrounding environment and applying innovative production and logistics methods, with a significant space reserved for the R&D division. “Our new factory,” adds Mela, “was designed and built with a view to environmental sustainability and the safety and liveability of its working environment. One of the focal points of the project was integrating increased productivity with greater control over our quality levels and material flows, without forgetting the energy impact of our production processes. The same principle was applied to our paintshop, which was built by a team coordinated by Tecnofirma (Monza, Italy) and composed as follows: Futura Convogliatori Aerei for the conveyor, DN Chemicals for the pre-treatment chemicals, and Siver for the coating application booths.”
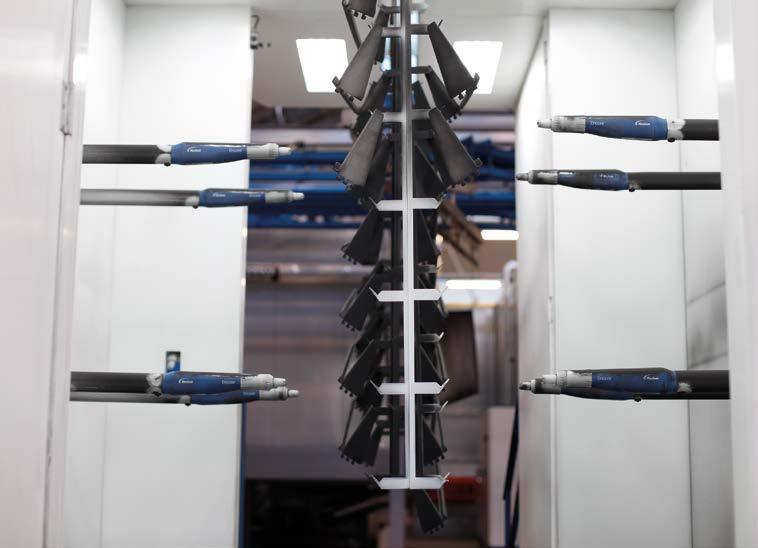
Perfect teamwork
ISA’s research study to choose the supplier of its new coating line took almost two years. “Given the importance of the coating process for our products,” notes Mela, “we wanted to carefully select our partner. After thorough analysis of the proposals made by more than fifteen suppliers, our choice fell on Tecnofirma: we visited and certified its design division and workshops and we checked the operation of some of its old and new systems installed at other companies. We were thus able to confirm its technical and construction skills and verify the robustness of its technological solutions. In Tecnofirma’s staff, we found the same expertise level and the same desire to innovate that has distinguished our company for almost sixty years.” “Compared to their previous coating line, now dismantled,” says Alex Buzzi, Project Manager at Tecnofirma, “the new system features a
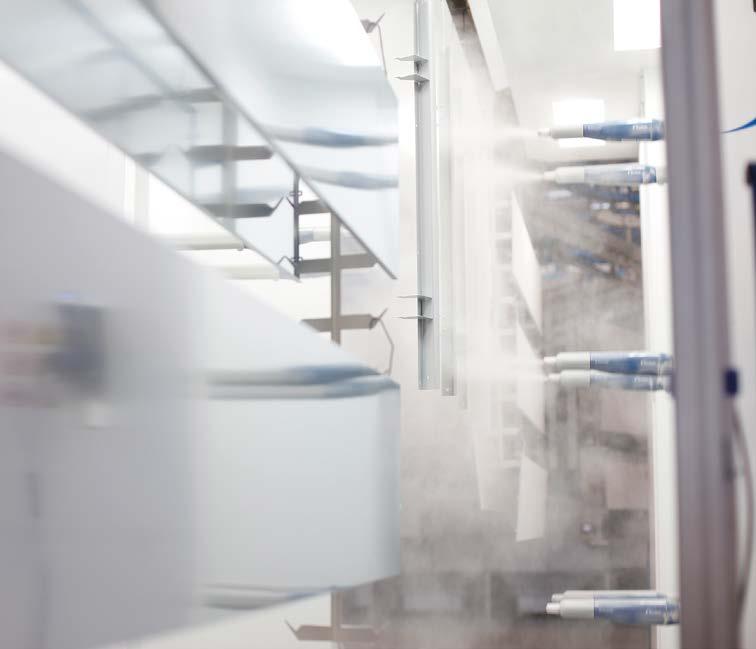
© Tecnofirma
© Tecnofirma
Interior of the coating booth.
A phase of the coating application.
higher-performance conveyor, combined with a multi-stage pretreatment process developed by DN Chemicals to increase the range of products and thicknesses that can be handled. Lastly, the oven was fitted with an energy recovery system that reuses the extracted hot air to pre-heat the new one, so as to reduce methane gas consumption and increase overall energy efficiency.”
The multi metal pre-treatment process
“The pre-treatment process developed by DN Chemicals,” explains DN Chemicals Sales Director André Bernasconi. “is an alkaline pretreatment phase guaranteeing good salt spray resistance properties on hot dip galvanised sheet metal, aluminium, and cold rolled steel. The process does not produce any sludge at all, thus extending both the replacement interval and the maintenance interval of tanks, bars, nozzles, and the heat exchanger.” If the line is stopped, no oxidation phenomena occur for a sufficiently long time and this makes it possible to avoid programming empty racks, thereby increasing production efficiency. “The surfactants package,” says Bernasconi, “was designed both to ensure the almost total absence of foam even during rinses up to almost room temperature and to facilitate the de-emulsion of oils in the alkaline pre-treatment tank and their subsequent elimination. Finally, the plant was prearranged for any future upgrade of the current process, with the possibility of integrating a final passivation stage, with or without atomisation.”
Lean production in the paintshop
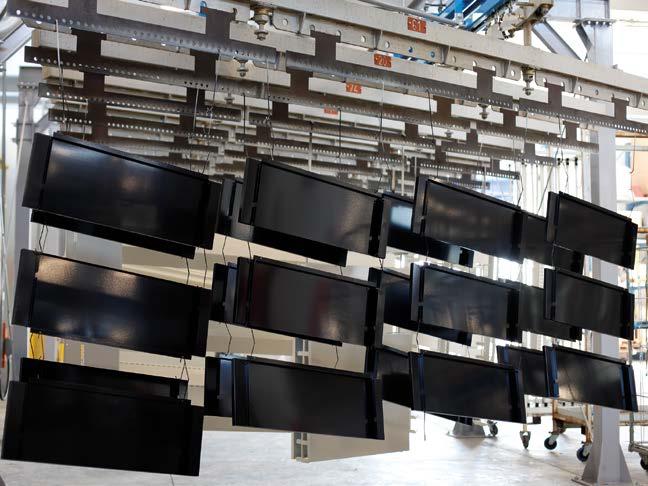
“The line provided by Tecnofirma,” notes Mela, “consists of two separate loading stations, three coating booths, and two unloading stations connected to software interfaced to ISA’s management system, thus guaranteeing maximum flexibility and speed in the handling of orders. We are able to meet any request from our partners thanks to a colour catalogue of more than 100 RAL tints, applied with about sixty colourchange operations per day. Implementing the Industry 4.0 parameters in a paintshop means optimising its process and making it as lean as possible by eliminating unnecessary activities and reducing waste, in order to achieve a tense or semi-tense production flow even in such a complex production phase.” “The use of an advanced coating process management system such as the one developed for ISA,” points out Buzzi, “guarantees constant workflow control and production optimisation, from the received orders to the end products. In particular, in this system, a barcode reader enables the loading operator to scan a production order that contains all the information needed to start a process, including the pretreatment cycle and paint colour required. The multimedia system that manages the plant keeps the information acquired throughout the cycle, while at the same time integrating it with the main process parameters. Thus, the data string reaching the coating line is further enriched with a series of information that, once the end product is unloaded, can be sent back to the management system to guarantee workflow control and data analysis.”
© Tecnofirma Conclusions
“Numerous key elements characterised the design of our new paintshop,” states Mela. “First and foremost, we wanted it to respond to the pressing demands for safety, quality, and sustainability that should now be on the agenda of any company. In order to achieve these three objectives, we first had to achieve maximum energy efficiency, reduced consumption of raw materials, and good production flexibility combined with high plant and process reliability and, last but not least, a reduction in the size of the coating system. By optimising the management of energy resources, this new coating line has enabled us to achieve the results we had set ourselves during the proposal analysis phase. Tecnofirma has long been feeling the same market ‘pressure’ for production processes with minimal environmental impact and it has been and is able to keep up with such requests by investing its technical resources and expertise to meet the demands of its customers, just like ISA is doing.”
Some coated items.
INNOVATIONS: PRESENT&FUTURE

The MATE-TX exoskeleton developed by Comau.
Comau’s New MATE-XT: A Robust, Lightweight Exoskeleton to Support Coating Operators and Reduce Muscle Strain
Stefania Bernabeo
Comau, Grugliasco (Turin) – Italy stefania.bernabeo@comau.com
Finishing operations require considerable physical effort from operators. Comau’s MATE-XT reduces the fatigue experienced by coating line workers even in less than ideal conditions and environments, without sacrificing convenience and safety. Certified EAWS by the Ergo Foundation, the MATE-XT exoskeleton effectively reduces the biomechanical risks encountered by coating operators, typically involved in loading/unloading or manual painting activities. It is now available in a more light and slim, and highly breathable version, offering more adjustment options and providing an excellent, measurable improvement in ergonomics.
The work performed on a coating line subjects operators to continuous muscular and bone strain, which can lead to health problems, mainly in the back area, and general fatigue. Both while hanging parts on frames and during manual coating activities, the physical effort and repetitive movements required of workers are high and constant. At the beginning of December last year, Comau presented MATE-XT, a revised and updated version of its wearable exoskeleton, which is particularly suitable for supporting operators during finishing processes.
Reducing physical effort
Comau has been developing industrial automation systems and products for almost half a century, specialising also in wearable and collaborative robotics solutions that reduce operator fatigue during coating operations. With the aim of helping companies, whatever their size or sector, to improve the quality and productivity of their processes and at the same time the wellbeing of their workers, the development of this type of product has been an absolute priority for this company. By providing support during physical activities, Comau’s exoskeleton reduces the effort required, thus making operations less burdensome and improving operators’ health. Thanks to its very thin, lightweight carbon fibre structure and its extremely intuitive adjustment system, MATE-XT can be quickly adapted to any body type, from the slimmest to the largest ones. By replicating the physiological movements of human operators and providing optimal upper body support, it facilitates any coating operation while greatly reducing the effort required. In addition, the MATE-XT exoskeleton does not require batteries, motors, or other devices to operate, which could hinder the workers’ movement and make the equipment heavier. There are currently 8 different levels of support available, which can be set or changed quickly even while the activity is in progress, thus guaranteeing a high degree of convenience during use. An exoskeleton of this type, therefore, facilitates the day-to-day operations carried out during finishing and coating processes, which require ever-higher quality and effort levels. Finally, Comau’s global sales network enables it to quickly meet any user needs and solve any issues that operators may face when using its exoskeletons, wherever they may be.
COATING PLASTIC PARTS?
Coating systems and application technology from one supplier Your expert for automatic coating machines for coating metal parts, plastic parts, glass and many more will be happy to advise you!
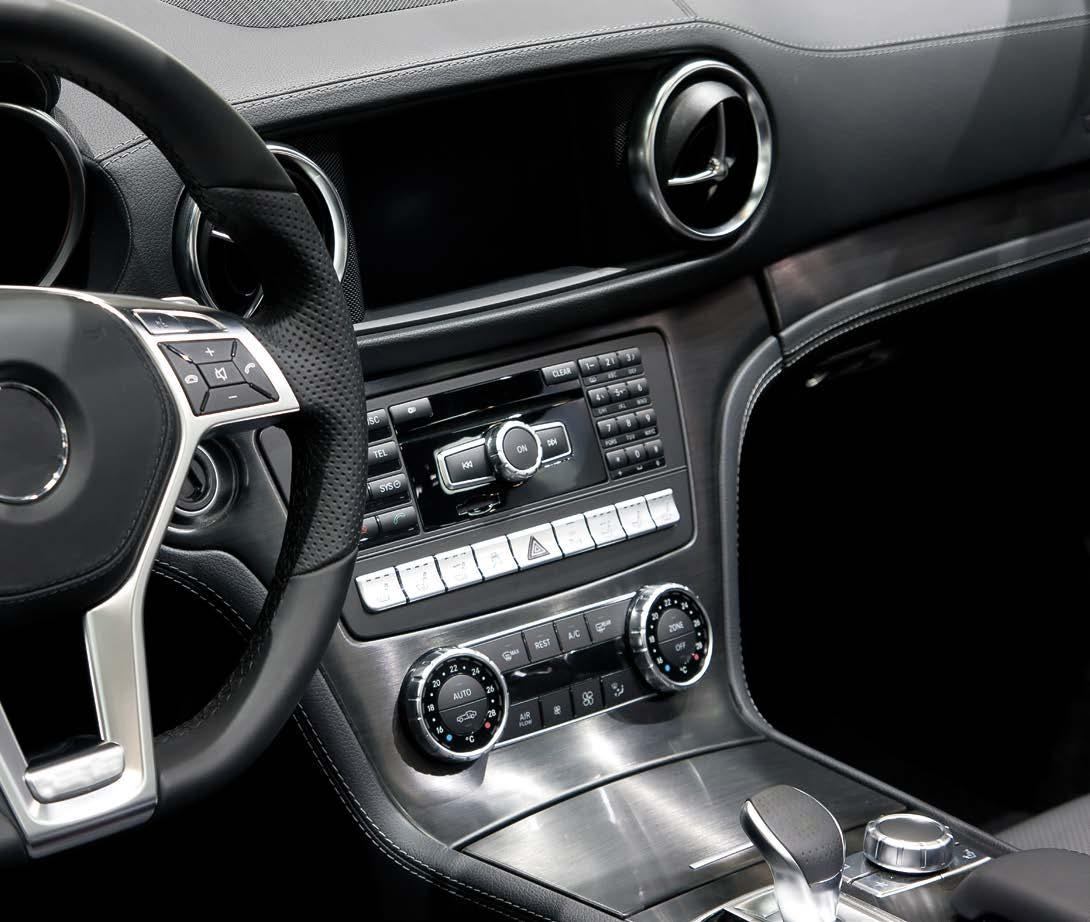
© Comau © Comau
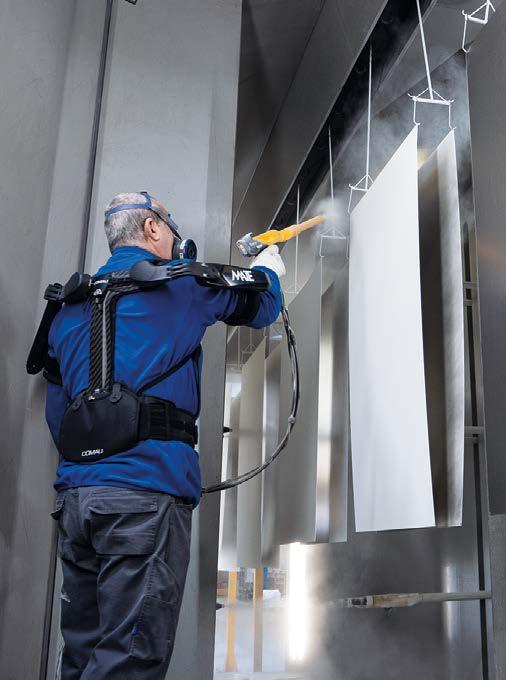
With the new product of Comau the muscular activity of shoulders decreases by 30%, and a considerable back support is guaranteed.
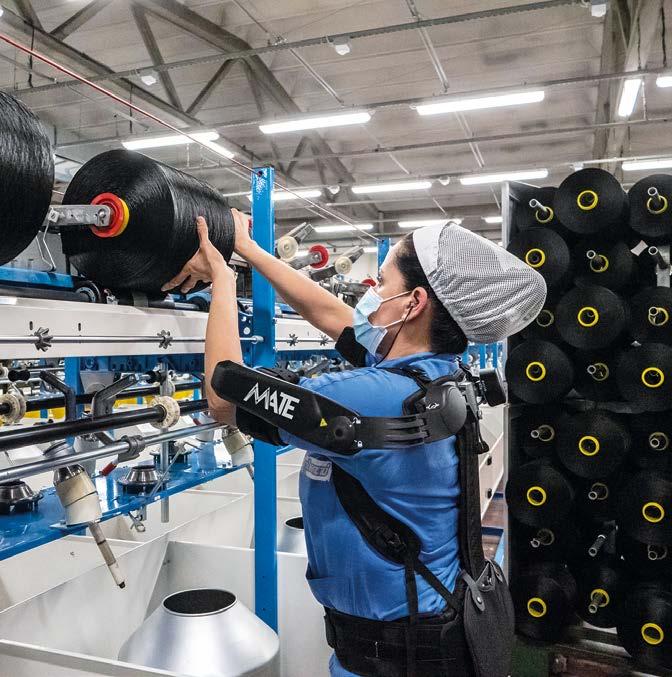
Certified, measurable physical wellbeing of coating operators
MATE-XT is currently the only exoskeleton available on the market to be included in the ergonomic risk evaluation index of EAWS (Ergonomic Assessment Work-Sheet) issued by the Ergo Foundation, which attests to a system’s ability to reduce biomechanical loads while carrying out particularly demanding work. More than half of the workers who wore this exoskeleton said that they felt a much lower level of exertion – the muscular activity of shoulders decreased by 30%, and a considerable back support is guaranteed – which led to positive improvements in the quality of their working day.
Improved efficiency: a positive side effect
In addition to the health benefits for workers, Comau’s new product also reduces the risk of painting defects due to operator fatigue. In fact, from an operational point of view, MATE-XT promotes higher precision, quality, and performance. Customers can easily calculate their return on investment (ROI) through measurable ergonomic performance factors. Comau itself carried out studies with its customers using the EAWS calculation method and it found that its MATE-XT exoskeleton can help to increase work precision during activities involving continuous arm lifting by 27% and speed of execution by 10%. Moreover, cycle times are reduced by at least 5%. Resistant to water, dust, ultraviolet rays, and high temperatures, MATE-XT is particularly suitable for industrial, non-industrial, and outdoor use in finishing and coating operations, but also for carpentry, construction, agriculture, assembly, and logistics applications.