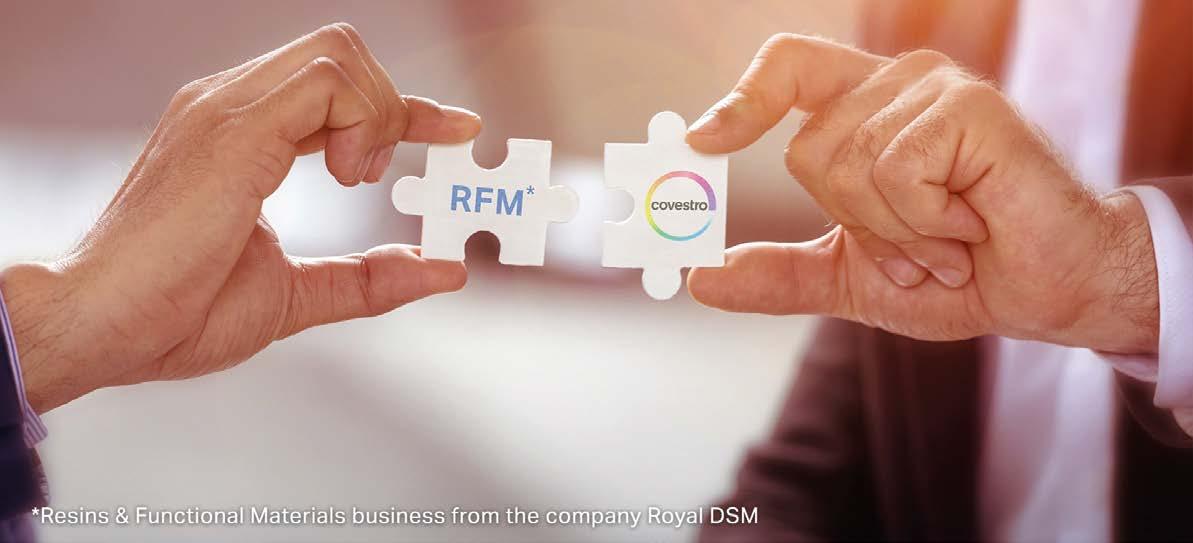
7 minute read
BRAND NEW
Covestro ha completato con successo l’acquisizione della divisione Resine & Materiali Funzionali (RMF) dell’azienda olandese Royal DSM.
Con lo scopo di diventare uno dei leader globali tra i fornitori di resine sostenibili per rivestimenti e di espandere ulteriormente la propria gamma, Covestro ha acquisito la divisione Resine & Materiali Funzionali di DSM. La transazione ha ricevuto l’approvazione delle autorità dopo che Covestro e DSM hanno firmato un accordo di acquisizione alla fine di settembre 2020. L’integrazione della divisione RMF porterà i ricavi del Gruppo a circa un miliardo di euro e aggiungerà più di 20 nuovi siti alla sua rete produttiva mondiale. “L’acquisizione di questo business contribuisce in modo significativo all’implementazione della nostra nuova strategia di gruppo. Con questa transazione facciamo un altro importante passo verso la sostenibilità, generando allo stesso tempo una crescita sostenibile”, ha affermato il Dr. Markus Steilemann, CEO di Covestro. “Non vediamo l’ora di incontrare i nuovi colleghi e di dargli il benvenuto in Covestro”. Con questa acquisizione Covestro aggiunge al suo portfolio una gamma completa di resine poliacriliche ad acqua, nonché marchi forti in termini di sostenibilità come Niaga®, soluzioni per la manifattura additiva e un innovativo business di rivestimenti solari. Covestro sta inoltre potenziando il suo portfolio includendo tecnologie ibride ad acqua, resine per rivestimenti in polvere, nonché resine a polimerizzazione con radiazioni. “Con questa transazione rafforziamo il nostro portfolio con prodotti e tecnologie ancora più innovativi, che ci permetteranno di soddisfare le esigenze dei nostri clienti in modo ottimale. Adesso il nostro focus è integrare i team, sfruttare i talenti e offrire il miglior supporto possibile ai clienti nuovi ed esistenti”, aggiunge Sucheta Govil, Chief Commercial Officer di Covestro. A seguito di un’analisi completa, Covestro prevede che gli effetti sinergici permanenti (il “run rate”) aumenteranno fino a circa 120 milioni all’anno, dalla piena integrazione fino al 2025. Questi consistono in circa i due terzi dei costi e un terzo dei ricavi derivanti dalle sinergie.
Per maggiori informazioni: www.covestro.com e www.dsm.com
© Covestro
La nuova cabina C-Expert è progettata per la verniciatura a polvere di profili con geometrie complesse ed è perfettamente integrata con il nuovo sistema di visione SAT VISI-1 per la verniciatura automatica dei profili.


SAT ha lanciato la nuova cabina di verniciatura a polvere C-Expert progettata specificamente per verniciare in modo efficiente ed uniforme profili con geometrie complesse, anche a velocità elevate. A causa del peso medio crescente dei profili e della complessità della geometria nel settore dell’architettura, spesso le aziende sono costrette a variare la velocità del trasportatore sulla linea verticale. La nuova cabina invece consente di mantenere una velocità costante. Questo implica una maggiore capacità produttiva e una notevole riduzione degli scarti. C-Expert è inoltre perfettamente integrata con il nuovo sistema di visione SAT VISI-1 per la verniciatura automatica dei profili, consentendo la ripetibilità dei risultati ed efficienza di verniciatura. “Siamo convinti che questa cabina rappresenti un vero e proprio game-changer per mercati esigenti e di fascia alta. È senza dubbio la miglior cabina di verniciatura progettata da SAT” ha detto Andrea Trevisan, CEO di SAT.

Per maggiori informazioni: https://c-expert.com e www.sataluminium.com
© SAT
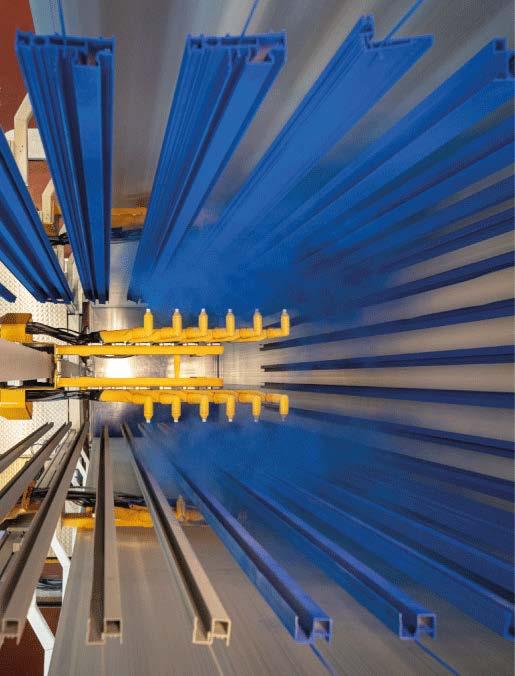
FOR . .TEC SRL
Senza titolo-5 1 22/01/2014 12:08:51
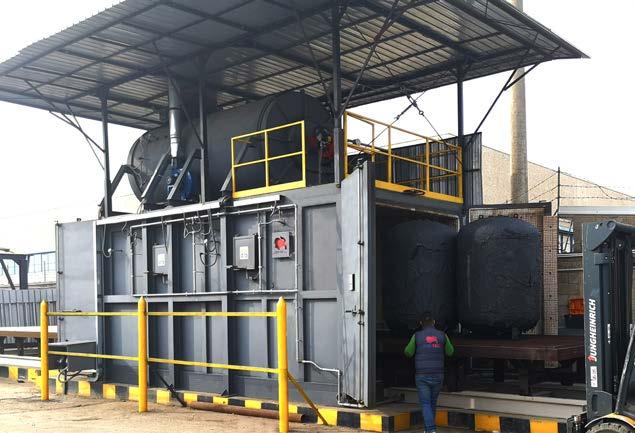
PAINT STRIPPING OVENS
Forni pirolitici per termosverniciatura e...
Sverniciatura bilancelle
Hooks paint stripping
Sverniciatura serbatoi gas Gas tanks paint stripping Rigenerazione motori elettrici
Electric motors regeneration Pulizia estrusori
Extruders cleaning Restauro carrozzerie
Body work restoration
Vedere oltre l’ordinario: finiture esclusive e sempre più personalizzate per gli occhiali Raleri
Intervista con Francesco Rambaldi, CEO di Raleri Srl
Dal motor sport fino agli occhiali da sole e da vista: l’evoluzione dei prodotti Raleri passa attraverso lo sviluppo di soluzioni sempre più originali e personalizzate, ottenute tramite stampa 3D e l’utilizzo di tecnologie di finitura innovative.
Raleri è nata nel settore eyewear per lo sviluppo di un prodotto specifico: una visiera oscurante per motociclisti. Può descriverci brevemente quale idea ha dato il via a questo progetto e come la vostra azienda si è evoluta per raggiungere le competenze tecnologiche che attualmente la caratterizzano?
L’idea è nata dalla mia passione per le moto unita alle esperienze lavorative acquisite nel settore della tecnologia e dell’informatica, in particolare. Già agli inizi degli anni ‘90 lo studio di progettazione da me fondato si fece notare per le abilità nella modellazione 3D di turbine per aziende energetiche Italiane di respiro internazionale. In quegli anni nacque l’idea di poter indossare un casco che avesse una visiera elettro oscurante automatica che avrebbe reso molto più sicuro e decisamente più piacevole la guida della motocicletta. I molti viaggi all’estero intrapresi per cercare produttori e fornitori di LCD e componenti elettronici che si combinassero con questo progetto mi ha portato a fare esperienze in Paesi come il Giappone e gli USA, notoriamente all’apice nell’impiego della tecnologia. Infine, lo studio relativo al segmento ottico per poter disporre del miglior prodotto sul mercato mi ha portato ad acquisire profonde conoscenze per realizzare prodotti di altissima qualità come le lenti per le maschere sportive o gli occhiali, nonché le strutture portanti delle lenti stesse.
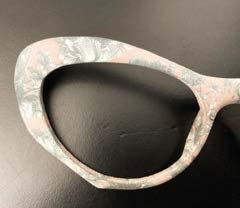
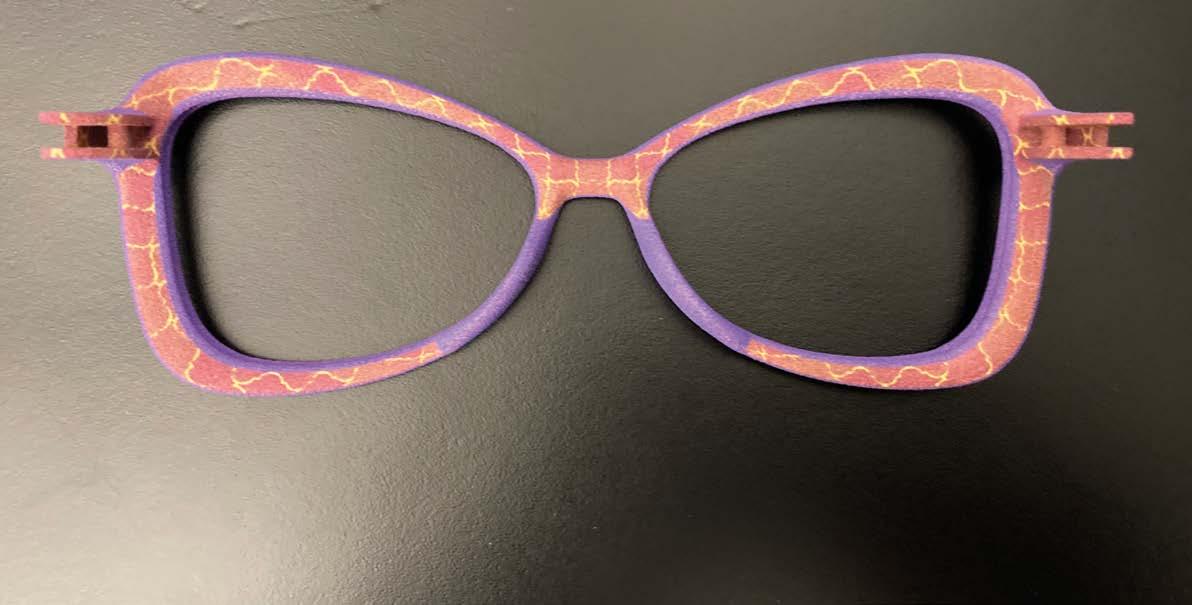
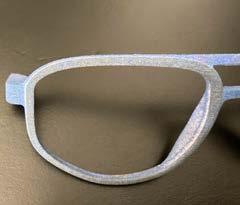
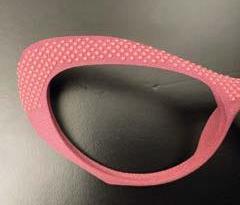
© Raleri
La gamma Raleri include oggi prodotti destinati a settori diversi, dallo sport al fashion. Potrebbe descriverci il ciclo produttivo standard?
In Raleri lavorano diverse persone con esperienze e competenze verticali che vanno dalla progettazione 3D all’I.T., dal marketing allo sviluppo del prodotto, unite dalla passione per gli sport estremi come l’alpinismo, il paracadutismo ed ovviamente i motor sport, dove possiamo testare personalmente i nostri prodotti, che poi saranno sia venduti a marchio Raleri sia realizzati in private label per brand del settore. A seconda che il progetto parta da un briefing con un cliente o da una nostra idea, saranno sempre coinvolte delle figure professionali che si occuperanno dei diversi aspetti del ciclo produttivo come il disegno, la modellazione 3D, la prototipazione per l’approvazione del modello finale fino all’industrializzazione vera e propria, che può essere fatta all’interno dei nostri stabilimenti produttivi in Italia o presso quelli del cliente. Raleri si prenderà cura di seguire tutto il ciclo produttivo fino alla consegna del prodotto finale o la messa a punto della produzione negli stabilimenti del cliente finale.
Che importanza rivestono i trattamenti superficiali dei vostri prodotti, dal lavaggio alla finitura?
I trattamenti superficiali come il lavaggio e la finitura nei prodotti stampati con tecnologia 3D sono passaggi molto delicati, ma al contempo essenziali per poter offrire un prodotto di qualità superiore e con delle finiture il più possibile personalizzate. Ad oggi riteniamo di poter offrire delle lavorazioni uniche sui nostri prodotti come ad esempio la pulitura ad ultrasuoni o micro-blasting, il deep coating per ottenere un effetto colore diverso da quello offerto dalla stampante, il vibro-finishing ed il semi-gloss finishing per avere risultati unici sulle superfici trattate che al tatto possono ricordare il legno invecchiato, la pietra pomice vulcanica o ancora la delicatezza del soft touch.
Recentemente avete introdotto una nuova tecnologia per la realizzazione di occhiali dalle finiture complesse: la stampa 3D. Quale motivo vi ha spinto a questa integrazione?
Le infinite potenzialità nella realizzazione di pezzi unici personalizzabili sono stati gli ingredienti di base che ci hanno spinto ad utilizzare la stampa 3D anche per le montature degli occhiali. Le finiture poi sono state studiate appositamente per questo prodotto per renderlo distinguibile ed unico.
Contrariamente a quanto avviene nei processi di stampa 3D comunemente diffusi, Raleri stampa i propri occhiali direttamente a colori. Può spiegarci nel dettaglio come si svolge questo processo e quali trattamenti superficiali successivi sono necessari?
Utilizziamo la nuovissima HP MJF 580 che permette di stampare già a colori e questo rende il tutto più veloce. L’accortezza è tutta nella creazione del job di stampa per conferire al prodotto finale performance ottimali in termini di resistenza. I trattamenti fisico-chimici sono svariati e, come accennato sopra, differiscono a seconda del tipo di effetto che vogliamo realizzare.
Che futuro pensa potrà avere questa nuova tecnologia di stampa e come si evolveranno i trattamenti superficiali dei vostri prodotti in rapporto ad essa?
Senza ombra di dubbio la stampa 3D è il futuro per quanto concerne la realizzazione di prodotti personalizzati. In particolare cambiano le necessità dei clienti che vogliono ottenere prodotti a partire da modelli realizzati in digitale. L’impatto della stampa 3D professionale è evidente invece sui processi produttivi per la realizzazione di prototipi, ma anche sulla logistica integrata perché permette di produrre pochi pezzi in tempi brevissimi e ad un costo accettabile se confrontato con le opzioni sul mercato industriale. Per tutti quindi, la stampa 3D presenta vantaggi evidenti rispetto ai metodi di produzione convenzionali, poiché́ permette di trasformare un’idea in un prodotto finito partendo da un disegno realizzato sul computer di casa o dell’ufficio.
Per maggiori informazioni: www.raleri.com
