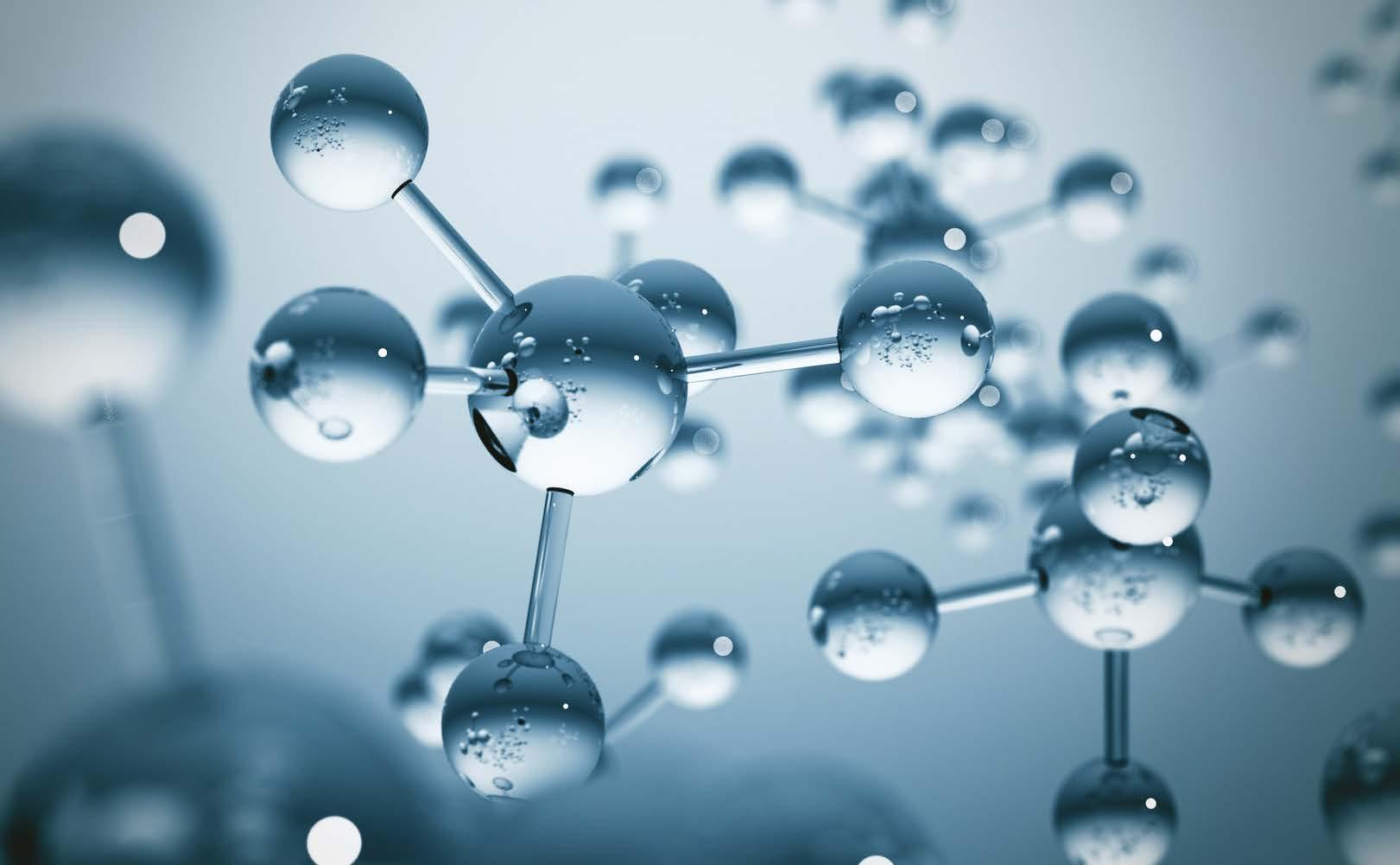
24 minute read
BRAND NEW
Richiedi la versione in italiano a info@ipcm.it This is 2022. The Omicron variant (hopefully) seems to be leading the SARS-CoV-2 infection towards the transition from pandemic to endemic. The industry has rebounded with growth figures well above expectations, in some Euro area countries. This is proven by the partial cut of the European Recovery Funds earmarked for nations with real growth trends above the 2020 forecasts, including Italy. The year 2021 ended with a more negative sentiment than December 2020. Perhaps, our exhaustion for a situation that has brought the extraordinary into the ordinary of our lives, as well as the spread of yet another variant of the virus towards the end of the year, made us end 2021 with the gloomiest thoughts, overshadowing all the good things that the past year gave us. One of them was certainly unexpected economic growth, although not homogeneous across Europe and despite still having to deal with the raw materials crisis and out-of-control energy tariffs, an emergency only partly linked to the management of the pandemic crisis. Undoubtedly, these crises have led to profound changes in the value chain, in supply methods and, in general, in the economic scenario of the next five years. Although it was already underway before the pandemic, another transformation has received a major boost from it: digital transformation, which has had a major impact on the information and publishing world. I do not often use this space on ipcm® to talk about topics related to the magazine itself, but please allow me to take you through this first issue of the year by sharing a few thoughts with you, because the way the world of information is being shaped will also have a major impact on technical and industrial magazines. According to analysts, within twenty years journalistic information will be distributed exclusively online, thus completing its transition to the digital form. It is undeniable that this is also the future of technical information. However, because of its specificity and, above all, because it is less about current affairs and more about in-depth information, with a value that is maintained for a much longer time than journalistic information, readers’ loyalty to print media is still high – not only among the Boomers but also among the Gen Xers, that is, the current company managers. The next few years will certainly see a profound transformation of editorial offices. Already today, ipcm® is a digital magazine more than a printed one: its digital circulation through the web, newsletters, and social media is at least five times higher than in print. The future of publishing and information, however, cannot be reduced to a battle between digital and paper, new and old: the real battle lies in the quality of content, in knowing how to attract readers and build their loyalty, in continuing to be an authoritative source of information, both digital and traditional. Regardless of whether you are “team paper” or “team digital”, this January issue will be distributed, together with the following March issue, at the world’s most important trade fair for the industrial coating sector: PaintExpo 2022, which is making a comeback after an absence of four years. Everything is ready for this event (of which ipcm® has been the media partner and exclusive representative for Italy, Spain, and Portugal since 2010) to be a success: the number of exhibitors has already exceeded 400, 90% of the exhibition space has been reserved, and hundreds of visitors have already pre-registered. ipcm® is going to be waiting for you there as well, and this January/February issue already gives you a preview of the industrial excellence and innovative products you are going to find.
Alessia Venturi
Editor-in-chief Direttore Responsabile
2021 in review
2021 has been an unusual year, more difficult than the previous one at times. Fortunately, the industry never stopped and so did the ipcm® team. Let’s retrace our 2021 together.
2021 bas been another anomalous year, like the previous one. However, despite the difficulties, something has improved: we have started traveling again (albeit only in Europe) to meet our clients and write reports; we took part in fairs and events (albeit to a limited extent compared to past years); and we started hosting ipcm® Academy students in presence in our classrooms (when it was possible). Despite these limitations, which still belong to a new and different normality that nobody wants to get used to, the work for the ipcm® editorial team has continued and in 2021 we have launched several new features. First there is our new website, launched online on March 1st. Available in different 5 languages, the site features a new graphic design, an improved user experience, a responsive layout that has optimised mobile navigation, new features and new tools for companies interested in promoting their brand and their products. Since last September, the site also hosts the official ipcm® blog: Surface Treatment 101. Currently available in English and Italian, the articles published in this new space aim to help those taking their first steps into the world of surface treatment to gain a better understanding of the processes and technologies involved in it. Compared to past years, we have also changed course on our social media pages, presenting new original contents that aim to inform the sector about the various technologies and processes. It has been a year of running-in that helped us understand how and where to improve and study the new strategy that will accompany our followers during 2022. As for printed magazines, the issues continue to become more and more rich in content.
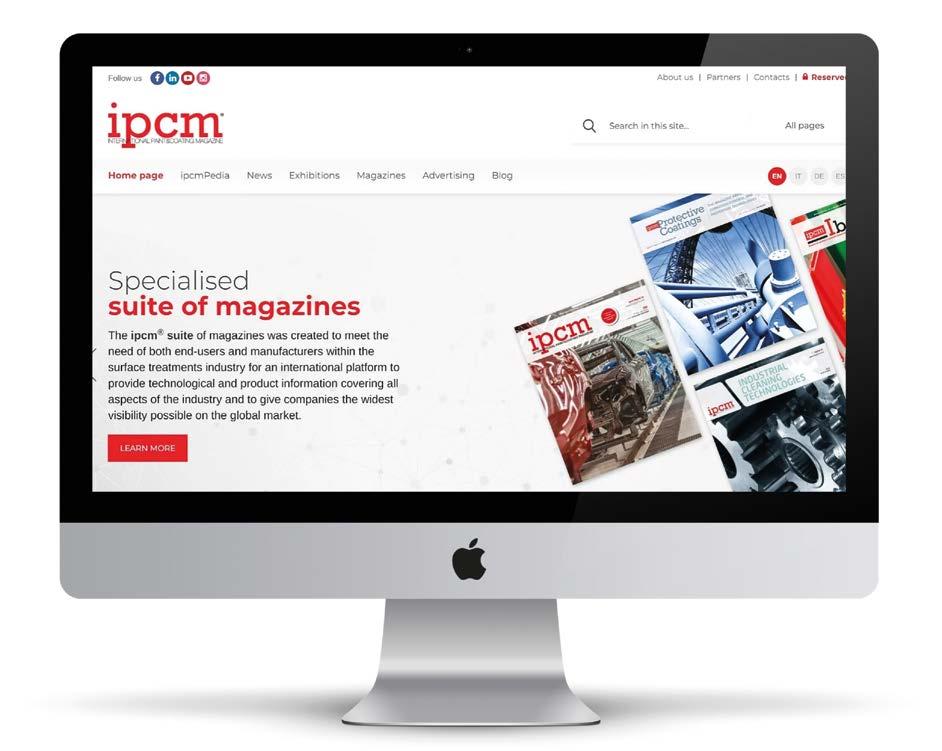
To this end, two new sections were added during the year: How It’s Coated, inspired by the well-known television programme “How it’s made” and aimed at describing the production cycle and the coating phase of particular products, and The Marketing Corner, a section dedicated to in-depth articles, trends and best practices on marketing and corporate communication edited by eos mktg&communication, which – in addition to being the publisher of ipcm® magazines – offers marketing, communication, graphic design and event-planning services. Our magazines have also leveraged the digital wave to provide readers with a broader and more interactive reading experience. In this regard, we have integrated a QR code in the pages of the magazines, in order to enrich the issues of ipcm® with multimedia content, in-depth video interviews, product demos, applications and much more. In addition, since the first issue of 2021, all digital editions have been equipped with an interactive index that facilitate reading, giving users the ability to click on the title of any article in the index and be sent directly to the page of interest. Despite the limitations related to the health emergency, the five ipcm® magazines were distributed throughout the year at the main trade fairs and conferences of the sector. 2021 has been also the year in which the course of ipcm® Academy, the branch dedicated to professional training, resumed at full capacity with over 20 participants. The lecturers have been busy for a long time defining the new training programme for 2022, that presents several innovations. First of all, the addition of a new section dedicated to the coating of plastic materials: a recent and still niche topic in the world of painting, regarding a highly specialized sector with limited dissemination of technical skills. It will offer an overview of the market and insights into thermoplastics, thermosets, painting cycles, main suppliers, characteristics of the systems, cleaning, pre-treatment, application, curing, environmental impact and control solutions. The complete programme is available at the following link (https://ipcmacademy.com/programmaformativo/) Last, but not least: the arrival of a new colleague, Falkor, a Miniature Schnauzer puppy who will soon turn one year old.
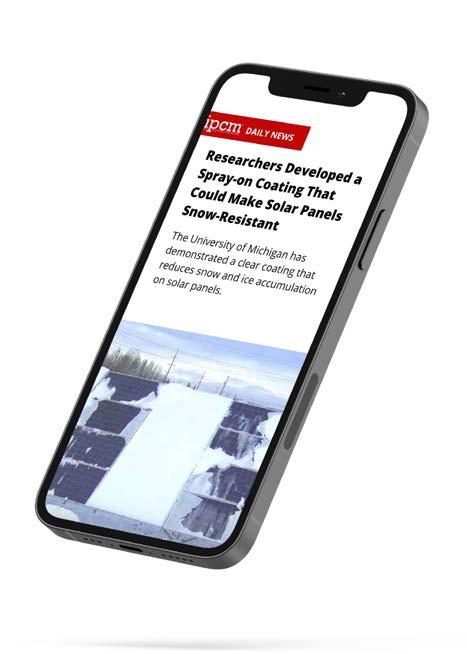
At work for 2022
In addition to the ipcm® Academy training courses, one of the activities that will most engage the ipcm® team is PaintExpo, the world’s leading trade fair dedicated to coating technologies, which will be held from 26 to 29 April 2022 in Karlsruhe, Germany. eos mktg & communication, as the official agency of the fair, will support companies in the pre-event organisation and give the opportunity to exploit the magazines as an effective communication tool for the promotion of their services and products. Besides PaintExpo 2022, we plan to participate in numerous other trade fairs and events that will allow us to further expand the presence of our magazines globally.
Battling Myocardial Infarction with Drug-coated Balloon Catheters
Roman Möhlmann
Fraunhofer-Gesellschaft - München, Germany presse@zv.fraunhofer.de
Fraunhofer researchers are developing an automated coating machine to better treat coronary heart diseases.
In Germany, nearly 6 million people suffer from coronary heart disease. The disease is caused by calcium deposits which constrict the coronary arteries. Doctors generally use a stent to widen the narrow pathway. However, the blood vessel often constricts further, thus necessitating further interventions. For this reason, a drug-coated balloon catheter inserted in minimally invasive cardiac surgery is increasingly serving as a replacement for the risky stent treatment. In current practice, the balloons are often coated manually. A new device is intended to automate this timeconsuming procedure. Along with partner companies, a team from the Fraunhofer Institute for Production Systems and Design Technology IPK is developing a prototype of such a device. Shortness of breath and acute chest pain can be signs of coronary heart disease (CHD). If left untreated, this can lead to severe consequences, including myocardial infarction. Caused by calcium deposits on the inner linings of the arteries, CHD is a leading cause of death among adults. This build-up causes blockage in the veins, and the heart no longer receives a sufficient supply of oxygen. Doctors thus widen the constricted pathways to allow the blood to once more have unrestricted flow. To achieve this, they insert a balloon catheter with a plastic support, i.e. a “stent”, into the constricted artery. When the balloon catheter is inflated, the stent expands, thus expanding the stenosis. The problem is that over the course of a few months, the tissue around the stent can grow back into the blood vessel. This leads to further constriction called restenosis. This risk has increasingly led doctors to favour an alternative procedure whereby no foreign objects are left in the damaged arteries: balloon catheters coated with immunosuppressors and cytostatic drugs are expanded and cause the vessel to dilate mechanically. The active substances that are thus injected into the vessel can inhibit restenosis, i.e. the increased growth of the tissue cells due to the mechanical stress, keeping the vessel from closing back up. The
© BVMED © InnoRA GmbH

Optical inspection of a balloon catheter and a stent on a drug-coated balloon catheter.

substances are conveyed via the surface of the balloon directly onto and into the artery walls. At present, the coating of the catheters with drugs – especially with particularly advanced ones – is often performed manually by skilled workers. This process is time consuming and error prone. The procedure is very specific, and specialists with appropriate expertise are few and far between.
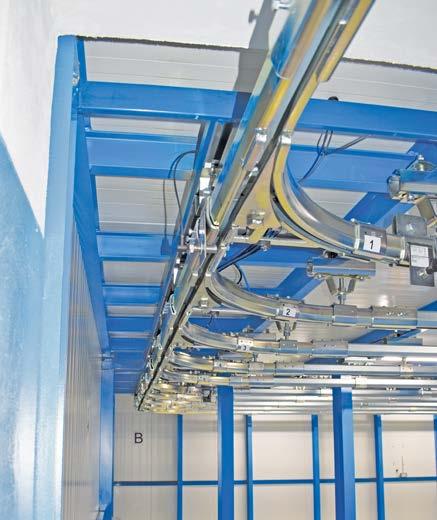
Process security via automation
For this reason, a team at Fraunhofer IPK is researching how the laborious process of coating balloon catheters could be automated. In the joint project “Heliko – Automated and process-safe coating of balloon catheters with active substances” funded by the German Federal Ministry of Education and Research (BMBF), an automated coating machine prototype is being developed. The scientists are closely cooperating with InnoRa GmbH, a spin-off of Berlin’s Charité, and Organical CAD/CAM GmbH. InnoRa has developed and patented numerous coating procedures, Organical is developing the machine system for the automated coating system in order to enable serial production of the balloon catheters. The objective of the project is to reduce the reject rate, significantly increase the sales volume of balloons and guarantee process safety. This is no trivial task, as the microscopic crystals of the medication ideally need to point outward in the same direction. This is the only way that the active substance can penetrate the cell walls quickly and effectively. The thickness of the coating and the composition of the coating surface play key roles in the success of the process. “The balloon catheters must convey the medication immediately into the artery wall. This process must not take any longer than one minute in order to keep the heart’s supply of oxygen from being interrupted for too much time. For this reason, the surface may not be too smooth: a vectored conformation of the crystals ensures more optimal transfer of the active substance,” says Gregor Dürre, researcher at Fraunhofer IPK. At the same time, the desired structure of the crystals results in the medication having a prolonged effect in the artery wall. Once the drug has been released, the balloon catheter is deflated and then removed.
Fragile membrane – difficult coating process
Numerous factors such as kinematics, amount of pressure applied, coating speed, coating duration and speed of rotation impact the crystal structure and thus the construction of the automatic coating machine. “The catheter balloon is a fragile and exceptionally thin membrane that needs to be coated in its expanded state. That is incredibly difficult. The slightest of mistakes can lead to tears in the membranes that are only 20–80 micrometres thick,” says Annika Brehmer, biotechnology specialist and colleague of Gregor Dürre. The construction of the coating unit is equally challenging, a task with which the Fraunhofer IPK has been charged. In order to achieve the desired conformation for the crystallization of the solution on the balloon membrane, the crystallization conditions must be precisely controlled during the coating process. For this purpose, there are two motors which rotate the filament on which the balloon is stretched to ensure that it is evenly coated. The coating head is positioned in relation to the balloon membrane. The coating process then takes place in sequential fashion with the balloon rotating and the coating head simultaneously being shifted from one strip to another. An integrated, high-resolution optical surface measurement device takes over for the quality control by constantly measuring the coating thickness. The coating procedure typically takes between three to five minutes. The throughput can be drastically increased in comparison to the manual procedure – not to mention the added benefits of process safety and the quality control with the measuring device. Researchers are currently working on optimizing the prototype. At a later point in time, the effectiveness of the balloons will be tested in in vivo studies. The automated coating machine should be marketready in early 2023.
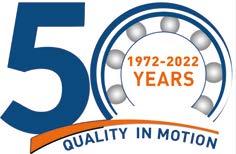
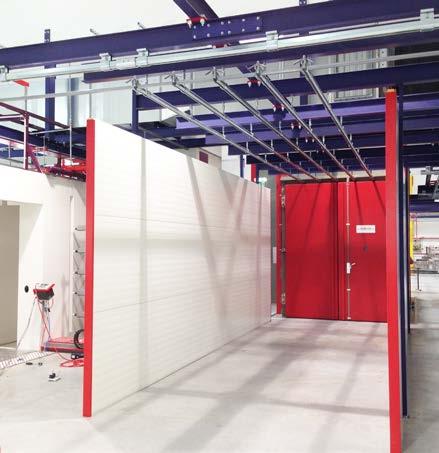
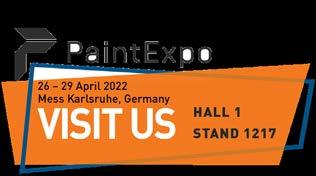
Illini Solar Car Scores Great Placement Thanks to AERO Sustainable Material Technology
The Illini Solar Car team managed to obtain a great placement at the American Solar Challenge thanks to AERO’s innovative film-based coating technology.
AERO Sustainable Material Technology’s partnership with the Illini Solar Car program at the University of Illinois Urbana-Champaign has helped catapult the Illini Solar Car team to success in the American Solar Challenge. AERO’s solution is a film-based coating technology composed of an ultra-durable, self-healing urethane film, colour, and adhesive, in a single-stage, which makes it an easy to apply, 100% recyclable material. “As a result of AERO’s contributions, our team had the best finish ever in this summer’s American Solar Challenge with our SOV car Brizo finishing 3rd at the track qualifier race and 4th during the main road race,” said Hongbo Yuan, mechanical lead on Illini Solar Car. “Besides AERO allowing us to ’dress up‘ our car, the durable film safeguarded the carbon fiber body of the car from degradation. The AERO lightweight film allowed us to coat and decorate the car without heavy spray paint, and the film itself was much easier to apply compared to spray painting. With AERO’s support, we are optimistic for the future as we continue toward our goal of becoming a world-renowned team whilst forwarding progress in sustainable energy.” AERO’s coatings technology finds wide application in the automotive, marine, motorsports, wind energy, and architectural industries. In such sectors, where enhancements in durability, aesthetic value, and environmental sustainability are all competitive differentiators, AERO is paving the way by offering a material finish which compromises neither product nor planet. Moreover, the Illini Solar Car sponsorship reflects the company’s dedication to environmental sustainability and “paying it forward” to future chemists and engineers. “We were excited to work on Brizo with the Illini team for the American Solar Challenge” said Jim McGuire, CEO of AERO Sustainable Material Technology, Inc. “AERO lives at the crossroads of environmental sustainability and performance, without compromise on either attribute. The team both developed and successfully demonstrated the capability of sustainable performance, while also completing their university studies! This kind of future-forward thinking in environmentally sustainable products is exactly what drives AERO, so we’re extremely enthusiastic for what the future generation will bring this industry.”
For further information: www.sustainablematerialtechnology.com and www.illinisolarcar.com

© AERO
aap Implantate AG announced the beginning of the human clinical study for its antibacterial silver coating technology for application on anatomical plates and screws for fracture treatment.
© aap Implantate AG
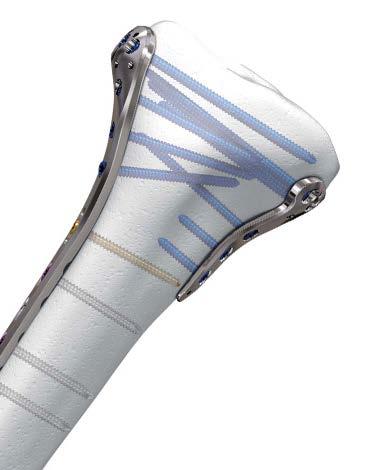
aap announced the launch of the world’s first human clinical study for antibacterial silver coating technology on anatomical plates and screws for fracture treatment. The University Hospital in Regensburg is the first trial centre which was equipped with the study materials and trained to perform surgeries with aap’s silver coated implants. This achievement, which represents another milestone on the way to get CE approval, makes aap the first company to test an antibacterial silver coating on anatomical plates and screws for fracture treatment as part of a study of this kind. The aim of the study
With its antibacterial silver coating technology, aap aims at solving one of the greatest challenges in traumatology: the reduction of surgical site infections (SSI), which represent a major burden both for the patients concerned and for global healthcare systems. One of the causes of SSI is antibiotic-resistant bacteria. In its annual report on the state of research to overcome antibiotic resistance, the WHO recently found that some of the world’s most dangerous bacteria have developed resistance to known drugs1 . Moreover, according to the WHO, almost all antibiotics currently in development work little better than existing drugs. aap’s antibacterial silver coating technology represents an alternative solution in the fight against bacterial infections that is not based on antibiotics and therefore offers enormous market potential. As a platform technology, the technology has a broad range of applications and can be used not only in traumatology but also in other areas of orthopaedics as well as in cardiology, dentistry, or medical instruments.
For further information: www.aap.de
1 2020 Antibacterial agents in clinical and preclinical development: an overview and analysis. Geneva: World Health Organization; 2021.

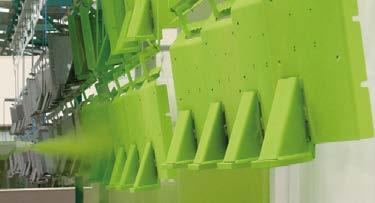

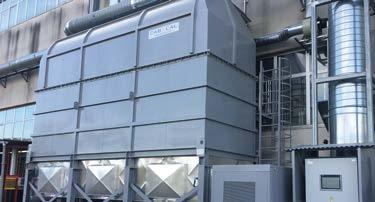

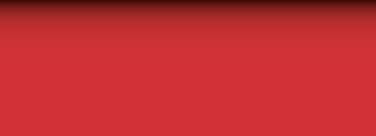
Airbus To Seek an Independent Legal Assessment After Dispute with Qatar Airways Over Surface Degradation
Following the on-going dispute between Airbus and Qatar Airways over the surface degradation on the air carrier’s fleet of A350 aircrafts, Airbus announced that the company is preparing for an independent legal assessment.
Airbus has addressed the © Airbus on-going controversy with Qatar Airways over the paint degradation of the airline’s fleet of A350 jetliners with a rare statement in which the company announced an independent legal assessment to resolve the dispute, as the two parties have been unable to settle during direct and open discussions. Qatar Airways declared that the surface degradation on its A350 aircrafts led to the grounding of 20 jets by its domestic aviation regulator. However, in its statement, Airbus pointed out that “the surface paint-related findings have been thoroughly assessed by Airbus and confirmed by the European Aviation Safety Agency (EASA) as having no airworthiness impact on the A350 fleet”. “The attempt by this customer to misrepresent this specific topic as an airworthiness issue represents a threat to the international protocols on safety matters”, continued Airbus. “While Airbus regrets the need to follow such a path, it has become necessary to defend its position and reputation. Airbus has worked actively with its customers in order to minimise the impact and any inconvenience caused by this in-service surface degradation on the aircraft. These solutions have all been dismissed by the above-mentioned customer without legitimate justification”. Airbus also stated that, in parallel, the company is working to reestablish a constructive dialogue with the customer on this matter but that it is not willing to accept “inaccurate statements of this kind to continue”. According to Reuters1, Airbus officials confirmed the statement referred to Qatar Airways. A spokesman for the airline said it would not comment
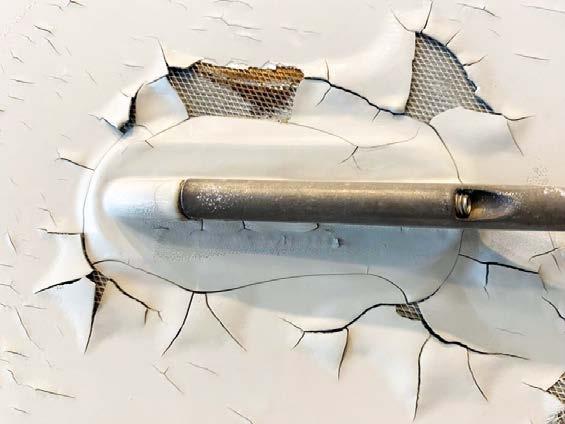
1 https://reut.rs/3yNldTU on the Airbus statement before reviewing it. The dispute between Airbus and Qatar Airways became public in May 2021, six months after Qatar Airways sent an A350 to be stripped and repainted in special livery for the FIFA World Cup, which will take place in Qatar this year. At first, this was presented as an isolated issue related to Qatar’s severe heat. However, according to a private maintenance message board used by Airbus and A350 operators and reviewed by Reuters, at least five other airlines had complained about paint or other skin flaws since late 2016. Reuters also published exclusive photographs that show exposed and corroded lightning protection beneath cracked paint.
Where the problem may stem from
When Airbus 15 years ago launched the A350, it chose to use carbonfibre instead of metal, making the jet lighters and thus reducing fuel consumptions. However, experts say these are harder to deck out in a way that makes paint stick. The new jets also need a layer of metallic mesh to dissipate lightning strikes because carbon-fibre is not conductive. Finally, unlike metal, carbon does not expand and shrink as temperatures change but paint does – a factor that can cause peeling over time.
For further information: www.airbus.com/en and www.qatarairways.com
AkzoNobel Launches the New Interpon W Range for Heat Sensitive Substrates
The new Interpon W powder coatings developed by AkzoNobel allow to provide consistent finish and protection to the most challenging substrates.
The coating producer AkzoNobel has recently launched Interpon W, a new range of powder coatings solutions that are particularly suitable for designers and manufactures dealing with heat sensitive substrates (HSS) such as wood and plastic. Interpon W powder coatings include the Interpon W Core, Flex Pro, Fast and Fast Pro products. Besides physical attraction and sustainability, the new series allows to provide a consistent finish and chemical, scratch, liquid and heat resistance even to the most challenging shapes and substrates, ranging from furniture, kitchen and bathroom products to building and construction materials. In addition, Interpon W Core and Interpon Flex Pro enables a lower thermal curing process that offers even higher weatherability and gloss retention for several applications, while Interpon W Fast and Interpon W Fast Pro combine low temperature curing range (between 80°C-120°C) with short curing time (2-5 minutes). The new products allow materials such as MDF/HDF, Plywood, OSB, Natural Wood, Gypsum Board/Plasterboard, Fibre cement and plastic composites to benefit from a powder coating that is free from Volatile Organic Compounds (VOCs) and have a high utilisation of material - up to 99% - with any overspray able to be recycled. “Through innovation and worldwide market development, we are creating solutions that are transforming the potential of low cure powder coatings, and taking sustainable solutions and business performance to new heights,” stated Daniela Vlad, the Managing Director of the Powder Coatings business line at AkzoNobel. “The ‘Safe and Easy’ process has been introduced to ease the transition to new technologies: we know that switching to new technologies may come with uncertainty, which is why our dedicated teams will support you in making a Safe and Easy choice for your business. In close cooperation with global network of powder coating line manufacturers, we will help you from start to finish in creating and implementing a fully-operational coating line. This includes understanding the products and processes required, and the financial benefits you can expect. It also includes supporting you with staff training and ensuring a smooth integration between the powder and coating line.” The Interpon W powder coatings were developed at the AkzoNobel’s Global Competence Center for powder on heat sensitive substrates in Como (Italy). The Interpon W range performance has also already been proven through partnerships with several Interpon customers in the company’s regional hubs and in close co-operation with other line manufacturers.
For further information: www.akzonobel.com
© AkzoNobel
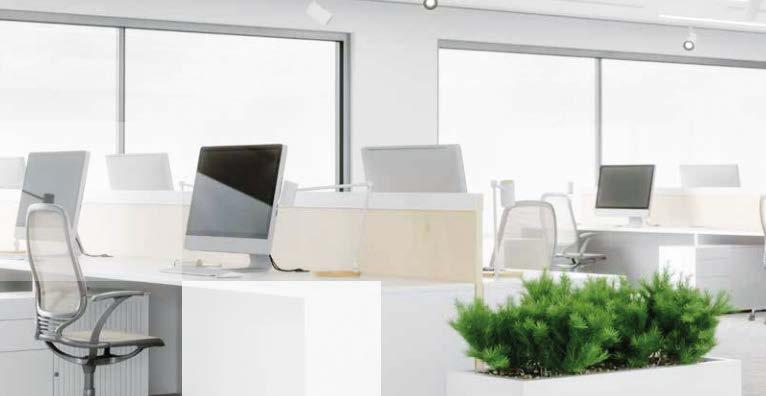
Pantone today unveiled its colour of the year 2022: Pantone® 17-3938 Very Peri, a periwinkle blue hue with a vivifying violet red undertone.
As per tradition, Pantone presented its colour of the year 2022. This year the choice fell on Pantone® 17-3938 Very Peri, a periwinkle blue with a vivifying violet red undertone. The colour of the year 2022 combines the fidelity and constancy of blue with the energy and excitement of red. Pantone 17-3938 Very Peri is characterized by light-hearted confidence and bold curiosity, helping us to embrace this altered landscape of possibilities, opening us up to a new vision as we rewrite our lives. Pantone 17-3938 Very Peri is a symbol of the global zeitgeist of the moment and the transition we are going through. As we emerge from an intense period of isolation, our notions and standards are changing and our physical and digital lives have merged in new ways. Digital design helps us extend the limits of reality, opening the door to a dynamic virtual world where we can explore and create new colour possibilities. Pantone® 17-3938 Very Peri illustrates the fusion of modern life and how colour trends in the digital world manifest themselves in the physical world and vice versa. “As we move into a world of unprecedented change, the selection of Pantone 17-3938 Very Peri brings a novel perspective and vision of the trusted and beloved blue colour family,” says Leatrice Eiseman, Executive Director, Pantone Color Institute. “Encompassing the qualities of the blues, yet at the same time possessing a violet-red undertone, Pantone 17-3938 Very Peri displays a spritely, joyous attitude and dynamic presence that encourages courageous creativity and imaginative expression.” “The Pantone Colour of the Year reflects what is taking place in our global culture, expressing what people are looking for that colour can hope to answer,” added Laurie Pressman, Vice President of the Pantone Color Institute. “Creating a new colour for the first time in the history of our Pantone Colour of the Year educational colour program reflects the global innovation and transformation taking place. As society continues to recognize colour as a critical form of communication and as a way to express and affect ideas and emotions and engage and connect, the complexity of this new red-violet-infused blue hue highlights the expansive possibilities that lie before us.”
For further information: www.pantone.com
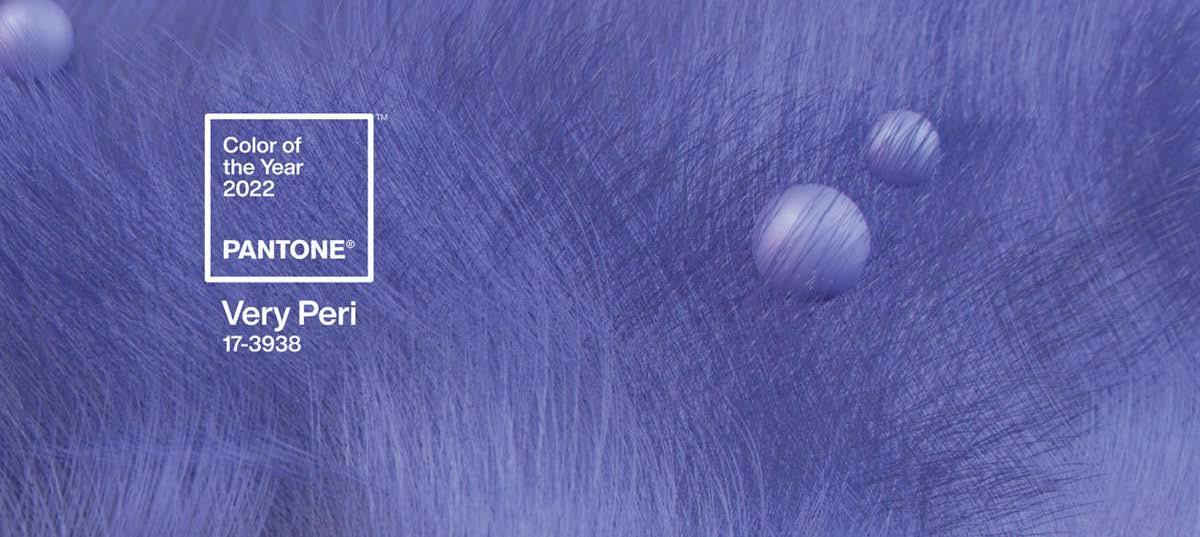
© Pantone
PPG Expands Its Automotive OEM Clearcoat Production in Germany

The €3 million investment allows PPG to increase operational efficiency, sustainability and flexibility.
PPG has recently announced the beginning of an expanded automotive OEM clearcoat production in its German facility at Erlenbach. The project, that required an investment of almost €3 million, nearly doubles the site’s capacity for premium clearcoats and employs advanced manufacturing technology in order to improve operational efficiency, sustainability and flexibility compared to conventional processes. PPG acquired the Erlenbach site from Hemmelrath in 2019 specifically to enhance its automotive coatings offering and add formulating and manufacturing capability. The facility uses a fully automated, innovative and highly sustainable production process that boasts shorter and faster manufacturing times and flexible manufacturing of multiple batch sizes of up to 25 metric tons. “This is an important investment that ensures we will continue to meet the growing regional demand for our premium clearcoats, which offer the world-class finish with superior appearance and durability that our customers demand. Using advanced manufacturing technology also gives us increased flexibility to produce different products in multiple batch sizes in the most sustainable way,” stated Roald Johannsen, PPG vice president for EMEA automotive OEM coatings. “This investment makes our Erlenbach facility a centre of excellence for clearcoats, using best-inclass technologies to deliver superior scratch- and chemical-resistant coatings that are highly durable. It will further strengthen our position as a leading manufacturer of the most advanced and innovative clearcoats that are capable of meeting or exceeding the most demanding OEM quality and performance specifications.”
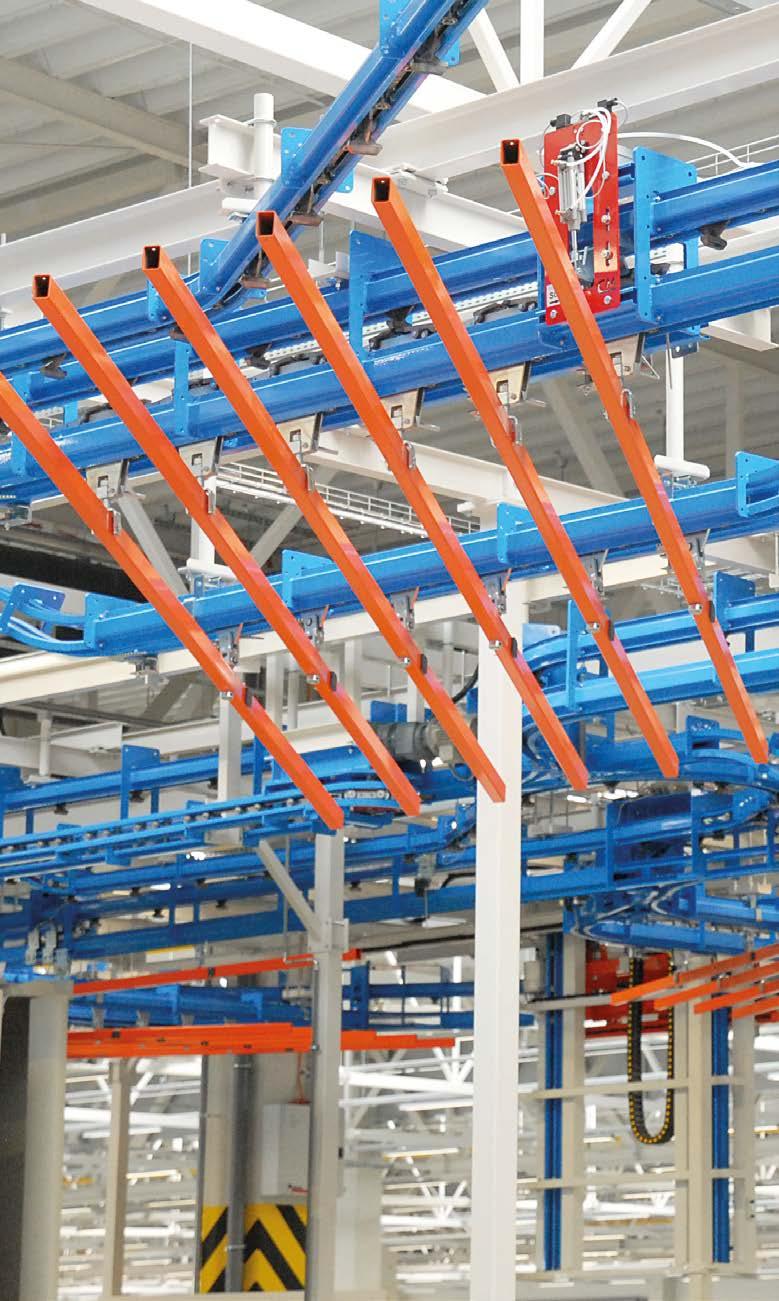