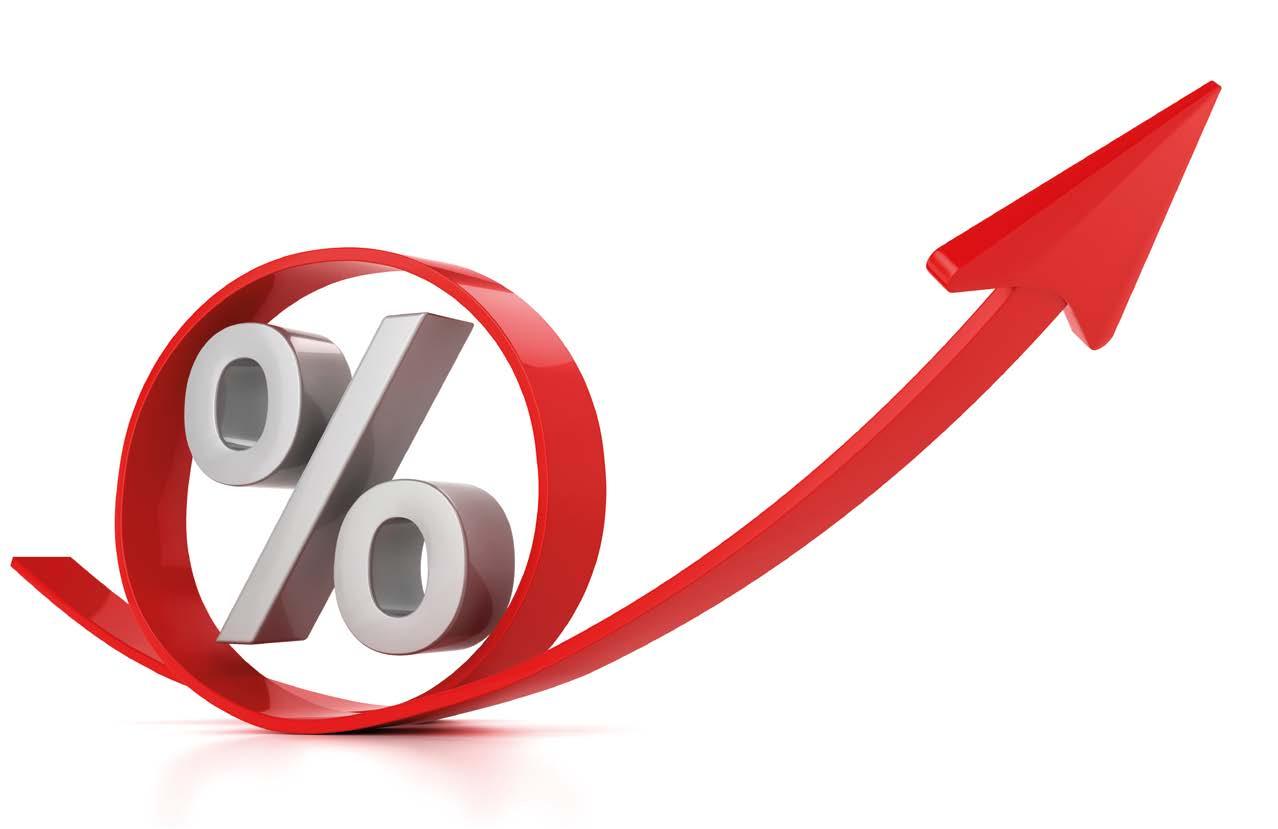
16 minute read
THE MARKETING CORNER
RAW MATERIALS
Rising Raw Material Costs: What Will Happen in 2022?
As an issue that is difficult to interpret and whose consequences do not seem easily foreseeable, the increase in the cost of raw materials and energy resources in 2021 is subverting the manufacturing industry as well as other sectors. The upswing in business activities following the stoppage due to the global health crisis has been so explosive and characterised by such exceptional demand for resources that it has created a short circuit in the supply chain, which has been added to the complications arising from export restrictions imposed by certain countries and to the Brexit, which has led to delays in European transport. Overseas, the situation in the United States was further complicated by winter storm Uri, which slowed down transport and shipments, leading to an exponential rise in prices at the very beginning of the economic recovery. The coating industry has suffered major repercussions, especially due to the sudden shortage of solvents, resins, and pigments, which are essential elements in the formulation of paint products. This has led to a surge in the cost of these key raw materials for the sector. Solvent costs, in particular, have risen by 200 to 300% compared with the previous year, as reported in the latest press release of the British Coating Federation, one of the most active trade associations in Europe. In order to provide a general overview of what can be expected in 2022, we have chosen to collect communications from some of the world’s
leading raw material companies, which have chosen to inform their customers about the rising costs of their products. Forecasts are not encouraging: leading experts predict that energy costs and oil costs in particular will remain stable, and therefore high, in 2022. What we hope is that the market will withstand the impact of this situation, whose future outlines are still so uncertain.
Archroma
Since 01 October 2021, Archroma has increased the prices of its products by up to 0.25 USD per kg. These adjustments were applied to all Archroma products globally. The increase was necessary to offset the ongoing exceptionally high freight and logistics costs. “Archroma made every effort to absorb these increases,” said Marcos Furrer, Chief Operating Officer at Archroma. “We have however reached a point where these adjustments were needed for us to be able to maintain our service levels.”
Axalta Coating Systems
In July 2021 Axalta announced that it would implement additional price increases across all of its global lines of business due to continued inflationary pressures. The increases were effective immediately or as permissible by contract. Since the beginning of 2021, the cost of raw materials used in the manufacturing of coatings has increased significantly, and non-raw material input costs, including freight, energy, and labour, continue to increase well beyond earlier expectations. Price adjustments varied depending on geographic region, products offered, and market(s) served. In some cases, increases may be greater where conditions necessitate additional adjustments. “Even with aggressive cost-control measures in place across our global supply chain, we’re encountering extraordinary cost and inflationary pressures,” said Sean Lannon, Axalta’s Chief Financial Officer. “These pressures have made it necessary to appropriately raise prices to help offset ongoing cost increases and ensure our ability to continue delivering exceptional support, innovative solutions, and best-in-class products to our customers.” Axalta will continue to drive operational excellence throughout the organization with the aim of minimizing the impact of cost and inflationary pressures. Axalta sales representatives communicate price increase details directly to customers for all affected products.
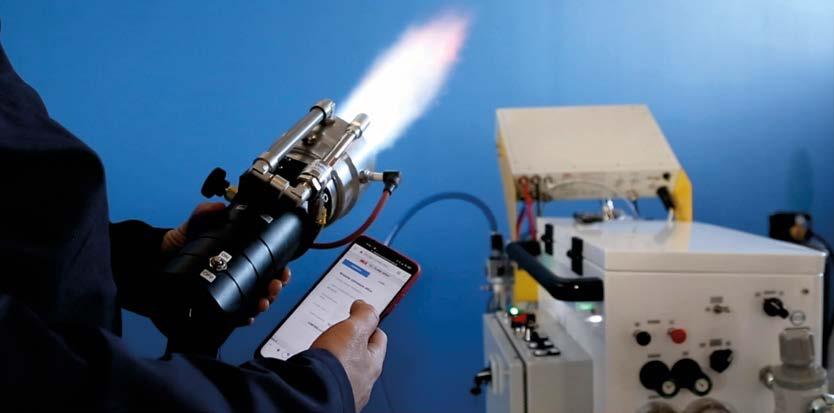
BASF
Since December 1 2021, BASF increased the prices of its additives for the paint and coatings industry globally: Attagel®, Dispex®, Efka® , Foamaster®, FoamStar®, Hydropalat®, Irgafos®, Irganox®, Loxanol® , Rheovis®, Sterocoll®, Tinuvin® and Uvinul® . The price increase was subject to the contract in force. To offset the rising costs of raw materials, transportation and energy, as well as other rising costs, including labour, packaging and maintenance, BASF raised prices by up to 35%. “The increases were necessary to continue to support our customers with high-level products and services”, said the company.
BYK Additives
Since January 1, 2022 the supplier of additives and measuring instruments BYK has increased the prices of its additives by 15%. The increase may vary depending on the cost situation. “This measure was necessary to keep BYK Additives’ level of service and innovation high for its customers in light of the rising costs of raw materials, transportation, packaging and energy”, said the company.
Clariant
Clariant raised the prices of all product lines in its Industrial & Consumer Care portfolio in the EMEA (Europe, Middle East and Africa) region in the range of 25-35%, with larger increases for individual products particularly affected by cost increases. These price adjustments result from major increases in the cost of essential raw materials, the cost of domestic and intercontinental transport, packaging and energy costs.
ECKART
ECKART, manufacturer of metallic effect and pearlescent pigments for various applications, has announced the price increase for its products since the beginning of the new year. The company has tried to minimize the impact of the continuing increases in the cost of raw materials and other supplies in recent months. However, the ongoing global cost inflation of raw materials, logistics, energy and packaging led to this decision: a price increase for products issued on or after January 1, 2022. “While never popular, these actions are necessary for ECKART to remain a responsible, quality supplier to the specialty chemical and coatings industries”, said the company.
LANXESS
The specialty chemicals company LANXESS has stated that it imposed temporary inflation surcharges for its range of inorganic pigments worldwide. The reason for this choice is due to the massive increase in energy costs for electricity, gas and steam. After a first increase at the beginning of September 2021, prices for iron oxide and chrome oxide pigments from all production sites rose in October by € 300 per metric ton, or the equivalent amount in the national currency. LANXESS individually informed its customers about the effects of this increase. The Inorganic Pigments business unit (IPG) of the company is a global manufacturer of synthetic iron oxides and inorganic chrome oxides. Its products have been used as colorants for building materials, paints and coatings, plastics, paper and other applications for many decades. All the inorganic pigments are produced according to strict sustainability criteria.
Sun Chemical
Sun Chemical has recently announced that it will increase the prices across the entire portfolio of packaging, commercial sheetfed and screen inks, coatings, consumables and adhesives in North America. The company will communicate specific increases directly with the clients. The company has declared that the price increase is caused by the unprecedented pace of inflationary cost movements that are still impacting raw materials and packaging components for the ink industry, as well as the sustained shortage of available labour and the supply and demand dynamics in both the global and regional logistics markets. “Sun Chemical’s priority throughout 2021 has been to keep our products flowing to our customers, allowing them to keep their facilities operating. We continue to leverage our global network to secure raw materials and needed services. However, the competition for these resources is significant and is driving costs higher and faster than we can overcome through efficiency programs. This requires us to raise prices to our customers so that we can continue to secure the needed inputs to make and deliver quality products,” stated Chris Parrilli, President of North American Inks.
Researchers Developed a Nanoscale Window Coating That Reduces Energy Costs
The nanoscale technology could elevate the thermal performance of single-pane windows to that of double-pane.
Researchers from the Penn State University have recently developed a nanoscale technology that could help to elevate the thermal performance of singlepane windows to that of double-pane windows in winter. By sandwiching a layer of insulating air, double-pane windows allow to improve energy efficiency over single-pane windows, although replacing them can be expensive or technically challenging. A more economical but less effective alternative would be to coat single-pane windows with translucent metallic films capable of absorbing some solar heat in winter without compromising clarity of the glass. However, the solution developed by the researchers may now improve the coating’s efficacy. “Near-infrared light — a portion of solar light that humans cannot see but can feel as heat — can activate unique light-to-heat effects on certain metallic nanoparticles, enhancing how heat flows inward through a window. We were interested in understanding how these effects could be helpful in saving energy in buildings, particularly during the winter season,” stated Julian Wang, associate professor of architectural engineering and affiliated with the College of Art and Architecture’s Department of Architecture and the Materials Research Institute at Penn State.
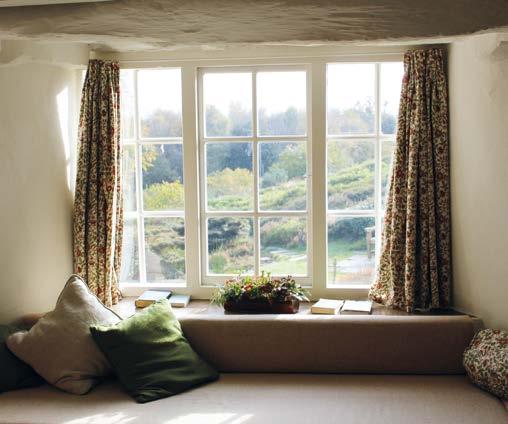
The study
The research team first developed a model to estimate how much heat from sunlight would be reflected, absorbed into or transferred through a window coated with metallic nanoparticles. They selected the photothermal compound because of its ability to absorb the sun’s near-infrared light while allowing for ample visible light transmission at the same time. The model predicted that the coating would reflect less near-infrared light or heat, absorbing more of it through the window than most of other coating types. Then, by testing a single-pane window coated with the nanoparticles under simulated sunlight in the laboratory, the researchers confirmed the predictions that had been made by the simulation: there was a significant rise in temperature on the side of the window coated with the nanoparticles, indicating that the coating could pull heat from the sunlight inside, in order to compensate for internal heat lost through a single-pane window. The researchers then implemented their data into a larger-scale simulation to analyse the energy savings for an entire building with coated windows across different climates. Compared to a commercially available single-pane window’s low-emissivity coating, the photothermal coating absorbed much of the light in the near-infrared region of the spectrum while the conventionally coated window reflected it outside. This nearinfrared absorption resulted in a roughly 12% to 20% reduction in heat loss compared to the other coatings and an overall building energy saving potential of up to around 20% when compared to a building with no coatings on single-pane windows. To account for seasonal changes, the researchers also implemented awnings into their building-scale simulation, blocking the more direct rays of sunlight that heat the environment in summer, largely negating the undesirable heat transfer and any associated cooling costs. “As demonstrated by this study, we can still improve the overall thermal performance of single-pane windows to be similar to double-pane windows in the winter season at this research stage. These findings challenge our conventional solution of using more layers or insulation materials to retrofit single-pane windows for energy savings,” added Wang.
© Unsplash
For further information: www.psu.edu/news/
Three Generations of Innovations and Technology in the Manufacturing of Premium Quality Overhead Conveyor Chains
Orbita, a well-established company in the sector of components for overhead and floor conveyors celebrates 60 years of activity.
Established in 1962 for the production of small metal parts mainly intended for the automotive industry, as early as the mid-’60s Orbita expanded its production range with the design and construction of chains and bearings for conveyors, the products that currently account for almost all of its turnover. The continuous investment in technology made since the beginning has enabled the company to establish itself in the coating plant market and be fully repaid by the trust of its loyal customers. The entrepreneurial path of Nazzareno Roda, the President of TSPGROUP, belonging to Trafilerie San Paolo, is the emblem of that of an entire generation. In the mid-1960s, Nazzareno Roda crossed destinies with Trafilerie San Paolo, a company established in 1966 by three partners and specialising in drawing stainless steel tubes. Nazzareno Roda made their business take off, importing the cold plastic deformation technique to Italy. This important innovation gradually turned Trafilerie San Paolo’s customers from turners (with 60% waste and non-constant quality levels) to moulders. In addition to the parent company Trafilerie San Paolo, the Group includes two other drawing mills, Gerosa and Meal, each with a different specialisation; Raptor, for the development of application software; Tramev, with its tools intended for the main drawing machines; and Orbita. The latter is located in Cesana Brianza (Lecco, Italy) and it is the pride of the Roda family. “The company was established in 1962 to
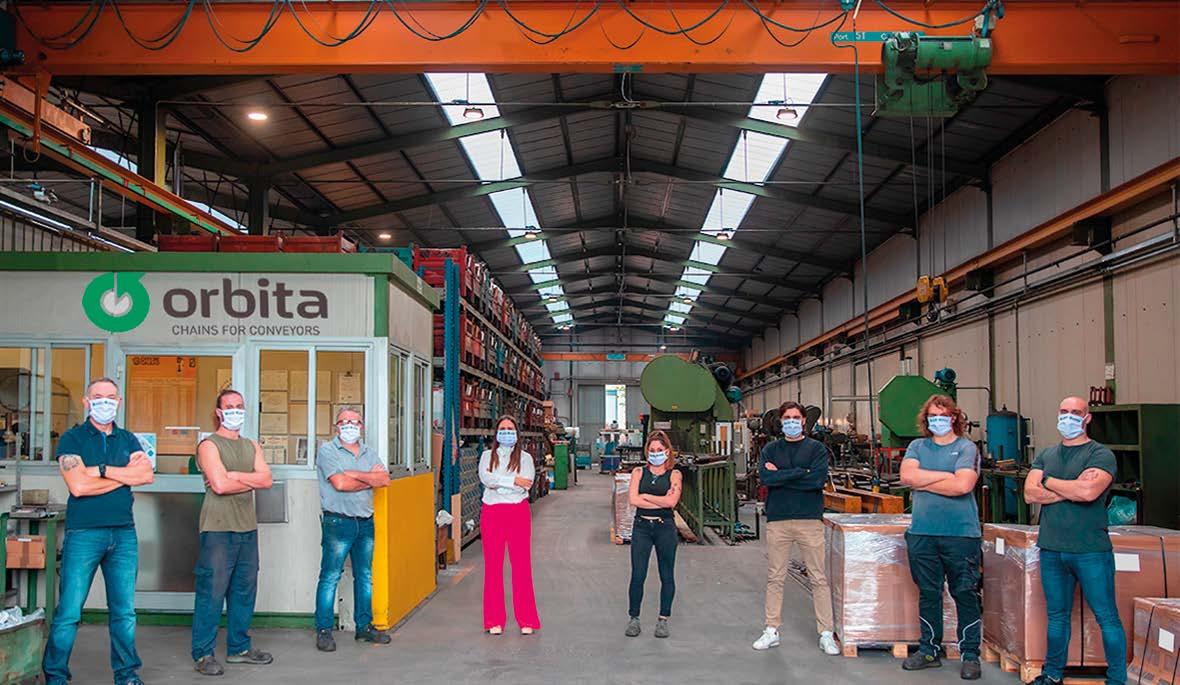
© Orbita manufacture overhead conveyor chains: this is a small niche in which we are the European leader with our products of excellence. We work for the world’s major manufacturers of conveyor systems and our chains are basically the ‘core’ of the whole mechanism,” say Matteo and Giacomo Roda, who represent the third generation working in the company. “By observing these plants, our grandfather realised that the chains used were extremely heavy, thus adding a further burden to those structures. Thanks to his experience with the highest quality steels, he invented a much lighter chain combined with a new full-complement bearing also invented by him, which featured no ring nuts to withstand high temperatures. It was not easy to fight against the ‘battleships’ of the great British and US manufacturers, but in the end Orbita got the upper hand. It now produces tens of thousands of meters of chain per year.” Today, the company’s activity is carried out in a modern plant of about 2,000 square meters. Its highly qualified staff uses sophisticated automatic machines, as well as assembly robots able to complete the production process of an entire component autonomously and in absolute safety. Technical skills and innovation are still the forte and the distinctive feature of the entire Group.
For further information www.orbita.it
Anton Paar Celebrates its 100th Anniversary
On January 4, 2022, Anton Paar celebrated its 100th anniversary.
Anton Paar, specialized in density and concentration measurement, rheometry and CO2 measurement, has recently celebrated its 100th anniversary. Founded on January 4, 1922 as a locksmith’s shop, the company now counts more than 3,500 employees.
Early history
The company was founded by Anton Paar who, right from the start, involved his two daughters Hermine and Margareta (called Gretl), in the business. While Hermine was responsible for the bookkeeping, Gretl worked in the workshop. Later, Anton Paar gradually withdrew from the business and Gretl, at that time the first female master locksmith in Styria, took over the management. The Kratky small-angle X-ray camera was the first scientific analytical instrument developed by the company.
The expansion
From the 1950s onwards, the company focused on measuring and analysis technology for several industries – from beer, wine and soft drink producers to pharmaceutical and cosmetics companies to chocolate or cell phone display manufacturers. In 1963, Gretl’s son-in-law Ulrich Santner (1932-2020) took over the management of the company and set the foundation for the company’s expansion in the field of measurement technology, making contacts with universities and contributing to the transfer of new technologies from research to industry. Finally, in 1997, his son-in-law and current CEO Friedrich Santner joined the management. Under his leadership, many new sales and service subsidiaries were established, and complementary measurement technology companies were acquired. Anton Paar now has 45 sister companies and subsidiaries as well as 50 sales partners and operates in more than 110 countries around the world. Friedrich Santner also focused on expanding internal research and development.
Sustainability and the fifth generation
The non-profit Santner Private Foundation has owned the company since 2003. The foundation has two purposes: to promote non-profit science and research as well as to prevent and combat drug addiction. In January 2020, Friedrich Santner’s sons Jakob and Dominik Santner joined the company’s Executive Board, making it the fifth generation to be part of the management team. “Talent, commitment and inner cohesion, in both successful and difficult times, have always distinguished us and our company. With these attributes, we are confidently entering the second century of our history,” resumes CEO Friedrich Santner.
For further information: www.anton-paar.com/corp-en/
© Anton Paar
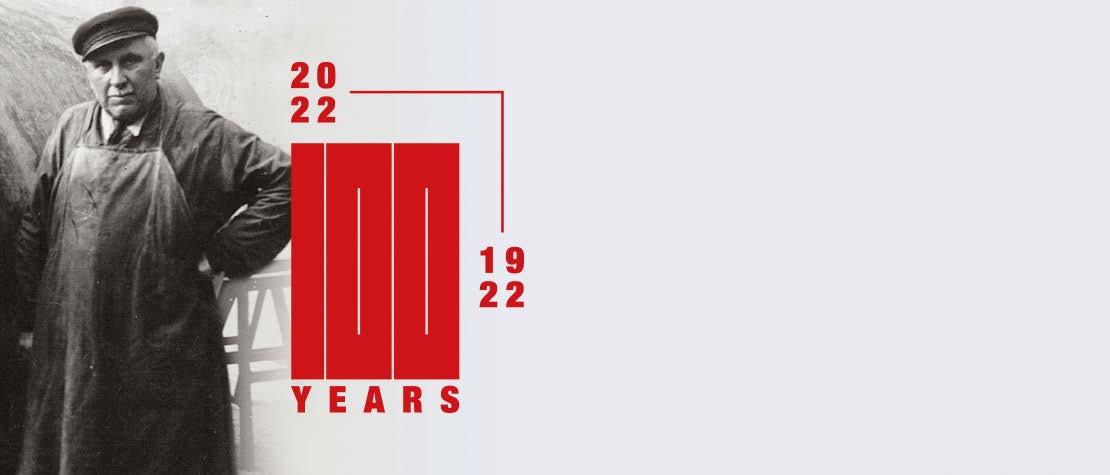
NASA’s Perseverance Spotted a Purple Coating on Mars
NASA’s Perseverance rover has spotted a thin, smooth, purple coating on some stones on Mars, which could hold clues to the planet’s potential for ancient life.
Red dust paints Mars in ruddy hues, from the surface to the skies. But NASA’s Perseverance rover has spotted swaths of another colour among the rusty shades. At nearly every site the robotic geologist visits, the Martian palette includes purple. The colour forms a thin, smooth coating on some stones, and it leaves paint-like blobs on others. Still other rocks look as if they’ve been partially frosted in magenta icing, says Ann Ollila1, a geochemist at Los Alamos National Laboratory who presented an early analysis of the coatings2 at a recent conference of the American Geophysical Union (AGU). The colour touches rocks of all different shapes and sizes—even tiny pebbles haven’t escaped the pops of purple. But how, exactly, did these coatings form? “I don’t really have a good answer for you,” Ollila says. Scientists are eager to know more. “There’s a lot to look forward to as we continue to do analyses,” says Nina Lanza3, the team lead for Space and Planetary Exploration at Los Alamos National Laboratory, who has been studying the coatings alongside Ollila.
1 https://scholar.google.com/citations?hl=en&user=2b-ZCF8AAAAJ&view_op=list_ works&sortby=pubdate 2 https://agu.confex.com/agu/fm21/meetingapp.cgi/Paper/989148 3 https://www.lanl.gov/discover/publications/national-security-science/2021-spring/mars.php
© JPL-CALTECH
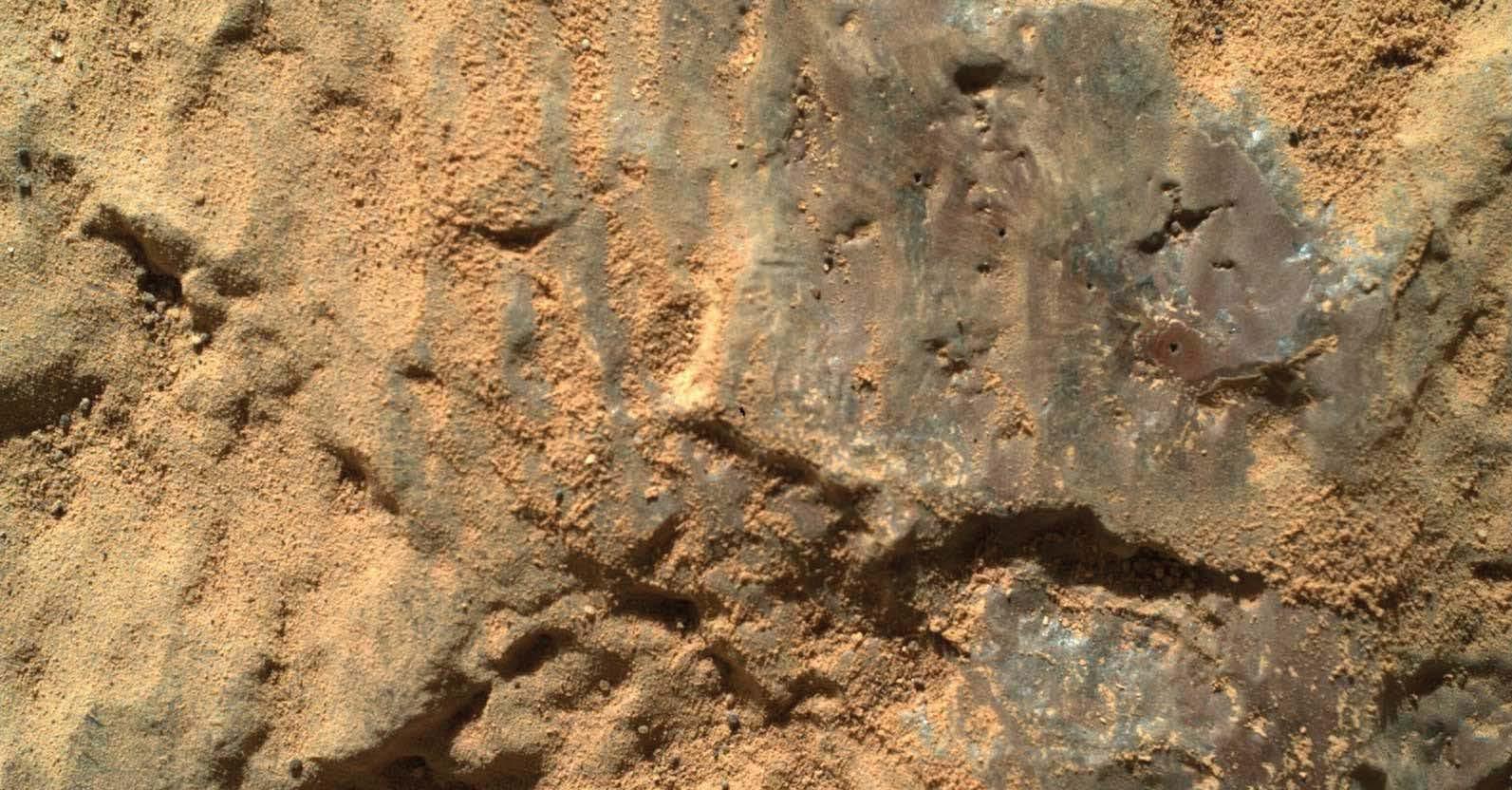
NASA’s Perseverance rover captured this image of the rock Nataani in May 2021, which includes a purple smear near the right edge of the frame. Five tiny holes punch through the coating where a series of laser shots were used to study the rock’s composition.
The origin of the mysterious splotches could help reveal clues about Mars’s past, including whether it might have hosted ancient life. As the coatings formed, they could have encoded information about the surrounding conditions in their chemical and mineral makeup, helping scientists reconstruct environments now long gone. They also could hold more direct evidence of life: On Earth, microbes help craft many similar stony veneers. The purple Martian coatings were found in Jezero crater, a 28-milewide pockmark blasted out by a meteorite impact billions of years ago that once hosted an ancient lake. Perseverance landed in the crater in February 20214 and has since been roaming across it. At almost every stop along the rover’s route, flashes of purple have popped up in its images. Early analyses point to the presence of hydrogen and oxides, suggesting water played a role in the purple patches’ formation. But so far the team has only analysed a few samples, and they are still contending with many challenges. For example, separating the chemical signatures of the coatings, the underlying rock, and the ever-present dust on the Martian surface is complex. The team hopes to further untangle the chemistry of the coatings and search for organic matter associated with the Martian crusts, which could hint at the presence of microbes. But getting the rocks back to Earth for lab analysis is one of the few ways to definitively pin down how the patches formed.
4 https://www.nationalgeographic.com/science/article/nasa-perseverance-rover-has-just-landed-on-mars
Scan OR click the QR Code to read the full article by Maya Wei-Haas at www.natgeo.com
GLOBAL SOLUTIONS FOR WATER TREATMENT
with a complete service that includes system design manufacturing installation technical support chemicals
SPRAY BOOTHS WATER SLUDGE REMOVAL RESIN DEMINERALIZATION SYSTEMS REMEDIATION OF CONTAMINATED SITES BIOLOGICAL SYSTEMS BATCH TREATMENTS PHYSICAL-CHEMICAL SYSTEMS ADSORPTION FILTRATION REVERSE OSMOSIS MEMBRANE SYSTEMS EVAPORATORS BIOGAS BIOMASS SYSTEMS OIL SEPARATORS DESANDERS DESALINATION SYSTEMS PYROCHAR OTHER SYSTEMS CHEMICALS