
32 minute read
BRAND NEW
Table 1: Drying speed of INVERPUR/R.
100 µM WFT (≈ 50 µM DFT) 150 µM WFT (≈ 70 µM DFT)
Drying conditions RT 40 °C 60 °C RT 40 °C 60 °C
INVERPUR 25% 72870
INVERPUR/R 30% 40301
Tack-free time >8 h >1 h 30 min >8 h >1 h 35 min
Dry-to-handle time >8 h >2 h 35 min >8 h >3 h 40 min
Tack-free time 3 h 20 min 10 min 3.5 h 20 min 10 min
Dry-to-handle time 4 h 30 min 10 min 4.5 h 50 min 15 min
Table 2: Accelerated light resistance test on INVERPUR/R.
Product
INVERPUR 25% 72870
INVERPUR/R 30% 40301
(*) SAE J2527 test 20°
60°
20°
60°
Gloss
83
92
84
92 47
73
56
75
After 1700h (*) Gloss Retention %
57
79
67
82
Table 3: Other technical characteristics of INVERPUR/R.
Test Reference Note (*) Result
Humidity resistance ASTM D1735 400 h No blistering, rusting, visual defects. Adhesion Gt 0-1 Water immersion ASTM D870 300 h No blistering, visual defects. Adhesion Gt 0-1
Impact test ASTM D2794
Flexibility ASTM D522 B Cylindrical mandrel
Chemical resistance
CNH MTM0108 Drop, 24 h
Buchholz hardness ISO 2815 Direct impact > 60 kg/cm Reverse impact > 30 kg/cm
Elongation > 10%
Gasoline, Diesel, Motor oil, Antifreeze (sol. H2O 1:1), NaOH 5% w/w, HCl 10% w/w
No visual defects, swelling, blistering. No adhesion loss
> 100
(*) tested on CRS, 50-70 µm DFT The main features of INVERPUR/R can be summarised as follows: • Product code: 45763 INVERPUR/R, twocomponent, RAL 9010 white • Mixing ratio: 30% w/w • Solid content (calculated typical value, ready to use product): 58.5% w/w and 47.9% v/v • Yield (calculated typical value): 393 m2/kg (ready to use product) • Gloss: ≥ 90 to 60° - ≥ 80 to 20° • VOC content (2010/75/EU): 144 g/l • Pot life: 2 hours at 20 °C.
Fast drying at low temperatures
Table 1 compares the drying times of the standard INVERPUR top coat and the new INVERPUR/R top coat at different temperatures. Table 2 shows the results of the accelerated light resistance test conducted on the two products. It should be noted that the gloss and gloss retention values of INVERPUR/R after 1700 hours in the Xenon test are comparable to those of Inverpur’s conventional waterbased technology. Further test results obtained by the INVERPUR/R top coat are shown in Table 3.
Different fields of application
The laboratory has succeeded in creating a product that cross-links at lower temperatures than those generally used for baking water-soluble products and that features characteristics and a performance degree comparable to those of the traditional INVERPUR technology. Launched on the market in 2020, the INVERPUR/R top coat is also proving very popular with users that are actually equipped with a drying oven. Indeed, reducing drying process times and, above all, temperatures guarantees considerable savings in terms of time and energy. Conceived to meet market needs, this product has been optimised for application in harsh situations and it can now also be used in sectors other than those for which it was originally created.
© Axalta

HIGHLIGHT OF THE MONTH
Axalta Extends Automotive Colour Leadership with the 69th Global Automotive Color Popularity Report
Jessica Iben
Axalta Coating Systems Ltd. – Philadelphia, United States jessica.iben@axalta.com
Axalta’s report shows an increase in blue vehicles and a decline in white ones, with grey hues still popular.
Axalta’s 69th Global Automotive Color Popularity Report reveals the top automotive colours on the road today are white (35%), black (19%) and grey (19%). Grey increased by four percentage points worldwide due to increased interest seen around the globe. White vehicles have been found in the most abundance on the roads since 2011 worldwide with Asia leading in white vehicle builds. Overall, the popularity of white hit a long-term high of 39% in 2017 and has seen declines in several regions each year since. This year, white declined three percentage points, largely due to a decrease seen in all regions, especially China with a seven percent decrease. For the third year in a row, Europe ranks the only major region to report grey as the most popular colour at 27%. Silver is most popular in South America as it ranks second place with twenty-three percent usage. Black is most found in Europe at twenty-two percent and continues to lead in the luxury segment. North America has the most amount of new red cars on the road at eight percent. The results of Axalta’s Global Automotive Color Popularity report are tabulated on Axalta’s analysis of 2021 automotive build data in major markets and are an indicator of current market trends. Axalta began reporting on the industry’s coatings colour in 1953 and continues to report on colour trends and colour preferences. Axalta celebrated its 2021 Global Automotive Color of the Year, ElectroLight, around the world. The refreshing yellow-green hue was inspired by bold, contemporary flavours that echo style, energy and flair. This colour is soothing and calm with an opaque simplicity, yet exciting and fresh with its vibrancy. The unique personality of ElectroLight evokes
a blend of customized, modern style with sporty performance. Push the boundaries of design by combining ElectroLight with two tone charcoal colour accents or matte finishes to reveal its versatility. ElectroLight aims to illuminate a path toward a green future for vehicles of all sizes with a formula for reflective properties and powerful vehicle-to-vehicle sensing and communication capabilities. ElectroLight combines a passion for individualization with coating science to show how colour can be expressive and dynamic. Axalta designs conceptual colours that are aesthetically and functionally beneficial to the vehicle surfaces.
Colour Popularity at a Glance
World
• White holds the #1 position at 35% but also saw a (-3%) decline. • Interest is shifting as grey increased (+4%) and blue increased (+1%) this year. • Holding steady are black at 19%, silver at 9%, red at 5%, brown/beige at 3% and green at 1%.
Asia
Increased interest in grey at 13% and green at 2% also lead to decrease in white at 45% and silver at 7%.
China
• White has finally begun to drop in China holding 50% of the market. • Grey at 14% with an increase (+8%) from last year.
India
The combined usage of white, silver, grey and black increased 3% year-over-year.
Japan
• White at 37% increased (+2%) due to pearlescent white vehicle increases. • Grey at 6% increased (+1%). Blue, red and brown/beige all decreased (-1%).
South Korea
• Brown/beige increased (+1%). • Silver decreased (-1%) and dropped to the sixth position.
Europe
• White’s zenith has been passed, the volume reduced by another -2% and was mainly driven by the decline of solid whites. • For the third year, grey is positioned as the first choice, by increasing once more (+2%) in popularity. This year interest was especially found in the compact-sport sector. • Blue (11%) is the high chromatic colour of interest in Europe with a continued gain of +1% again this year.
North America
• Grey increases +2% and now totals 21% to move to second place. • Blue (10%) is steady and red (8%) increased (+1%). • Silver is waning in interest and white drops (-2%) in popularity.
Russia
• Significant increase of blue (+3%) and decrease of silver (-3%). • White and grey are top colours and each increased 1%. • A (-1%) decrease of black and (-2%) decrease of red shades were found.
Africa
•The decline of white has started (-3%). • Blue at 10% increased (+3%) and grey at 21% increased (+5%). • The biggest loss of -5% was found on silver vehicles, now totalling 6%.
South America
• This region stands out as reporting a +4% increase in grey vehicles and a (+3%) increase in silver vehicles. • Off-setting these increases were declines of white (-6%) and black (-1%).
CONDOROIL Group and AIRMADI Painting: A Virtuous Example of ‘Coopetition’
Thanks to their ‘coopetition’ strategy, Condoroil Stainless and Airmadi have joined forces to revamp the cataphoresis plant of IIA - Industria Italiana Autobus (formerly Irisbus) in Flumeri, one of Europe’s leading bus production centres.
Arecent neologism in English is the term ‘coopetition’, a word that expresses well the concept of cooperating with competitors to create a competitive advantage. In fact, it defines a competitivecooperative strategy between two or more competing companies, which takes the form of a collaboration aimed at jointly carrying out one or more production phases of a given good and/or service. Coopetition is often applied to R&D: competing companies walk a stretch of road together, integrating their resources and expertise and cutting R&D costs to realise a project for a customer or end user. Contrary to what one might think, such cooperative, or rather coopetitive attitude is the one that, in the medium to long term, will guarantee the sustainable and lasting survival of those enterprises that we usually consider being in competition with each other. Indeed, interdependence has proven to be the natural evolution for companies that cannot have all the sufficient and necessary resources to achieve and maintain success. In addition, coopetition will certainly be the key to success in a context of scarce resources. Electrodialysis cells
The ED-cells produced by Condoroil are equipped with ion exchange membranes and they are created with a wrapped and welded polymer sheet, featuring low deformability and electrical resistance but long service life and greater current intensity characteristics.
© Condoroil
United we stand, divided we fall
Supported by Airmadi, a company specialising in the design, engineering, construction, and installation of industrial coating systems, Condoroil Stainless, the division of the Condoroil Group devoted to the supply of spare parts for ED-Painting, has long since adopted the strategy of coopetition. Thanks to this, the two firms were able to integrate electrodialysis cells produced by Condoroil into the cataphoresis plant that Airmadi was revamping at the production plant of IIA - Industria Italiana Autobus (Flumeri, Avellino, Italy), the most important bus manufacturer in Italy and one of the leading ones in Europe, which has a long tradition of building high-quality buses.
Scan or click the QR Code to see the new cataphoresis plant at the IIA Flumeri plant:

The cataphoresis tank of the IIA Flumeri plant.
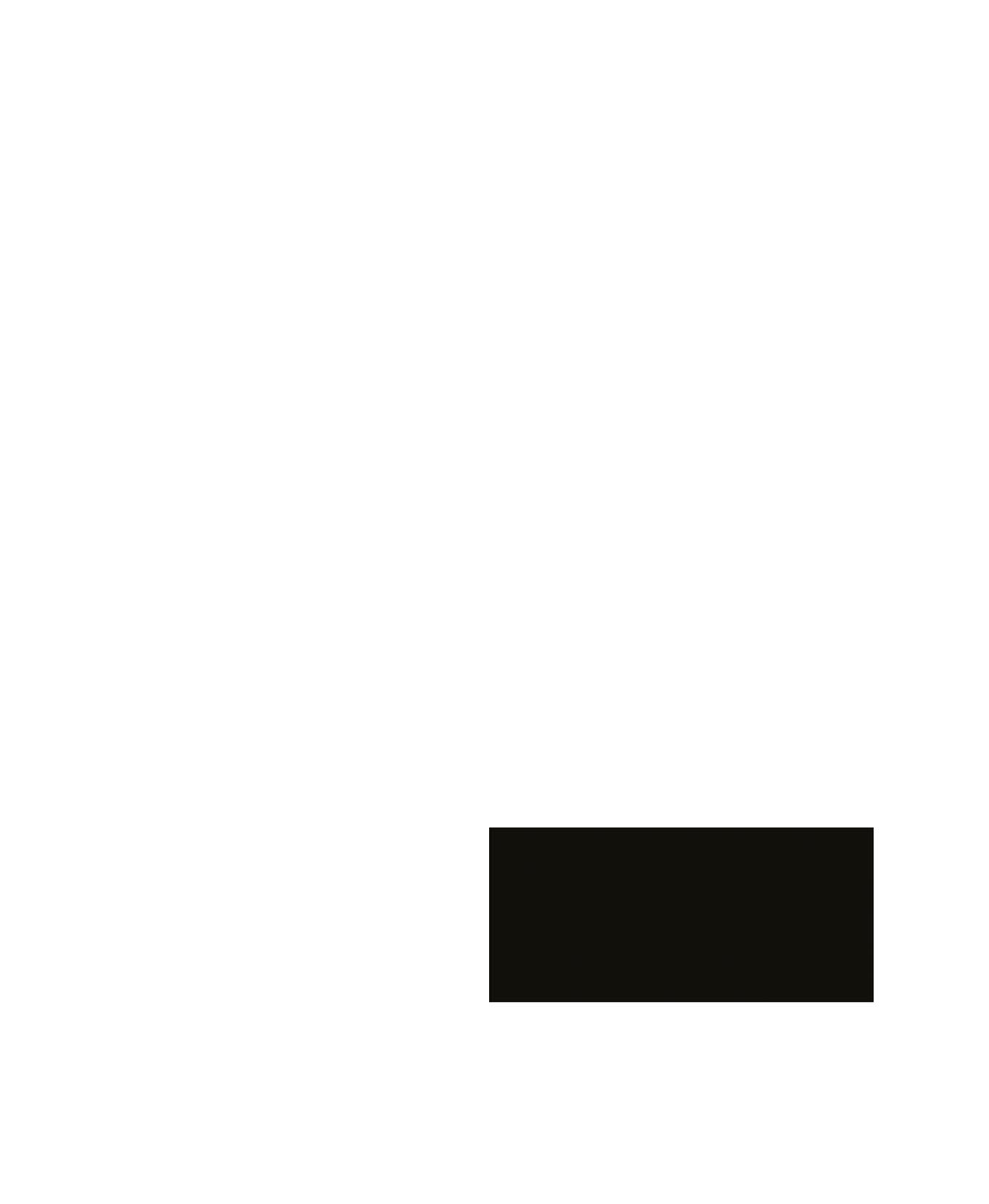
Future-proof and reliable overhead and floor MONORAIL and P+F
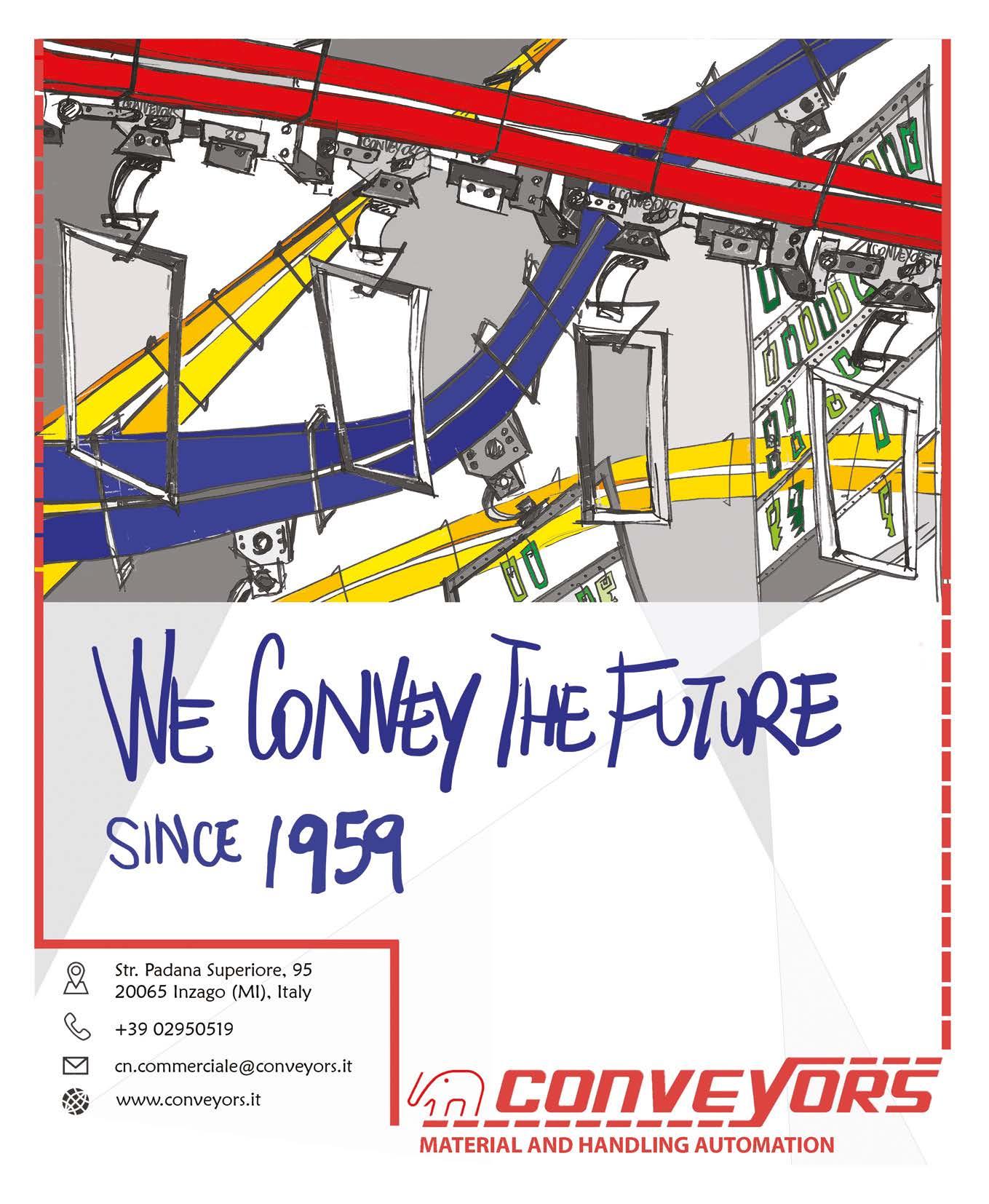
CONVEYOR systems that can be perfectly integrated into your production processes.
We take care of all your requirements and create a tailor-made and cost-optimized concept for you.
Towering Cranes with Powder Coatings
Wilbert, a German company manufacturing cranes for construction industry for more 80 years, relies on weatherproof, UV-resistant powder coatings from Karl Bubenhofer AG to keep its innovative products, which are rented out and in operation over a number of years, looking as good as new.
Cranes are eye-catching machines, particularly when they grow along with the structure that is being built. Wilbert TowerCranes from Waldlaubersheim in Germany has been well known for its innovative products for more than 80 years. The company’s trolley and luffing jib cranes are based on a sophisticated modular system that makes it easy to add individually manufactured components as required. These tower cranes are used by major building companies worldwide, particularly for the construction of high-rise buildings and power stations. Wilbert relies on weatherproof, UV-resistant powder coatings from Karl Bubenhofer AG to keep its cranes, which are rented out and in operation over a number of years, looking as good as new. Regional sales manager Markus Ammann from KABE has always had an interest in supplying powder coatings for cranes. “These fascinating machines are masterpieces of technology and can be seen from miles away. They have to withstand all types of weather conditions over long periods. I think a hard-wearing powder coating is the perfect solution for them.” One day, Markus Ammann was talking to a business colleague about the fact that a producer of grape harvesting machines in the town where Wilbert TowerCranes is based is successfully using KABE powder coatings. His contact mentioned that Wilbert TowerCranes also powder coated its cranes. After Markus Ammann had made initial contact with the company, plant manager Andreas Glaser took him out into the yard and showed him an old crane. “The plan was to have this crane
© Jürgen Stresius
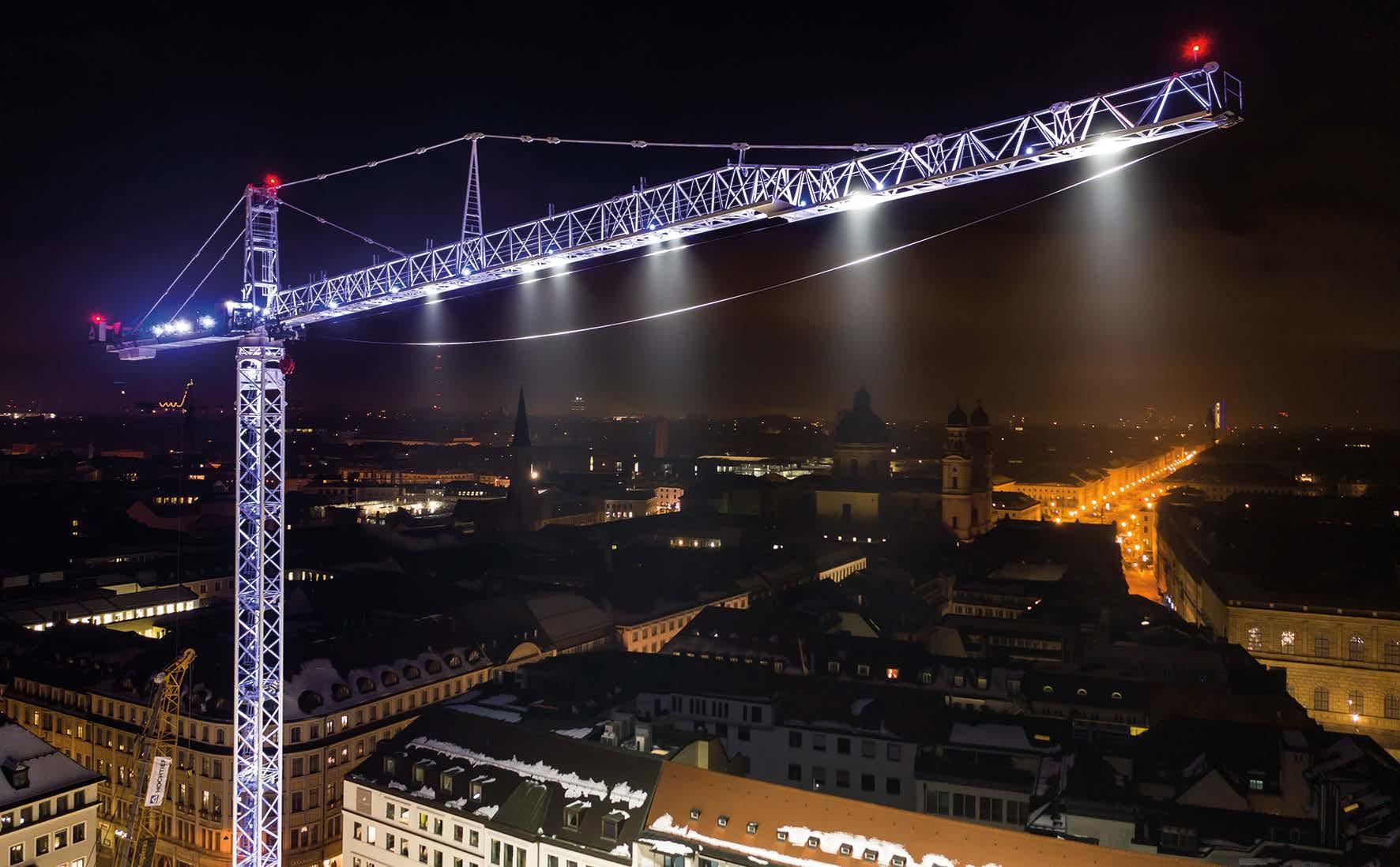
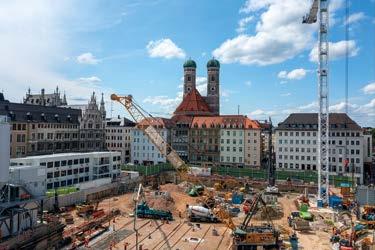
restored by the team at one of our long-term customers in Switzerland in time for the company’s anniversary. But we haven’t been able to find the right colour coating and there isn’t much time left,” said Andreas Glaser. The old crane had been given several coats of an old iron primer and all the enquiries made by Wilbert about a suitable replacement paint had come to nothing. This was an additional incentive for Markus Ammann to step in to help both the assembly team at the Swiss company and Wilbert TowerCranes. Karl Bubenhofer AG is well known for finding the right matching formulation for almost any colour of paint and powder coating. The family firm, based in Gossau in the Swiss canton of St. Gallen, specialises in coatings in unusual colours and with special effects. Of course, KABE was able to find a solution for Wilbert TowerCranes. In its laboratory, the original shade was “copied” to produce a powder coating that perfectly matched the existing colour. The newly restored crane was ready and waiting on the Swiss customer’s site in time for the anniversary, much to the surprise of the managing director.
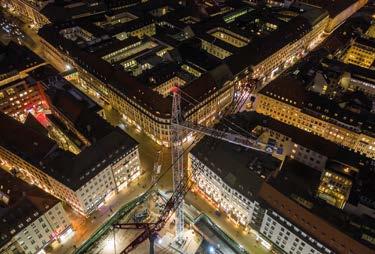
Special solution launches a long-term partnership
The solution developed by KABE proved to be the start of a long-lasting business partnership. The Wilbert cranes are now coated in the company’s characteristic shade of red with powder coatings supplied by Karl Bubenhofer AG. Because of the large size of the components, the powder coating is applied manually, which requires a lot of skill and a good eye. The Wilbert cranes are supplied as standard with a highly UVresistant powder coating to give the best possible protection against weathering. P-20Korroflexprimer NT-GU (article 13594) in RAL 7035 is used as the primer, while the top coat is PES-165-NT (article 13524, which has GSB and Qualicoat approval) in the company’s corporate colours RAL 3020/3000 and a range of special colours. Since 1 January 2021, liquid paints from GEHOLIT+WIEMER have been added to the product portfolio of the KABE Swiss Group. A UV-resistant, two-component, polyurethane-based paint, which is used for coating small parts and for touch-up repairs, has been perfectly matched with the colour and gloss level of the powder coating. In addition, in safety-related areas, where anti-slip properties are needed, a two-component, polyurethane-based anti-slip coating with a high filler content is applied. However, it is not only the excellent quality of the powder coating that is a decisive factor in the collaboration from Wilbert’s perspective. “KABE and Wilbert, which is now part of the Chinese Zoomlion Group, are both traditional family businesses. We have the same corporate values and philosophy and we have known from day one that we can rely on one another,” said Andreas Glaser.
© Jürgen Stresius
© Jürgen Stresius
Two tonnes of powder coating for one tower crane
To resolve a bottleneck in the urban rail system in Munich, Deutsche Bahn, Germany’s largest railway company, is building a second line covering a distance of around ten kilometres between the stations in Laim in the west of the city and Leuchtenbergring in the east, on behalf of the Free State of Bavaria. The centrepiece of the line is a sevenkilometre-long tunnel that connects Munich Central station with Munich East station. Wilbert has supplied a tailor-made crane for the construction site. The WT 1000 e.tronic towers over the centre of Munich at a height of 75 metres and with its 65-metre jib supplies the Marienhof construction consortium with building materials. It is not only the size of the crane that is impressive, but also its colour, which is not the characteristic Wilbert red, but, at the customer’s request, a special shade of white. The white was specially formulated by KABE for its 13524 coating to create an unusual glowing effect. This allows the crane to be illuminated at night, for example in the colours of the state of Bavaria. During the day, the shade of white makes the crane visible from a long way off. This powder coating too is, of course, highly UV-resistant. “We have developed the formulation specially for the Marienhof consortium following specifications from the consortium partners Implenia and Hochtief Infrastructure. After several years exposed to wind, rain, ice and snow, the coating must make the same impact as it did on day one,” explained Markus Ammann. One tonne of primer (RAL 7035) and one tonne of top coat (RAL 9003) were needed to give the new Wilber tower crane its special appearance. It will be part of the Munich skyline for several years to come and, because of its size and colour, it is likely to become a new landmark.
For further information: www.kabe-farben.ch
Researchers Developed a Spray-on Coating That Could Make Solar Panels Snow-Resistant
The University of Michigan has demonstrated a clear coating that reduces snow and ice accumulation on solar panels.
Ateam of researchers from the University of Michigan has developed an inexpensive clear coating that could prevent snow and ice accumulation on solar panels, improving their productivity also in cold climates by up to 85%, as demonstrated in early testing that took place in Alaska. The coating is mostly composed by PVC or PDMS plastic and silicon or vegetable-based oils. It can be sprayed or brushed on in cold weather and, in its current iteration, can keep shedding snow and ice for up to a whole year. “Renewable energy is really taking off right now, but snow is a huge problem in northern climates. Solar panels might lose 80 or 90% of their generating capacity in the winter. So, figuring out a way for them to continue generating energy throughout the year was an exciting challenge,” stated Anish Tuteja, the U-M professor of materials science and engineering who led the study in collaboration with Sandia National Laboratories and the University of Alaska. “Ice is relatively dense and heavy, and our previous coatings used its own weight against it. But snow can be 10 times less dense than ice, so we weren’t at all certain that the tricks we use on ice would translate to snow.”
A precise combination of low interfacial toughness and low adhesion strength
The researchers employed two key properties that have already powered ice-shedding coatings in the past: low interfacial toughness and low adhesion strength. Low surface adhesion is suitable for small areas, but it needs more force to slide snow and ice off bigger surfaces. Low interfacial toughness allows to create cracks between the ice and the panel that propagate along it, regardless of its size, breaking the ice and snow free. The team has then focused on accurately balance the two in order to provide snow and ice repellence for both small and large surfaces. The scientists from the University of Michigan collaborated with the University of Alaska to test the material on a solar field in Fairbanks (Alaska), applying the coatings to a subset of panels that were monitored by automated cameras for almost two weeks. The tests showed that the coated panels had an average snow and ice coverage of approximately 28% over an entire winter season, in comparison to about 59% for the uncoated panels. However, the team plans to tweak the coating further, with the aim of developing a coating that can last at least five years. “As the cost of solar energy has dropped and profitability has climbed, much of the growth in solar energy in recent years has been in northern states, where snow is common. Snow-phobic coatings, if we can demonstrate their long-term efficacy, will make solar power more reliable and more affordable in snowy regions, helping accelerate our nation’s transition to a more solar-dominated energy economy,” commented also Laurie Burnham, the project’s principal investigator. The coating was developed as part of a project led by Sandia National Laboratories, a U.S. Department of Energy research and development lab, with funding provided by the DOE’s Solar Energy Technologies Office. The study is published in Advanced Materials Technologies. Other researchers on the project were former U-M materials science and engineering graduate researcher Abhishek Dhyani; Christopher Pike and Erin Whitney at the Alaska Center for Energy and Power at the University of Alaska; and Jennifer Braid at the Photovoltaics and Materials Technology Department of Sandia National Laboratories.
For further information: https://news.umich.edu/
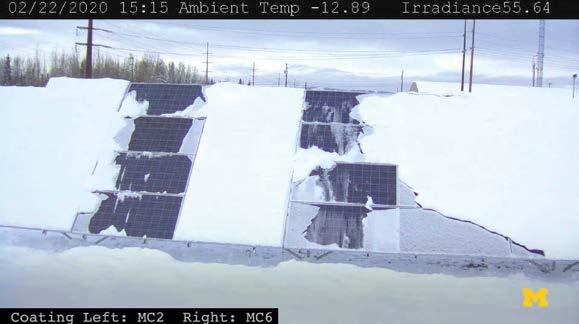
Scan or click the QR Code to watch the video
Dörken Took Part in the Development of a New Innovative Coating Process
A joint project led by Dörken, EJOT and WMV developed a new coating technology for fasteners and small parts with internal drives.
After a joint development conducted by Dörken, EJOT and WMV that lasted almost five years, the companies have presented a new technological innovation for the coating of fasteners and small parts with internal drives. The new coating technology, developed at the EJOT site in Tambach-Dietharz (Germany), ensures an extremely even and thin coating structure for small fasteners with internal drives such as TORX® or TORX PLUS®. The corrosion protection experts at Dörken were involved from the initial planning of the project and provided the parts-specific coating materials. The three companies together identified an ideal and parts-specific coating process and developed the world’s first system capable of coating 120 kg material with a simultaneous position shifting at an acceleration of 32 g. The WMV PULZ® unit (a planet wheel, roller and coating centrifuge) coats items such as small parts with hollow spaces as well as fasteners while a Dörken’s zinc flake system provides corrosion protection. The permanent rotation with simultaneously high acceleration level (32g) results in an even, process-safe and thin coating of the part. The new coating technology also benefits the environment, as the optimised coating process results in a reduction in CO2 emissions (almost 30% compared to previous processes).
For further information: www.doerken.com, www.ejot.com/coating-competence and www.wmv.com
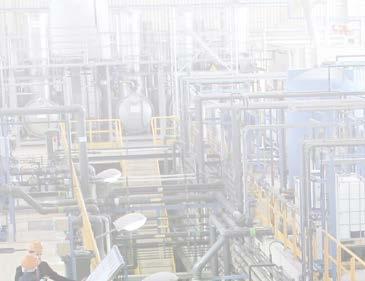
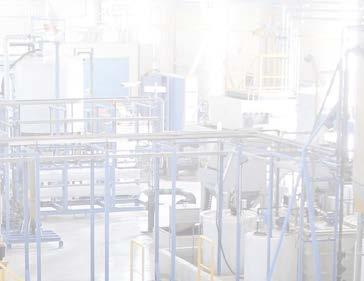
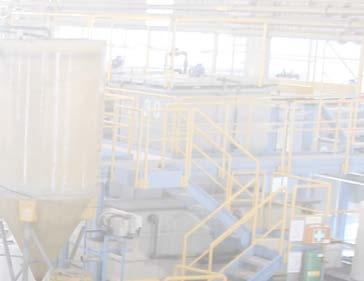

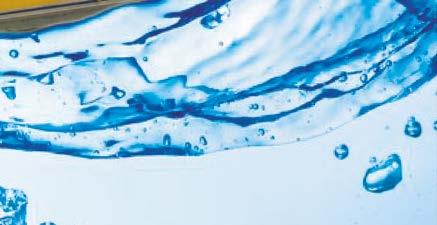
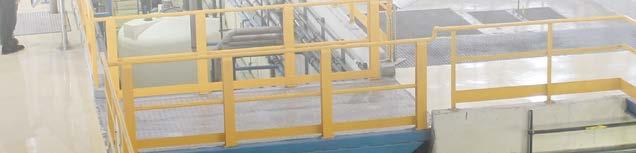
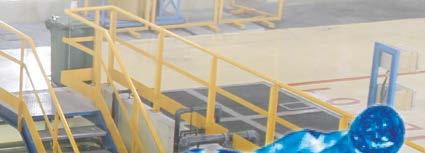
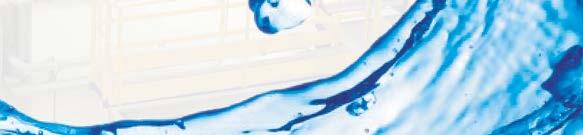

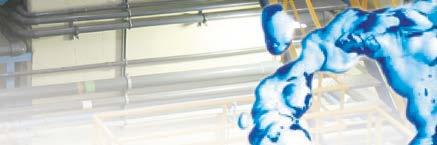
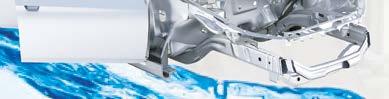
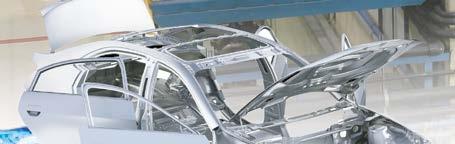
WAGNER Awarded Among the TOP 100 Innovators
Wagner was named for the second time among the TOP 100 innovators, impressing the jury in the “Innovative processes and organization” category.
For the second time, J. Wagner Gmbh is named among the TOP 100 innovative companies, impressing in size class C (more than 200 employees) in the category “Innovative Processes and Organization”. This medium-sized company is known as one of the leading manufacturers of systems and equipment for applying powder, paint and other liquid finishings to surfaces. Its portfolio of products ranges from spray guns for do-it-yourself enthusiasts to industrial coating systems. Ever since it was founded in 1947 the company has always striven to innovate and now it has gone several steps further. “With our ‘WINNOVATION 2025’ corporate strategy, we are striving for no less than to be the technological leader in the field of liquid and powder coating”, said CEO Dr. Bruno Niemeyer. This recognition, obtained for the second time, as Top 100 innovator in 2021 shows that this aspiration is not only about innovative products, but is also supported by processes and structures within the company, and not least a culture that has been designed to foster innovation. The commitment of the staff to innovation has already paid off: for example, a web-based platform that enables the visualization of coating systems. And a new business model is just about to be established with the “IONIQ Skin” project, as the firm has used the know-how gained in industrial wheel-rim coating to develop a skincare spray device called IONIQ ONE, which is currently being launched online to the market and which has already won the national Digital Champions Award (DCA) this fall. “Along with the Top 100 award, the national Digital Champions Award 2021 is further confirmation of the good work we have done in terms of innovation, something which we at WAGNER can be proud of the world over”, declared Niemeyer. The company received the compliments of Ranga Yogeshwar, science journalist and mentor in the 28th edition of the innovation contest.

IONIQ Skincare
IONIQ Skincare, a WAGNER corporate start-up, has already this fall won the national Digital Champions Award (DCA) for IONIQ ONE, a sprayer that is unique in the world in its use of the natural physical attraction of the skin to apply a perfect coat of skincare product and sun-protection product on the body. The prize recognizes flagship digital projects from German small and medium enterprises, and awards prizes to companies that implement digital solutions in a particularly consistent and innovative manner, or who have developed new business models. “Along with the Top 100 award, the national Digital Champions Award 2021 is further confirmation of the good work we have done in terms of innovation, something which we at WAGNER can be proud of the world over”, declared the company’s delighted chief executive Bruno Niemeyer.
© WAGNER
For further information: www.wagner-group.com

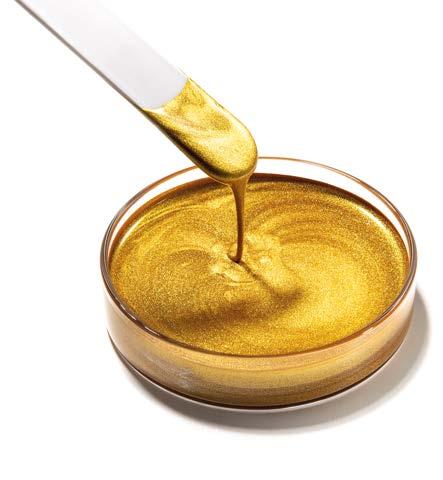
Clariant Pigments Presented its Colour of the Year 2022: Memory Gold
Launch of new Decorative Colour Trend Palette “golden” with 40 new shades.
© Clariant
In December Clariant Pigments, now part of the Heubach Group, released “golden”, a new palette that encompasses the new Decorative Coatings Trends for 2022. The “golden” palette offers consumers 40 new shades to inspire them to decorate their rooms and furniture. These shades reflect 4 different phases of natural human behaviour in the new world we live in: • “memotions”: a calm colour selection with some poppy colour accents which represents a coming back to life of sorts, where we’re re-orienting ourselves, considering our recent pasts to plan our futures. This palette includes Colour of the Year “memory gold”, an antique gold tone with a touch of luxury developed to inspire us to create new memories distinct from the past. • “wembrace”: includes more colourful tones like greens, beiges and blues that reflect the happiness and feelings of being allowed to “breathe” again. • “wescalate”: this palette evolves to become yet more colourful again, as we take these new opportunities into overdrive and go beyond our previous comfort zones. Blue tones continue to be dominant, but are accompanied by intense shades such as pink, orange and turquoise – ideal as accent colours to create a focal point without overwhelming the room. • “metox”: includes very calm colours that are more on the cool side. Greys, blues, greens and beiges are the key colours that can be used for colour schemes in our homes. “Now close to the end of another slowed-down year, we’re really craving what comes next, for the chance to move forward and re-experience life following the intense focus on our behaviours, lifestyles and desires,” comments Franziska Hammerl, Segment Head Decorative and Wood Coatings, Global Technical Marketing Coatings at Heubach.
Heubach’s Colour of the Year: memory gold
Heubach’s Colour of the Year was formulated with Colanyl® 500 pigment preparations and mixed with SHINEDECOR C393, a brand new readyto-use golden pearlescent effect pigment concentrate for water-based paints from Heubach’s styling partner, Eckart, to get the final antique and sparkling golden tone. “Memory gold is set to be an ever-present through 2022, perfect for accenting, or for colour drenching and blocking techniques to partner other colours of the years announced by decorative coatings brands. The combination of a neutral gold shade and effect pigment brings something meaningful and special to homes and lives,” adds Franziska.
For further information: www.clariant.com/pigments
GemaConnect: Visualizes, Analyses and Optimizes the Coating Process
Gema launches the new GemaConnect software, which has been developed in order to allow users to check the powder coating equipment’ performances, regardless of location or time.
GemaConnect is Gema’s new production information tool that provides the user with full transparency of the current status and performance indicators of the powder coating equipment, regardless of location or time. The web-based tool stores real-time powder coating data and provides comprehensive monitoring and analysis capabilities from a single source. With dashboard visualization and data analysis of key coating indicators, operators, maintenance personnel and management are provided with validated tools. This enables them to make quick and informed decisions to effectively improve their individual powder coating process and equipment performance. In addition to viewing real-time information on the production status and maintenance and operational status of the plant, users can put customized indicators and favourites on their screens. In this way, they always keep critical areas in view. Furthermore, GemaConnect provides historical information about the performance and utilization of the plant as well as relevant process parameters. GemaConnect is suitable for all companies that want to improve their overall operational efficiency, maximize resources and reduce operating costs. Production managers and senior executives use GemaConnect to continuously monitor the coating process. This improves the utilization of coating equipment, optimizes production flow and increases the bottom line. The software also offers the possibility of preventive maintenance, which increases the availability of the equipment.
For further information: www.gemapowdercoating.com
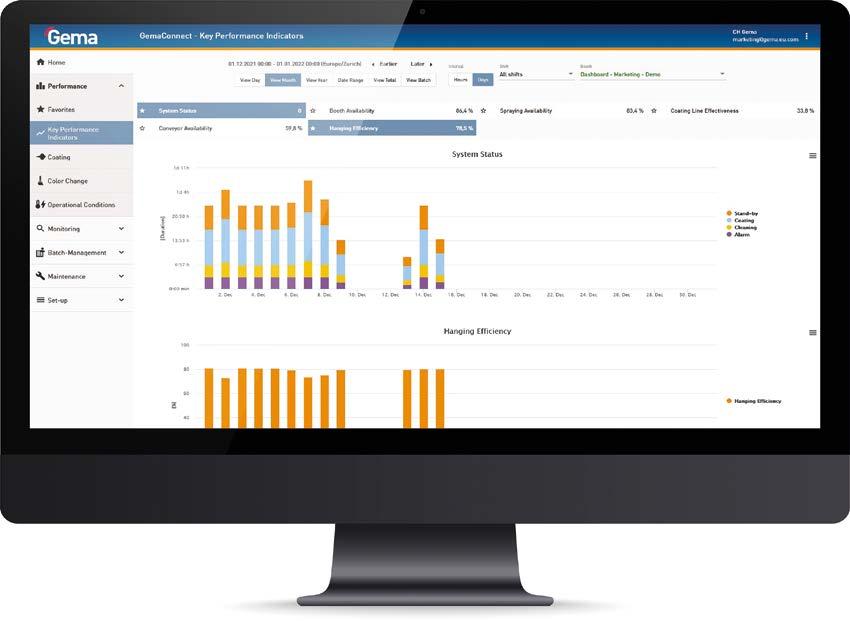
© Gema
A New Glass Coating Plant as a Tailor-Made Suit for Ever More Striking and Attractive Finishes
Monica Fumagalli ipcm®
Metallising and coating: this is Plast-met Metallizzazione’s winning combination for providing high-quality coatings for glass and plastics. Recently, its partnership with plant supplier M.I. DUE has enabled it to cope with an increasing number of requests and achieve unrivalled quality performance in terms of customised finishes.
© Plast-met
For more than fifty years, Plast-met has specialised in metallisation, iridescence, and coating processes for semi-finished plastic, glass, and metal alloys. One of the most popular effects is iridescence.
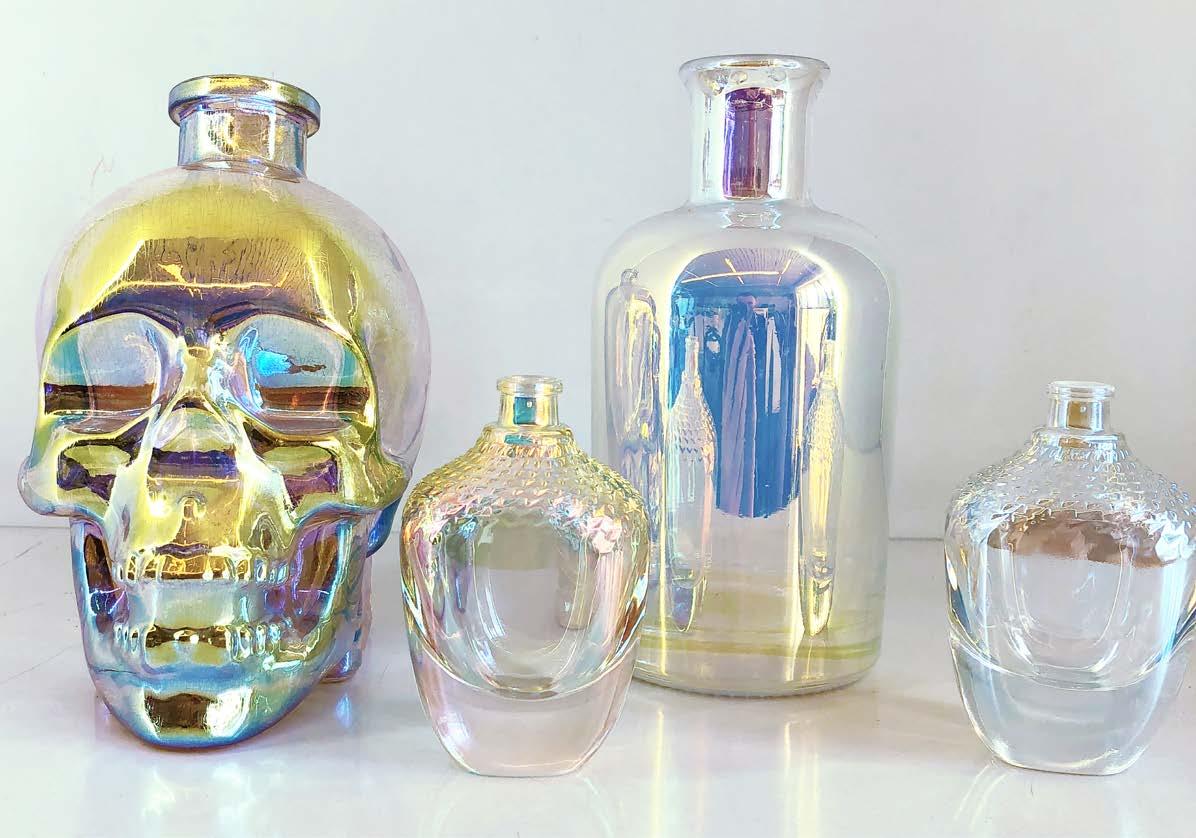
Transforming what is not metal into metal: this is the essence of the process called “metallisation”. In 1835, German chemist Justus von Liebig coated a sheet of glass with a layer of silver nitrate for the first time. This was the first case of metallisation: it was a revolutionary process at the time, because it led to the industrialisation of mirrors, which until then had been considered a niche product due to the high costs involved in their complex manufacturing process. Nowadays, this technique has reached high levels of development and it can be applied to all non-metallic materials, such as ceramics, plastics, and glass. “The potential customisation options that this process makes possible are very wide-ranging,” explains Mauro Cremonesi, Plast-met Metallizzazione’s sales manager, who, together with his brothers Piergiorgio and Corrado, runs this company founded by their parents Nino and Rosi in Cassano d’Adda (Milan, Italy) over half a century ago. Its initial mission was the metallisation of components for model cars, but it has evolved over time to expand the firm’s service portfolio up to including the metallic coating of plastic and glass for the design, fashion, food & beverage, and cosmetics sectors. “Metallisation is a very delicate treatment that consists in applying a layer of metal, in our case aluminium, which is transformed into a film with a thickness of less than 1 micron through sublimation and condensation at a low pressure (10-4 Torr). It has immediately been a huge success because its results are aesthetically attractive and impress with their shimmering colours. Thanks to metallisation and iridescence – that is, the particular effect also known as Aurora Borealis whereby coatings change colours as the light changes – the treated products can reflect the enchantment and preciousness of gold and the luminosity and
© Plast-met © Plast-met

Metallised bottles with an ice effect. Some bottles metallized and coated by Plast-met.
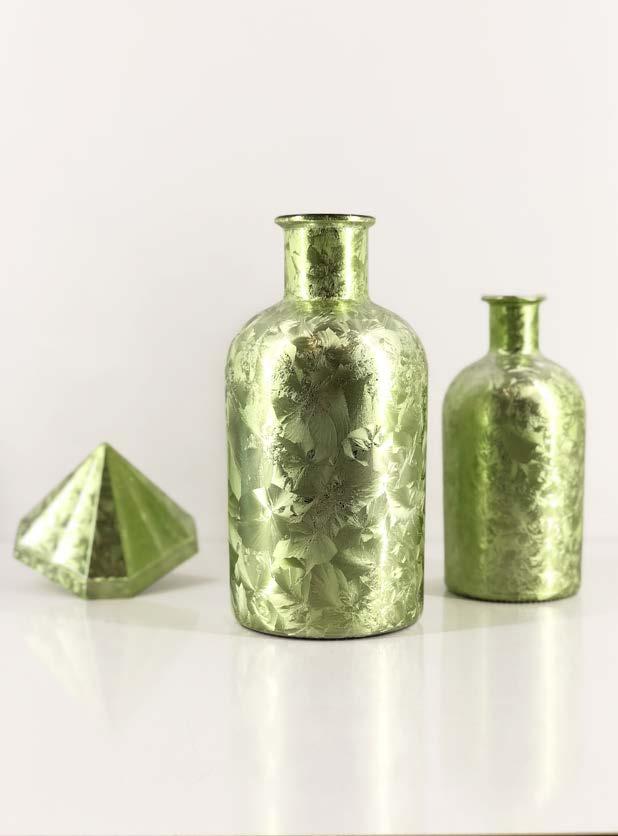
A bird’s eye view of the glass bottle coating system installed by M.I. DUE Srl (Besana in Brianza, Monza e Brianza).

© Plast-met
reflections of silver in a wide range of colours and finishes.” In order to offer this infinite variety of effects, Plast-met has equipped its factory with state-of-the-art equipment.
Plast-met’s plant equipment
“We have installed three of out our six PVD systems over the last five years,” notes Cremonesi. “Our knowledge of the metallisation process has gone so far that our own team designed and installed two of these systems with the aim of achieving iridescent effects, which have been so successful in recent years. In our metallising department, we have integrated the most technologically advanced metallisation machines, so that the average cycle time for treating batch components is now 6 minutes. The same high productivity had to be achieved in our paint shop.” The coating department is equipped with three plants. The first one is a manual system installed in February 1996 and equipped with six stations for coating small parts after metallising. The second one is a semi-automatic machine with load bars handled by an inverted conveyor, designed and installed by M.I. DUE in June 2017; it is equipped with a water-curtain booth for application of UV coatings on small plastic objects, such as caps and packages for the cosmetics industry. The third one is a fully automatic plant with two watercurtain coating booths; also designed by M.I. DUE, it was started up in February 2019 and it is devoted exclusively to the coating of glass bottles.
Plast-met: the experts of glass metallisation and coating
“For about eight years now,” says Cremonesi, “we have been specialising in glass metallisation and coating. Both processes are very
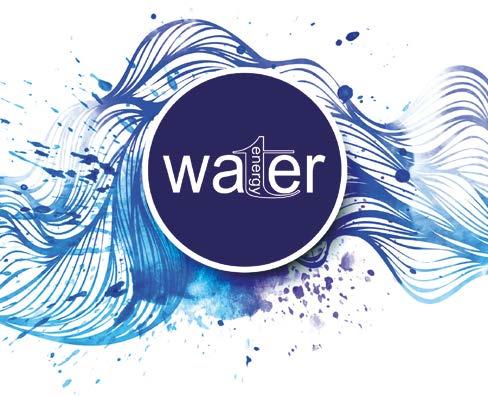
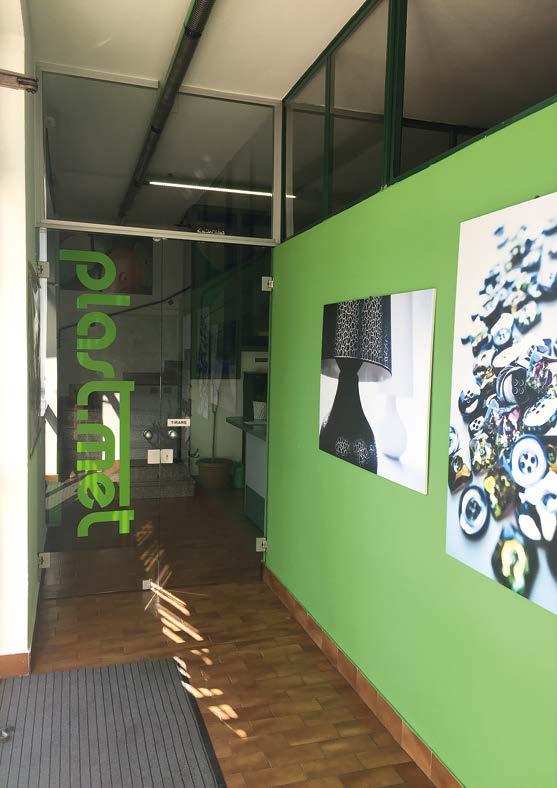
The entrance to Plast-met’s headquarters in Cassano d’Adda (Milan).
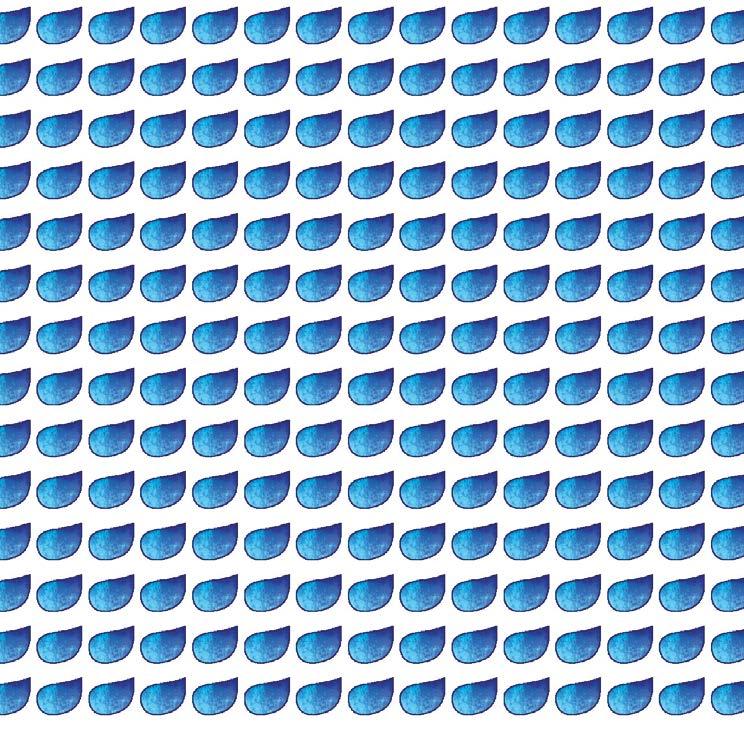
© Plast-met
delicate due to the inherent characteristics of the material to be treated. In particular, the coating of glass requires the application of specific paints. Some time ago, we had reached such a high daily production capacity that it was necessary to invest in a new, fully automatic plant to relieve our employees from coating operations. We were looking for a plant solution that would not only cope with peak production volumes, but also enable us to improve our coating quality level and create finishes that were ever more attractive. We therefore analysed the best solutions available on the market: M.I. DUE was the answer we were looking for, both because of its long-standing experience in the design and manufacture of systems for coating glass and plastic components, including metallised ones, and because of the quality of its systems, confirmed by its partnerships with numerous leading companies in our sector. M.I. DUE has proven a reliable supplier, capable of creating a
Get more from water
Turn key solutions for industrial wastewater treatment Design and manufacturing of plants and chemicals for industrial wastewater treatment Chemical-physical plants Sludge treatment and compactor systems Ion exchange demineralization systems and reverse osmosis systems Oil separators Filtering systems Batch type systems Flotation units Chemicals and spare parts for water treatment Technical service, support and maintenance of wastewater treatment plants
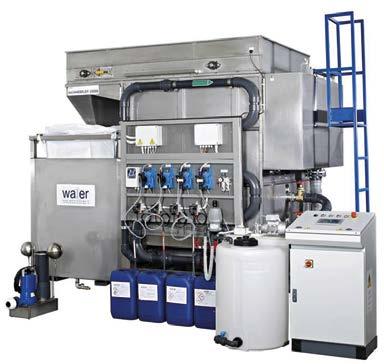
Beware of imitations, buy the original!
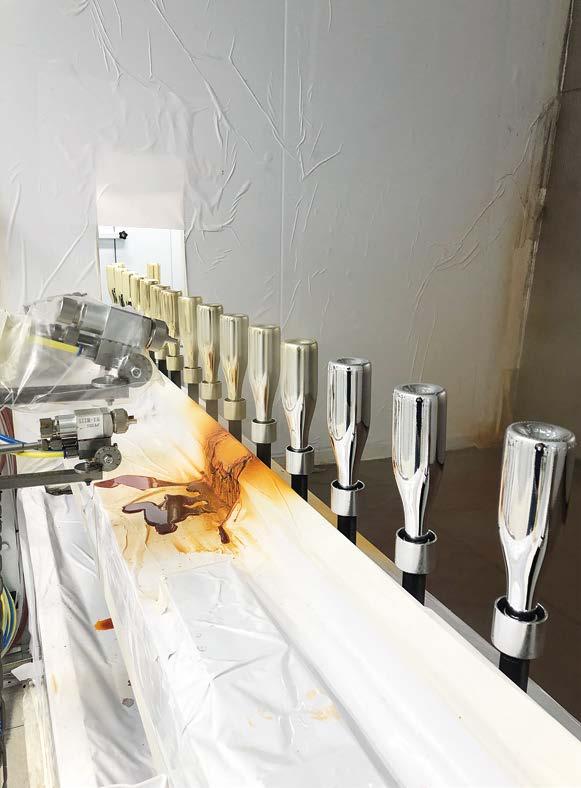
© Plast-met © Plast-met
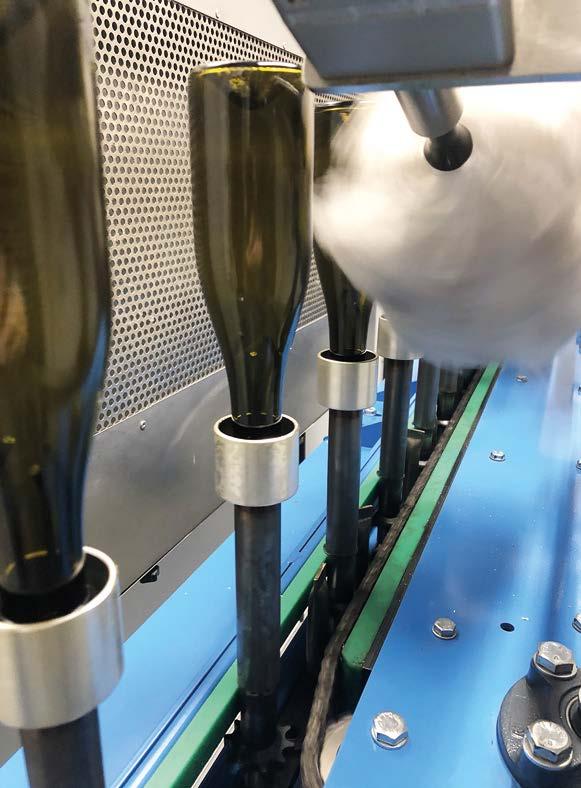
The brushing phase with synthetic brushes.
customised system based on our requirements, particularly in terms of available space and specific technical features.”
The new coating system as a made-to-measure suit
“The line consists of a single-spindle inverted conveyor with a variable speed,” indicates M.I. DUE owner Carlo Casiraghi, “with a manual loading and unloading area. The bottles are loaded onto the racks and sent to the following stations: brushing, de-ionised air dedusting, and flame hardening; the latter features flame heads positioned at different heights, so that the top one acts on the bottom of the bottle and the others act on its middle and neck. As this operation greatly overheats their surfaces, the bottles are then sent to an air-conditioned chamber to reduce their temperature. After flame hardening, the workpieces are transferred to the first booth with a double roller for base coat application. This phase is followed by flash-off, polymerisation in the oven, and passage through a cooling tunnel at room temperature.” If the bottles need to be metallised, after cooling, they are unloaded from the conveyor and taken to the vacuum machine for substrate metallisation. They are then taken back to the coating line and loaded for entry into the second booth, identical to the first one, where the top coat is applied. At the end of the cycle, the bottles pass through the drying oven and the air-conditioned cooling tunnel so that they can be handled immediately for unloading and packaging.
Application of the gold-effect top coat.
Behind the scenes of the plant’s design phase
Some of the technical features of this plant have been implemented