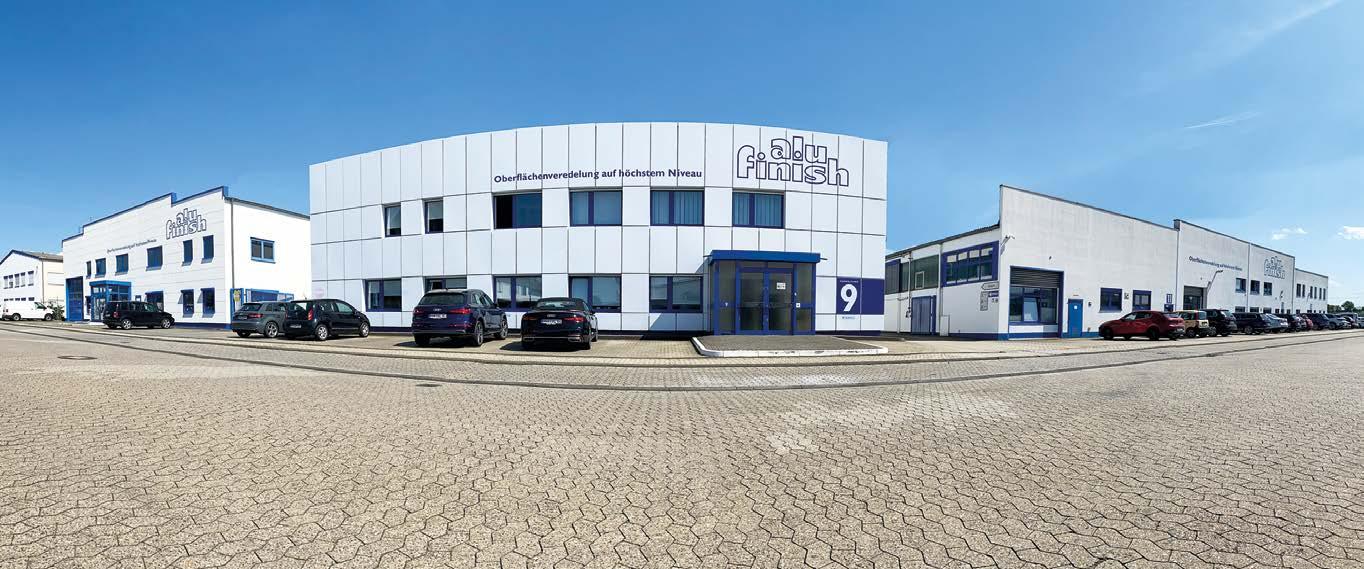
16 minute read
HIGHLIGHT OF THE MONTH
From a Family-Owned Business to an International Supplier of Pre-Treatment Products: Cooperation and Partnerships as Corporate Pillars
Interview with Nils Monreal and Stephan Zegers
Alufinish GmbH & Co. KG – Andernach (Germany)
Cooperation, global partnerships, and flexibility: these are the key elements that allowed the German developer of surface treatment products Alufinish to succeed in its field. During the celebrations of the 50th Anniversary of its foundation, we interviewed the managing directors Nils Monreal and Stephan Zegers to better understand the growth strategy of the company.
Anniversaries are a joyful time and are also a good moment to reflect on both the past and the future. This is especially true for the foundation anniversary of companies, that can transform the celebration into an opportunity to provide an overview on the past accomplishments as well as to plan for the future. Alufinish GmbH, a developer and manufacturer of chemical pre-treatment products and processes for aluminium, steel and zinc surfaces based in Andernach (Germany), is celebrating its 50th anniversary. In the last issue of this magazine, we dedicated an article to the company’s history. So, this time we have visited their site to interview Nils Monreal – the son-in-law of one of the original founders – and Stephan Zegers, the managing directors of Alufinish GmbH & Co. KG. They provided interesting insights into the strategies that ensured the success of Alufinish, the current developments of the surface treatment industry and the future trends that the company foresees.

How do you feel when thinking about the 50th anniversary of Alufinish? Do you consider it a very important landmark?
“It makes you feel old,” jokes Stephan Zegers, the first who started to answer to our questions. “But seriously, I think it’s a great achievement for a privately-owned company, which is quite rare these days. The founder Otmar Monreal understood that the pre-treatment of metal surfaces needed quality products and processes, because this sector offers a lot of opportunities for several industries. So, fifty years ago he entered this niche market and tried to provide the best solutions available at that time. The celebration of this anniversary means that his actions and vision have been successful. I am very proud of that.”

What do you consider to be the company’s greatest successes over the past 50 years?
“Our company has established its success on several small activities that ensured its growth over the course of fifty years. We started as a small familyowned business that manufactured standardised products through standardised processes and, over time, we innovated and grew bigger and bigger until we reached the global diffusion and the production capacities of today,” continued Zegers. “There is not a single key success, although we are very proud of our achievements such as the improvements in the quality of the products, their carbon footprint, and our efficient and environmentally friendly production processes. Our greatest success is then a combination of all the activities that allowed us to become what we are today,” added Nils Monreal.

Both the world and the industry of surface treatments have changed a lot since the foundation of Alufinish. How have your services changed over the past fifty years?
“They have not, that is another important aspect. Let me explain better: we have been able to anticipate the evolution of the market, we innovated and modified our production processes, we improved our internal organisation and adapted the business to the new emerging customers’ needs and requests, but the core of our services has remained the same,” clarified Zegers. “The expectations of our customers have become increasingly higher, so we acted accordingly. When we started the operations, we delivered the products by bike”, remembers Monreal. “Nowadays we have a global network of suppliers and we ship all over the world, so we now obviously rely on more sophisticated logistics processes. But our corporate mission and, therefore, our services are the same: to provide the best and high-performing solutions for the quality pre-treatment of metal surfaces.”
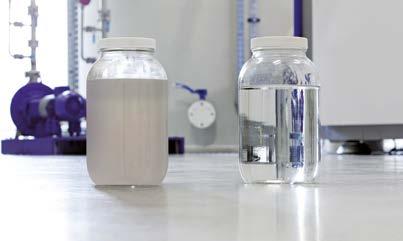
However, we guess both you and the industry as well have faced several obstacles and challenges. How has Alufinish overcome them?
Zegers: “There have been undoubtedly some difficulties, such as the 2008 global economic crisis or the recent increase in the price of raw materials and their shortages, but our two corporate pillars have allowed us to overcome them. First, we decided to differentiate our production and offer solutions for several sectors. When the automotive market dropped down, we focused more on architecturerelated services, as we were also specialised in processes for aluminium facades with ENVIROX NR. Second, we have also valued the human capital as the most important resource of our company. The greatest challenge we have ever faced is to create a successful team and retain it. Thus, we have been able to optimise our pipeline. The communication and the data flow between the teams is excellent and the production stages are perfectly interconnected, so every aspect of them is carefully planned and executed: from the development and design phase to the production, from the quality control to the post-sales assistance. This does not only include our personnel at the Andernach site, but also our suppliers as well.” Monreal: “Or we should say, partners. Answering to the new requests of the clients quickly and efficiently is very difficult, so we rely on a global network of partners that distribute our products but also help us to stay in contact with the customers, to listen to them and act promptly as soon as they need our help. Just supplying products is not enough
Your Leaders in Zero Liquid Discharge
Industrial Wastewater Treatment
Simple Principle
Effective Result
Leading companies rely on vacuum distillation systems for the sustainable treatment of industrial wastewater.
Do you want to benefit from a zero liquid discharge production with VACUDEST aswell?
Visit us at IFAT Munich! Hall A2, stand 147
© Alufinish
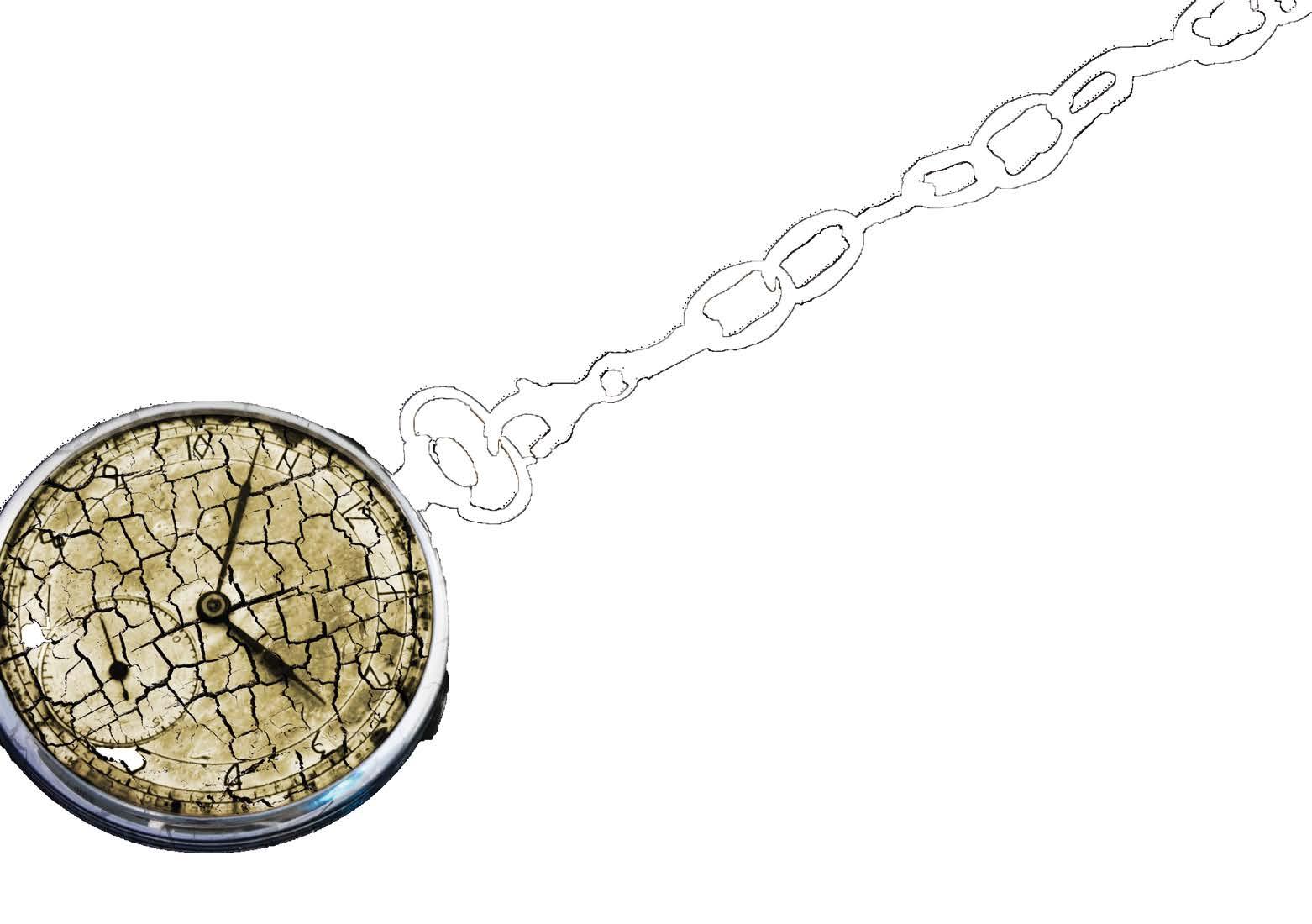
to succeed in the market, you should also interact with the customers, understand their processes and develop together the most suitable solutions.” “Let me add something here. Mr. Monreal rightfully said that we really value the efforts of our team. As a matter of fact, we also focus on improving the know-how of everyone involved. When, for instance, a technician is planning to retire, we will have them flank a younger operator not just for a couple of months, but for years. We want to provide a natural overflow of competences. In this way, also the customers find themselves comfortable with the new staff of Alufinish. The same happens with our partners. We have been working together for several years, we share valuable information and knowledge and we keep updating each other. Different countries have different laws, regulations, materials, climate, temperature and water quality. Obviously, a single product developer cannot know them all, so cooperation is extremely important,” explained Zegers.
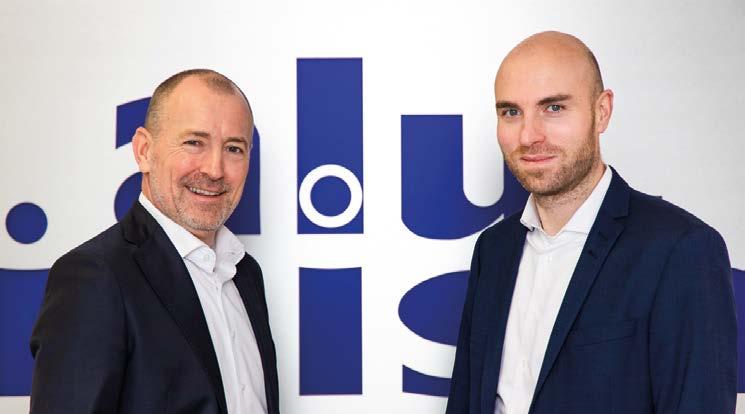
We talked about the past, now let’s focus on the future: how do you think the aluminium surface treatment sector will change in the next 5 to 10 years?
Monreal: “This is a very interesting question. I think that the aluminium sector will expand
Stephan Zegers (left) and Nils Monreal.
its market in new areas of the world, as aluminium can be a very useful material for several sustainable applications. For a company operating in the pre-treatment industry, the key for a successful industrial expansion will be to identify what will be included in the surface treatment sectors in the next years: there might be new bio-based raw materials, new packaging solutions, new process technologies. It will be important to stay up-to-date with the evolutions. In addition, also energy efficiency and the recycling rate (second and even third usage of materials) will likely play a very important role.” Zegers: The sector needs also to find efficient ways to handle procurement and shipping, in order to have positive effects on the entire carbon footprint. To do so, it is important to develop successful business relationships with suppliers and all the other partners. Creating a trustworthy network can help to better manage all the aspect of the business operations. From the procurement of raw materials to the shipment of the products and the post-sales assistance”.
That is why Alufinish motto is “Build on Trust”, isn’t it?
Zegers: “That is correct. If we build the future together, we can successfully face all its challenges. We really value the trust given by our partners, they believe in our activities and products as the best solutions to treat surfaces and excel. We listen to both our partners and final clients, so we are able to improve the processes involved and save costs for everyone. The core value we stand for is that we are more than just a supplier, we are the partner you can trustfully rely on: service-orientated, flexible and adaptable. It is a big responsibility, so cooperation is the key.”
Finally, can you introduce our readers to the latest developments of Alufinish?
Monreal: “We are focused on environmentally friendly chrome-free and boron-free products based on titanium and zirconium, suitable not only for aluminium but also for steel and hot dip-galvanised surfaces, as well as on new and optimised handling and cleaning properties. We are also working to help our clients on the anodising site to improve their etching processes with our additives that ensure better drainage and low foaming, and we increased our efforts on sealing products that are more environmentally friendly: nickel-, cobalt- and heavy metal-free systems. Since 2018, we started a partnership with a supplier for a full range of organic dyes, from those dyes many are also heavy metal free.”
The continuous-flow powder coating plant for aluminium coils.
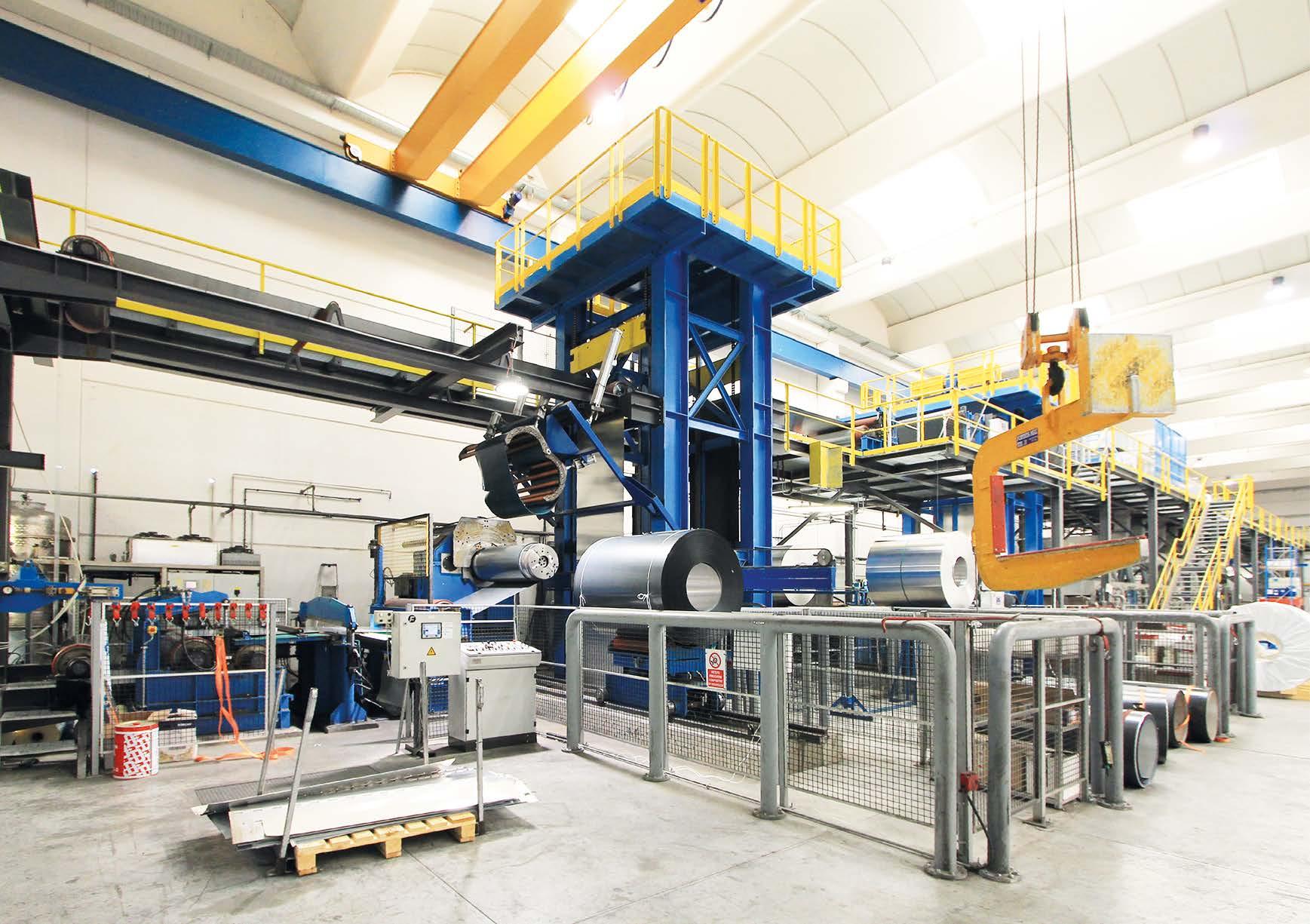
FOCUS ON TECHNOLOGY
SPECIAL ISSUE ON ARCHITECTURE & DESIGN
AluCoating Chose Catalytic IR Technology to Speed up Powder Coating on Aluminium Coils
Monica Fumagalli ipcm®
Making a coil coating line more compact through the most advanced plant innovations: AluCoating, a company specialising in the powder coating of aluminium coils, has chosen the catalytic IR technology developed by Infragas Srl to speed up its process without over-expanding its plant.
In the coil coating industry, where the volumes of materials to be processed are extremely high, line speed is simply crucial. In order to understand its importance within a production cycle, exactly one year after our previous meeting1, we returned to visit AluCoating Srl in Corzano (Brescia, Italy), which was among the first companies to specialise in the powder coating of aluminium coils. “We coat our coils at a speed of 7 m/min, but we aim at increasing it even further,” states AluCoating owner, Paolo Di Massimo. “However, one of the bottlenecks we encounter is related to the drying phase needed after pre-treatment and to the powder coating’s curing phase: the size of the oven that would be required to accommodate our production speed is not acceptable for the space we have available. This has prompted us to look for a solution that would guarantee very fast drying and curing phases without expanding the length of our line with the installation of large-sized ovens. Eventually, we found it in the catalytic infrared panels manufactured by Infragas Srl (Mappano, Turin, Italy), capable of optimising the heat treatment of powder-coated coils.”
1 https://www.ipcm.it/en/open/ipcm/2021/69/52-58.aspx
© ipcm A compact coil coating line
AluCoating’s production department is equipped with a modern continuous-flow plant for powder coating aluminium coils and a line for roll flattening and cutting the end products into different formats. This compact line carries out the following treatment process: • levelling by means of a 17-roller sextuple machine; • surface cleaning by spray pre-treatment with alkaline and acidic products to prepare the coils for further processing; • conversion by a chem-coater with the application of no-rinse chromium-free products (fluotitanation and fluozirconation); • electrostatic application of powder coatings specially developed for post-bending processes; • powder curing by gas catalytic infrared irradiation; • application of a UV-resistant clear or white/black self-adhesive film to protect the coated surfaces during subsequent processing and installation phases.
“From the earliest processing stages to the latest ones, when we prepare our pre-coated coils for shipment to customers,” emphasises Di Massimo, “each station is designed to minimise the equipment’s
The movable platform with the two Gema booths.

© ipcm
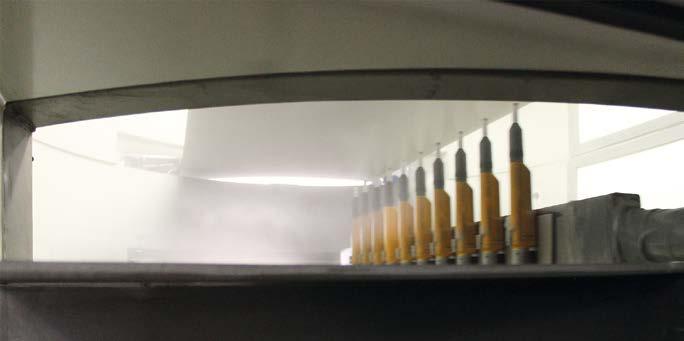
© ipcm

© ipcm footprint while maintaining maximum process efficiency. From the pre-treatment system onwards, we have tried to keep our line compact and effective by doubling the number of rinses for more effective cleaning operations. In fact, we carry out an initial cleaning phase followed by two rinses to remove grease residues, an acid cleaning phase to remove surface oxides remaining on surfaces after lamination, two further rinses (one with mains water and the other with demineralised water), and the final conversion stage using a chem-coater. The waste water is filtered and recirculated by the closed-loop water treatment system and the sludge disposed of every three months.”
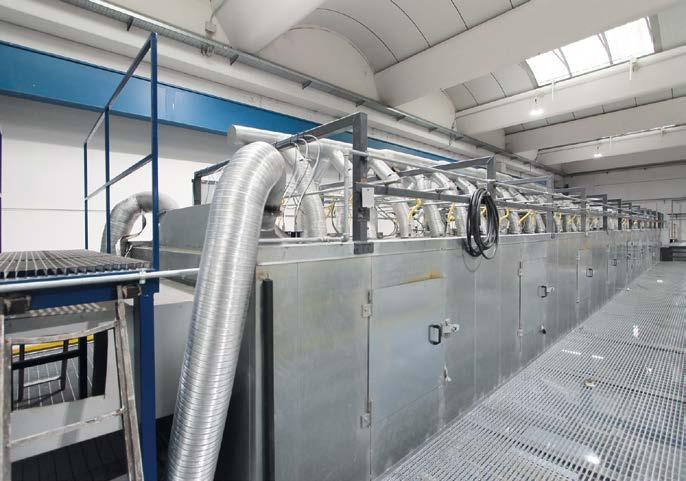
Comparison between liquid and powder coating processes
“As already mentioned during your visit last year,” adds Di Massimo, “the shift from liquid coil coating to powder coating, which has been the trend of the last few years, is still in full swing. At the same time, new powder application and curing systems are being developed that do not compromise the compact design of coil coating plants with the integration of oversized heat treatment systems.” The drying phase of liquid paint applied to coils is very different from that of powder paint. “In the case of liquid coatings,” explains Di Massimo, “air flow and air pressure parameters can be adjusted in order to achieve optimal heat exchange with drying times of up to 30 seconds, precisely thanks to the higher temperatures. With powder, on the other hand, a higher airflow might remove a part of the applied coating, as it is a very volatile product; in this case, therefore, the two parameters must be set to lower values, although this leads to longer process times. This is why we looked for a solution that would allow the fastest heat transfer to the top of coils – and we found it in Infragas’ IR catalytic panels. We installed them both in the drying station after pre-treatment, where they operate at temperatures of 70 °C, and in the curing station, where they operate at temperatures of 240 °C for a cycle time of 2 ½ min in a 20 m long oven.”
From top to bottom: The set of dispensers in operation, the nitrogen generator module and the powder centre, the curing oven.
The two IR technology stations
The two stations with IR technology, therefore, were installed for drying the treated coils after conversion with the chemcoater and for curing them after powder application, as Di Massimo indicates: “After conversion and before the application of the first layer of paint, the coils are dried using IR technology; after powder coating application and before curing, the second Infragas system helps us significantly reduce our drying and curing times.” “The devices installed at AluCoating’s premises,” says Francesca Marabotti, marketing manager at Infragas, “belong to our Boostercat 25K series, representing the enhanced (Booster) model of Infragas’ catalytic IR panel family, characterised by a built-in ventilation system located on the back of the burner. In other words, these catalytic infrared gas panels are complete with rear flanges connected to the air inlet pipes on the back of the machine, in order to enhance gas oxidation and combine the infrared effect with the convective effect.

© ipcm
The infrared panels positioned after the entrance to the curing oven.
ALUMINIUM vertical and horizontal plants over 60 years of experience in surface finishing lines
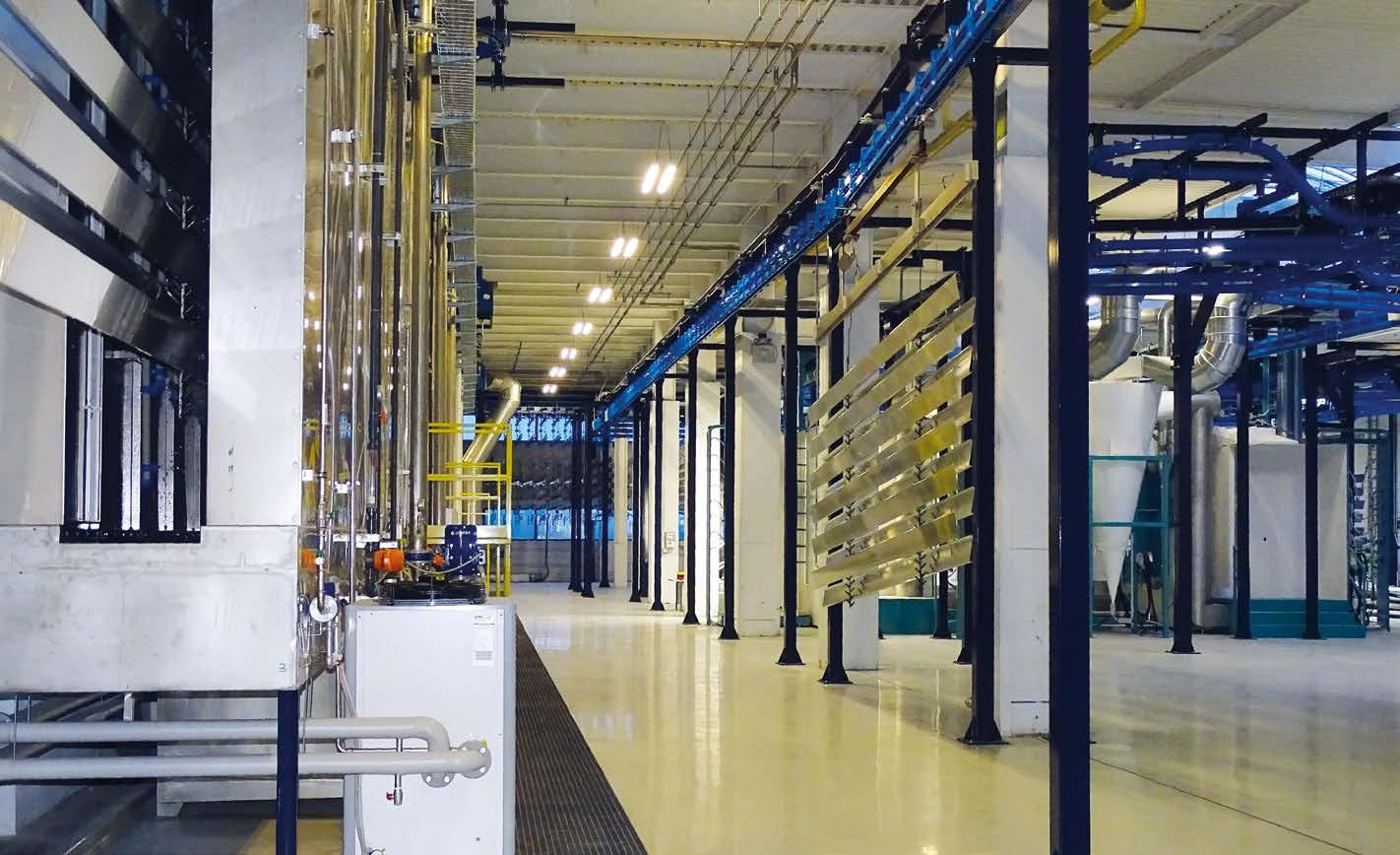
The power density of the Boostercat devices is 30 kW/m2 and the maximum surface temperature is 650 °C.” One of the advantages of installing these panels is the uniformity of the heat treatment carried out on the coils’ surfaces. “We have equipped the panels with three gas inlets in order to expand the inlet capacity and make the radiating area of all sides of the coils as uniform as possible,” adds Marabotti. “Powder coating is ideal for this technology, because the organic material absorbs infrared rays very well. A further benefit is that, with catalytic IR technology, the coils do not overheat and they can be subjected to final rolling immediately after curing, without the need to wait for them to cool down.”
Energy benefits
The ability of catalytic technology not to heat the air and to concentrate its action on the workpiece means that no energy is wasted. “One of the most important requirements of recent times is precisely that of energy consumption,” states Marabotti. “Infrared technology actually represents an optimisation of metal heat treatment.” “During pre-curing,” confirms Di Massimo, “it also has the advantage of ‘locking’ the powder onto the surfaces, thus preventing contamination between coils – an aspect not to be underestimated, in an industry that is becoming increasingly demanding in terms of thicknesses and surface quality.” Recently, the IR system by Infragas has been upgraded with Radiant High Temperature gas burners to further speed up the coils’ curing phase. “They are pre-mixed infrared systems that reach a surface temperature of 950 °C and have a power density 10 times higher than that of catalytic panels, which have 30 kW/m2 power compared to RHT burners’ 180 kW/m2. This solution requires several trials in order to find the perfect balance of the heating parameters, but with sustained speeds such as those of AluCoating and considering that the coil coating industry is always aiming at maximum line speeds, it could be the ideal solution.”
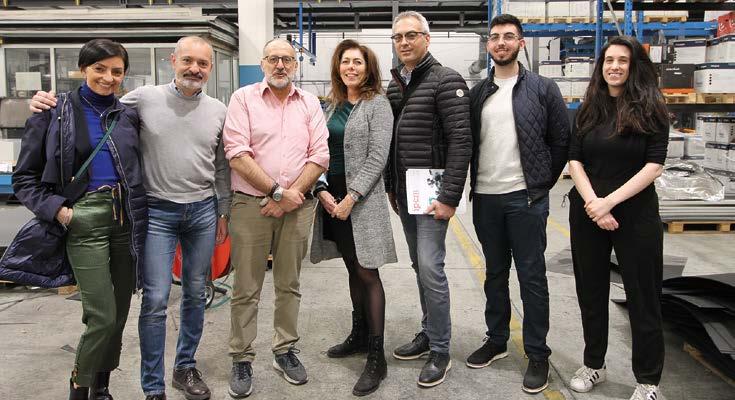
Technical specifications of the BOOSTERCAT 25K system with rear flanges
Dimensions: 492 x 1841 x 311 mm Electricity consumption for pre-heating: 1210 W Supply voltage for pre-heating: 230 V Pre-heating control: type K thermocouple, 2 m long cable Pre-heating time: 10’ Wattage: 25.0 kW max – 15.0 kW min Natural gas pressure: 20 – 8 mbar (200 – 80 mmH2O; 2 – 0.8 kPa) Natural gas consumption: 2.5 m3/h max – 1.5 m3/h min Propane pressure: 37 – 15 mbar (370 – 150 mmH2O; 3.7 – 1.5 kPa) Propane consumption: 1.87 kg/h max – 1.12 kg/h min
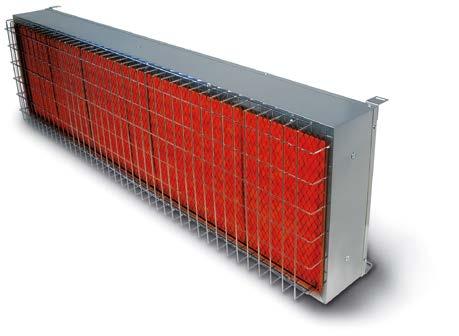
© ipcm