
19 minute read
BRAND NEW
The new versatile viscometer line of BYK-Gardner offers robust measurement and repeatability.
BYK-Gardner GmbH, a manufacturer of quality control instruments and tools for colour, appearance and physical properties, has recently announced that it has developed the byko-visc RT Rotational Viscometer. The new solution allows precise measurement results with each test condition recorded and offers detailed results analysis and review. The Rotational Viscometer has been specifically designed to test the viscosity of liquids and pastes in compliance with ASTM D2196, ISO 2555 and ISO1652 standards. It is then suitable to test the viscosity of lacquers, paints, primers, resins, lubricants, pharmaceuticals, creams, lotions, liquids soaps, beverages, dressings and sauces. The product is available in two different models: the byko-visc RT and byko-visc RT Lite. They both feature versatility and compatibility with three different sensitivities and optional accessories. In addition, the company supplies an ISO 17025 calibration certificate with each instrument, in order to confirm its performances. The byko-visc RT offers an intuitive navigation thanks to its colour touch-screen display – that features pre-set buttons to quickly recall often used measuring parameters – and several other control options, allowing to reduce operation times. Furthermore, it includes an easy snap-on spindle attachment to protect the instrument and an adjustable stand to allow the operator to easily raise and lower the viscometer head. The precision of the measurement is repeatable day-to-day and instrument-to-instrument as the new line developed by the company is also compatible with many other rotational viscometer models in terms of results, measurement parameters and accessories. As well as the new byko-visc RT Rotational Viscometer, BYKGardner offers also a wide range of viscosity instruments, such as flow cups, bubble viscometers, the digital stormer viscometer and cone and plate viscometers.
© BYK-Gardner GmbH
For further information: www.byk-instruments.com/en
Dr. Lan Deng Is the New Director of ChemQuest
Deng will work on improving the sustainable innovations and growth of ChemQuest.
The ChemQuest Group, an international business strategy and external technology development firm focused on the specialty chemicals markets, has recently announced that it has appointed Lan Deng as director. Deng has obtained a B.E. in polymer materials and engineering from the University of Science and Technology of China and a Ph.D. in chemistry from the University of California - Berkeley. In addition, she has co-authored six journal articles and holds sixteen granted patents. More recently, she received the R&D 100 Awards and the EPA’s Presidential Green Chemistry Challenge Award. The new director of ChemQuest has over fifteen years of experience in the chemical industry, as she covered several leadership roles in Dow Chemical, Sherwin Williams and PPG. Before joining the company, she has been in fact the Global Technical Director for Automotive OEM business within PPG, where she oversaw the development of pre-treatment products, E-coat, primers, basecoats and clearcoats, as well as adhesives and sealants. “Our society is at a point when the next innovation wave is starting to pick up and accelerate. There are tremendous opportunities in health care, sustainable energy and digital transformation. The companies that can seize the opportunity to ride these waves will have long-lasting competitive advantages in the decades to come. As a technology leader, I want to help more companies, public or private, to catch and ride these waves; I also want to help the capital market find the right growth opportunity to invest so that our whole economy can benefit,” stated Deng. “ChemQuest can provide me an opportunity to do just that. I look forward to partnering with my colleagues and clients to create sustainable innovation and growth for the society.” “We are fortunate to have someone with Dr. Deng’s depth of experience and capabilities join our team. Her passion for innovation, growth and job creation, and her strength in partnering with customers to create mutual value will help both ChemQuest and our clients to create win-win,” also declared Dan Murad, the CEO of ChemQuest.
For further information: www.chemquest.com
GLOBAL SOLUTIONS FOR WATER TREATMENT
with a complete service that includes system design manufacturing installation technical support chemicals
SPRAY BOOTHS WATER SLUDGE REMOVAL RESIN DEMINERALIZATION SYSTEMS REMEDIATION OF CONTAMINATED SITES BIOLOGICAL SYSTEMS BATCH TREATMENTS PHYSICAL-CHEMICAL SYSTEMS ADSORPTION FILTRATION REVERSE OSMOSIS MEMBRANE SYSTEMS EVAPORATORS BIOGAS BIOMASS SYSTEMS OIL SEPARATORS DESANDERS DESALINATION SYSTEMS PYROCHAR OTHER SYSTEMS CHEMICALS
British Coatings Federation Reports Negative Impact of Brexit on Coatings Industry
According to the latest report by the British Coatings Federation, Brexit has had a negative impact on the coatings sector’s trade with the EU.
According to a new survey of British Coatings Federation – which set out to measure its member companies’ experience of the UK-EU Trade and Co-operation Agreement (TCA) – while a few firms managed to retain or increase exports, the majority of survey respondents saw exports to the EU fall over the past 15 months. Members also reported they had experienced a significant increase in operating costs due to the various new rules, procedures, and knock-on effects of the UK-EU TCA. Conversely, there was, as yet, little sign of compensating growth in trade elsewhere in the world due to new FTAs. Moreover, there is still substantial concern about the future UK chemicals regulation regime, particularly UK REACH, and how this will impact on future business competitiveness.
Some data
Nearly one in six members (59%) reported increased operating costs due to Brexit of more than 4%. Nearly a third (32%) said it had added more than 6%. One in ten had experienced additional costs of more than 15%. Nearly four in ten (39.5%) reported that exports to the EU had decreased, with a plurality losing between 6-10% of exports over the last year or so, although some significantly more. Logistics remains the biggest issue for members: availability of hauliers (69%), delays to shipments of raw materials coming into the UK (67%), and cost of shipping (64%) are the most commonly cited ongoing problems due to Brexit. Nearly a quarter of members (23.1%) reported that EU suppliers no longer wanted to export to the UK, up from 19% last year. Looking ahead, regulatory issues still loom large in terms of worries over future business competitiveness. The top three concerns cited were: © Adobe Stock additional trading costs due to customs paperwork (59%); the impact of future divergence of UK REACH from EU REACH (59%); and the impact UK REACH could have on raw material prices in the UK (61%). “The Government needs to work harder with businesses to help make exporting to and from the EU easier, ideally looking to enhance the terms of the TCA. Instead, it looks as though things are moving in the opposite direction with threats to trigger Article 16 of the Northern Ireland Protocol which could collapse the whole trade agreement. That would be a disaster for industry, especially given we are in the middle of the worst global raw material and supply chain crisis seen for a generation”, says Tom Bowtell, CEO of the British Coatings Federation. “Looking beyond the EU, we need to see more support for UK businesses growing their exports to the rest of the world. At the moment, despite new FTAs being signed and talked about there seem to be few opportunities developing for our sector. BCF will be playing its part by working with the Department for International Trade, most imminently through a joint export seminar in Manchester next month”. “Finally, we must not take our eye off the regulatory ball. Our survey showed problems and concerns about UK REACH have slightly diminished since this time last year. This is probably because Defra has said they are looking at a new model that should hopefully be less burdensome on industry. However, those concerns about REACH are still substantial and loom large over our members’ future business competitiveness. We need to see Defra come up with a new approach for UK REACH as quickly as possible to provide businesses with the certainty they need to plan, and the ability to access a full range of necessary substances to aid innovation in future”, he concludes.

For further information: www.coatings.org.uk
Anton Paar Will Construct a New Technology Centre
The headquarters of Anton Paar in Graz (Austria) will be expanded to include a new technology centre.
Anton Paar, the manufacturer of measurement instruments and technologies, has announced that it intends to expands the company’s headquarters in Graz-Straßgang (Austria) to include a new technology centre. The new technology centre will cover an area of 26,800 m2 and will include all business units as well as the central research and development department, while the three oldest buildings of the site were demolished. The expanded site will be characterised by an open space concept to serve natural ventilation and will also include two atriums that allow the interior rooms to be supplied with natural light. “The planning for the new technology centre began back in 2014. However, a development plan obligation and restrictions on the height of the building delayed the project by year. 650 employees will move into the new building in 2024. With the construction, we have not only created more space for growth, but the building is also technologically state-of-the-art,” stated Dominik Santner, the COO of Anton Paar and head of the construction project. There are currently around 1,400 employees at the Graz site, but the expansion will allow to host up to 1,000 workplaces. On 25th April 2022, Anton Paar celebrated the beginning of the €60 million construction works, that are carried out by the architectural office KFR ZT GmbH and are expected to be completed by the end of 2023.
The solar thermal ice energy storage system
The new technology centre of Anton Paar will employ an innovative ice energy storage system with heat pumps for almost half of the cooling and heating needs of the site. It is composed by an underground basin with a diameter of 19 m and a depth of 6 m, corresponding to a water volume of about 1.7 million l. Before the summer, the water is frozen. The melting heat and then the cold water are used to cool the building. Heat pumps are used to transfer the heat from the building to the storage tank, which is then heated over the course of several months. At the beginning of the cold season, the storage tank is then warmed up and can be used to heat the building in the winter until it freezes again at the end of the winter. In addition, the company will have photovoltaic and solar thermal systems installed on the roof.
For further information: www.anton-paar.com
© Anton Paar
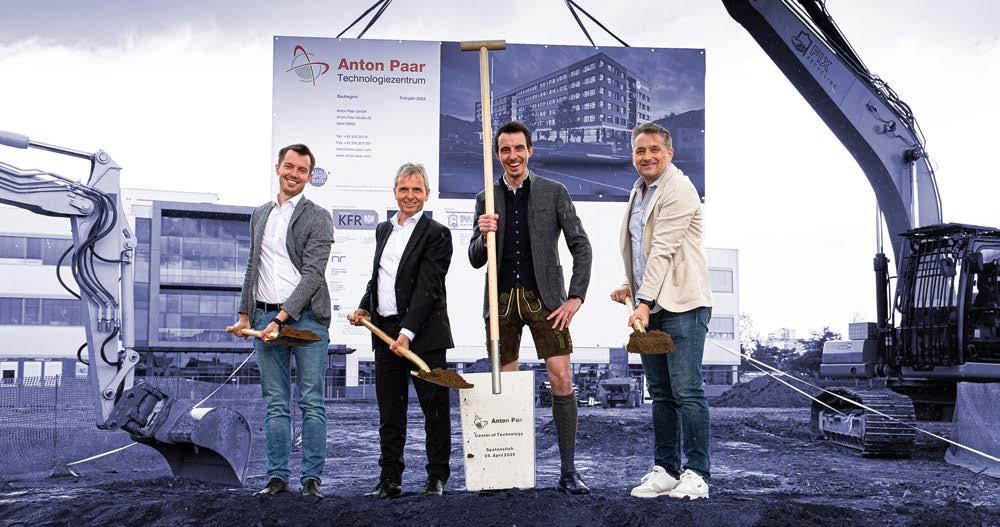
GEINSA Supplies the Paint Booth for Metro Bangkok’s Vehicles
GEINSA supplied a paint booth to Design&Project for coating Metro Bangkok’s vehicles.
Design&Projects International is a company specialized in providing railway maintenance projects and acquired from GEINSA a paint booth for Min Sen Machinery, leader in machine tool distribution in Thailand for the Bangkok subway red line project. The painting and drying process of Metro vehicles is carried out in the supplied cabin. The cabin has a dimension of 30 m. long, 5 wide and 5 high and is equipped with pneumatic painter platforms, application equipment and a paint preparation laboratory. It has lighting with LED technology and frequency inverters in impulsion and extraction motors. About GEINSA
GEINSA was founded in 1967 and has developed advanced technology in more than 2000 installations worldwide. Its activity consists of the design, manufacturing, assembly and Technical Assistance Service of installations and booths for surface treatment and subsequent painting. We provide: the design and engineering project, both in the planning and in the manufacturing, assembly and after-sales, and in each of these stages all the personnel belong to GEINSA.
For further information: www.geinsa.com
© GEINSA
View inside the spray booth installed in Min Sen Machinery, Bangkok. Spray booth 3D image.
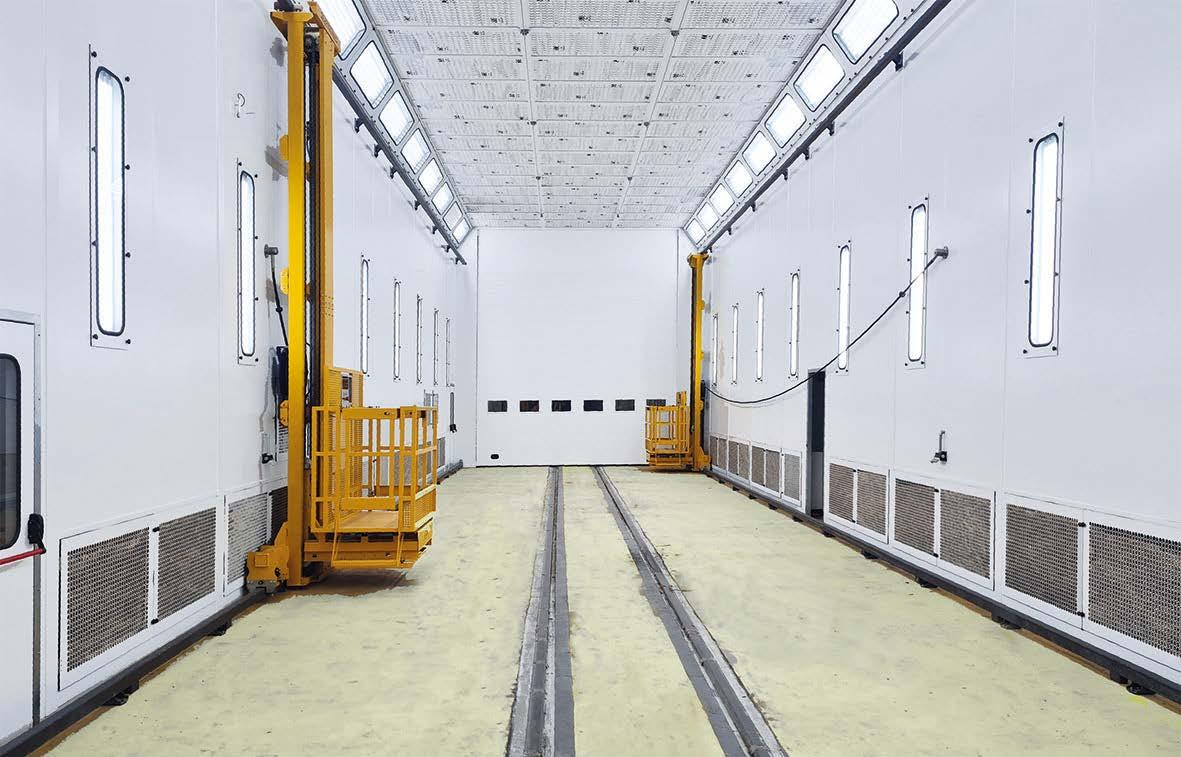
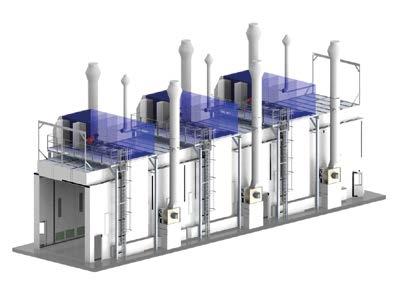
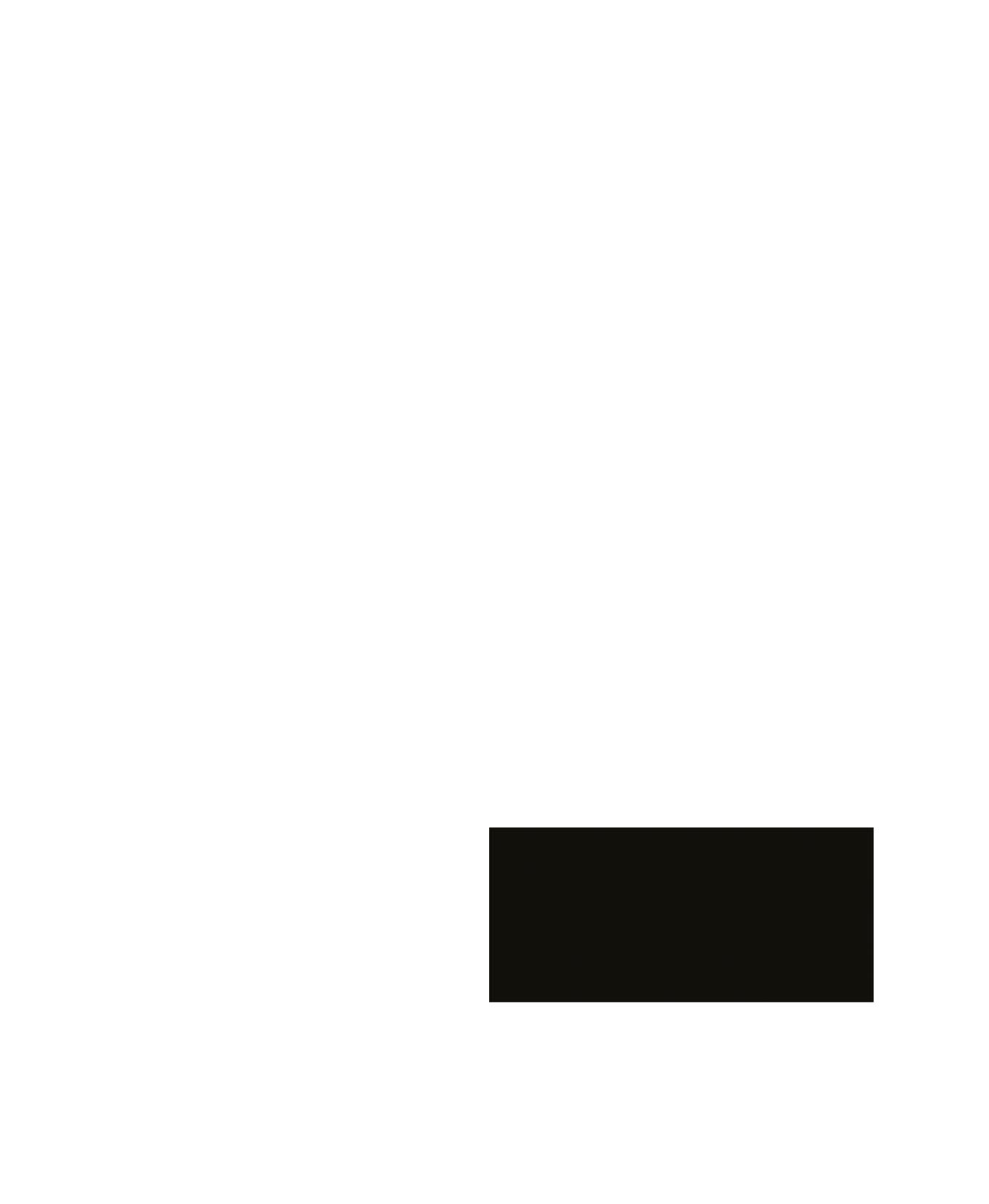
Future-proof and reliable overhead and floor MONORAIL and P+F
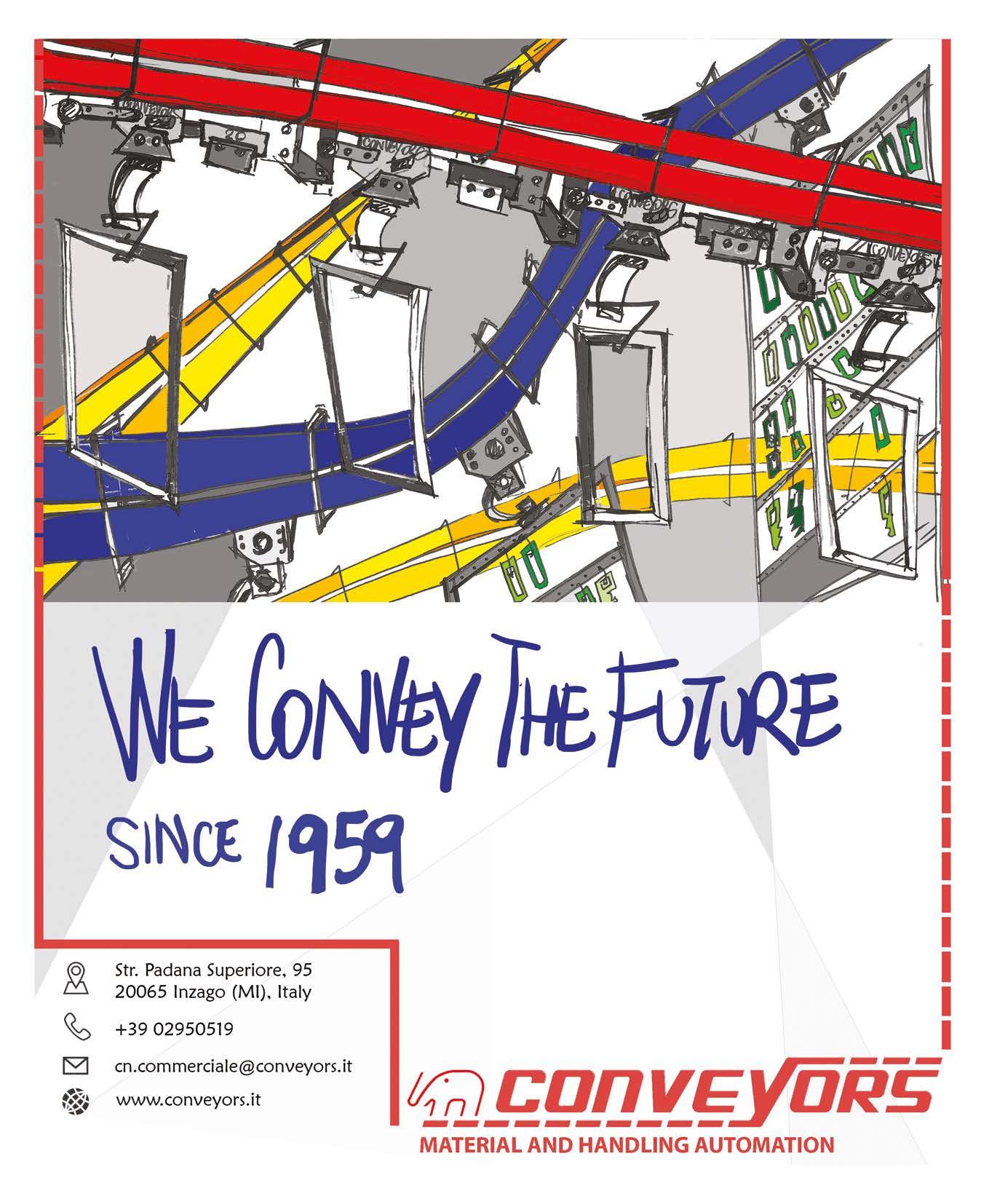
CONVEYOR systems that can be perfectly integrated into your production processes.
We take care of all your requirements and create a tailor-made and cost-optimized concept for you.
Reduce to the Max- 3-in-1-Coating System for Mechanical Clock Components
Germany’s most prestigious maker of clocks and clockworks has high demands for the coating solution used for its delicate and highly varied small clock components. The system has to run like clockwork. It has to offer extreme accuracy while also remaining flexible and easy to use. In the search for a suitable system concept, the two long-established companies Hermle and Venjakob got together.
© Venjakob
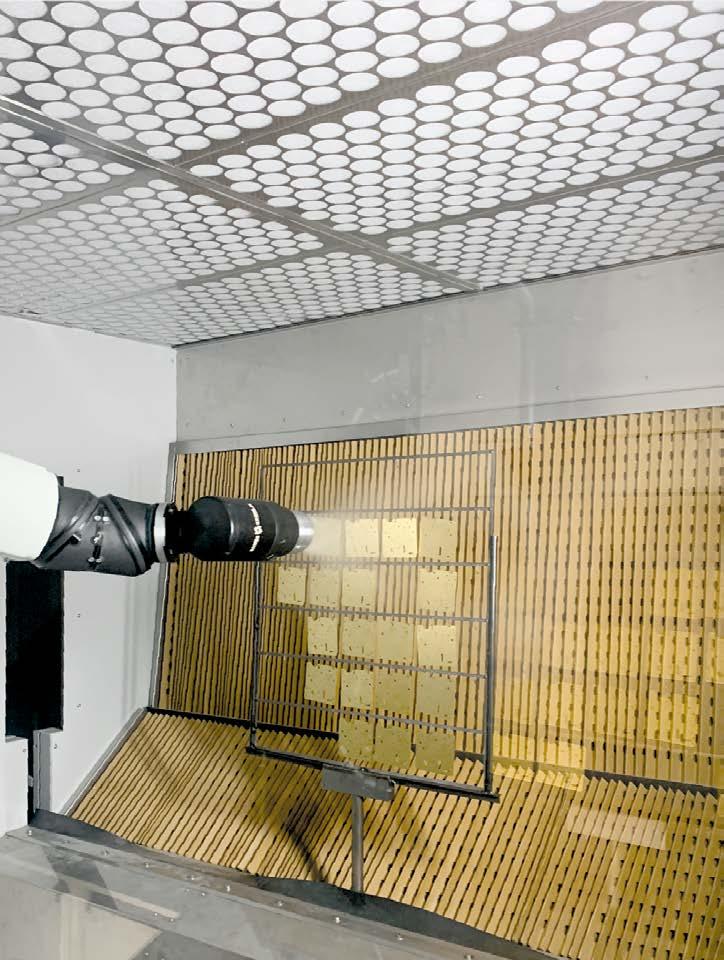
View of the compact fully automatic coating system with painting robot and a floor conveyor with rotary drive for 360° coating in one pass.
In this place, time never seems to stand still. The production site and company headquarters in Reichenbach am Heuberg in the German state of Baden-Württemberg is where the medium-sized family company Hermle, which looks back on 100 years of clockmaking, manufactures its clocks and clockworks. Hermle runs one of the most modern clock production facilities in the world and is one of the last remaining clock manufacturers. Where production of mechanical clockworks for large clocks is concerned, Hermle is the only full range supplier in the whole world.
Request for a compact system made to measure
The clockmaker wanted a new solution for coating mechanical clock components to be installed in the facilities built in Reichenbach in 2021. The plan was to have this system replace the previously used but now dated machines. These included a manual spraying bench for special components, an automatic coating system with an overhead conveyor for coating clock frames and a spindle chain conveyor for coating rotationally symmetrical clock components. “Ideally the new system should combine all the different solutions we were using before,” was the customer’s request. But Heiko Dreher, Purchasing Manager at Hermle, only had a vague idea of what such a 3-in-1 solution could look like. Following detailed discussions, Kornelius Berg, the Venjakob Sales employee responsible for Hermle, submitted three different concepts for the new system, each offering different functions. “We came to an agreement quickly,” says Berg. The main differences affected the conveyor system. Heiko Dreher seemed taken by the ideas and the precise details of the concepts. In the end, Hermle chose the concept featuring a small, compact, fully automatic coating system with ABB coating robots and a floor conveyor with a rotary drive. The conveyor system accommodates the carrier frames that carry the clock components and is intended for cycled transport through each of the processing stations.
Set-up, install, and go
The selection criteria also included the available space. The function and design of the system were adapted to the dimensions of its future installation site. To facilitate quick commissioning, which was another customer request, the coating system was delivered in only a few separate parts. That way, only the platform for the supply and exhaust air and the spray booth had to be attached. “The customer even agreed to remove two walls from the room to make it possible for the system to be transported to the installation site in as few pieces as possible,” reports Venjakob’s Kornelius Berg. This small anecdote is sure to stick in the minds of all those involved for a long time to come.
Special master program for autonomous operation
The system concept developed by Venjakob allows Hermle to coat the greatest variety of small components in just one installation with a single conveyor system. The workpiece carriage is firmly installed on the tracks. The machine capacity was adapted to the application (with a cycle time of 5 minutes per item carrier) but an increase by approx. 20 percent remains possible. The entire system is designed to be flexible and as easy to use as possible. Venjakob’s software engineers programmed a special input interface for controlling the coating robot, giving the customer the simplest possible option for creating recipes of their own. “You simply copy the recipe, then enter the different parameters such as dimensions of the coated component, the coating speed or the angle of the coating gun,” Kornelius Berg explains the principle. The ease of use and adaptation to customer requirements applies to the entire system. A central operating system is used to control the coating system including the conveyor technology. Training the machine operator likewise only required a basic training course for maintenance and service of the coating robot by its manufacturer ABB.
Function sequence and process steps
The coating system transports items counterclockwise, the feeding and removal station are at the same location. The clock components being coated are attached to the item carrier frames by hand. These are then positioned in a form locking manner on the workpiece
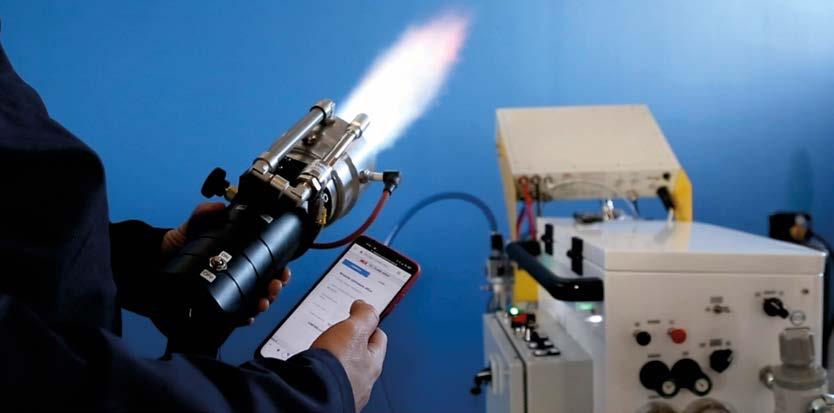
© Venjakob
View into the heart of the plant, the coating booth. Venjakob’s special master program stands for high line performance and enables easy creation of recipes for the wide variety of watchmaking parts.
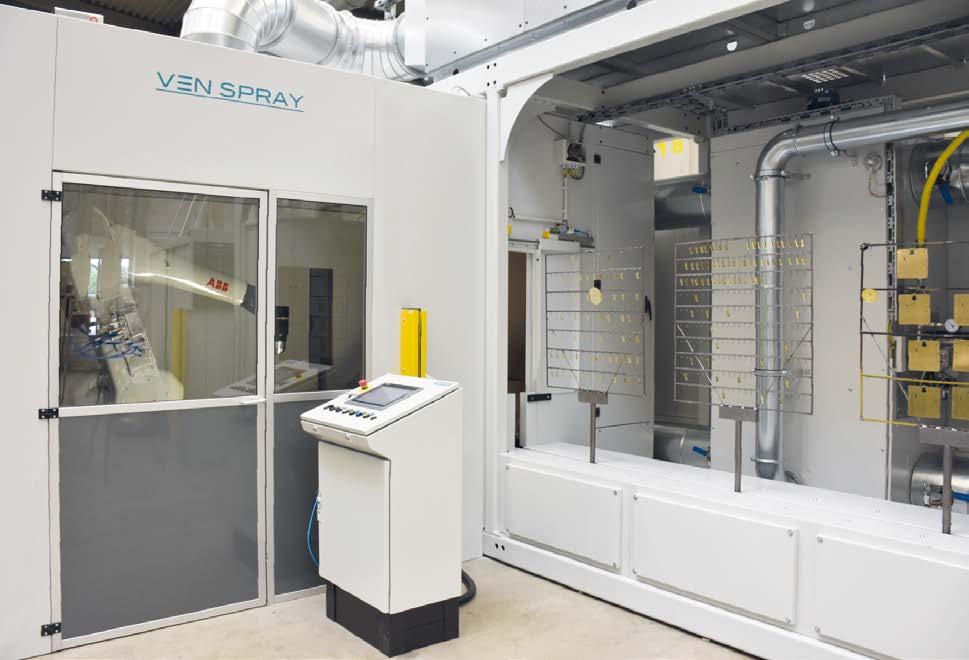
carriage of the floor conveyor and are quick to remove after the coating process is complete. Prior to the coating process, the desired recipe is selected on the system control desk and transmitted to the controls. The system controls contain the parameters for processing the parts according to each recipe. After selecting the desired recipe, a simple push of the start button on the control desk will start the system. The floor conveyor moves the item carrier into the coating booth. Once the first side of the part has been coated by the robot, the item carrier rotates automatically thanks to the rotary device to permit coating of the other side. The next step is evaporation. The evaporation zone can contain two item carriers at once. After a 10-minute evaporation period, the item carriers are transported to the drying channel. The drying temperature is 80° to 120°C. The length of the through-feed dryer makes it possible for six item carriers to dry at the same time. The item carriers enter it in a 5 minute interval and remain there to dry for 30 minutes. The subsequent cooling process takes 10 minutes and happens outside of the channel at room temperature. Afterwards the item carriers are simply removed from the rods of the floor conveyor at the removal station.
For further information: www.venjakob.com
The Curious Link Between a Shark and a Formula One Car
After working in the Formula One world, artist Alastair Gibson began creating carbon-fibre sculptures of marine specimens that are painted using a very complex process directly in the Mercedes AMG Petronas racing team’s factory.
At first glance, marine fauna and Formula One single-seaters do not seem to have much in common. Yet, Alastair Gibson, a creator of special carbon fibre sculptures, claims there actually are many similarities: “For example, both Formula One cars and sharks have well-defined centre lines and are strikingly symmetrical. They are magnificent creatures that move sinuously through space – cars are aerodynamic and sharks are hydrodynamic. This is why I decided to use majestic sea animals as subjects for my works.” Combining artistic inspiration, attention to details, interest in colour, and engineering skills, Alastair Gibson creates carbon fibre sculptures incorporating parts of Formula One cars, each with a production number that refers to specific vehicles or races. In order to bring his sculptures to life, he has them painted with Spies Hecker products, the Axalta Coating Systems brand dedicated to developing practical coating systems for car bodies. Originally from South Africa, the sculptor began his career in motor sports. After working as a mechanic and engineer in some minor racing classes for seven years, he made his Formula One debut as the chief mechanic of the Benetton team. In his fifteen years in the top motorsport championship, he also served as chief race mechanic for the BAR and Honda Grand Prix teams. However, being interested in art as well, in 2008 Gibson made the decision to pursue his passion and become a full-time sculptor. “I started by toying with discarded carbon-fibre fragments and car pieces in the downtime before and after the racing season, because that was all I had on hand at the time. I realised that it was possible to create new, beautiful objects through these scraps, but I did not expect that someone would want to buy them!” he jokingly recounts. Making his sculptures requires a lot of effort, time, and practice. He starts by carving a 1:1 scale model of his work by hand in balsa wood. Then, he uses CAD software to decide on the positioning of details such as eyes, gills, or fins. Afterwards, he places thin sheets of carbon fibre precisely into moulds, whose number depends on the type of sculpture being made. “This is a particularly tricky phase, because in some of my sculptures the carbon fibre weave is visible through the clear coating. Therefore, it is essential to place the material correctly and make sure that there is nothing between the mould and the carbon fibre layer.” The carbon fibre-covered moulds are then subjected to a debulking process in a pressurised environment and placed in an autoclave to create a perfect final sculpture section. Once assembled, the works of art are taken to the Mercedes AMG Petronas body shop, where they are painted with Spies Hecker products, the same coatings also used by the team.
© Alastair Gibson
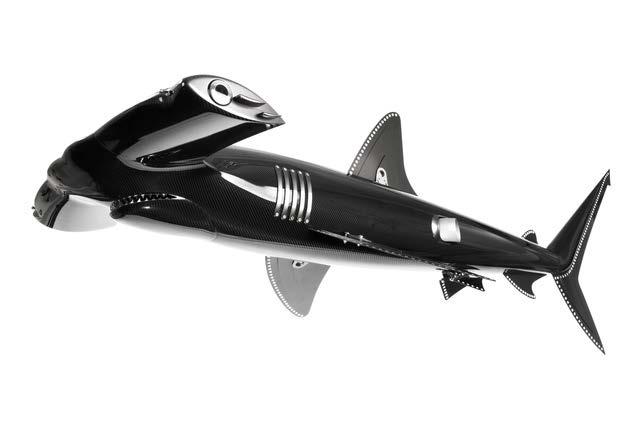
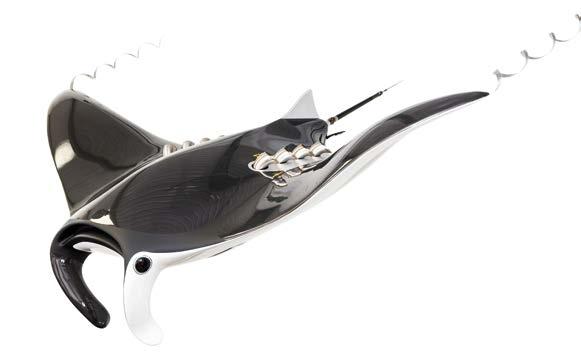
Sharks are one of sculptor Alastair Gibson’s favourite subjects. Aero Manta, a metre-long sculpture that took 25 hours to coat.
© Alastair Gibson
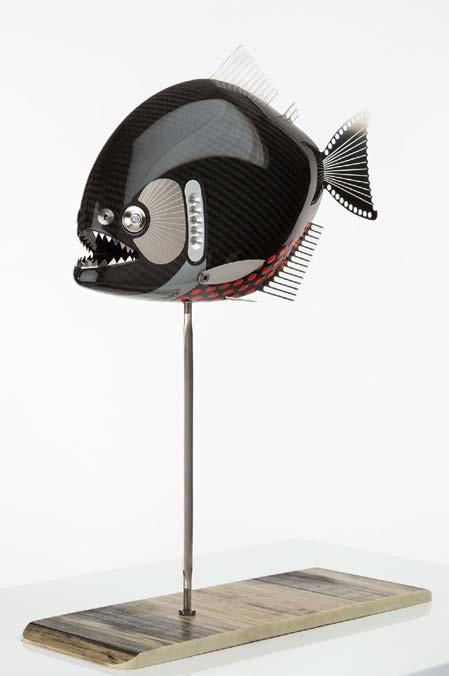
Racing Piranha.
In addition to the clear coats, Permahyd® Hi-TEC Basislack 480 and Permasolid® HS Optimum Plus Klarlack 8650 are sometimes applied, guaranteeing a high gloss degree. In order to ensure that his artistic visions are realised, Gibson consults with Andrew Moody, the team’s Head of Paint and Graphics, who relies on Spies Hecker’s ColorDialog spectrophotometer to identify the most suitable colours and effects. “We love these kinds of challenges, although they are timeconsuming. In fact, the painting of the Manta sculpture took 25 hours, while one of the Racing Piranhas took about 10 hours. However, coating something completely different is very exciting,” says Moody. The painted sculptures are finally sent back to Gibson’s studio, where the artist adds final details such as photo-etched stainless steel fins or bismuth alloy teeth. Gibson’s works of art have been presented at countless British and international exhibitions, as well as being purchased by collectors. He says: “I take inspiration from many things around me and I put a lot of passion into creating these sculptures and making sure their finishes are perfect. I hope this can be perceived, by looking at them.”
towards the future
SOLUZIONI ROBOTIZZATE DI
ROBOTIC PAINTING SOLUTIONS VERNICIATURA

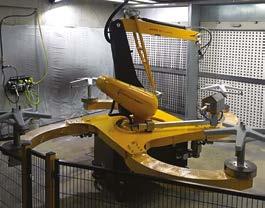
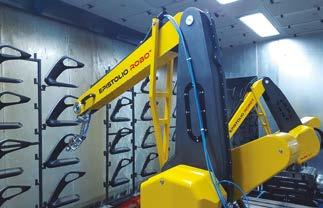

Epistolio Srl.
Via Piemonte 120 21100 Varese (VA) ITALY Ph: +39 0332 212692 Fax: +39 0332 223666 info@epistolio.com www.epistolio.it

