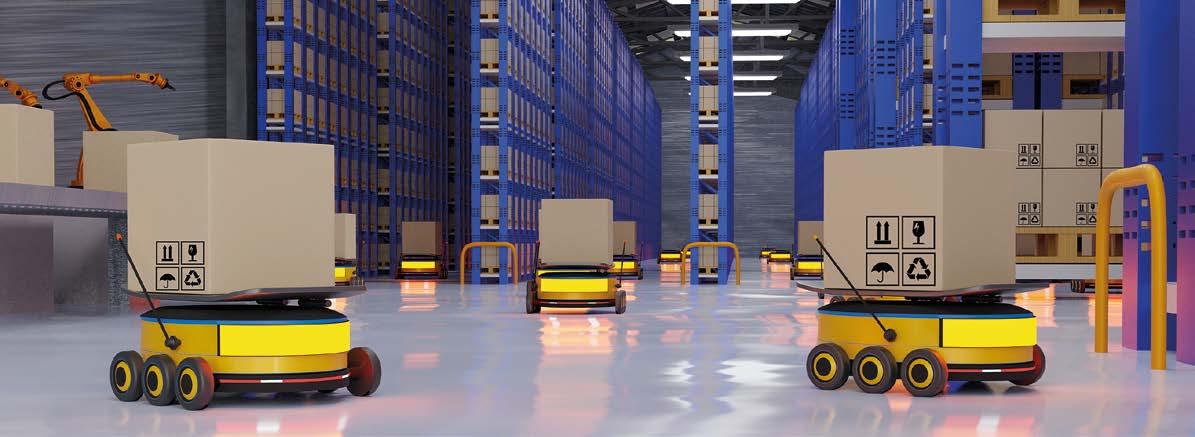
2 minute read
STANDARD &LEGISLATION
STANDARD & LEGISLATION - UCIF Informs
Automated Guided Vehicles in Finishing
UCIF – Italian Surface Treatment Equipment Manufacturers’ Association
Milan, Italy info@ucif.net
In the last article published on ipcm®, we dealt with the new technologies and dynamics required of industrial surface treatment processes by the market1. These do not involve only materials, surfaces, and cost optimisation, but also modularity, digitalisation, and automation. This brings us now to the topic of design and integration of smart AGV systems for internal logistics. AGV stands for Automated/Automatic Guided Vehicle: the name itself suggests the idea of an object capable of moving autonomously, which is the actual purpose of AGVs. This technology has existed for many years, from simple models with elementary drive units to modern systems with natural navigation, which are able to move autonomously within production departments using various technologies, from odometry to laser detection and, in some cases, GPS. In the automotive industry, AGV systems are used for a variety of tasks, such as transporting workpieces among different points on workstations. It is indeed no coincidence that, in coating departments, their use is becoming more and more widespread for transporting chassis, with clear advantages in terms of flexibility compared with conventional handling systems, such as overhead or floor conveyors, belts, or roller conveyors. Benefits also include these vehicles’ safe interaction with the surrounding environment and, above all, with operators, through the use of laser scanners and presence sensors.
1 https://www.ipcm.it/en/open/ipcm/2022/74/192.aspx This also translates into the possibility of linking them with MES systems to run automatic cycles with fleet control for the safe movement of multiple AGVs through natural navigation and active control of obstacles on the route with collision avoidance and, if feasible, autonomous route change features. This ensures safe interaction even in the presence of sudden obstacles and/or people thanks to their stop functions. Precise positioning to within +/- 10 mm is also ensured. On the other hand, one aspect that needs to be assessed during project development is that of AVGs’ energy supply, as no physical connections can be put in place during movement. Actually, there exist various solutions, such as recharging on special fixed stations with autonomous management of these phases exploiting idle time, or recharging systems at workstations using super capacitor technology, or even inductive charging both on the move and on fixed stations. Another advantage of AGVs is the possibility to offer various configurations, from integrated lifting systems to bi-directional roller conveyors and on-board 6-axis robots. The world of AGVs is undoubtedly evolving and their use in various industrial sectors is becoming increasingly widespread due to their ability to transport even bulky and heavy objects. This can take finishing processes to the next level – and the Italian companies represented by UCIF are already using these technologies to make their solutions faster and more flexible.
© Adobe Stock