
7 minute read
CASE STUDY - ICT
Effective and flexible degreasing thanks to ultrasound
Custom system manufacturer FK Galvanik GmbH created a fully automatic anodizing plant with a total of 47 tanks for an important electroplating service provider based in Dresden, Germany. The new large-scale electroplating plant for aircraft parts sets standards in the fields of regular anodizing, hard anodizing, chromating, and dyeing. The equipment in the degreasing and rinsing tanks, which employ a total of 54 ultrasonic systems from Weber Ultrasonics, also makes an important contribution to this. It ensures clean parts that are free of any residues, which in turn secures optimum coating results.
It was a fire breaking out at Nehlsen-BWB Flugzeug-Galvanik Dresden GmbH & Co. KG that necessitated investment in a new anodizing plant. The company, which is part of the Swiss BWB Group, is a longstanding partner to industry and the aviation sector with numerous certifications (QSF-A/B extended workbench with additional capabilities). The quality, capacity, and process stability were therefore all subject to strict requirements, together with the size of the components to be treated in the new electroplating system. The company chose Keltern-based FK Galvanik GmbH (Germany) as its partner for planning, manufacturing, and commissioning the system. For more than 30 years, this special plant manufacturer has been specializing in customer-specific complete solutions for the electroplating sector. It also offers plant modernization, extension, and reconstruction services, as well as manufacturer-independent maintenance and spare parts provision.
A fully automatic anodizing plant was designed for NehlsenBWB Flugzeug-Galvanik Dresden GmbH & Co. KG. This plant satisfies current requirements in terms of sustainability, profitability, and occupational safety. It also means that the treatments which were previously performed in three different plants can now all be performed in a single plant. In addition to this, the new plant offers greater capacity and process flexibility, meaning that additional market segments can also be served.
© FK Galvanik GmbH The electroplating plant has a total of 47 tanks and is designed for parts measuring up to 5,000 x 1,800 x 800 mm (W x D x L).
To achieve this, the plant has a total of 47 tanks for parts measuring 5,000 x 1,800 x 800 mm (W x D x L). The new electroplating system was set up in the renovated hall in two rows, each measuring around 50 meters in length and 15 meters in width.
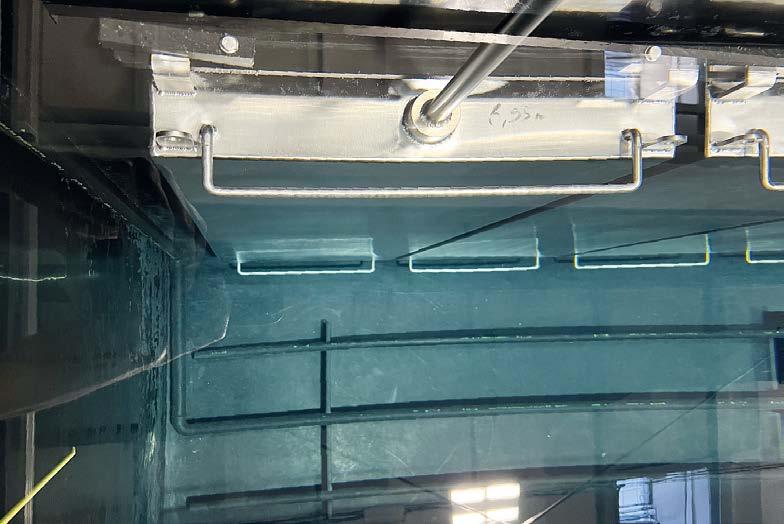
Ultrasound for clean surfaces that are ready for coating
Boreholes, undercuts, and cup-shaped geometries represent a challenge when electroplating workpieces. Depending on the component and the machining performed, these can contain residues from machining media that are extremely tough to remove. When still using the old plants, this required time-consuming pre- and post-treatment, some of which had to be performed by hand. “To eliminate this additional effort, which is not possible in fully automated plants, and secure optimum quality, we equipped the degreasing tank and the two end rinsing tanks used for pretreatment with ultrasound,” explains Dr. Thomas Kempe, CEO at FK Galvanik GmbH. The significantly improved cleaning efficiency achieved thanks to ultrasound is based on two concepts, the first of which is the physical effect of cavitation. The second involves the liquid being kept in motion as a result of the currents caused by the ultrasound, which allows the hard-to-reach areas to be thoroughly rinsed out. The plant manufacturer decided to go with ultrasonic components from Weber Ultrasonics. “When it comes to ultrasound, Weber Ultrasonics has been our partner of choice for many years. We are really happy with the overall package of consulting, technology, quality, flexibility, and service. In fact, we don’t even bother getting comparison estimates from other providers anymore,” comments the CEO, explaining the decision. A total of 54 ultrasonic systems are used, employing the latest technology at a frequency of 25 kHz.

The aircraft parts pass through the plant as individual parts on racks.
In the cleaning tanks and two end rinsing tanks used for pretreatment, a total of 18 ultrasonic systems ensures clean surfaces that are ideal for subsequent coating.
© FK Galvanik GmbH
© FK Galvanik GmbH
© FK Galvanik GmbH
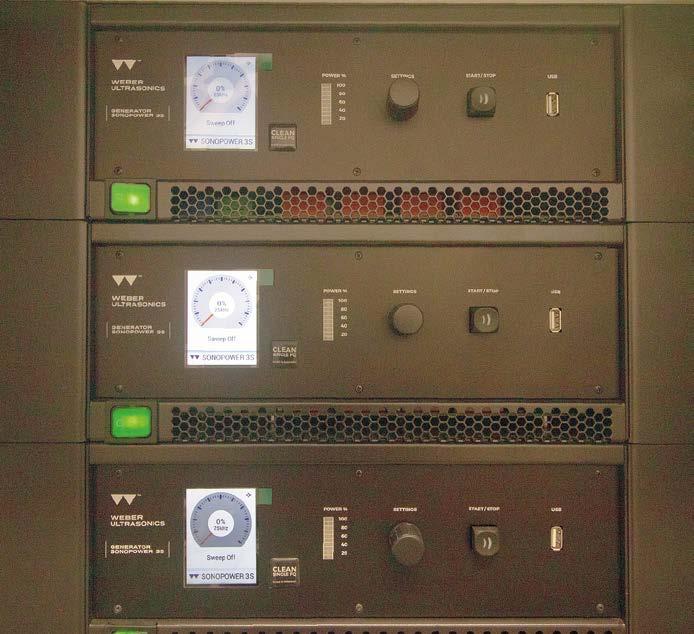
With dimensions of 1,800 x 535 x 90 mm, the transducers guarantee optimum insonification of the parts in the large tanks. The 54 SonoPower 3S generators, each boasting a power output of 3,000 W, are housed in six control cabinets and integrated into the Siemens control system used for the plant via optional PROFINET interfaces.
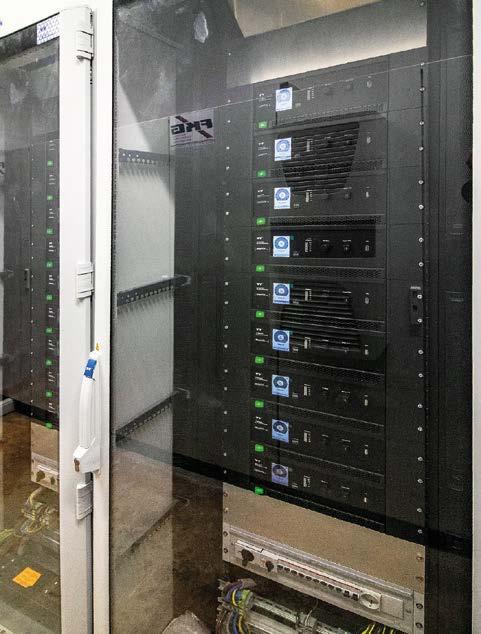
© FK Galvanik GmbH
Designed to deliver high process and operational reliability
The degreasing tank and the two rinsing tanks are each equipped with 18 power-matched Sonosub submersible transducers. Thanks to their dimensions of 1,800 x 535 x 90 mm, these guarantee optimum insonification of the parts in the large tanks. Since the capsules are produced using special laser welding technology, the transducers are also extremely well sealed and dimensionally accurate. Digital frequency generation and control are performed for each transducer by a 4th generation SonoPower S3 with power output of 3,000 W, which can be adjusted steplessly between 10 and 100 percent. Through combined frequency and amplitude modulation, this singlefrequency generator facilitates highly homogeneous sound fields and prevents so-called standing waves, which in turn improves the ultrasound effect. “Among other things, this helps us limit the ultrasonic support required during the cleaning and rinsing processes to just one or two minutes,” reports Dr. Thomas Kempe. The Sonoscan also contributes to consistent ultrasonic performance. It determines the operating frequency automatically before ultrasonic output and adjusts the system settings accordingly. Together with other patented smart features, this means that the most efficient power output is always applied, even in the face of changing operating conditions such as temperature fluctuations. The adjustments are performed during operation, so the three-shift system at Nehlsen-BWB Flugzeug-Galvanik Dresden GmbH & Co. KG can continue to run without any interruptions. The generators are equipped with an optional PROFINET interface and integrated into the Siemens control system used for the electroplating unit. The parts-specific cleaning programs can therefore also be automatically selected.
Minimized energy, water, and chemical consumption
To secure sustainable and energy-saving operation, all of the active tanks are heated with district heating, while the 98 °C (208°F) sealing tank is equipped with effective insulation and a cover to minimize heat losses. An extractor also secures a pleasant temperature and humidity level in the working environment. The cascade system used for the rinsing tanks reduces water
consumption. To compensate for fluid losses in the various active tanks, the water from the first rinsing tank is used. The ingredients this contains also allow the total amount of chemicals used to be reduced.
About Weber Ultrasonics AG
Weber Ultrasonics AG develops, produces, and markets solutions and components for ultrasonic technology in industrial use. Its business area focuses on cleaning, welding, and cutting with ultrasound and includes other special applications. The company is certified to DIN EN ISO 9001 and has received multiple awards for exemplary corporate governance. The family-run mediumsized company with HQ in Karlsbad, Germany, has 160 employees worldwide. Weber Ultrasonics AG owns subsidiaries in the USA and Asia as well as Weber Entec GmbH & Co. KG based in Waldbronn (Germany), which specializes in ultrasound-based plant technology for biogas and sewage treatment plants.
© FK Galvanik GmbH
FK Galvanik GmbH
For more than 30 years, the name FK Galvanik has stood for ultimate precision in the manufacture of electroplating equipment. The company’s aspiration here is always to offer maximum quality, while securing on-time delivery and fair prices. Automatic plants for surface coating are its main area of expertise. The company not only specializes in the manufacture of new plants here, but also modernization and remodeling of non-automated plants. Its expertise stretches from consulting, through planning, design, and construction, all the way up to maintenance of electroplating systems. The production process and service provided are strongly customer-oriented and have a practical focus, regardless of whether working on a new FK Galvanik plant or an existing object from a different manufacturer. Around 30 highly motivated and specialized employees are on hand to meet even the most complex customer wishes.
More Information
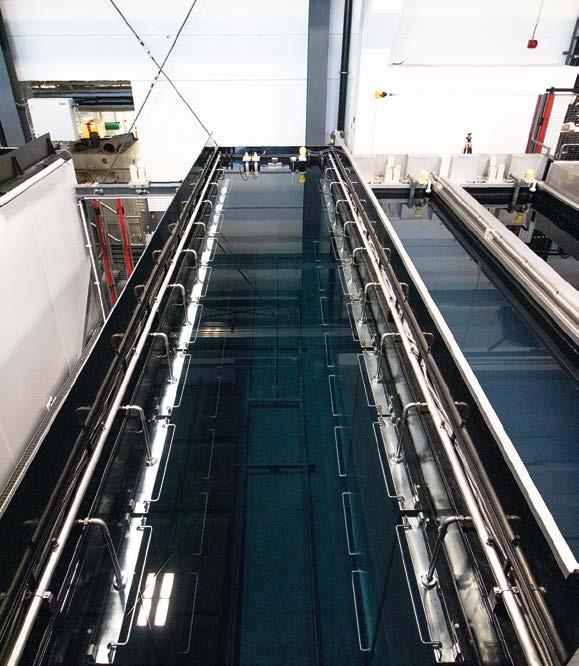
With the 4th Generation SonoPower generators, patented smart features ensure that the most efficient power output is always applied, even in the face of changing operating conditions such as temperature fluctuations.
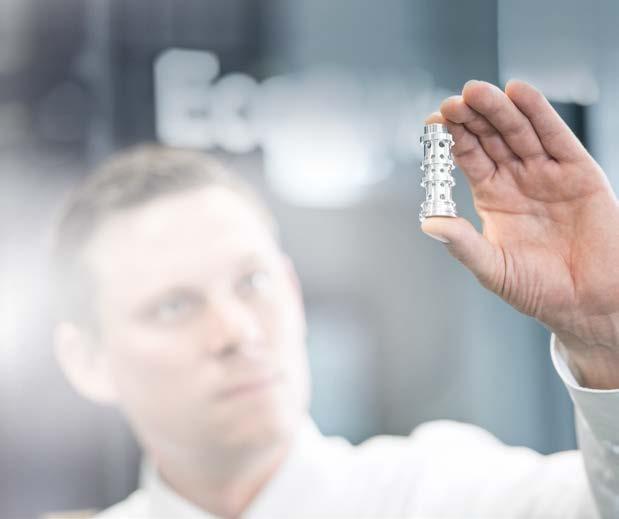
Clean Workpieces.
Economical and Sustainable.
www.ecoclean-group.net
Solvent Cleaning Aqueous Cleaning Ultrasonic Cleaning
High-pressure Waterjet Deburring Surface Processing & Selective Cleaning