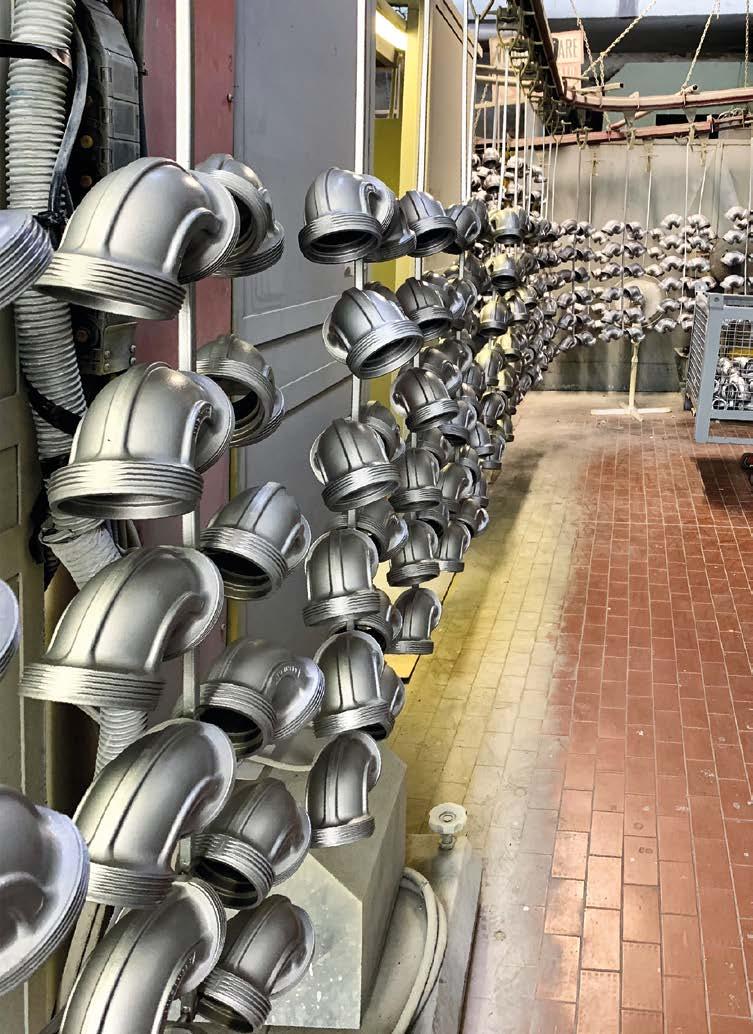
19 minute read
CASE STUDY - ICT
An innovative multi-drum vacuum impregnation plant becomes a technological lever for business growth
Cofra Snc is a company specialising in the surface treatment of castings, from vibratory finishing to cleaning, up to liquid coating. It has recently installed a new vacuum impregnation plant designed by STS srl (Ravenna) in order to offer an all-round service to its customers, operating mainly in the automotive sector, and start a long-planned development project.
© Cofra Snc
Cofra Snc specialises in cleaning, vacuum impregnation, and painting of automotive components. Microporosity is among the most common surface defects resulting from casting, diecasting, and sintering processes. It is caused by the shrinkage of metal as it passes from the liquid to the solid state, due to the release of previously absorbed gases. The presence of microporosity in the mechanical manufactured castings can compromise their seal, leading to the rejection of large quantities of parts. Vacuum impregnation is one of the most popular methods to solve this problem: the components are immersed in catalysed thermosetting resin to seal their pores and enable them to pass leakage tests and be suitable for eventual coating. Although little known, vacuum impregnation is actually a popular process among contractors performing surface treatments on castings. It is, in fact, one of the services often offered by metal cleaning firms in one of the areas with the highest density of foundries and metallurgical companies in Italy, that is, the Brescia area. This is also home to a company, Cofra Snc, which is experimenting with an innovative system capable of performing vacuum impregnation and cleaning with one automatic system, designed and installed by STS srl (Ravenna, Italy). This firm was founded around forty years ago, and it is now managed by Paola, Federica and Luca Cometti, with the aim of offering contract cleaning services to local manufacturers of fittings and automotive components. Then, it gradually integrated vibratory finishing and liquid painting plants into its factory and, in order to offer an even more complete service, it insourced first the assembly and then the vacuum impregnation process phases, previously entrusted to an external company also belonging to the Cometti family.
© ipcm
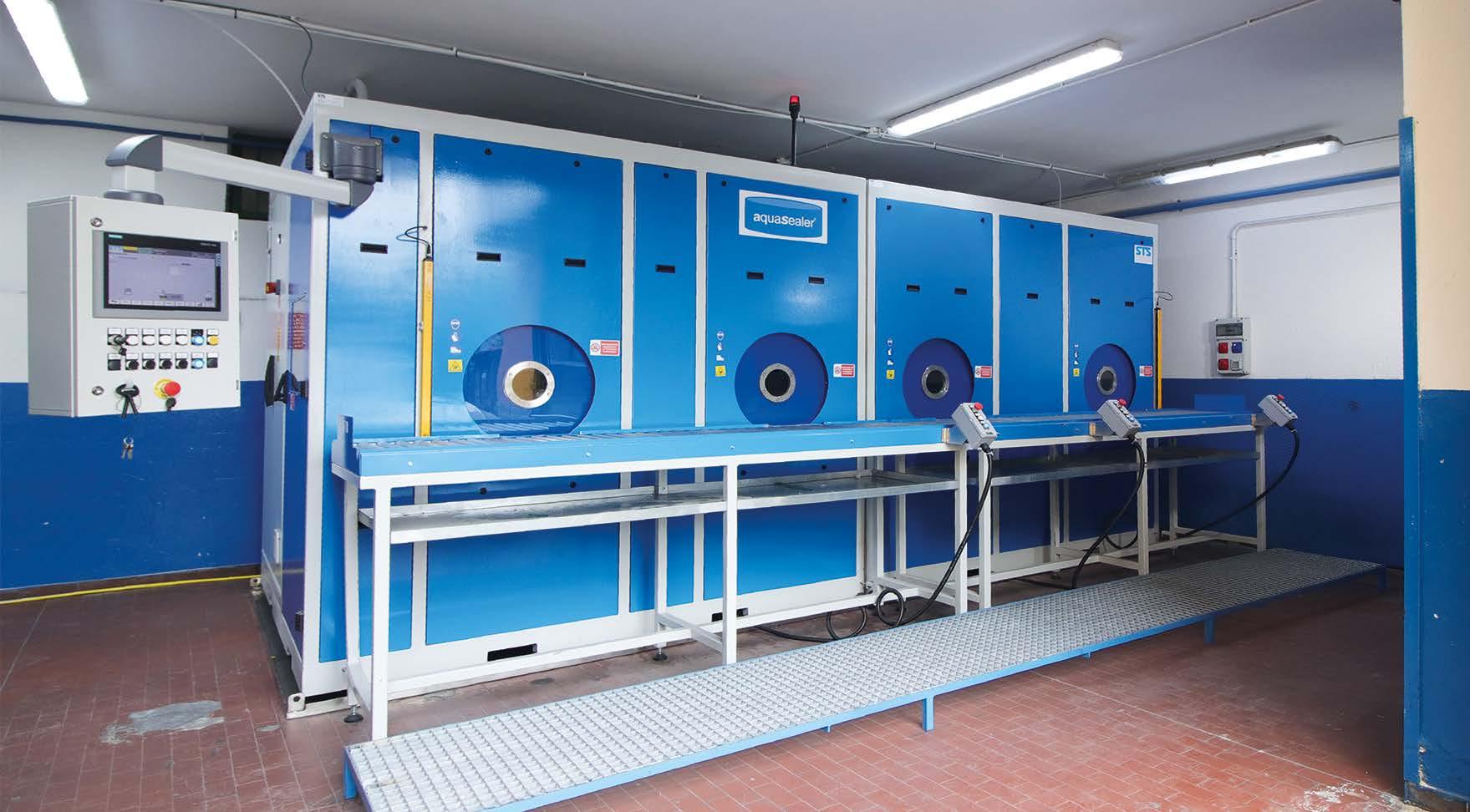
© STS
The RS30-4 vacuum impregnation system from STS’ AQUASEALER® series.
“As soon as the foundries send us their castings and other mechanical components,” explains Luca Cometti, the technical manager of Cofra, “we treat them in our vibratory finishing plant to remove burrs, clean them, dry them, and send them to a few metallurgical companies for some machining operations such as threading. Then, we receive them back to perform vacuum impregnation and its related drying phase; afterwards, we send them to our coating department, where they are pre-treated in our belt phospho-degreasing and passivation system, and finally we liquid coat, dry, assemble, and package them.” The choice to insource the vacuum impregnation process, in particular, was motivated by Cofra’s need to supply its customers with finished products quickly and without excessive handling. STS’ plant engineering solution met this requirement perfectly, thanks to the possibility of managing several stages in a single machine via the control PLC equipped with a touch screen display. “The installed system has been in operation since January this year,” indicates the technician from STS. “It is an RS30-4 machine from STS’ AQUASEALER® series, designed for vacuum impregnation operations. It is the result © ipcmof more than twenty years’ experience gained by the company in the vacuum impregnation field and by STS’ technical staff in the cleaning field. Compared with the first vacuum impregnation plant installed by STS back in 2003, numerous technological evolutions have led to the integration of an additional cleaning chamber and of some technical measures related to the recovery of resin and water coming out of the treatment tanks and even of air, which is also recirculated into the system.”
The multi-drum system
The plant consists of four treatment stations: vacuum impregnation, cleaning, rinsing, and polymerisation. The components are placed inside the baskets in bulk or in a fixed-position mode, depending on their characteristics and geometry. Even those whose surfaces are less complex and do not risk denting, however, are only allowed limited movement of 1 or 2 mm within the basket. The most delicate parts, on the other hand, are carefully placed and separated on several © ipcm
© STS
© ipcm

The plant consists of four treatment stations: vacuum impregnation, cleaning, rinsing, and polymerisation.
© ipcm

The inside of one of the plant’s four chambers. levels with custom-made nets, depending on their size. The multi-drum structure allows the simultaneous processing of baskets in all four stations. The plant is configured for manual loading, but it is also prearranged for the integration of an automatic handling and loading system. Already now, however, thanks to the front-loading option instead of the more common top-loading one, material handling by the operator is easier.
The first and second phases: vacuum impregnation and cleaning
“Once a basket containing material is placed inside the drum,” explains the technician from STS, “the first dry vacuum phase begins. A vacuum pump extracts air until a residual pressure of less than 25 mbar is reached. Then, liquid resin is introduced into the drum until the components are fully immersed. Vacuum below 25 mbar is maintained for a few more minutes, in what is known as the “wet vacuum” stage. When a pressure value of 1 atm is restored in the drum, the liquid resin penetrates the material’s pores, driven by the atmospheric pressure itself. Finally, a basket rotating phase helps to remove all resin residues, which drip toward the collection tank. This ends the first stage.” The basket is then moved manually into the second chamber for the cleaning phase. “The material inside the basket is washed in the second drum with demineralised water at room temperature. In this way, liquid resin is completely removed from the parts’ surfaces, whereas it remains in the micropores due to the principle of capillarity. In other words, the resin that seals the castings’ porosity remains locked in the micropores and is not removed during cleaning. The water used, appropriately filtered by the recovery system, is separated from the resin, which is insoluble in water, so that it can be reused in the first stage of vacuum impregnation. Thanks to the filtration system, it is indeed possible to recover 80% of resin and 100% of water, which are fed back into the system.”
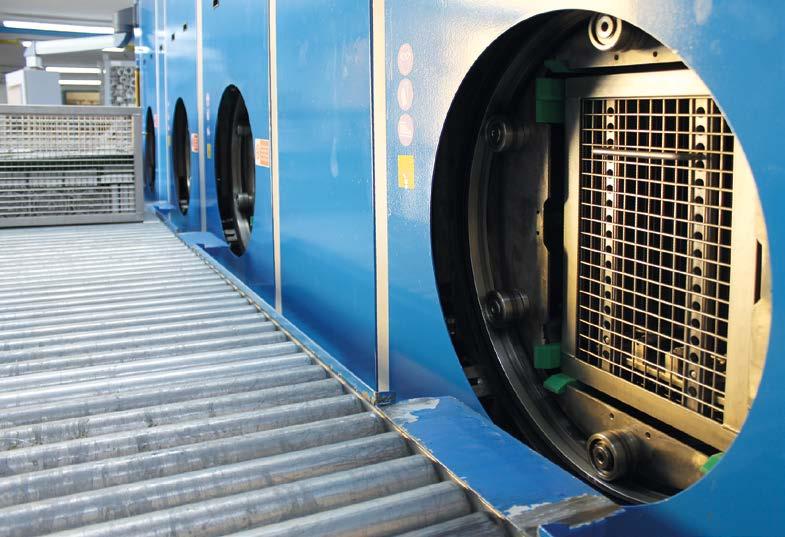
© ipcm
The third and fourth phases: rinsing and polymerisation
The third step involves rinsing the components at room temperature with demineralised water and additives compatible with the resin used, in order to prevent their surfaces from oxidising. At this stage, rinsing is essential to remove any microdroplets containing water and resin stuck inside the threaded holes and grooves, which could jeopardise the success of the subsequent polymerisation. “In addition, this prevents any deposit of polymerised resin from forming at the bottom of the polymerisation chamber, which would require frequent removal with a high-pressure cleaner,” emphasises the technician from STS. Precisely the polymerisation process takes place in the fourth drum. “The basket, kept rotating at all times to promote uniformity of treatment, is immersed in hot water at 90 °C, which, by heating the parts, causes rapid and complete polymerisation of the resin contained in the micropores. While the hot water is collected in the storage tank, a device insufflates air for drying, which can reach 150 °C thanks to a heater. The last stage consists of creating vacuum to remove moisture from the inside of pores, with two purposes: guaranteeing optimal paint adhesion for the parts to be coated and eliminating any risk of oxidation for the parts to be stored, thanks to the antioxidant product mixed with the hot water used.”
Fundamental time savings and additional benefits
The cycle time of each phase is about 15 minutes in compliance with the standard MIL 276A, which sets out the parameters to be met for vacuum impregnation processes. “The entire vacuum impregnation and cleaning cycle, therefore, lasts about one hour,” says Cometti, “After that, the workpieces leave the plant at room temperature and they are ready for further processing or leakage tests. This is a strategic advantage for us. With other

© ipcm
The components are placed inside the baskets in bulk or in a fixed-position mode, depending on their characteristics and geometry.
At Cofra, basket loading is done manually by an operator.
© ipcm
© ipcm

Liquid coating of parts.
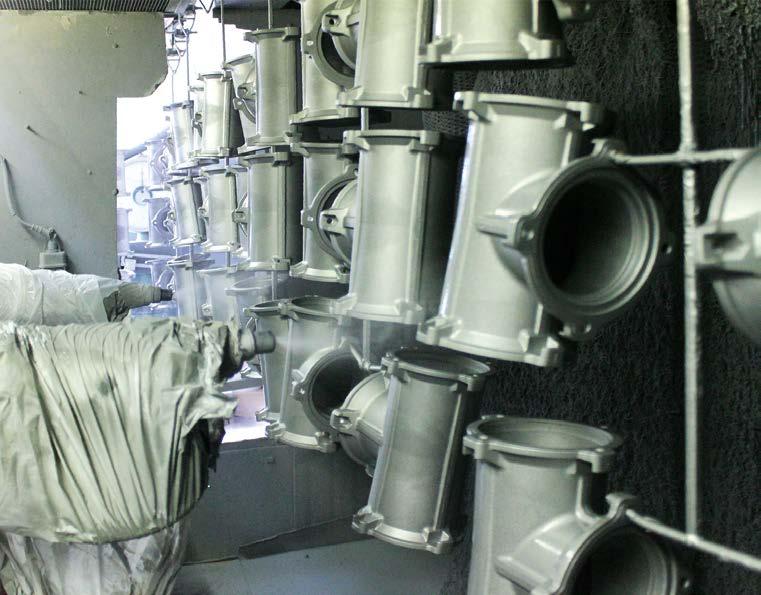
© ipcm
The coated components.
© Cofra Snc
technologies, the waiting time before handling the parts is of 48 to 72 hours: therefore, this enables us to save two to three days.” “Another innovative element of AQUASEALER®,” notes the technician from STS, “is its air purification system that condenses the vapours produced by the plant: both the air extracted from the chambers by the vacuum pumps and the vapour generated in the polymerisation tank are sucked by a condensation filter that returns them to the treatment chambers. This eliminates the need for a chimney and creates a completely closed-loop and, consequently, environmentally friendly system.” The machine’s Industry 4.0-oriented configuration is also an added advantage, as Cometti explains: “The possibility to manage orders directly from the control PLC has simplified our business. With this system, we can manage cycle times and temperatures, retrieve and record detailed data for each process step and, in the event of any problems, remotely connect with the STS technical assistance team. Indeed, their support service, both remotely and in person, has always been very precise and reliable, an important aspect for Cofra: the STS team advised us on the ideal solution when we had some issues with the quality of resins and corrosion inhibitors and helped us preparing our first offers to customers. Their assistance service really went beyond the mere sales and after-sales relationship. We can therefore only be satisfied, especially since our customers are equally pleased with our part quality degree and delivery speed. I am sure that focusing precisely on quality and speed of delivery will be the right weapon to start the expansion of our business that we have been planning for a long time.”
Scan or click the QR code to see how this vacuum impregnation system works
High cleaning quality for upmarket special purpose machinery manufacture
In order to make cleaning gunmetal parts as efficiently as possible, Eckerle Industrie GmbH in Ottersweier uses a MAFAC JAVA type spray-flooding machine. In particular the new vector kinematics method is designed to meet the high cleanliness requirements of these customers from the medical technology industry with efficiency and reliability.
For over 50 years, Eckerle has been manufacturing complex assembly groups and system components that are used in a variety of industries. For the renowned medical technology company Maquet, for example, which has been part of the Getinge Group since, the CNC specialist manufactures three assembly groups for the electrical operation of operating tables. Production Manager Reiner Schäfer explains what is important for these high-quality components: “Modern operating tables are highperformance medical devices that use many sophisticated technical features to ensure safe and easy patient positioning. To ensure that they can be used reliably for a long time, all components must meet the highest quality standards in terms of materials, technology and workmanship. For our assembly group it is important that the surfaces do not show any contamination from machining and leave the cleaning process absolutely dry. This enables us to guarantee not only corrosion-free storage and shipping, but also trouble-free further processing at our customer’s site.” Up to now, the components have been washed in a simple cleaning system, then dried manually, stored, and cleaned and dried again shortly before shipping. “This procedure had since become uneconomical and would not have been able to meet the increasing demands of our customers for much longer,” summarises Ferdinand Ernst, team leader at Eckerle.
Multi-faceted requirement profile for cleaning
The new machine is now meant to combine these work steps and make them more efficient. Before the gunmetal components reach the final cleaning stage, they pass through a multi-stage production chain. They are deburred and polished after the turn-milling process. At the end of the process, their surfaces show machining residues such as cooling emulsion, polishing dust and chips that must be carefully cleaned off. It is important that all regions of the component are free from particles, because even the smallest contamination can jeopardise the assembly requirements at Getinge-Maquet and prevent the necessary smooth running of the engines installed in them. In view of these cleanliness requirements, the numerous boreholes and undercuts in the component parts and the now very small particle sizes of the contaminants pose a challenge. In addition, gunmetal creates further requirements because it is a rather soft material and, due to its high copper content, tends to stain and develop verdigris. For the cleaning process this means: it should be effective and at the same time very gentle and involve a drying system that releases components with stain- and moisture-free surfaces at reduced temperatures. For this reason, the Eckerle technicians decided to use the MAFAC JAVA spray-flood machine with two-tank technology. In combination with the technology options of vector kinematics and
© Klaus Hohnwald/Getinge
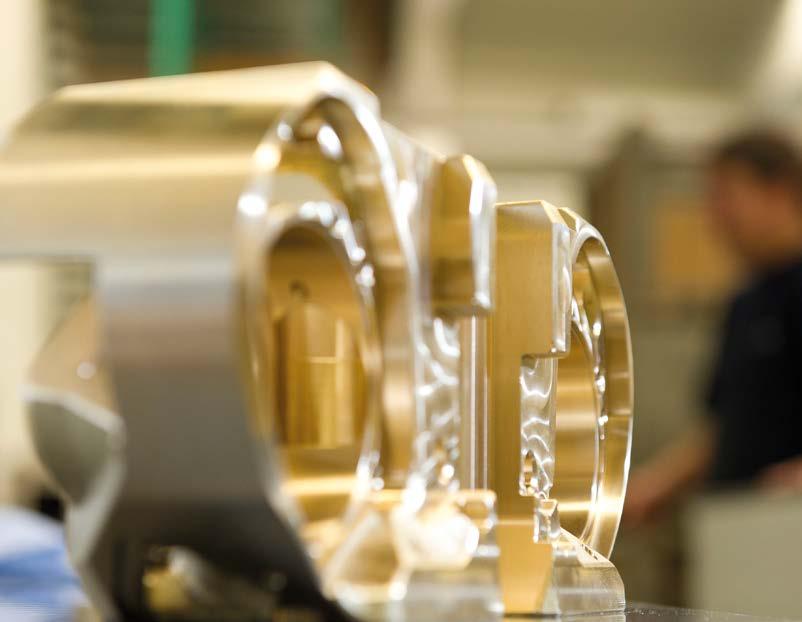
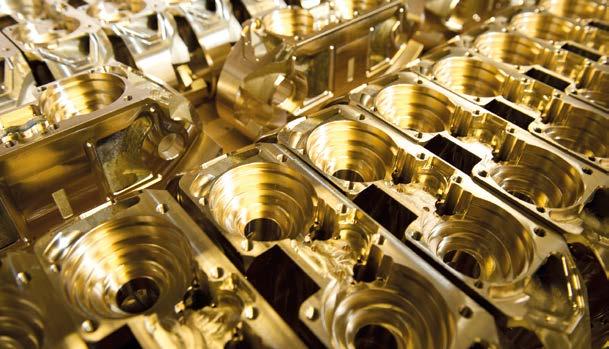
Eckerle Industrie GmbH has been manufacturing a three-part gunmetal central body casing for the assembly of operating tables for more than 15 years. After CNC processing with subsequent deburring and polishing, the surfaces show contaminations like cooling lubricant, chips and polishing dust. Their complex geometries are an additional cleaning challenge.
© MAFAC
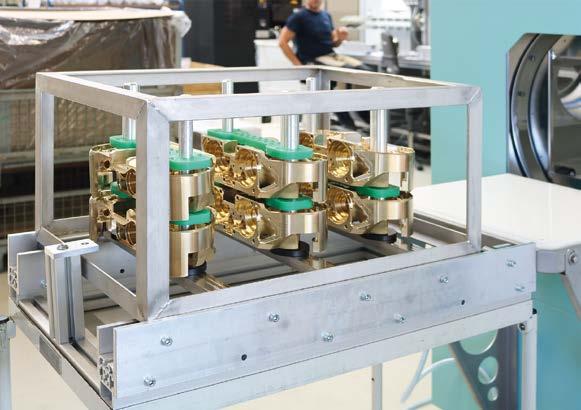
© MAFAC

© MAFAC
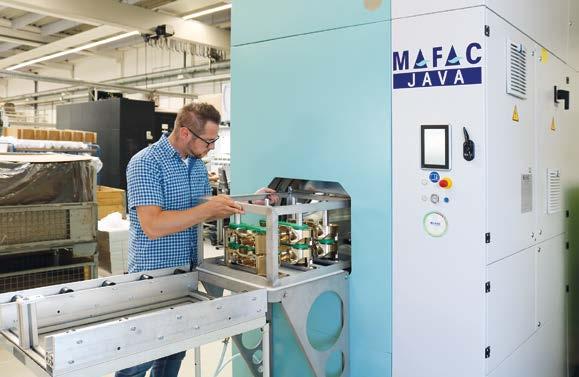
The compact MAFAC JAVA with double-bath technology is equipped with the new MAFAC vector kinematics and ensures larger and more even impact on the component parts during cleaning and drying with strong turbulences. Small batches of the components are fed into the cleaning process as sensitive components. The machine is loaded manually via a mobile transfer system.
vacuum drying, it achieves high cleanliness values on the surfaces within a short time while being gentle on the material and reliable for all component regions.
Vector kinematics - even more movement for better effectiveness
In particular by choosing MAFAC vector kinematics, Reiner Schäfer and Ferdinand Ernst demonstrate their pioneering spirit and a farsighted view in to the future. “What we are dealing with here is a further development of the patented process technology of counter- or corotation of the spray and basket receptacle system”, explains Sascha Klos, sales representative at MAFAC. The new principle succeeds in achieving a greater and more uniform impact on the component parts during cleaning and drying with strong turbulence. For this extra movement, the nozzle tube performs both a rotating and a rocking movement. The rocking movement is performed around its own axis by 35° to both sides. The basket receptacle system rotates synchronously at an optimally adjusted speed. This results in an optimally coordinated interplay of nozzle tube and basket movement, with both synchronous and counter-rotating operation being possible. As a result, workpieces are impacted more evenly and hard-to-reach regions such as blind holes are reached even better. Due to the higher mechanical part, vector kinematics leads to the desired cleaning result in a shorter time. This improved flow effect both during the cleaning and the drying phase, which had already made a very positive impression on them at the parts2clean trade fair, finally convinced the two technicians to invest in
the new MAFAC vector kinematics: “With this method, we do not only gain effectiveness. In future, we will also be able to respond more flexibly to changes in the range of parts or to growing cleanliness requirements”, says Reiner Schäfer.
Two-stage cleaning process with bypass filtration
Small batches of the parts, which measure approximately 500 x 200 x 200 millimetres (l/w/h), are fed into the cleaning chamber as sensitive components, where they undergo an approximately 11-minute treatment process with the sequence cleaning - rinsing - vacuum drying. During the cleaning phase from tank one, to which 2.5 percent of a mild cleaning medium is added, a spraying and flooding process alternate. Flooding is carried out cyclically, i.e. two-thirds of the water from the cleaning chamber are drained and then re-flooded. This process is repeated several times. Parallel to this, the nozzle and basket receptacle system carry out a counter-rotating movement, using a 35° rocking movement of the basket to protect the parts. The temperature of the entire wet phase is 60° C. Before the process switches to the rinsing phase, a so-called lifting process (blowing off of the component parts) prevents the carryover of particles and media. Afterwards, the parts are rinsed with demineralised water from tank two. This is particularly important because of the high copper content in gunmetal and the associated risk of oxidation. This means that the conductivity in the water must remain low, which is why the rinsing bath is also equipped with a rinse care module. This contains an activated carbon unit and two ion exchange units. In addition, it is permanently filtered with a resin cartridge in the bypass. “That such an additional component is recommendable and ultimately proves its worth was already apparent during the test cleanings in the MAFAC technical centre,” explains Ferdinand Ernst. There it also became obvious that the cleaning agent must be matched to the cooling lubricant so that the component parts leave the cleaning chamber without a grey haze. Therefore, the decision was made to use Kluthe’s mildly alkaline cleaning agent HAKAPUR 56170, which, in combination with the water-miscible cooling emulsion of the HAKUFORM range, also from Kluthe, produces high cleanliness values.
Vacuum drying - an important final step
The drying phase is an important stage of the treatment to ensure surface quality. To make sure that the components leave the machine without residual moisture, the MAFAC JAVA is equipped with a warm air impulse blowing system and a vacuum drying system. Warm air at 40 °C is first supplied to the treatment chamber via the impulse blowing system. Based on the basket-nozzle rotation, the rotational movement and the impulse-like impact ensure an efficient heat and mass transfer, achieving homogeneous heat distribution. In addition, the water droplets are broken up into many small units by the compressed air pulses. The resulting increased surface area means that the water can dry faster. With the subsequent vacuum drying process, which is particularly suitable for heat-sensitive materials
© MAFAC © MAFAC
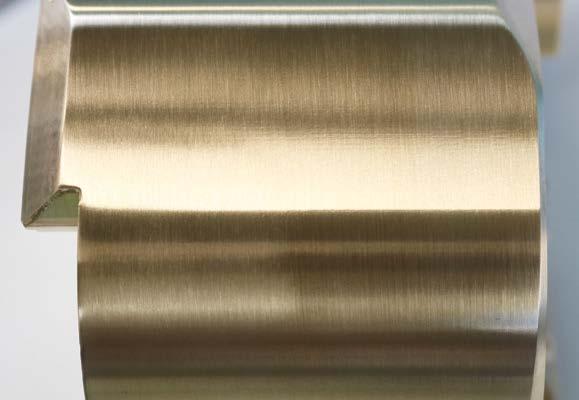
An 11-minute cleaning and drying process under the impact of high turbulence frees the component parts effectively and gently from any contamination. After cleaning and drying the surfaces of the component parts are free from residue and absolutely dry. The high copper content in the gunmetal could lead to oxidation if there is any residual moisture. This is meant to be avoided with additional vacuum drying.
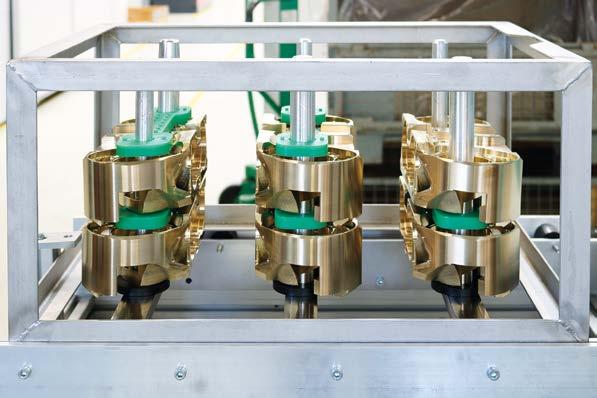
such as gunmetal, the material to be dried is subjected to negative pressure. This leads to evaporation of the water at lower temperatures, as the boiling point of the water is reduced. Under this effect, the drying time is considerably reduced while the surfaces of the components are still absolutely dry and free of residues.
An important step towards the future
Now that the MAFAC JAVA has been in use for five months, the first positive effects in terms of economy and cleaning quality are already becoming apparent. For Ferdinand Ernst and Reiner Schäfer this is an important aspect in view of the increasing cost and time pressure in the future. “The demands of our customers in the medical sector but also in all other sectors are very high and will increase in the future. As the parts produced are always custom-made products with high quality standards, we want to raise our standards in special purpose machinery manufacture and set them up safely for the growing demands. The acquisition of the MAFAC JAVA with the new vector kinematics was a significant step in this direction and is expected to increase our USP value in the industry and create a competitive advantage,” says Reiner Schäfer.
About MAFAC
MAFAC is one of the leading manufacturers in aqueous parts cleaning. The company offers a wide range of compact series machines for a large variety of cleaning requirements tailored to customers’ requirements, for example in the automotive and aerospace industry, in machine building, metal-cutting production, hydraulic and medical engineering, and in the electrical industry. All machines are developed and produced at the Alpirsbach site in the Black Forest by currently almost 100 employees. Founded in 1968, MAFAC has been involved in industrial parts cleaning since 1974 and has focused on this field since 1990. The patented cleaning technology of counter- or co-rotating spray system and basket receptacle system sets new standards in terms of cleanliness and efficiency. The company is globally active with a network of technical agencies and its own branch in France.
With its CNC machining division, Eckerle Industrie GmbH from Ottersweier near Rastatt offers the manufacture of individual parts and assembly groups according to drawings. Everything is possible, from prototypes and small series to the production of medium-sized series. The company was founded as a crafts enterprise in Bühl in the Baden region in 1968 and is now part of the family-run Eckerle group of companies, together with Eckerle Holding and Eckerle Automotive. It was taken over by the Prettl Group in Pfullingen at the end of 2019.
Purely aqueous
Inspired by nature. Developed for industry.
As family business with more than 50 years of experience, we are specialists in the field of aqueous parts cleaning. Our claim unites tradition and innovation, our machines are ecological and energy-efficient. We develop process solutions to customer specifications and serve our customers worldwide through a reliable network of sales partners.
MAFAC – E. Schwarz GmbH & Co. KG · Max-Eyth-Str. 2 · 72275 Alpirsbach · www.mafac.de