
29 minute read
BRAND NEW
Cortec has launched EcoShield VpCI-380, a DTM fast drying, water-based fluoropolymer modified acrylic one-coat system that provides corrosion protection and weatherability on metals in harsh outdoor environments.
The latest addition to Cortec® Corporation’s portfolio of Micro-Corrosion Inhibiting CoatingsTM is EcoShield® VpCI®-380 topcoat for industrial painters, a fast drying, water-based fluoropolymer modified acrylic one-coat system that can be applied direct to metal and provides corrosion protection and weatherability on metals in harsh outdoor environments. The EcoShield® VpCI®-380 system provides UV resistance (colour and gloss retention), and gives optimal outdoor performance without cracking or chipping upon prolonged exposure to sunlight. Its hardness (H-2H Pencil Hardness), moisture resistance, and fast-dry properties make it particularly suited for air-dry/force-dry industrial finishes. The coating also provides corrosion protection, having passed more than 1,000 hours in ASTM B117 salt spray conditions and ASTM D1748 humidity conditions at 4.0-4.5 mils (100-112.5 µm) DFT.
Fields of application of EcoShield® VpCI®-380
EcoShield® VpCI®-380 can be applied direct to metal (DTM) on carbon steel and top-coated over a wash primer (e.g., VpCI®-373 Green) on stainless steel, galvanized steel, and aluminium. It shows excellent 5B adhesion and even adheres well to some engineered plastics for greater versatility. It is thixotropic and exhibits alkyd-like gloss, flow, and levelling properties with good resistance to sag. It can be tinted to most custom colours and has a VOC of 1.6 lbs/gal (192 g/L). Originally designed for the railcar industry, EcoShield® VpCI®-380 is an alternative to solvent-based, zinc rich coatings and can be used in a wide range of industrial painting markets such as refineries, power plants, outdoor storage yards and for any other metal equipment application to achieve protection against corrosion in harsh outdoor environments. It can also be used for mass-produced parts needing to be force-dried with a high durability, high gloss coating for outdoor use.
For further information: www.corteccoatings.com
© Cortec
AkzoNobel Supplies Powder Coatings for the Pearl River Delta Project
AkzoNobel will provide Resicoat R2 coatings for the coating of potable water pipes’ interior, as part of the Pearl River Delta water resource allocation project in China.
AkzoNobel signed an agreement with Guangdong Water to provide high-performance Resicoat R2 coatings for the Pearl River Delta water resource allocation project, a major infrastructure project in China, for the coating of potable water pipes’ interior.
About the Pearl River Delta Project
Designed to ensure the supply of clean and safe potable water to more than 50 million people, the landmark project will feature the highest water transmission pressure and the longest shield tunnel in the world. It consists of a mainline, a branch line, three pumping stations and four storage reservoirs. In fact, the Pearl River Delta is one of the world’s most densely populated areas and the water supply has to be continuously expanded. The water resource allocation project is designed to channel water from the Xijiang River in the west to the eastern Pearl River Delta. As well as helping to prevent water scarcity, it will create emergency water reservoir for the Southern areas in China including Hong Kong. “We have rich global experience in drinking water and pipeline projects and will continue to play our part in improving people’s lives through our eco-premium and high-performance solutions,” says Daniela Vlad, Director of AkzoNobel’s Powder Coatings business. “We’re excited to be contributing to this significant project by supplying products that will provide comprehensive protection to the new water pipeline.”
Resicoat R2 features
Resicoat R2 coating is specially designed to be used in the drinking water industry, typically being applied to valves and fittings and water pipelines. The product’s high density and high hardness provide robust abrasion resistance, anti-cathodic stripping, anti-bending, anti-corrosion and adhesion, all of which combine to help prolong the lifecycle of pipelines. Resicoat R2 has also received the drinking water safety product license in China. “Applying safe, environmentally friendly coatings to potable water projects is fundamental to ensuring water quality throughout the delivery process,” adds Karen Yin, AkzoNobel Powder Coatings’ Regional Commercial Director for North Asia. “Our Resicoat range can therefore play a vital role in drinking water sanitation and the reinforcement of regulations and environmental protection.”
For further information: www.akzonobel.com
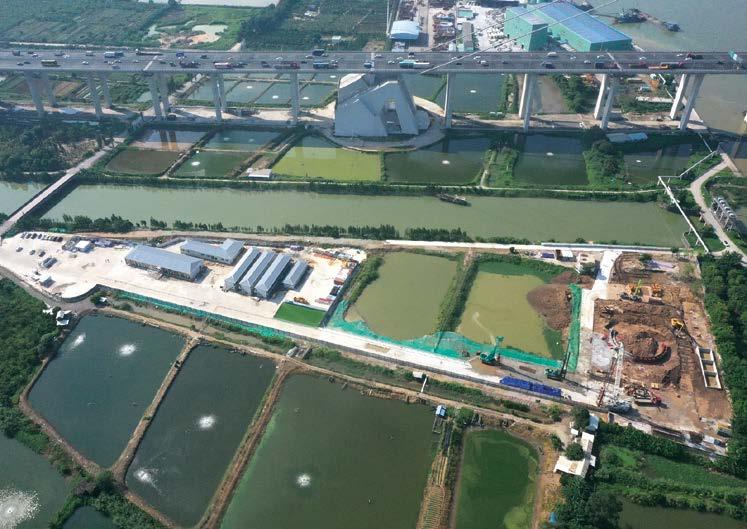
© AkzoNobel © AkzoNobel
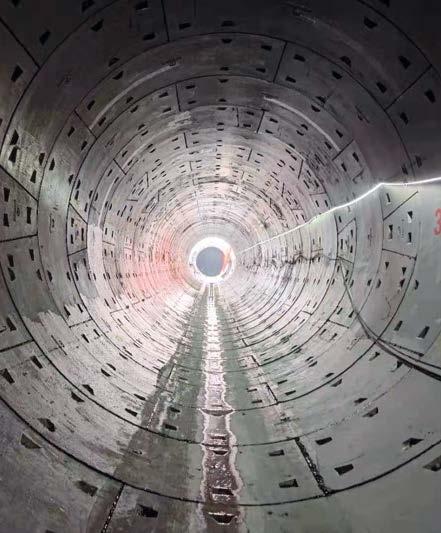
Jotun, HHI and HMM Collaborate to Challenge Biofouling and Ensure Green Proactive Hull Cleaning
Hyundai Heavy Industries has signed an agreement with Hyundai Merchant Marine and Jotun to ensure cleaner, more efficient and greener vessel hull performance and optimal environmental protection.
On December 8 2020, Hyundai Heavy Industries (HHI), which controls 10% of the global new construction market, has signed a MOU with container line giant HMM and marine coatings supplier Jotun to use its Hull Skating Solutions (HSS) on a number of new vessels. This technology, launched by Jotun at the beginning of the year, consists of HullSkater, which adheres to ships and gently deletes all biofouling, the SeaQuantum Skate antifouling, and proactive condition monitoring using a proprietary big data algorithm tailored to the needs of individual vessels. According to Geir Axel Oftedahl, Jotun’s Director of Business Development, HSS is “the ideal combination for vessels facing the toughest biofouling conditions and perfect for protecting new builds in the outfitting and testing phases.” Biofouling is in fact an important problem that affects ships that are inactive for long periods. But, HSS is able to clean the hulls before biofouling forms, eliminating associated drag, fuel consumption and emissions, protecting ship linings and safeguarding ecosystems from potentially invasive species seeking to populate them. HSS’s unique robotic cleaning units are controlled by specialized Jotun operators via 4G connections.
A joint effort in the name of sustainability
“HHI and HMM have understood the importance of the problem of biofouling and are committed to better environmental protection by signing a unique MOU. The innovative technology will be used to tackle the biofouling challenge simply, effectively and with minimal disruption and maximum impact. We believe this is a new way of working for a new generation of forward-thinking owners and shipyards and we are happy to be involved in such an important industrial project”, said Morten Sten Johansen, Regional Marine Director, North East Asia. HHI is currently committed to building a series of state-of-the-art 16,000 TEU container ships for HMM and the HSS technology will be used to ensure that the ships meet environmental key performance indicators, keeping hulls clean, pristine coatings, providing optimum efficiency and limiting any potential release of biocides. The HullSkater will move from hull to hull during the main stages of outfitting. In addition, HMM has stated that it is committed to building an entire sustainable fleet that will allow the company to achieve zero CO2 emissions by 2050. “Jotun’s solution is perfect for achieving this ambitious project”, commented Jong-Chul Choi, Executive Vice President of HMM. Oh-Min Ahn, HHI’s Executive Vice President, further added: “Sustainability is at the heart of our business and we are focused on partnering with pioneering owners and suppliers to pave the way for a cleaner, greener industry that can set sail towards achieving IMO’s decarbonization goals. It will be very interesting to see HullSkater solve the biofouling problem once and for all. We are convinced that this development can significantly contribute to changing the future in the marine coatings market.” Jotun estimates that if all ships facing severe biofouling problems adopted the proactive HSS approach, marine CO2 emissions could be reduced by at least 40 million tonnes per year.

For further information: www.jotun.com
© Jotun

Evonik has launched VP 4200, a new structure modified silica type for anti-fouling coatings to reduce biocide content. The new product allows for a more controlled release of biocide, which is needed in lower quantity for the same performance, and ensures a low thickening effect and easy incorporation.
FIT FOR WORKERS
WHERE DOES IT WORK? WHERE YOU DO.
Evonik’s latest addition to the silica-based AEROSIL® product group is VP 4200, a new structure modified silica type with free OH-groups that enables formulating more eco-friendly, cuprous oxide containing anti-fouling coatings. VP 4200 is tailor made for both CDP (Controlled Depletion Polymer) and SPC (Self-Polishing Coating) coatings. Thanks to its ability to form a complex with Cu2O, VP 4200 ensures a better control of the release of the biocide. The performance is guaranteed by its formulation with only 10 pbw% cuprous oxide and 4 -6 pbw% VP 4200, which leads to the same performance as the standard type with up to 50 pbw% Cu2O.
VP 4200 has a relatively low thickening effect, so higher amounts can easily be incorporated into the systems, especially in combination with TEGO® Dispers 1010.
© Shutterstock

FIT FOR WORKERS
WHERE DOES IT WORK? WHERE YOU DO.
MATE-XT is the exoskeleton that brings the qualities of MATE to an eXTreme level.
The new MATE-XT is the latest version of the Comau exoskeleton that has been vastly improved, taking its benefits to the next level and adding important new features.
Resistant to water, dust, UV rays and high temperatures, it is ideal for applications in difficult environments..
MATE-XT is easy to put on, easy to adjust and easy to use, ensuring the worker: • Reduction of muscle fatigue MATE-XT è l’esoscheletro che porta le qualità di MATE ad un livello eXTreme. • Improved posture and comfort Il nuovo MATE-XT è l’ultima versione dell’esoscheletro Comau che è stato estremamente migliorato, portando i suoi vantaggi a un livello superiore e aggiungendo nuove importanti • Reduction of risk from biomechanical overload funzionalità.certified with EAWS methodology Resistente all’acqua, alla polvere, ai raggi UV e ad alte temperature è ideale per applicazioni in ambienti difficili. • Better quality of work MATE-XT è facile da indossare, facile da regolare e facile da usare, garantendo al lavoratore: • Riduzione dell’affaticamento muscolare MATE-XT works when, where and how you do. • Postura e comfort migliorati • Riduzione del rischio da sovraccarico biomeccanico certificata con metodologia EAWS • Migliore qualità del lavoro Come and find out at comau.com/mate
MATE-XT lavora quando, dove e come fai tu.
Vieni a scoprirlo su comau.com/mate
Cortec Launches the World’s First Compostable Corrosion Inhibiting Stretch Film
Adding to its commercially compostable film technologies, Cortec has recently launched EcoStretch, a corrosion-inhibiting stretch film powered by Nano VpCI.
EcoStretch by Cortec is the world’s first commercially compostable corrosion-inhibiting stretch film, which combines commercially compostable resins with Vapour phase Corrosion Inhibitor Technology (VpCI®) for corrosion protection of multiple metal types, including aluminium, galvanized steel, carbon steel, silicon steel, stainless steel, copper, brass, and cast iron. equipment or components that need to be kept rustfree while minimizing the environmental impact of traditional plastic packaging. Therefore, it can be used for warehousing or shipment of metal parts, metal equipment or steel coils in the appliance, automotive, electronics, energy, engine and turbine, marine, manufacturing, mining, structural steel and tubing and pipe industries.
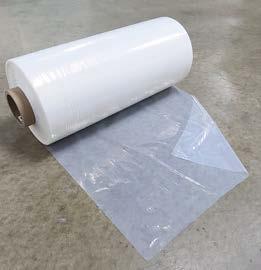
How it works
© Cortec
Laboratory Compostability Study
Due to its high elasticity, operators can increase EcoStretch powered by in accordance with ASTM D6400 the tension of EcoStretch as needed. The self- Nano VpCI is the world’s first and EN 13432 adhering film bonds each layer to itself for added commercially compostable EcoStretch meets the ASTM D6400 standard for strength. Once the metals are wrapped, EcoStretch corrosion-inhibiting stretch film. commercial composting1 and may avoid tariffs, fines, will provide contact, barrier, and vapour-phase and tip fees in areas where polyethylene is prohibited corrosion inhibition while also helping keep dust, dirt, and moisture or restricted. off warehouse stock. EcoStretch is available for worldwide distribution from Cortec EcoStretch is self and curb stable and will retain its integrity until Advanced Films (Cambridge, Minnesota) in North America and disposed of properly. After use, the EcoStretch can be sent to a EcoCortec (Beli Manastir, Croatia) in Europe. commercial composting facility to turn into a soil amendment for future use. For further information: www.cortecadvancedfilms.com
Fields of application
EcoStretch is particularly suited for stretch-wrapping metal
1 This product is intended to be composted in a commercial composting facility operated in accordance with best management practices. Check locally to see if such a facility exists in your community and if they will accept this product. Not suitable for backyard composting.
© Cortec
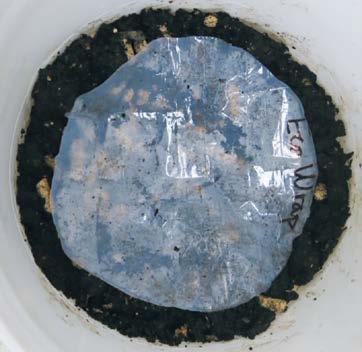
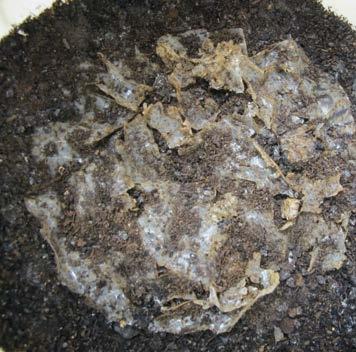

Laboratory Compostability Study in accordance with ASTM D6400 and EN 13432: From left to right – Day 1; Week 3; Week 6.
Spray Galvanising as Essential for Motorist Safety
Numerous accidents have been caused by the corrosion of bridge and tunnel support structures. Hot spray galvanising is a useful protective solution that ensures that both structural and non-structural elements have a service life of more than 80 years.
The death of a truck driver in the Lehigh tunnel in Pennsylvania (USA), occurred on February 21, 2018, was caused by the detachment of a lighting fixture from the vault due to the breaking of a corroded support bracket. The analysis conducted by the Federal Highway Administration (FHWA) confirmed that the PVC coated bracket was completely corroded. Subsequent inspections found that other similar support systems were corroded and these were immediately replaced. It is worth noting that spray galvanising is the most effective corrosion protection system in such highly corrosive environments, not only for structural elements, such as the iron reinforcements of reinforced concrete, but also for non-structural ones, including lighting systems, sign posts, gutters, etc. Indeed, spray galvanising is the only system that enables to apply zinc coatings up to 300-500 microns, guaranteeing a service life of more than 80 years before first maintenance is required.

For further information: www.colimet.it
© Wikipedia
1 – The entrance to the Lehigh tunnel in Pennsylvania (USA), where in February 2018 a lamp broke off causing the death of a truck driver.

2 – In December 2019, a part of the ceiling of the Berté tunnel along the A26 motorway in Italy (Genova-Gravellona Toce section) collapsed, fortunately without consequences for the drivers of passing vehicles.
© Motorionline S.r.l.
© Monti Group



Monti Group Expands with MontiPower Brasil
MontiPower Brasil is a new joint venture between MontiPower America’s Inc. and Tecnofink LTDA created with the aim to market the entire range of the Monti’s surface preparation products and services to the South American country.
MontiPower America’s Inc., the North American subsidiary of Monti - Werkzeuge GmbH, has entered into a joint venture agreement with
Tecnofink LTDA, the Monti’s long-time distributor in Brazil, to market the company’s surface preparation solutions - including the patented Bristle
Blaster - in the South American country.
The new venture, which is based in Macaé in the Rio de Janeiro state, will be called MontiPower Brasil and it will introduce the entire range of Monti surface preparation products and services under the Monti brand to the
Brazilian market. Dirk Pohlmann will move from Tecnofink to MontiPower Brasil to take up the role as General Manager of the new venture. Monti Group CEO J.F. (Frits) Doddema said “Brazil is an incredibly interesting market for us across several key industry segments and we are very pleased to be able to combine forces with Tecnofink to serve these growing markets. Tecnofink is an experienced industry leader in the coatings industry in Brazil and this combination under the Monti brand will give us a stronger and more focused platform for our surface preparation technologies. We see great opportunities in Brazil, and we are excited to get underway as MontiPower Brasil”.
Emilio Castro, CEO of Tecnofink LTDA, added “It is always an honour to work with the Monti technology in Brazil, and I am very pleased that Thomas Fink and I are able to take this step today with Monti and create
MontiPower Brasil. Tecnofink has an important position on the Brazilian market and this new venture under the MontiPower brand will better allow us to pool our collective resources and educate and grow the surface preparation market. Monti is a company with a unique vision of this market and over the past couple of years it has introduced many new innovations and tools that we will bring to Brazil. We look forward to working together with MontiPower’s international team to develop and build the MontiPower Brasil business”.
For further information: www.montipower.com
AkzoNobel Partners with Polar Pod for Pioneering Scientific Mission in Antarctica
AkzoNobel is the exclusive paints and coatings partner of a pioneering scientific expedition which will send an oceanographic platform around Antarctica to study the Antarctic Circumpolar Current.
Polar Pod, created by explorer and environmentalist Jean-Louis Etienne, will enable scientists and explorers to study the Antarctic Circumpolar Current, which has a great influence on the Earth’s climate and contains a reserve of marine biodiversity.
How Polar Pod works
Polar Pod is a 100-metres high platform, thus taller than the Statue of Liberty, that will be towed horizontally to its first study area and tilted vertically by filling seawater ballast tanks – when most of the structure will be submerged. As it gradually makes it way around the Antarctic continent, driven by the circumpolar current (thus ensuring zero emissions), it will allow the acquisition of data and long-term observations that will be transmitted to researchers, oceanographers, climatologists and biologists at 43 scientific institutions in 12 countries. Operating in an area that sailors refer to as the Furious Fifties (between 50° S and 55° S), studies will include: air/ocean exchange measurements, in particular related to CO2; wave dynamics; plankton collection and evaluation of the impact of acidification; acoustic inventory of marine fauna; validation at sea of satellite measurements and aerial observation of marine life. The Polar Pod will be supported by a dedicated offshore supply vessel, which will be permanently assigned to the mission. It will leave the nearest port to join the platform on its drift course as it crosses the Indian, Pacific and Atlantic Oceans.

AkzoNobel’s sponsorship
AkzoNobel will sponsor the 1,000-ton platform for the next five years, © AkzoNobel from project construction through to the completion of its three-year mission, which is expected to start in December 2023. This collaboration has a strong link to AkzoNobel’s 2030 “Planet” ambitions, which include reducing carbon emissions by 50% and moving towards zero waste as a company. “This is a really exciting partnership and a fantastic example of how we’re prepared to go to the ends of the Earth to help our customers and discover pioneering ways to become even more sustainable,” says AkzoNobel CEO, Thierry Vanlancker. “It represents an intriguing blend of visionary thinking and environmental ambition which fits perfectly with our own People. Planet. Paint. approach to sustainable business. We’re extremely proud to be involved.” “As an industry leader in sustainability and a global market leader in marine and yacht coatings, lowering our environmental impact on the planet and contributing towards ocean preservation are key aspects of our strategy,” adds Jean Michel Gauthier, Director of the company’s Marine and Protective Coatings business. “Sponsoring the Polar Pod expedition is a great way for us to help advance scientific knowledge of the pivotal role the Southern Ocean plays on the Earth’s climate and marine biodiversity. We’re looking forward to supporting the team and raising awareness of the program as the mission begins to gather momentum.”
For further information: www.akzonobel.com and www.oceanpolaire.org/en/polar-pod/
INNOVATIONS: PRESENT&FUTURE
Managing Hidden Risk
Simon Daly
Hempel A/S – Cwmbran, United Kingdom sida@hempel.com
Analysing customized coatings’ solutions is essential to hinder the corrosion under insulation (CUI) phenomenon. In this article Simon Daly explains how Hempel, one of the corrosion protection coatings world leaders, supports the applicators to overcome this issue.
The problem of corrosion under insulation (CUI) is one that affects a wide range of industries but is particularly common in equipment used within the petrochemical, refining, offshore and maritime industries which must contend with particularly corrosive environments. CUI, a localised form of corrosion, occurs when moisture becomes trapped between insulating materials and pipework, ductwork, valves and other key external equipment vital to the operation of many hydrocarbon facilities. This severe and particularly disruptive form of corrosion occurs on insulated carbon and low alloy steel as well as stainless-steel equipment that operate at a temperature range between 50-175°C, and as it is located out-of-sight is particularly difficult to detect and treat. If left undetected, CUI can result in catastrophic leaks or explosions, equipment failure, prolonged downtime due to repair or replacement, and safety and environmental concerns.
The issue of corrosion under insulation (CUI) is particularly common in equipment used within the petrochemical, refining, offshore and maritime industries.
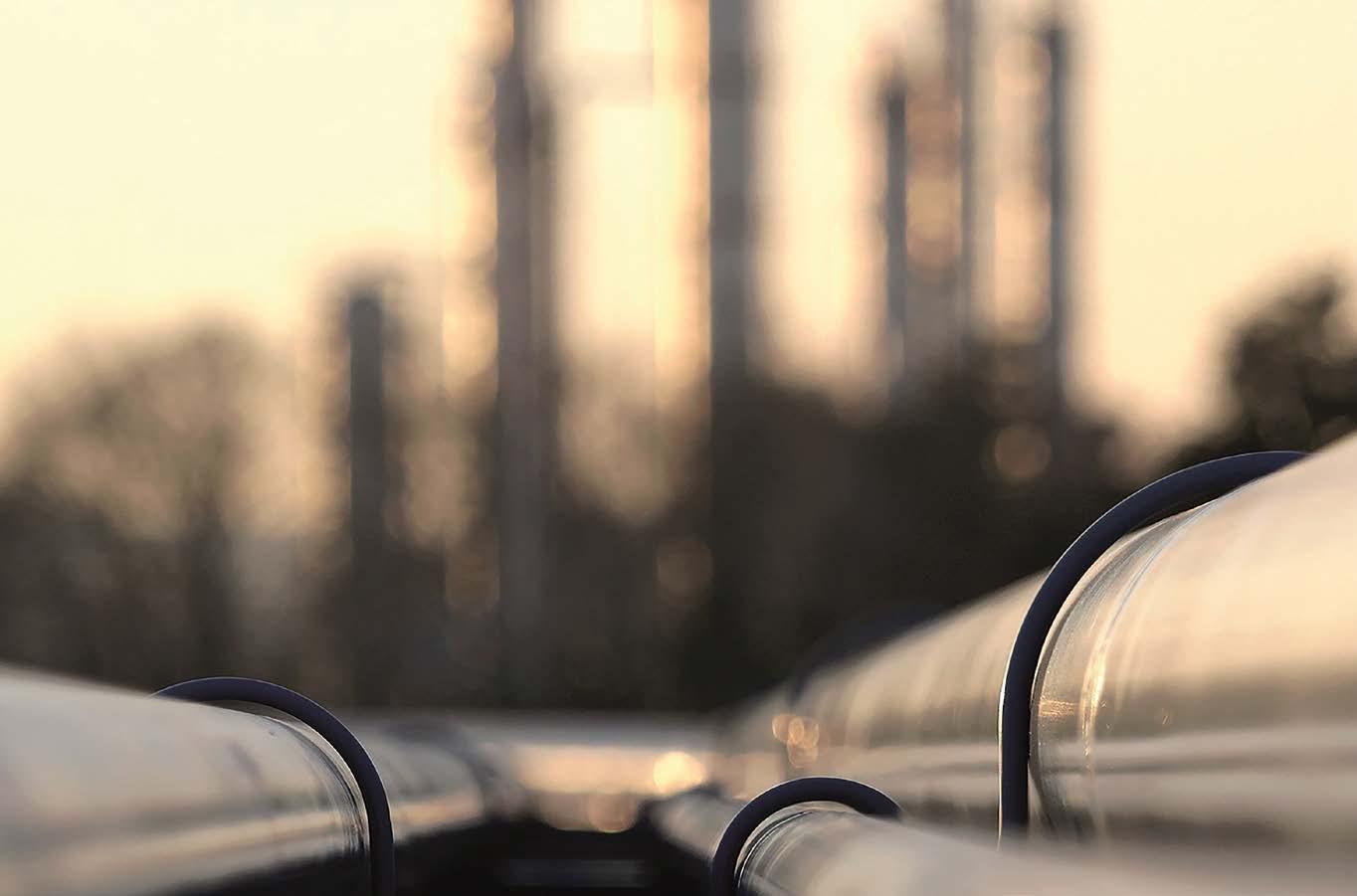
Protecting against CUI
Therefore, ensuring the correct protective coating systems are applied to piping and equipment at the point of construction is vital. However, as temperatures vary considerably across the constituent parts of each asset – be it a refinery or a pipeline, or adjoining processing and distribution infrastructure, temperature requirements usually require to be accounted for separately and protected with a suitable coating system. There is rarely a one-size-fits-all approach for selecting a coating solution. This makes preventing CUI across an asset and specifying a simple coating solution to meet the precise needs of each piece of equipment a challenging process. While there are asset-specific reasons for its development, CUI is most often caused by external water seeping through leaking or poorly maintained joints in outer cladding, or condensation formed within the insulation during process operations. As this moisture accumulates beneath the insulation, the water does not have the opportunity to evaporate and so settles on the metal surfaces in the space between the insulation and the equipment substrate, in time,
© Hempel leading to corrosion. Repeated drying and wetting cycles can result in concentration of salt species furthering corrosion. Protection from CUI and maintaining of asset integrity is reliant upon four key barriers: • Weathering barrier, the combination of insulation and jacketing/ cladding. • Coating barrier, the protective coating applied to protect the metallic surface. • Material barrier, the choice of the equipment material itself, steel, stainless-steel etc. • Design barrier, the combination of piping diameter, configuration and wall thickness. While damage tends to occur slowly, localised pitting corrosion may ultimately compromise the pressure integrity of the piping and equipment if allowed to progress unchecked. Additionally, it is very expensive to detect and correct. This is why it is worth dedicating time to working with a coatings supplier that will create a specification for each asset is a valuable use of project resource. While the
© Hempel

CUI occurs when moisture becomes trapped between insulating materials and pipework, ductwork, valves and other key external equipment.

© Adobe Stock
If left undetected, CUI can result in catastrophic leaks or explosions, equipment failure, prolonged downtime due to repair or replacement, and safety and environmental concerns.
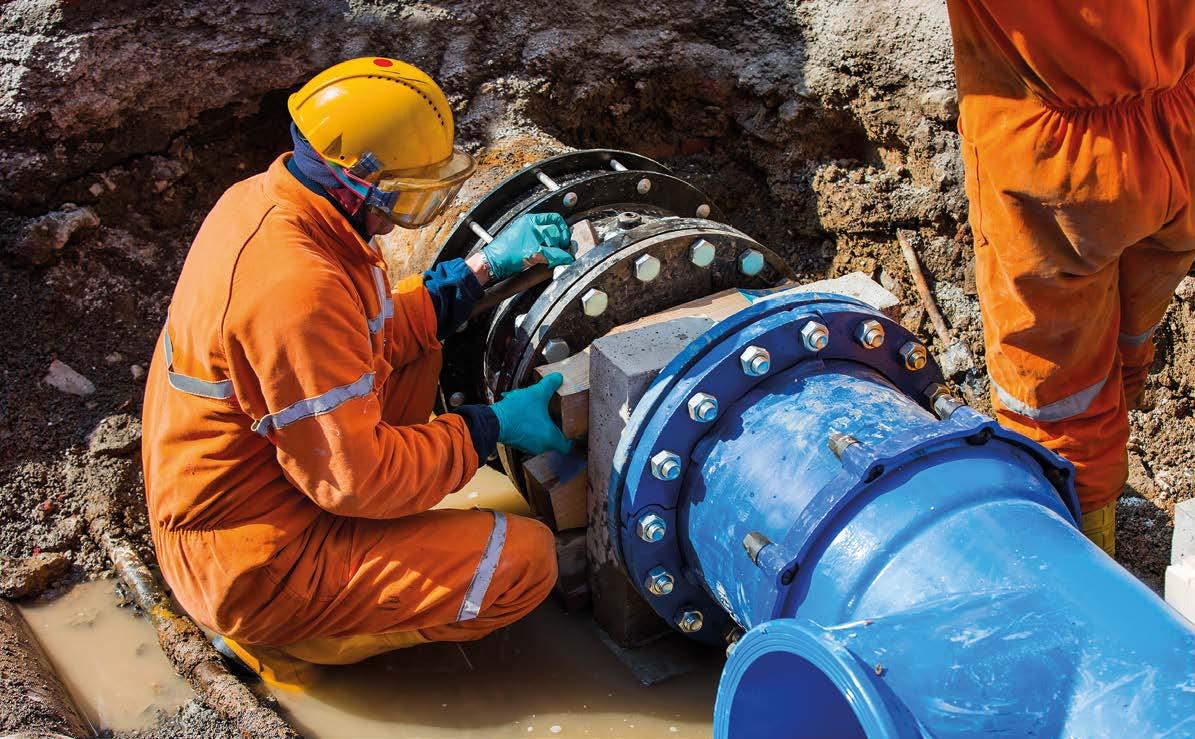
requirements for each project will differ in oil, gas and petrochemical processing and storage facilities, there are three types of coating systems that are commonly used. These are epoxy/epoxy phenolics, zinc silicates and inert multi-polymeric matrix type materials.
Understanding protective systems
Epoxy/epoxy phenolic coatings systems offer excellent performance when operating in the CUI temperature range, generally defined as being between 50-175°C. However, when temperatures exceed this range, or cycle, above and into this temperature range the coating is more likely to crack. This means water and moisture can get below the coating and directly onto the surface material, which is then susceptible to corrosion. Historically epoxy phenolic (or Novolac) materials have been used extensively due to their proven performance in “wet” conditions however recent years have seen the development of numerous pure epoxy systems which offer equivalent performance but without some of the drawbacks, such as sensitivity to over application. Zinc silicate systems, meanwhile, can also resist a wide temperature range – up to 400°C. However, the drawback with this solution is that zinc silicates are ‘sacrificial’ in their defensive approach, and degrade rapidly when exposed to hot, wet CUI environments. Overcoating them with thin film silicone paints - based on silicone resins – has not been typically successful due to their inability to provide suitable corrosion protection ultimately resulting in breakdown and exposure of the lower zinc layer to the CUI environment. Inert multi-polymeric materials such as Hempel’s Versiline CUI 56990 have been specifically designed to combine excellent high temperature performance with resistance to CUI conditions, without some of the drawbacks of other coating types. The product is a fibre-reinforced, single component, inert modified inorganic copolymer. In simpler terms, the Versiline CUI 56990 has been developed to provide better resistance to CUI as well as a unique resistance to micro-cracking.
© Adobe Stock
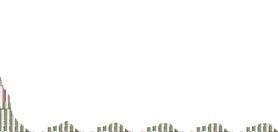
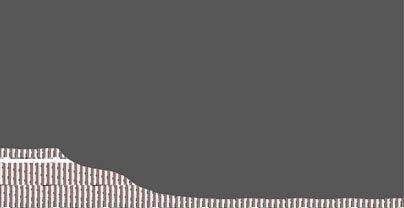

An example of the CUI phenomenon.
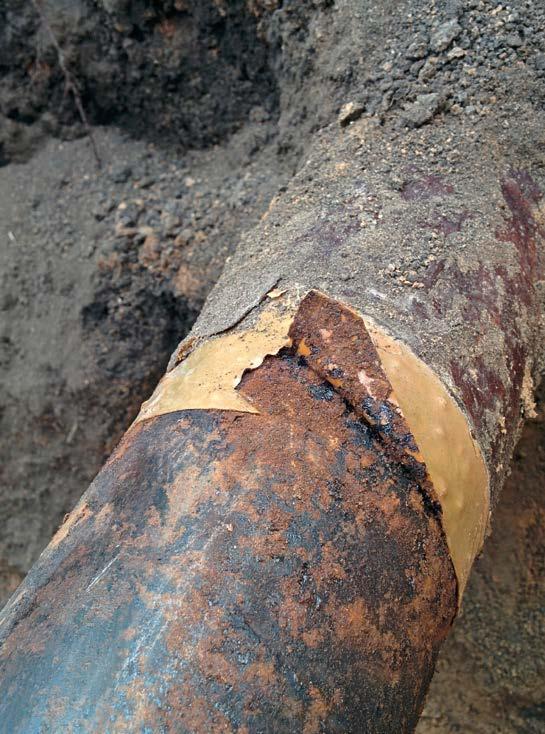
Providing additional reassurance
An inert multi-polymeric matrix type material, the Versiline CUI 56990 coating contains a silicone backbone that delivers a high temperature resistance. This means that in combination with its unique fibre-reinforced filler package, it is applied in thicker films and has superior barrier properties than thinner film silicones, which offer limited corrosion protection. The coating is formulated for resistance against temperatures of between -196 and up to 650°C, making it suitable for all types of assets processing hydrocarbons where corrosion under insulation can occur. An additional advantage with inert multi-polymeric matrix type materials is simplicity for applicators. Inert multi-polymeric matrixes can be specified for several temperature and performance categories, making them ideal for bulk items such as pipework and valves, or any items where the exact operating temperature may not be known at the design stage. Additionally, as the product is a single component it does
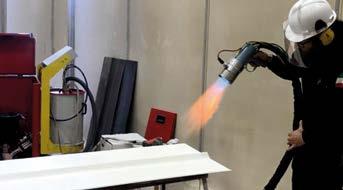

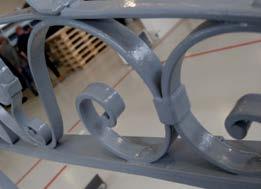

© Adobe Stock
According to a recent study, in a typical refinery piping is responsible for nearly 80 per cent of the hydrocarbon leaks but only receives 10-20 per cent of the inspection operations.
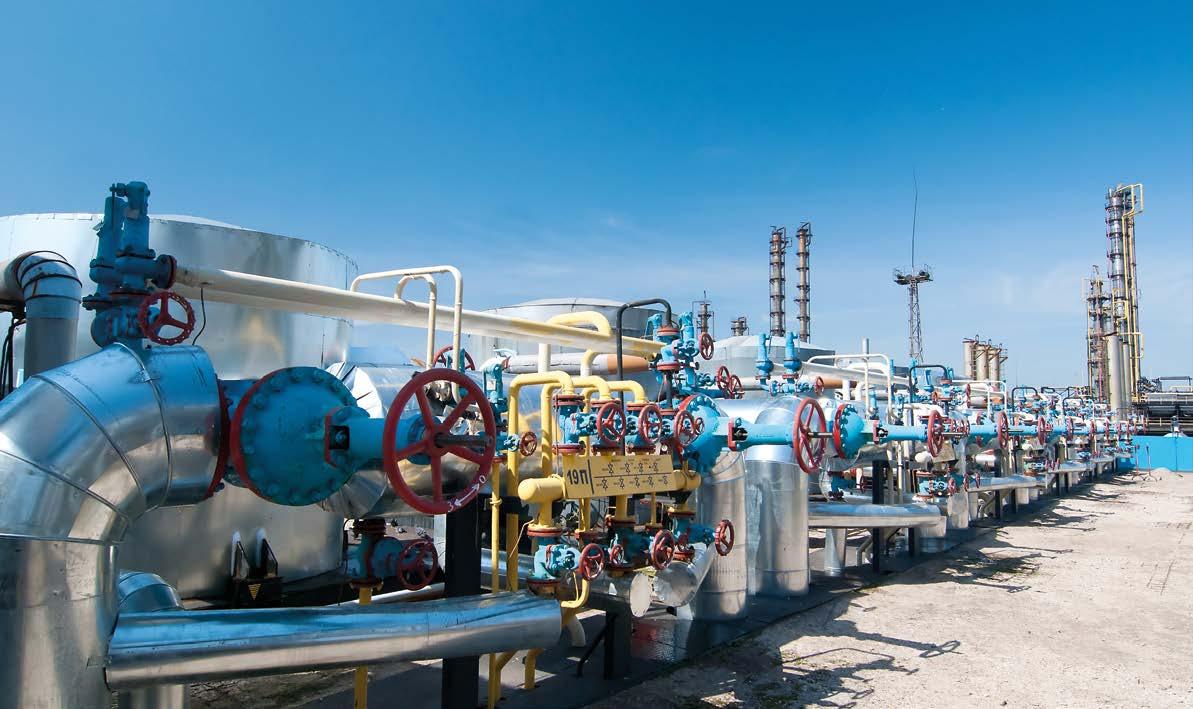
not suffer from high levels of wastage which may occur with 2-component materials due to the pot life being exceeded, which makes it ideally suited for tie-ins and field repairs where multiple locations require to be treated.
Managing lifecycle costs over build costs
According to the most recent IMPACT Study, developed by NACE International, the not-for-profit professional organisation for the corrosion control industry, savings of between 15 and 35 per cent of the cost of corrosion could be avoided or recovered by using suitable corrosion control practices. This saving was calculated to be in the region of USD $375 and USD $875 billion annually on a global basis. This is of course a wide estimation across all industries, but it does give an indication as to the scale of the problem. A recent study also suggested that whilst piping accounts for 50-60 per cent of the surface area in a typical refinery it is responsible for nearly 80 per cent of the hydrocarbon leaks but only receives 10-20 per cent of the inspection “effort”. Whilst clearly these numbers will differ from facility to facility, they highlight a real need to ensure that everything that can be done to help prevent CUI from a new construction stage will assist with the overall facility return on investment. The issue of corrosion under insultation is one that impacts the profitability of every asset in the downstream supply chain. While the impact may not be sudden, and can go undetected for many years, the costs incurred can be considerable. Therefore, investing in the right protective coating solution to protect against CUI should therefore be considered into the total cost of ownership of the asset. The cost savings from early corrosion control, and through the implementation of a robust corrosion management system will be returned. With the application of the most suitable CUI coatings, properly installed, maintenance costs will decrease over time, with the additional benefits of less production downtime, and – most importantly – a lower risk of harm to people or the environment. ‹
© ITF

The shot blasting system designed and manufactured by ITF for domestic boilers.
INNOVATIONS: PRESENT&FUTURE
An Innovative Technology for Automatically Shot Blasting the Internal Surfaces of Electric Water Heaters
Davide Silva
ITF Srl, Mesero, Milan, Italy davide.silva@itf.it
Coating the inside of their tanks is essential to protect electric water heaters from corrosion, since, by their very nature, their internal surfaces are cyclically in contact with water, whose aggressiveness increases as the operating temperature rises. Typically, indeed, the finishing cycle of these devices for domestic use focusses on the internal surfaces of their tanks and it involves mechanical pre-treatment through shot blasting and enamelling with a liquid or powder product. The coating lines required for finishing boilers can be semi-automatic or automatic. These are faced with several critical issues, including the significant dimensional variability of tanks, the need to work with a continuous flow and a high efficiency degree, and the high coating quality required.
ITF, a company active in the production of shot blasting, industrial cleaning, and deburring equipment, has developed very innovative, advanced automatic shot blasting lines for electric water heaters that have already been installed all over the world. These are highly efficient and they can be easily integrated with downstream process steps (i.e. enamel application and curing), thus creating fully automatic enamelling plants manned by a few operators who handle the loading and unloading of tanks.
Main features of the automatic shot blasting system
Electric water heaters consist of a carbon steel tank with an enamelled inner surface. Shot blasting enables the tank’s metal surface to be properly prepared for subsequent enamel deposition, especially when using the powder enamelling technology. The plant developed by ITF is a multi-station system (four or more, depending on production requirements) with a step-by-step movement that does not involve rotation of boilers. After being loaded onto the overhead conveyor, the tank stops at an external station where sensors perform a dimensional check to select the most appropriate shot blasting recipe; this includes specific movements for each lance, which depend on the tank’s diameter and
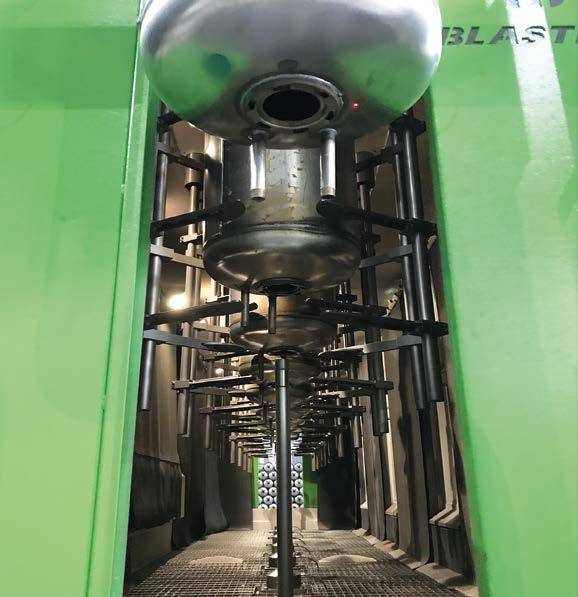
© ITF
Chamber view of shotblasting machine with eight stations.
THE INDUSTRY JUST GOT QUICKER
TankFast linings are formulated to allow your tanks to return back to service quicker than ever before, with excellent chemical resistance capabilities. It’s about time your tanks were earning to their full potential. It’s about time you opted for TankFast. Find out more at jotun.com/tankfast
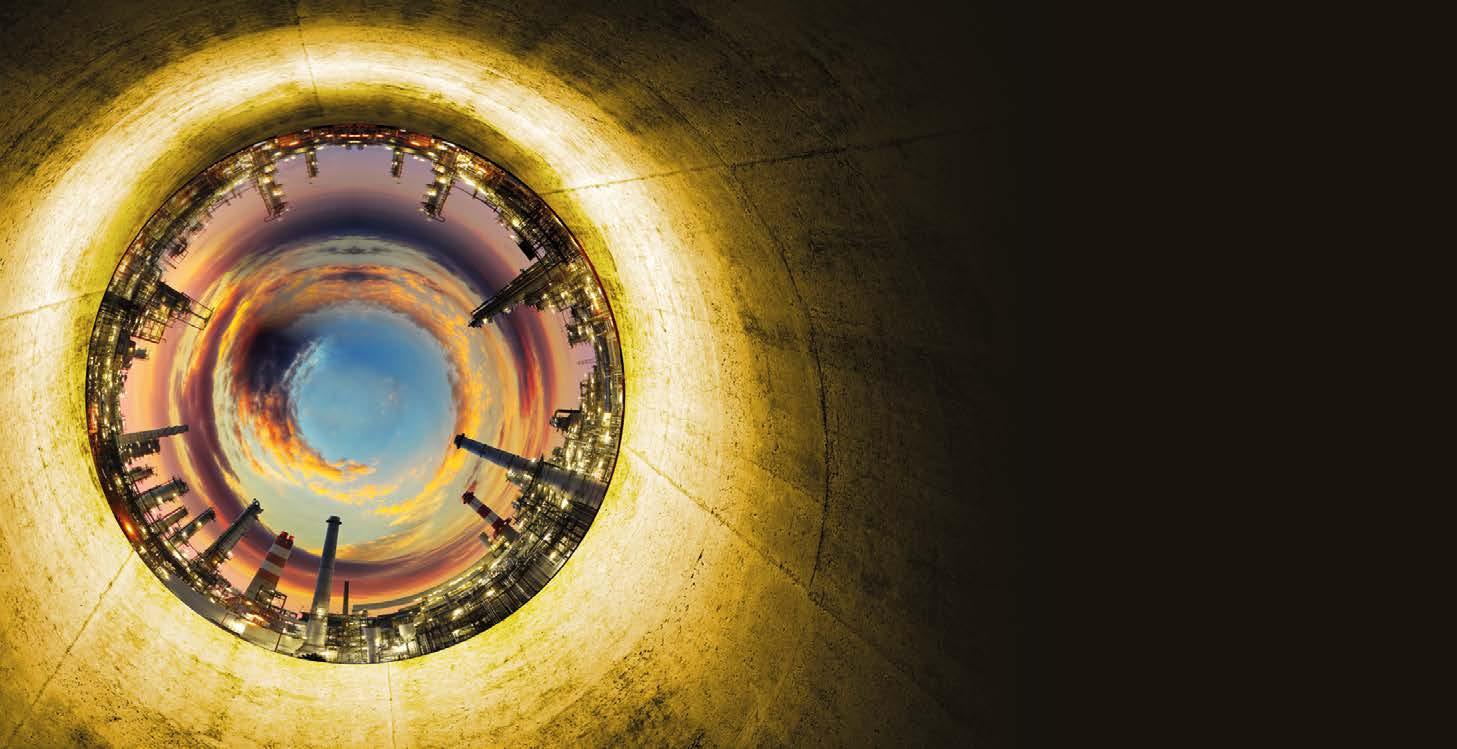
© ITF
Multi-stage powder enamelling machine.

height. This guarantees the use of the right program, thus avoiding any selection errors by the operators. Afterwards, the tank is transferred to the first station of the shot blasting chamber. Each station has a centring system to align the bottom hole of the tank with the shot blasting lance. The lances feature special nozzles at their upper end; each plant actually comes with three different types of blast nozzles that differ in the angle at which the grit is ejected, in order to guarantee total coverage of the tank’s inner surface. Each lance is attached to a motorised shuttle positioned under the shot blasting chamber; the shuttle enables the lance to be moved vertically and it is controlled by a laser system, in order to respect the positions set in each recipe and ensure that the tank is only moved when the lance is out of the way. A rotary joint attached to the shuttle enables the lance to rotate as it moves in and out of the tank. Such combined movement guarantees a homogeneous shot blasting process on every surface area. Each tank is processed in several consecutive stations to prepare its whole surface. After shot blasting, the tank stops in a station similar to the previous ones, where compressed air is used to remove any dust and grit deposited at its bottom. This means that the tanks leave the shot blasting chamber correctly prepared for enamel deposition and free of any impurities that could pollute or hinder the following stages integrated in the line. The subsequent powder enamelling process occurs within a multi-station system conceptually similar to the shot blasting one. The powder deposited in this way is transformed into enamel by moving the tank through a curing oven with an operating temperature of 850 °C. After leaving the oven and cooling down, the tank is unloaded from the conveyor and sent to the assembly line. All HMIs of the machines in the line are interfaced with each other for just-in-time exchange of signals.
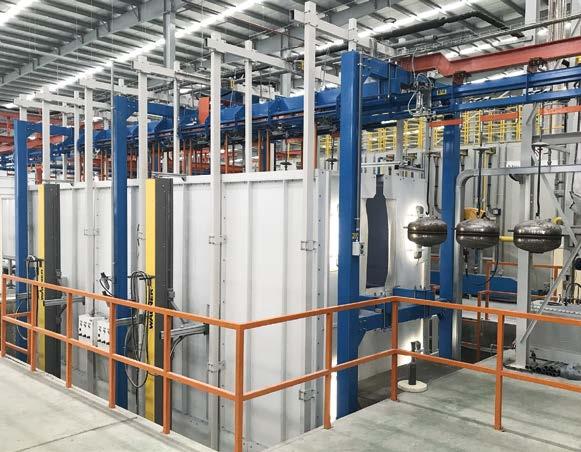
© ITF
Oven for enamel conversion.
Lance rotation: a guarantee of quality
The use of a rotary joint on the shuttle that moves the shot blasting lance is a special feature of ITF’s shot blasters for domestic boilers. This technical choice was dictated by the will to avoid the rotation of boilers because these are never perfectly balanced due to the presence of side connectors, which complicates the alignment between the tank hole and the lance; moreover, the connectors may interfere with the blast chamber’s centring devices during rotation. The use of rotary joints also simplifies the design of the conveyor’s hooks, thus reducing the investment cost and guaranteeing a much more stable system. All these advantages translate into a stable, accurate process not only in the shot blasting machine but also along the entire enamelling line. Finally, ITF’s system is designed according to a modular concept. The number of stations is determined by the productivity required by each user, while the distance between one station and the other and the height of the chamber are defined by the maximum size of the tanks treated. ‹