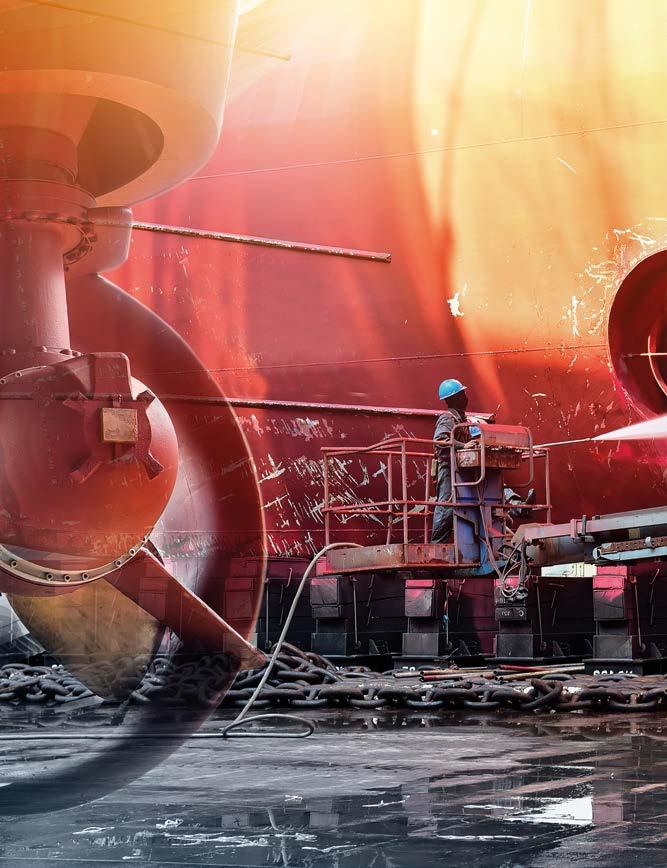
5 minute read
INSPECTION LOGBOOK
Massimo Cornago
NACE International Certified Coating Inspector, NACE CIP PEER Reviewer
cornago@ipcm.it
As mentioned in our previous article1, we will now examine the most common surface preparation systems. We will begin with the “water cleaning” method. This is often used in the preparation of both metal and cement surfaces, using quality-controlled industrial water that can be heated and used with the addition of a detergent, which optimises the cleaning action, or with abrasives, which can be injected into the water flow – in this case, the correct term is “water blasting”. Depending on the pressure used, water cleaning processes can be further defined as “power washing” or “water jetting” and classified according to SSPC-SP12/NACE 5 as follows: • low-pressure water cleaning, under 34 Mpa (5000 psi) • high-pressure water cleaning, in the range 34-70 Mpa (5000-10000 psi) • high-pressure water jetting, in the range 70-170 Mpa (10000-25000 psi) • ultrahigh-pressure water jetting, above 170 Mpa (25000 psi).
Advantages and disadvantages of the two techniques
Although the water cleaning operation requires the addition of a corrosion inhibitor to prevent flash rusting, it has the advantage over conventional abrasive blasting of removing soluble salts as well. Environmentally acceptable sodium and potassium nitrite inhibitors are generally added. Low-pressure water cleaning is effective in removing visible dirt and mould on coated metal and it is generally safe for any adjacent wood, concrete, and masonry (although it is always necessary to carry out a specific check first). High-pressure water jetting is generally able to remove loose rust and the majority of intact coatings: the very highpressure jet can remove coatings and even rust. Water blasting cannot be used to remove scale and roughen metal surfaces. Steel cleaned with water will not be roughened, without any abrasive injection.
1 M. Cornago, Coating Inspections - Inspection of Steel Surface Preparation, Part 1, in ipcm® Protective Coatings no. 36 (December 2020), pp. 40-41.
© Adobe Stock
Equipment inspection
The equipment used for water cleaning is quite complex. Its main components are as follows: • A power source to operate the pump • A pump to pressurise water • A hose and fittings to delivery water to the nozzle • A high-pressure nozzle • A control valve system to enable to the operator to start and stop the water flow.
If the job specification requires the water cleaning equipment to be inspected, the manufacturer should be consulted for specific instructions. In each of the major components, some of the items that may require inspection are as follows: • Power source and pump. It should be sufficient to maintain the required pressure during all the work phases. Only clean water should be used. Filters should be in place and working properly in order to avoid clogging the system. • Hose and fittings. They should be of the right size and pressure rating and free of excessive wear. The fittings should be compatible with the hose and tested as a unit.
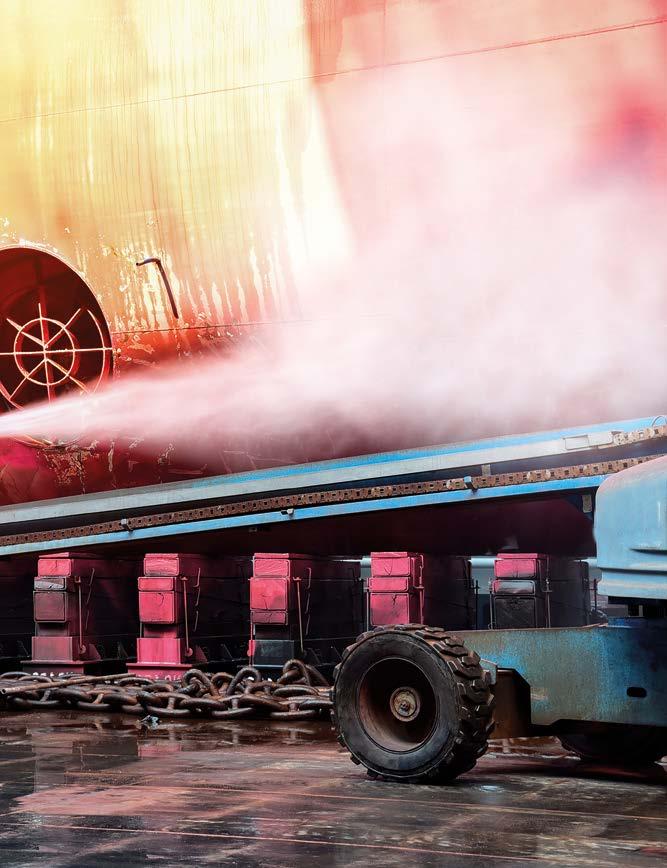
• Nozzle and control valves. They should be in working order. The nozzle should be of the appropriate type for the job. Special nozzles are sometimes required for inside pipes or floor gratings.
Testing for surface cleanliness
The inspector should verify that the specified level of surface cleanliness has been attained. Both SSPC and NACE, now AMPP (Association for Materials Protection and Performance), have developed a written standard that addresses the degree of cleanliness, type of equipment, operating procedures, and safety factors associated with water jetting. The actual SSPC-SP 12/NACE 5 standard contains visual (WJ-1,2,3,4) and nonvisual (SC-1,2,3) definitions of various degrees of surface cleanliness, as follows.
Visual surface preparation definitions for the water jetting of steel (SSPC-SP 12/NACE 5)
1. WATER JETTING WJ-1: the surface should be free of all previously existing visible rust, coatings, mill scale, and foreign matter and have a matte metal finish. 2. WATER JETTING WJ-2: the surface should be cleaned to a matte finish with at least 95% of the surface area free of all previous visible residues and the remaining 5% containing only randomly dispersed stains of rust, coatings, and foreign matter. 3. WATER JETTING WJ-3: the surface should be cleaned to a matte finish with at least two-thirds of the surface area free of all visible residues (except mill scale) and the remaining one-third containing only randomly dispersed stains of previously existing rust, coatings, and foreign matter. 4. WATER JETTING WJ-4: the surface should have all rust, loose mill scale, and loose coatings uniformly removed.
Nonvisual surface preparation definitions (SSPC-SP 12/NACE 5)
1. SC-1: an SC1 surface should be free of detectable levels of contaminants as determined using available field test equipment with sensitivity approximating laboratory test equipment. For purposes of this standard, contaminants are water-soluble chlorides, iron salts, and sulphates. 2. SC-2: an SC2 surface should have less than 7 µg/cm2 chloride contaminants, less than 10 µg/cm2 of soluble ferrous ion levels, and less than 17 µg/cm2 of sulphate contaminants as verify by field or laboratory analysis using reliable, reproducible test equipment. 3. SC-3: an SC3 surface should have less than 50 µg/cm2 chloride and sulphate contaminants as verify by field or laboratory analysis using reliable, reproducible test equipment.
Inspection of solvent cleaning (SSPC-SP 1)
Solvent cleaning is a method for removing all visible oils, greases, soil, drawing and cutting compounds, and other soluble contaminants from steel surfaces. The methods of solvent cleaning included in the SSPC-SP 1 are: • Wiping or scrubbing the surface with rags or brushes wetted with solvent, then using clean solvent and rags or brushes for the final wiping. • Spraying the surface with solvent, using clean solvent for the final spraying. • Vapour degreasing using stabilised chlorinated hydrocarbon solvents. • Immersing completely in a tank or tanks of solvent. For the last immersion, using solvent that does not contain detrimental amounts of contaminant. • Using emulsion or alkaline cleaners. After treatment, the surface is washed with fresh water to remove detrimental residues. • Steam cleaning, using detergents or cleaners, followed by steam or fresh water wash to remove detrimental residues. It is intended that solvent cleaning be used prior to the application of paint and in conjunction with surface preparation methods specified for the removal of rust, mill scale, or paint, such as hand tool and power tool cleaning and abrasive blast cleaning.
In the next article, we will discuss other systems of surface preparation and the related inspections to be carried out. ‹