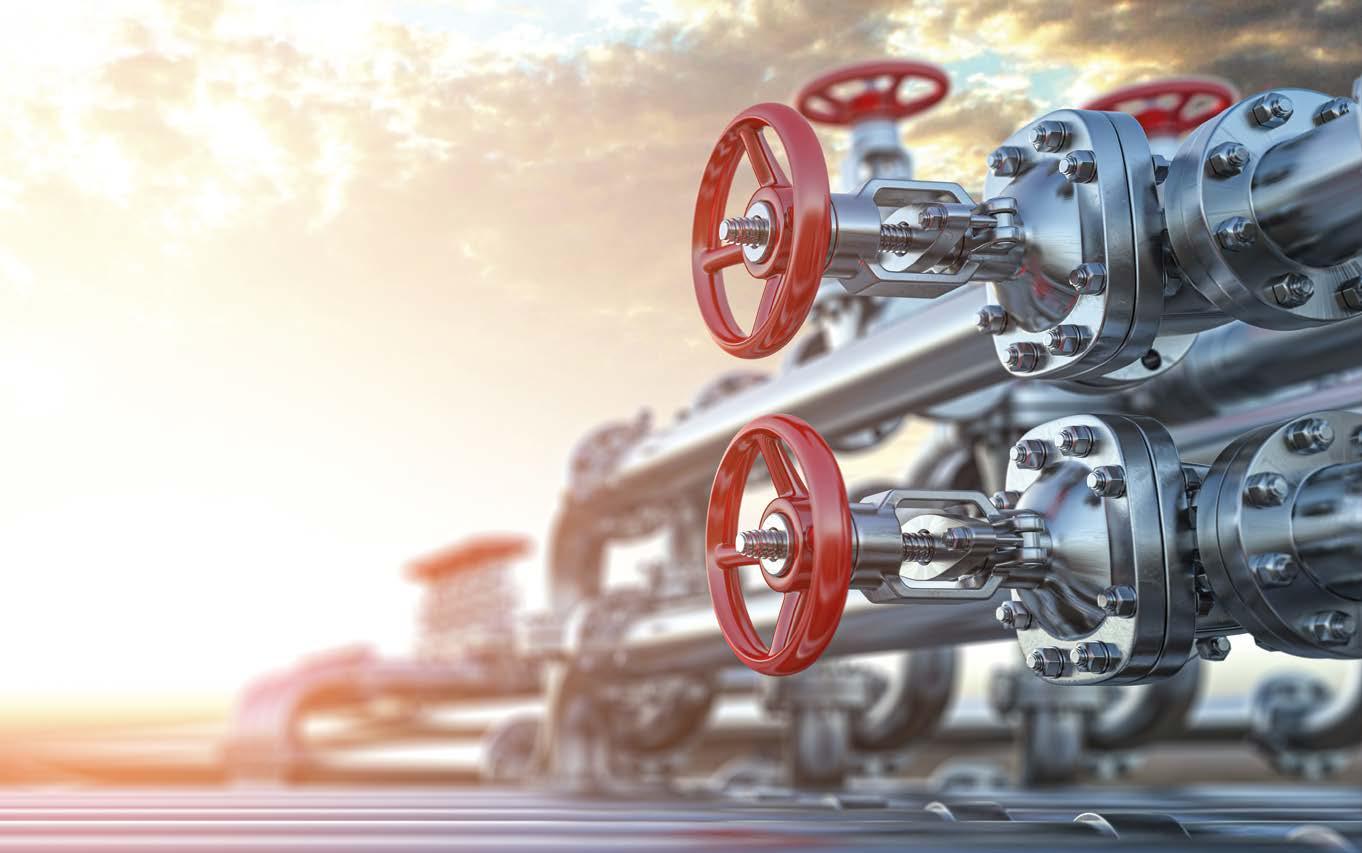
15 minute read
FOCUS ON TECHNOLOGY
A High-Performance Waterborne Coating System to Protect Steel Valves for an Egyptian Oil Storage Facility
Marco Trentini
Ti.Pi.Ci. S.a.s. Technology in Protective Coatings – Arenzano, Italy commerciale@tipici.net
The PetrolValves Group has chosen a coating system consisting of waterborne paints produced by the Italian company Ti.Pi.Ci. Technology in Protective Coatings for the anti-corrosion treatment of 140 valves for an Egyptian oil storage facility.
In this article, we would like to highlight the strategic initiatives undertaken by the PetrolValves Group, a leading provider of flow control solutions for the energy industry, specialising in the engineering of valves, actuators, and control systems. For some time now, the PetrolValves Group has been placing particular emphasis and interest in investing in the continuous improvement of its business through the adoption of innovative technologies and environmentally friendly protection systems that protect the health of people and the environment and meet the highest safety standards. A very effective choice in the field of anti-corrosion treatments for the flow control sector are waterborne, high-build, long-lasting, and overcoatable coatings that, in addition to the corrosion protection of steel substrates exposed to marine environments, are characterised by non-flammability, which is crucial for the operational aspects of
Table 1: System 1 required in the specifications.
SURFACE PREPARATION Sandblasting to grade Sa 2.5 ROUGHNESS PROFILE 50 – 75 µ PRIMER Zinc-rich epoxy coating
DFT
INTERMEDIATE COAT
75 µ High-build residue, epoxy coating with micaceous iron oxide
DFT
TOP COAT
DFT
TOTAL DFT
200 µ Polyurethane coating 50 µ 325 µ
paintshops. Waterborne coatings developed specifically for use in the protective sector are now well established in both new construction and maintenance projects. Ti.Pi.Ci.’s technology for this specific purpose has been perfected over the last few decades and it has already achieved considerable successes, among which the experience of the PetrolValves Group stands out.
The specifications of the international order
This international order concerned the supply of 140 carbon steel valves intended for an oil storage facility in Egypt. The specifications for the selection of the protective system was drawn up by a well-known Egyptian engineering company and the protective system required was System 1 (Table 1).
Table 2: System 1 composed by selecting qualified products.
SURFACE PREPARATION Sandblasting to grade Sa 2.5
ROUGHNESS PROFILE 50 – 75 µ
PRIMER
HYDROGUARD Zinc 78
DFT
INTERMEDIATE COAT
DFT
TOP COAT
DFT
TOTAL DFT
75 µ
HYDROGUARD HB MIO
200 µ
HYDROTHANE
50 µ
325 µ
The 140 valves produced by the PetrolValves Group were intended for exposure in a C5 environment, as defined in the standard ISO 129442:2017. Consequently, the protective system was designed by selecting high-performance waterborne products that belong to coating systems qualified according to the strictest international standards, such as ISO 12944:2017 and NORSOK M-501 Rev. 6 (Table 2). Surface preparation and coating were carried out by System Car Srl (Carpaneto Piacentino, Piacenza, Italy), a company established in 1987 that extends over an area of about 100,000 m2 (of which about 50,000 m2 are covered) and currently employs more than 200 people. The work was carried out on two types of parts: the primary component, composed of the valve and the bracket, whose function is to connect the valve to the secondary component, that is, the actuator. The

Valves awaiting surface treatment.

© Ti.Pi.Ci.
The detail of an assembled bracket.
© Ti.Pi.Ci.
function of the actuator (supplied already coated with an unknown protective system) is to “actuate” the valve, thus enabling the flow of fluid in the storage system to advance or stop.
Surface preparation
The surface preparation started by visually examining each valve, checking for any surface defects such as sharp edges, non-optimal bending radius, and so on. Then, the surfaces were cleaned to remove any oils and greases remaining after the testing and assembly operations carried out in the production departments of the PetrolValves plant in Gerbido (Piacenza). This crucial preliminary phase was then concluded by checking for the presence of soluble salts using the Bresle test. The subsequent sandblasting operations were performed using garnet abrasive, thus obtaining a medium (grit) roughness profile. The coating phase was then started.
Coating of the 140 valves
First layer
As mentioned, these valves were intended for a structure exposed in a C5 environment, as defined in the standard ISO 12944-2017. It is therefore understandable that the Egyptian company owning the plant asked for a zinc-rich epoxy primer to be applied. The product chosen by Ti.Pi.Ci. to meet this need was HYDROGUARD Zinc 78. This is a fast-drying, two-components, waterborne, zinc-rich epoxy primer with 78 (±2)% zinc on dry film in accordance with the SSPC Paint 20 Level II regulation, supplied with ASTM D520 Type III zinc dust. It was chosen among all zinc-rich epoxy products offered by Ti.Pi.Ci. because it can be used as a primer in a variety of systems qualified according to ISO 12944:2017 for exposure in C5 environments, as well as in NORSOK M-501 qualified systems and for structures immersed in salt water (System 7B).
Second layer
The second layer required by the specifications was a high-build epoxy intermediate coat formulated with micaceous iron oxide (MIO). Since a thickness of 200 microns in a single layer was required, the choice fell on a product from the HB (High Build) range. This unique waterborne product line is currently one of the highest technological expressions of the know-how of Ti.Pi.Ci. HYDROGUARD HB MIO is a waterborne epoxy primer-intermediate coat with a dry residue by volume of 74%, which can be applied in a single layer up to 250 dry

© Ti.Pi.Ci.

Components treated with the waterborne, zinc-rich epoxy primer HYDROGUARD Zinc 78.
© Ti.Pi.Ci.
The detail of some brackets following the application of the first layer.
microns. Another distinguishing feature is its high percentage of MIO on dry film, around 30%.
Third layer
The third and final layer required by the specifications was a polyurethane topcoat in the RAL 7035 (Light Grey) colour. In this case, the HYDROTHANE finish was selected, a waterborne polyurethane coating with a glossy appearance. The range of finishes formulated by Ti.Pi.Ci. is very wide-ranging and it offers to customers and international engineering companies many different solutions, in terms of both gloss (and therefore aesthetics) and chemical and physical characteristics (as in the case of fluorinated finishes). HYDROTHANE represented the beginning of the entire range and it was selected for this project not only to enhance the final aesthetics of the valves, but also and above all for its excellent chemical, physical, and mechanical characteristics. This topcoat is in fact used in numerous systems qualified according to the ISO 12944:2017 standard for exposures in CX environments, as well as in NORSOK M-501 qualified systems, both in the System 1 and for structures immersed in salt water (System 7B).
A new environmental vision for the oil industry
For over twenty-five years, Ti.Pi.Ci. (Technology in Protective Coatings) has been striving to open the way to possible applications of sustainable protective systems in the Oil&Gas and Offshore industry, where it is still mistakenly believed that the only way to protect structures is the use of solvent-based products – with the consequent worsening of environmental pollution, which, unfortunately, has been going on for too long. The PetrolValves Group has long since decided to join this philosophy, as have other major multinational groups using Ti.Pi.Ci.’s technology not only in Italy but also abroad, including in the USA, the Middle East, and Northern and Eastern Europe. The PetrolValves Group’s choice to market itself as a promoter of green solutions, actively pursued by its technical, production, and quality departments, proves that a vision focused on protecting people and the environment can be readily accepted by international engineering firms. At the same time, such environmental choice made by contracting entities enables applicators (better technically prepared than others and ready to comply with the increasingly binding European regulations) to achieve a higher safety degree in their plants, significantly reduce their emissions (which is no mean feat), and save money. ‹

© Ti.Pi.Ci.

Some valves painted with the waterborne protective system developed by Ti.Pi.Ci.
© Ti.Pi.Ci.
The detail of a finished valve.
INNOVATIONS: PRESENT&FUTURE
Assured Corrosion Protection for Wind Energy Units
Laura Saure
Dörken Coatings GmbH & Co. KG – Herdecke, Germany
coatings@doerken.de
High-performance corrosion protection for screwed fasteners in high-tensile steel enables wind energy units to be largely maintenance free. Zinc flake systems have proven their reliability in the area of rotor blade fastenings for over 30 years.
The rotor blades are fundamental, key components of a wind energy unit. They are used to extract energy from flows of air and move this to the generator. The blade lengths of up to 85 metres and a weight of up to 25 tonnes mean that the fastening of the rotor blades to the rotor hub is particularly significant. This is achieved using fasteners, consisting of so-called double ends, barrel-nuts and hexagonal nuts, typically in the M30 to M36 dimension range.
Diverse stresses and requirements
The rotor blades and thereby also their screwed fasteners are subjected to extreme climatic as well as dynamic stress from wind load and the operation of the unit itself. This is joined by static forces from prestressing of the bolts and the mass of the connected elements. As a consequence of the high level of stress for the screwed fasteners, the choice of corrosion protection is especially important. The protective coating needs to meet specified coefficients of friction in order to guarantee problem-free fastening on the construction site, typically with considerable time pressure and under difficult conditions. In addition, the coating must offer highly-effective and long-lasting corrosion protection to ensure the long-term, reliable operation of the unit.
Corrosion protection with multiple benefits
The best solution is therefore a coating system like the extremely thin zinc flake coatings from Dörken. They fulfil all of these requirements and consist of a basecoat and an organic or inorganic topcoat tailored to the respective components. The zinc-containing basecoat determines the corrosion properties and is responsible for the cathodic corrosion protection. In addition to adding further protection, the tailored topcoat enables the observance of defined coefficients of friction and therefore safe and fast assembly.
© Dörken
Rotor blade fastener comprising double end, barrel nuts, hexagonal nuts and washers.

The racked dip-spin process has proved itself in the coating of the components.
A further advantage of the zinc flake systems: coated screws and bolts do not display setting behaviour, meaning that cost-intensive maintenance work is reduced and service life increased. Even the risk of application-related, hydrogen-induced stress corrosion cracking can be avoided, due to the fact that no hydrogen is involved in the coating process. In addition, the low cross-linking temperature of around 200°C avoids changes in the properties of the high-tensile components. The highly-effective and long-lasting corrosion protection offered by zinc flake systems is displayed in comprehensive outdoor weathering tests conducted at the Deutsches Institut für Bautechnik (DIBt) and the Federal Institute for Materials Research and Testing (BAM).
Efficient coating with the racked dip-spin procedure
The size of the rotor blade fasteners in particular means that the proven racked dipspin procedure is advisable for coating the components. This application technology enables even, high-performing protective coatings to be achieved. Following extensive pre-treatment, at the beginning

© Dörken of this process the bolts or barrel nuts are fixed to a rack or multiple small supporting points, or alternatively placed individually in a basket with grille. After this, the unit is dipped in the coating medium in the scope of a precisely-defined process. This ensures that the smallest hollow spaces are reliably coated. After the rack has been removed from the bath, the centrifuge is utilised. The intensity and duration of this spinning process depends on the geometry and desired coat thickness of the parts. All excess material in the area of the interior spaces is effectively spun off. In the last step the entire unit including the rack is subjected to the drying and cross-linking process. In this the coated parts are hardened and cross-linked in a special oven with a defined temperature and duration. This results in an even and adhesive coating that enables problemfree and secure fastening to the rotor blades of the wind energy unit in subsequent use. In conclusion, high-performance coating solutions help to extend maintenance intervals and working life of wind energy units, whilst also increasing levels of efficiency. ‹

INNOVATIONS: PRESENT&FUTURE
Reducing VOC Emission by Using Dynasylan SIVO 140 and SILIKOPON EF
Edited by Evonik Industries AG
Essen, Germany info-tego@evonik.com
Zinc dust paints based on Dynasylan SIVO 140 and ultra-high solid topcoats based on SILIKOPON EF enable the formulator developing low VOC coating systems. The VOC emission can be reduced from 120 g/m² to 20 g/m² compared to a common solvent born coating system. This reduction is environmentally friendly and protects steel from corrosion.
More than any other sector, the corrosion protection market illustrates the impact the use of perfectly tailored binder and pigment systems can have on the function of the coating as a whole and furthermore on the protection/durability of valuable objects. The combination of two especially eco-friendly binder systems is presented.
Primer based on a waterborne silane
The waterborne silane system was developed for use in two-pack zinc dust paints, which are the coating of choice for long-term corrosion protection. The binder contains special organofunctional groups which can interact with the filler and stabilize the formulation. Formulations based on the waterborne silane binder can be used to formulate nearly VOC-free zinc dust paints (Table 1).
Silicone hybrid resin for corrosion protection applications
Conventional coating systems for heavy corrosion protection are based on a three-layer system, specified in ISO 12944 (C5, high). The abilities of the intermediate epoxy layer and the PU top coat can be combined by a one-layer formulation of the silicone hybrid resin cured with an amino alkoxy silane1 (Fig. 1).
1 B. Bröskamp, F. Böss, S. Herrwerth, Ch. Cova-Hög, Ressource Efficient Corrosion Protection, ECJ 03/2015. This technology provides coating systems with significantly less than 250 g/L VOC (sometimes even less than 100 g/L) and moreover permits isocyanate-free crosslinking.
Reduction of three to two coating layers
In order to reduce from three to two coating layers, a combination of low-VOC zinc dust primer based on waterborne silane binder and top coats based on a silicone hybrid resin can be used. This two-layer system showed in Figure 1 spares costs and time, in particular: • material cost • labour cost • production time. By reducing the film thickness, less coating materials are needed and labour costs are reduced significantly2. Moreover, the working time is considerably reduced due to less coating layers and less curing time.
Eco-friendliness (VOC-regulations)
Zinc dust paints that are formulated with this innovative binder and ultra-high solid top coat based on the silicone hybrid resin, enable the formulator to develop low-VOC coatings systems without compromising properties.
2 M. Hallack, Flyer, Perfect Team for Eco-friendly Corrosion Protection Systems, ECS, 03/2019.
© Evonik © Evonik
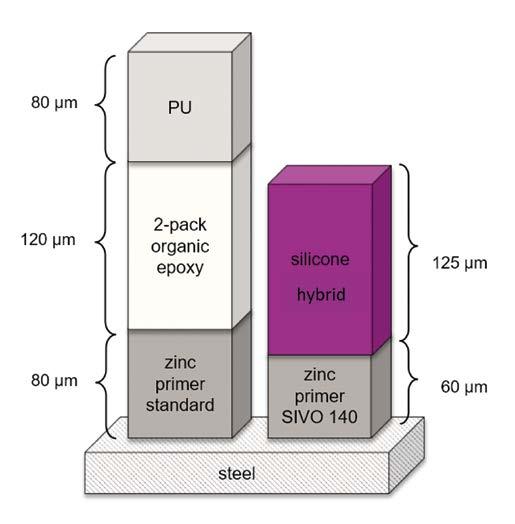
Table 1: Guiding Formulation based on waterborne silane-based binder. Figure 1: Advantages of silicone hybrid resins.

© Evonik © Evonik
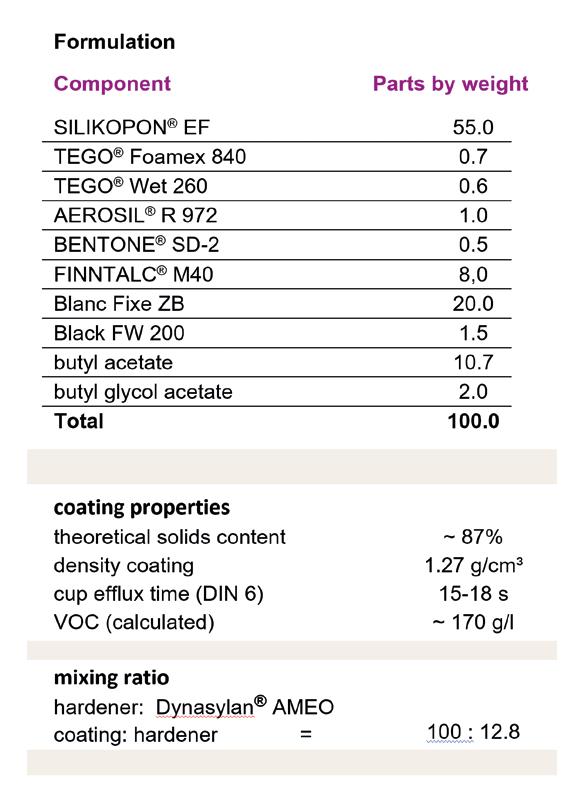

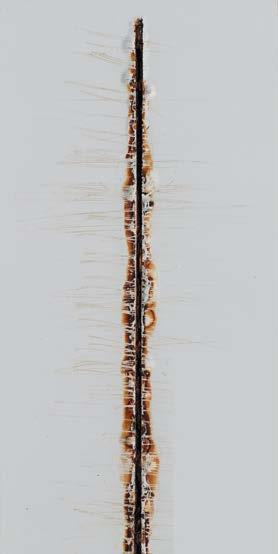
© Evonik The VOC emission can be reduced from 120 g/m² to 20 g/m² compared to a common solvent borne coating system. This reduction not only protects the substrate, it also protects the environment. The eco-friendliness is obvious, because of the reduced coating thickness and hence less material using less solvents (Table 2).
Test results
The corrosion protection performance was investigated with coatings on blasted steel, according to DIN EN ISO 12944-6 (C5 high, test program 1). A standard three-layer coating, a commercial 2-pack zinc dust epoxy-primer, a 2-pack epoxy-intermediate layer, and a 2-pack polyurethane top coat (in total: 280 µm dry film thickness, Fig. 2a) were compared to the two-layer combination of the waterborne silane-primer with the 2-pack silicone hybrid top coat (in total: 185 µm dry film thickness, Fig. 2b). In the humidity chamber test, carried out according to ISO 6270-1, no difference could be detected. Both coating systems showed no blistering after 720 hours exposure. However, the adhesion on the two-layer system was better (GT 0-1 versus GT 2). Another advantage, which is achieved with top coats based on silicone hybrids, is the higher chemical resistance. The coating was exposed at room temperature to 10% solutions of sodium hydroxide and of sulfuric acid; no damage was evident on the paint surface. Surfaces based on silicone hybrids also show a good performance in terms of easy-to-cleanproperties and good abrasion resistance.
Summary
The high crosslinking of coatings based on a silicone hybrid resin qualifies this binder-technology for highly durable coatings - extraordinary gloss, colour retention and weather resistance. Compared with a conventional three-layer system, this two-layer system has better corrosion protection, even though the dry film thickness is 95 µm less. In combination with the waterborne zinc dust primer, based on silane, we achieved an eco-friendly coatings system, which offers a brilliant solution for the reduction of solvents and material and thus the reduction of costs and additionally provides a long-lasting protection against the formation of micro-channels. ‹
Table 2: Guiding Formulation based on the silicone hybrid resin.
Figures 2a and 2b: The results after 1440 hours of neutral salt spray test, according to ISO 9227: 2a (left) - Three-layer coating system: 2-pack zinc dust epoxy-primer, DFT: 80 µm + 2-pack epoxy-intermediate layer, DFT: 120 µm + 2-pack polyurethane top coat, DFT: 80 µm. 2b (right) - Two-layer coating system: Zinc dust primer based on waterborne silane, DFT: 60 µm + 2-pack silicone hybrid top coat, DFT: 125 µm.