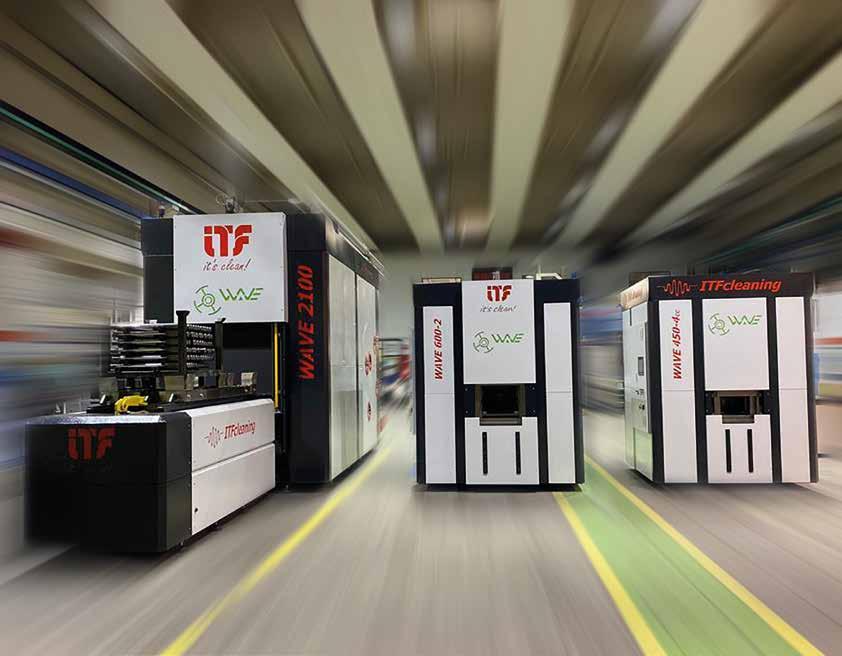

Nel mercato odierno, qualsiasi componente, particolare o pezzo prodotto, sia esso in fase di lavorazione interoperazionale ma soprattutto in fase di lavorazione finale, prima di essere immesso sul mercato, debba essere lavato.
Il risultato atteso dal mercato è nessuna o poca contaminazione residuale sul pezzo stesso. Il mercato richiede pezzi conformi, il che significa parti perfettamente pulite.
È un “MUST”: i contaminanti presenti sui pezzi devono essere rimossi.
Utilizzando una metodologia corretta, si avrà:
Alta potenzialità dei risultati ottenuti
Affidabilità ed efficienza del processo
Impatto ambientale ridotto
Conformità alla sicurezza dei lavoratori
Il mercato sta imponendo ad implementare con continui miglioramenti le operazioni del processo di pulizia.
Al giorno d’oggi ci sono sempre maggiori richieste di qualità e conformità alle norme (es ISO 16232) che va di pari passo con un’elevata affidabilità del processo operativo.
Un processo di pulizia migliore si riflette in una parte perfettamente pulita, questa non è una richiesta remota del mercato, ma è un dato di fatto.
Non è una questione se il prodotto è pulito o no, ma quanto è pulito!
Tutti i nostri impianti sono da sempre in grado di soddisfare le esigenze più selettive e le richieste più stringenti di lavaggio.
Tutti i nostri impianti rispondono alle normative di riferimento vigenti nazionali e internazionali, a protezione degli operatori e per la tutela dell’ambiente, una responsabilità che dipende da tutti noi.
Il mercato richiede specifiche di pulizia sempre più stringenti per qualsiasi componente in produzione.
Le esigenze di pulizia attuali non consentono alcun residuo di contaminante sul prodotto finale.
In fase di produzione finale non è in genere consentito neppure del residuo d’acqua.
Il solvente pulisce meglio, più velocemente, in modo più efficiente, in parti di forma complessa rispetto a qualsiasi processo a base d’acqua questo era vero nei tempi passati e oggi è vero più che mai!
La nostra produzione include impianti ad alcool modificati, ad acqua, misti alcool acqua e impianti con solventi clorurati e idrocarburi. Abbiamo così la possibilità di consigliare la soluzione corretta e dunque l’impianto adatto per le reali esigenze e soddisfare la richiesta produttiva del cliente e non di spingere una sola tipologia di impianto, sia esso ad acqua o a solvente. Disponiamo di un’ampia gamma di impianti di lavaggio industriali (e non lavasecco), consigliando ogni singolo cliente non solo il ciclo di lavaggio più appropriato, ma il processo corretto per il miglior risultato atteso. Ogni cliente ha una tipologia di componente da decontaminare che necessità di una soluzione ad-hoc, ed è per questo che associamo al tipo di inquinante da rimuovere il corretto processo, sia esso ad alcool, ad acqua o a solvente.
I nostri impianti di lavaggio a solvente a circuito chiuso sono in grado di eseguire il trattamento di lavaggio e asciugatura completamente sotto vuoto.
Utilizziamo solventi di derivazione alcolica (alcoli modificati o meglio alcossipropanoli), i quali consentono un forte potere sgrassante, superiore agli idrocarburi.
Possiedono una bassa tossicità ed ecotossicità, evaporano completamente senza lasciare residui sui pezzi, non sono corrosivi e sono in grado di asportare l’acqua dalle superfici metalliche.
Gli impianti di lavaggio a solventi clorurati hanno un funzionamento a circuito completamente chiuso e sono in grado di eseguire il trattamento di lavaggio e asciugatura completamente sotto vuoto. La lavorazione avviene con percloroetilene super-stabilizzato che possiede un alto potere solvente ed una grande stabilità. Il percloroetilene è compatibile con la maggior parte dei metalli, in particolare con quelli che si ossidano facilmente quali l’alluminio, l’acciaio inox, il magnesio, lo zinco e le leghe come l’ottone, ecc.
I nostri sistemi di lavaggio a solvente a circuito chiuso sono in grado di effettuare il trattamento di lavaggio e asciugatura completamente sotto vuoto. Utilizziamo solventi idrocarburici (isoparaffine) classe AIII, che hanno il minor impatto ambientale.
Un importante esempio di impiego nell’assemblaggio dei cuscinetti, è la pulizia in fase finale dei cuscinetti, l’applicazione di questo tipo di solvente è poi obbligatoria, vista la necessaria leggera untuosità residua lasciata dal solvente stesso sulle parti.
Rimozione totale di ogni tipo di inquinante dai pezzi trattati (metallici e non metallici) semplici o morfologicamente di complessi, dotate di fori ciechi e filettati, maschiati o rullati, planari o con recessi o cavità, fino alla microstruttura dei componenti in materiale sinterizzato. Vengono rimossi contaminanti e impurità organiche e inorganiche, polari e non polari come olio (intero ed emulsioni), oli di lappatura, paste di lucidatura, cere, trucioli, polveri e particolati, grassi, impronte, terre e sabbie di fonderia, sali, ecc.
A seconda della tipologia del solvente utilizzato e del ciclo proposto i nostri impianti possono pulire ottimamente: AVP, AVZ, Acciaio, Acciaio inossidabile, Ghisa, Alluminio, Ottone, Rame, Ergal, Materiali plastici.
I cestelli una volta introdotti nella camera di trattamento, in modalità manuale tramite l’operatore cliente o in modalità automatica tramite un dispositivo posizionato frontalmente la camera di lavoro, possono essere movimentati o essere statici in base alla tipologia di programma inserito anche in considerazione della conformazione o della delicatezza dei pezzi stessi.
Il cesto o nel caso di impianti a cesti multipli, i cesti possono essere posti:
in rotazione sull’asse cestello
in basculamento controllato
resi statici
Chiusura del cestello per evitare che i pezzi escano in fase di rotazione. Nel caso che in cui l’operatore non voglia essere aggravato dall’operazione di apporre il coperchio sul cesto, l’impianto è dotabile della chiusura automatica del cesto in camera di lavoro
Doppie pompe per creare
regime di vuoto richiesto
totale del solvente ad ogni ciclo
Asciugatura e deodorazione dei trucioli in estrazione
ermetico di lavaggio/carica/scarico solvente
Distillazione continua del solvente, anche durante l’operazione di pulizia in atto
Siemens per la gestione di tutti i parametri
funzionamento
pannello operatore Siemens HMI con indicazione continua dello stato del sistema;
Connessione remota per assistenza remota
La costruzione in acciaio inox AISI 304 (DIN AISI 1.403) di alto spessore (a differenza delle macchine derivate dalle macchine di lavanderia) permette di raggiungere alti regimi di vuoto per evitare di stressare il liquido lavante e consente di asciugare i pezzi molto rapidamente.
Tutto il ciclo dell’impianto, fase a spruzzo, immersione con o senza ultrasuoni, fase vapori e asciugatura, avviene sottovuoto garantendo la tenuta ermetica dell’impianto.
Ogni fase di lavaggio viene eseguita con liquido pulito grazie alla dotazione di doppio distillatore che garantisce solvente sempre pronto e pulito anche per tempi ciclo ridotti. Questo si tramuta in un processo continuo di lavaggio con prodotto salubre e, quindi, una elevata e costante qualità di lavaggio L’asciugatura in vuoto e un ambiente ermeticamente sigillato evitano la contaminazine dei pezzi dai corpuscoli presenti nell’aria.
In nessuna fase di conduzione impianto e di manutenzione impianto l’operatore entra in contatto con il liquido. Le operazioni del carico e scarico del solvente e di drenaggio avvengono in automatico, mentre la pulizia dei filtri avviene con la deodorazione preventiva.
WAVE 450 - 1 1 300 x 450 x 200
La nostra modalità costruttiva è differente dagli altri impiantisti presenti sul mercato in quanto la costruzione della nostra camera di lavoro è integrata nel corpo impianto.
Ciò comporta considerevoli vantaggi:
➣ nessun serbatoio esterno
nessuna tubazione esterna
tutte le connessioni sono realizzate internamente
nessuna dissipazione di calore
garanzia della tenuta del sottovuoto nel tempo
Tramite la costruzione a modulo integrato, i vapori di solvente generati dal distillatore sono utilizzati per dotare la camera di energia termica, creando una distillazione continua mai interrotta. Si riduce così l’energia termica da utilizzare per ripristinare il regime di distillazione, riducendo sensibilmente i consumi elettrici e ottenendo sempre una maggior quantità di vapori per la fase finale del processo e per la loro condensazione. Lo spostamento e la ricollocazione nello stabilimento del cliente dopo i test di pre-collaudo nel nostro stabilimento, garantiscono che quanto riscontrato in pre-collaudo sia effettivamente quanto atteso e richiesto in fase di collaudo finale e messa in produzione.
x 17,7 x 7,9
x 450 x 200
11,8 x 17,7 x 7,9
WAVE 450 - 2 2 300 x 450 x 200 h 11,8 x 17,7 x 7,9 h 450 x 600 x 200 h 17,7 x 23,6 x 7,9 h
WAVE 450 - 3 3 300 x 450 x 200 h 11,8 x 17,7 x 7,9 h 450 x 900 x 200 h 17,7 x 35,43 x 7,9 h
6 - 8
5 - 7
WAVE 450 - 4 4 300 x 450 x 200 h 11,8 x 17,7 x 7,9 h 450 x 1200 x 200 h 17,7 x 47,25 x 7,9 h 300 660 4 - 6
WAVE 600 - 1 1 470 x 620 x 400 h 18,5 x 24,4 x 15,75 h 470 x 620 x 400 h 18,5 x 24,4 x 15,75 h 250 550 4 - 6
WAVE 600 - 2 2 470 x 620 x 400 h 18,5 x 24,4 x 15,75 h 470 x 1240 x 400 h 18,5 x 48,8 x 15,75 h 400 900 3 - 4
WAVE 900 - 1 1 600 x 900 x 600 h 23,6 x 35,43 x 23,6 h 600 x 900 x 600 h 23,6 x 35,43 x 23,6 h 600 1300 3 - 4
WAVE 1000 - 1 1 600 x 1000 x 750 h 23,6 x 39,37 x 29,5 h 600 x 1000 x 750 h 23,6 x 39,37 x 29,5 h 700 1500 3
WAVE 1200 - 1 1 800 x 1200 x 800 h 31,5 x 47,25 x 31,5 h 800 x 1200 x 800 h 31,5 x 47,25 x 31,54 h 1000 2200 2 - 3 WAVE 2100 - 1 1 850 x 2100 x 850 h 33,46 x 82,68 x 33,46 h 850 x 2100 x 850 h 33,46 x 82,68 x 33,46 h 2000 4400 2
Idatitecnicielecaratteristichesonosuscettibilidimodifichesenzapreavviso.