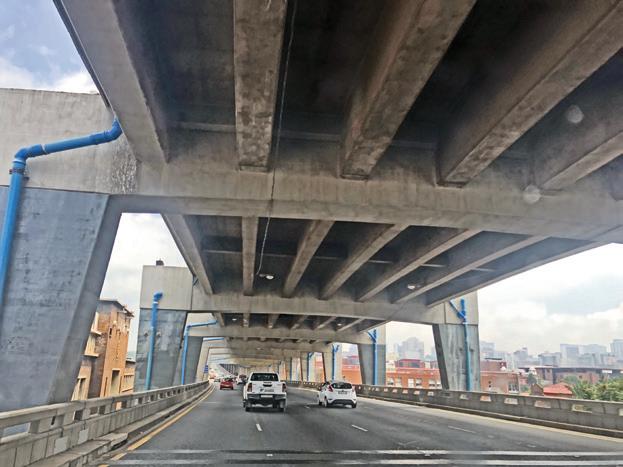
4 minute read
JOHANNESBURG TWIN-DECK HIGHWAY BRIDGE REPAIR
HIGHWAY BRIDGE REPAIR JOHANNESBURG TWIN-DECK
Several Sika products were specified for structural repairs, strengthening and the coating of a 1,02km section of Johannesburg’s M1 twin-deck highway bridge between Newtown and Fordsburg. The bridge consists of two reinforced concrete deck super-structures mounted on concrete columns, one directly above the other. The R15 million rehabilitation project required the expertise of many specialists, including main contractor Khato Civils, which was assisted by 17 small, medium and micro-enterprises.
A major challenge for all involved was the requirement for the motorway to remain open to traffic. Therefore, it was anticipated that it would be difficult to complete the task within the allotted 22-month time-frame. However, thanks to the use of Sika’s tailor-made products and the appointment of a committed contractor, the project was completed three months ahead of time. SikaTop Armatec-110 EpoCem was used as a protective coating for exposed rebar and Sika Monotop-615 HB and SikaGrout-212 were applied for the repair of lateral and vertical bridge elements. SikaWrap-300 C was used for strengthening reinforced concrete structures and for increased sheer load capacity.
T he bridge’s concr ete sur f aces were treated with the Sikaguard-705 L Silane water repellent and SikaTop Seal107. The latter is a polymer modified waterproof cement coating which is chloride- and carbonation-resistant.
The council had stated that the main concern was the safety of motorists and ensuring that all product applications were executed correctly at every stage, so all those involved in the project were provided with training and on-site support by the Sika team. This included training such as surface preparation, product mixing and product application.
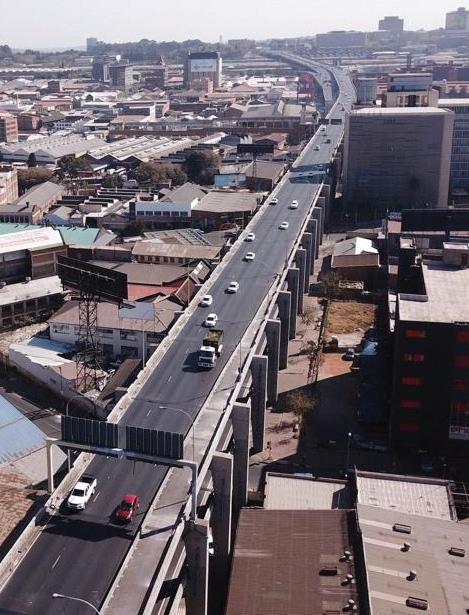

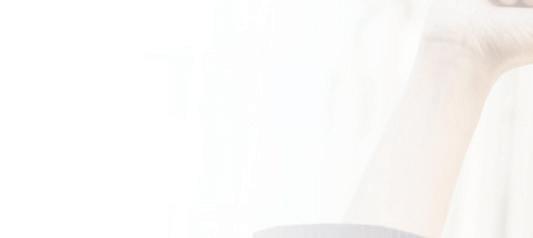
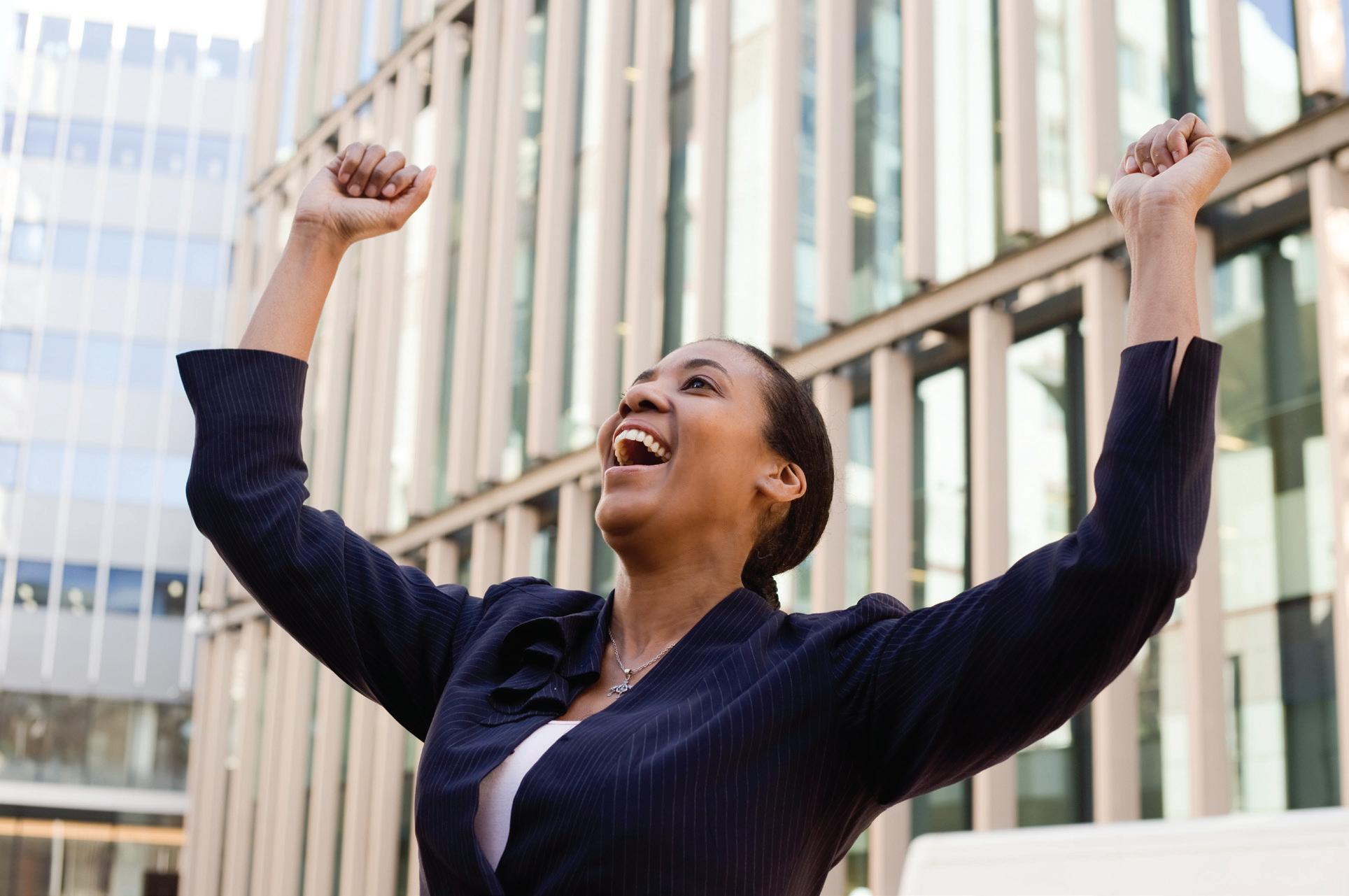
We are there when you celebrate
Need to excel in concrete? Our School of Concrete Technology offers internationally recognised courses for anyone interested in concrete. Master concrete with us.
Concrete block producers tend to fall into two broad groups: those who base their marketing on price and compromise on quality, and those who are first and foremost qualityfocused. One company which falls emphatically into the latter grouping is Cape-based BluBlok.
BluBlok sells concrete blocks and bricks of consistently superior quality to builders’ supply merchants and property developers. Situated on large premises in Somerset West, it operates with fully automated plants in the Western Cape. The kerb plant turns out kerbing of exceptional quality using wet casting manufacturing and indoor curing chambers. This division is spearheaded by Kevin Coetzee, who is well known in the industry.
“We follow a simple, but ef fective business philosophy,” says BluBlok general manager Frans Benadé. “It’s based on what we term our ‘golden triangle’ of quality, price and delivery. We use it in tandem with a secondary triangle of morale, cost control and safety. Morale plays an important role. We strive to ensure that people enjoy working here and get job satisfaction. We also aim to keep costs to a minimum by getting things right the first time.
Quality-driven “Quality underpins the whole organisation and is based on our own quality systems. Besides using the best possible raw materials, it involves continuous checking and testing by our in-house quality controller. In addition, our scales are calibrated regularly to ensure we get our material mixes consistently right and besides daily in-house testing, our blocks and kerbs are also tested externally by professional quality auditors,” says Benadé.
“Our kerb moulds are made in-house, while our in-house workshop also ensures that our two plants are kept up to spec. And because our kerb plant is automated, it ensures the minimal handling of our moulds, which extends their lifespan.
“All our kerbs have excellent strength properties, uniform finishes and exceptionally smooth faces. They come in the standard length of 1m and are available in the following types: edging for pavements; barrier kerbs and channels for stormwater drainage; a combination and mountable kerb for the townships; and a channel on-side kerb.”
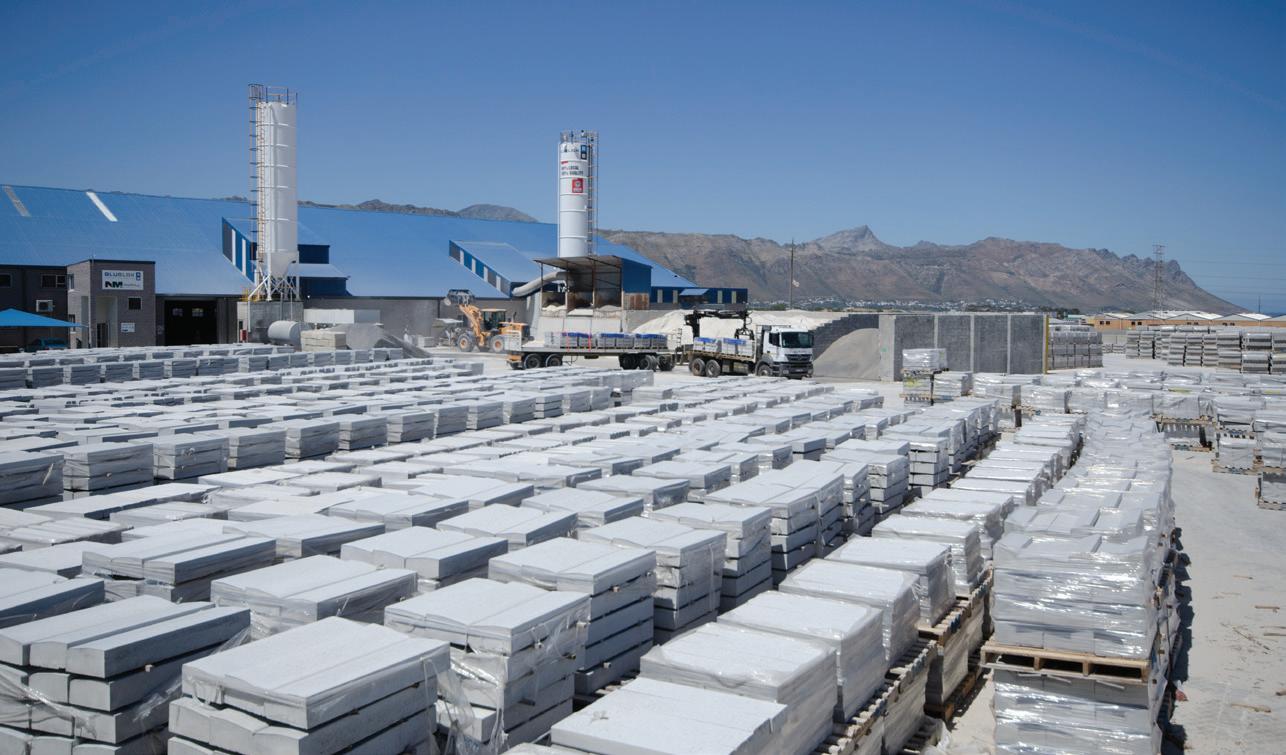
the standard range of masonry products, such as all sizes of bricks and blocks, as well as retaining wall blocks and decking blocks. As of 2019, we’ve been making a 140mm U block which builders are using as an alternative to lintels,” says Benadé. “Quality and fair pricing count for nothing if you can’t deliver and our customers know that when they place an order with us, the products will be delivered promptly.
“Housing projects in which our bricks and blocks have been used include Satari, Croyden Olive Estate and Somerset Lakes in Somerset West, as well as projects in Bredasdorp and Hawston.”
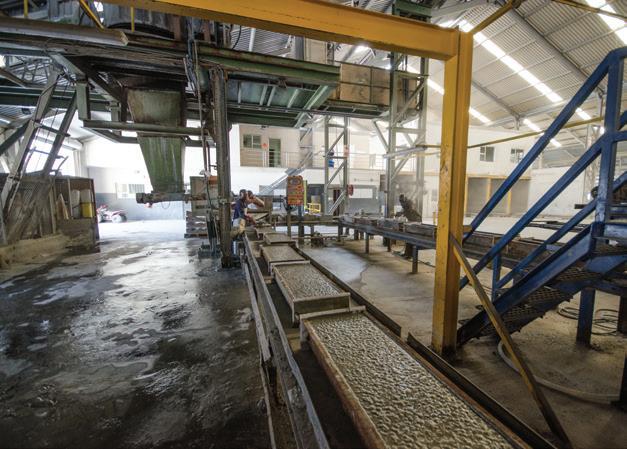
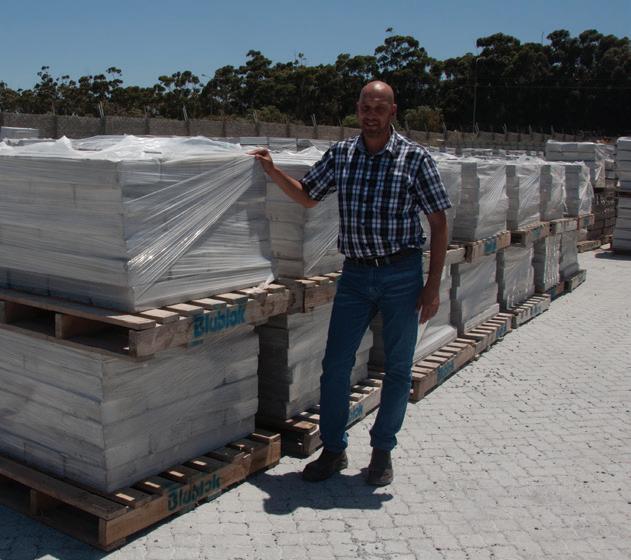
Recent projects Recent kerbing projects supplied by BluBlok include roads in Moorreesberg, Ceres, Lutzville and Montague Gardens. In addition, the company has supplied Burger & Wallace Construction, Cornfield Construction, Shar Civils, Martin & East and Asla Contruction with kerbs for various road projects.
“Our block range is made to SANS 1215:2008 standards and comprises
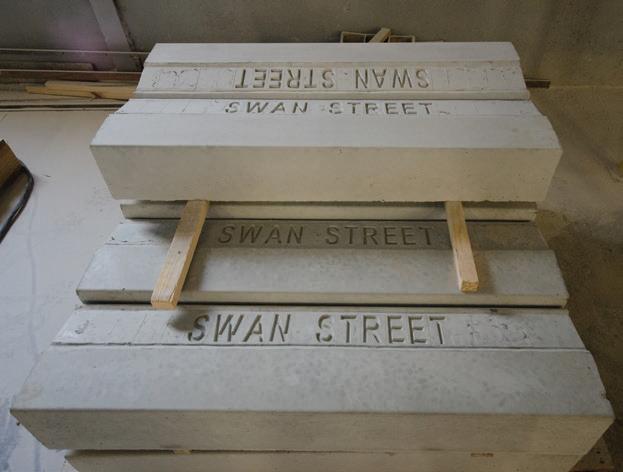
(Top): BluBlok’s storage yard and precast concrete factory.
(Above, from top): BluBlok’s fully automated kerb plant and specially embossed BluBlok kerbs prior to delivery.