
5 minute read
SA ARCHITECTURE SHAPES UP WITH DECORATIVE TILT-UP CONCRETE
Function, rather than form, has always been the predominant selection factor in precast concrete applications. But no longer, as increasing numbers of local architects are requesting decorative elements in their precast designs.
According to David Kitching, general manager of SA’s leading tilt-up practitioner, Bedrock Group, architects are calling for varied finishes such as textured and woven concrete, the embossing of company names and logos, and eye-catching lines and shapes in their tilt-up designs, as well as relief or depth. “Our aim is to enable local architects and property developers to achieve what their contemporaries are doing overseas. Increasingly, we find ourselves moving away from our typical fast-track tilt-up projects to much more aesthetic-driven projects and to this end, we’ve been involved in several decorative concrete projects in Durban, Johannesburg and Cape Town,” says Kitching. casting required on a site that was ecologically sensitive,” says De Jongh.
What follows are potted profiles of some of Bedrock’s decorative tilt-up projects:
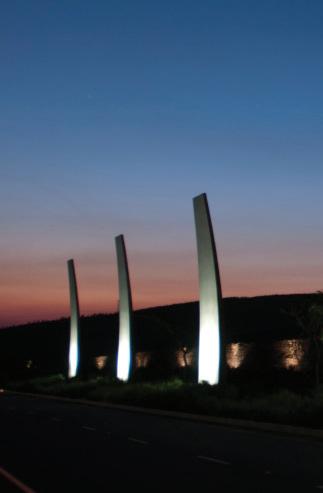
Rubro Construction, Durban Attractively embossed with the company name and logo using high-density foam rubber moulds, these panels were used for constructing a retaining wall that was 2,5m high. They were erected in the same way as tilt-up columns, which involved placing them on blindings and then casting a reinforced foundational base around them.
Distribution centre Ian Bell, a director o f Paton Taylor Architects in Durban, says his company uses decorative concrete in tilt-up applications on a regular basis. “We used it on the Mr Price distribution centre in Hammarsdale, KwaZulu-Natal, with bespoke patterns which came out nicely. However, we mainly use it on a repetitive basis, embossing the same motif on several panels.
“The CAD-generated designs are handed to Bedrock for transferring into precast concrete using either high-density foam rubber cut on CNC machines or steel moulds,” says Bell.
Anton de Jongh of Arc Architects says decorative tilt-up concrete is relatively new to SA and besides its aesthetic attributes, one of its major benefits is faster construction. “We saved two months of a 14-month construction period on our concrete laboratory project at the University of Pretoria and Bedrock achieved Class 1 off-shutter finishes. We were impressed with the smoothness and flatness achieved.
“Moreover, we were able to specify indents on some of the panels, which gave us additional design freedom. Another plus was the very small footprint the King Shaka Airport – Durban, Henry Fagan Architects Resembling elephant tusks, 10 arched concrete obelisks – each weighing 28 tonnes – were cast and placed on either side of the entrance road to the airport in 2010 and 2014. Designed by Henry Fagan of Fagan Architects, the casting was done using concrete moulds which were considerably cheaper than their steel equivalent and involved a process similar to shaping a surfboard by hand. The architect wanted all the obelisks to be the same colour in a light-coloured concrete.
To achieve this materials comprising sand, stone and white cement were set aside so that when the casting was done, each column was made from the same material batch. The sand and stone came from a single day’s quarry output and was washed before delivery. It was then stored in a covered area until the project was completed.
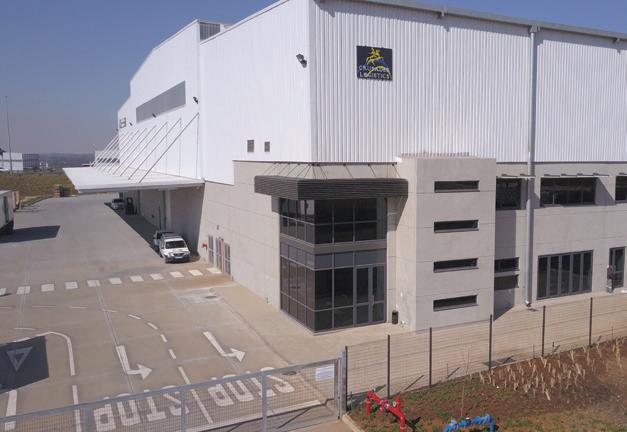
Crusader Logistics, Johannesburg, Empowered Spaces, Sonia Rodrigues Low-cost entry-level features, such as a protruding stairwell constructed with precast concrete panels, lift the appearance of this large warehouse from the ordinary into something special, thereby creating a pleasant workspace. Other precast panelling combines well with the tinted windows framed in glazed aluminium and the IRB sheeting above.
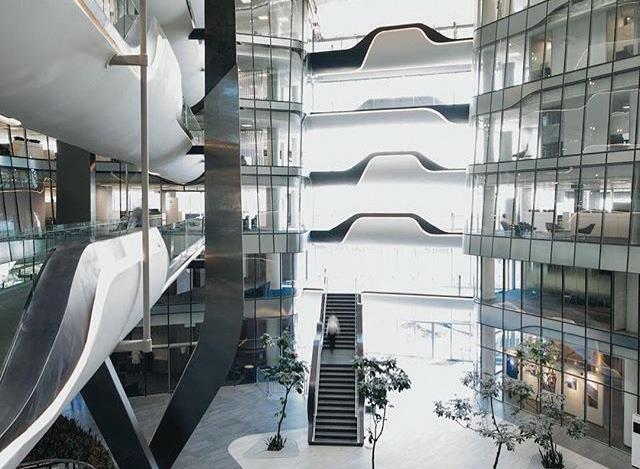
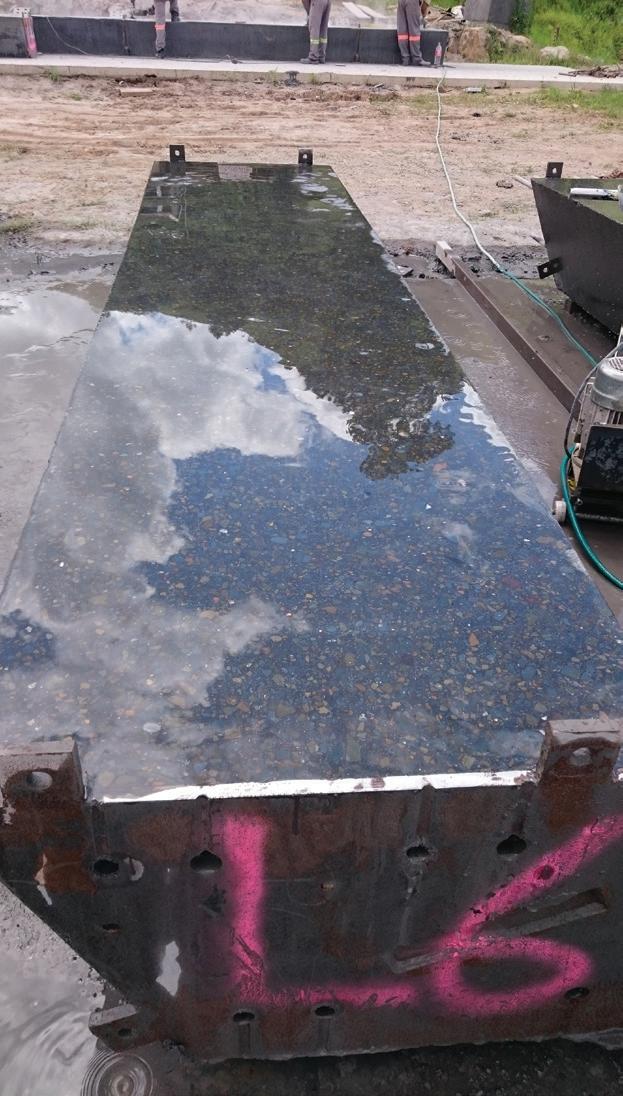
Sasol HQ, Johannesburg, Paragon Architects Sasol’s new headquarter building is an architectural masterpiece. Bedrock supplied 3m polished exposed-aggregate column sections which were used to erect two tapered concrete columns that rise from the second to the ninth floor. The columns were designed to resemble tuning forks and are named as such. Part of Bedrock’s brief was to cast in steel connecting plates at the end of each beam. The plates have a tolerance factor of only 1mm and are connected to the beams with steel brackets.
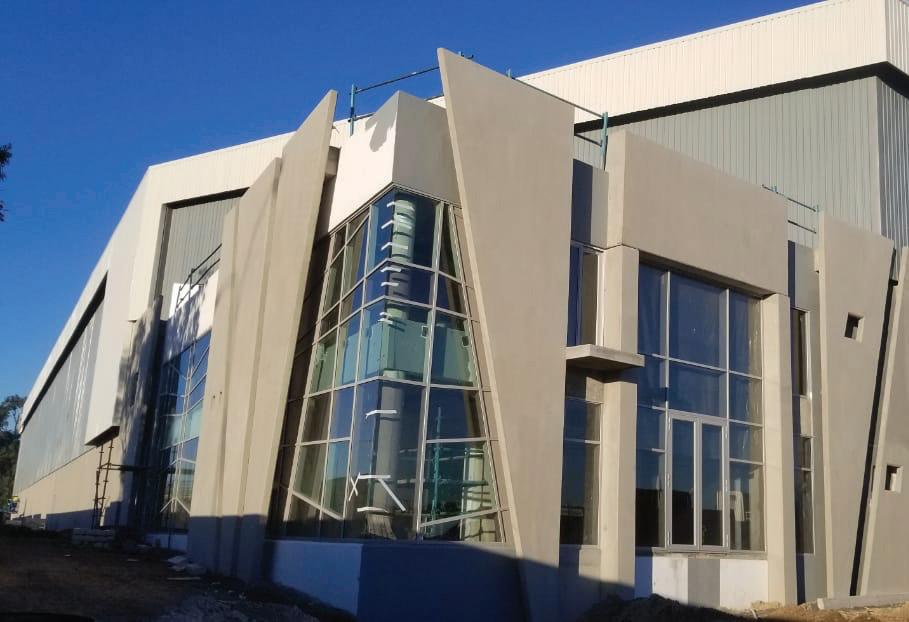
Agrinet, Cape Town, Tim Hughes Architects Cladding wall panels in various shapes and sizes add an interesting visual dimension to this building. The application of cementitious mix stains the concrete to a uniform colour by being absorbed into the pores of the concrete. Unlike paint or cement, the stain will not require any maintenance.
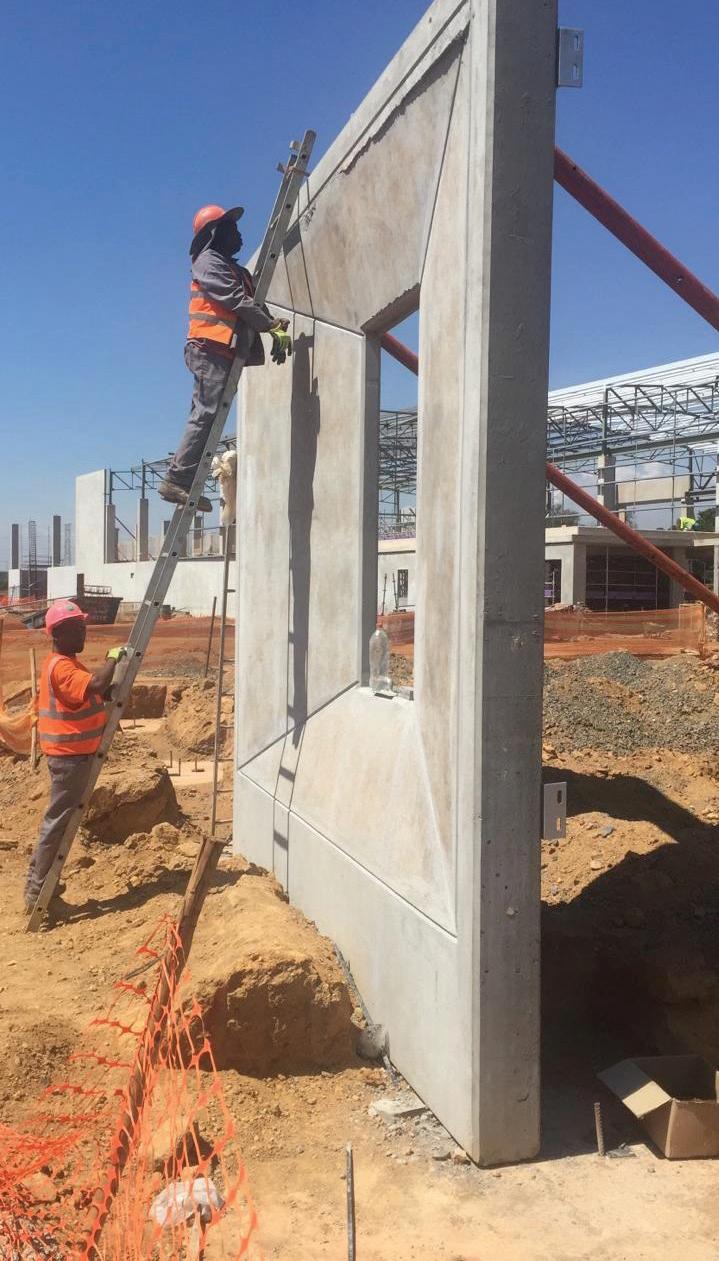

Mr Price, Hammarsdale, Paton Taylor Architects, Ian Bell This image shows how patterns and logos are embossed onto concrete panels. High-density foam rubber is cut with CNC machines based on CAD designs. The rubber is then attached to the casting surface and painted with a bond breaker before the concrete is poured. University of Pretoria Concrete Laboratory, Arc Architects Bedrock was challenged by the University of Pretoria to achieve an exceptionally high class of concrete finishes in the construction of a world-class concrete testing laboratory and educational facility using tilt-up walls. Arc Architects wanted the lab to show of f what is achievable with concrete and Bedrock delivered superb finishes. Moreover, the walls are decorative in that they are shaped with depth and relief and also support the roof and other parts of the building.
SUBSCRIBE TO PRECAST FOR FREE
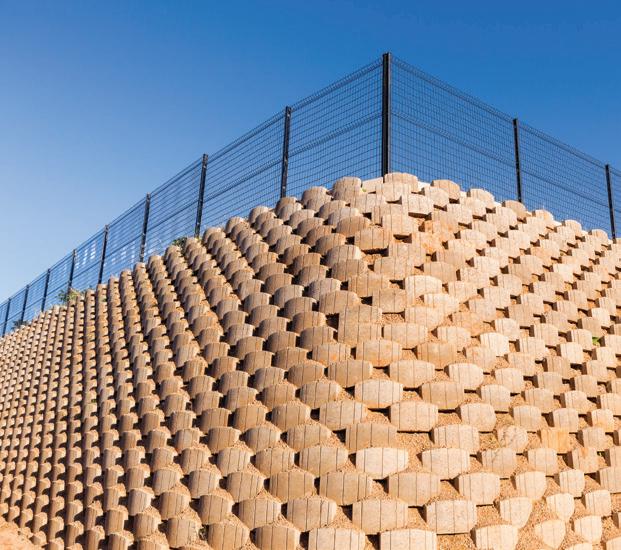

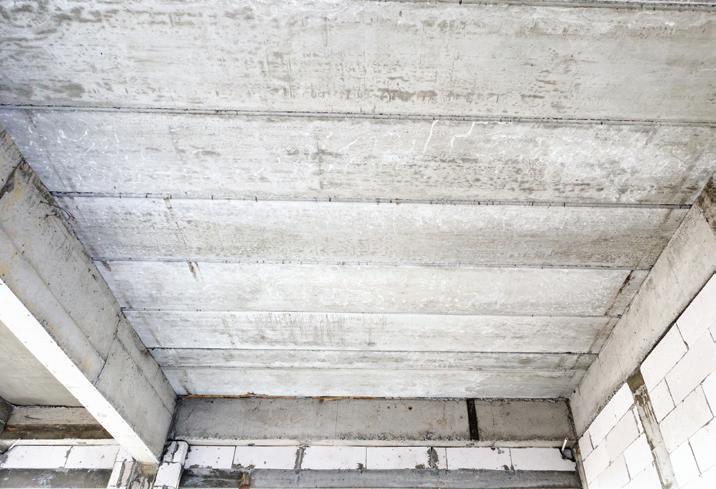
subscription form

C O N C R E T E M A N U F A C T U R E R S A S S O C I A T I O N Q u a l i t y c a s t i n c o n c r e t e
Yes, I want a FREE subscription to Precast magazine
SUBSCRIBER’S DETAILS:
Mr Mrs Ms Other