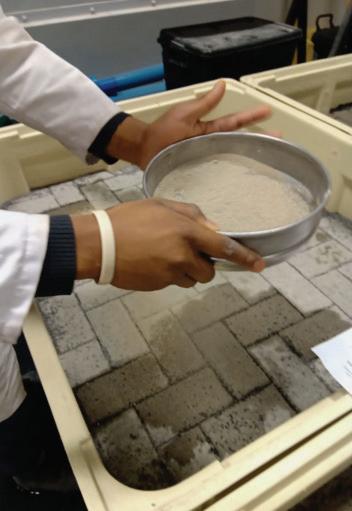
7 minute read
UCT conducts experiment on geotextile clogging in PICP
(Below): Sprinkling fine material with a sieve.
(Below): Paver silhouettes were visible on the base course after the removal of the pavers.
The first in a series of experiments on how the use of geotextiles affects clogging in permeable interlocking concrete paving (PICP) installations was run by the Civil Engineering Department of the University of Cape Town (UCT) during May/June.
Supervised by Prof Neil Armitage and civil engineering Master’s student Motlatsi Monyake, the day-to-day execution of the research work was conducted by fourth-year civil engineering student Josh Blackshaw, with additional input from Monyake.
“The primary goal of this and the research to come is to provide South African PICP users and designers with solid recommendations on PICP design based on empirical evidence, rather than what we think the answers are,” said Armitage.
Worthwhile experiment
“We were feeling our way with this initial experiment and, as could be anticipated, the results were by no means conclusive. Although we didn’t achieve our chief objective, namely to get one or more of the research cells clog completely, the experiment certainly proved worthwhile. If nothing else, it provided a stepping-stone for further research.
“But it did more. For example, it revealed that no matter how good the
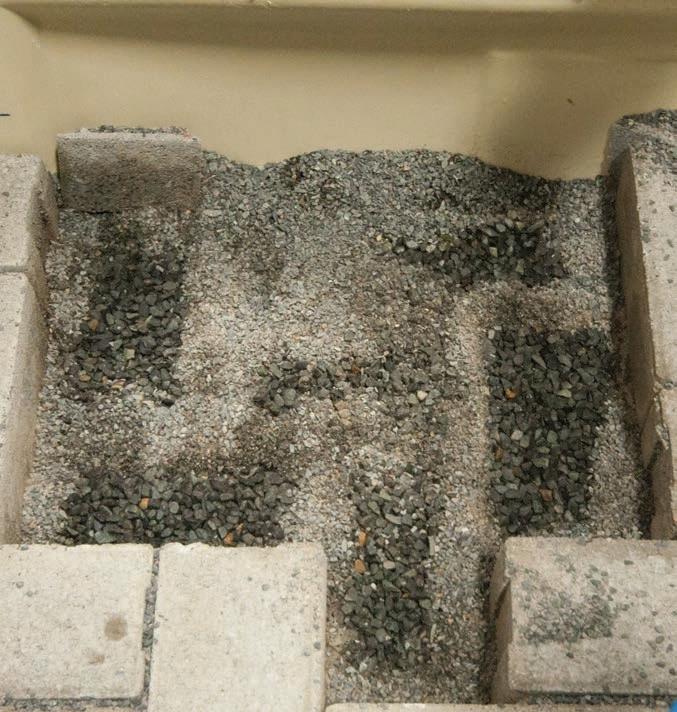
infiltration properties of geotextiles, they do cause some loss of infiltration capacity. Moreover, the choice of geotextile seems to make very little difference to the rate of clogging.”
The laboratory testing involved four cells (A-D) which mimicked live PICP installations. Each cell comprised the following: a 200mm sub-base layer of 1925mm aggregate; a 50mm base course of 9mm aggregate; a 50mm bedding layer of 2-6mm aggregate, and grit stone of 2-3mm for insertion between the pavers. Cell A was devoid of a geotextile layer, while cells B, C and D had different geotextiles installed between the base course and the bedding layer. These were: Fibretex F25 (heatsealed/treated) – cell B; Kaytech Bidim A1 (needle-punched/non-woven geotextile) – cell C, and Kaytech Kaytape S120 (woven geotextile) – cell D.
Careful assessment
“We chose the Fibretex F25 because it’s similar to Inbitex, which forms part of the Aquapave standard PICP package. Everyone in SA knows Bidim, so it was an obvious choice. For cell D, we wanted a geotextile with large openings, which was why we opted for Kaytape.
“All the cells followed the same drop-off curve and there was no discernible difference in behaviour between the geotextile and nongeotextile cell. By the end of the experiment, infiltration rates had declined on the following basis: cell A by 83,6% from 12 861 to 2 106mm/hr; cell B by 94,5% from 11 523 to 637mm/hr; cell C by 84,7% from 10 363 to 1 590mm/hr, and cell D by 91,7% from 10 670 to 889mm/hr.” (See Tables 1 and 2.)
Using a sieve, loadings of fine material (pollutant) recovered from Blue Route Mall and previous PICP laboratory experiments
were sprinkled onto the paved surface at an initial rate of 100g/m² per week. In addition, 500mm/m² of simulated rainwater per week was sprayed onto the surface with a watering can at 100mm/m² per day from Monday to Friday. Notionally based on Cape Town’s annual rainfall, the purpose of the water was to wash the material into the gaps between the pavers and help migrate it to the geotextile. Neither the fine material nor the water was applied over weekends, thereby imitating dry periods in the real world. Some fine material remained on top of the pavers after the first watering, but during the course of the week, it was all infiltrated.
Base test
Before the first fine material and waterloading took place, a base infiltration test was conducted using a single-ring infiltrometer, the standard American test method. It is more accurate than the Modified Swift Test and is therefore better suited to laboratory work. After the base test, infiltration tests were run at the beginning of each week. Some intermediary testing was also done.
“The infiltration rate dropped off week by week and, as predicted, the decline was rapid at first. However, after the second and third weeks, it became obvious that complete blockage wasn’t going to happen in the allocated five-week period. So we added a lot more material during the last two weeks, upping the loading to 200g/m² in the fourth week and to 500g/m² in the fifth,” said Armitage.
Because there was little discernible difference in the decline of infiltration performance between the geotextile and non-geotextile cell, it indicated that most of the blocking was taking place between the pavers. This proved to be the case when the pavers were lifted and the bedding layers removed at the end of the fifth week. Only a very thin layer of loading material had been deposited on all three geotextiles. Infiltration tests were run directly on all of them which demonstrated they were not blocked at all and that the drop-off in performance was minimal.

(Above): A water infiltration test on the exposed geotextile using a single-ring infiltrometer. Table 1. 5-week infiltration tests of PICP cells
Interesting results
When the pavers were removed, it was also apparent that the stone grit and fine material between the pavers had fallen onto the bedding layer. This was because the fine material was granular and had a very low clay content. Moreover, the gaps between the pavers were comparatively narrow – another reason most of the blockage occurred between them. However, once the pavers had been lifted, their silhouettes on the bedding layers were visible in patterns which were identical across all four cells.
“We’re looking at making several changes to our next experiment, with the aim of actually inducing failure in one or more of the cells. We intend reaching a point where we achieve what we witnessed at Steen Villa, a residential complex in Cape Town where the geotextile in the PICP installation was completely blocked.
“We’ll probably start with a material loading of 500g/m² because in the first experiment, we saw that the bedding layers have enormous capacity for absorbing fine material. We could have pumped in a lot more material without affecting the openings between the stone grit and the bedding layer.
Week/ Period Cumulative Load (g/m²) Infiltration Capacity (mm/hr): A Infiltration Capacity (mm/hr): B Infiltration Capacity (mm/hr): C Infiltration Capacity (mm/hr): D
1 Week/ Period
Cumulative Load (g/m²) Infiltration Capacity (mm/hr): A Infiltration Capacity (mm/hr): B Infiltration Capacity (mm/hr): C Infiltration Capacity (mm/hr): D
2 1 3 4 2 5 3 4 5 Table 1. 5-week infiltration tests of PICP cells
0 (Base infiltration) 12861 100 10912 200 0 (Base infiltration) 7502 12861 300 100 500 200 1000 300 7009 10912 2568 7502 2106 7009
500 2568 11523 8574 7871 11523 5649 8574 2705 7871 637 5649 2705 10363 8574 5487 10363 3311 8574 1840 5487 1590 3311 1840
1000 2106 637 1590 10670 9059 6117 10670 4052 9059 2182 6117 889 4052 2182 889
Infiltration capacity reduction (mm/hr) Infiltration capacity reduction (mm/hr)
Infiltration Capacity (mm/hr): A Infiltration Capacity (mm/hr): B
(mm/hr): C
83,6% Infiltration Capacity (mm/hr): A 94,5% Infiltration Capacity (mm/hr): B 84,7% Infiltration Capacity (mm/hr): C
83,6% 94,5% 84,7%
Infiltration Capacity (mm/hr): D
91,7% Infiltration Capacity (mm/hr): D
91,7%
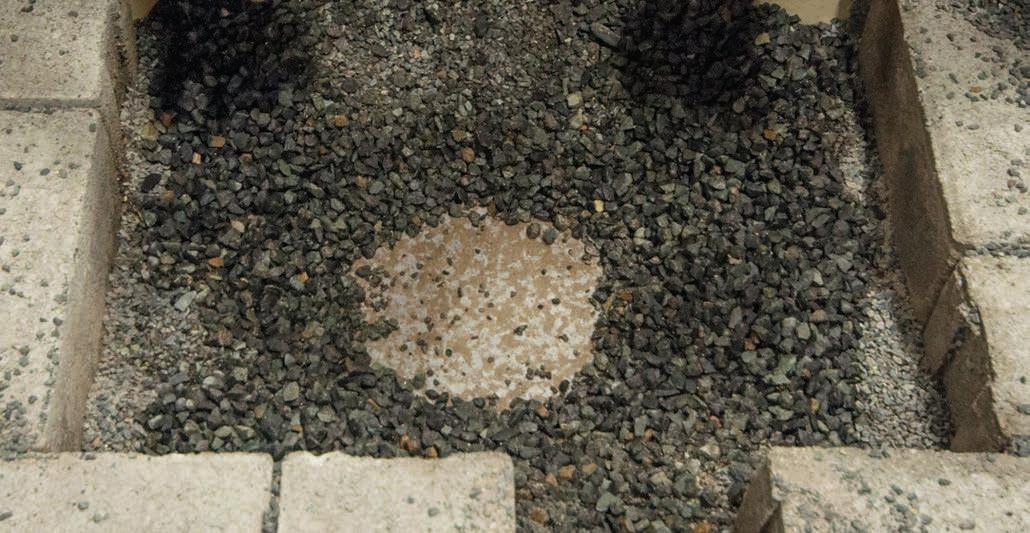
“Increasing the application of water from 500L to 2 000L per week is also being contemplated. In the real world, PICP installations normally handle water from beyond the permeable paved area and it’s quite common to have run-on factors of three-to-one. What’s more, additional water will be needed to mobilise the additional fine material,” said Armitage.
Vehicle damage
“One of the differences between lab testing and what we see on site is the lack of vehicle loading. Real-life paving is subject to vehicle
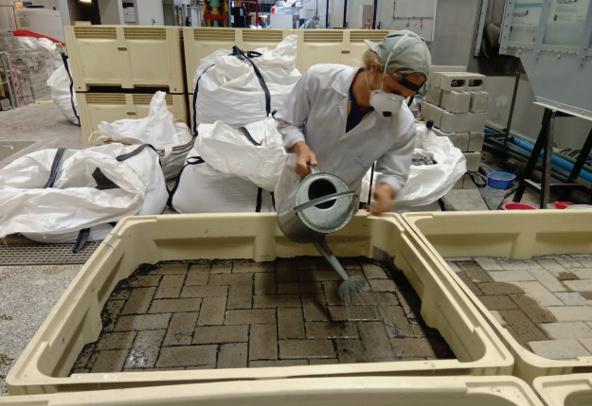
(Above): Simulated rainfall using a watering can. (Above): A partially exposed geotextile membrane showing minimal fine material deposit.
traffic, with its attendant braking and acceleration. This sends shock waves through the sub-base layers and causes the pavers to open and close slightly. These factors mobilise the migration of fine material at a faster rate than simply applying water, so we’re looking at simulating vehicle-loading by applying some sort of vibration, which is yet to be decided.
“We’ve recruited five more fourth-year students who’ll be adopting pieces of this project during the coming year under the guidance of Motlatsi, whose involvement forms part of his Master’s degree. One will carry on with Josh’s work and the others will look at software and different guidelines from around the world. We’ll approach it from different angles and try to come up with something we can defend.
“As is often the case, one learns more by the experiments which don’t work than those that do. Even though our research so far is inconclusive, our understanding of the processes involved is improving all the time,” said Armitage.