
2 minute read
Hollow-core slabs used for chemical storage facility


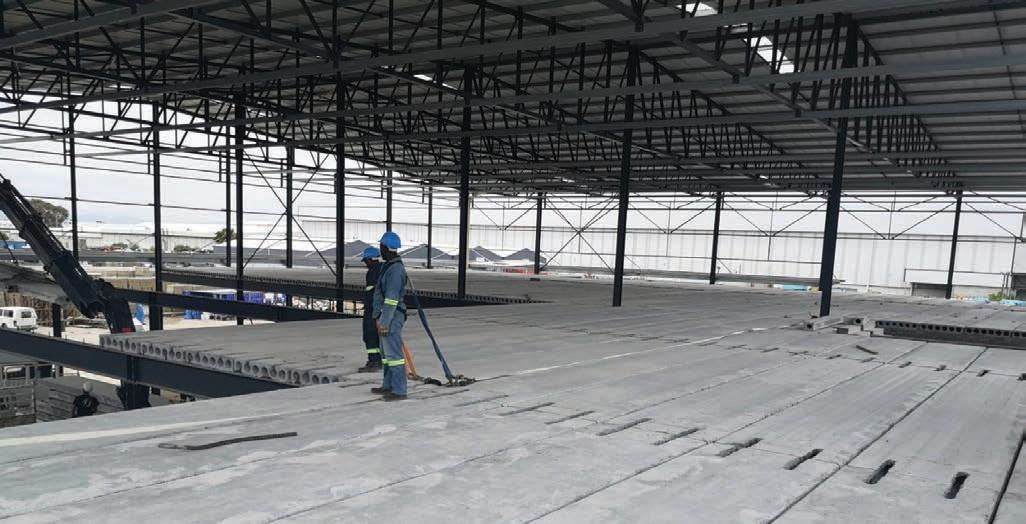
Hollow-core slabs manufactured and supplied by CMA member Portland Hollowcore have been used for the construction of first-floor decking in a new 3 800m² warehouse for Caprichem, a manufacturer and distributor of a wide range of chemical-based products to more than a dozen market sectors.
Completed in January 2021, the property was designed and project-managed by Structural Survey, which also supplied all the steel used for the project, including insitu columns, steel beams, the roof structure and a steel framework for outdoor shelving, the latter being constructed with hollowcore slabs as well.
Just over 8m long and 200mm thick, and covering a fl oor area of 1 900m², the slabs were installed by mobile crane at a rate of 220-240m² per day.
“Normally our installation rate’s a lot faster, but in this instance, the building’s roof – which was integral to the stability of the entire structure – had already been installed, which meant our headroom was limited,” says Petrus Theart, divisional manager of Portland Hollowcore.
The slabs span load-bearing walls and steel beams, the latter being supported by the reinforced concrete columns. Each slab was cast with two 50cm exposed core cavities. Y16 rebar was inserted into the cavities of opposing slabs and sealed with concrete.
“This gave the entire structure additional strength and rigidity,” says Structural Survey owner Hendri Barnard.
A reinforced, power-fl oated concrete screed was thrown once all the slabs had been installed. The outdoor shelving was constructed with Portland’s 5m slabs. In
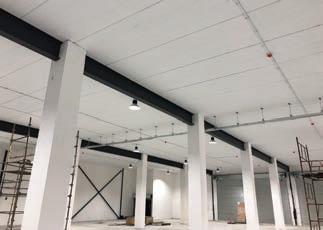
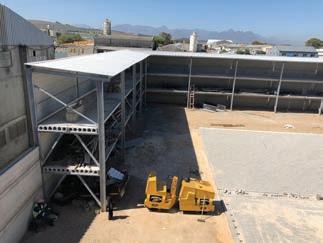
(Above): The partially completed fi rst fl oor showing the open cores prior to fi lling.
(Left): Part of the soffi t side of the hollow-core fi rst fl oor and the hollow-core shelving and walling. addition, 300m² of twin-decked shelving was mounted adjacent to two hollow-core boundary walls, each just over 30m long and 6m high. The walls were erected with 486m² of 5m slabs sandwiched in fi ve layers between steel H-beams, while the shelving panels were mounted on a steel frame attached to the beams.
The wall slabs were cast with a tongueand-groove system so that they could slot into each other without the need for adhesive. However, once a slab was installed, the gaps between the slab and the H-beams at either end were grouted to prevent panel movement.
Barnard believes approximately six weeks were saved by using hollow-core slabs. “Being a warehouse, the fl oor-toceiling height of the ground-fl oor section was over 5m, which would have made the installation of scaff olding for in-situ construction impractical, as well as timeconsuming,” he says.