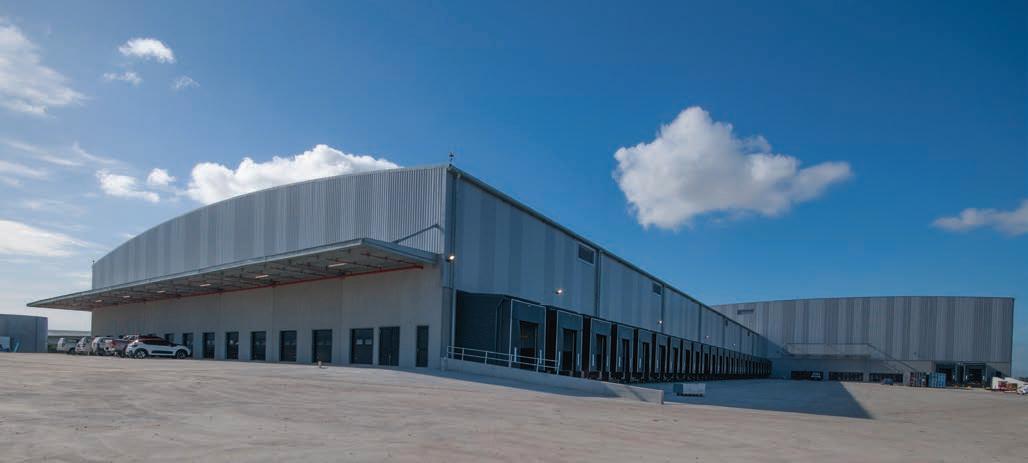
5 minute read
Massive logistics warehouse built with precast concrete
Massive logistics warehouse
BUILT WITH PRECAST CONCRETE
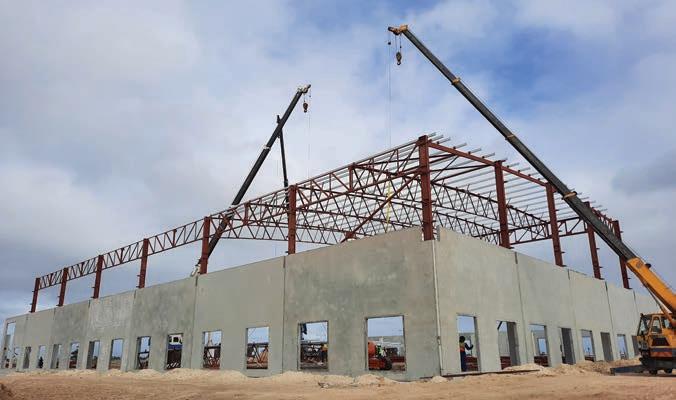
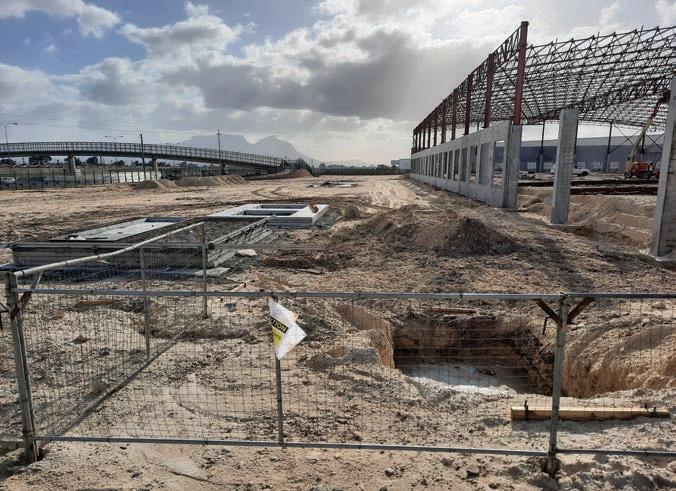
Solar City, Cape Town is where a massive 37 000m² warehouse was completed at the end of June for a global transport and logistics company.
Situated on a corner site flanked by one of the runways of Cape Town International Airport and the N2 highway, the structure was built using precast columns and tiltup panels supplied by precast building specialist Superstruct. The warehouse has two main sections: a 30 000m² logistics section and a 7 000m² cross-dock facility.
Marius van den Berg, MD of Berg Partnerships, the development’s project managers, says that four to six weeks were saved by using the precast elements. “Besides in-situ construction being slower than its precast equivalent, we were able to begin casting before approval had been granted, which also saved time,” he says.
Heavy lifting
Forty-one different column configurations in heights of 4,7m-17,2m and varying widths and thicknesses were cast. The
(Top left): The cross-dock section flanked by one of the western elevations and the smaller southern elevation. (Top right and left): The warehouse under construction adjacent to the N2 highway.
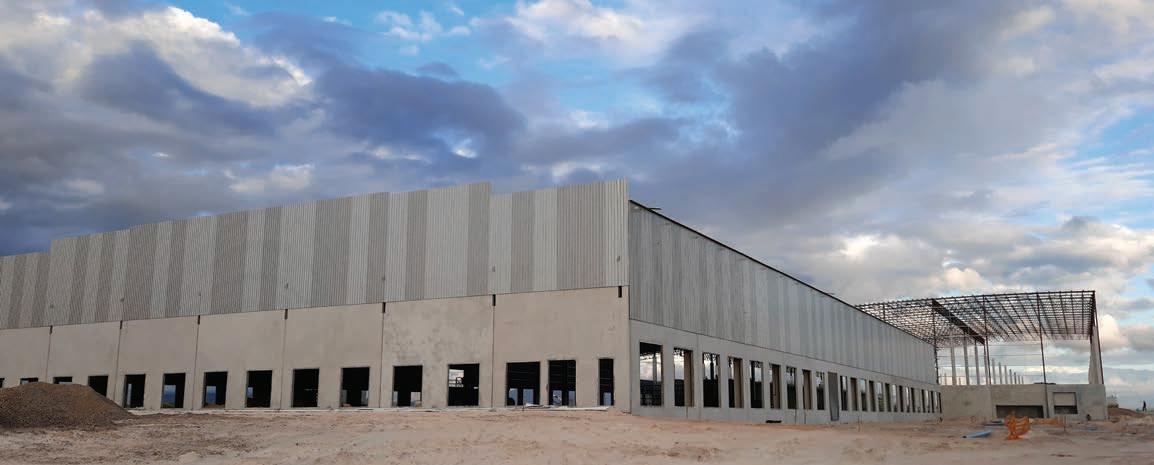
BUILT WITH PRECAST CONCRETE
panels are extremely large, their 9,6m (width) x 6,155m (height) being close to the outer limit for a panel thickness of 150mm, which was used on this project.
“Lifting and placing of panels as large as these is an operation which requires careful planning and execution,” says Bruere Visser, managing director of Superstruct. “The placement of lifting anchors in the panels must be accurately calculated to avoid cracking during installation, a process which must be as brief as possible.
“Therefore, to minimise any damage during installation, we worked with numerous casting beds so that all the precast elements could be cast as close to the installation points as possible. Mobile cranes with loading capacities of 90-140 tons were used to lift the columns and panels off the casting beds into their final positions.”
Multi-purpose
Superstruct’s columns provide three support functions: for the panel walling, some mezzanine flooring and for the roof’s steel structure. They were cast with starter bars for meshing with the column-base rebar and HD bolts at the top end for tying into the structural steel.
All the blindings were checked for levels before the columns were placed, which – once done – were shimmed to the correct height and plumbed to the correct alignment. Where necessary,
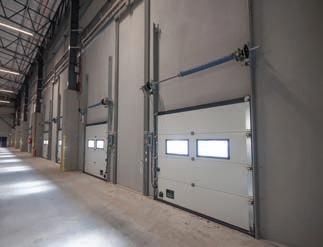

(Left): Some of the panels inside the northern elevation of the cross-dock section and some of the 17,2m columns in the warehouse’s logistics section.
further alignment adjustments were made immediately after the foundation concrete had been poured.
All the panels were lowered onto the column bases at each panel end and were attached to the columns with steel brackets. Besides providing the building’s perimeter walling, the panels retain the sub-grade soil under the flooring to depths varying from 600mm-2,075m.
Docking panels
The warehouse has six elevations; the southwestern corner is recessed and therefore carries two additional elevations. Fortythree docking panels were installed on the northern elevation over its 413m length. All 9,6m wide, they were cast in heights which varied from 6,7-8m. Steel dock houses were fixed and built in front of the panel openings once the latter were securely in position.
A further 26 docking panels were installed on the narrower of the two southern elevations, which is 125m long and provides loading access to the cross-dock section. Also 9,6m wide, these panels were all 6,025m high and their openings were lined with galvanised steel frames to protect
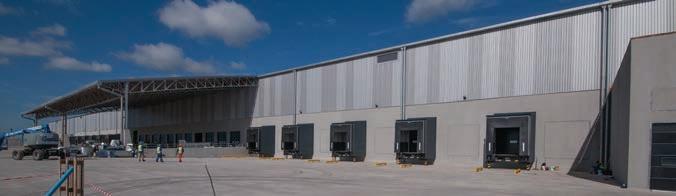
the concrete facings against damage from forklifts and other vehicles.
The wider of the two western elevations was installed with seven open-faced panels measuring 8m (width) x 6,8m (height) for vehicle access to the cross-dock section. The smaller western elevation was built with seven open-faced panels measuring 8m (width) x 6,3m (height) and provides access to the logistics section.
Loose sand
The wider of the southern elevations runs for 290m from end-to-end and was built with 30 closed-face panels. Due to its close proximity to the N2 highway, these panels were cast inside the building’s perimeter, unlike in the rest of the building, where they were cast on the outside of the building. The southern elevation was also installed with 1,3m x 1,3m x 250mm thrust blocks which were cast insitu at the bottom and centre of the panels.
Using kickers, they lend additional support to the panels, which on this side of the building must retain sub-grade to a depth of 2m. The eastern elevation, which is where the administration section is housed, has only two panels. The remainder of the walling on this elevation was built with conventional masonry.
Visser says that one of the major challenges on the site was the loose sand, which required the use of smaller cranes and more casting beds. “Moreover, this was
(Left): The northern elevation with some of the docking bays installed.
a tight programme and although we started with the columns, much of the casting had to be done concurrently,” he adds.
“Steel-ribbed sheeting was installed between the panelling and the roof to complete the walling and, in line with client preference, the tilt-up panels were given a cementitious coating for a superior external finish,” says Visser.
Project team Structural engineers:
Ekcon Consulting Engineers
Project managers:
Berg Partnerships
Architects:
François du Toit Architects
Precast concrete elements:
Superstruct
Quantity surveyors:
CHS Quantity Surveyors
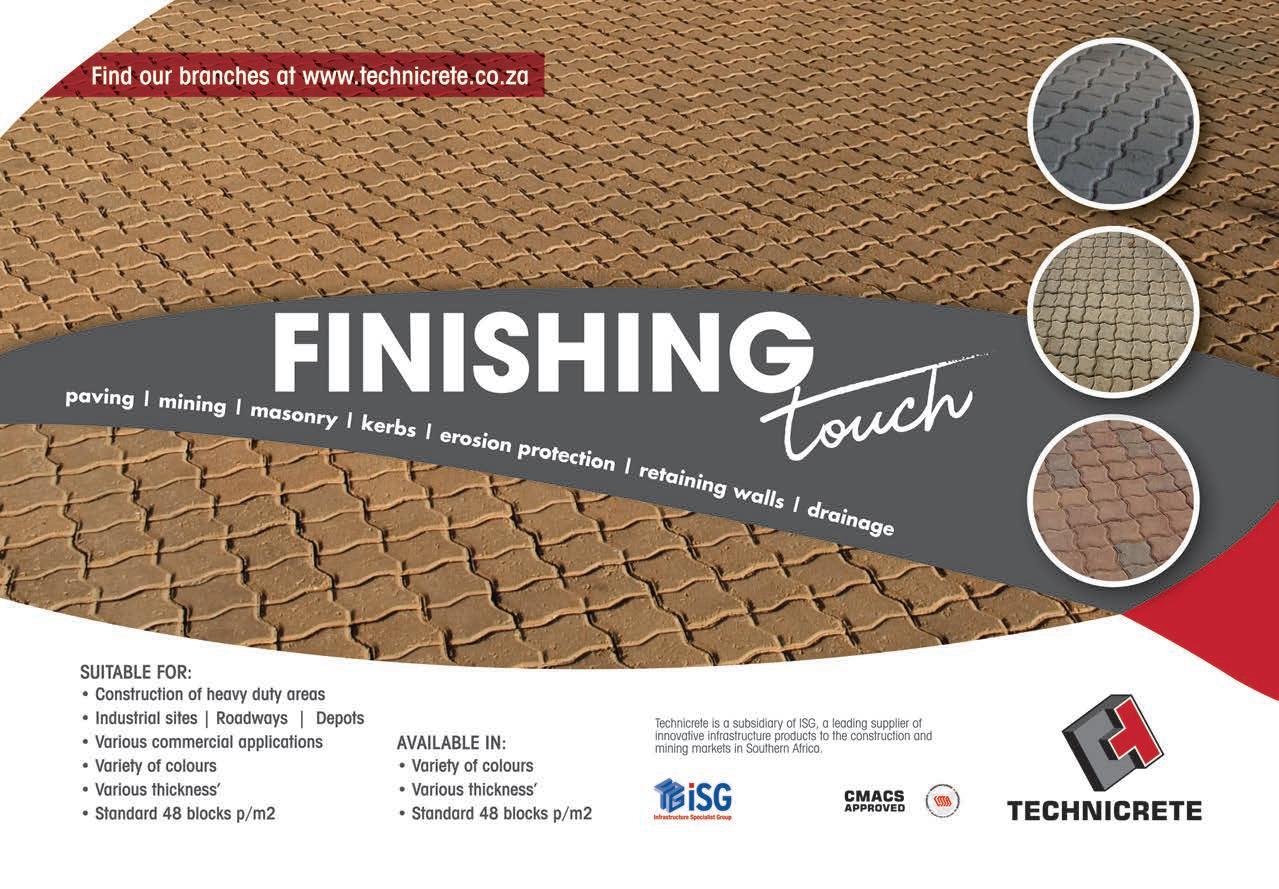