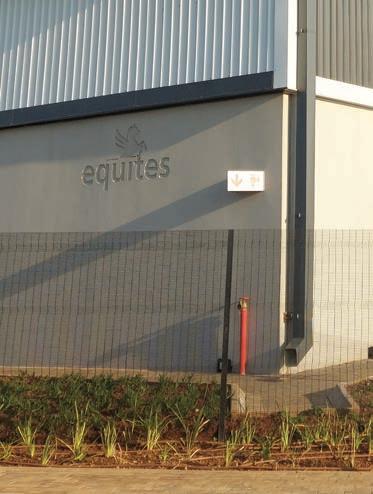
3 minute read
Precast warehouse completed despite lockdown restrictions
(Below and bottom): The Equities Property Fund logo was expertly embossed into some of the concrete panelling by Superstruct.
(Right): The completed Imperial Logistics warehouse.
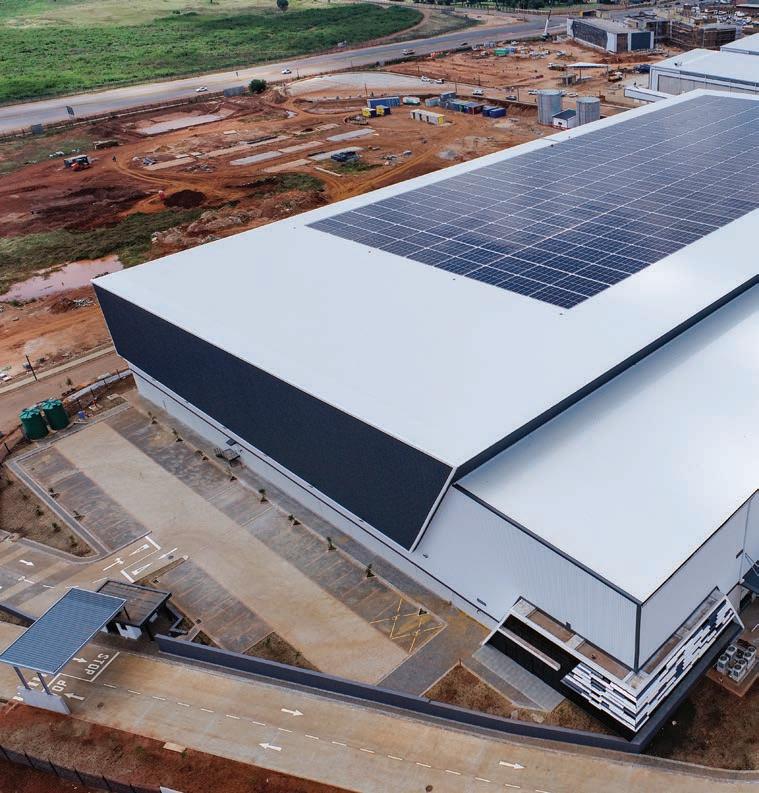
Precast warehouse completed
DESPITE LOCKDOWN RESTRICTIONS
Despite lockdown restrictions, rock-blasting and rain delays, a 17 000m² healthcarecompliant warehouse was constructed for Imperial Logistics in 2020 within the seven-month contractual period. Developed at Witfontein X57 in Pomona, Gauteng, by JSE-listed Equites Property Fund, the warehouse shell was completed in December using precast columns and tilt-up panelling, cast and installed by tiltup specialist Superstruct.
Other members of the professional team included architects, Empowered Spaces, structural engineers DG Consulting, quantity surveyors Schoombie Hartman, Imperial and Lead Logistics Provider Division (formally Resolve Capacity) and main contractor Ndwala Construction.
Lloyd Zacharias, Equites Property Fund project manager, comments: “A substantial advantage of building with precast concrete is that one can get going with the concrete preparation while waiting for council approval. We had to pause all construction work during the April lockdown, but as soon as it was lifted, we were able to begin with the assembly of the precast elements in June. This major win for the project enabled us to complete the project on time.”
Superstruct supplied 103 columns in heights which varied from 11,75-15,66m. Seventy-seven panels were supplied in heights from 3,7-10,7m and widths which ranged from 2,3-10,5m. Twenty-one columns were placed inside the building in three rows to support the roof structure. The rest were mounted on the building’s
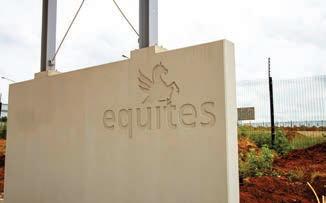
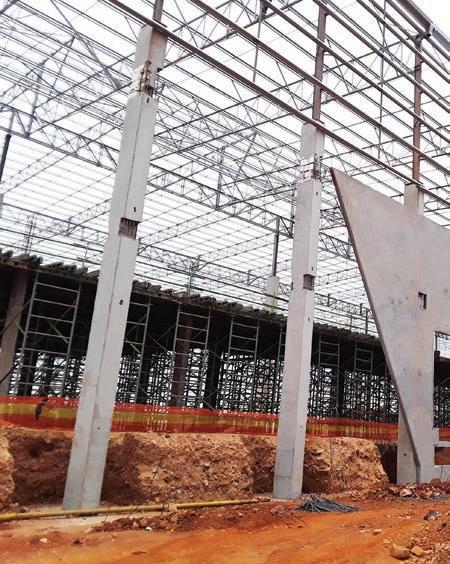
DESPITE LOCKDOWN RESTRICTIONS
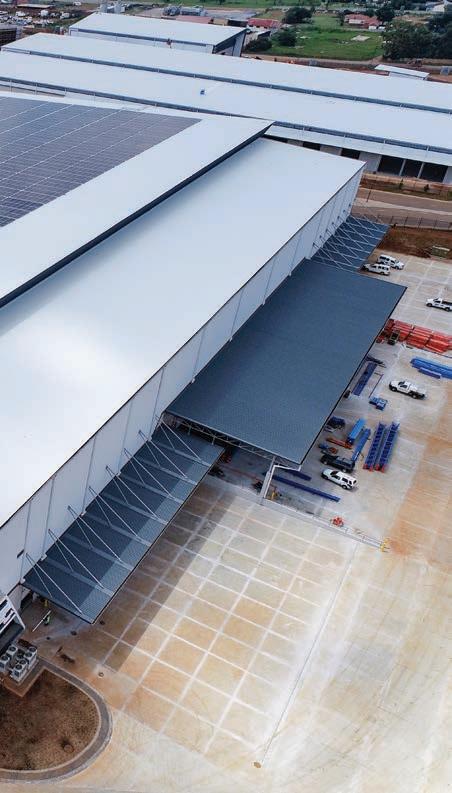
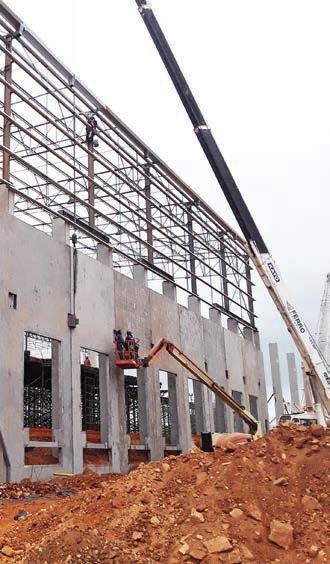
perimeter to support the panels and the roof.
Bruere Visser, managing director of Superstruct, comments: “Under Level 4 lockdown restrictions, we managed to cast all columns shorter than 13m offsite at our manufacturing facility at Lords View, manufacturing only a handful of columns on site.
“When we moved on site, we cast the panels and the few remaining columns. All columns were cast with protruding starter bars, stitched together with the rebar, which had been cast into the column bases. While the concrete was poured and during a seven-day curing period, the columns were supported with push-pull props. We make it easy for the design team to follow the in-situ rebar design using precast columns because we simply swap the starter bars from inside the footings to inside the columns. Everything else stays the same,” explains Visser.
The panels were cast on site on sacrificial beds which were stack-cast up to five panels each. Carefully positioned lifting inserts were cast into the columns and panels to prevent cracking during lifting into position, which was done by a crawler crane. The panels were lowered onto the column bases and then bolted onto the face of the columns with steel brackets and wedge anchors. Besides functioning as exterior walls, the panels act as retaining walls, retaining soil under the warehouse floor to a depth of 2,1-2,45m.
Once the panelling had been installed, it was given a cementitious coating. It binds with and resembles concrete and gives a world-class uniform finish. Unlike naked concrete, it offers consistent colouring. In addition, it is very stable and does not flake.
Superstruct was founded in 2018 by Bruere Visser. Its first project was a 33 000m² BMW warehouse in Midrand. Since then, the company has completed over 50 projects in greater Johannesburg and the Cape Peninsula.
“Our core business is the construction of warehouses for clients who intend keeping their properties for a long time. Clients who want to leave a legacy tend to use us, as they appreciate the superior properties of precast concrete,” says Visser.
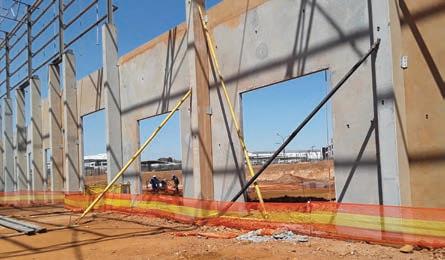
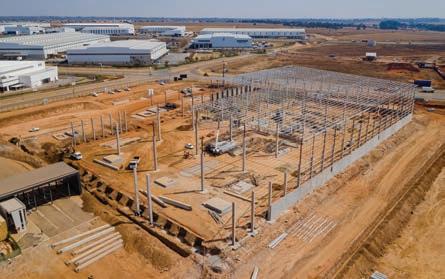
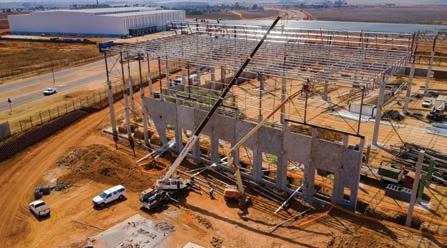
(Left and above): The Imperial Logistics warehouse takes shape with precast columns and panels supplied by tilt-up construction specialist, Superstruct.