
5 minute read
New stormwater drainage system for Hermanus CBDs
New stormwater drainage system FOR HERMANUS CBD
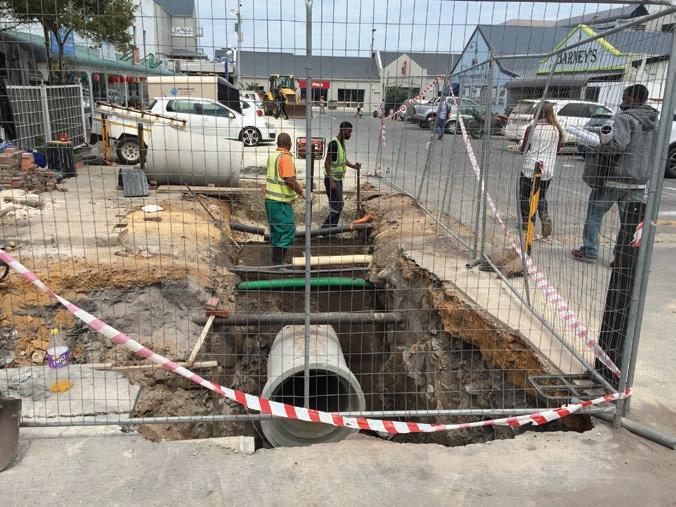
A new stormwater drainage system has been installed at South Africa’s whalewatching hotspot. A substantial increase in non-permeable paved surfaces and buildings over the decades, combined with an increase in the intensity of rainfall, meant that the CBD’s original ø300mm stormwater drainage system could no longer cope and the area’s High St and Main Rd had flooded on at least three occasions during the previous eight years. The new system comprises a combination of 450mm, 525mm, 750mm and 900mm
(Above): Tertius Retief of Element Consulting Engineers inspects the outlet structure and the construction of gabions around the ø900mm pipe outlet above the entrance to the ø450mm exit pipe.
(Left): A section of ø750mm pipe installed in Dirkie Uys St between High St and Main Rd.
diameter concrete piping supplied by CMA member Rocla, as well as a short section of HDPE structured wall pipe which was installed under luxury apartment block Hamewith Penthouse.
Hermanus falls under the jurisdiction of the Overstrand Municipality. In 2013, Dennis Hendriks from the council’s Engineering Services Department commissioned Element Consulting Engineers to develop a stormwater masterplan for the town’s CBD and industrial area. When the first funding was allocated by the municipality in 2018, Element Consulting Engineers proceeded with a detailed design of the stormwater network based on the guidelines outlined in the masterplan. Pipe-laying in the CBD section, which was handled by main contractor Meyer Beton Siviele en Boukontrakteurs, commenced in May 2020 and was completed in February 2021.
New piping was installed along High St, Main Rd and Dirkie Uys St. A section of ø525mm Class 100 pipe was run over 45m from the eastern end of High St to the point where it intersects with Dirkie Uys St. Similarly, a 117m portion of ø525mm pipe was installed from the western end of High St to the same intersection. Both feed into a ø750mm pipe which was installed at right angles to High St and runs from the High St/Dirkie Uys junction for 52m to Main Rd, where it links into a ø750mm pipe at right angles. The Main Rd pipe drains in an easterly direction for 43m, ending at one of the road’s trapped low points outside the entrance to Hamewith Penthouse. There is no overland escape route for large volumes of stormwater from this point and it is here that additional grid-inlet catch-pits were installed and the stormwater piping system was increased to ø900mm.
“Initially, the proposed route for the ø900mm pipe was all the way down Main Rd in an easterly direction towards the Marine Hermanus Hotel,” says civil engineer Uli du Toit of Element Consulting Engineers. “However, after investigations and then consultations with the owner, we agreed to redesign the pipe layout and route
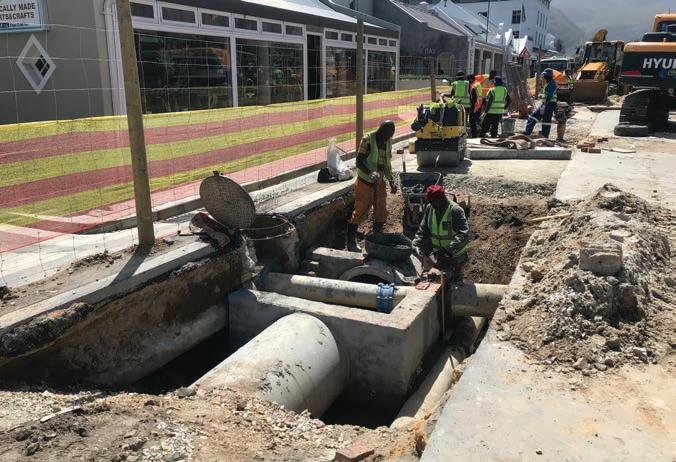
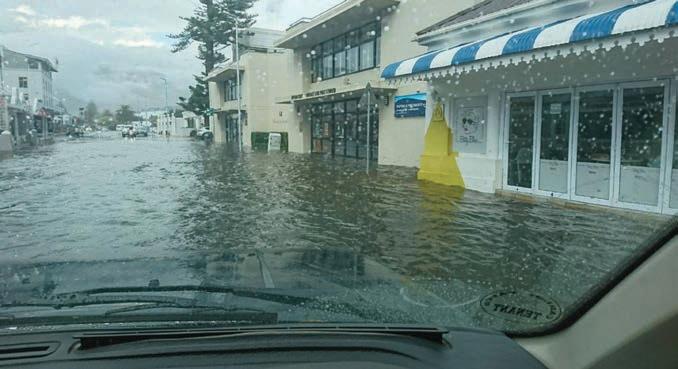
it under the Hamewith Penthouse building. This resulted in a considerably shorter route from Main Rd to the outlet, which is located off Marine Drive, and reduced the Main Rd installation/closure period. “Constructed as a concrete frame structure, Hameworth Penthouse is supported on concrete footings and columns. Consequently, we were able to route the ø900mm HDPE structured wall pipe through the ground-floor driveway without jeopardising the structural integrity of the building’s foundations. We opted for lightweight HDPE pipes due to a limited overhead clearance, which precluded the use of large construction plant for lifting much heavier concrete pipes. “Another consideration in favour of the HDPE option was that the building’s vehicular loading is considerably lower than loading on public roads. The HDPE
(Above): A manhole under construction where the new ø750mm and ø900mm pipes intersect under the existing ø300mm piping.
(Left): The flooding Main Rd’s trapped low-point during heavy rainfall. (Photo by Johan Pretorius)
pipe is linked to a ø900mm concrete pipe which runs under Marine Drive and the Marine Drive parking lot to a newlycreated outlet structure seaward of the parking lot,” says Du Toit.
“The ø900mm pipe discharges stormwater from the outlet structure into an existing ø450mm exit pipe. The outlet structure was positioned over and drains into a cavity which we cut into the exit pipe. The pipe descends to the shoreline at a steep angle, which gives it the capacity to handle large volumes of stormwater. However, should it become blocked or reach its full capacity – for instance, during a once-in-50-years storm – any overflow will discharge down the embankment into the sea. In anticipation of this occurrence, gabion boxes were installed to act as energy dissipators to protect the embankment from severe flood erosion.”
The new drainage system has been installed with grid inlets in High St and a combination of grid and kerb inlets in Main Rd. In addition to the new stormwater drainage system, High St is undergoing a facelift and the old tarmac road surface and kerb system has been replaced by concrete block paving laid on the road and pavement surfaces. These are interspersed with open stormwater channels which were covered with the same concrete block paving, supplied by CMA member CEL Paving Products. Although Main Rd has retained its tarmac and kerbing system, grid inlets have been added for additional drainage capacity.
The new system traps most litter before it enters the stormwater system, but some debris does get through, especially via the kerb inlets in Main Rd. To counter this, a steel grid was installed into the exit-pipe opening into which the ø900mm pipe discharges.
According to Nollie Meyer, managing director of Meyer Beton, the installation of the stormwater system presented several challenges.
“The existing stormwater, sewer, water and electrical utilities had been randomly installed from the time Hermanus gained municipal status in 1904 and only limited as-built drawings, indicating where these services had been installed, were available. The fact that the new stormwater pipes had to be laid below and above all of these existing services complicated and slowed the installation process. Moreover, the in-situ soil conditions in the installation area comprised mainly 400MPa rock which had to be excavated using a metapinion, concrete compressors and electric breakers,” says Meyer.

(Above): Excavation for the ø900mm HDPE structured wall pipe underway in the undercover parking at Hamewith Penthouse.
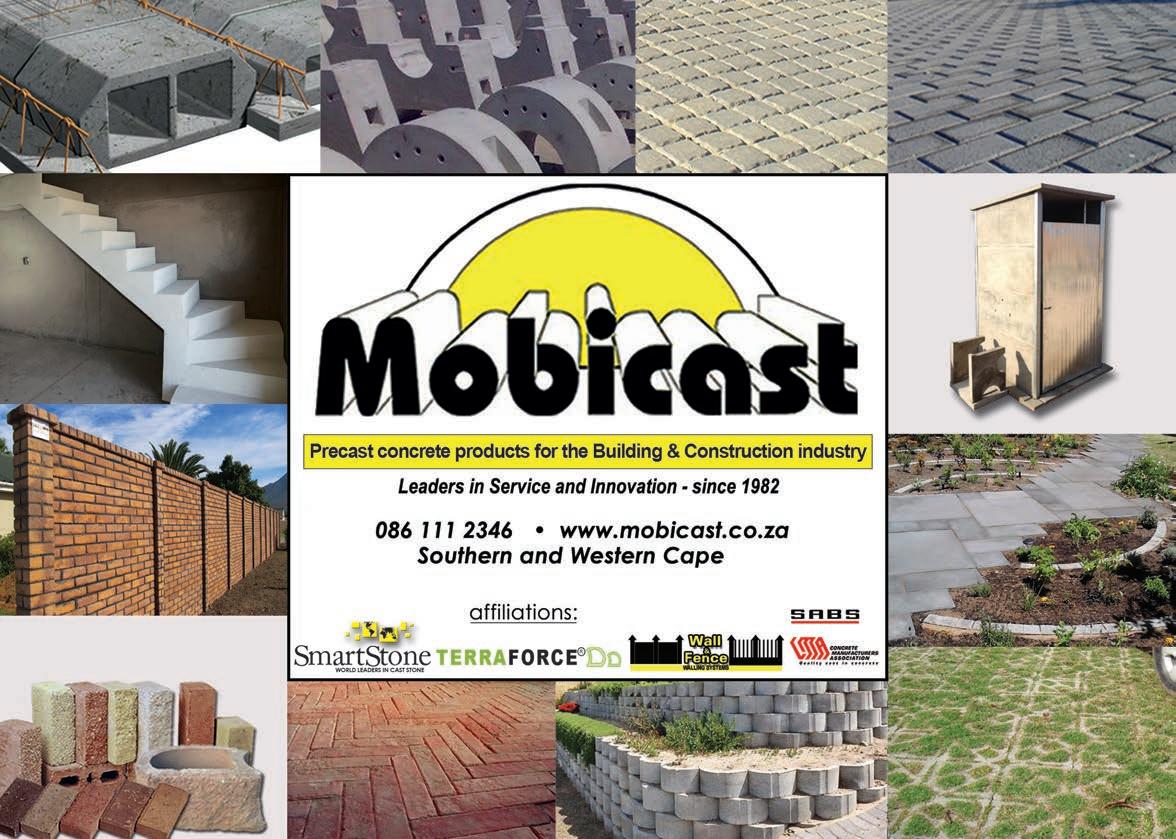