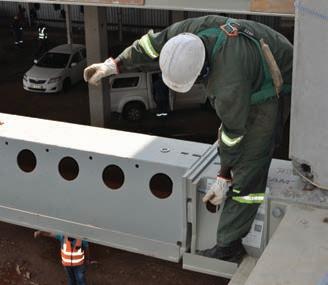
4 minute read
Production continues during biscuit factory expansion
Production was not interrupted at biscuit producer Continental Brands when Peikko SA’s precast concrete building framework and bolted-connection system was used for converting ground-floor factory/warehouse buildings into multi-level structures.
Continental Brands is adding 7 000m² to its Johannesburg-based factory over two phases, providing additional production, storage and office space. Phase 1 extension took place in 2020 and added a 2 000m² mezzanine level above the ground-floor factory (Block A). Phase 2, which is earmarked for completion by the end of 2021, will see the addition of two floors to an adjacent warehouse (Block B) and the construction of a new building on open ground situated between Blocks A and B. The open-ground building is being attached to the extended Block B to form a seamless three-storey structure.
Both extension phases were designed by Marco Riccardi Architectural Design.
Principal partner, Marco Riccardi, says the expansion will enable the doubling of output from two to four production lines and will provide for any future expansion of production and storage space.
“We looked at various construction opanchor bolts, column shoes, delta beams, hidden corbels and copra anchor couplers. The project’s only in-situ construction elements were the structural toppings on the hollow-core slab flooring and the construction of stub columns and flooring on the ground level of the open-ground section.
“We prepared a 3D model so that the client could see the precise column placement. We then drew up a detailed engineering plan which included column design and the placement of rebar, column shoes and the levels of the hidden corbels,” says Peikko project engineer Winston Visser.
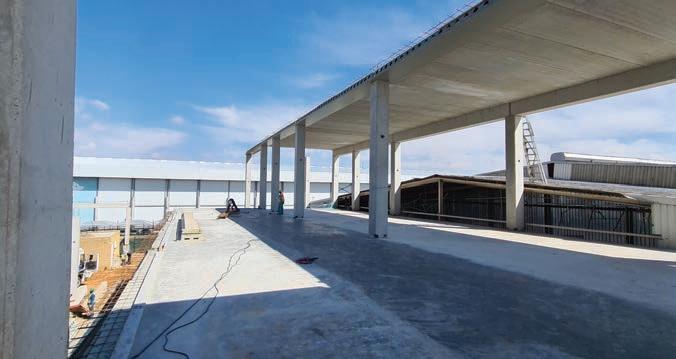
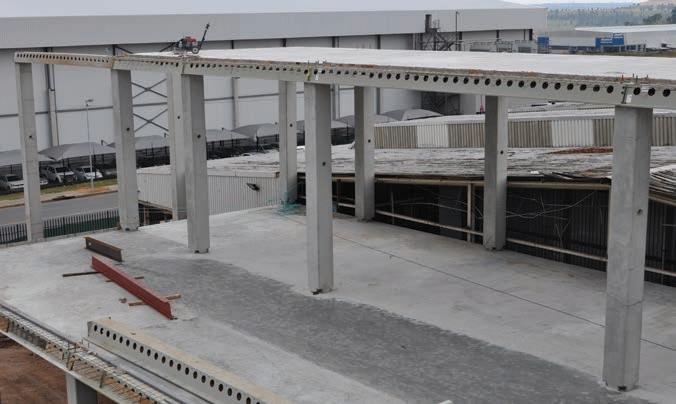
tions. Speed of erection, column strength and the use of as few columns as possible were some elements which informed our decision-making process. Besides fulfilling these criteria, Peikko is part of a renowned international brand, which was a selling point. However, the fact that production could continue during construction was the clincher,” he says.
Having successfully extended Block A using the Peikko system, Peikko SA was appointed to design and manage the construction of Block B’s precast concrete framework, a process which was begun in March and completed at the end of April 2021.
The project involved using precast concrete columns and hollow-core slabs in combination with five Peikko products:
(Top): The partially completed open-ground section of Block B.
(Left and right): Piekko’s delta beam installation.
The columns were precast off -site by Ludikon Construction and the hollow-core slabs were produced and installed by CSS Concrete Slab Supplies.
“The extension of Block B’s factory section involved a top-down construction process. It was begun by cutting the surface bed of the factory’s existing ground fl oor and casting mini-pile caps with anchor bolts. Columns 12m high were then lowered through the roof onto the mini-pile caps, a process which involved threading the anchor bolts through the column shoes attached to the bottom of the columns. Steel nuts were then screwed onto the anchor bolts to hold the columns securely in position. The installation and securing of the 12m columns inside Block B only took a day,” says Visser.
Once the ground-floor columns had been installed, construction of the second fl oor was begun. The second fl oor was constructed before the fi rst fl oor so that when the existing steel roof of the ground fl oor unit was removed, the ground fl oor would not be left at the mercy of the elements. Delta beams were attached to anchor bolts on top of the 12m columns and hollow-core slabs were laid on the delta beams. The former process was done in the morning and the latter in the afternoon. Once the were attached using hidden corbels which had been inserted inside the 12m columns.
The next phase involved installing 22 7,5m perimeter columns and one 9,5m central roof column using anchor bolts and column shoes. Copra® anchoring couplers were precast into the top of the columns to provide for the installation of a structural steel roof.
The construction of Block B’s openground section used the same material mix and construction process as the extension of the existing ground-fl oor factory. However, it involved traditional bottom-up construction using three sets of columns which measured just under 6m each. It also involved raising the fl oor of the open-ground section by 1m above ground-level to tie in with the existing factory fl oor.
“The Peikko system is transforming the South African construction landscape,” says Riccardi. “We have several international clients who are moving in this direction. Besides saving time, it complies with SA’s health and safety requirements.”
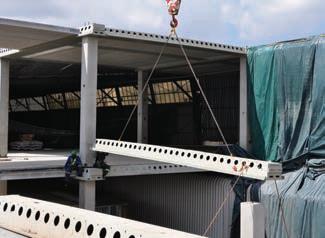
hollow-core beams were in position, they were covered with a reinforced in-situ structural topping
The steel roof of the ground-fl oor building was then removed and the construction of the fi rst fl oor was begun. It followed a similar process to the construction of the second fl oor, except that the delta beams
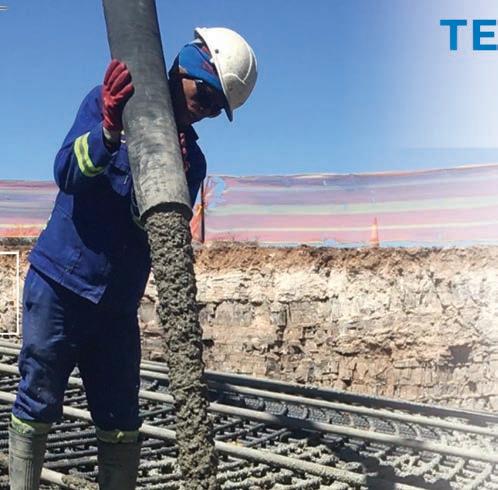
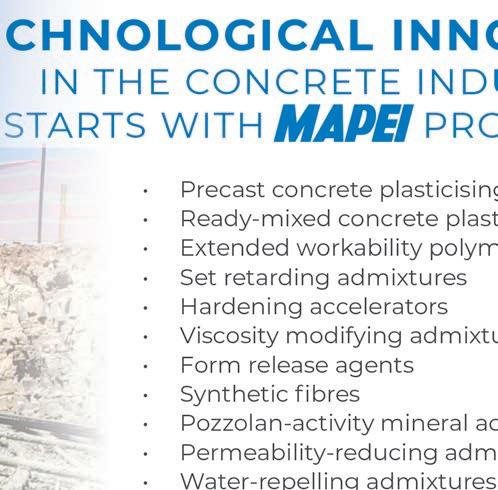

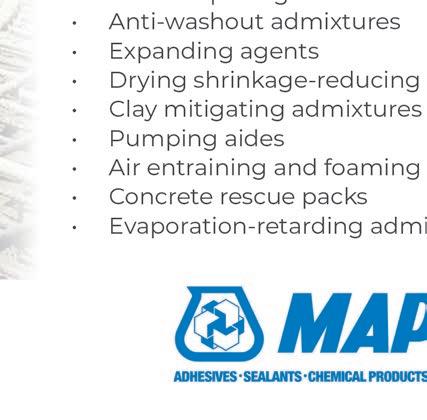