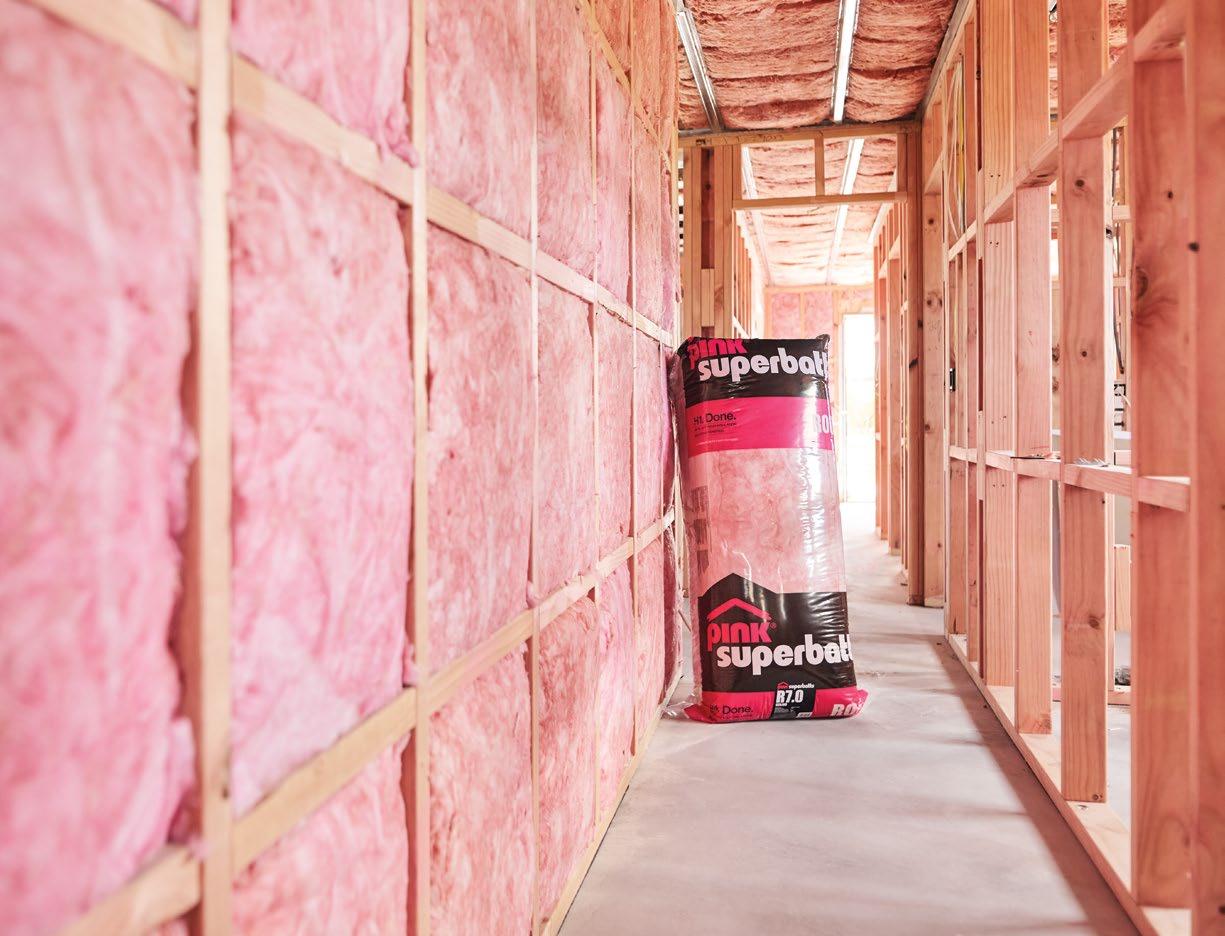
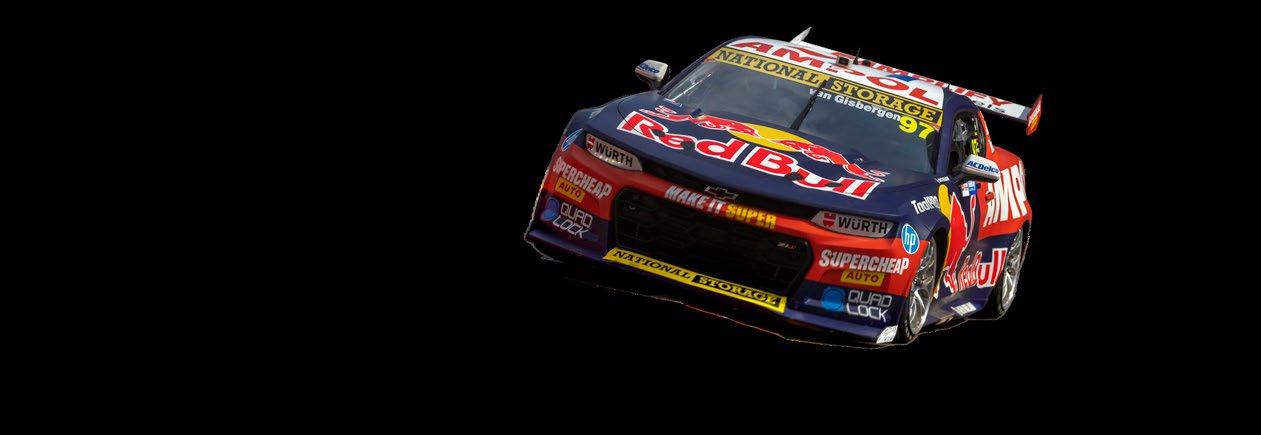

Building Business contributes towards your LBP skills maintenance requirement. Log-in to the LBP portal lpb.govt.nz and update your Skills Maintenance activities today.
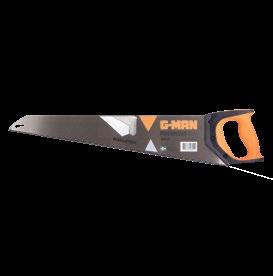
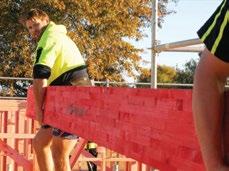


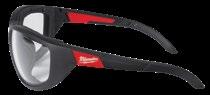
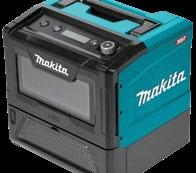
Building Business contributes towards your LBP skills maintenance requirement. Log-in to the LBP portal lpb.govt.nz and update your Skills Maintenance activities today.
To support the industry in meeting the new H1 Building Code requirements, Comfortech® has introduced a new product range, Pink® Superbatts® insulation.
Specifically designed to meet H1 and developed in partnership with the local industry and installation network, the Pink® Superbatts® insulation range is extra wide to maximise thermal performance and reduce thermal bridging.
Tried and tested right here in New Zealand, these batts® ensure a quality product for our New Zealand environment – the best fit for your build.
To address concerns around thermal bridging and heat loss between segments in ceilings, Comfortech® has developed the new extra-wide Pink® Superbatts® insulation.
▷ Pink® Superbatts® insulation range is extra wide to maximise thermal performance and reduce thermal bridging.
▷ It is available in various R-values for compliance via the Calculation and Modelling methods.
▷ Comfortech® has also developed a two-layer solution. A 110mm thickness for the first layer and 160mm thickness for the second layer.
At 460mm wide, rather than the traditional 432mm, Pink® Superbatts® ensures a tight fit around the truss chords, with optional on-site notching to eliminate air gaps and airflow around structural members.
Comfortech® is committed to supporting the industry by providing the best H1 insulation solutions and regular up-to-date information on navigating these changes. With that in mind, the Comfortech® team has created the ‘H1 Hub’, a go-to source for all H1 information, residential and commercial solutions, tools, advice, and downloadable resources.
The introduction of the H1 Building Code changes supports Comfortech® in achieving its goal of creating a more sustainable and comfortable future for all New Zealanders, enabling Kiwis to live and work in warmer, healthier and more energyefficient buildings.
Pink® Superbatts® is available as an R7.0 for compliance via the Schedule method and other R-values for compliance via the Calculation and Modelling methods; these will include Pink® SuperBatts® insulation R4.5, R5.0 and R6.0.
In developing its two-layer solution, Comfortech® knew it needed a denser first layer to ensure the expected thermal performance was still delivered under the compression of the second layer, as two layers of R3.6 would not deliver R7.2 once compression was factored in.
Furthermore, while typical truss bottom chords are 90mm or 140mm in height, Comfortech® identified that it also needed to accommodate metal ceiling battens hung below the truss chords and not fixed directly to them.
H1 Done. Your insulation solutions covered.
Changes to Building Code clause H1 bring the biggest energy efficiency improvements in over a decade. Comfortech®, are well prepared to help you with these changes.
Damp, mouldy, poorly ventilated homes affect the respiratory health of many New Zealanders. To help address these issues, MBIE has introduced the new 5th edition of H1/AS1 and H1/VM1 for housing and H1/AS2 or H1/VM2 for buildings greater than 300m².
This means significantly more insulation will be needed in the ceiling, walls and floors of new buildings from 1st May 2023.
Comfortech® has developed its two-layer solution, with the first layer being the Pink®Batts® insulation R2.6 with a 110m thickness for 90mm truss chords and Pink® Batts® R3.0 with a 160mm thickness for 140mm truss chords. The extra 20mm thickness ensures that the top of the first insulation layer aligns with the top of the truss chord. When the second layer is laid over, there are no pockets or paths for heat flow/loss that would reduce the effective performance.
To learn more about the H1 changes and Comfortech’s insulation solutions, visit H1done.co.nz
7L Cooler & Warmer (skin only)
#CW003GZ01
• Powered by a single 40V XGT, 18V LXT, 12V car adaptor or AC power (batteries not included)
• Cooling -18°C to 10°C
• Warming to 60°C
• IPX4 water resistance
$859
Air Compressor (skin only)
#AC001GZ
• Brushless motor provides up to 135 PSI
• Lightest weight cordless compressor in its class
• Up to 1,400 finish nails using a fully charged 40V XGT 8.0Ah battery
$699
Kettle (skin only)
#DKT360Z
• 18Vx2 (36V)
• 800ml water capacity
• 8-minute boiling time (from 23oC)
• 2 x 5.0Ah batteries will boil 1.4L of water (approx)
$259
50L Cooler & Warmer (skin only)
#CW002GZ01
• Powered by a single 40V XGT, 18V LXT, 12V car adaptor or AC power (batteries not included)*
• Cooling -18°C to 10°C
• Warming to 60°C
• IPX4 water resistance
*Two batteries can be used for increased runtime, even a combination or 40V/18V batteries can be used simultaneously.
$1359
Microwave (skin only)
#MW001GZ
• Powered by a single 40Vmax XGT battery. Runs on two batteries for extended run-time.
• Dual stage power output 350W/500W
• 8 litre capacity
• Run-time: up to 35 mins with 2 x 8.0Ah batteries
$1199
Coffee Maker (skin only)
#DCM501Z
• 12V Max or 18V battery
• 240ml water tank
• Approx 5 minutes to brew a 160ml shot (at 300W)
• Includes dedicated cup and lid
$179
The Government has announced changes to retention money requirements to give subcontractors confidence that they will be paid the retention money they are owed should a head contractor’s business fail.
The retention provisions in the Construction Contracts Act 2002 were put in place to protect retention money owed to subcontractors in the event of a business failure and to ensure that retention money withheld under construction contracts is responsibly managed.
On 30 March 2023, the Construction Contracts (Retentions Money) Amendment Act 2023 was passed by Parliament. The changes in the Amendment Act aim to strengthen and clarify protection for subcontractors’ retention money and make it easier for subcontractors to access retention money without a court order in the event of a company’s insolvency.
Many head contractors are already doing the right thing and appropriately holding retention money aside. For these people, there will be very little change.
The changes will safeguard subcontractors’ retention money by:
▶ clarifying that retention money is automatically held on trust by the head contractor once the contract allows it to be withheld from the subcontractor.
▶ removing the ability to mix retention money with other money and assets.
▶ requiring that retention money held as cash must also be held separately in a bank account with prescribed ledger accounts.
The Ministry of Business, Innovation and Employment (MBIE) is now responsible for providing information and education to the sector on the retention money regime. This allows MBIE to help businesses, companies, and subcontractors understand what they are responsible for and how to comply with the new provisions.
MBIE will also monitor compliance and have new investigation and enforcement powers.
New offences and penalties of up to $200,000 have been introduced for companies and, in some cases, directors who fail to meet the new requirements, including:
▶ failure to comply with accounting, recording and reporting requirements.
▶ use of retention money for a purpose other than remedying defects in the subcontractor’s performance.
▶ failure to provide regular information to the subcontractor on retention money.
The new retention money requirements come into force on 5 October 2023. This gives head contractors looking to hold retention money, six months to ensure processes are established and standard contracts are renewed before the new offences and penalties apply.
VB20 Vented Batten
Dristud RU24 or FRu38 roof underlay insulation guard
Dristud wall wrap
proctorpassive smartvap
Cool window flashing tape
Note: VB20 can be used in roof and wall. use in wall for vermin proofing and as a cavity batten
Over Fascia Vent
insulation R7.0
note: thicker insulation in the roof cavity, use g502 as insulation guard for 25mm air gap to minimise condensation
DriSpace H1 Systems reduce risks of condensation as a result of thicker insulation (R7.0)
ProctorPassive internal and external airtight membranes for energy-efficient buildings
CodeMark Certified DriStud Roof
Underlays and Wall Wrap
Passive Ventilation with BRANZ
Appraised Vent products Systems for all roof pitches and designs
For more information or other systems, visit DriSpace.co.nz
AI or ChatGPT. Everybody's talking about it, and a growing swell of doomsayers reckon it will mean widespread job losses. According to a report in March this year from Goldman Sachs, up to 300 million jobs could be lost to AI automation in Europe and the US. So are building careers on the line?
Yes. And no. AI can potentially eliminate some jobs in the future on large commercial building and infrastructure projects. But for the average Kiwi tradie working on residential homes, the threat of some robotic device taking your job is almost zilch.
Martin Ford, the author of Rule of Robots: How artificial intelligence will transform everything, believes there are three main categories of jobs that are going to be relatively insulated in the foreseeable future from job losses because of AI.
They include "jobs that require lots of mobility and dexterity and problem-solving ability in unpredictable environments," says Ford, who singled out trade jobs as a good example – builders, electricians, plumbers and the like.
"These are the kinds of jobs where you're always dealing with a new situation. They are probably the hardest of anything to automate."
While AI won't threaten most trade jobs in the building industry, it doesn't mean they will be totally insulated from its effects. Most jobs, regardless of industry, have aspects that are likely to be automated by the technology.
These days, many components in a home are prebuilt using a degree of automation – think frames and trusses, kitchen and bathroom cabinetry, engineered structural timber components etc.
With advanced AI, this trend is likely to continue at pace. But while AI will change the nature of some jobs, the technology will complement builders' skills rather than replace them entirely.
Skilled builders will always be required for critical decision-making, creativity, problem-solving, collaboration, and tasks that require human judgement and adaptability.
We used AI to evaluate the effects of AI in the building industry. Here's a summary:
▶ AI can automate repetitive and labour-intensive tasks, such as bricklaying, concrete pouring, or material transportation.
▶ AI algorithms can analyse data from sensors, cameras, and other sources to identify safety risks, such as unsafe working conditions or equipment malfunctions.
▶ AI can assist builders in the design and planning phase by generating optimised layouts and configurations based on historical data, building codes, and other relevant information.
▶ AI can assist in project management, including resource allocation, scheduling, and progress tracking.
▶ AI-powered training tools can provide builders with interactive and personalised learning experiences, while virtual assistants or chatbots can assist builders by answering questions and offering access to a vast repository of construction knowledge.
#4822895x - M to XXL
• Cut level 5
• Touch screen friendly
• High dexterity finger tips
• Breathable
• Ideal for wet and oily conditions, metal and glass handling and cutting
#48739030
• Cut resistance level 3
• 40cm length
• High stretch nylon
• Lightweight and breathable 15-gauge material
#48732901 - Clear, #48732906 - Tinted
• Flexible nose bridgeadjustable fit, easy fit over respirator
• Comfortable rubber arms
• Light weight
• Anti-scratch and anti-fog lenses
• AS/NZS 1337.1 2010 compliant
#NZPKOFA128
• 128 piece kit
• Part of the PACKOUT™ System
• IP 65 rated seal
• Ready for any emergency
• St John first aid leaflet included
#48739050
• Cut resistance level 5
• 40cm length
• High stretch nylon
• Lightweight and breathable 13-gauge material
#48732940 - Clear, #48732945 - Polarised
• Anti scratch, anti fog lens
• Comfortable arms for extended wear
• Removable gasket protects against debris
• Soft case included
• AS/NZS 1337.1 2010 compliant
Accelerated silicosis is a distinct and aggressive form of silicosis - especially affecting those working with engineered stone. WorkSafe have been working with health and safety professionals and other government agencies since early 2019 on how best to respond to this emerging issue.
Silicosis is a disease that causes scarring of the lungs. Accelerated silicosis is a type of silicosis which may occur after a worker has been exposed to large amounts of respirable crystalline silica (RCS) dust. It typically develops over three to 10 years but there have been cases overseas after less than one year of exposure.
Accelerated silicosis is a serious health condition.
Crystalline silica is a natural substance found in concrete, bricks, rocks, sand, clay, and stone. It’s also found in artificial or engineered stone used to make composite benchtops for kitchens, bathrooms and laundries.
Respirable crystalline dust is created when materials containing crystalline silica are cut, ground, drilled, sanded, polished, or otherwise disturbed. RCS particles are extremely small (‘respirable’); they can’t always be seen with the naked eye. Exposure to RCS dust, from any source, can harm human health.
Workers in the following industries or who work with the following materials are most at risk of being exposed to RCS dust:
▶ quarrying
▶ roading
▶ foundries
▶ construction: concrete, stone, bricks, mortar, fibre cement products
▶ manufacturing of concrete, bricks and tiles
▶ kitchen benchtop manufacturing (natural and engineered stone), finishing and fitting
▶ abrasive blasting
▶ monumental masonry work
▶ mining
▶ concrete drilling, cutting, grinding, fettling, mixing, handling, dry shoveling, tunneling.
As a PCBU, you must ensure the health and safety of workers and that others are not put at risk from your work.
Before starting work using artificial/engineered stone, you must complete a risk assessment and review your controls.
You must eliminate risks that arise from your work so far as is reasonably practicable.
▶ When deciding how (control measures) to eliminate or minimise risks, you must identify when work tasks may create RCS dust.
▶ Give preference to effective control measures that protect many workers at the same time.
▶ Talk to your workers to get their views on which control measures to use.
Use alternative products (e.g. metallic shot, slag products or grit instead of sand for abrasive blasting).
If you can’t eliminate risks, you must minimise them so far as is reasonably practicable.
Instead of using engineered stone, use materials with a lower silica content. Engineered stone has approximately 90% silica compared with natural stone like marble and limestone which have around 2% silica.
Abodo’s decking range has been extended to include a silky underfoot Vulcan Smooth Decking.
Abodo introduced this semi-vertical grainoriented premium decking board in response to the residential market wanting a super stable, super durable, smooth-faced decking surface. It will appeal to those seeking a local, sustainable alternative to imported tropical hardwood.
Abodo's Vulcan timber comes from 100% plantation, rapidly renewable, NZ-grown Radiata Pine with a FSC® Chain of Custody certificate (SGSCOC-004944). Thermally modified to enhance its durability and treated with an organic preservative system, it's also a safe alternative with verified carbon-storing benefits.
As with the reeded face Vulcan Decking, Vulcan Smooth decking boards will come uncoated in their beautiful homogeneous brown colour, weathering to a grey appearance. It can be coated with decking oil, but we recommend uncoated for lower maintenance.
Abodo's brushed finish is expertly crafted with the look of timber grains that have aged naturally.
Shown here on Vulcan Cladding, the textural aesthetic stands on its own or complements a smooth material beautifully.
Over many years of exposure to wind and driving rain, softwood timbers are affected by what is known as 'grain erosion'. The softer earlywood of the wood weathers back while the harder latewood of the wood's growth rings stand out. This results in a three-dimensional textured surface with unique natural grain variation and a beautifully textured look.
Abodo can replicate this natural effect using a state-of-the-art machine, using a series of abrasive brushes to scour out the softer timber - perfectly mimicking nature's efforts.
When combined with a pigmented coating, many different visual effects can be achieved. Vulcan Brushed is available in cladding, panelling and screening.
The sale of electric vehicles is zooming upwards – battery-powered EVs accounted for just 4% of light vehicle registrations in January 2022 but 20% by the end of the year.
While all EVs can be charged from a standard 10 amp (10A) domestic power outlet, this is very slow –adding approximately 10–15 km of range per hour. For most daily travel, this is no problem since the vehicle has plenty of time to recharge overnight, but if the user wanted to do multiple long trips back to back, they may want a faster charging solution. The average New Zealand vehicle travels 40km in a day, so for most users, the charging capacity from a standard outlet is sufficient.
However, charging cables are intended as a temporary solution, not a permanent full-time charging option. Most charging cables cannot be remotely managed, which means charging can occur at peak times or require inconvenient user intervention to avoid peak times. Additionally, charging cables may pose a safety risk, particularly if they are not handled carefully or they are used with extension cords or in other non-recommended use cases.
Faster, safer home charging requires a dedicated charging unit installed by a registered electrical contractor. These units are typically wall mounted in the garage or on an exterior wall. It requires a higher-rated connection circuit and must:
▶ be connected to a separate subcircuit.
▶ be connected to a heavy-duty cable capable of supplying the amount of power that the unit delivers.
▶ have a type-B residual current device (RCD) installed to shut off the power supply if a fault is detected – type-A RCDs are commonly installed in homes but may not be sufficient protection against faults that can occur while charging an EV.
▶ have a supplier declaration of conformity to show the unit has been tested and meets the New Zealand electrical safety laws.
Dedicated chargers tend to come in one of three sizes:
▶ 3.7kW chargers require a 20A circuit (common in many garages already) and will provide adequate charging for most users. Older EVs cannot accept more than this level of charge from an AC source.
▶ 7kW chargers require a 40A circuit, which is less common. They may need to be managed carefully to avoid overloading the standard 62A single-phase connection or have a second line added, which obviously adds cost.
▶ 22kW charging requires three-phase power, which costs more both to connect and in monthly charges. Only a small number of the current EVs can cope with this level of AC charge.
All installed chargers should have smart functionality incorporated, including as a minimum, the ability to connect to the internet and be controlled remotely, either manually by the user or ideally by a load management system. These are able to manage the demand from the charger to fit within the other needs of the household and may be able to provide (and be paid for) services to network companies and retailers.
The relevant standards to consider (freely downloadable from www.standards.govt.nz) are:
▶ SNZ PAS 6011:2021 Electric vehicle (EV) chargers for residential use
▶ SNZ PAS 6012:2022 Smart home guidelines
▶ SNZ PAS 6010:2021 Electric vehicle (EV) chargers for commercial applications (for residential complexes with shared facilities and a common connection to the network).
When restricted building work became law in 2012, measures were put in place to enable homeowners to build or alter their own homes following some intense lobbying to protect the DIY tradition in New Zealand.
Sections 90A to 90D were inserted into the Building Act 2004 on 13 March 2012 and introduced the owner-builder concept, allowing the tradition to continue, but with conditions.
A homeowner who qualifies for this exemption does not need to use a Licensed Building Practitioner (LBP) for any restricted building work on their home. However, they still need to apply for building consent.
The owner is required to complete the statutory declaration form as part of the building consent application to obtain an owner-builder exemption, outlining what restricted building work they intend to complete under the owner-builder exemption.
The owner must give notice to the building consent authority if there is a change in the owner-builder carrying out the restricted building work or when the owner-builder ceases to carry out the restricted building work under the approved exemption.
To qualify for the owner-builder exemption, the owner of a building must:
▶ live, or intend to live in the home (this includes a bach/crib or a holiday home).
▶ carry out the restricted building work themselves or with the help of unpaid friends or whānau.
▶ not have used the owner-builder exemption to carry out restricted building work to any other home in the previous three years.
An owner-builder will be responsible for ensuring that restricted building work carried out under the owner-builder exemption complies with the building consent and the plans and specifications to which the building consent relates. The building consent authority will still carry out the normal building inspections.
Any restricted building work not done by the owner-builder or their unpaid friends or whānau must be carried out by an LBP who holds the appropriate licence. The LBP must provide a Record of Work (RoW) once that work is completed. The owner-builder may also hire a designer to draw their plans. The designer will need to provide a Certificate of Work.
There is some specialised work that the ownerbuilder cannot carry out, including plumbing, gasfitting, drain-laying, and electrical work.
The council will record the building work and who carried it out on the property land information memorandum (LIM). Any future buyers will have access to this information showing whether it was carried out as a do-it-yourself project by the owner or done by an LBP.
Given the requirement that any person who assists the owner must do so without payment and on the basis that they are friends or whānau, an LBP hired by the owner does not come within the ownerbuilder exemption.
An LBP who carries out Restricted Building Work (RBW) in relation to an owner-builder exemption for reward must provide a RoW for any RBW they carry out or supervise.
An LBP should also take care when being engaged to carry out RBW on a building consent issued under an owner-builder exemption that they do not unwittingly breach the building consent. In this respect, an LBP should also note the provisions of section 89 of the Act, which requires them to notify the building consent authority of a breach of the building consent.
The code of ethics applies to LBPs carrying out any building work, whether it’s restricted building work or not, and therefore applies when you’ve been engaged by an owner carrying out work under the owner-builder exemption.
If you are on-site as an LBP, be mindful of the behaviours expected of an LBP and what RBW you can carry out or supervise under your licence. If, for instance, your licence is in roofing and there is someone on-site carrying out blockwork which is RBW, make sure that you have made the owner aware that you cannot supervise that blockwork as it is outside your licence class.
However, suppose the owner is helping you put the roof on. In that case, you must ensure they’re doing the work correctly, and you will need to show on your RoW that you were supervising them.
Knowing what work you’re allowed to do is just one part of the code of ethics – the other 18 standards will also apply to at least some extent while working on the above project, just as they do while you’re undertaking any building work under your licence. You can learn more about the LBP code of ethics on the website: www.lbp.govt.nz/for-lbps/code-of-ethics
The above does not apply to an LBP licensed in the site licence class. The site licence holder could not work for payment on a project under the ownerbuilder exemption as they cannot carry out or supervise restricted building work. They may only work as an unpaid friend or family member. They would be under the supervision of the ownerbuilder.
by Bruce Duggan Senior Technical Advisor Occupational Regulation MBIEMore information on the obligations and responsibilities of owner-builders and their building project can be found at Owner-builder obligations on the Building Performance website: Go to www.building.govt.nz and search for 'owner-builders'
This article is relevant to these classes:
There is still some confusion around the site licence and what the site licence holder's responsibilities are on-site.
The site licence class is critical to the Licensed Building Practitioner (LBP) scheme. Holders of a site licence are practitioners recognised as possessing specific skills related to the oversight, coordination, organisation, and, in some cases, the management of building projects.
A site licence indicates that a practitioner has the skills to manage personnel and provide technical site supervision within the scope of their licence. A practitioner with a site licence can supervise general building work but not restricted building work.
If you are providing control, instruction or direction to others who are carrying out building work, or those working in other restricted areas, you are supervising them. Being a supervisor means you are responsible for making sure that the work is done competently and correctly to the relevant building consent. Where no building consent is required, the building work must still meet the Building Code.
An important point to remember is that, even if the work an LBP is supervising is not restricted building work, they may still be held accountable by the Building Practitioners Board for issues they are responsible for. This includes a site licence holder.
Schedule 1 of the LBP Rules sets out the competencies that make up the minimum standards for each licence class and the performance indicators that the Registrar will regard when determining whether a competency has been met.
An applicant for an LBP licence must demonstrate competence in each of these competencies in the licence class they are applying for. The Rules can be found at: www.lbp.govt.nz - search for 'LBP rules'
One way the site licence class differs from trade license classes is that the last competency in the site licence class is about providing technical supervision rather than carrying out work. In trade licence classes such as bricklaying and blocklaying, carpentry, external plastering, foundations, and roofing, the last competency is instead about carrying out the work related to that licence class.
Only LBPs can carry out or supervise RBW, and they can only supervise work they are licensed to carry out themselves. Site licence holders are not licensed to carry out building work and therefore cannot supervise RBW or issue records of work. Check out the practice note – supervision at www.lpb.govt.nz/for-lbps/lbp-practice-notes.
As noted, site licence holders can supervise general building work. They may also carry out RBW like any non-licensed person if they are supervised by an LBP with the appropriate licence.
The three areas of practice (AOP) within the site licence class can also be an area of confusion:
▶ Site 1 AOP is the coordination and oversight of Category 1 buildings.
▶ Site 2 AOP is the coordination and oversight of Category 1, 2 and 3 buildings.
▶ Site 3 AOP is the management of Category 1, 2 and 3 building projects.
Apart from the differences in envelope complexity between sites 1 and 2 (explained below under categories of buildings), the main difference between the three practice areas is that the site 3 licence holder manages the project and the technical supervision staff on what are usually large commercial projects. The staff could include one or more AOP 2 site licence holders who would carry out the coordination and oversight of the on-site construction.
The categories of buildings are found in the Schedule of the Building (Designation of Building Work Licensing Classes) Order 2010:
▶ A Category 1 building is a sleeping single home use, with a risk matrix score that does not exceed 12. More about the risk score can be seen in Part 4 of the Order, or in E2/AS1 of the Building Code, but it essentially refers to the complexity of the weathertightness envelope.
▶ Category 2 buildings are defined as neither Category 1 or Category 3 buildings - therefore, they are single home use where the risk score is greater than 12 - or any other building except for an ancillary building or an outbuilding up to a height of 10m - the vertical distance between the upper surfaces of the building's lowest and highest floors.
▶ Category 3 buildings are not single home use, and the building height exceeds 10m.
RBW is defined in the Building (Designation of Restricted Building Work) Order 2011 as being the construction or alteration of the primary structure or the external moisture management system of a house or small-to-medium apartment building.
A small-to-medium apartment has a maximum height from the lowest point of the ground to the highest point of the roof of 10 metres. This means that, as Category 3 buildings are not single home use and they're over 10m in height (measured floorto-floor), they do not contain RBW.
by Bruce Duggan Senior Technical Advisor Occupational RegulationMBIE
This article is relevant to these classes:
For article: The Owner-builder Exemption (pg 15)
1. Is the owner allowed to carry out Restricted Building Work (RBW) on their house under the owner-builder exemption?
a) Yes, this is what the owner-builder exemption is all about.
b) No, they must employ a LBP to do this work.
c) Only if they're supervised by an LBP.
2. If you are hired as an LBP on a project being carried out under the ownerbuilder exemption, you must:
a) Supervise all restricted building work being carried out on site.
b) Supervise only the work which your licence class allows you to carry out.
c) Not supervise any restricted building work as the owner is responsible for doing this.
3. If you are hired as an LBP in relation to an owner-builder exemption, are you required to provide a record of work for any RBW you carry out or supervise?
a) No, the owner is responsible for any RBW under this exemption.
b) Yes, as an LBP you must complete a record of work for any RBW you carry out or supervise.
For article: The Site License Class (pg 17)
1. Who can supervise general building work?
a) Only a trade licence holder
b) Only a site licence holder
c) Anyone
2. Can a site licence holder supervise restricted building work?
a) Yes
b) No
c) Only on Category 1 or 2 buildings.
3. Can a site licence holder be held accountable by the Building Practitioners Board for issues they are responsible for when supervising work that is not RBW?
a) Sometimes
b) No
c) Yes, this provides the client confidence that the LBP has been assessed as being competent in supervising building work.
4. Can the holder of a site 2 AOP licence coordinate and oversee work on Category 3 buildings?
a) Yes, provided they are competent to do so
b) No
c) Only if someone is living in it.
These articlea are from Codewords Issue 112.
Log-in to the LBP portal lbp.govt.nz and update your Skills Maintenance activities.
To quote Kermit the Frog, "It's not easy being green". That may be so, and it made for a cute song, but it's much more challenging when you are red. By that, I mean in the financial red.
If you want to grow a business for the longer term and build a life for yourself and your family, that's comfortable, but with just enough stress to make it interesting, you need to build a financially sustainable business.
You are not doing yourself, your team members, your suppliers and even your clients a favour if you cannot make a fair, consistent profit and sustain it in the long term. By building a profitable business, you can provide better service to your customers and assure them that you will be there if they need you to fix any issues or help them with their next project.
There are many aspects, and I welcome feedback from readers on what you consider essential. Please email me at andy@tradescoach.co.nz with your thoughts. Here are five suggestions I have, in no particular order:
1. Know your numbers. Do you know the average gross margin % you must achieve across your projects each year to hit your required dollar profit amount? What amount of gross profit will cover your overheads, pay you an owner/ manager salary, and leave a bit in the pot? This figure is vital to building a sustainable business and may require you to put a brief budget together. Contact me if you need help with this.
2. Move away from adversarial to collaborative selling. The traditional sales model in building is for the client (and maybe the architect) to be in one corner and the builder in the other. The selling process is a game of punch and counter punch until one of the parties throws in the towel and a deal is done. Both parties probably have bloody noses and feel a little hard done by. Is this the way to start the build relationship for the long term? Is it better and more sustainable for all parties to get together and make the project's outcome the main focus? Work together to come up with the best solution for all parties.
3. Learn. As a business owner, you need to find time to learn how to run your business better,
consider new ideas and put a plan together for the next 3-5 years. I know it's tough to find the extra time and energy to do this, but the reward of more money and less stress will ultimately be worth it. Keep sharpening the (mental) saw.
4. Know when to hold 'em and when to fold 'em. Be prepared to walk away from an unsustainable project from an economic standpoint. Knowing your true worth and having a clear idea of what your required gross margin on a project must be to balance the risk involved will give you the confidence to draw that line in the sand, or know exactly how much wriggle room you have in the final negotiation stage.
5. Grow at a sustainable rate. It is relatively easy to grow a construction business, at least in terms of revenue. Being overly aggressive in expanding the volume of work you take on is often done at the expense of profits. It can lead to quality control issues, which further impact profits. It can also strain your cash position because the faster a business grows, the more cash it needs to sustain that growth. Growing steadily allows your production capacity and management systems to keep pace, thus helping to deliver steady profits and keeping your stress levels in check.
by Andy Burrows Business Advisor, Mentor and CoachIf you want to hear even more tips for building a financially stable business and how we can implement them into your business, email me at andy@tradescoach.co.nz or visit my website www.tradescoach.co.nz
#ST32RW3+1
• Dual toothed for extremely fast cutting in wood
• Ideal for quick detailed plunge cutting and trimming
• Compatible with Starlock fitment multi-tools
#032CTL3+1
• Extra long reach for hard to access areas
• Heat treated, hard pointed teeth extends working life
• Super thin 0.8mm precision blade provides flexibility when working at odd angles
#ST35MB3+1
• Incredibly tough tungsten carbide toothing enables cuts through steel bolts and hardened screws
• 35mm cutting width
• Starlock fitting
#044BMT3+1
• 44mm wide titanium coated bi-metal blade
• Titanium alloy coating reduces heat build up and extends blade life
• Universal open-back fitting
#035HCT3+1
• Coarse toothing for fast yet precise cuts
• Heat treated toothing for extra long-life
• Super thin blade providing flexibility while maintaining core strength
#B3EBHCK
• Set contains two hole saw cutters and a box cutter
• Minimal dust creation and a clean finish
• Suitable for cutting plasterboard
• Handy 3 piece pack
Designed and manufactured in New Zealand, the innovative Prolam PLX20 steelreinforced laminated timber beam provides superior support for today's build.
With experience spanning more than 20 years, Prolam design, manufacture and supply glulam timber beams and posts for the residential and commercial building industry across New Zealand. They are dedicated to simplifying construction with innovative smart structural solutions that provide confidence, design flexibility and ease. Prolam's newest product, the PLX20, is no exception, offering a sustainable, lightweight alternative to steel or flitch beams with increased strength and excellent spanning capability.
Precision engineered from quality pine with steel laminated into the top and bottom laminates for extra strength and stiffness, the steel inserts of the Prolam PLX20 Beams work to provide greater strength and spanning capability, allowing a smaller beam to span further.
▶ Garage lintels
▶ Ridge beams
▶ Floor beams
▶ Rafters
The Prolam PLX20 Beam is the ideal choice for:Specifying the PLX20 beam is an easy, straightforward process. Using the online Prolam Specifier (www.prolamnz.com/the-prolamspecifier-specify-with-certainty), you can specify the Prolam PLX20 into your project and download a PS1 certificate for council compliance. The Prolam technical team can always assist with specification queries or special requirements.
two installers required on site. The ability to cut the beams to length on site and secure them with Prolam's recommended fixings makes installation straightforward. With no extra assembly, equipment or staff required for installation, you save valuable time and site costs.
Manufactured from FSC-certified New Zealand plantation timber with less steel than alternatives, the PLX20 is a sustainable high-strength solution, reducing environmental impact.
The PLX20 offers unparalleled support, load-bearing capacity and dimensional stability, with reduced risk of splitting, twisting or warping. Manufactured from select NZ-grown pine and steel components, the PLX20 beam is rigorously checked and tested, meaning you can be confident in the quality and consistency of the PLX20 beam.
You can be assured of outstanding support at every step – from specification to supply, Prolam's highly trained staff, the online specification tool, and an efficient ordering process.
Using simple product codes, the PLX20 beam is easy to specify on plans, quotes, or to place orders. With pricing on hand and some of the industry's best lead times, the Prolam team can quickly quote and manufacture your order through ITM.
Installing the PLX20 is a quick and easy process. Using less steel than alternative products, the PLX20 is compact and up to 40% lighter. Installation is faster, simpler and safer with only
Exclusive technology and market-leading New Zealand innovation combine to create stunning handle-free design. Backed by extensive research and development, the unique soft45™ panel delivers the signature uninterrupted lines of the minimal range –elegant, subtle and sophisticated.
• Premium cabinetry range featuring the unique, soft45™doors. Subtly rounded, the continuous pull-edge creates a seamless, moisture proof barrier
• 60 customisable specialty cabinets include integrated soft-close drawers, soft-close doors, colour-matched cabinet edging, LeMans and Magic Corner solutions
• Peace of mind from the superior combination of European laminates and New Zealand made board, bonded together with PUR glue –the gold standard in UV, heat, and moisture resistance
minimal -available in selected ultratouch and ultragloss finishes
quietly elegant - where less is more
the ultimate in handle-free design featuring seamless soft45™ doors
quietly elegant - where less is more
Clean, stylish, uninterrupted symmetry is the signature style of the minimal range. The secret lies in the integration of the unique soft45™ pull-edge doors with the premium cabinetry range. Together these two elements combine to create the timeless, elegant, handle-free look that will always be in demand.
Advanced technology and market-leading New Zealand innovation delivers the continuous, subtly rounded soft45™pull-edge in premium gloss and matt laminates. This all important seamless edge–superior to joined or mitred alternatives–eliminates dirt traps, and creates the ideal moisture proof barrier.
The premium cabinetry range has been created from an extensive design program to showcase the minimal style. Sixty cabinets feature fully adjustable dimensions, integrated soft-close drawers, soft-close doors, colourmatched cabinet edging, and Lemans and Magic Corner solutions
New Zealand makes the world’s best low emission MDF board, sourced from our sustainable plantation forests. ultragloss and ultratouch laminates from Europe’s most innovative supplier are PUR bonded onto the board by TDC Manufacturing -the pioneer of PUR Laminating in New Zealand. PUR bonding is the industry gold standard for moisture and heat resistance. The end result is a surface more durable and UV-resistant than paint or vinyl, ensuring complete peace of mind.
ultratouch and ultragloss finishes
pure white silk grey stone tungsten black#OLXH1
• Wheel lock
• Snap-off blade
• 25mm blade width
• Made in Japan
$16
#RG318-11
• 280mm x 120mm
• Hard-wearing carbon steel
• ABS plastic easi-grip handle
• Part-worn in blade
#GM255H22
• 550mm
• For cutting insulation material and mineral wool
• Ergonomic soft grip handle
• Wave formed edge
#TWJS1956
• 180mm
• Solid aluminum body
• CNC machined edg
• Thick edge is useful as a saw guide
• Easy-read laser etched markings
#TWCHALK4
• String Line with 120g blue chalk refill bottle
• Rubber surround for protection and grip
• 6:1 Line retraction ratio
#TWD30M
• 30m x13mm steel tape
• Heavy-duty, impact and shock resistant ABS casing
• Yellow steel blade
• 3-to-1 gear drive for faster rewind
Currently out of stock - new stock arriving early August
When it's not done carefully, the selection of concrete, steel or timber for a new building can seem like a scaled-up version of rock, paper, scissors – an instinctive choice based on personal preferences, what’s worked in the past and the desire to make an instant impact. Too often, there is too little consideration for the long-term performance of a building and what will eventually happen to the materials in it.
Going up more than 3 storeys? The obvious choice is concrete or steel. Worried about the carbon footprint? You need timber. That’s been a relatively common way of thinking, but the world is changing so fast that it’s already outdated.
Engineered timber is now playing a key role in ever-taller buildings, and the carbon footprints of concrete and steel are shrinking. Fossil-free steel has been produced. The Global Cement and Concrete Association – representing 80% of the global cement industry excluding China – has committed to producing carbon-neutral concrete by 2050, a move fully supported by Concrete NZ and the New Zealand concrete industry.
While there are extraordinary changes taking place in the manufacture and use of each of the three materials, an equally important change is in the overall mindset behind their use. It is no longer a matter of choosing either/or but of looking at what materials are the best match for particular needs and, above all, taking the longer-term view that is summed up in the idea of a circular economy.
A one-way, linear economy starts off with extracting raw materials and ends up with demolition waste filling landfills, but a circular economy designs out waste and keeps materials in use. Products are designed for a long life and are able to be repaired and eventually disassembled and reused or recycled. The process is fuelled by renewable energy. The benefits range from reduced waste and greenhouse gas emissions to long-term cost savings.
Jonas Bengtsson, CEO and co-founder of Edge Environment in Australia, specialising in sustainability, points out that planning for adaptive reuse is becoming one of the most impactful strategies, such as behind a new car parking building. The building’s owner could have built a
World-class research, award-winning designs and a new mindset are all helping New Zealand manufacturers, architects and designers take a fresh approach to those most fundamental of building materials – concrete, steel and timber.
structure with low floor heights that could only ever be used as a car park. Instead, they allowed the possibility for the building to be converted to offices or apartments in a few decades’ time by designing higher floor heights from the beginning.
Another example that can be applied to any building is designing for maintenance – designing a structure that will have a long service life thanks to the ease of maintenance.
The whole concept of a circular economy is informed by life cycle assessment (LCA) –calculating the potential environmental impacts of materials, products and services across their life cycle.
One of the key findings of LCA is that both embodied and operational carbon emissions make significant contributions to a building’s greenhouse gas emissions over its service life.
Results show that a large proportion of embodied emissions occur from building product manufacturing, transport and construction before a house is occupied (Figure 1). In fact, these emissions can be the highest of any yearly emissions during the building life cycle.
While these emissions may be lower overall than operational emissions (from energy and water use), the operational emissions occur incrementally over many decades.
In terms of whole-of-life embodied emissions, some of the main contributors by material we see are carpets, sheet metal roofing and concrete.
If concrete brings to mind strength and durability, it’s with good reason. Concrete sea walls built by the Romans 2,000 years ago are still fit for purpose. The magnificent 1,900-year-old Pantheon in Rome is still the largest unreinforced concrete dome in the world.
Concrete is also at the forefront of new construction technologies such as 3D printed buildings.
For all its substantial benefits, concrete currently has a comparatively big carbon footprint, largely from the production of Portland cement. This cement is made by heating limestone and other ingredients at very high temperatures – a process that results in large volumes of carbon dioxide emissions from the fossil fuels used and the heated limestone itself.
The New Zealand concrete industry is making significant improvements, however:
▶ Emissions from Portland cement production/ consumption reduced by 15% between 2005 and 2018 from the use of alternative kiln fuels and a lift in manufacturing efficiency. That’s impressive when you consider that concrete production increased by 13% during the same period.
▶ The industry is targeting another 15% drop by 2030. Some will come from reducing waste and lifting recycling. A real gain is anticipated from replacing some Portland cement in concrete mixes with low-carbon supplementary cementitious materials (SCMs) – byproducts from heavy industry such as fly ash or slag, or natural materials such as volcanic ash (see SCMs reduce concrete emissions for more).
Rob Gamister of Concrete NZ says that the organisation is currently collaborating with its members to develop a roadmap tailored for New Zealand with a similar framework to that adopted by the Global Cement and Concrete Association. The roadmap will set milestones on the path towards net-zero carbon concrete by 2050, with actions needed:
▶ Increased use of SCMs – recycled and natural.
▶ Efficient energy sources for manufacturing and delivery.
▶ Driving waste minimisation in manufacturing, delivery and construction.
▶ Using recycling processes to minimise the use of virgin materials.
▶ Adopting appropriate new technologies – for example, carbon capture and utilisation.
▶ Engaging with local communities.
The New Zealand concrete industry is very excited about the growth in uptake of natural SCMs –pozzolanic volcanic ash from New Zealand’s North Island volcanic plateau. The domestic supply of natural SCMs is currently being commercialised through a programme of mix design research. Once complete, this will enable strong market demand for low-carbon concrete to be met.
Given the range of concrete mixes available today, it is no longer enough for engineers, architects and designers to specify concrete just on the traditional factors of strength, slump and so on.
Steel production in Aotearoa is a good example of a circular economy – 85% of our building and construction steel waste is recycled.
Rick Osborne, Chief Executive of Metals New Zealand, points to improvements under way in the domestic steel industry:
▶ New Zealand Steel worked with its supplier of co-generated electricity, Alinta Energy, to lift on-site electricity generation at Glenbrook by almost 10% – which is 5% of total electricity requirements.
▶ Fletcher Steel has received funding to decarbonise its coil coating process. This will reduce fossil fuel consumption by up to 89% and eCO2 emissions by 67%.
▶ Steel & Tube’s greenhouse gas emissions are down 9% year on year through a range of initiatives.
Even more exciting is the prospect being explored at Victoria University of Wellington for replacing coal with hydrogen as the fuel behind steelmaking. The hydrogen can be produced from water using renewable energy such as wind power.
Victoria’s Robinson Research Institute has demonstrated the process using hydrogen and New Zealand iron sand at temperatures up to 1,000°C to produce very high-purity iron. The key benefit is that this process releases water vapour, not carbon dioxide.
The team has received $6.5 million from MBIE’s Endeavour Fund for research into the scale-up of hydrogen steelmaking in New Zealand. (In Sweden, a venture formed by steel, car and mining companies and supported by two universities, the Swedish Government and the European Union has already produced its first fossil-free steel. Fossil-free steel is earmarked for building Volvo cars.)
Timber, including engineered timber, is a very carbon-friendly building material thanks to trees absorbing carbon dioxide from the atmosphere as they grow. Where timber is used on a building, it typically helps reduce its carbon footprint.
LVL (laminated veneer lumber) is the key component in Te Whare Nui o Tuteata, the new Rotorua headquarters and innovation hub for Crown research institute Scion. The building has won multiple national and international awards for its design. The architects have said that the building achieved embodied carbon zero when it was completed.
Timber buildings have traditionally been limited in size and come with particular fire risks, but both of those limits are changing, with engineered timber behind some big advances. The weight of timber is only one-fifth that of concrete, but engineered timber has similar compressive strength as concrete.
Research at Canterbury University, funded by the Earthquake Commission, has found that multistorey walls constructed from cross-laminated timber (CLT) can be strong and resilient in earthquakes. The research team designed highcapacity connections for the walls. They found that steel dowels in the connections bent to absorb energy and prevent the walls from being significantly damaged or collapsing. After an earthquake, the dowels could just be replaced and building occupants could quickly return.
Innovations are continuing. Professors and students at the University of Auckland and AUT developed the Tectonus earthquake protection device. This New Zealand initiative is being picked up around the world.
In Australia, Building 4.0 CRC, an industry-led research initiative co-funded by the Australian Government, is looking into a low-carbon suspended floor system capable of spanning 8m or more. The idea is to enable large-scale application in multi-storey mass timber projects.
There are a growing number of resources available to help engineers, architects and designers in their material selection, including environmental product declarations (EPDs) published by manufacturers about their products and BRANZ carbon tools.
EPDs are independently verified public statements of the environmental performance of materials or products. They allow comparison of products based on their environmental impacts.
Not all manufacturers publish EPDs, but the number is growing rapidly. In New Zealand, this is partly because government agencies such as Kāinga Ora now have specific requirements around greenhouse gas emissions and environmental impacts in their work with construction companies.
BRANZ has a series of online carbon tools that can help. The suite of tools available on the BRANZ website is made up of three carbon foot-printing tools and two life cycle assessment tools:
▶ CO2NSTRUCT is a database of embodied carbon and energy figures for building materials and products.
▶ CO2RE covers greenhouse gas emissions for residential wall, floor and roof constructions (expressed as per m² of the building element). It allows evaluation based on construction R-value and whole-of-life embodied carbon.
▶ CO2MPARE is a database of calculated greenhouse gas emissions for a set of reference residential and office buildings. It also contains carbon budgets for those buildings. It can be used for benchmarking and target setting.
▶ LCAQuick calculates environmental impacts of any building designs, with a focus on residential and office typologies.
▶ LCAPlay is a concept-level exploratory LCA tool for commercial buildings.
by David Hindley Freelance Technical WriterThis article was first published in BRANZ Build magazine issue 189, April 2022. www.buildmagazine.co.nz
We’ve been using bituminous black building paper as a roof underlay in New Zealand for over 100 years. Now there’s a recyclable and affordable alternative. All new Covertek 215 is a versatile, synthetic roof underlay that has superior performance... and is easy on your pocket!
When it comes to roof underlay, the choice is black AND white!
Absolutely. The materials are available in New Zealand right now. And while the windows will initially be used mainly in commercial buildings, the technology will inevitably evolve and spread to residential construction.
High-rise buildings typically have limited solar panel roof space but a much greater exterior wall area for solar generation. In the past, building owners have chosen to fix traditional solar panels to the exterior walls, but the visual effect is less than desirable.
“This BIPV (Built In Photovoltaic) technology means we can provide high-performance engineered panels with integrated solar generation in an aesthetic way.
Photovoltaic (PV) glass has been around for more than a decade, but technological advances have improved its efficiency, and like traditional solar panels, the cost has become more affordable.
PV glass windows look identical to ordinary windows and work the same way as solar panels to convert solar energy into electricity. The difference is that the solar cells are microscopic and virtually invisible, so you can still enjoy the view while you power your home.
Kent Nixon is general manager at Thermosash, a company that is embracing Building Integrated Photovoltaics (BIPV), where solar cells are integrated on the façade of the building rather than installed on the roof, as in a conventional residential or industrial installation.
“If you blended a conventional solar panel system into a glass window, you get that signature octagonal appearance of the solar photovoltaic cells, which takes up a huge amount of your viewing zone and is aesthetically displeasing.
“With this newer technology, you can hardly see the solar cells. They’re tiny little ceramic dots. The generation is lower than conventional dedicated solar panels, but as part of an overall building solar energy plan, and with constant advancements in the technology and clarity of panel, they can make a significant contribution.”
“In Europe, where they use these panels, the power they're getting in a high-rise building is way more than could be achieved with a roof-based system. And visually, you couldn't tell the difference between standard cladding and voltaic cladding.
“The other crucial aspect is that they don’t need to face the sun. As long as there is light, they will generate power.”
One of the biggest criticisms of the electricity system in New Zealand, and the biggest hurdle to increasing uptake of solar power, is the low rate electricity generators pay for power fed back into the national grid.
“New Zealand power generators have a low buyback of 7-17¢/kWh, depending on supplier and contract, for power fed back into the grid, whereas in many other countries, they pay a lot more, which supports the uptake and reduces the payback period,” says Nixon.
“If the power companies could offer a buy-back closer to what they charge people, that would make a huge difference to the uptake of solar systems.
“If the government is serious about their 2050 net zero carbon target, they could support an initiative similar to the EV rebate system. Investing in solar energy is potentially just as beneficial to NZ as subsidising electric vehicles, considering how much demand our country will require for the greater future demand imposed on our nation's power grid.”
Latest developments in battery technology could lead to a new breed of EV utes that will rival the performance and towing capacity of New Zealand’s marketleading utes, such as the Ford Ranger and Toyota Hilux.
Chinese company CATL (Contemporary Amperex Technology) has just released details about a new condensed matter battery that can potentially double the range of a vehicle with a conventional lithium-ion battery.
For example, the LDV EV T60 electric ute available now in New Zealand has a range of 325 kilometres. But when towing a trailer with the maximum load of 1 tonne (braked), that range goes down to around 162 kilometres. Not ideal.
CATL’s condensed matter battery has other significant advantages over current EV batteries. It uses electrodes made from a gel-like material rather than solid metal, which means fewer binding agents are needed to assemble the battery, reducing weight dramatically.
To put this in perspective, a Tesla Model 3 Long Range has a 288 kg, 75 kWh battery pack, giving it a range of 579 kilometres. If the Tesla were powered by an equivalent weight CATL condensed matter battery, it would have a capacity of 144 kWh giving it a range of 1112 kilometres.
The weight issue is one of the primary reasons why the development of electric utes has lagged behind that of passenger vehicles.
Utes are work vehicles and are often used to carry large loads or tow heavily laden trailers. This extra weight substantially reduces the range of an EV vehicle, in some cases, by as much as 50%.
The battery is also claimed to be more environmentally friendly, using less material per kWh and taking less energy to assemble.
CATL has released only limited details about the new battery, and it’s unknown when mass production will commence. But when it does, expect significant changes in the EV space.
CATL are currently suppliers and partners to Tesla, Ford, Lotus, Volvo, Polestar and Zeekr, and they may form alliances with other mainstream manufacturers in the future.
Rangiora ITM 03 313 4862
☐ Timaru ITM 03 688 8074
☐ Waimate ITM 03 689 7427
☐ Dunedin ITM 03 262 1008
☐ E H Ball ITM Invercargill 03 218 3787
☐ Fraser Hardware ITM Balclutha 03 418 0170
☐ Gore ITM 03 208 0649
☐ Mosgiel ITM 03 489 8885
☐ Southbuild ITM Winton 03 236 6055
☐ Southern Lakes ITM Alexandra 03 427 2221
☐ Southern Lakes ITM Cromwell 03 445 0081
☐ Southern Lakes ITM Queenstown 03 451 1567
☐ Southern Lakes ITM Wanaka 03 443 2545
GRAND PRIZE
(For you plus three mates )
This includes:
• Return flights and luxury accommodation
• 2-day hospitality experience, hosted in ITM’s exclusive pitlane villa
• Supercars Course Car ride, grid walk, helicopter ride and more
JUST
$10K