Supercars are all go at SuperTaupō
Codewords: Energy based hazard recognition
Do I claim on public liability or contract works insurance?
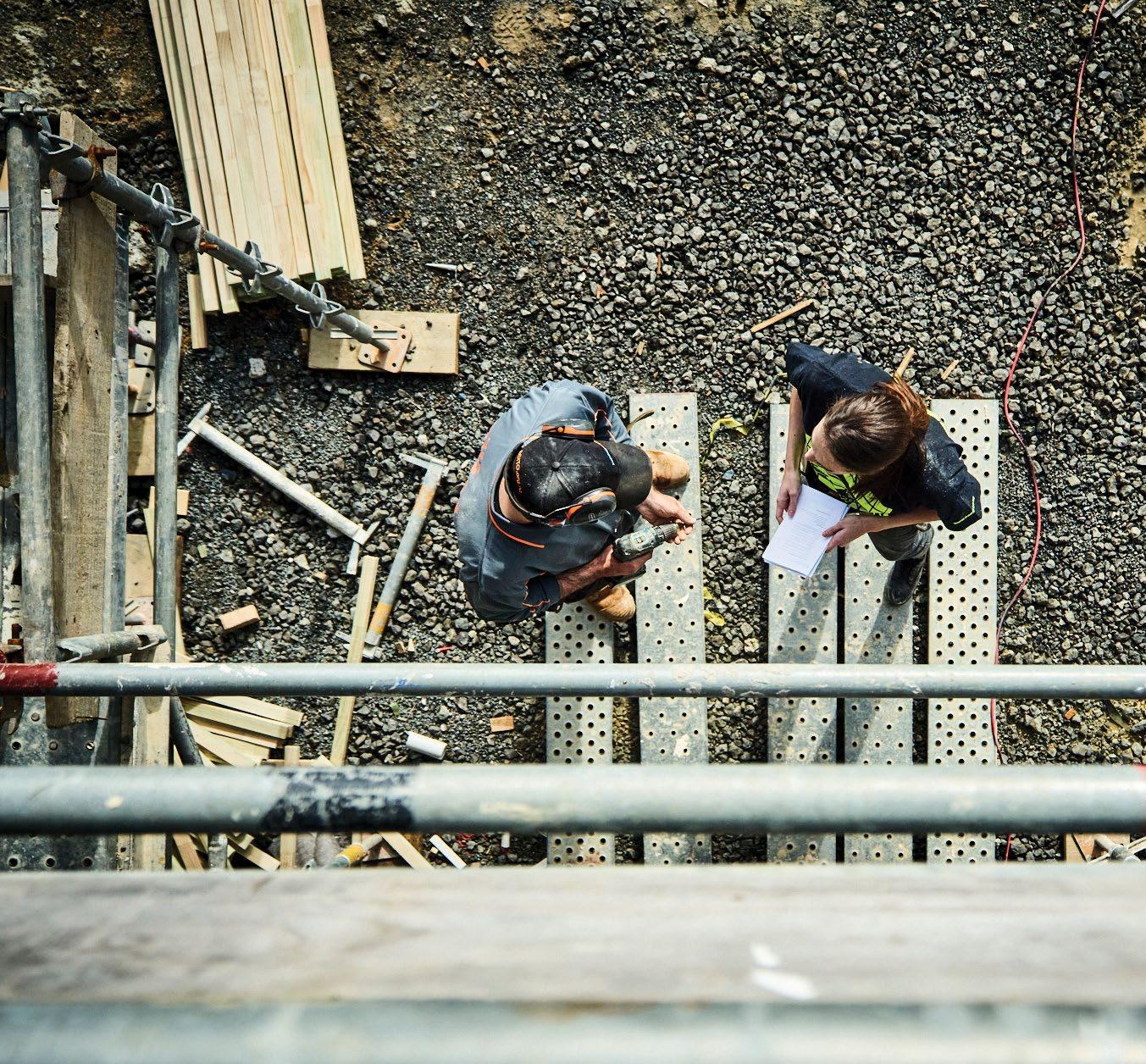
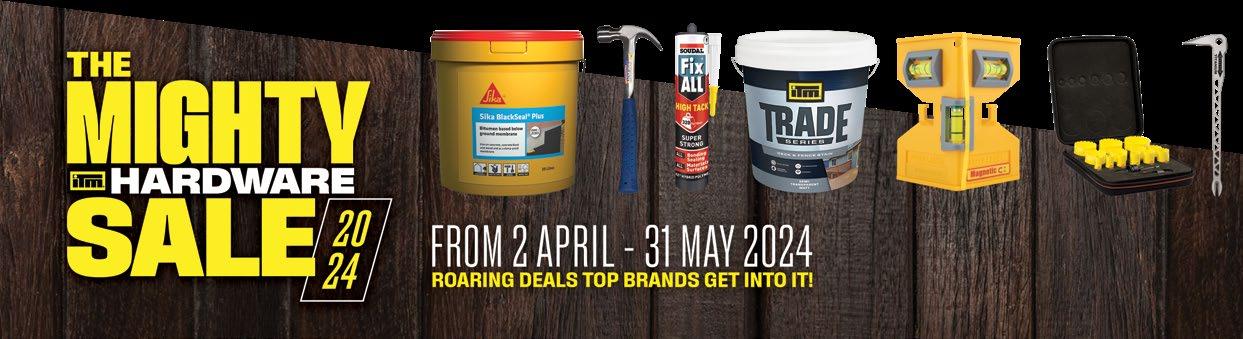
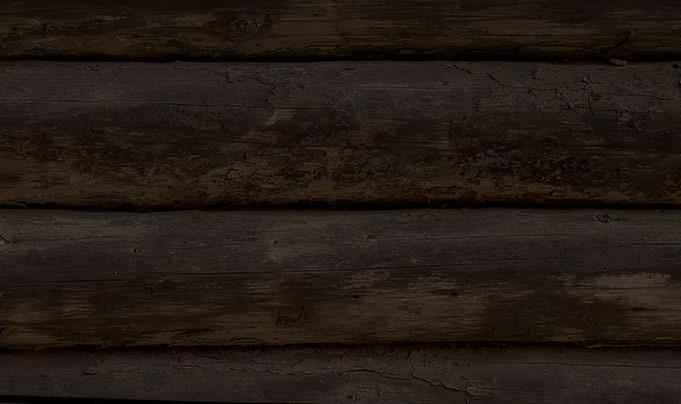
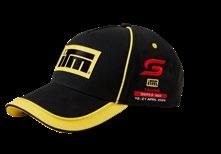
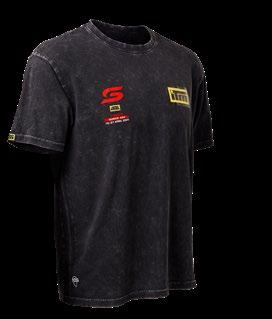
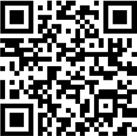
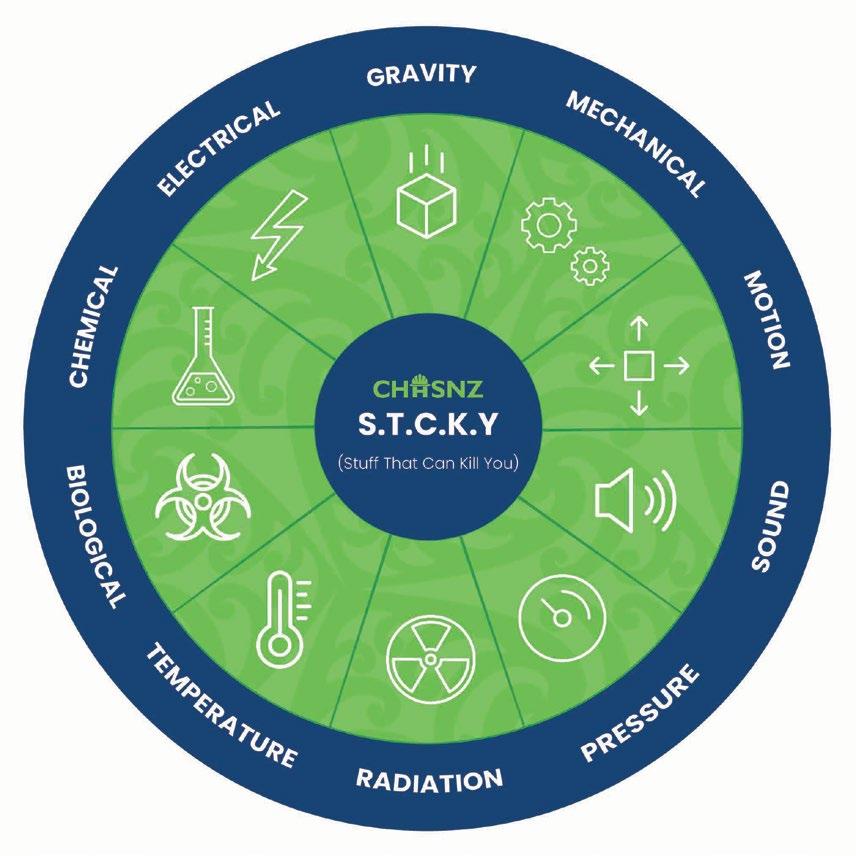
Supercars are all go at SuperTaupō
Do I claim on public liability or contract works insurance?
What if I said to you that people working on building sites up and down New Zealand can only identify up to 45% of the hazards they are working amongst?
How about if I said that 35% of hazards are missed because of limitations in the way our brains process what we see, and 20% are missed because work is often unpredictable?
A recent US study measured hazard recognition in data collected from 4,800 worker-hours of field observations from 12 different construction trades, and that’s exactly what they found.
Hazard recognition is vital for nearly every safety activity, including pre-task safety briefings, safety observations, risk assessments, and design reviews.
Most safety practices are built on the assumption that workers can see hazards that are there and can anticipate those that may arise from work.
In fact, inadequate hazard recognition appears as a contributory factor in around 50% of workplace incidents. Because they appear so obvious after an event, people have often been wrongly blamed for being complacent or negligent.
Let’s start with an example. There are two scenarios below:
Scenario A
An unprotected exposure to a fall hazard over 5m:
An individual is placed at the edge and is asked to look down at the ground below.
Scenario B
An unprotected exposure to a 3m deep, clear-cut excavation wall of sandy-clayey soil:
An individual walks to the bottom of the excavation and is asked to reach out and touch the soil wall opposite the roller.
In scenario A, nearly anyone would identify that they are in a dangerous situation, and many would experience fear, anxiety, elevated heart rate, weakness in the legs, or even feel sick.
In scenario B, although the scenario is potentially fatal if the soil wall were to collapse, an individual may fail to understand the seriousness of the hazard. Even well-trained workers are unlikely to experience the same intense emotional and physiological response as in Scenario A.
So why do we tend to have a physiological and emotional response to one but not the other?
The answer lies with our brain and how it processes information. When we look at hazards that involve energy, such as gravity or motion, the instinctive part of our brain fires up. That’s because human brains have evolved shortcuts over very long periods to quickly recognise things in our environment that are potentially dangerous to us. That same part of our brain is also responsible for our ‘fight or flight response’, which is why when we instinctively see such hazards, we tend to feel something.
Alternatively, hazards that are most commonly missed (e.g. mechanical, pressure, chemical, biological) are processed in more advanced locations of the brain and require much greater effort to process the information. What can we do about it?
As every injury is the result of the unwanted release of, and contact with, one or more energy sources, we can use energy categories to prompt our thinking. To do this, we use the energy wheel (see Fig.1).
Each of the ten icons in the energy wheel represents a different type of energy. Although not strictly scientific, the icons represent the most common ways that energy is present at work.
Gravity: Force caused by the attraction of all masses to the mass of the earth
Motion: Change in position of objects or substances
Mechanical: Rotation, vibration, tension, or compression
Uneven work surface
Work at height
Unsecure materials
Traffic
Mobile equipment
Projectiles
Augers
Cables
Grinder wheels
Electrical: The presence of an electrical charge or current Wires
Pressure: Liquid or gas compressed or under a vacuum
Sound: Audible vibrations caused from the contact of two or more objects
Radiation: Elements that emit ions or atomic particles
Biological: Living organisms that pose health or safety risks
Chemical: Reactive elements in the environment
Power lines
Power tools
Vehicle tyres
Piping systems
Hydraulic lines
Heavy machinery
Power tools
Nail guns
Welding
Sun exposure
X-ray testing
Bites and stings from animals
People (aggression)
Toilets
Cleaning products
Engine exhaust
Silica dust
Temperature: Differences in thermal energy with the human body Friction Engines
Steam
You can use this simple 2-step process:
1. To start, put the energy wheel away and recognise hazards using your instincts.
2. Then, go around the energy wheel to see if you missed any hazards.
Points to note:
▶ The energy wheel helps us to do what we already do better.
▶ Do not identify hazards then try to classify them.
▶ The name of an energy source (e.g. gravity) is not a hazard.
▶ The energy wheel adds structure and strategy to pre-job safety briefs.
▶ The energy wheel can help provide clearer understanding of hazards and when change is a factor.
▶ The energy wheel can support meaningful conversations and the sharing of knowledge experienced people gain over time, that isn’t normally written down.
Construction Health and Safety New Zealand (CHASNZ) is an industry-led charitable trust working to improve the lives of construction workers by raising the standard of health, safety, and wellbeing in construction. Energy wheel resources can be found on the CHASNZ website here: chasnz.org/energy-wheel. The source material for this article has been developed by our friends at the Construction Safety Research Alliance, Colorado USA csra.colorado.edu/knowledge-center
1. Which energy source does sun exposure fit into?
a) Mechanical
b) Chemical
c) Radiation
d) Gravity
2. What’s the maximum percentage of hazards a person can be reasonably expected to identify on a building site using their instincts alone?
a) 90%
b) 40%
c) 55%
d) 45%
3. 35% of hazards are missed because of cognitive 'blind spots'. 20% of hazards are missed because:
a) Our fight or flight response is activated.
b) People can be negligent or complacent.
c) They are not reasonably identifiable before work starts.
d) These are processed in more advanced locations of the brain and require much greater effort to process the information.
“We do a lot of community support, and it came back to us tenfold.”
While the disastrous fire at Takaka ITM in January was a shocking blow to the local community, the aftermath was even more unbelievable. In an overwhelming show of support, the whole town gathered around, pitched in, and got the business up and running again in just five days.
"They were awesome, we were totally blown away," says store manager Luke Brown. "It was just unreal the offers of help we had. One day, there were over 30 people on site cleaning up and moving stuff.
"We had people from the Golden Bay Football Club, offers of help from our competitors. I especially remember five-year-old twins from our kids' holiday building programme bringing us chocolate brownies. We do a lot of community support, and it has come back to us tenfold."
The fire in the early hours of the morning on Jan 11th totally gutted the 700m2 store. Fortunately, the Takaka ITM site has a large separate joinery shop that wasn't affected, thanks to "the fantastic effort of the Takaka Volunteer Fire Brigade.
"Three of our staff are members of the brigade, so they were familiar with the site layout and were able to coordinate things to protect the joinery shop, thank goodness.
"Over the next few days, everyone pitched in to clear the space, and we created a make-shift pop-up store. With help from ITM stores in Motueka and Nelson, we were able to get our trucks running between all three stores so we could deliver our customers' orders."
Luke says the rebuild is expected to be completed in 12-18 months, but in the meantime, it's business as usual.
"It was rough for the first week, but everything's going smoothly now, and we're back up to about 90% of what we were. By coordinating with the Nelson and Motueka stores, we can provide pretty much the full ITM services we had before the fire.
"It's incredible how a small community like ours can come together when things get tough. The support we got was staggering, and all our staff are incredibly grateful."
"The outpouring of support received from within our Co-operative underscores the power of solidarity in times of adversity. Together, we're stronger, ready to rebuild and move forward", remarked Sara Johnson, ITM CEO.
Thom Sullivan, General Manager of Procurement, also praised the support Takaka ITM received from suppliers, "At ITM, suppliers are part of our community, and the support provided to the Takaka team has been truly appreciated. Many have gone above and beyond to expedite a return to trading.”
A perfect mix of fine detailing and durability
These are some of the most frequently asked health and safety questions that get submitted to Site Safe's safety advisor via the Ask an Advisor online form.
Q: Can you please provide some clarity on what work WorkSafe must be notified about?
A: WorkSafe requires 24 hours' notice of any work that is particularly hazardous.
Below are some hazardous activities they require notification of:
▶ Construction work with a risk of falling 5 metres or more (exclusions apply).
▶ Erecting or dismantling scaffolding with a risk of falling 5 metres or more.
▶ Logging or tree felling undertaken for commercial purposes.
▶ Use of a lifting appliance where the appliance must lift a mass of 500 kilograms or more at a vertical distance of 5 metres or more (exclusions apply).
▶ Work in any drive, excavation, or heading in which any person is required to work with a ground cover overhead.
▶ Work in any excavation in which any face has a vertical height of more than 5 metres and an average slope steeper than a ratio of 1 horizontal to 2 verticals.
▶ Work in any pit, shaft, trench, or other excavation in which any person is required to work in a space more than 1.5 metres deep and having a depth greater than the horizontal width at the top.
▶ Work involving the use or storage of explosives at the worksite.
▶ Work in which a person breathes compressed air or a respiratory medium other than air (diving).
▶ Work in which a person breathes compressed air or a respiratory medium other than air (not diving).
Q: What are the requirements for providing PPE and payment for the PPE?
A: If you're an employer, it's up to you to ensure your workers have the proper personal protective equipment (PPE) for the job and to provide it for them if they don't.
If the PCBU wishes to change the PPE required onsite, the PCBU is responsible for this themselves. The exception is when workers "genuinely and voluntarily choose to provide their own".
Q: Are there any restrictions on wearing slip-on type safety boots on a construction site?
A: Any restrictions on wearing slip-on type footwear are at the discretion of the site or employer.
There is no industry or WorkSafe position on this matter. Slip-on safety footwear is considered OK for many construction activities; however, some PCBUs will not accept them for jobs requiring ankle support.
Q: Can I wear a cap or other hat under my Hard Hat?
A: Wearing a cap or other hat under your Hard Hat is usually non-compliant. Winter liners (beanies/ skullcaps) may be worn but must be close-fitting to ensure they do not adversely affect the proper fit or function of the hard hat. If in doubt, consult your safety helmet supplier.
Safety helmets require the harness to be in direct contact with the skull to be most effective; usually, a baseball cap will impede performance.
Sustainability seems to be the "it" word of the century, but what does it really mean for kiwi builders? This is the first in a series of stories in Building Business to highlight the key things you can do to build a more positive future for your business.
So let's start with a simple definition: Sustainability means making choices and adopting practices that balance environmental, social, and economic considerations to ensure a healthier life for people and the environment now and for generations to come.
For builders, sustainability means choosing environmentally friendly materials, building systems that minimise waste, and adopting design principles that reduce the carbon footprint of a building and facilitate the most efficient use of natural resources, energy and water.
Sustainability also encompasses social responsibility, including how you treat your employees, suppliers and sub-contractors.
All these factors are included in the United Nations Sustainable Development Goals, which New Zealand has embraced as a roadmap for building a sustainable future in this country.
Developed by the UN in 2015, the Sustainable Development Goals are the blueprint to achieve a better and more sustainable future, with longterm benefits for people, the economy and the environment. They address critical global challenges of poverty, inequality, climate change and environmental degradation.
The UN monitors these goals to gauge progress and action across member countries. In New Zealand, the goals have been incorporated into much of the legislation relating to building and infrastructure development.
A good example is the Green Star and Homestar rating systems, whereby many government buildings, residential developments and local authority buildings must have verifiable environmental, energy and sustainability ratings.
In many cases, builders who work on these projects must only use materials and labour where a chain of custody can be verified. This shows that the materials have been produced, manufactured and distributed sustainably, and everyone employed in the supply chain is treated fairly with no discrimination.
There is a vast amount of information available about sustainability in building, and it isn't easy to distil it down to practical steps builders can take to embrace the sustainable drive.
Of the 17 UN Sustainable Development Goals, five are most pertinent to builders and building companies in New Zealand. In future articles, we will focus on each and provide a breakdown of the key things relevant to you.
Supercars racing is about to kick off at the motorsport capital of the country, with a clutch of brilliant kiwi drivers determined to extend the legacy that has made New Zealand drivers a dominant force on the world’s most demanding racetracks.
So how good is the ITM Taupō Super400 going to be? At the end of February, all five kiwi drivers were in Taupō to scout out the track and dropped in on the team at Taupo ITM to catch up on some local knowledge. Andre Heimgartner of Brad Jones Racing and Taupo ITM manager Andrew Milne share some of their thoughts about what to expect.
Kiwi drivers have won five of the last six Supercars championships: Scott McLaughlin in 2018, 2019, 2020 and Shane van Gisbergen in 2021 and 2022. Now that both drivers have moved to the USA, the remaining kiwis are amped up to continue the legacy.
Andre: “I think it gives us more opportunity to try and take over that role, do a bit better and fly the flag a bit higher. It's probably something that needs to be studied. Like why do we have so many successful New Zealand motorsport people in the world?
“Motorsport is very large internationally and we’ve managed to find our way to the top of many different categories. It’s something everyone asks us. Is there something in the water? What is it? And honestly, I don't actually know.”
How does Andre feel about Taupō as a venue?
“I think when people come to Taupō, they'll see the ITM Taupō Super400 as a true international event. And all of us drivers know that it's not just going to be about the racetrack, it's going to be about all the things that are around it.”
Andrew: “I wasn’t a petrol head before, but I’m fast becoming one. We all are. The atmosphere at our store is electric with anticipation and it was fantastic to have the kiwi drivers here for a barbecue and meet some of the locals.
“A lot of the guys brought their kids down and the drivers were only too happy to sign some autographs. They're not aloof in any way, just young kiwi lads that like to have a chat just like any of us. They were very engaging and super excited about racing at home.
“We've got a history of punching above our weight, so I think the kiwi boys especially on home soil will be a force to be reckoned with.
“This is a huge event for Taupō. It’s a great showcase for the whole region. The lead-up has been thrilling and I think the after effects will have a positive impact well beyond the event. As for the racing itself, I think it's the kind of event that will bring everybody to a standstill. It’s going to bring the town to a stop.”
The 2024 Repco Supercars Championship returns to New Zealand on 19th-21st of April. The ITM Taupō Super400 will consist of two 200km races, one each on Saturday and Sunday.
Track distance: 3.2km
Lap record: 1.14.679 by Neel Jani, 2008 A1GP
Turns: 14
Remember when you started out and someone gave you a chance?
You’ve come a long way to become a great builder, picking up new skills on each project.
To ensure we continue to lead the industry with quality standards the next generation needs your kind of experience. The NZCB Apprentice Network is a programme designed to support you, your business and your apprentice to an unrivaled level.
nzcb.nz/apprenticeships
DumaWall is a new lightweight and easy to install impervious wall tile/panel.
Within the tiling industry, technology is advancing at almost the same rate the trends that drive it. For several years, larger format tiles have been a dominant style, so technological innovation has responded in kind.
It's not just the increase in average size that has prompted technological advances. Market demand for minimised grout lines, easier installation, and more efficient waterproofing – these are the factors that drive the industry forward.
Rigid Core Board (RCB) technology has the potential to be a significant disruptor in this regard. A patented solution from PSP, the finished product is a standout when paired with the company's DumaWall waterproof tiles.
The composition of DumaWall includes a protective PU top layer, decorative realistic printed multicoloured film, a high-quality stability layer and RCB technology. This also results in a very strong adhesion of the decorative layer to the board, preventing it from peeling and making it the ideal substrate for wet areas in residential and commercial applications.
DumaWall comes in two formats: DumaWall+ (375mm x 650mm) and DumaWall XL (2600mm x 900mm) – the smaller size has a visible grout line, while the larger size has a seamless join. Both use a tongue and groove system, allowing easy installation.
With traditional tiles, grout lines are unavoidable. When installing these tiles, getting the combination of screed and bed-level consistency requires expertise. In contrast, DumaWall is adhered using MS Polymer High Tack Adhesive which is simply applied to the wall or tile.
In contrast clay-based tiles require specialised blades and tools, whereas DumaWall+ can be easily cut using conventional cutting tools such as a hand saw or a jigsaw.
DumaWall+ is also lighter (5kgs per m2) than claybased tiles, making handling more efficient and an ideal retro-fit solution over most existing surfaces.
The tongue and groove system makes installing it quick and easy as the DumaWall tiles and panels interlock together.
For DumaWall+ tiles, it instantly and visually creates a grout line without the time and hassle. For DumaWall XL panels, it makes a virtually seamless join without the need for H jointers. The absence of the H jointers provides additional cost savings as they're not required with DumaWall XL panels and can provide a more seamless finish due to its tongue and groove installation method.
DumaWall can be simply maintained by using a sponge with warm, soapy water to remove dirt or grime. We do not recommend using abrasive substances. Also avoid chloride-based products and solvent based cleaners.
Learn more about PSP and DumaWall by visiting dumawall.co.nz
All new wet wall areas such as shower boxes, must be waterproofed over an approved wet wall substrate prior to DumaWall being installed. For more info visit www.building.govt.nz – Code of practice for internal wet area membrane systems.
DumaWall can be retrofitted over existing approved shower boxes such as tiles and branded aqua linings.
As a business owner or manager, you need to be aware that the minimum wage rates increased on 1st April 2024.
The details of the increase are:
▶ Adult minimum wage went up from $22.70 to $23.15 per hour.
▶ Starting-out and training minimum wage went up from $18.16 to $18.52 per hour.
▶ All rates are before tax and any lawful deductions, for example, PAYE tax, student loan repayment, child support.
If you have not yet talked to your accountant, payroll provider or your finance/HR teams now is the time. It is also an opportunity to check your employment records, processes and systems are current.
1. Advise the team
If you have employees on the minimum wage, let them know about the increase they will be getting. You should send them a letter or email (variation of employment contract) advising them of the new wage.
2. Check your payroll systems and processes
Make sure your payroll provider, accountant, lawyer, HR, or finance people are ready to implement the change.
If your system is manual or computer-based, you should check and confirm the settings will be adjusted for the new rates.
If any of your employees are on starting-out or training wages, now is a good time to check when they will be eligible to move onto the adult rate.
If any employment agreements (contracts) are not current or you did not give one to your employees, now is an ideal time to discuss with them in good faith.
Update the contract with any terms and conditions that were agreed to by both parties before the contracts were last reviewed. Make sure they include all the mandatory clauses a contract should have by law. Another useful tool is the employment agreement builder if your employees do not have one.
Scan to view the Employment Agreement Builder - on the business.govt.nz website
Scan to view the things an employment agreement must contain - on the employment.govt.nz website
3. Employee pay relativity
You may also wish to consider potential impacts on your business due to internal wage relativity and external benchmarking. For example, how employees are paid compared to each other, and how your pay rates compare to others in your industry or sector. Employees on higher wages may want to negotiate a pay increase to keep the relative difference.
4. Update your business budget
You should add any expected increased costs to your short and medium-term budget forecasts. This will help you plan for and manage the effect of higher wage and holiday pay liabilities.
5. Upskill on minimum wage obligations
Now is also an ideal time to ensure you know the details around the minimum wage, including that:
▶ it applies to all hours worked, unless both parties agree to a higher rate in the employment agreement
▶ it applies to employees paid with a salary or piece rates or commission.
Note the minimum wage does not apply in some situations including:
▶ employees under 16 years of age
▶ where a Labour Inspector has issued a minimum wage exemption permit to an employee who has a disability that limits them carrying out their work.
This information comes from www.employment.govt.nz
WORK
TRAIN
ALREADY
GROW
ARCHITECTURAL
FRAME
BRICK
EXTERIOR
Employers can use 90-day trial periods when hiring new employees. Trial periods must be agreed between the employer and employee in a written employment agreement prior to the employee starting work.
Employers may employ a new employee on a trial period of up to the first 90 calendar days of their employment.
An employee can’t be on a trial period if they’ve worked for that employer before.
Prior to Saturday 23 December 2023 this has only applied to employers with 19 or fewer employees. If employers are hiring people on certain work visas, they will also need to consider immigration requirements relating to the use of trial periods.
▶ must be agreed to in the employment agreement before the employee starts work, or the trial period is invalid
▶ must have a valid notice period in the employment contract
▶ can be used in any industry and for any job
▶ must be agreed by the employer and employee in good faith – an employee can’t be forced into being employed on a trial period
▶ means that the employee can’t bring a personal grievance for unjustified dismissal or other legal proceeding about their dismissal (as long as the employer has given the right amount of notice to the employee)
▶ must be in the employment agreement and must state that:
• from the very start of their employment, the employee will be on a trial for a set period which isn’t more than 90 days (but can be less). The exact time period must be stated, for example, it could be 30 days, or 90 days, or another stated time period; and
• during the trial, the employer can dismiss the employee, and
• the employee can’t bring a personal grievance or other legal proceedings about their dismissal.
If an employee is a union member employed on a collective employment agreement, they can’t have a trial period (in their individual terms and conditions) inconsistent with the collective employment agreement. For example, if the collective employment agreement states that an employee can’t be employed on a trial period, then they can’t have a trial period in their individual terms.
Jennifer’s trial period is invalid because she started work before signing the agreement
Jennifer’s boss, Omesh, tells her that she has the job on Monday, she starts work on Tuesday and she signs her employment agreement on Wednesday.
Jennifer’s employment agreement has a trial period for 60 days, but this is invalid because Jennifer didn’t sign the agreement before she started work.
Omesh can’t dismiss Jennifer under the trial provision and if he did, she could bring a personal grievance for unjustified dismissal.
If Omesh wanted a trial period for Jennifer, he should have made sure that she agreed to it, had a chance to get advice and raise any issues, and signed her employment agreement before she started work.
Employees on valid trial periods:
▶ have all minimum employment rights and responsibilities (for example, in relation to health and safety, minimum pay, annual holidays, public holidays, sick and bereavement leave and equal pay), except bringing a personal grievance for unjustified dismissal
▶ must be treated the same as other employees who aren’t on a trial period.
If the trial period isn’t going well and the employer decides to dismiss the employee, they must give notice to the employee that they will be dismissed.
If the employer doesn’t give the employee notice by the end of the trial period, then they are no longer on trial and their employment will continue.
The employer doesn’t have to give reasons for a dismissal during a trial period, or give the employee a chance to comment before the dismissal. But it is good practice to tell the employee why they are being dismissed.
This information comes from www.employment.govt.nz
bbi® has introduced a new version of our BlondeLine® Lite with a Falcata Core.
BlondeLine® is an economical wall lining ply that has an attractive face on both sides. It is great for lining your garage or industrial structure. bbi® BlondeLine® has been P21 Brace Tested by Scion Research New Zealand. It also comes in a prefinished version known as BlondeLine® Plus, this has three coats of a matt polyurethane on both sides.
Key features
- Plywood is hard wearing and takes knocks well
- P21 Brace tested
- Both sides are finished to the same standard
- Comes in both raw and a pre-finished version
- Economical Lining Ply
- Lightweight and Easy to Install
- No stopping or sanding required
For more details or to download the bbi® PlyBrace™ Technical Document, go to www.bbi.net.nz
BlondeLine® Lite Birch Falcata Core
2400 x 1200 x 9, & 12mm
BlondeLine® Plus Matt Coated Birch Poplar Core
2400 x 1200 x 9 & 12mm
2700 x 1200 x 9 & 12mm
Endless possibilities.
0800 224 759 / sales@bbi.net.nz www.bbi.net.nz
This article is the third in a series about the LBP Code of Ethics and what it means to you. So far, we have looked at the first three principles of the LBP code of ethics. Now, we will cover the final principle - Behave Professionally.
The code of ethics (COE) applies to all LBPs, regardless of whether they are an employer, a contractor, or working for wages. As an LBP carrying out building or alteration work, you risk having a complaint made against you if you do not behave professionally.
The Building Practitioners Board (the Board) noted in a recent complaint decision (CB26224) that the COE differentiates between LBPs who are in business and those who are employed. Employed LBPs are unlikely to be involved in certain affairs, for example, pricing work or running a business, and their obligation is limited to the instructions of their employer.
The following seven standards, which make up Principle 4, come down to the things most LBPs understand and adhere to, whether they are employed or used as the foundation in their own business.
1. Behave professionally
When carrying out or supervising building work, you must act professionally and treat the clients and your colleagues with respect.
2. Act in good faith during dispute resolution
If there is a dispute between you and your client, you should attempt to resolve it and be available to discuss it with them so that all parties can express their views and be heard. You must be respectful and act in a professional manner at all times during the process.
In the Board decision referred to above, the LBP was abusive and threatening towards the clients.
The clients were so intimidated that they increased security measures at their home and made a complaint to the police.
3. You must price work fairly and reasonably
You must not use inappropriate methods to win a contract, including accepting or paying bribes. Do not quote unrealistically low prices just to get the job and then add extras to make up costs once the work is underway.
If any issues arise during the work which will cause additional costs, you need to let the client know and get their agreement before those costs are incurred.
For example, you may find soft ground during foundation excavations that would need an Engineer to investigate. This would lead to additional costs, so you must let the client know so that they can make an informed decision.
4. Declare and manage actual or potential conflicts of interest appropriately
A conflict of interest exists when you, your whānau, or your company have a personal or financial connection that may adversely affect your professional judgement or actions.
This is not to say you cannot do the job, but it is important to declare it to an appropriate person, such as the client, and manage those conflicts appropriately.
For example, an LBP has bought materials from a company owned by his brother, knowing he will receive some perks further down the track. However, the quote he provided to his client said he would buy the materials from the company the client stipulated based on their ethical and sustainability standards. He does not tell the client he has done this. The LBP has left himself open to a complaint to the Board.
5. Maintain confidentiality of client details unless there is good reason for sharing information
If you become aware of a client’s confidential information, you must take all reasonable steps to keep that information confidential unless you are legally required or authorised to disclose it. This could include seeing a private document the client inadvertently left in plain view.
6. Acknowledge and respect the cultural norms and values of your clients and colleagues
Make sure you act in a way that is respectful of the cultures and values of your clients and workmates, and make an effort not to intentionally cause offence to others.
7. Conduct your business in a methodical and responsible manner
If you run your own business, make sure you maintain accurate accounts and records. Ensure the way you operate is honest, fair, and professional. Charging the client for an item a second time because your records are not up to date will not improve their confidence in your business practices.
The COE upholds the integrity of the licensing regime to protect the public and maintain their confidence in LBPs. The COE is not designed to catch people out. It is a plain language document that sets out the level of ethical behaviour expected of LBPs.
Further information on the COE is available on MBIE’s LBP website. This includes resources to support your understanding of the COE. The resources include a detailed guidance document, a poster (including in te reo Māori, Chinese (simplified), Hindi, and Samoan) and an online learning module, which can be claimed as a skills maintenance point once completed.
1. Is it ok to provide a low quote just to get the job, with the intention of adding on extras during the work to make up the costs?
a) Yes, I have no work and must keep my employees busy.
b) Only if I know the client can afford it.
c) No, this is dishonest conduct and may result in a complaint against you.
2. What is a conflict of interest?
a) A disagreement with your client.
b) It’s where a potential personal gain may affect your professional judgement or actions.
c) Wondering whether to go to work today or go fishing.
3. Is it ok to make fun of your workmate’s culture?
a) No, you must act in a way that is respectful of your workmates’ culture.
b) Yes, it’s only fun and we do it all the time.
c) It’s ok if your workmate is out of earshot.
“Never a problem, always a solution - HTL will change the way you experience timber supply”.
H-Lam Post Packs
Custom Sizes to Suit
HTL supply and manufacture any timber species, in any shape, profile & finish for all of your special order projects. Mouldings, handrail, skirting, flooring, panellingyou’ll find it here!
Frame & Truss Packs
CNC Pre-Machining
H3.1 Clear LOSP Onsite
Specialists in NZ-Grown Timbers
Vertical, Bevelback, Board & Batten, and Rusticated Profiles
Super Over-Length for Architectural and Commercial Specs
H3.1 Clear LOSP Onsite
CNC Pre-Machining
Factory Pre-Coating
Farm Sheds
Onsite Re-Lam for Commercial Sizes
Alternative Solutions
Standard, Custom and Made-to-Match
Factory Pre-Coating in Dryden WoodOil
The next generation portal bracing solution is here
Proudly designed and manufactured in New Zealand, this smart and sustainable alternative to heavy steel portals is set to revolutionise residential building construction. Constructed from three precision-engineered glulam timber elements (including the renowned PLX20 Beam), the PLX Portal has unparalleled load bearing capacity, making it ideal for expansive internal openings, garage portals and window portals.
• Up to 40% lighter than steel portals
• Simple on-site assembly using standard tools
• Fast installation – no extra equipment or staff
• Cut to length to suit
• Awesome spanning capability
• FSC certified timber options available
• Easy to specify with PS1 certificate
Unleash the power of the PLX Portal on your next building project.
Our team of experts are ready to assist.
03 526 7436 | info@prowoodnz.com
prolamnz.com
Building better together
A glulam timber bracing portal system from Prolam is set to revolutionise building construction, offering a strong, lightweight and more sustainable alternative to steel portals.
Designed by New Zealand-engineered structural timber specialists, Prolam, and manufactured at the company’s state-of-the-art production facility in Nelson, the PLX Portal System represents homegrown innovation at its best.
The beauty of the PLX Portal System lies in its builtin strength, bracing capacity, eco-credentials and design flexibility.
The PLX Portal is constructed from three glulam timber elements, including Prolam’s trademarked PLX20 Beam, precision engineered from layers of quality radiata pine reinforced with steel for increased load-bearing capacity.
The timber elements are made from timber sourced from renewable and sustainably managed New Zealand plantations using 14 times less energy than their steel equivalents.
The reinforced beam offers excellent spanning capability to deliver optimal design flexibility for architectural features ranging from large internal openings to garage and window portals or anywhere extra bracing is required.
A commitment to designing smart solutions simplifying construction has been front and centre in Prolam’s development of the PLX Portal System.
Answering the industry’s call for a cost-effective and time-saving timber bracing option that replaces the hassle of steel, the portal’s lightweight
construction and straightforward bracing system facilitates easy onsite assembly and installation.
Up to 40 per cent lighter than their steel equivalents, the timber lintel and legs can be cut to length onsite to suit a project’s specifications, assembled using standard tools, and installed and fixed without needing specialised skills, extra labour or equipment.
The PLX Portal System has been rigorously tested to New Zealand building standards.
Before its release to market, the PLX Portal System was independently tested by Scion to provide a structural bracing solution for buildings within the scope of NZS3604 and proven to resist wind and earthquake loads using the P21 BRANZ test methodology.
The Prolam Specifier online tool assists architects in designing structural timber elements to exceed the span and loaded dimension requirements of NZS3604 and generate a PS1 for council compliance.
The PLX Portal System is now available on the Prolam Specifier. Contact the Prolam team to learn more about this breakthrough glulam portal and to discuss your project requirements.
When deciding whether to claim on public liability insurance or contract works insurance, it’s essential to understand the differences between the two and consider the specific circumstances.
It's not uncommon for accidental damage to potentially be covered under both contract works and liability insurance. Generally, this comes up when a sub-contractor has caused damage to other parts of the work in progress.
When a plumber hasn't fitted the hot water cylinder correctly in a new build, and it leaks, a claim could be lodged under the contract works insurance, which would cover the repair costs. However, main contractors and homeowners are often reluctant to make claims on the contract works (or house) policy if someone else has clearly caused the damage. Instead, they would hold the plumber liable for the damage they've caused, which the plumber could claim under their liability insurance.
The generally accepted and preferred practice is for the claim to be made under the primary policy (the one insuring the building/contract works itself). This would pay to repair the damage and the insurer would then look to recover their costs (and the customer's excess) if they can identify someone responsible for the damage. In the case of contract works, subbies are generally also noted as insured parties on the policy, so the insurer would not be able to recover from them. But the subbie would be expected to cover the excess (and this is often written into the contract).
An increasing number of liability insurers now expressly exclude claims if a contract works insurance policy is in place that would cover the damage. As a subbie, if the contract works policy includes sub-contractors as insured parties (which most will), you're entitled to be covered by it, it's just that the main contractor usually holds the details of the policy and would lodge the claim.
In some cases, contract works insurance might not cover the damage, most commonly if it is for defective workmanship. Another example could be scratched glass, a common contract works exclusion. In that case, a liability claim could be made, but this can be complicated as issues of care, custody or control and who owned the damaged items come into play.
In a nutshell
If you cause accidental damage to works under construction, the policy to claim on is the contract works insurance, whether this is arranged by the main contractor or the homeowner.
Even as a subbie, you are entitled to make a claim under it. An increasing number of public liability policies won’t cover claims if there is contract works insurance in place that would do so. If a contract works claim fails, you could look to your liability cover, but whether cover is available will depend on the specific circumstances.
Builtin are New Zealand’s trade insurance experts. For more information and to request a quote visit builtin.co.nz or contact ben@builtin.co.nz or 0800 BUILTIN.