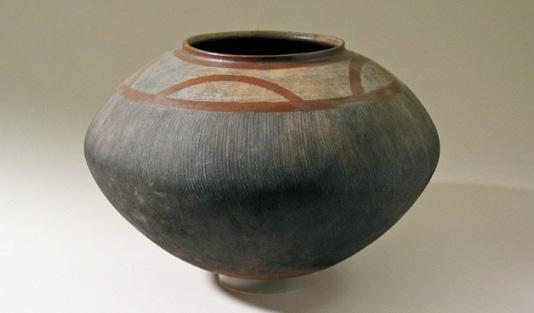
7 minute read
5.3 Ceramic and clay
5.3 CERAMICS AND CLAY
5.3.1 Introduction to ceramic materiality in Africa
Advertisement
Clay manufacture is an ancient craft, with the earliest records going back 6000 and 5000 years ago in Egypt and China, respectively.
Ceramic products, notably pottery, have several functions in Africa. They serve as data keepers, providing insight into cultural exchanges within societies. African ceramics are both art and craft, presenting both philosophical concepts and practical utility (Contemporary African Art, 2021).
In rural settlements, ceramic goods or vessels are used to transport water or store food and milk and cook, serve and drink beer. These products are designed solely for functional purposes. In addition to their functional utility, some ceramic goods have a vital spiritual role, which is a potent part of African ceremonial arts (Contemporary African Art, 2021).
It is worth noting how ceramic goods are made in Africa as the intention of the design of the craft centre is to focus on social sustainability and traditional ceramic processes have this quality. Making ceramic goods in Africa traditionally begins with the extraction and preparation of clay. Once retrieved, the contents are
Fig 79: Beer storage vessel Nkakusa, Tanzania from African pottery, 2021
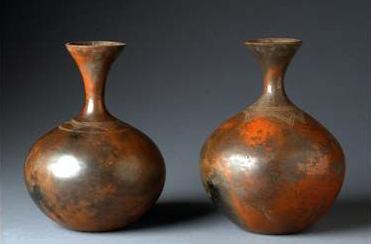
combined with water until they become pliable. To reduce shrinkage during the drying and fire processes, sand-like debris, pebbles or old ceramic goods, grass and dung are kneaded into the clay.
Ceramic goods are often wrapped around a flat base before being moulded or polished. Moulds were created in certain circumstances by re-purposing ancient pottery, wood and calabashes. After achieving the required shape, the objects were sun-dried before being wood fired at a low temperature for roughly five hours.
Firing would frequently take place over a pit or, subsequently, in brick kilns. Short, round brick walls with air openings at the bottom encircle a heavy layer of fuel on which the pots are placed. The kiln is then ignited from the bottom, with old, broken pottery stacked on top to keep the heat in (Contemporary African Art, 2021).
After the ceramic goods have been sun-dried, they can be decorated. The artisan frequently decides to add new shapes or carve the surface to accentuate detail and narrative.
Natural colours such as provided by chalk, leaves and
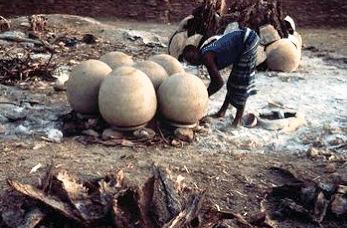
Fig 81: Pot firing in Burkina Faso from African pottery, 2021.
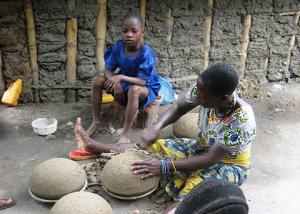
dung are employed to add an aesthetic layer. Animal fat, soot and a pebble were typically used to polish ceramic items, which were then refried to obtain a glossy finish.
Contemporary African ceramics have an elegant form and a fine finish that one does not often expect in a pot designed to be used. This is the point of modern ceramics because very few of these pots have any purpose apart from being decorative.
Nevertheless, one cannot separate their modernity from their past; their very survival is founded on centuries of production, innovation and trade perfection (Contemporary African Art, 2021).
To conclude, there is a personal attachment to crafts and the workings of ceramics, where one can learn and develop skills. There is a distinct unity between objects, people and landscapes where tactility comes in. This reinforces the proposed design idea of having users experience the crafting process as set out below.

Fig 83: Decorated global vessel, everted lip, Igbo from African pottery, 2021.
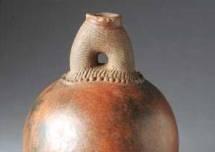
SEMI-INDUSTRIAL
SEMI-INDUSTRIAL
5.3.2 Ceramic Processes (wet)
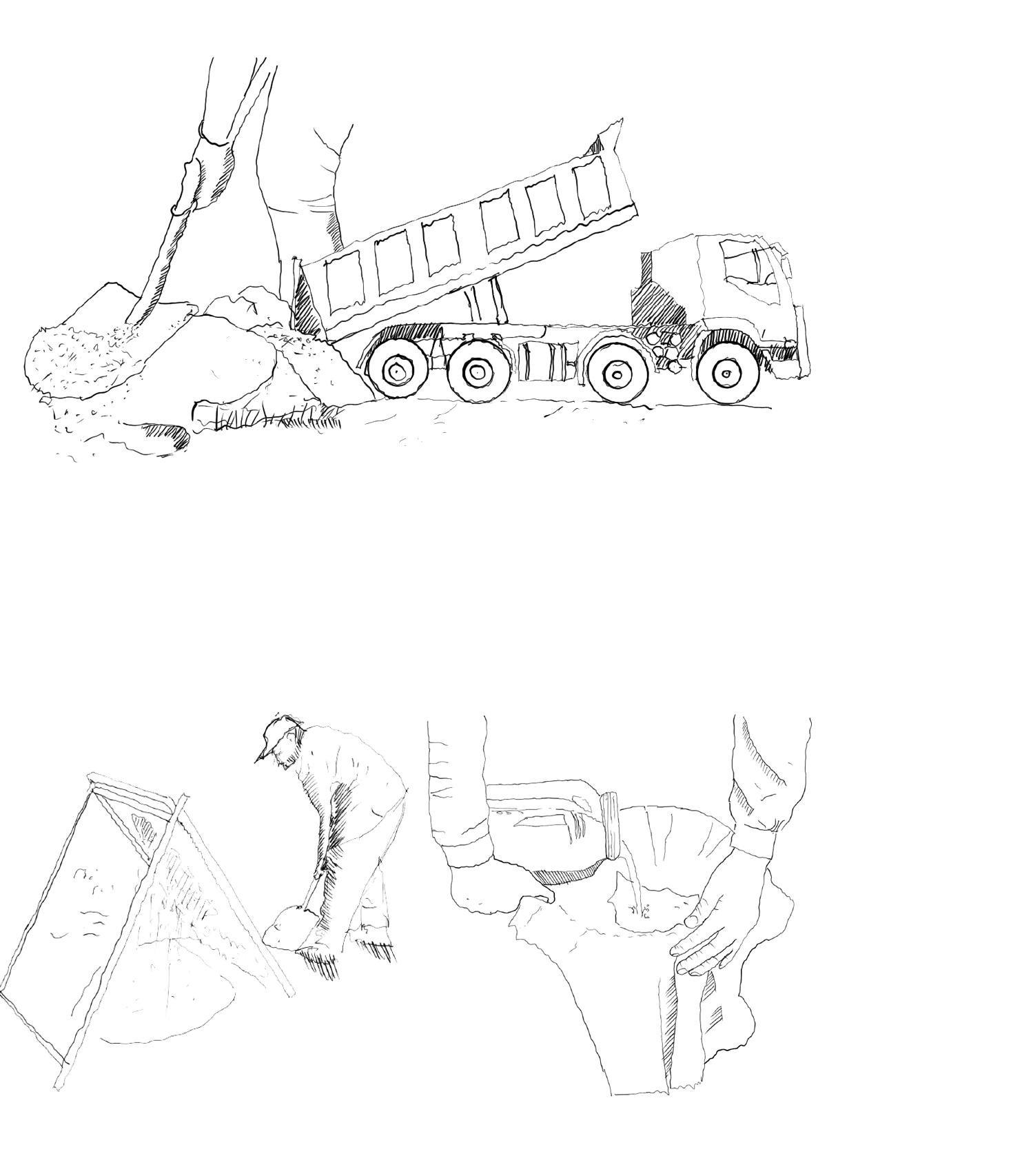
a) Extraction and collection The ceramic processes described below are accommodated in the design of the intervention, which focuses on the manufacturing of ceramics in the Berea Park community craft centre. The processes form part of the overall process flow, as indicated in Figure 93.
Several layers of components from which ceramics are made are present in generic sand taken from the earth. Primary coarse sand, silt and clay are just a few examples. The planned design includes a location where sand donations can be dropped off, such as those from building sites. The concept of repurposing sand is related to the themes of adaptive reuse and recycling. However, not all sand contains a high concentration of clay; therefore, any excess sand would be recycled into the environment or donated to other events.
b) Separation
Sand grains are separated from other organic materials such as leaves and twigs by sieving the sand particles. The remaining sand is placed in a container with a screen on top and stirred until the content is workable using the wet sieving process (see Fig. 86). The content is allowed to settle for a few hours to separate the sand particles. The fabric screen keeps the clay content inside while the rest of the material is removed. This method may be scaled up to manufacture a significant volume of clay (Fritzlan, 2021).
Fig 85: Sketch of shovel and sand delivery truck, (By author, 2021)
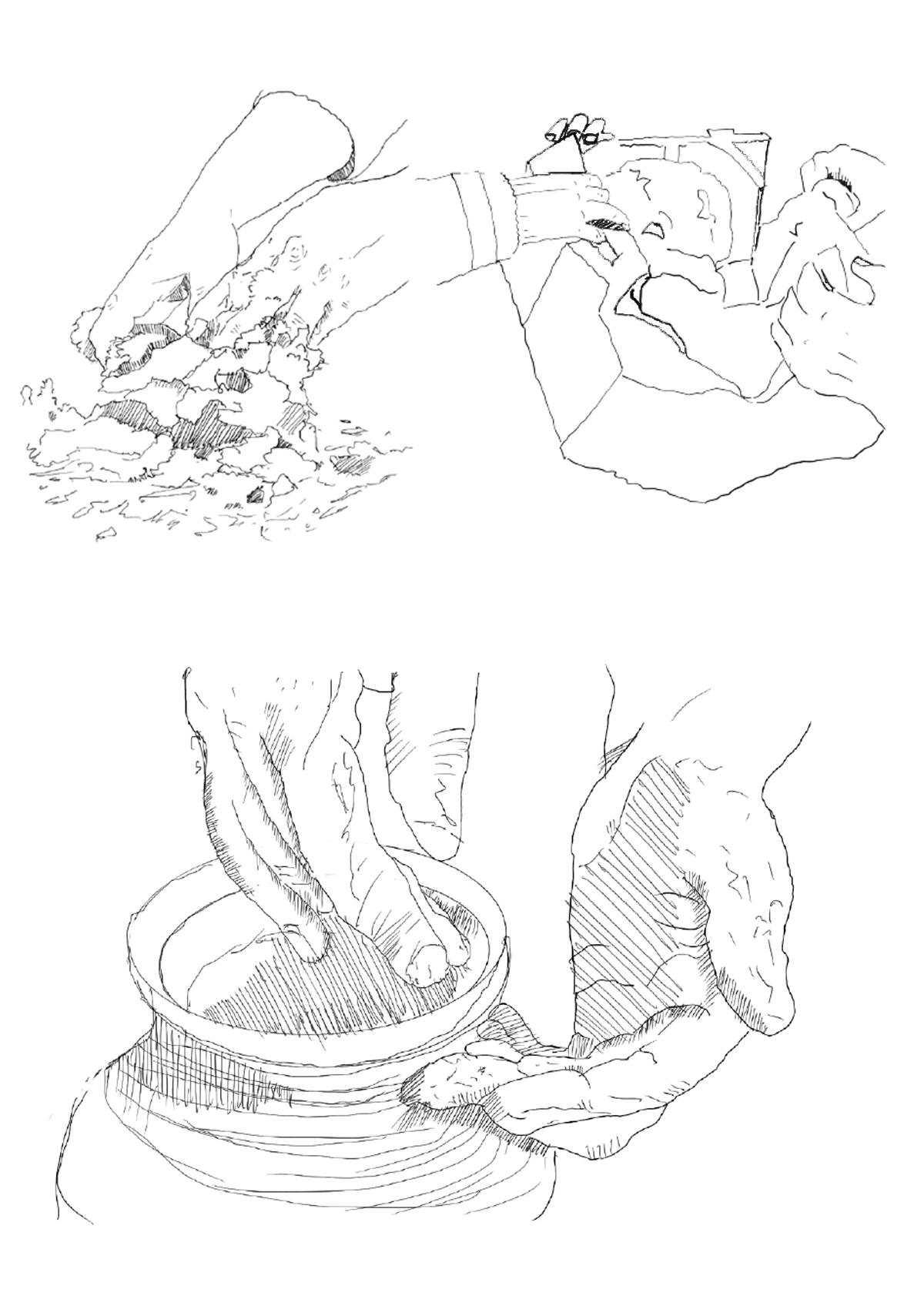
TACTILE
TACTILE
c) Moulding
Moulding starts the process of bringing tactility and involvement from the consumers to the products. Clay can be moulded with various tools, including hands, spinning tops, cast moulds and machines. The proposed design intends to accommodate a variety of potential moulding types. Moulding workshops will be offered, allowing users to create moulds for many manufacturing runs. Before storing the clay content in various studios where users can sculpt, the clay will be cut into workable blocks. This stage serves to create the mass for the final iterations.
d) Sculpting
Sculpting workshops will be held in the craft centre. Sculpting provides freedom of expression and is a good way to portray creative ideas on a physical object. The clay sculpture is a rewarding and innovative art form, which gives it a long history of over 20,000 years and keeps it popular today. The size, form and detail of the clay sculptures one can create may vary; however, artists can express a story through detail and creation (Fritzlan, 2021).
Fig 87: Sketch of hand moulding and cast moulding, (By author, 2021)
TACTILE
TACTILE
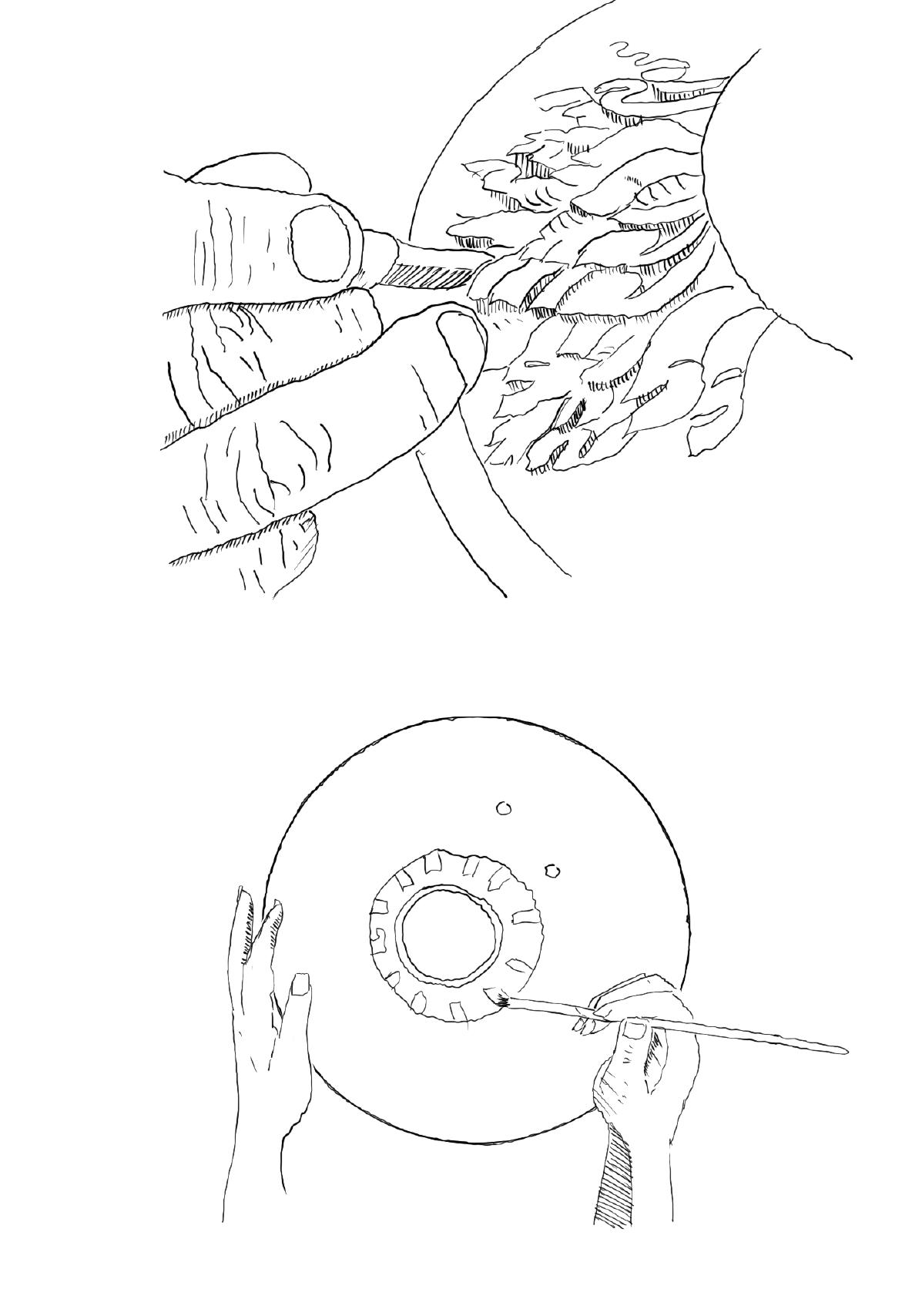
e) Carving
Carving adds another dimension to sculpting by allowing users to better define and express features on the ceramic product using various instruments such as a damaged brush, markers and sticks.
The carving technique is also an excellent way to build mass. This mass can come from outdated or discarded ceramic goods that can be modified and included in the final product. The recycling of outdated ceramic objects allows for smaller-scale recycling (Fritzlan, 2021).
f) Painting
Painting is an option for those who want to add decorative elements to the ceramic products. Natural dyes such as the contents of banana peels, seaweed, hair, and dung can be used, but they must be coupled with minerals such as iron to keep the paint from fading during the firing process. Recycle rubbish to create a meaningful outcome in clay can be achieved in this way, reflecting the study’s theme of sustainability.
Fig 89: Sketch of sculpting and carving, (By author, 2021)

TACTILE
g) Glazing
The process of glazing is accommodated in the crafts centre. Glazing is an impenetrable covering or coating fused to ceramic objects during the firing process. Glazing can serve to colour, embellish and waterproof the ceramic item to some extent. Glazing also makes earthenware ceramic objects suited for retaining liquids and imparts a glossy surface.
h) Drying and Firing
The final but most crucial phase is drying and firing. Drying is the process of reducing the moisture content of clay and transforming it into an authentic ceramic. Owing to the high temperatures, firing the clay product transforms it into a durable substance. There are two fire procedures: bisque firing (first) and glaze firing (second), depending on the preceding operations. It is planned that both will be available at the crafts centre.
Fig 91: Sketch of hand glazing, (By author, 2021)
5.3.3 Process flow
Deliver & collection
Sieving Soaking beds Filtration Use of water from Apies River when applicable and mains and that of rain water harvesting
Crusher
Excess sand
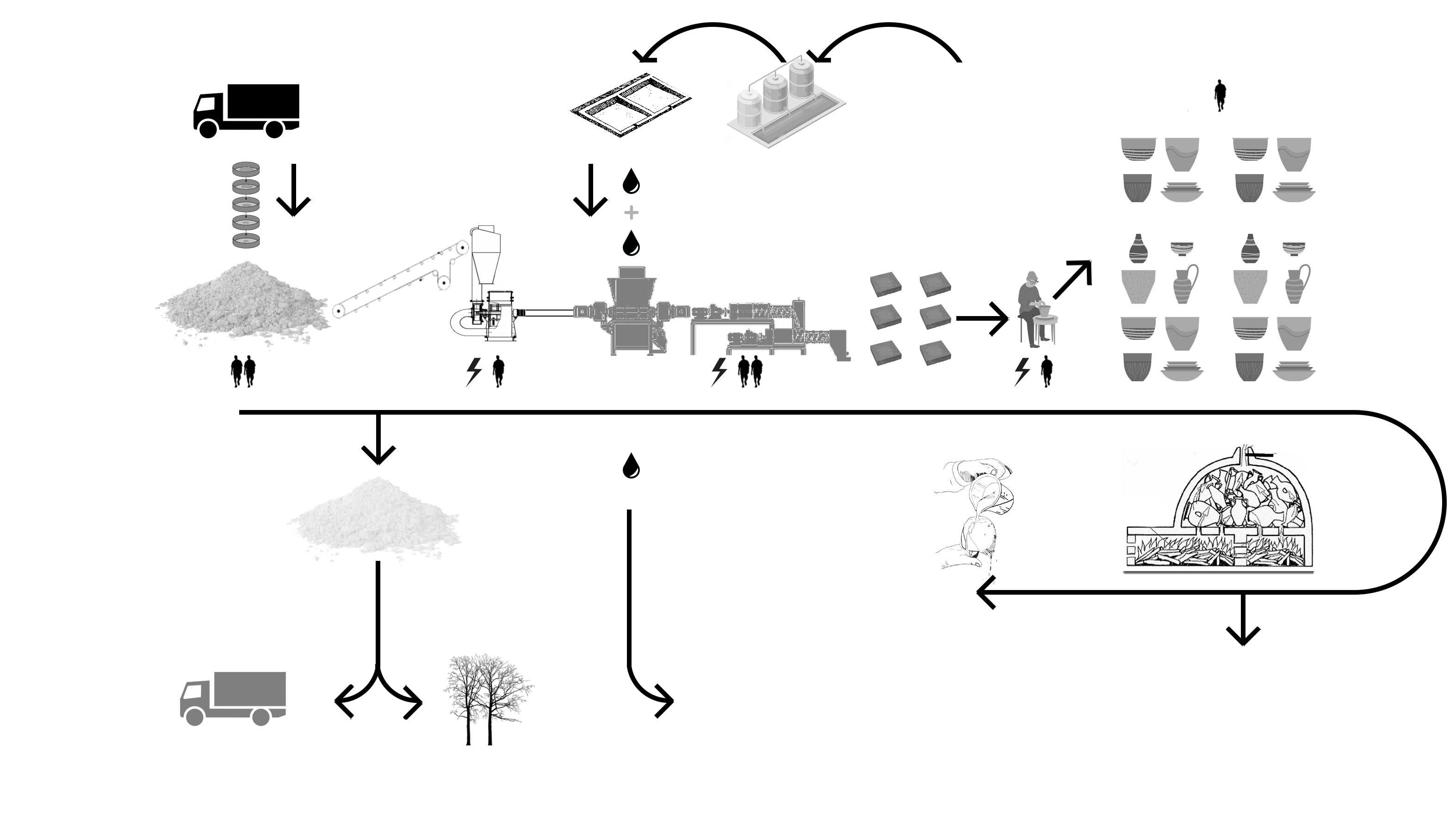
Transported or recycled Organic life Excess water
Filtrated and pumped back into the Apies River Moulding
Extruder Clay blocks Preparation Drying
Glazing Firing
Use of Gas Kilns with charcoal activated filters to capture CO2