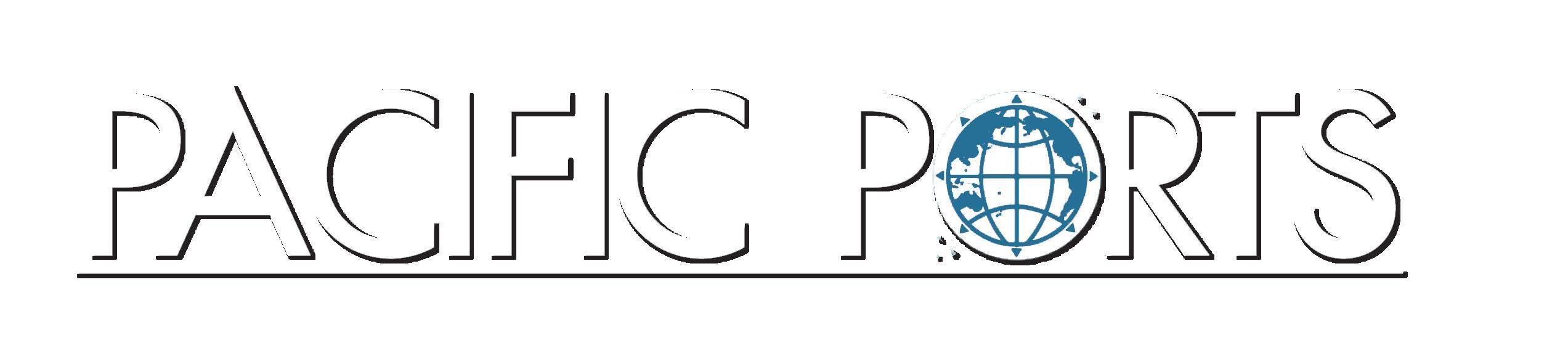
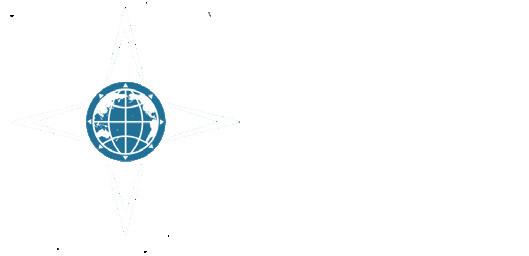
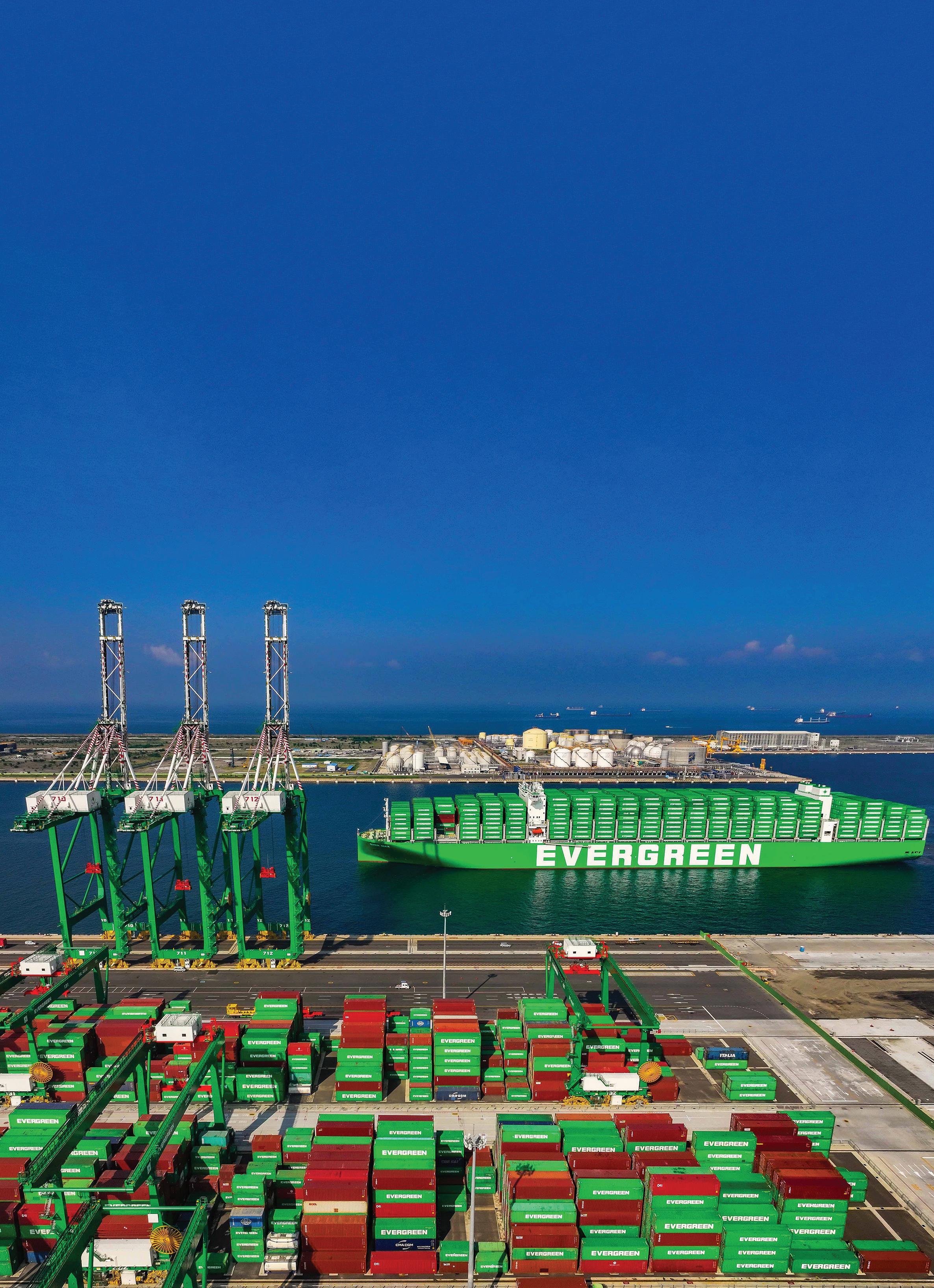
Spotlight on Taiwan
Leading the way to a vibrant and successful future for TIPC
New Leadership
Leonard Barnes, Port of Grays Harbor: A formula for success
Port Support of Industry
Keeping wheat’s story — and profits — local
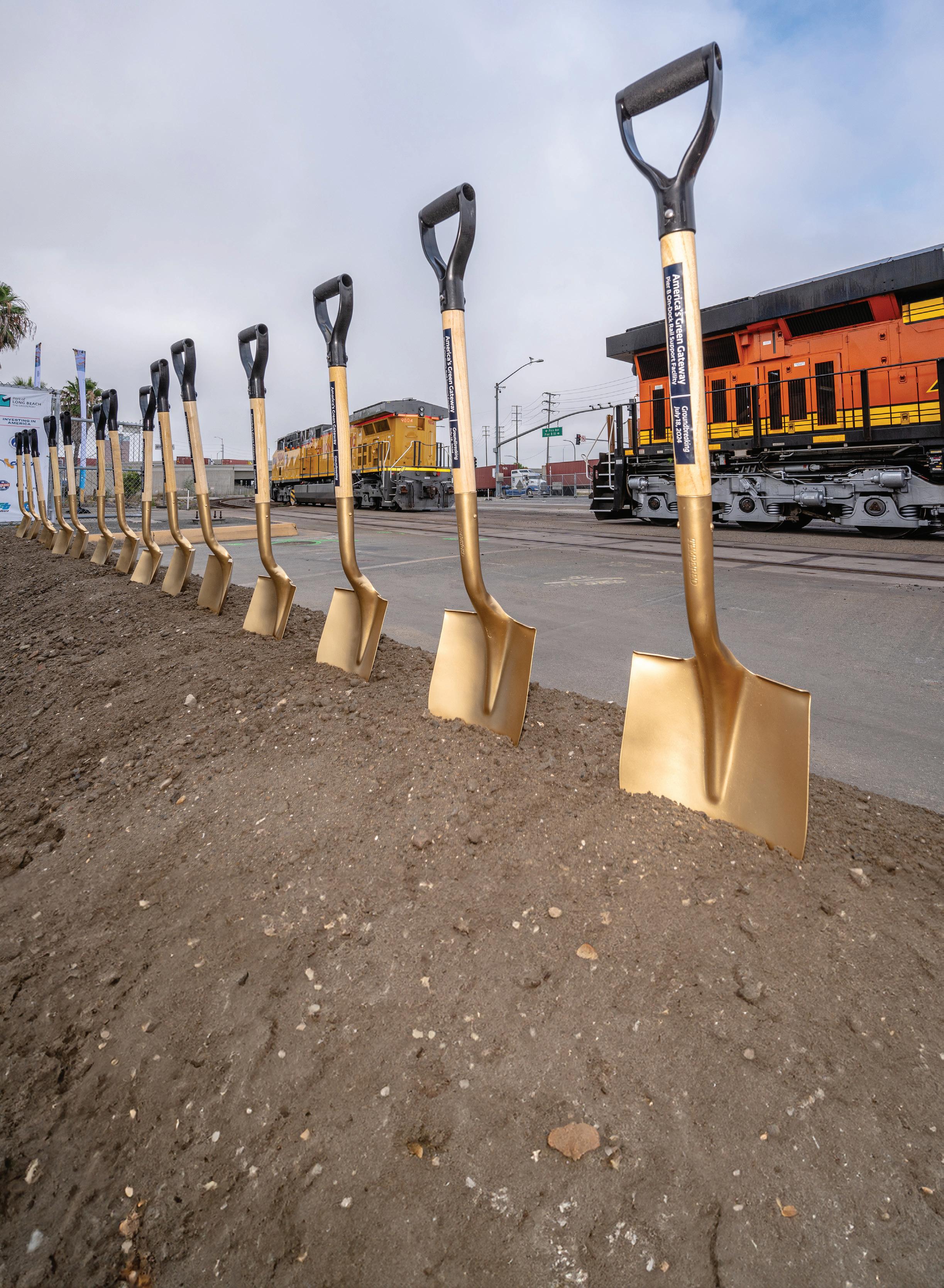
Leading the way to a vibrant and successful future for TIPC
Leonard Barnes, Port of Grays Harbor: A formula for success
Keeping wheat’s story — and profits — local
The Port of Long Beach just broke ground on our Pier B On-Dock Rail Support Facility – a $1.6 billion investment in rail infrastructure. We’ll increase throughput, lower emissions, lessen traffic impacts and move cargo faster and more efficiently.
ships calling at the terminal
The expansion at Trans Mountain’s marine oil export facility is complete and our newly commissioned modern three-berth dock complex is receiving tankers. We are efficiently loading vessels for overseas destinations, showcasing the terminal’s increased capacity to connect Canada’s resources with global markets.
Strategically located in the Port of Vancouver on Canada’s West Coast, Westridge Marine Terminal is committed to safe and efficient oil cargo transfers and vessel turnaround. With the Expansion Project complete, Trans Mountain is now well-positioned to meet the growing demands of the international oil market.
To learn more about the terminal, visit transmountain.com.
For shipping via Westridge, visit transmountain.com/shipper-services.
Leonard Barnes, new Executive Director, Port of Grays Harbor
Pacific Coast Congress celebrates 50 years of success
Keeping wheat's story — and profits — local
Adam M. Sowards
Port Alberni: Gateway to maritime excellence
Ryan Pessah
Seascour:
Ports Canada 2024 Conference heading to the heart of Vancouver Island
U.S. Federal funds are flowing from Biden's Department of Transportaton By Gordon Feller
Port of Long Beach breaks ground on ‘America's Green Gateway’
Shao-Liang Chen, President, Taiwan International Ports Corporation, Ltd., Taiwan
Kim B. Puzey, First Vice President/Treasurer, Port of Umatilla, OR USA
Conchita Taitano, Second Vice President, Port Authority of Guam, Guam USA
Stephen Ribuffo, Third Vice President, Port of Alaska, AK
Bobby Olvera Jr., Past President, Port of Long Beach, CA
Shu-Hui Cheng, Taiwan International Ports Corporation, Ltd., Taiwan
Sean Clark, Port of Columbia County, OR USA
Lorianna Kastrop, Port of Redwood City, CA USA
Zoran Knezevic, Port Alberni Port Authority, BC Canada
Thomas Maddison, Republic of the Marshalls Islands Port Authority, RMI
Sara Young / Kevin Ware, Port of Skagit, WA USA
AT-LARGE REPRESENTATIVE
Falenaoti Loi-On Fruean, American Samoa Department of Port Administration
Ian Marr, Port of Nanaimo, BC Canada
Kimberlyn King-Hinds, Commonwealth Ports Authority, Commonwealth of Northern Mariana Islands USA
Jane McIvor (jane@pacificports.org)
Philippe Critot (philippe@pacificports.org)
The APP has been committed to building partnerships, facilitating dialogue, and encouraging best practices for port governance and management throughout the Pacific since it was established in 1913 as the Pacific Coast Association of Port Authorities.
Throughout our 100+-year history, our objectives have remained consistent. With a focus on collaboration, the APP strives to encourage and facilitate best practices and professional development through conferences, workshops annd strong communications.
July/August 2024
Volume 5/Issue 2
Publisher
Association of Pacific Ports
Executive Director & Editor
Jane McIvor
Contributors
Leonard Barnes Shao-Liang Chen
Yen Chun Chuang Kayla Dunlap
Gordon Feller Carmela Ferro
Scott Grindy Jane McIvor
Ryan Pessah Chris Richardson
Adam M. Sowards
Advertising Phone: 323-578-2452
Philippe Critot (philippe@pacificports.org)
Editorial & Association business Phone: 604-893-8800
Jane McIvor (jane@pacificports.org)
Contents copyrighted 2024
Association of Pacific Ports
300 - 1275 West 6th Avenue, Vancouver, British Columbia Canada V6H 1A6 Phone: 604-893-8800 / E-mail: jane@pacificports.org
The opinions expressed by contributing writers are not necessarily those of the Publisher. No part of this magazine may be reproduced in any form without written permission of the publisher.
EDITOR’S NOTE: Due to the international nature of our membership, spelling within each article remains consistent to the country of origin.
s we get set to travel to Kaohsiung, Taiwan for the Association of Pacific Ports 110th Annual Conference, it’s a good time to reflect on the three main goals of the Association’s mandate, specifically: To build partnerships within the port community; to learn and share best practices; and to demonstrate leadership in fostering good relations with ports throughout the Pacific. The Taiwan International Ports Corporation (TIPC) has organized an agenda that will meet and exceed these goals.
With two sister port agreements to be signed at this conference (Port of Kaohsiung and Port of Long Beach
as well as Port of Kaohsiung and Republic of Marshall Islands), TIPC has not only exceeded the first goal of building partnerships but has demonstrated great leadership in fostering good relations. These agreements will have a positive and lasting influence for ports on both sides of the Pacific Ocean for years to come.
The agenda that TIPC has developed further stays true to the APP’s goal of providing a forum for learning and sharing best practices. Demonstrating an eagerness to engage in robust discussions on topics of relevance to all ports, TIC has provided numerous opportunities for attendees to engage
their peers and discover how each is addressing the issues we all face.
Perhaps most importantly, TIPC has set an itinerary that balances learning with fun! With renown Taiwanese hospitality on full display, our hosts have planned a number of off-site events and excursions that will allow attendees to enjoy the culture and customs of traditional Taiwan as well as the company of each other.
It is with great gratitude that I thank TIPC’s President, Mr. Chen, and his entire team for all of their hard work in organizing what promises to be a most memorable event.
— Jane McIvor
MarineLabs has announced Forecast AI, accurate and hyper-localized coastal weather forecasts delivered through their new machine-learning models and extensive data from their fleet of realtime sensor nodes. Forecast AI is a muchanticipated addition to MarineLabs’ flagship product, CoastAware, a realtime weather intelligence solution that enhances safety, efficiency, and sustainability in maritime operations.
MarineLabs’ Forecast AI generates profoundly more accurate wind and wave forecasts that account for each location’s unique characteristics and geography. It does this by combining extensive observed data from its expanding sensor network with data from third-party forecast models while continuously learning and improving with time.
“Forecast AI represents a giant stride forward in our mission to revolutionize marine mobility,” said Dr. Scott Beatty, CEO of MarineLabs. “By leveraging our unique observations to train thousands of machine learning models, we have the ability to more accurately predict weather in a way that addresses critical gaps in traditional forecasts. This empowers our subscribers and partners with the precise, forward-looking, hyper-local wind and wave forecast information they need to make safe and informed decisions in the face of increasingly volatile weather.”
In an in-depth study over a twomonth period from December 2023 to February 2024 at a site on the East coast of Canada, MarineLabs’ Forecast AI made 23 percent more correct calls due to significant wave height exceeding critical safety thresholds for port
operations than a trusted publicly available forecast model. To date, in aggregate over 32 locations in MarineLabs’ sensor network with forecasting available, Forecast AI has 50 percent lower average errors in predicting weather parameters compared to publicly available maritime forecast models. Access to this kind of tactical, highly reliable, hyper-local forecast data with customizable alerts specific to weather thresholds offers new efficiencies and levels of trust in decision-making for mariners and ports.
MarineLabs is transforming the global weather intelligence landscape with features like Forecast AI, which empowers port authorities, vessel pilots, and others in the maritime industry to make decisions with more certainty. To learn more about MarineLabs’ Forecast AI, visit marinelabs.io/forecastai.
FortisBC Holdings Inc (FortisBC) is pleased to announce that the Government of Canada has approved Tilbury Jetty Limited Partnership’s Tilbury Marine Jetty (TMJ) project.
The TMJ project involves the construction of a jetty, or dock, on the south arm of the Fraser River. This facility will supply LNG bunkering vessels with refueling services in the Vancouver region. Strategically located adjacent to FortisBC’s existing Tilbury LNG facility, the jetty will leverage the facility’s production of LNG, which is less carbon-intensive compared to the global average due to its use of hydroelectric power.
LNG reduces local air pollutants, this is especially important for ports and populated coastal areas. With about 3,100 ships calling on the Port of
Vancouver each year, switching from conventional marine fuel to LNG marine fuel could remove 90 per cent of the particulate matter associated with marine shipping from the local airshed, according to a third-party study.
In 2022, FortisBC and the Musqueam Indian Band signed an agreement that will see both parties working in close collaboration as the Tilbury projects are developed. A shared goal of the agreement is to develop a world-leading LNG facility that provides mutual benefits for Musqueam and the region.
The TMJ will help create economic and employment opportunities for Delta, neighbouring communities and Indigenous communities.
FortisBC will continue to work closely with Indigenous groups and local communities on environmental
Service Wharf: 300ftx75ft, D25ft
• 4.5 acre Container Yard
• 40,000sqft Warehouse
Pago Pago International Airport (PPG) – Tutuila Island
• 700-acre public airport
6 miles SW of Pago Pago,
•
•
•
mitigation, as well as explore opportunities for training, employment and contracting.
TMJ will now proceed with securing the necessary remaining approvals and permits and will work towards making a final investment decision for the project.
“This significant milestone allows the project to move forward in its goal of reducing emissions in the marine industry and provide benefits to our local economy, including through our agreement with Musqueam,” said Roger Dall’Antonia, President and CEO of FortisBC.
Located in South Pacific Ocean, in the heart of Polynesia, Pago Pago Harbor is one of the world’s largest natural harbors, and it is also considered one of the best and deepest deepwater harbors in the South Pacific Ocean or in Oceania as a whole.Pago Pago International Airport is capable of accommodating any size of commercial aircraft. When combined, our seaports and airports make the movement of cargo and people to and from American Samoa easy because of its strategic midpoint for several shipping and air routes between the U.S. West Coast, Honolulu Hawaii, Australia, New Zealand and other pacific nations.
The Port of Hueneme is excited to support and enhance the movement of goods across the state of California and throughout the supply chain with the announcement of a $3.935 million award from the Governor’s Office of Business and Economic Development (GO-Biz). This historic investment, known as the California Port Data Partnership, will revolutionize direct
cloud-based data management and sharing amongst California’s five containerized ports to accelerate climate adaptation and resiliency, workforce development, zero-emission vehicle deployment, and increased grid support and reliability. As the nation’s preeminent global goods movement gateway, California ports are responsible for handling forty percent of all containerized imports and thirty
SHIPPING SOLUTIONS AT TWO DEEP SEA TERMINALS LINKING VANCOUVER ISLAND’S ECONOMY TO THE WORLD.
• The Port of Nanaimo ships 18 different Vancouver Island products to 25 ports in 14 countries.
• Short-sea shipping to Vancouver with capacity to handle containers, bulk, break bulk, heavy lift and project cargoes.
percent of all containerized exports in the United States.
“California’s ports are critical to the stability of our national and global supply chains, as well as the health of our worldwide economy,” said GO-Biz Director and Senior Advisor to Governor Gavin Newsom, Dee Dee Myers. “These historic, first-of-theirkind awards will allow us to use data to improve the functionality of our supply chain, and we look forward to working with our ports to further the momentum that these projects will generate across the state.”
• Enhanced infrastructure providing versatility and efficiencies for diverse cargo and vessel solutions and to meet a growing container business both locally and globally.
LOCAL BENEFITS — GLOBAL REACH
For Cargo and Terminal oppportunities, please contact: Jason Michell, VP - B.D. (250) 734-3457
JMichell@npa.ca
www.npa.ca
100 PORT DRIVE, NANAIMO, BC
This one-time state investment of $30 million is a significant milestone funded under the Governor’s Budget Act of 2022. The funding aims to bolster data interoperability, reduce emissions, and align the world’s fifth largest economy with federal objectives through the California spirit of innovation, equity, and leadership.
The Port of Hueneme is among California’s five containerized ports (San Diego, Los Angeles, Long Beach, and Oakland) to receive this critical investment. Development of direct cloud-based data systems amongst California’s containerized ports will further support and accelerate emerging data aggregation and analysis that will undoubtedly support freight and supply chain efficiency.
Port of Hueneme Board President, Celina Zacarias, added: “Our commitment to data-driven solutions will enhance our competitiveness and benefit the entire California economy. This grant is a testament to our dedication to data driven excellence.”
“This grant is a game-changer for our port and the entire state of California,” said Kristin Decas, CEO and Port Director of the Port of Hueneme. “By enhancing data connectivity, we can optimize operations, reduce environmental impact, and strengthen our position as a vital gateway for global trade.”
Leading the way to a vibrant and successful future for TIPC
Following on from the last issue of Pacific Ports Magazine, we continue our look at Taiwan International Ports Corporation (TIPC). As the Host Port for the APP’s 110th Annual Conference, TIPC has many innovative and progressive initiatives that will be highlighted throughout the conference in both presentations and field trips, including a tour of the new fully automated Terminal 7 and operations throughout the Port of Kaohsiung. To provide context, Mr. Shao-Liang Chen, President of TIPC, shares insights into the strengths and opportunities that are being realized for the future of Taiwan’s ports.
PP: Could you provide some insight into what you feel are the main keys to success that you applied during your leadership of TIPC?
SLC: TIPC is marching into its 12th year since being established in 2012. We currently have approximately 2,000 employees and operate seven international commercial ports
in Taiwan. Twelve years may not seem like a long time, but TIPC was restructured out of Harbor Bureaus and our staff have many decades of experience in port operations. In terms of leading the Taiwan ports, we focus foremost on “teamwork” as each port operates according to its unique characteristics. For example, the Port of Kaohsiung is positioned as the International Container Terminal, and the Port of Taichung is the Green Port for energy and bulk supplies storage. We invest in, and develop each port, according to its corresponding position so as to maximize its operational efficiency.
Secondly, I encourage all staff to continue striving for innovation and improvement, especially as Industry 4.0 (i.e., the realization of digital transformation) has created revolutionary changes in all sectors globally. Cutting-edge technologies, including automation and AI, are introduced to port operations, but it’s the mindset that truly counts. Ultimately, technologies are there to assist, but it is only
with a mindset of continuous improvement and innovation that will we be able to harness and use technology to lead the transition of port operations. Finally, it is sustainable growth, the most important topic to all enterprises. In addition to achieving sustainable port operations through introducing technology and green energy, more importantly, we have to reinforce our
core businesses and develop diversified businesses, so that TIPC can continue to achieve better performance and aspire to become some of the best ports worldwide.
PP: You mention moving away from the Harbor Bureau system in 2012. Could you describe the benefits, opportunities, and challenges this has created for Taiwan’s port system?
SLC: After restructuring, the operation and management of ports transformed from “administrative agencies” to “companies”. The loosening from the administrative system gave TIPC more flexibility in operations. Take staff recruitment for example, we can recruit talents with related backgrounds according to the diversified business developments of the ports. Through recruitment and training programs, TIPC can foster professional talents and optimize the organization and human resources. Furthermore, the restructuring has made TIPC more flexible and agile, allowing us to expand into more diversified fields and investing overseas. So far, we have invested in seven subsidiaries focused on marine, logistics, land development, and offshore wind
In terms of leading the Taiwan ports, we focus foremost on “teamwork” as each port operates according to its unique characteristics.
power, increasing overall company revenue and profit growth.
Facing the trend of net-zero carbon emissions, low carbon and energy transitions will present challenges as well as opportunities in the future. Following Taiwan’s national net-zero policy, TIPC has drafted a carbon reduction roadmap and relevant carbon reduction measures for Taiwan ports, aiming to reduce carbon by 50 percent by 2030 and to achieve net zero by 2050. In the meantime, responding to business opportunities in carbon reduction, we will introduce an energy-related industry chain to proactively take part in green energy businesses and create further growth for Taiwan ports.
PP: Could you give us an idea of the types of cargo moving through the ports?
SLC: Cargoes moving through Taiwan ports are mainly imports, with a total weight of 142.97 million tons in 2023, accounting for 79 percent of
total throughput volume; imported container cargoes amounted to 29.28 million tons in 2023, accounting for about 20 percent of total imports. The top three imported goods were minerals (92.55 million tons), iron and steel products (13.59 million tons), and grains (9.91 million tons), accounting for approximately 81 percent of total imports. Cargoes are mainly imported from Australia (coal, iron ore), the United States (crude oil, grains), China (sand, iron and steel products), and Qatar (LNG).
The weight of exported goods in 2023 was 39.06 million tons, of which container cargoes were 26.81 million tons, accounting for approximately 70 percent of total exports. The top three exported goods were iron and steel products (12.28 million tons), plastic products (9.57 million tons), and chemical products (5.4 million tons), and the top three categories accounted
for roughly 70 percent of total exports. Exports go mainly to China, the United States, and Vietnam.
PP: What are some of the unique characteristics of TIPC’s ports?
SLC: Environmental protection is essential to TIPC as we promote port development. In 2014, the Port of Kaohsiung obtained the first EcoPorts certification by European Sea Ports Organization and became the first port to be certified in Asia-Pacific. In 2017, TIPC’s seven international commercial ports were all certified as EcoPorts, and their status remains valid through re-evaluations. This demonstrates TIPC’s commitment towards the ecology and environment.
As a state-owned enterprise, TIPC holds the mission of promoting national policies. As Taiwan has been proactively promoting offshore wind power in recent years, TIPC has invested in infrastructure including quays, land reclaim, and road improvements in the ports of Taipei and Taichung, providing the lands and facilities for offshore wind power operations. We have also invited relevant domestic and overseas companies to the ports, provided turbine
pre-assembly and localized manufacturing areas, assisted operation and maintenance service, and talent cultivation, all to build the offshore wind power industry cluster. Under the policy of national energy transition, TIPC will continue to play an important role in meeting the needs of clean energy and renewable energy development. In the future, ports will be important locations for the receiving, storage, transfer, and even production and processing of LNG, hydrogen energy and related renewable energy, becoming the strong foundation on which to promote national policies.
PP: There are a variety of issues I’d like to raise to see how TIPC is meeting the challenges and finding the opportunities with them. Let’s start with overall environmental sustainability.
SLC: With the world addressing the challenge of climate change and moving toward net zero by 2050, as the operator of international ports, TIPC is responding by establishing a carbon reduction target of 50 percent by 2030 and net zero by 2050. Our strategy includes setting up renewable energy power generation facilities, adopting low-carbon and clean energy practices,
and establishing energy management systems. We also promote a circular economy to reduce the carbon emissions of port construction to be able to build low-carbon and green ports. At the same time as we move toward these goals, we are highly concerned about the balance between marine and terrestrial ecological conservation and the issue of biodiversity. To address this, we are protecting and monitoring marine and terrestrial ecosystems such as cetaceans, wild birds, corals, and mangroves, and continuing to expand the vegetation area of the ports, which has reached 773 hectares, helping to reduce carbon emissions by approximately 7,730 tonnes per year.
PP: What about resiliency efforts, especially noting the recent earthquake and its impact on the Port of Hualien?
SLC: TIPC has developed various response standard procedures for common or possible disasters, including shipwrecks, oil pollution, ship collisions, wind disasters, earthquakes, fires, and even compound disasters. We hold drills with the Harbor Police Department, Harbor Fire Brigade, coast guards, Maritime Port Bureau, medical units and businesses inside the ports on
different topics from time to time and we continue to improve disaster protection and response capability through cross-unit cooperation and familiarity with the response mechanism.
On April 3 this year, a magnitude seven earthquake struck Hualien. The Hualien Branch immediately set up an emergency response team to conduct a comprehensive inspection of the port area according to the Earthquake Response Standard Procedure to assess the damages suffered by the Port of Hualien. An emergency response and recovery meeting was quickly convened to take contingency measures such as suspending cargo handling at the quay, and shipping traffic control. Real-time information related to the earthquake was also reported via the company’s internal communications group with the head office reporting to the Ministry of Transportation and Communications upon compiling information from various ports.
PP: What about digitization of port operations and cybersecurity?
SLC: Regarding port cybersecurity, since TIPC plays an important role in national economic growth, maintaining important livelihoods, and developing the shipping industry, in order to maintain port operations and ensure system security, we have included all important service systems at various international commercial ports in the scope of ISO 27001 certification. This confirms that all systems comply with international cybersecurity standards and the Cyber Security Management Act in Taiwan. We also successfully passed the thirdparty verification of the new version of ISO 27001:2022 in 2024.
To further detect risks that may affect system services or security in real-time, TIPC has introduced a comprehensive cybersecurity monitoring service covering the network, cybersecurity equipment, and terminal computers.
TIPC has developed various response standard procedures for common or possible disasters, including shipwrecks, oil pollution, ship collisions, wind disasters, earthquakes, fires, and even compound disasters.
In the case of abnormal events, the monitoring service can immediately initiate contingency actions such as a system backup or a remote redundancy mechanism to ensure uninterrupted port services.
Regarding digitization, most of the stakeholders in the port, including ship operators, cargo owners, shipping agents, customs brokers, and logistics operators, have developed their own operational information systems, albeit these systems are for their respective needs only.
In response to the continued advancement of digital technology, TIPC plays a key role in communication in the port operation process. To assist stakeholders in the port industry to stay on top of changes within the port environment, information technology is applied, and priority is given to set up a number of digital systems in the port infrastructure. Meanwhile,
creative thinking from private companies is introduced by allowing the port to be used as the test field for innovative technology. Regarding the pain point of port operations, small-scale technical testing (PoC, Proof-of-Concept) can be conducted. Upon verification of the technical feasibility, the service scale of application can be expanded to PoS (Proof-of-Service), and further to PoB (Proof-of-Business). Incentives are additionally provided to assist businesses in the port area to adopt digital innovation services and build an innovative smart port ecosystem.
In the future, the digital development of Taiwan ports will focus on a more comprehensive integration of information systems, foster a closer digital connection with stakeholders, and provide high-quality and flexible port services.
PP: What technological advances are helping TIPC achieve greater efficiencies?
In the future, the digital development of Taiwan ports will focus on a more comprehensive integration of information systems...
SLC: Following the technical and digital transformation trend of automation and AI, Taiwan ports applied digital technology to various software and hardware facilities. For example, the 7th Container Terminal of the Port of Kaohsiung has built a highly automated system, using remote-controlled ship-to-shore container cranes for cargo handling and fully automated Rail Mounted Gantry Cranes for container yard management. This not only greatly reduces the original manpower by 60 percent, but also achieves an efficient 24-7 uninterrupted operation. With this new terminal, annual operation capacity could reach up to 6.5 million TEUs.
Also, to monitor port area operations, environmental sensing and AI image recognition actively analyze real-time images of the port area to accelerate the identification of abnormal events. For example, AI technology was applied to the automatic gate sentry post control system in the port area. Images of personnel, vehicles, and cargo are identified by AI to provide
automatic customs clearance services. At the Port of Kaohsiung, daily traffic through the gate system is more than 30,000 trucks. With the automatic gate sentry post control system quickly and accurately identifying license plates and container numbers, vehicle clearance time is improved from four minutes per vehicle to 10 seconds, improving the efficiency of traffic clearance while achieving the goals of convenience, paperless, and carbon reduction. The system can also monitor the entire journey from the vehicle entry to exit and issue, real-time warnings for suspicious vehicles to enhance the safety of the port area.
Further, we plan to introduce digital technology to optimize on-site operations of the port area. Currently, the port terminal is still manually patrolled and managed, including the ship berthing dock, alongside cargo handling, longshoring, goods retained, and cargo handling safety. Meanwhile, since the port operation is 24-7, it is impossible to carry out real-time inspections as the ship docks and leaves
with the limited patrolling manpower and shift hours. Therefore, TIPC invited vendors to assist in introducing AI verification technology which can aid general management, hoping that with an AI algorithm in place to assist the patrol and management, we can achieve the result of automated determination, warning, and even prediction of possible events. Results of image recognition can also be reported to the site management for verification and management, which can help improve overall efficiency and strengthen the safety of port operations.
In terms of container handling, TIPC worked with vendors to introduce the AI-OCR technology, which is combined with the automatic container damage identification technology and integrated into the self-operated container yard of the Port of Kaohsiung through the vehicle positioning and guidance function of the shipside lane. We are building a smart maritime port with AI technology at heart and hope to optimize marine terminal operation efficacy, including the handling management efficiency of the container wharf, saving costs, automating container damage identification, and image retrieval efficiency, and in turn move towards smart transition of the port.
PP: Could you describe TIPC’s efforts regarding recruitment, labor and skills training?
SLC: Believing that employees are the most valuable asset of the company, TIPC is committed to building a sustainable and happy workplace based on the “four Fs approach”: Flexibility - flexible management, Friendlyfriendly workplace, Family - treat colleagues like family, and Future - a foreseeable future. This approach helps us to achieve stable employee retention and increased attraction of talents.
Also, in response to the global trend of smart port development and sustainability, and to ensure that employees improve their overall capabilities aligning with these trends, TIPC tailors systematic training resources and learning methods for employees, organizing not only physical courses according to professional skills, career stages, and management capabilities, but also providing multiple online learning channels, and continuing to provide substantial incentives to encourage employees to participate in courses offered by domestic and international training institutions.
PP: Considering emerging trends such as alternative energies and vessel sizes, can you describe TIPC’s short (one year) and longer-term (five years) expansion projects?
SLC: Regarding the trend of megaships, short-term expansion includes the first phase of the 7th container terminal of the Port of Kaohsiung which commenced operations in mid-2023 and expected to be in full operation by July this year (2024). This container terminal, with a total length of 2,415 meters and a depth of 18 meters, can accommodate four 24,000-TEU class container ships to berth at the same time, adding an extra 6.5 million TEUs annual capacity to the Port of Kaohsiung in the long run.
Looking at long-term expansion plans and the overall development of the Port of Kaohsiung, we continue with the renovation project of the 3rd and 5th container terminals, which will accommodate 18,000 TEU and 24,000 TEU mega-ships upon completion.
Looking at new and alternative energies, an important project is the development of key infrastructure for the offshore wind power industry. In addition to fixed bottom wind turbines, Taiwan also plans to develop floating wind turbines in response to the development of energy trends. In line with the national energy transition policy, hydrogen energy is also one of the 12 key strategies for Taiwan’s 2050 netzero transition. According to research by Taiwan’s Industrial Technology Research Institute, the future source of hydrogen energy will mainly be imported (75 percent) and supplemented by self-production (25 percent),
so hydrogen supply chain activities such as manufacturing, transportation, handling, storage, and distribution will be carried out at ports. TIPC has developed a port expansion plan that includes a total of 65 hectares of land in the South Reclamation Area of Port of Taichung as “the base for floating wind turbines, hydrogen energy, and green energy development”. We anticipate having 50 hectares of land by the end of 2026. The Environmental Impact Assessment process for this development must be approved by 2025 at the latest so that the 800-1000 meters of outer breakwater can be completed by the end of 2028 to provide for relatively calm waters for floating offshore wind farms. TIPC is also planning to develop 100 hectares of land in the South Wharf Area of the Port of Taipei as “the green energy and logistics industrial zone”, and it is expected that the land will be available for use in phases from the end of 2028. PP
Ahost of senior ferry leaders will speak at Interferry2024, the 48th annual conference of the association representing the ferry industry worldwide. During the conference’s two-day Speakers Program on October 28 and 29 in Marrakech, noted ferry industry leaders and keynote speakers will expand on the theme of Safety, Security and Sustainability.
Interferry strives to find a good balance between ferry executives and those supplier members whose activities are related to the conference themes when designing the speakers program, and they have once again managed to attract a representative cross section of the world’s ferry community to discuss “Safety, Security, and Sustainability”. Earlier this year, Interferry — together with the IMO —hosted the Africa Ferry Safety Seminar in Dar es Salaam, Tanzania. A good part of the Safety program will continue building on domestic ferry safety and what Interferry achieved in Dar es Salaam. Presentations regarding the Security theme will cover all areas of operational security, including physical security concerns pertaining to ports and ships, but also rapidly increasing cybersecurity risks. The sessions focusing on Sustainability will continue to highlight zero-emission
solutions as well as presentations on sustainable ship construction and interiors.
Ferry operator heavyweights from all four corners of the world will speak, with conference host and Interferry President Ronny Moriana Glindemann of FRS/DFDS leading off the program. Although the ferry sector is still maledominated, Interferry is pleased to report that three well-respected female ferry leaders will be on the stage. Greta Bédard, the first woman to hold the position of President and CEO of Canada’s Société des traversiers du Québec (STQ), will give insights from the Canadian East Coast ferry scene. Stena Line CCO Elisabeth Lönne, will talk about the transformation efforts at the Gothenburg-headquartered ferry company. Indonesia is probably the world’s most ferry-dependent nation and Interferry is therefore extremely proud to welcome ASDP Indonesia Ferry CEO Ira Puspadewi to one of the ferry leaders panels. Ira, whose leadership has been marked by innovative strategies and operational enhancements, will also talk about the Indonesian ferry system’s challenges and opportunities.
Other distinguished speakers include: Götz Becker, CEO of FRS and Interferry Board Vice-Chairman;
Torben Carlsen, the CEO of DFDS who has been instrumental in the company’s expansion during the past 15 years; Matteo Catani, CEO of GNV, a leading Western Mediterranean ferry operator controlled by MSC Group —the world’s largest shipping company; Ettore Morace, the Grimaldi Trasmed CEO with over 40 years of industry experience; Steve Nevey, who recently succeeded Patty Rubstello as head of Washington State Ferries, the largest ferry system in the US; and Mark Wilson, who will join the discussion as newly appointed President and CEO of Northumberland/Bay Ferries.
Interferry has also lined up two informative and insightful keynote speakers in Bud Darr and Sotiris Raptis. As EVP Maritime Policy and Government Affairs at MSC Group, Bud is engaged across MSC’s Cargo and Passenger divisions, continuing to develop and refine the company’s central Government Affairs function. Sotiris is Secretary General at the European Community Shipowners’ Associations, ECSA.
The complete speakers program with all speakers, sessions and schedule will be announced at the end of July. The latest conference information can be found on InterferryConference.com.
and sessions, ferry leaders panels, outstanding networking opportunities, and a technical tour. The full conference program with sessions, speakers and schedule will be posted on InterferryConference.com by the end of July. Sponsors and exhibitors will enjoy a large exhibition area in which to display their products and services. A limited number of exhibit spaces remain and will likely sell out by the end of August – so contact us soon if you’re interested! For the latest info check the conference website, follow our social media, and subscribe to our mailing list.
“Interferry welcomes delegates to our first ever conference on the African Continent in Marrakech, Morocco, October 26-30, 2024!”
Mike Corrigan – CEO, Interferry
BOARD OF COMMISSIONERS CHAIR:
COMMISSIONERS:
10,077
TOTAL NUMBER OF J OBS THE PORT PROVIDES
DON YOUNG PORT OF ALASKA
www.portofalaska.com
2000 Anchorage Port Road, Anchorage, AK 99501 USA
T: 907-343-6200
E: portofalaska@anchorageak.gov
Key staff
Stephen Ribuffo, AMPE, Port Director (Steve.Ribuffo@anchorageak.gov)
John Daley, Port Modernization Program Engineering Manager (John.Daley@ anchorageak.gov)
Commissioners
Ron Ward, Chair | Aves Thompson, Vice Chair | Dick Traini | Simon Lisiecki | Christopher Manuculich | Mike W. Robbins | Peggy Jean Rotan | Scott Selzer | Stephanie Kesler
americansamoaport.as.gov
PO Box 656, Pago Pago, AS 96799 USA
T: 684-633-4251
Key staff
Falenaoti Loi-On Fruean, Director (falenaoti.loionfruean@pa.as.gov)
www.portofbrookingsharbor.com
16330 Lower Harbor Road PO Box 848
Brookings, OR 97415 USA
T: 541-469-2218
Key staff
Port Manager (info@portofbrookingsharbor.com)
Travis Webster, Harbormaster (travis@portofbrookingsharbor.com)
Commissioners
Wesley Feraccioli | Joseph Speir | Sharon Hartung | Larry Jonas | Daniel Fraser
www.portofcolumbiacounty.org
Main Office: 100 E Street, Columbia City, OR 97018 USA
Mailing Address: PO Box 190, Columbia City, OR 97018 USA
T: 503-397-2888
General email: inquiries@portofcolumbiacounty.org
Key staff
Sean Clark, Executive Director (clark@portofcolumbiacounty.org)
Commissioners
Brian Fawcett, President | Chip Bubl, Vice President | Nancy Ward, Second Vice President | Nick Sorber, Treasurer | Robert Keyser, Secretary
COMMONWEALTH PORTS AUTHORITY
www.cnmiports.com
PO Box 501055, Saipan, MP 96950 CNMI
T: 670-237-6500
Key staff
Leo B. Tudela, Executive Director
Jerra Cing, Port of Saipan Manager (jerra.cing@cnmiports.com)
Antonio L. Borja, Tinian Ports Manager (alborja@cnmiports.com)
Directors
Jose C. Ayuyu, Chair | Antonio B. Cabrera | Steve K. Mesgnon | Dolores P. Kiyoshi | Ramon A. Tebuteb | Thomas P. Villagomez | Joseph M. Diaz
FIJI PORTS CORPORATION LIMITED
www.fijiports.com.fj
1 Tofua Street, PO Box 780
Suva, Fiji
T: 679-892-8301
E: info@fijiports.com.fj
Key staff
Vajira Piyasena, Chief Executive Officer
Florence Nand, Manager, Planning & Strategy Implementation
PORT OF GRAYS HARBOR
www.portofgraysharbor.com
111 South Wooding Street, PO Box 660 Aberdeen, WA 98520-0141 USA
T: 360-533-9528
Key staff
Leonard Barnes, Executive Director (lbarnes@portgrays.org)
Commissioners
Phil Papac | Stan Pinnick | Tom Quigg
PORT AUTHORITY OF GUAM
www.portguam.com
1026 Cabras Highway, Suite 201, Piti, Guam 96915
T: 671-477-5931
Key staff
Rory Respicio, General Manager (rrespicio@portguam.com)
Dominic G. Muna, Deputy GM, Operations (dgmuna@portguam.com)
Directors
Dorothy P. Harris, Chairperson | Conchita S.N. Taitano, Vice Chairperson | Fe R. Vanencia-Ovalles, Board Secretary
451 Atkinson Drive, Honolulu, HI 96814 USA
T: 808-949-4161
Key staff
Dustin Dawson, Division Director (ddawson@hawaiilongshore.org)
Edwin Hayashi, Vice Division Director (ehayashi@hawaiilongshore.org)
LTD.
https://hl.twport.com.tw/
No.66 Hai-An Road, Hualien City, Hualien County 970, Taiwan
T: 886-3-8325131
E: business@twport.com.tw
Key staff
Pai-Feng Wang , Vice President & CEO
Board of Directors
Hsien-Yi Lee, Chairman | Shao-Liang Chen, President
www.portofh.org
333 Ponoma Street, Port Hueneme, CA 93041 USA
T: 805-488-3677
Key staff
Kristin Decas, CEO & Port Director (kdecas@portofh.org)
Austin Yang, Deputy Executive Director, CFO/CAO (ayang@portofh.org)
Commissioners
Celina Zacarias, President | Jess Ramirez, Vice President | Jason Hodge, Secretary | |Mary Anne Rooney | Jess Herrera
CORPORATION, LTD.
https://kh.twport.com.tw/en/
No.62.Linhai 2nd Road, Gushan District, Kaohsiung, 804002 Taiwan
T: 886-7-5612311
E: business@twport.com.tw
Key staff
Chin-Jung Wang, Vice President and CEO
Directors
Hsien-Yi Lee, Chairman | Shao-Liang Chen, President
CORPORATION, LTD.
https://kl.twport.com.tw/en/
No.1, Chung-Cheng Road, Keelung 202202, Taiwan
T: 886-2-24206100
E: business@twport.com.tw
Board of Directors
Hsien-Yi Lee, Chairman | Shao-Liang Chen, President
www.polb.com
415 W. Ocean Boulevard, Long Beach, CA 90802 USA
T: 562-283-7000
Key staff
Mario Cordero, Executive Director (mario.coredero@polb.com)
Dr. Noel Hacegaba, Chief Operating Officer (noel.hacegaba@polb.com)
Commissioners
Bonnie Lowenthal, President | Frank Colonna, Vice President | Steven Neal | Bobby Olvera Jr. | Sharon L. Weissman
PO Box 109, Majuro, MH 96960
Republic of the Marshall Islands
Airport T: 692-247-7612
Seaport T: 692-625-7613
Key staff
Thomas Maddison, Executive Director (tmaddison37@gmail.com)
Directors
Kessai H. Note | Stephen Phillip | Ladie Jack | Larry Hernandez | Anjojo Kabua | Loreen Bigler | Fred Pedro | Biten Lanki | Jerry Nahan
www.npa.ca
Box 131, Nanaimo, BC, V9R 5K4 Canada T: 250-753-4146
Key staff
Ian Marr, President & CEO (imarr@npa.ca)
Jason Michell, Vice President, Business Development (jmichell@npa.ca)
Directors
Michelle Corfield, Chair | Captain Fred Denning, Vice Chair | Phil Dwyer, C.M., J.D. | Shiva Dean | Barbara Coe | Jeet Manhas
www.portofnewport.com
600 SE Bay Blvd, Newport, OR 97365 USA T: 541-265-7758
Key staff
Paula Miranda, General Manager (pmiranda@portofnewport.com)
Aaron Bretz, Director of Operations (abretz@portofnewport.com)
Commissioners
Gil Sylvia, President | Kelley Retherford, Vice President | Walter Chuck, Secretary/ Treasurer | Jeff Lackey | Pat Ruddiman
POHNPEI PORT AUTHORITY
www.ppa.fm
P.O. Box 1150, Kolonia, Pohnpei State 96941 Federated States of Micronesia T: 691-320-2793
Key staff
Grilly Jack, General Manager (grilly.jack@ppa.fm)
Directors
Limanman Helgenberger, Chair | Quincy Lawrence, Vice Chair | Brandon Tara, Secretary | Sihna Lawrence | Joseph Saimon | Aurelio Joab | MaryAnn Eperiam
www.papa-appa.ca
2750 Harbour Road, Port Alberni, BC, V9Y 7X2 Canada
Telephone: 250-723-5312
Key staff
Zoran Knezevic, President and CEO (zknezevic@papa-appa.ca)
Mike Carter Vice President of Operations (mcarter@papa-appa.ca)
Directors
Shelley Chrest, Chair | Jeff Cook, Vice Chair | Cynthia Dick | Arne Elias
OF REDWOOD CITY
www.redwoodcityport.com
675 Seaport Boulevard, Redwood City, CA 94063-5568 USA
T: 650-306-4150
Key staff
Kristine Zortman, Executive Director (kzortman@redwoodcityport.com)
Rajesh Sewak (rsewak@redwoodcityport.com)
Linda Alvarado (lavarado@redwoodcityport.com)
Commissioners (Note: as of July 31, 2024)
Lorianna Kastrop, Chair | Stan Maupin, Vice Chair | Nancy C. Radcliffe, Secretary | Richard Claire | Ralph Garcia
www.portofsandiego.org
P.O. Box 120488, San Diego, CA 92112-0488 USA T: 619-686-6200
Key staff
Joe Stuveysant, President/CEO (jstuveysant@portofsandiego.org)
Robert “Bob” DeAngelis, VP/CFO (rdeangelis@portofsandiego.org)
Michael LaFleur, VP / Maritime (mlafleur@portofsandiego.org)
Commissioners
Frank Urtasun, Chair | Danielle Moore, Vice Chair | Ann Moore, Secretary | Dan Malcolm | Gilanthony Ungab | Sid Voorakkara | Michael Zucchet
www.portofskagit.com
15400 Airport Drive, Burlington, WA 98233 USA
T: 360-757-0011
Key staff
Sara Young, Executive Director (sara@portofskagit.com)
Commissioners
Dr. Kevin E. Ware | Steven Omdal | Mahlon Hull
www.portofstockton.com
PO Box 2089, Stockton, CA 95201 USA
T: 209-946-0246
Key staff
Kirk deJesus, Director(kdejesus@stocktonport.com)
Katie Miller, Deputy Port Director, Administration(kmiller@stocktonport.com)
Jason Katindoy, Director of Maritime & Real Estate (jkatindoy@stocktonport.com)
Jeff Wingfield, Deputy Port Director, Regulatory & Public Affairs (jwingfield@ stocktonport.com)
Commissioners
William R. Trezza, Chair | Stephen Griffen, Vice Chair | R. Jay Allen | David B. Atwater | Anthony Barkett | Michael Patrick Duffy | Allen Sawyer | Margaret Shea Stephens|
https://tc.twport.com.tw/en/
No.2, Sec. 3, Zhongqi Road, Wuqi Dist., Taichung City 43501 Taiwan
T: 886-4-26562611
E: business@twport.com.tw
Key staff
Rung-Tsung Chen, President of Taichung Port Board of Directors
Hsien-Yi Lee, Chairman | Shao-Liang Chen, President
www.portsauthoritytonga.com
P.O Box 144, Vuna Road, Ma’ufanga, Nuku’alofa Kingdom of Tonga
T: (+676)23168
Key staff
Alo Maileseni, CEO (alo.maileseni@tongaports.to)
Directors
Dr. Ngongo Kioa, Chair | Michael Bloomfield, Deputy Chair | Toimoana Takataka | Fakahau Valu | Sione Havea Taione | Soakai Motuapuaka | Etuate Sakalia
www.portofumatilla.org
PO Box 879
Umatilla, OR 97882 USA
Telephone: 541-922-3224
Key staff
Kim B. Puzey, General Manager (kimpuzey@uci.net)
Commissioners
Jerry Simpson | Jason Middleton | Jerry Baker | Jerry Imsland | Robert J. Blanc
www.valdezak.gov/151/Port
PO Box 787
Valdez, AK 99686 USA
T: 907-835-4564
Key staff
Jeremy Talbott, Ports & Harbor Director (jtalbott@valdezak.gov)
Commissioners
Stu Hirsch, Chair | Tim Bouchard | Trevor Milch | Alan Steed | Colleen Stephens | Mark
Swanson | Andrea West
Larry Aikins
Hugh Anderson
Mike Avent
Walt Barham
Elizabeth Blanchard
Dan Buell
Antonio Camacho
Jack Chong-Gum
Bill Clark
Mario Cordero
Jack Castle
Stanley Daily
Richard Dodge
Thomas Fujakama
Mike Giari
Byron Hanke
Dave Hunt
Bob Jennings
Joe Johnson
Ieske Iehsi
Frank Kitchell
Stan Kurowski
Robert Larson
Susan Lew
Ken Maddison
Brad Madelung
Chris Marshall
Fugo Matsuda
Robert McCrorie
Edward Millan
Lewis Miller
Bill Mills
Robert Penner
ASSOCIATION OF BC MARINE INDUSTRIES
www.abcmi.ca
201 – 2527 Beacon Avenue, Sidney, BC V8L 1Y1 Canada
T: 778-430-2264
Alex Rueben, Executive Director (alex@abcmi.ca)
GREEN MARINE
www.green-marine.org
Quebec, Canada: Véronique Trudeau, Program Manager T: 418-558-9832 / E: veronique.trudeau@green-marine.org
Seattle, USA: Eleanor Kirtley, Senior Program Manager
T: 206-409-3943 / E: eleanor.kirtley@green-marine.org
Lisa Pomasl
Dr. Claire Poumele
Melvin Shore
Patrick Trapp
Lonnie Washington
Don White
Miriam Wolff
James Wright
John Chung-Chuang Wu
INLAND RIVERS PORTS & TERMINALS
www.irpt.net
4625 Lindell Boulevard, Suite 200-#2179, St. Louis, MO 63108 / T: 618-468-3010
Aimee Andres, Executive Director (aandres@irpt.net)
www.interferry.com
Canada: Mike Corrigan, CEO T: 250-888-0215 / E: mike.corrigan@interferry.com
Sweden: Johan Roos, Director of Regulatory Affairs
T: 46-707-930790 / E: johan.roos@interferry.com
INTERNATIONAL ASSOCIATION OF MARITIME AND PORT PROFESSIONALS
www.iampe.org/ | PO Box 2729, South Portland, ME 04116 USA | Telephone: 318-471-0534
Eric Gilmore, Director of Business Development (eric.gilmore@iampe.org) | Captain Jeffrey Monroe, Director of Education (jeffrey.monroe@iampe.org)
www.adelte.com
Headquarters: Avenida Josep Tarradellas nº20, 4th Floor
08029 Barcelona Spain
USA office: 405 Atlantis Rd, Building A, Suite 206
Cape Canaveral, FL 32920
E: asivilla@adelte.com
Key contact
Martin Westphal, Group Marketing Director (mwestphal@adelte.com)
www.albionmarine.com
Suite 304 – 800 Carleton Court Delta, BC V3M 6Y6 Canada
T: 604-529-8488
Key contacts
Sergiy Yakovenko, Director (sergiy.yakovenko@ albionmarine.com)
www.amibrokers.com
J&G Commercial Center
Suite 113F, 215A Chalan Santo Papa Street, Hagatna, Guam 96910
Mailing address: P.O. Box 2797, Hagatna, Guam 96932 USA
T: 671-477-2632 / 671-477-2642
Email: contact@amibrokers.com
Key contacts
Annmarie Muna, President & General Manager (amuna@amibrokers.com)
Tricia Granillo, VP/Marketing Manager (tgranillo@amibrokers.com)
www.thebeckettgroup.org
8715 Randall Dr NW, Gig Harbor, WA 98332 USA
T: 253-905-8904
Key contact
Jeannie Beckett, Principal (jbeckett@thebeckettgroup.org)
LLP
www.bbklaw.com
300 South Grand Ave, 25th Floor
Los Angeles CA 90071 USA
T: 213-787-2569
Key contact: Ruben Duran (ruben.duran@bbklaw.com)
www.burnsmcd.com/
733 Bishop Street, Honolulu, Hawaii 96813-4014 USA
T: (808) 780-1854
Key contact
Derek Chow, Pacific Islands Business Development Manager (djchow@burnsmcd.com)
www.oregon.gov/biz
775 Summer St NE #200, Salem, OR 97301 USA
T: 503-949-1710
Key contact
Margaret Barber, Ports Program Coordinator (Margaret. BARBER@biz.oregon.gov)
AND TECHNOLOGY, INC., PBC
www.eaest.com
2200 6th Ave #707, Seattle, WA 98121 USA
T: 206-452-5350
Key contact
Richard Price, Program Manager (rprice@eaest.com)
PO Box 914, Kolonia, Pohnpei, VM 96941
T: 510-231-2200
Key contact
Freddy Olter (freddy.olter@gmail.com)
www.fortisbc.com
16705 Fraser Highway Surrey, B.C. V4N 0E8 Canada
T: 604-576-7000
Key contact
Sarah Smith, Director, Low Carbon Transportation & LNG Business Growth (sarah.smith2@fortisbc.com)
www.globalterminals.com
Head Office: 400 – 2925 Virtual Way Vancouver, BC V5M 4X5, Canada
T: 604-267-5200
Email: info@globalterminals.com
Key contact
Jennifer Perih, Manager, Corporate Affairs (jperih@ globalterminalscom)
www.hknal.com
140 Fenchurch Street
London, UK EC3M 6BL
T: +44 (0) 207 782 0537
Key contact
DAlan Rixon, Head of International (arixon@hknal.com)
www.kongsberg.com
1598 Kebet Way
Port Coquitlam, BC V3C 5M5 Canada
T: 604-464-8144
Key contact: Konrad Mech, Sales Director – Coasts, Ports, Inland Waterways (konrad.mech@km.kongsberg.com)
LAW OFFICE OF ALAN K. GOLDSTEIN
www.alankgoldsteinlaw.com
P.O. Box 2595
Napa, CA 94558 USA
T: 415-870-5127 and 314-609-3404
Key contact
Alan Goldstein, Attorney and Owner (alan@ alankgoldsteinlaw.com)
www.liebherr.com
15101 NW 112th Avenue, Hialeah Gardens, FL 33018 USA
T: 305-817-7500
Key contacts
Torsten Paas (Torsten.paas@liebherr.com)
Jonathan Luikens, Senior Sales Manager (jonathan.luikens@liebherr.com)
www.liftech.net
344 20th Street #360, Oakland, CA 94612-3593 USA
T: 510-832-5606
Key contacts
Erik Soderberg, President, Principal (esoderberg@liftech.net)
Sugiarto Loni, Principal (sloni@liftech.net)
www.lynker.com
West Coast and Pacific Office: 740 Moowaa Street, Suite G, Honolulu, HI 96817 USA
Corporate Headquarters: 202 Church Street, SE / Suite 536, Leesburg, VA 20175 USA
T: 855-596-5371
Key contact
Sarah Pautzke, Scientist (spautzke@lynker.com)
PO Box 1018, Majuro, MH 96960 RMI
T: 692-625-3369
Key contact
Charles Stinnett, Managing Director (charles@mstcormi.com)
LTD
www.marineandcivil.com.au
U9/41-43 Higginbotham Rd Gladesville, NSW 2111 Australia T: 1800-000-626
Key contact
Blane McGuiness, Executive Manager – Engineering (blanem@marineandcivil.com.au)
www.marinelabs.io
4470A Markham Street Victoria, BC V8Z 7X8 Canada
T: 778-817-1198
Key contact
Scott Beatty, CEO (scott.beatty@marinelabs.io)
Colin Bishop, Sales Engineer (colin.bishop@marinelabs.io)
www.motcmpb.gov.tw
No.1, Ln. 1, Sec. 3, Heping E. Road, Da’an Dist., Taipei City 10669, Taiwan
T: 886-2-8978-2790
Key contacts
Ms. Wu (ljwu@motcmpb.gov.tw)
Mr. Chang (jwchang01@motcmpb.gov.tw)
Hsieh-Lung, Yeh, Director-General –director@motcmpb.gov.tw)
www.matson.com
Guam: 1026 Cabras Hwy, Suite 115, Piti, Guam 96925
T: 671-475-5961
Honolulu: 1411 Sand Island Pkwy, Honolulu, HI 96819 USA
T: 808-848-1211
Key contacts
Vic Angoco, Sr. Vice President, Pacific Region (vangoco@matson.com)
Lek Friel, Container Operations Manager (lfriel@matson.com)
www.northerneconomics.com
PO Box 110914
Anchorage, AK 99511-0914 USA
T: 907-274-5600
Email contact form: https://northerneconomics.com/ contact
Key contact
Marcus Hartley, President and Principal Economist
Mike Fisher, Vice President and Principal Consultant
www.pashagroup.com
4040 Civic Center Drive, Suite 350 San Rafael, CA 94903 USA
T: 415-927-6400
Key contact
President & CEO — George Pasha, IV (about@pashanet. com)
www.pavementtechnicalsolutions.com
Main office: 43133 Huntsman Square, Ashburn, VA 20148
T: 703-858-5875 / E: ptsvirginia@pavementtechsolutions.com
Hawaii: 94-1221 Ka Uka Boulevard, #108, Box #321
Waipahu, HI 96797
T: 808-672-2690 / E: ptshawaii@pavementtechsolutions.com
Key contact
Brian Orandello, President/CEO
www.pm-bm.com
Grand Montreal area, Canada
T: 438-825-1234
Key contact
Emmanuel Polman (emmanuel.polman@pm-bm.com or info@pm-bm.com)
www.reidmiddleton.com
728 134th St SW #200, Everett, WA 98204 USA
T: 425-741-3800
Key contact
Willy Ahn, Ph.D, PE, LEED AP, Director, Waterfront (wahn@ reidmiddleton.com)
LLC.
www.schraderco.com
514 State Ave Suite 202, Marysville, WA 98270 USA
T: 425-377-1550
Key contact
Tom Spear, Principal (tom@schraderco.com)
SEEN SAFETY
www.seensafety.com/
14451 Cornerstone Village Dr., Suite 120
Houston, TX USA 77014
T: 972-532-1892
Key contacts
Hamish Clark, President (hamish@seensafety.com)
Heather Lucas, Head of Operations
T: +64-21-243-1536 | E: heather@seensafety.com
www.shey-harding.com
PO Box 67, Seal Beach, CA 90740 USA
T: 562- 799-8854
Key contacts
Susan Dvonch, Managing Partner (sue@shey-harding. com)
Jeff Dvonch, Partner (jeff@shey-harding.com)
www.ssamarine.com
1131 SW Klickitat Way, Seattle, WA 98134 USA
T: 206-623-0304
Key contact
Joe Carrillo, SSA Pacific-Northern California operations (Joe.Carrillo@SSAMarine.com) - Direct: 209-420-5693
www.transmountain.com
General Inquiries About the Pipeline System or Expansion Project
T: 866-514-6700
E: info@transmountain.com
Key contact
Corporate Office and Reception
T: 800-535-7219
PO Box 99, Chuuk, FSM 96942
T: 691-330-2143
Key contacts
Myron Hashiguchi, President/CEO (transco@mail.fm)
Gideon Bisalen, General Manager (transco@mail.fm
www.tynebridge.ca
5634 Westhaven Court West Vancouver, BC V7W 1T6
T: 778-990-7626
Key contacts
Robert Hedley, President (robert.hedley@tynebridge.ca)
Ben Thompson (ben.thompson@tynebridge.ca)
www.preservedwood.org
12503 SE Mill Plain Blvd #205, Vancouver, WA 98684 USA
T: 360-693-9958
Key contacts
Ryan Pessah, Director of Government Relations (ryan@ wwpi.org)
Jeff Keller, Executive Director (jeff@wwpi.org)
When Executive Director
Gary Nelson decided it was time to retire after 24 years at the helm of the Port of Grays Harbor, the Commission needed to look no further than their Deputy Executive Director to fill the role. Leonard Barnes, an employee of the Port for nearly 40 years, has the experience, the knowledge, and, most importantly, the passion to take the Port to new heights. These leadership qualities are further strengthened by his respect and admiration for his team who themselves enjoy a long tenure at the Port. Indeed, the sum of Barnes’ attributes coupled with those of his staff, have provided for a formula of success that ensures the growth of the Port for many years to come.
PP: Congratulations on your recent appointment to Executive Director. Could you provide an overview of your history with the Port, highlighting the responsibilities and strengths you bring to the role?
LB: I started with the Port on December 1, 1984, in operations —vessels, labor, customers, that type of activity — and worked my way up to become manager of all marine terminal activity. From there, I was asked to take over the real estate portfolio where I oversaw all of the real estate operations. Eventually, I became Director of Operations, overseeing all operations, including marine terminals, security, labor contracts, real estate, even some of the marina operations. And from there, I took on the role for trade development, which entailed travelling abroad to places like Japan, Korea and then into Russia, China, and Europe. I was moved into the position of Deputy Executive Director around 2000 and continued in that position until April 1 of this year when Gary Nelson retired, and the
A large part of our success comes from the diversity of commodities we handle and our strategic location on Washington State’s Pacific Coast.
Commission appointed me to his position. Gary was a great leader whom I admired very much and it’s an honor to continue and build on his legacy.
As for strengths I bring to the position, knowing the history of the Port and its inner workings is certainly beneficial but more than that, I have a passion for what I do and the people with whom I work. We have a great team of people — 58 employees in total. The support we give each other allows us to be as successful as possible. We’re blessed with great staff, including our ILWU labor who are one of the best teams on the West Coast, especially when you consider the diversity of activities we have. They work more per person hours than any other shop on the West Coast of the U.S. according to the annual report from Pacific Maritime Magazine.
PP: That’s a good segue into looking at the background of the Port of Grays Harbor and the cargoes handled, as well as the features that contribute to the Port’s success.
LB: As I said, we’re very diverse. We are the largest exporter of soy meal in the United States; we handle a lot of automobiles as well as military cargo; we export wood chips to British Columbia and logs to China; we have liquid bulk exports such as canola oil, biofuels, glycerin, and methanol. Our Westport Marina is number one for fish and seafood landings in Washington State and ninth overall in the U.S. They ship product out to 70 countries.
A large part of our success comes from the diversity of commodities we
handle and our strategic location on Washington State’s Pacific Coast. Our road, rail, air and deep-water access are second to none. We are less than one hour from Interstate 5; we have two Class 1 railways (Burlington Northern Sata Fe and Union Pacific) linked by Puget Sound & Pacific and including a marine terminal rail system with more than 50,000 feet of continuous loop tracks; ample upland cargo storage facilities; and a 5,000-foot jet-capable runway at Bowerman Airport.
Just before Gary retired, we announced a record year in 2023, and it looks like 2024 is tracking for records on all fronts.
PP: You currently have a number of major redevelopment projects underway. Could we spend some time looking at these?
LB: For starters, we have the Terminal 4 Expansion & Redevelopment Project. This is being done in partnership with AG Processing (AGP), the Port, and
funding from both state and federal governments. It will double AGP’s current capacity for exporting soybean meal, recognizing the growing demand for both protein and renewable fuel.
At present, AGP exports about three million metric tons of soybean meal out of Terminal 2. They are a leader in processing soybeans in the Midwest and bring meal to the Port by rail (both BNSF and Union Pacific) where it is exported to places like the Philippines, Indonesia, Australia and other countries in the Asia Pacific, as well as providing biofuel demand in both domestic and international markets.
AGP will continue to export out of Terminal 2 — in fact, they recently invested about $60 million into their existing facility — but they are investing $170 million into a new bulk agricultural transload facility at Terminal 4 that will double their current exports. We refer to this part of the project as T4B.
The other part of the project — Terminal 4A — is being developed by the Port and includes the construction of new rail to support offloading,
storage and assembly of unit trains to accommodate rail traffic to AGP’s T4B facility. We’ll also be redeveloping 55 acres of an old pontoon casting basin to provide for more cargo storage and laydown space, constructing secured access and roadway improvements as well as upgrading fendering and stormwater systems. There are two berths so, in addition to AGP’s dedicated berth, we’ll also be able to continue to
accommodate our other partners that traditionally use T4.
In terms of timing, we should be starting construction by the middle of July this year and expect the project to be completed by the beginning of 2026. It’s estimated that this project alone will create more than 80 longterm jobs.
I think it’s important to stress the significance of the partnerships
Westport Marina is very important to the Port of Grays Harbor but also to the community at large. The number of jobs and the economic development that is created by this relatively small footprint is significant.
involved with this project. In addition to AGP and both Class One rails, we’re also working with the Genessee and Wyoming Railroad to link the Port to the main lines and, of course, the relationship we have with the ILWU is incredibly important to us, as is the support we receive from our very diverse customer base.
PP: Another project (featured in the July 2023 issue of Pacific Ports Magazine) is the Westport Marina Modernization Project. I’ll refer readers to this article for the main components of the project, but can you provide an update?
LB: As you learned last year, this is a multi-phase project that will replace old docks with wider slips to better accommodate the size of fishing vessels we’re now seeing. The Marina was originally built for 40-foot trawlers but
vessels arriving from the South Pacific are now double, and sometimes triple, that length. Our first priority is the South Marina, followed by the Mid Marina and then the North Marina.
Westport Marina General Manager Molly Bold and her team are working on strategies that align with the funding as it gets confirmed. They’re a tremendous team and we’re all committed to the project. The phased approach gives us flexibility to address different sections of the Marina as the funding presents itself. Last year, we received funding from the Community Project Funding Grant secured by Congressman Derek Kilmer which allowed us to get underway with procuring the preliminary design. Coupled with the Port’s matching funds and a $1M grant from the Washington State
Recreation Conservation Fund, we are able to work on a new abutment, 80-foot gangway and 14 slips for recreational users.
Westport Marina is very important to the Port of Grays Harbor but also to the community at large. The number of jobs and the economic development that is created by this relatively small footprint is significant. We service vessels from over 70 countries and the docks are full — we’re talking about hake, tuna, shrimp, Dungeness crab, salmon — and we have even more vessels that want to come in.
PP: You’ve also got the day-to-day additional components of the Port — the commercial docks, Bowerman Airport, and industrial and commercial properties. Could we spend a bit of time looking at those?
LB: Let’s start with the Satsop Business Park. We inherited that site in 2013 from the Grays Harbor Public Development Authority — it was an unfinished nuclear power plant. We hired Alissa Shay to be the General Manager on Day One and she has
done an amazing job transforming the area into a 1,800-acre mixed-use business and technology park complete with all the utilities needed for manufacturing, warehousing and distribution operations.
The Park is surrounded by 1,200 acres of sustainably managed forest and we partner with Grays Harbor College (GHC) to help with their Forestry Program. They do everything to manage the land and we let the class hold timber sales once or twice every year. We also have a CDL (Commercial Driver’s Licence) Truck Program done in partnership with GHC, and then there’s the Laborer’s Union at the Park that provides training. Alyssa is really good at putting the Park’s assets to use in terms of creating jobs and opportunities for our communities.
Looking at Bowerman Airport, this used to be a military airport during World War II before the Port of Grays Harbor took over sole ownership and control in 1962. It has a 5,000-foot runway that is the only jet-capable runway on Washington’s Pacific Coast. It has full amenities, including Jet A and 100LL fuel services available 24 hours a day plus hangars for rent and U.S. Customs for flights coming in from other countries. We also recently added Life Flight (or air ambulance) services for emergency needs within the many small communities up and down the coast.
We already talked about the Modernization Program underway at Westport Marina which focuses on upgrading infrastructure, but this is also an important facility for public access. Friends Landing offers camping and RV spots along with access to both the Chehalis River and Lake Quigg, as well as a park for kids. We continue to enhance the assets we have there for both the community as well as the tourism industry. There are some great viewing spots where people
...we work well as a team and can attribute our success to our diversity and commitment to growth that everyone shares including our current
can see the fishing vessels and ships coming and going. It was actually in the early 1990s that one of our commissioners came up with the vision of getting the community closer to the water, so we found a place right next to the river channel.
In addition to the ships, they get to see the big tractor tugs in operation. These are state-of-the-art tugs moving our ships in and out. On that point, I should note that we are one of the few ports in the U.S. with bar pilots who are port employees. We worked with state legislators many years ago to put that in place.
PP: You’ve just mentioned your Commission and we haven’t discussed them yet. Could you provide some information about them and their importance to the vision for PGH.
LB: We have three elected commissioners on six-year terms representing different districts within our county. One thing that works to our benefit
customers.
is their longevity in serving the community — it provides for consistency in direction and vision. That’s a reflection of their efforts in meeting the goals of the community and making the right policy decisions which they do by engaging the public on the issues. They’re great leaders who are patient when it comes to moving through the process of creating that vision. And, most importantly, they provide good guidance for our executive team.
Whether it’s Westport Marina or Satsop Business Park or Bowerman Airport, we work well as a team and can attribute our success to our diversity and commitment to growth that everyone shares, including our current customers. I think that’s very important. You take care of those who have invested in the community and are creating jobs and economic opportunities.
To mark their 50th anniversary, the Pacific Coast Congress of Harbormasters and Port Managers (PCC) are not only reflecting on their legacy but are deep in the throes of planning for the next 50 years. With recently elected President Scott Grindy providing an energized message to the membership, calling for “nothing short of a remarkable future”, PCC is poised to strengthen not only the Association, but the industry as a whole.
Established in 1974, the PCC started with a small group of seven people who recognized the importance of providing a forum for commercial and recreational marina and port professionals to promote the development and growth of the industry through communication, education, and professional certification. Since that time, the PCC has grown to represent over 150 members hailing from all parts of the North American West Coast — from Alaska, British Columbia, Washington, Oregon, and California.
“The diversity of our members is our strength,” he said. “From newly hired staff to senior directors; from industry sectors such as management of recreational marinas, cargo/breakbulk terminals, to property development, and harbor/port activities, it’s a great family of friends that make up PCC. There is not one harbor or port that you can visit that doesn’t have something new to share.”
Grindy went on to say that “Over the past 50 years, PCC has continued its strong membership base with activities that engage in ways that help improve member collaboration, teamwork, and just having a colleague to confer with from a neighboring harbor to hundreds
“Over the past 50 years, PCC has continued its strong membership base with activities
that engage in ways that help improve member collaboration [and] teamwork..."
of miles away,” he said, adding that “we are a diverse international team of harbormasters, managers, directors of various ports and marinas focused on sharing best practices, learning new innovations of technology and related harbor equipment to support our maritime industries and customers.”
As Harbor Master for the San Francisco Marina Small Craft Harbor, falling under the jurisdiction of the San Francisco Recreation and Park Department, City & County of San Francisco, Grindy describes his involvement with PCC as “one of the best networking opportunities I have been a part of in all of my various maritime adventures.”
While his 30+year professional career has not always been in the marine sphere, he credits his current success as the culmination of experiences in other areas — management of personnel, major capital projects, facilities management, capital and operational budgets, public works, building and engineering design, risk management, safety, and emergency operations to name just a few. “I was running facilities for two Washington State-area colleges as well as the University of Washington for years before coming into the maritime side. Scott also taught evening college courses in engineering and vocational licensing programs for almost twenty years. I think the simplest way to put it is that every one of those skills is something you deal with in the harbors, whether
it be the water, the plumbing, the electrical, etc. Whether it’s a high-rise building or a dock with power, there are commonalities that I’ve been able to apply in my current role.” Indeed, Grindy’s activities in San Francisco Bay run from managing two harbors with numerous international sailing events, recreational and commercial fishing, to monitoring activities in over 50 recreational marinas.
For his work with the PCC, Grindy is especially proud of the way the Association maintains its focus on professional development and networking activities. In addition to the Barbara Schwantes Memorial Fund Scholarship Grant (named after the PCC’s first Executive Secretary) that supports individuals entering a post-secondary
program in a marine-related field or a project that contributes to making a difference in coastal regions (for example, children’s boating safety and education or community marine outreach programs), the PCC has a very active Training and Education Committee, bringing together experienced leaders to identify existing and create new training opportunities for members. The committee provides conference content, webinars, group discussions, and partnerships that can help those in the marine industry expand their knowledge and operate high-quality facilities.
The PCC also has agreements with the University of Alaska Southeast, University of Washington, and the Association of Marina Industries to provide training and certification in areas directly related to harbor management, including Certified Marina Manager/Operator, Clean and
Resilient Marina Professional, Basic Marina Management.
The third — and perhaps the most relevant activity that advances PCC’s goals — is the organization of two industry conferences per year. “We rotate the location of the conferences — one in the spring and another in the fall — between Alaska, B.C., Washington, Oregon, and California. They provide excellent opportunities for reconnecting with colleagues and peers, learning new information together and learning from each other,” Grindy said, noting that the next conference will be held in Victoria, British Columbia, October 28 to 30, 2024. Information about the conference is available on the PCC website at www.pccharbormasters.org
Sessions at the upcoming conference already identified include marina/harbor maintenance, electrical upgrades, succession planning, and opportunities for members to highlight their own
issues as well as hear from others who may have experienced the same thing and are able to offer a solution. When it comes to developing the agenda for the conference, Grindy was quick to point out some of the common issues that are trending throughout the industry will no doubt be raised. “Recruitment and training, and cybersecurity are just two areas that come to mind,” he said.
Looking to the next 50 years, Grindy reported that the PCC Board was working on a new strategic planning document that would provide new focus and new energy for the Association. “Having a mission with specific goals is so important for a member-centric group and the Board is already gearing up for the lively conversations that will result in a path forward for the future.”
To learn more about the Pacific Coast Congress of Harbormasters and Port Managers, visit www.pccharbormasters.org.
By Adam M. Sowards (as published in Salish Current)
When Kevin Morse started out as CEO of Cairnspring Mills in Burlington, he traveled frequently to find customers. He toted bags of flour in his backpack, and at airports Transportation Security Administration officers routinely pulled Morse aside.
“What is that, sir?”
“That’s flour.”
“Why are you carrying flour in a Ziploc bag?”
“I’m a miller.”
“What’s a miller?”
“Millers make flour.”
These TSA officers could be forgiven their ignorance. Around 150 years ago, more than 23,000 flour mills operated in the United States. Today, that number has fallen below 200, and five companies control about 80% to 85% of the milling capacity, according to Morse.
“Most of the world still thinks flour is a ubiquitous white substance that should be cheap,” said Morse. “And they don’t understand there can be a difference.”
A broad effort in Skagit County is developing a small-scale, local and resilient grain system that helps farming communities while producing better flour.
Craft beers, coffees and chocolate exist as growing parts of their markets. Why not flour?
That is what Cairnspring Mills is doing.
“We’ve been eating stuff that’s on a shelf in a bag and never even questioned where it came from. Never expected it to have flavor or ‘terroir’ or story. Never knew how it was growing,” said Morse.
Flour can be a way to reset people’s assumptions around food and farming.
The work in Skagit exemplifies efforts to rebuild local, regenerative food systems with sustainability and resilience at the core, all while increasing profits.
The enterprise involves local government, farmers, millers, bakers and others, including consumers willing and able to pay a premium for high-quality, locally grown and processed flour.
Morse is quick to point out the mill was not his idea.
More than a decade ago, the Port of Skagit, local farmers, the Washington
State University Bread Lab and others considered how best to sustain agriculture in the Skagit for at least another century.
They identified value-added grains as one potential avenue to ensure agriculture continues to be economically viable. The port started focusing on value-added agriculture in 2010.
The port serves as an economic engine and invests in publicly owned infrastructure to support resilience and economic opportunity for industries, including value-added agriculture.
The Port of Skagit built malting and milling facilities, including the
only publicly owned granary in Skagit County in 2016.
According to a port document, this grain-processing infrastructure ensures “greater economic certainty for the diverse grain producers in our region.”
“These are ways to add value to these lower-value crops and contribute to the long-term vitality of the farmers,” said Morse.
Without the port, launching Cairnspring Mills would have been slower or would not have happened at all.
“The port has been such a great partner. They’ve helped us invest, build, lease back all of the equipment,” said Morse. “It’s really a public asset.”
This infrastructure is essential for Cairnspring Mills’ scale of operations, a scale that serves a different purpose than the large industrial systems where the vast majority of flour originates.
“One mill in Arlington, Texas, will make six to seven million pounds of flour in one day,” said Morse. “We made six million pounds last year
The port serves as an economic engine and invests in publicly owned infrastructure to support resilience and economic opportunity for industries, including valueadded agriculture.
running two shifts a day five days a week.”
What is needed for the local scale is infrastructure for storage, processing and distribution in what is sometimes known as the messy middle.
Morse prefers the “remarkable middle” or “magnificent middle,” because at this scale, Cairnspring Mills “can deliver traceability, cleanliness, identity preservation, quality and story that none of the big mills are set up to do,” said Morse.
The commodity system that dominates the flour market — and so much else of the food system — makes it difficult to break into the business or maintain local agricultural identity.
When selling into the commodity stream for mass-produced flour, a farmer trucks wheat to a grain elevator which sells it to another, larger grain
elevator, that sends it on to a large flour mill. At each step, the story of that crop and that farmer disappears into a bland, indistinguishable product. Meanwhile, farmers capture a smaller and smaller part of the value at each stage.
What is happening in Skagit is preserving that story and that value.
“We’re still operating at a human scale. I still know every farmer we source from. We walk every farm, every year,” said Morse.
The port along with other investors made this local, small-scale operation possible.
Morse counts 70 impact investors who are patient and “want to see us change the system and disrupt it for the better.”
This approach allows for more stability, too. Last summer, Skagit Valley
Malting abruptly closed and filed for bankruptcy in the fall.
“By the Port owning it, when unfortunate things happened at the malting company, it didn’t get cut up and sold off in pieces and parts,” said Morse. “It stayed here in the community. We were able to lease it and, frankly, stay in business.”
Overall, the investments have been successful enough that the port is planning to expand its granary. Its first phase is to install a grain dryer and conveyance infrastructure to move the grain, followed later by more silos for storage.
The port requested $500,000 from the legislature for the expansion and received $125,000 in this year’s supplemental capital budget. It is not yet clear how the port plans to make up the shortfall, but Morse said, “We’ve always been scrappy here, and we figured out how to get things done with a little bit of money.”
The port is looking “at all tools in the toolbox,” said Linda Tyler, Port of Skagit communications director. “The Port is very committed to the project and finding ways to fund it.”
Once the expansion is completed, the port’s granary will increase its capacity for finished product by 40%.
That will help Skagit farmers, who provide 70% of the wheat heading to Cairnspring Mills.
“I love growing wheat,” said Michael Hughes, a partner in Hughes Farm. “I enjoy the plant. I enjoy watching it grow. I enjoy harvest.”
Its value remains lower than other crops such as potatoes, so wheat is only one part of the Hughes Farm operation. “Partnering with companies like Cairnspring is getting me closer to being able to consider myself a wheat farmer,” said Hughes, “and that kind of makes me happy.”
Although more famous for tulips and potatoes, Skagit Valley has an excellent climate for growing wheat.
Yields there are about double the national average and do not require supplemental irrigation, said Hughes. The wheat also produces particularly nutritional and flavorful flour.
Farmers have grown grains in Skagit Valley since they diked and drained the deltas in the late 19th century. But much of the time, farmers “are just hoping to cover the costs” of growing wheat, said Hughes.
As a cover crop, wheat returns organic matter to the soil, protects the ground from erosion and works as weed control. When farmers plow it back into the ground, they may receive only the indirect economic benefit of an improved potato harvest.
Farmers receive higher economic benefits when they grow for the commodity stream. For Skagit farmers that means trucking it to Eastern Washington where it is combined with wheat from elsewhere. But transportation costs are rising. Over the last five years, freight costs have doubled for Hughes Farm to ship their wheat there, eating into their profits.
Local milling opportunities change the economics even more.
Because Cairnspring Mills specializes in regenerative agriculture that demands higher growing standards and practices, it pays farmers a higher premium. Hughes estimated that they receive up to 50% more. And because the mill is in Burlington, transport costs are minimal, which increases the profit farmers keep.
Someone purchasing Cairnspring Mills flour is only “two steps away from the grower,” said Hughes.
Grain growers are increasing in Skagit County in part because of this opportunity.
According to the most recent agricultural census, Skagit County produced more than $3.5 million in wheat and barley across nearly 7,000 acres.
At Hughes Farm, they have expanded their grain growing operation to about half their acreage. This started when canneries left the area two decades ago.
That departure removed a local market for high-value vegetable crops and left farmers in a bind that required adjustments.
This sort of dependence on large corporations is something that Morse thinks harms communities and makes farmers vulnerable.
“As soon as those big guys leave, there’s nobody else there to buy your product,” said Morse.
A locally-sourced, value-added market for wheat adds a layer of resilience to the system.
Today, more people want to know where their food comes from, said Hughes, and Cairnspring Mills helps make that easier.
The evolution of wheat farming and flour milling in Skagit Valley is all about adding value and keeping more of it close to home where customers can see the impact on the land, in the community and even on their tastebuds.
“A big thing for us is getting people’s hands in the dough and giving them the taste and hear the story,” Morse said. “And then they become customers.”
Adam M. Sowards is an environmental writer and historian living in Skagit Valley. He is the author or editor of five books and countless articles and essays.
You can find more information at adamsowards.net.
Thank you to Salish Current (www.salish-current.org/) for their permission to reprtint this article.
By Ryan Pessah, Western Wood Preservers Institute
Over the past few months, Western Wood Preservers Institute (WWPI) has received inquiries about the restrictions on using preserved wood in the Puget Sound from various ports and marinas in the area. After some digging, WWPI found the Salish Sea Nearshore Programmatic Biological Opinion (Biological Opinion) that was published in June of 2022 (use Google to find the report online). Biological Opinions are a programmatic consultation that create the framework for projects in a geographic area to protect and recover imperil species and the ecosystem. In other words, if a project is able to comply with the requirements outlined in the Biological Opinion, it will get expedited approval. Unfortunately, the Biological Opinion places unreasonable restrictions on the use of preserved wood in the Puget Sound. These restrictions will increase the cost of projects in the Puget Sound.
One new restriction is limiting wood pilings to chromated copper arsenate (CCA) or ammoniacal copper zinc arsenate (ACZA). Additionally, all treated wood pilings must be sealed with a wrap or a polyurea barrier. The use of a different preservative or not sealing a treated wood piling is not covered by the biological opinion.
Preserved wood can only be used for substructures that are not in direct exposure to water. The Biological Opinion does not state whether it covers the use of preserved wood products that are sealed and used for other parts of a structure that is in direct exposure to water.
The final restriction in the Biological Opinion prohibits treated wood
Unfortunately, the Biological Opinion places unreasonable restrictions on the use of preserved wood in the Puget Sound. These restrictions will increase the cost of projects in the Puget Sound.
products for decking and the repair or replacement of bulkheads.
Since hearing about these unrealistic restrictions on the use of preserved wood products in the Puget Sound, WWPI has initiated contact with National Oceanic and Atmospheric Administration (NOAA) and the National Marine Fisheries Service (NMFS) to schedule a meeting. The purpose of the meeting will be to get clarification on the ambiguity of the Biological Opinion and provide peer reviewed studies that note the use of preserved wood products will not adversely impact species and the ecosystem.
The Puget Sound is a highly regulated area and has many restrictions on construction activities as well as construction materials. It does not seem likely that other regions in the United States will adopt the unreasonable restrictions noted in the Biological Opinion. However, to ensure that these restrictions do not spread to other parts of the United States, WWPI and other industry partners are ready to advocate for the use of preserved wood products by providing a balanced narrative. If you are looking to start a project in Washington’s Puget Sound, please take some time to review the Biological Opinion.
BNAC Environmental Solutions has spent the last 20 years solving industrial problems with powerful, safe alternatives.
Working with companies like Seaspan, BC Ferries, and Global Container Terminals, BNAC has introduced products that replaced traditional toxic hydrualic fluids, solvents ,caustic cleaners and acids with safe alternative that "Perform and Protect”.
In the dynamic world of the maritime industry, innovation is key to staying ahead. One such groundbreaking development is the introduction of Seascour, a revolutionary product that has been changing the game in maritime safety and environmental awareness.
Developed for BNAC Environmental Solutions’ marine clients, Seascour is a product that effectively removes sea shells, scale and barnacles, including the barnacle root, from internal seawater piping through a simple flushing process. Initially met with skepticism, Seascour was put to the test by Cordova Marine Services Ltd., a company founded by a seasoned marine engineer with over 40 years of experience.
The results were so impressive that Cordova Marine Services arranged to conduct a test on the BC Ferries' Salish Eagle at Long Harbour, British Columbia. The remarkable effectiveness of Seascour in dissolving and removing barnacle growth, as evidenced by before-and-after photos provided. This organic product has USDA BioPreferred certified approval for disposal into sewers, making it a safe and environmentally friendly solution for maritime maintenance.
Seascour works by breaking down the calcium carbonate of seashells, barnacles, and mussel shells into carbon and CO2 components, preventing regrowth from the same root. It can also be strained of residual shell and barnacle residue and reused multiple times, offering significant cost savings for projects and yards.
Seascour presents itself as a valuable asset for maritime operations seeking efficient and cost-effective solutions. Seascour can be used three or four times, maximizing efficiency when cleaning box coolers and heat exchangers.
As we look towards the future of maritime safety and environmental protection, Seascour stands out as an innovative tool that has the potential to streamline maintenance processes and enhance efficiency. With ongoing developments and collaborations in the pipeline, the possibilities for Seascour in the maritime industry are vast.
Seascour works by breaking down the calcium carbonate of seashells, barnacles, and mussel shells into carbon and CO2 components, preventing regrowth...
It is crucial for industry stakeholders to stay informed and explore the benefits of transformative solutions like Seascour. By embracing innovation and sustainable practices, we can create a safer and more environmentally conscious maritime industry for generations to come.
Let us continue to collaborate and stay connected to harness the full potential of Seascour and other pioneering technologies in maritime safety and environmental protection. Together, we can usher in a new era of excellence in the maritime industry.
For more information on Seascour, visit https://seascourcanada.ca/, or contact Chris Richardson, President, BNAC Environmental Solutions (chris@bnac.ca / 604-780-3020).
Come this September 17 to 19, Port Alberni’s vibrant port will take centre stage as it hosts the Ports Canada annual conference — a momentous occasion that will showcase the town’s unique blend of economic growth and incredible natural beauty.
Ports Canada will welcome over 200 leaders and experts from the global and Canadian maritime sector. The only Canadian annual conference dedicated to port business and issues, delegates come to make valuable connections and to keep abreast of latest technologies and marine policies. The two-day program will feature insightful keynote presentations from global speakers, a tradeshow, panel discussions and several networking events set against the backdrop of Vancouver Island, consistently named one of the most beautiful places in the world. Located in the heart of Vancouver
The two-day program ... [is] ... set against the backdrop of Vancouver Island, consistently named one of the most beautiful places in the world.
Island, Port Alberni is a town with picturesque harbours, deep roots in industry, and a coastal community on the cusp of rejuvenation. The Alberni Inlet is home to one of the finest deepsea inland harbours on the North American continent and the closest deep-sea port to the Pacific Rim.
The Port Alberni Port Authority's strength comes from it's ability to support a range of local industries, including tourism, forestry and aquaculture. The Dock+, a processing facility and commercial kitchen is a great example of this diversity. Operated by the Port
Alberni Port Authority, it is part of the B.C. regional food hub network and is a shared 17,000-square-foot space, consisting of anchor tenants, a cold storage facility, blast freezer, and ice plant. The facility will embark on a significant expansion in partnership with Nova Harvest Ltd. and Huu-ayaht First Nations Fisheries LP, aimed to be completed in the spring of 2025. Investment and grant funding will enable a 3,000-square-foot expansion, enhancing infrastructure to support local food producers and community partners, including Indigenous groups. The expansion will integrate cuttingedge High-Pressure Processing (HPP) technology, creating new economic
opportunities, boosting local jobs, and positioning Port Alberni as a leader in sustainable seafood processing.
The thriving seafood hub on the waterfront plays an important role in ensuring a resilient local food system in the region and adds economic value to the unique, locally sourced resources that are found in the water and on land.
Each year, a port member of the Association of Canadian Port Authorities has the unique opportunity to run the Ports Canada conference and play host to a celebration of the resilience and growth of Port Authorities across Canada. To showcase the best that Port Alberni has to offer, attendees will enjoy evenings filled with local flavours and cultural experiences, starting with a cocktail evening at the West Coast River Lodge. Here, amidst the tranquil surroundings, guests will savor local culinary delights, sample gin from Antidote Distillery, while networking to the background music of a live musical performance.
This year, the Alberni Pacific Railway (APR) made a nostalgic return to the waterfront, offering scenic train rides that highlight Port Alberni’s waterfront attraction. This diesel locomotive-powered train will traverse a round trip covering approximately 1.3 kilometers, and it is the start of getting back on track for potential future rail expansions. Conference delegates and guests will be treated to a ride on this historic route for a port tour. Another highlight will surely be the cultural reception at the McLean Mill National Historic Site, hosted in partnership with Tseshaht First Nation. All will be treated to a traditional salmon dinner and sample the area’s award-winning craft breweries—a testament to Port Alberni’s community spirit. The conference wraps up
with a celebration night at the Rim Rock Casino, with exceptional food, drinks and if you’re lucky, a win at the slots!
Looking ahead, the Port Alberni Port Authority envisions the Port Alberni Transshipment Hub (PATH) as a transformative project with national implications. PATH has long been envisioned as a modern, fully automated container terminal, able to handle any size vessel. This year has seen renewed interest in this pivotal project that will transform trade dynamics on Vancouver Island and throughout the Pacific Northwest. PATH was recently asked to be nominated by the Conference Board of Canada, as they undertake a national engagement to identify leading-edge projects in the trade-related transportation infrastructure sector. By establishing a modern container terminal in the strategic Alberni Inlet, PATH aims to bolster regional economic resilience, increase sustainability impacts, streamline logistics, and enhance market access.
The trans-shipment hub aims to support container handling facilities in the Lower Mainland and even Puget Sound in Washington State. PATH will service a catchment area of over 13 million people within a 500-kilometre radius, and significantly enable growth and development through its hub-andspoke model. This project will mark a significant step towards sustainable and efficient trade operations in the Pacific Northwest and Asia-Pacific Gateway.
Port Alberni and the Pacific region have tremendous opportunities for maritime partners.
By attending Ports Canada, you will be part of a maritime industry’s premier
event, where you can strengthen connections and make exciting new ones. This is an exceptional chance to showcase your organization to CEOs, directors, and staff from port authorities and other marine community stakeholders. Our Tradeshow offers a dynamic platform to raise your brand’s visibility, connect with industry leaders, and pitch your product or service to potential partnerships. The conference still has sponsorship levels that can optimize awareness of your products and services in front of a targeted audience eager to explore innovations and solutions driving the future of maritime trade. Visit portscanada.ca to learn more.
As the Port Alberni Port Authority prepares to host the Ports Canada 2024 conference, it celebrates its past achievements and looks forward to a future overflowing with opportunities. This gathering will be more than business as usual—it will be a testament to the port’s resilience, diversity, and commitment to sustainable growth.
Port Alberni is thrilled to invite you to experience our beautiful way of living and working along the waterfront, and within our community! Join us in September as we share the town’s scenic beauty, rich cultural heritage, and leading-edge spirit. Discover why this town on Vancouver Island is a beacon of maritime excellence and community pride.
To register or learn more about the Ports Canada 2024 conference, sponsorship and exhibitor opportunities visit portscanada.ca. Follow the Association of Canadian Port Authorities on LinkedIn and @acpa_ aapc on Twitter for the latest updates and insights leading up to this exciting event.
By Gordon Feller, Global Fellow: The Smithsonian Institution, Wilson Center
The U.S. Department of Transportation (DOT) has unveiled three significant notices of funding opportunities (NOFO), marking a pivotal moment in the development of the nation’s transportation infrastructure.
The three competitive grant opportunities are each important: the Fiscal Year (FY) 2025-2026 Multimodal Project Discretionary Grant (MPDG) program, the FY 2023-2024 Consolidated Rail Infrastructure and Safety Improvements (CRISI) program, and the FY 2024 Maritime Administration’s (MARAD) Port Infrastructure Development Program (PIDP) program. Together, they will inject a historic $8 billion in federal funding for the enhancement and construction of the transportation and supply chain network nationwide.
The MPDG opportunity includes funding for these three separate grant programs:
• DOT announced the release of $450 million for the PIDP, which uses federal funding to modernize ports and strengthen supply chains. Specifically, awards will be made to projects that focus on improving the safety, efficiency, or reliability of the movement of goods through ports and intermodal connections to ports. Similar to MPDG and CRISI, the Biden Administration will prioritize projects that advance their goals of climate and sustainability, equity, and workforce development.
• Of the $5.1 billion allocated, $2.7 billion is included for the Nationally Significant Multimodal Freight
Together, they will inject a historic $8 billion in federal funding for the enhancement and construction of the transportation and supply chain network nationwide.
and Highway Projects grants program (INFRA), which awards grants to multimodal freight and highway projects with a focus on improving the safety, accessibility, efficiency, and reliability of the movement of freight and people in and across rural and urban areas.
An additional $1.7 billion is for the National Infrastructure Project Assistance grants program (Mega), which invests in large, complex projects that have national or regional economic, mobility, or safety benefits.
• The final $780 million is allocated for the Rural Surface Transportation Grant program (Rural), which awards funding to similar projects as Mega and INFRA, but is dedicated specifically to projects in rural areas. While the project, applicant, and cost eligibilities all vary by program, DOT will be seeking to make awards under the MPDG opportunity that align with the Biden Administration’s strategic goals to improve safety, economic strength and global competitiveness, equity, environmental justice, and sustainability. Unlike MPDG — which funds a variety of transportation projects — the CRISI program is focused entirely on enhancing the nation’s rail infrastructure. The Federal Railroad Administration (FRA) will administer more than $2.4 billion in awards this
cycle, that will go towards improving railroad safety, efficiency, and reliability, mitigating congestion at both intercity passenger rail and freight rail chokepoints, enhancing multi-modal connections, and building or improving passenger rail corridors. Important projects under this program are those that increase safety, support economic vitality and job creation, and increase capacity and supply chain resilience. The FRA will also fund projects that align with the Biden Administration’s priorities, especially those that explicitly address climate change, gender equity and racial equity. In addition to the funding made available for the CRISI Program, the NOFO includes funds for eligible projects under the Magnetic Levitation Technology Deployment Program (Maglev Grants Program).
Taken together, these grant announcements amount to the largest funding opportunities for transportation investment ever issued by the U.S. Federal government. They offer a massive opportunity for public and private entities looking to make significant improvements to the transportation network, enhance the nation’s supply chain, and expand the capacity for people and goods movement throughout the U.S.
PIDP represents a significant investment in modernizing America’s ports and strengthening supply chains. This initiative is part of a broader effort to enhance the nation’s transportation
infrastructure and improve the movement of goods across the country.
Biden’s team has come to realize that ports play an increasingly crucial role in the U.S. economy, serving as vital gateways for international trade and domestic commerce. They handle over 95 percent of overseas trade by volume and 70 percent by value, making them essential components of the national transportation network. The PIDP funding aims to address several key areas:
• Port Modernization: Many U.S. ports are in need of upgrades to handle larger vessels and increased cargo volumes. The funding will support projects that expand port capacity, improve efficiency, and implement new technologies.
• Intermodal Connections: Enhancing the connections between ports and other transportation
modes (rail, road, and inland waterways) is crucial for efficient cargo movement. PIDP grants can fund projects that improve these intermodal links.
• Environmental Sustainability: Ports are significant sources of emissions and environmental concerns. The program prioritizes projects that reduce port-related emissions, improve air quality, and implement clean energy solutions.
• Resilience: With increasing climaterelated risks, ports need to enhance their resilience to natural disasters and sea-level rise. PIDP funds can be used for projects that strengthen port infrastructure against these threats.
• Improving port safety and security measures is another key focus area for the PIDP grants.
The PIDP grants are available to various entities, including port authorities,
states, local governments, and private companies in partnership with public entities. This broad eligibility encourages collaboration between public and private sectors to address port infrastructure needs.
Some examples of projects that could be funded through the PIDP include:
• Dredging and widening of navigation channels to accommodate larger vessels
• Construction of new berths and wharves to increase cargo handling capacity
• Implementation of automated cargo handling systems to improve efficiency
• Development of on-dock rail facilities to enhance intermodal connections
• Installation of shore power systems to reduce emissions from docked vessels
B On-Dock Rail Support Facility – a $1.57 billion project that will bring new efficiency, speed and sustainability to cargo flow through the port complex. Pictured from left are Dr. Noel Hacegaba, Port of Long Beach Chief Operating Officer; Long Beach Harbor Commissioner Sharon L. Weissman; Long Beach Councilmember Kristina Duggan, 3rd District; Long Beach Councilmember Roberto Uranga, 7th District; Mark Tollefson, Undersecretary, California State Transportation Agency; Long Beach Harbor Commission President Bobby Olvera Jr.; Long Beach Mayor Rex Richardson; U.S. Transportation Secretary Pete Buttigieg; U.S. Rep. Dr. Robert Garcia, California 42nd District; Long Beach Councilmember Megan Kerr, 5th District; Port of Long Beach CEO Mario Cordero; Patricia Aguirre, Board Secretary, International Longshore and Warehouse Union Local 63; Long Beach Harbor Commission Vice President Bonnie Lowenthal; Long Beach Harbor Commissioner Steven Neal; Long Beach Councilmember Al Austin, 8th District; Los Angeles City Councilmember Tim McOsker, 15th District. For more details on the Pier B On-Dock Rail Support Facility, visit page 49.
• Construction of flood protection barriers to improve port resilience
• Deployment of cybersecurity systems to enhance port security
The PIDP aligns with the Biden Administration’s broader goals of improving economic competitiveness, addressing climate change, and promoting equity. By investing in port infrastructure, the program aims to create jobs, reduce supply chain bottlenecks, and support economic growth in port communities.
Moreover, the PIDP complements other DOT initiatives, such as the MPDG program and the CRISI program. Together, these programs form a comprehensive approach to enhancing the nation’s transportation network and supply chain resilience.
The impact of improved port infrastructure extends beyond the immediate port areas. Efficient ports can help reduce transportation costs, lower consumer prices, and improve the
competitiveness of U.S. exports. They also play a crucial role in supporting key industries such as agriculture, manufacturing, and energy.
As global trade patterns evolve and new technologies emerge, the role of ports in the U.S. transportation system continues to grow in importance.
The PIDP funding represents a recognition of this critical role and a commitment to ensuring that U.S. ports remain competitive in the global marketplace.
This $450 million PIDP funding opportunity is a significant step towards modernizing U.S. port infrastructure. By addressing key areas such as capacity, efficiency, sustainability, and resilience, this program aims to strengthen the nation’s supply chains and support longterm economic growth. As ports continue to evolve and adapt to changing global trade dynamics, such investments will be crucial in maintaining the competitiveness of U.S. ports and supporting the broader economy.
Gordon Feller has worked for more than four decades at the intersection of global trade and technology innovation. Upon arriving in Silicon Valley in 1983 he began work, from inside the executive suite, to develop ambitious projects aimed at solving some of the world’s most complex problems. Current and past clients include World Bank, IHS Markit, World Economic Forum, Ford Motor Co. Toyota, The Financial Times of London, The Economist Group, Apple, The Rockefeller Foundation, numerous national governments (Germany, Canada, US), Reuters, and many others. From 2010 to 2017, he served as Director at Cisco Systems HQ. He founded Meeting of the Minds in the 1990s, stitching together a global leadership network which is enabling the adoption of new policies and systems. Gordon was appointed by the Obama/Biden White House to serve on the US Federal Comm. established by The US Congress. He currently serves as a Global Fellow at the Smithsonian Institution. Since 1979, he has published 450+ magazine articles. (Twitter: @GordonFeller)
U.S. Secretary of Transportation Pete Buttigieg and officials from across the nation on July 18 attended a historic groundbreaking ceremony for “America’s Green Gateway,” the Pier B On-Dock Rail Support Facility, a $1.567 billion endeavor that will define the future of cargo movement at the Port of Long Beach.
About 500 people gathered for the event celebrating the project, which will double the footprint of the existing rail yard from 82 acres to 171 acres. Pier B will be built in phases, each enhancing cargo movement, with construction scheduled for completion by 2032. The project will more than triple the Port’s capacity for on-dock rail to 4.7 million twenty-foot equivalent units per year. On-dock rail cargo is moved directly to and from marine terminals by trains, reducing emissions and stress on the local and regional road network.
“Today, work starts on a rail network that triples cargo volume, keeps costs down, and reduces pollution — and it’s all because of the historic funding made possible by the Biden-Harris Administration,” said Buttigieg. “Through projects like America’s Green Gateway and the hundreds of other supply chain improvements we’re making across the country, we’re making our supply chains more robust and resilient in the face of any potential future disruptions.”
“The Pier B On-Dock Rail Support Facility will add 130,000 feet of new tracks, build 36 new support tracks and more than double the number of trains leaving the Port to 17 per day,” said Port of Long Beach CEO Mario Cordero. “These improvements will benefit the entire U.S. supply chain and get us closer to the operational and environmental transformation into a zero-emissions port.”
In recognition of the facility’s importance to the future of the U.S. supply chain, the Port of Long Beach has won $643 million in grant funding from federal, state and local transportation agencies for the project. The federal government alone has awarded $404.1 million, while the state of California has invested $228.8 million and Los Angeles County $10 million. Besides Buttigieg, also in attendance Thursday were members of the U.S. Congress and California Legislature, and officials from various California state agencies, Los Angeles County, L.A. County Metropolitan Transportation Authority and the International Longshore and Warehouse Union.
“The Bipartisan Infrastructure Law continues to deliver for California by modernizing the ports that power our economy, enhancing the reliability and capacity of rail
operations, and creating good-paying jobs,” said U.S. Sen. Alex Padilla (D-Calif.). “This funding is a win for our economy and our environment. The Port of Long Beach’s ondock rail expansion project will slash emissions and reduce air pollution in near-port communities while creating a more efficient gateway into our national supply chain.”
“This project is a homerun for good jobs, clean air, and a strong supply chain,” said U.S. Rep. Robert Garcia, D-Long Beach. “As Mayor, we worked to electrify and green our port, and this major investment will do just that. In Congress, we have fought for this project every single day, and I’m grateful to President Biden and Secretary Buttigieg for investing in Long Beach and the region.”
“This project exemplifies our work to create jobs, cut pollution, eliminate bottlenecks and build a more dynamic supply chain — faster,” said Gov. Gavin Newsom. “California is proud to work with the Biden-Harris Administration on this and other projects that enhance our state’s supply chain while flexing our power in global trade.”
“The investments made by our local, state and federal partners are key to creating this state-of-the-art rail junction, giving shippers even more reasons to choose the Port of Long Beach as their gateway of choice,” said Long Beach Harbor Commission President Bobby Olvera Jr. “This gathering today marks a historic milestone that will bring new jobs and other economic benefits to Long Beach, this state and the nation.”
Buttigieg and other speakers arrived at the event in a passenger rail car transported by Pacific Harbor Line’s Progress Rail “Joule” zero-emissions switcher engine, in a display of the Port of Long Beach’s industry-leading sustainability initiatives.
Port of Alaska (www.portofalaska.com)
American Samoa Port Administration (americansamoaport.as.gov/)
Port of Brookings Harbor, Oregon (www.portofbrookingsharbor.com)
Port of Columbia County, Oregon (www.portofcolumbiacounty.org)
Commonwealth Ports Authority, Northern Mariana Islands (www.cnmiports.com)
Fiji Ports Corporation Limited (https://fijiports.com.fj/)
Port of Grays Harbor, Washington (www.portofgraysharbor.com)
Port Authority of Guam (www.portguam.com)
Honolulu / State of Hawaii Ports
Port of Hualien, Taiwan International Ports Corporation, Ltd. (https://hl.twport.com.tw/)
Port of Hueneme, California (www.portofh.org)
Port of Kaohsiung, Taiwan International Ports Corporation, Ltd. (https://kh.twport.com.tw/en/)
Port of Keelung, Taiwan International Ports Corporation, Ltd. (https://kl.twport.com.tw/en/)
Port of Long Beach, California (www.polb.com)
Republic of Marshall Islands (RMI) Ports Authority, Marshall Islands
Nanaimo Port Authority, BC, Canada (www.npa.ca)
Port of Newport, Oregon (www.portofnewport.com)
Pohnpei Port Authority, Micronesia (www.ppa.fm)
Port Alberni Port Authority, BC, Canada (https://portalberniportauthority.ca/)
Port of Redwood City, California (www.redwoodcityport.com)
Port of San Diego, California (www.portofsandiego.org)
Port of Skagit, Washington (www.portofskagit.com)
Port of Stockton, California (www.portofstockton.com)
Port of Taichung, Taiwan International Ports Corporation, Ltd. (https://tc.twport.com.tw/en/)
Ports Authority Tonga (www.portsauthoritytonga.com)
Port of Umatilla, Oregon (https://portofumatilla.org/)
Port of Valdez, Alaska (https://www.valdezak.gov/151/Port)
ADELTE Ports & Maritime (www.adelte.com)
Albion Marine Solutions (albionmarine.com)
AM Insurance (www.amibrokers.com)
The Beckett Group (www.thebeckettgroup.org)
Best Best & Krieger Attorneys at Law (www.bbklaw.com)
BNAC Environmental Solutions Inc. (www.bnac.ca)
Burns & McDonnell (www.burnsmcd.com)
Business Oregon (www.oregon.gov/biz/)
Davies Transportation Consulting Inc. (www.dtci.ca/)
EA Engineering, Science and Technology, Inc. (www.eaest.com)
Federated Shipping Company
FortisBC (www.fortisbc.com)
GCT Global Container Terminals (www.globalterminals.com)
Harman Kemp North America Limited (www.hknal.com/)
Innovative Manufacturing Inc. (www.marinetapes.com)
Kongsberg Maritime Canada Ltd. (www.kongsberg.com)
Law Office of Alan K. Goldstein (www.alankgoldsteinlaw.com)
Liebherr USA, Co. (www.liebherr.com)
Liftech Consultants (www.liftech.net)
Lynker (www.lynker.com)
Majuro Stevedore & Terminal Company, Inc.
Marine & Civil Maintenance Pty Ltd. (www.marineandcivil.com.au)
Marine Labs Data Systems Inc. (www.marinelabs.io/)
Maritime and Port Bureau, Taiwan (www.motcmpb.gov.tw)
Matson (www.matson.com)
Nautical Consulting International Inc. (www.nauticalconsulting.com)
NEC (www.necam.com)
Northern Economics Inc. (https://northerneconomics.com/)
The Pasha Group (https://www.pashagroup.com)
Pavement Technical Solutions Inc. (pavementtechsolutions.com)
Port and Maritime Business Management (www.pm-bm.com)
PortLink (www.portlinkglobal.com)
Reid Middleton, Inc. (www.reidmiddleton.com)
Salus Resources Inc. (www.salusresources.com)
Schrader Co. Sales, LLC (www.schraderco.com)
Shey-Harding Associates (www.shey-harding.com)
SSA Marine (www.ssamarine.com)
Trans Mountain (www.transmountain.com)
Truk Transportation
Tynebridge Solutions Inc. (www.tynebridge.ca)
Western Wood Preservers Institute (www.wwpinstitute.org)
Association of BC Marine Industries (abcmi.ca)
Green Marine (https://green-marine.org/)
Inland Rivers, Ports & Terminals Association (https://www.irpt.net/)
Interferry (www.interferry.com)
International Association of Maritime and Port Executives (www.iampe.org)