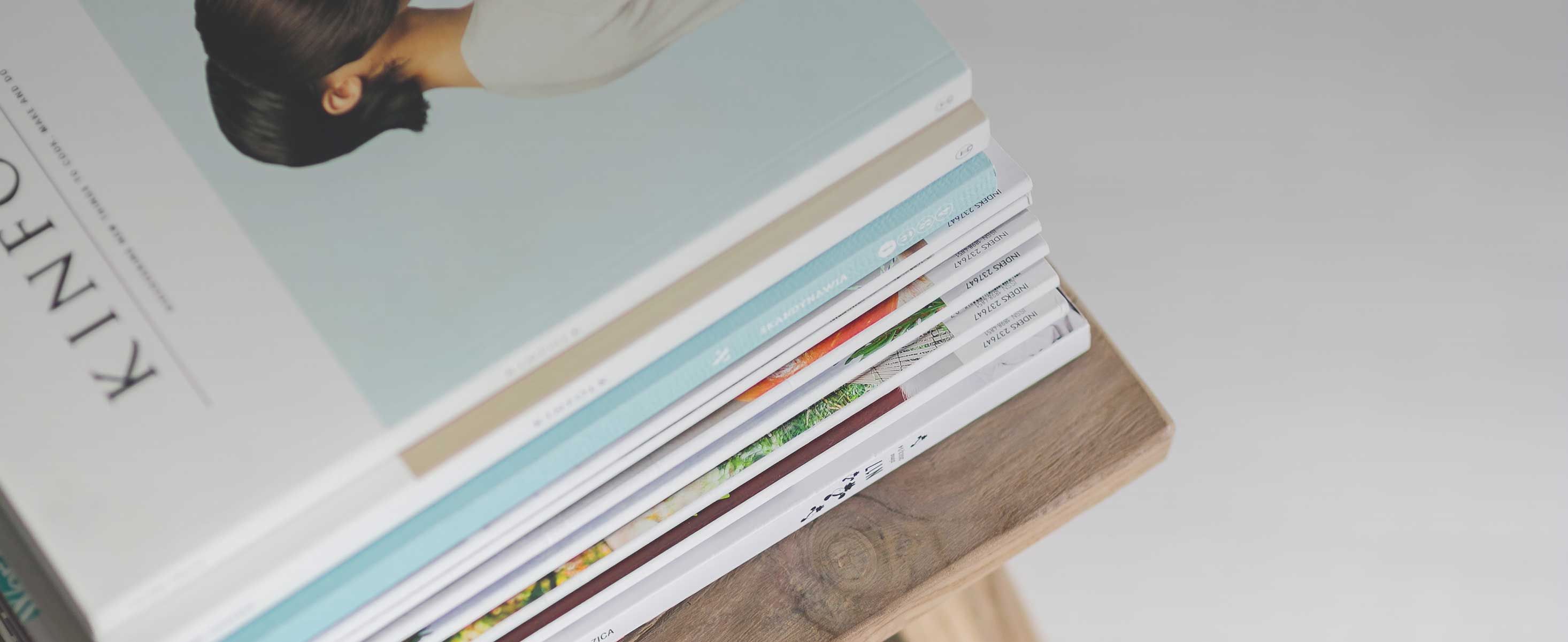
4 minute read
Biesse High Dynamics
In nesting cabinet parts, speed is everything. The more panels you produce per shift, the more profit you make. The challenge is to increase productivity whilst maintaining your reputable quality standard. It’s a challenge Biesse has solved with their new High Dynamics technology, available now from Biesse Group Australia.
The new Rover B FT HD nesting machine is now available through the Biesse Group and will significantly increase the number of sheets processed per shift. Biesse Group has worked to deliver the benefits of higher speeds, acceleration/deceleration, and angular speeds (in one word, Dynamics) to their customers by re-thinking the nesting process from the ground up. Every aspect of the machine has been considered with the goal of increasing the actual processing speed while strongly maintaining quality and safety. The result is a product Biesse Group claims is the fastest and most productive nesting machine available.
To achieve faster acceleration and deceleration and high lineal and cornering speeds, the key factors include chassis design, weight, vacuum, and power. Biesse Group have considered the entire process in a new and creative way to achieve a cutting solution where every second of movement has been considered to produce a CNC nesting result that saves an enormous amount of time. Biesse has achieved highest and actual linear cutting speeds of 50 metres a minute, high angular interpolations (cornering) movement; and a positioning speed over 170 metres a minute are now possible with Biesse HD.
High cutting speeds place huge demands on every aspect of the machine so Biesse Group started with the chassis, or frame of the machine. To hold even the smallest parts on the edge of the sheet, the vacuum table has been completely re-designed. All vacuum design has been improved to guarantee a smooth, uninterrupted flow of air, exactly like a good dust extraction system. Tests indicate a 30% to 70% better holding of even the smallest parts!
Stability is another important factor that affects the possible cutting speed round the entire panel, as well as the quality of your production. To guarantee the highest confidence, Biesse widened the stance of the gantry frame. The rack and pinion, still the best technology for dusty environments, is fitted with bigger and deeper teeth. And Biesse have located the linear guides closer to the rack for higher performance under load. As a oneoperator cell the CNC machine can be enclosed in a cabinet and in this case the machine hood can be removed, reducing weight, saving wear and tear, and offering improved visibility and safety for the operator.
To power the High Dynamic cutting solution, Biesse increased the power in the axis drive motors by three times and added a more rigid reduction gearbox. A fast, 12-position tool-change travels with the processing head, further eliminating downtime. An optional 33-position tool change can be mounted at the rear of the machine. The automatically lubricated 42-bit vertical drilling head is now water-cooled, an additional low-cost advantage for continuous production. And finally, at the cutting station, the new design dust hood with shorter bristles and high-tech anti-ejection fabric, is now set to the millimetre for near-perfect dust removal on any thickness sheet and tool length.
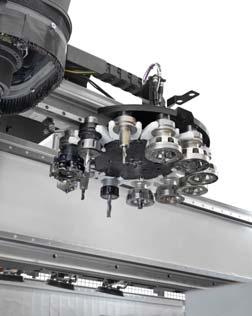
Biesse HD is not just a machine, it’s a philosophy, a new way of thinking that directly benefits the customer. It’s fast, dynamic, unique, unlike anything you have seen before. Equipped with the optional twin configuration of two routing spindles and two drilling units, even greater savings can be achieved.
The savings are everywhere
The performance of the new Rover B FT HD nesting machine is measured in milliseconds, but it’s as a manufacturing cell with automated infeed and outfeed where the machine really shines. The cell’s infeed; CNC machine; and outfeed, and every aspect of work has been optimised for continuous, high-speed processing. After the first sheet has been labelled, the rest of the day’s production continues without a break, ensuring your equipment delivers the maximum return on your investment.
Every aspect of the machine has been considered with the goal of increasing the actual processing speed while strongly maintaining quality and safety.
First, the label printer moves with the applicator and after the first sheet, the cell production is continuous. The sheet is aligned with a single stroke on the machine table, saving fifteen seconds per sheet compared to other brands and adding up to twenty minutes of production within the same shift! Finished parts are moved onto the outfeed while the next sheet is loaded at the same time. The very next level is when the cell is integrated to an automatic storage solution like the Winstore and with offloading and sorting of finished components by robot. It’s a symphony of motion that never stops.
With high cutting speeds, manufacturing marginality can greatly improve. Past machines have made claims of high speeds but rarely deliver because of the time the tool takes to reach the claimed feed speed. Biesse HD’s improved rack and pinion and more powerful drive motors accelerate to reach the claimed top speed of 50 m/min in around 100mm of travel and decelerate in the same distance! But lineal speed is not the only gain through Biesse High Dynamics. Biesse HD technologies will produce sharp, square corners on your nested MDF doors a lot faster and guaranteeing the quality for which Biesse is famous for!
On a typical 600mm by 600mm panel the tool achieves 50metres/ minute for over 70% of the time. In a test for an Australian kitchen manufacturer, cutting typical cabinet components from a 3.6 X 1.8 sheet took less than three minutes to process. An unseen benefit is the tool operating with its optimal chip load and lasting longer, especially with superior Australian manufactured board. Biesse HD offers the reality of using one machine instead of two or three, or the possibility of eliminating overtime or weekend work. It is a revelation like no other.
Go faster
There is no better example of technology innovation than Formula One. Frank Williams CBE, of Williams F1 motorsport fame asks of innovation, “Does it make the car go faster?” In the case of CNC nesting with Biesse High Dynamics, the answer is yes! There is no better champion of performance than Enzo Ferrari who says, “The dreams become bigger, much bigger, to build a car that doesn’t slow in the curves, that flies without leaving the ground.”
Biesse know that to continue as a World leader in performance woodworking machinery, they need to push the design envelope. Biesse Group’s latest CNC nesting equipment can be compared to F1 where the design of the chassis; table; drive motors and safety equipment has been optimised to provide the customer with a totally new and re-imagined processing solution, a solution that really flies. Welcome to the World of Biesse High Dynamics.
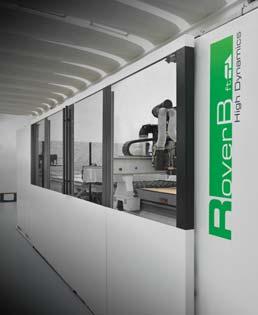
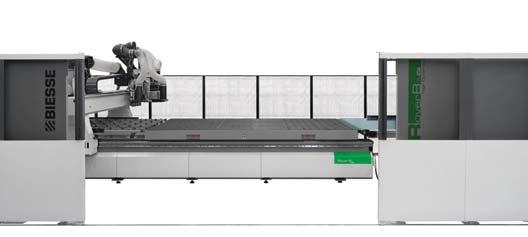
We’ll be giving away a free 12 months subscription courtesy of 3D Kitchen™ with every issue of JOINERS Magazine!