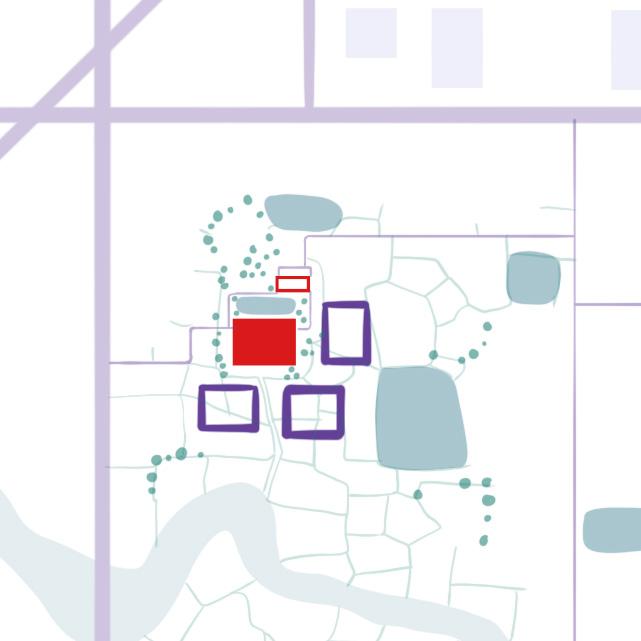
7 minute read
Vernacular architecture always responds to the climate
Marina Tabassum
The Materials.
Advertisement
Taking the feminist route and using vernacular materials
After revisiting Bangladeshi vernacular and architecture, alongside gaining inspiration from Marina Tabassum’s ‘Khudi Bari’ and her other work, have selected new materials (since 3.1).
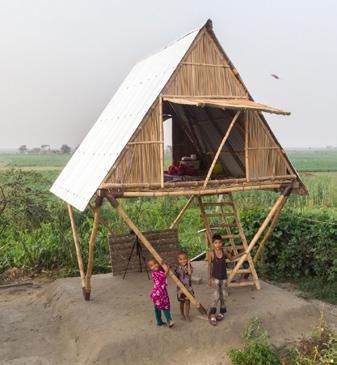
3. 4.
Bamboo Site Plan
Bamboo. Feminist Characteristics
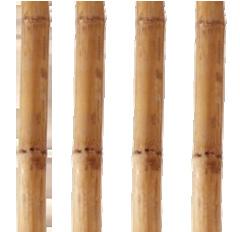
Name: Location: Uses: Height: Diameter: bamboo forests
2.
Internodes: Bangladesh production:
Bambusa Balcooa (Female Bamboo) Northeast India, Bangladesh, Laos, Myanmar, Nepal and Vietnam construction, scaffolding 16-25 m 7-15 cm tropical-subtropical 20-45 cm 1200-1700 culms/ha/yr produces full -sized shoots in 5/6 yrs low cost + light weight ages well in increased rain climate
Fired: Bangladesh production: renewable + natural resource clay is natural resource recyclable + compostable local worker production
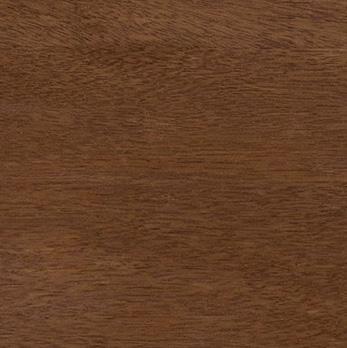
Size: rapid growth rate low maintenance handmade brick Bangladesh construction, aggregate for concrete or ballast chippings 105x60x220 mm using open circular kilns most common product of manufacturing durable + long lasting thermal mass properties
Precedent. Precedent.
release oxygen + abosrb CO2 low cost + high availability on-site brick-making
1.
Brick Site Plan Feminist Characteristics Brick.
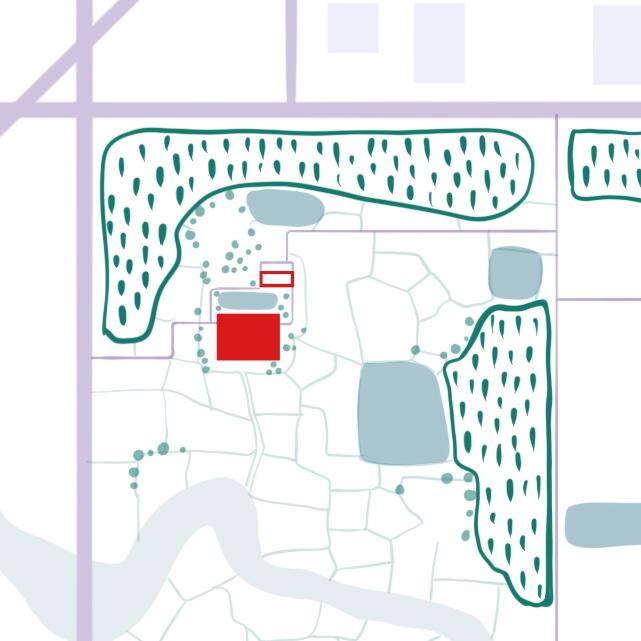
Khudi Bari
Marina Tabassum Architects
Coastal Bangladesh 2020
Baitur Rauf Mosque
Marina Tabassum Architects
Dhaka, Bangladesh 2012
Clay brick made by hand is one of Bangladesh’s most common materials; it is cheap and in high supply/ demand. Because of its structural attributes, it also allows experimentation with brick perforations to create more playful facades. It is able to be produced on site which reduces transportation costs/ emissions.
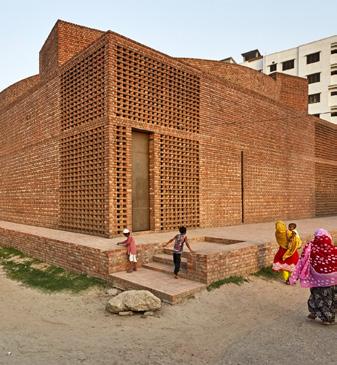
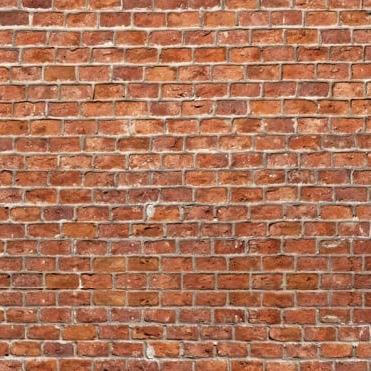
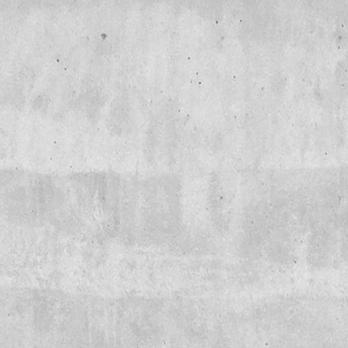
Bamboo was chosen for its strenghth, high availability and its overall sustainability. Furthermore, a lot of brick is used and the bamboo ‘softens’ the volumes; it plays with light and transparency in between the gaps of the poles. Local construction methods can also be taken advantage of.
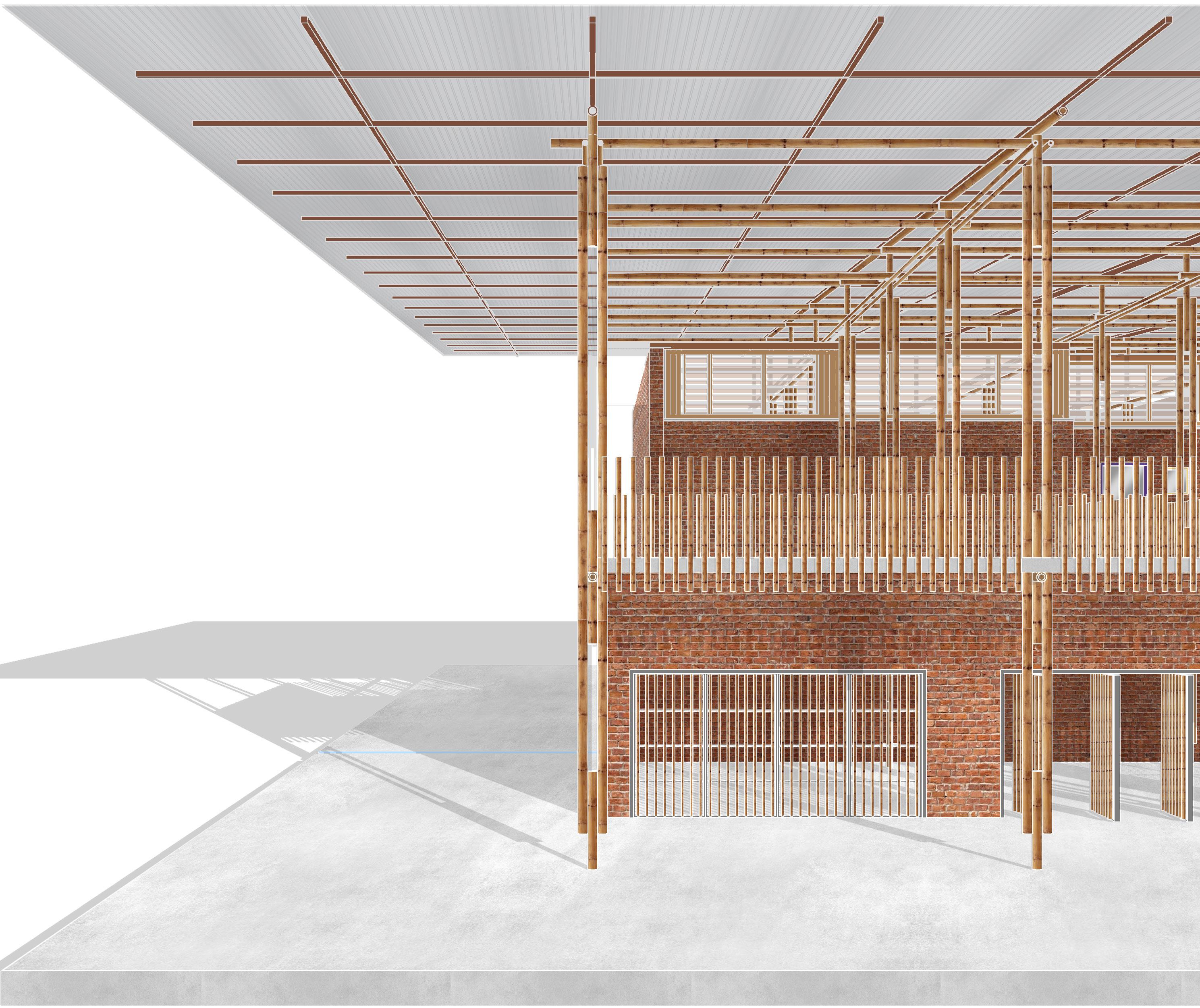
Mango wood is easily and cheaply sourced in Bangladesh, and is ideal for secondary structure such as the roof battens. It has low embodied energy, making it a sustainable option, and its light weight eases the construction process.
Foundations and main floor are concrete due to its durability and ability to support the brick and bamboo. Even though it has high embodied carbon, its use has been minimsed by using pile foundations. Brick foundations could have also worked well, however concrete is a quicker process.
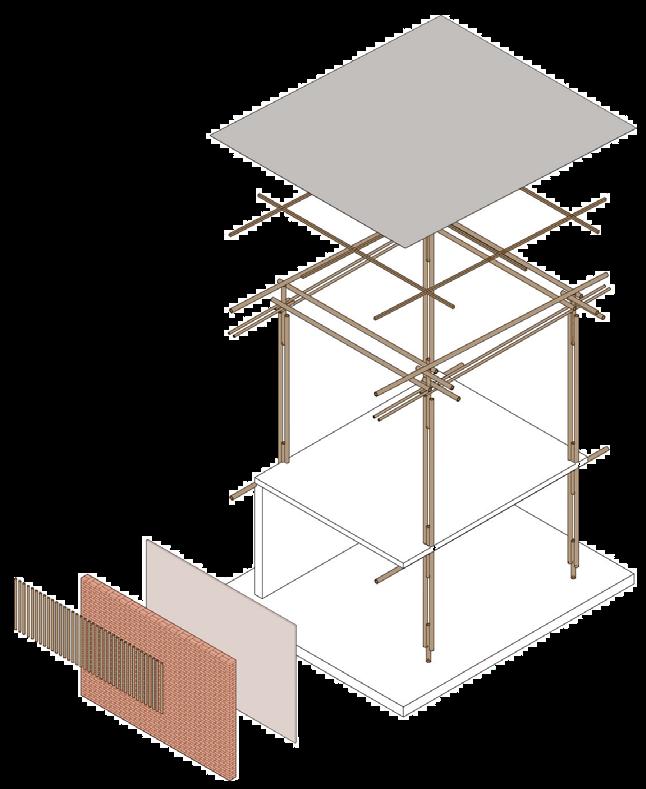
The purpose of the roof is to shade the building and protect it from rainfall. The ideal roof is therefore lightweight and waterproof. A tin roof has been chosen for these reasons, with an additional white coating to minimise heat absorbption
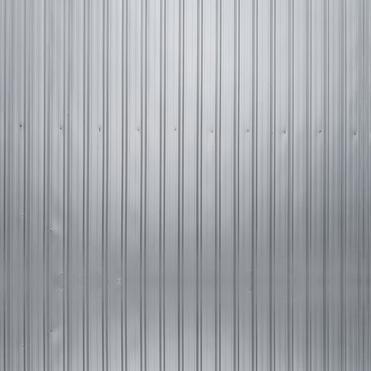
A Hybrid Structure.
Bamboo and brick connections
The overarching structural system is made up of bamboo columns/beams and loadbearing brick walls. The bamboo system holds up the roof over the brick enclosed spaces to keep the spaces protected from direct sunlight and heavy rainfall. Both structural systems (bamboo + brick) have moments of connection, to increase stability in the bamboo system (bamboo isn’t standardised in quality and size, therefore additional support is beneficial).
Precedent.
Connection Techniques
Pani Centre
SchilderScholte
Architects
Rajarhat, Bangladesh 2014 insulated brick wall with air cavity bamboo column bamboo beam hexagonal nut
Bamboo Column to Beam Connection (iso)
2 long bamboo poles make up the majority of the columns, with a smaller pole in between to increase stability and support the connecting bamboo beams. The joints are held in place with a threaded rod and hexagonal nut it is a low-tech solution for ease of construction and can be disassembled without comprimising bamboo strength for future use.
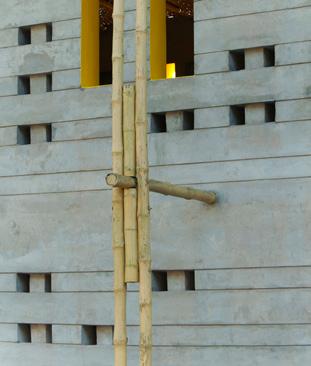
Bamboo to Brick Connection (type 1 plan) secondary bamboo beam primary bamboo beam
This is the connection between the bamboo system and the brick structural system of the factory volume. The beam is inserted into the brick outer leaf (so as to not compromise insulation layer) and is cemented in place. As a result, the bamboo system becomes stronger.
Bamboo to Brick Connection (type 2 iso)
In the cafe and learning centre, the bamboo beams penetrate through the wall to support the 1F level. Additional secondary structure bamboo beams are also used to support the 1F. Clay is used to cement the bamboo beams in place and to reduce thermal bridging as much as possible.
Bamboo Structural System
Bamboo Columns
The primary bamboo structure consists of a 5m x 5m grid of bamboo columns. Two long poles are strengthened by central smaller poles which are bolted together
Bamboo Beams
The bamboo beams connect the columns at 3.5m high and at moments connect the bamboo structure with the brick volumes
Bamboo Roof Structure
The roof structure is made up of layered bamboo poles to support the metal roof
Wire Cross-Bracing
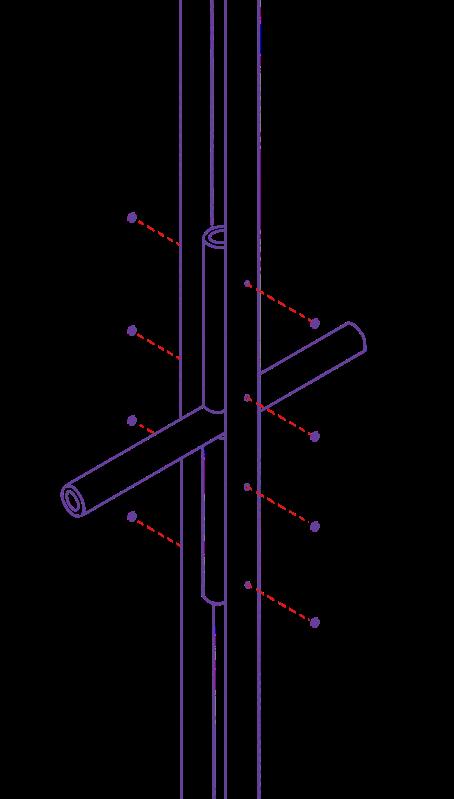
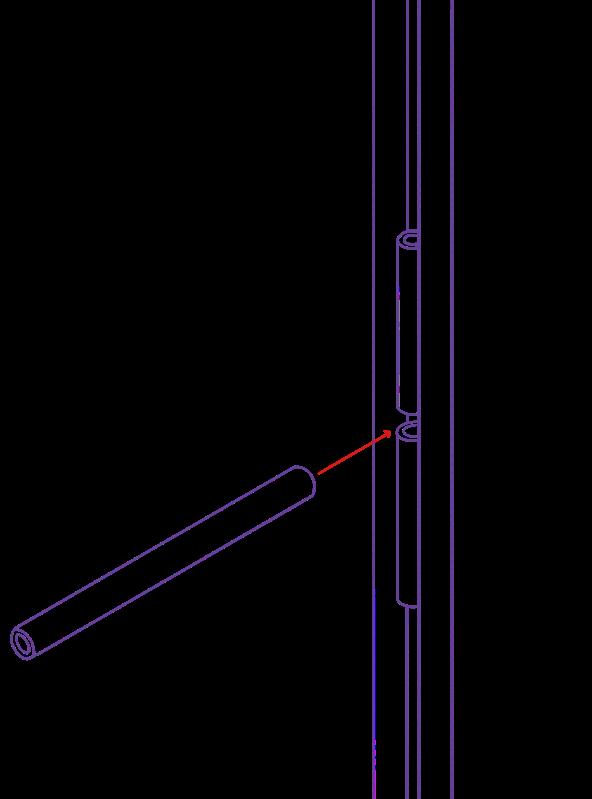
This is used to strengthen the bamboo frame in bays that aren’t connected into the brick structure
Bamboo + Wire Truss
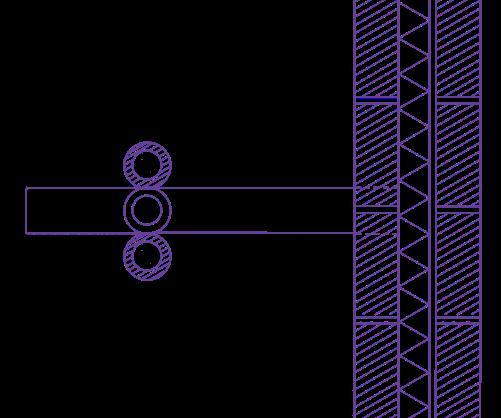
There are no bamboo columns in the factory space to keep the space open, so a truss has been used to hold up the factory roof and to distribute the loads holding up the metal roof
Roof Roof Battens
0.8 mm corrugated metal sheeting
Feminist Lens.
This structural system has many feminist technologies as drivers. These include:
60/60 mm mango wood battens
1. 2. 3. 4. 5. 6. 7.
Low-Tech Construction Design for Disassembly and Re-Use Vernacular Materials Local Construction Techniques Cheap and Accessible Materials Sustainable and EcoFriendly Structure Lightweight and Easy to Assemble
Roof Structure top chord of beam Ø 110 mm bamboo pole; lower chord 2 x Ø 60 mm bamboo pole; purlins Ø 110 mm bamboo poles
Factory Truss beam 2 x Ø 110 mm bamboo pole; column Ø 110 mm bamboo pole with 2 x Ø 110 mm bamboo pole to strengthen column column 2 x Ø 110 mm bamboo pole with Ø 110 mm bamboo pole to strengthen column; beam Ø110 mm bamboo pole; wire cross-bracing
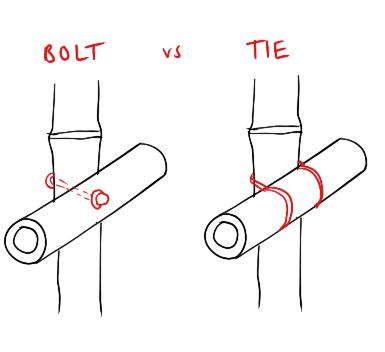
Bamboo Primary Structure
Structural Exploded Axonometric
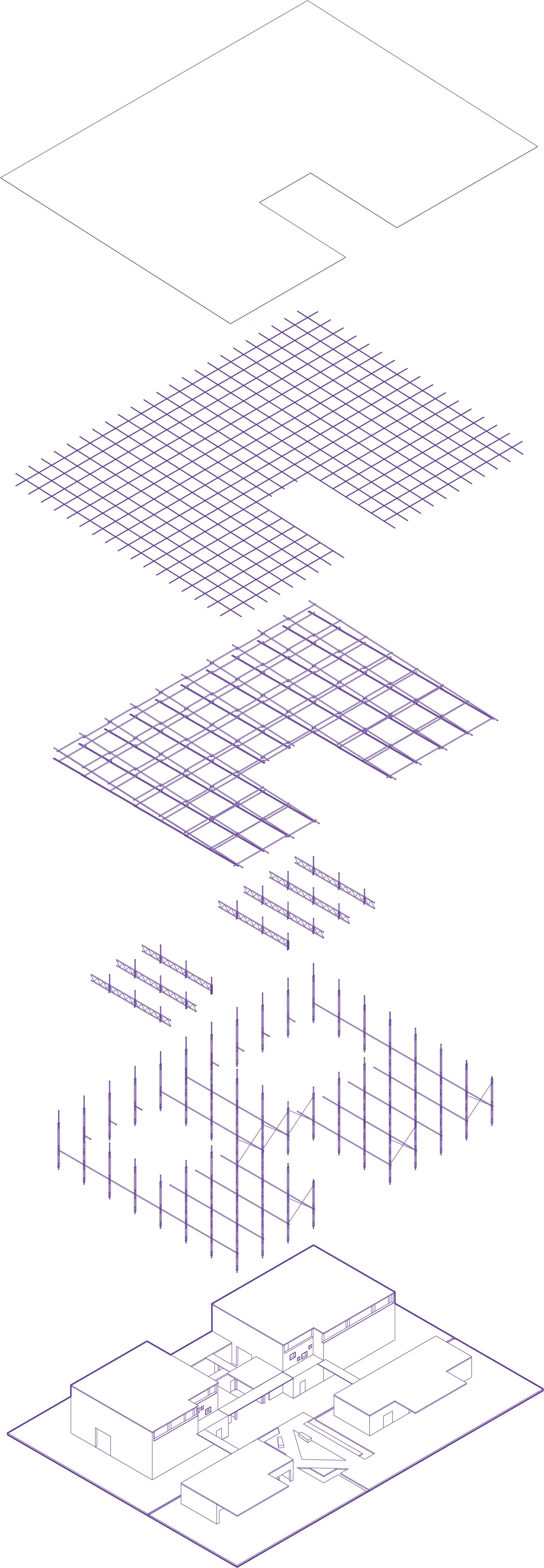
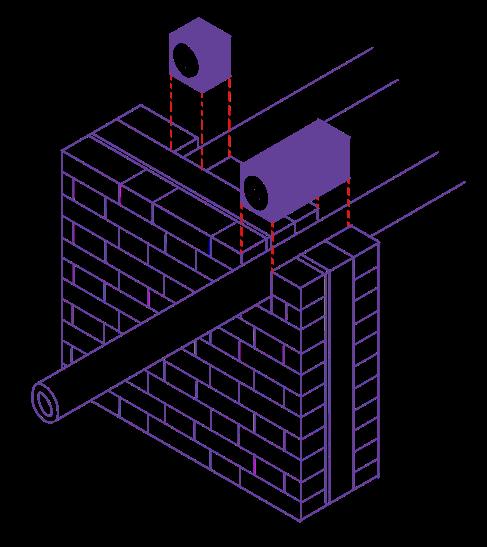
This diagram shows the exploded layers of the bamboo structural system which supports the canopy roof
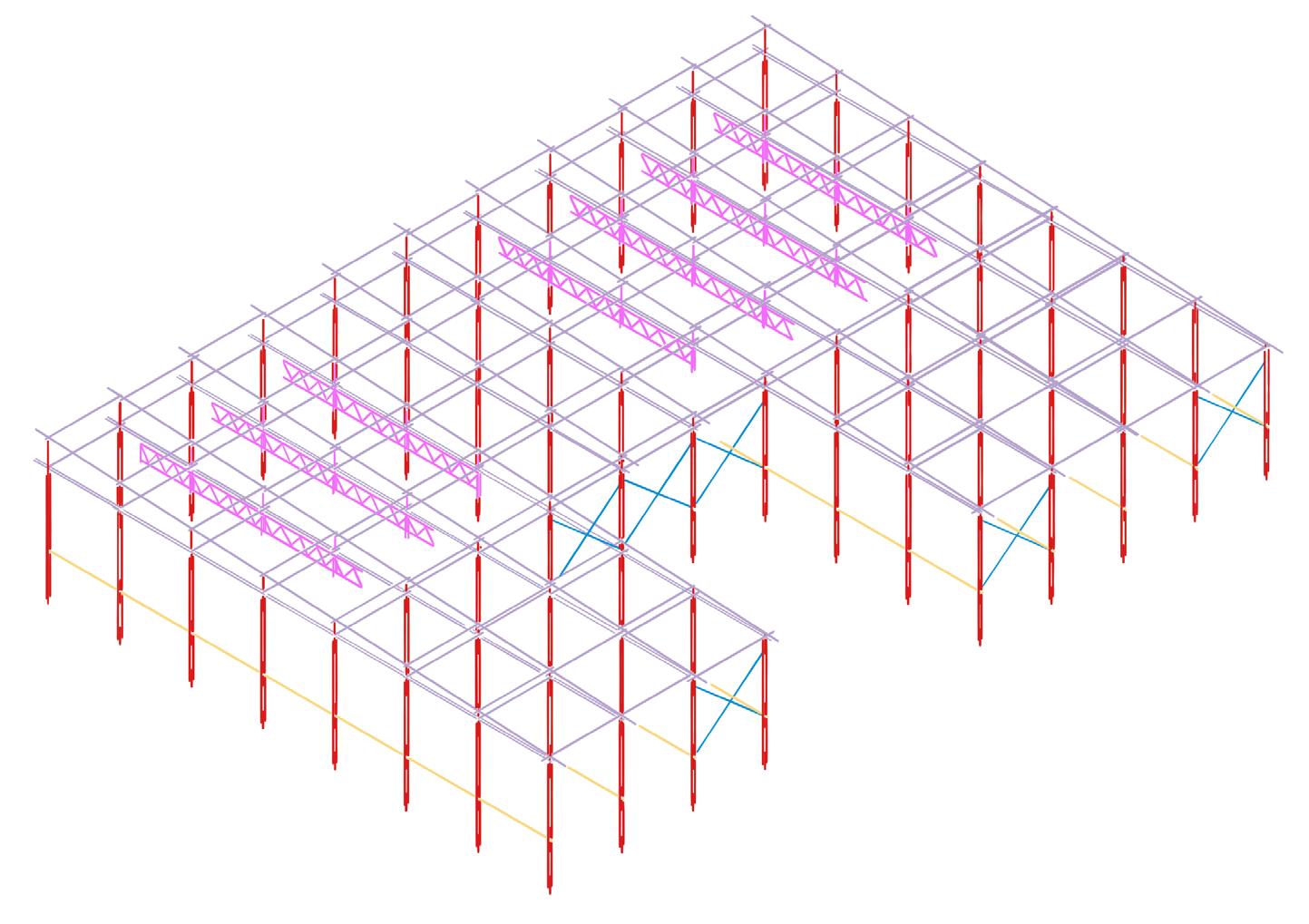
For the Love of Detail.
1:20 Sectional Perspective
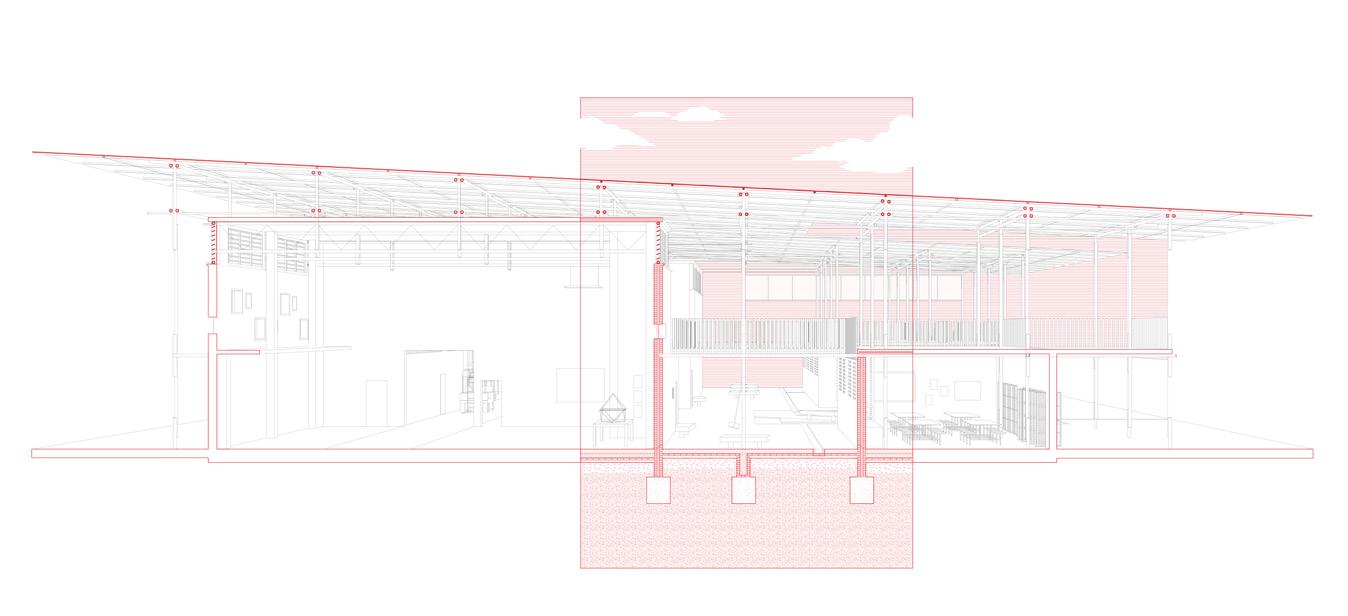
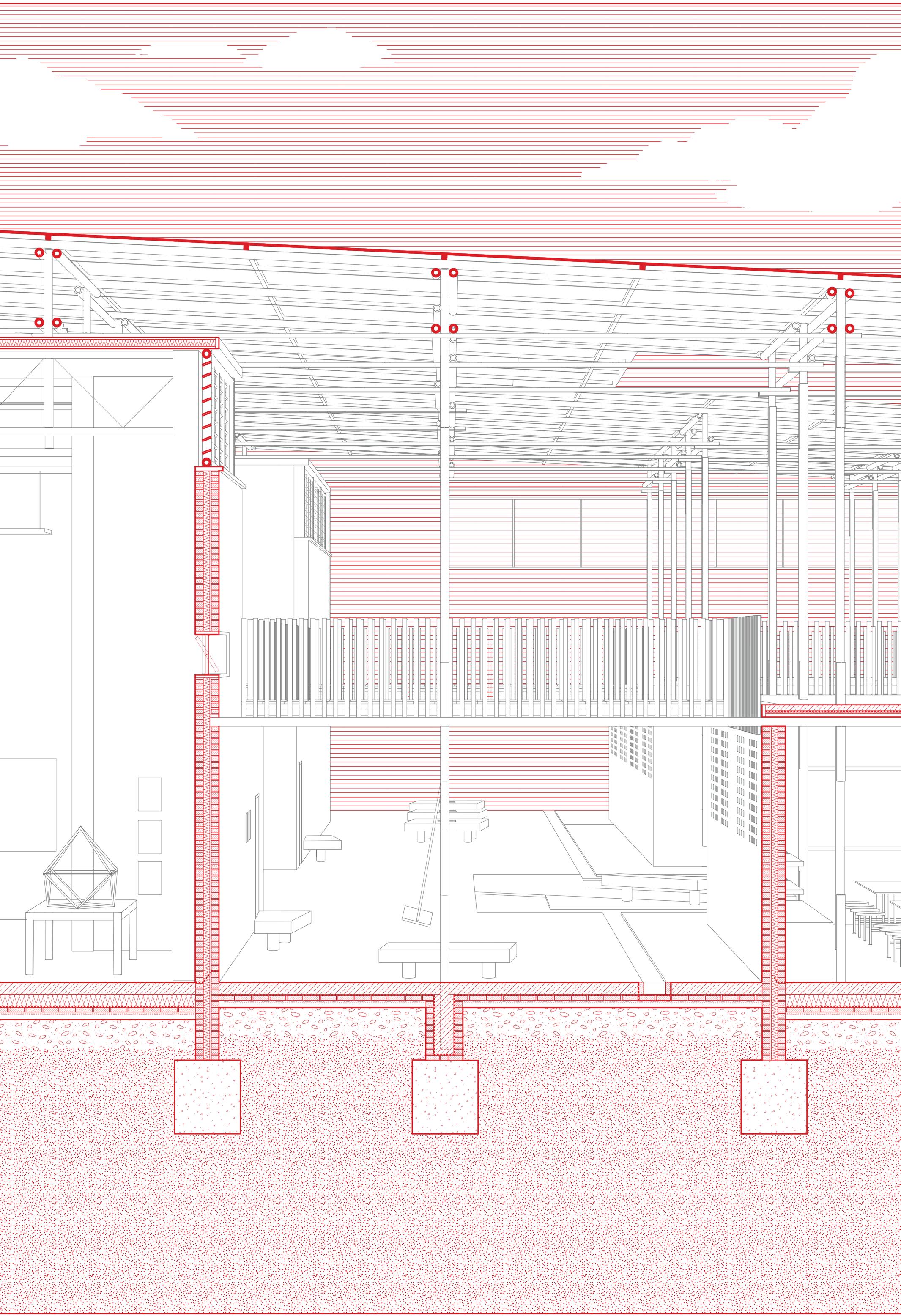
Roof Build-Up
0.8 mm corrugated metal sheeting; 60/60 mm mango wood battens; top chord of beam Ø 110 mm bamboo pole; lower chord 2 x Ø 60 mm bamboo pole; purlins Ø 110 mm bamboo poles
Bamboo Primary Structure column 2 x Ø 110 mm bamboo pole with Ø 110 mm bamboo pole to strengthen column; beam Ø 110 mm bamboo pole; wire cross-bracing footing: Ø 120/5 mm steel tube in reinforced concrete
Factory Truss beam 2 x Ø 110 mm bamboo pole; column Ø 110 mm bamboo pole with 2 x Ø 110 mm bamboo pole to strengthen column
1F Build-Up
70 mm reinforced concrete with protective coating;
2-ply PE foil; 25 mm mineral wool insulation; 40 mm fibre cement panel with white paint finish
Bamboo Beams
Ø110 mm bamboo pole; waterproof mortar to attach bamboo pole with brick wall
Window Build-Up
6 mm toughened glass + 10 mm cavity + 6 mm toughened glass laminated mango wood frame
Wall Build-Up
105/60/105 mm handmade brick; wall tie;
20 mm air cavity;
80 mm recycled cotton textile insulation;
105/60/105 mm handmade brick
GF Build-Up 110 mm reinforced concrete with protective coating; (internal) 110 mm reycled cotton insulation;
DPM;
220/60/105 mm handmade brick;
80 mm brick chippings; 300 mm sand bed, compacted
Waterway
Brick-encased water stream with DPM lining
Foundations Reinforced concrete foundation
Construction Process.
RIBA Plan of Work meets Bangladesh vernacular
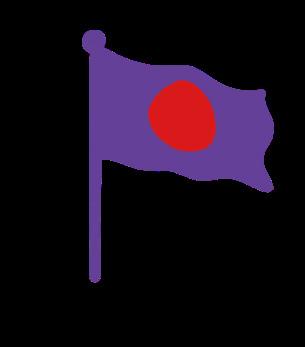
The strategic definition and preparation and briefing occurred during 3.1, where we undertook site analysis, defined our feminist position and set a brief to best accommodate our clients (actors). Further preparation was undertaken at the start of 3.2, where redefined my brief: building the Khudi Bari in my factory (3.1 WikiHouse).
Between both 3.1 and 3.2, have cycled through these stages as have reset the brief and carried out new conceptual designs. In 3.2, was heavily influenced with modern Bangladeshi architecture interventions such as work by Marina Tabassum and Anna Heringer. This is where Nari Bari emerged to truly accommodate the needs of the user and reflect the environment.
The programme was tested using digital massing models, spatial bubble diagrams and sketches. A lot of work was carried out in my sketchbook, which I shared with my tutors in order to resolve the design before the detail stage. We met with tutors from outside perspectives, which helped prompt new ideas and solutions. This information was conveyed in 1:200 sketch plans, which were ready to push to the next step.
Ground clearing and trenches built in the site to pour foundations for brick and bamboo
Bamboo poles attached together onsite and inserted into steel tubes
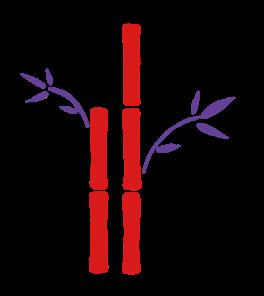
Brick walls built up around bamboo leaving space for openings. Bamboo scaffolding aids this process
Ground layers are filled in: brick chippings, brick layer, insulation (internal spaces) and then cement screed
Gaps left in brick structure to insert bamboo pole beams as part of primary structure and to also support the roof
The technical design firstly involved resolving the bamboo structural system and collecting the information needed to construct the building. This included zooming into scales of 1:100, 1:50, 1:20 and 1:5. With aid of precedents from Bangladesh and Brazil, was able to produce the required information. Bamboo isn’t a common structural material in the UK, so a lot of my technical decisions relied on research.
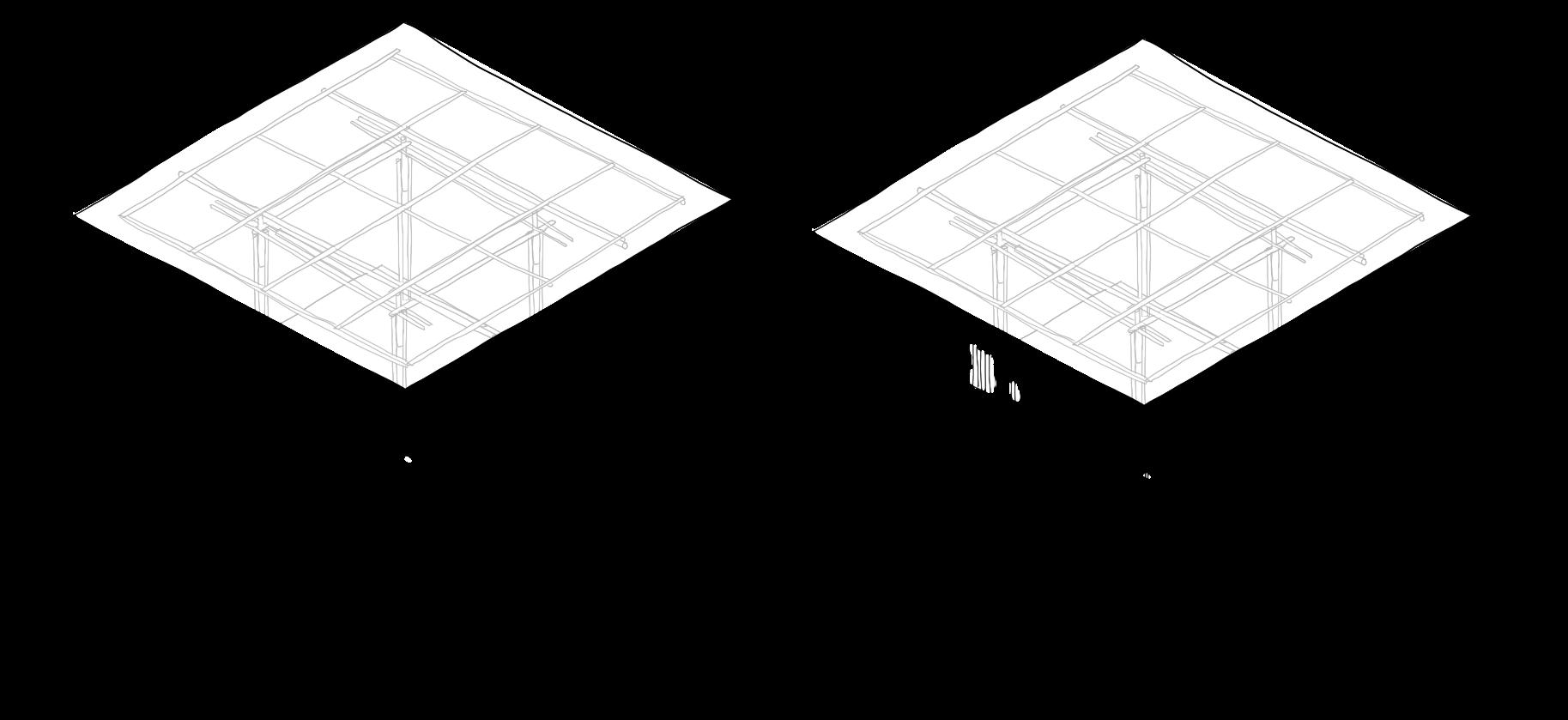
During the manufacturing and construction process, the workers are a mixture of local construction workers (bringing their local techniques) as well as international workers/ architects and volunteers. The fusion enables the mix of vernacular methods with new technology and the sharing of ideas. This is where the process moves away from the RIBA Plan of Work as this process is very collaborative and wouldn’t satisfy UK construction regulations.
As the project is only speculative, there is no handover or measure of building use.
In theory, the handover would be seamless, as the team working on the building will also be using the building. For newcomers, it would involve briefing on the wayfinding system in the factory and the door wayfinding. The open spaces give room for rearrangement so it would include working with the user to finalise these details in the early stages of use.
Roof panels manufactured on-site and ,with the help of a small crane, are lifted into place
Roof structure goes up with the aid of bamboo scaffolding
Roof purlins installed on top of structure to support the roof
Teaching each other and sharing ideas lowcost materials
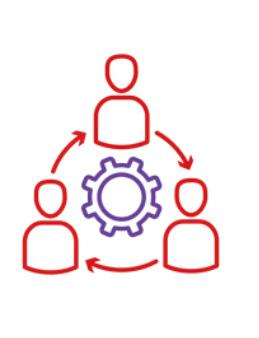
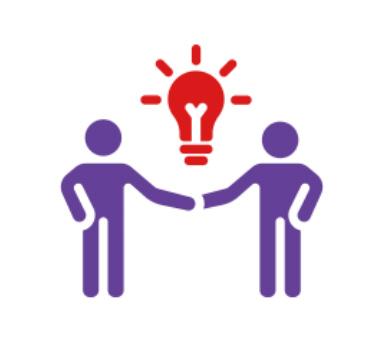
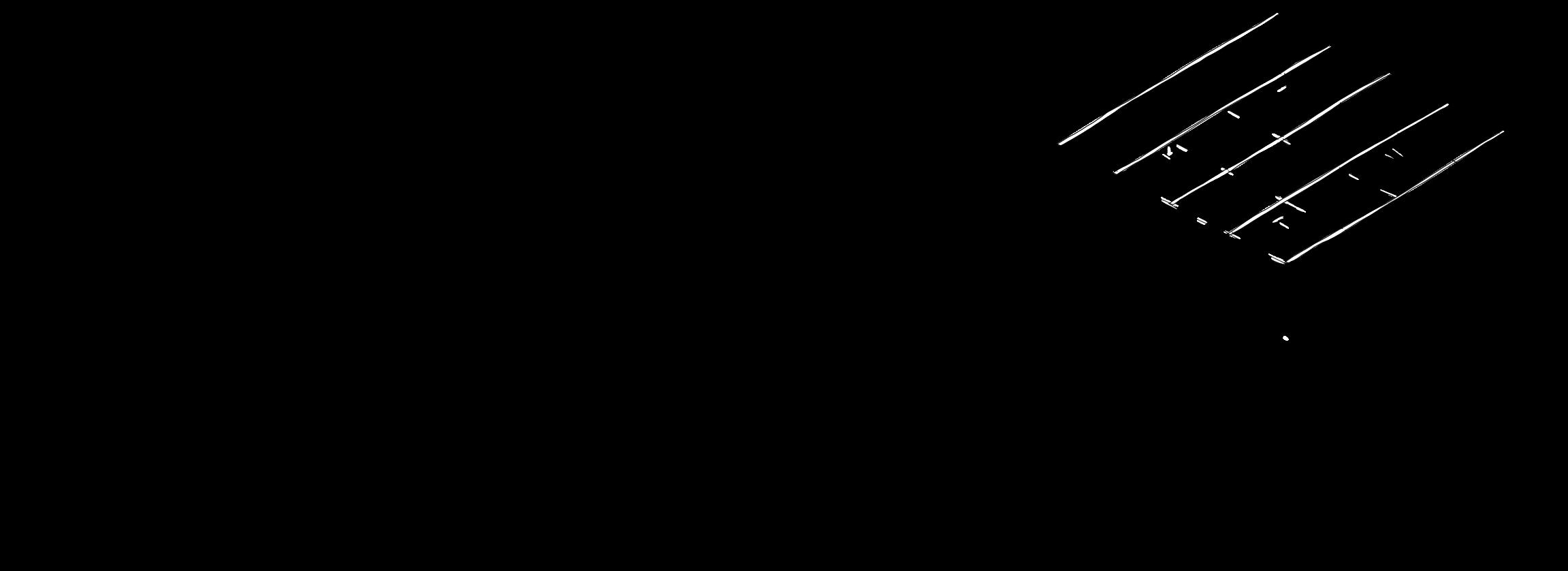
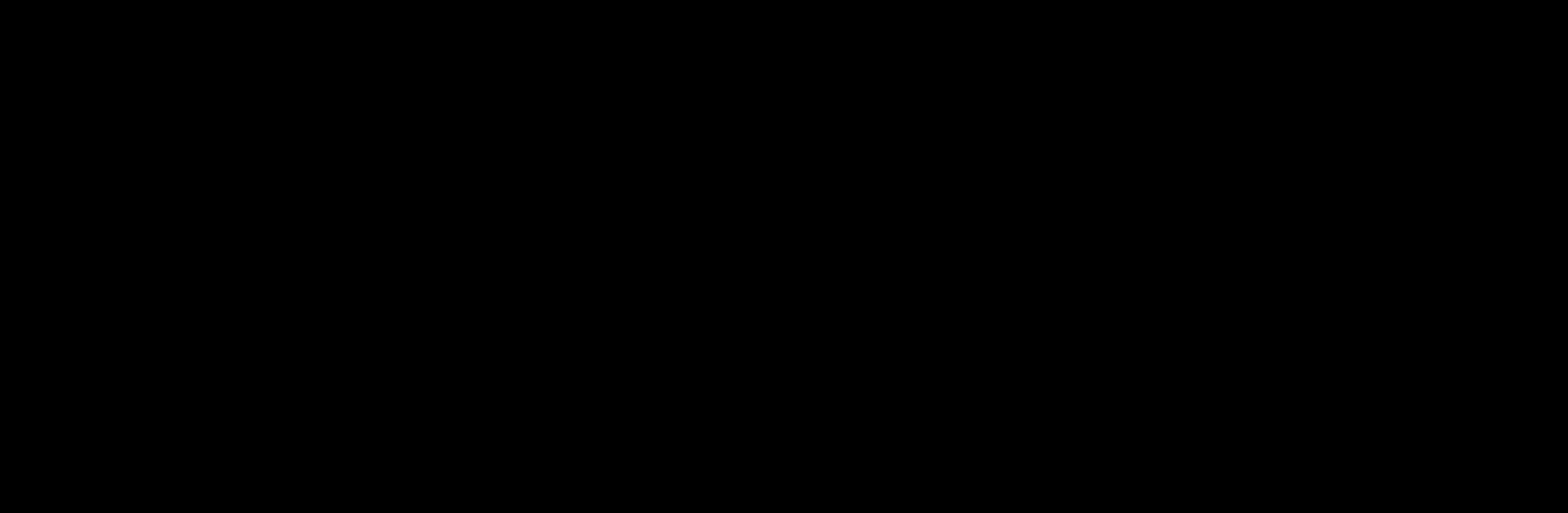
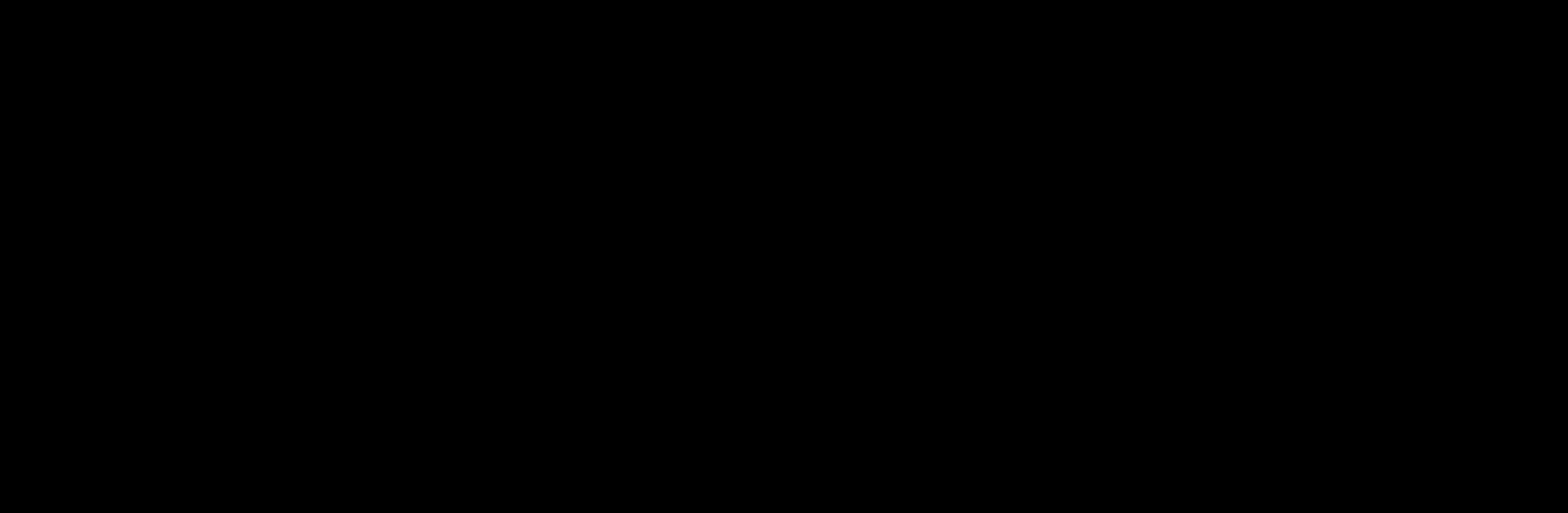
Tin sheet metal roof goes up in small sections, in order to make it manageable without machinery
Finally the bamboo handrails are installed, with aid of steel ties cemented into brick during wall-building process