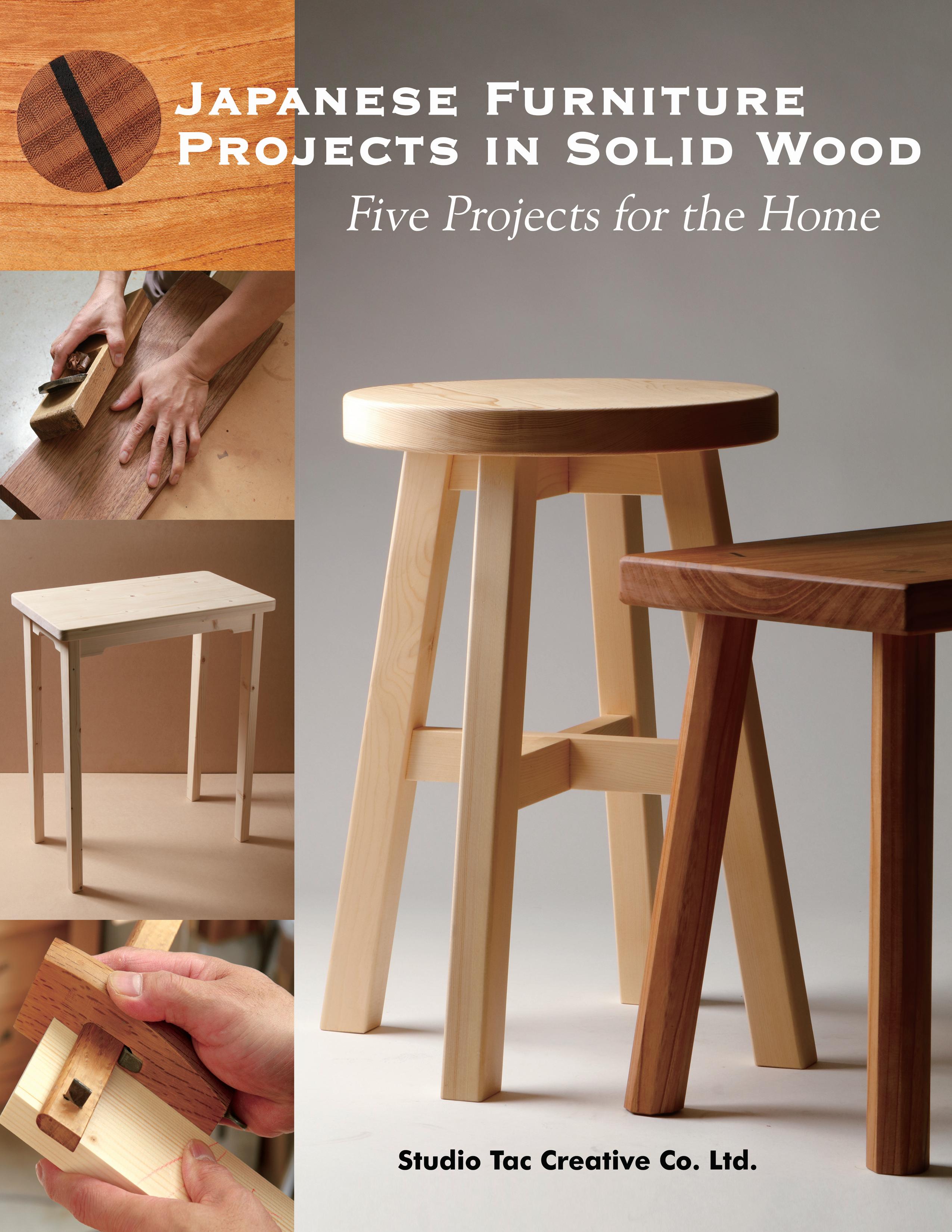
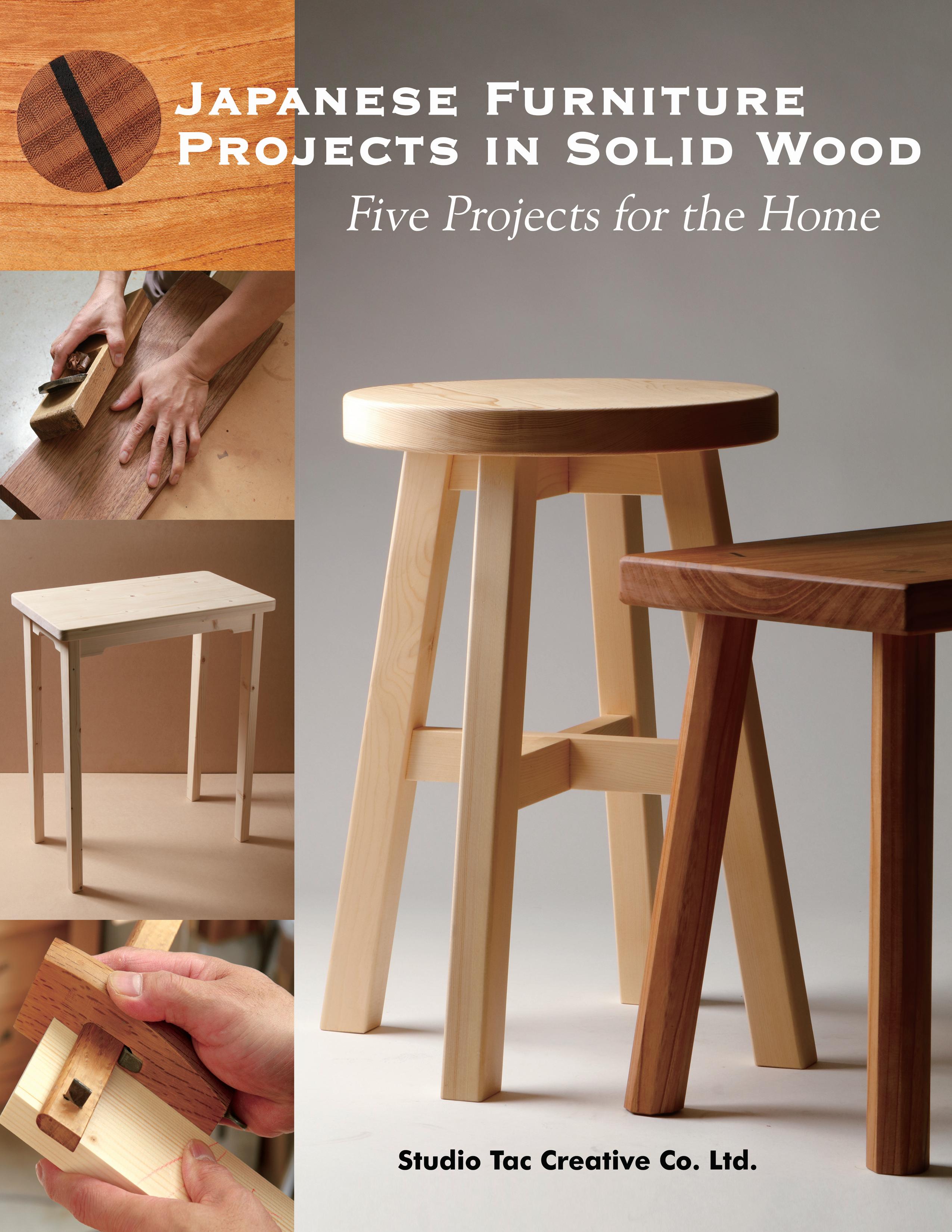
Japanese Furniture Projects in Solid Wood
Five Projects for the Home

Fresno, California
Useful metric/imperial conversions rounded to the nearest millimeter.
Divide mm by 25 to get inches: 50mm divided by 25 equals 2 inches 10mm divided by 25 equals .4 0 inches
Multiply inches by 25 to get mm: 2 inches x 25 equals 50mm 1/2 inch x 25 equals (.50 x 25) = 12.5 mm
1 millimeter equals .03937 inch
1 inch equals 25.4 0 mm
Japanese Furniture Projects in Solid Wood Five Projects for the Home
All rights reserved. No part of this book may be reproduced or transmitted in any form or by any means, electronic or mechanical, including photocopying, recording, or by an information storage and retrieval system, without written permission from the publisher.
English language edition © Linden Publishing Co. Inc. 2024 Art direction by Clarity Designworks Cover design by James Goold
Translation by Luke Baker
ISBN: 9781610354080 135798642
Originally published in Japanese as How to Make Wooden Furniture with Solid Wood Copyright © 2017 Studio Tac Creative Co. Ltd. All rights reserved.
Original Japanese edition published by STUDIO TAC CREATIVE CO. LTD
Supervisor: Mitsuo Fujimoto
Photographer: Hideyo Komine, Takashi Kajiwara (Studio Kazy)
This English language edition is published by arrangement with STUDIO TAC CREATIVE CO. LTD. Printed in the United States of America Library of Congress Cataloging-in-Publication data on file.
Woodworking is inherently dangerous. Your safety is your responsibility. Neither Linden Publishing nor the author assume any responsibility for any injuries or accidents. Photographs in this book may depict the usage of woodworking machinery where the safety guards have been removed. The guards were removed for clarity. We urge you to utilize all available safety equipment and follow all recommended safety procedures when woodworking.
The Woodworker’s Library ®
Linden Publishing, Inc. 2006 S. Mary Fresno, CA 93721 www.lindenpub.com
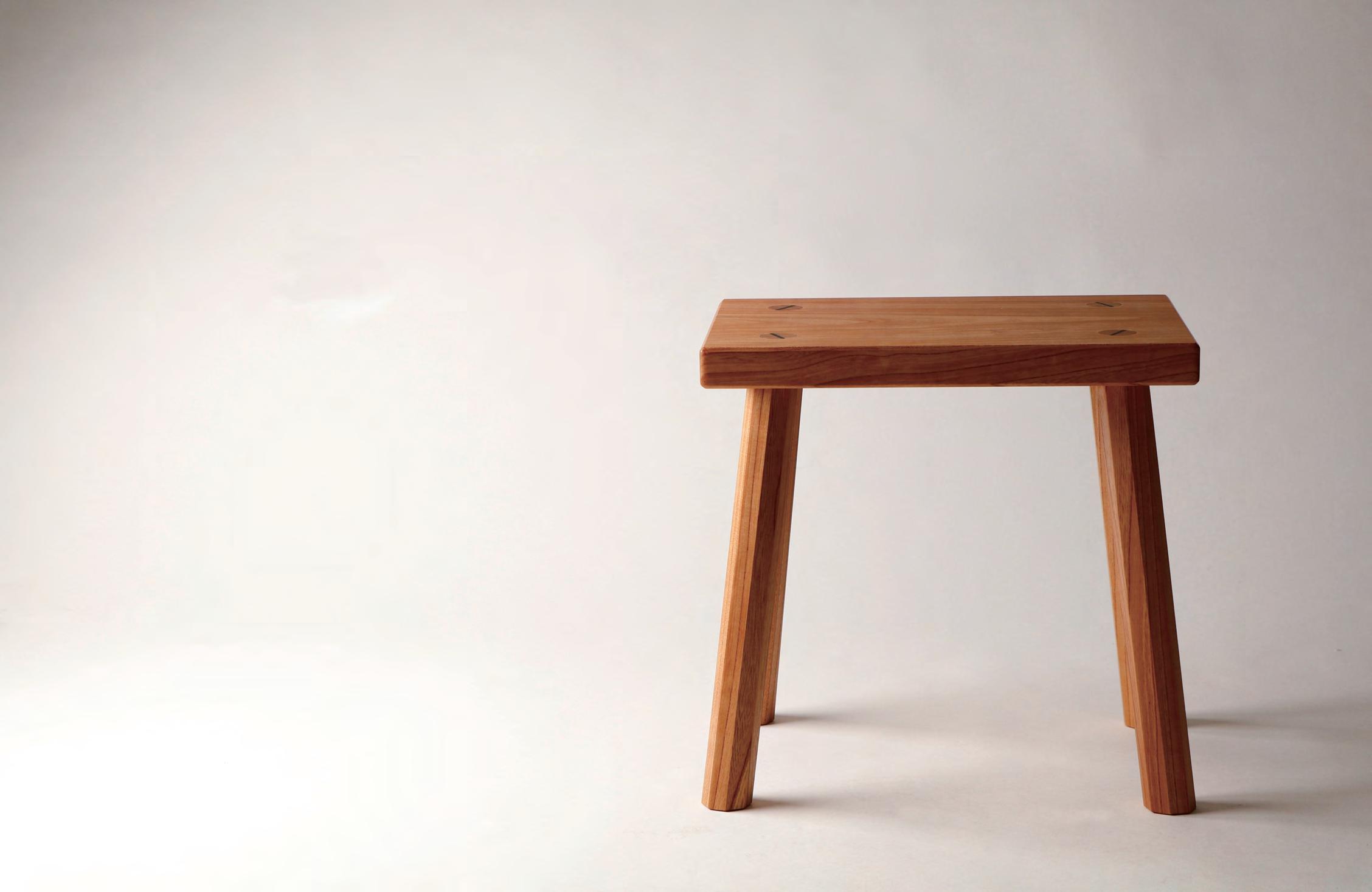
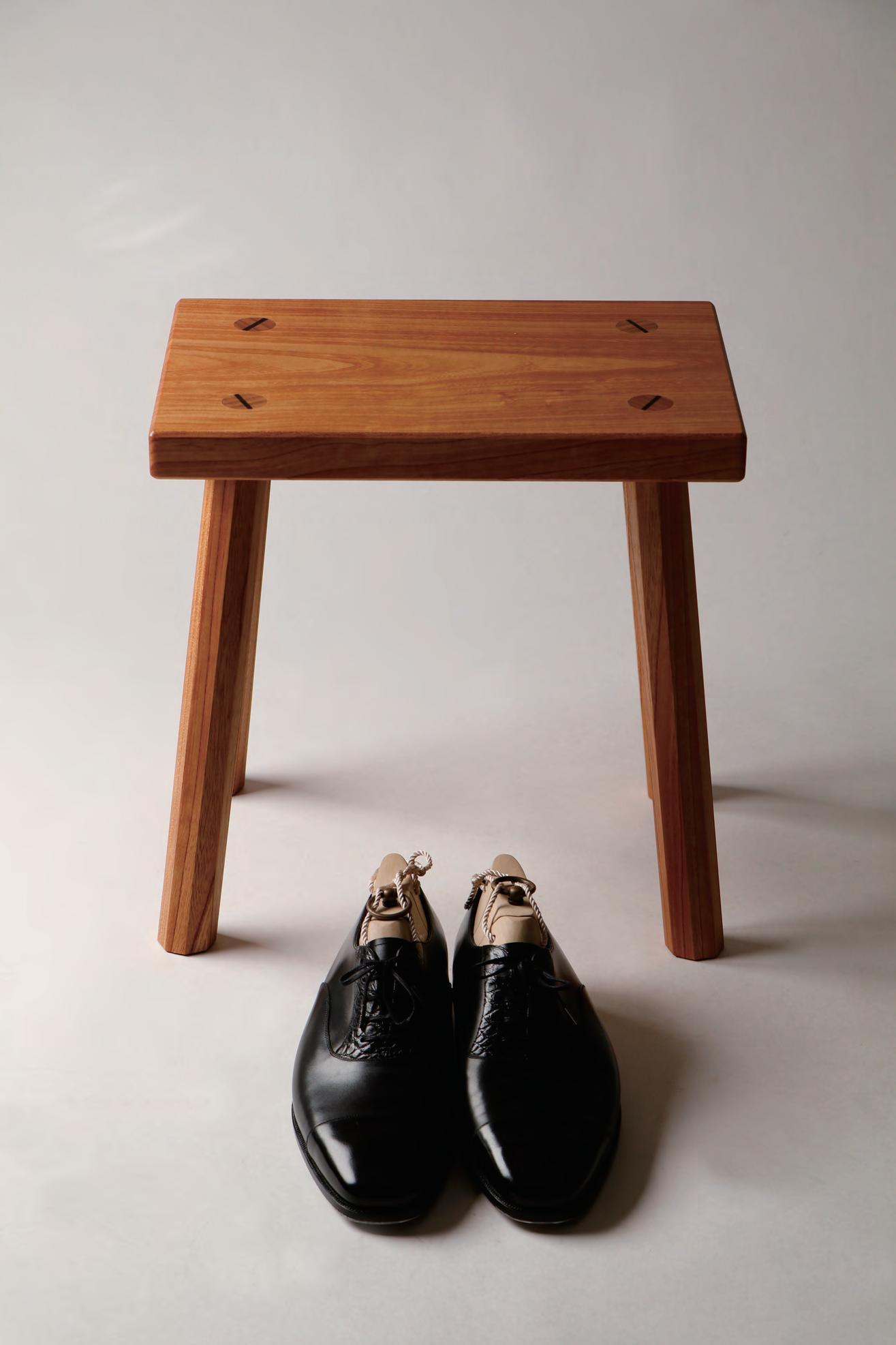
Projects in this Book
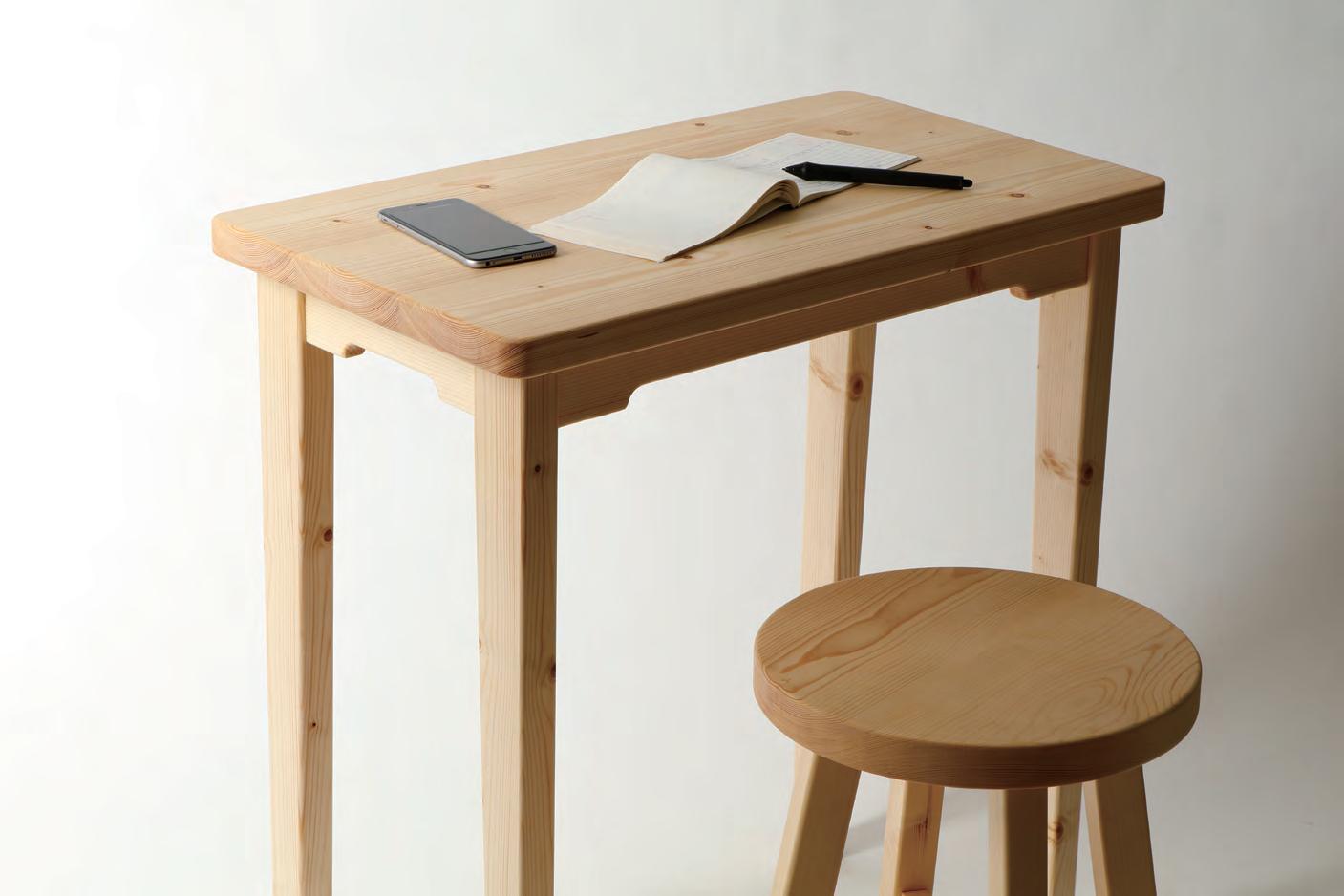
STOOL 1 Page 22
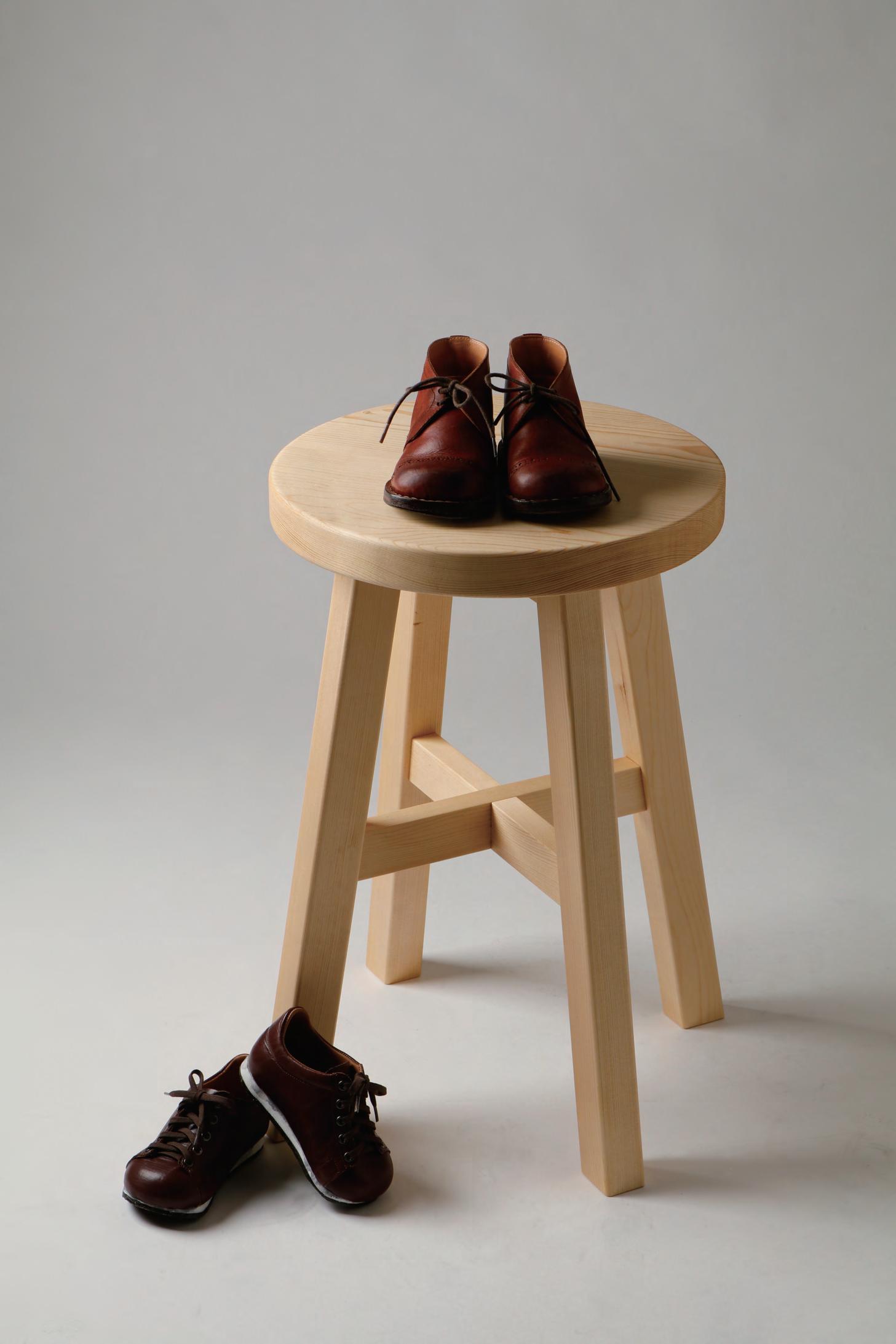
Projects in this Book

AUDIO RACK Page 110
STOOL II Page 84
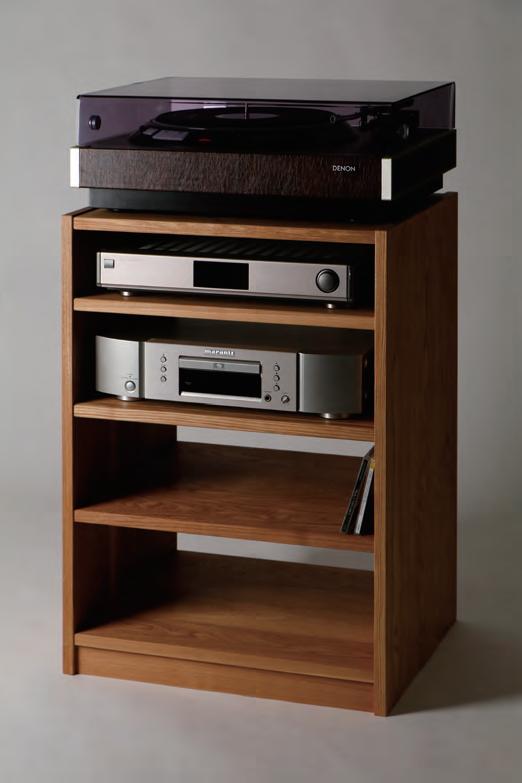
Projects in this Book
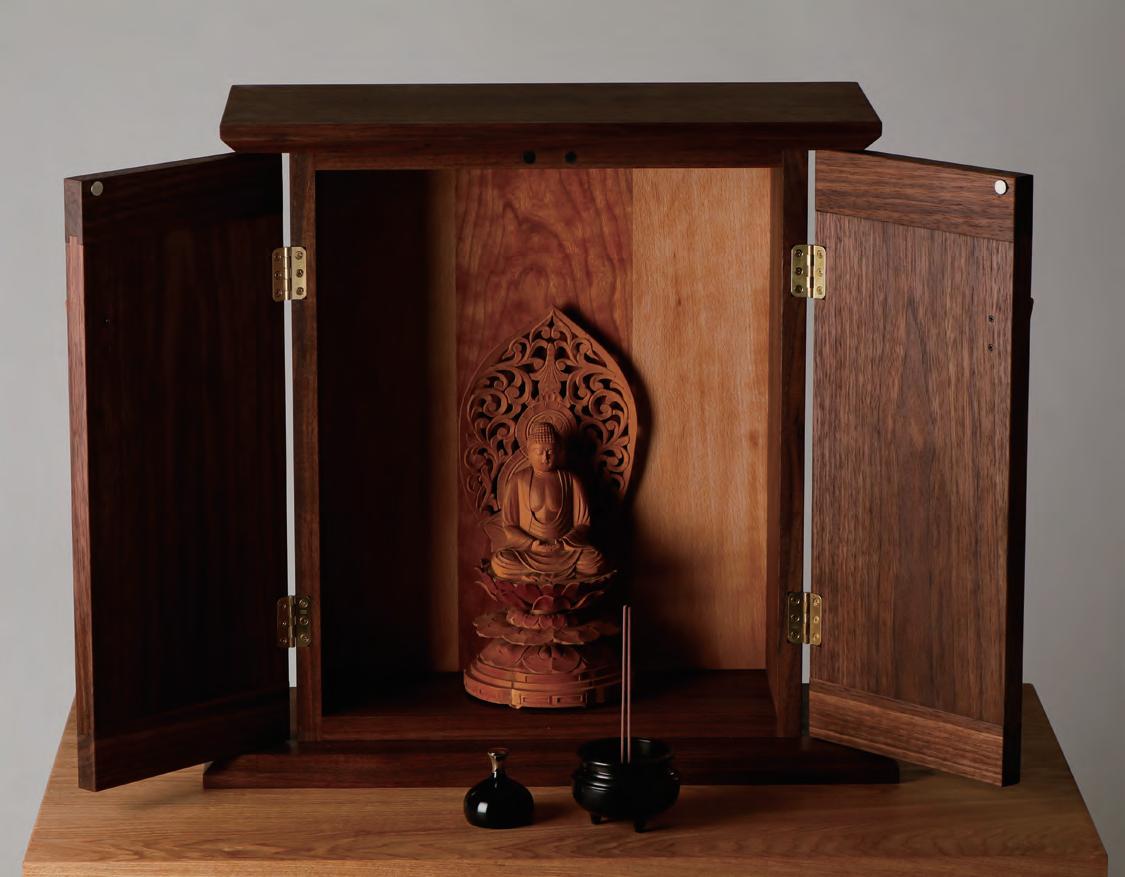

Page 136
ALTAR CABINET
Basic Tools and Equipment
Tools and equipment are needed to do woodworking. Power tools are easily available and have rapidly improved the efficiency of many work processes. However, power tools are, at the end of the day, merely hand tools enhanced for productivity, and this is perhaps why many people even now prefer to use hand tools to apply the finishing touches to projects.
People did everything with hand tools in the days before power tools existed, thus it follows that anything possible with power tools can generally be done with their non-power equivalents with enough time and labor. That said, it would not be realistic to work entirely with hand tools.
POWER TOOLS
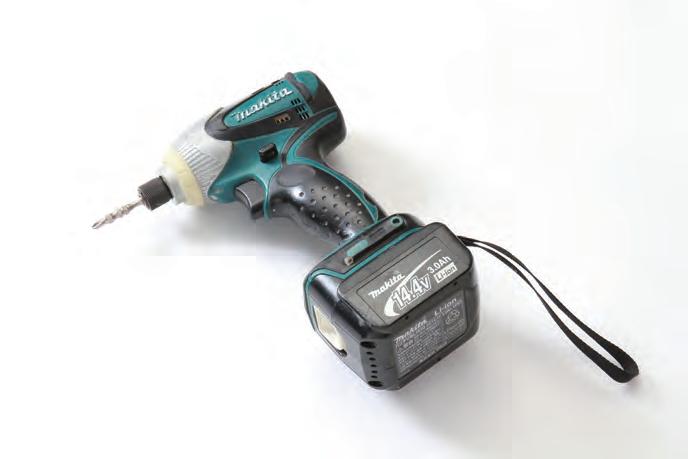
Used to fasten wood screws. Applying impact gives torque to the screw, causing it to lock in tightly.
ELECTRIC CIRCULAR SAW
An electric saw with a circular blade. Great for making straight cuts as well as angled cuts. The model pictured has a dust collector.


JIGSAW
An electric saw well suited for detailed work with a narrow blade that moves up and down. Used primarily for cutting curves.

POWER DRILL
A tool that uses a motor to drill holes. The size of the hole can be adjusted by changing the size of the drill bit.
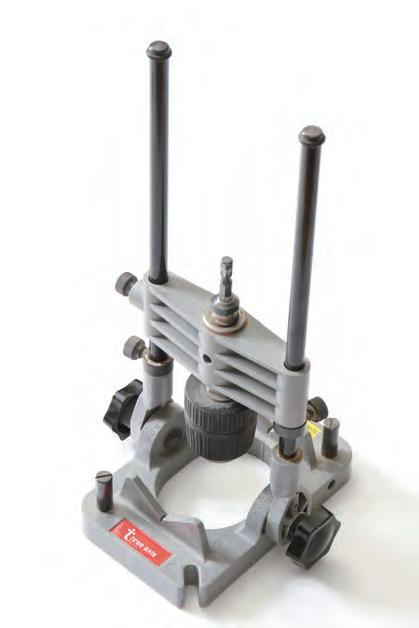
DRILL GUIDE
Pair this with a hand held power drill to fix the angle and position of holes.
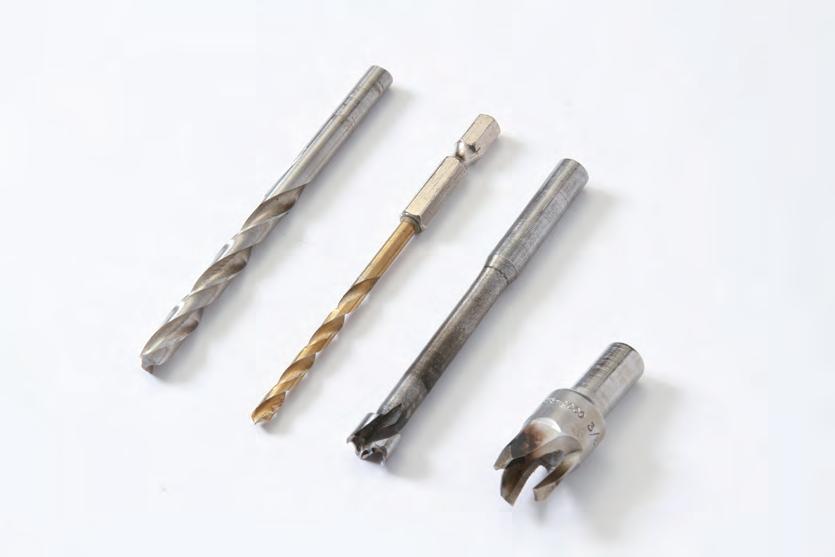
BITS
Cutting tools used in combination with the power drill and drill press. Be sure to use bits with the correct shank shape.
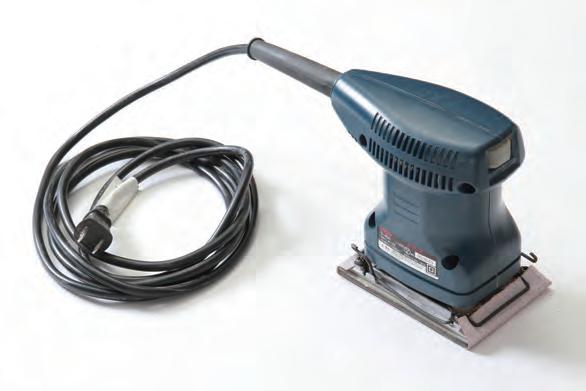
SANDER
Enables sanding to done with the aid of an electric motor. Great labor saving device!
LAMINATE TRIMMER
A power tool used primarily for chamfering that can also perform various functions by switching bits.
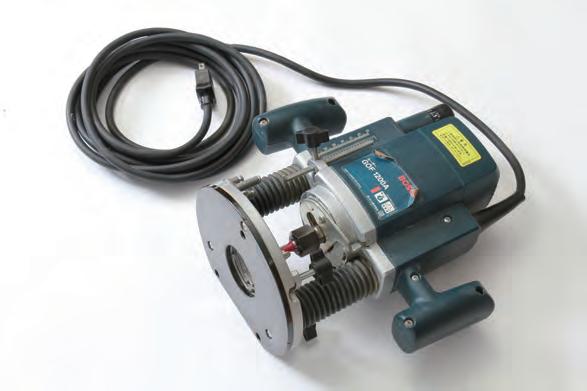
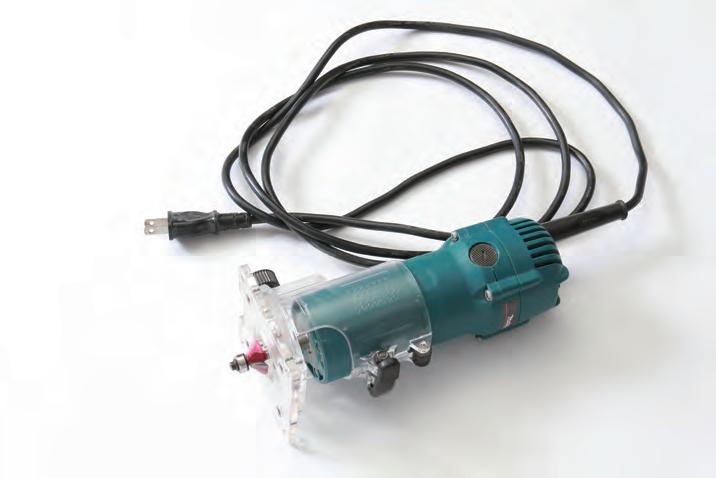
ROUTER
Though used in much the same way as a laminate trimmer, this tool boasts greater power that enables large-scale tasks such as flattening.
PLATE (BISCUIT) JOINER
A specialized tool for cutting slots when using biscuits in joinery. Having this tool on hand will drastically improve joint precision and work speed.
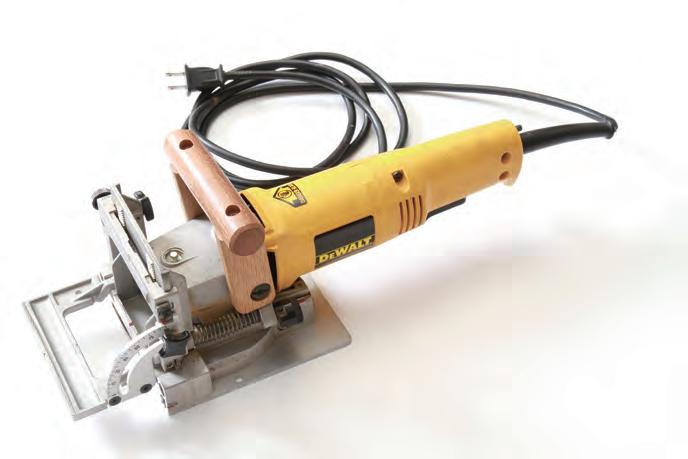
DRILL PRESS
A large power drill with the bit fixed in place, allowing for accurate hole positioning.

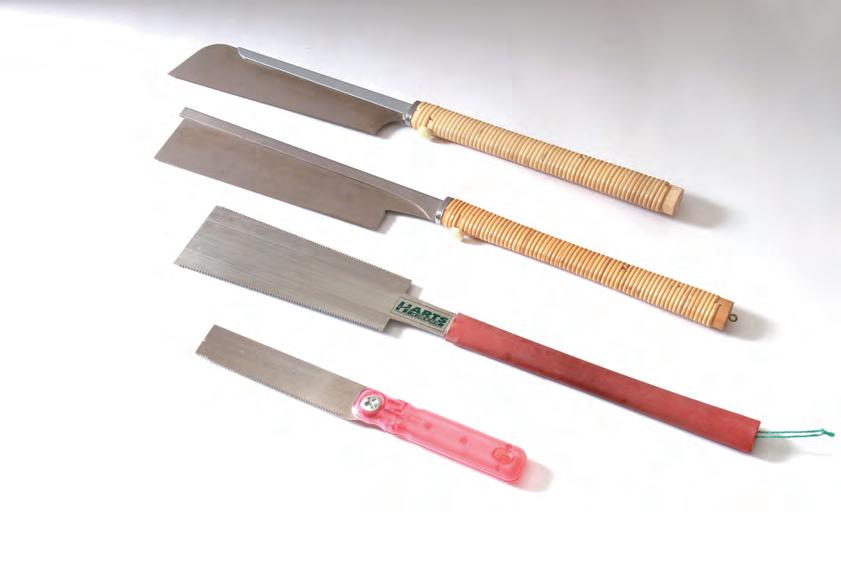
KANNA (BLOCK PLANE)
A tool for shaving the surface of wood. Indispensable when making minute adjustments to thickness or finishing surfaces.
SAWS
Edged tools for cutting wood. Variations include double edge saws with different teeth on each side, saws with guides for detailed processes, as well as saws with "no-set" teeth (no division between left and right on the blade).
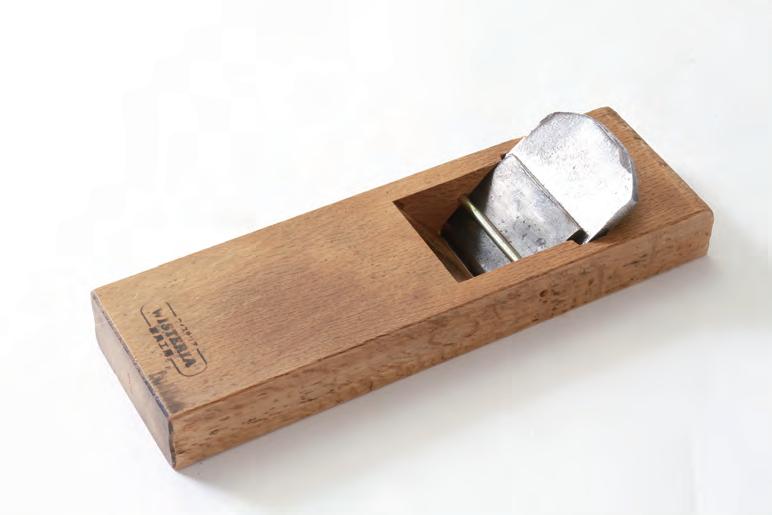
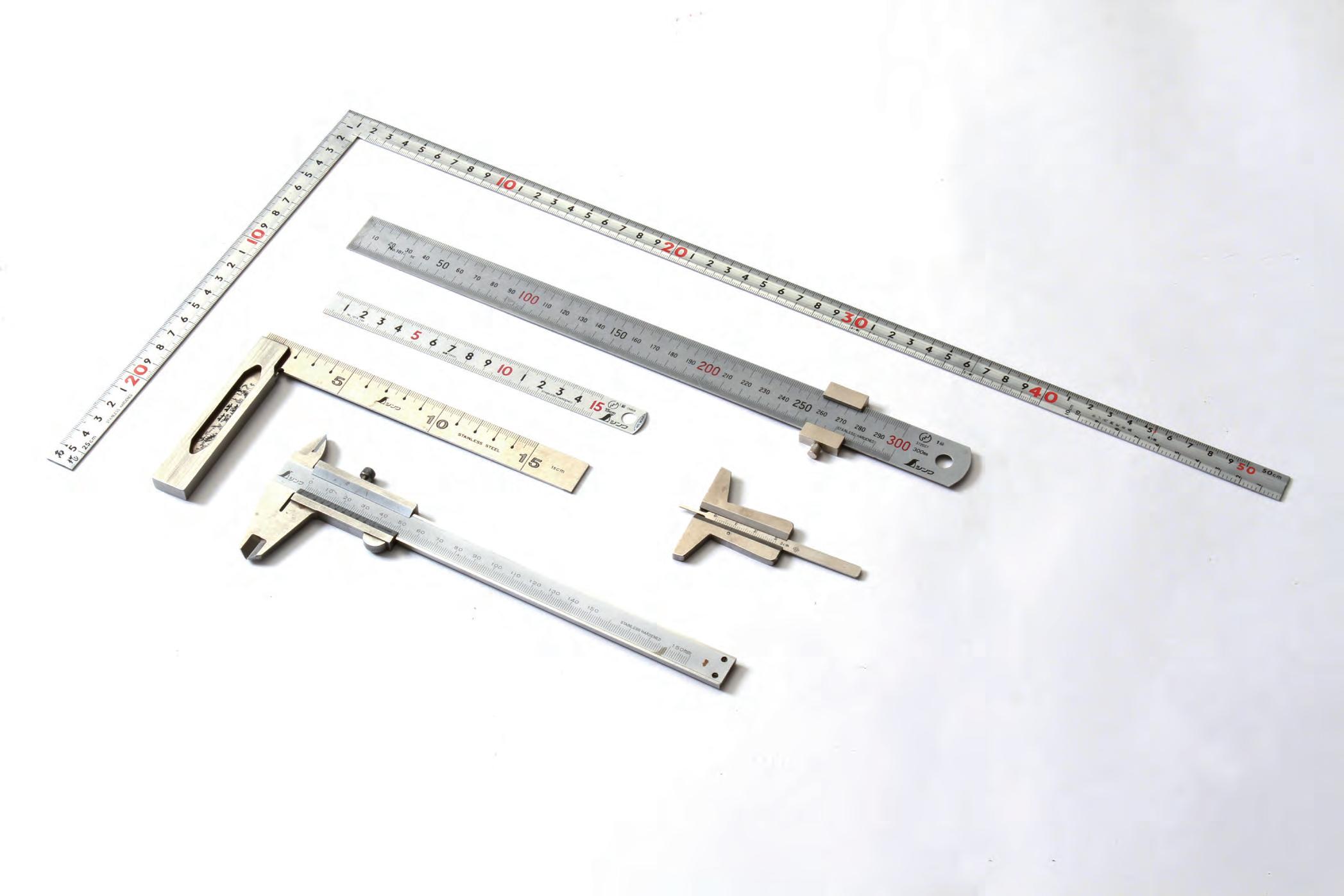
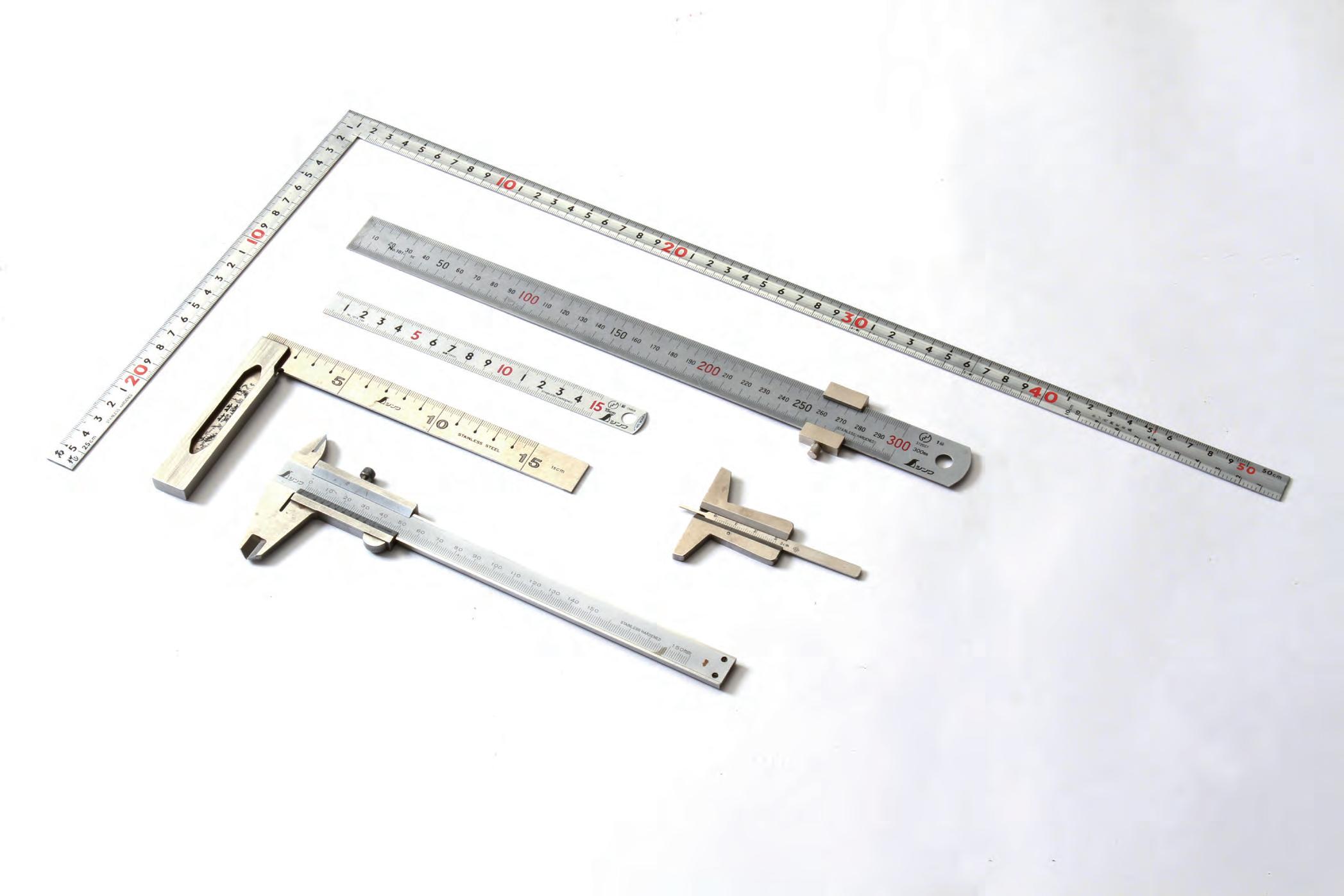
HAMMERS
While those pictured here are made of softer materials, they include a shockless hammer, typically a leather faced mallet with pellets inside to provide powerful impact, a general hammer, and a plastic hammer with faces of soft plastic.
MEASURING TOOLS
In addition to normal rulers, there are also models used for different purposes like carpenter's squares for measuring right angles, Vernier calipers for measuring thickness, or depth gauges for measuring depth.
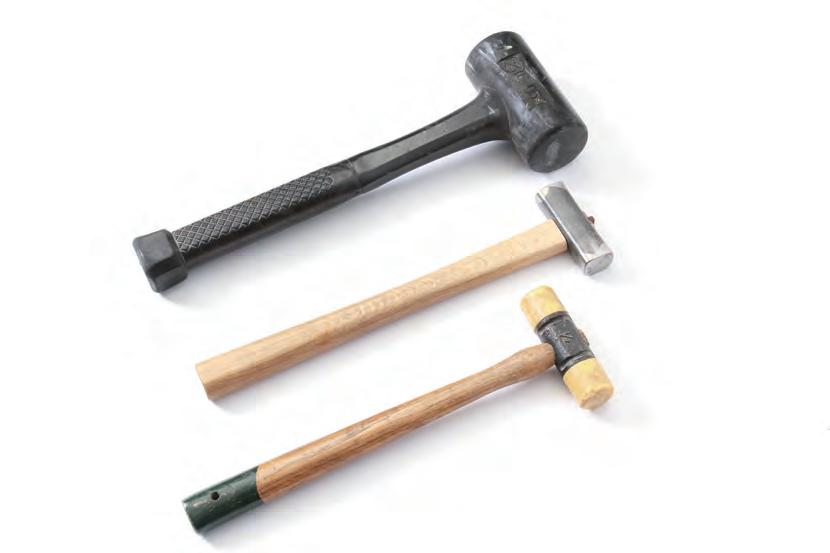
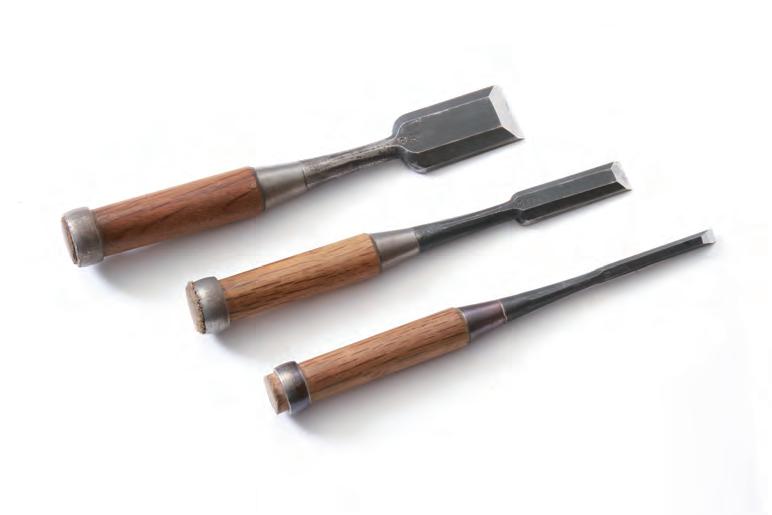
CHISELS
Tools used when making mortises or other types of holes in wood, or to apply finishing touches by shaving down the surface of detailed parts.
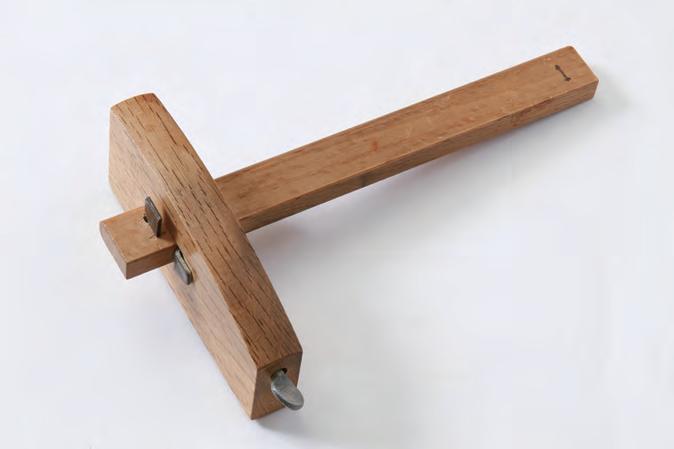
TEMPLATE (TOP) AND SHIRAKAKI (MARKING KNIFE - BOTTOM)
Templates are tools for making guided cuts following a particular shape, used mainly in making crosscuts for tenons. A shirakaki marking knife is finer than a pencil and used to create guiding lines for chisel work.
KEBIKI (MARKING GAUGE)
A tool for making parallel lines along the edges of lumber. The kebiki makes it possible to create lines uniformly at the width of the interval between the blades and the movable portion, referred to as the "ruler".

KIRI (GIMLET)
Used to make dot-shaped marks or pilot holes at locations for drilling. Can also be used to make small diameter holes on its own.
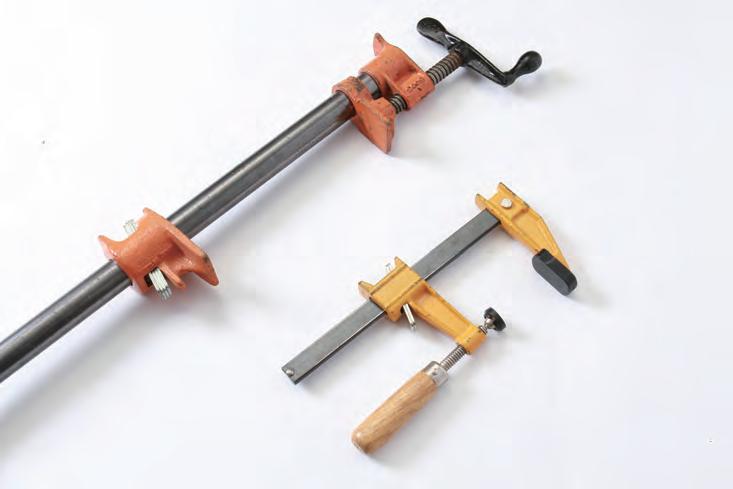


KIRIDASHI (POINTED KNIFE)
A small blade used for things such as shaving off fine portions. Available in various sizes, so use what suits the particular location best.
CLAMPS
Tools used when fixing lumber or jigs in place, or when clamping to apply pressure to pieces that have been glued together.

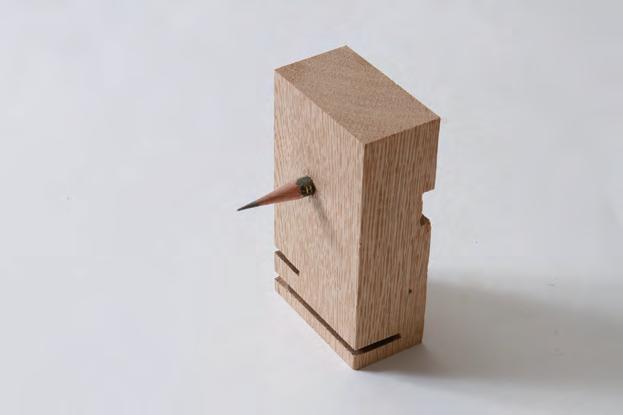
Tools that act as guides in various processes. Creating jigs at right angles or other set angles will make it easier to perform the same task repeatedly.
ADHESIVES AND OILS
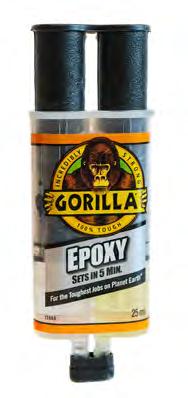
P.I. BOND
A two-component woodworking glue that offers more powerful adhesive force than standard wood glues, making it useful for areas where strength is needed.
SURFACE GAUGE
A scribing tool for marking parallel lines on vertical surfaces. Useful in processes like making leg length uniform.
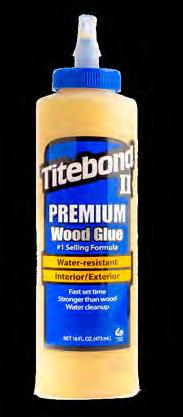
WOOD GLUE
Adhesives made especially for fastening wood together. On the left is a general woodworking glue, while on the right is a fastdrying epoxy type.
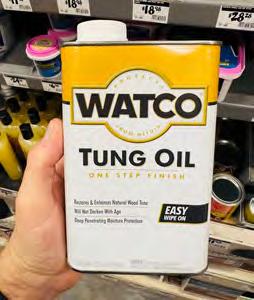
WOOD FINISHES
A finishing oil. Applied to the wood with a brush, then polished with a cloth after it has been allowed to dry for twenty minutes. Dries completely approximately eight hours after polishing.
Basic Lumber Milling
What we'll be introducing here is a process known as "milling" that produces sawn lumber. Milling lumber efficiently requires large woodworking machinery and thus a setting where such equipment is available. These days one can obtain lumber cut to specified sizes through other means such as ordering online or at a local lumber yard. Lumber yards will usually charge a fee for mill work. Mill work usually consists of jointing one edge and surfacing one side (S1S). This will give you one square edge and one flat edge. Having your lumber milled will make production much easier for those with minimal woodworking skills.
During the milling stage, the lumber will be processed to a size one step larger than needed for the actual components, then size-matched while also checking various details such as the condition of the materials. One thing to pay attention to during this stage is that the planes of the lumber are level and all right angles are properly squared. In other words, everything is square and flat. While we will be checking these things along the way during subsequent processes, the project will not go well if the planes and right angles are wrong at the milling stage.
After milling, there is an important step called "seasoning" where the lumber is allowed to adjust to the space in which it will be used for a certain amount of time (usually around two weeks) before machining. This time is set aside to allow any flaws in the wood to emerge and thus prevent any possible warping from occurring post production.
CUTTING
The very first step is to cut the milled wood into the general size we'll be using. After the condition of the milled wood has been checked over, measurements are made to determine which pieces will be cut from where. The cuts will then be made at a size one step larger than the actual size needed.
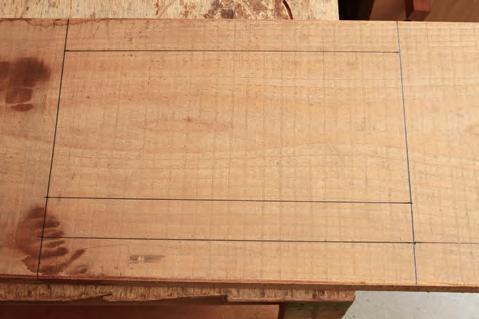
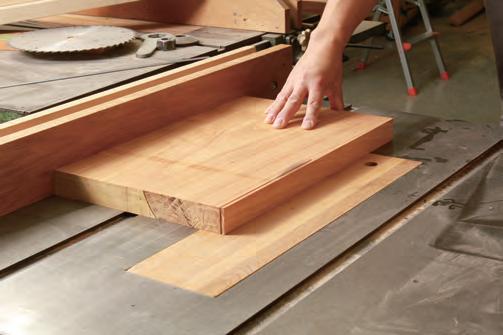
Cut lines are marked on the surface of the wood for use during milling.
Cuts are then made along the lines. If a table saw is available, then the cut sections will be at nearly right angles.

If cutting with a hand held circular saw, we recommend using a jig with a right angle, as seen in the photo.
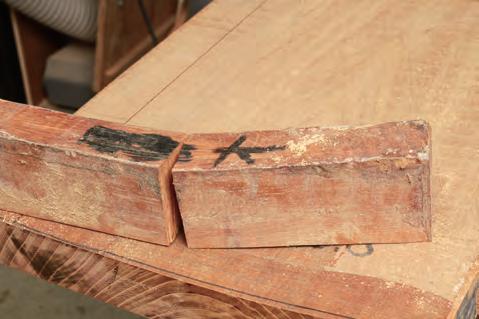
Often the ends of some pieces of lumber will be split or damaged as seen here, in which case 100 to 200 millimeters will need to be cut off before use.
FLATTENING AND SQUARING THE PIECES
Now that the pieces are cut, we will first need to flatten them, and then get all the corners at right angles. The process of producing these right angles is a basic woodworking skill called "squaring". Here we will plane the surface of the wood flat and make sure the corners are all at right angles.
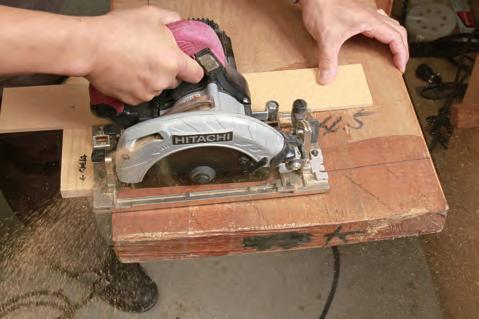
Place the saw against the jig and cut along the marked line.

Here is how things will look once the cutting is completed. The next step is to check the pieces for warping and determine how much machining is needed. If the lumber has been surfaced you should already have one good (flat) side and one good (straight) edge.
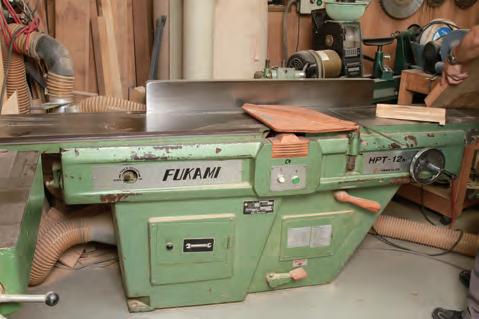
We will be using a machine called a "jointer" to square the lumber.

A jointer is used to plane down one edge of the piece. Once this edge (the reference plane) has been planed, the angles can then be squared. We check the curvature of the surfaces after each pass through the jointer.
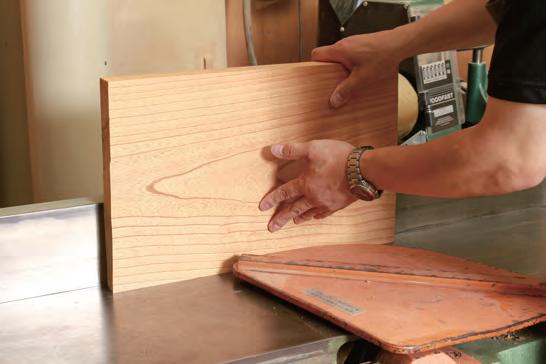
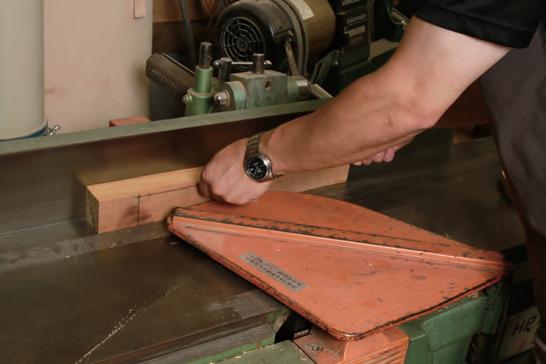
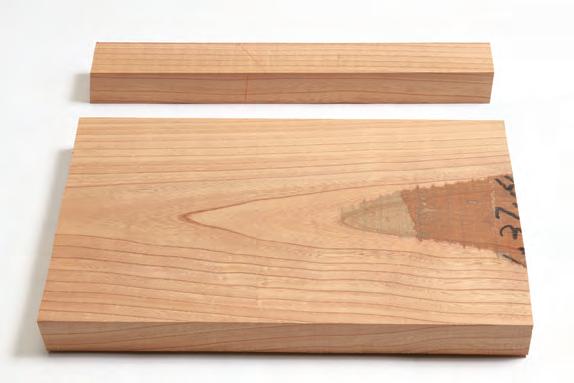
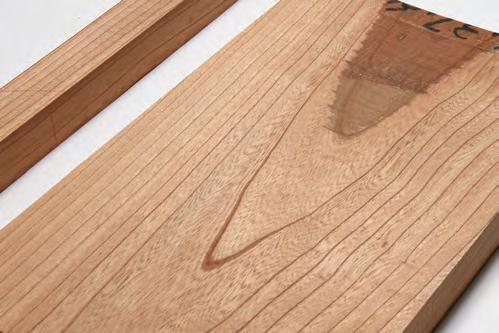
ADJUSTING THICKNESS
The last step is to adjust the thickness of the wood. We do this at a machine called a planer. The wood is planed in increments of 1-millimeter each time until we reach the necessary thickness.
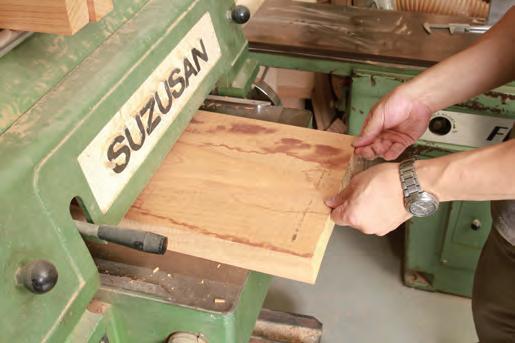
We feed the wood through the planer. This particular machine can only plane one side at a time, so we will flip pieces over and feed them back through several times.
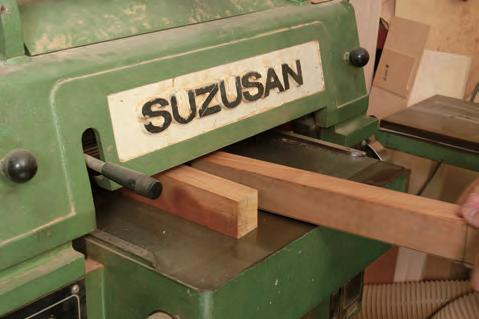
We can do several pieces at once when doing pieces like legs that need to be of a uniform size.

From here we can begin the main machining process.
FIND THE RIGHT MATERIALS AND WORK ENVIRONMENT FOR YOU
Thanks to the advanced online and mail order systems we have today, you can chose what condition to obtain your lumber in. What's more, milling one's own lumber is no longer an impossibility thanks to the increased availability of small, affordable woodworking machinery though there are limits to the sizes they can handle.
For hobbyists, what level of tools and machinery one can access and use will greatly affect both the kind of carpentry projects you can undertake and the quality of your output. If procuring the machinery on your own will prove difficult, there is also the option of working in a location with the proper equipment, such as a rental workshop or woodworking classroom. So, determining what materials and work environment suit your needs best is also extremely important.
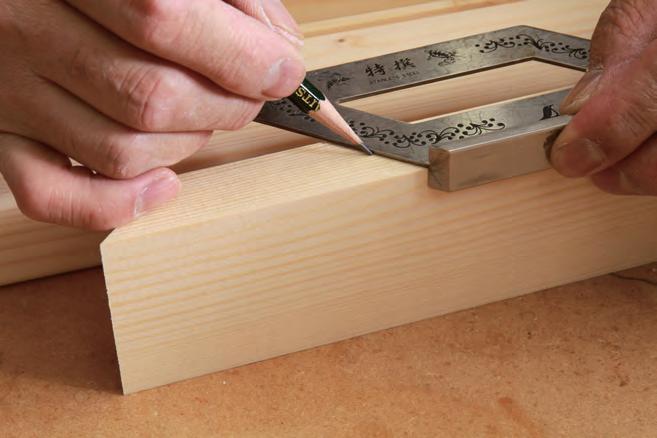
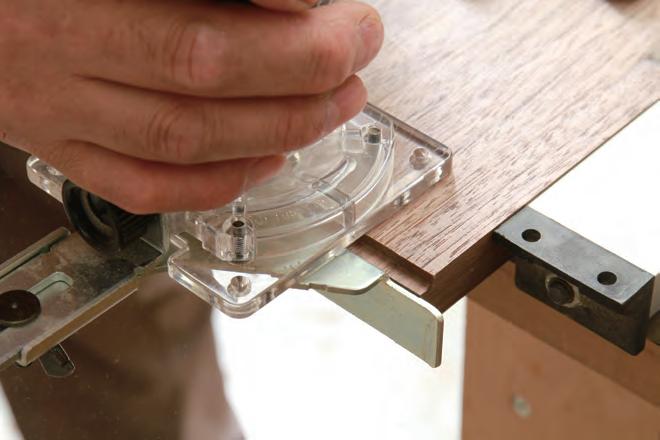
Furniture Projects
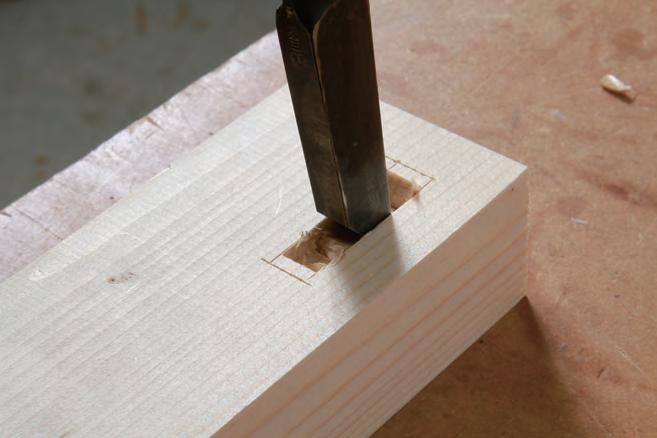
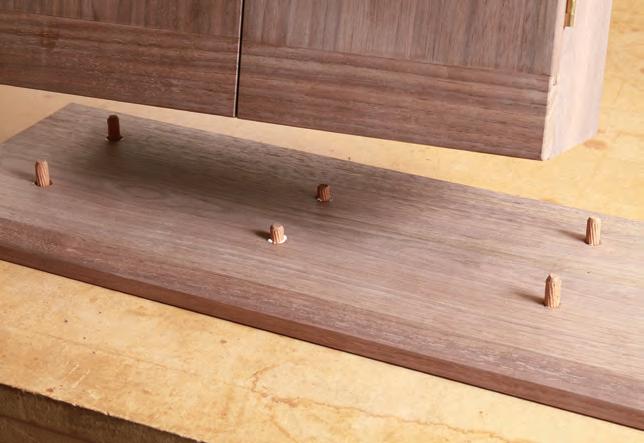
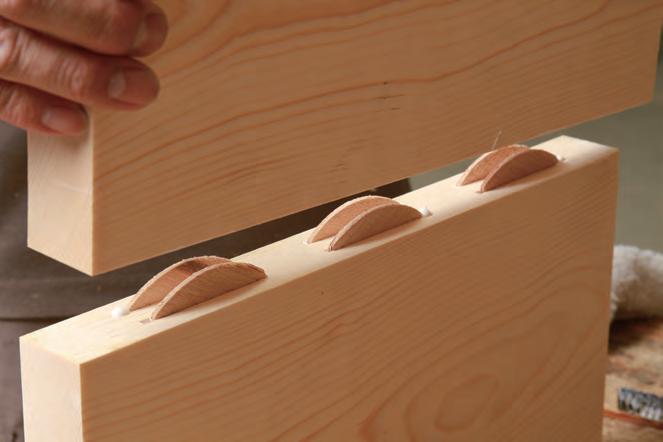
Here we will be laying out the instructions for five kinds of woodworking projects, each of which incorporate full-fledged carpentry techniques to produce items that may look simple at a glance but are satisfying to make. The impression the finished item has will vary greatly depending on the type of wood used, so choose materials that suit your preferences to add a dash of originality.

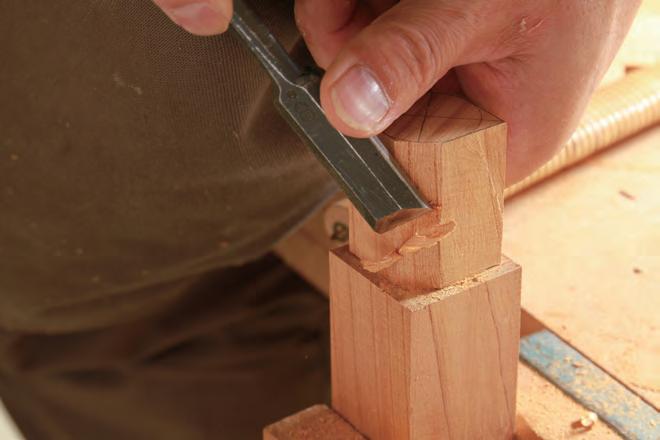
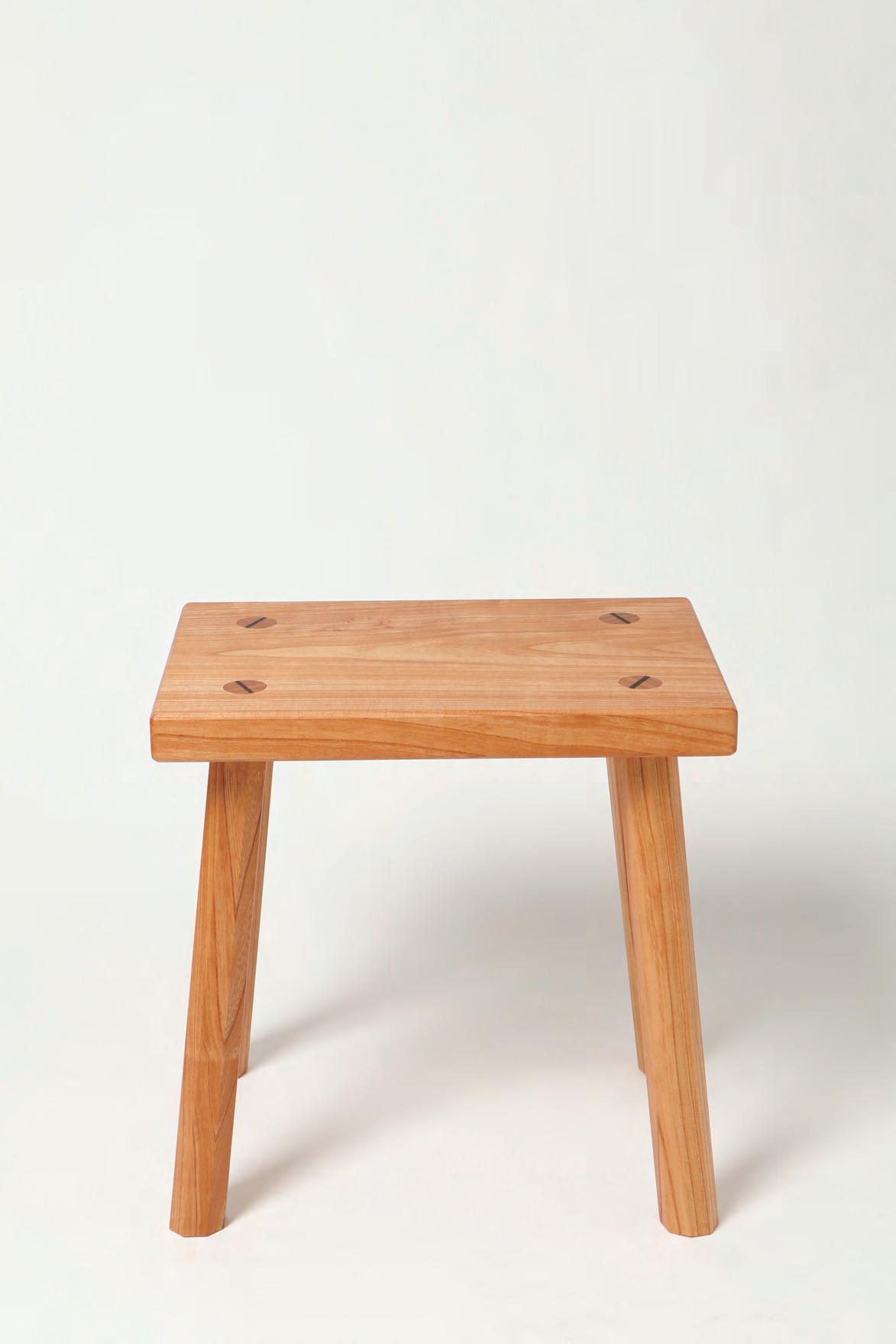
STOOL 1
This stool has an uncomplicated design featuring a rectangular top with octagonal legs. The legs are attached at 10° angles and then fixed in place with wedges. Despite not having many pieces, this project features a good range of woodworking techniques.

Chamfering enhances the level of completion in the finished stool.
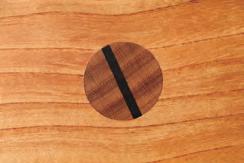
Rosewood is used for the wedges that lock the legs in place to provide a bit of accent.

The octagonal legs give the stool a clean effect.
The angle of the legs is the key to the design
The wood for the stool featured here will be keyaki (zelkova serrate, a member of the elm family). Hardwood is used for the legs to provide sufficient strength at the point where they are attached. In order to attach the legs at an angle pointing 10° toward the corners of the top, it is vital that the mounting holes be angled as well. Also, while wedges will be used to lock the legs in place, we will be making them out of rosewood to give an accent to the design.
Angled image
Chamfered edge Angled image
Top board: 400mm x 280mm x 35mm
Legs (4): 440mm x 40mm x 40mm
天 板 天板 400mm×280mm×35mm 脚 440 mm×40 mm×40 mm×4本
Octagonal
Octagonal
PREPPING THE MATERIALS
Once the lumber has been squared and flattened, we will be cutting it according to our measurements. The top can be cut as measured since we won't be making any major size adjustments. However, the legs should be cut around 50mm longer than needed since we will be making some length adjustments post assembly.
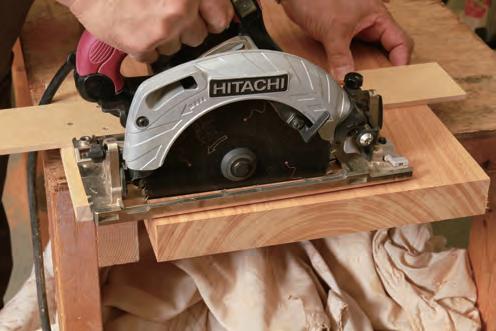
Cut the top to 400mm x 280mm.
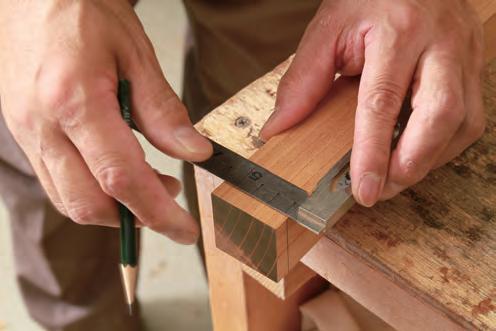
We will be cutting the top and bottom surfaces of the leg lumber so that they are parallel, so use a square to draw cut lines.
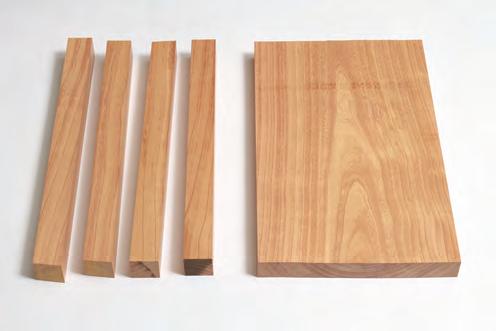
01 Start with lumber that has been planed flat.
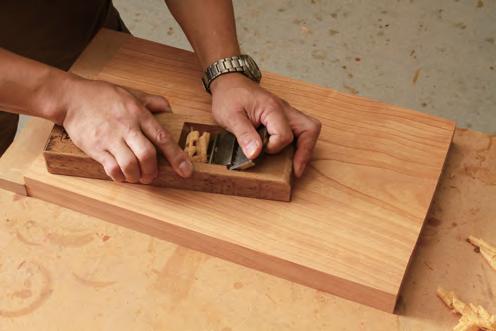
Go over the surface of the top with a block plane. We will be using a block plane several more times but it's good to put the surface in order once here.
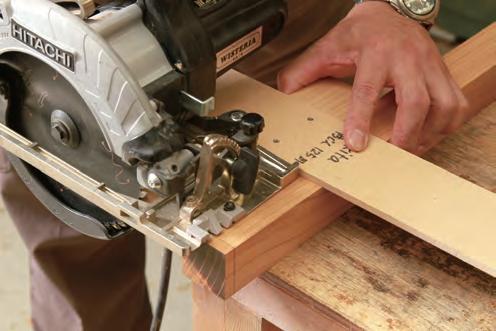
Cut the top and bottom of the leg lumber along the cut lines drawn in step 04.
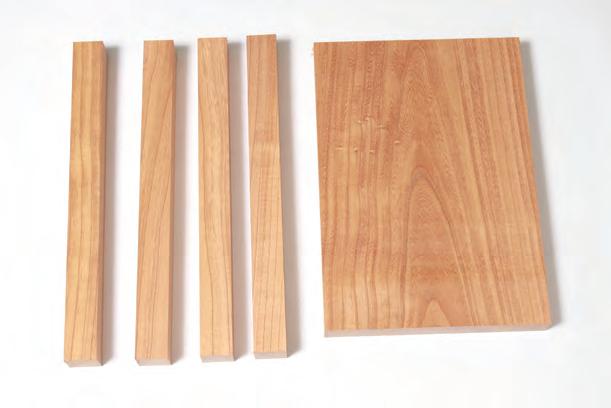
Here we see the top of the stool, now cut to its basic size, and the legs with their top and bottom surfaces made parallel.
MAKING THE LEGS
We will now cut the legs. This stool has octagonal legs, but we will be cutting the upper tips into a cylindrical shape 30mm in diameter so that they can be inserted into the top board. We will use a hand saw to cut out the portion that will be inserted, then apply the finishing touches with a chisel and kiridashi knife. The octagonal portions will be finished using a block plane.

The completed circle. Check to make sure that it is in the center of the leg.
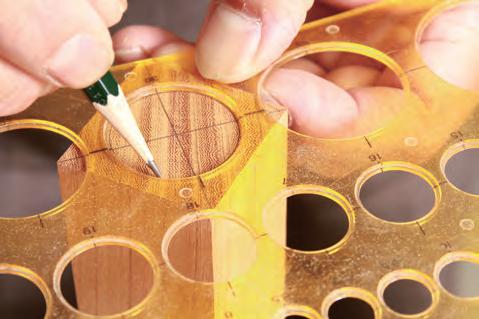
01
Draw lines connecting the corners of the surface that will be the top of the leg to find the center, then trace a circle with a diameter of 30mm.
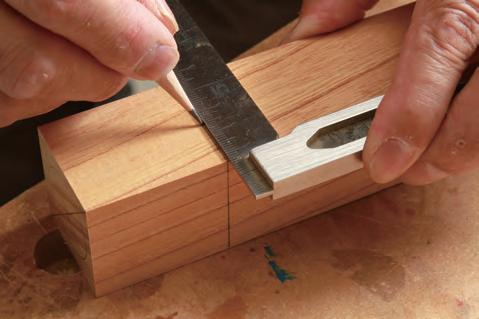
Use a square to draw lines at a position 50mm below the top of the leg. Everything above this line will be worked into a cylindrical shape.
KEY POINT

Make an incision about 5mm deep on all four sides along the lines drawn in step 03.
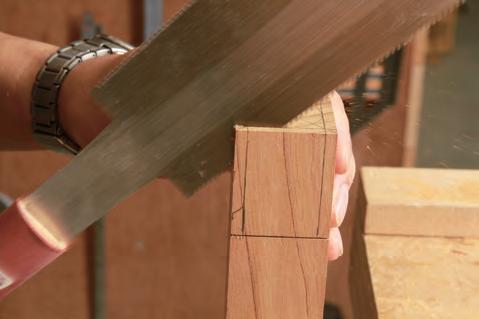
Cut a vertical incision along the edges of the circle.

Connecting the vertical and horizontal incisions will allow 5mm to be removed from each side down to 50mm from the top, resulting in what you see here.
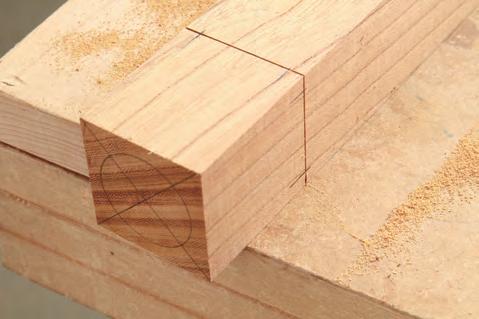
A leg with incisions cut into all sides.
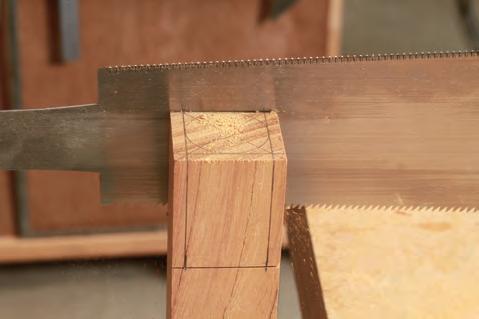
Make these vertical incisions on all four sides, cutting until you reach the horizontal incisions made at the 50mm mark.
KEY POINT
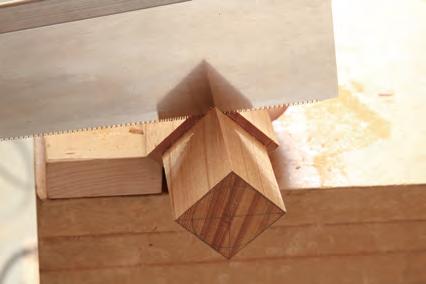
Fix the leg in place with a corner facing up. Then, at 50mm from the top of the leg, make an incision to the line of the circle.

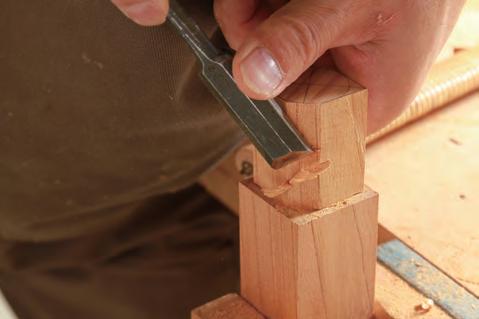

Once incisions have been made on all four corners, shave off the corners vertically using a chisel following the outline of the circle. Rather than trying to shave off an entire corner in one go, repeat several times, chiseling down as close to the line as possible.
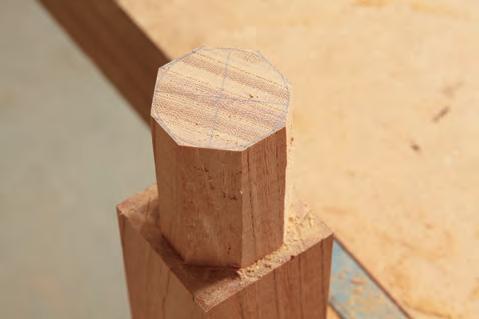
The tip of the leg should resemble an octagon once all four corners have been removed.
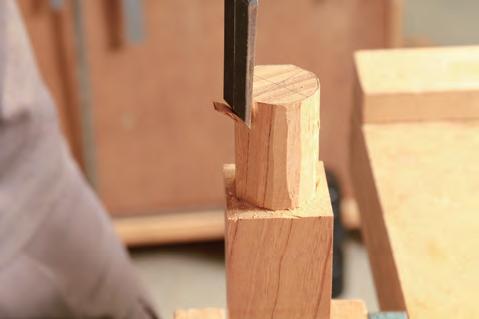
Chisel vertically along the outline of the circle to further perfect the octagon. Make sure your approach is straight downward so that the chisel doesn't stray inside the circle.
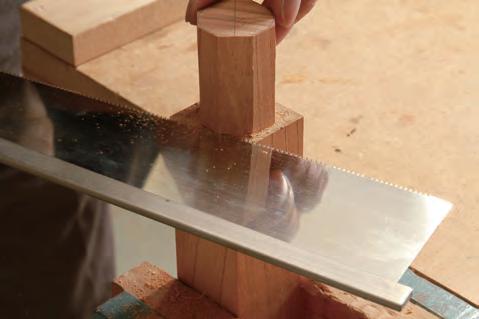
Now make incisions down to the outline of the circle at all eight corners.
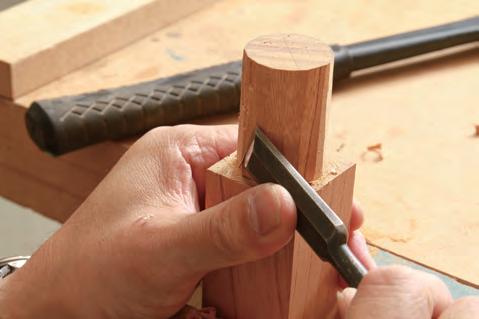
Once you have the octagon, chisel off the corners to reach more of a cylindrical shape.
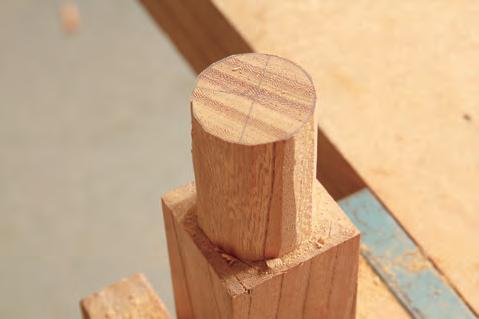
Shave the wood down a bit at a time to reach the desired shape, checking the circle on the tip as you go.
KEY POINT
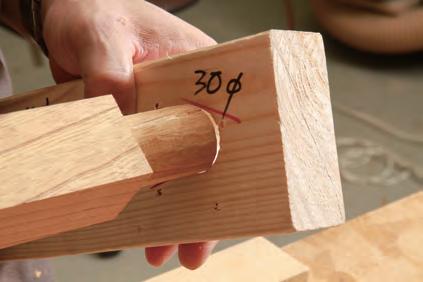
Prepare a piece of scrap with a 30mmdiameter hole and cut the leg down bit by bit until it fits inside.
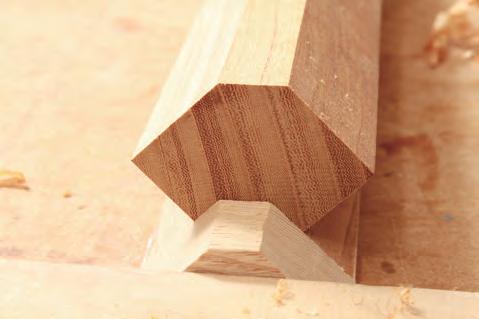
The leg with one side planed off. Plane the other three corners so that each side is approximately 15mm wide.
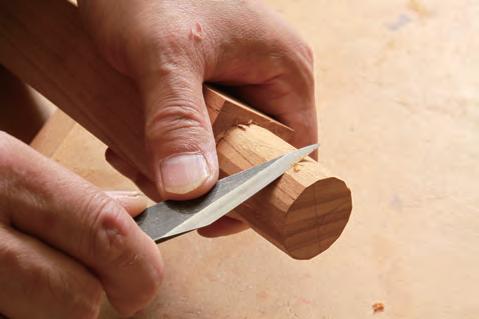
Use a kiridashi knife and file to make the tip of the leg as rounded as possible.

Once the tip is completed, we will then plane the remaining square portion of the leg to make it octagonal.
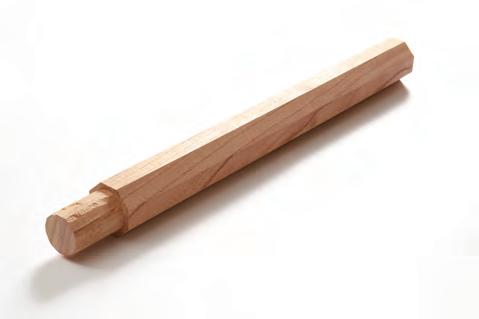
As can be seen here, the end of the leg that will be inserted in the top is round, while the external portion is octagonal. Repeat these steps until you have a total of four legs.
MAKING THE TOP
We will be drilling holes in the top of the stool angled 10° toward the corners, with the legs then attached splaying outwards. It is crucial that the holes for attaching the legs be made precisely, so make use of a drill guide if working with a hand drill, or a jig at a 10° angle if using a drill press.
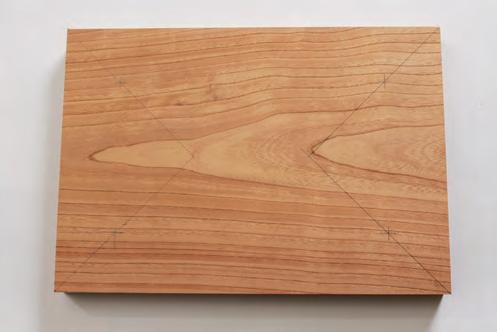
Measure 50mm from the short side, then make marks at the points where the lines drawn in step 01 intersect with this position. These marks indicate the center points of where the legs will be attached.
KEY POINT
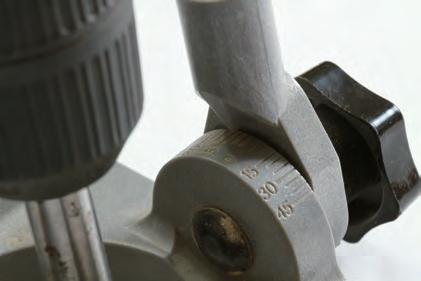
Set the angle of the drill guide to 10°, then make sure the screw is fastened tightly.
DRILLING THE HOLES FOR THE LEGS

Draw lines at 45° from each corner on the upper face of the top. The lines will run into the lines drawn from opposite corner on the short side.
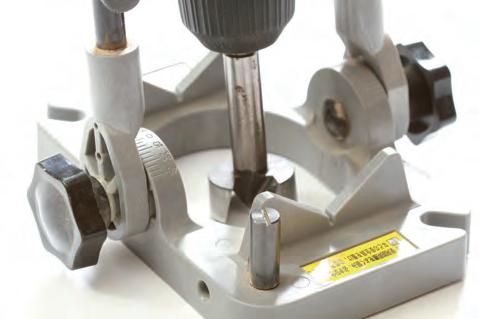
We will be using a drill guide to angle the holes for the legs at 10°.
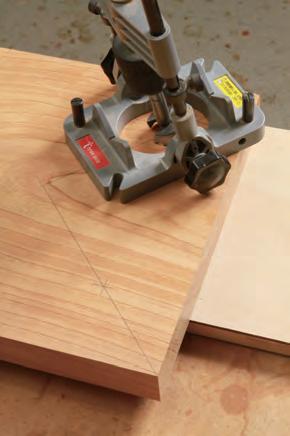
Center the drill guide on the line drawn in step 01, then set the tip of the bit on the mark made in step 02.
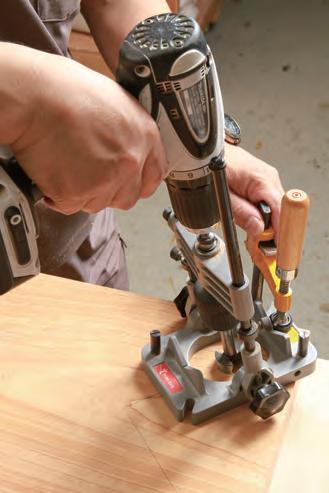
KEY POINT

Clamp the drill guide down tightly so that it will not move. Drill the leg hole using a 30mm-diameter bit.
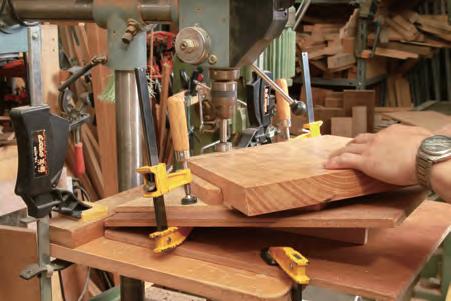
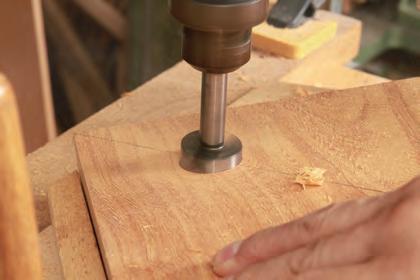
If making the leg holes with a drill press, make a jig with a 10° angle, then set the stool top on top of the jig before drilling the hole.
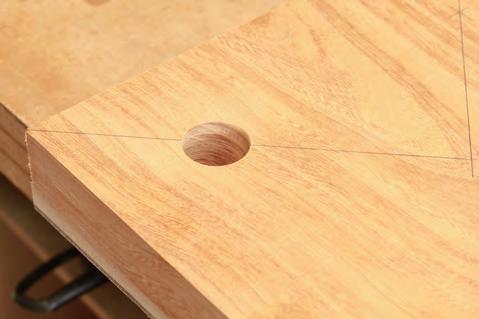
The top with a hole drilled at a 10° angle toward the corner.
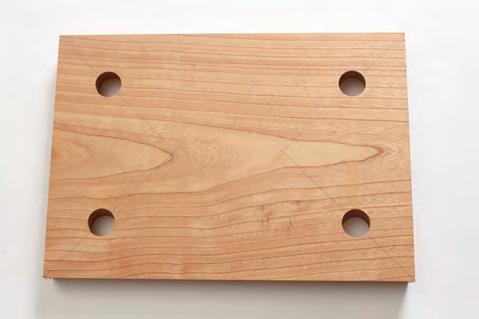
Repeat these steps until all four leg holes are complete.