
6 minute read
Luxury Sinks Handmade in the Heart of Lancashire
The Whitebirk Sink Company specialises in handcrafting unique Belfast sinks, utilising the technical expertise of sister company Darwen Terracotta, allows customers to choose from a vast library of sink designs, textures and shades.
When one of the UK's oldest and most highly respected terracotta companies closed its architectural division to concentrate on their fireclay sink business, the opportunity arose for former employees to set up a new business and re-employ the very skilled craftspeople.
Advertisement
“It was really important that we could employ many of the team we have worked with for so many years. Apart from the friendships involved, the product is so specialised that we could not see the loss of these skills that Darwen has been famous for since the end of the 19th century.
The industry, including Architects and Contractors, has been so very supportive, that it has been heartwarming and keeps alive the passion required to produce this high-quality product.”
— Jon Wilson, Darwen Terracotta
Darwen Terracotta have an expert team that has many years of experience within the industry, having worked on both restoration and new build projects for some of the most prestigious buildings in the UK, Europe, North America, Canada and Australia. We have the specialist skills required to design, sculpt, match and produce terracotta and faience to the highest standard to restore any building.
Darwen’s work is featured on building such as the London Collessium, home of the English National Opera, this Frank Matcham designed, Grade II theatre required 4600 new terracotta blocks to the façades and tower, along with replacement Atlas figures and lion sculptures.
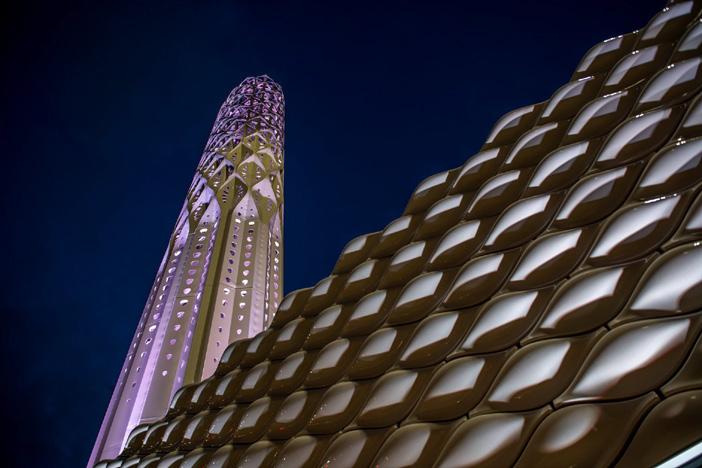
The Natural History Museum in which our sculptors have worked on both the external and internal facades. Harrods Department Store, which we have been working on continually for over twenty-six years, recreating the terracotta to the facades and roof areas.
As for the New Build sector of the business, because handmade terracotta and faience offer practically unlimited design flexibility for shape, size and colour, the only real limit is your imagination. The most recent job to be completed is the 'Wall of Energy', this building encompasses the new 40m tall 'Tower of Light', delivered by Manchester City Council and Vital Energi. The wall will be partially transparent and will allow passersby a glimpse into the energy centre. This scheme includes over 1300 of our hand made ceramic units for the low-carbon energy centre. The centre is projected to save 3,100 tonnes of carbon emissions in its first five years of operation, the scheme will help Manchester achieve its ambition to be carbon-free by 2038.
Harrods Department Store, London
The skills that are required to manufacture first-class terracotta products sit side-by-side with crafting our luxury fireclay sinks. Our skilled craftsmen have been mastering the handmade manufacturing process for over 50 years. Over time, our minds wandered to further possibilities of what could potentially come from these remarkable sinks.
Technical raw materials and knowledge aid innovation and assist in the development of new sink glaze colours, textures and applications with results ranging from matt pinks and metallics to high gloss mottles.
We are able to create gloss levels, glaze colours and textures which are not normally associated with sanitary ware products. This is due to the ready availability of ceramic matte to high gloss glazes, pigments and oxides used in the production of terracotta and faience. However, the more challenging, extraordinary or mottled the finishes are may require the sourcing of additional raw materials, and therefore take a little while longer. We are lucky to have a technical department at our disposal with over 50 years' experience and 100 years worth of glaze recipes, but we are still developing and pushing the boundaries of colour technology to achieve our client's requirements today.
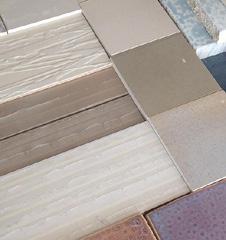
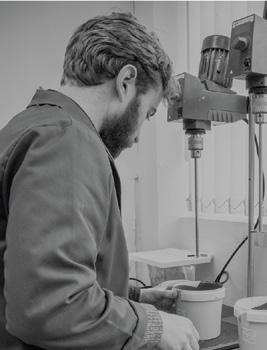
Every authentic sink in our Collections takes time to create, and the result is a true masterpiece of traditional manufacturing.
The nature of our handmade process creates tiny but distinctive variations between each sink, making every one of them truly unique.
Each handcrafted single sink in our traditional Heritage Collection is as practical as it is beautiful, and equally at home in traditional or contemporary kitchens. They are available in a range of understated styles, all guaranteed to provide a lifetime of service and pleasure.
Add a splash of colour with the beautifully designed sinks in our exclusive Colour Collection. They are available in various contemporary finishes, that put a modern twist on a classic traditional style, making them iconic focal points for any kitchen.
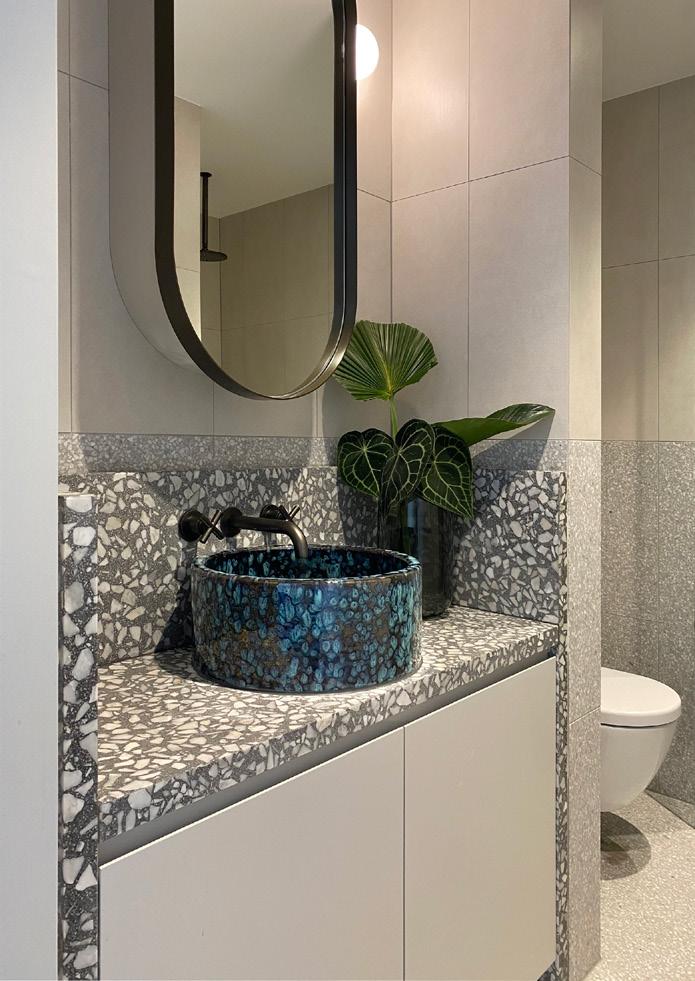
Complex glazes are used in the manufacturing process to create the stunning sinks in our Mottled Collection, producing distinctive patterns that give them a vibrant contemporary look – perfect for making a statement.
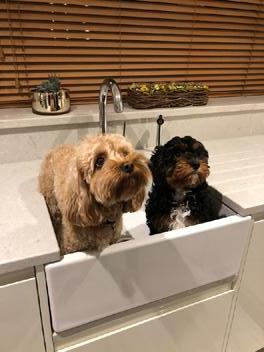


MODELLING AND MOULDING
Each different design of sink is hand modelled in plaster, formed slightly oversize to allow for the natural clay shrinkage that occurs through the production process. From here we make the reverse plaster mould, which will be dried for up to two weeks in dedicated temperature-controlled rooms. This ensures optimum production performance and dimensional consistency.
CLAY CASTING
We use virgin local clays, giving us an industry-leading level of control over dimensional accuracy and consistency. Our clay is cast into the preconditioned moulds, tightly packed to a controlled thickness and left to start the drying process. This method has been used for centuries and is tried and tested to offer the best performance specifications and strength.
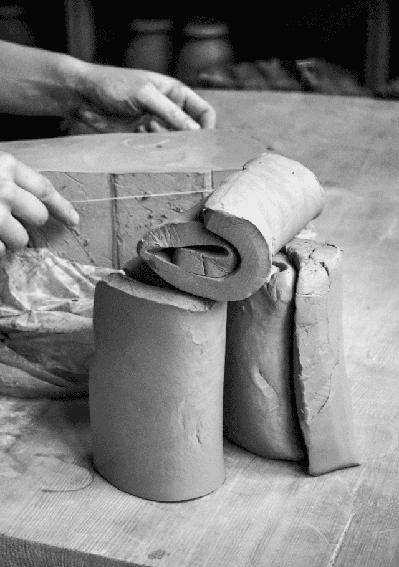
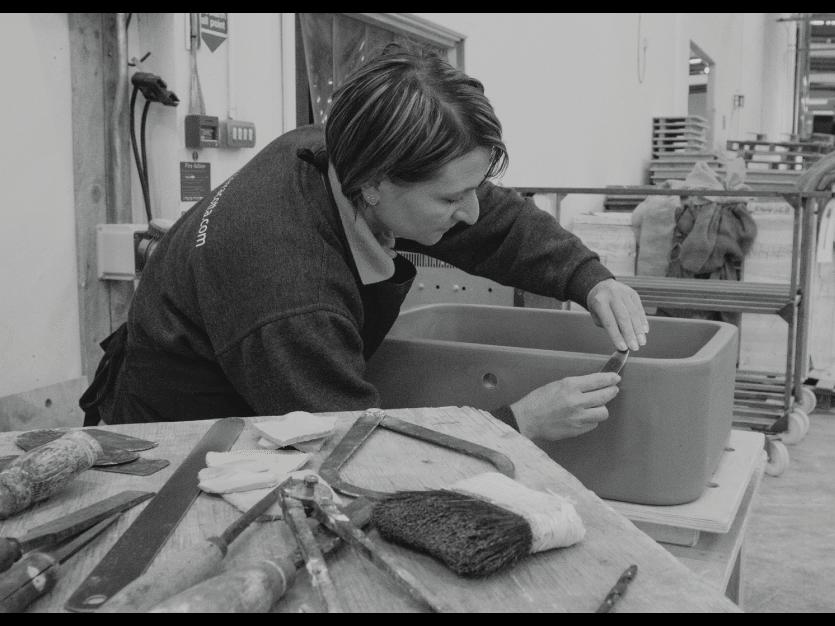
HAND FINISHING
After the sink has been turned out of the mould, we meticulously hand finish the surfaces with a variety of wooden and metal tools, along with leathers, all to give the required finish.
DRYING
The sinks are allowed to dry naturally at room temperature for a few days. Then, they’re moved into our automated, humidity-controlled drying rooms, to fully remove any residual moisture.
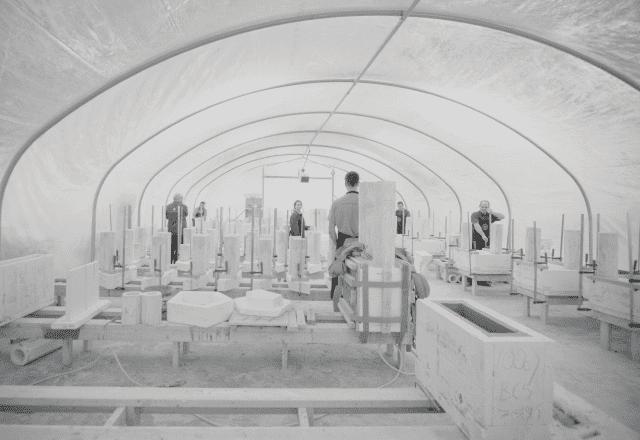
GLAZE APPLICATION
The glazing is done in two stages. First, the englobe (an undercoat) is applied, then they are given the final coat of glaze. In the case of our mottled finish, complex glazes are required to achieve this beautiful effect. This process takes a three-coat application. Now, they’re ready for the kiln.

FIRING
The sinks are set on the kiln for a firing process that will take them over 36 hours, reaching temperatures of more than 1180 degrees Celsius. We obtain the beautiful finish by firing at varying temperatures during this time, before the sinks are allowed to cool naturally in the kiln.
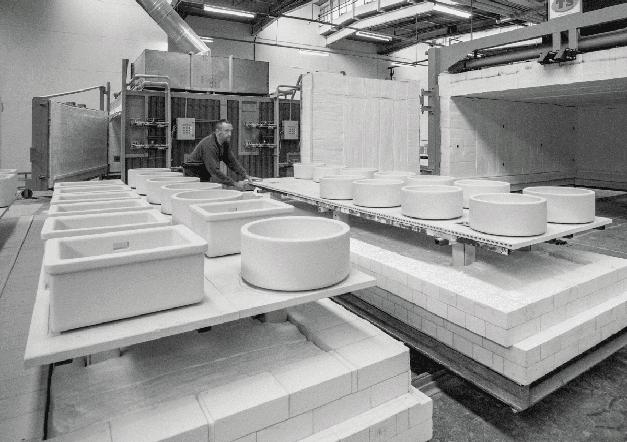