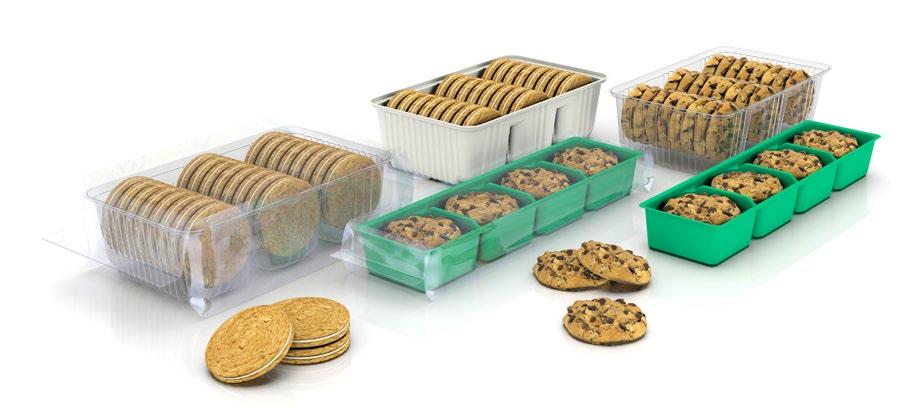
4 minute read
Syntegon: New Intelligent Direct Packaging technology
This is intelligent handling
Syntegon has developed a new solution for the handling and portioning of cookies and crackers. The compact, smart machine ensures gentle processing as well as flexibility.
© Syntegon
Both vertical and horizontal assemblies can be realized
+Syntegon’s new handling and portioning equipment features Intelligent Direct Handling (IDH), a solution based on a recently developed picker technology that uses linear motors. The IDH station or leg can be integrated into conventional flat handling systems for distribution, portioning, or on-edge and flat loading into trays or flow-wrapping machine infeeds.
Its pick-and-place system is designed for gentle product handling and has a high output, with the option of loading different products both flat and on-edge. The IDH can be equipped with up to 40 vacuum pickers, which are all attached to a picker bar. Each picker is controlled by a linear motor, ensuring that each product is picked from the process belt and placed into a flow-wrapper infeed or trays. “Thanks to the controlled movement of the motors, the picker’s movements are slow and smooth. In combination with low vacuum suction, the IDH ensures gentle handling with minimal mechanical stress and breakage,” Syntegon tells us. The IDH picks the cookies directly from the process belt to keep the transport distances between the oven and the packaged product as short as possible, thereby reducing abrasion.
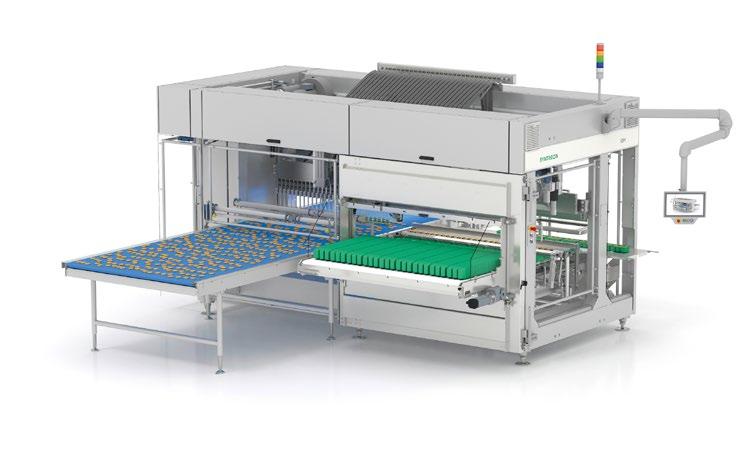
Linear motor technology is one of the key efficiency features of the IDH. Philipp Kathan, Lead Engineer IDH at Syntegon, explains: “Thanks to the slow and smooth movements of the linear motor movers, the cookies and crackers are handled with minimal mechanical stress and vacuum application –preventing breakage or damage to the product surface and ensuring optimal production efficiency.”
The picker’s smooth and controlled movements are possible due to an integrated camera-based vision system. It even detects the position and shape of cookies and crackers that are randomly placed on the infeed belt: “The system transmits this information to the picker control system so that the linear motor is able to align each picker correctly with the incoming product. Moreover, an integrated mini buffer automatically fills incomplete product rows, thus increasing system efficiency,“ Syntegon explains.
Any shapes in all packaging styles
The IDH is flexible in terms of production volumes, product shapes and pack styles. In case of an increase in product
© Syntegon
output, for example, up to 40 vacuum pickers can be added to the picker bar. When integrated into horizontal packaging lines, the IDH can package cookies, biscuits or crackers of any shape, as piles and slugs, in trays or flow wraps.
In addition, the IDH makes the packaging process less complex: its design not only minimizes conveying distances but also allows for new system layouts traditionally used in bar production. Despite its compact size, the IDH achieves a maximum output rate of up to 800 products per minute. In combination with low reject rates and short downtimes, the high output contributes to the equipment's overall effectiveness (OEE). “Cookies and crackers are picked directly from the process belt and placed into trays or the infeed of the downstream flow wrapping machine either on-edge or flat. This allowed us to omit long belts with chicanes and make the system design even more flexible,” explains Daniel Bossel, Product Manager at Syntegon.
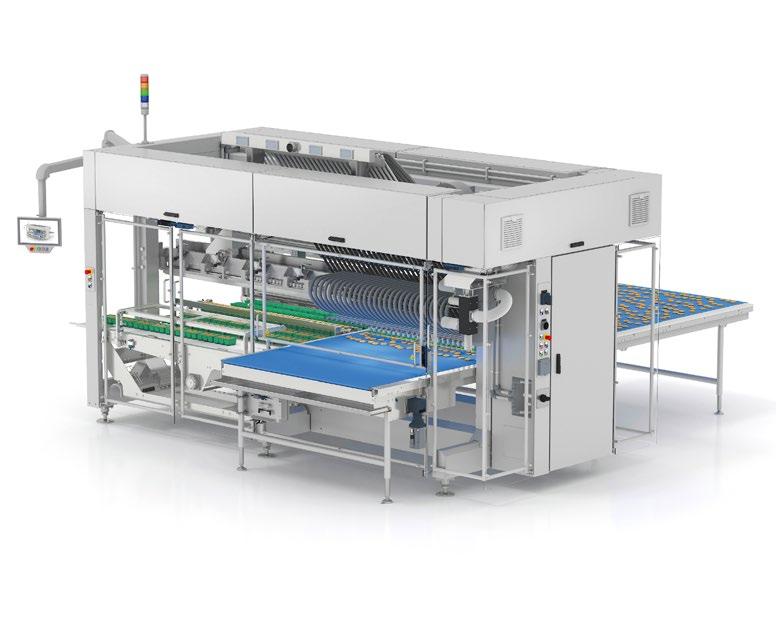
The IDH system simplifies the packaging process in several other ways as well: its compact layout means that there are fewer wear parts, sensors and actuators, and shorter buffers are required. “The use of pickers further enables software-based format changes that only require a couple of clicks. Operators can easily switch from pile to slug and change the product count of any given configuration. The IDH’s hygienic design also simplifies production.“
“The Syntegon IDH complements the Syntegon RPP pickand-place platform launched in 2021 perfectly,” Bossel explains. “While the RPP's delta robots pick up to 120 products per minute from a narrow belt, the IDH is ideal for higher volumes and particularly wide process belts. With our comprehensive portfolio for the cookie and cracker industry, we are able to offer our customers tailored system solutions with a low TCO from a single source.” The IDH system makes its debut at this year's Pack Expo, held in Chicago from October 23 to 26. +++
ADVERTISEMENT
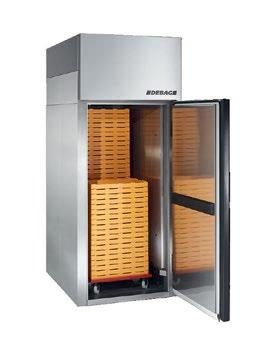
DECON: Now with highperformance steaming
GUV 1: Long-term dough process in store
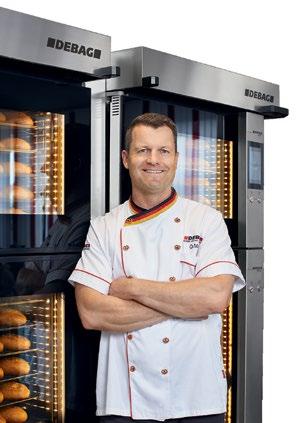
A strong duo for stores!
DECON in-store oven
Multifunctional: baking, cooking, regenerating Now with high-performance steaming for particularly gentle baking
GUV 1 fully automatic dough retarder
Compact, powerful Ideal for long-term processed dough in stores