
4 minute read
New start in Würselen
After a change of owner and a fresh start, Kronenbrot’s entire business went through a thorough optimizing and restructuring examination. The first steps included a new, automated raw materials metering controller in the Würselen works.
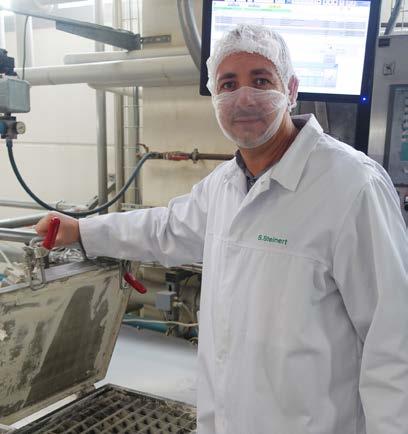
+Silvio Steinert is not easily frightened by anything. When he came to Kronenbrot in 2015, the word “insolvency” was no longer unknown. He signed the contract nevertheless, and in a sense he benefits from that today. He knows better than anyone else the problems and weaknesses of the production facilities in Cologne (sliced and unsliced bread), Witten (toast-bread and sandwich bread) and Würselen (brown bread, sliced and toast bread, and fine pastries), and is aware of the investment backlogs that need to be dealt with first of all.
The silo controller in Würselen, built in 2000 and with a dozen metering points for dry materials and two for liquids, seven blowers and 156 flaps, weighing machines and valves, was at the very top of his list of urgently needed investments. Although vital for daily production operations, it was almost impossible to obtain spare parts for the old server, and on top of that the plant had been modified and adapted several times during the past 17 years and the documentation was anything but continuous and complete.
When it was clear in 2017 that the business would carry on, the raw materials metering controller was at the very top of
Steinert’s wish list. Speed was essential, since even partial failures of the old controller could have brought the dough production process to a standstill instantly at any time.
So in February his planning was already finalized and he received the budget. As well as the new controller, the plan was to include two residual bread plants that would convert finely comminuted scrap bread from the production operation, segregated by product types, into a liquid that could be metered automatically and stored in tanks, some of which already existed.
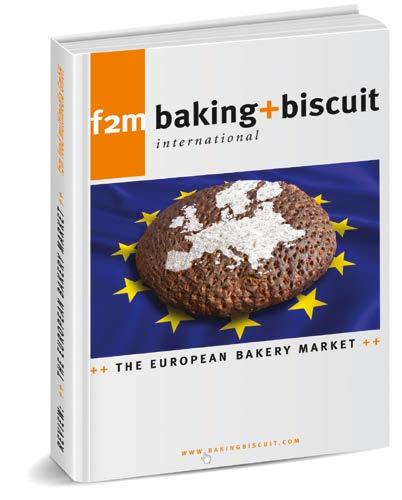
The contract was awarded to Automation X in early May. Heiner Siegrist, the Austrian automation specialist’s agent in Germany, had given an assurance that an emergency manual control program would already be available from July onwards. On top of that, the Graz company guaranteed that the changeover would take no longer than 48 hours.
To be certain of implementing it, two technicians accepted and analyzed the whole plant in detail in Würselen. Kronenbrot staff travelled to Graz to familiarize themselves with the controller and test it during a Factory Acceptance Test (FAT), because the Styrian company’s software system can test all the functions, recipes etc. and simulate the entire workflow of actual orders even without the physical plants behind it. The test is part of the employee training procedure at the same time.
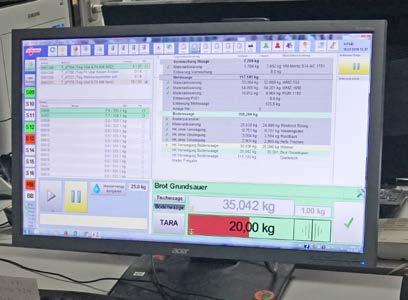
ADVERTISEMENT
Final installation in Würselen took place in late October. The network, servers and remote maintenance had already been installed beforehand. The raw materials metering system’s master switch was finally thrown on Sunday afternoon. Input and output signal transducers in the switchgear cabinet were replaced by modern ones, and the signaling and functioning of the plant components actuated by each of them were tested. “Everything done” was then announced on Tuesday morning. An Automation X technician remained available for a couple more days “for emergencies”, but the raw materials metering system has operated without any malfunctions since then.
©Automation X don‘t miss it f2m food multimedia gmbh Ehrenbergstr. 33 · 22767 Hamburg · Germany info@foodmultimedia.de · Phone: +49 40 39 90 12 27 Fax: +49 40 39 90 12 29 · www.foodmultimedia.de
With a view to future modifications of the lines, the controller’s structure was designed in such a way that plant expansions and/or the incorporation of further process steps are possible at any time. Moreover, the server-client concept allows the whole plant to be operated and supervised by any of the operating staff with the correct password. In addition, the controller’s construction with redundancy provides maximum operating reliability.
A new feature compared to the old plant is that the installation has a comprehensive information package extending far beyond recipe management. Basically, this creates a batch report from which it is possible to retrace what was weighed out, with which metering tolerances, for which recipe and when, irrespective of whether it was done automatically or, as currently happens with small components, by hand. At the same time, this batch report is a batch traceability tool, since it records not only where the raw materials came from and where they went, but also the complete materials consumption in a given period of time, and combines this information with that for the batches produced from it.
To enable the line functions to be monitored centrally, and breakdown risks to be detected if necessary, the system meticulously records every switching operation of valves, motors etc., thus enabling fast, precise analysis in the event of a malfunction, what led to it and where there is a need to intervene. Likewise, based on these recordings it is also possible to define trigger points, e.g. that critical components must be checked or replaced after a certain time or number of movements in order to forestall a breakdown. If, with the appropriate approval, someone intervenes and switches a valve or motor manually, that is also recorded and can thus be included in the technical analysis at a later time.
The stored batch traceability data, such as that for function monitoring, can equally well be used by the production management, both as a retrospective analysis tool and as an instrument to optimize future production planning.

For one thing, the new controller has averted one of Silvio Steinert’s acute failure risks. However, he’s still a long way from being able to lean back and relax because of that. A ten or fifteen year investment backlog can’t be made up for in just a few weeks. Investments in automated slicing processes, a bread line and a sterilization oven are already being pushed forward. Reorganization and system standardization of the process automation are equally important to him, to enable a faster, more flexible response. There is also a need for central control of production in the various works, and networking them with ERP system is planned in the next phase.
Although one or two top performers were lost due to the insolvency, and great demands were made of the remaining employees, Steinert knows he now has the backing of the workforce. No day goes by without him being present in the production buildings, listening, looking and responding. The fact that investment is taking place again has been noticed just as favorably as the increasing capacity utilization. According to Steinert: "We will soon regain the stollen market as we are one of the few producers that hearth-bake stollen in the traditional way. Although we were down by 10,000 units in 2017, we will be back in 2018 with higher turnover." +++