
7 minute read
technologies
20 technologies
Reinventare il taglio laser utilizzando il coil
Advertisement
Francisco Pérez, Direttore del canale OEMs
Anche se può sembrare relativamente nuovo, il taglio di pezzi 2D da coil è abbastanza vecchio e non è affatto un processo legato al laser. Infatti, le prime macchine alimentate da coil, invece che dai formati standard pretagliati, sono state le macchine al plasma e, in particolare, le macchine orientate al settore della ventilazione e dell’aspirazione (HVAC) in quanto utilizzavano principalmente spessori sottili, 0,6...1,2 mm, solitamente forniti in formato coil.
Tuttavia, è con il boom dei laser a fibra, con i loro risparmi sui costi, con la loro “facilità” di produzione e quindi con la riduzione del prezzo e della diffusione, che questa nicchia di mercato si è aperta, fornendo alcuni vantaggi rispetto ai laser convenzionali che utilizzano formati pretagliati e con un piano di lavoro fisso. Qui ci concentreremo principalmente sul taglio laser, anche se tutto potrebbe essere applicato a qualsiasi tecnologia di taglio 2d (principalmente plasma). Va ricordato che queste macchine sono destinate ad una specifica nicchia di mercato, quella della lamiera sottile e con elevati tassi di produzione. Il taglio da coil risolve alcune delle problematiche del laser convenzionale, tra queste:
Ottimizzazione del tempo: Sulle macchine convenzionali, utilizzando formati standard di lamiera (ad es. 3000x1500) e spessori sottili, le attuali potenze laser permettono di tagliare ad alte velocità (oltre 8000 mm/min), questo rende il tempo di cambio della lamiera (cambio dei piani) rispetto al tempo di taglio di un nesting completo (una lamiera) talvolta superiore al 30%, o, a parità, un terzo del tempo totale del ciclo viene utilizzato per il cambio della lamiera. Le macchine che tagliano da coil non hanno questo handicap, in quanto alimentano la zona di taglio in modo continuo.
Ottimizzazione del materiale: Trattandosi di un formato “illimitato”, gli scarti che possono rimanere alla fine dei formati pretagliati vengono utilizzati nella successiva area di lavoro. A seconda del tipo e del mix di pezzi, questo risparmio può arrivare fino al 10% del materiale. È possibile tagliare i pezzi di “qualsiasi lunghezza”: Le macchine a banco fisso limitano la lunghezza massima dei pezzi alla loro dimensione di banco, in una macchina per il taglio delle bobine questa limitazione non esiste. Ottimizzazione dei costi: Il taglio laser da coil riduce il prezzo del materiale rispetto a quello acquisito in formati pretagliati e, se a questo aggiungiamo l’ottimizzazione del tempo, ci troviamo al cospetto di un sistema adeguato per volumi importanti di pezzi ripetitivi. Ma, come per ogni nuovo processo, ci sono questioni specifiche da affrontare: -Evacuazione dei pezzi: Lo spostamento della lamiera (coil) e quindi dei pezzi, quando sono stati tagliati, può causare la collisione del materiale con l’ambiente circostante.
-Evacuazione dei residui generati: Durante il processo di taglio, soprattutto durante il taglio dei fori, si generano pezzi di lamiera che possono di nuovo causare la collisione del materiale con l’ambiente circostante.
-Tempo di cambio della bobina: Nonostante il miglioramento dei tempi di questo processo, se fosse necessario cambiare il materiale e/o lo spessore dei pezzi con grande regolarità, il cambio della bobina potrebbe diventare un ostacolo.
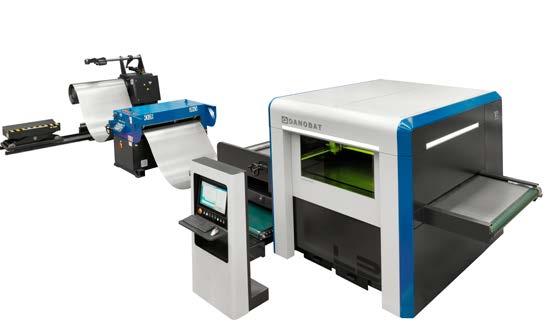
Il taglio laser partendo da coil riduce il prezzo del materiale rispetto all’acquisto di formati pretagliati

Ogni costruttore sviluppa varie “soluzioni” a questi primi due problemi: botole, microsezioni, distruzione dello scheletro, ecc..., sarà interessante vedere quali metodi verranno imposti sul mercato. Proseguendo con il tipo di macchina sviluppata per il taglio di materiale continuo (coil), possiamo trovare due gruppi: -Macchine che tagliano a materiale fermo: Queste macchine srotolano una parte della bobina e alimentano un’area di lavoro. All’interno di questa, la macchina funziona come una normale macchina a banco fisso/chiusura normale, spostando il ponte e la testa in XY. Quando tutte le parti dell’area di lavoro sono state tagliate (alcuni pezzi possono essere parzialmente tagliati perché più lunghi dell’area di lavoro o si trovano tra due aree), la macchina srotola nuovamente la bobina e fa avanzare/posiziona la lamiera. -Macchine che tagliano con il materiale che si muove “on the fly”: Queste sono ovviamente le macchine più produttive, ma anche le più complesse e sofisticate. Di solito, data una velocità costante dell’avanzamento della bobina all’interno di un’area di lavoro, il ponte con la testa di taglio si muove in XY, consentendo elevate velocità di taglio.
Siamo davanti ad un sistema adatto a volumi importanti di pezzi ripetitivi
Per ottenere velocità di taglio più elevate, queste macchine sono state dotate di più teste di taglio (2 o 3), ciascuna delle quali è in grado di tagliare contemporaneamente una zona diversa dello stesso pezzo e di ottenere velocità di taglio molto elevate.
Queste macchine sono state chiamate a competere con le tradizionali linee di “blanking” di tranciatura a pressa. Infatti, il loro nome abituale è “laser blanking” e la loro maggiore presenza è stata focalizzata sul mercato automobilistico, sugli OEM e sul TIER1, anche se va notato che, data la versatilità del laser, questa soluzione può essere applicata a qualsiasi settore che richieda alti tassi di cadenza dei pezzi. -Esiste anche un piccolo gruppo di macchine in cui la testa di taglio è fissata su un asse, si muove solo trasversalmente all’avanzamento della lamiera, e la lamiera/bobina si muove avanti e indietro. Queste macchine sono ovviamente più economiche, ma non hanno avuto un grande impatto sul mercato. Lantek offre la possibilità di programmarle per ottenere il massimo dalle capacità della macchina. Ancora una volta il software gioca un ruolo essenziale in quanto non solo controlla, ma fornisce al processo un’intelligenza sufficiente per collegare i diversi agenti che entrano in gioco sulla linea.
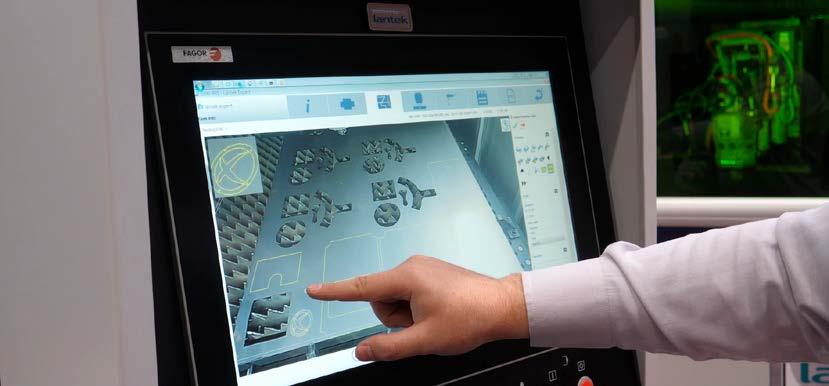
24 innovation
Connettività della macchina
José Antonio Lorenzo, Ingegnere software
Uno dei principali facilitatori dell’Industria 4.0 è la capacità di connettersi con le macchine dell’impianto ed estrarre informazioni sul loro stato, sui loro parametri, sul lavoro che stanno svolgendo e così via. La connettività delle macchine è vitale per realizzare la visione dell’industria 4.0 perché è il primo collegamento nel ciclo di elaborazione dei dati. Disponendo di dati possiamo elaborarli per ottenere informazioni, e sulla base di queste informazioni possiamo capire meglio ciò che accade nell’impianto. Questo ci porta ad intraprendere azioni volte a migliorare la produttività, che possono eventualmente richiedere l’estrazione di nuovi dati e/o metriche dalle nostre macchine, chiudendo così il ciclo.
Da un punto di vista tecnico questo primo anello è il più difficile. Una volta che si hanno i dati, completare il resto del ciclo è un problema che si riduce ad avere il giusto software e la giusta competenza. Tuttavia, il primo passo è di solito il più complicato. Perché? L’ecosistema delle macchine utensili è estremamente complesso, con centinaia di costruttori, macchine altamente specializzate e una moltitudine di caratteristiche. I produttori sono concentrati nel rendere le loro macchine più veloci e più precise e hanno tradizionalmente relegato le caratteristiche di connettività in secondo piano. Fortunatamente, la situazione sta cambiando. Sempre più macchine stanno incorporando un qualche tipo di connettività standard, come la ben nota OPC-UA. Quest’anno, nonostante tutte le difficoltà legate alla pandemia, sarà possibile assistere al lancio dello standard UMATI, che rappresenterà un importante passo avanti in termini di connettività delle macchine. UMATI fornisce un vocabolario standard per la comunicazione con le macchine utensili attraverso l’OPC-UA e sarà senza dubbio uno degli standard che le macchine future incorporeranno come opzione.
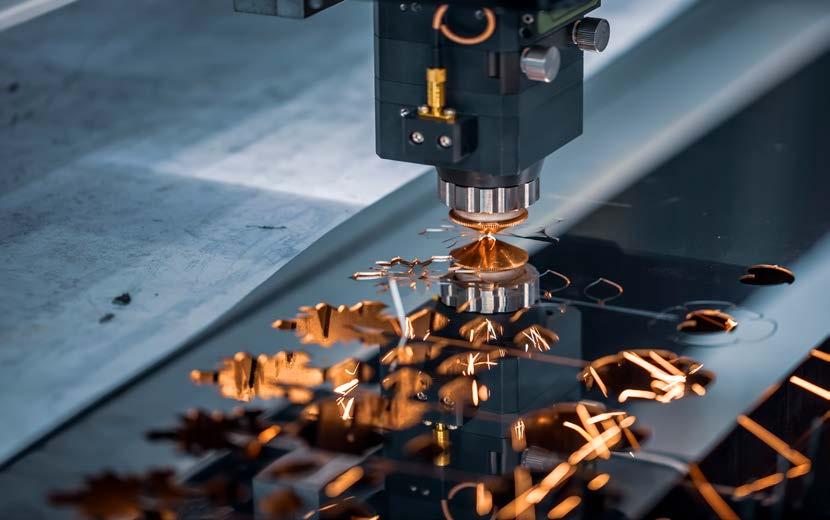
Nel frattempo, la necessità di connettività è una realtà in questo momento, e il parco macchine esistente non incorpora ancora meccanismi di connettività così avanzati. È quindi necessario collegare tutte queste macchine per continuare a beneficiare degli investimenti che sono stati fatti in esse all’epoca senza perdere il treno dell’Industria 4.0 e l’aumento di produttività che essa promette. Senza perdere di vista l’evoluzione dello standard UMATI, Lantek sta già lavorando per offrire ai propri clienti soluzioni di connettività perfettamente integrate con il software che già produce. Lantek, in qualità di facilitatore dell’implementazione dell’Industria 4.0 nel settore del taglio della lamiera, fornisce gli strumenti per rendere molto più facile ai nostri clienti il raggiungimento di quel primo anello di cui abbiamo parlato all’inizio: la connettività delle macchine.
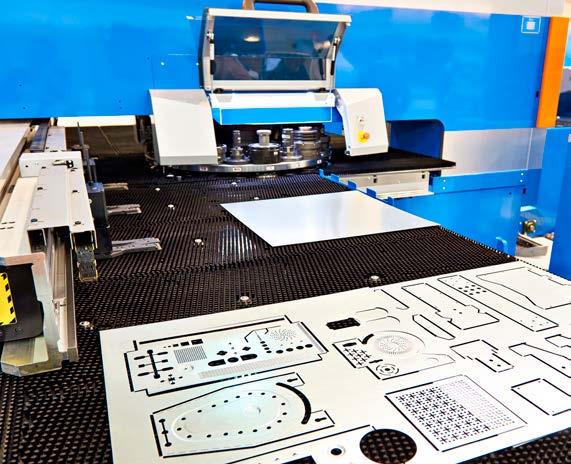