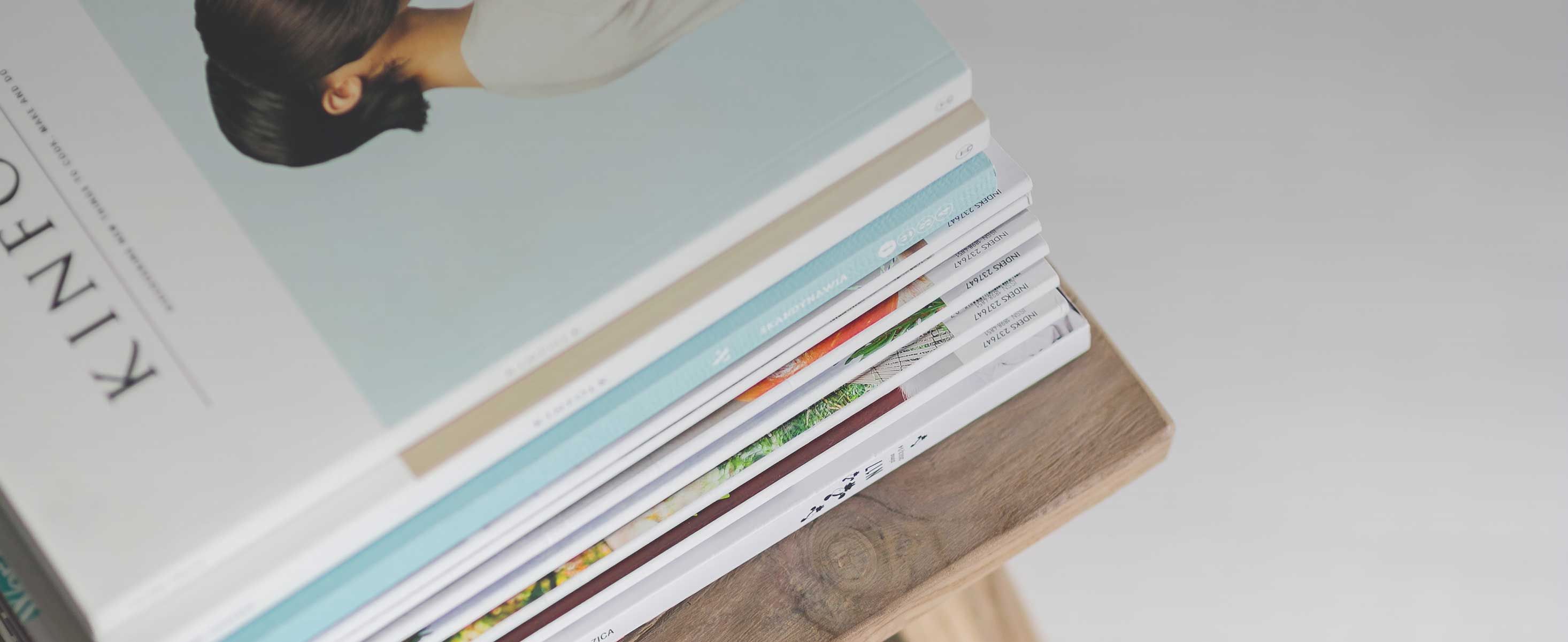
1 minute read
HUMIDITY
to a world of different climates, moistures and temperature environments that each cause a different reaction to its stability and performance over time. These changes can make a huge impact on the visual quality of the wood along with cupping and warping that’s a natural part of the drying process. As thin sheets of wood veneer make their way through the mill and are bonded together to make different thicknesses of plywood panels, each dries at a different rate. In the final milling stages sheets are often kiln or heat dried to speed up the process before they’re banded and end wrapped to be shipped around the world… and voila, you’ve got laser ready Baltic Birch! Not so fast… if you’re using it in your laser, you’re likely not grabbing a sheet fresh from the mill in Russia or the Baltic Region.
Now the journey begins as those bundles of plywood make their way from the mill to the port to continue their journey to countries across the world including the United States. As they’re packed into sea crates they once again face a new set of elements including temperature changes and biggest of all, humidity changes, as they travel the ocean for hundreds and sometimes thousands of nautical miles until they reach their destination ports. Once they reach their destination they’re unloaded and transported to warehouses typically along the western and eastern coast of the country, depending on the port of arrival where they experience yet another change in environment. These gargantuan warehouses are home to thousands of materials that are imported